Runde Sache beim Fahrraddesign: 3D-Druck revolutioniert den Innovationsprozess bei The Rider Firm
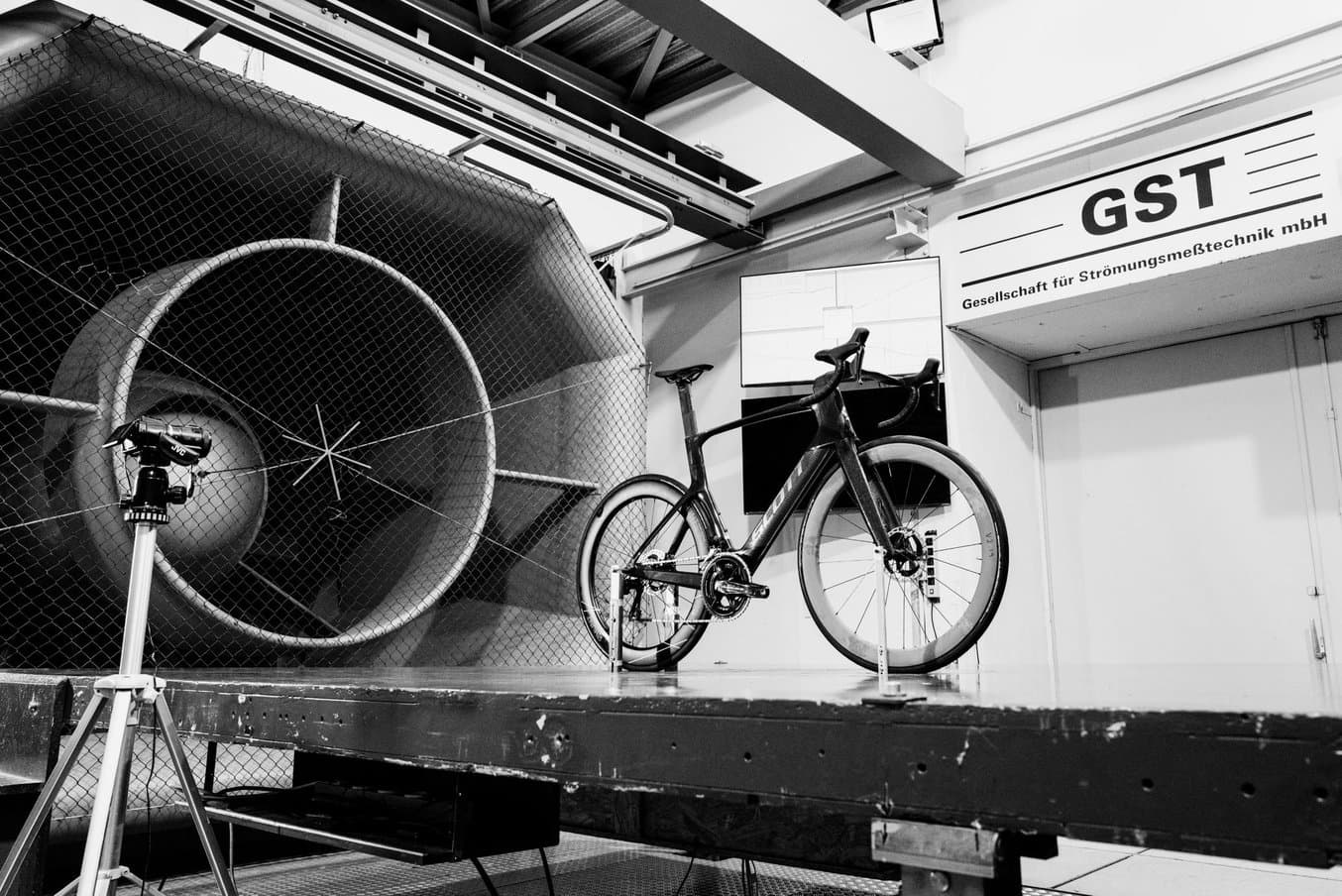
Hunt Bike Wheels testet Felgenprofile im Windkanal Friedrichshafen im Süden Deutschlands.
Da sich die Welt für Arbeitswege, Naturerkundung, Fitness oder Rennen zunehmend dem Rad widmet, müssen Fahrradhersteller unbedingt mit den ständig fortschreitenden Trends und technologischen Entwicklungen Schritt halten. The Rider Firm ist das Unternehmen hinter einer der weltweit führenden Marken für direkt an Verbraucher vertriebene Fahrradfelgen, Hunt Bike Wheels, sowie anderen innovativen Leistungsausrüstungen, Komponenten und Fahrradmarken wie Privateer Bikes, Cairn Cycles und Dissent 133.
Ziel ist es, Hochleistungsfahrräder und -komponenten herzustellen, die nicht nur für Wohlhabende erschwinglich sind. Daher muss der Entwicklungsprozess intelligenter und effizienter sein als der traditioneller Fahrradmarken mit größeren Budgets. Die Anschaffung eines betriebsinternen großformatigen SLA-3D-Druckers vom Typ Form 3L war das neueste Unterfangen des Unternehmens, um Innovationen voranzutreiben und die Arbeitsabläufe neu zu gestalten.
Obgleich das Hauptfertigungszentrum der Fahrradindustrie in Taiwan liegt, findet der Produktentwicklungsprozess bei The Rider Firm zu Hause im Vereinigten Königreich statt. Dort verlassen sich die Teams stark auf den Form 3L, hauptsächlich für die Prototypenentwicklung. Dan Hicks, Development Engineer bei Privateer Bikes, und Patrick Brown, Design Engineer bei Hunt Bike Wheels, haben uns einige Einblicke in ihren Arbeitsprozess gegeben und gezeigt, wie die Ingenieurteams mit dem Form 3L ständig innovieren und neue Produkte auf den Markt bringen.
Hunt Bike Wheels: 3D-Druck funktionsfähiger Prototypen in Originalgröße für Windkanaltests
Der Name Hunt Bike Wheels leitet sich von der Mission des Unternehmens ab, beharrlich allen kleinen Details nachzujagen, die das Produkt verbessern. Das erfahrene Ingenieurteam arbeitet unermüdlich an der Entwicklung von Laufradsätzen, die auf verschiedenen Terrains außergewöhnliche Leistung bieten. Durch umfangreiche Forschung und Entwicklung optimiert das Team die Aerodynamik der Räder, um Geschwindigkeit, Stabilität und Effizienz voranzutreiben. Im Profi-Radsport zählt jede marginale Verbesserung: Der aerodynamische Widerstandsunterschied zwischen Laufradsätzen ist minimal – bei 45 km/h im Bereich von 2 % bis 5 % –, aber dieser Unterschied kann die Sekunden ausmachen, die den ersten und den zehnten Platz trennen.
Patrick Brown erklärte uns den Entwicklungsprozess der Räder. Dieser beginnt damit, dass die Ingenieure verschiedene Felgenprofile entwerfen und sie mithilfe numerischer Strömungsmechanik (CFD, von engl. Computational Fluid Dynamics) testen, die im Wesentlichen einen virtualisierten Windkanal darstellt. Mit der CFD-Analyse identifiziert das Team die besten Felgenprofile, die später mit 3D-gedruckten Prototypen praktisch getestet werden.
Bei ihren jüngsten LIMITLESS-Laufradsätzen testete das Team etwa 45 verschiedene Felgenprofile mithilfe der CFD-Analyse und identifizierte diejenigen mit dem geringsten Luftwiderstand und den besten Eigenschaften für die Seitenwind-Einwirkung. Am Ende hatte man vier Vorderräder und drei Hinterräder, die das Team 3D-druckte und im Windkanal Friedrichshafen im Süden Deutschlands testete.
Dank des großen Fertigungsvolumens des Form 3L druckten die Ingenieur*innen die Fahrradreifen in fünf oder sechs Abschnitten, abhängig von der Anzahl der Speichenlöcher, und platzierten dabei vier dieser Felgensektionen gleichzeitig auf der Konstruktionsplattform. Nach der Nachhärtung und Nachbearbeitung wurden die gedruckten Teile mit Epoxidharz verklebt und zu funktionalen Prototypen zusammengebaut, mit Naben, Speichen und Reifen.
Über die Nutzung von Grey Pro Resin sagt Patrick Brown: „Die 3D-gedruckten Räder sind etwas weich, halten aber etwa 65 % der Spannung eines Kohlenstofffaser-Radsatzes stand. Wir bauen sie also ziemlich gerade und genau, dann sind sie gut genug für den Windkanal.“
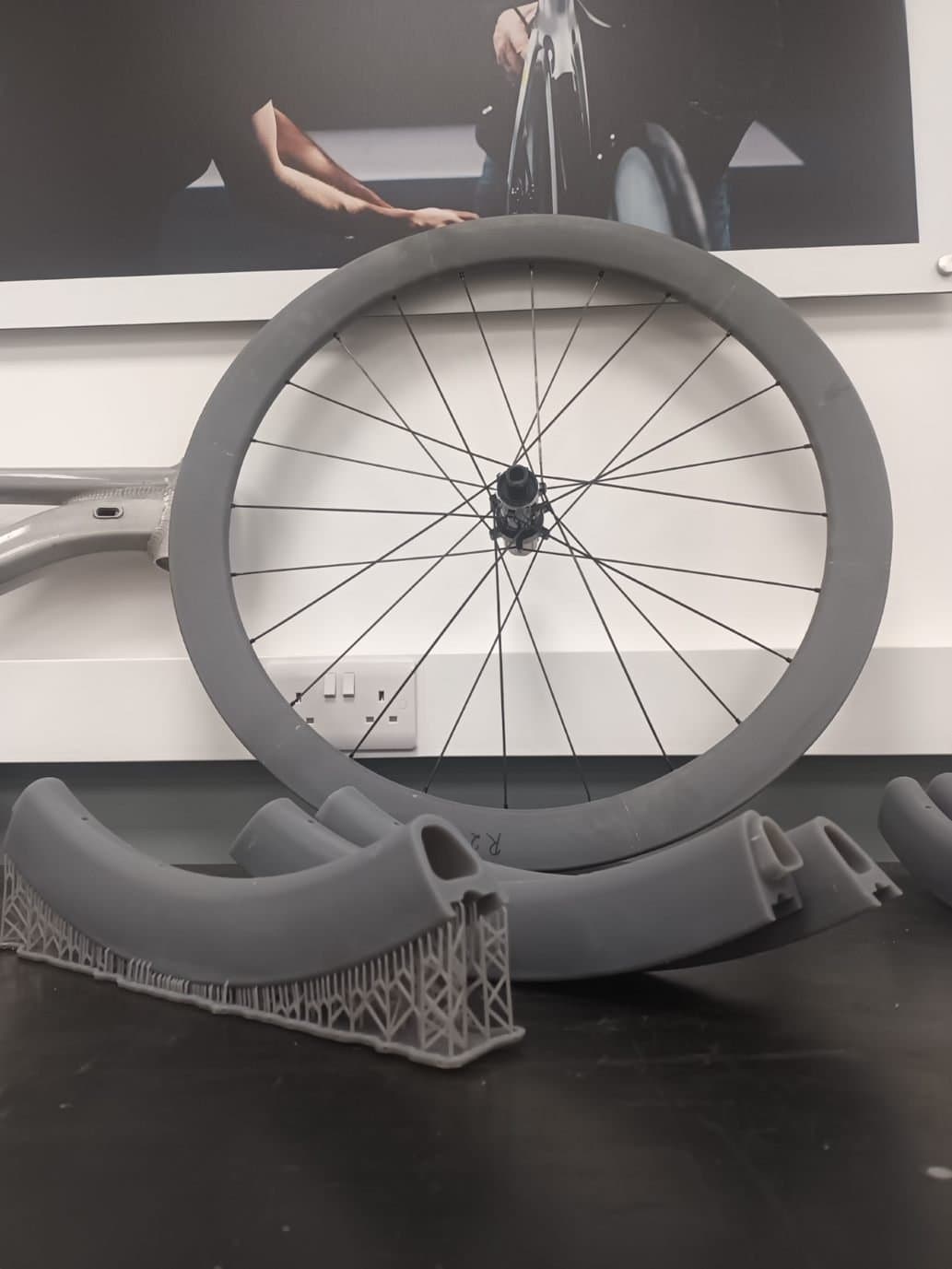
Grey Pro Resin ist ein großartiges Material für Prototypen, da es etwa 65 % der Spannung eines Kohlenstofffaser-Laufrads aushält.
Früher wandte sich Hunt Bike Wheels für den Druck der verschiedenen Radabschnitte an einen Drittanbieter, aber das hatte viele Nachteile. Zuerst musste das Ingenieurteam die fertigen Radprofile zwei bis drei Monate im Voraus senden, was den Prozess verlangsamte und die Flexibilität einschränkte. Brown gab an, dass sie bei ihrem neuesten Projekt mit dem Form 3L „die letzten Drucke direkt vor [ihrer] Abreise erhalten“ hatten. Das bedeutet, dass sie bis zur letzten Minute Änderungen vornehmen konnten. Die outgesourcten Teile waren auch nicht stark genug, um den Reifen auf den erforderlichen Druck aufzupumpen, denn einige der Teile konnten reißen und untauglich für Tests werden.
„Heute kann ich viel länger Simulationen durchlaufen und weiter neue Profile entwickeln. Diese betriebsinterne Flexibilität bringt uns großen Nutzen.“
Patrick Brown, Design Engineer bei Hunt Bike Wheels
„Die Reifen müssen den Druck erreichen, der die richtige Form des Rads gewährleistet. Für uns ist es entscheidend, dass die Drucke nicht nur geometrisch genau sind, sondern auch stark genug, um das richtige aerodynamische Profil zu gewährleisten.“ Grey Pro Resin erfüllte diese wichtigen Anforderungen mit beeindruckender Präzision und hielt die bis zu 3,5 Bar Druck der aufgepumpten Reifen aus. Brown hob auch die ausgezeichnete Oberflächenbeschaffenheit von Grey Pro Resin hervor, ein Schlüsselelement bei der Aerodynamikprüfung.
„[Im Windkanal] laufen sie auf einer Rolle – das Rad dreht sich also mit 45 Kilometern pro Stunde.“
Patrick Brown, Design Engineer bei Hunt Bike Wheels
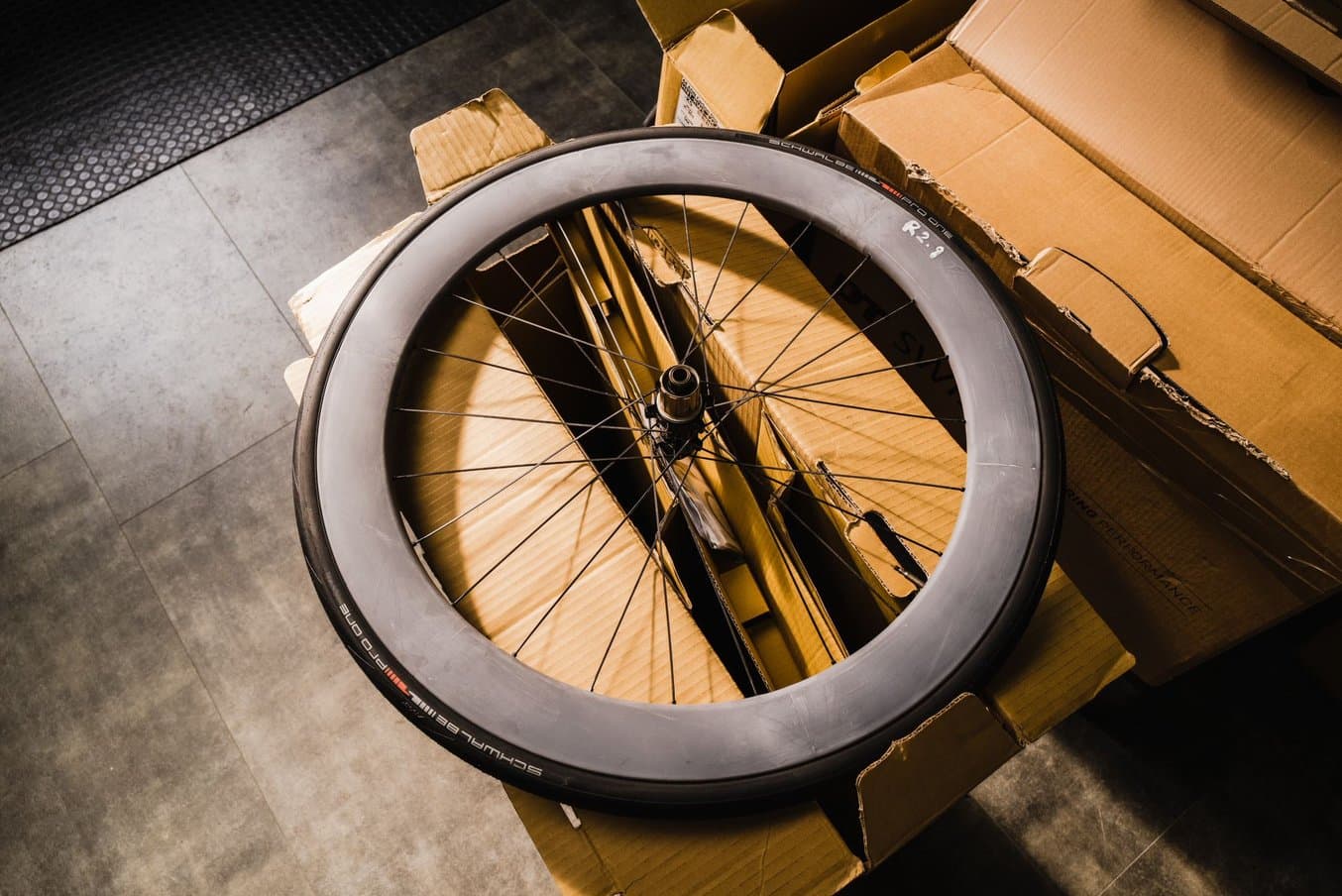
Die ausgezeichnete Oberflächenbeschaffenheit von Grey Pro Resin war entscheidend für die aerodynamischen Tests.
Zudem ermöglicht der betriebsinterne 3D-Druck dem Ingenieurteam noch umfangreichere Iterationen und senkt gleichzeitig die Kosten. In der Zeit des Outsourcings investierte Hunt Bike Wheels etwa 2000 £ in einen einzigen Felgenprototyp. Dank des Form 3L wurden diese Kosten um 90 % auf rund 200 £ gesenkt.
„Das bedeutet, wenn wir zum Windkanal gehen, können wir eine viel größere Anzahl an Rädern mitnehmen, um breitere CFD-Studien zu validieren. Dadurch können wir drei oder vier Produktiterationszyklen überspringen, um ein erstklassiges Produkt zu erhalten. Jedes Mal, wenn wir ein Produkt herausbringen, wissen wir, dass es von Anfang an in einem sehr guten Zustand ist“, sagt Hicks.
Der Form 3L repräsentiert jetzt einen wesentlichen Teil des Geschäftsmodells, da The Rider Firm mit ihm der Konkurrenz immer einen Schritt voraus ist. Tatsächlich sagt Hicks: „Durch kluges Prototyping und schlanke Geschäftsprozesse bieten wir Ihnen ein Rad, das die gleiche aerodynamische Leistung wie bei größeren Unternehmen hat – und das zum halben Preis.“
Privateer Bikes: Mit vollständigen Fahrradrahmen und Rapid Prototyping die Grenzen austesten
Bei Privateer Bikes nutzt das Entwicklungsteam den Form 3L für eine Reihe von Prototyping-Anwendungen, einschließlich kompletter Fahrradrahmen sowie Rahmenschützern.
Bei der Entwicklung einer neuen Fahrradreihe hat das Ingenieurteam von Privateer Bikes vollständige Fahrradrahmen und einige der komplexeren Abschnitte des Rahmens in verschiedenen Größen gedruckt. Dadurch konnte es Komponenten darauf montieren, beispielsweise Lager und Federgabeln in den Rahmen pressen, um die Produktionsfähigkeit zu gewährleisten und die Abstände für verschiedene Rahmengrößen zu prüfen. „Wir können Freiräume prüfen, wie es sich zusammensetzt, ob Komponenten passen oder ob etwas anschlägt, wenn sich die Federungen bewegen.“
Darüber hinaus hat der Druck des gesamten Rahmens dem hauseigenen Grafikdesigner ermöglicht, ihn anzusprühen, um Konzepte mit der Grafik auszuprobieren und Decals für die neuen Fahrräder zu entwerfen. Die Rahmen wurden aus Grey Pro Resin in mehreren kleineren Drucken hergestellt, die später zusammengebaut und verklebt wurden. Sobald das Fahrrad vollständig montiert ist und die Teile verklebt sind, kann es erheblichen Belastungen standhalten, „was ein grobes Handling ermöglicht“.
„Ein 3D-Druck ist praktisch, um damit zu experimentieren“, so Hicks. Er fügt an, dass es „für die Marketingteams von Vorteil ist, etwas Greifbares zu haben. Wenn wir über ein Design sprechen, können wir es viel besser vermitteln, indem wir das Modell den Leuten zeigen.“
Hicks fand den Form 3L besonders nützlich bei der Prototypenentwicklung maßgeschneiderter Rahmenschützer für seine Fahrräder. Bei einem Mountainbike stößt die Kette oft gegen die Kettenstrebe, was ziemlich laut werden kann und den Rahmen beschädigen könnte. Deshalb hat das Team diese passenden Rahmenschützer aus Gummi entwickelt, die an der Kettenstrebe befestigt sind.
Normalerweise hätte das Team keine Möglichkeit gehabt, Prototypen solcher Teile herzustellen. Stattdessen hätte man das Design an den taiwanesischen Zulieferer gesendet, der die Produktionswerkzeuge herstellt und ihnen eine Probe des endgültigen Teils schickt. Dieser gesamte Prozess dauert normalerweise drei bis vier Monate und kostet etwa 3000 bis 4000 $. Es wäre schwierig gewesen, das Teil anzupassen und zu optimieren, da jede Designänderung neue Werkzeuge erfordert hätte, was wieder Kosten nach sich zieht.
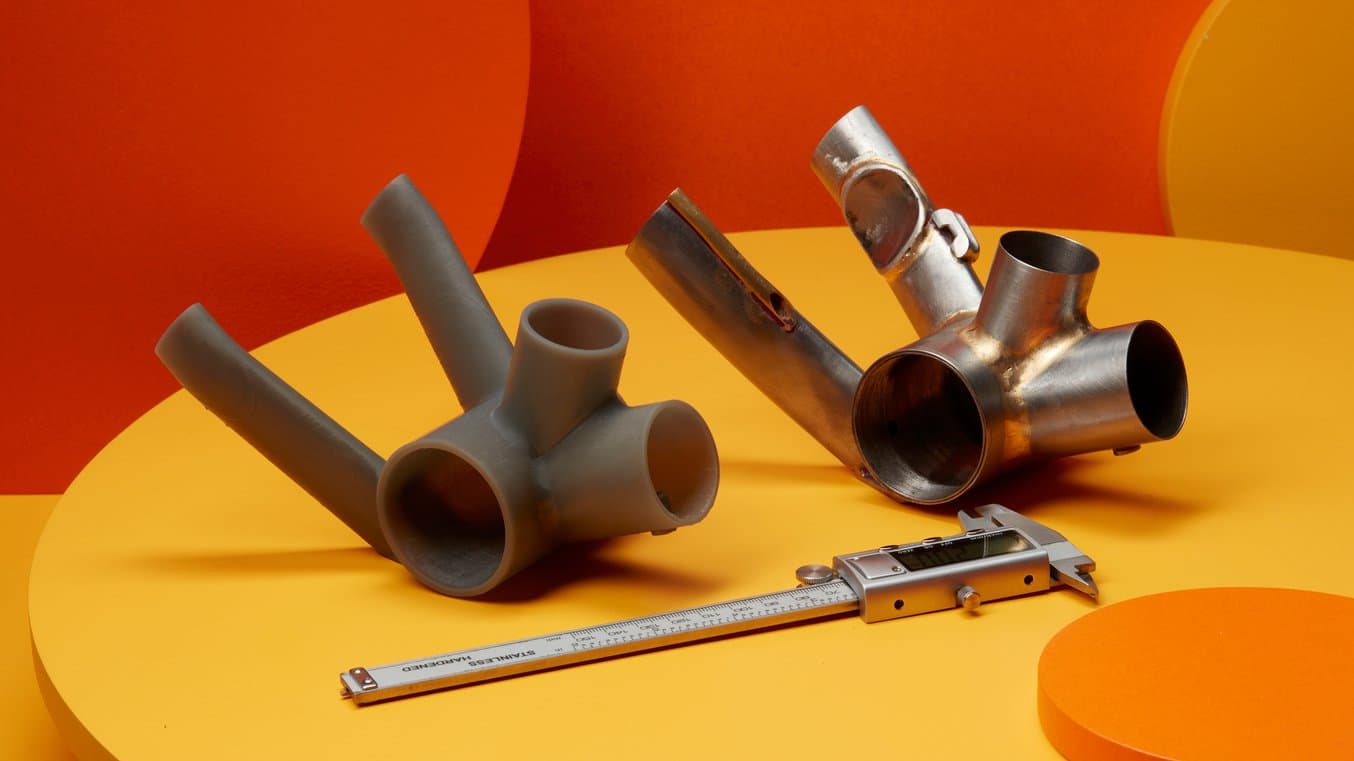
Rapid Prototyping: Die Wahl des richtigen Verfahrens und Materials
Erfahren Sie in diesem Webinar, wie Sie Konzeptnachweise und funktionale Prototypen schneller denn je erstellen und Ihre Designs in kürzester Zeit anhand von Praxistests überarbeiten.
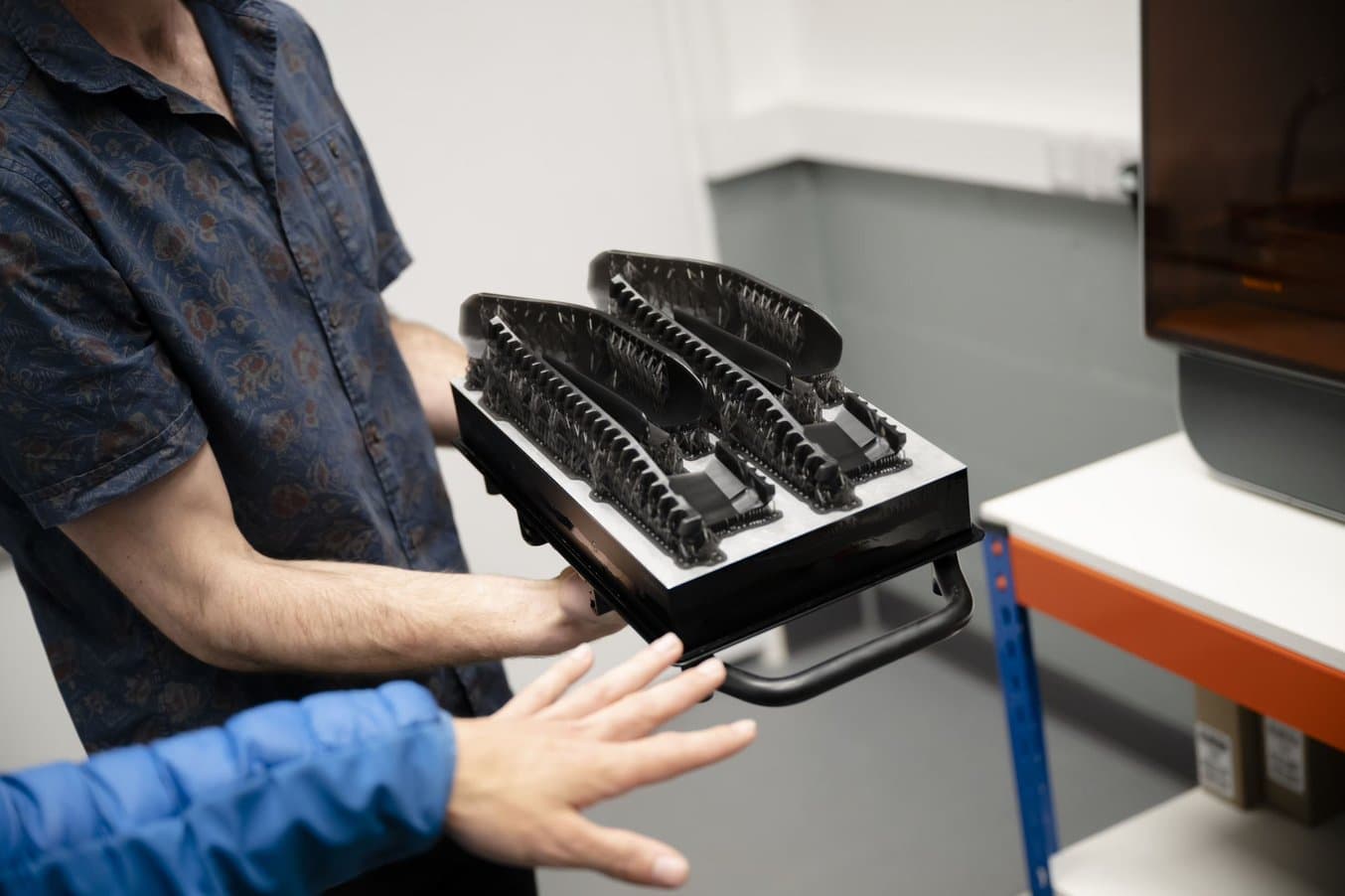
Der Form 3L erwies sich als großartiges Werkzeug zur Herstellung der Prototypen der Rahmenschützer aus Flexible 80A Resin.
Durch den 3D-Druck validieren die Ingenieure bei Privateer Bikes drei oder vier Designs schnell und einfach. „Es kostet uns nichts, das Design zu ändern. Das bedeutet, dass wir eine Produktionsdatei an den Hersteller senden und sofort mit der Produktion beginnen können“, berichtet Hicks. Er fügt hinzu, dass dies ihnen wahrscheinlich etwa sechs Monate im Projekt gespart hat sowie ungefähr 4000 oder 5000 $ an Produktionswerkzeugkosten.
„Wenn wir eine Produktionsdatei an den Hersteller senden, können wir sofort mit der Produktion beginnen.“
Dan Hicks, Development Engineer bei Privateer Bikes
Für diese spezielle Anwendung wählte das Team als Material Flexible 80A Resin, das „über den richtigen Härtegrad verfügt“ und somit ideal für funktionale Prototypen ist, die direkt an Fahrrädern getestet werden. Das Team hat diese Schützer mehrere Monate an den Fahrrädern getestet und überprüft, wo die Kette noch anschlägt und wo es noch Geräusche gibt. Basierend auf diesen Ergebnissen wurden dann Verbesserungen vorgenommen.
„Wir können viele Aspekte des DFM implementieren, da es viel einfacher ist, über Trennlinien im Werkzeug und deren Funktionsweise nachzudenken, wenn man das Ganze vor sich hat.“
Dan Hicks, Development Engineer bei Privateer Bikes
Mit 3D-Druck reaktionsschnell auf sich ändernde Trends eingehen
„Jeder fährt Fahrrad anders. Wir wissen nicht, was die Leute in zwei Jahren machen. Aber wir sind jetzt in einer sehr guten Position, um schnell auf sich ändernde Trends zu reagieren, um neue Dinge aufzugreifen.“
Dan Hicks, Development Engineer bei Privateer Bikes
In absehbarer Zukunft plant The Rider Firm, mehr E-Bikes und deren Komponenten zu entwickeln. Diese Fahrräder umfassen komplexere Designs. Wie Hicks betonte: „Je mehr Komponenten man unterbringen muss, desto schwieriger ist es.“ Doch der 3D-Druck wird ihnen die Prototypenentwicklung all dieser Setups erlauben.
„Jeder fährt Fahrrad anders.“ Deshalb ist das Team von The Rider Firm schon gespannt, was sich die Leute als Nächstes einfallen lassen. Dank des Form 3L ist das Unternehmen nun gerüstet, um schnell auf sich ändernde Trends zu reagieren, während es weiterhin Innovationen vorantreibt.