Form 4L definiert den großformatigen SLA-3D-Druck neu – mit unübertroffener Schnelligkeit, Zuverlässigkeit und Genauigkeit
Formlabs präsentiert den neuen Form 4L, unseren großformatigen Kunstharz-3D-Drucker der nächsten Generation, der die Schnelligkeit, Genauigkeit und Zuverlässigkeit des Form 4 in einem völlig neuen Maßstab eröffnet.
Der Form 4L und sein biokompatibles Pendant Form 4BL basieren auf derselben bahnbrechenden Technologie wie Form 4 und Form 4B: Low Force Display™ (LFD). Dabei liefern Sie jedoch nahezu fünfmal größere Teile als unsere Desktop-Modelle.
Egal ob Prototypen in Lebensgröße, auf Abruf verfügbare Fertigungshilfsmittel oder verkaufsfertige Endprodukte – der Form 4L bietet erstklassige Teile in Rekordzeit und liefert selbst volle Fertigungsvolumen in unter sechs Stunden.
Zusammen mit den neuen SLS-Pulvern und der Öffnung des Formlabs-Ecosystems bildet der Form 4L den nächsten Schritt in Formlabs' Mission, unseren Kunden die Werkzeuge zu bieten, die aus Ihren Ideen Wirklichkeit werden lassen – egal wie groß oder wie komplex.
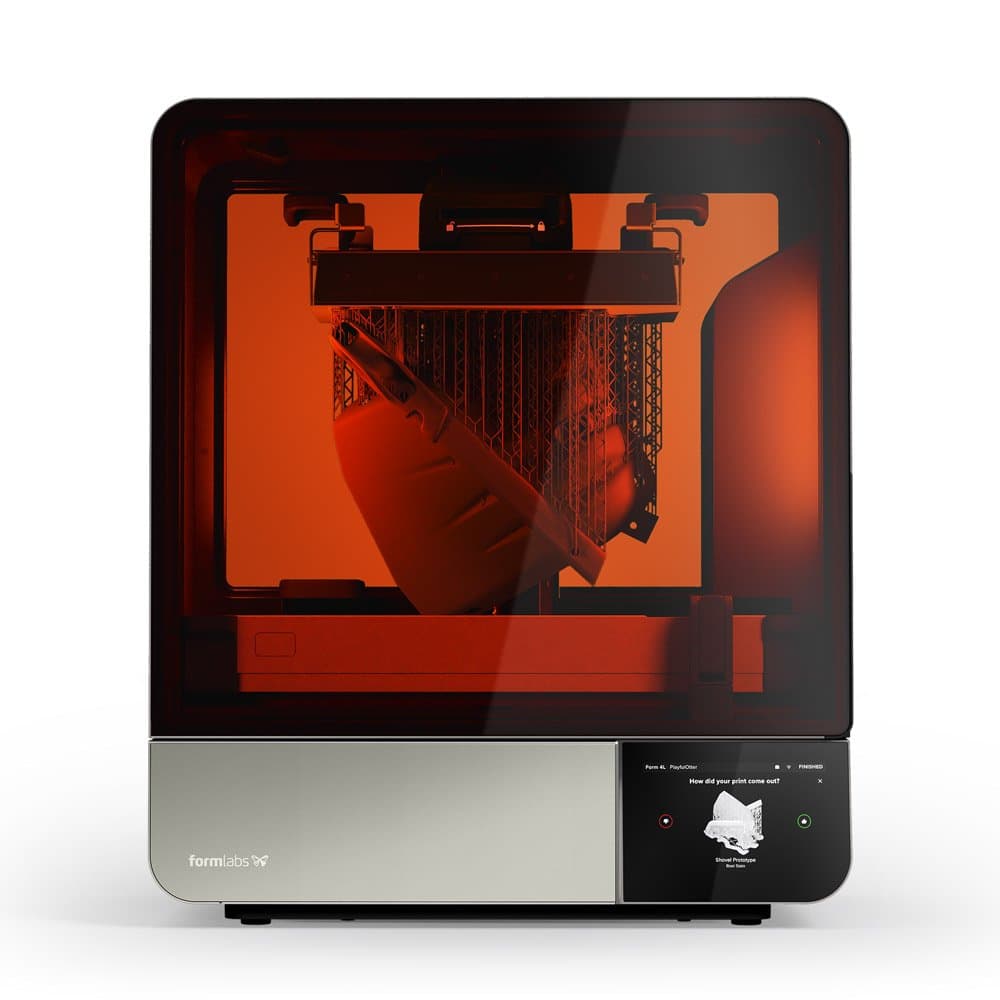
Produktdemo: Form 4L
Entdecken Sie, wie der neue Form 4L, unser großformatiger Kunstharz-3D-Drucker der nächsten Generation, die Schnelligkeit, Genauigkeit und Zuverlässigkeit des Form 4 in einem völlig neuen Maßstab eröffnet.
Wachsen Sie über sich hinaus, mit der Technologie der nächsten Generation
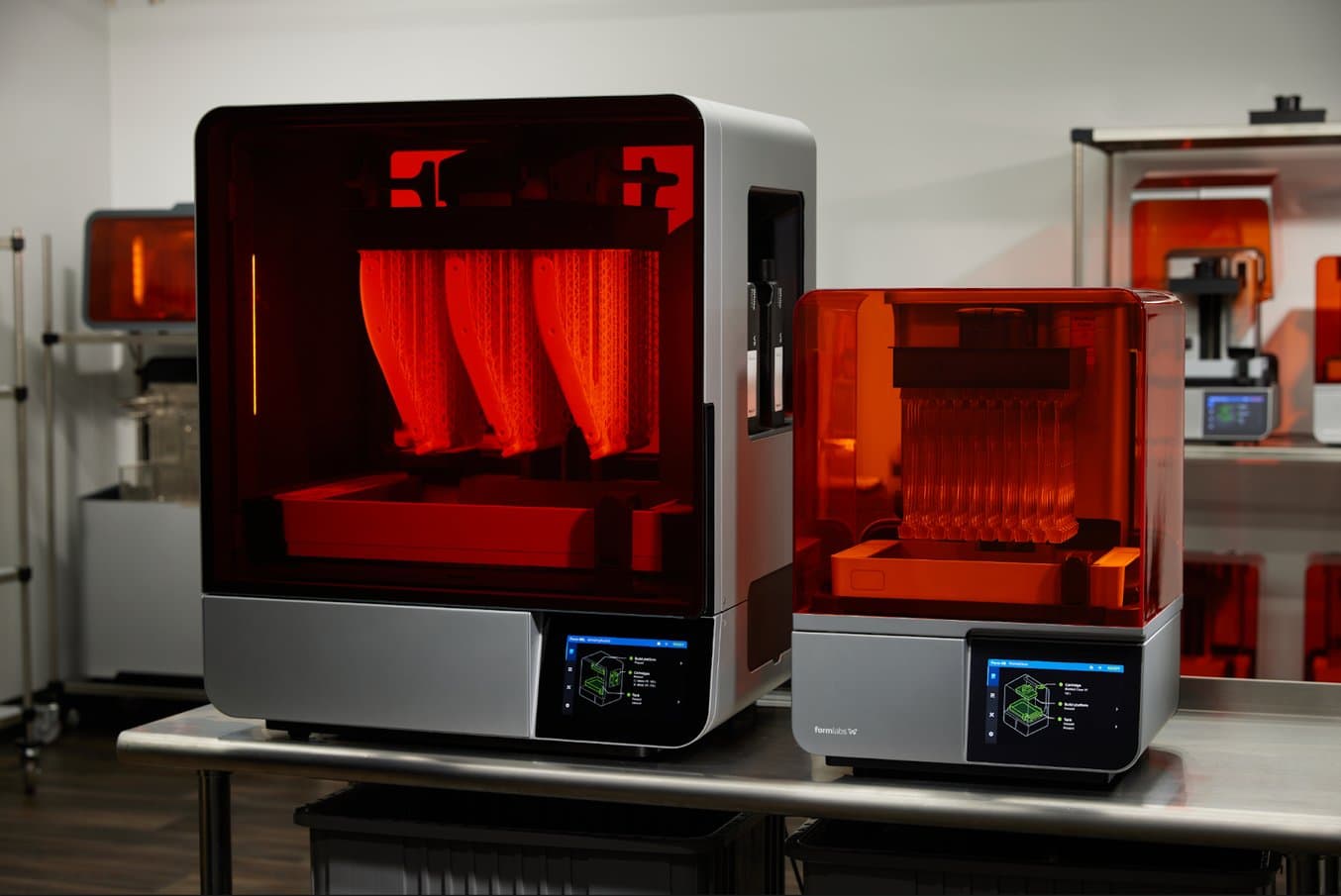
Der Form 4L ermöglicht die Fertigung großer, hochdetaillierter Teile aus einer breiten Palette von Materialien binnen eines Tages.
Der Form 4 hat einen Wendepunkt für den erschwinglichen SLA-3D-Druck eingeleitet. Die neue und innovative LFD-Technologie eröffnet nie dagewesene Druckgeschwindigkeiten, ganz ohne Kompromisse bei der Genauigkeit oder Druckzuverlässigkeit. Der Form 4L basiert auch auf demselben Drucksystem und wächst noch über den Form 4 hinaus: Mit einer Größe 35,3 x 19,6 x 35 cm ist sein Fertigungsvolumen 4,6-mal größer als das des Form 4 und sogar 13 % größer als das des Vorgängermodells Form 3L.
Im Vergleich zu unseren vorherigen großformatigen SLA-3D-Druckern, Form 3L und Form 3BL, ist der Form 4L schneller, zuverlässiger und einfacher zu bedienen und zu warten. Im großformatigen Form 4L wird jede Schicht flüssigen Kunstharzes von der leistungsstarken Light Processing Unit 4L (LPU 4L) in Sekundenschnelle belichtet, während im Form 3L jede Schicht mit einem dualen Laser nachgezeichnet werden musste. Beim Druck großer Teile oder mehrerer kleiner Teile auf dem Form 3L kann der Druckvorgang mit zwei Lasern die Druckzeit um Stunden verlängern. Beim Form 4L spielt es keine Rolle, welcher Anteil des Fertigungsbereichs mit Teilen bedeckt ist – die Lichtquelle härtet jede Schicht augenblicklich aus, um gleich zur nächsten überzugehen. So stehen selbst große Teile schon nach der Mittagspause bereit.
Der Form 3L war der erste wirklich zugängliche Kunstharz-3D-Drucker im Großformat, aber sein langsameres Druckverfahren stellte für iterative Workflows oft ein Hindernis dar. Im Produktdesign, Maschinenbau und Werkzeugbau, wo die Materialvielfalt und die Druckqualität von SLA gefragt sind, führen Druckzeiten von mehreren Tagen zu Verzögerungen und Leerlaufzeiten im Entwicklungsprozess.
Die rekordschnellen Druckgeschwindigkeiten des Form 4L machen es möglich, solche Projekte ohne Stillstandszeiten voranzutreiben. Druckaufträge mit großen Teilen oder vielen kleinen Teilen sind jetzt mehrmals am Tag umsetzbar, sodass Ihre Innovationen mit dem Tempo Ihres Teams Schritt halten können.
Form 4L fertigt bei Brose Roboter-Schweißvorrichtungen an einem Tag
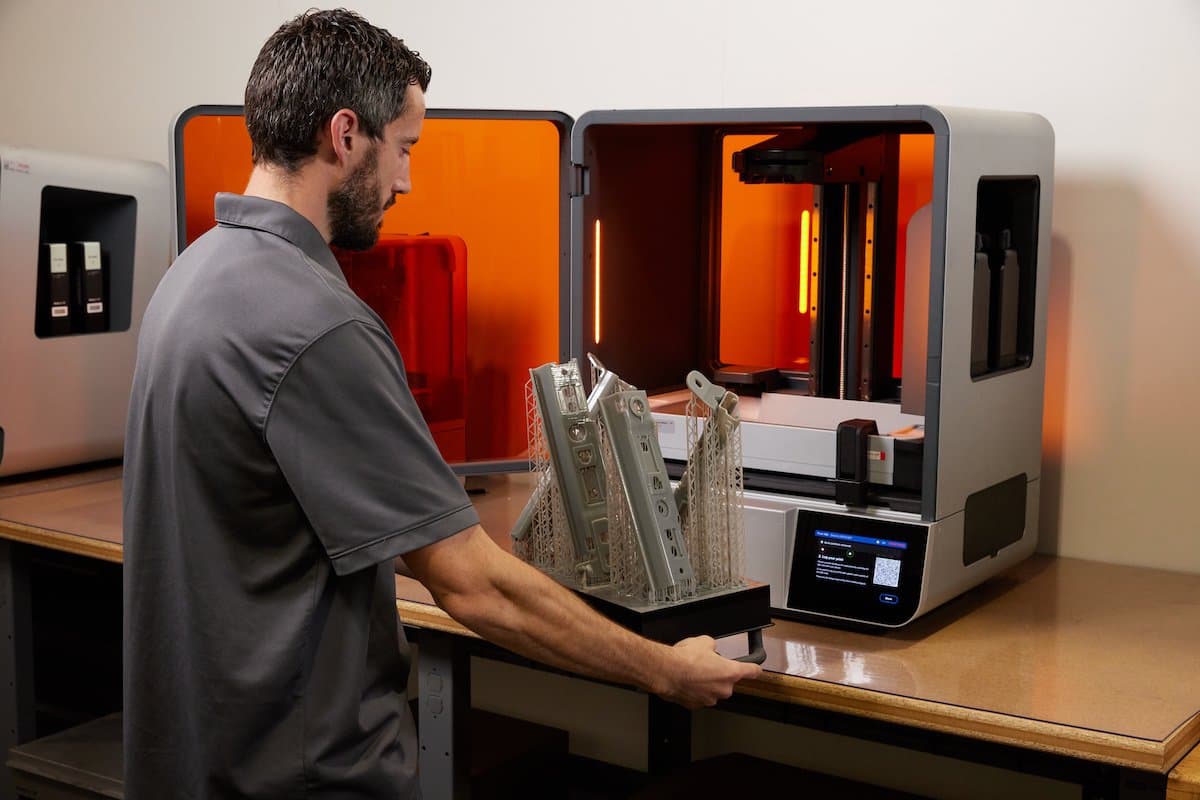
Jeremy MacMillan von Brose North America entnimmt eine robotische Passungsvorrichtung für das Schweißen, die er in knapp vier Stunden in mehreren Teilen gedruckt hat. Nach dem Waschen und Aushärten kommt das Teil sofort in der Schweißabteilung zum Einsatz, die es zur Einrichtung eines neuen Schweißprogramms für Autositzrahmen verwendet.
Bei Brose, einem der fünf größten familiengeführten Automobilzulieferer der Welt, spielt die additive Fertigung sowohl beim Produktesign als auch bei der Endfertigung eine wichtige Rolle. Am nordamerikanischen Standort von Brose werden mit 3D-Druck hochpräzise Prototypen in großen Stückzahlen erstellt, Halterungen und Vorrichtungen auf Abruf gefertigt und sogar Hunderttausende von endgültigen Automobilbauteilen für OEM-Partner wie BMW mit SLS gedruckt.
Bei Brose North America wechselt die Schweißabteilung häufig zwischen Projekten, und jedes Mal, wenn der Schweißroboter auf eine neue Produktlinie umgestellt wird, muss er für die jeweiligen Parameter des neuen Projekts vorprogrammiert werden.
Einen Schweißroboter mithilfe von endgültigen Metallkomponenten zu programmieren ist kostspielig. Zudem sind die Teile oft noch nicht verfügbar, wenn die Schweißzelle für das Programmieren bereit ist. Der 3D-Druck bietet eine schnelle und kostengünstige Lösung, allerdings unter bestimmten Voraussetzungen: Aufgrund ihrer Größe erfordern diese Sitzschienen einen großformatigen 3D-Drucker, der in der Lage ist, schnell präzise Teile mit hoher Maßgenauigkeit und der nötigen Festigkeit für die Befestigung an einer Schweißvorrichtung herzustellen.
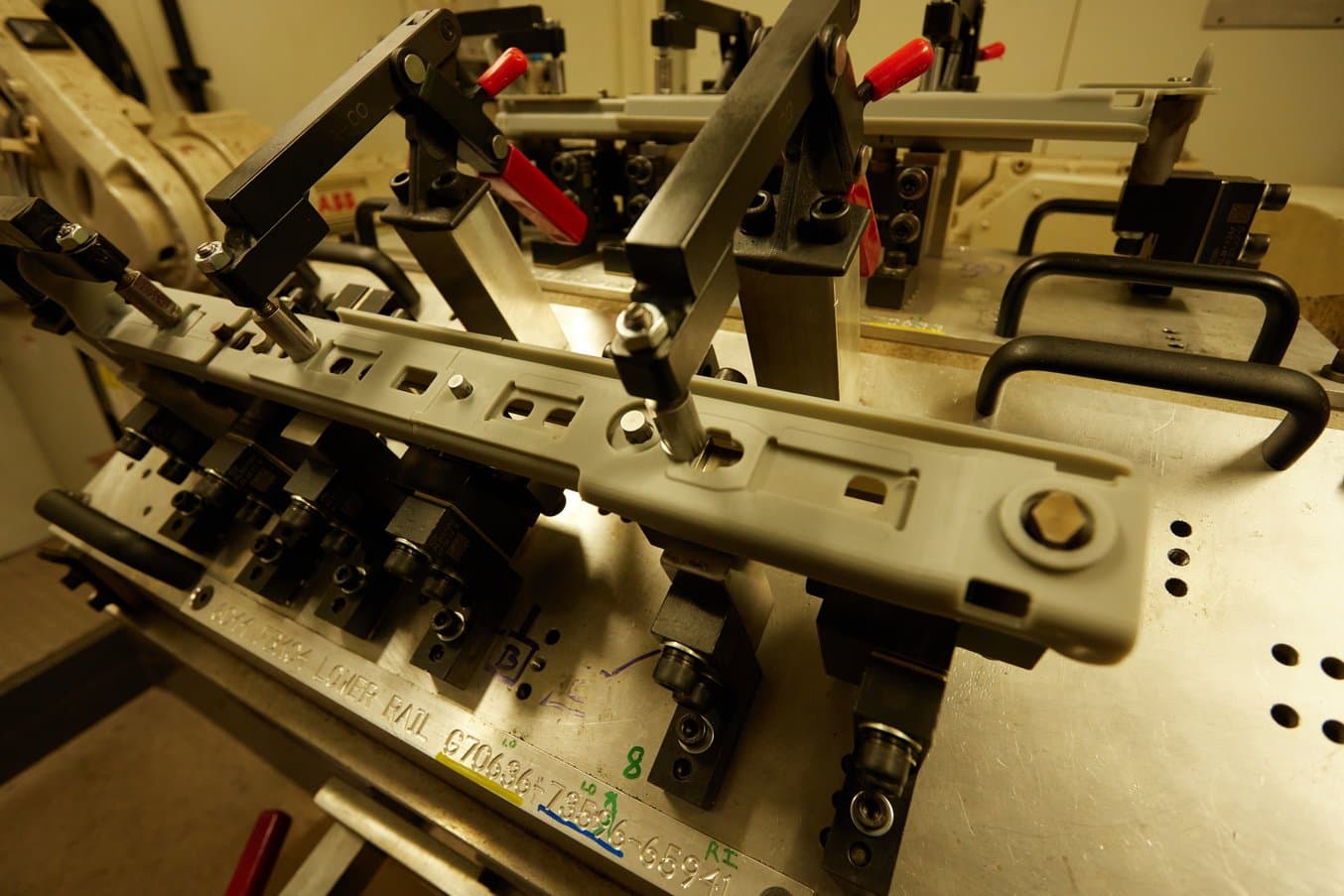
Diese Sitzkomponente wurde in weniger als drei Stunden auf dem Form 4L aus Fast Model Resin gedruckt, gewaschen, nachgehärtet und auf dem Schweißroboter montiert. Dadurch ist das Team in der Lage, den Roboter schnell auf die nötigen Bewegungen einzustellen.
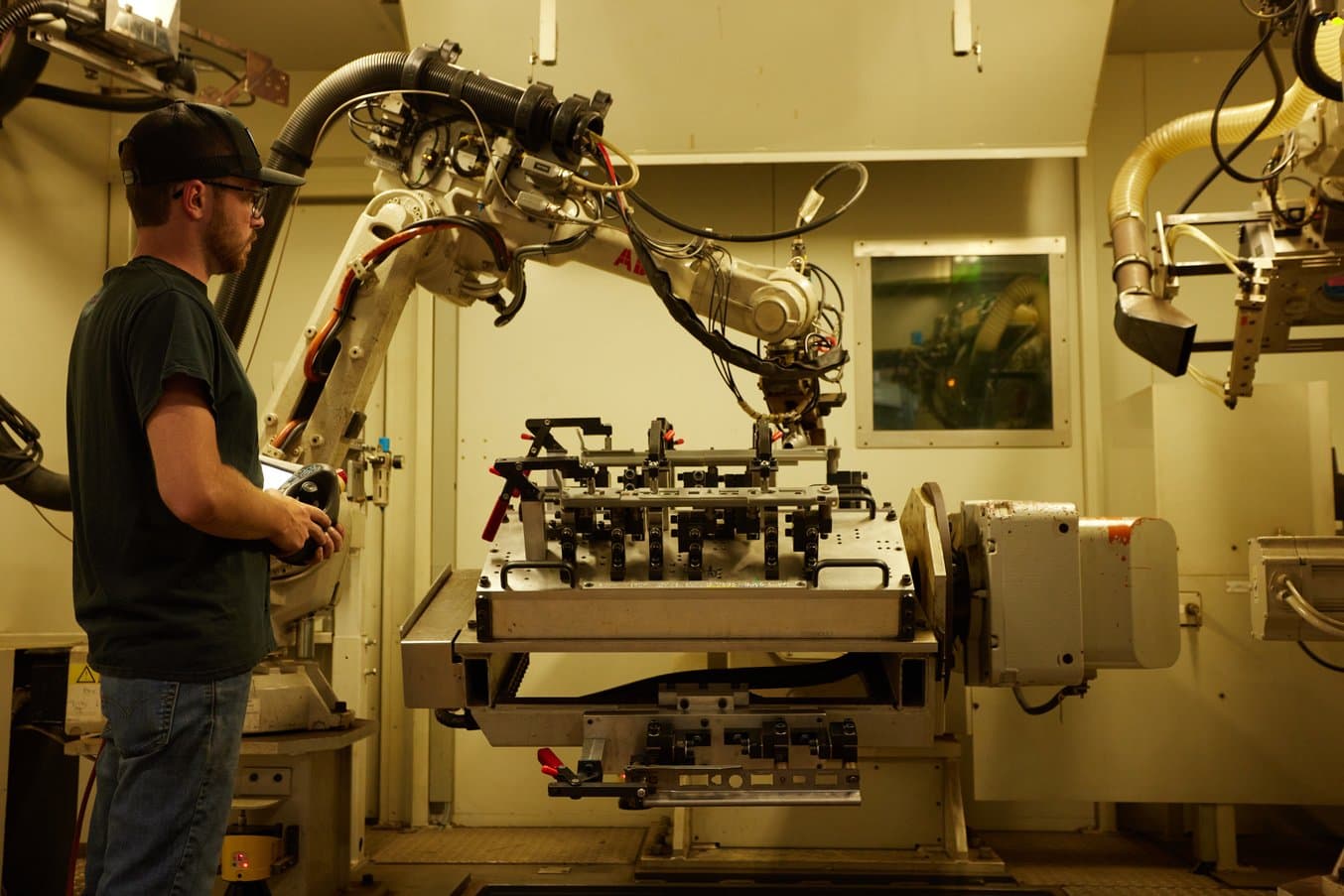
Passungsvorrichtungen wie diese helfen dem Schweißerteam, schnell und effizient zwischen Produktlinien zu wechseln. Sie sind hochpräzise, erschwinglich und können beliebig oft nachgefertigt werden, falls Änderungen oder Ersatzteile erforderlich sind.
Das Brose-Team öffnete sein Paket des neuen großformatigen Formlabs-SLA-Druckers Form 4L an einem Dienstagmorgen. Die Einrichtung beanspruchte nur 30 Minuten, und schon bald druckte das Team aus Fast Model Resin große Teile für die Einrichtung der Schweißzelle. Aufgeteilt in vier Einzelteile füllten diese Teile fast das gesamte Fertigungsvolumen aus. Trotz dieser Größe druckte der Form 4L die Vorrichtung in weniger als zwei Stunden, und nur 45 Minuten später, nach einem kurzen Waschgang und einer Nachhärtung, war sie auf dem Schweißroboter montiert.
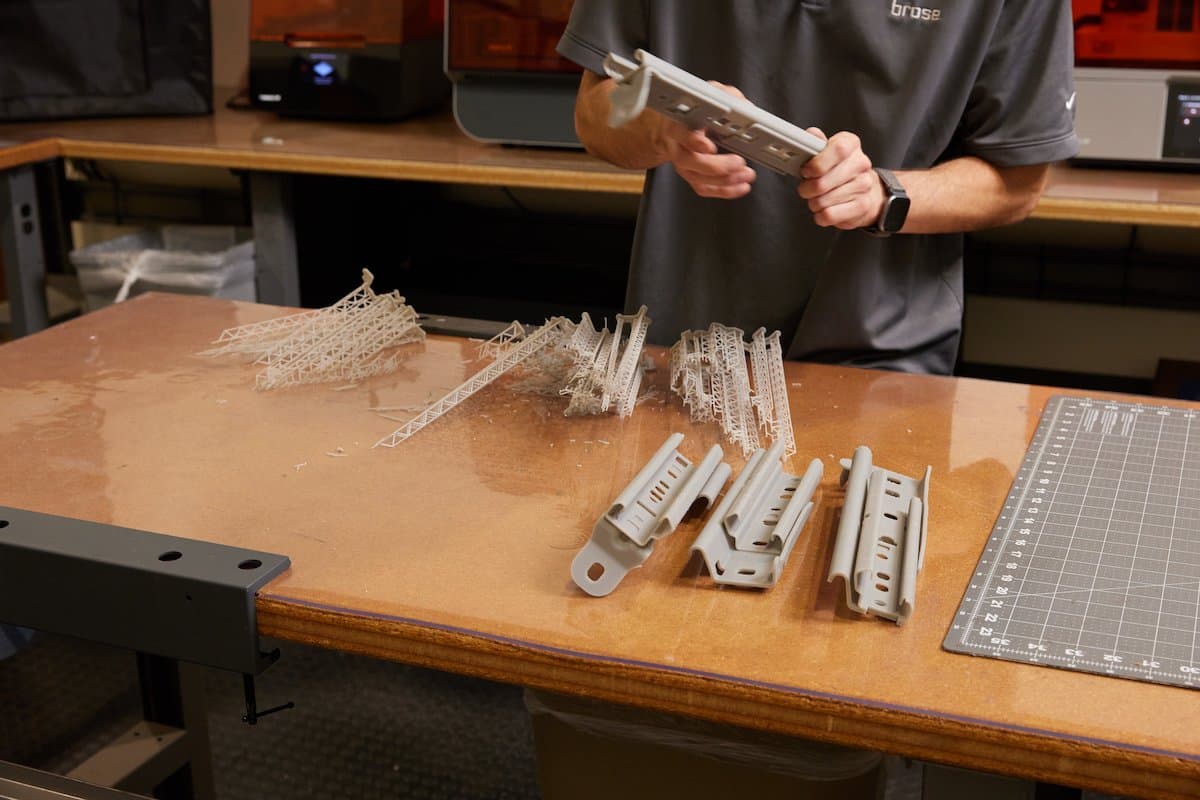
Diese Teile imitieren das Design der Autositzschienen, die zu einer Sitzrahmenbaugruppe verschweißt werden. Aufgrund des größeren Fertigungsvolumens des Form 4L kann das Brose-Team die Schienen in wenigen Einzelteilen drucken, um die Schweißmaschine genau zu programmieren.
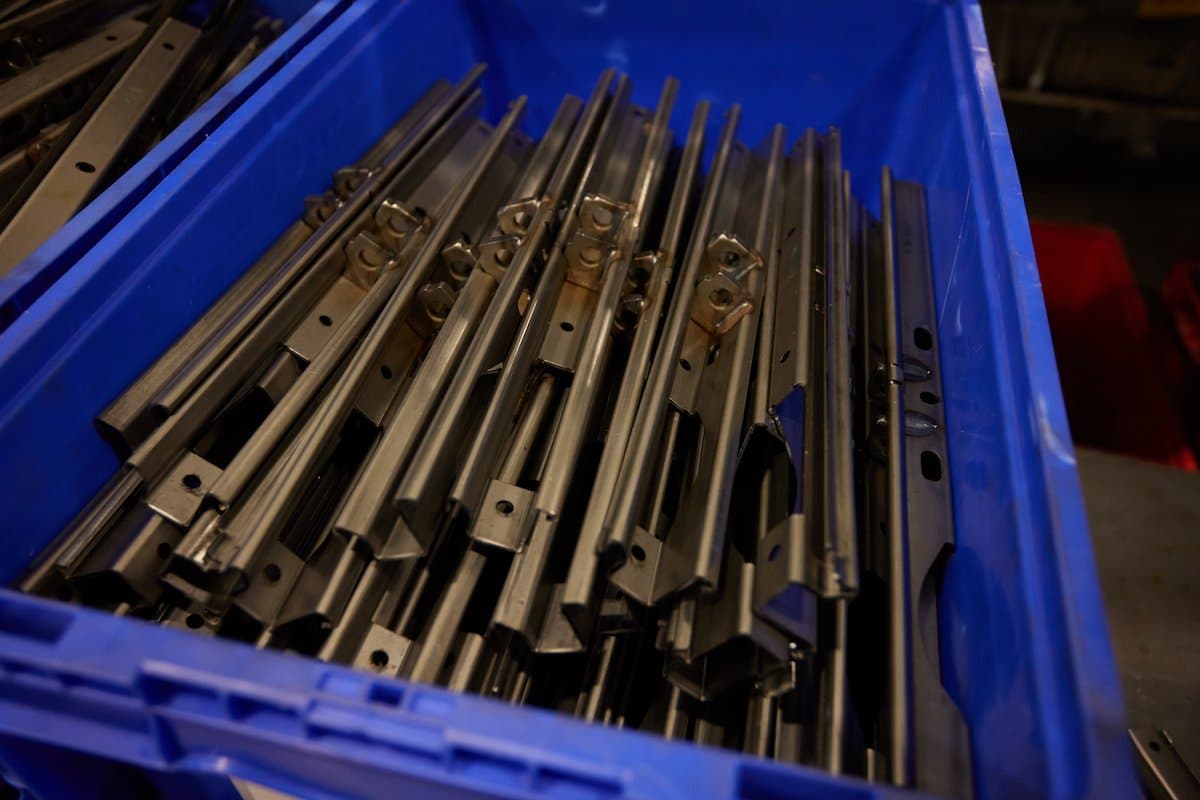
Sobald der Schweißroboter über die richtigen Parameter verfügt, kann er schnell und effizient Hunderte oder Tausende von Sitzschienen schweißen und für die Montage des Sitzrahmens vorbereiten.
„Mit dem neuen Form 4L von Formlabs können wir große Teile schnell drucken. Zum Beispiel nutzen wir den Form 4L zum Drucken von Teilen für unsere Schweißzelle in nur wenigen Stunden statt über Nacht. So kann das Schweißerteam von Brose den Roboter programmieren, bevor die gestanzten Metallbauteile eintreffen. Mit dem neuen Fast Model Resin erreichen wir den nötigen Detailgrad und die nötige Steifigkeit schneller als je zuvor.“
Matthias Schulz, Leiter der Prototypenentwicklung für Sitze, Brose North America
Bei Brose ist man die Arbeit mit engen Zeitplänen gewohnt – einige der OEM-Partner erwarten die Lieferung ihrer Teile innerhalb von 24 Stunden nach Bestellung. Seine Druckgeschwindigkeit und Druckqualität machen den Form 4L zu einem essenziellen Werkzeug, auf das sich das Brose-Team verlassen kann, wenn es um die Einhaltung knapper Fristen geht. Um mehr über die 3D-Druck-Initiativen von Brose zu erfahren, lesen Sie den vollständigen Anwenderbericht oder sehen Sie sich unser On-Demand-Webinar an.
Großformatige Teile in Stunden statt in Tagen
Für jeden, der in seinem Arbeitsalltag einen 3D-Drucker nutzt, bedeuten großformatige Drucke in der Regel eine Verlangsamung der Produktivität. Um das Design eines Helmprototyps zu prüfen, muss man ihn auf dem Kopf eines Menschen sehen; um die Passung eines E-Bike-Akkugehäuses zu prüfen, muss man es am Fahrradrahmen befestigen. Wenn solche Produkte in mehreren Teilen gedruckt werden, Schaumstoff geschnitzt wird oder Teile gefräst werden, kann der Unterschied in Optik und Haptik Ihre Iteration verlangsamen – während Ihre Frist immer näher rückt.
Mit dem leistungsstarken Drucksystem und der branchenführenden Materialbibliothek des Form 4L erhalten Sie innerhalb weniger Stunden Teile im menschlichen Maßstab, und zwar aus Materialien, die spritzgegossenen Kunststoffen in Optik und Haptik gleichkommen. Große Hersteller von Endprodukten benötigen für Funktionstests und Verbrauchertestphasen Prototypen in größeren Stückzahlen, bevor sie sich auf ein Design festlegen und die Bestellung von Produktionswerkzeugen sich lohnt. Dank der Größe und der Schnelligkeit des Form 4L können diese höheren Druckvolumen betriebsintern umgesetzt werden, ohne dass eine Auslagerung an 3D-Druck-Dienstleister, Maschinenwerkstätten oder Spritzgießer erforderlich ist.
Der Zugang zu schnellem 3D-Druck im Großformat öffnet Unternehmen die Tür zu mehr Testrunden und mehr Verbraucherfeedback, was letztlich zu besser erforschten, getesteten und validierten Produkten führt.
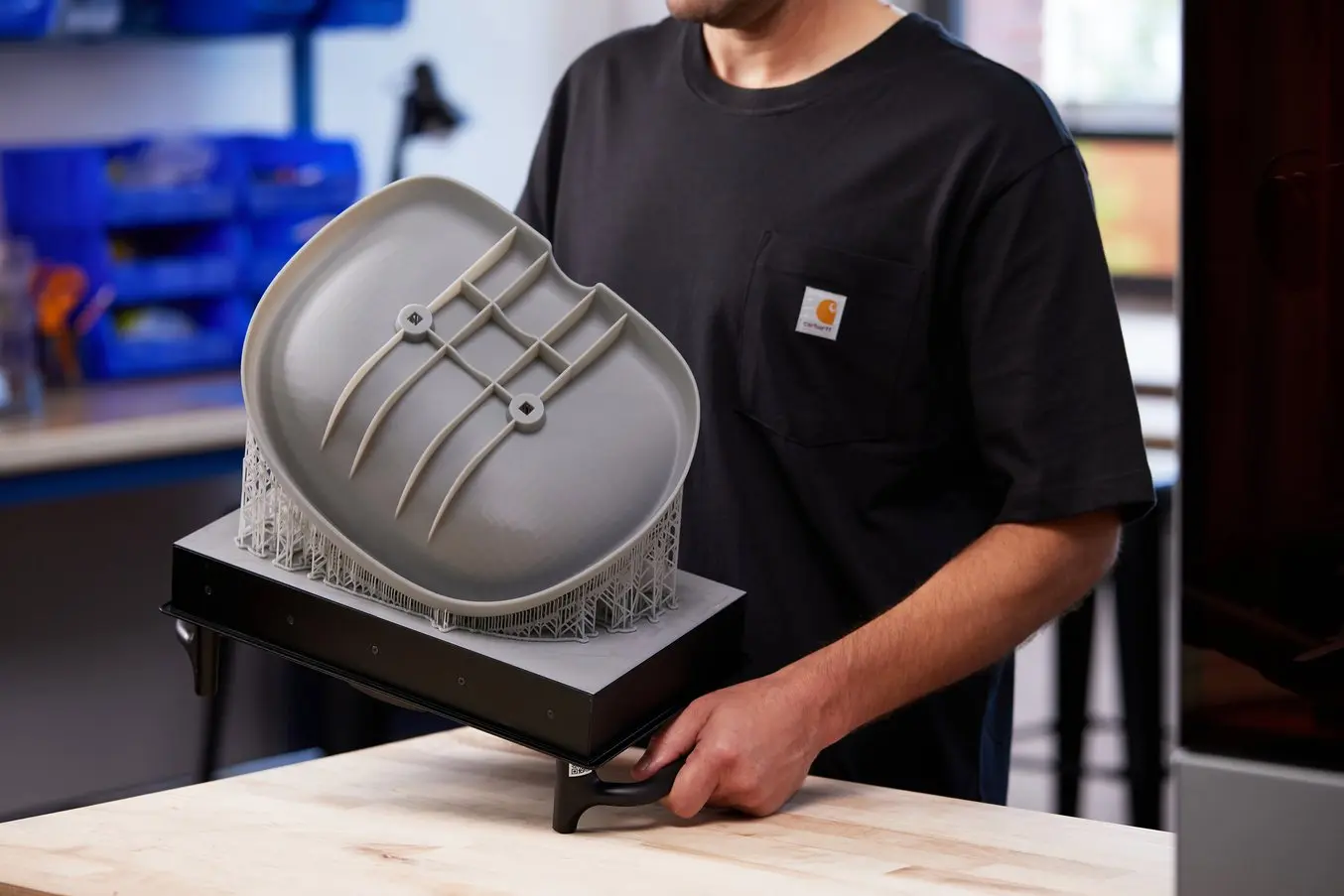
Druckgeschwindigkeit im Vergleich: Sitzprototyp von Radio Flyer
Form 4L | Form 3L | Großformatiger FDM-3D-Drucker | |
---|---|---|---|
Druckzeit | 2 h 37 min | 21 h 6 min | 42 h 3 min |
Vergleich von Druckern und Druckparametern:
- Form 4, Fast Model Resin, 200 Mikrometer Schichthöhe
- Form 3L, Draft Resin, 200 Mikrometer Schichthöhe
- Ultimaker S7, PLA, 100 Mikrometer Schichthöhe, 20 % Fülldichte
Wie Microsofts Prototyping-Labor betriebsintern höhere Stückzahlen liefert
Microsoft steht seit Jahrzehnten an der Spitze der technischen Fertigungshierarchie, und sein Advanced Prototyping Lab (APL) verfügt über ein schwindelerregend großes Arsenal fast aller denkbaren Fertigungsmethoden. Das APL bearbeitet Anfragen aus dem gesamten Ecosystem von Microsoft, darunter Xbox, Surface-Tablets und mehr.
Vor kurzem benötigte ein Mitarbeiter ein Tablet-Gehäuse, das das Fertigungsvolumen des Form 4 überstieg, allerdings schon bald gebraucht wurde. „Vor dem Form 4L konnten wir so etwas nicht drucken, die Durchlaufzeit hätte zu lange gedauert, weshalb 3D-Druck ausgeschlossen gewesen wäre. Das hätte den iterativen Prozess verlangsamt“, erklärt Mark Honschke, Leiter der Prototypenentwicklung im APL. Das 3D-Druck-Team sendete die Prototypen an den Form 4L und stellte die Teile noch am selben Nachmittag bereit. „Mit nur vier Stunden ist das für uns eine Revolution“, so Honschke.
Aber die Druckzeit ist nicht alles – auch die Vor- und Nachbearbeitungszeit kann sich auf die Produktivität und Effizienz eines Teams auswirken. Der Form 4L hat den Arbeitsablauf des Kunstharz-3D-Drucks für das APL vereinfacht und sowohl die Vorbereitungsarbeiten als auch die Fertigstellung verkürzt, damit Teile noch schneller vom Konzept zur Lieferung gelangen.
Dank des Bauvolumens des Form 4L gehört das Zerteilen von Modellen der Vergangenheit an, und das Team ist in der Lage, tagsüber schnelle Teile sowie über Nacht größere Stückzahlen zu produzieren. Die Nachbearbeitungszeit hat sich dank kleinerer Berührungspunkte bei den Stützstrukturen ebenfalls verkürzt.
Das APL erhält häufig Anfragen nach Baugruppen für Konzeptnachweis-Prototypen (Proof of Concept), die von Xbox über Surface-Tablets bis hin zu Headsets und mehr reichen. Da die Bauteile aber nicht zur gleichen Zeit gefertigt werden, muss der 3D-Druck einspringen. „Sie bekommen die Leiterplatinen vielleicht in einer Woche, aber erst drei Wochen später die Midframes. Und wir müssen Probleme lösen wie zum Beispiel, dass die Leiterplatine einen halben Millimeter zu dick ist und wir den Gehäusedeckel nicht schließen können. Wenn wir also solche Teile fertigen, sind es nicht nur ein, zwei Stück, sondern 50 bis 100 Teile“, berichtet Honschke.
Vor kurzem wurde ein Konzeptnachweis für 50 Xbox-Midframes angefordert, da es Probleme mit dem Outsourcing einiger interner Bauteile gab. „Ich sagte: 'Ja, wir können euch die 50 Teile liefern, aber wir können sie nicht reinigen.' Aber mit dem Form 4L war das eigentlich kein Problem, weil sich die Stützstrukturen so viel leichter ablösen lassen. Und wir konnten drei komplette Druckaufträge in drei Tagen statt in anderthalb Wochen durchführen. Der Form 4L hat sich also schon allein durch dieses Projekt bezahlt gemacht“, sagt Honschke.
Gemeinsam haben Form 4 und Form 4L dem APL einen ganz neuen Weg geebnet – wenn das Team hochwertige Teile in so kurzer Zeit bereitstellen kann, ist es in der Lage, mehr große Konzeptnachweise betriebsintern umzusetzen. „Xbox macht ein bis zwei Konzeptnachweise pro Jahr, Surface zwei bis drei, und wenn wir diese Dienstleistung betriebsintern anbieten können, ist das einerseits sicherheitstechnisch besser und andererseits können wir Probleme auch schneller erkennen, wenn wir schneller arbeiten. Meiner Meinung nach bieten Form 4 und Form 4L gute Geschäftsmöglichkeiten. Ich denke, es wird sich sogar lohnen, Personal einzustellen, um sie zu betreiben“, meint Honschke.
Verbesserter Workflow: Zuverlässigkeit und Benutzerfreundlichkeit
Ganz gleich, ob Sie 3D-Druck einsetzen, um Design-Fristen einzuhalten oder Endprodukte an Kunden zu liefern: Sie müssen sich darauf verlassen können, dass Ihre Geräte durchgehend eine hohe Leistung erbringen. Unser Verfahren für Kunstharz-3D-Druck im Großformat wurde von Grund auf überarbeitet, sodass Sie jetzt großformatige Teile genauso zuverlässig herstellen können wie kleinere Teile auf dem Form 4.
Das vereinfachte Drucksystem mit nur einer leistungsstarken Light Processing Unit 4L macht den Form 4L nicht nur bedeutend schneller als laserbasierte Kunstharz-3D-Drucker, die zur Vergrößerung des Bauvolumens mehrere Laser benötigen, sondern durch die geringere Anzahl beweglicher Teile ist der Drucker auch einfacher zu warten und weniger fehleranfällig.
Neben dem unkomplizierten Aushärteprozess sorgen hochwertige Verbrauchsmaterialien dafür, dass ihre Drucke jedes Mal gelingen. Zudem können Sie sie viel länger verwenden, bevor sie ersetzt werden müssen. Die Verbrauchsmaterialien des Form 4L wurden konzipiert, um Ihr Leben leichter zu machen, nicht schwerer – sowohl der Form 4L Resin Tank als auch die Light Processing Unit wurden auf Langlebigkeit getestet und müssen erst nach 75 000 bzw. 600 000 bis 1,9 Mio. Schichten ersetzt werden. Das vereinfachte, fortschrittliche Design des Ecosystems des Form 4L lässt viel weniger Raum für Fehler, sodass Sie nicht mehr nachkalibrieren oder Ihr Gerät während des Drucks im Auge behalten müssen.
Da es beim Drucken jedoch nicht nur um die Hardware geht, hat Formlabs' Materialentwicklerteam Hunderte von Teilen aus jedem Material und mit jeder Einstellung gedruckt, um die Druckergebnisse und Druckparameter zu validieren. Unabhängig von Materialänderungen bleiben die Teilequalität, die Oberflächenqualität, das Entfernen von Stützstrukturen und die mechanische Leistung gleich.
Prototyping und Produktion sollten sich ganz um die Leistung des Teils drehen – wie gut ein Helm den Schädel schützt oder wie ein Bremshebel auf Druck reagiert – und nicht um die Leistung des Druckers, der Ihnen das Teil liefert. Nach Jahren der Entwicklung, der Forschung und der Rücksprache mit unseren Kunden im großformatigen SLA-Druck freuen wir uns, einen Drucker anbieten zu können, der erfolgreiche Drucke ohne Kopfzerbrechen liefert, sodass Sie Ihren Fokus ganz auf das Wesentliche legen können.
Das Comeback der SLA-Anfragen bei Radio Flyer

Der ursprüngliche SLS-gedruckte Prototyp (links), der mit SLA-3D-Druck gedruckte und lackierte Roadshow-Prototyp (Mitte) und der endgültige Bubble Buddy Walker Wagon.
Als seit über 100 Jahren bewährtes und von Familien geschätztes Unternehmen ist Radio Flyer vor allem für seinen klassischen Ziehwagen Little Red Wagon® bekannt, der auch einen Platz in der US-amerikanischen Toy Hall of Fame errungen hat. Die Produkte des Unternehmens sind in der Populärkultur und auf Weihnachtswunschzetteln seit jeher ganz vorne dabei, denn im Bereich fahrender Spielzeuge ist Radio Flyer führend. Dazu gehören etwa Wagen, Roller, Dreiräder, Go-Karts, elektrische Fahrräder und andere innovative Produkte, mit denen Familien gemeinsam neue Orte entdecken.
3D-Druck ist ein wichtiger Bestandteil des Entwicklungsprozesses von Radio Flyer. Der Konstrukteur Agostino LoBello leitet ein Labor, zu dem zwei SLS-3D-Drucker (selektives Lasersintern) aus Formlabs' Fuse-Serie, Großformat-SLA-Drucker vom Typ Form 3L und Form 4L sowie FDM- und PolyJet-Drucker gehören. Bevor er seine Flotte um den Form 4L erweiterte, erhielt LoBello nicht viele Anfragen nach SLA-Drucken – die Design- und Ingenieurteams zogen die mit der Fuse-Serie gedruckten SLS-Teile vor. Nach nur wenigen Wochen des Druckens mit dem Form 4L bemerkte LoBello jedoch, dass mehr Anfragen nach kurzfristigen Teilen aus dem großformatigen SLA-Drucker eingingen.
„Ich denke, der Form 4L hat die Lücke sehr geschlossen. Zuvor haben wir SLA wegen der Druckzuverlässigkeit und Maßgenauigkeit nicht oft eingesetzt. Aber jetzt merke ich deutlich, dass die Leute nach Drucken aus dem Form 4L fragen, weil er eine so viel höhere Genauigkeit liefert, und auch, weil wir die Teile so schnell bekommen können“, sagt LoBello.
Bei den meisten Teilen, die den SLA-Prozess durchlaufen, handelt es sich um sogenannte Roadshow-Modelle. Diese Teile werden geschliffen, lackiert und bearbeitet, um ein Oberflächenfinish in Spritzgussqualität zu erreichen, bevor sie zu Fotoshootings für E-Commerce-Websites wie Target, Wal-Mart und Amazon geschickt werden. „Die Händler erhalten die Produkte zur Prüfung, bevor sie sie ins Sortiment aufnehmen, deshalb dürfen sie von den endgültigen Produktionsteilen praktisch nicht zu unterscheiden sein. Für so etwas nutzen wir SLA“, erläutert LoBello.
Die „präsentationsfertigen“ Teile sind nur ein kleiner Teil der Anfragen, die bei LoBello eingehen; die übrigen Anfragen wurden meist mit dem Fuse-Drucker umgesetzt – bis der Form 4L kam.
„Die Geschwindigkeit hat den großen Unterschied ausgemacht, aber auch die Maßgenauigkeit. Derzeit drucken wir mit Erfolg eine Schachtel in der vollen Größe des Bauvolumens – als wir versucht haben, diese Größe auf dem Form 3L zu drucken, passten die Schachtel und ihr Deckel nicht zusammen. Vor dem Form 4L haben wir solche Teile lieber CNC-gefräst oder mit SLS gedruckt und zusammengesetzt.“
Agostino LoBello, Product Design Engineer bei Radio Flyer
Mit dem Form 4L hat LoBello mehr Spielraum, um Anfragen aus den Design- und Ingenieurteams zu bearbeiten – die Drucker laufen nach wie vor nonstop, aber dank der höheren Druckgeschwindigkeiten schafft das Team mehr. Lesen Sie den vollständigen Anwenderbericht, um mehr über Radio Flyer und Form 4L zu erfahren.
Größer, schneller, aber stets auf der Spur
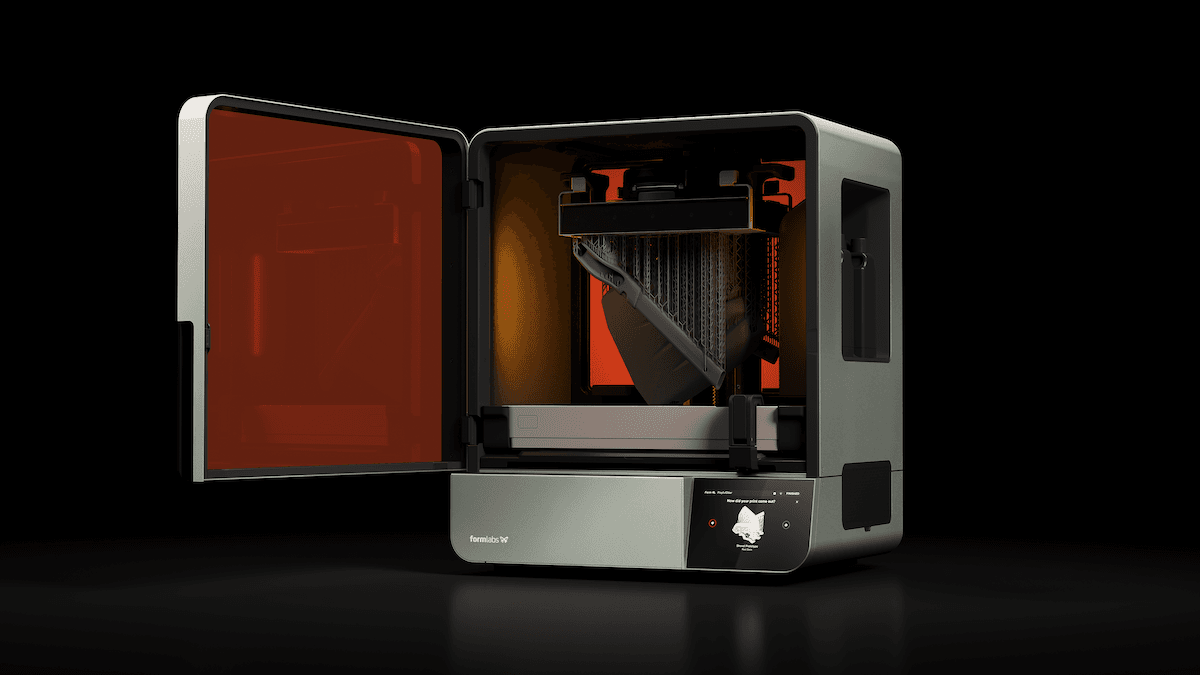
Der Form 4L hat es Kunden wie Microsoft, Radio Flyer, Brose und anderen ermöglicht, hochpräzise, große, maßstabsgetreue Teile in kürzester Zeit zu produzieren, um ihre Iterationen zu beschleunigen und wichtige Fristen einzuhalten.
Mit dem Form 4L werden einige Unbekannte im Design- und Konstruktionsprozess beseitigt: Wird das Teil rechtzeitig zur Designprüfung fertig, schaffe ich noch eine weitere Änderung, lohnt sich der Werkzeugbau für bessere Oberflächenqualität?
Rechtzeitig zur Besprechung fertig zu werden, weitere Merkmale hinzuzufügen oder etwas ganz Neues auszuprobieren ist mit dem Form 4L praktisch keine Herausforderung mehr. An der Druckqualität, auf die die Kunden des Formlabs-SLA-Drucks setzen, hat sich nichts geändert, und die Materialvielfalt des Formlabs-Ecosystems erhält eine noch breitere (und höhere) Plattform. Alle Eigenschaften, die den SLA-3D-Druck auszeichnen, sind in diesem Gerät gebündelt. Der schnellste und zugänglichste, erschwinglichste und benutzerfreundlichste großformatige Kunstharz-3D-Drucker der Welt steigert Ihre Produktivität und nimmt Ihnen die Sorgen beim Export von Teilen aus der Design-Software in die Realität.
Bestellen Sie den Form 4L noch heute, um gleich mit dem Kunstharz-3D-Druck in blitzschneller Geschwindigkeit loszulegen. Um den Drucker und Ihre individuellen Prozesse mit Fachleuten zu besprechen, kontaktieren Sie unser Vertriebsteam.