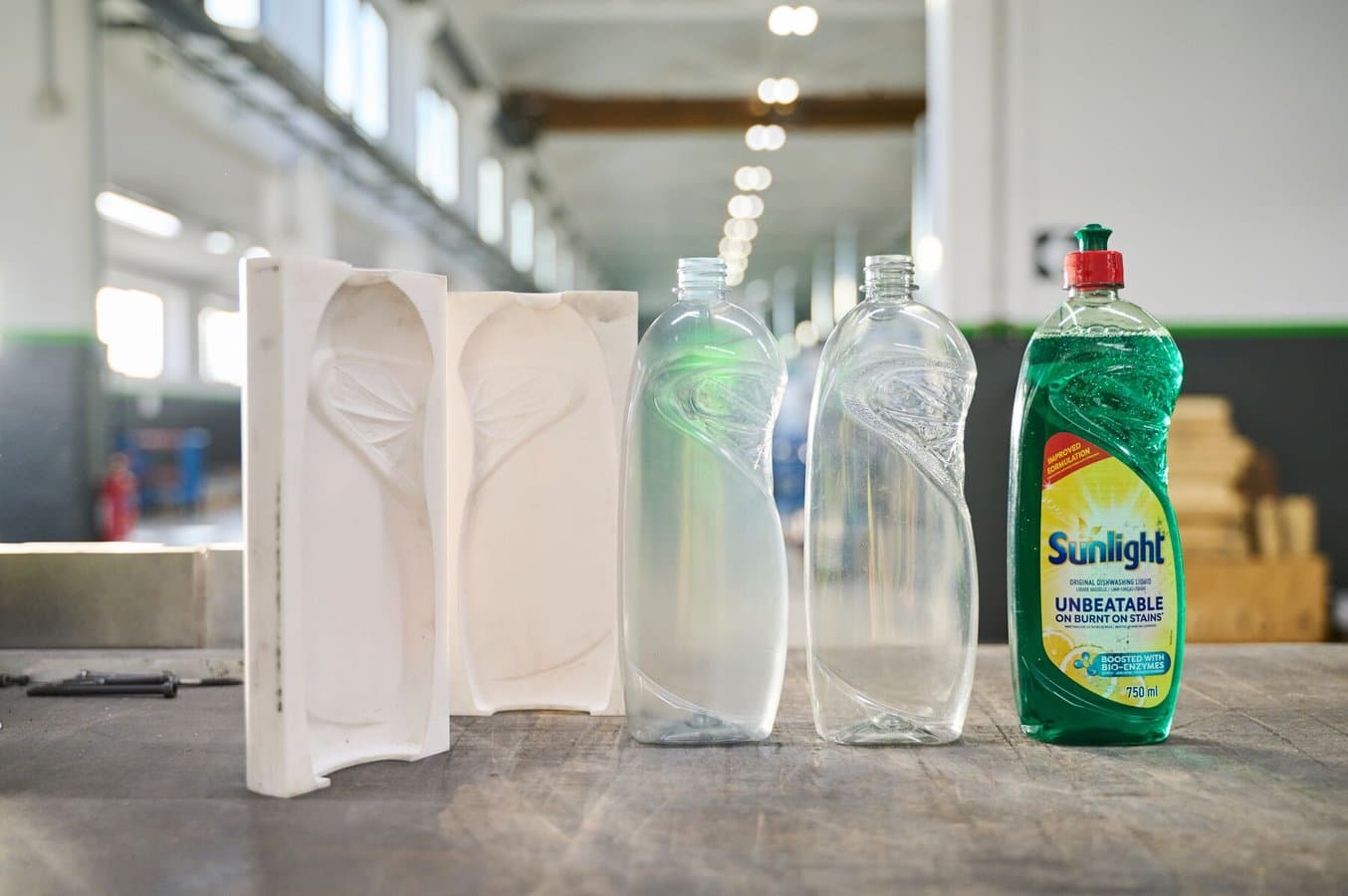
Als moderner Fertigungsprozess zur großangelegten Produktion von Kunststoff-Hohlkörpern existiert das Blasformverfahren bereits seit 1938, als die amerikanischen Erfinder Enoch Ferngren und William Kopitke ein Patent für eine „Vorrichtung zum Formen von Hohlkörpern aus organischem Kunststoff“ anmeldeten. Das Grundprinzip des Blasformens ist jedoch mindestens seit dem 1. Jahrhundert v. Chr. bekannt, als das Glasblasen im alten Syrien entwickelt wurde. Heute tragen 3D-Druck und andere fortschrittliche Fertigungstechnologien dazu bei, das Blasformen von Kunststoffteilen effizienter, effektiver und damit für eine Vielzahl von Herstellern zugänglich zu machen.
Bei den drei Hauptarten des Blasformens – Extrusionsblasformen (EBM), Spritzblasformen (IBM) und Spritzstreckblasformen (ISBM) – wird ein erhitzter Kunststoffvorformling aufgeblasen, sodass er die Konturen der ihn umschließenden Form annimmt. Während mit Extrusionsblasformen in der Regel die niedrigsten Stückkosten erzielt werden, sind das Spritzblas- und Streckblasverfahren in der Lage, komplexere Produkte mit einer Funktionalität herzustellen, die mit Extrusionsblasformen gefertigte Teile nicht erreichen. Insbesondere das Spritzstreckblasen wird häufig zur Herstellung von Produkten eingesetzt, die ein hohes Maß an Festigkeit und Transparenz erfordern.
Dieser Artikel bietet eine detaillierte Übersicht über die verschiedenen Arten von Blasformverfahren für Kunststoffe, die gängigsten Polymere, die zum Blasformen verwendet werden, und das Wichtigste zum Einstieg in diesen Fertigungsprozess.
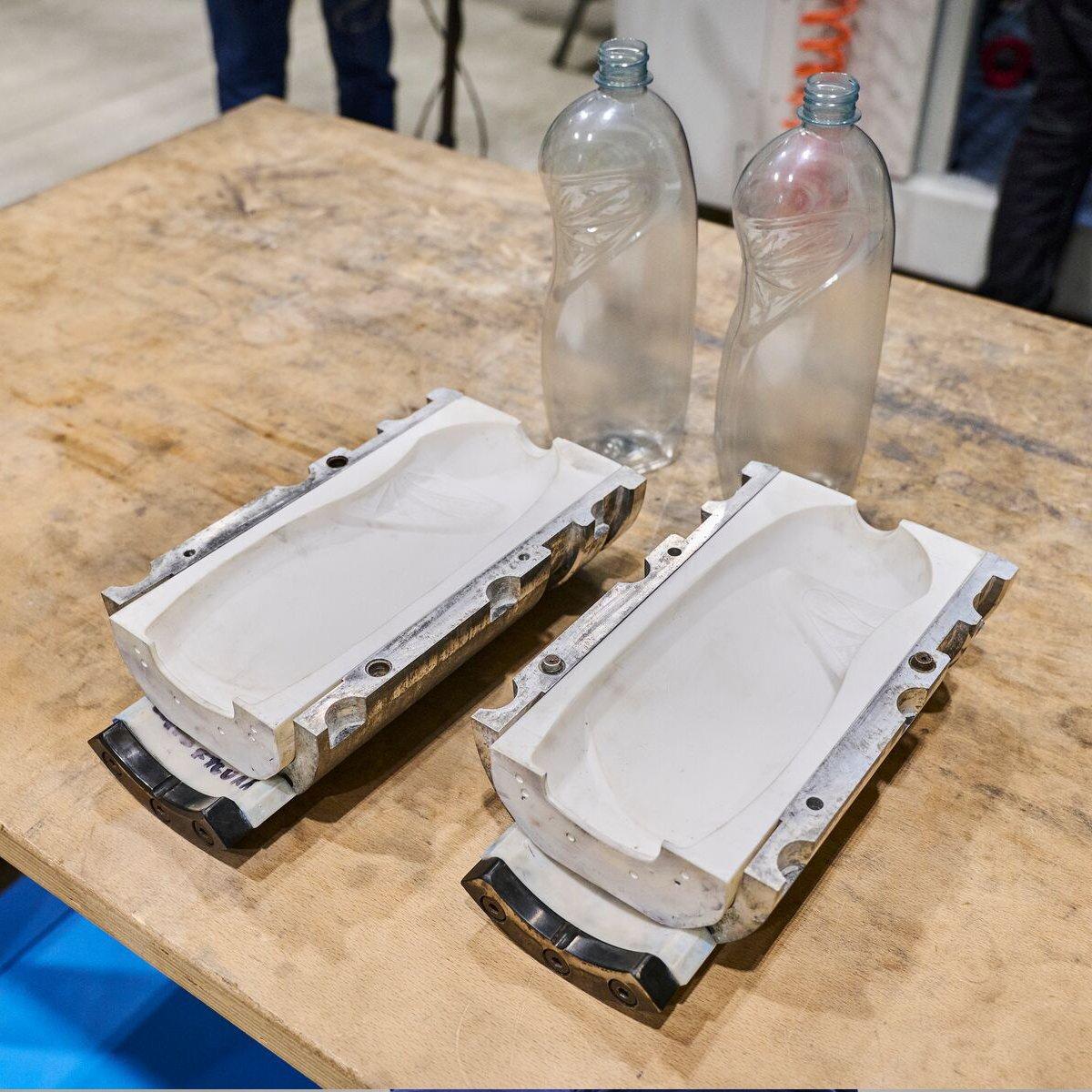
Schnelles Streckblasen von Kleinserien mit Formen aus dem 3D-Drucker
Dieses Whitepaper beschreibt Methoden und Richtlinien für die Herstellung SLA-3D-gedruckter Formen und deren Einsatz im Streckblasverfahren zur Reduzierung der Kosten und Durchlaufzeit in der Vorproduktion. Angefangen von den wichtigen Faktoren beim Design und beim Arbeitsablauf bis hin zu den Prozessbedingungen stellen wir eine Machbarkeitsstudie der Branchenexperten Unilever und Serioplast vor.
Was ist Blasformen?
Blasformen ist ein industrielles Fertigungsverfahren zur Herstellung hohler Kunststoffteile. Zahlreiche Branchen setzen Blasformverfahren für Kunststoffe ein, darunter die Automobilindustrie, unter anderem für Tanks, Ansaugvorrichtungen und Leitungen, und die Agrarindustrie für Schüttgutbehälter, Bewässerungsteile und Flüssigkeitsbehälter. Am bekanntesten ist das Blasformen jedoch in der Verpackungsindustrie, wo das Verfahren zur Herstellung von Kunststoffflaschen und anderen Behältnissen für alle erdenklichen Produkte verwendet wird – von Wasser über Kosmetikprodukte bis hin zu Reinigungsmitteln.
Das Kunststoffblasformen ist eine zuverlässige und kostengünstige Methode zur Herstellung von Kunststoffteilen im großen Maßstab. Wie bei vielen anderen Fertigungsverfahren können die Anlaufkosten hoch sein. Daher ist das Blasformen oft erst dann wirtschaftlich sinnvoll, wenn ein Hersteller Tausende Exemplare von ein und demselben Teil benötigt. Während einige Methoden eine höhere Komplexität ermöglichen als andere, ist das Blasformen wahrscheinlich am effektivsten bei der Fertigung hohler, dünnwandiger Teile.
Im Vergleich zum Spritzgießen hat das Blasformen in der Regel niedrigere Werkzeugkosten. Ebenso können viele verschiedene Materialien blasgeformt werden, was es zu einem geeigneten Verfahren für eine Vielzahl von Anwendungen macht.
Für die Kleinserienfertigung und das iterative Produktdesign eignen sich daher in der Regel Geräte mit geringeren Anschaffungskosten und mehr Designflexibilität, wie z. B. 3D-Drucker. Einige Branchenführer setzen jedoch bereits beide Technologien in ihren Fertigungsprozessen ein, indem sie Blasformwerkzeuge mit Stereolithographie-3D-Druckern herstellen, um so die Kosten für den Werkzeugbau zu senken und die Qualität des Endprodukts verbessern.
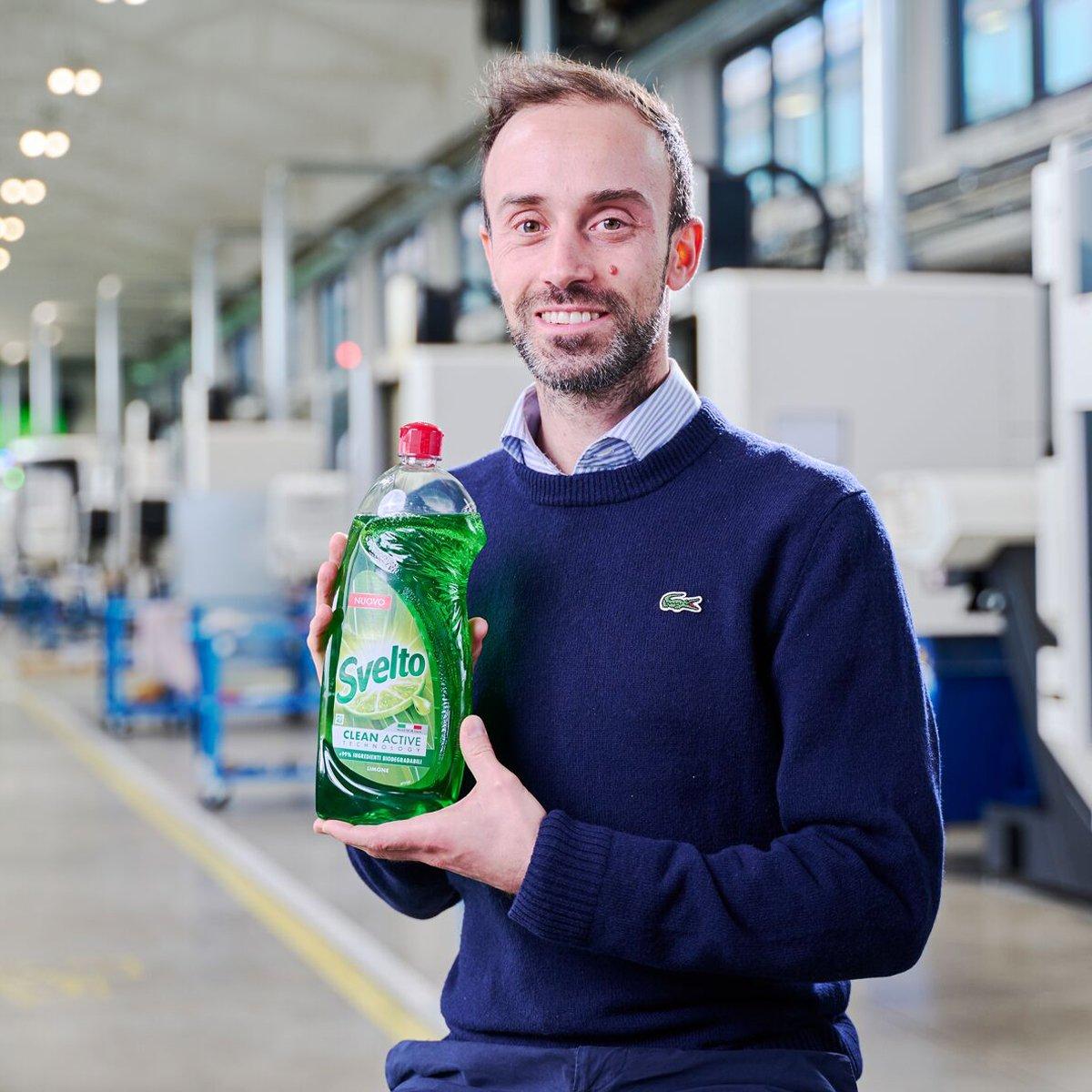
Senken Sie Kosten und Zeitaufwand für Pilottests von blasgeformten Verpackungen
In diesem Webinar stellt Ihnen Blasformexperte Flavio Migliarelli den Arbeitsablauf Schritt für Schritt vor und erläutert die zentralen Vorteile und Anwendungsbereiche 3D-gedruckter Formen für das Streckblasen.
Wie funktioniert das Blasformen?
Beim Blasformverfahren wird Druckluft durch eine Düse in einen erhitzten Kunststoffvorformling gepresst, der sich ausdehnt und an die Konturen eines Formwerkzeugs anpasst. Dadurch wird eine dünne Kunststoffwand in der Geometrie des Formwerkzeugs geformt, sodass ein Hohlraum entsteht. Anschließend wird der Kunststoff abgekühlt, bis er seine Form auch ohne das Formwerkzeug beibehält. Dieses wird schließlich entfernt, überschüssiger Kunststoff abgeschnitten und das Kunststoffteil vor dem Versand auf Qualität geprüft.
1. Aufheizen des Vorformlings
Die Herstellung des Vorformling funktioniert bei den drei wichtigsten Blasformverfahren, EBM, IBM und ISBM, jeweils unterschiedlich. In diesem Artikel werden diese Unterschiede im Abschnitt „Arten von Blasformverfahren“ ausführlich beschrieben.
Sobald der Vorformling hergestellt ist, muss er auf eine bestimmte Temperatur erhitzt werden, bei der er seine Integrität während der Befüllung mit Druckluft beibehält. Je nach Verfahren und Kunststoffart kann der Vorformling bereits auf eine Temperatur erhitzt werden, die für die Ausdehnung in das Formwerkzeug ausreicht. In anderen Fällen werden Werkzeuge wie Heizbänder und Heizringe verwendet, um den Vorformling in den thermoelastischen Temperaturbereich zu bringen.
Die richtige Temperatur hängt vom Material, der Methodik und dem gewünschten Endprodukt ab. Polyethylenterephthalat (PET), ein Material, das häufig zur Herstellung von Getränkebehältern verwendet wird, wird in der Regel auf etwa 100 °C erhitzt. Um eine konsistente Wandstärke zu erreichen und das Endprodukt nicht zu beschädigen, ist eine gleichmäßige Erhitzung des Vorformlings essenziell.
2. Umformung
Sobald der Vorformling verformbar ist, wird Druckluft durch eine Düse zugeführt. Wie ein Ballon dehnt sich der Vorformling aus, bis die dünnen Kunststoffwände an die Konturen des Hohlraums angepasst sind. Die Formwerkzeuge verleihen der Flasche verschiedene Formen und Texturen und können Logos und Schriftzüge enthalten. Wie bei anderen Arten der Umformung, z. B. Formpressen und Spritzguss, kann bei Blasformwerkzeugen überschüssiger Kunststoff aus der Form entweichen, um einen Druckaufbau zu vermeiden und gleichmäßige Ergebnisse zu gewährleisten.
Die Druckluft muss gleichmäßig zugeführt werden, damit sich der Vorformling ausdehnen kann, ohne zu reißen oder zu brechen. Komplexere Formen können die Produktionszeit pro Teil erhöhen, was zu einem Kostenanstieg führt.
3. Abkühlung und Verfestigung
Nach der Formung des Hohlkörpers muss dieser abgekühlt werden, bis er sich nicht mehr im thermoelastischen Bereich befindet, damit er nach dem Entformen seine Form beibehält. Daher kann ein effizientes, wirkungsstarkes Kühlsystem einen großen Einfluss auf die Effizienz jedes Blasformverfahrens haben.
Wie beim Erhitzen und Umformen muss auch das Abkühlen und Erstarren gleichmäßig erfolgen, um Schäden zu vermeiden. Eine zu schnelle Abkühlung kann auch zu Verformungen und Unregelmäßigkeiten im fertigen Teil führen. Viele Blasformmaschinen verwenden gekühlte Druckluft und/oder Flüssigkeitskühlkanäle, um die Effizienz des Blasformprozesses zu erhöhen.
4. Entformen und Nachbearbeiten
Wenn die Temperatur unter den thermoelastischen Bereich gesunken ist, kann der Hohlkörper aus der Form entnommen und zur Produktionslinie transportiert werden, wo er entgratet, zugeschnitten, auf Undichtigkeiten geprüft, einer Qualitätskontrolle unterzogen und für den Versand verpackt wird.
In vielen modernen Fertigungsstraßen werden Entformung und Nachbearbeitung, einschließlich Zuschneiden und Dichtigkeitsprüfung, fast vollständig automatisiert, wobei besonders große oder kundenspezifische Designs eine manuelle Nachbearbeitung erfordern können. Die menschliche Aufsicht ist jedoch nach wie vor ein wichtiger Bestandteil der meisten Blasformprozesse, sowohl für die Qualitätskontrolle als auch für die Endverpackung.
Arten von Blasformverfahren
Es gibt drei Hauptarten des Blasformens: Extrusionsblasformen (EBM), Spritzblasformen (IBM) und Spritzstreckblasformen (ISBM). Die Hauptunterschiede zwischen diesen drei Typen liegen in der Art und Weise, wie der Kunststoffvorformling hergestellt wird.
Extrusionsblasformen (EBM)
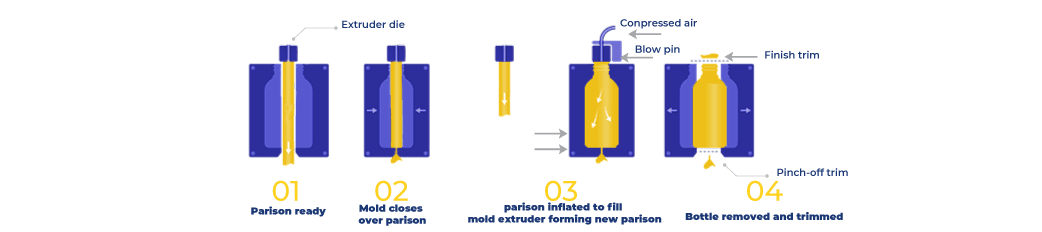
Quelle: GAP Polymere
Das Extrusionsblasformen (Extrusion Blow Molding, EBM) ist die häufigste Art des Blasformens und zugleich auch die einfachste und kostengünstigste. Allerdings ist die strukturelle Komplexität und Detailgenauigkeit von mit EBM hergestellten Produkten meist eingeschränkt.
Beim EBM-Verfahren wird geschmolzener Kunststoff durch einen Extruder gepresst, wodurch ein hohles Rohr entsteht: der Vorformling. Anschließend wird die Form um den Vorformling geschlossen. Der Vorformling wird mit Druckluft aufgeblasen, bis er den Formhohlraum vollständig ausfüllt und sich den inneren Konturen der Form anpasst.
Nachdem der Vorformling vollständig ausgedehnt wurde, folgt der Abkühlungs- und Verfestigungsprozess, häufig mithilfe von Flüssigkeitskühlkanälen oder Druckluft. Da EBM jedoch die simpelste Blasformmethode ist, stützen sich einige EBM-Maschinen schlicht auf eine natürliche Kühlung.
Beim Extrusionsblasformen wird häufig Polyethylen (PE) verwendet, ein beliebter Kunststoff für landwirtschaftliche Tanks, Flaschen für Kfz-Flüssigkeiten (wie Motoröl und Kühlmittel), Shampooflaschen und viele andere gängige Produkte. EBM ist auch die gängigste Methode zum Blasformen von Nylon.
Neben der begrenzten strukturellen Komplexität und Detailgenauigkeit kann es auch schwierig sein, die für das Produkt erforderliche Wandstärke zu erreichen. In solchen Fällen sind Hersteller gezwungen, auf IBM oder ISBM auszuweichen. Für viele Anwendungen, wie z. B. einfache Behälter und Flaschen, ist das Extrusionsblasformen jedoch ausreichend.
Obwohl EBM nur ein kleines bis mittleres Aufblasverhältnis zulässt, können fertige EBM-Teil recht groß sein, was es zur bevorzugten Methode für die Herstellung von Produkten wie Industriefässern, Koffern und Kraftstofftanks macht.
Spritzblasformen (IBM)
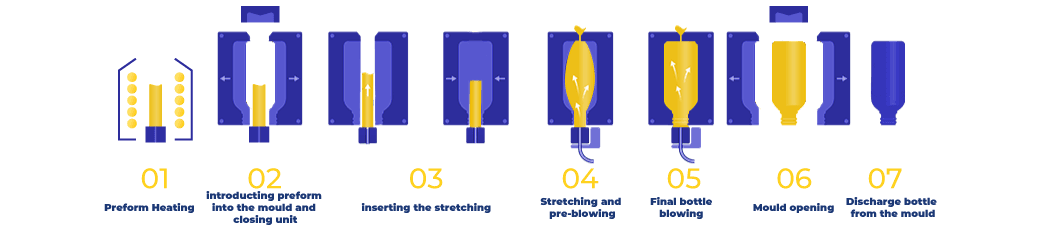
Quelle: GAP Polymere
Beim Spritzblasformen (Injection Blow Molding, IBM) werden Spritzgießen und Blasformen kombiniert. Zunächst wird durch Einspritzen von geschmolzenem Kunststoff in eine Form der Vorformling hergestellt. Dieser wird anschließend abgekühlt, um einen einsetzbaren Vorformling zu erhalten. Dann wird der Vorformling in den Hohlraum des Blasformwerkzeugs überführt, erneut erhitzt und mit Druckluft gefüllt, bis er sich ausdehnt und den Hohlraum der Form ausfüllt. Ab diesem Punkt ist der Prozess dem EBM sehr ähnlich: Der geformte Kunststoff wird abgekühlt, aus der Form entnommen, zugeschnitten und versandt.
Für das Blasformen muss der Vorformling nicht immer auf die gleiche Temperatur erhitzt werden wie beim vorangegangen Spritzgießen. Dies macht das Spritzblasformen oft zur bevorzugten Option für Hersteller, die mit Materialien mit langer Trocknungszeit arbeiten, wie z. B. PET – dem Material, das am häufigsten in Softdrink- und Wasserflaschen verwendet wird.
IBM eignet sich für komplexe Formen oder für Produkte mit engeren Toleranzen besser als EBM (z. B. Medizinflaschen, die eine strenge Halstoleranz haben). Hersteller in der Kosmetik- und Pharmaindustrie stützen sich aufgrund der höheren Präzision also mit hoher Wahrscheinlichkeit auf das Spritzblasverfahren. Aufgrund des mehrstufigen Prozesses und der zusätzlichen Designkomplexität können die Werkzeuge jedoch sehr viel teurer sein, und die Gesamtzeit pro Teil übersteigt in der Regel die des EBM.
Spritzstreckblasformen (ISBM)

Quelle: GAP Polymere
Wie IBM kann auch das Spritzstreckblasverfahren (Injection Strech Blow Molding, ISBM) komplexere Teile und eine höhere Maßgenauigkeit erreichen als EBM. Insbesondere bei der Verwendung von PET-Kunststoff können mit ISBM oft noch detailliertere und feinere Designmerkmale erzielt werden als mit IBM. Ein zusätzlicher Bonus ist, dass einige ISBM-Fertigungsverfahren Kunststoffüberschuss reduzieren oder eliminieren, was zu weniger Abfall und einem glatteren Endprodukt führt.
ISBM ist IBM insofern sehr ähnlich, als es sich um ein zweistufiges Verfahren handelt, bei dem zunächst durch Spritzguss ein Vorformling hergestellt wird. Sobald der Vorformling jedoch in das Formwerkzeug eingelegt und erhitzt wird, wird ein vertikaler Stab ausgefahren, um den Vorformling zu strecken, bevor Druckluft eingeblasen wird. Durch diesen entscheidenden zusätzlichen Schritt ist ISBM in der Lage, ovoide, quadratische und polygonale Formen zu erzeugen, die mit anderen Methoden schwer umsetzbar sind.
Somit erfordert ISBM im Vergleich zu IBM einen zusätzlichen Schritt – das Strecken –, was zu etwas längeren Verarbeitungszeiten führt und im Durchschnitt die höchsten Werkzeugkosten der drei zentralen Blasformverfahren verursacht.
Materialien für das Blasformen
Material | Eigenschaften | Kosten | Biegemodul (Schätzung)* | Wärmeformbeständigkeitstemperatur (HDT) (Schätzung)* | Anwendungen |
---|---|---|---|---|---|
Ultrahochmolekulares Polyethylen (HDPE) | Transluzent, mittlere Härte, leicht färbbar | $ | 1170 MPa | 71 °C | Landwirtschaftliche Tanks, Industriefässer, Koffer, Flaschen für Kfz-Flüssigkeiten, Shampooflaschen |
Polyethylen niedriger Dichte (LDPE) | Transluzent, weich bis mäßige Härte, leicht färbbar | $$ | 275 MPa | 60 °C | Spritzflaschen, Bootsfender, Blasfolien für Plastiktüten |
Polyethylenterephthalat (PET) | Transparent, ziemlich hart, leicht färbbar, starke Feuchtigkeitssperre | $$ | 3400 MPa | 79 °C | Softdrink- und Wasserflaschen, Plastikdosen |
Polypropylen (PP) | Transluzent (einige Mischungen können fast transparent sein), mäßige bis hohe Härte, leicht färbbar, autoklavierbar | $ | 1030 MPa | 77 °C | Schläuche für Kraftfahrzeuge und Geräte, Lebensmittelbehälter, Kunststoffbehälter |
Polyvinylchlorid (PVC) | Transparent (aber leicht einfärbbar bis zur Opazität), hohe Variabilität in der Härte, haltbar | $$ | 2300 MPa | 79 °C | Faltenbälge, Verkehrsleitkegel, Rohre, Armaturen |
Nylon (Polyamid, PA) | Transluzent, mittlere Härte, stark, schlagfest | $$$$ | 2900 MPa | 169 °C | Schläuche und Behälter für Kraftfahrzeuge |
Polycarbonat (PC) | Transparent, ziemlich hart, leicht färbbar, sehr zäh, schlagfest | $$$ | 2350 MPa | 143 °C | Große Wasserflaschen, Lebensmittelbehälter, Spritzen |
Cyclin-Olefin-Copolymer (COC) | Transparent, hart, autoklavierbar, starke Feuchtigkeitssperre | $$$$ | 2480 MPa | 77 °C | Blasfolie, Schrumpffolie, Spritzen, medizinische Lagerbehälter (Alternative zu Glas) |
Acrylnitril-Butadien-Styrol-Copolymer (ABS) | Undurchsichtig, hart, zäh, schlagfest | $$$ | 2680 MPa | 88°C | Gehäuse für Elektronik, Stoßstangen, Koffer, Rohre und Schläuche |
*Die Werte für HDT und Biegemodul sind von den spezifischen Inhaltsstoffen und dem Herstellungsverfahren der jeweiligen Charge abhängig.
Entwicklung von Produkten für das Blasformen mit 3D-Druck
Aufgrund hoher Anschaffungskosten, komplizierter und teurer Werkzeugbauprozesse und mangelnder Fertigungskenntnisse lagern viele Unternehmen das Design und die Produktion blasgeformter Teile derzeit an Drittanbieter aus. Die Formen selbst werden häufig aus Aluminium-, Zink- oder Stahllegierungen hergestellt, die in der Bearbeitung teuer sind. Selbst wenn ein externes Unternehmen in der Lage ist, Prototypen von Formen zu erstellen, sind solche Designdienstleistungen oft kostspielig und mit einer langen Durchlaufzeit verbunden, was echtes iteratives Prototyping unmöglich macht.
Mithilfe des 3D-Drucks können Unternehmen nun Prototypen und Formwerkzeuge im eigenen Betrieb entwerfen und so die Kosten und die Durchlaufzeit für die Entwicklung hohler Kunststoffverpackungen für ihre Produkte reduzieren. Viele Unternehmen entscheiden sich zwar immer noch für die Auslagerung der Produktion, aber der 3D-Druck gibt ihnen mehr Kontrolle über das fertige Produkt – und das in kürzerer Zeit und zu viel geringeren Kosten.
Unilever ist kürzlich auf 3D-Druck umgestiegen, um die Kosten zu senken und den Designprozess für Kunststoffverpackungen zu beschleunigen. Gemeinsam mit seinem Fertigungspartner Serioplast validierte das Unternehmen die 3D-gedruckten Formen für das Streckblasformen von Kleinserien mit dem Formlabs-3D-Drucker Form 3L und Formlabs Rigid 10K Resin.
„Mit der 3D-gedruckten Form sparen wir bis zu 70 % an Zeit und bis zu 90 % an Kosten im Vergleich zu einer Standardform. In der Vergangenheit mussten [Kunden] bis zu 12 Wochen lang auf ein einzelnes Design warten. Jetzt schaffen wir in der gleichen Zeit fünf Designs.“
Flavio Migliarelli, R&D Design Manager, Serioplast Global Services
Da 3D-Drucker Teile in wenigen Stunden herstellen können und 3D-gedruckte Formwerkzeuge nur einen Bruchteil so viel kosten wie jene aus Metall, haben Unternehmen jetzt ein größeres Maß an Kontrolle bei der Entwicklung von hohlen Kunststoffteilen. Formendesigns können digital mit CAD erstellt und in einen 3D-Drucker exportiert werden, um hochdetailliertes Rapid Tooling aus Materialien herzustellen, die stark und temperaturbeständig genug für den Einsatz in einer industriellen Blasformmaschine sind. Das ermöglicht es Unternehmen, sowohl von der Form als auch vom endgültigen Teil Prototypen herzustellen. Wenn eine Designänderung erforderlich ist, kann die angepasste Form schnell und kostengünstig gedruckt werden.
„Man kann eine echte Flasche fertigen, bevor man die endgültige Form herstellt. So kann man sofort feststellen, ob man bei der Entwicklung auf dem richtigen Weg ist oder ob etwas geändert werden muss, um Fehler zu vermeiden, die einen teuer zu stehen kommen.“
Stefano Cademartiri, Leiter CAD & Prototyping, Unilever
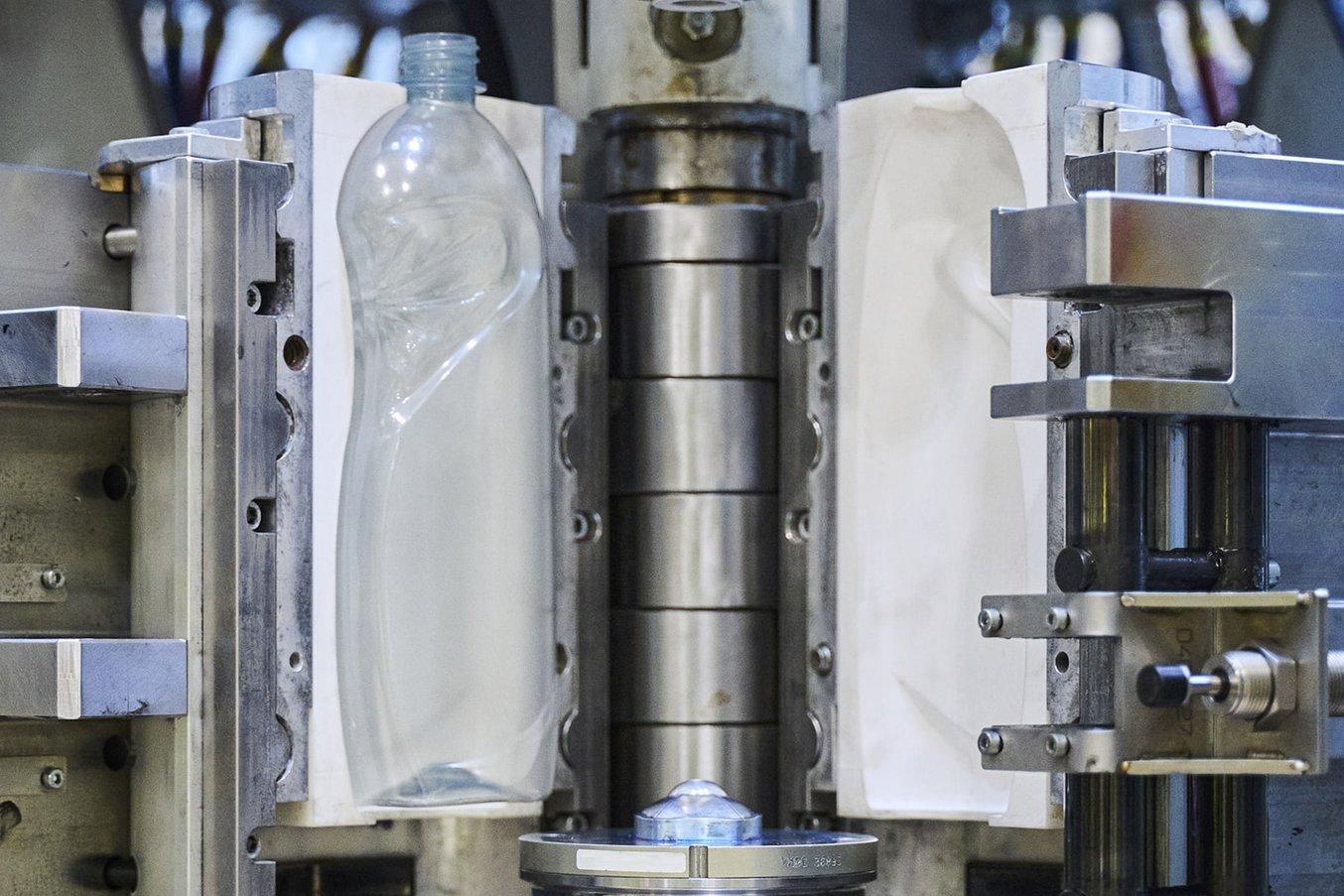
Für eine 750-ml-Flasche für Unilever Slice wurde eine Form aus Rigid 10K Resin 3D-gedruckt und in der Formenhalterung der Maschine installiert. Da das Team dasselbe Prozessfenster verwenden kann wie mit standardmäßigen Pilotformen, lässt sich der endgültige Prozess zuverlässig prüfen.
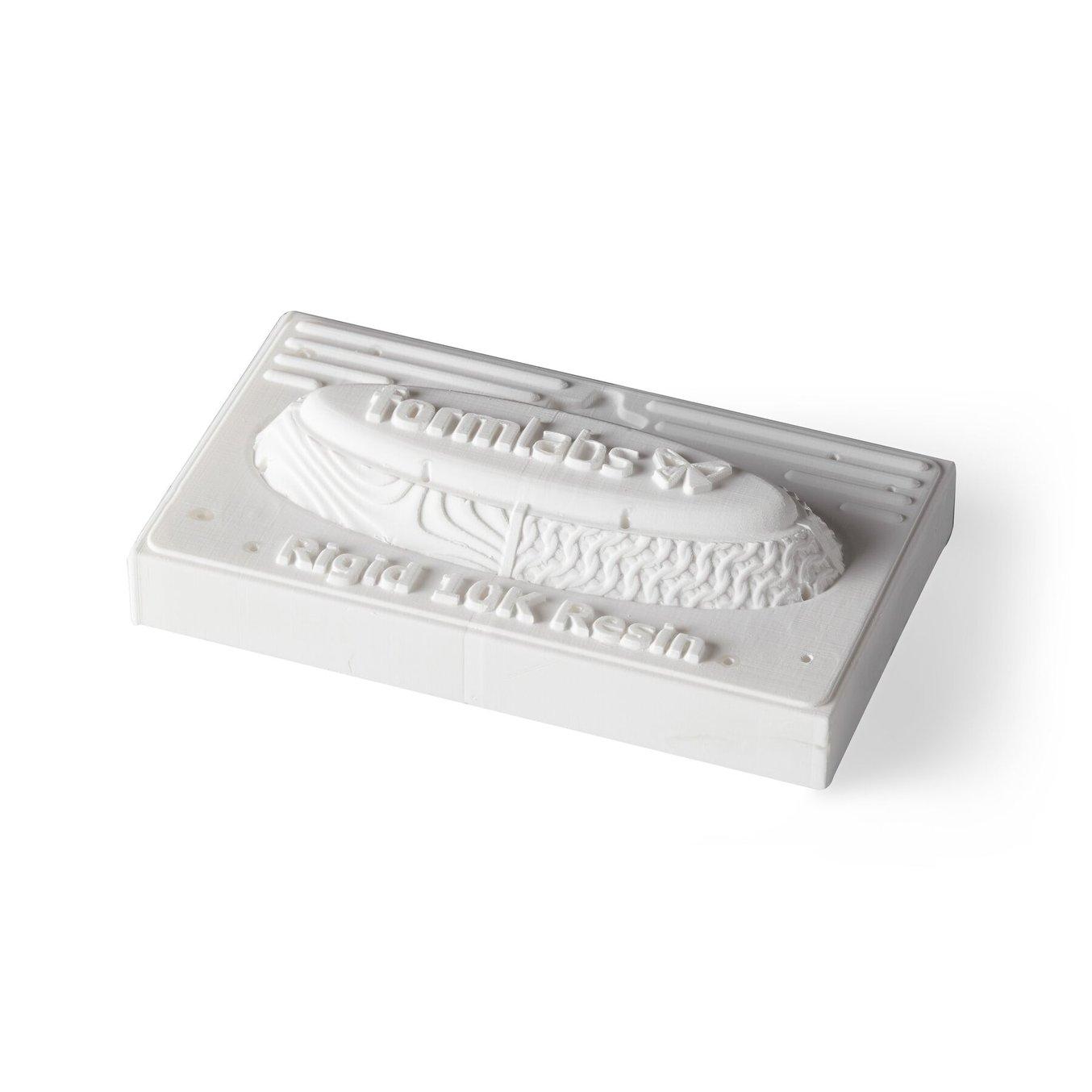
Kostenlosen Probedruck anfordern
Sehen und fühlen Sie die Qualität von Formlabs aus erster Hand. Wir senden Ihnen einen kostenlosen Probedruck an Ihren Arbeitsplatz.
Ihr Einstieg ins Blasformen
Das Kunststoffblasformen ist ein beliebtes Herstellungsverfahren, das in einer Vielzahl von Branchen eingesetzt wird und eine Reihe gängiger Materialien verarbeitet. Beim Blasformen wird thermoelastischer Kunststoff mithilfe von Druckluft ausgedehnt und in die gewünschte Form gebracht. Sobald er diese erreicht hat, wird das Teil gekühlt, nachbearbeitet und an den Kunden versandt.
Beliebte Materialien für das Blasformen sind Polyethylen (PE), Polyethylenterephthalat (PET) und Polypropylen (PP). Seine Materialvielfalt, Skalierbarkeit und Zuverlässigkeit machen das Blasformen zu einem der Hauptverfahren zur Herstellung von Verpackungen, Lagerbehältern und Maschinenkomponenten, unter anderem für die Konsumgüter-, Automobil-, Agrar-, Pharma- und Kosmetikindustrie.
Heute senken Technologien wie der 3D-Druck die Einstiegshürden für das Blasformen sowohl für kleine als auch für große Hersteller, indem sie vor allem das iterative Prototyping von Formen ermöglichen. Produktentwickler und kleine Hersteller, die das Design und die Fertigung von Blasformwerkzeugen bisher auslagern mussten, können betriebsinternen 3D-Druck nutzen, um bei verringerten Kosten mehr Kontrolle über Ihre Prozesse zu erhalten.
Je nach Anwendung können Unternehmen zwischen den Verfahren Extrusionsblasformen (EBM), Spritzblasformen (IBM) und Spritzstreckblasformen (ISBM) wählen. Im Allgemeinen bietet EBM kürzere Durchlaufzeiten und ein größeres Spektrum an Größen, während der Detailgrad und die Designkomplexität eingeschränkt sind. IBM ermöglicht einen hohen Detailgrad, aber die Größe des endgültigen Teils kann begrenzt sein. ISBM wiederum kann eine größere Bandbreite an Geometrien umsetzen. EBM ist in der Regel kostengünstiger als IBM und ISBM.
Möchten Sie mehr über das Blasformen mit 3D-gedruckten Formwerkzeugen erfahren? Laden Sie unser Whitepaper herunter, um detaillierte Richtlinien für den Einsatz von 3D-gedruckten Formen im Blasformprozess und eine ausführliche Fallstudie mit Unilever und Serioplast zu erhalten.