In vier Monaten vom Konzept zur Kommerzialisierung: Wie Arbutus Medical mit 3D-Druck in Rekordzeit Medizinprodukte entwickelt
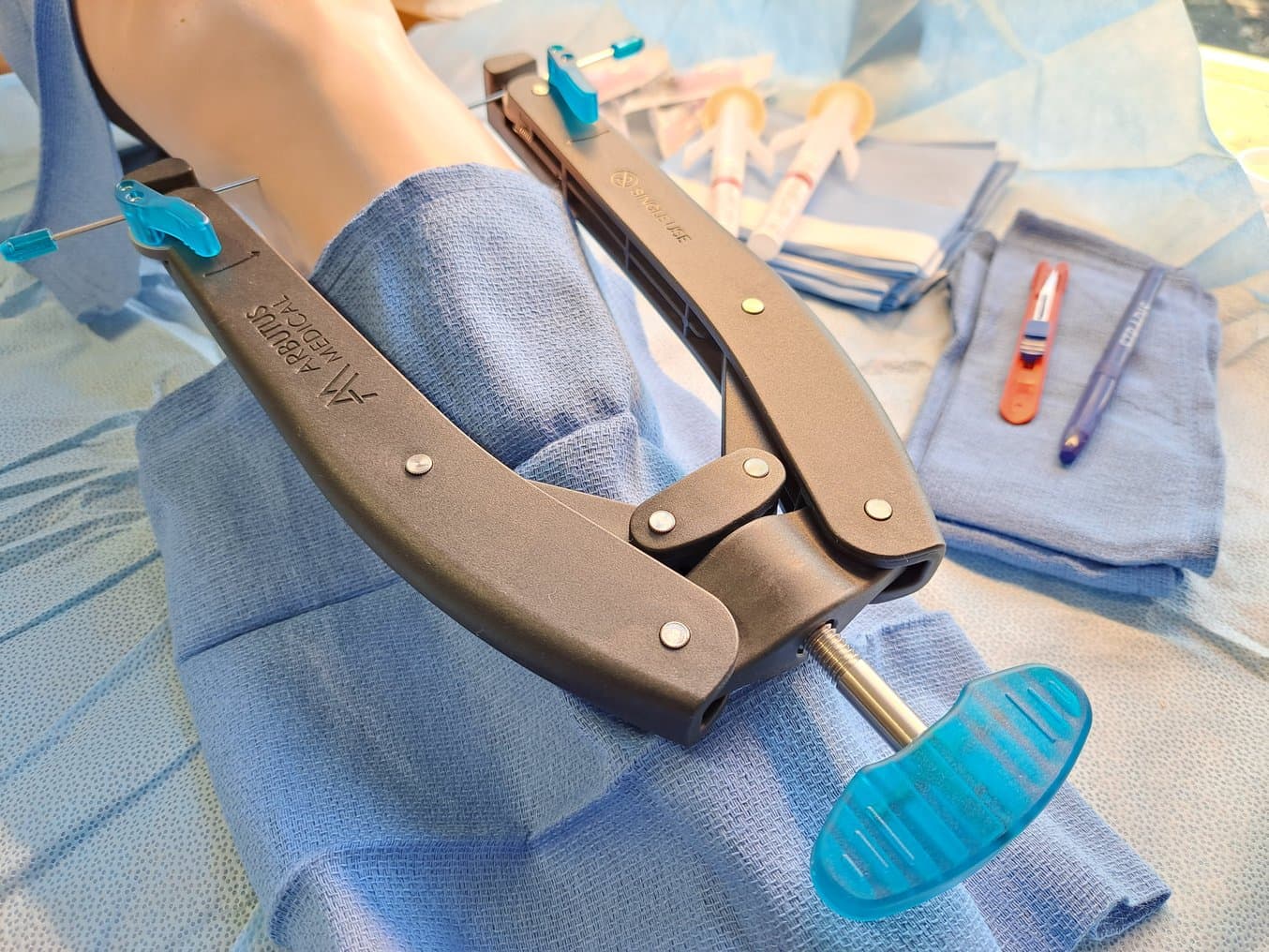
Bei kleineren chirurgischen Eingriffen in der Notaufnahme von Unfallkliniken haben OP-Teams oft nur begrenzt Zugang zu den benötigten Hilfsmitteln und müssen bestimmte Medizinprodukte aus anderen Abteilungen des Krankenhauses beschaffen, was die Behandlung verzögert. Arbutus Medical möchte dies ändern und reagiert mit der Entwicklung spezieller Behandlungskits auf die Probleme von OP-Teams. Diese Kits erfordern häufig leistungsstarke Einweginstrumente zur Optimierung bestimmter Verfahren, damit Patient*innen schneller versorgt werden können und Ärzt*innen sich auf die Behandlung konzentrieren können, anstatt Hilfsmittel zu beschaffen.
Der 3D-Druck ist bei Arbutus Medical der Schlüssel zu Design und Fertigung. Radu Postole, Leiter des Produktdesigns bei Arbutus Medical, verwendet die Kunstharz-3D-Drucker von Formlabs nicht nur für die Prototypisierung von Medizinprodukten, sondern auch für die Fertigung von Hilfsmitteln für Tests und die Pilotfertigung. Für die neueste Vorrichtung, einen Kirschner-Bogen, arbeitete Postole mit Phil Tsao zusammen, einem Formlabs-Botschafter und Gründer des Unternehmens Ember Prototypes, das sich mit Rapid Prototyping, Beratung und Produktdesign beschäftigt. Ziel war, mithilfe von 3D-Druck innerhalb eines Jahres von der Idee bis zur Kommerzialisierung zu gelangen. Dabei wurde der 3D-Druck sogar für die Übergangsfertigung eingesetzt, wobei über 800 Teile pro Monat hergestellt wurden.
Für Arbutus Medical und Ember Prototypes haben Zuverlässigkeit und die umfangreiche Materialbibliothek des Ecosystems von Formlabs die Entwicklung und Fertigung von Medizinprodukten in Rekordzeit möglich gemacht.
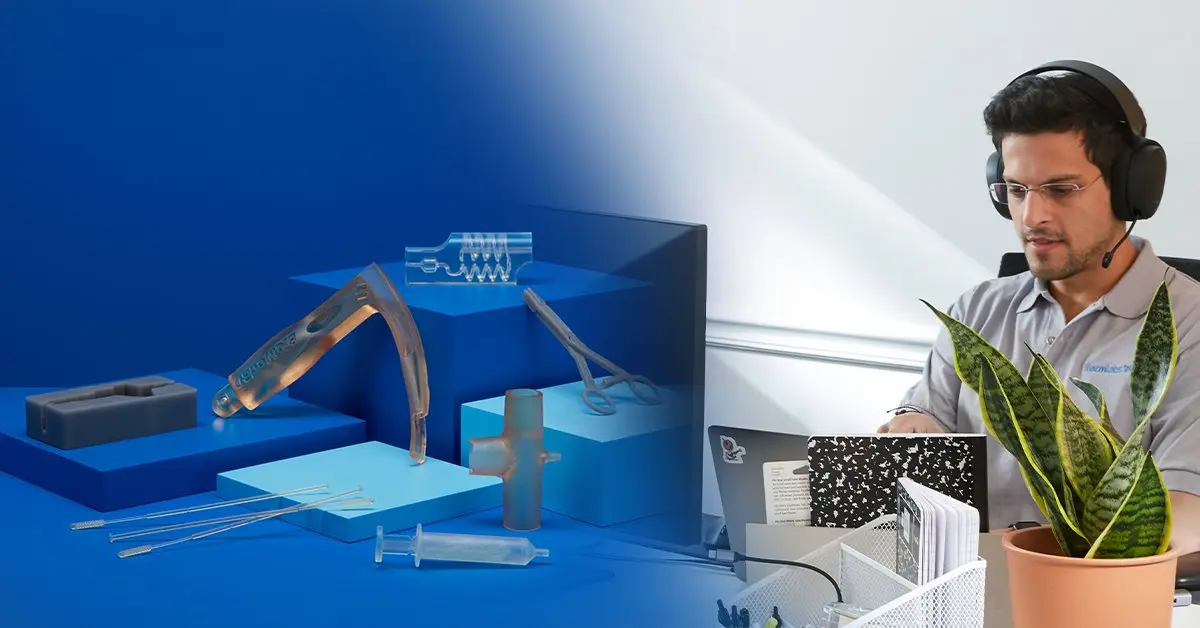
Kontakt zum Vertriebsteam von Formlabs Medical
Ob Sie patientenspezifische chirurgische Instrumente erstellen möchten oder Prototypen kardiologischer Medizinprodukte anfertigen: Wir stehen Ihnen zur Seite. Hinter Formlabs Medical steht ein engagiertes Spezialistenteam, das Sie und Ihr Unternehmen bei Bedarf mit professioneller Hilfe unterstützt.
Spezialisierte Behandlungskits lösen Probleme in Traumazentren
Das TrakPak® von Arbutus Medical wurde im Jahr 2021 eingeführt. Das Kit wird verwendet, um bei Oberschenkel- oder Beckenfrakturen beim Warten auf eine Operation schnell eine skelettale Traktion anzuwenden, durch die Frakturen reduziert und stabilisiert werden. Die ursprüngliche Version des Kits enthielt einen modifizierten DeWalt-Bohrer mit einer sterilen Abdeckung und einem implantierbaren Pin. Als Postole diese Vorrichtung entwarf, suchte er nach einem 3D-Drucker, um die Prototypenentwicklung zu beschleunigen. Tsao empfahl ihm Formlabs' Form 3. Nicht nur sind einige Elemente des TrakPak® auf dem 3D-Drucker prototypisiert worden, sondern Tsao und Postole konnten die endgültigen Designs mit 3D-Druck schnell in ausreichenden Mengen herstellen, um Studien zum menschlichen Faktor und Leichentests durchzuführen. Seit seiner Markteinführung wurden in den USA über 4000 Patient*innen mit dem TrakPak® behandelt.
Studien mit 3D-gedruckten Vorrichtungen
Das Testen menschlicher Faktoren kann ein langwieriger Prozess sein, oft aufgrund der Zeit, die für die Beschaffung der Formwerkzeuge und den Start der Fertigung benötigt wird. Dank 3D-Druck konnte Postole schnell funktionsfähige Prototypen liefern, die nicht nur auf dem Prüfstand und an Leichen getestet werden konnten, sondern der endgültigen Vorrichtung auch optisch entsprachen. Bei der Ästhetik war ein klares Erscheinungsbild wichtig, damit sich das Feedback der Chirurg*innen ausschließlich auf die Leistung und den Nutzen des Teils konzentrierte.
„Weil es sich hier um ein Produkt der Klasse II handelt, ein Implantat, waren die Hürden für die Veröffentlichung ziemlich hoch. Wir mussten eine sehr ausführliche Studie des menschlichen Faktors durchführen, und das gänzlich mit den 3D-gedruckten Teilen. Einige Unternehmen müssen warten, bis die spritzgegossenen Teile für die Studie zur Verfügung stehen, aber wir konnten dank des 3D-Drucks drei bis vier Monate an Zeit sparen.“
Radu Postole, Leiter des Produktdesigns, Arbutus Medical
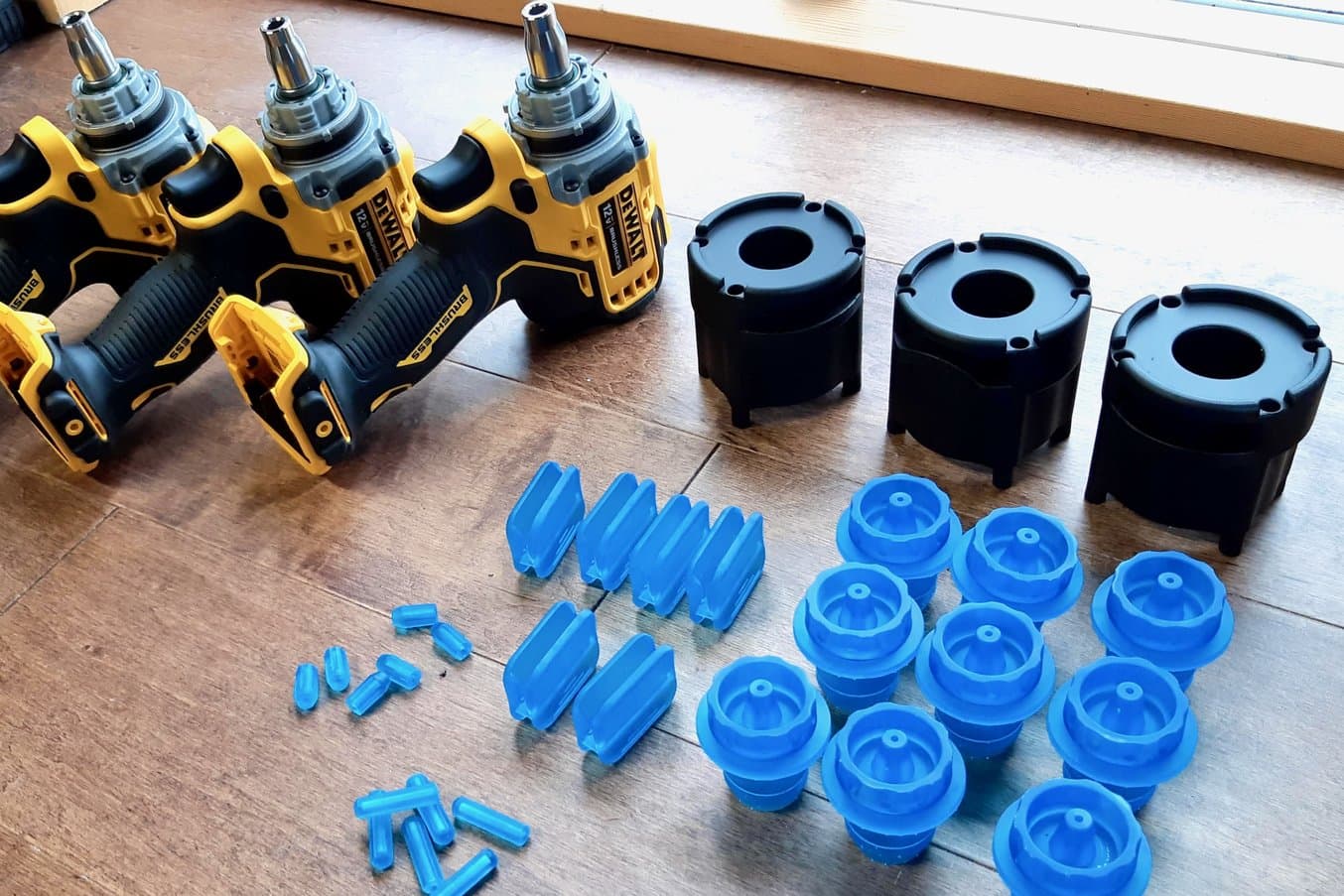
Die Prototypenentwicklung des TrakPak® umfasste das 3D-Drucken eines Adapters für eine Bohrmaschine sowie von Pin-Komponenten.
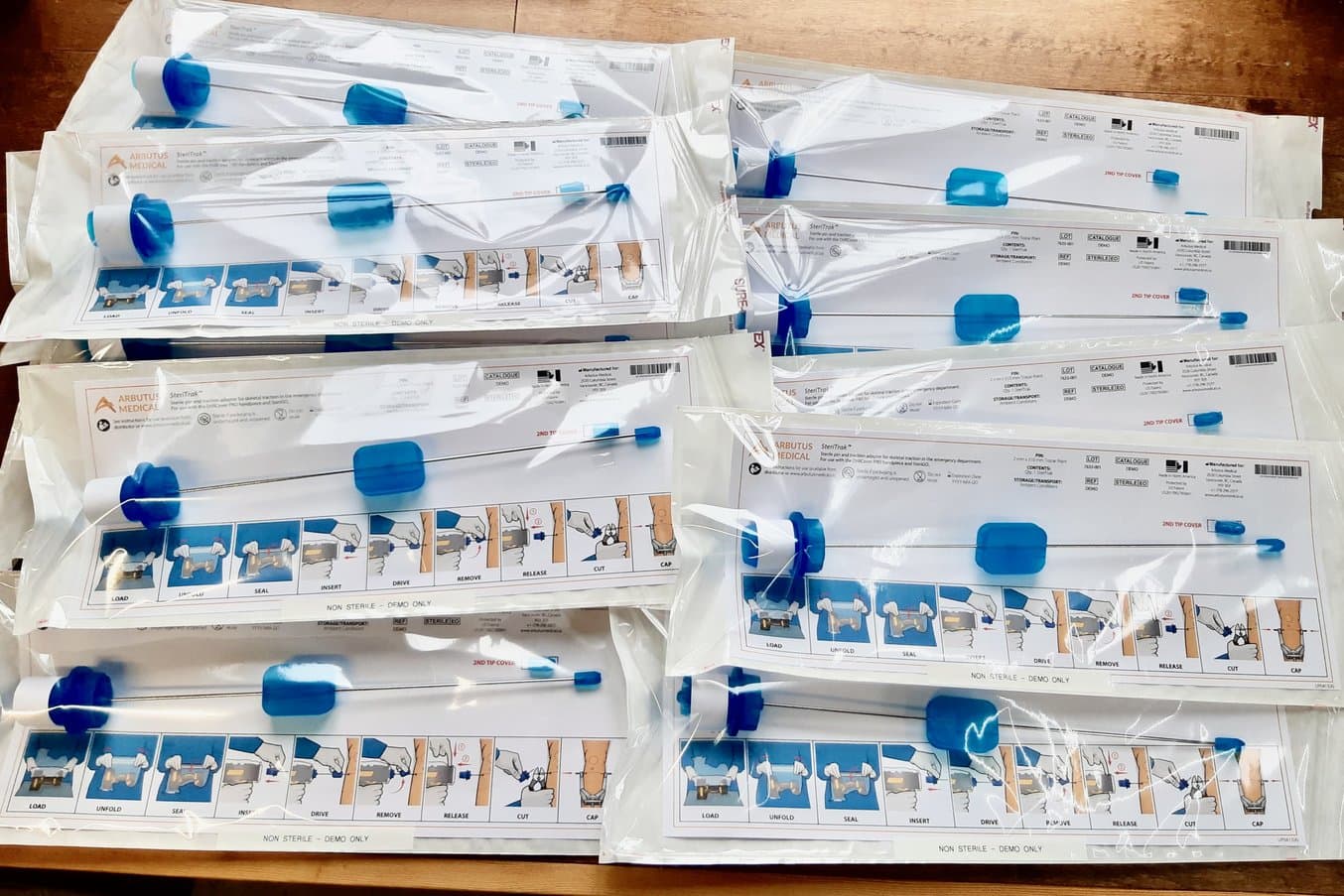
Das TrakPak® besteht aus einer sterilen Einweghülle für einen Bohrer und einem implantierbaren Pin. Die blauen Komponenten auf dem Pin sind 3D-gedruckt.
Während die erste Version des TrakPak® ein Problem von Unfallkliniken löste, machte die enge Zusammenarbeit mit den Chirurgieteams jedoch ein weiteres Problem deutlich: den eingeschränkten Zugang zu Kirschner-Bögen (K-Bögen) im OP. Diese werden in der orthopädischen Chirurgie zur Spannung des implantierten Pins und zur Anwendung von Zugkräften am Skelett verwendet. Sie sind allerdings schwer zu beschaffen, da sie in der Regel in der Nähe von Operationssälen aufbewahrt werden, jedoch auch in der Notaufnahme zum Einsatz kommen. Eine weitere Herausforderung ist, eine Vorrichtung zu finden, die tatsächlich funktioniert, da die Greifzähne für den Pin und der Spannmechanismus häufig verschleißen. Dies führt nicht nur dazu, dass Patient*innen unter Schmerzen warten müssen, während der K-Bogen besorgt wird, sondern es verschwendet auch die Zeit des Behandlungsteams in der Notaufnahme. Die Antwort von Arbutus Medical war der Pin-Spanner QuikBow®.
Der QuikBow® kam 2023 auf den Markt und verringert die Abhängigkeit von zentralen Sterilgutversorgungsabteilungen (ZSVA) in Krankenhäusern, während er zugleich die Geschwindigkeit und Qualität der Patientenversorgung verbessert. Mithilfe von Druckern des Typs Form 3, der Erfahrung von Ember Prototypes und der umfangreichen Materialbibliothek von Formlabs wurde der QuikBow® innerhalb eines Jahres entworfen, entwickelt, getestet und auf den Markt gebracht.
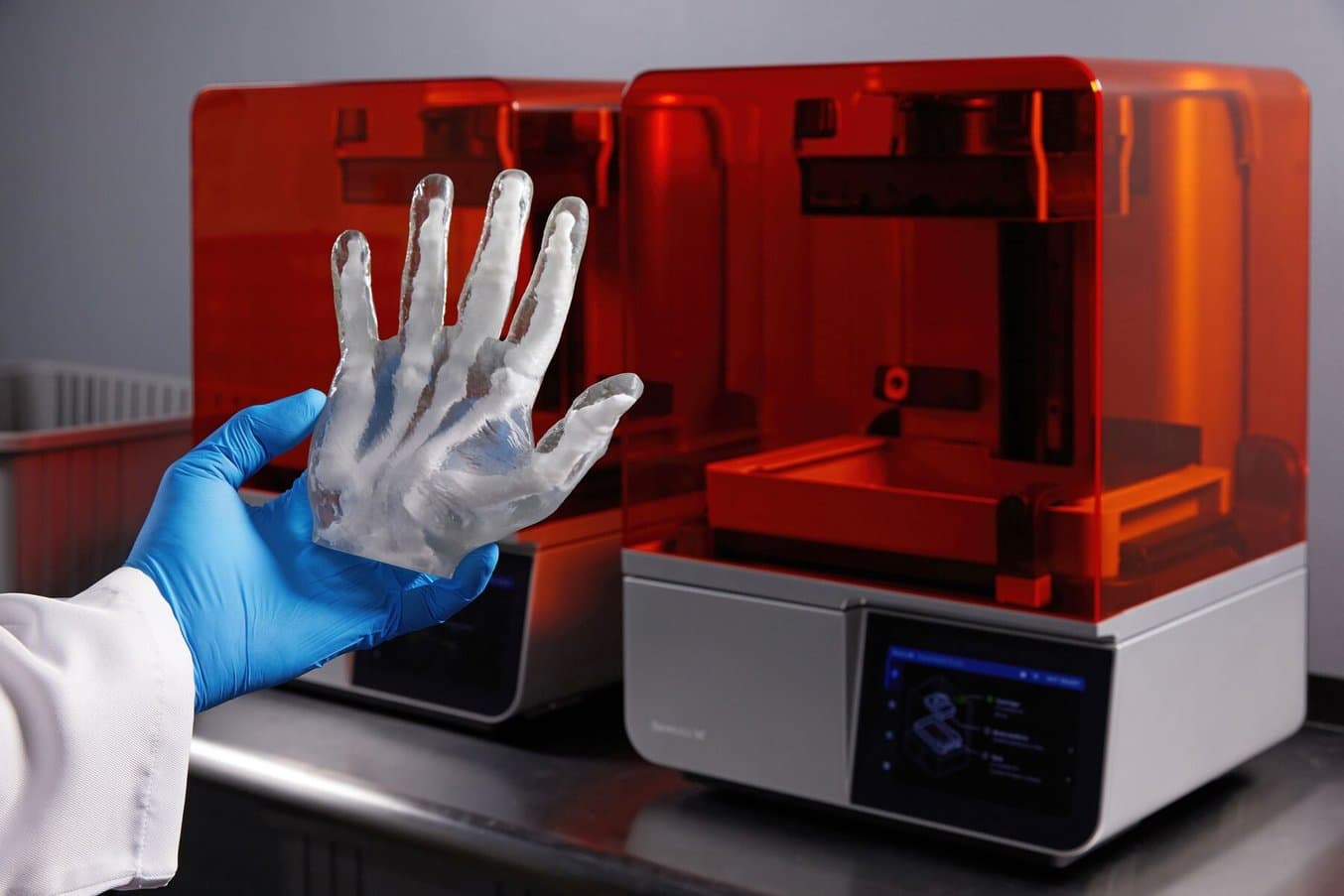
Formlabs' biokompatible Kunstharze: Ein umfassender Leitfaden zur Wahl des richtigen Materials
Formlabs bietet derzeit mehr als 40 einzigartige Materialien für den Stereolithografie-3D-Druck (SLA).Dieses Dokument hilft dabei, unsere biokompatiblen Angebote zu vergleichen und die beste Lösung für Ihre medizinischen Anwendungen zu finden.
Rapid Prototyping mit den 3D-Druckern der Form-Serie und Ember Prototypes
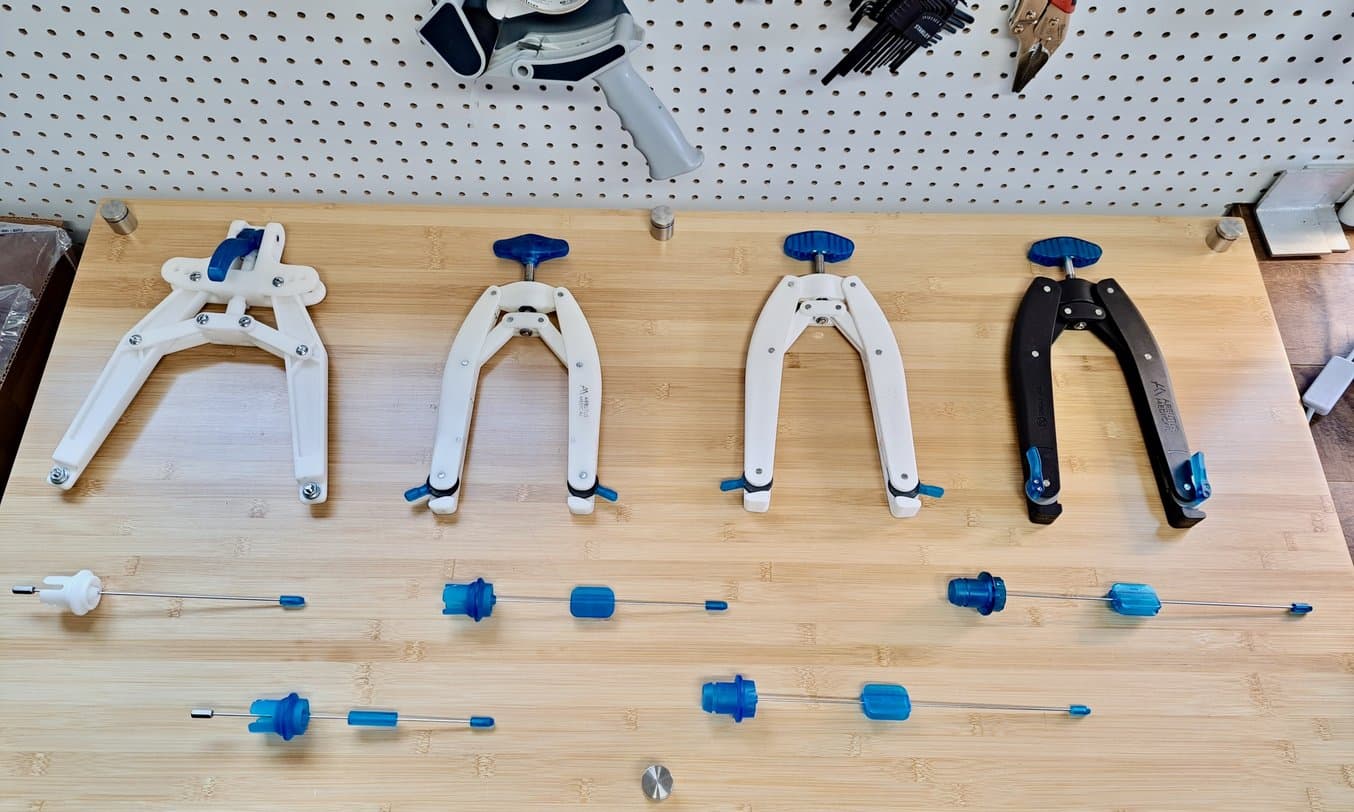
Drei Prototypen des QuikBow® (weiß) und das endgültige Medizinprodukt (schwarz). Die weißen und blauen Teile wurden mit Druckern der Serie Form 3 3D-gedruckt, und die blauen Teile stellen Berührungspunkte dar, mit denen der Nutzer interagieren wird.
Für das Prototyping des QuikBow® zog Postole zunächst die Zerspanung von Teilen des Bogens in Betracht, einschließlich der Arme. „Aber sie sind so massiv und es sind so viele Entkernungen nötig, dass es eigentlich unerschwinglich teuer war, die Arme für die Tests mit Zerspanung zu fertigen, vor allem für die mehr als 30 Designiterationen, die wir erstellt haben. Der 3D-Druck mit dem Formlabs-3D-Drucker bot sich als Lösung an.“
Im Zuge des Designvorgangs wandte sich Postole an Tsao von Ember Prototypes, da die Arme, die er prototypisierte, nur in den Form 3L passten – den großformatigen SLA-3D-Drucker von Formlabs. Tsao verfügt über umfangreiche Erfahrungen mit dem 3D-Druck und der Formlabs-Materialbibliothek. Er arbeitete mit Postole zusammen, um die besten Materialien für den QuikBow® auszuwählen.
Für die Arme war ein hartes Material vonnöten. Tsao druckte die Arme mit verschiedenen Materialien, darunter Tough 2000 Resin, Rigid 4000 Resin und Rigid 10K Resin, um Postole bei der Auswahl des besten Materials für seine Anwendung zu helfen. Letztendlich entschied sich Postole für Rigid 10K Resin als die beste verfügbare Option. Zusätzlich zur Belastbarkeit muss der Bogen in der Lage sein, eine Spannung von über 45 kg auf den Pin auszuüben und 18 kg Zuggewicht zu tragen. Um die Prototypen stabiler zu machen, iterierte Postole das Design des Teils, damit es den erforderlichen Prüfungen standhalten konnte.
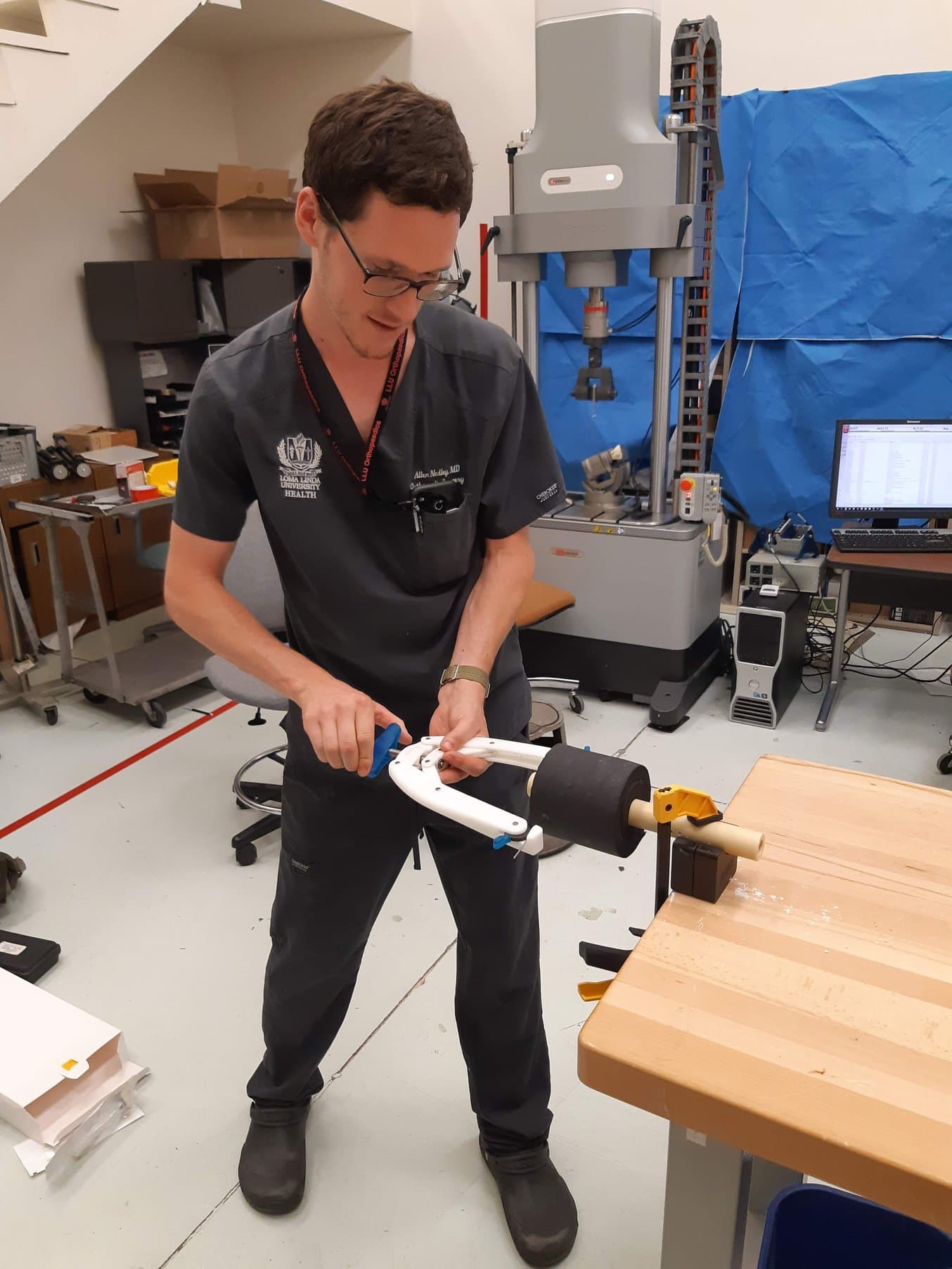
Allen Nedley, MD, orthopädischer Chirurg, testet an der Loma Linda University School of Medicine in Kalifornien die Nutzbarkeit und Festigkeit eines QuikBow®-Prototyps.
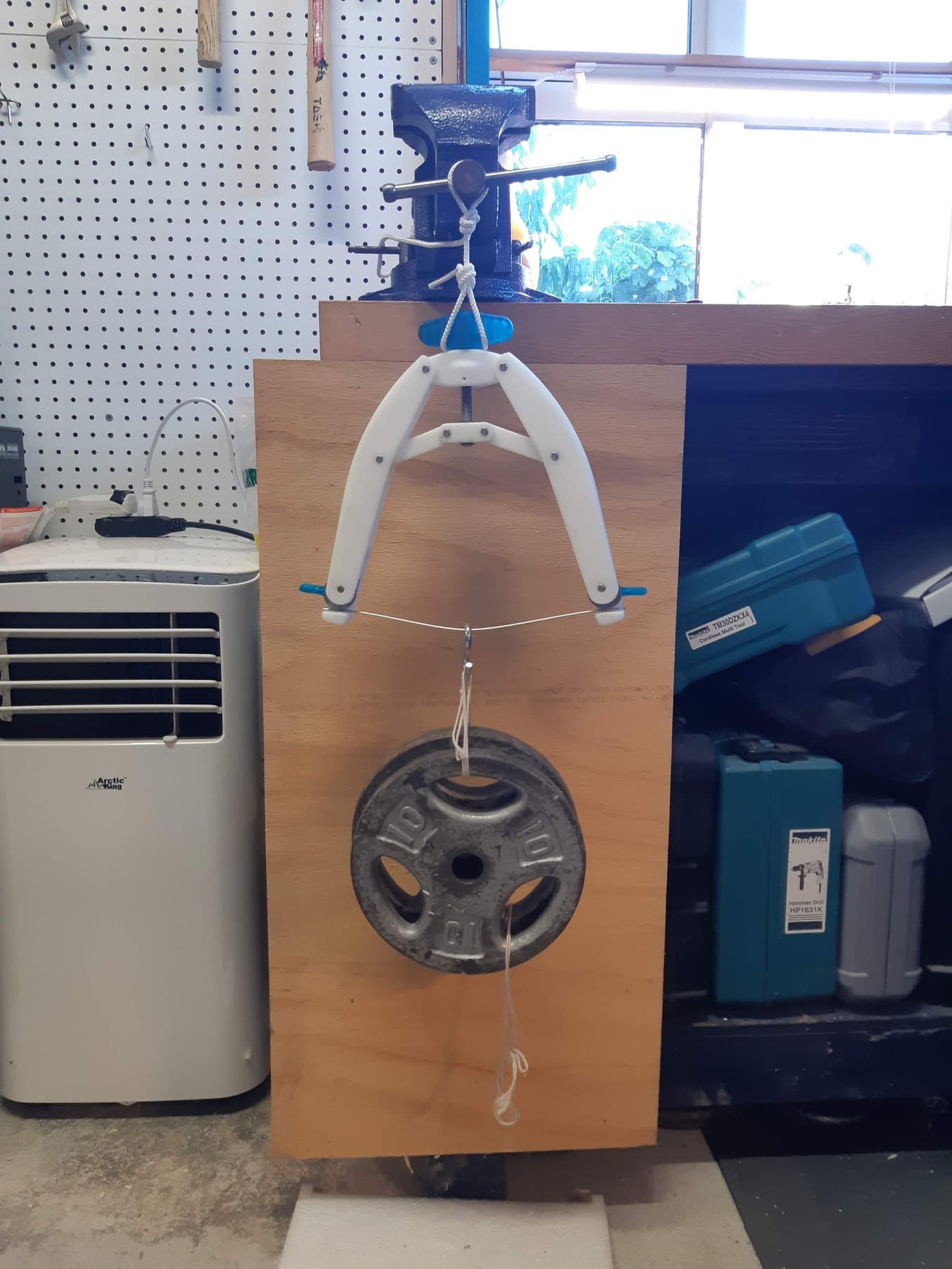
Prüfung des Pins des QuikBow® an einem 3D-gedruckten Prototyp.
„Wir hatten ganz bestimmte Anforderungen an Festigkeit, Steifigkeit und Ästhetik, und diese konnten wir erfüllen. Die Chirurgen erkannten schnell den Wert und die Leistung der Vorrichtung, obwohl es sich um 3D-gedruckte Prototypen handelte.“
Radu Postole, Leiter des Produktdesigns, Arbutus Medical
Die Ästhetik der Materialien war ebenfalls ein Faktor bei der Auswahl. Tsao platzierte die Stützstrukturen manuell und richtete die Dateien so aus, dass nur eine minimale Nachbearbeitung erforderlich war. Dies gewährleistete, dass die Drucke so sauber wie möglich waren und eine gleichmäßige Oberflächenbeschaffenheit aufwiesen.
Postole berichtet: „Phil hat hervorragende Arbeit dabei geleistet, die Endanwendung der Teile zu berücksichtigen und die Dateien dementsprechend in PreForm einzurichten. Die Frage war, welche sind die ästhetischen Flächen und was sind die kritischen Merkmale?“ Da diese Prototypen für Anwenderdemonstrationen und zur Einholung von Feedback verwendet wurden, mussten sie wie endgültige Produkte aussehen. Durch das Platzieren der Stützstrukturen in inneren Bereichen konnte Tsao Teile liefern, die von spritzgegossenen Teilen nicht zu unterscheiden waren. Zusätzlich zur Druckeinrichtung in PreForm entwickelte und druckte Tsao eine Haltevorrichtung, um die Teile beim Waschen zu fixieren, damit sie eine einheitliche, ästhetisch ansprechende Oberflächenqualität erreichen.
„Die Auflösung und die Oberflächenbeschaffenheit mit dem Formlabs-Drucker ist so gut, dass die meisten nicht erkennen, dass das Teil 3D-gedruckt wurde.“
Radu Postole, Leiter des Produktdesigns, Arbutus Medical
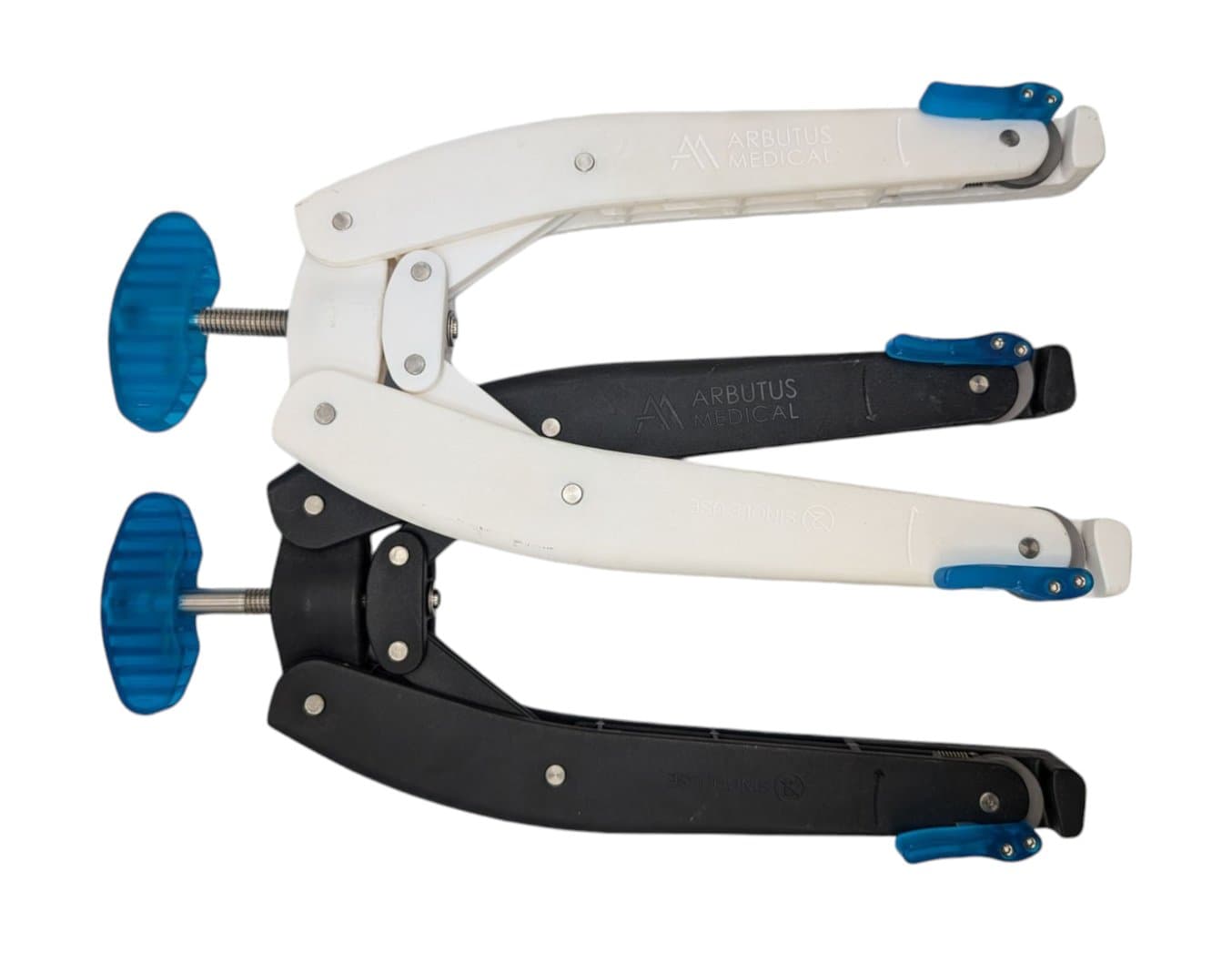
3D-gedruckter Prototyp aus Rigid 10K Resin (oben) und spritzgegossener T1 (unten). Letztendlich entschied sich Arbutus Medical für die endgültigen Medizinprodukte für eine schwarze Farbe, da Blutflecken darauf weniger sichtbar sind als auf weißen Teilen.
„Ich habe den Prototyp aus Rigid 10K Resin und das spritzgegossene T1 immer noch. Jedes Mal, wenn jemand in meine Werkstatt kommt, zeige ich ihm die Teile als Beispiel dafür, was alles möglich ist. Die Leute sind immer wieder begeistert, wie gut die Baugruppe aus Rigid 10K Resin aussieht. Sie können den Unterschied zum Spritzguss nicht erkennen, außer anhand der Farbe.“
Phil Tsao, Gründer von Ember Prototypes
„Während dieser Phase der Prototypenentwicklung haben wir im Grunde fast wöchentlich iteriert“, so Tsao. „Alle drei oder vier Tage sendete Radu uns eine neue Iteration, die wir druckten und dann zu ihm schickten. Das ist wie eine Rapid-Prototyping-Abteilung, nur nicht als Teil des eigenen Unternehmens, sondern extern.“
Ein Vorteil der Zusammenarbeit mit Ember Prototypes war die Zeitersparnis. Da Tsao die Arm-Komponenten druckte, konnte Postole mit seinem Form 3 intern andere Bauteile drucken, was seine Iterationsgeschwindigkeit noch beschleunigte. Insgesamt haben Postole und Tsao in vier Monaten mehr als 30 Iterationen von Prototypen durchgeführt, darunter auch einige Durchläufe im Tagesturnus, die bereits am Folgetag zur Begutachtung an Chirurgieteams versendet wurden.
Zu diesem Prozess gehörte auch, die Anwenderrückmeldungen hinsichtlich Benutzerfreundlichkeit, Leistung und Mehrwert auszuwerten, was ein Hauptgrund dafür war, dass die 3D-gedruckten Prototypen wie fertige, spritzgegossene Vorrichtungen aussehen sollten.
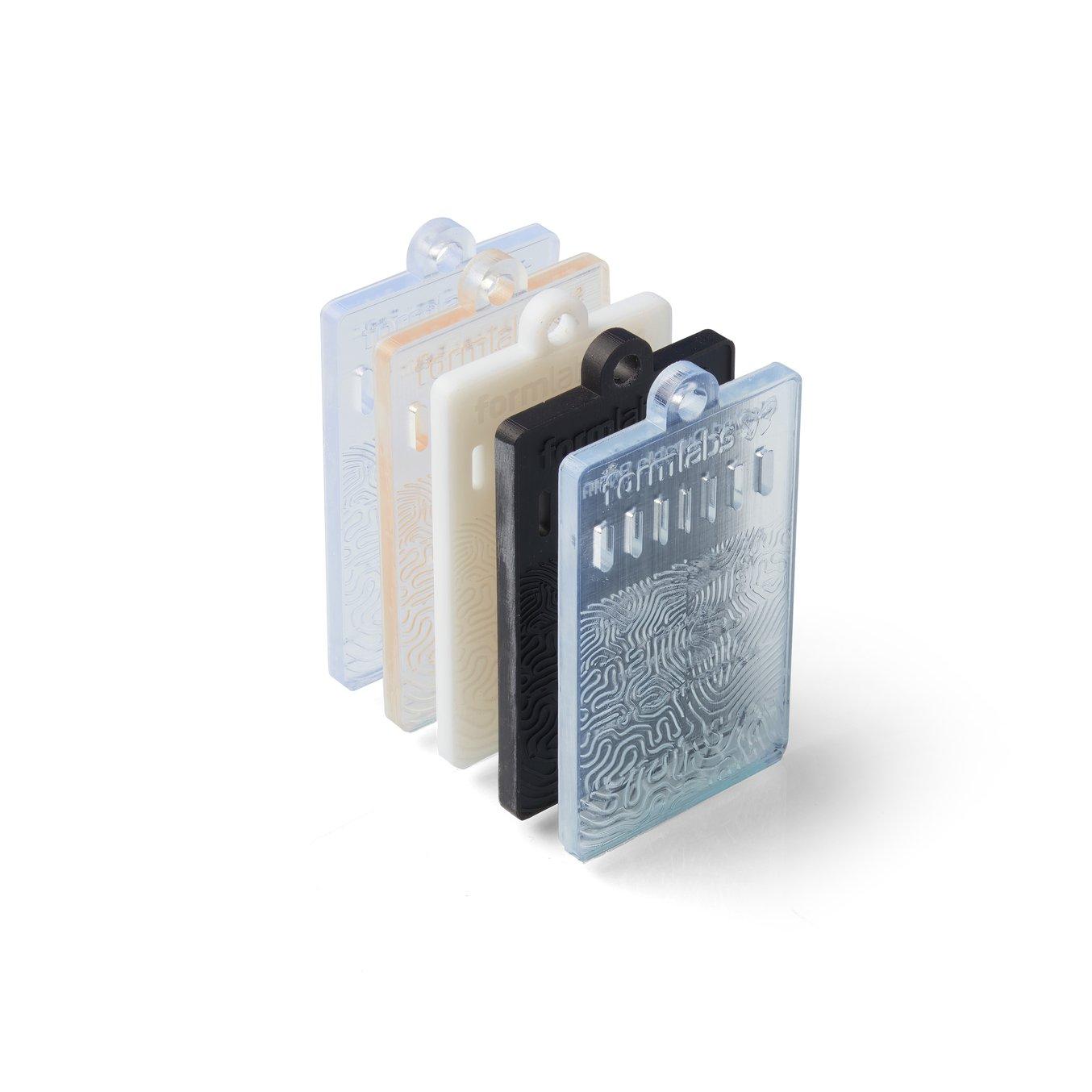
Proben der BioMed-Kunstharze
Jedes Probestück umfasst geprägte und hervorgehobene Merkmale, Ausschnittstärken von 0,5–2 mm sowie behördliche Regulierungen des jeweiligen Kunstharzes.
Aufwertung kommerzialisierter Medizinprodukte
QuikBow® kam Anfang 2023 auf den Markt. Innerhalb weniger Monate erhielt Arbutus Medical das Feedback, dass Notaufnahme-Teams mit dem QuikBow® eine schnellere und bessere Patientenversorgung erreichten. Es war jedoch immer noch ein Bettrahmen notwendig, um Zugkraft nach oben zu erzielen und die Vorrichtung vom Schienbein des Patienten abzuheben.
Bettrahmen sind klobig und erfordern eine spezielle Einrichtung, Lagerung und Nachverfolgung, was Zeit und Ressourcen von Krankenhäusern verschwendet. Um dieses Problem zu lösen, hatten Radu und das Design-Team von Arbutus einen Geistesblitz: Sie konnten Adapter für den QuikBow® mit seitlichen Scharnieren entwerfen, die den Bogen anheben, sodass er das Schienbein des Patienten freigibt. „Mit dieser Innovation konnten wir im Grunde auf herkömmliche Bettrahmen und Rollensysteme verzichten, deren Beschaffung im Krankenhaus bis zu zwei Stunden dauern kann“, erklärt Postole.
Die Hinzufügung der Scharniere erfolgte volle drei Monate nach der Markteinführung von QuikBow®. „Wir haben in kürzester Zeit verschiedene Iterationen dieses Aufsatzes 3D-gedruckt und sie an die Chirurgen unseres Vertrauens gesendet. Die Lösung gefiel ihnen so gut, dass sie sie sofort haben wollten“, berichtet Postole. „Da kam der Form 3B ins Spiel. Wir wussten, dass wir den Chirurgen diese neue Produktkomponente sofort an die Hand geben können, wenn wir das richtige Material verwenden.“
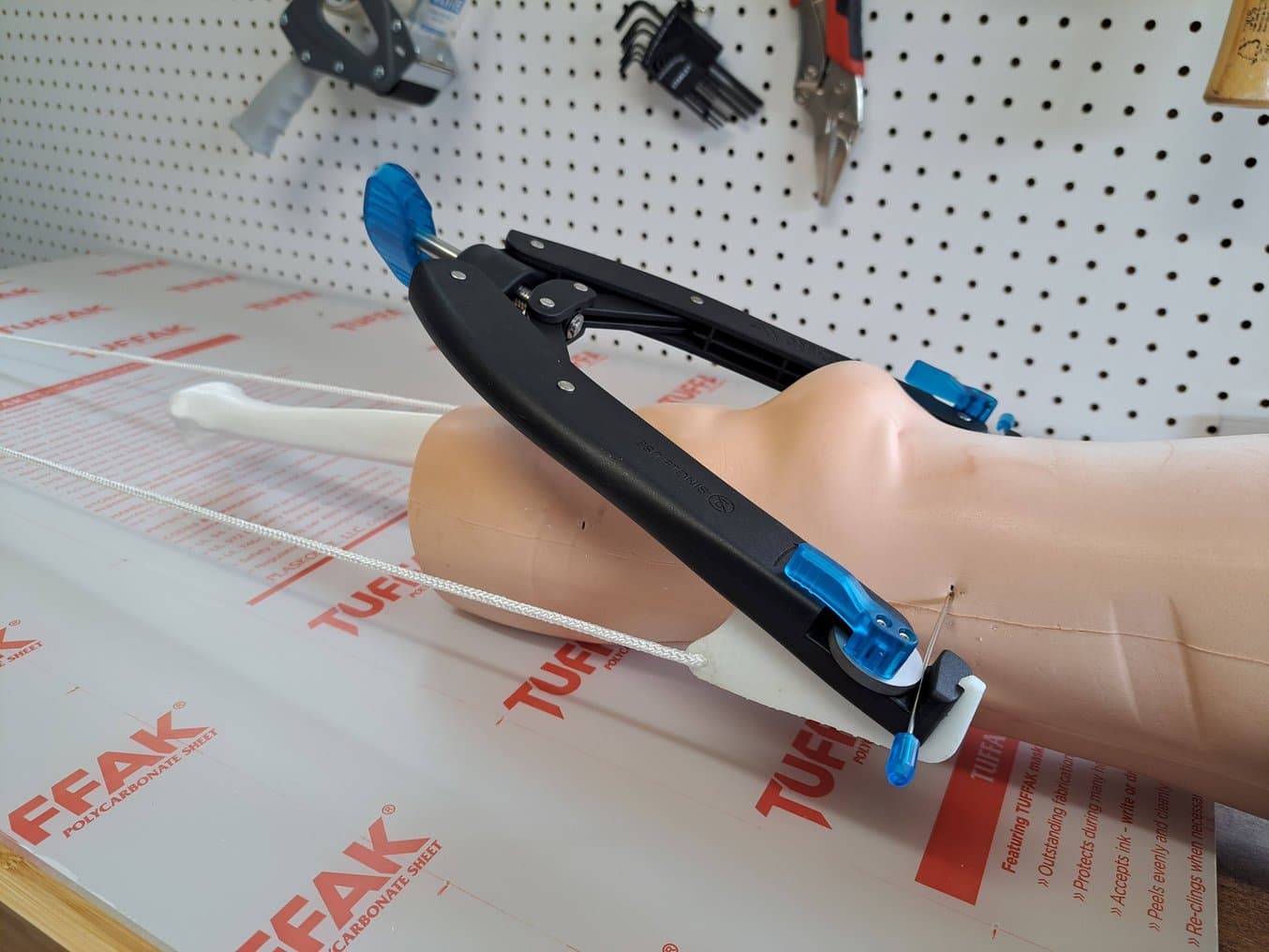
Ein früher Prototyp der Scharniere für den QuikBow®. Indem Spannung auf die Scharniere gelegt wird, hebt sich der Bogen vom Schienbein ab, wodurch das Risiko von Druckgeschwüren vermindert wird.
Für die biokompatiblen Teile suchte Postole nach einem transparenten Harz, das zu den anderen lichtdurchlässigen Teilen der Baugruppe passen sollte. Er testete BioMed Clear Resin und BioMed Durable Resin, wobei die Wahl wegen seiner überragenden Schlagfestigkeit schließlich auf BioMed Durable Resin fiel. Postole stellte fest: „Beide Materialien waren für unsere Anwendung sehr tauglich. BioMed Clear Resin hat zwar unsere erste Schlagprüfung bestanden, aber BioMed Durable bot uns einen größeren Sicherheitsspielraum für wiederholte Aufpralle.“
Innerhalb weniger Monate produzierte Arbutus Medical die ersten klinischen Einheiten, die durch ein Qualitätssicherungssystem freigegeben wurden.
„Wir haben alle Tests und Validierungen mit 3D-Druckteilen durchgeführt. Es war im Grunde ein Viermonatsprojekt von der Idee bis zum verkaufsfähigen Teil.“
Radu Postole, Leiter des Produktdesigns, Arbutus Medical
Bei den meisten herkömmlichen Medizinprodukten dauert es mehr als drei Monate, bis überhaupt die Formwerkzeuge hergestellt sind und die Produktion der Teile beginnen kann. Bei all den Hindernissen, die ein Medizinprodukt überwinden muss, um in einem Krankenhaus eingesetzt zu werden, wollte Arbutus Medical seine Verbesserung sofort umsetzen können, ohne auf Formwerkzeuge zu warten. Daher musste eine andere Fertigungsmethode her.
3D-Druck für die Übergangsfertigung mit Ember Prototypes
Da Postole kontinuierliches Feedback zu den neuen Scharnierpunkten des Bogens wünschte und den Chirurgen den QuikBow® weiterhin zur Verfügung stellen wollte, wollte er sich nicht auf Formwerkzeuge für die Scharniere festlegen. Diese kosten nämlich rund 25 000 Dollar und können nach ihrer Fertigstellung nicht einfach ausgetauscht werden. Postole erläutert: „Da kam der Form 3B zum Einsatz, denn er war für uns eine gute Zwischenlösung – wir fertigten die Teile einfach weiter mit 3D-Druck. Irgendwann war die Nachfrage so groß, dass wir intern nicht mehr mithalten konnten, und so kam Ember ins Spiel und übernahm im Grunde den gesamten 3D-Druck.“
3D-Druck ermöglicht nicht nur eine schnelle Fertigung, sondern auch eine Fertigung mit denselben Verfahren wie bei der Prototypenentwicklung, was die Effizienz erhöht. Außerdem lässt sich die Fertigung durch Hinzufügen von Druckchargen oder Druckern bei steigender Nachfrage leicht skalieren.
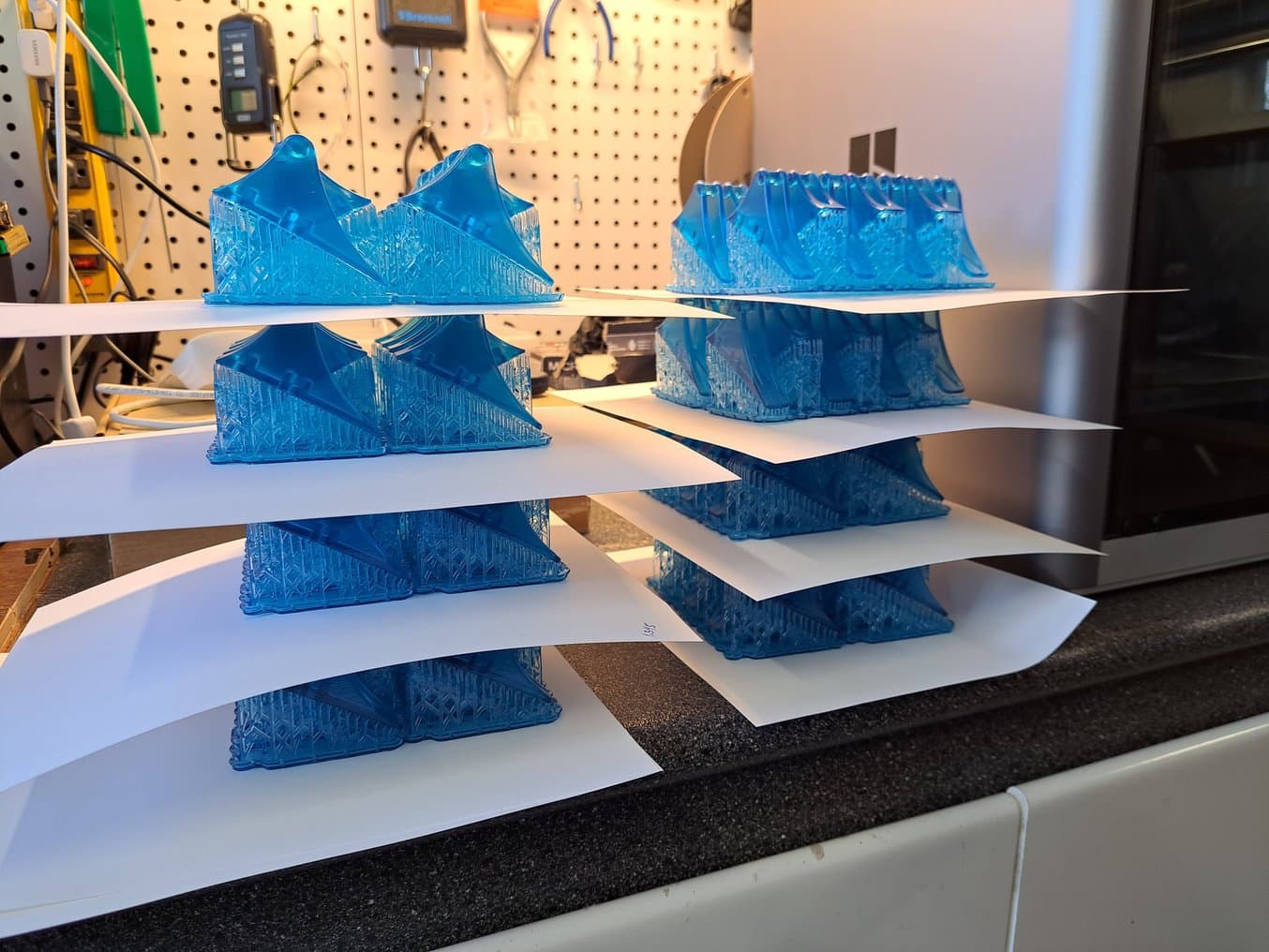
Die Übergangsproduktionsserien des QuikBow®-Scharniers wurden im Form 3B 3D-gedruckt.
Als die Nachfrage stieg, lagerte Arbutus Medical die 3D-Druck-Fertigung der Scharniere an Ember Prototypes aus, wo Tsao zwei Chargen pro Tag druckte. Mithilfe dieser Zwischenlösung für die Fertigung konnte Arbutus Medical zur Verbesserung der Patientenversorgung beitragen und mit seinem neuen Produkt fünf bis sechs Monate früher einen Umsatz generieren. Gleichzeitig senkte das Unternehmen sein Risiko, da keine Investitionen in teure Formwerkzeuge nötig waren, bevor klinisches Feedback vorlag.
Nachdem Arbutus Medical zunächst davon ausgegangen war, dass insgesamt 200–500 Teile benötigt werden würden, druckte Tsao schon bald etwa 200 Teile pro Woche (14 Teile pro Druck, zwei Drucke pro Tag) und lieferte etwa 800 Teile pro Monat. Der 3D-Druck in diesem Maßstab erforderte einen gut durchdachten Workflow, unter anderem zum Waschen und Verpacken der Teile. Tsao entwarf und produzierte mit 3D-Druck eine maßgefertigte Halterung, um die Teile beim Waschen zu fixieren und so eine optimale Oberflächenbeschaffenheit zu gewährleisten. Beim Verpacken der Teile stellte er fest, dass Papier oder andere Materialien Fasern auf den Teilen hinterlassen konnten, während sie in Plastikbeuteln sauber blieben. Diese Arbeitsabläufe ermöglichten es Tsao, Teile mit der Optik und Haptik von spritzgegossenen Produkten zu liefern, jedoch ohne den Kostenaufwand und ohne Einbußen bei der Designfreiheit.
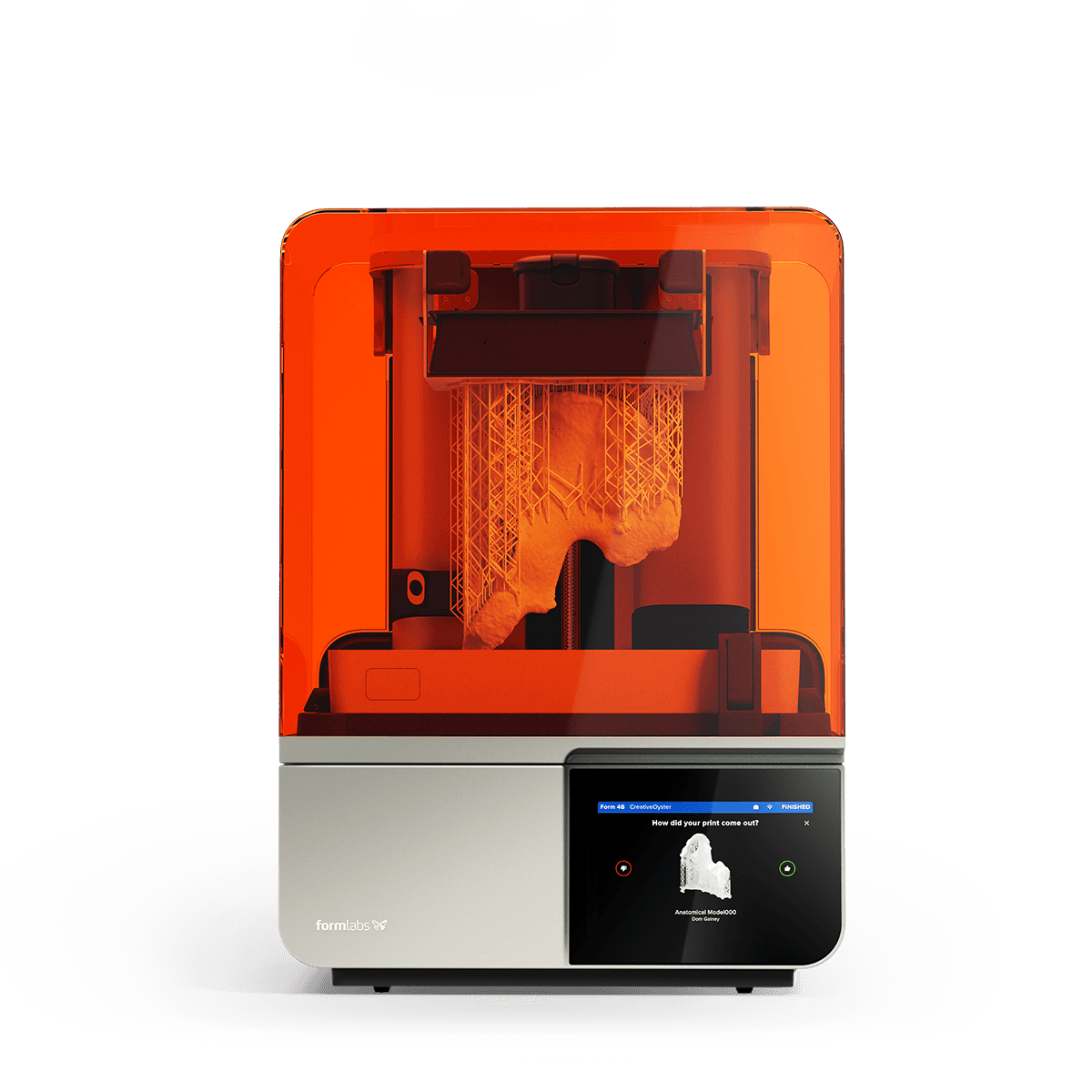
Der neue Form 4B: Schnellere Fertigung, höhere Präzision, behördliche Konformität
Das Team von Formlabs Healthcare präsentiert unseren neuen Form 4B. Neben einem technischen Überblick erörtert Bradley Heil, Leiter für Qualitätssicherung und regulatorische Fragen bei Formlabs, die behördlichen Aspekte der Medizinprodukteherstellung mithilfe von Formlabs-3D-Druckern.
Die Arbeitstiere hinter Prototyping und Fertigung: 3D-Drucker der Form-Serie

Form Wash, Form 3B, und Form 3L bei Ember Prototypes. Tsao verwendet den Form 3B für die Fertigung biokompatibler Teile und den Form 3L für den Druck im Großformat.
Schon seit der Einführung des Form 2 arbeitet Tsao mit Kunstharz-3D-Druckern von Formlabs. Seitdem hat er einen Form 3, einen Form 3B für biokompatiblen Druck und einen Form 3L für großformatigen Druck im Einsatz.
„Der wichtigste Faktor für mich ist die Benutzerfreundlichkeit direkt nach dem Auspacken und die Auswahl der Materialien. Ich arbeite nicht nur mit Leuten wie Radu zusammen, sondern auch mit vielen anderen Startups und Unternehmen aus dem Ingenieur- und Technologiebereich, und jeder hat unterschiedliche Anforderungen. Manche brauchen Teile mit geringer Reibung. Manche interessieren sich nur für Ästhetik. Manche brauchen eine besonders hohe Steifigkeit, wie Radu und Arbutus. Für Ember ist es deshalb wichtig, über diese breite Palette von Materialien zu verfügen und genau zu wissen, welche mechanischen Eigenschaften sie bieten und wie zuverlässig sie sind.“
Phil Tsao, Gründer von Ember Prototypes
Bis 2019 hatte Postole FDM-Drucker verwendet. Mit dem FDM-Druck konnten wir nicht diese Leistung erreichen. Die Teile waren nicht solide. Wir hatten ständig verstopfte Düsen. Es erforderte einfach eine Menge Arbeit und verschwendete viel Zeit“, sagt Postole. Er bat Tsao um eine Empfehlung: „Als er uns den Form 3 empfahl und wir ihn bekamen, waren wir von der Festigkeit der Teile und der Möglichkeit, ohne Probleme wiederholt zu drucken, einfach überwältigt.“
Letztendlich, so Postole, „konnten wir durch den 3D-Druck von Produkten für den klinischen Einsatz einerseits schnell in den Markt eintreten und andererseits den Mehrwert und die Vermarktbarkeit des Produktes schnell validieren.“
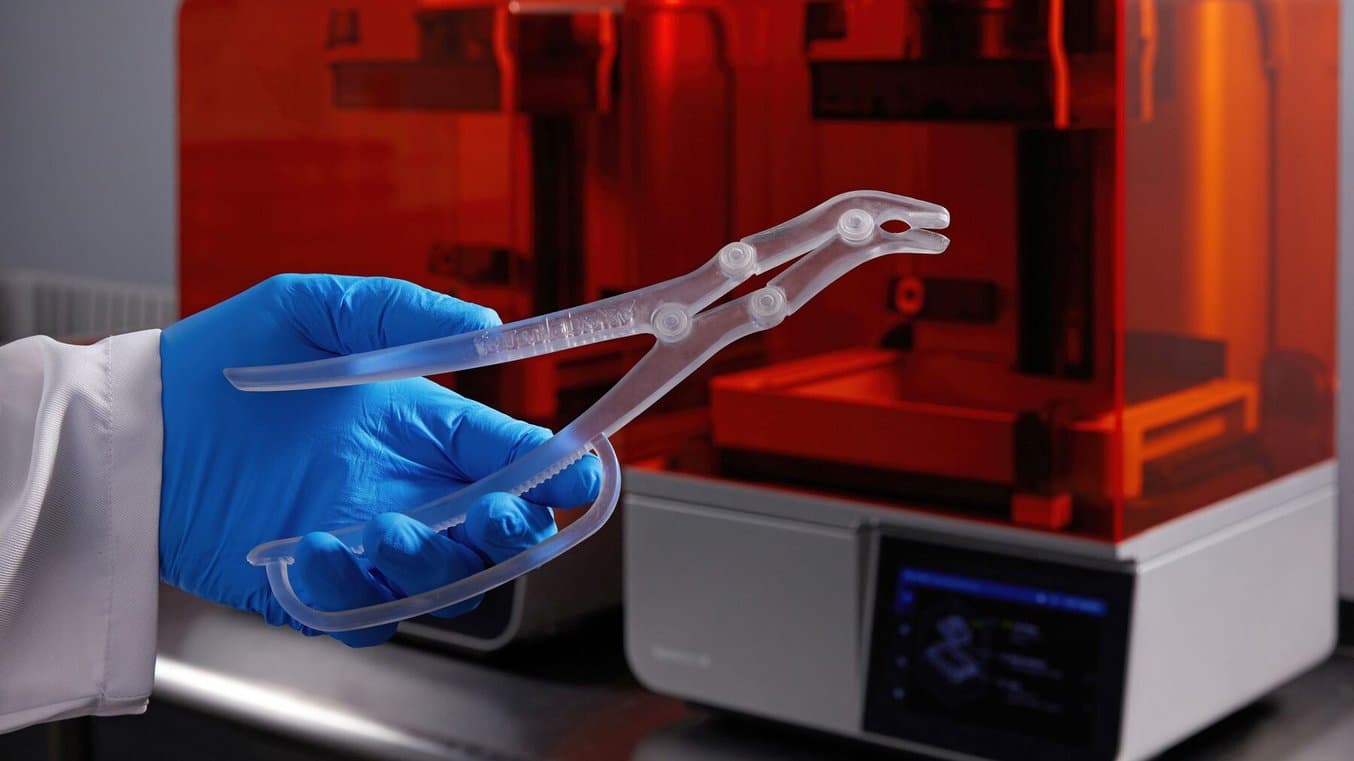
Von der Prototypenfertigung zur Produktion: Wie der betriebsinterne 3D-Druck die Entwicklung von Medizinprodukten vorantreibt
Medizinprodukte haben in der Regel längere Entwicklungszyklen als Konsumgüter, was zum Teil auf klinische Tests, Qualitätsstandards und behördliche Vorschriften zurückzuführen ist. Die Verringerung der Anzahl der Prototyping-Zyklen oder sogar das direkte 3D-Drucken von Endprodukten kann sich erheblich auf die Markteinführungszeit auswirken.
Was die Zukunft bereithält
Postole war ursprünglich davon ausgegangen, dass Arbutus Medical die adaptiven Scharniere für den QuikBow® auf unbestimmte Zeit mittels 3D-Druck fertigen würde. Als er jedoch feststellte, dass das Unternehmen auf dem besten Weg war, 10 000 Einheiten pro Jahr zu produzieren, führte Arbutus Medical eine Kostenanalyse durch und entschied sich für den Wechsel zum Spritzguss, nachdem das Design von chirurgischer Seite bestätigt war und nicht mehr geändert werden musste. Für das nächste Medizinprodukt, die Radu entwickelt, zieht er den 3D-Druck für die Produktion in Betracht, wobei die Materialeigenschaften, die verschiedenen Optionen und die Kosten abzuwägen sind.
„Je mehr sich die Materialieneigenschaften verbessern, die Kosten sinken und die Druckgeschwindigkeit steigt, umso mehr kann ich mir vorstellen, dass wir Produkte einfach länger mit 3D-Druck produzieren, bis wir eine Nachfrage von 10 000 pro Jahr erreichen.“
Radu Postole, Leiter des Produktdesigns, Arbutus Medical
Für Arbutus Medical sind sowohl der 3D-Druck als auch der Spritzguss wichtige Fertigungsmethoden. Mit 3D-Druck lassen sich visuelle wie auch funktionale Prototypen produzieren und das Produkt kann in der frühen Phase der Kommerzialisierung weiter verfeinert werden. Zudem kann der 3D-Druck für die Übergangsfertigung genutzt werden, während auf die Fertigstellung von Produktionswerkzeug gewartet wird.
„Wir haben jetzt einen Ablauf, der funktioniert. Wir fertigen mit dem Form 3 in kürzester Zeit hochgenaue Prototypen, die unsere Chirurgen beeindrucken. Damit haben wir etwas, das für uns sehr gut funktioniert, und iterieren einfach weiter und finden neue Wege, um die Patientenversorgung zu verbessern.“
Radu Postole, Leiter des Produktdesigns, Arbutus Medical
Arbutus Medical und Ember Prototypes arbeiten weiterhin zusammen. Die Vielfalt der Projekte, an denen Tsao bei Ember Prototypes arbeitet, zeigt auf, wie viele Probleme bei der Fertigung und Produktion auftreten, und er ist entschlossen, diese für seine Kunden zu lösen, genau wie für Arbutus Medical.
„Wir haben interne Produkte entwickelt, die speziell die Probleme der Fertigung und des 3D-Drucks lösen. Diese entwickeln wir jetzt zu eigenen Produkten weiter. Das Ecosystem von Formlabs spielt dabei eine ziemlich zentrale Rolle.“
Phil Tsao, Gründer von Ember Prototypes
Sehen Sie sich Ressourcen zur Entwicklung von Medizinprodukten mit 3D-Druck an, oder wenden Sie sich an unser Expertenteam, um mehr darüber zu erfahren, wie unsere 3D-Drucker Sie bei Prototyping, Fertigung und Produktion unterstützen können.