So produziert Braskem mittels 3D-Druck Spritzgussformen für Endverbrauchsteile
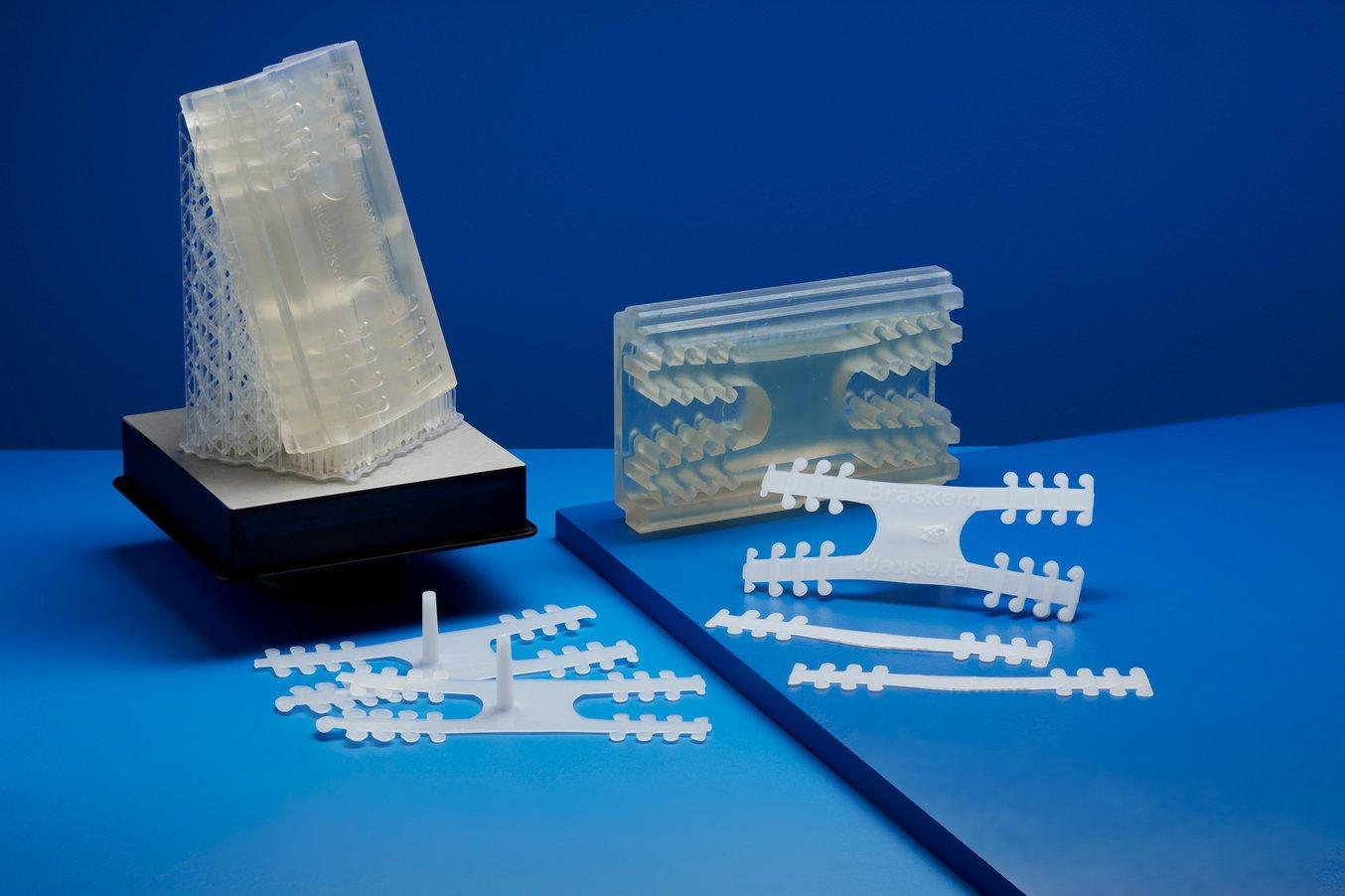
Die Herstellung von Gussformen wird in verschiedenen Sektoren von Produktdesignern, Unternehmern und Lehrern eingesetzt, um identische Teile zu erstellen. Der Spritzguss ist ein besonders vielseitiger Formenbauprozess, der typischerweise für die Herstellung von Großserien eingesetzt wird. Mit diesem Verfahren lassen sich auf kostengünstige, hocheffiziente, wiederholbare Weise hochqualitative Teile in großen Mengen produzieren. Für kleinere Produktionsmengen sind der Kosten- und Zeitaufwand für die Herstellung der Form aus üblichen Werkzeugmetallen jedoch ein Hindernis und machen es für viele Unternehmen unmöglich, den Spritzguss als Verfahren für die Massenproduktion zu nutzen.
Was macht man also, wenn man eine dringende Anfrage erhält, innerhalb einer Woche ein einige Tausend identische Teile zu produzieren? Die Nutzung von 3D-gedruckten Spritzgussformen für die Kleinserienproduktion reduziert die Kosten und die Zeit im Vergleich zum CNC-Fräsen von Metallformen erheblich, während dabei immer noch hochqualitative und wiederholbare Teile produziert werden.
Formlabs hat mit den Technologieentwicklungsingenieuren Michelle Sing und Jake Fallon, dem Prozessingenieur für additive Fertigung, Collin Azinger, und dem globalen Technologiemanager für additive Fertigung, Fabio Lamon, bei Braskem, einem weltweit führenden Petrochemieunternehmen, gesprochen, um mehr über Braskems erste Erfahrungen mit dem Spritzguss mit einer 3D-Druckform zu erfahren.
Schnelle Fertigung von Spritzgussformen in Kleinserie: Eine Live-Podiumsdiskussion
Nehmen Sie an unserer Podiumsdiskussion teil, in der Experten aus der Spritzgussbranche besprechen, wie 3D-Druck den Formenbau auf Abruf ermöglicht, um Hunderte Teile in nur wenigen Tagen von der Idee zur Produktion zu bringen.
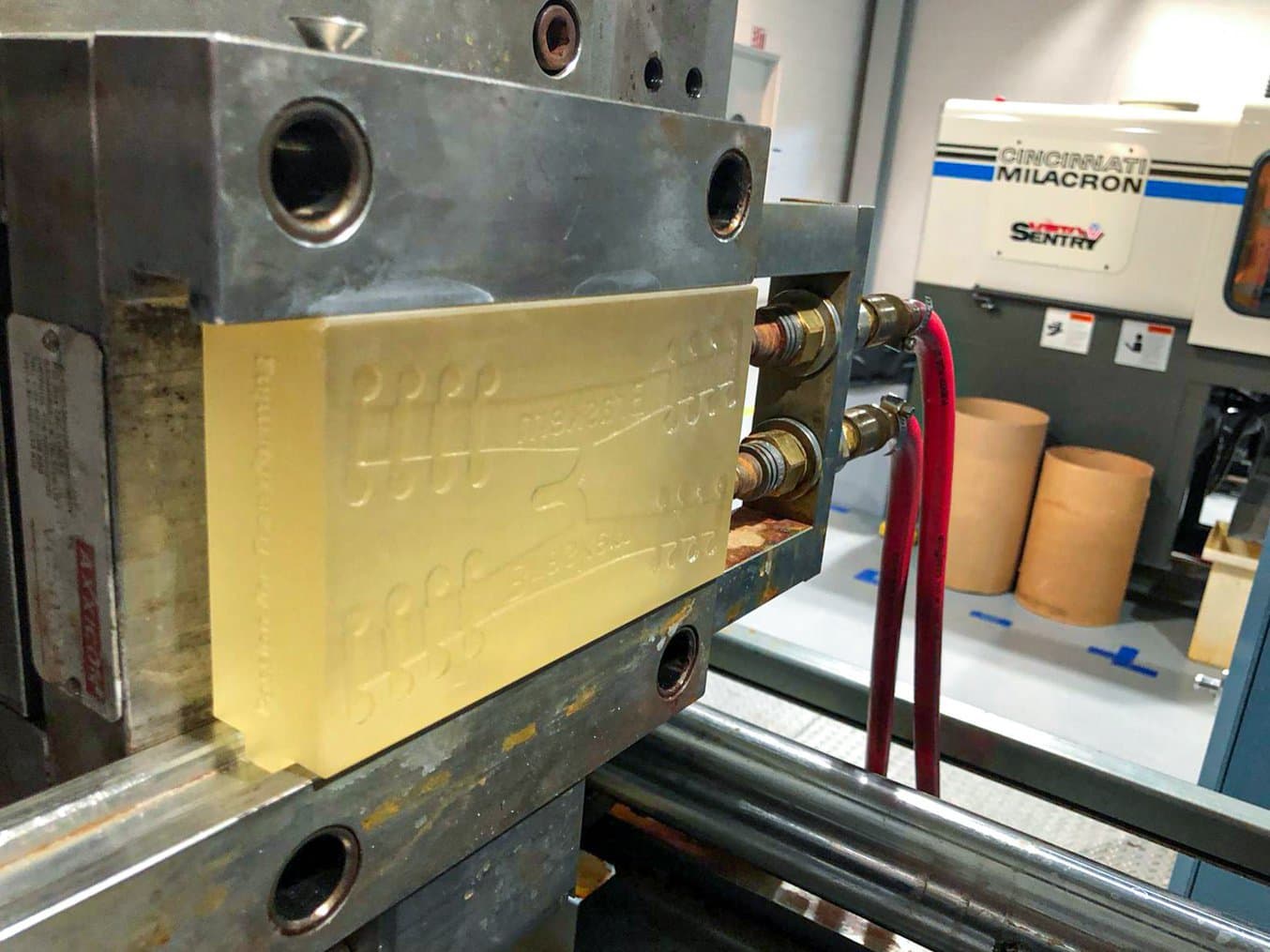
Direktdruck oder Spritzguss?
Jake Fallon öffnete sein Postfach und sah eine dringende E-Mail von einem der Vizepräsidenten von Braskem: Da sich COVID-19 verbreitet, muss das Unternehmen Tausende Bänder für Masken herstellen, um die globale Belegschaft zu schützen. Was konnte Jake innerhalb von 48 Stunden mit der Ausrüstung tun, über die Braskem verfügte?
Als sich Jake mit seinen Kollegen aus dem Team für additive Fertigung bei Braskem traf, dachten sie zunächst daran, die Bänder mit einem FDM-Drucker direkt herzustellen. Doch selbst bei der Geschwindigkeit von FDM würde es geschätzte 17 Minuten dauern, bis ein Band fertig wäre. Da Tausende Bänder gedruckt werden sollten, würde dies viel zu lange dauern. Neben den Benchtop-FDM-Druckern verfügte das Technologiezentrum von Braskem in Pittsburgh auch über einen Formlabs Form 3 und industrielle Spritzgussausrüstung. So entstand eine Idee, die aber gleichzeitig viele Fragen aufwarf.
Was kann Spritzguss leisten? Spritzguss ist bekannt als effiziente und schnelle Möglichkeit für die Massenfertigung von Teilen, doch bestand zunächst Skepsis, als es darum ging, eine 3D-gedruckte Kunststoffform für ihre vollelektrische Cincinnati Milacron Roboshot Spritzgießmaschine mit 110 Tonnen Schließkraft herzustellen. Würde eine Kunststoffform dem Druck der Maschine standhalten? Würde sie nach 50, nach 500 oder erst nach 1000 Schüssen brechen?
Braskem entschied sich für High Temp Resin von Formlabs, ein Material, das für den Druck von Formen und Einsätzen geeignet ist, die in anspruchsvollen Prozessen wie dem Spritzguss eingesetzt werden können, um mit Produktionsmaterialien für die Endverwendung Teile herzustellen. High Temp Resin weist eine Wärmeformbeständigkeitstemperatur von 238 °C bei 0,45 MPa auf. Dies war wichtig, da das Team den Druck so gering wie möglich halten musste, um das Risiko eines Bruchs der Angussöffnung zu verringern. Dadurch war eine erhöhte Temperatur erforderlich, um eine geringere Viskosität zu erreichen. High Temp Resin war das ideale Material, um den höheren Temperaturen und niedrigeren Drücken für diese spezifische Form standzuhalten.
Das Team hat eine Form gestaltet, die pro Schuss zwei Bänder herstellt. Sie nahmen die erste 3D-gedruckte Form aus dem Form 3, entfernten die Stützstrukturen und polierten das Druckteil minimal. Schuss folgte auf Schuss und schnell stapelte sich ein Berg aus Bändern. Ein flexibles Polypropylen mit geringer Viskosität wurde in die Form gespritzt, um den Druck im Hohlraum zu verringern und die Lebensdauer des 3D-Druckteils zu verlängern.
Die allerste Iteration der Form hielt 5 Tonnen Schließkraft stand sowie 20 Sekunden Zykluszeit, einer Einspritzgeschwindigkeit von 1,27 cm/s und einer Zuhaltekraft von 34,5 MPa für ca. 8 Sekunden. Die durchschnittlichen Temperaturen beim Spritzguss betrugen ca. 230 °C.
„Wir haben High Temp Resin V2 mit einer Schichthöhe von 50 Mikrometern verwendet. Die Qualität war echt toll und die Auflösung fantastisch. Wenn man das Band vom Tisch nahm, konnte man kaum den Unterschied zu einem Teil erkennen, das mit einer Metallform hergestellt worden war.“
Jake Fallon
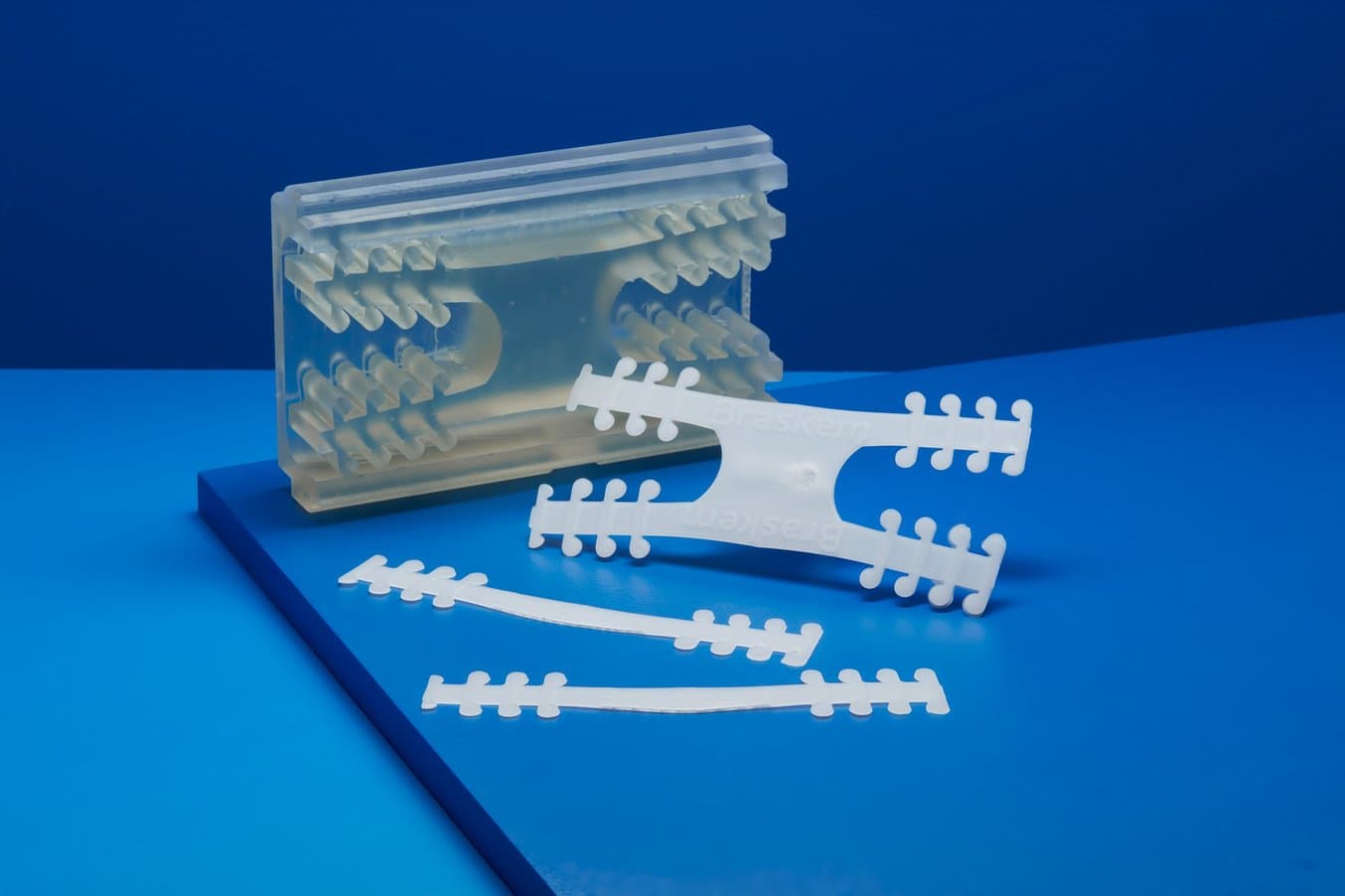
Das Team nutzte ein standardmäßiges Formentrennmittel als Spray, wodurch es pro Spray 40 bis 50 Schüsse durchführen konnte. Die Effektivität des Sprays wurde durch den Druck mit einer Schichthöhe von 50 Mikrometern erhöht, wodurch eine superglatte Oberflächenbeschaffenheit erzielt wurde, durch die sich die Teile leicht aus der Form entfernen ließen. Für die 3D-gedruckte Form war keine zusätzliche Kühlung erforderlich und es gab keinen Hinweis darauf, dass das Spritzgussmaterial mit dem gedruckten Kunstharz reagierte.
Ohne Zugang zu 3D-Druck hätte Braskem eine teure Metallform outsourcen müssen, die das Team Geld und wertvolle Zeit gekostet hätte. Durch die Nutzung von 3D-Druck, konnte das Team innerhalb einer Woche nach dem Eingang der E-Mail des VP, Tausende Bänder fertigen und sie für die Auslieferung an Niederlassungen auf der ganzen Welt vorbereiten.
Designiterationen und Schüsse
„Wir haben den Materialverbrauch durch Designiterationen um 28 % gesenkt“
Jake Fallon
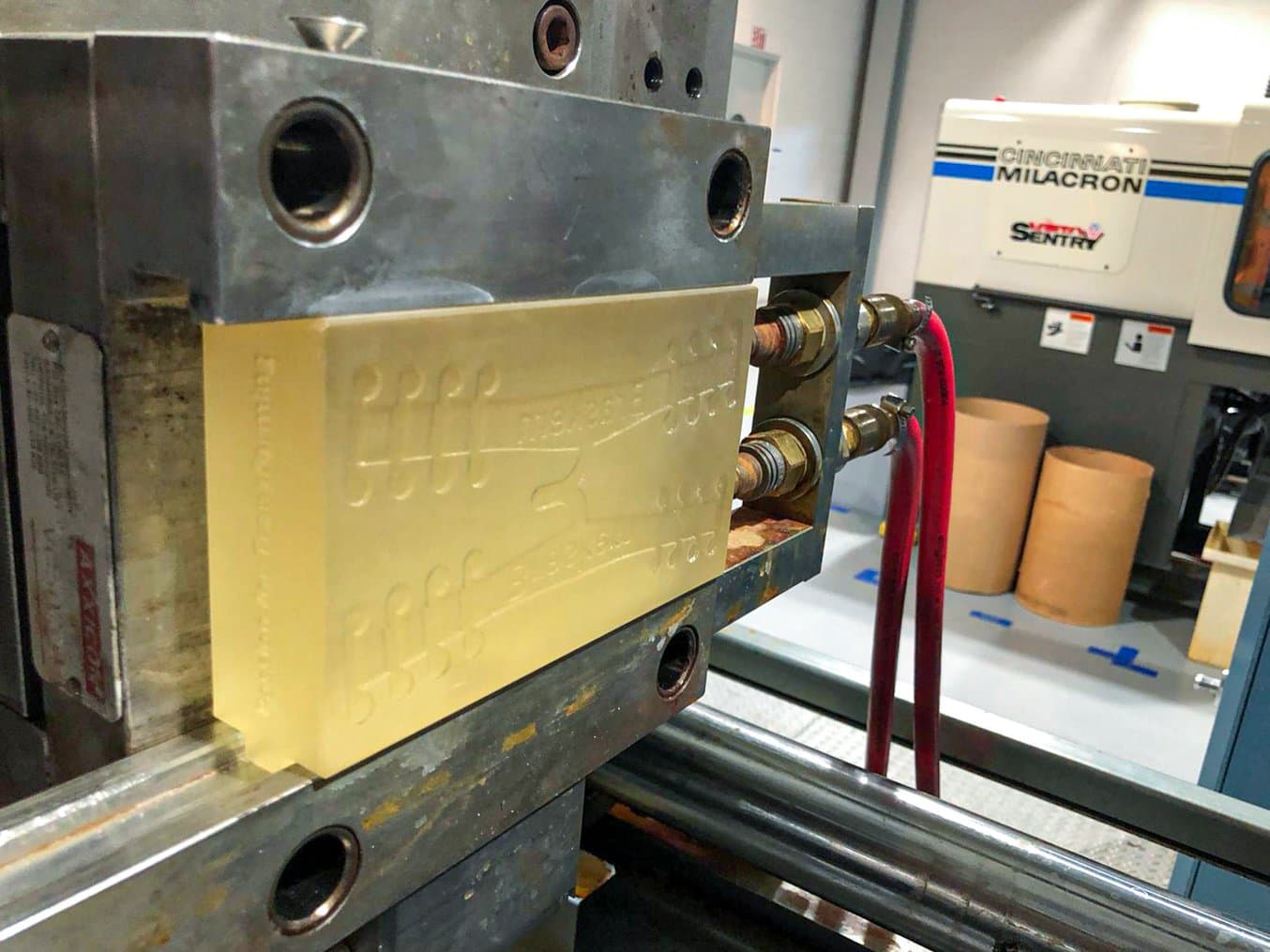
Während die Roboshot-Spritzgießmaschine die Bänder fertigte, bearbeitete Fallon das Formdesign in seiner CAD-Software, wobei er besonders den Anguss vergrößerte. Fallon wollte auch den Fluss im Hohlraum verbessern und den Druck reduzieren, um die Lebensdauer der Form zu verlängern und Gratbildung zu verhindern. Im Laufe des Formverbesserungsprozesses konnte er die Menge an High Temp Resin, das zum Drucken der Form verwendet wird, um 28 % verringern, dem Unternehmen so Geld sparen und die Druckzeit verkürzen.
Obwohl die erste Version der Form bereits beim ersten Versuch funktionierte, wurde die zweite Version mit einem größeren Anguss jetzt so gestaltet, dass sie Tausenden Schüssen standhält. Die neue Form könnte mindestens 1500 Schüssen standhalten, bevor sie ersetzt werden muss. Sie ermöglichte es dem Team, den Bestellungen für Bänder nachzukommen. Die neue und verbesserte Form, die vier Bänder pro Minute herstellt, war genau das, was das Team brauchte, um die Aufgabe zu erfüllen.
Das Team von Braskem sieht Dutzende potenzielle Anwendungsmöglichkeiten für 3D-Druckmodelle in der Zukunft. Erschwingliche 3D-gedruckte Formen, die pro Einheit weniger als 100 US-Dollar kosten, könnten Kunden helfen, schnell Kleinserien zu fertigen. Ein Beispiel wäre eine saisonale Verpackung, mit der ein Produkt aus dem Regal heraussticht. Zuvor konnten kleinere Unternehmen die Kosten für Metallformen und Werkzeuge nicht rechtfertigen. Doch mit 3D-gedruckten Formen, die Tausenden von Schüssen standhalten, könnten sich neue Möglichkeiten für Marken und Märkte ergeben.
Weitere Informationen
„Die Zeit war der Hauptvorteil. Wir haben die Form in einer Woche getestet und dann an einem Tag ein zweites Design gestaltet, das für erhebliche Verbesserungen sorgte.“
Jake Fallon
Das Team von Braskem war erstaunt, wie Spritzguss das Potenzial von 3D-Druckern über das Rapid Prototyping hinaus erweiterte und für die Produktion nutzbar machte. Da Braskem Hunderte Materialien für den Spritzguss anbietet, ist das Unternehmen seit langem ein zuverlässiger Partner für Firmen, die den Spritzguss für die Massenproduktion nutzen. Das Unternehmen vertreibt auch über 300 Materialien für das Thermoformen, Blasformen und weitere Fertigungsverfahren, die von 3D-gedruckten Formen profitieren könnten.
Zukünftig möchte das Team die Spritzgussmöglichkeiten des Form 3L erproben, da dieser größere Teile herstellen kann. Jake sagt dazu: „Mit der 3D-gedruckten Form stießen wir fast an die Grenzen des Fertigungsvolumens des Form 3; wir freuen uns wirklich darauf, die Möglichkeiten des Form 3L zu erproben.“
Laden Sie unser kostenloses Whitepaper herunter oder sehen Sie sich das Webinar an und erfahren Sie mehr über den genauen Prozessablauf, die Designrichtlinien sowie weitere bewährte Praktiken für die Herstellung von 3D-gedruckten Spritzgussformen. Es enthält zusätzliche Fallstudien aus der Praxis von Holimaker und Novus Applications.