Bubble Butt, also known as positive buoyancy syndrome, is an increasingly common disorder among turtles like Charlotte, a male green sea turtle at Mystic Aquarium in Connecticut. The syndrome is caused by trauma — typically from run-ins with boats — and creates an irregularity in the turtles’ shells that traps air, crowds their organs, and makes it very difficult to swim normally.
Charlotte was initially found in 2008 in Jekyll Island, Georgia, and taken into care when it became obvious that he couldn’t swim or eat enough to survive. The team at the Georgia Sea Turtle Center cared for him before calling in reinforcements from the Mystic Aquarium.
Dr. Jenn Flower was the Chief Clinical Veterinarian at Mystic Aquarium at the time and realized that Charlotte — by this time identified as a male but keeping his name — needed help. Mystic's aquarist and veterinary teams tried everything, from adhering weights directly onto Charlotte’s shell, to outfitting him with a multi-strap weighted belt made from fabric. These early attempts proved unsuccessful; the adhesive would cause irritation, or he’d scrape the weights off on the side of his tank. Dr. Flower and the rest of the veterinary team realized they needed to think outside the box for a solution, and 3D printing was at the top of the list.
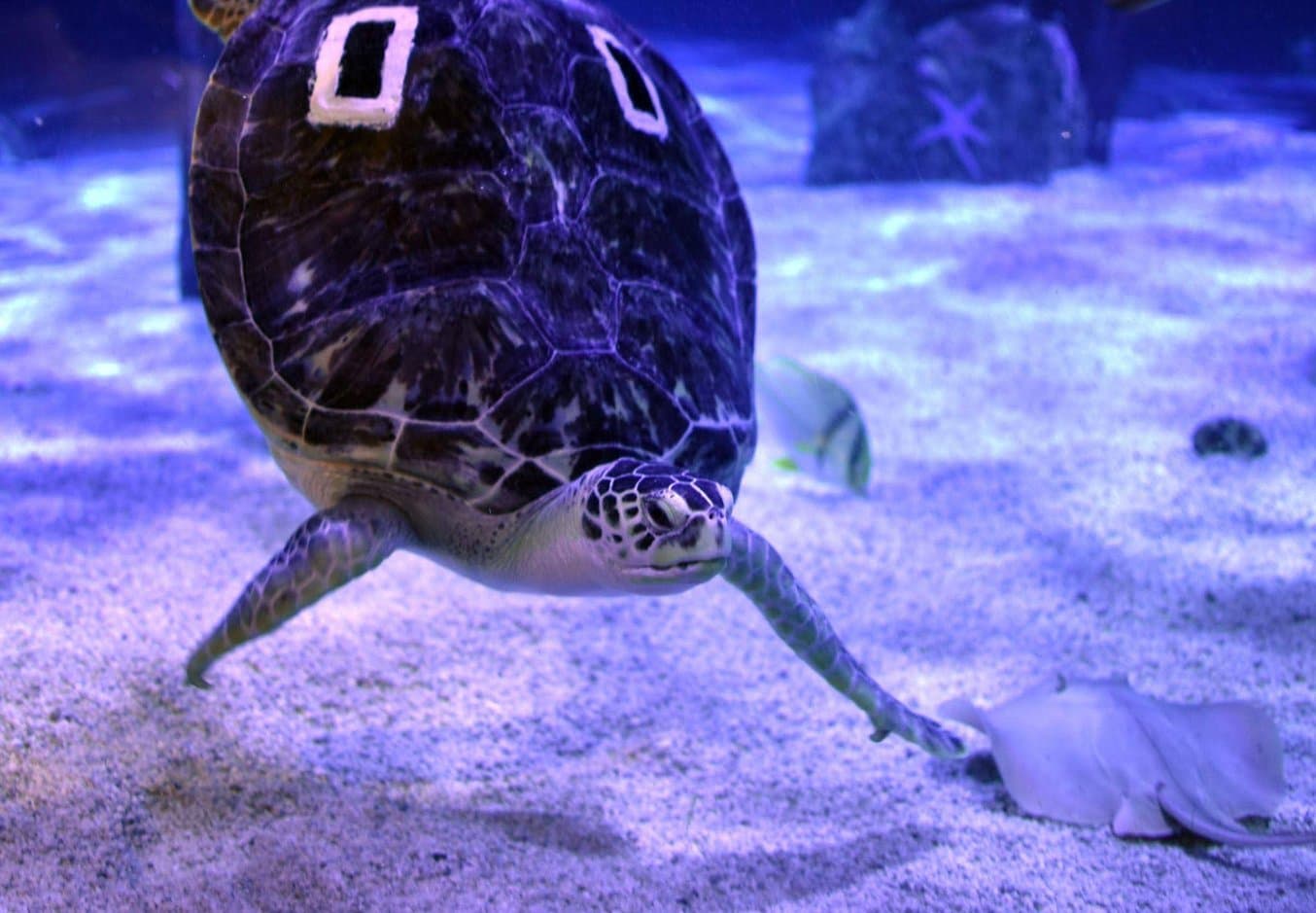
Mystic tried several methods of weighing down Charlotte’s Bubble Butt: including weights stuck directly onto his shell. The adhesive caused some irritation however, and the team had to keep trying.
Inspiration from Minnesota to Mystic
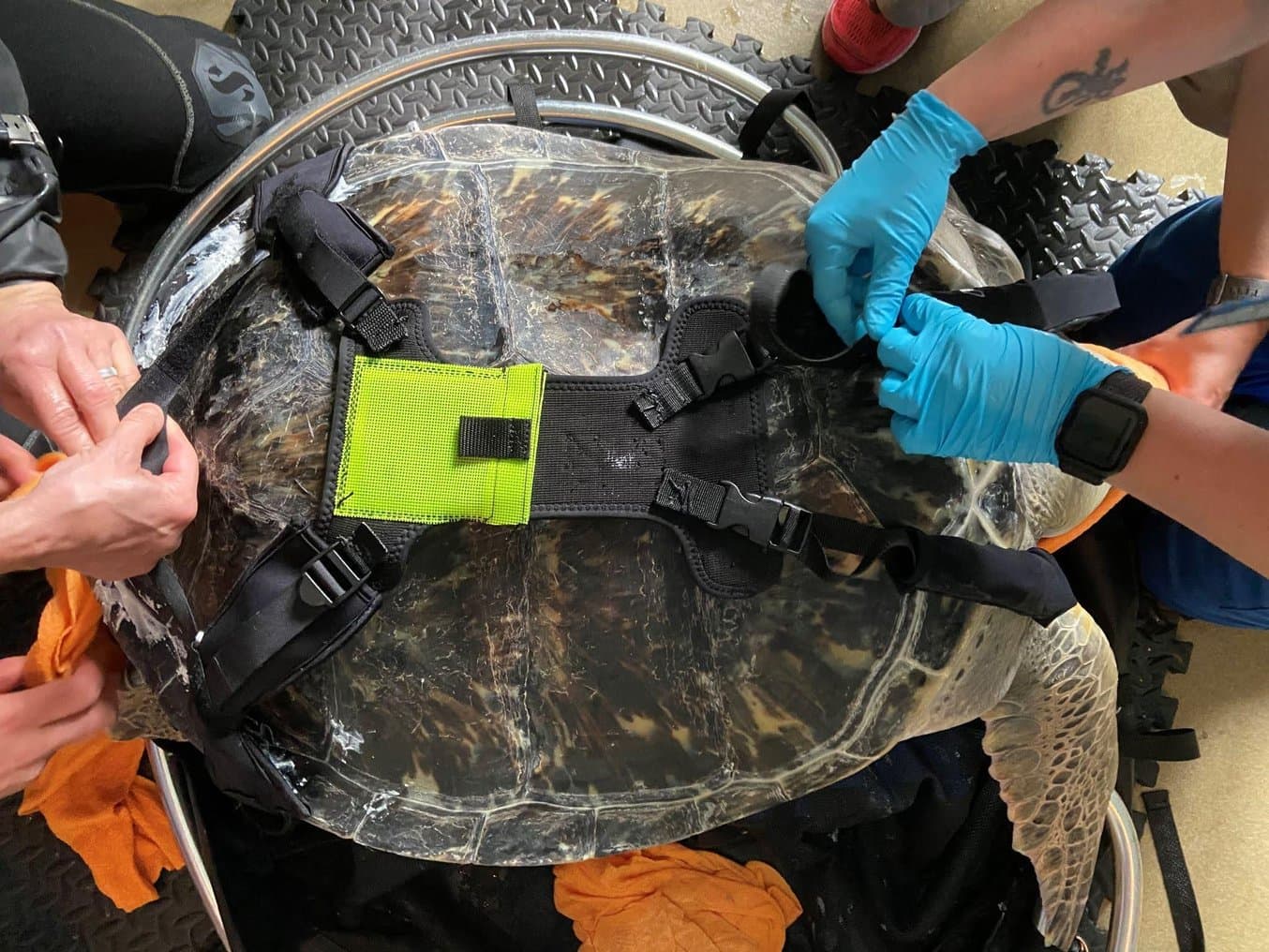
This fabric harness seemed like it was working, and its adjustability was helpful because it allowed movement and growth. However, the harness wasn’t snug enough, and Charlotte was able to scrape it off and detach it.
One source of inspiration in particular spurred the Mystic team to consider 3D printing. A high school student in Minnesota, Gabriela Queiroz Miranda, had developed a weighted belt for turtles suffering from Bubble Butt. Queiroz Miranda used a 3D scanner and 3D printer to iteratively design and test her solution on her classroom turtle, Voldetort. Her project was published in Science News Explores, and the article inspired Dr. Flower to reach out to Adia, a 3D printing solutions provider in Connecticut. When Dr. Flower contacted Adia, Director of Additive Manufacturing Nick Gondek immediately knew that they could leverage their 3D printing expertise to do some good.
3D workflows excel in applications requiring some degree of customization. When complex geometries, low volumes, and organic shapes make it too difficult to fabricate parts using traditional methods, 3D printed parts are the most cost-effective and simple option.
“The problem we have been trying to solve is essentially putting weights on the back of Charlotte, which sounds very simple, but it ended up being a very challenging process. The only way to really get something to stick to Charlotte was to build a custom device,” says Gondek.
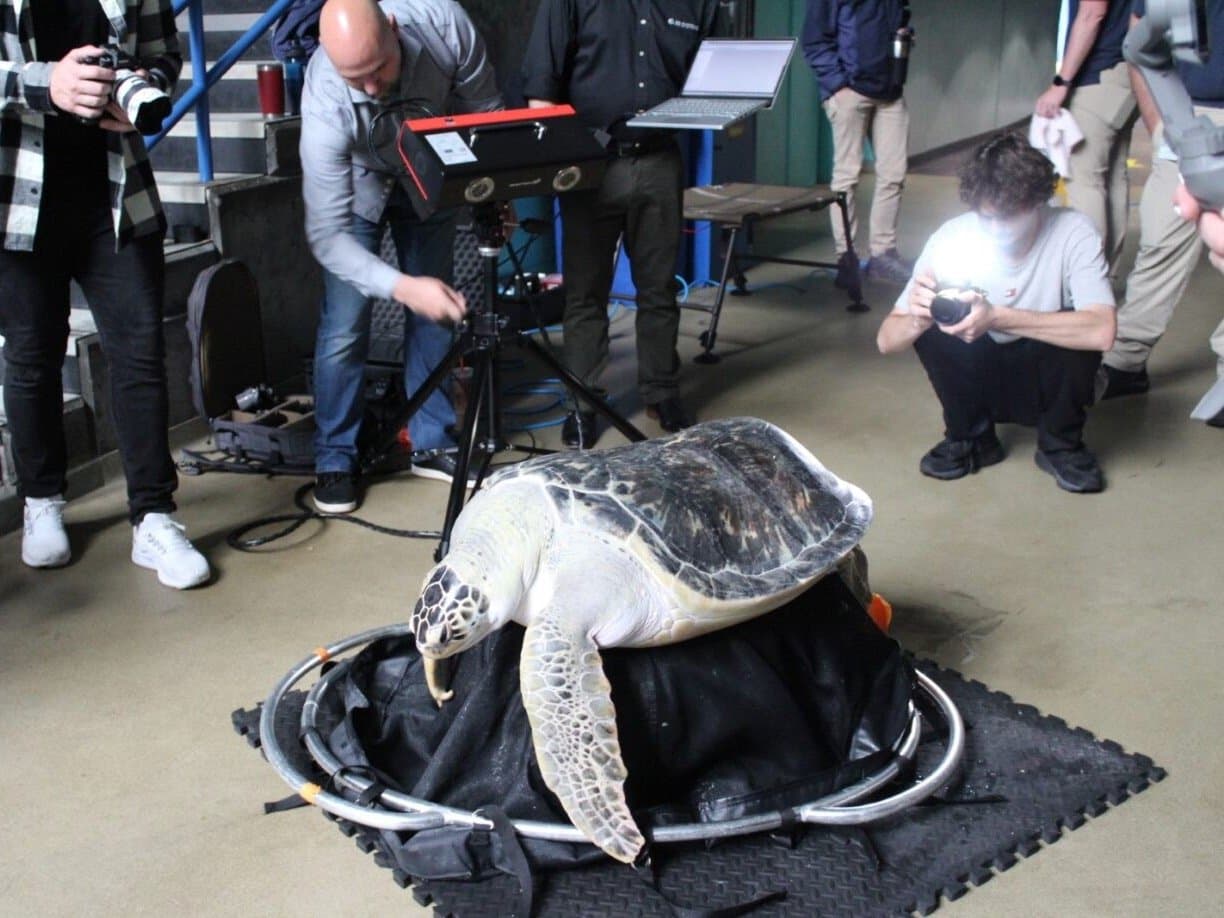
Chris Wilczewski and the Functional 3D team are experts in 3D scanning – they were able to create high-resolution 3D images of Charlotte’s shell so that the software design team, led by New Balance’s Chris Wawrousek, could design a computational model that generated a custom harness for Charlotte.
To build the 3D workflow, Adia brought on Chris Wilczewski and the Functional 3D Team - experts in 3D scanning, to help perform high-resolution 3D scans of Charlotte. These scans would be the bedrock for the rest of the design project, allowing designers and engineers to create something snug but comfortable for Charlotte that could be removed and altered whenever necessary.
The Functional 3D Team also needed to balance their need for precision and thoroughness with the veterinary precautions that Dr. Flower and the Mystic aquarist team had in place to keep Charlotte safe. “Their contributions were a significant part of this project, driving the digital workflow on the design of the harness,” says Gondek.
Helping Charlotte Find New Balance
New Balance is a leader in computational design for footwear, and Senior Creative Lead, Chris Wawrousek, saw an opportunity to repurpose his design skills for a good cause — developing and modeling the generative system that could help not only Charlotte, but turtles like him.
When the time came to develop a design built upon the scan data, Adia knew that there was one company with the level of expertise needed. New Balance Athletics designs and manufactures some of the most advanced athletic gear in the industry, utilizing cutting-edge design technology to push the boundaries of what’s possible in sports performance.
Senior Creative Lead, Chris Wawrousek, is a computational design expert. Computational design refers to a method that uses pre-set algorithms and parameters to take in information and generate designs that can solve the problems that information presents, then run simulations that give feedback on the design and help refine it.
“To help solve Charlotte's swimming issues, digital technology has been a great help. Computational design really kind of comes into play where you obviously don't really want to be designing one-for-one manually because it would take a very time-consuming process. So, being able to create a workflow that allows for a custom-generated harness is really powerful,” says Wawrousek.
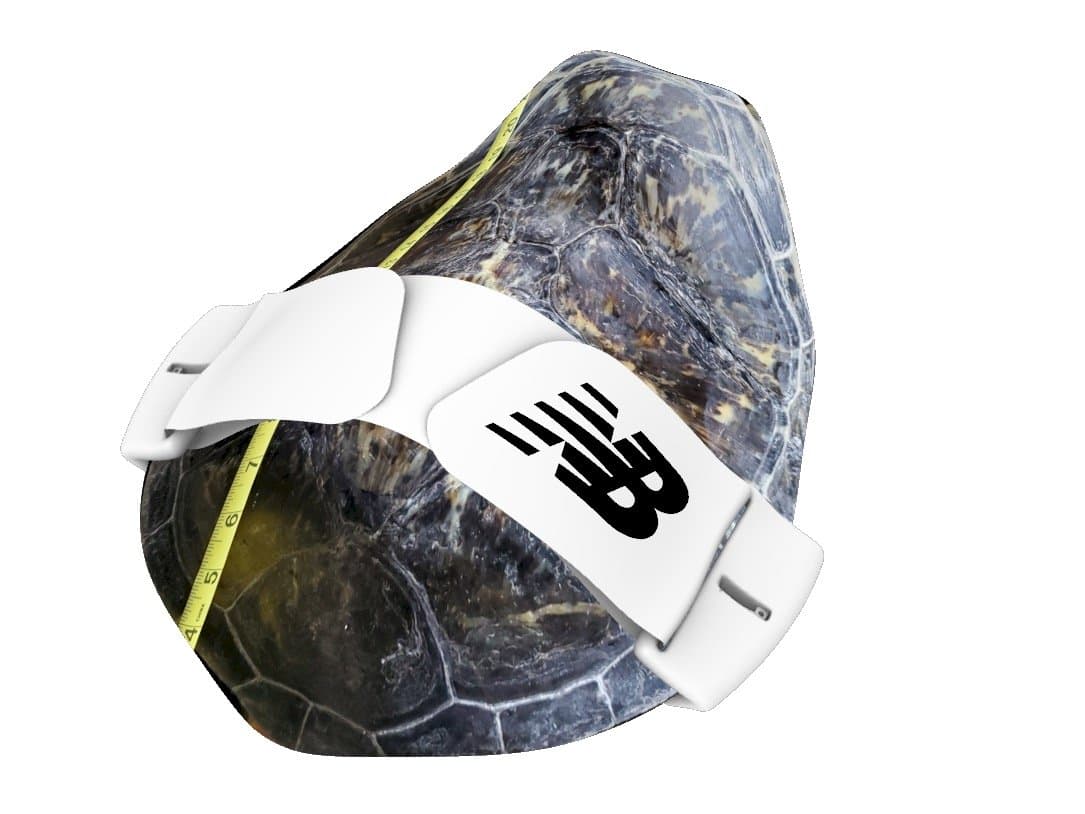
This wide, belt-like harness was an early iteration using the 3D scan data and Wawrousek’s computational design program.
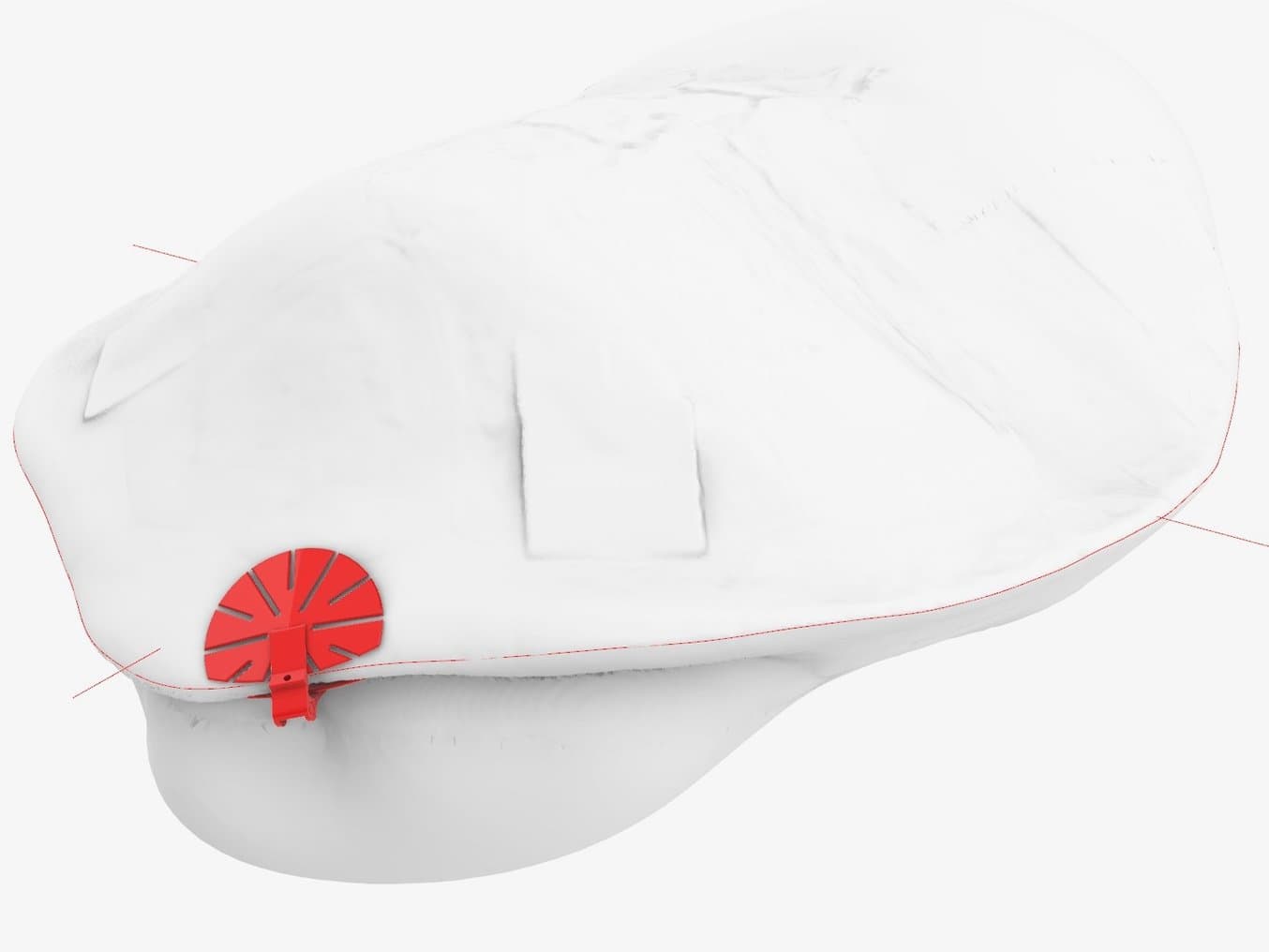
Another iteration consisted of several small clips that clamped around the outer edge of Charlotte’s shell.
The team used Wawrousek’s design to develop multiple iterations, from a wide, belt-like apparatus, to small clips, to thick harnesses with snap-fit features. “A lot of the iterations have stemmed from the comfort to the sea turtle. So we've really had to pinpoint where on the shell we could get enough leverage to hold the harness on and how we could place weights on the harness with the ability to adjust their location,” says Gondek.
After months of design work, they settled on a nimble, lightweight, adjustable harness that wraps around the edge of Charlotte’s shell and can be removed and adjusted as needed. Though they had arrived at a workable design, the job was far from over - they needed to fabricate the harness, maximizing strength, accuracy, and repeatability.
Testing on Turtle Time
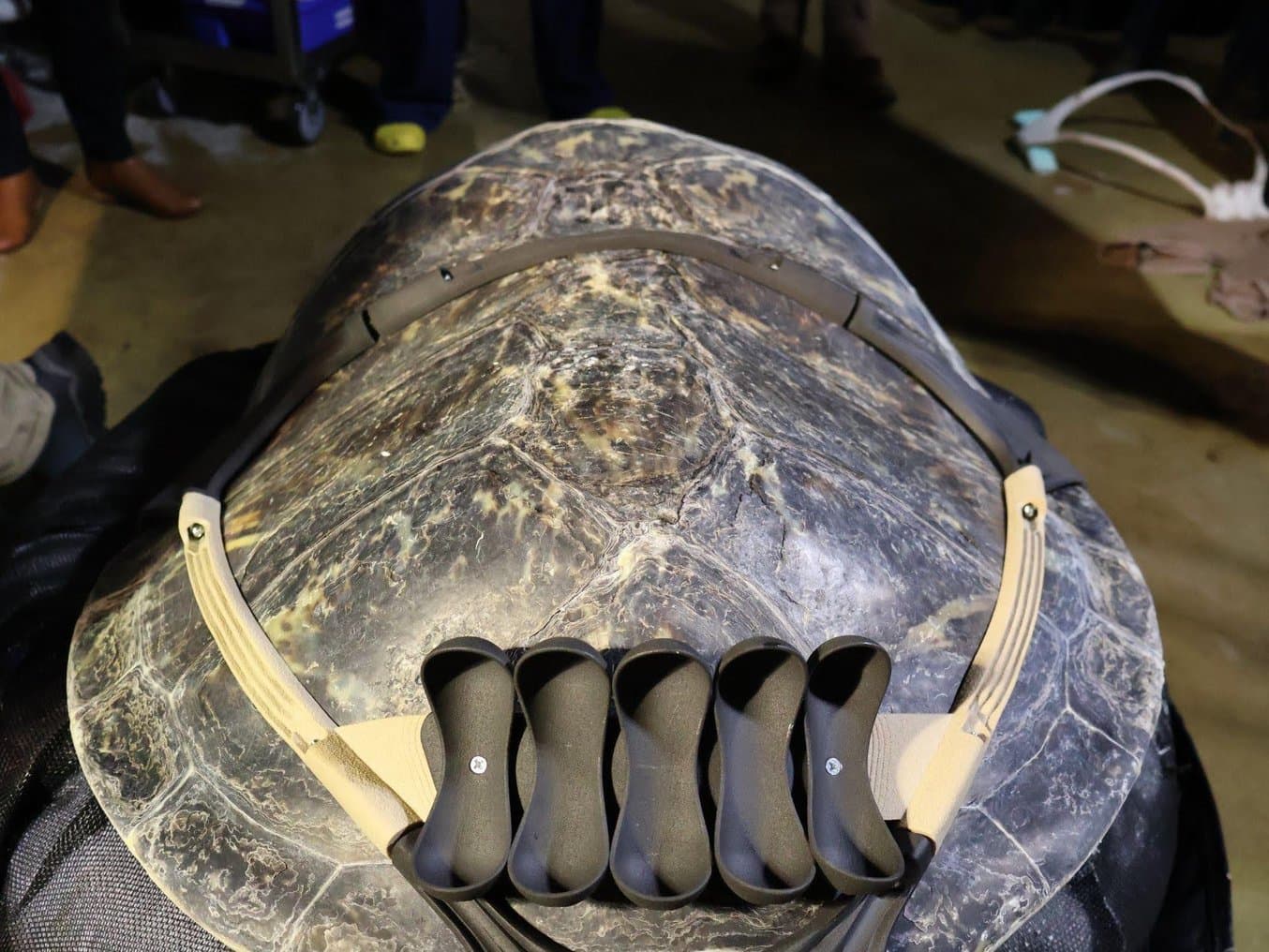
The harness made using Oxford’s Performance Material’s custom material (beige components) and Formlabs’ Fuse Series Nylon 12 Powder (dark grey weight holder components) worked well, and the final iteration looks much like this one.
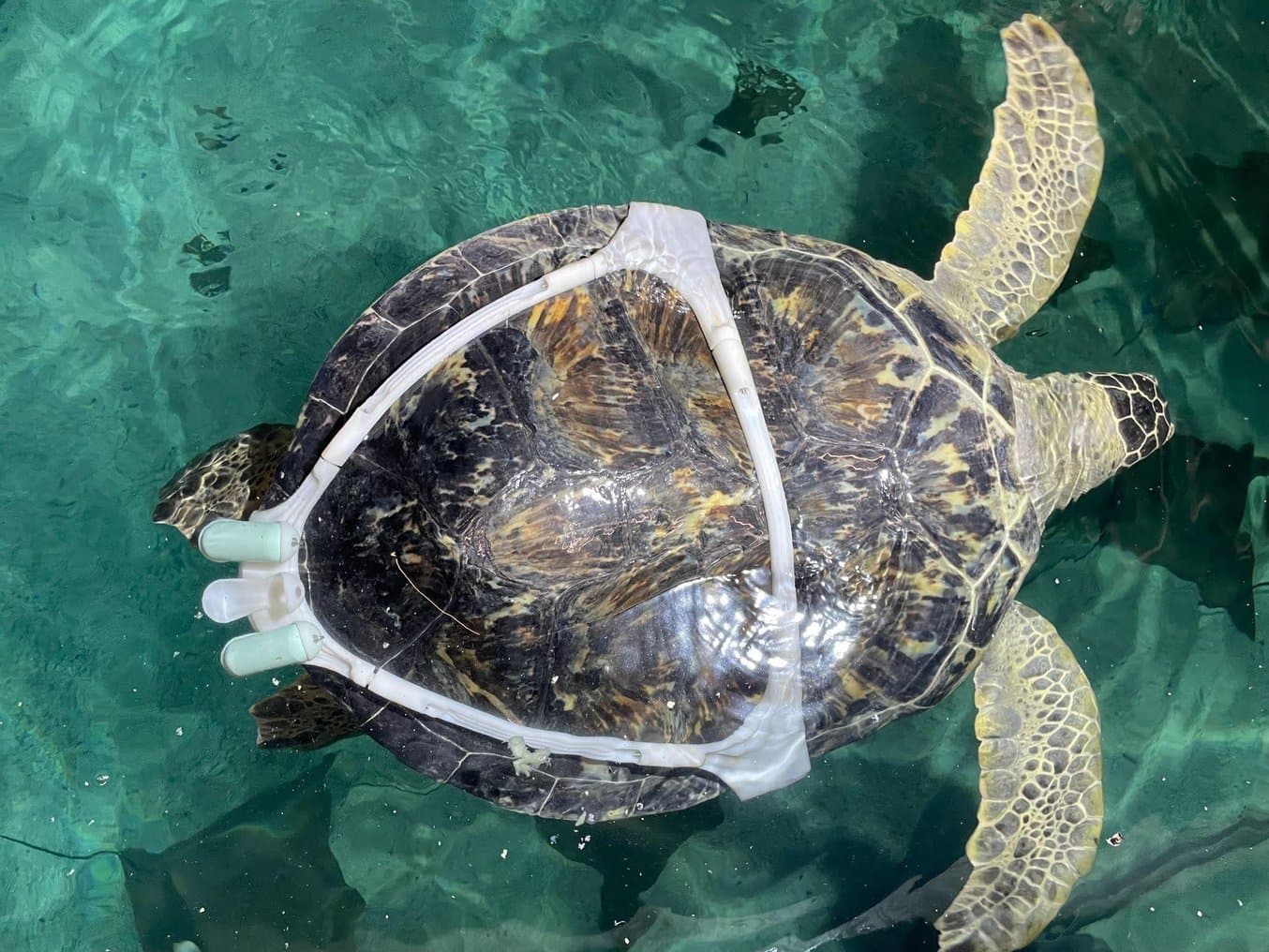
Charlotte was able to swim normally again! This harness, using mostly OPM's material, proved that a snugly-fitting, durable, and lightweight harness was possible, and that Charlotte could get used to the contact around his shell.
Adia has worked with different 3D printing manufacturers and printing materials for years, and collaborated with many of them trying to find the ideal solutions. Oxford Performance Materials (OPM), a manufacturer of 3D printing materials, helped develop a custom material that could be printed on a selective laser sintering (SLS) 3D printer. The SLS parts were high quality and strong, without adding much weight to Charlotte’s body and allowing for slight flexibility as he swam around.
The final iteration 3D printed with the OPM white sintered powder worked well, and Charlotte was able to swim normally and start exercising his rear fins, all steps on the road to getting fully healthy again. But the OPM workflow was customized — both the material and the print process. Adia needed a solution that matched the scalability and accessibility of Wawrousek’s computational design system. “We've looked at many different 3D printing processes for this project and we landed on SLS for a few reasons. One is the build volume, and size of components. Two is that we could build parts without supports. And three was we could find the proper materials that had the rigidity we needed for this project,” says Gondek.
Adia’s partnership with Formlabs presented the perfect option — Formlabs’ Fuse Series SLS ecosystem delivers parts that have the industrial strength that the harness needed, but with an accessible workflow and a diverse range of materials. Formlabs’ Nylon 11 CF Powder offered the rigidity they were looking for, but without the monolithic printer size and complex workflow of other SLS 3D printing systems. “We've had a number of aquariums reach out again asking for assistance. So going into this project, we actually wanted to design the harness to fit in a Fuse build volume solely for the purpose of accessibility. We want to have other aquariums and other facilities have access to SLS technologies. And we believe that the Fuse has one of the largest installation bases and would be most accessible,” says Gondek.
Swimming Straight Forward
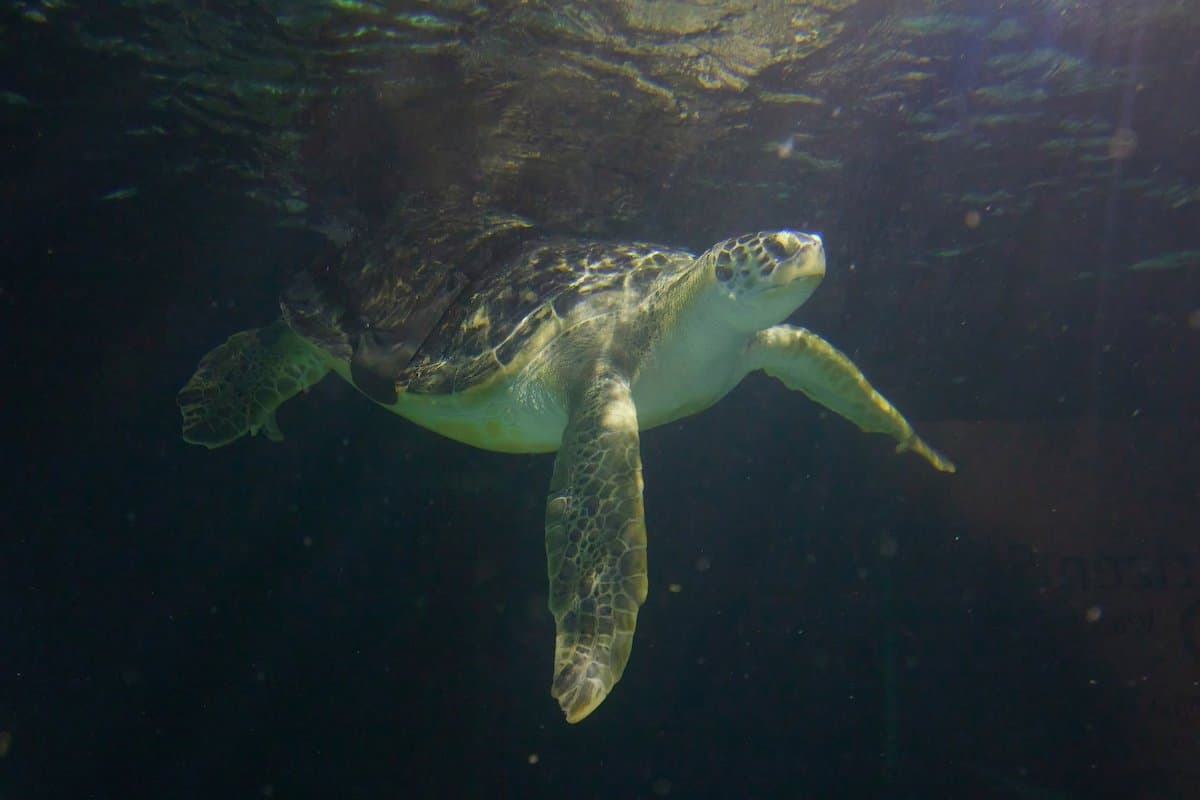
Charlotte was able to swim with the final harness, printed on the Formlabs Fuse Series ecosystem in Nylon 11 CF Powder, and assembled by New Balance, Adia, and Mystic. As he becomes more comfortable, the team will add weights to the harness, counteracting his positive buoyancy even further.
When the final harness was printed, assembled, and attached to Charlotte, the team held their breath. As he gets older, Charlotte, understandably, has less and less patience for people bringing him out of his tank and attaching strange new belts to his shell. But when he was put back in the water, he swam happily, and seemed comfortable.
Claire Bolster, his handler and Aquarist at Mystic, pronounced, “It's looking like a very positive interaction. It's been a little bit since we last put the harness on him. So this new version of the harness is so far seeming like a really good addition for him. And as we're getting him to wear it more and be more consistent, we'll be able to add the weights back in and just see how he tolerates it. But for now, it's a really positive sign that he's doing well with it right off the bat.”
Are you interested in helping Charlotte and turtles like him? The Adia and New Balance teams are looking for qualified individuals to help them continue this project. Check out the poster below, and fill out the short questionnaire if you think your skills would be a good fit.
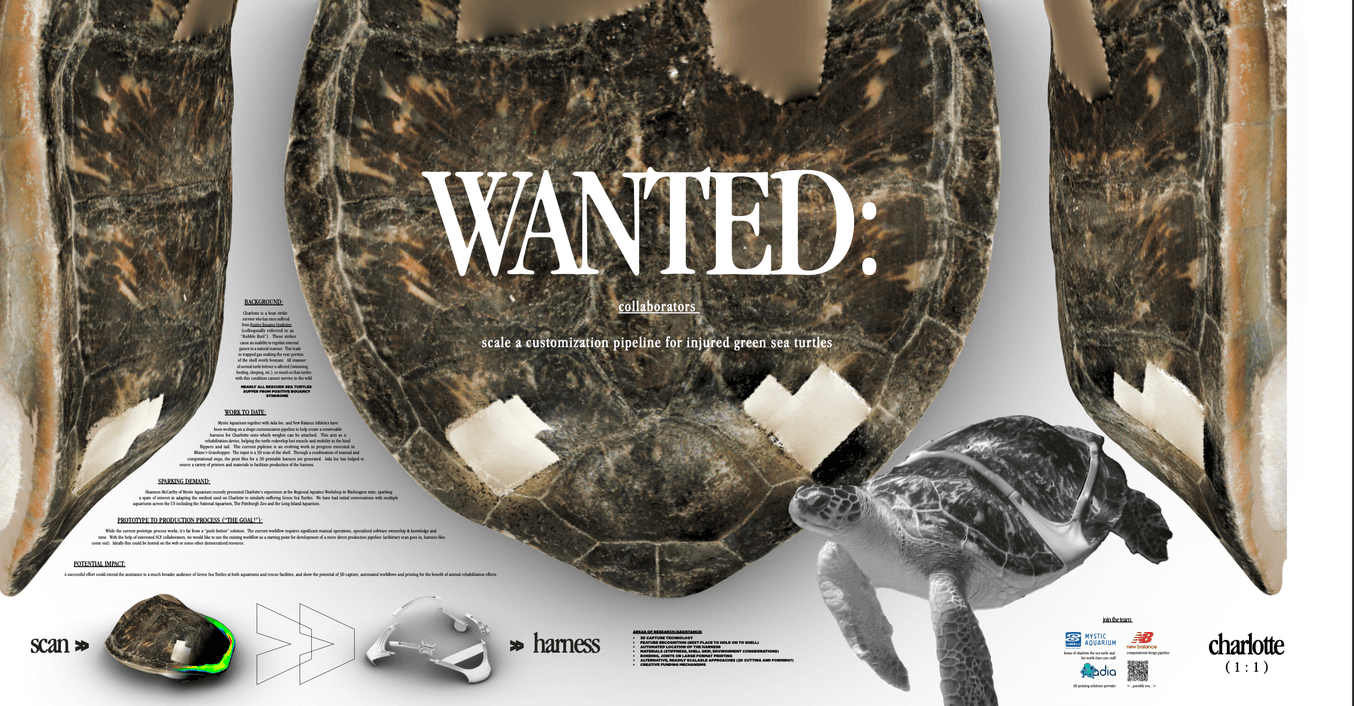
If you have a background in computational design, 3D capture technology, feature recognition, material engineering, large-format 3D printing, or creative funding mechanisms and would like to help turtles like Charlotte, please fill out a short questionnaire. Charlotte's team will reach out if your skills are a good fit for the project moving forward.