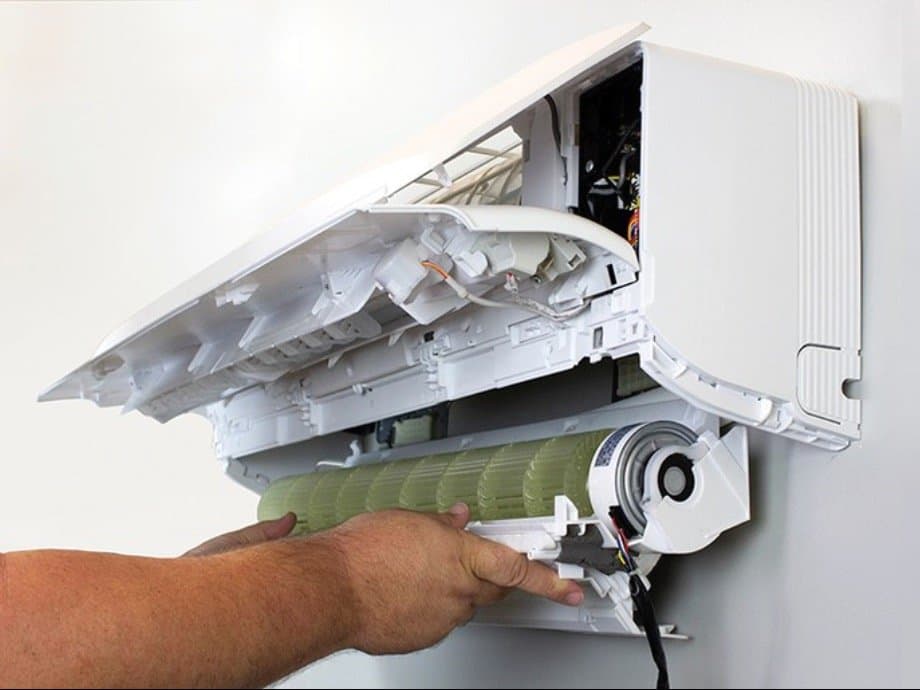
Friedrichs neuentwickelte kanalfreie Lösungen mit FastPro™ – Floating Air Pro® und Floating Air Premier – wurden mit Blick auf HLK-Fachleute und Installateure entwickelt. Fotos mit freundlicher Genehmigung von Friedrich AC.
Jeder, der schon einmal eine schlaflose Sommernacht verbracht und sich nach Erlösung von der Hitze gesehnt hat, weiß, dass eine Klimaanlage die Lebensqualität sofort drastisch verbessern kann. Zumindest, wenn das Gerät der Aufgabe gewachsen ist.
Klimaanlagen sind komplexe Geräte, bei denen die Optimierung des Luftstroms, die Effizienz des Wärmeaustauschs und der Formfaktor in Einklang gebracht werden müssen. Um wettbewerbsfähig zu bleiben und branchenführende Produkte auf den Markt zu bringen, hat Friedrich AC durch die Einführung betriebsinternen 3D-Drucks seinen gesamten Designprozess optimiert. Das Team hat eine Hightech-Prototyping-Anlage rund um den großformatigen Kunstharz-3D-Drucker Form 3L von Formlabs aufgebaut und so noch bessere Produkte geschaffen und gleichzeitig eine Innovationskultur gefördert.
140 Jahre Innovation
Friedrich AC ist seit 1883 im Geschäft, als der Gründer und Erfinder Ed Friedrich in San Antonio, Texas, mit der Entwicklung und Herstellung von Haushaltsgeräten begann. In den letzten 140 Jahren hat sich Friedrich zu einer der führenden Marken für Raumklimageräte entwickelt und dabei seine Fähigkeit unter Beweis gestellt, sich an die wechselnden gesetzlichen Rahmenbedingungen und Marktverhältnisse anzupassen.
Heute verfügt Friedrich in seinem Design- und Entwicklungszentrum, das sich immer noch in San Antonio befindet, über ein hochmodernes UL-Prüflabor. Als Mitglied der Programme UL Client Test Data Program und Intertek Satellite 3 ist das Design- und Entwicklungszentrum eine der wenigen privaten UL-zertifizierten Prüfeinrichtungen in den USA.
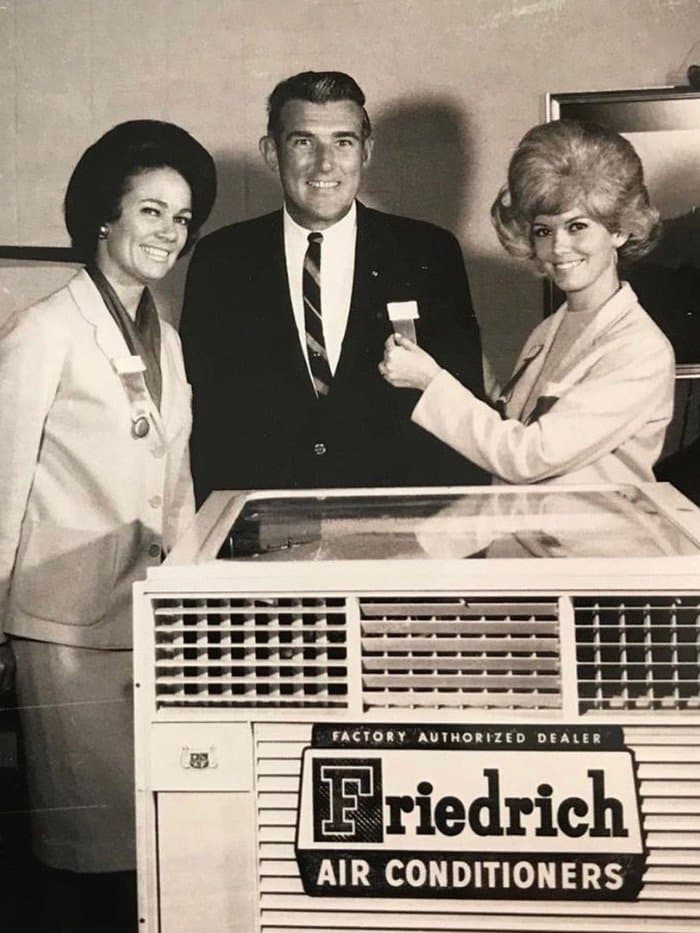
Friedrich AC blickt auf eine lange Geschichte von Innovation und Spitzenleistungen zurück.
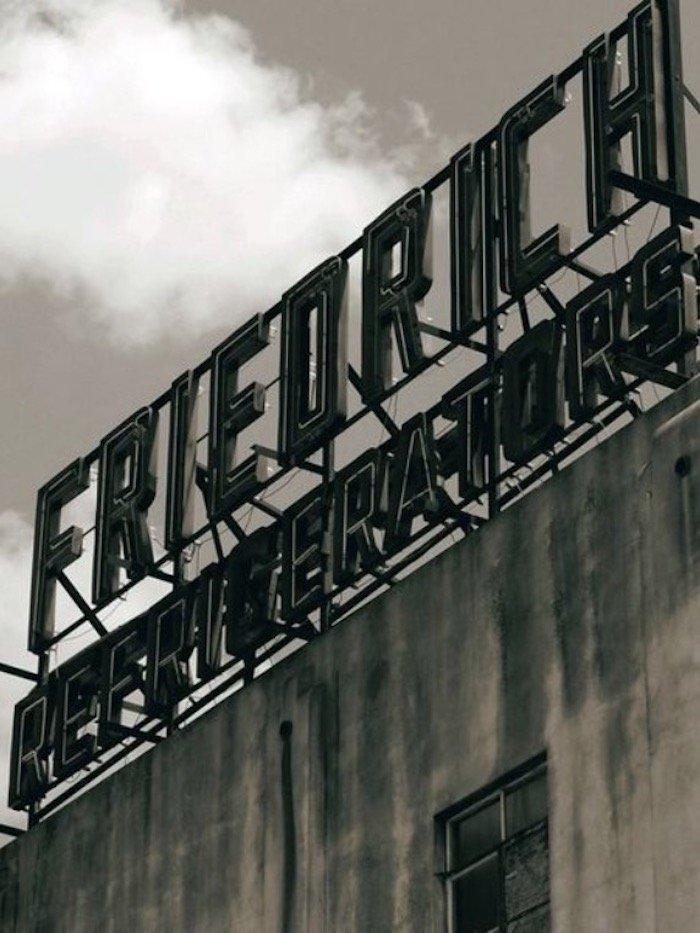
Sein Design- und Entwicklungszentrum ist eine der wenigen privaten UL-zertifizierten Prüfeinrichtungen in den USA.
Keine Kompromisse mehr: Hohe Geschwindigkeit, niedrige Kosten
Im Design- und Entwicklungszentrum arbeitet der Maschinenbauingenieur Noah Trent an der Entwicklung von Kühlsystemen und ist für die Bearbeitung von Anfragen nach 3D-Druckteilen aus dem gesamten Unternehmen zuständig. Das Labor, das als Friedrichs primärer Fertigungsbereich für mehrere Ingenieurteams dient, verfügt über Prozesse für die Blechumformung, das Rohrbiegen, die Montage und die Leistungsprüfung. Bevor das Team den Form 3L in den Betrieb holte, fertigte es in der Regel Prototypen mit vereinfachten Blechteilen oder lagerte dies an externe Anbieter aus. „Wir haben vereinfachte Entwürfe und einfache Geometrien mit Blechen gefertigt und uns für kompliziertere Teile an Fertigungsbetriebe gewandt“, so Trent.
Durch die Blechverarbeitung konnten nur die grundlegendsten Formen im eigenen Haus iteriert werden. Wenn Teile ausgelagert wurden, wurden diese zwar relativ schnell von großen 3D-Druck-Anbietern geliefert, aber der Preis war exorbitant hoch. Manche Produktentwicklungszyklen erforderten bis zu 10 Prototypen desselben Teils, und die Kosten summierten sich. Design Supervisor Emma Flores erinnert sich: „Es war extrem teuer. Wir hätten Teile in China bestellen können, aber es könnte Monate dauern, bis sie ankommen. Beides bekamen wir nicht: einen guten Preis und eine schnelle Lieferung.“
Flores war fest entschlossen, eine Lösung für das Prototyping zu finden, die sowohl schnell als auch kostengünstig sein konnte. Bei der Vorbereitung eines besonders aufwändigen Design-Sprints begann das Team, die Investitionsrendite eines eigenen hochwertigen 3D-Druckers zu bewerten. „Wir haben uns für den Form 3L entschieden, weil er über den Wash L und Cure L verfügt, einen guten Preis, eine gute Größe, hohe Qualität und den Support von Formlabs bietet“, sagt Flores.
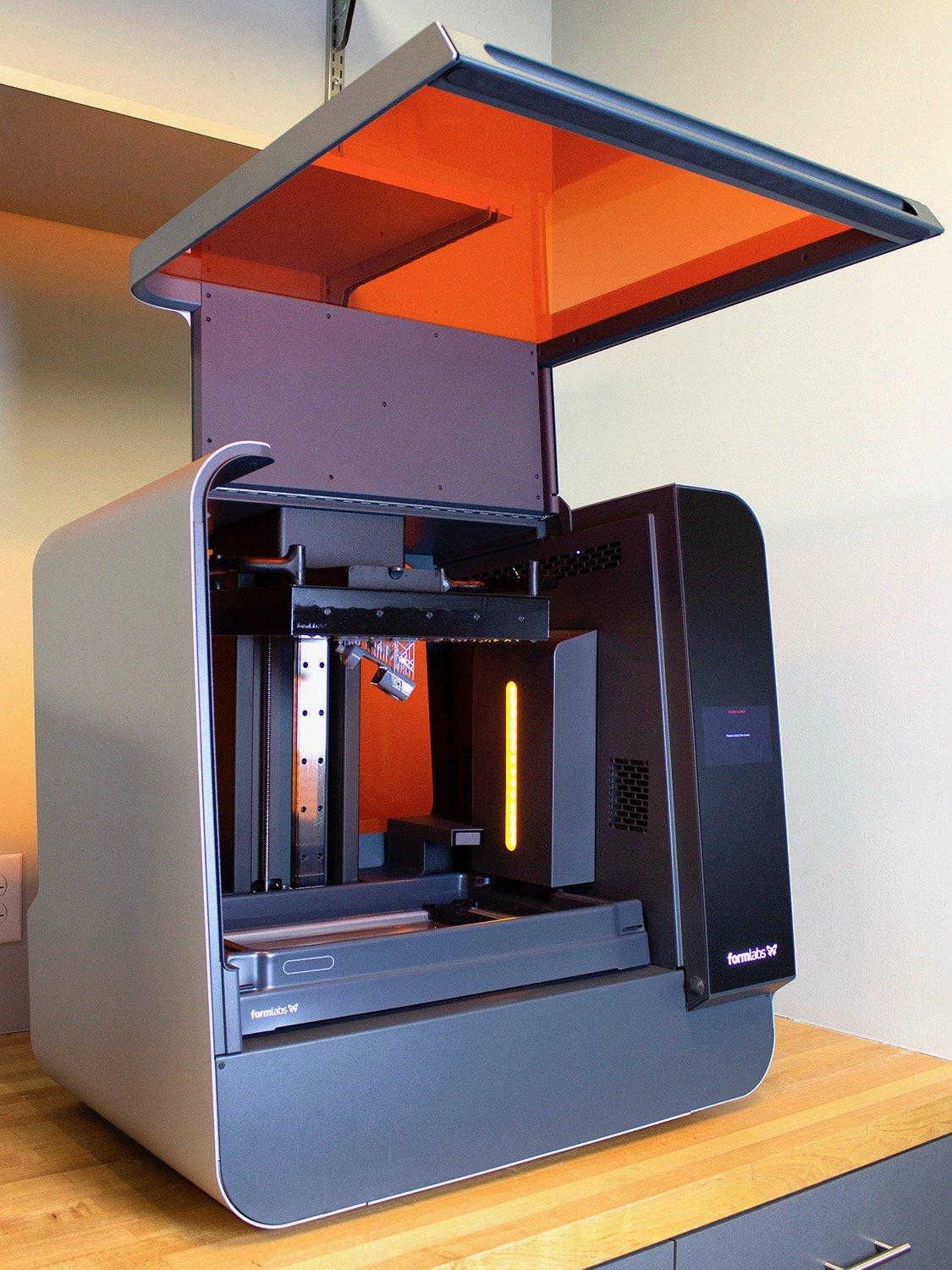
Der Form 3L erweitert die Möglichkeiten des Teams zur schnellen Herstellung von Prototypen großer Teile.
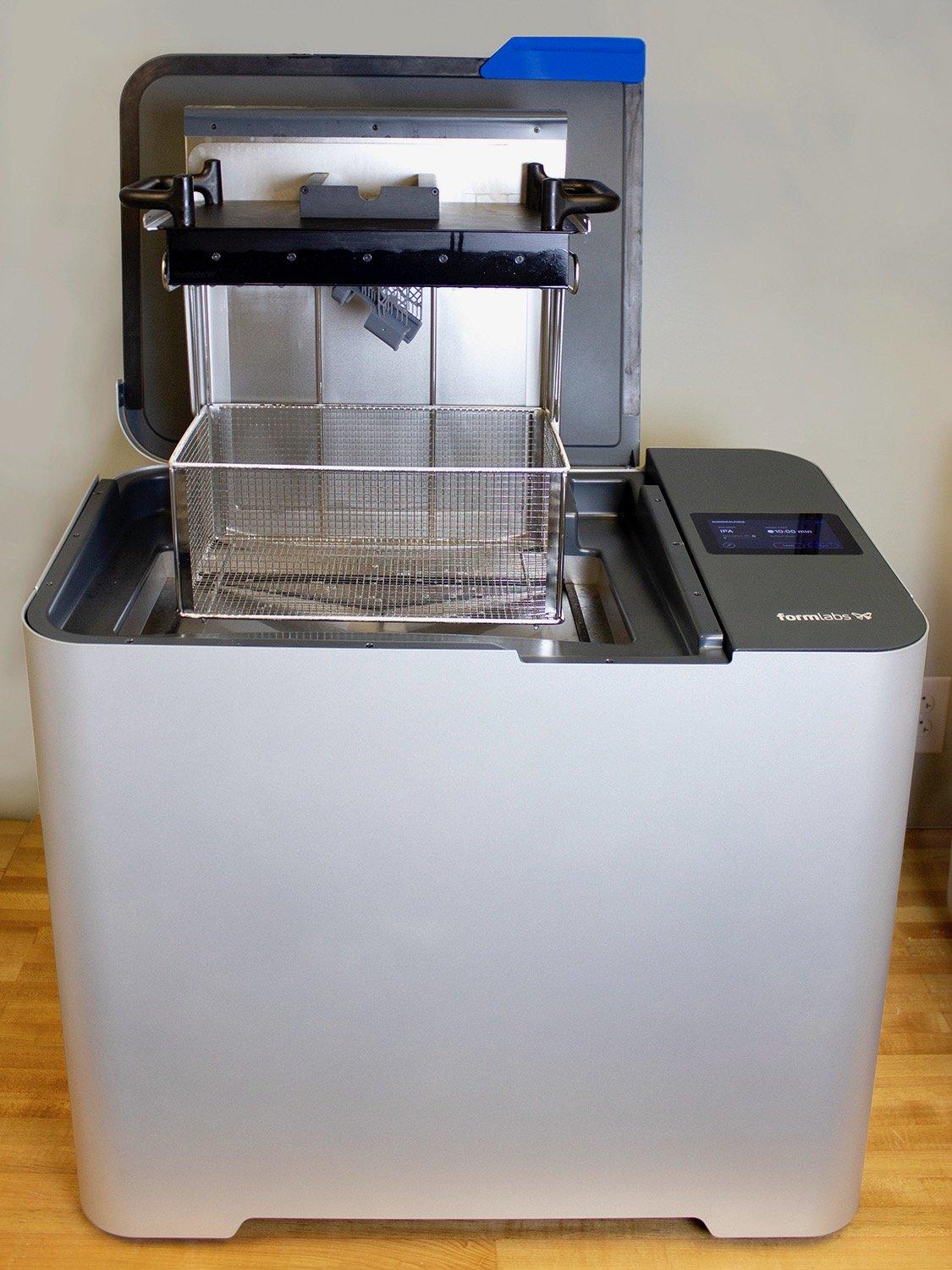
Der Form Wash L rationalisiert den gesamten Workflow für den großformatigen Kunstharzdruck.
Aufbau eines internen Zentrums für additive Fertigung
Seit der Integration des Form 3L in den Arbeitsablauf des Design Development Centers haben Trent und Flores ein organisches System für interne Anfragen von den verschiedenen Einrichtungen und Arbeitsgruppen von Friedrich eingeführt, wie etwa Elektrotechnik, Industriedesign und Maschinenbau. „Wann immer jemand von unseren Standorten in San Antonio oder Monterrey, Mexiko, einen Bedarf hat, schicken sie eine Anfrage an Noah – er ist der Experte geworden“, so Flores.
Die meisten Anfragen, die bei Trent eingehen, betreffen Prototypen von Kunststoffteilen wie Lüfter, Schutzblenden, Gehäuse, Knöpfe oder Paneele. Das Design dieser Teile kann von einer Designiteration zur nächsten verbessert werden, um die Passform, die Haptik und die Funktion kontinuierlich zu verbessern. Zusätzlich zu den Anfragen nach Prototypen von Kunststoffteilen bearbeitet das Team auch einige Anfragen nach Fertigungshilfsmitteln, wie z. B. den Prototyp eines Sondengehäuses, das später in der Fertigungslinie eingesetzt werden soll.
„Jeder arbeitet an drei oder vier verschiedenen Projekten zugleich. Einmal war der Drucker einen Monat lang fast 24 Stunden am Tag in Betrieb. Er ist ständig in Gebrauch. Wann immer man den Raum betritt, sieht man ihn mit höchster Wahrscheinlichkeit drucken“, so Trent.
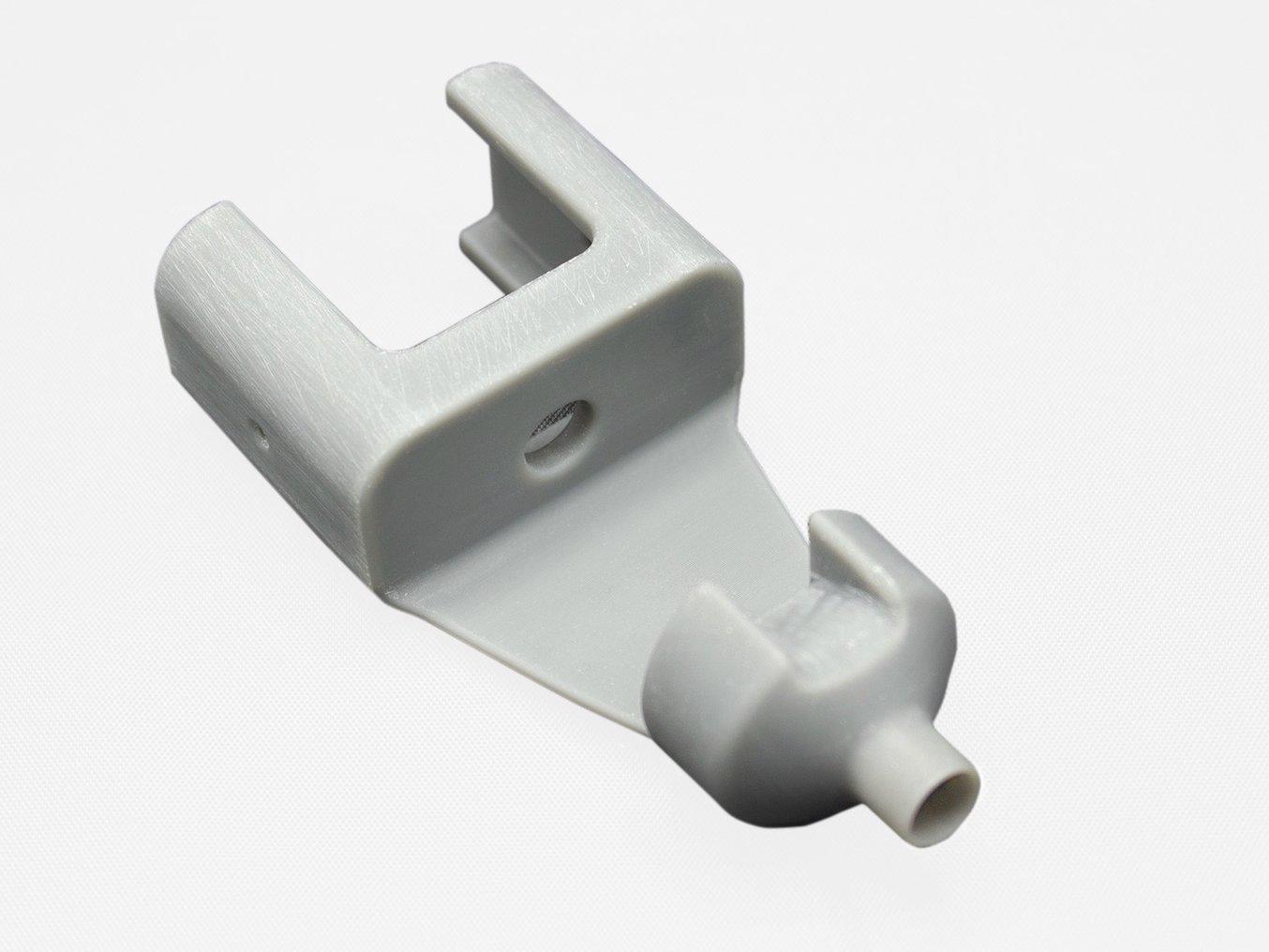
Dieses Sondengehäuse, gedruckt aus Rigid 10K Resin auf dem Form 3L, wurde als Prototyp für die Verwendung in einem internen Prozess in der Fertigungslinie entwickelt.
3D-Druck für Leistung, Herstellbarkeit und Wartungsfreundlichkeit
Bei der Konstruktion einer Klimaanlage müssen zahlreiche Aspekte berücksichtigt werden, um eine gute Leistung zu gewährleisten. Einer von vielen wichtigen Gesichtspunkten ist der Luftstrom. „Wir entwickeln in erster Linie leistungsorientiert. Einer der wichtigsten Punkte bei der Konstruktion von Klimaanlagen ist, dass genügend Luft durchströmen kann. Wir verbringen viel Zeit damit, Geometrien zu entwickeln, die den Luftstrom verbessern“, erklärt Trent. Dank des großen Fertigungsvolumens des Form 3L und der glatten Oberflächen, die das LFS-Druckverfahren (Low-Force Stereolithography) erzeugt, kann das Team Prototypen im Maßstab 1:1 nach genauen Spezifikationen für maximale Kühleffizienz testen.
Der 3D-Druck kann zwar hinsichtlich Geometrie neue Möglichkeiten eröffnen, das ist aber noch längst nicht alles. Da die Bauteile letztendlich spritzgegossen werden, müssen die Komponenten auch für die Fertigung ausgelegt sein. „Wir müssen 3D-gedruckte Prototypen entwerfen, die dann im Spritzgussverfahren in großen Mengen hergestellt werden können. Wir nähern die 3D-gedruckten Teile so nah wie möglich an das spätere Spritzgussmaterial an. Dann testen wir sie. Manchmal testen wir im Windkanal, manchmal geht es um die Passform und manchmal um die Kraft“, erläutert Trent. Das Team von Friedrich AC verwendet die Standard-Kunstharze wegen ihrer glatten Oberfläche und hohen Maßgenauigkeit und Tough 2000 Resin wegen seiner Stärke und Haltbarkeit.
Neben optimaler Leistung und Herstellbarkeit muss das Team auch sicherstellen, dass die Geräte leicht zu warten sind, sei es durch den Eigentümer oder einen HLK-Techniker. „Diese Geräte sind von hoher Qualität und auf Langlebigkeit ausgelegt. Sie müssen sich leicht montieren und demontieren lassen und für die Wartung gut zugänglich sein“, sagt Flores.
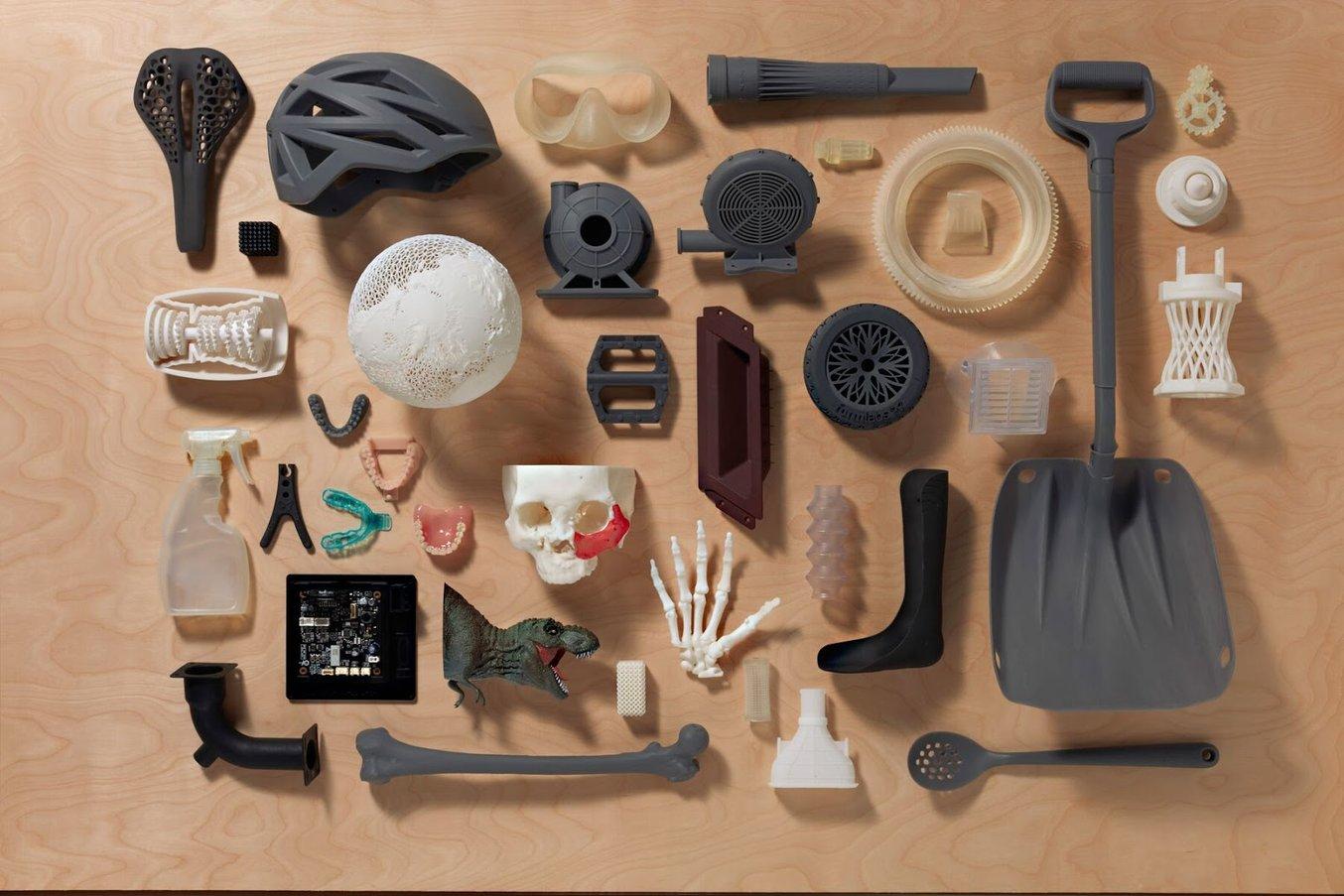
Rapid Prototyping: Finden Sie das richtige Material für Ihre Anwendung
Dieses Tool stellte Trent dem Ingenieurteam zur Verfügung, mit dem er bei Friedrich AC zusammenarbeitet, damit es die Kunstharzpalette nach bestimmten Eigenschaften durchsuchen konnte.
Die Iterationsschleife
Werden bei der Entwicklung Leistung, Herstellbarkeit und Wartungsfreundlichkeit im Blick behalten, dann zählt jede noch so kleine Verbesserung. Um winzige Anpassungen vorzunehmen, verlassen sich Trent, Flores und das Team auf die Präzision und Geschwindigkeit des Form 3L. Sie erhalten häufig Anfragen nach einzelnen Bauteilen, die in vier oder fünf leicht unterschiedlichen Varianten entworfen wurden. Indem Sie das große Bauvolumen des Form 3L ausnutzen, können sie alle Iterationen auf einmal drucken und haben sie am nächsten Tag für Vergleichstests bereit. Mit nur einer Maschine vervierfacht das Team so seine Iterationskapazität, um zu ermitteln, welches Design am besten funktioniert, am einfachsten spritzgegossen werden kann und im Praxiseinsatz gewartet werden kann.
„In was für eine Schleife man mit diesem 3D-Drucker einsteigen kann... Wenn ich eine Idee habe und sie sehen und mehrfach testen will, bevor ich sie abschicke, kann ich das tun. Das ist bei der Herstellung eines qualitativ hochwertigen Produkts so unglaublich wertvoll. Früher haben wir vielleicht ein oder zwei Iterationen durchgeführt, jetzt sind es immer mindestens drei oder vier. Und in diesen zwei letzten Schleifen können noch echte Kunststücke passieren.“
Noah Trent, Maschinenbauingenieur
Eine Kultur der Innovation fördern
Die Verfügbarkeit eines eigenen Druckers mit der Kapazität, funktionale Prototypen herzustellen, hat weitere Teams dazu ermutigt, Neues auszuprobieren. Auch außerhalb des 3D-Druck-Raums und sogar an anderen Standorten erkennen Ingenieur*innen immer mehr Möglichkeiten, nachdem sie Druckteile von Trent und Flores erhalten. „Vor der Anschaffung des Form 3L kam es einigen der Ingenieure gar nicht in den Sinn, einen Prototyp ihrer Ideen zu erstellen, aber jetzt, wo sie das passende Werkzeug haben, denken sie: 'Okay, vielleicht könnten wir das testen'. Sie betrachten die Dinge auf ganz neue Art", meint Flores.
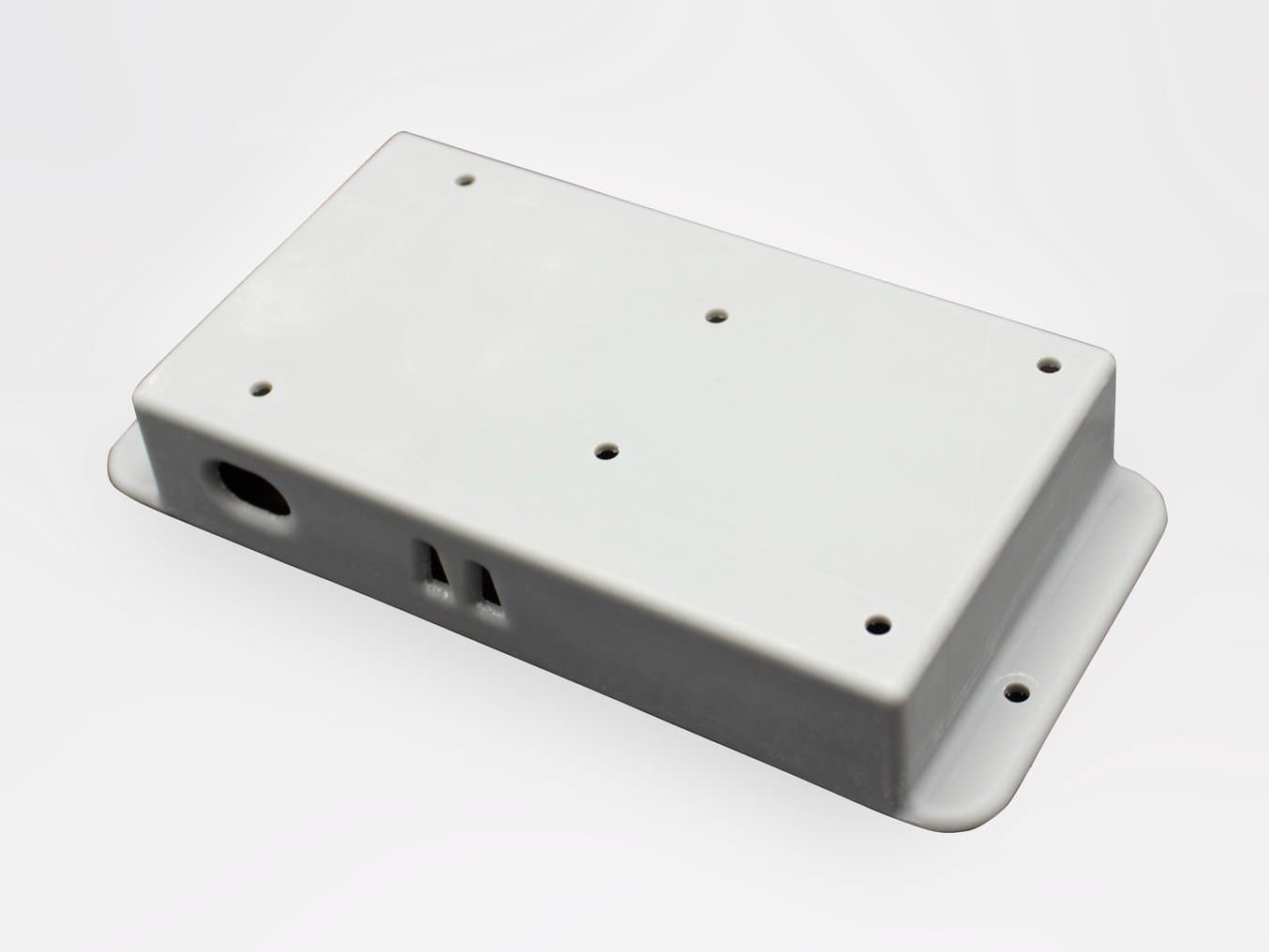
Dieser Deckel für eine Elektronikbox (E-Box), 3D-gedruckt aus Rigid 10K Resin, wurde als Prototyp für eine neue Produktlinie auf dem Form 3L erstellt.
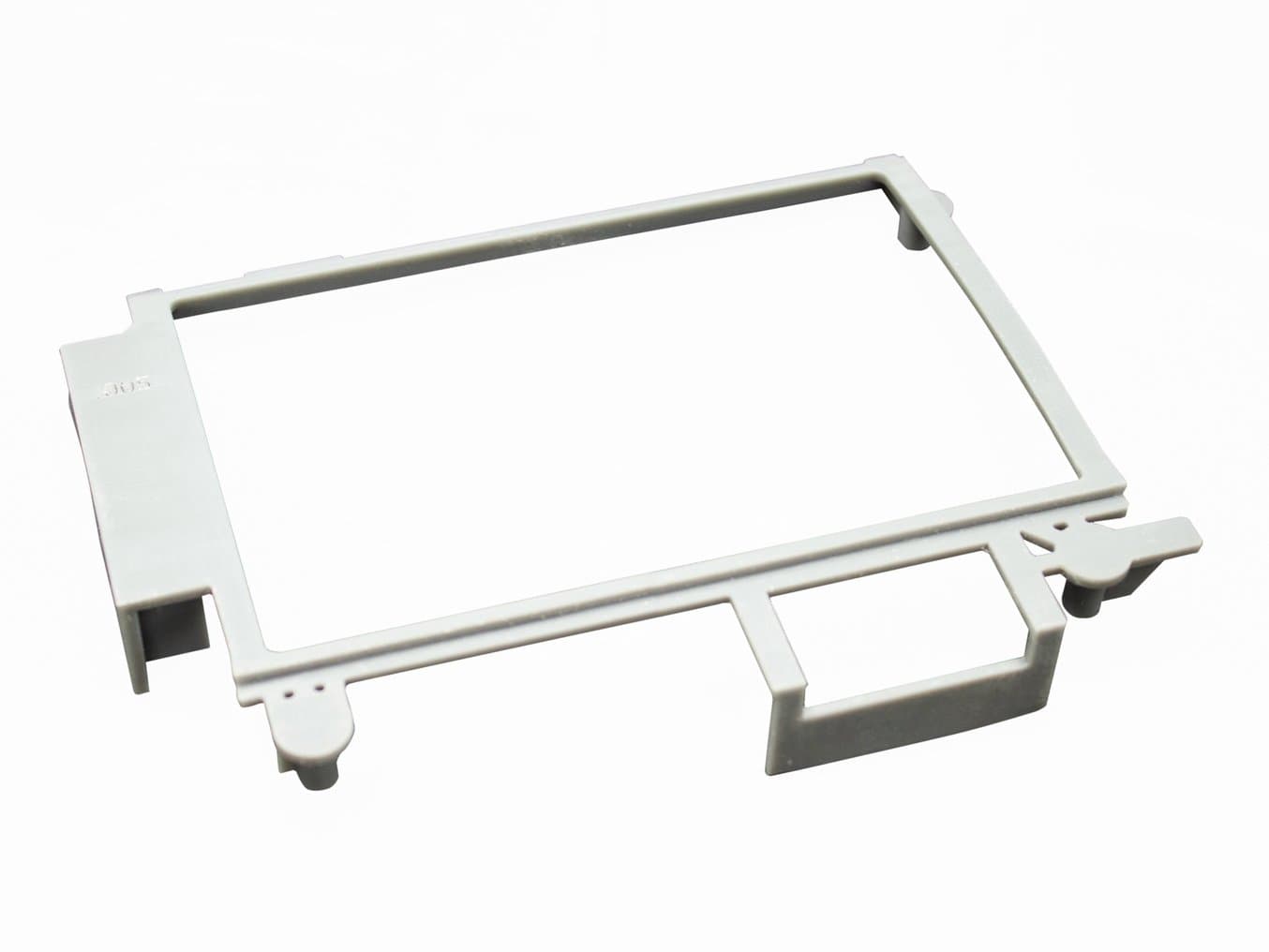
Dieser Rahmen für die Benutzeroberfläche, ebenfalls aus Rigid 10K Resin gedruckt, wurde für interne Tests verwendet, um die Abstände im Hinblick auf Form, Passform und Funktion an einem größeren Teil zu bestimmen.
Etwas Neues auszuprobieren war früher mit viel Bürokratie verbunden – ein Antrag musste gestellt, dann begründet und genehmigt werden, bevor eine Bestellanforderung erstellt wurde. Das Warten auf das Teil von einem externen Zulieferer konnte Wochen dauern, und die lange Zeitspanne erstickte die Kreativität im Keim. Nachdem sie gesehen haben, wie der betriebsinterne Form 3L konstant leistungsstarke Teile hervorbringt, schieben die Teams in Elektrotechnik, Produktdesign und sogar Praktikant*innen die Grenzen der Leistungsfähigkeit immer weiter hinaus, und die Begeisterung im Unternehmen wächst. „Früher haben wir nur das extern 3D-drucken lassen, was ich wirklich brauchte, aber jetzt haben wir mehr Raum für Forschung und Entwicklung. Das Team ist offen für diese Kreativität und Innovation“, so Flores.
Wie Friedrich bewiesen hat, erfordert die Entwicklung branchenführender Produkte Entschlossenheit. Der Form 3L kann Produktdesign- und Ingenieurteams dabei unterstützen, die Iterationsgeschwindigkeit für eine Vielzahl von Komponenten zu erhöhen, indem sie die umfangreiche Materialbibliothek ausnutzen. Neben dem Prototyping bietet der 3D-Druck auch für die Herstellung individueller Fertigungshilfsmittel eine kostengünstige Lösung, wie z. B. die Sondengehäuse von Friedrich. Weitere Informationen über den Form 3L finden Sie auf unserer Website.