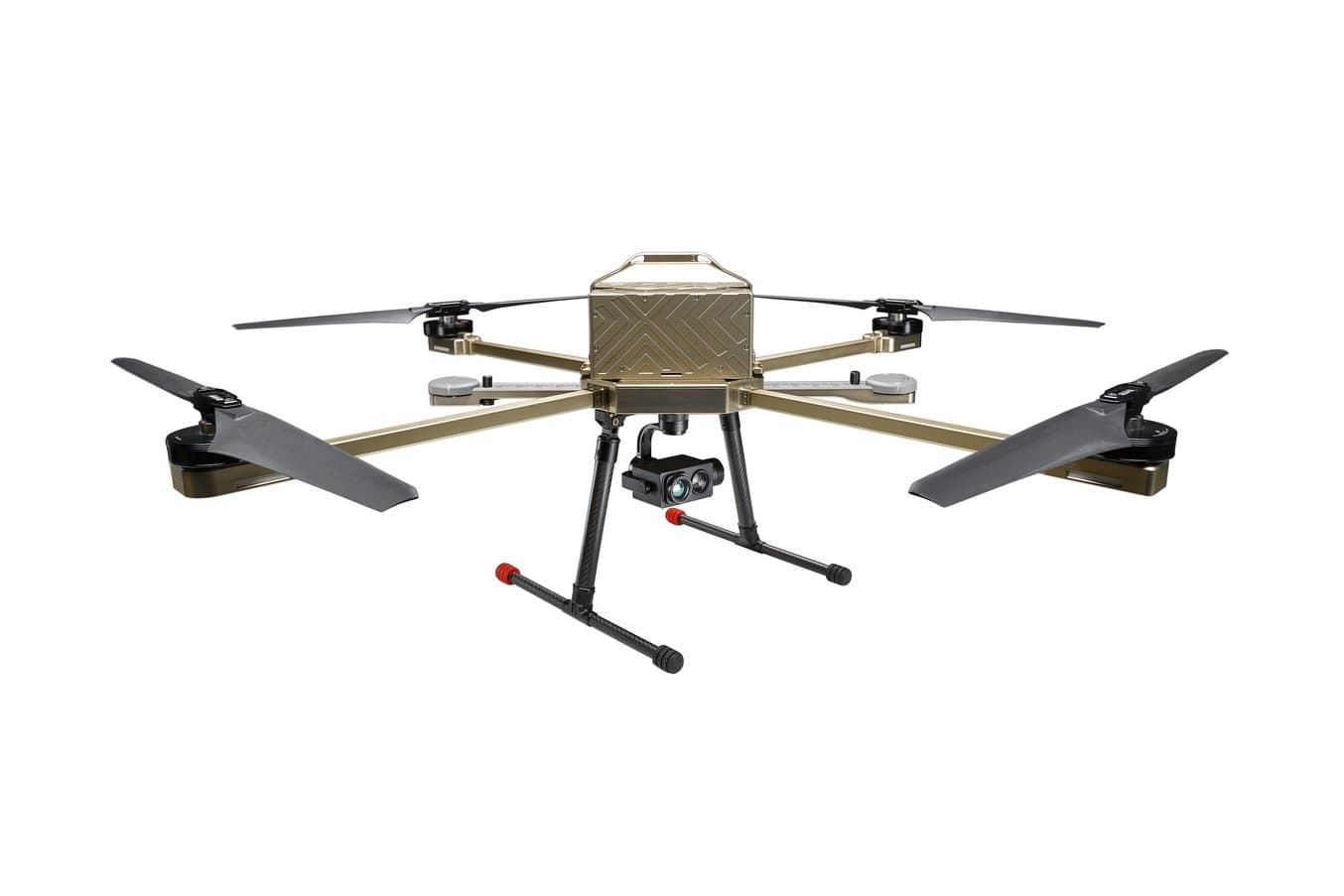
Naturkatastrophen, Militärinvasionen, Schiffsunglücle und Flugzeugabstürze... Bilder solcher Ereignisse ziehen die Aufmerksamkeit der ganzen Welt auf sich. Bei solchen Aufnahmen ist die Wahrscheinlichkeit groß, dass sie von einer relativ neuen Technologie gemacht wurden: nämlich Drohnen oder unbemannten Luftfahrzeugen (UAVs). Mit kontinuerlichen Fortschritten in der Drohnentechnologie setzen Hersteller die Grenzen dessen, wie weit, wie schnell und wie schwer ihre Maschinen fliegen können, ständig neu.
Nextech, ein in Südafrika ansässiger Drohnenhersteller, setzt SLS-3D-Drucker (selektives Lasersintern) von Formlabs ein, um für seine Kunden aus einer Vielzahl von Branchen individualisierte Hochleistungsdrohnen herzustellen. Die robusten, für die Endverwendung geeigneten SLS-Teile machen es Nextech möglich, die Entwicklung, den Prototypenbau und die Fertigung in einem einzigen rationalisierten Arbeitsablauf abzuwickeln.
Maschinenbauingenieur Liam Kroone hat sich mit uns über die Stärken dieses hybriden Arbeitsablaufs unterhalten, und darüber, wie der SLS-3D-Druck ihnen geholfen hat, sich in einer hart umkämpften Branche zu behaupten. „Der Prozess des 3D-Drucks macht es uns möglich, individuelle Anforderungen von Kunden zu erfüllen, neue Produkte zu entwickeln und Designs viel schneller zu verbessern“, so Kroone.
In diesem Beitrag erfahren Sie, wie Nextech mit SLS-3D-Druck folgende Ziele erreicht hat:
-
Millionen von Dollar für die CNC-Bearbeitung durch einen einzigen Fuse 1+ 30W zu ersetzen
-
Mit 3D-gedruckten Formen Carbonfaser-Flügelspitzen für Drohnen herzustellen
-
Maschinelle Bearbeitung, Kohlenstofffaser und SLS-3D-Druck zu kombinieren, um Gewicht und Festigkeit zu optimieren
Das Drohnen-Problem
Unbemannte Luftfahrzeuge werden schon seit Jahrzehnten eingesetzt, vor allem für militärische Überwachungs- und taktische Missionen. In Branchen wie der Landwirtschaft, dem Wildtiermanagement oder der Klimawissenschaft waren Drohnen aufgrund des hohen Kostenaufwands noch nicht weitläufig einsetzbar. Jeder Auftraggeber hat eigene Anforderungen – beispielsweise im Bezug auf die zu erwartende Lufttemperatur und die Wetterbedingungen, die Art der Kamera oder anderer Nutzlasten oder die Entfernung zwischen der Treibstoffquelle und dem Zielbereich. In den meisten Drohnenmodellen werden massenproduzierte Komponenten verbaut, aber die unterschiedlichen Details führen unweigerlich zu einem gewissen Maß an Individualisierung.
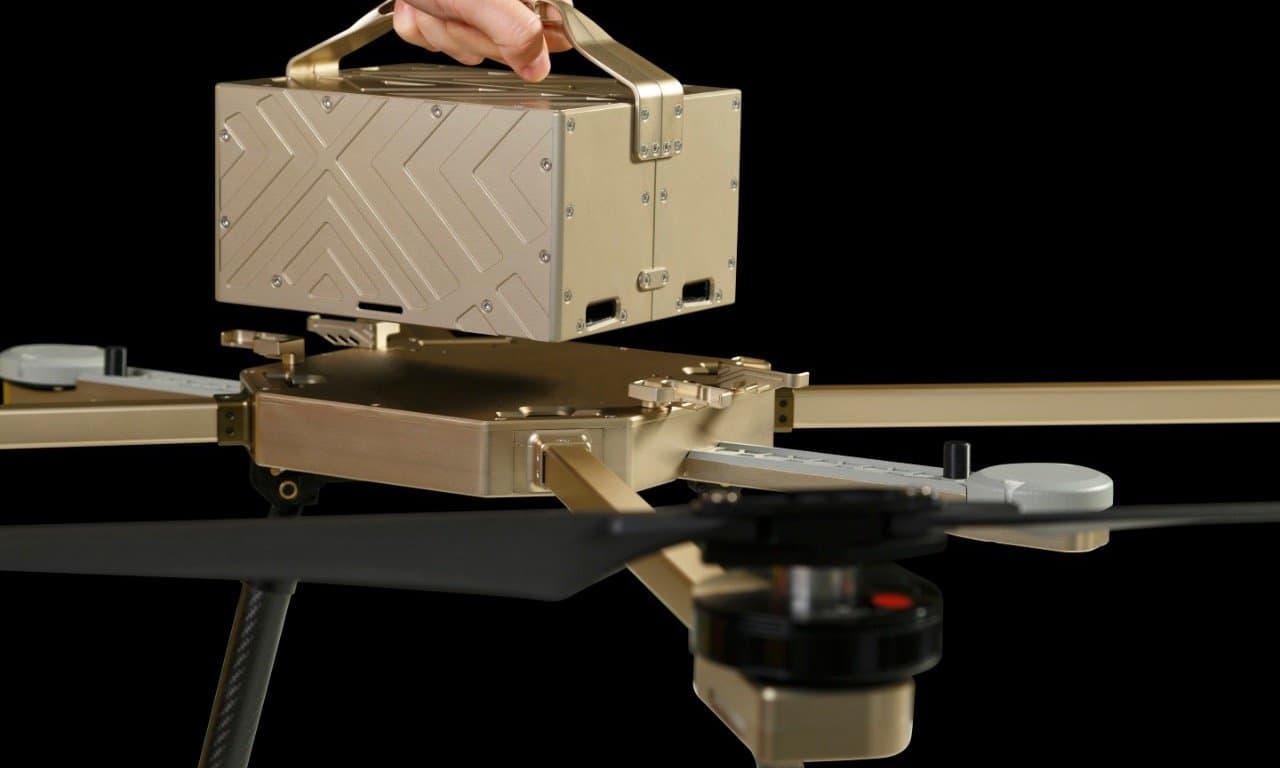
Das schwerste Teil einer Drohne ist oft das Batteriegehäuse. Nextech nutzt daher den 3D-Druck, um das Gewicht anderer Komponenten zu optimieren, sodass die Drohnen weiter fliegen können, ohne an Stärke oder Nutzlast einzubüßen.
Solche Anpassungen sind mit herkömmlichen Fertigungstechniken schwierig – die Herstellung von Formen, die maschinelle Bearbeitung oder Wasserstrahl- und Laserschneidverfahren sind teuer, insbesondere bei komplexen Geometrien. Der 3D-Druck hat Drohnenherstellern die Möglichkeit eröffnet, komplexe Geometrien und kundenspezifische Produkte kostengünstig herzustellen, doch die schwierige Wahl zwischen den Technologien und Materialien hat die Etablierung des Verfahrens beeinträchtigt. Der SLS-Workflow mit dem Fuse 1+ 30W ermöglicht Nextech eine schnelle Prototypenfertigung, verbessert den Iterationsprozess durch Kundenfeedback und erlaubt eine kostengünstige Serienproduktion von kundenspezifischen Komponenten.
SLS im eigenen Haus
Bevor Nextech seine Fertigungskapazitäten um den SLS-Drucker Fuse 1+ 30W erweiterte, wurden 3D-Drucke ausgelagert oder Prototyping-Komponenten durch Zerspanung gefertigt. „Wir hatten Chargen von kleinen 3D-gedruckten Komponenten, die an der örtlichen Universität auf großen industriellen EOS-Maschinen gedruckt wurden, aber es dauerte Wochen, bis wir sie geliefert bekamen“, erinnert sich Kroone.
Indem das Team den 3D-Druck in den eigenen Betrieb verlagerte, konnte es seine Entwicklungszeit verkürzen und enger mit Kunden zusammenzuarbeiten. „Wir setzen für Kunden einzigartige Projekte um, also müssen wir Prototypen möglichst schnell erstellen. Dabei handelt es sich aber um komplizierte, detaillierte Teile mit hochwertiger Oberfläche“, erklärt Kroone und ergänzt: „Wir fügen Halterungen hinzu und testen die Festigkeit, die Haptik und das Gewicht, oder wir fügen eine Dichtung für eine bessere Isolierung hinzu und testen die Passform und die Tauglichkeit, um sicherzustellen, dass die endgültige Lösung, die wir an die Kunden schicken, von hoher Qualität ist.“
Mit Outsourcing war dieser iterative Rhythmus nicht aufrechtzuerhalten. Wenn das Team Tage oder Wochen auf die Arbeit an einer Iteration warten musste, rückte die Lieferfrist zu nahe und die Anzahl der möglichen Funktionstests wurde eingeschränkt. „Mit einem betriebsinternen Drucker kann man das Volumen wirklich erhöhen und die Materialnutzung optimieren. Wir können unsere Kunststoffteile produzieren, ohne Spritzgussformen herstellen zu müssen, die sehr teuer sind und viel Zeit in Anspruch nehmen“, sagt Kroone.
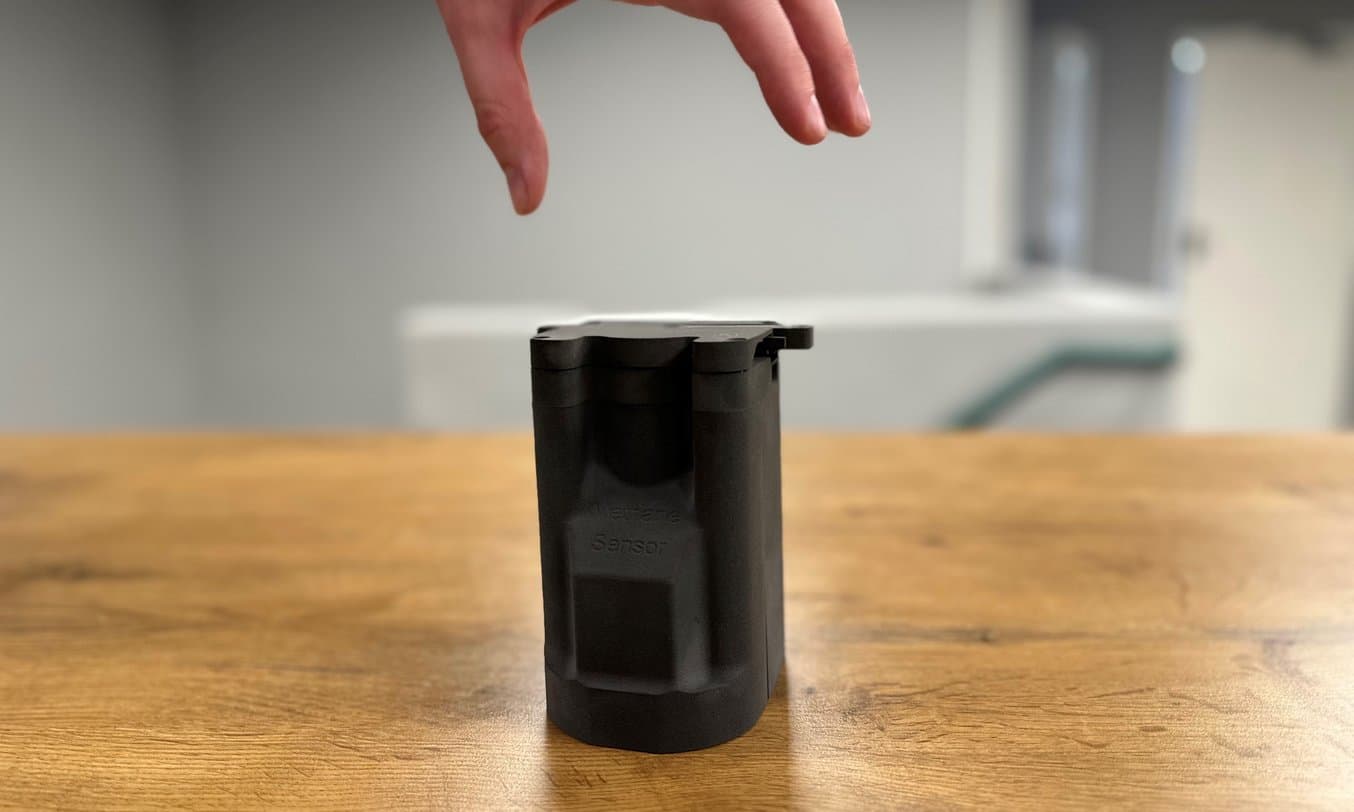
Ein kundenspezifischer Methansensor, gedruckt mit Nylon 12 Powder auf dem SLS-3D-Drucker Fuse 1+ 30W. Durch die In-House-Produktion konnten die Entwicklungs- und Herstellungskosten gesenkt werden.
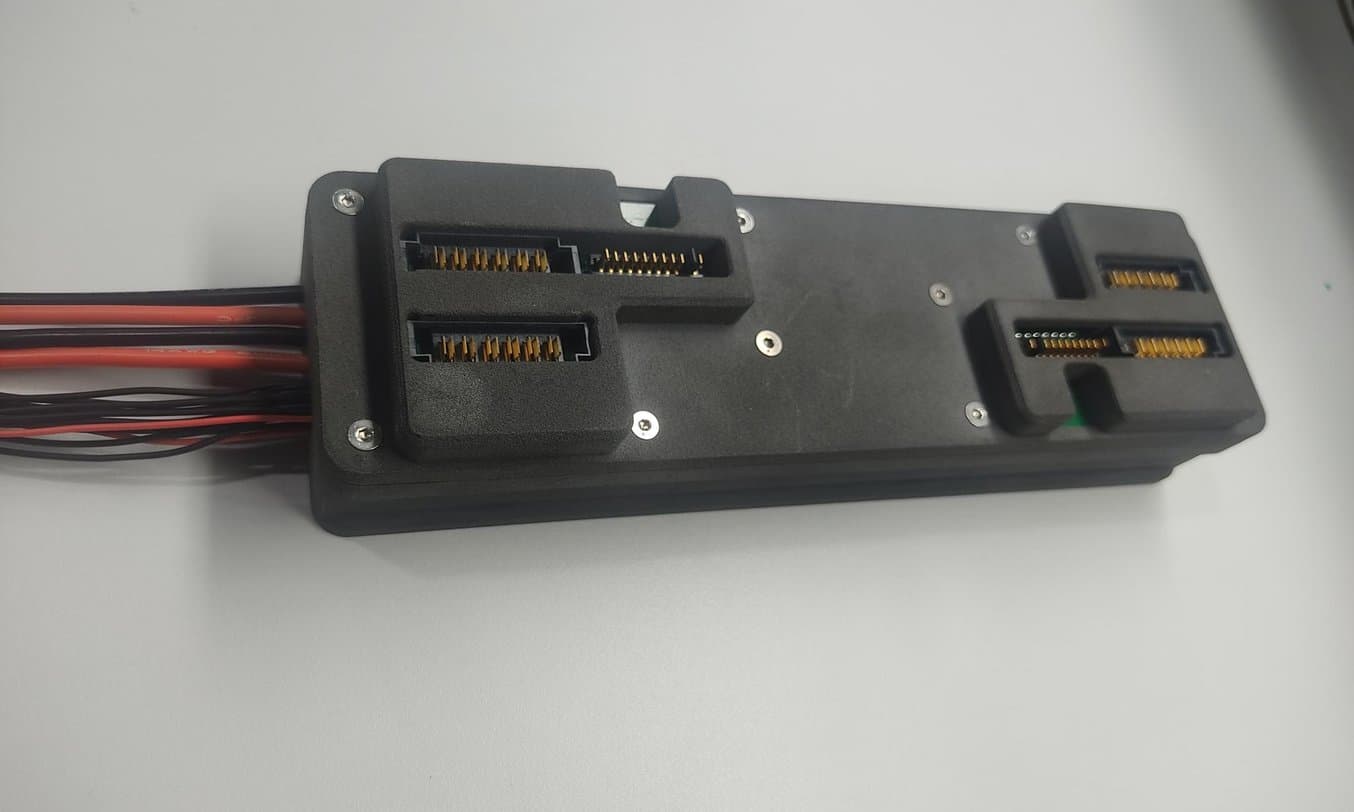
Auch dieses kundenspezifische Batterieladegerät wurde auf dem Fuse 1+ 30W aus Nylon 12 Powder gedruckt. Durch die betriebsinterne Produktion ist Nextech flexibler geworden und kann besser auf die Designwünsche seiner Kunden eingehen.
Komplexe Teile durch Technologien, die sich ergänzen
Die speziellen Frachten der Kunden, wie z. B. verschiedene Arten von Kameras oder Sensoren für die Landwirtschafts-, Umwelt- oder Wildtierüberwachung, erfordern maßgefertigte Halterungen, um sie am Rahmen der Drohne zu befestigen. Diese Halterungen können bei jedem Projekt anders aussehen, wobei die Last manchmal weiter von der Brennstoffquelle entfernt angebracht wird, da diese sich über lange Strecken erhitzen kann, oder auch in einem anderen Winkel gehalten wird. Zur Entwicklung und Herstellung dieser Halterungen, die fest und haltbar sein müssen, verwendet Nextech eine Kombination aus SLS-3D-Druck, Verbundwerkstoffen und maschineller Bearbeitung. Ihre Stärke ist dabei, dass die Technologien einander ergänzen, nicht ersetzen.
„Die Mischung aus traditioneller Zerspanung und SLS-3D-Druck hat das hervorgebracht, was ich für die nächste Generation der Fertigung überhaupt halte.“
Liam Kroone, Maschinenbauingenieur bei Nextech
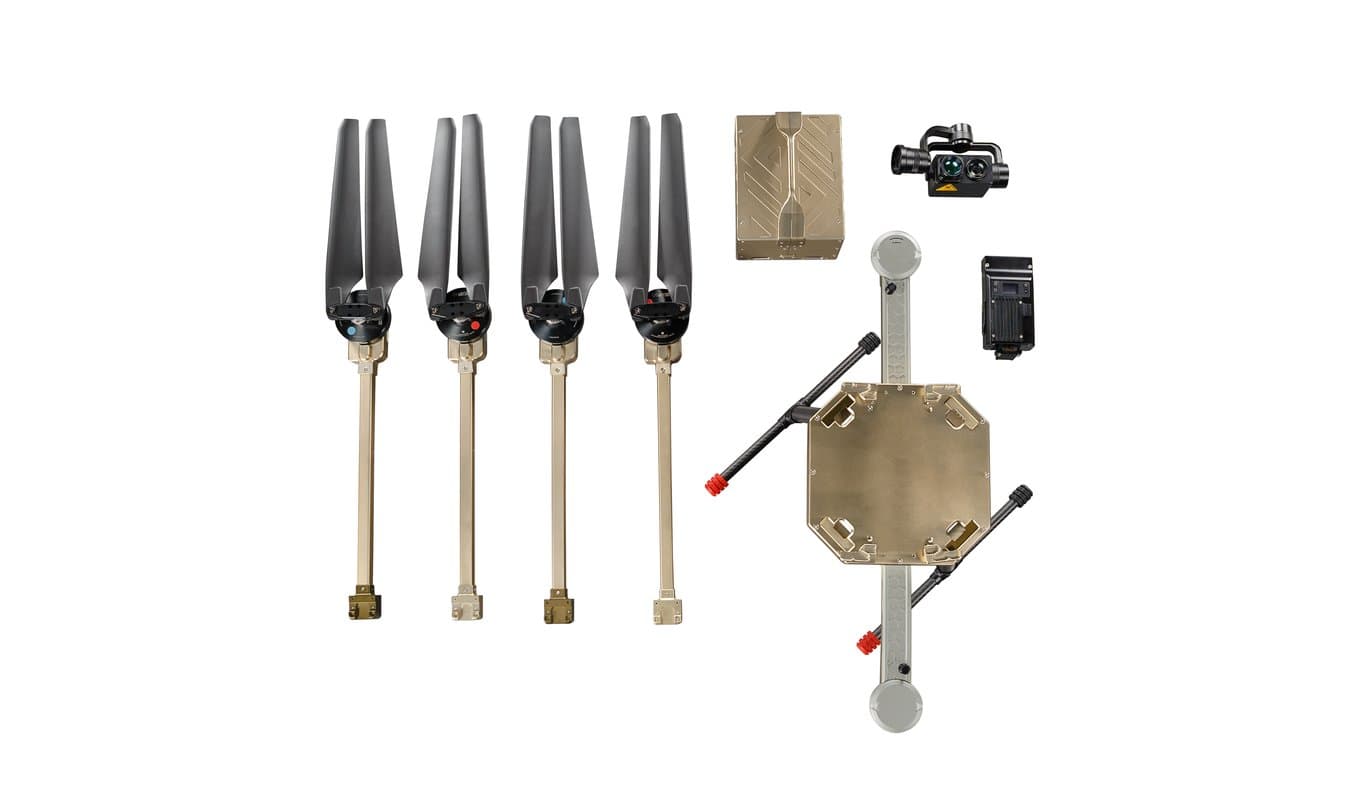
Das Quadcopter-Modell Atlas T verwendet eine Kombination aus 3D-gedruckten SLS-Teilen (Antennenblätter und Abdeckungen von Gimbal und Methansensor), maschinell bearbeiteten Metallteilen und Carbonfaserteilen, um die Nutzlast zu optimieren und einzigartige Geometrien mit Spitzenleistung zu ermöglichen.
Das Messen der Schmelze
Eines der Modelle von Nextech ist eine Starrflügel-Drohne mit einer Spannweite von 3,2 Metern und einer Reichweite von 100 Kilometern. Für ein Projekt der französischen Regierung machte die Drohne einen Flug zur Aufnahme und Vermessung der schrumpfenden Eiskappen in der Arktis. Die Drohne war mit Aufnahmegeräten für Multispektralbilder und spezielle Wärmebildaufnahmen ausgestattet, um den Einfluss des Ozeans auf die Geschwindigkeit des Abschmelzens der Eiskappen zu messen. Das Nextech-Team musste individuelle Halterungen und Gehäuseteile entwickeln, um die empfindliche Fracht zu transportieren, sowie Flügelspitzen, die unter den extremen Bedingungen funktionieren.
„Wenn sich die Masse der Drohne oder die Umgebung ändert, muss sich auch das Profil der Flügelspitze ändern. Während der Prototypingphase, in der sich diese Variablen ändern können, ist die maschinelle Bearbeitung sehr teuer, bevor wir genau wissen, wie die Drohne funktionieren wird“, erläutert Kroone.
Die endgültigen Flügelspitzen werden aus einem Kohlenstofffaser-Verbundwerkstoff hergestellt, aber die Herstellung von Formen für solche Verbundwerkstoffe ist zeitaufwändig und die Zerspanung zu teuer. Die Verwendung von Nylon 12 Powder auf dem Fuse 1+ 30W ermöglicht es dem Team, mit komplexen Formen zu experimentieren, wobei die Teile ein ähnliches Gewicht haben wie die späteren Carbonfaserteile.
„Wenn man versucht, so etwas aus Aluminium oder sogar aus Kohlefaser herzustellen, wäre es ziemlich kompliziert, die Formen in den frühen Phasen eines Projekts richtig hinzubekommen. Mit dem Fuse 1+ 30W sind wir in der Lage, verschiedene Versionen auszuprobieren, und wenn sich das Projekt ändert, können wir mit wenig Aufwand ein neues Design drucken“, sagt Kroone.
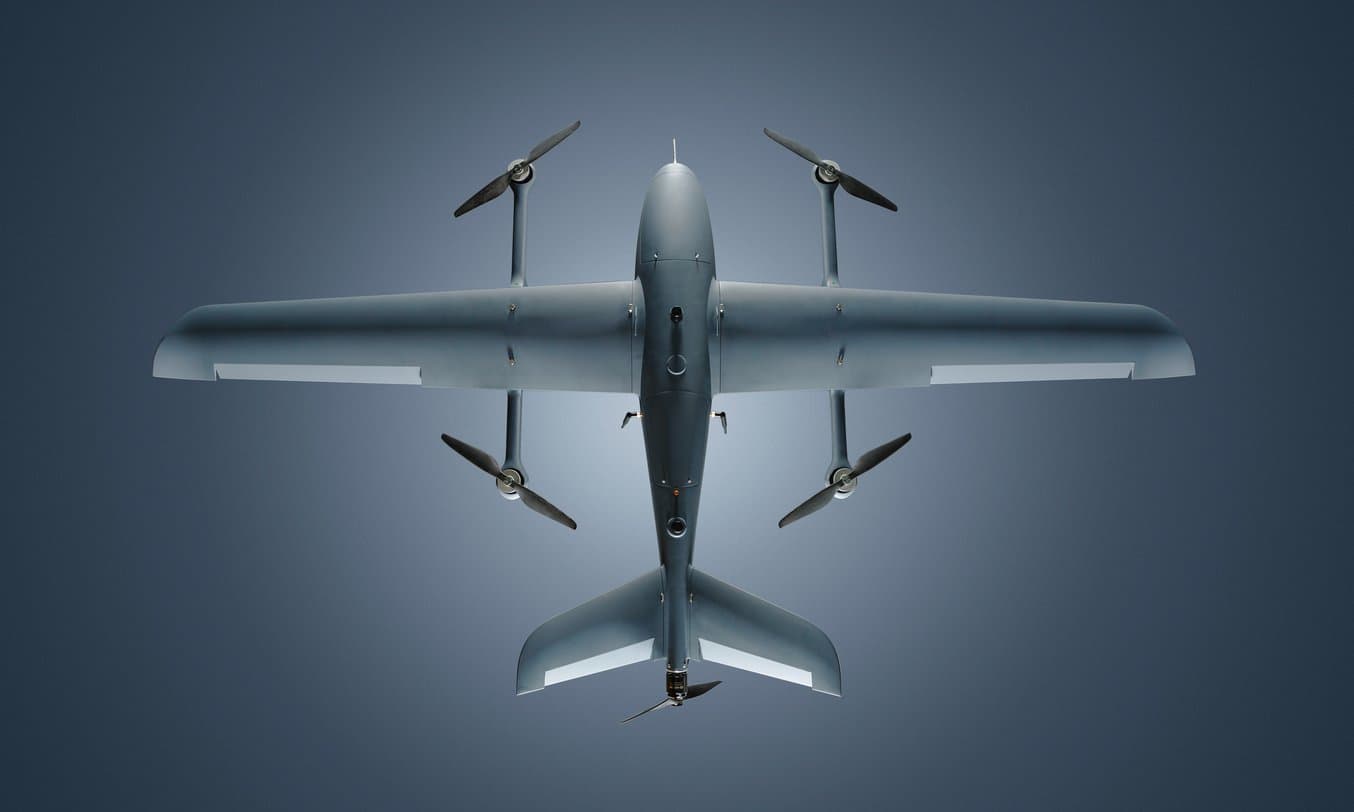
Dieses Rendering von Nextechs Starrflügel-Drohne zeigt den Umfang und die Komplexität des Designs.
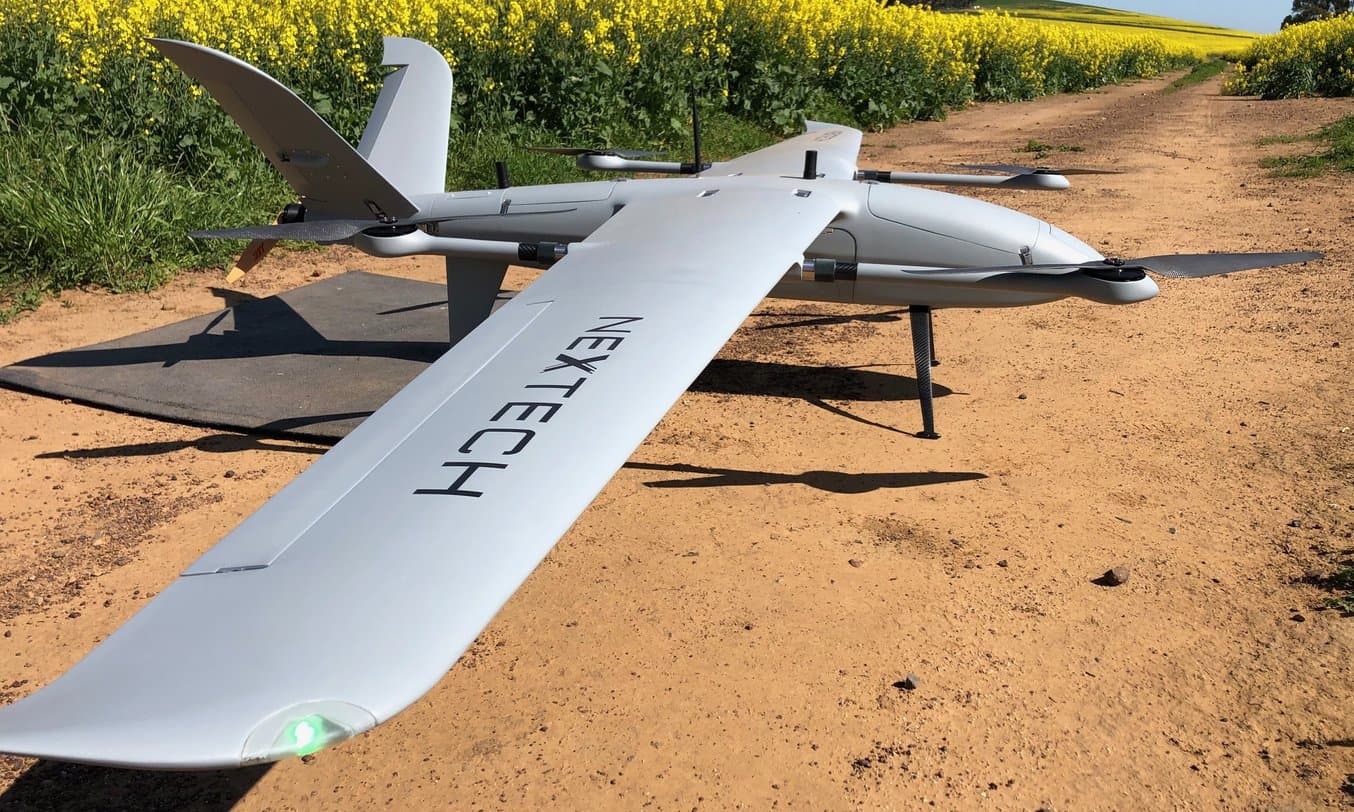
Das Nextech-Team stützte sich auf einen Designprozess mittels Carbonfaserformen, die auf dem Fuse 1+ 30W aus Nylon 12 Powder gedruckt wurden. So konnte es schnell funktionale Flügelspitzen für die Starrflügel-Drohne iterieren und testen.
100 auf einen Streich: Endverbrauchsteile in der Serienproduktion
Für die Atlas T, eine Drohne im Multirotor-Stil, hat das Team mehrere Designs erarbeitet, um die Übertragungstechnik in bestimmten Winkeln und Abständen zu halten. Die Art und Weise, wie das Gerät gehalten wird, wirkt sich auf seine Leistung aus. Wenn GPS und Antenne richtig positioniert sind, erhöht sich die Reichweite und die Qualität der Übertragung. Die Antennentechnologie für große Entfernungen darf nicht durch leitende, sperrige Materialien behindert werden. Um sowohl die Lastenhalterungen als auch die Antenne individuell anpassen zu können, sind daher komplexe Geometrien und viele iterative Testrunden mit einem nicht leitenden Material erforderlich.
Kroone nutzte den Fuse 1+ 30W, um intelligente Batterie-Locator mit Einrastfunktion zu entwickeln. Es gab sowohl Außen- als auch Innenkomponenten für die Endanwendung in der Drohne, die aus Nylon 12 Powder gedruckt wurden. Die Größe der internen Komponenten und das hohe Volumen machten eine effiziente Programmierung auf der CNC-Maschine schwierig. „Es handelte sich um kleine Teile, für die das Setup auf einer CNC-Maschine viel Zeit in Anspruch genommen hätte. Aber mit dem Fuse 1+ 30W können wir 100 Stück auf einmal drucken“, berichtet Kroone.
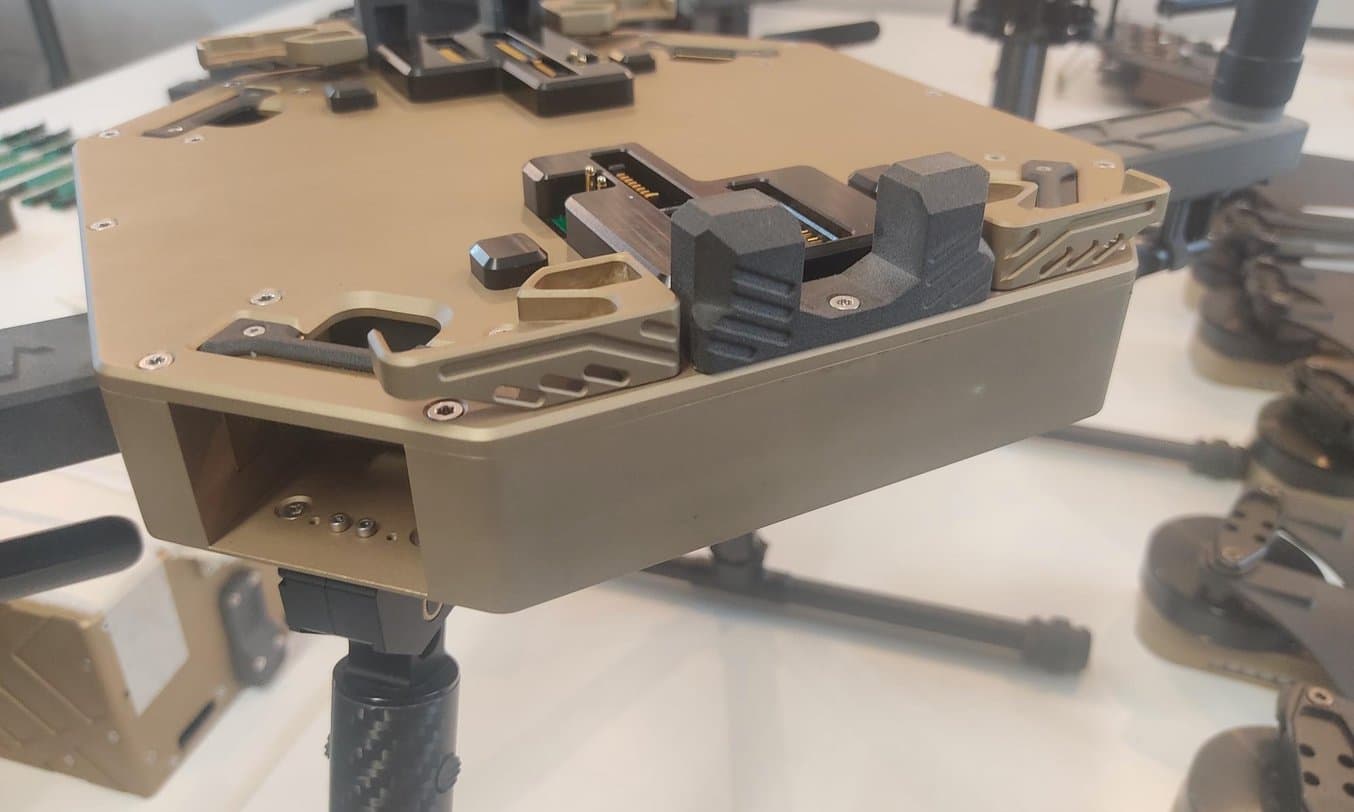
Der Batterie-Locator des Atlas T Quadcopters wurde mit dem SLS-Drucker Fuse 1+ 30W aus Nylon 12 Powder 3D-gedruckt.
Ein Durchsatz, der mit Millionen-Dollar-Equipment mithält
Die Kombination von SLS- und CNC-Technologien gibt Nextech mehr Flexibilität im Design- und Fertigungsprozess. Das Team ist in der Lage, mit dem Fuse 1+ 30W die Serienproduktion und Fertigung komplexer Geometrien abzuwickeln und hochfeste Aluminiumteile für andere Komponenten zeitgleich spanend zu fertigen. Bei Auswahl eines SLS-Druckers war es wichtig, ein Gerät zu finden, das die Qualität der CNC-Maschinen erreichen konnte. Mit dem Fuse 1+ 30W hat das Team die richtige Lösung gefunden. „Es ist wirklich ein wunderbares Stück Technik. Wir haben Millionen von Dollar für CNC-Maschinen ausgegeben, und die Produktionskapazität [des Fuse 1+ 30W] ist die gleiche, dabei ist es ein 60000-Dollar-Gerät“, so Kroone.
Mit jedem erfolgreichen Einsatz einer Nextech-Drohne wächst die Bekanntheit und die Kundennachfrage. Deshalb muss sich Nextech darauf verlassen können, dass der Fuse 1+ 30W konstant und reibungslos funktioniert. „Wiederholbarkeit und Zuverlässigkeit sind sehr wichtig, um sicherzustellen, dass wir qualitativ hochwertige Drohnen in einem kurzen Zeitrahmen herstellen können. Viele SLS-Drucker sind für Druckfehler und Druckabbrüche bekannt, aber der Fuse 1+ 30W ist ein hochwertiges Gerät mit großartigem Support“, berichtet Kroone. Die Zuverlässigkeit des Druckers selbst und Formlabs' Engagement für erstklassigen weltweiten Support unterstützen das Team dabei, die Produktion aufrechtzuerhalten.
Die Drohnenbranche ist extrem wettbewerbsintensiv, und große Aufträge aus den Bereichen Regierung, Forschung und Landwirtschaft sind bei den Unternehmen stark umkämpft. Um an der Spitze zu bleiben, müssen Drohnenhersteller ihre Technologie ständig aktualisieren und individualisierbare Optionen für jedes Projekt anbieten. Durch die 3D-Technologie und betriebsinterne Produktionskapazitäten mittels SLS und CNC-Bearbeitung hebt Nextech sich aus der Masse ab.
„Ich würde sagen, ein Unternehmen, das nicht über ein solches System für die Serienfertigung verfügt, weiß wirklich nicht, was es in Zukunft tun wird – man stellt sich selbst ein Bein, wenn man seine Produktionskapazitäten nicht intern auf Abruf verfügbar hält.“
Liam Kroone, Maschinenbauingenieur bei Nextech
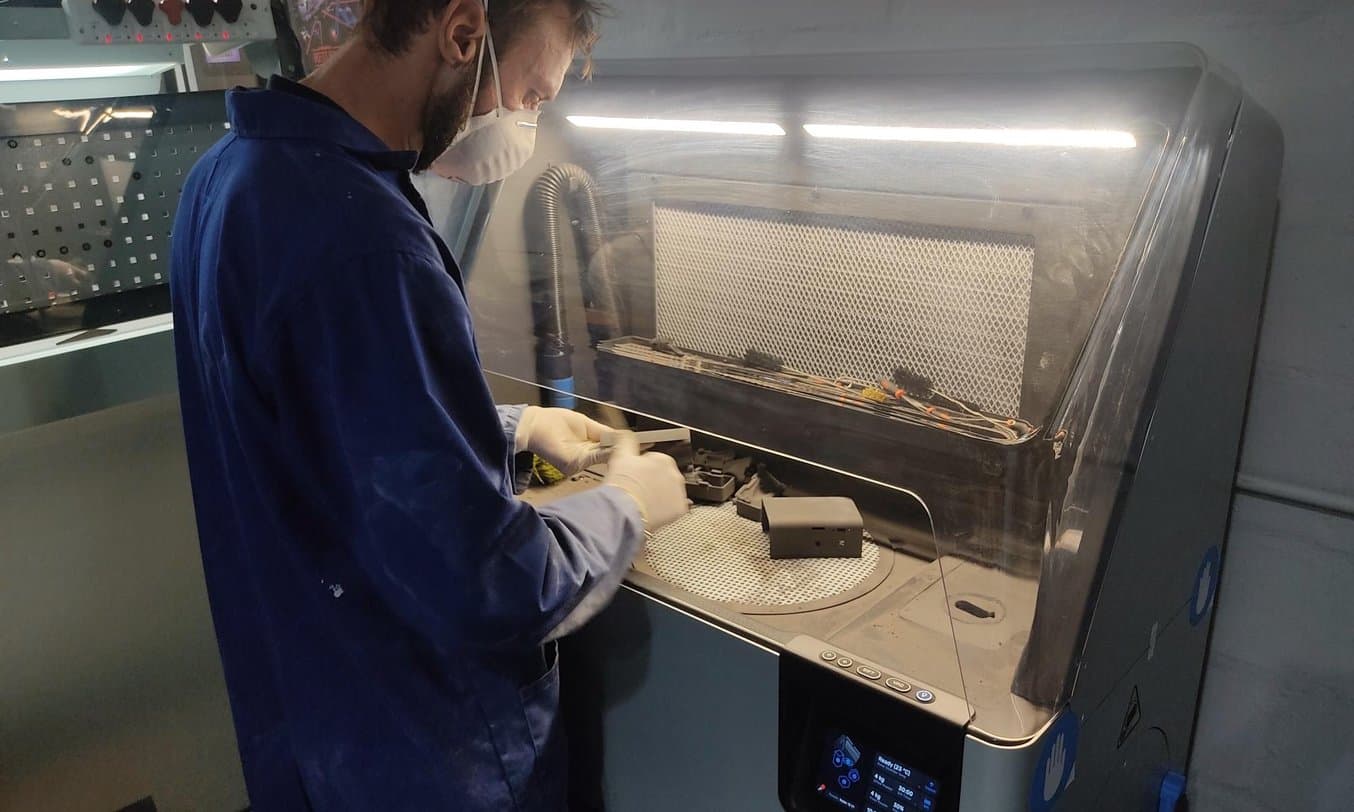
Der Fuse Sift ermöglicht einen sicheren und effizienten Arbeitsablauf für die Entnahme von Teilen und das Recycling von Material.
Durch die Kombination konventioneller Fertigungstechnologien mit fortschrittlichen additiven Arbeitsabläufen im eigenen Betrieb hat sich Nextech einen Platz an der Spitze der Drohnenindustrie verschafft. Die Zuverlässigkeit der SLS-Drucker der Fuse-Serie von Formlabs verhilft dem Unternehmen dazu, flexibel zu bleiben, auf Änderungen der Zulieferer und auf Kundenwünsche zu reagieren und sein Produkt ständig zu verbessern.
Besonderen Dank an unseren südafrikanischen Vertriebspartner BuildVolume für die Beratung und Unterstützung von Nextech mit den 3D-Drucklösungen von Formlabs.