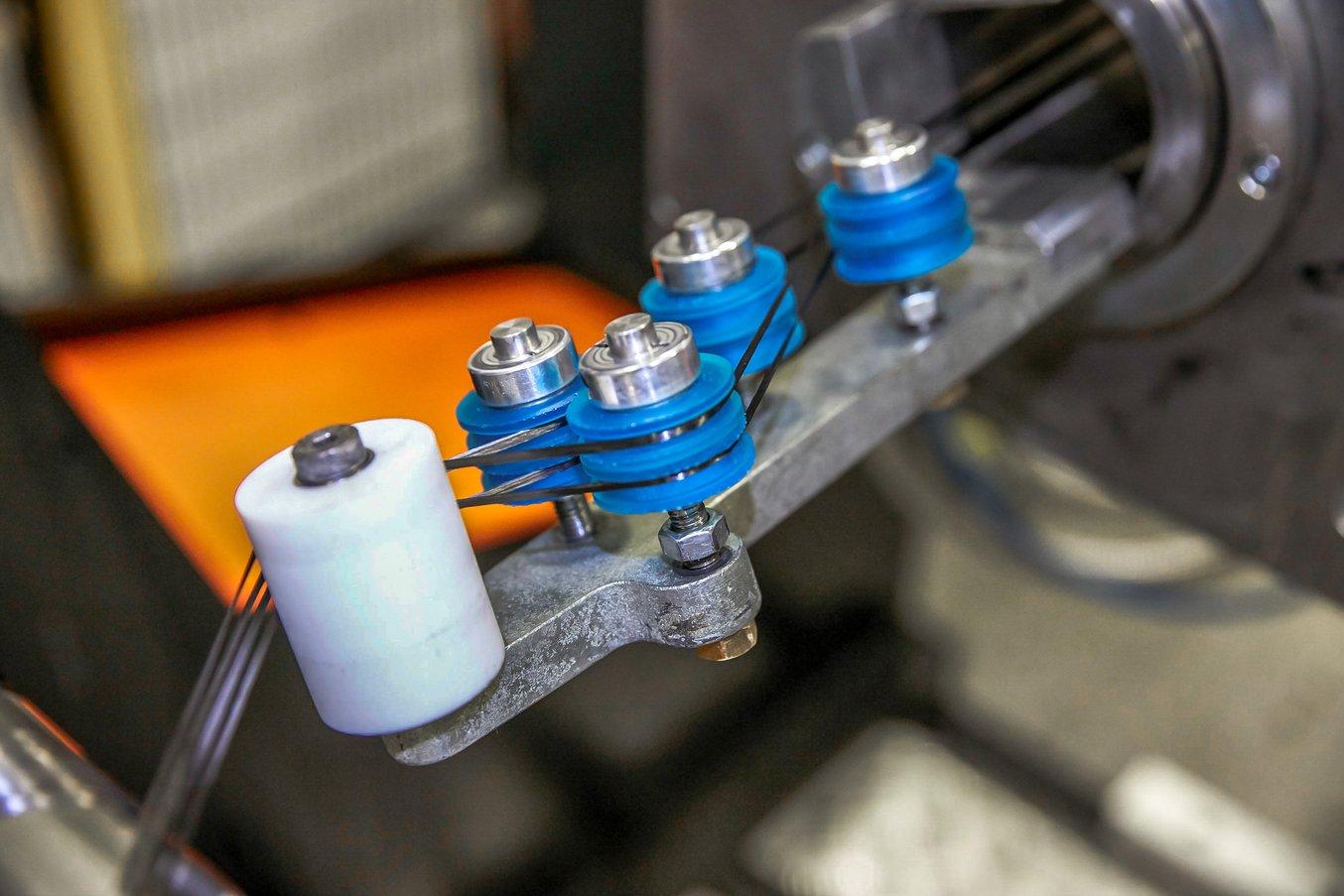
Verbundwerkstoffe wie Glasfasern und Kohlenstofffasern erhalten ihre hohe Festigkeit und ihr leichtes Gewicht von der Art und Weise, wie die Faserstränge gewebt und in den Teilen verlegt sind. So bieten sich einzigartige Möglichkeiten zur Verbesserung von Designs auf Grundlage der Belastungen, die laut Analyse der Ingenieure auf die Bauteile einwirken werden. Aber die Arbeit mit diesen maßgeschneiderten und nicht-standardisierten Materialien birgt auch zahlreiche Herausforderungen bei der Fertigung.
Das Composites Centre des Advanced Manufacturing Research Centre (AMRC) der University of Sheffield führt Forschungen durch, bei denen hochmodernen Methoden eingesetzt werden, um diese Herausforderungen für Branchen mit hoher Wertschöpfung wie Luft- und Raumfahrt, Schiffs- und Kraftfahrzeugbau zu lösen.
Eines der Forschungsprojekte in dem Zentrum untersucht die Faserwicklung, die für gewöhnlich zur Fertigung von Kraftstoffrohren, Schläuchen, Behältern und Wellen für die Luft- und Raumfahrt und die Automobilindustrie eingesetzt wird. Bei der Arbeit mit unterschiedlichen Materialien, die verschiedene Breiten aufweisen, mussten die Forscher das System anpassen, um die Fasern mit der hohen Genauigkeit verarbeiten zu können, die in der Luft- und Raumfahrt gefordert wird.
Lesen Sie weiter, um von Alexander Shaw, einem Verbundwerkstoff-Automatisierungstechniker, der an dem Projekt arbeitet, zu erfahren, wie die Forscher verschiedene Versionen von maßgeschneiderten Rollen entwickelt, 3D-gedruckt und die frei zugängliche additive Fertigungsstation des AMRC genutzt haben, um die Teile innerhalb von Tagen herzustellen.
Sehen Sie sich das Video an, um einen Einblick ins Composites Centre zu erhalten und zu sehen, wie die Forscher die maßgeschneiderten Rollen für die Faserwicklung eingesetzt haben
Shaw und das Ingenieurteam arbeiteten an der frei zugänglichen additiven Fertigungsstation des AMRC, um die erforderlichen Teile herzustellen. Lesen Sie unsere Fallstudie, um zu erfahren, wie der freie Zugang zu 3D-Druck hunderten von Ingenieuren an einem Standort helfen kann.
Die einzigartigen Herausforderungen bei der Arbeit mit Verbundwerkstoffen
Eine Faserwickelmaschine funktioniert wie folgt: eine Faserspule läuft durch ein Harzbad und anschließend durch dünne Rollen, und gelangt so vom Spulengatter im hinteren Bereich des Systems zum Abgabekopf an einem sechsachsigen KUKA-Roboter. Die Faserfäden erreichen dann eine metallische Spindel, die sich wie ein Werkstück in einer Drehmaschine dreht. Der Roboterkopf bewegt sich und trägt die Faser auf die sich drehende Spindel auf.
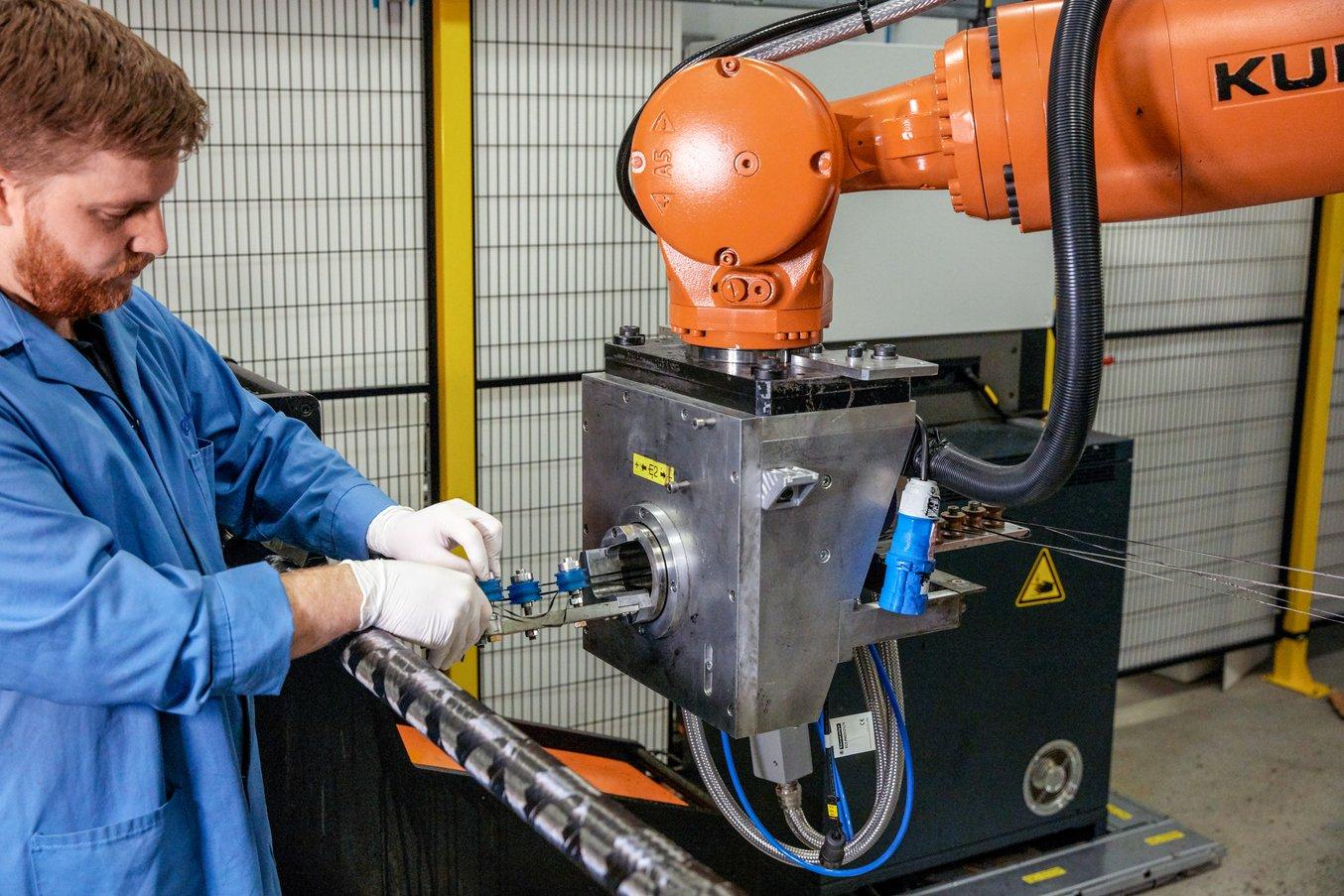
Verschiedene Fasern können verschiedene Materialbreiten aufweisen oder etwas unregelmäßig sein, was Probleme beim Durchführen durch die Rollen verursachen kann. Als die Forscher auf ein anderes Material umstiegen, das etwas schmaler als das Vorgängermaterial war, musste aufgrund der zusätzlichen Variation der Breite eine Rolle hergestellt werden, die etwas schmaler war als die ursprüngliche Rolle, die in der Maschine verbaut war.
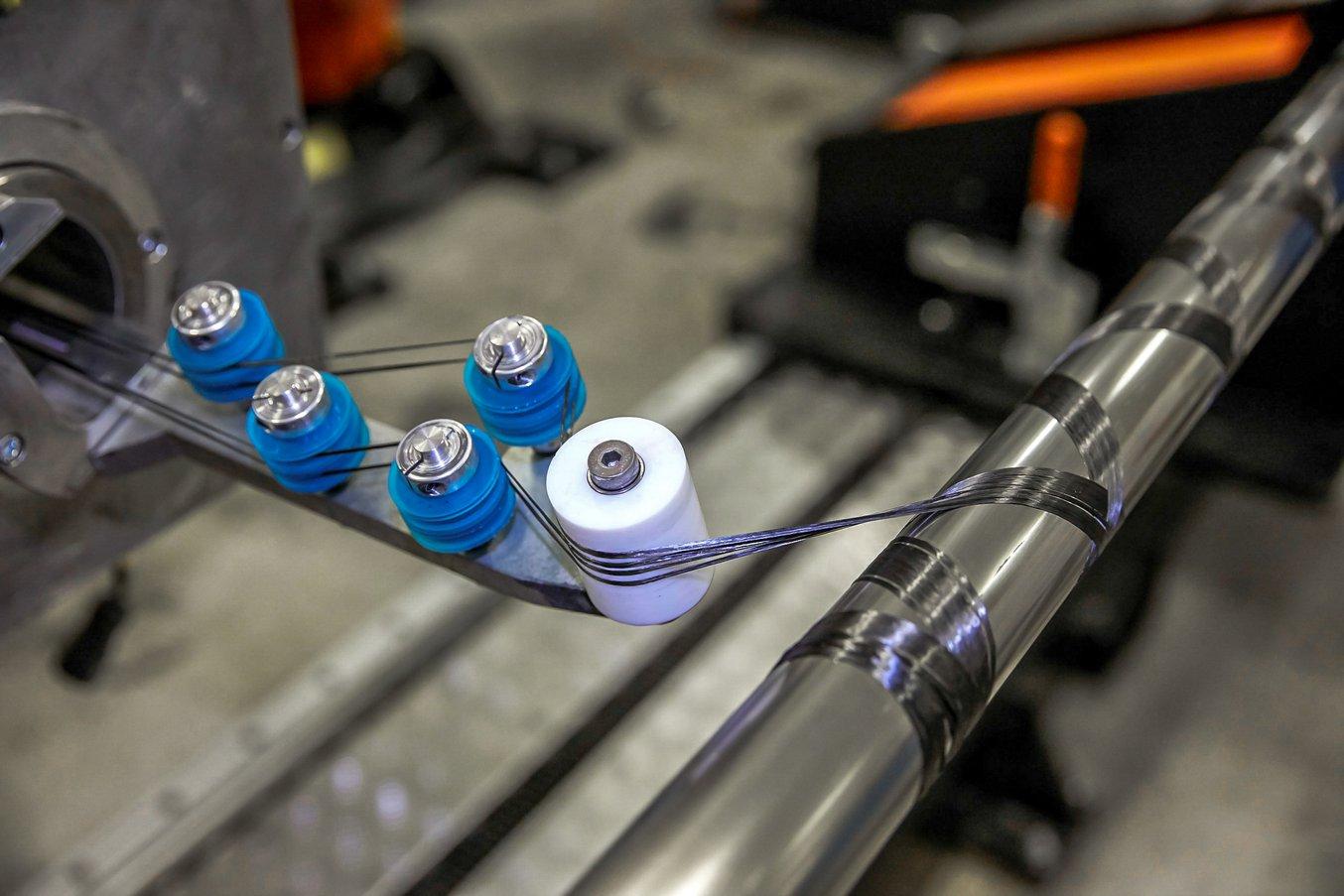
„Wenn man eine schmalere Laufbreite hat als das Material, das über die Rollen läuft, kommt es zu Spalten auf der Lauffläche und das Material wird ungleichmäßig verteilt. Wenn diese Spalten größer sind als etwa ein Millimeter, erfüllen die Teile nicht die Richtlinien der Luft- und Raumfahrt“, erklärt Shaw.
Fertigung der Teile mit additiven statt zerspanenden Werkzeugen
Um das System an die neuen Materialien anzupassen, hat Shaw die Standardrollen untersucht und drei neue Versionen entwickelt, die alle über unterschiedliche Durchmesser und Breiten verfügten, abhängig von dem Material, für das sie gedacht waren. Beispielsweise haben sie für ein 6 mm breites Material Rollen gedruckt, die über eine Mittelfläche mit 6 mm und Außenflächen mit 3 mm verfügen, so dass beim Zusammenführen von zwei Fäden nebeneinander kein Spalt zwischen den oberen und den unteren Gattern entsteht.
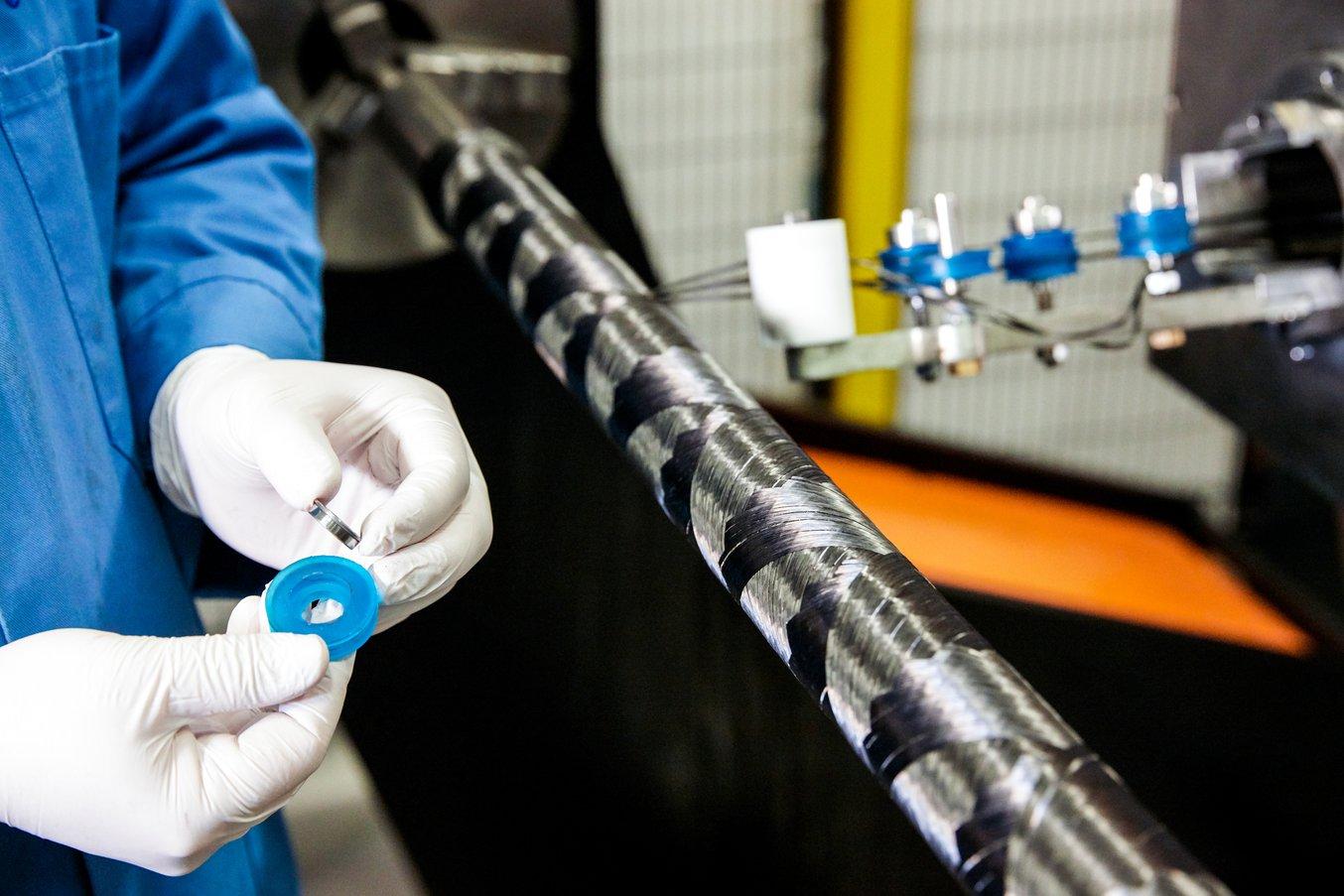
Das Team benötigte die neuen Rollen so schnell wie möglich, um mit dem Projekt fortfahren zu können, und entschied, dass der 3D-Druck die beste Methode zur Fertigung der Teile sei.
„Die spanende Fertigung neuer Rollen würde deutlich mehr kosten und die Durchlaufzeiten wären möglicherweise länger als eine Woche, wohingegen wir mit den Formlabs 3D-Druckern etwas drucken und noch am selben Tag in den Händen halten konnten“, so Shaw.
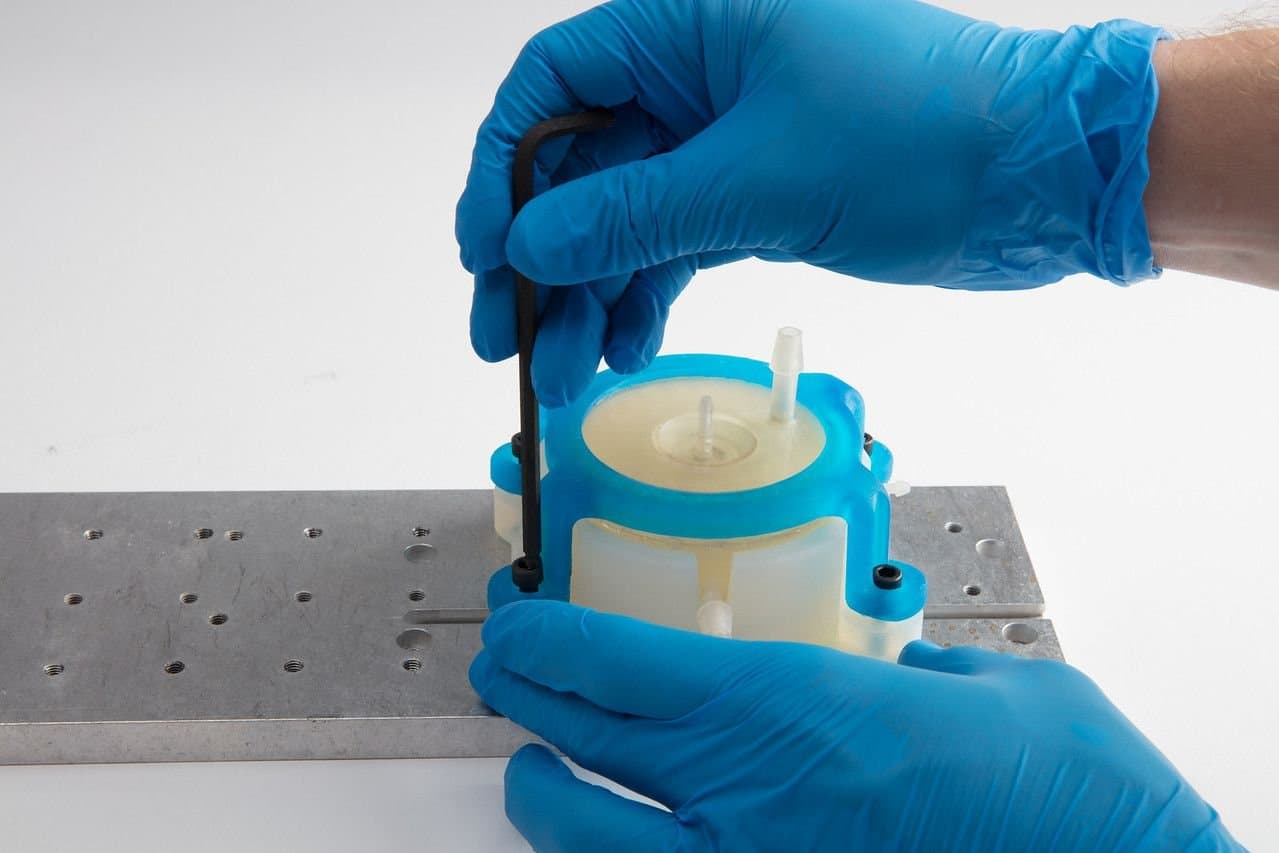
3D-gedruckte Haltevorrichtungen
Laden Sie unser Whitepaper herunter, um zu erfahren, wie Sie mit 3D-gedruckten HaltevorrichtungenKosten reduzieren, die Entwicklungszeit verkürzen und besser optimierte Arbeitsprozesse schaffen können.
White Paper herunterladen
Nutzung der firmeninternen 3D-Druckstation
„Wir haben uns schon vorher mit dem 3D-Druck beschäftigt. Es ging einfach darum, wie zugänglich es für alle sein würde. Es gab nur drei oder vier Leute, die für die Anwendung der Geräte geschult waren. An die Software und alles andere mussten wir uns erst ein bisschen heranarbeiten“, so Shaw.
Shaw hat mit der Design and Prototyping Group des AMRC zusammengearbeitet, um die 3D-Druckteile herzustellen. Die Gruppe hat vor kurzem eine neue additive Fertigungsstation mit einer Flotte von 12 Form 2 installiert, die allen Ingenieuren am Standort freien Zugang zum 3D-Druck bietet.
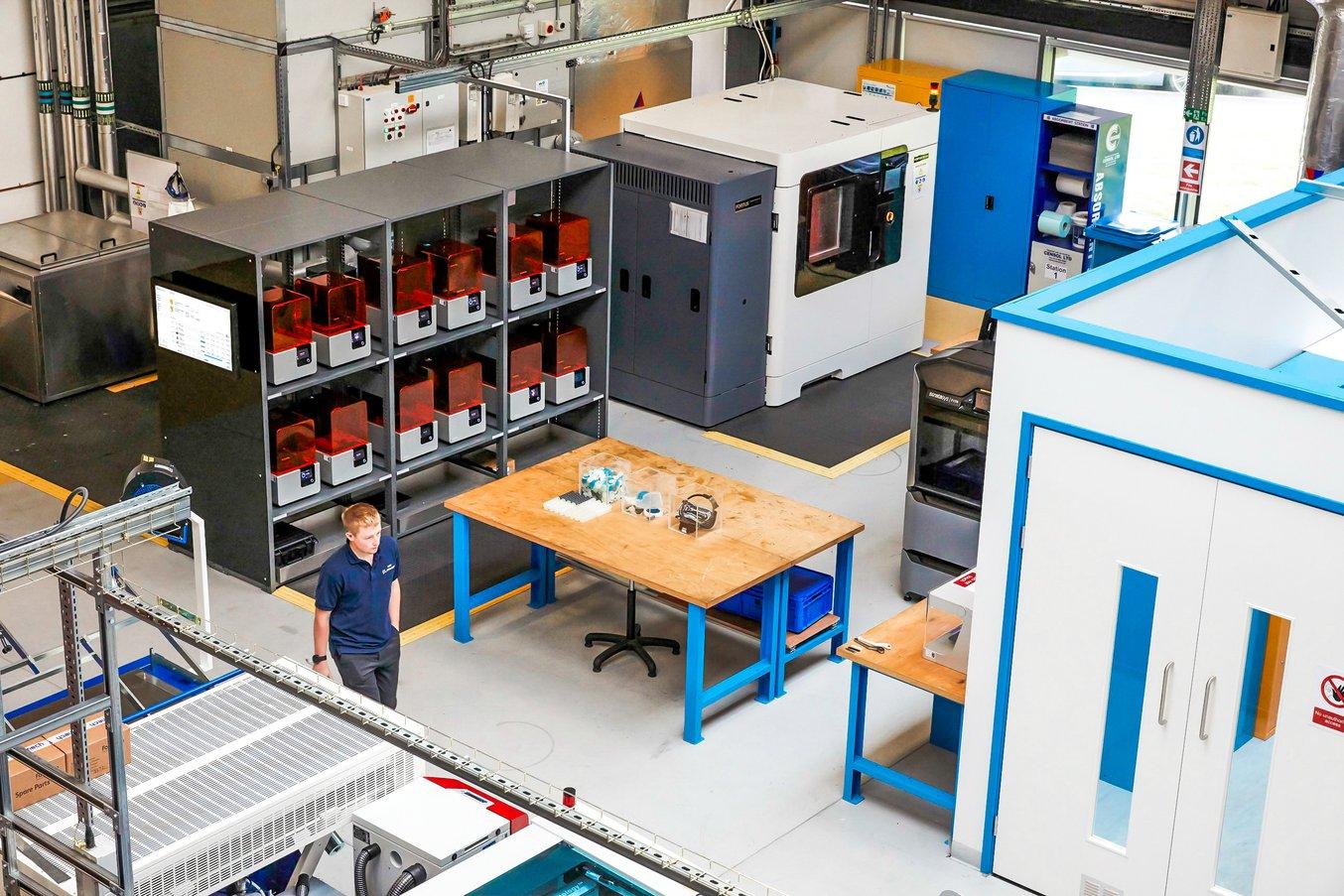
Nachdem die neuen Drucker eingetroffen waren, meldete sich Mark Cocking, der technische Leiter für Polymeradditive, an alle Mitarbeiter im Composite Centre und fragte, ob sie an einer Schulung interessiert wären.
„Ich glaube 90 Prozent aller Mitarbeiter im Composites Centre sagten: ‚Ja, das ist etwas, das wir auf jeden Fall gebrauchen können.‘ Die Softwarevorführung und die Besprechung der Details dauerte nur etwa 20 bis 30 Minuten. Die Software lässt sich so einfach bedienen. Man erstellt einfach eine STL, fügt sie per Drag & Drop in die Software ein und diese kümmert sich um den Rest. Heute gibt es knapp ein Dutzend Mitarbeiter in unserer Gruppe, die an den Formlabs Druckern geschult worden sind“, erzählt Shaw.
Erfahren Sie, wie eine 3D-Druckstation hunderte von Ingenieuren im AMRC unterstützt
Erfahren Sie mehr über die 3D-Druckstation des AMRC und über andere Anwendungen wie den Seriendruck von 500 hochpräzisen Bohrkappen für Bohrversuche für Airbus, eine temperaturbeständige Sensorhalterung für eine Schweißanwendung und hochkomplexe Halterungen für einen Robotergreifer bei der Herstellung von Verbundwerkstoffen.
Möchten Sie mehr über die Drucker und die Technologie hinter der 3D-Druckstation des AMRC erfahren? Lernen Sie den Form 3, den großformatigen Form 3L, und Bibliothek an technischen Kunstharzen von Formlabs für Ihr eigenes Projekt kennen, oder fordern Sie einen kostenlosen Probedruck an, um sich selbst einen Eindruck von den Materialien zu verschaffen.