Topology Optimization 101: How to Use Algorithmic Models to Create Lightweight Design
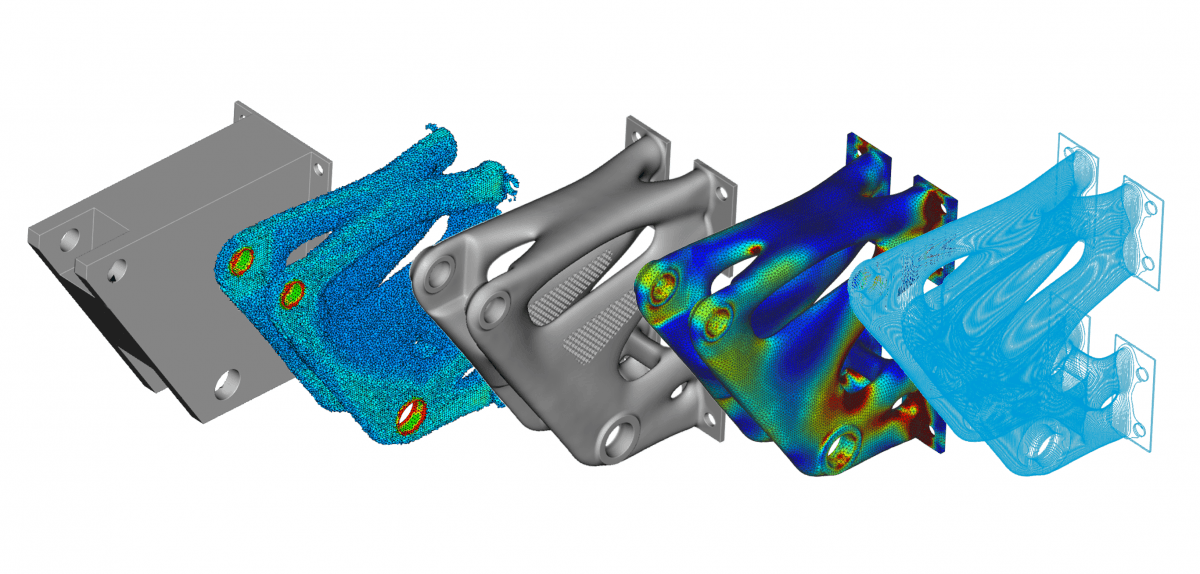
Where does good design meet function? As computer-aided design (CAD) continues to evolve and advanced manufacturing techniques like 3D printing become more widespread, making it possible to create complex parts easier than ever before, designers and engineers can leverage topology optimization software to push boundaries and find new ways to maximize design efficiency.
In this guide, learn about the basics of topology optimization, its benefits and applications, and which software tools you can use to get started.
What is Topology Optimization?
Topology optimization (TO) is a shape optimization method that uses algorithmic models to optimize material layout within a user-defined space for a given set of loads, conditions, and constraints. TO maximizes the performance and efficiency of the design by removing redundant material from areas that do not need to carry significant loads to reduce weight or solve design challenges like reducing resonance or thermal stress.
Designs produced with topology optimization often include free forms and intricate shapes that are complex or impossible to manufacture with traditional production methods. However, TO designs are a perfect match for additive manufacturing processes that have more forgiving design rules and can easily reproduce complex shapes without additional costs.
Topology Optimization vs. Generative Design
Generative design and topology optimization have become buzzwords in the CAD design space, but it’s a common misconception that they’re synonymous.
Topology optimization isn’t new. It has been around for at least 20 years and has been widely available in common CAD software tools. The start of its process requires a human engineer to create a CAD model, applying loads and constraints with project parameters in mind. The software then removes redundant material and generates a single optimized mesh-model concept ready for an engineer’s evaluation. In other words, topology optimization requires a human-designed model from the outset to function, limiting the process, its outcomes, and its scale.
In a way, topology optimization serves as the foundation for generative design. Generative design takes the process a step further and eliminates the need for the initial human-designed model, taking on the role of the designer based on the predefined set of constraints.
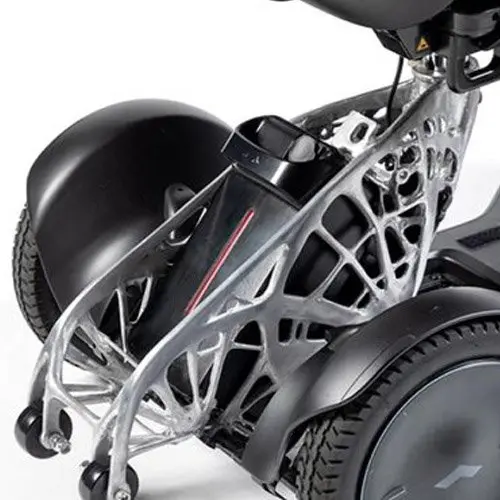
An Introduction to Generative Design for Producing Lightweight Parts With 3D Printing
In this webinar, Formlabs Product Marketing Lead Jennifer Milne will provide a simple overview explaining what generative design is, framed in a way that is applicable to mechanical part design, including a step-by-step tutorial of Fusion 360 where she’ll produce a lightweight bracket.
How Topology Optimization Works
Topology optimization usually takes place towards the end of the design process, when the desired part needs to have a lower weight or use less materials. The designer then works to discover certain preset parameters, such as applied loads, material type, constraints, and layout.
Structural topology optimization first determines the minimum allowable design space necessary for shape optimization of the product. Then, virtually, the topology optimization software applies pressure on the design from different angles, tests its structural integrity, and identifies unnecessary material.
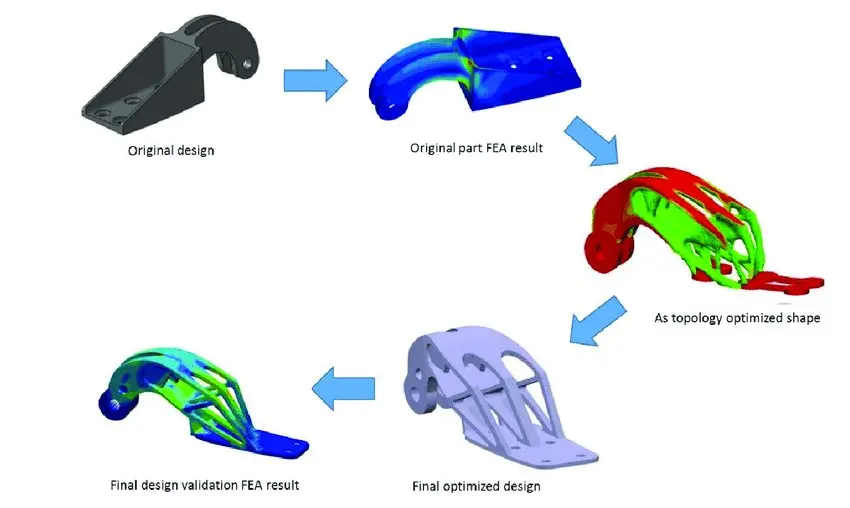
The topology optimization workflow. (source)
The most common and practical technique for topology optimization is the finite element method (FEM). First, FEM takes into account the geometric design for the minimum space allowed—along with other factors—and breaks the design into parts. It then tests each finite element for rigidity, compliance, and redundant material. Finally, FEM stitches the parts back together to finalize the full design.
Validating the design involves determining a threshold for the element density field between a value of 0 and 1. A value of 0 voids material in a designated region of the structure, while a value of 1 sets the designated region as solid material. The designer can then strip the model of all unnecessary material and finalize the topology optimization portion of the design.
Before additive manufacturing, designers discarded many of the complex shapes created by topology optimization as they were not feasible to manufacture, and its potential remained unrealized.
Advantages of Topology Optimization
Engineers need a good reason to break away from classic design and manufacturing methods. If an innovative design does not cost less, work better, or save time, a manufacturer will see little reason to change. Let’s look at the benefits of topology optimization.
Saving Money
Many of the complex geometries that come from topology optimization would make production costs unfeasible with traditional manufacturing practices. But when paired with 3D printing, this complexity comes at no additional costs.
Manufacturing 3D printed parts can still be more expensive to produce than their non-optimized, traditionally manufactured counterparts, but these lightweight designs can offer larger cost savings to manufacturers in other ways:
-
Better fuel efficiency as there is less energy required to put parts in motion thanks to the lower friction (airplanes, automotives)
-
Lower packaging and transportation costs
-
Less heavy machinery necessary for assembly lines
Solving Design Challenges
Topology optimization can solve common challenges in the design process, such as the following:
-
Resonance occurs when the force permitted by a shape in a system overpowers the system. This can result in mechanical deformation, reduction of mechanical structure, and pollution emissions.
-
Thermal stress is any change in a material’s temperature—due to friction or other factors—resulting in thermal fatigue and deformation within a system.
Sometimes, design optimization involves competing objective functions, such as size optimization and weight. For example, aerospace parts benefit from being lightweight but also must withstand tremendous amounts of torque, stress, and heat. An algorithm can balance a design to account for each of these objective functions and find the sweet spot.
Saving Time
While working with topology optimization software still requires significant expertise, TO tools can rapidly produce high-performance designs that an engineer could not create manually. This means less time and energy spent in CAD design and reliable end results with fewer iterations of the design.
When it comes to the manufacturing of the parts, additive manufacturing processes can also turn around final parts quickly as they don’t require tooling, which can take weeks or months to be delivered for traditional manufacturing methods.
Reducing Environmental Impact
Creating smaller, lightweight products reduces a manufacturer’s overall carbon footprint by requiring less building material in the first place. When compared to traditional subtractive manufacturing tools, parts produced through additive processes also generally require less raw material and produce less waste.
Oftentimes, the most significant savings occur throughout the lifetime of the parts. For example, lightweight parts for airplanes reduce their environmental impact by requiring less fuel.
Eliminating Errors
At its foundation, topology optimization is about eliminating errors. By conducting stress testing, the process accounts for a wide range of variables and avoids risky assumptions that could lead to faulty products.
Applications of Topology Optimization
The high performance, efficient, and lightweight designs possible with topology optimization techniques apply across a wide range of industries.
Aerospace
Due to the importance of weight reduction, topology optimization is a natural match for aerospace engineering and aeronautics. TO has been used, for example, to improve the layout design for airframe structures, such as stiffener ribs or brackets for aircraft.
Beyond enabling structural lightweighting, topology optimization can help unlock the potential of advanced manufacturing technologies like additive manufacturing or composite materials that are increasingly popular in the sector.
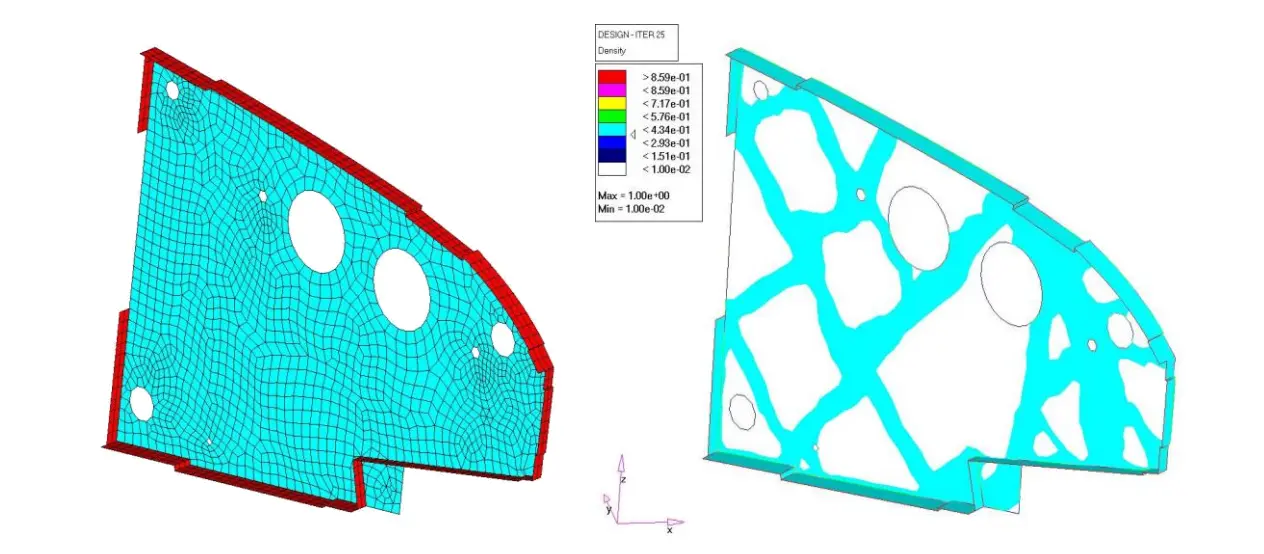
Topology optimization of an Airbus A380’s edge rib component. (source)
Automotive
In the automotive industry, topology optimization balances the desirability of lightweight parts for fuel efficiency and power with the stability and strength of a body that can withstand torque and impact.
Besides mass savings, topology optimization can also improve passenger safety by defining the way a structure collapses during an accident.
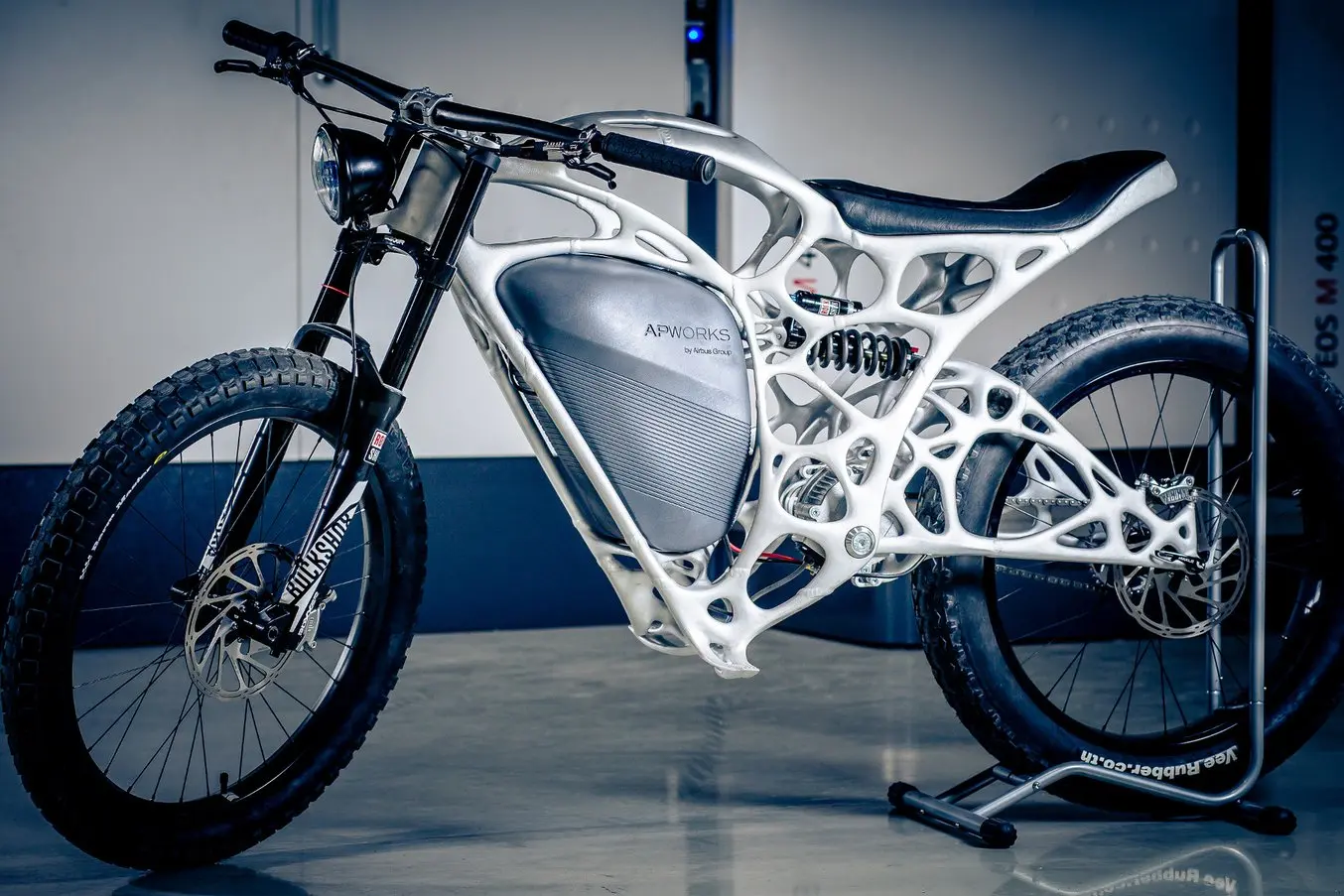
A lightweight topology optimized motorcycle frame manufactured using metal 3D printing. (source)
Medical
Additive manufacturing is ideal for creating medical implants, as it empowers medical professionals to create free-form shapes and surfaces, and porous structures. Thanks to topology optimization, the designs can feature lattice structures that are more lightweight, provide improved osseointegration, and last longer than other implants.
TO tools can also optimize the designs of biodegradable scaffolds for tissue engineering, porous implants, and lightweight orthopedics. Nanotechnology applications—such as cell manipulation, surgery, micro fluids, and optical systems—also use topology optimization.
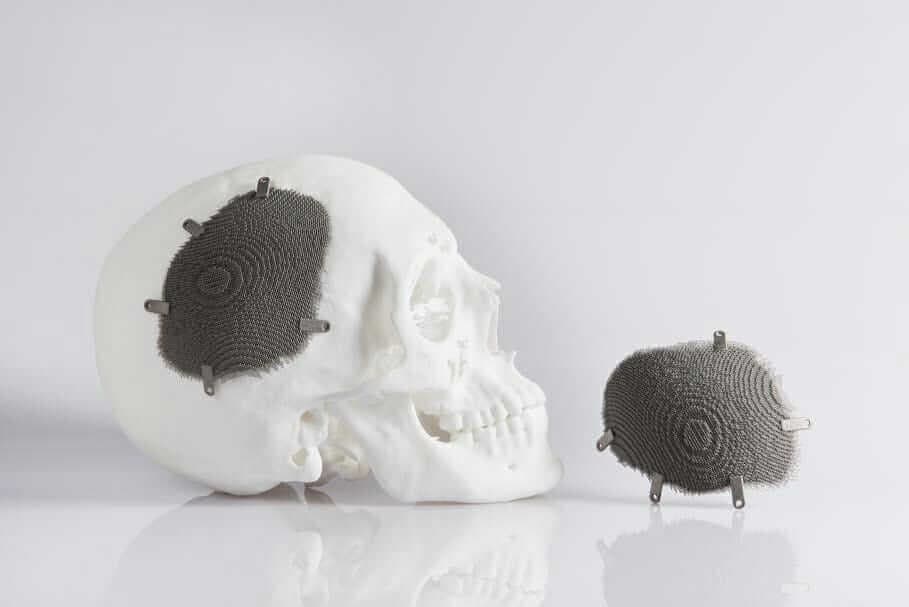
Skull implant, produced with metal additive manufacturing. Source: Autodesk
Topology Optimization Software
Designers are increasingly recognizing the versatility, speed, and robust capabilities of harnessing topology optimization. Software companies are responding by providing the necessary toolkits, either within their preexisting offerings or through new software solutions.
The following are some examples of topology optimization software:
-
nTopology offers a “unique toolset of generative design and automation capabilities,” speeding the design process by combining advanced geometry, simulations, and experimental data. Its geometry engine applies across a variety of applications, from aerospace and automotive to the design of football helmets to patient-specific devices in the medical field.
-
SOLIDWORKS Simulation Solutions feature topology optimization among their structural analysis tools and offer multiple methods to take these optimized designs back into a CAD environment.
-
Autodesk’s Fusion 360 cloud-based CAD platform offers shape optimization and advanced features to support design verification for manufacturing on both traditional and digital fabrication tools like 3D printing.
-
Creo 7.0 generative design software includes the Generative Topology Optimization extension, enabling users to account for product constraints and requirements and “rapidly explore innovative design options to reduce development time and expense.”
-
Altaire OptiStruct integrates structural optimization and analysis. Specializing in lightweight and structural efficiency, it features a proprietary method of topology optimization in designing lattice structures. Its integrated multiphysics environment—including heat transfer, vibrations and acoustics, rotor dynamics, and stiffness and stability—aids design in areas like consumer electronics, aero modelling, and medical technologies.
-
Tosca Structure works within FEA software and boasts realistic simulation models with the ability to change geometry quickly and reliably. Its morph capability allows shape optimization at the existing finite element mash, bypassing intermediate steps, and is especially important for designers of mechanical structures.
A Bright Future for Innovation
Engineers are increasingly using innovative methods of designing prototypes, machine parts, and consumer goods.
Algorithmic design and 3D printing technology go hand in hand, and it no longer comes at an exorbitant cost to manufacturers. Explore the Formlabs suite of resin 3D printers and take your designs to new levels.
Cover image source: nTopology