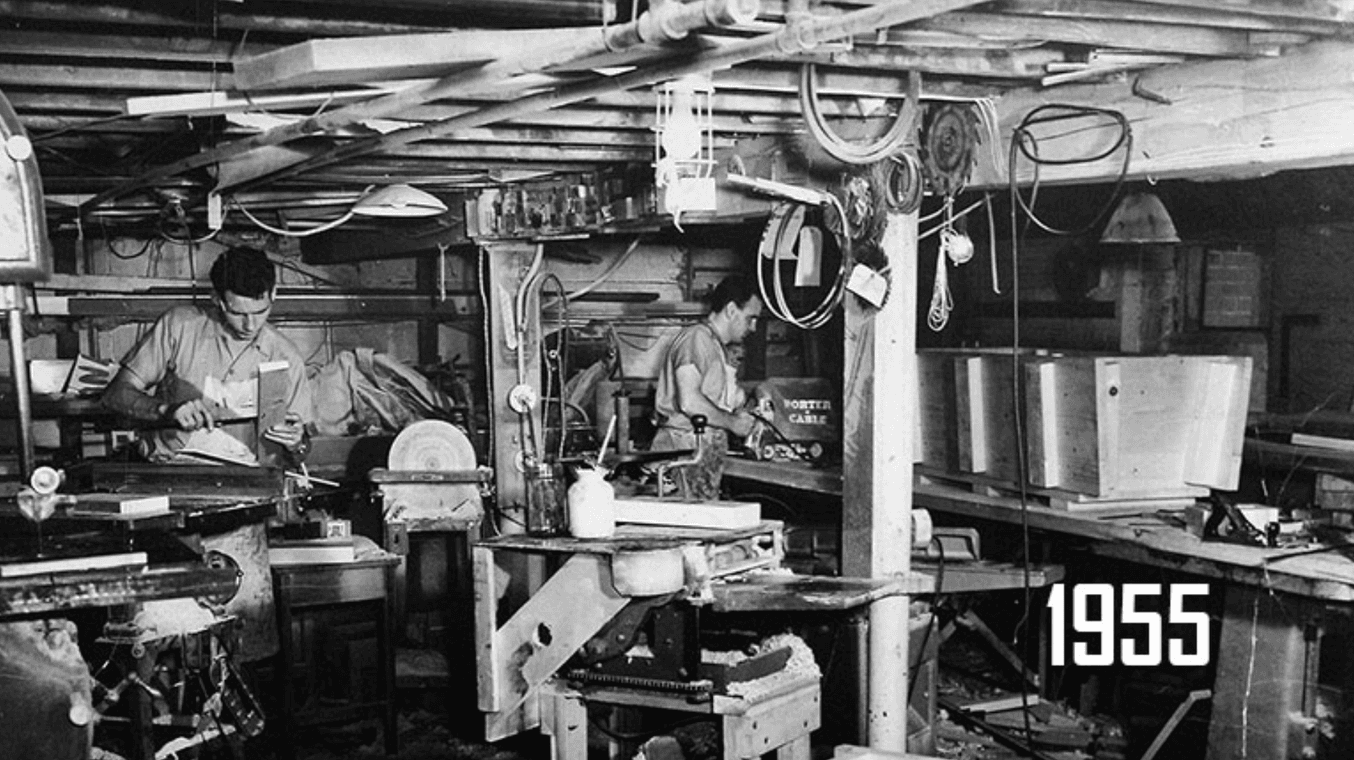
Das Unternehmen Productive Plastics besteht seit 1955 und beliefert unter anderem die Medizin-, Eisenbahn-, Elektronik- und Automobilbranche mit hochwertigen thermogeformten Teilen.
Als industrielles Thermoformunternehmen arbeitet Productive Plastics mit großen Maschinen, noch größeren Kunden und, wie der Name verrät, hohen Produktionsvolumen. Das Unternehmen erhält Aufträge in der Größenordnung von beispielsweise Hunderten von Schutzblenden für Medizinprodukte für mehrere Hersteller aus der Fortune-500-Gruppe oder auch Tausenden von Armstützenbauteilen für Zugwaggons.
Die von der Kundschaft angeforderten Teile sind stets verschieden, doch die Maschinen und die Arbeitskapazität von Productive Plastics bleiben konstant. Deshalb musste das Unternehmen all seine Prozesse optimieren und individualisieren, damit sie sich an immer neue Geometrien und Bauteiltypen anpassen lassen. Hierfür produzierte das Team eine umfassende Bibliothek von Fertigungshilfsmitteln auf dem Fuse 1, einem 3D-Drucker für selektives Lasersintern (SLS).
Mit Productive Plastics in der Fertigungshalle
Thermoformen ist ein Fertigungsverfahren, bei dem Kunststoffplatten oder -folien erhitzt und dann in die gewünschte Form gebracht werden. Dafür gibt es zahlreiche verschiedene Methoden, unter denen das Vakuumformen, das Druckformen und das mechanische Formen am gängigsten sind. Productive Plastics betreibt sechs Fertigungszellen, sodass mehrere Projekte zugleich laufen können. Jede dieser Zellen ist mit einer industriellen Thermoformmaschine, einer CNC-Fräsmaschine, einem Montagebereich und einem Computersystem zur Organisation und Überwachung des Betriebs ausgestattet.
Die sechs Fertigungszellen sind durchgängig in Betrieb und gehen mit Abschluss eines Auftrags sofort zum nächsten über. Die Fertigungshilfsmittel, die für die Aufträge jeweils notwendig sind, werden von Werkzeugingenieur Dustin Johnson bestimmt und entworfen. So erfordern bestimmte Aufträge zum Beispiel Bohrschablonen, dank welcher technische Mitarbeitende zwei Komponenten genau miteinander verbinden können, während für einen anderen Auftrag ein Ersatzteil für eine defekte Maschinenkomponente benötigt wird.
„Der Fuse 1 war unser erster 3D-Drucker. Bevor wir ihn hatten, haben wir Vorrichtungen durch Fräsen von Holz hergestellt, individuelle Halterungen an Spritzgussunternehmen ausgelagert oder einfach vollkommen auf bestimmte Fertigungshilfsmittel verzichtet und die Abstände abgeschätzt“, erzählt Johnson.
Durch die Anschaffung des Fuse 1 konnte das Unternehmen Kosten sparen, seine Produktivität steigern und Ausfälle oder Verzögerungen vermeiden. Johnson hat sogar begonnen, 3D-gedruckte Bauteile für die Endverwendung als Alternativen für die Baugruppen von Kunden zu entwerfen. „Intern haben wir den Zeitplan viel besser unter Kontrolle. Es ist viel einfacher, auf Drucken zu klicken, als ein Teil vom Kunden oder einem Drittanbieter anzufordern. Und je mehr wir betriebsintern erledigen können, desto kosteneffizienter wird es“, erklärt Kyle Davidson, Leiter von Vertrieb und Marketing bei Productive Plastics.
Kosten senken mit betriebsinternen Halterungen und Vorrichtungen
Productive Plastics ist auf das Thermoformen von dickeren Halbzeugen spezialisiert und nutzt für die thermogeformten Endprodukte häufig dicke Platten aus PVC/Acryl wie etwa Kydex. Solche Platten haben einen relativ niedrigen Stückpreis, aber indem das Team durch das sorgfältige Einrichten von Klemmen, Formteilen und Umformparametern Abfälle vermeidet, kann es für sich und seine Kunden dennoch Einsparungen im Tausenderbereich erzielen.
Bei einer Innenkomponente eines Zugwagons fielen die Umformparameter so aus, dass die Klemmen zu weit vom Formwerkzeug entfernt waren. Das Team musste zwischen Formwerkzeug und Spannrahmen einen Abstand von 0,6 cm einhalten, entweder durch eine Vorrichtung, die diesen Abstand ausfüllt, oder durch eine größere Materialplatte.
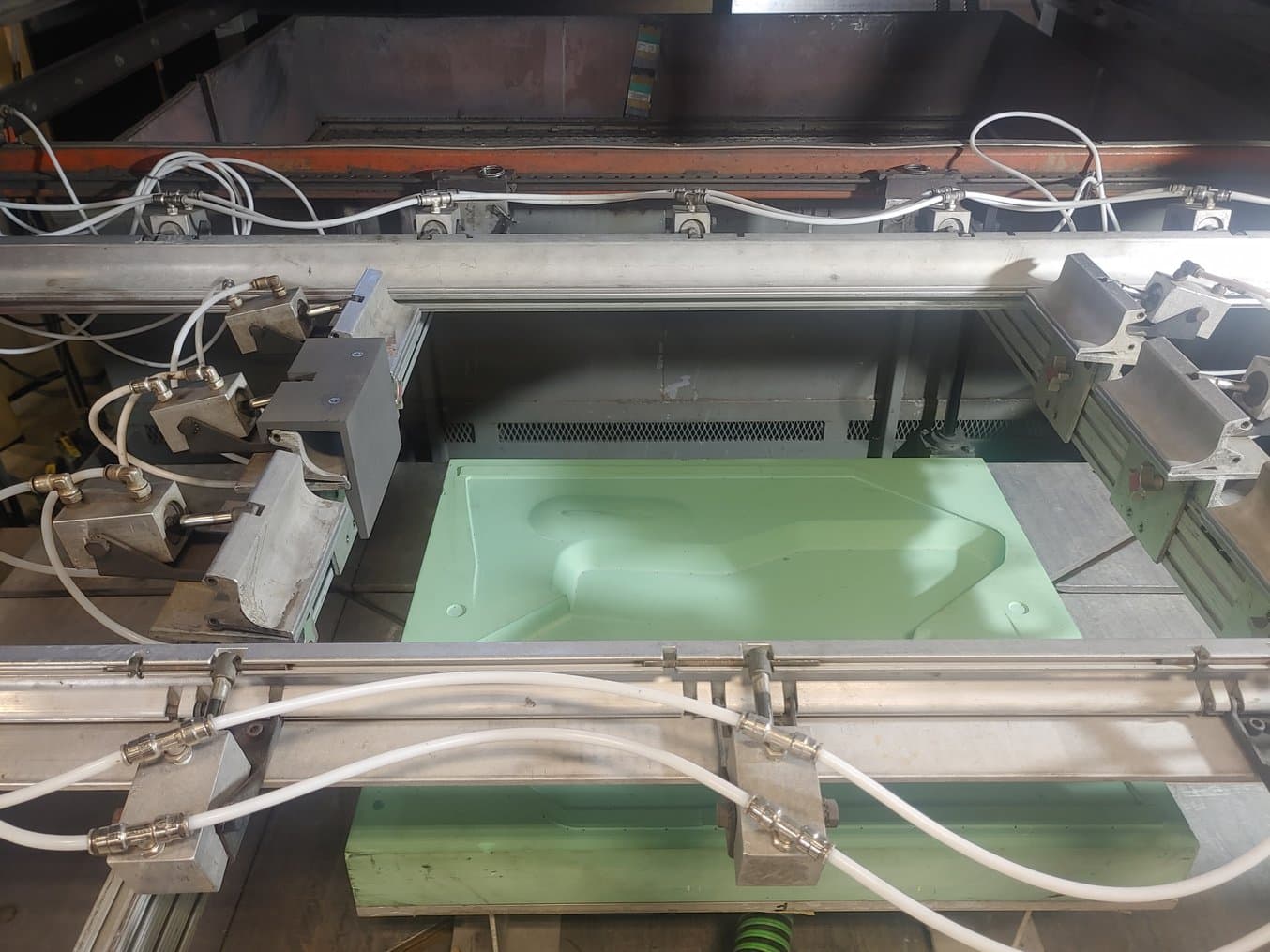
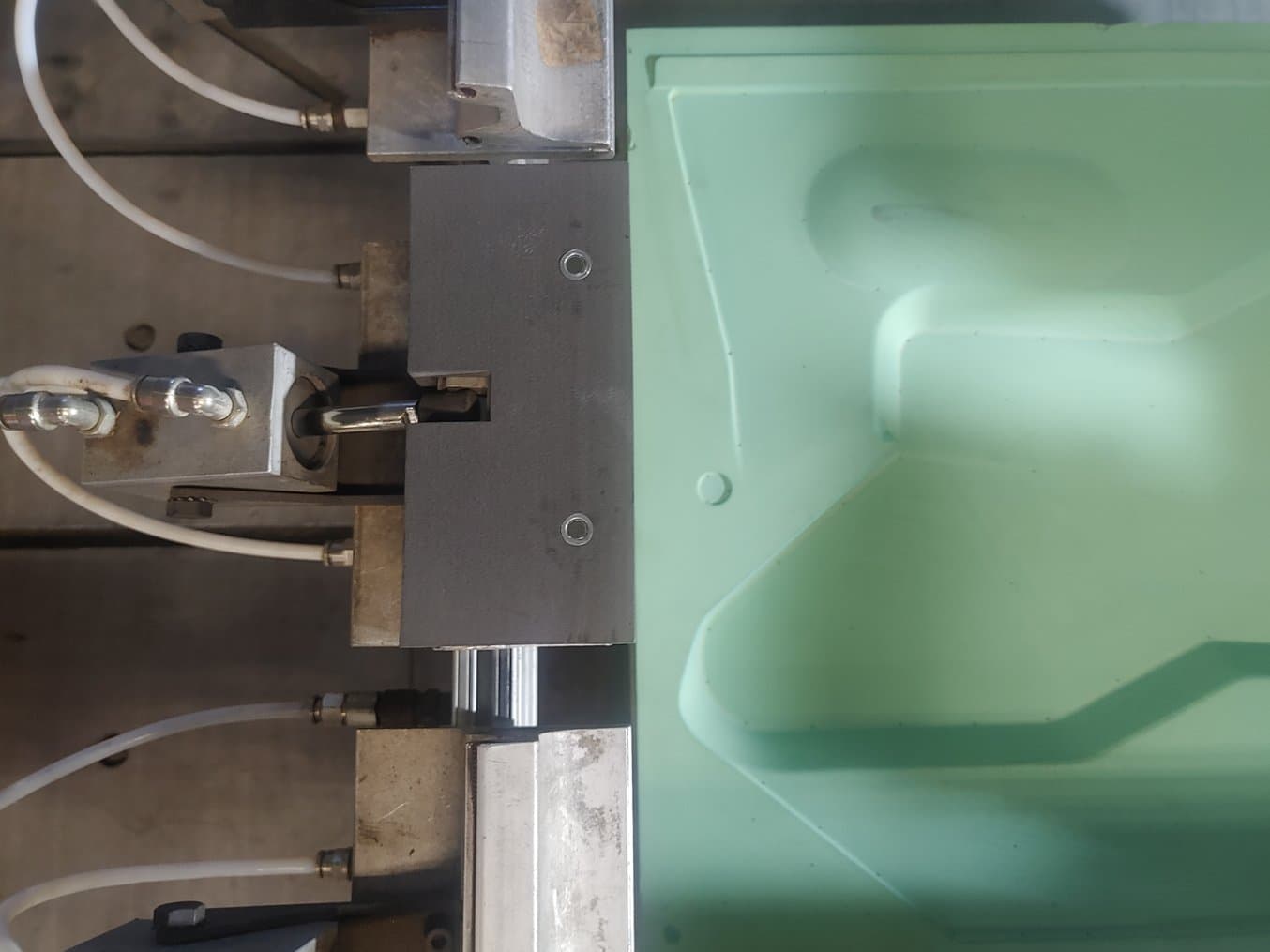
Die Spannvorrichtung (hellgraues Teil) sorgt für einen korrekten Abstand zwischen dem Formwerkzeug (hellgrün) und dem Spannrahmen (Metallstruktur).
Eine größere Platte wäre schwerer und würde höhere Stückkosten und mehr Abfall verursachen. Maßgefertigte Klemmen von einem externen Anbieter zerspanen zu lassen hätte hingegen die Durchlaufzeit um zwei oder drei Wochen verlängert. Der betriebsinterne 3D-Druck einer maßgefertigten Spannvorrichtung jedoch machte es dem Team möglich, eine Halbzeugplatte in der optimalen Größe zu nutzen, Kosten zu sparen und Abfälle zu minimieren, während Produktionsverzögerungen gleichzeitig vermieden wurden.
"Wenn wir Halbzeuge in ganz bestimmten Formaten nutzen können, spart das auch für den Kunden Kosten. Durch 3D-Druck lassen sich die Abstände durch maßgefertigte Klemmen genau anpassen, sodass man sehr differenziert vorgehen kann. Wir haben einen Tag benötigt, um zu drucken und mit der Produktion zu starten."
Kyle Davidson
Ersatzteile, die den Betrieb am Laufen halten
Bei einer solchen Vielzahl an Kunden und Aufträgen, die allesamt fristgemäß erledigt werden wollen, darf die Produktion für nichts und niemanden zum Stillstand kommen. Es sei denn natürlich, es geht dabei um die Thermoformmaschine selbst. Als das Pumplaufrad einer der Maschinen kaputtging, stand dem Unternehmen bis zum Erhalt eines Ersatzteils eine Lieferzeit von sechs bis acht Wochen bevor. „Wenn man als Thermoformunternehmen keine Vakuumpumpe hat, dann kann man nicht thermoformen. Wir können nicht eine ganze Fertigungszelle sechs Wochen lang stillstehen lassen – also brauchten wir eine Zwischenlösung“, so Davidson.
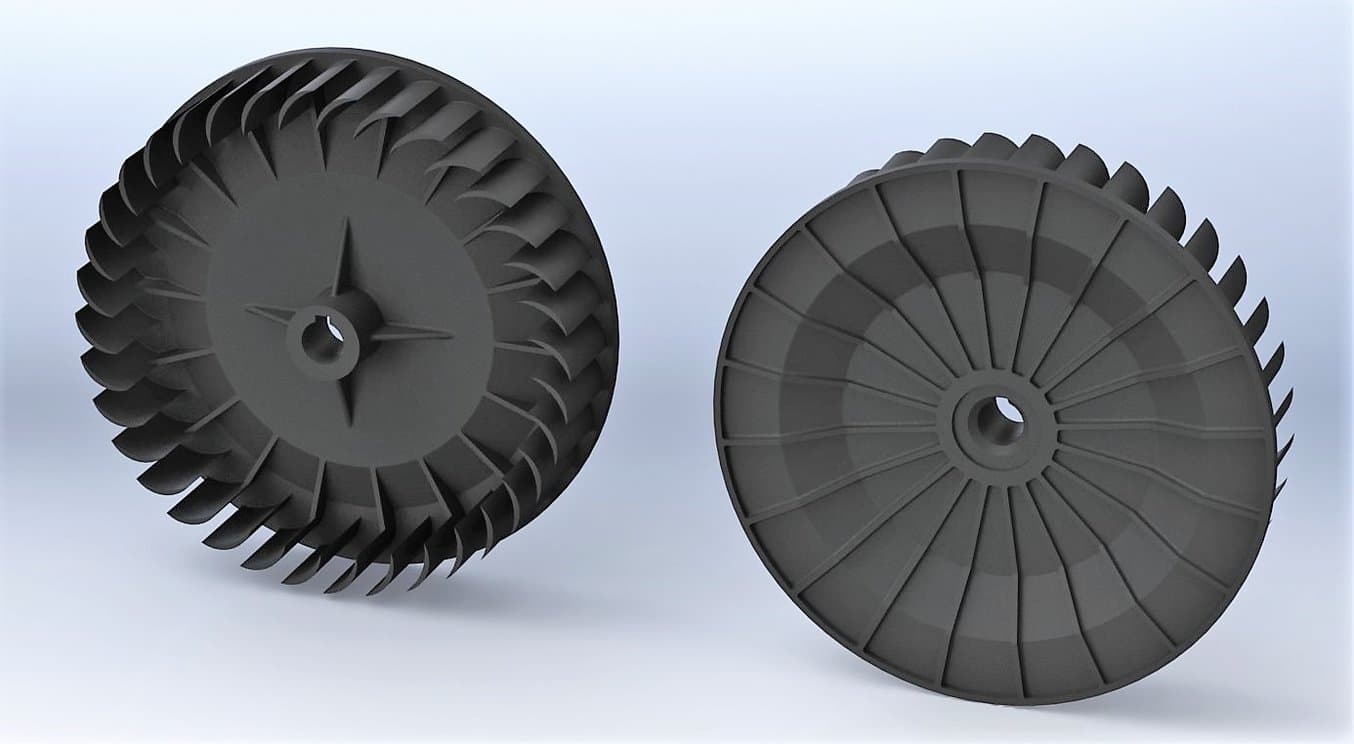
Die 3D-Datei des Laufrads in Solidworks. Beide Seiten weisen Negativ- und Positivbereiche sowie eine Mittelbohrung auf, weshalb Technologien wie FDM und SLA, die Stützstrukturen erfordern, nicht infrage kommen.
In Solidworks entwarf das Team zwei Iterationen des Ersatz-Laufrads und druckte diese über Nacht auf dem SLS-3D-Drucker Fuse 1 aus Nylon 12 Powder. Das Laufrad funktionierte auf Anhieb, passte genau in die bestehende Vakuumpumpe und brachte die Fertigungszelle somit wieder in Gang. Da beim SLS-3D-Druck keine Stützstrukturen erforderlich sind, konnte ein zweiseitiges Design mit einer Mittelbohrung umgesetzt werden – ohne das Entfernen oder Nachbearbeiten von Stützstrukturen war das Laufrad sofort bereit, um in die Maschine eingesetzt zu werden.
"Das Warten auf ein Ersatzteil hätte eine ganze Fertigungszelle wochenlang lahmgelegt. Das hätte einen Verlust von etwa 30 000 $ bedeutet, also hat sich der Drucker durch dieses eine Ersatzteil als Zwischenlösung praktisch sofort bezahlt gemacht."
Kyle Davidson
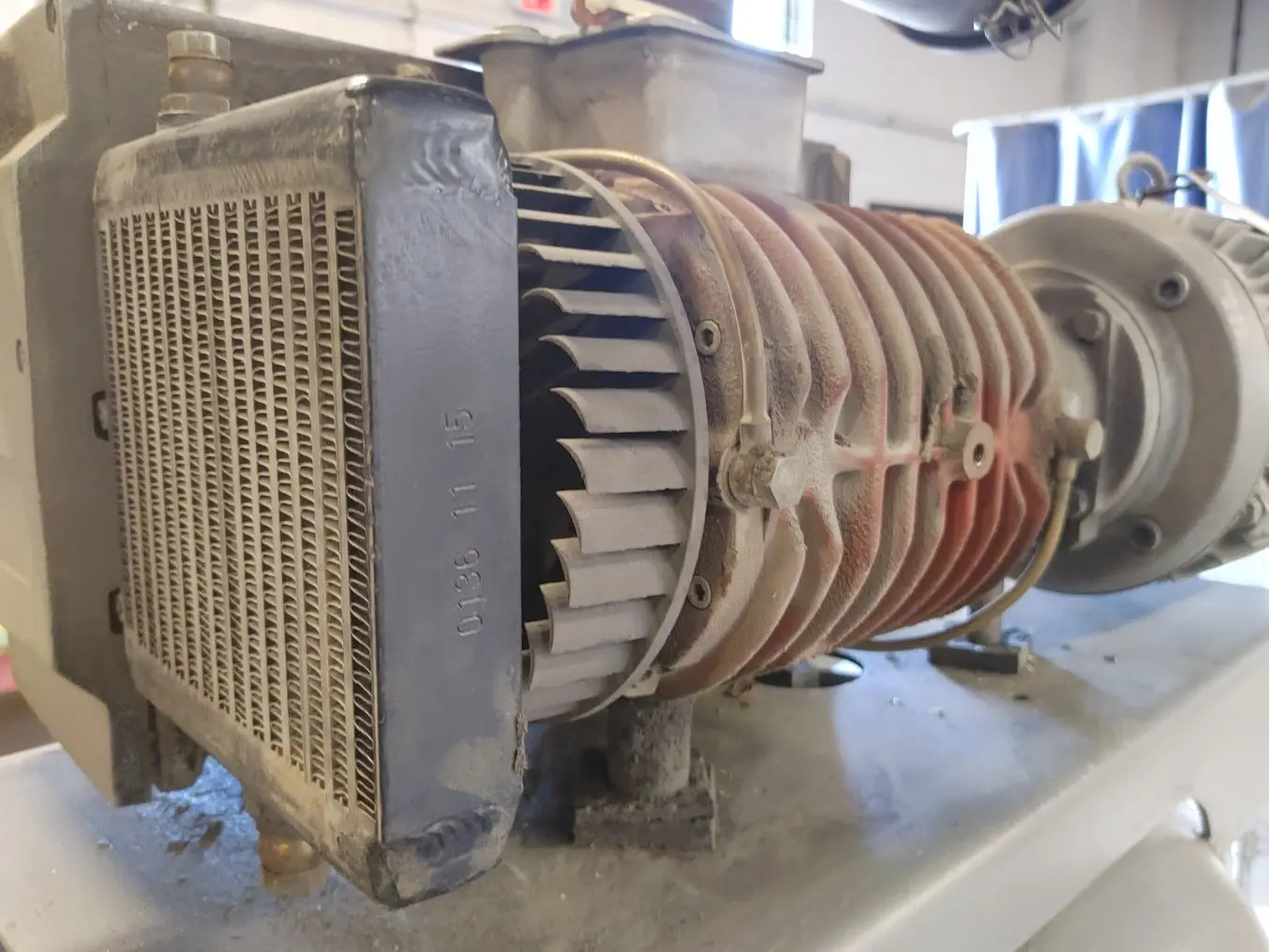
Eine Nahaufnahme (rechts) und eine Gesamtansicht (links) des 3D-gedruckten Laufrads, das sich nahtlos in die Vakuumpumpe der industriellen Thermoformmaschine einfügt.
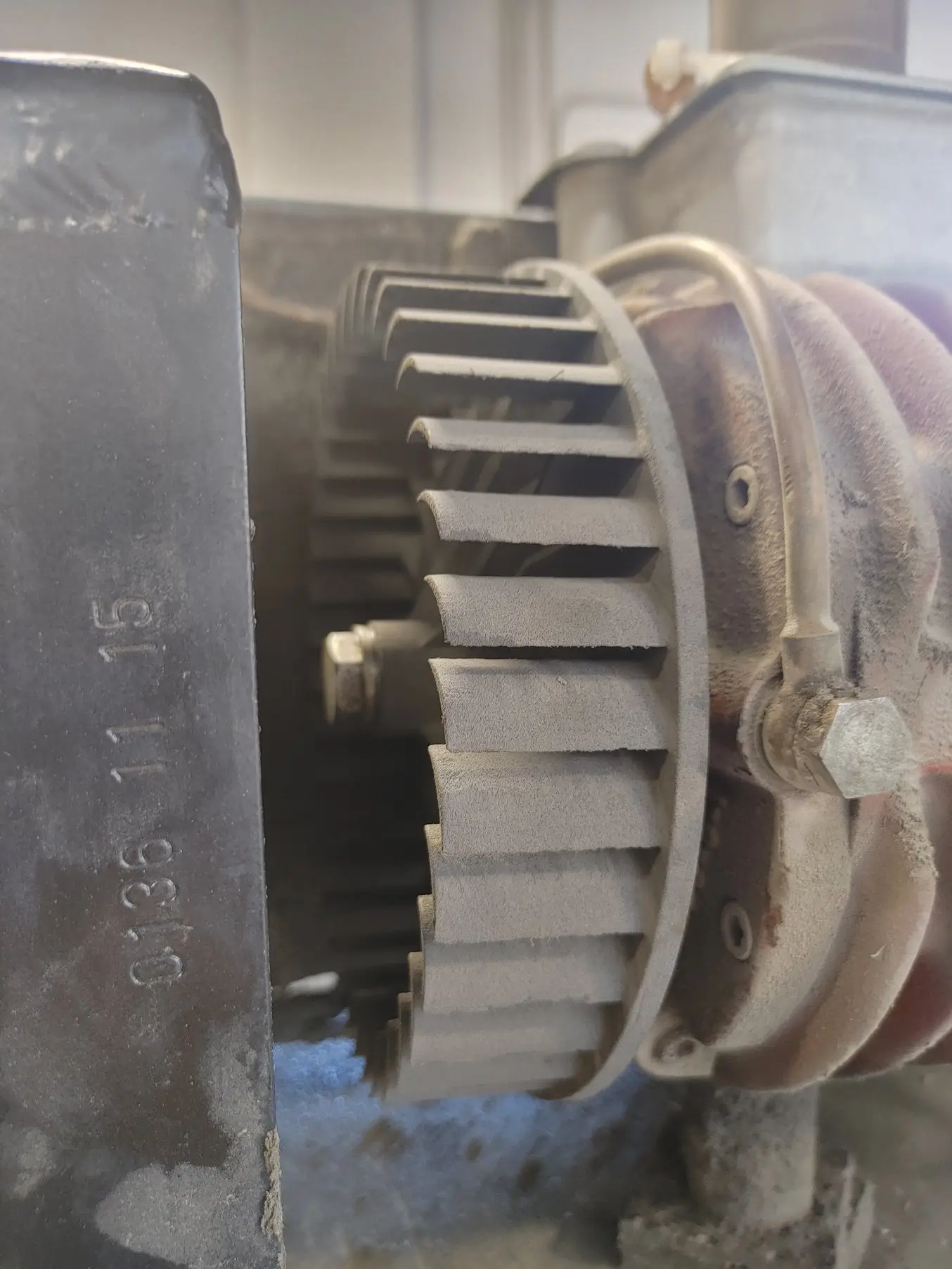
Auch gesparte Sekunden läppern sich
Nach dem Thermoformen durchlaufen die Formteile oft noch sekundäre Arbeitsschritte wie Montage oder Nachbearbeitung. Für diese Vorgänge ist spezielles Werkzeug notwendig, sowie Bearbeitungsschritte wie das Maskieren mit Klebeband vor dem Lackieren. Beim vorliegenden Teil deckte das Team eine mit Kupfer bearbeitete Oberfläche mit Kreppband ab und schnitt die Maskierung bis zum Ende der kupferbeschichteten Fläche zu, damit der Rest des Teils mit Farbe lackiert werden konnte. Dieser Zuschnitt wurde nach Augenmaß vorgenommen, sodass es häufig zu Fehlern, Kratzern auf dem Kupfer und Neuversuchen kam. Mit nur einer oder zwei 3D-gedruckten Vorlagen kann das Team die Abdeckung nun hingegen schnell und effizient zuschneiden.
„Auch wenn es uns nur 10 bis 15 Sekunden Zeit pro Teil spart, summiert sich das im gesamten Lebenszyklus des Produkts zu einer signifikanten Kostenersparnis“, erklärt Johnson. „Zuvor haben wir hierfür von Hand Holz zerspant, aber das war aufwendig und zeitraubend. Das 3D-gedruckte Teil kostet ein paar Dollar und es lässt sich leicht mit einer Hand ausführen.“
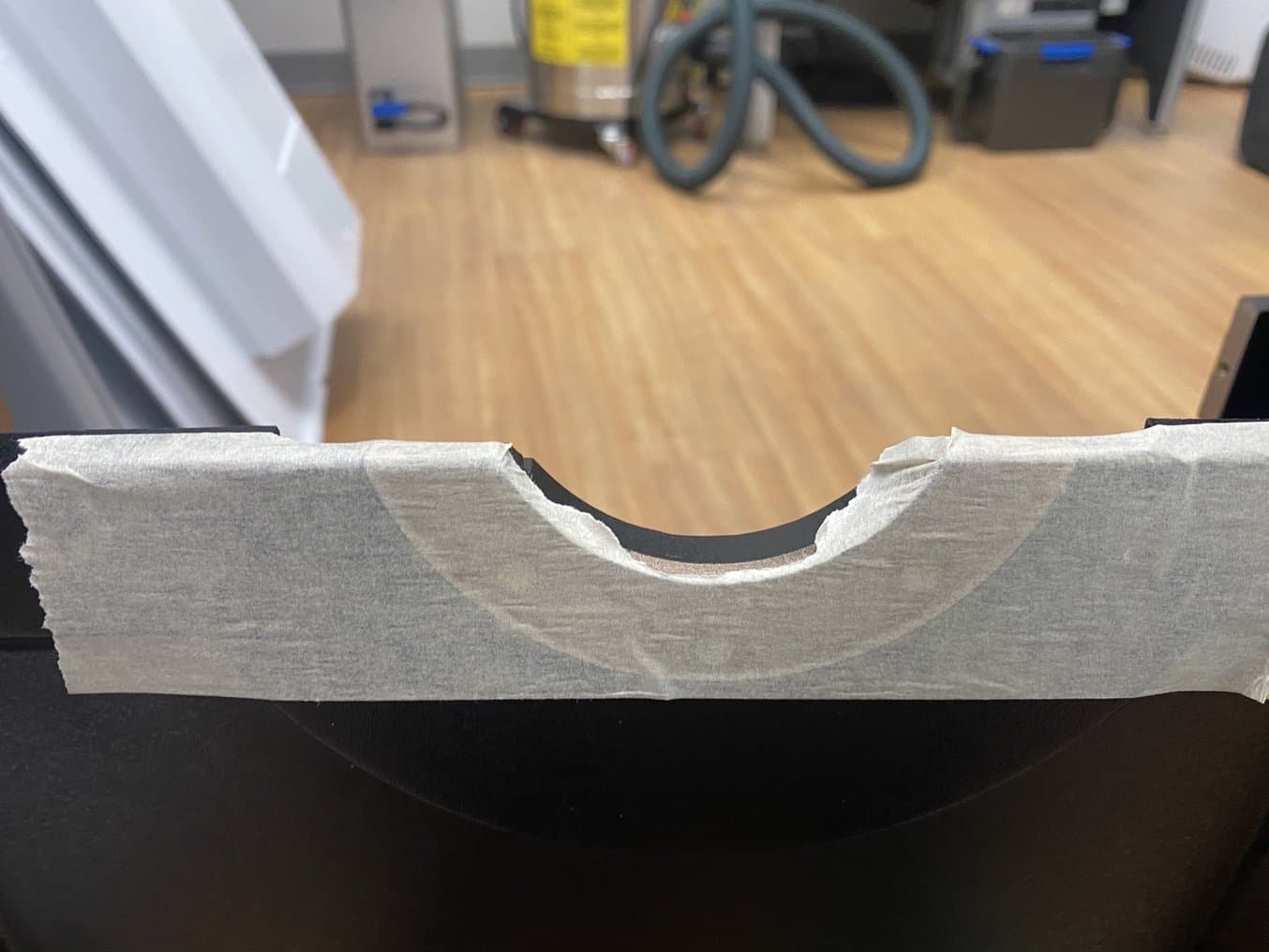
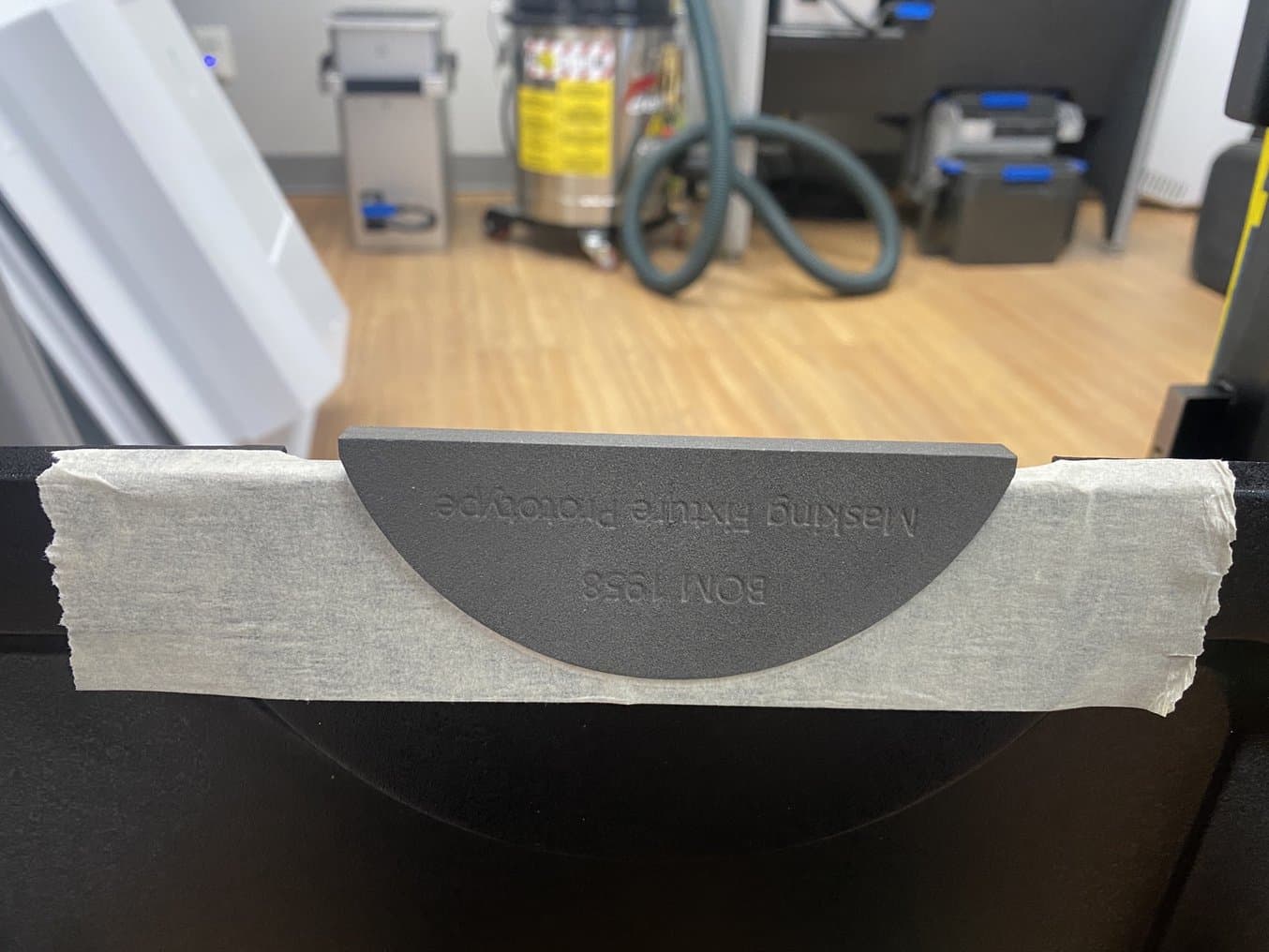
Im ersten Schritt werden große Bereiche des Teils mit Klebeband bedeckt. Im zweiten Schritt dient das 3D-Druckteil als Schablone, um die das Team den Rest des Klebebands abschneiden kann, sodass der kupferbeschichtete Teil frei von Lack bleibt, während der Rest schwarz lackiert wird.
Durch bessere Kundenkommunikation Überraschungen vermeiden
Beim Prozessdesign arbeitet Productive Plastics mit seinen Kunden zusammen, um das Teildesign, das Thermoformverfahren und die Blöcke, die in einem sekundären Arbeitsschritt an den Teilen befestigt werden, zu entwickeln. Diese Blöcke, die für die strukturelle Integrität oder Funktionsbaugruppen erforderlich sind, müssen sich perfekt in die thermogeformte Platte einfügen, und weil Hunderte oder Tausende davon benötigt werden, können Fehler teuer werden.
Früher skizzierte das Team eine Zeichnung der Blöcke mit den erforderten Abmessungen und Toleranzen, doch weil sich angewinkelte Oberflächen in zweidimensionalen Abbildungen schwer wiedergeben lassen, hatten die Blöcke oft die falsche Form oder Größe. Die Blöcke wurden unmittelbar vor dem Thermoformprozess geliefert, und wenn Fehler entdeckt wurden, brachte das die ganze Produktion abrupt zum Stillstand. Durch die Möglichkeit der betriebsinternen Fertigung mit dem Fuse 1 ist jedoch sichergestellt, dass jeder Kunde perfekt einheitliche Sets von Blöcken herstellt.
„Wir brauchen Tausende und Abertausende von diesen Blöcken, das heißt, selbst wenn bei einem einfachen Block die Maße nur ein klein bisschen falsch sind, verursacht das eine enorme Verschwendung und wir können das Projekt nicht abschließen. Wenn wir ihnen ein physisches Teil zuschicken, kostet uns das nur ein paar Dollar, aber wir vermeiden, dass Tausende von Teilen falsch produziert werden“, erklärt Johnson.
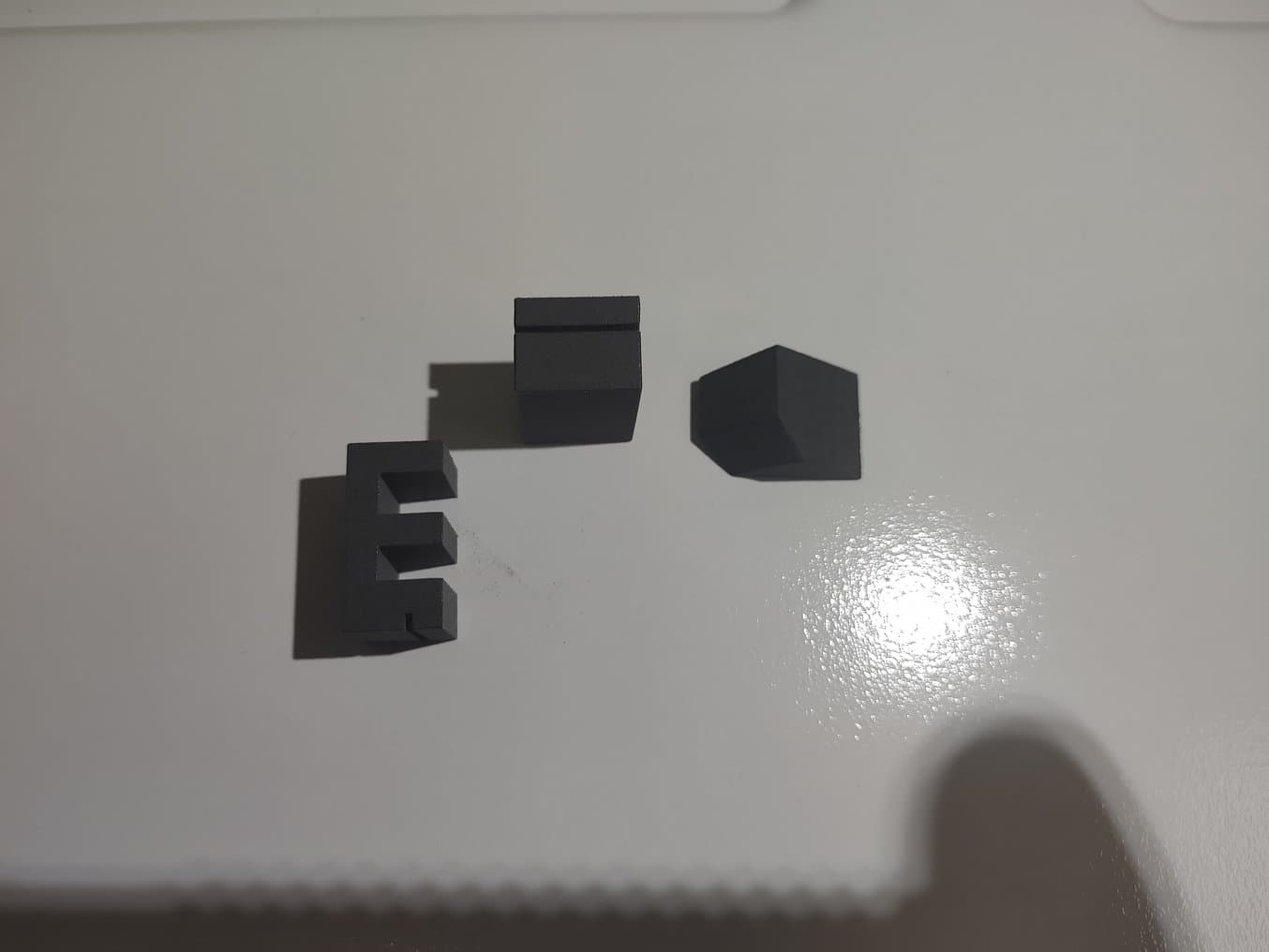
Die 3D-gedruckten, individuell entworfenen Blöcke kommen bei der Montage zum Einsatz, wo die thermogeformten Teile in die funktionale Baugruppe eingebaut werden. Ein falsch bemessener Block kann den ganzen Produktionsplan plötzlich zum Stillstand bringen.
Gesteigerte Effizienz in jeder Zelle
Angesichts der Auftragsmenge, der Vielfalt der Teile und der Anzahl der Schritte im Arbeitsprozess ist bei Productive Plastics ganz schön viel los. Deshalb wirken sich alle Mittel, die die Kommunikation zwischen den Abteilungen vereinfachen, übermäßig positiv auf die Effizienz des Teams aus.
In jeder Fertigungszelle kommt ein Computer-Überwachungssystem zum Einsatz, mit dem Aufträge, Maschinenhandbücher, das Inventar an Fertigungshilfsmitteln sowie Bauteile nachverfolgt werden. Als das Unternehmen dieses Computersystem auf Tablets übertragen wollte, gab es keine einfache Möglichkeit, die Tablets sowohl leicht erreichbar zu platzieren als auch mobil zu nutzen. Die robusten Schutzhüllen der Tablets passten in keine handelsübliche Montagelösung, sodass die Geräte oft auf Regalen oder an unordentlichen Arbeitsstationen liegen gelassen wurden. Johnson ist es gelungen, eine typische Telefonhalterung auseinanderzubauen und mittels Reverse Engineering eine größere Version zu entwerfen, die über die Hülle des Tablets gespannt und sicher auf einer Holzplatte montiert werden konnte.
„Das hat es uns möglich gemacht, das Gerät wenn nötig mobil zu behalten, aber es trotzdem am bestmöglichen Platz für unsere Arbeitskräfte erreichbar zu haben. Im Handel war für unter 300 $ nichts zu finden, aber diese Teile habe ich für 30 $ auf dem Fuse 1 gedruckt und wir haben sie jetzt in jeder Zelle angebracht, und noch ein paar extra“, berichtet Johnson.
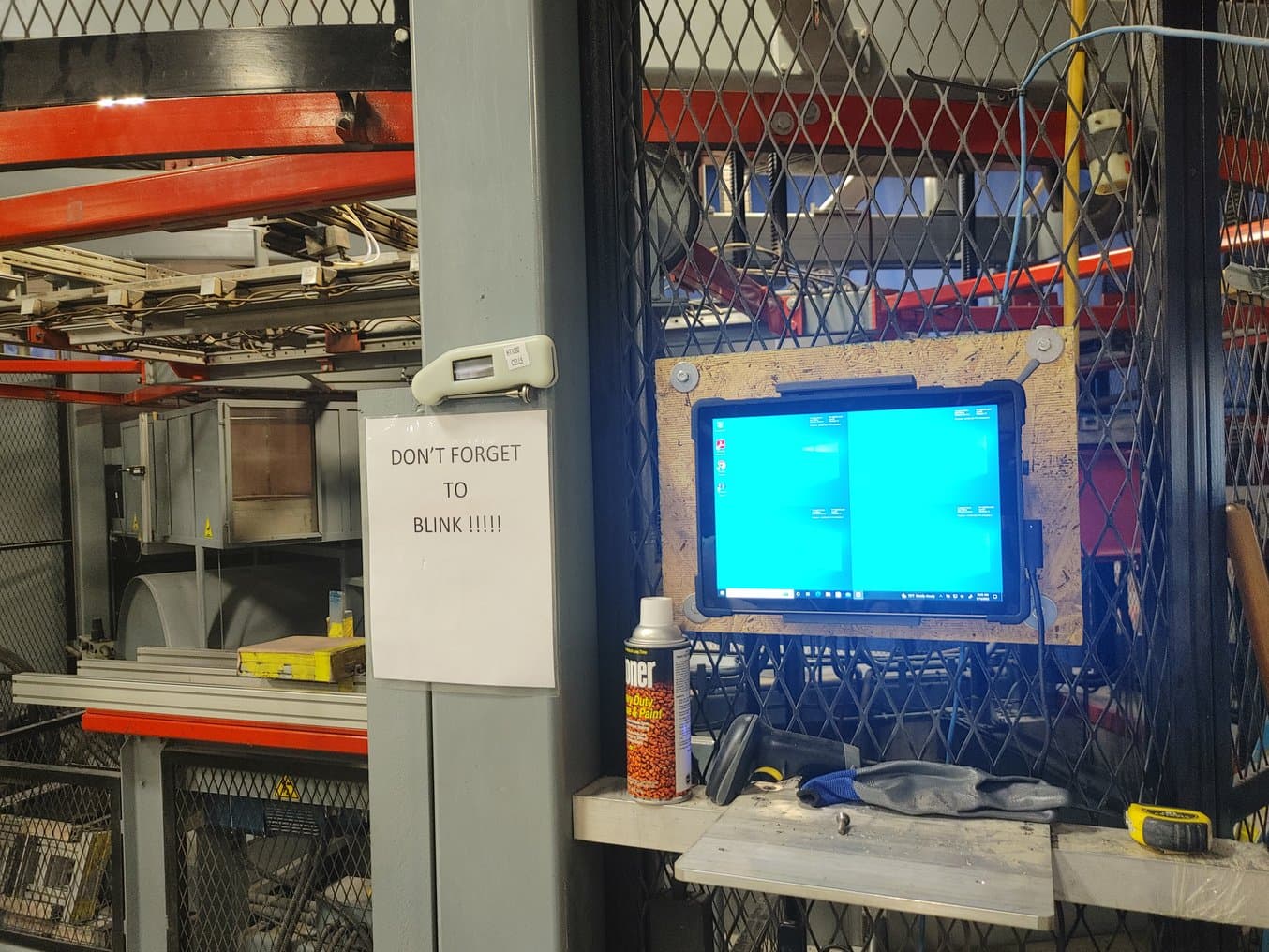
In die individuell entworfene Halterung kann das Tablet leicht eingespannt werden, um an der Wand gut zugänglich zu sein, die Halterung ist aber auch flexibel genug, dass das Tablet leicht entnommen und transportiert werden kann.
Die Produktion auf Touren halten
Nachdem der zugrundeliegende Prozess des Thermoformens abgeschlossen ist, werden je nach Bedarf weitere Arbeitsschritte durchgeführt – dies kann das Befestigen von Blöcken für die Montage, das Zuschneiden des Teils oder sonstige Tätigkeiten umfassen, die das Formteil für den Kunden vorbereiten. Beim Anbringen der Blöcke an die Formteile hält Productive Plastics eine Toleranz von 0,003 Zoll ein. Daher benötigte das Team ein Messverfahren, um sicherzustellen, dass alle Blöcke perfekt aufgesetzt sind.
Zuvor verzichtete das Team entweder gänzlich auf Führungshilfen und führte die Messung nach Augenmaß durch oder es nutzte Holzblöcke, die zusammengeklebt und auf die richtigen Maße zerspant worden waren. Beide Methoden waren aufwendig, langwierig und anfällig für Fehler, die dann ausgebessert werden mussten. Johnson gelang es, eine Positionierhilfe zu entwerfen, die präzise vorgab, wo die Blöcke mit dem thermogeformten Teil zu verbinden waren, sodass die Mitarbeitenden sie in Sekundenschnelle anbringen konnten.
„Wir haben mehrere Sets davon, die alle gleichzeitig verwendet werden, also kann unsere Produktion auf Hochtouren laufen. Die Positionierhilfen haben uns geholfen, die Genauigkeit bei der Platzierung der Blöcke zu steigern und die Zeit einzusparen, die wir vorher für das Schleifen oder Zerspanen der Blöcke benötigt hatten“, so Davidson.
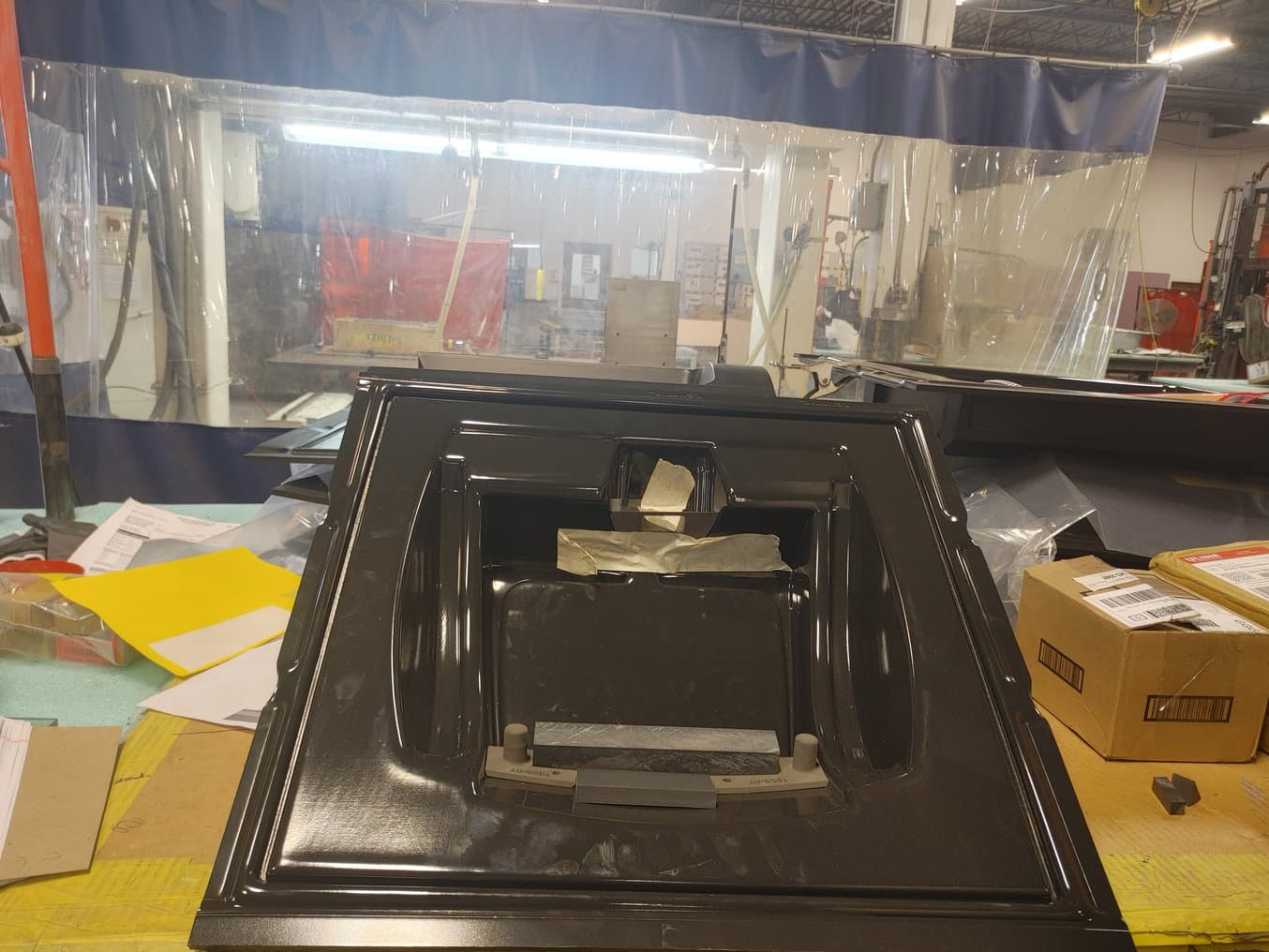
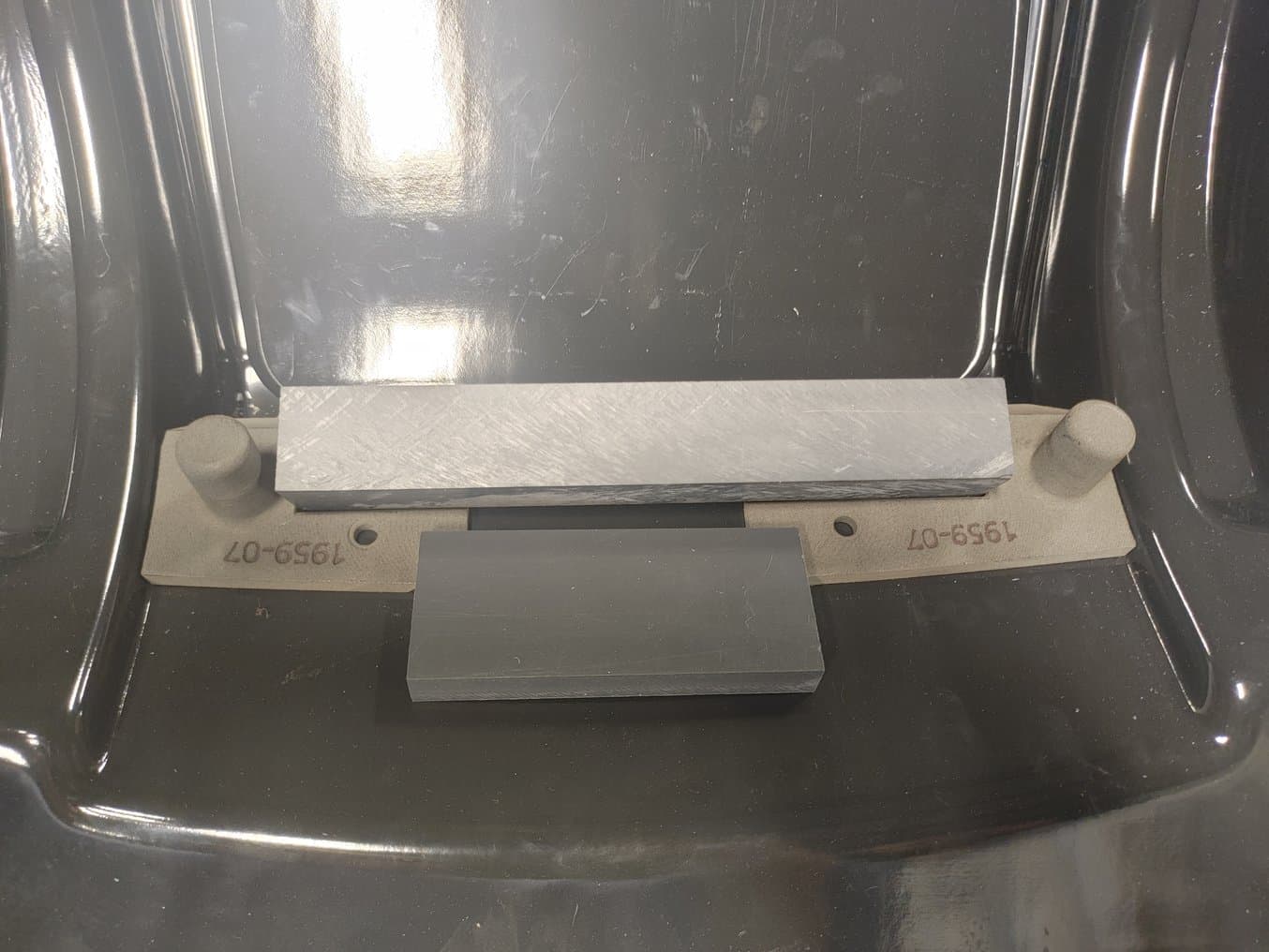
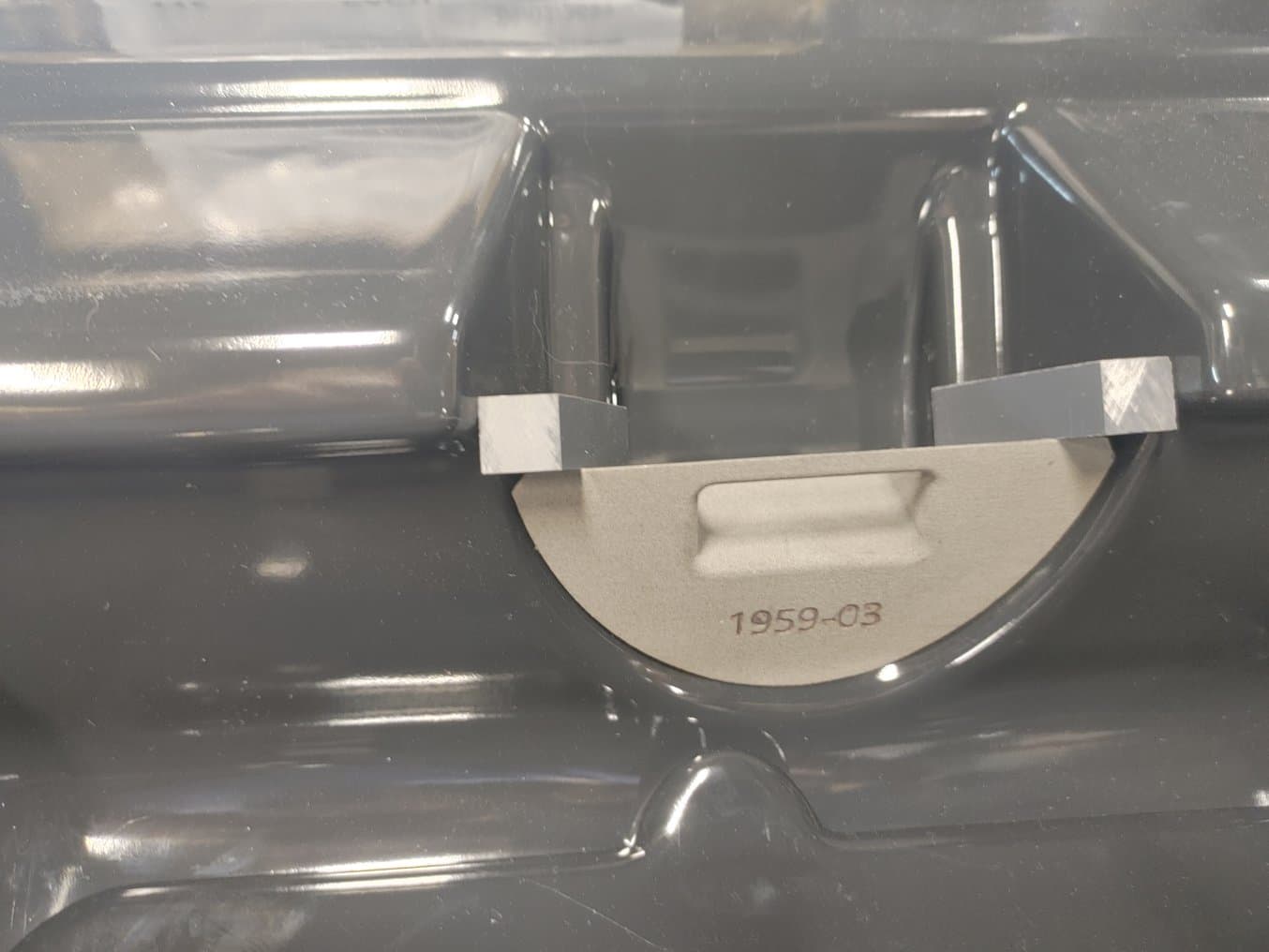
An dieser Schutzblende für Medizinprodukte (schwarzes Formteil, linke Abbildung) müssen zwei Blöcke (langer silberner Quader und kürzerer dunkelgrauer Quader) befestigt werden. Die beiden Positionierhilfen (links und rechts, hellgraue Teile mit Knubbeln) zeigen genau an, wo die Blöcke anzubringen sind, was Zeit spart und eine korrekte Platzierung garantiert.
Alternativen aus Nylon 12 Powder für die Endverwendung
Als Productive Plastics während der Lieferkettenengpässe im vergangenen Jahr Schwierigkeiten hatte, ein bestimmtes kleines Bauteil zu beschaffen, das normalerweise von einem Spritzgussdienstleister geliefert wurde, entschied sich Johnson, es mit dem 3D-Druck dieses Teils zu versuchen. Die Komponente gehört zu einem Gerät, das in medizinischen Einrichtungen eingesetzt wird, um Öffnungen wie etwa Verbindungen zu einem Tropf oder anderen Systemen zur Flüssigkeitsabgabe abzudecken, wenn das Gerät nicht in Gebrauch ist. Mit Nylon 12 Powder und dem Fuse 1 ist es Johnson gelungen, das Spritzgussbauteil perfekt zu replizieren. Für den Einsatz in einer medizinischen Einrichtung wäre zwar noch eine behördliche Genehmigung notwendig, doch das Team konnte dem Kunden mit dem Bauteil eine taugliche Alternative präsentieren, auf die im Falle von Lieferengpässen zurückgegriffen werden kann.
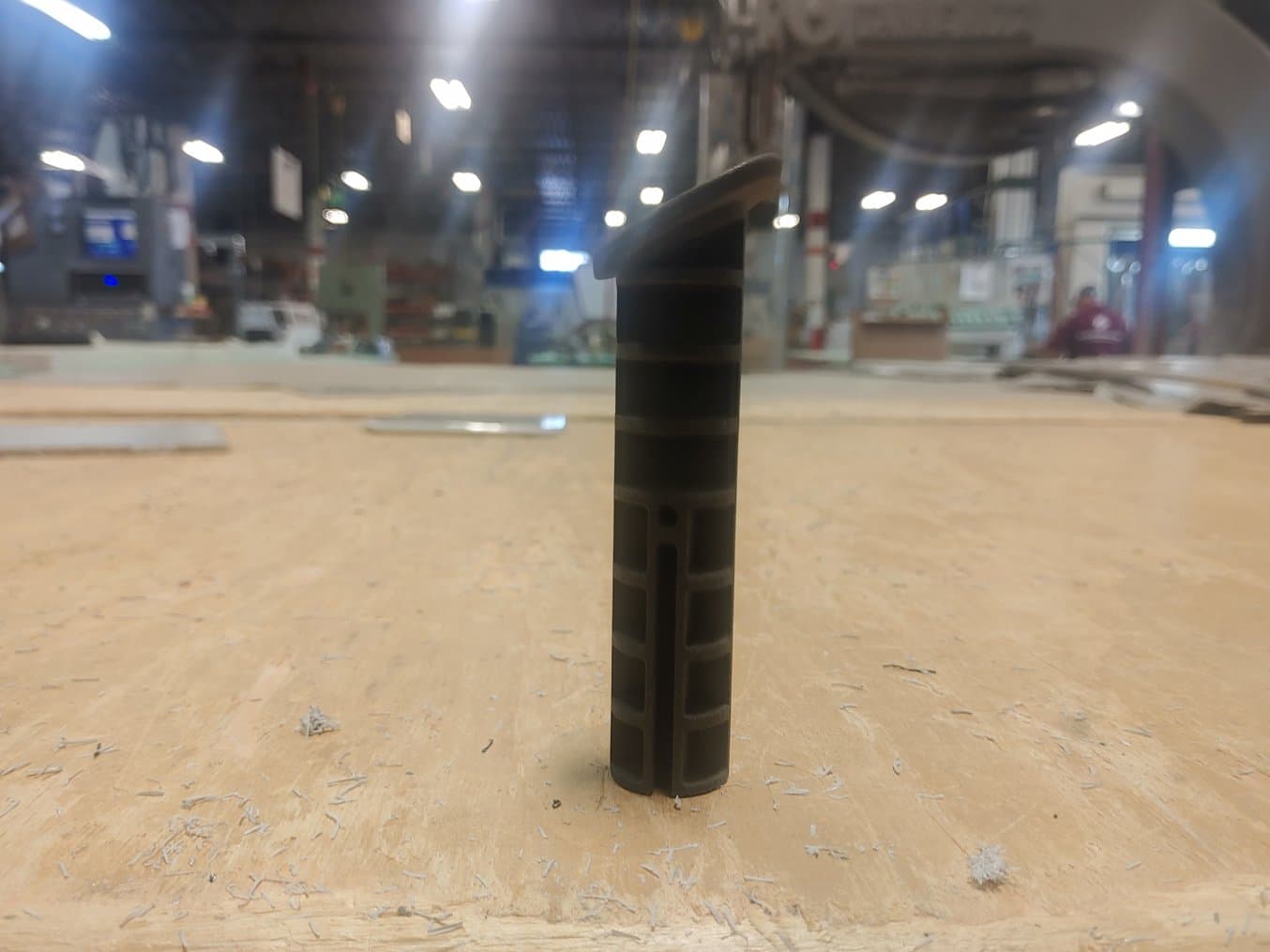
Die auf dem Fuse 1 aus Nylon 12 Powder gedruckte Komponente dient als intern gefertigte Alternative für Spritzgussteile.
Aufbau eines digitalen Inventars von Fertigungshilfen für die Zukunft
Wenn Kundenaufträge in Stückzahlen von Hunderten bis Tausenden gefertigt werden, machen selbst kleinste Details einen großen Unterschied. Kann das Montageteam pro Teil 10 Sekunden einsparen, indem es zur Befestigung von Blöcken eine Positionierhilfe nutzt, oder wird eine Maschine dank 3D-gedruckter Ersatzteile in Betrieb gehalten, dann sind das Verbesserungen, die zu einem effizienteren, optimierten Betrieb beitragen. Mithilfe des Fuse 1 und Nylon 12 Powder kann Johnson nicht nur Probleme beheben, sondern auch proaktiv Abläufe verbessern, bevor es überhaupt zu Problemen kommen kann. Diese Vorteile werden an den Kunden weitergegeben, indem sie die Stückkosten niedrig halten, was zur Kundenzufriedenheit insgesamt beiträgt.
„Die Jungs im Werk kommen manchmal zu mir und sagen ‚Ich habe was kaputt gemacht‘ oder ‚Können wir das hier vereinfachen‘, und dann sende ich das an den Drucker. Das hat mir enorm viel Zeit gespart“, berichtet Johnson. Das Team hat seine Gesamtproduktivität gesteigert, indem es sich schon im Vorhinein um Bereiche seiner Fertigung kümmerte, die durch Engpässe oder Reparaturfälle leicht die Produktion verlangsamen könnten. Obwohl der Fuse 1 der erste Drucker des Unternehmens war, hat er dem Team bereits neue Wege der Produktion eröffnet.