Wie der Brillenhersteller Plastinax mithilfe von SLA und SLS die Durchlaufzeit um 40 % verkürzt
Seit 1976 stellt Plastinax bereits Brillen für einige der größten Marken der Welt her. Das Unternehmen arbeitet mit globalen Kunden zusammen, um Sonnenbrillen, optische Fassungen und Sicherheitsfassungen zu entwerfen, und geht dann mit dem Spritzguss von 80 000 bis 100 000 Fassungen pro Monat in die Großserienproduktion über. Lieferzeit und Reaktionsfähigkeit sind von größter Bedeutung – um auf einem globalen Markt wettbewerbsfähig zu bleiben, muss Plastinax Design und Fertigung beschleunigen, um seine Brillenrahmen von ihrem Standort in Mauritius zu Kunden auf jedem Kontinent zu befördern.
Plastinax, ein Unternehmen der ENL Group, verwendet Formlabs' 3D-Drucker der Technologien Stereolithografie (SLA) und Selektives Lasersintern (SLS), um funktionale Prototypen von Rahmen in kleinen Stückzahlen zu produzieren, die vor dem Werkzeugbau von Kunden begutachtet und bewertet werden können. Das Unternehmen hat seine Fertigung auch auf 3D-gedruckte Werkzeuge für Kleinserien und die Übergangsproduktion von Brillenkomponenten ausgeweitet und verwendet dafür den SLS-3D-Drucker Fuse 1 und Nylon 12 Powder.
Der 3D-Druck-Workflow hat auch die Reaktionsfähigkeit erhöht und die Bandbreite der Designs erweitert, die das Team herstellen kann. Steeven Devasagayaum, Plastinax Design Engineer, hat sich mit uns über die Integration des Form 2 und Fuse 1 in seinen Arbeitsablauf unterhalten, und darüber, wie der 3D-Druck die Herangehensweise des Unternehmens an Design und Fertigung reformiert hat.
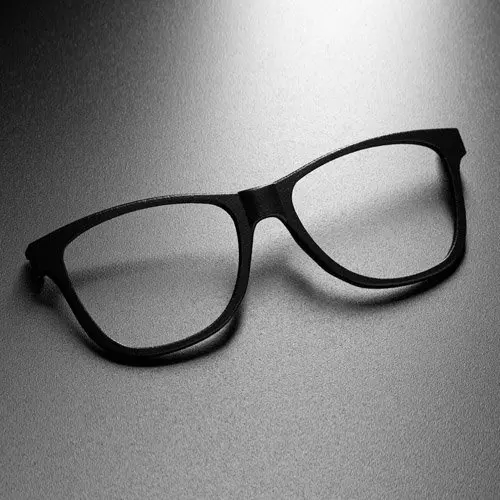
3D-Druck von Brillen auf dem SLS-Ecosystem der Fuse-Serie von Formlabs
In diesem Whitepaper behandeln wir Design- und Materialüberlegungen aktueller Hersteller, die die Möglichkeiten des 3D-Drucks in der Brillenbranche nutzen.
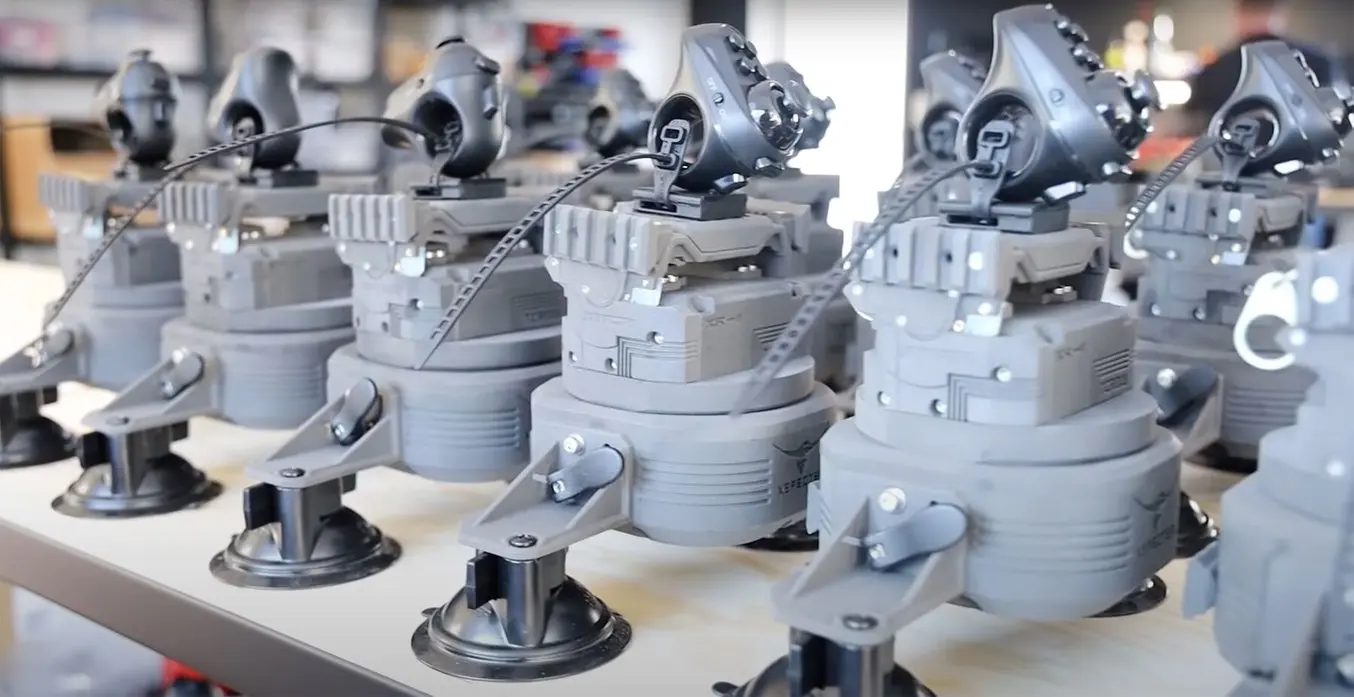
SLS-Produktion für die Endverwendung
3D-Druck für die Endverwendung ist nicht nur möglich, sondern dank des SLS-Ecosystems der Fuse-Serie auch noch erschwinglicher, agiler und leichter skalierbar denn je. Besuchen Sie unsere Seite zum Thema SLS für die Produktion und vergleichen Sie Produktionsverfahren, informieren Sie sich über unsere Mengenrabatte auf Pulver und entdecken Sie die Produktionsabläufe 15 verschiedener Hersteller, die derzeit die Fuse-Serie nutzen.
Großserienfertigung in Mauritius
Plastinax begann in den 1970er Jahren mit der Herstellung von Brillengestellen für bekannte Marken in den USA, Europa und weltweit. Wie in vielen anderen Branchen auch war der Designprozess zu dieser Zeit langsamer und praxisorientierter, obwohl die Brillenbranche schon früh auf Kreativität und Differenzierung durch komplexe Designs oder Branding ausgerichtet war.
Als Devasagayaum 2006 in das Unternehmen eintrat, half er dem Team beim Übergang von handgefertigten Prototypen zu ausgelagerten 3D-gedruckten Modellen. Dieser neue Arbeitsablauf trug dazu bei, dass frühe Iterationen dem endgültigen Spritzgussprodukt näher kamen und der Designprozess beschleunigt wurde – von einem Designbrief oder einer technischen Zeichnung konnte man zu einem handgefertigten Prototyp übergehen und dann zum ausgelagerten 3D-Scan und 3D-Modell.
Der zusätzliche Schritt des 3D-Drucks der Modelle half dabei, die Prototypen den endgültigen Teilen stärker anzugleichen, brachte aber immer noch Probleme mit sich, wenn ein Kunde weitere Änderungen verlangte – es konnte eine Woche oder länger dauern, bis ein zusätzlicher Satz von Prototypen eintraf. Die verlängerte Durchlaufzeit erschwerte es Plastinax, wettbewerbsfähig zu bleiben.
3D-Druck im eigenen Betrieb
Das Forschungs- und Entwicklungsteam von Plastinax begann sich nach einem SLA-3D-Drucker umzusehen, mit dem es seine Durchlaufzeiten verkürzen könnte. Die auf dem Markt erhältlichen Geräte waren jedoch teuer, und das Outsourcing von schnellen Prototypen war kostengünstiger als die Investition in die damals verfügbaren Drucker.
Im Jahr 2016 beschloss Plastinax, mit dem Form 2 3D-Druck-Kapazitäten in den eigenen Betrieb zu holen. Ein zweites Gerät folgte ein Jahr später, um die steigende Nachfrage nach schnellen Prototypen zu befriedigen. „Diese Maschinen waren bahnbrechend. Ich konnte einen schnellen Prototyp in wenigen Stunden entwerfen und in die Hand nehmen. Wir konnten unsere Reaktionsfähigkeit unter Beweis stellen und für unsere internationalen Kunden innerhalb einer Woche Anpassungen umsetzen. Sie haben das beste Preis-Leistungs-Verhältnis und sind vor allem zuverlässig“, so Devasagayaum .
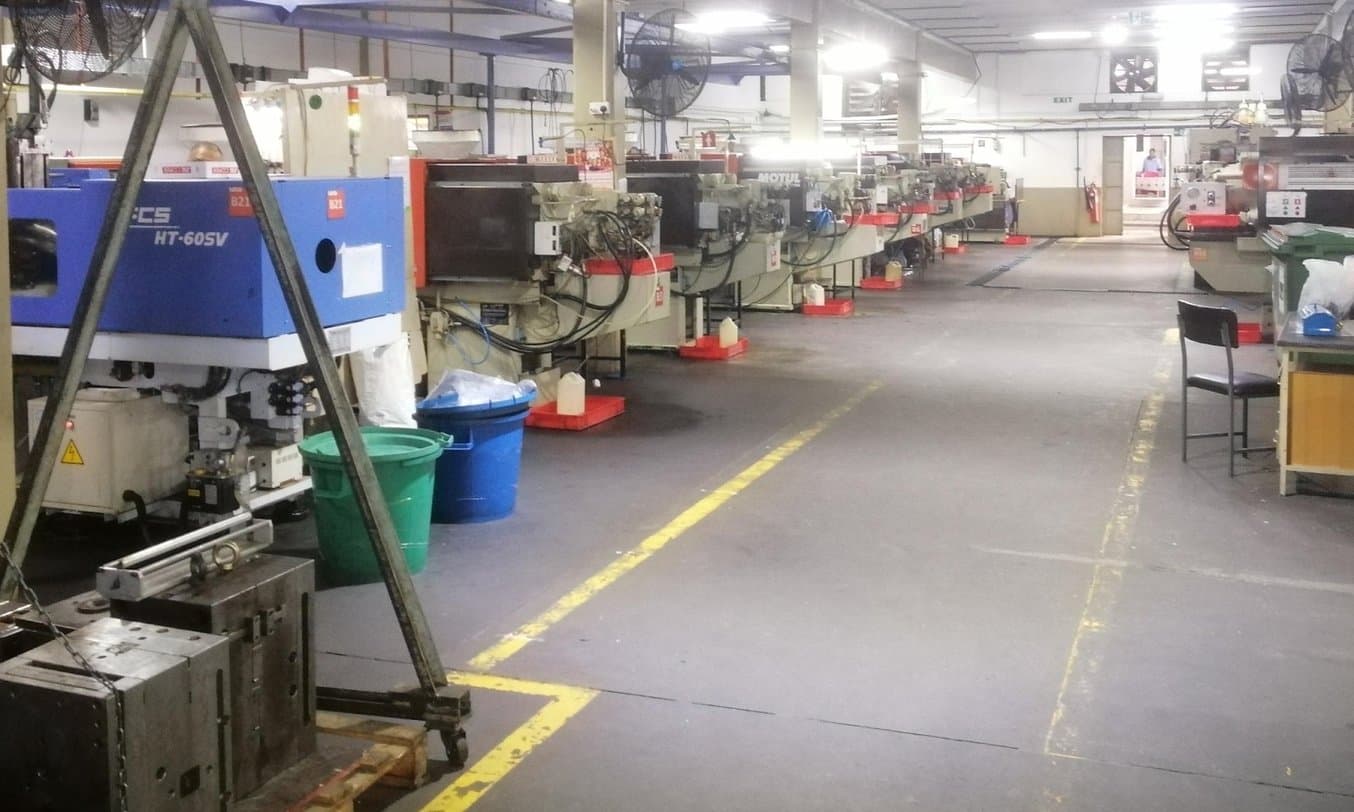
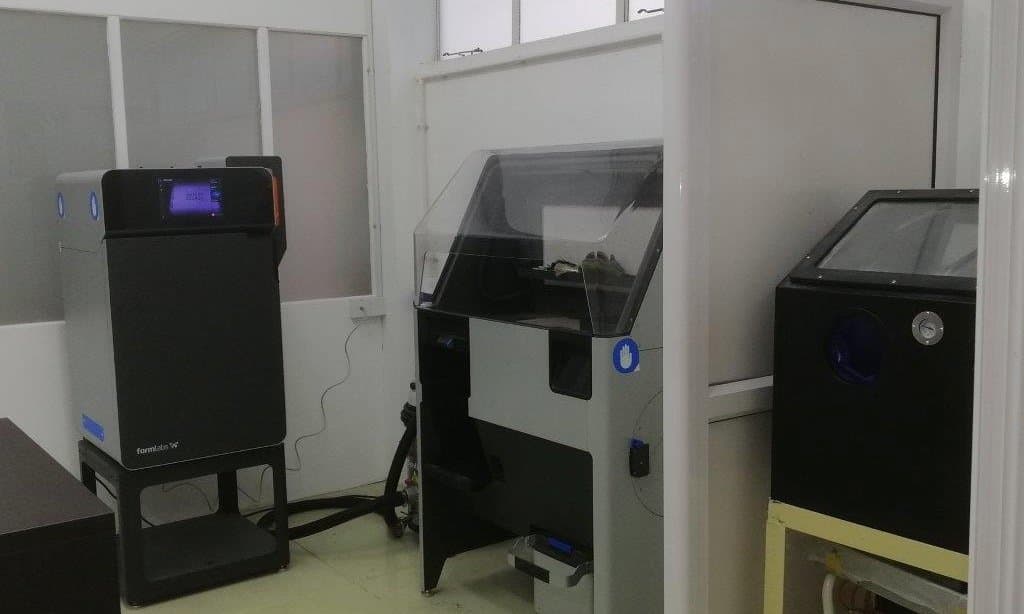
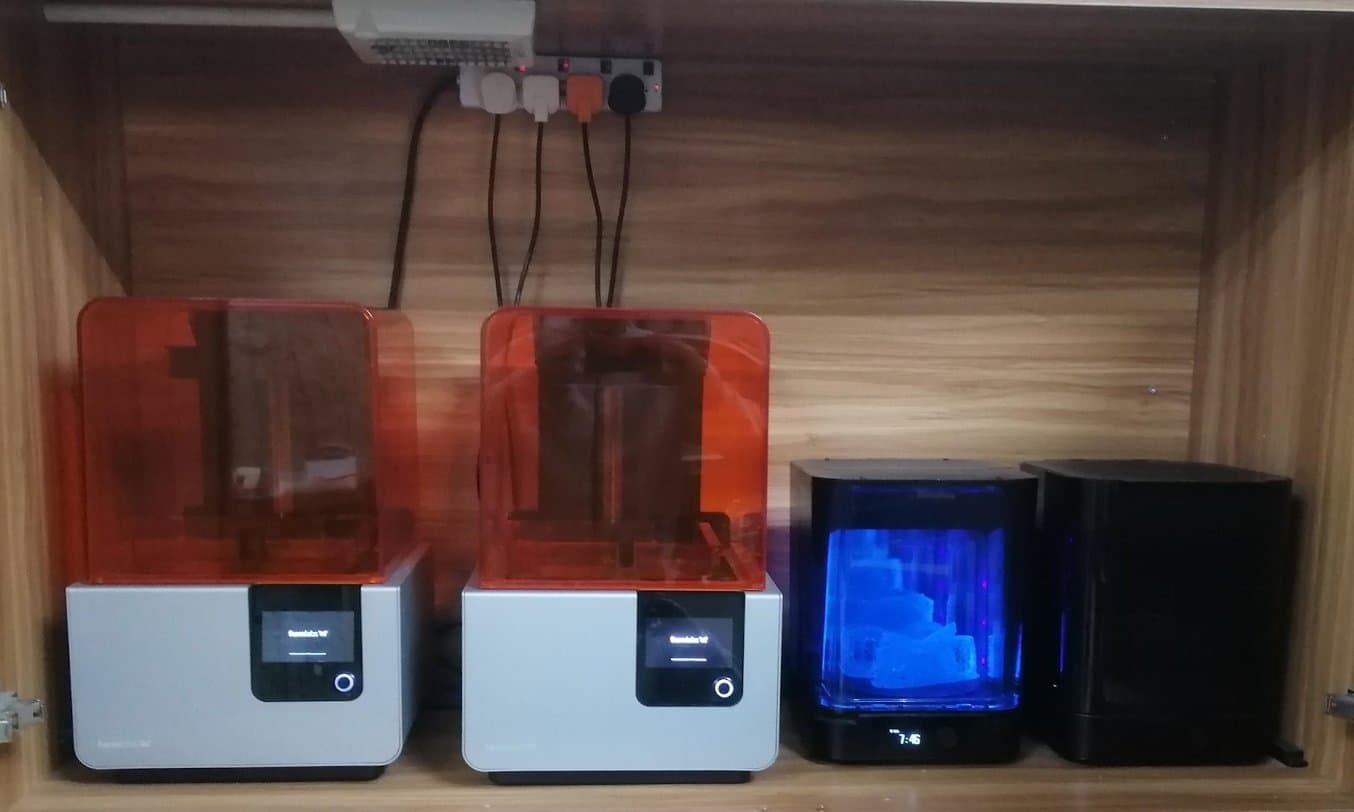
Plastinax nutzt die industrielle Leistung eines großen Produktionsbetriebs (links) und stellt jedes Jahr über eine Million Brillen her. Durch den Einsatz von betriebseigenen 3D-Druckern wie der Fuse-Serie (Mitte) und des Form 2 (rechts) kann das Unternehmen ausgiebiger iterieren und sein Geschäft weiter ausbauen.
Skalierung mit SLS
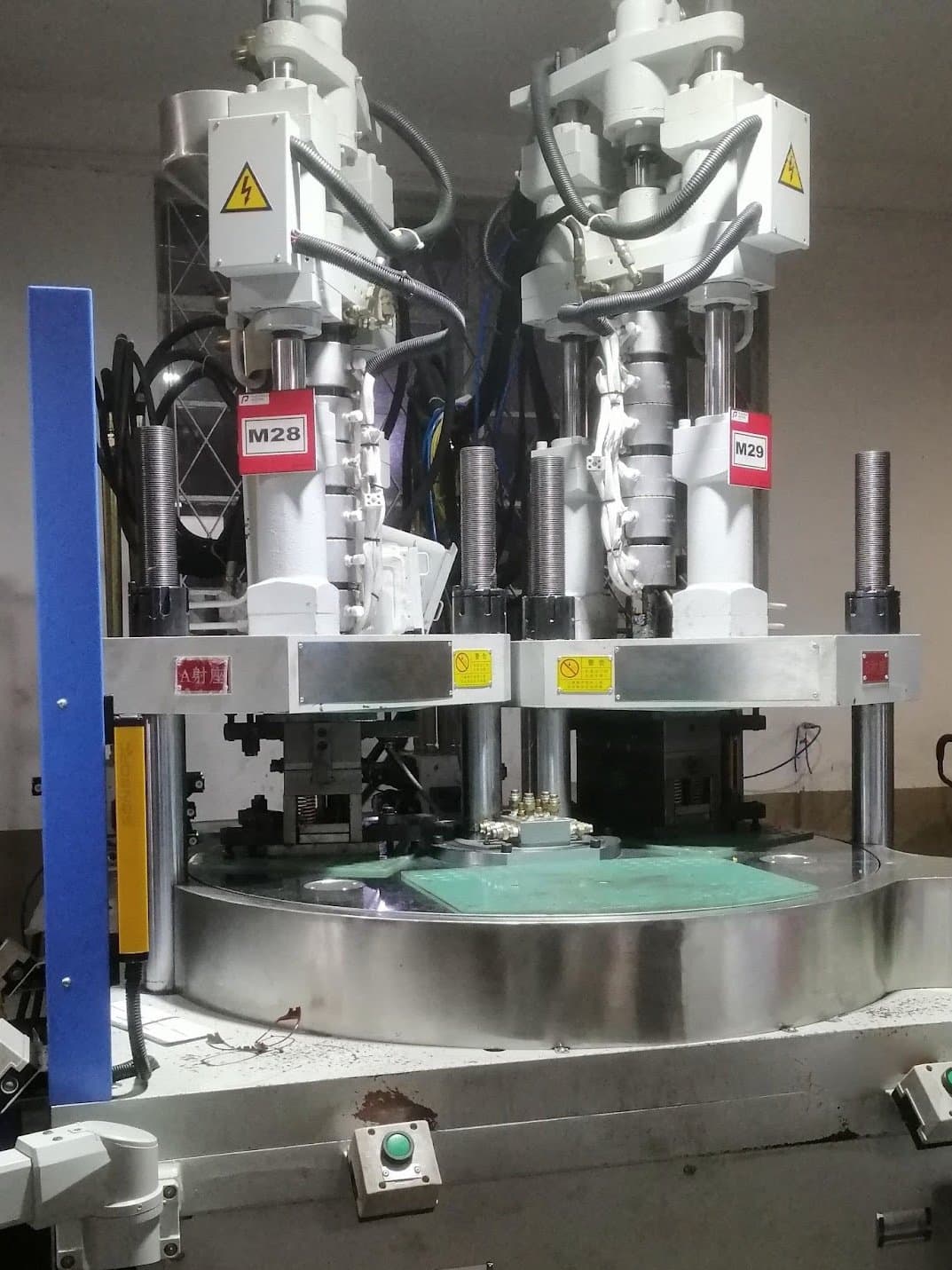
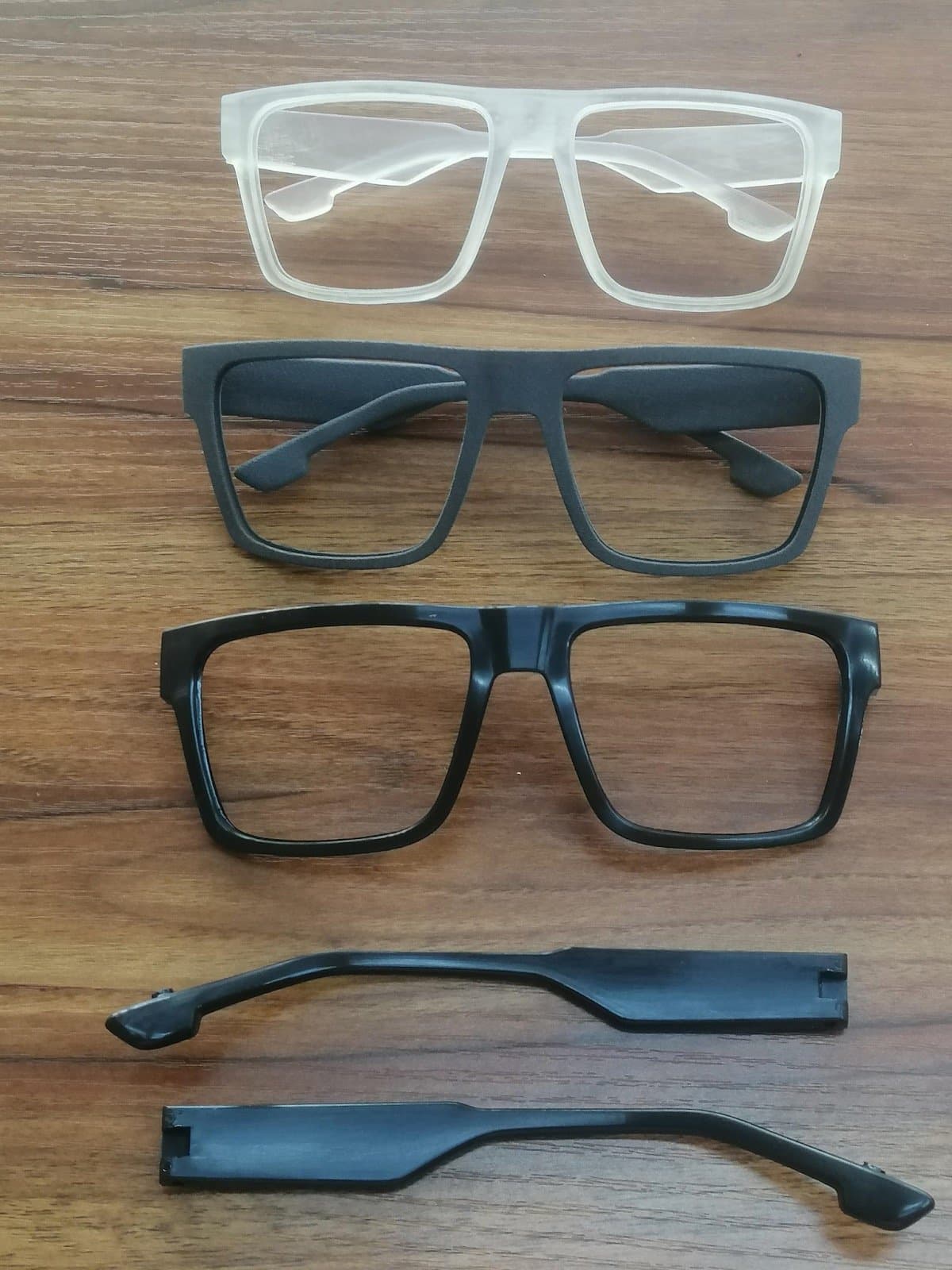
Plastinax ist jetzt in der Lage, mit seinen Industriemaschinen Spritzgussformen herzustellen (links) sowie SLA- und SLS-Materialien zu drucken (rechts, oben und Mitte). So erhält das Unternehmen Fassungen, die in Optik und Funktion dem Endprodukt gleichkommen (rechts unten).
Plastinax vergrößerte die Anzahl der verwendeten Kunstharze – von Clear Resin für lichtdurchlässige Designerfassungen bis zu Grey Pro Resin für Funktionstests. Im Jahr 2021 zeigte ein Kunde dem Team 3D-gedruckte Nylon-Prototypen eines ostasiatischen Konkurrenten und demonstrierte deren Langlebigkeit. „Damit begann die Suche nach einer Maschine, die so etwas kann. Wir mussten Innovationen einführen und zuverlässige, leistungsstarke Geräte anschafften, die uns so wettbewerbsfähig wie möglich machen. Zu der Zeit arbeiteten wir bereits seit sechs Jahren mit Formlabs zusammen. Die Unterstützung und der Service waren so großartig, dass wir uns für den Fuse 1 entschieden“, erinnert sich Devasagayaum.
Kleine Variationen, große Ergebnisse
Für einen internationalen Auftragsfertiger wie Plastinax hängt der Erfolg davon ab, Kundenaufträge zu sichern und zu beweisen, dass sein Endprodukt der Konkurrenz überlegen ist. Kunden ein einziges Design aus einem hochwertigen Material zu senden, reicht möglicherweise nicht aus. Steeven Devasagayaum stützt sich auf den Fuse 1, um auf winzige Änderungen in den Kundenanforderungen zu reagieren.
„Bei Brillen sind die kleinen Unterschiede extrem wichtig. Es mag sich nur um Zehntel Millimeter an Variation handeln. Ich wurde schon gebeten, den Winkel der Nasenbrücke um ein Grad anzupassen, und diese Drucker können das. Danach schicke ich dem Kunden die verschiedenen Versionen“, erklärt Devasagayaum.
Das selbsttragende Pulverbett der SLS-Technologie des Fuse 1 ermöglicht es dem Team, die Druckteile durch Verschachteln oder Stapeln effizient zu packen, um jedes bisschen Pulver voll auszunutzen. Damit ist es jetzt möglich, mehr als 10 Brillenrahmen auf einmal zu drucken. Dies vereinfacht den Arbeitsablauf und erleichtert die Nachbearbeitung aller Teile zugleich im Fuse Sift. Indem Plastinax mehrere Varianten zugleich anbot, ist es dem Unternehmen gelungen, Aufträge nach nur einem Gespräch zu gewinnen. Bei einem Auftrag waren auch Brillenrahmen der Konkurrenz im Rennen, die aber mit der falschen Linsengröße verschickt wurden, sodass Plastinax einspringen konnte. „Innerhalb weniger Stunden konnten wir die richtige Größe finden, die Rahmen 3D-drucken und ihnen am nächsten Tag einen neuen Druck schicken“, erzählt Devasagayaum.
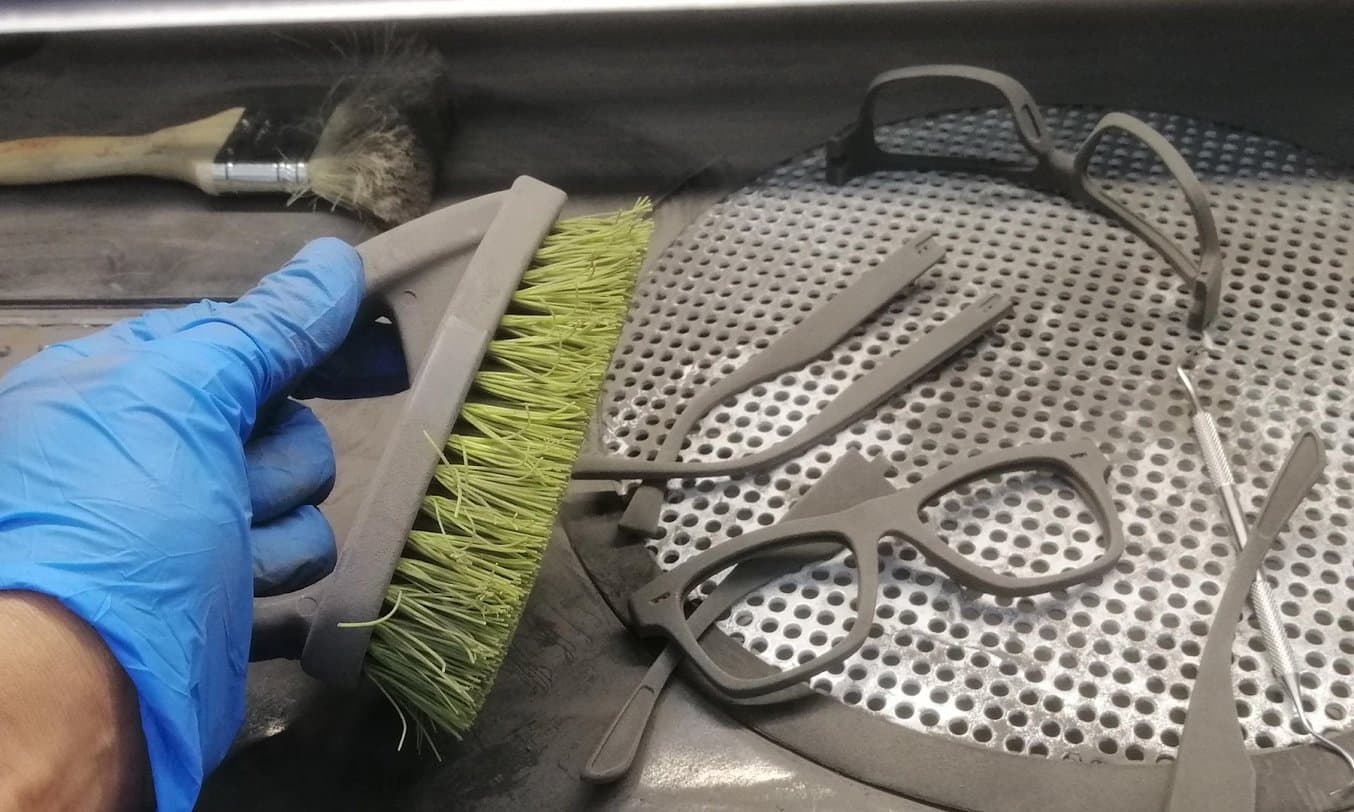
Der Fuse Sift rationalisiert den Arbeitsablauf bei Plastinax und ermöglicht die schnelle Herstellung von Prototypen, um Passform, Funktion und Stil zu testen.
Vereinfachter Arbeitsablauf mit SLA und SLS
Mit einer leistungsstarken Industrielösung im eigenen Betrieb lassen sich die Arbeitsprozesse effizient halten. Devasagayaum setzt in seinem Designprozess sowohl SLA als auch SLS ein, und da beide Drucker leicht zugänglich sind, kann er im Laufe eines Tages problemlos von einer Technologie zur anderen wechseln. Während im Fuse 1 funktionale Prototypen gedruckt werden, die winzige Messunterschiede genau anzeigen, kann der Form 2 zwei Rahmen aus Clear Resin fertigen, die dann lackiert werden, um Optionen für die endgültige ästhetische Ausführung zu demonstrieren.
„Beide Technologien helfen mir bei meinem Designprozess. Nylon 12 Powder ähnelt dem endgültigen Polyamid, aus dem die Rahmen im Spritzgussverfahren hergestellt werden, und auf die Teile aus Clear Resin können Lacke und Muster aufgetragen werden, um zu zeigen, welche Oberflächen wir herstellen können. Wir können uns beides zunutze machen – sowohl die Oberflächenqualität von SLA als auch die Festigkeit und Haltbarkeit von Nylon.“
Steeven Devasagayaum, Entwicklungsingenieur bei Plastinax
Dank der Ähnlichkeit von Nylon und Polyamid können Kunden sich einen Eindruck von Gewicht und Festigkeit ihres fertigen spritzgegossenen Brillenrahmens verschaffen. Für einen Kunden mit einem Designkonzept für eine Schutzbrille druckte Devasagayaum mehrere Prototypen, die dem Marketing-Team des Kunden präsentiert werden konnten. Die Schutzbrille musste robust, schlagfest und leicht biegsam sein, wofür SLS die perfekte Lösung bot. „Wir könnten die Teile in kurzer Zeit lackieren und sie sahen genauso aus wie die fertigen spritzgegossenen Kunststoffversionen“, so Devasagayaum.
Die inhärente Flexibilität von Teilen aus Nylon 12 Powder ist auch eine Hilfe, wenn es darum geht, Linsen in die Prototypen einzusetzen und zu entfernen. Plastinax ist in der Lage, voll funktionsfähige Prototypen mit unterschiedlich starken Linsen für eine Vielzahl von Rahmen vorzustellen, sodass seine Kundschaft ein Modell erhält, das den spritzgegossenen Rahmen hinsichtlich Optik und Funktion in nichts nachsteht.
Auf dem Fuse 1 kann Plastinax nun 28 Prototypen zugleich drucken, wenn für Anlässe wie beispielsweise Industriemessen größere Stückzahlen benötigt werden. „Wir können in kürzester Zeit Prototypen herstellen, die wie das Endprodukt aussehen und sich so anfühlen, und das ganz einfach betriebsintern. Wenn wir das auslagern müssten, würde es 10 Tage oder länger dauern“, erklärt Devasagayaum.
Zusätzlich zur Prototypenfertigung eröffnet die Fuse-Serie bei Plastinax auch neue Werkzeugbauprozesse. Die leichte Flexibilität von Nylon und seine hohe Maßgenauigkeit machen es möglich, haltbares Fertigungswerkzeug für die Optimierung der Fertigungsstraße zu entwickeln, zu testen und herzustellen. So druckt Devasagayaum zum Beispiel Formscheiben und Unterlagen für das Zuschneiden von Linsen sowie Unterlagen für das Einsetzen von Metallscharnieren an den Brillenbügeln oder für die Fixierung der Rahmen beim Bohren von Löchern zur Befestigung individualisierter Metall-Logos.
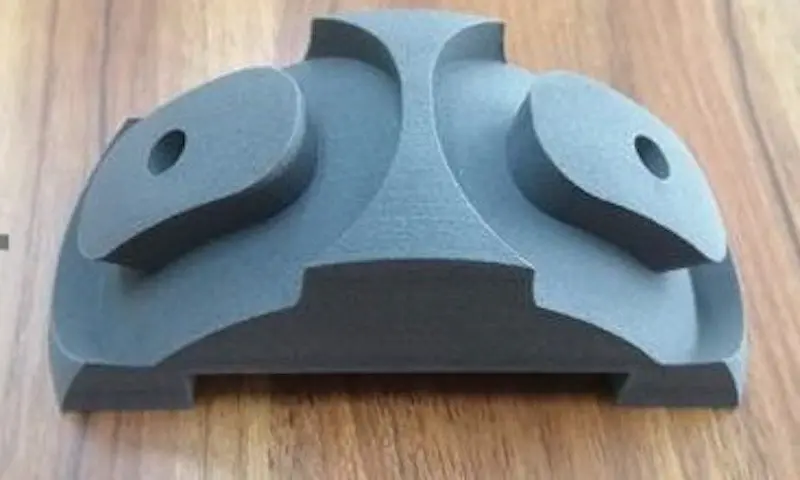
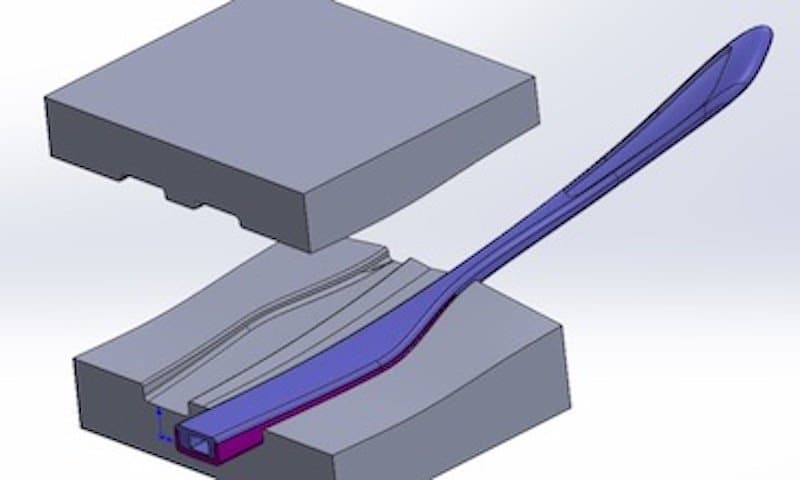
Plastinax fertigt Werkzeuge zur Herstellung von Linsen (links) oder Basen für die Einfügung von metallenen Flex-Scharnieren in die Bügelkomponenten einer Brille sowie für die CNC-Bohrung von Hohlräumen auf Brillenrahmen für maßgeschneiderte Metalllogos.
Der Blick in die Zukunft
Die Brillenbranche ist auf dem besten Weg, ein Vorreiter in Sachen Individualisierung zu werden. Brillen sind eines der wenigen Produkte, die einerseits als modisches Statement verwendet werden, aber auch als notwendiger Bestandteil des Lebens von Millionen von Menschen, die Korrekturlinsen benötigen. Beide Seiten der Branche können von der individuellen Anpassung an die Gesichtsform und von ästhetischen Personalisierungen profitieren.
Plastinax ist sich bewusst, dass Individualisierung in naher Zukunft eine wertvolle Leistung sein wird, und sieht sowohl SLA als auch SLS als potenzielle Workflow-Lösung. SLA-3D-gedrucktes Rapid Tooling für den Spritzguss aus Materialien wie Rigid 10K Resin bietet eine Alternative zu Metallwerkzeugen. Weiterhin hat Devasagayaum bereits im Visier, auf dem Fuse 1 kleine Stückzahlen von Brillenfassungen für die Endverwendung direkt zu drucken. „Die Möglichkeiten sind endlos. Der Form 2 hat unsere Arbeit 2016 revolutioniert und der Fuse 1 war ein weiterer Wendepunkt“, urteilt er.
Wenn Sie mehr über den 3D-Druck von Brillenrahmen erfahren möchten, lesen Sie unseren Anwendungsleitfaden, oder wenden Sie sich an unser Vertriebsteam, um mehr über den SLS- und SLA-3D-Druck im eigenen Haus zu erfahren.