Novus Applications setzt für Spritzguss von Prototypenformen auf Rigid 10K Resin
Spritzguss ist ein gängiges und vielseitiges Fertigungsverfahren für die Produktion von Teilen in großen Mengen. Spritzguss wird in Fertigungsverfahren für Haushaltsgeräte und Elektronik sowie in der Automobilindustrie verwendet und viele weitere Hersteller nutzen das Verfahren, um präzise, einheitliche Teile zu erhalten. Die Fertigung von Formen kann teuer und zeitaufwändig sein. Im Falle von spanend gefertigten Formen sind die Anschaffungskosten hoch, was sich erst über die häufig Hunderttausendenvon Endteilen, die letztlich hergestellt werden, wieder auffangen lässt. Für kleinere Produktionsmengen sind der Kosten- und Zeitaufwand sowie das spezielle Gerät und Fachwissen, das für die Herstellung der Form aus üblichen Werkzeugmetallen erforderlich sind, jedoch ein Hindernis und machen es für viele Unternehmen unmöglich, den Spritzguss als Verfahren für die Massenproduktion zu nutzen. Es gibt jedoch Alternativen zur spanenden Fertigung aus Metall.
Novus Applications ist ein auf Konsumgüter spezialisiertes Produktentwicklungsunternehmen. Hier wird der Arbeitsablauf mithilfe des 3D-Drucks beschleunigt, um einen agilen Ansatz zur Fertigung zu ermöglichen und den Spritzguss zu optimieren.
Durch die Herstellung von Spritzgussmodellen via 3D-Druck konnte Novus die Erstellung von Prototypen für die Kleinserienproduktion deutlich einfacher umsetzen, als dies Metallformen möglich ist. Zudem zeichnen sich die so produzierten Teile durch hohe Qualität aus und sind problemlos wiederholbar. Durch 3D-gedruckte Spritzgussformen, und unter Verwendung des Rigid 10K Resins von Formlabs, konnte Novus hochqualitative und wiederholbare Prototypen herstellen sowie Kosten und einige Tage Durchlaufzeit einsparen.
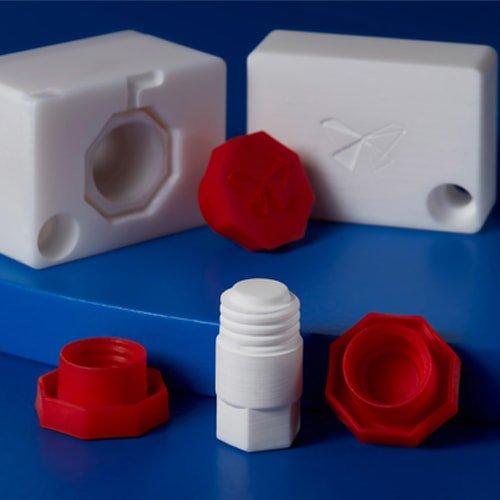
Schnelles Spritzgussgießen in kleinen Stückzahlen mit 3D-gedruckten Gussformen
Laden Sie unser Whitepaper herunter, um Richtlinien für den Einsatz von 3D-gedruckten Formen im Spritzgießprozess zur Senkung von Kosten und Vorlaufzeiten zu erhalten sowie über Fallstudien aus der Praxis mit Braskem, Holimaker und Novus Applications zu lesen.
Hohe Nachfrage für Spritzguss bei Novus
Novus arbeitet mit einigen großen Markennamen der Körper-, Gesundheits- und Mundpflegebranchen zusammen. Das Unternehmen fertigt Designs für den Hersteller an, führt Studien zur Formbarkeit durch, entwickelt in kurzer Zeit Prototypen und neue Versionen, druckt Teile in 3D und stellt kleinformatige Prototypen her, mit denen Kunden die Produkte testen können. Bei Novus liegt der Schwerpunkt auf spritzgegossenen Kunststoffen und deren Verwendung in Baugruppen für den Verbraucher.
Es besteht eine hohe Nachfrage für spritzgegossene Teilen, sei es von Medizintechnikunternehmen oder bekannten Marken wie Colgate und Liquiglide. Das Team von Novus ist durch jahrelange Erfahrung geschult.
„Der Spritzguss verlangt nach hoher Präzision und viel Erfahrung“, so Mark Bartlett, President und Gründer von Novus. „Diese Technik beherrscht nur, wer viel Erfahrung damit hat. Wenn man das aus dem Stand gut machen will, führt das zu Versuch und Irrtum und viel Frust, denn es gibt eine Menge unbekannter Variablen, die man zunächst verstehen muss.“
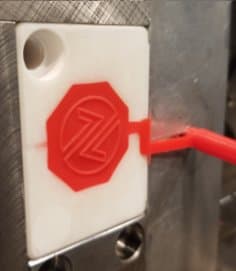
Die Gussform nach dem Einspritzen der Materialien P5M6K-048 Rot (links) und PP1013H1 Weiß (rechts).
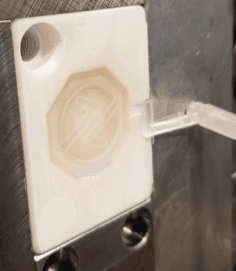
3D-Druck im Spritzgussverfahren nutzen
Dank 3D-Druck kann Novus auf High-End-Software und Bearbeitungsprozesse verzichten und Arbeitszeit sparen. Infolgedessen wird der Ablauf stärker automatisiert. Das vollständige und einfach zu verwendende Ecosystem von Formlabs macht es Ihnen einfacher, in die Welt des 3D-Druck-Spritzgusses einzutauchen.
„Die Produktion dieser Teile findet unbeaufsichtigt statt“, so Bartlett. „Ich brauche also niemanden mit umfassender Erfahrung, wohl aber jemanden mit Erfahrung im 3D-Druck. So verkürzt sich der Lernprozess. Und die Produktion erfordert nicht so viel Aufmerksamkeit.“
Novus stellt viele Verschlüsse her. Das Unternehmen musste viele Prototypen in Kleinserienfertigung herstellen und benötigte eine schnelle Produktionsmethode. Bartlett sagte, dass die schnelle Prototypenfertigung eines Verschlusses in einer 3D-gedruckten Form dazu beitrug, den Arbeitsablauf zu optimieren.
So verhalf Rigid 10K Resin Novus zu schnellerem Design
Ganz entscheidend für den Erfolg ist die Wahl des passenden Materials für den 3D-Druck. Mit seiner Festigkeit, Steifigkeit und Temperaturbeständigkeit eignet sich das Rigid 10K Resi ideal für die Kleinserienfertigung von Spritzgussformen. Genau das, was Novus benötigte, musste es doch schnell eine große Zahl von Prototypen in Kleinserienfertigung produzieren.
Beim Spritzguss kommt es auf die Präzision an, sodass die Teile von hoher Qualität sein müssen. Novus benötigte ein Material, das der hohen Hitze und dem hohen Druck bei diesem Verfahren standhalten und zugleich kleine Details wiedergeben konnte. Insbesondere der gewundene Innenteil war sehr filigran. Die hohe Festigkeit sorgt dafür, dass die aus Rigid 10K Resin gefertigte Spritzgussform dem Druck beim Klemmen und Spritzgießen standhält. Durch die hohe Steifigkeit ist hingegen gewährleistet, dass durch diesen Druck keine Verformung auftritt und präzise Teile gefertigt werden. Dank dieser Eigenschaften konnten Hunderte Teile mit nur einer Form in Polypropylen und Polyethylen gegossen werden, ohne dass es zu Brüchen kam.
Rigid 10K Resin wies nicht nur gute Formbeständigkeit auf. Der Druck war auch einfacher und schneller im Vergleich zum Fräsen von Aluminium und Stahl. „Wie handhabt es Druck und Temperatur in den Materialien, die wir verwenden?“, so Bartlett. „Es hat eine hervorragende Leistung gezeigt ... auf einem Niveau, das wir beim traditionellen Material [Rigid 4000 Resin] noch nicht gesehen hatten.“
Novus erreichte das endgültige Design nach einer Iteration und konnte Zeit sparen. „Ich kann komplexe Formen genau drucken, und das viel schneller, als ich sie maschinell bearbeiten kann“, so Bartlett. Bartlett hatte zwar nicht mit absolut makellosen Teilen gerechnet, doch musste Novus die Formoberflächen nicht anpassen. Lediglich die Außenflächen der Etagen wurden gesäubert. „Sobald wir die Form hatten, haben wir sie benutzt“, so Bartlett. „Danach haben wir die geformten Kunststoffteile untersucht und dafür, dass wir keine Iterationen durchlaufen hatten, waren sie überraschend präzise. Ein Druck, ein Durchlauf, und es hat wunderbar funktioniert.“
Letzten Endes konnte Novus die 3D-gedruckten Spritzgussformen nutzen, um für seine Kunden mit Endverwendungsmaterialien und Herstellungsmethoden schnell und erschwinglich Entwürfe zu prototypisieren. Es konnte die Form drucken, den Entwurf und das Material testen und das Teil noch am selben Tag modifizieren, um schnell zu iterieren und seinen Kunden zu helfen, bessere Produkte auf den Markt zu bringen.
Laden Sie unser kostenloses Whitepaper herunter oder sehen Sie sich das Webinar an und erfahren Sie mehr über den genauen Prozessablauf, die Designrichtlinien sowie weitere bewährte Praktiken für die Herstellung von 3D-gedruckten Spritzgussformen. Es enthält zusätzliche Fallstudien aus der Praxis von Braskem, Holimaker und Multiplus.