Wie eine Schweizer Brillenmanufaktur SLS 3D-Druck zur Herstellung hochwertiger Brillen einsetzt
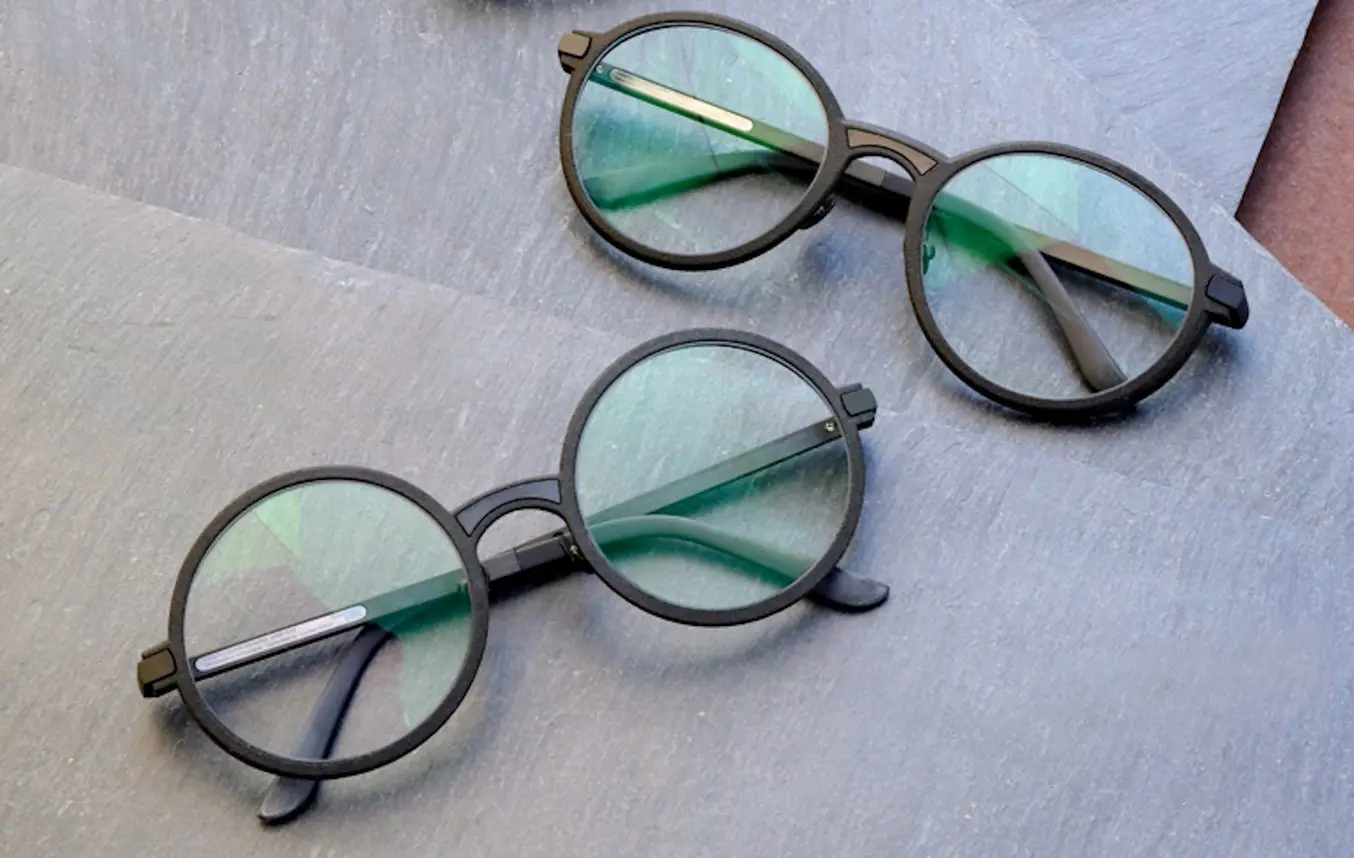
Durch ihre hochwertige und extravagante Materialauswahl, penible Handarbeit und fortwährend neuen innovativen Ideen, setzten sich die Brillengestelle der Marcus Marienfeld AG von konventionellen Brillengestellen deutlich ab.
Inhaber Marcus Marienfeld ist schon seit seinen Jahren als Goldschmied stets auf der Suche nach Innovation und Herausforderung, wenn es um das Design und die Herstellung neuer Accessoires geht.
Zuletzt integrierte er mit dem Fuse 1 den SLS 3D-Druck in die Produktionslinie seiner Brillengestelle in seinem Schweizer Atelier. Dieser wird bei Marcus Marienfeld für den Druck von Endverbrauchsteilen sowie für das Rapid Tooling von Werkzeugen zum Formen von Titan genutzt.
In diesem Interview mit Marcus Marienfeld spricht er leidenschaftlich über seine ersten Schritte mit dem SLS 3D-Druck, die Vorteile, die er dadurch in der Serienfertigung und auch bei Spezialanfertigungen hat und wieso ihm das Nylonmaterial von Formlabs so zusagt.
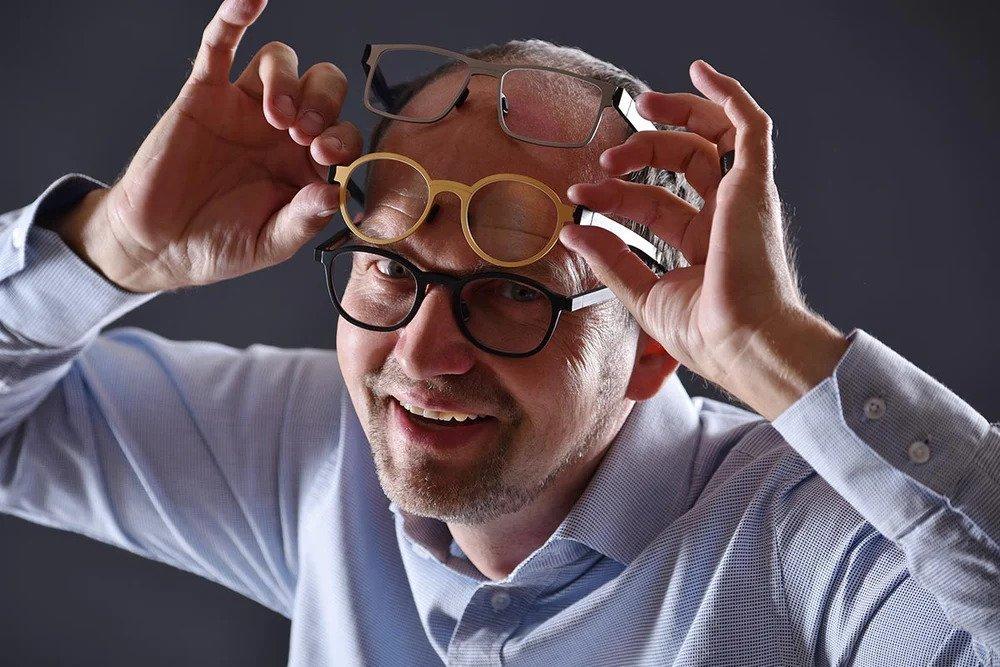
SLS-3D-Druck zur Herstellung hochwertiger Brillen
In diesem Webinar erfahren Sie von Marcus Marienfeld, Designer und Unternehmer, wie SLS-3D-Druck Endverwendungsteile für exklusive Brillengestelle sowie kostengünstige Betriebsmittel ermöglicht.
Von der Goldschmiede zur Brillenmanufaktur
Marcus Marienfeld kam als Goldschmied in seine heutige Heimat, die Schweiz. Schnell hat er in seiner Branche das Potenzial gesehen, die herkömmlichen und meist veralteten Produktionstechniken zu verändern, ja sogar zu revolutionieren.
Seine Mission war es nicht nur Technologie in das Schmuckdesign einzubringen, sondern auch in dessen Produktion.
Angefangen hat er mit einem Unternehmen, welches sich mit der Entwicklung von Schmuckkollektionen beschäftigte. Das Besondere: Bei Marienfeld wurde schon immer so viel wie möglich in das eigene Haus geholt und von Hand gefertigt, von der Zeichnung über den Modellbau bis hin zur Umsetzung und Produktion.
So war ihm ebenfalls schnell klar, dass ihm die 3D-Drucktechnologien Türen zu modernen Produktionsverfahren öffnen, die sich bis heute auch nicht wieder geschlossen haben. Schon seit der Markteinführung des Form 1 im Jahr 2013 druckt Marienfeld mit Formlabs 3D-Druckern und erfindet sich und seine Produkte immer wieder neu.
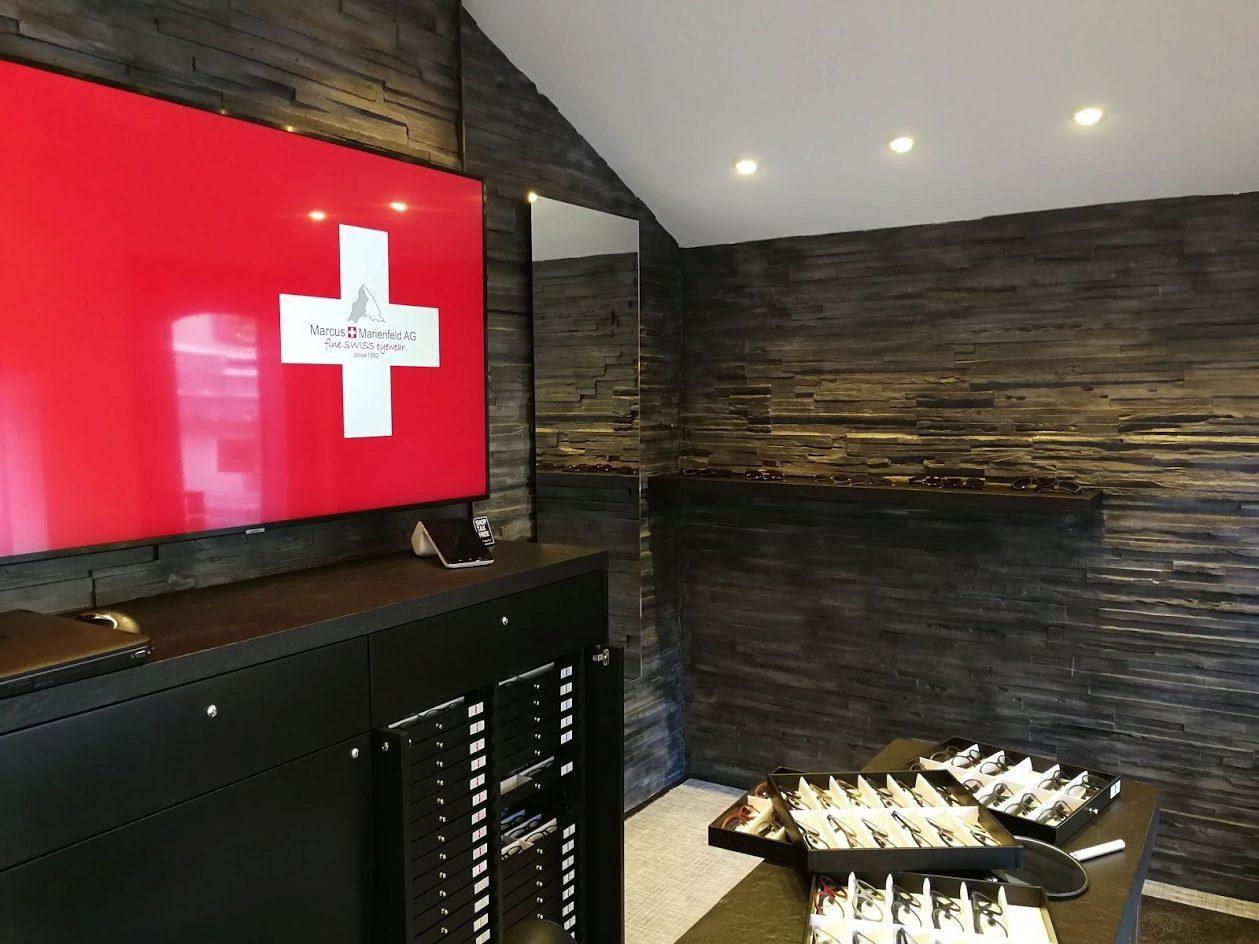
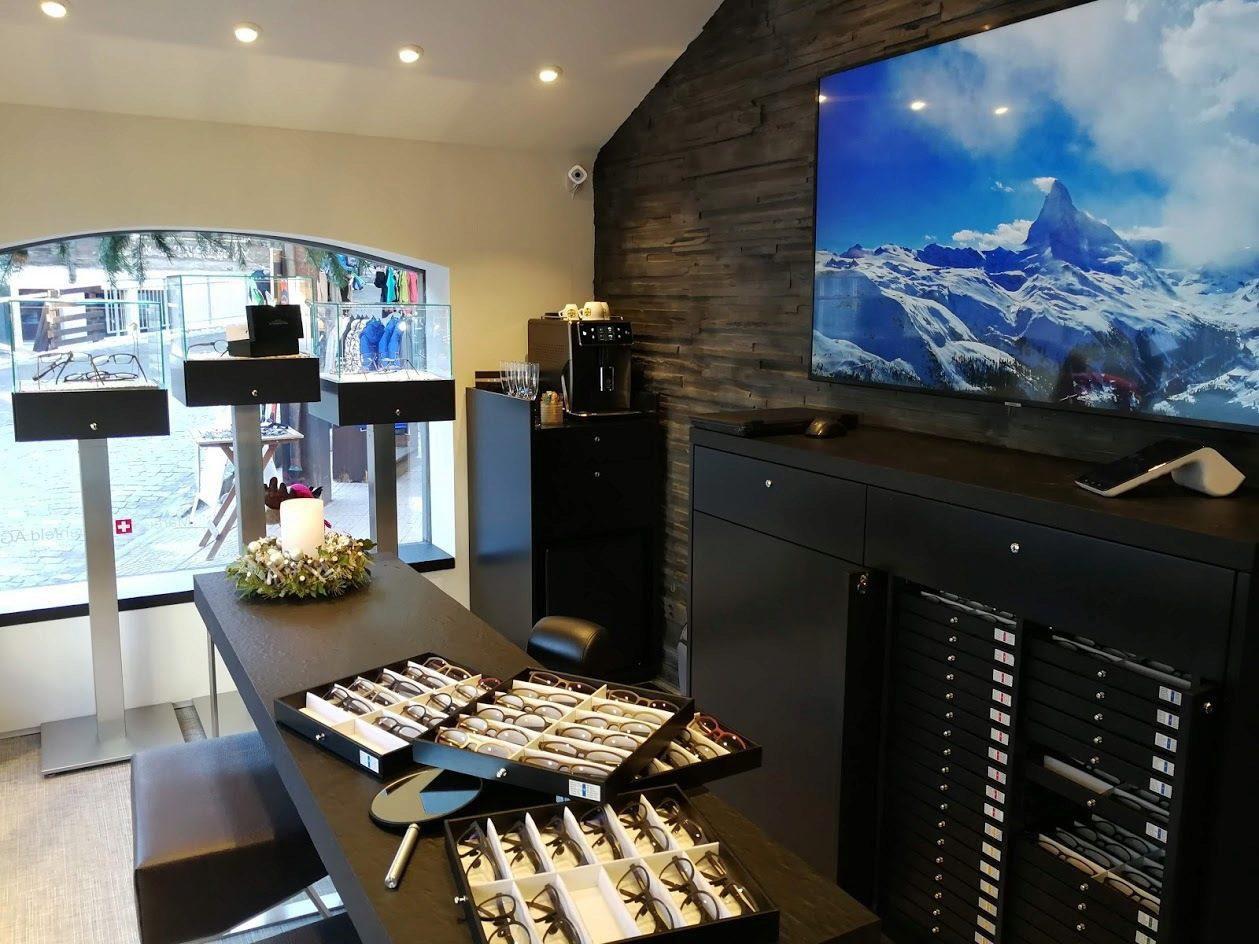
Als Goldschmied nutze er zunächst lange den SLA 3D-Druck für das Rapid Prototyping von Schmuck und Accessoires, bevor die Entwürfe auf einer CNC Maschine programmiert wurden.
Heute verwendet Marienfeld vorrangig den SLS 3D-Druck in seinem Expertengebiet - der Brillenmanufaktur. So integriert sein Unternehmen zum einen das Formlabs Nylonmaterial in seine raffinierten und hochwertigen Brillengestellen, zum anderen nutzt das Unternehmen das Nylon 11 Powder aber auch für die Herstellung von individuellen Werkzeugen für seine Manufaktur.
“Meine Grundidee ist, dass alles autark funktionieren kann, um sehr genau auf Prozesse Einfluss nehmen zu können und stets flexibel zu bleiben. Ein 3D-Drucker den ich mir selbst ins Haus holen kann erfüllt genau diese Vision.”
Marcus Marienfeld
Brillen in Serienfertigung auf dem Fuse 1
Seit diesem Jahr integriert die Marcus Marienfeld AG mithilfe ihres eigenen Fuse 1 SLS 3D-Druckers immer häufiger Nylon in die ausgefallene Materialauswahl ihrer Luxusbrillen. Diese reicht von Karbon und Titan über Büffelhorn bis hin zu dem Holz alter Barriquefässer.
“Unsere Brillen sind anders als die, die sonst da draußen sind”, so Marienfeld.
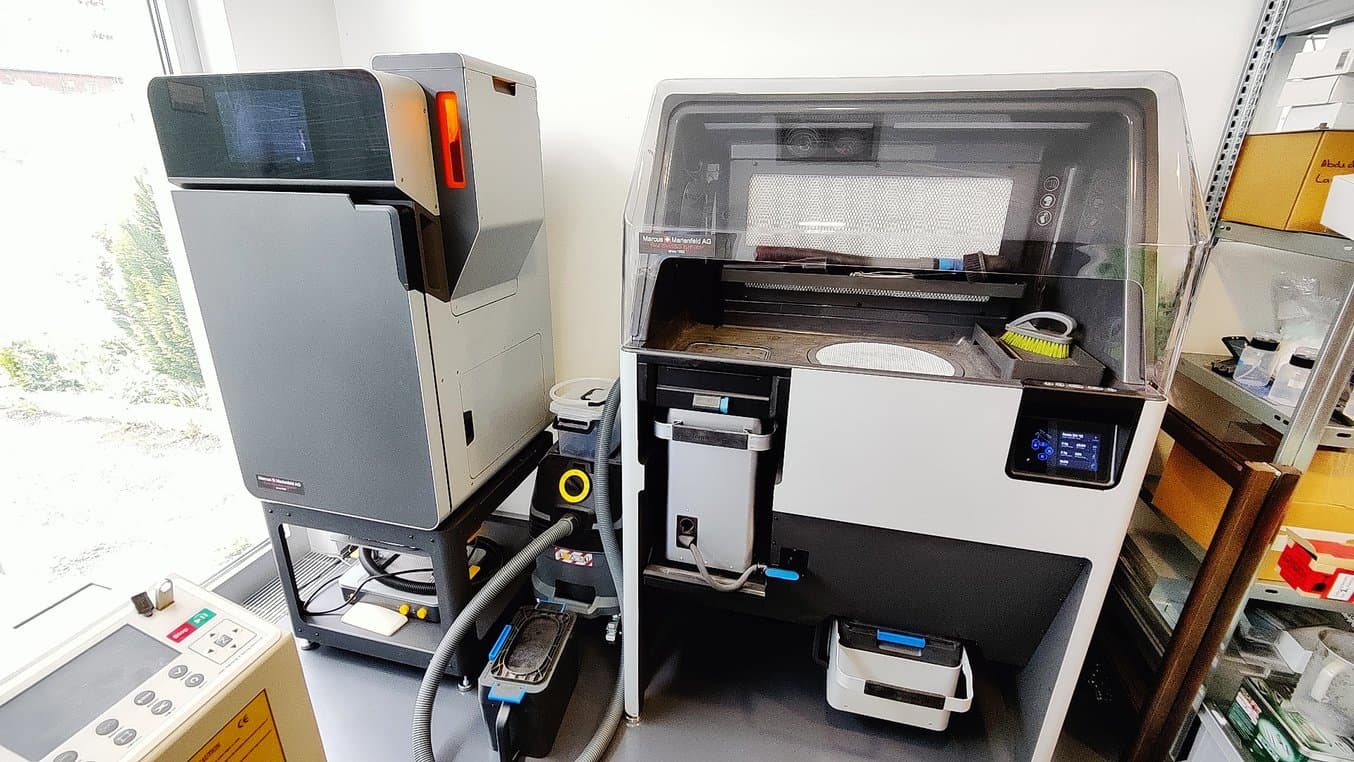
Mit dieser Ambition entschied er sich das Formlabs Material Nylon 11 Powder in seine Brillendesigns zu integrieren. Zunächst wurden viele unterschiedliche Entwürfe vorwiegend von Brillenfronten, gedruckt auf dem Fuse 1, im Marienfeld Atelier getestet. Vor Kurzem nutze man dessen Baukammer dann das erste Mal für eine Serie. Ganze 80 fertige Brillenfronten konnten in einem Druck in einer Zeitspanne von ca. 1,5 Tagen produziert werden.
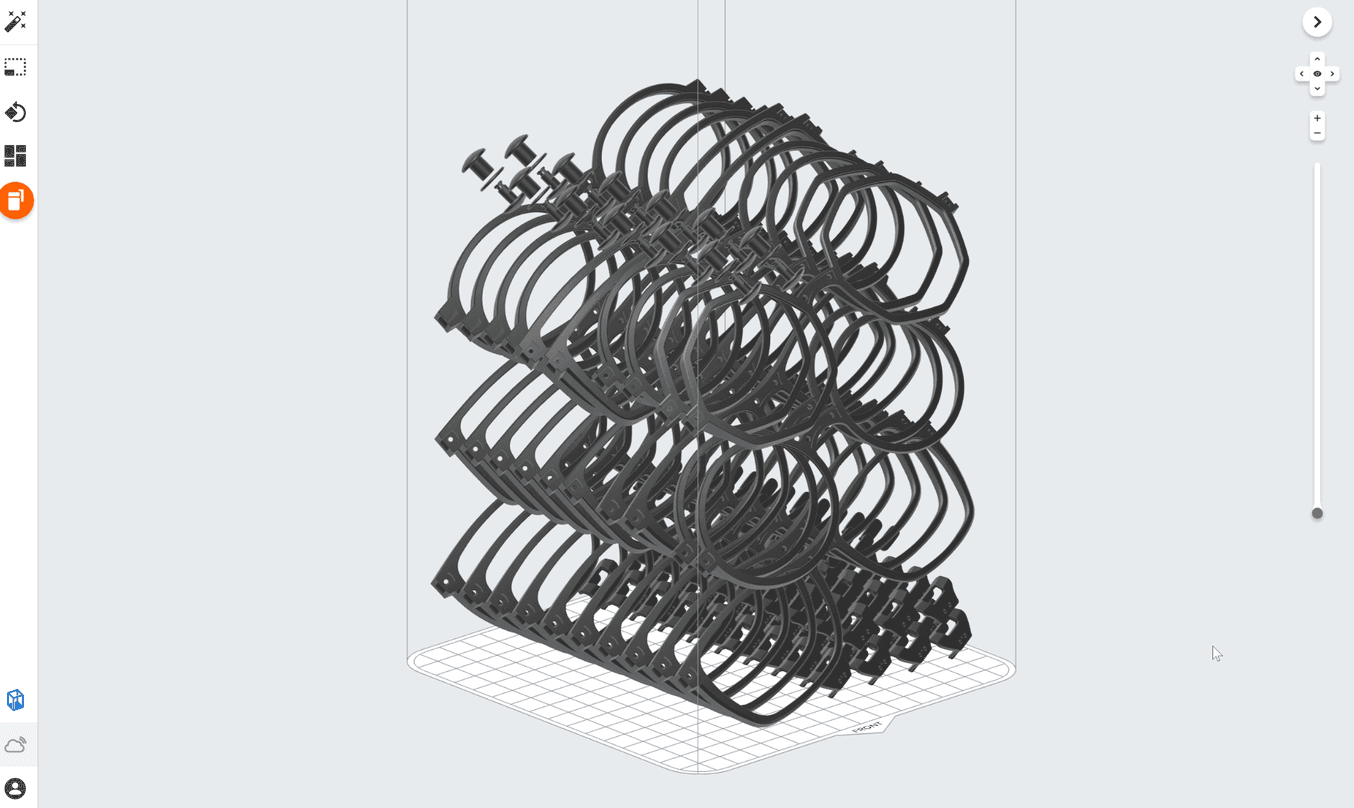
Dank des Bauvolumen und der Drucktechnologie des Fuse 1, konnten ganze 80 Brillenfronten gestapelt und ohne Stützstrukturen in einem Druck gefertigt werden.
Durch die Detailgenauigkeit der selektiven Lasersinterntechnologie und der nicht notwendigen Stützstrukturen eignet sich der Fuse 1 für genau solche filigranen Serienelemente, die später passgenau weiterverarbeitet werden sollen.
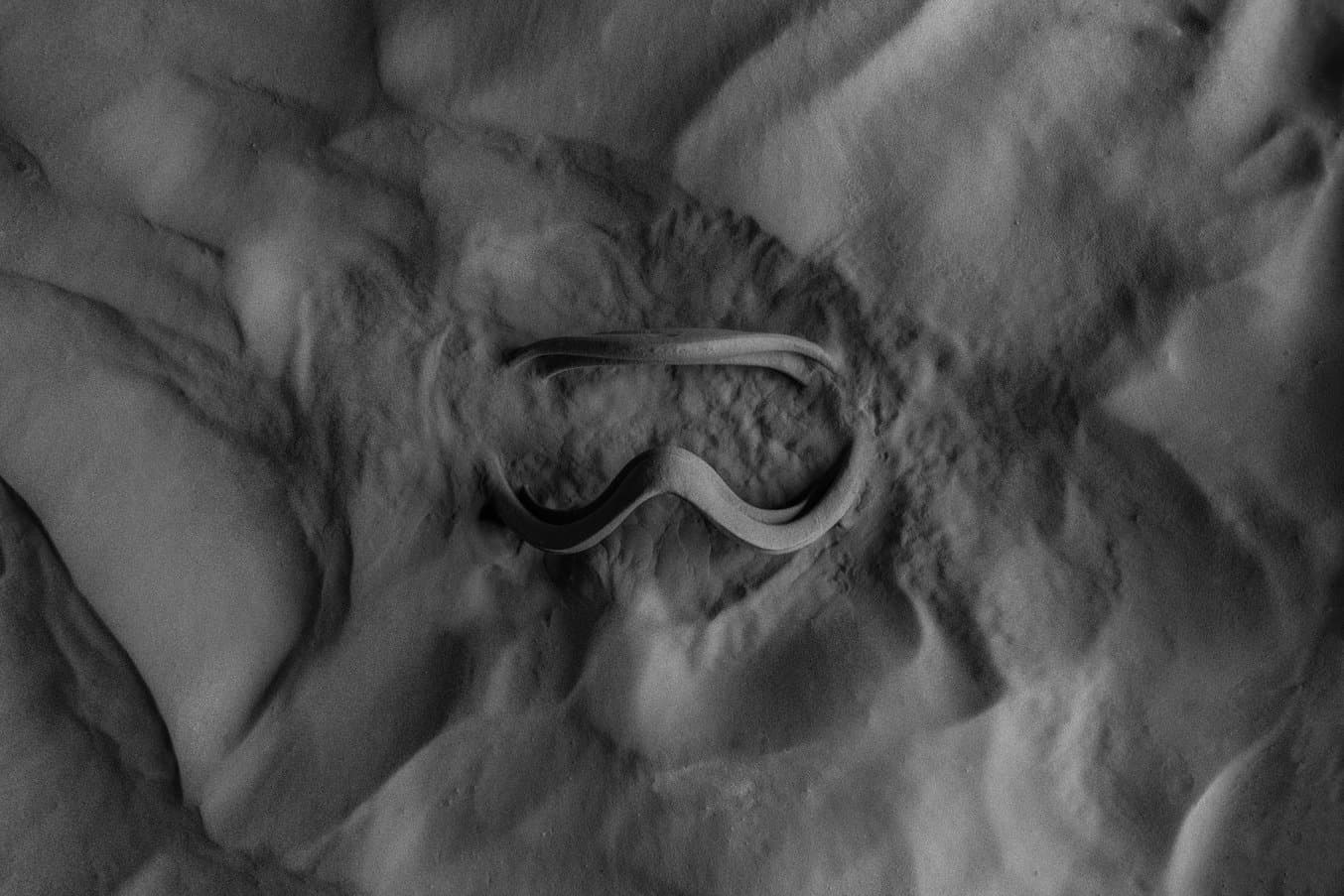
Leitfaden zum 3D-Druck mit selektivem Lasersintern (SLS)
In diesem umfangreichen Leitfaden werden wir das selektive Lasersintern und die verschiedenen, auf dem Markt erhältlichen, Systeme und Materialien sowie den Arbeitsablauf mit SLS-Druckern und die verschiedenen Anwendungen abdecken.
“Beim SLS 3D-Druck ist es besonders schön, dass er ohne Stützstrukturen in sich verschachtelte Dinge drucken kann.”
Marcus Marienfeld
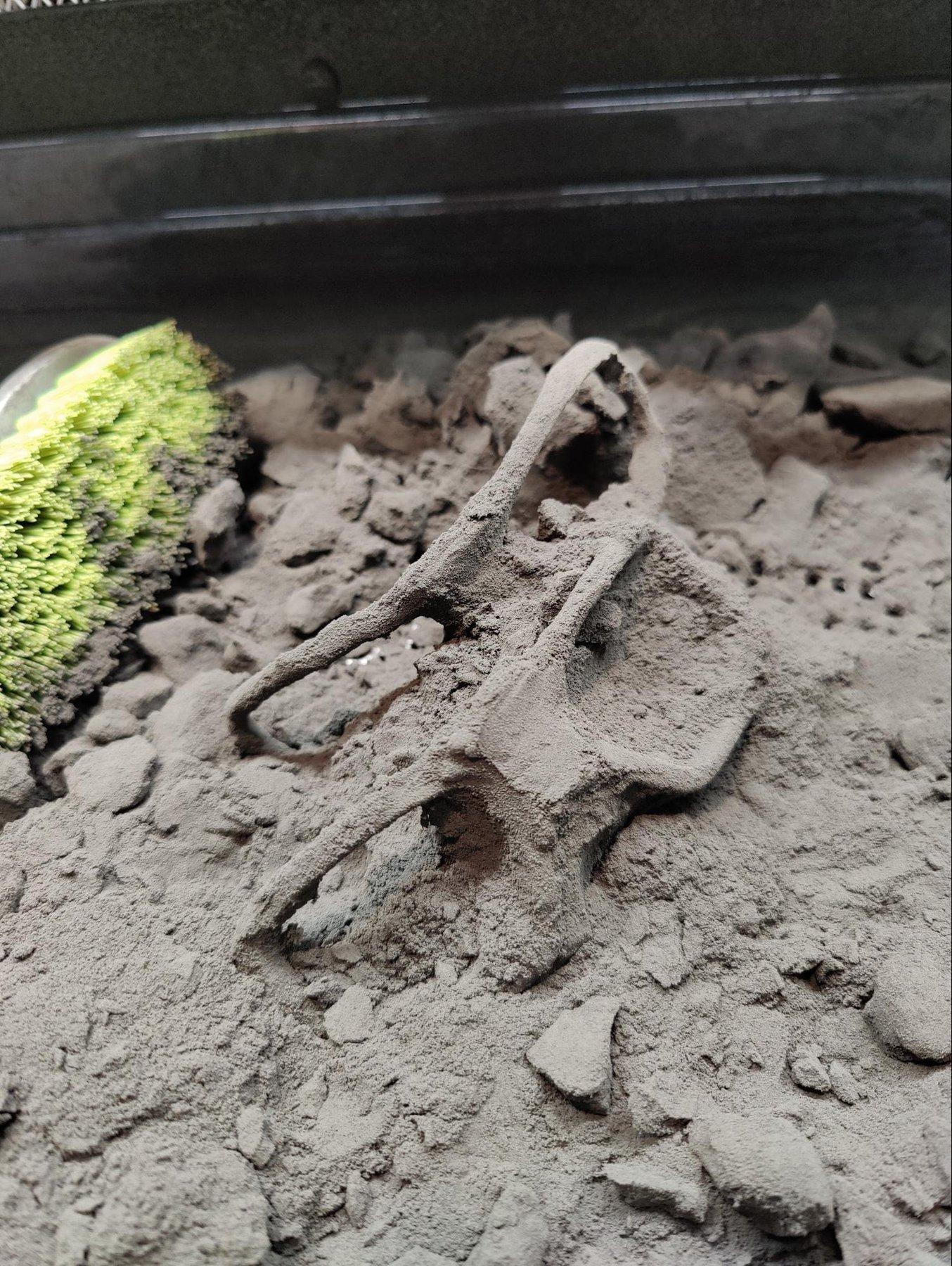
Brillenfronten aus Nylon 11 Powder bei der Nachbearbeitung im Fuse Sift
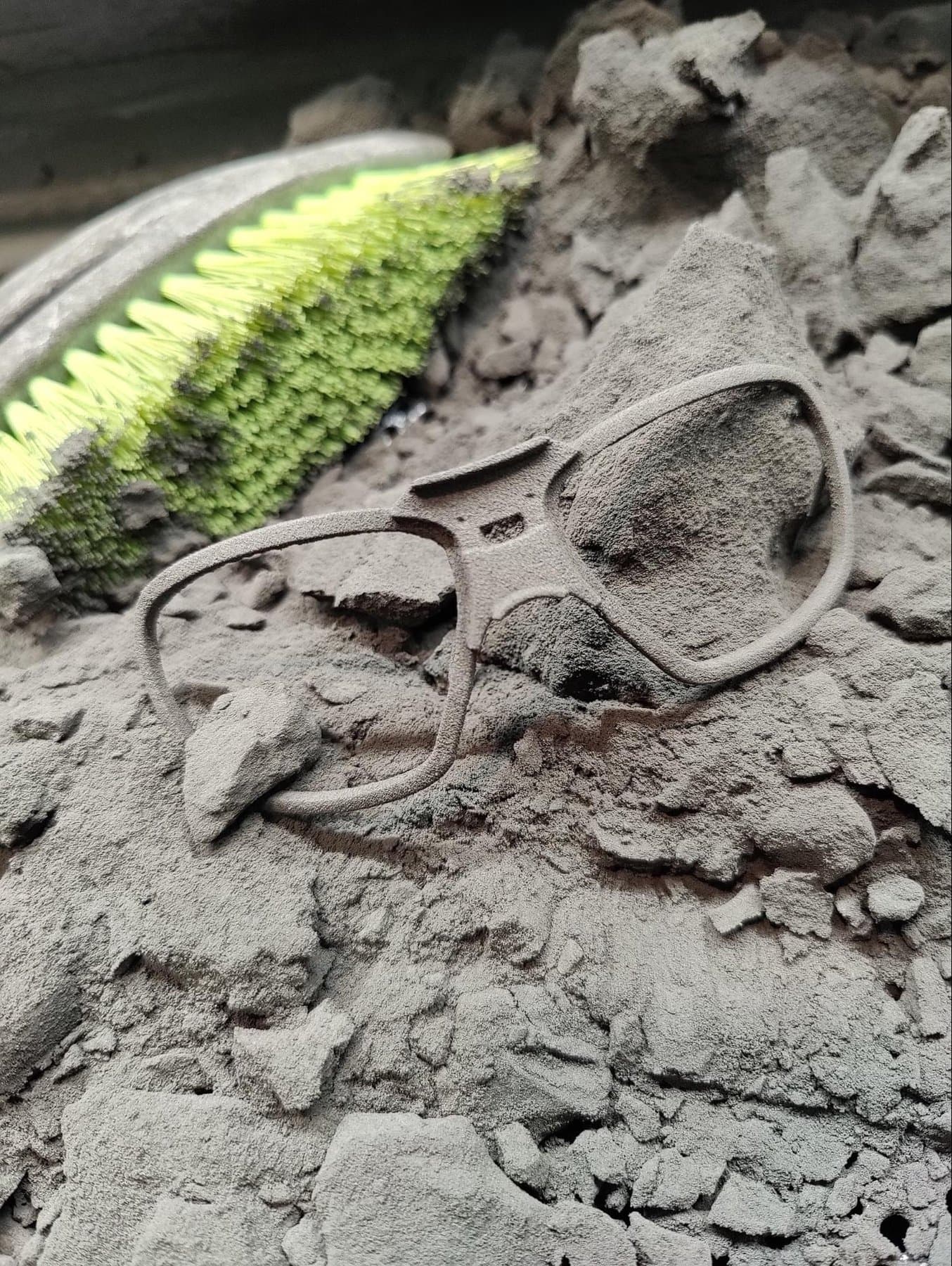
Diese erste Serie der SLS 3D-gedruckten Brillen, soll mit hochwertigen Karbonbügeln versehen werden und dann an Partner weltweit verkauft werden. Außerdem liegen schon andere Projekte für Brillen mit Nylonelementen bei Marienfeld auf dem Tisch. Es werden Sportbrillen mit integrierten Lüftungsschlitzen designt, die in einem verschachtelten Druck fertig gestellt werden sollen.
“Was die Genauigkeit angeht ist der Fuse 1 immer bei 100%. Das ist ziemlich genial.”
Marcus Marienfeld
Der Fuse 1 eröffnet dem Designer immer wieder neue Horizonte bei seinen Entwürfen:
“Wir haben spezielle Brillen designt, die nicht einfach nur flach sind, sondern nach außen dicker werden. Sie sind quasi konisch aufgebaut. Um so etwas zu bauen, ist der 3D-Druck prädestiniert. Wir können spezielle Designs simpel umsetzen, welche mit andere Technologien nicht funktionieren würden”, erklärt Marienfeld.
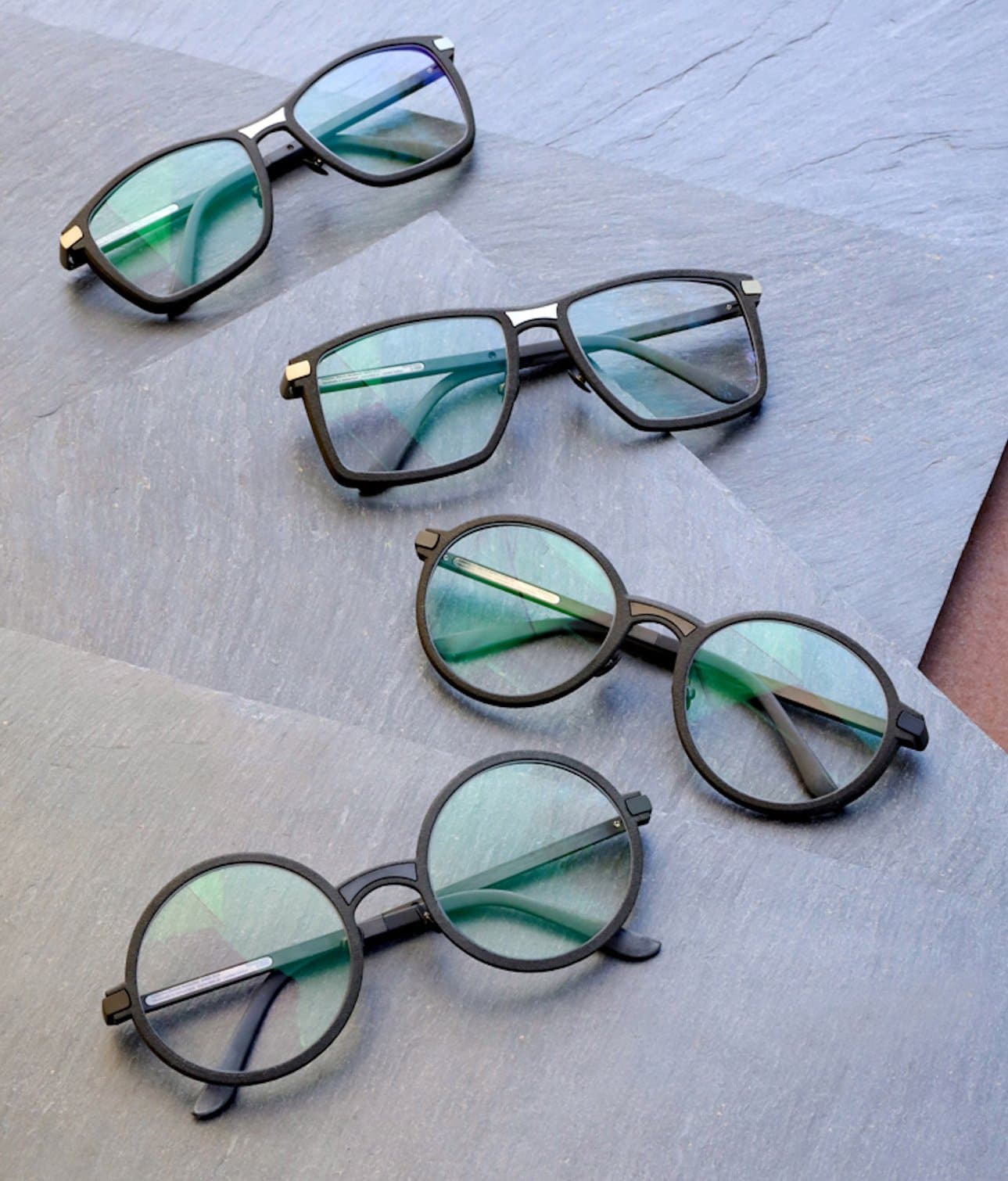
Fertige Marcus Marienfeld Brillen aus Nylon 11 Powder und Karbon
Die ästhetischen Vorteile des beständigen Nylonmaterials
An dem Punkt, an dem es für viele Fuse 1 Nutzer:innen um mechanische Eigenschaften wie Temperaturbeständigkeit oder Zugfestigkeit ankommt, nimmt Marienfeld eine ganz andere Perspektive ein.
Bei der Materialauswahl entschied sich der gelernte Goldschmied vorrangig aufgrund der ästhetischen Eigenschaften für Nylon 11 Powder.
“Dieses dunkle Anthrazit des Nylon 11 Powder möchte ich ein bisschen hervorheben. Es ist neutral in der Ansicht und man kann dort mit Materialkombinationen spielen und wenn es sich um Schmuck handeln sollte, kann man hervorragend bunte Elemente kombinieren”, sagt Marienfeld.
Überdies ist die seidenmatte Oberfläche, die trotzdem noch eine gewisse Griffigkeit nach den Nachbearbeitungsschritten beibehält, wichtig für den Verkauf und das Tragen der Nylon 11 Powder Brillen.
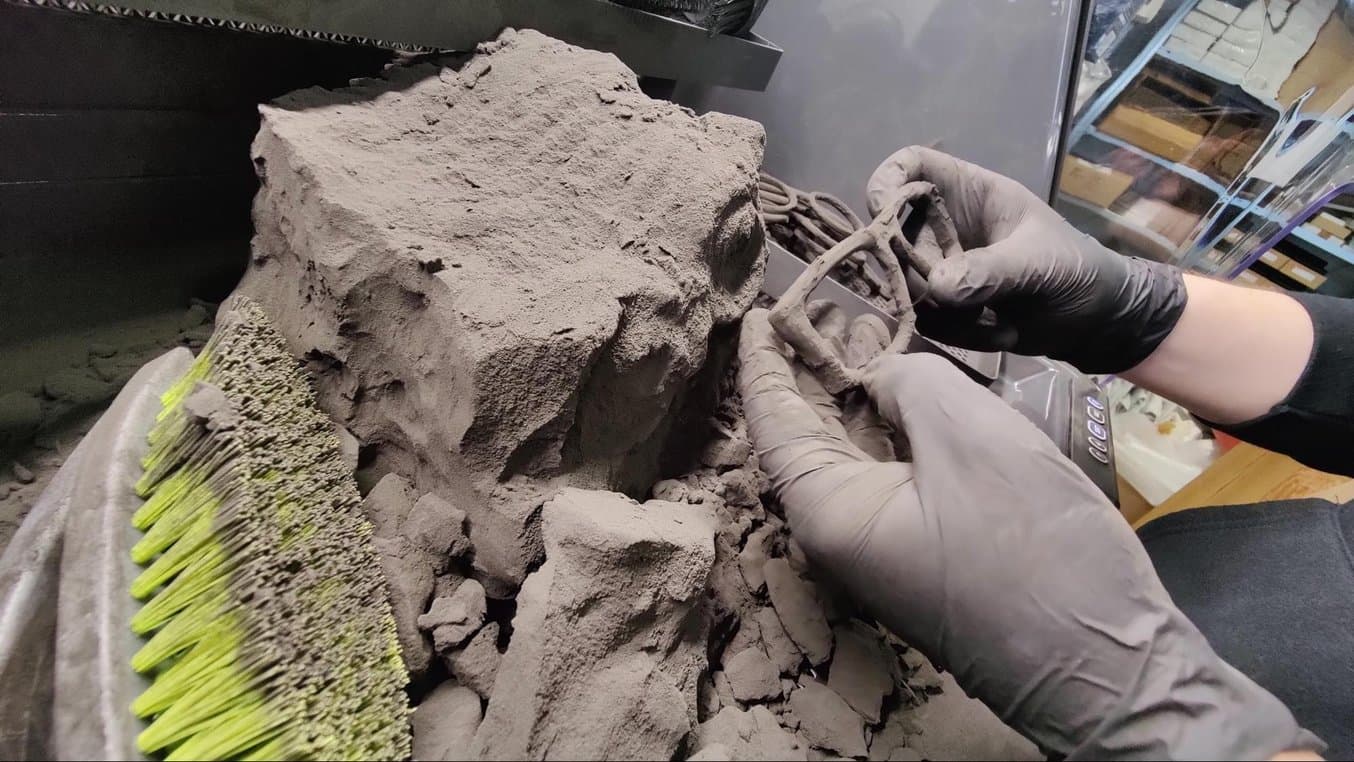
3D-Druck setzt individuelle Kundenwünsche in die Tat um
Da die Marcus Marienfeld AG schon länger auch viele andere Produktionstechnologien für ihre Brillen einsetzt, können anschauliche Vergleiche zwischen dem 3D-Druckverfahren und beispielsweise einer CNC-Maschine gezogen werden.
So werden die Karbonbrillen bei Marienfeld auf einer fünfachsigen CNC-Maschine gefräst.
Hinsichtlich der Detailgenauigkeit leistet diese ganze Arbeit, jedoch kann Marienfeld keine individuellen Änderungen vornehmen, um jedem/r Kund:in eine Brille zu bieten, die sich seinem/ihrem Gesicht perfekt anpasst.
“Das kann ich mit dem 3D-Druck sofort erledigen. Wenn man mit dem 3D-Zeichnen vertraut ist, kann man Anpassungen ganz einfach in der Zeichnung vornehmen, sie in die Software hochladen und direkt drucken. Beim Fräsen bräuchte ich hingegen immer wieder eine individuelle und teure Werkzeugentwicklung, um die Elemente in der Maschine zu halten”, erklärt Marienfeld.
Beispielsweise setzte er die Anfrage eines Bergführers nach einer solchen Spezialanfertigung um. Durch den Einsatz von 3D-Druck konnte die Sonnenbrille aus Nylon mit besonderen Seitenelementen gegen die Sonneneinstrahlung auf dem Berg nach nur 2 Wochen übergeben werden.
“Aus Vollkarbon, welches herkömmliche Methoden der Fertigung voraussetzt, müsste man wahrscheinlich mit zwei bis drei Monaten für eine solche Anfertigung rechnen”, erläutert Marienfeld.
SLS 3D-gedruckte Werkzeuge zur Bearbeitung von Titan
Neben der Anfertigung von Brillen mit Nylonelementen, produziert die Marienfeld Manufaktur außerdem ihr eigenes Werkzeug auf dem Fuse 1. Insbesondere für die Anfertigung von Brillen aus Titan ist das Nylon 11 Powder durch seine Festigkeit und Formstabilität sehr geeignet.
“Titan hat den Nachteil, dass es schwer zu verformen, biegen oder fräsen ist. Aber ich hatte die Idee es mit einem 3D-gedrucktem Presswerkzeug aus Nylon 11 Powder auszuprobieren und es funktioniert einwandfrei.”
Marcus Marienfeld
“Wir stellen Presswerkzeuge her, um Brillengestelle in die richtige Form zu biegen. Je nach Modell der Brille muss eine andere Wölbung des Gestells geschaffen werden. Das haben wir früher sehr aufwendig mit Stahlwerkzeugen gemacht, welche pro Modell hohe Kosten hervorrufen”, sagt Marienfeld.
Eine solche Arbeitshilfe aus Nylon 11 Powder, bestehend aus Ober- und Unterwerkzeug, wird in der Manufaktur in eine Kniehebelpresse eingeschraubt und hält einen Druck von ca. 90 Kilogramm aus. Durch die enorme Formstabilität des Nylon 11 Powder weist das Werkzeug zudem keine Vertiefungen an den Stellen auf, an denen die Titanränder mit diesem enormen Druck auf das Werkzeug treffen.
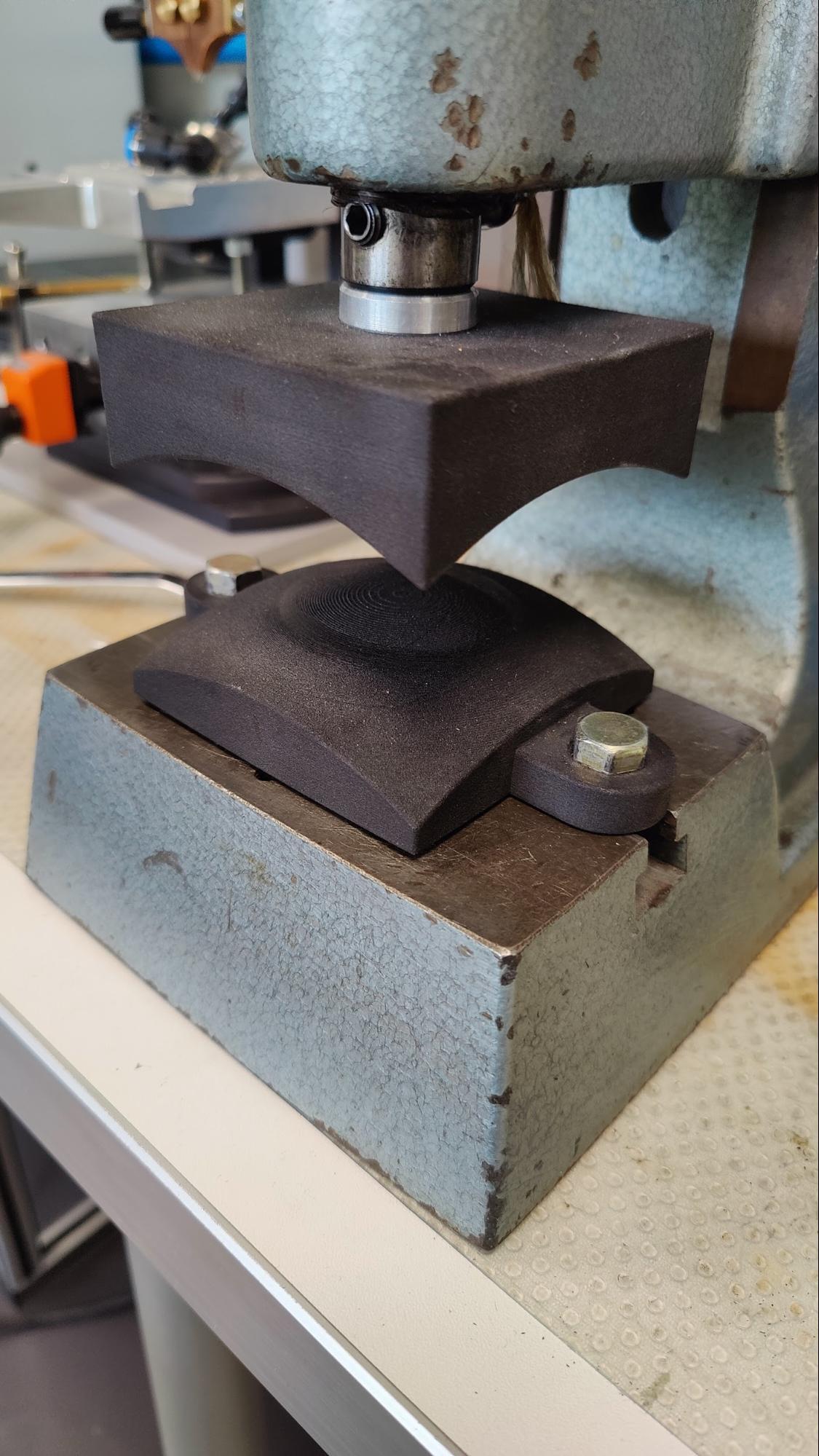
SLS 3D-gedrucktes Presswerkzeug aus Nylon 11 Powder eingeschraubt in eine Kniehebelpresse
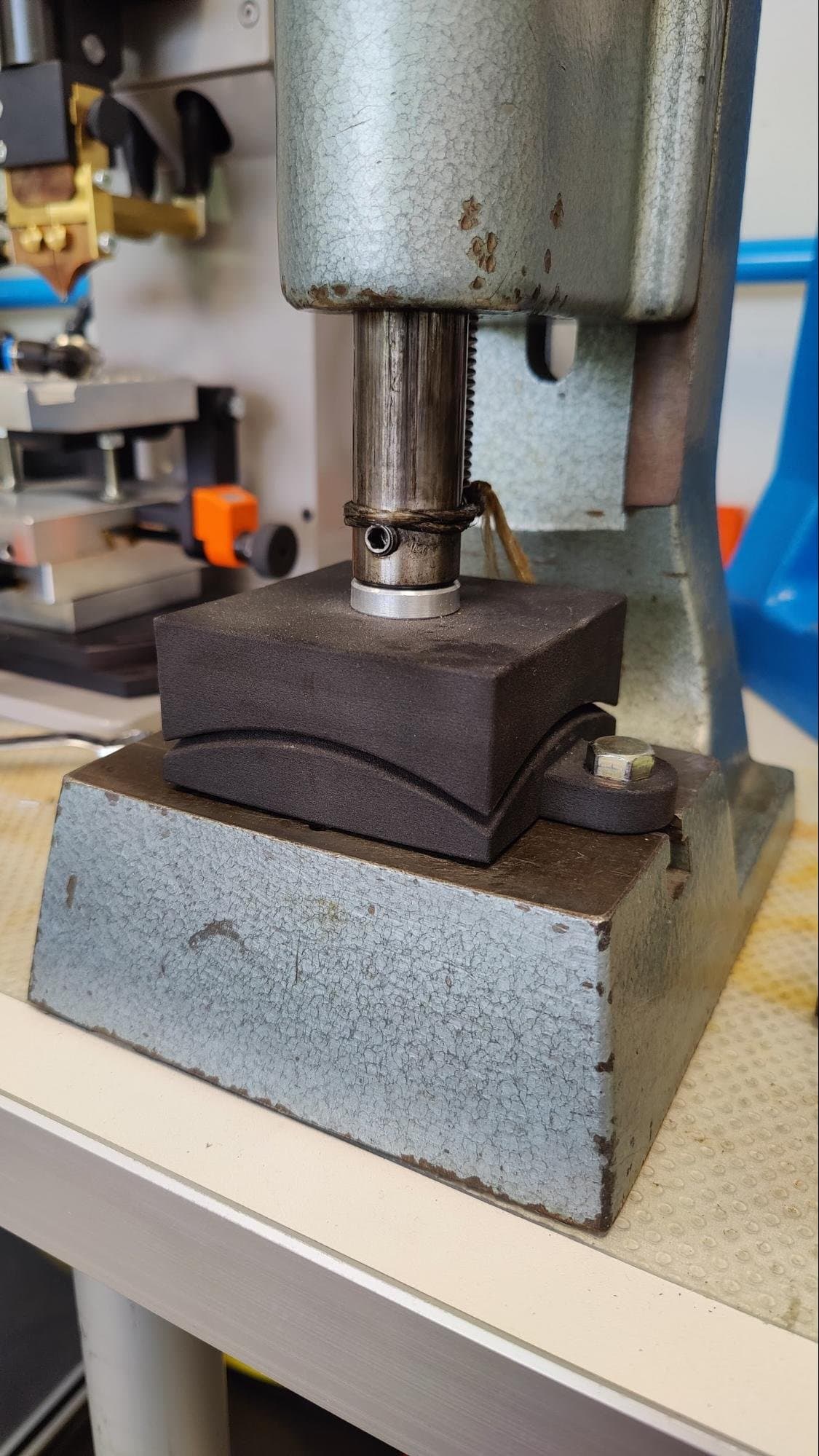
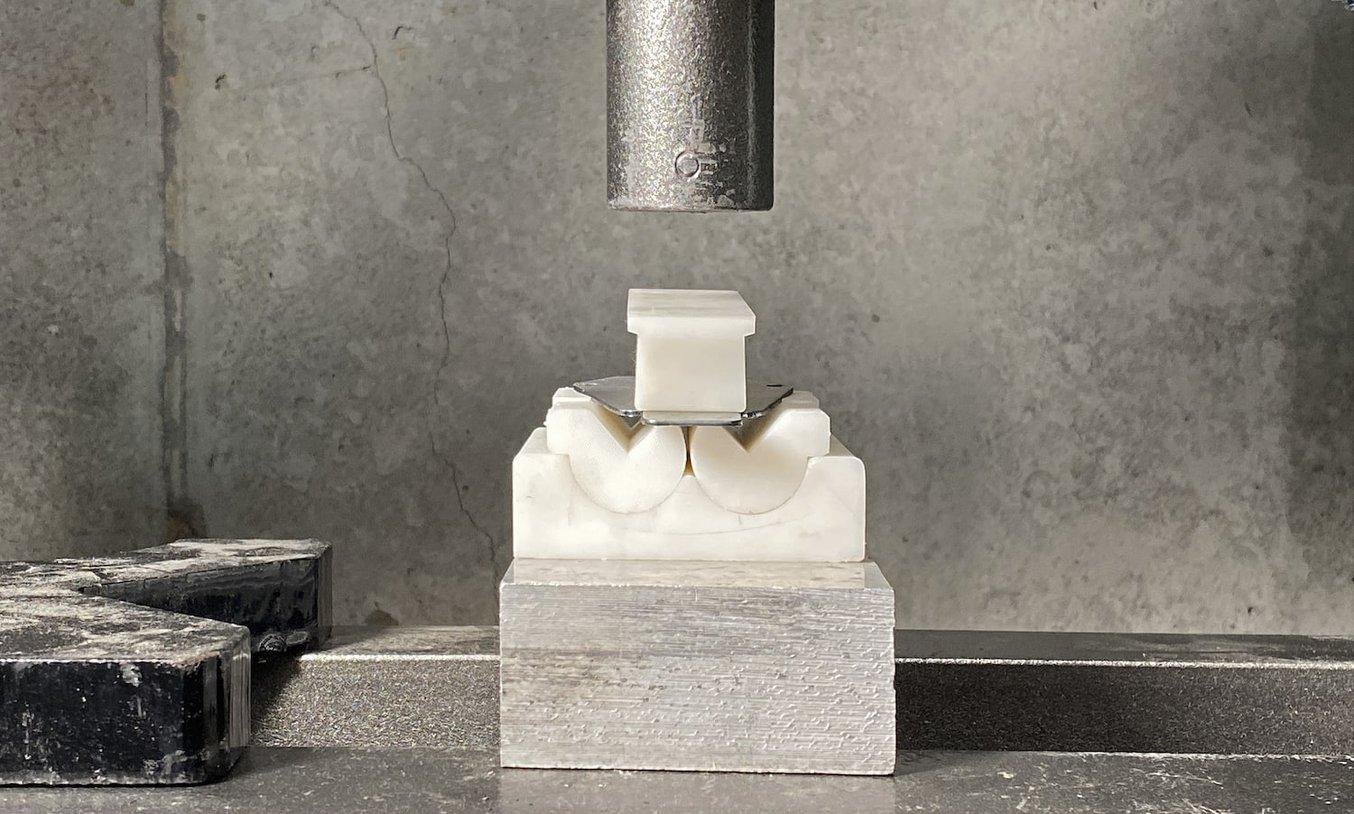
Rapid Tooling für die Blechumformung mit 3D-gedruckten Formwerkzeugen
Dieses Whitepaper schlägt ein alternatives Werkzeugbauverfahren vor, das durch den Einsatz von 3D-Druckern schneller und kostengünstiger ist.
“Unser Ziel ist es immer zu wachsen. Nicht in der Größe oder Absatzmenge, sondern in der Qualität und Innovation. Wir wollen eine Nische bleiben”, äußert sich Marienfeld zu seiner Marke.
So hat Marienfeld für seine Unternehmung mit dem 3D-Druck eine Technologie gefunden, die ihm auf der einen Seite durch den Prototypen- und Werkzeugbau Zeit und Geld ersparen kann, auf der anderen Seite bietet die Technologie ihm die Möglichkeit seine Produktdesigns und Herstellungsweisen immer wieder weiterzuentwickeln und damit seine Kund:innen stets zu begeistern.
“Man wird sehr erfinderisch und ideenreich wenn man einen solchen 3D-Drucker im Haus hat. Ich kann mit wenig Aufwand Dinge erledigen, die ich sonst erst gar nicht ausprobieren würde.”
Marcus Marienfeld