Serielle Maßanfertigung von Konsumgütern: 3D-gedruckte Schuhe, Ohrstöpsel, Rasierer und vieles mehr
Die Standardisierung von Produkten ist im Zeitalter der Massenproduktion zur Norm geworden. Konsumgüter sind in einer begrenzten Anzahl an Standardgrößen verfügbar, da sich so geringere Kosten erzielen lassen, denn die individuelle Anpassung auf die Bedürfnisse eines jeden Nutzers ist mit herkömmlichen Fertigungsmethoden in der Praxis unmöglich.
Dank seiner einzigartigen Fähigkeiten erschließt der 3D-Druck neues Potenzial und Geschäftschancen. Was früher für die Produktion mit herkömmlichen Methoden zu komplex, unerschwinglich oder unpraktisch war, ist heute mit digitalen Technologien ohne zusätzliche Kosten möglich. So haben Designer vollständige Kontrolle und umfassend individualisierbare Konsumgüter werden zur Wirklichkeit.
Lesen Sie weiter, um zu erfahren, wie Unternehmen wie Gillette und New Balance 3D-Druck und digitale Technologien nutzen, um die Grenzen der Individualisierung zu erweitern und Kunden die Produkte ihrer Wahl noch näher zu bringen.
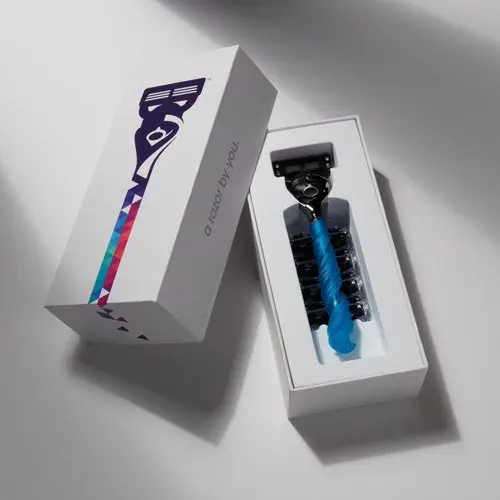
Leitfaden zu Mass Customization
In diesem Leitfaden erhalten Hersteller Einblick in die verschiedenen Ansätze zur Individualisierung von Produkten, die Auswahl der passenden Methode und mehr.
Sportliche Leistung der nächsten Generation mit 3D-gedruckten Schuhen
Schuhe sind ein Geschäft mit großem Inventar und hohen Volumina, bei dem oft immer noch viel Handarbeit und Handwerkskunst erforderlich ist. Unternehmen führen jedes Jahr Hunderte oder Tausende Designs ein, und ein einziges Modell umfasst Hunderte von SKUs an Farb- und Größenkombinationen, bei denen Komponenten mit verschiedenen Materialien, Toleranzen und Werkzeugprogrammen hergestellt werden.
Für Schuhersteller wird es immer schwieriger, die hohe Nachfrage nach Individualisierung zu bedienen. Moderne Kunden verlangen nach individualisierten Produkten, die von überall aus bestellt und dann schnell geliefert werden können. Doch durch die technologischen Einschränkungen waren individuell angepasste Schuhe bislang meist das Privileg von Profisportlern.
Durch den Einsatz von 3D-Druck bei der Herstellung von Schuhen ergeben sich neue Möglichkeiten zur Individualisierung, mit denen die Kundennachfrage bedient werden kann. Indem die Designeinschränkungen reduziert werden, kann sich die Individualisierung mit Hilfe von 3D-Druck auf jede Facette der sportlichen Leistung erstrecken, von Spike-Plates über das Fersendesign bis hin zu Zwischensohlen, die auf das individuelle Laufprofil angepasst sind. Alle Aspekte vom Gewicht über den Laufstil bis hin zur bevorzugten Dämpfung kann berücksichtigt werden.
Die Zusammenarbeit zwischen New Balance und Formlabs läutet die Zukunft der fortschrittlichen Schuhherstellung ein. Zusammen haben die beiden Unternehmen ein neues 3D-Druckmaterial namens Rebound Resin entwickelt. Es wurde für maximale Vielseitigkeit bei der Individualisierung der Optik und der Performance von Sportschuhen ausgelegt. Mit einer widerstandsfähigen Gitterstruktur können 3D-gedruckte Einlagen im Vergleich zu herkömmlichem Schaumstoff eine lebendigere, federartige Dämpfung bieten.
Durch die Reduzierung von Designbeschränkungen können Hersteller auf Daten zugreifen, um 3D-gedruckte Schuhsohlen zu gestalten, bei denen jede Facette der sportlichen Leistung berücksichtigt wurde.
Das erste TripleCell-Produkt, der limitierte 990S TripleCell, ist seit Juni 2019 im Handel. Der FuelCell Echo mit TripleCell-Vorderfuß folgt im Herbst 2019. Das erste High-Performance-Laufprodukt mit TripleCell entlang der ganzen Sohle wird 2020 veröffentlicht. Dank des schnellen Fortschritts können Schuhe zu den ersten individualisierbaren Konsumgütern gehören, die in großem Umfang mit 3D-Druck hergestellt werden.
Unvergleichliche Audioqualität mit 3D-gedruckten Ohrstöpseln
Eine bedeutende Branche befasst sich mit der Klangqualität. 3D-Druck ist dafür geeignet, hier für Disruption zu sorgen. Die Anzahl der optimierbaren Elemente von einem Paar Ohrstöpsel oder Kopfhörer kann sehr hoch scheinen – Passung, Stabilität, Lärmreduzierung und Verschleißverhalten müssen berücksichtigt werden. Hinzu kommt natürlich noch die Klangqualität.
Im oberen Marktsegement sorgen individuelle In-Ear-Monitore für ultimative Isolierung und Komfort. Doch ihr arbeits- und kostenintensiver Herstellungsprozess führt dazu, dass sie nur Audiophilen oder Künstlern zugänglich sind. Dank digitalen Arbeitsabläufen und 3D-Druck können jetzt kostengünstige maßgefertigte Ohrstöpsel auf Nachfrage hergestellt werden.
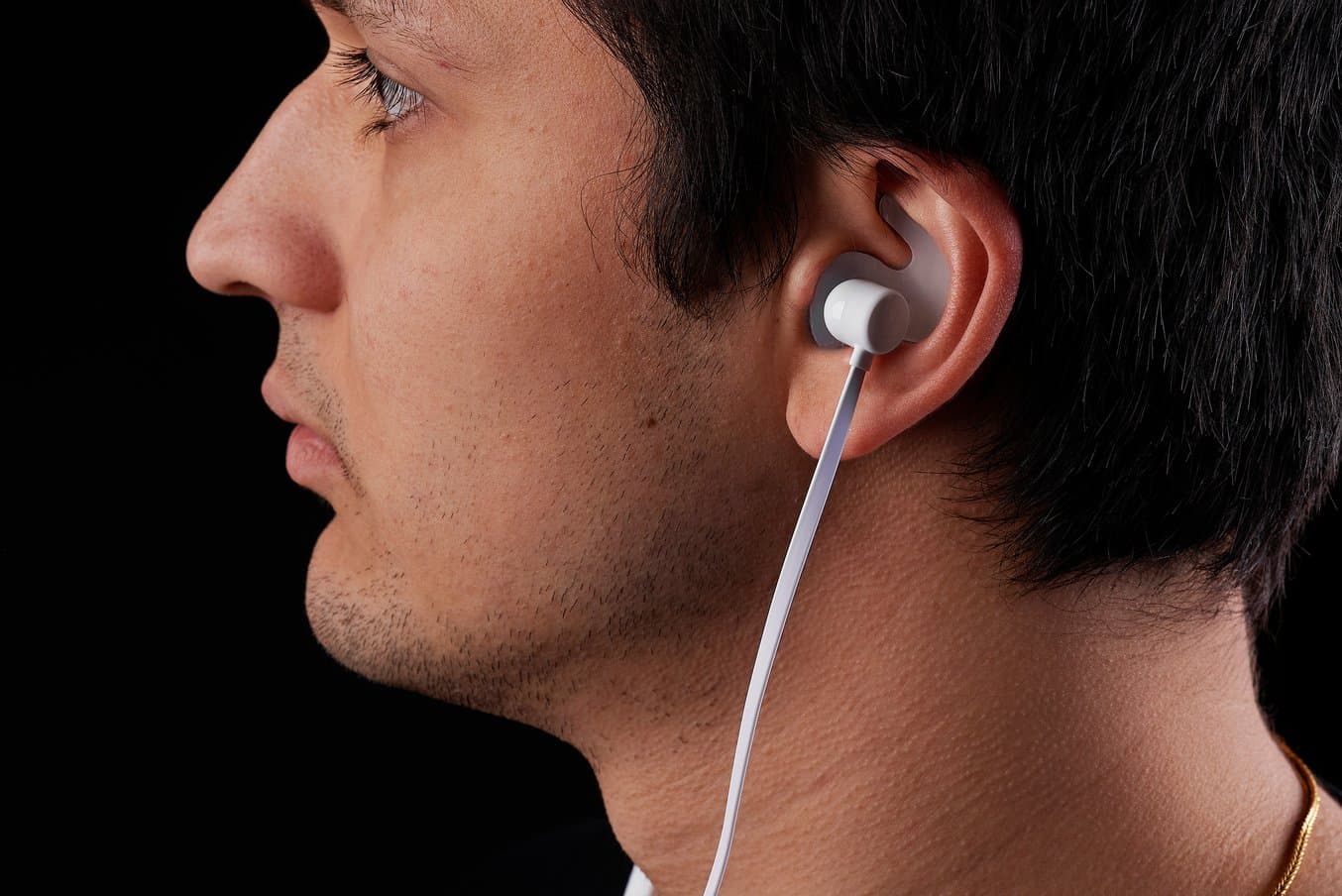
Maßgefertigte 3D-gedruckte Ohrstöpsel bieten die perfekte Passform, da die Ohren des Kunden zuvor präzise gescannt werden.
Zu Beginn des entsprechenden Verfahrens wird ein schneller, nicht-invasiver Digitalscan des Ohrkanals des Kunden angefertigt. Daraus entsteht eine genaue digitale Form. Audiologen können diese Form nutzen, um das Design der Ohrstöpsel-Aufsätze anzupassen. Dazu gehören auch ästhetische Anpassungen nach Kundenwunsch. Die Aufsätze können direkt 3D-gedruckt oder mit einer 3D-gedruckten Form gegossen und auf die Ohrstöpsel gesetzt werden. So entsteht ein maßgefertigtes Produkt, das in Sachen Leistung, Komfort und Benutzerfreundlichkeit seinen Gegenstücken aus der Massenfertigung um Längen voraus ist.
Ein glatterer Start in den Tag mit 3D-gedruckten Rasierern
Gillette ist zum Pionier bei 3D-gedrucktem Verbrauchsmaterial geworden, als das Unternehmen Ende 2018 das Konzept Razor Maker einführte. Das Projekt zeigte den Willen, nicht nur herkömmliche Produktionsabläufe zu verändern, sondern dem Kunden direkt 3D-gedruckte Produkte für die Endverwendung zu bieten, die zudem noch vollständig personalisiert werden können.
Rasierer waren bislang das Paradebeispiel für Wegwerfprodukte, die schlecht an die Nutzung angepasst sind (denken Sie nur an die ganzen Schrammen und Schnittwunden). Beim Razor Maker Programm wollte Gillette seine bewährten Rasierer als Grundlage nutzen und Kunden die Möglichkeit geben, ihren Geschmack und ihre Vorlieben einfließen zu lassen.
Mit dem Einsatz von SLA-3D-Druckern von Formlabs zur Fertigung bietet die Razor Maker Plattform Kunden die Möglichkeit, Rasierer mit individuellen 3D-gedruckten Griffen zu gestalten und zu bestellen. Es gibt eine wachsende Anzahl an verschiedenen grundlegenden Designs (48, Tendenz steigend). Davon ausgehend kann der Kunde mit der Individualisierung in den verschiedenen Farbvarianten und durch Hinzufügen von individuellem Text fortfahren.
Der Razor Maker von Gillette gibt Kunden die Möglichkeit, den Griff des Rasierers mit Hilfe von verschiedenen Designs, Farben oder eigenem Text individuell zu gestalten.
Durch die schichtweise Fertigung der Rasierergriffe fielen die Designbeschränkungen. Die Designer zogen Inspiration aus der Fülle der in Natur, Architektur und Technologie vorhandenen Geometrien und schufen so komplexe Formen, die mit konventionellen Fertigungsmethoden schwer oder gar unmöglich herzustellen wären.
Die Technologie kommt vollständig ohne Werkzeugbestückung aus, erfordert keinerlei Investitionen in Formen und negiert die traditionell exponentiellen Kosten für die Fertigung verschiedener komplexer Objekte. So kann Gillette seinen Kunden ultimative Wahlfreiheit zu einem konkurrenzfähigen Preis bieten.
Die Zukunft der Individualisierung
Von der anfänglichen Designphase bis hin zur Erstanwendung durch den Kunden kann 3D-Druck den Lebenszyklus eines Produkts tiefgreifend verändern.
Große Unternehmen setzen bereits auf die Möglichkeiten der digitalen Technologien und da diese Möglichkeiten beim 3D-Druck immer weiter wachsen, werden immer mehr Unternehmen versuchen, sie für ihr Geschäft zu nutzen. Da Individualisierung erschwinglich und einfach wird, sorgt der 3D-Druck auch bei Produkten aus der Serienfertigung für ein Kundenerlebnis der Spitzenklasse.