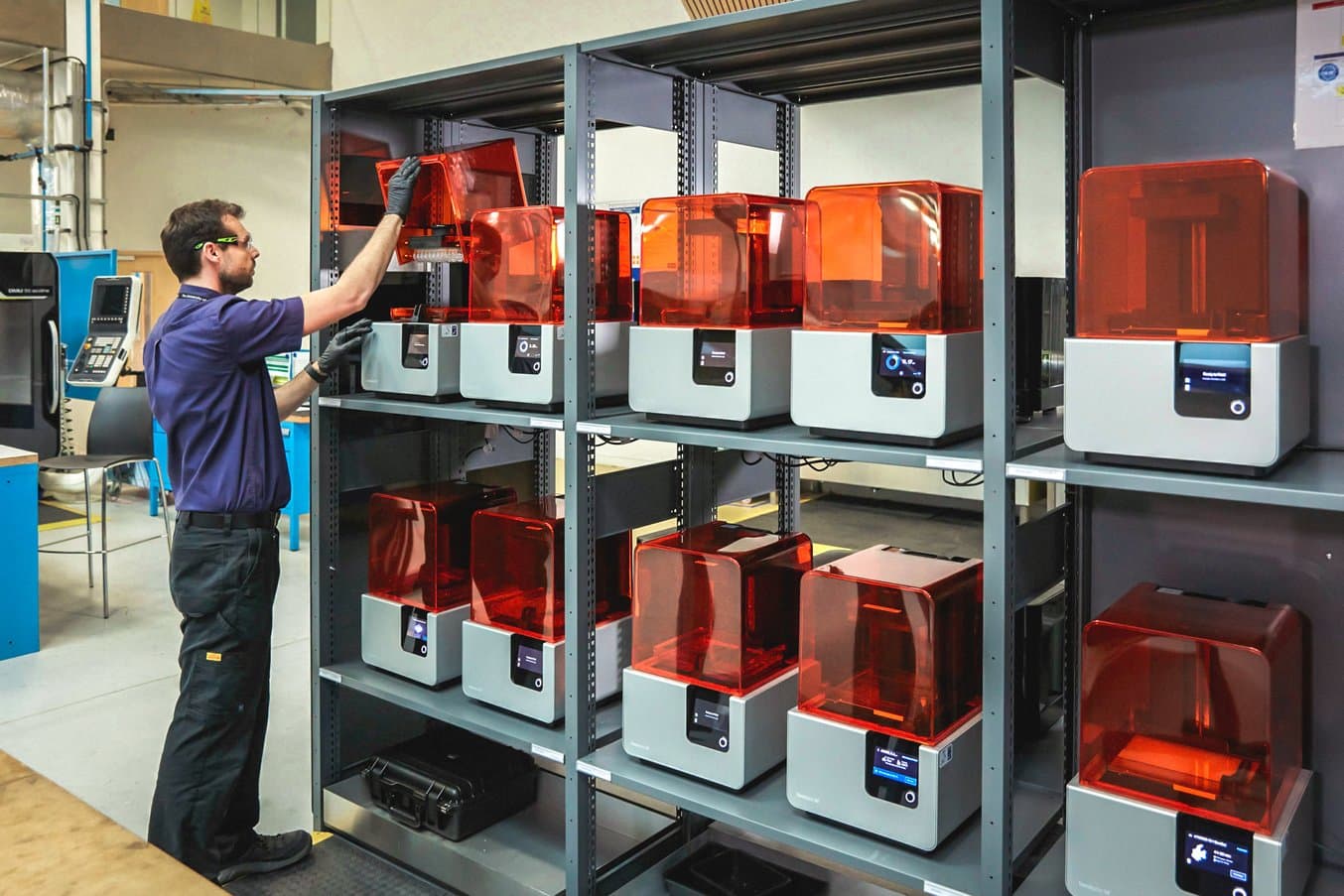
Ein ehemaliger Kohletagebau mag sich zunächst nicht wie der Ort anhören, an dem die Zukunft der Fertigungsindustrie bestimmt wird. Doch auf einem Grundstück aus mehr als 40 Hektar wiedergewonnenem Land außerhalb von Sheffield ist die höchste Dichte an fertigungstechnischen Fähigkeiten und Kenntnissen in ganz Großbritannien anzutreffen.
Das University of Sheffield Advanced Manufacturing Research Centre (AMRC) führt Forschung der Weltklasse in den Bereichen fortschrittliche Bearbeitung, Fertigung und Werkstofftechnik durch und hilft 100 Industriepartnern – von Global Playern wie Boeing, Rolls-Royce, BAE Systems und Airbus bis hin zu kleinen Unternehmen, die konkurrenzfähiger werden wollen. Diese Geschäftspartner treten mit spezifischen Herausforderungen an das AMRC heran, und die Forscher des Zentrums nutzen die neuesten Technologien und Prozesse, um Konzepte und Lösungen zu entwickeln, die die Partner in ihren Werken einsetzen können.
Additive Fertigung gehört seit langem zu den verschiedenen Verfahren, die Forscher nutzen könnten, um Konzepte und Ideen schnell umzusetzen, doch die komplexen und teuren Geräten haben den Zugang zu dieser Technologie und deren Nutzung bislang eingeschränkt. Sie stehen mit ihrer Herausforderung nicht alleine da. Häufig kaufen Unternehmen teure moderne Geräte, die die Innovation vorantreiben sollen, sich dann aber weder in die unternehmensinternen Arbeitsprozesse integrieren noch effizient einsetzen lassen.
Das Ziel des AMRC ist es, Pionier bei der Integration von Technologie zu sein, die die Innovation beschleunigt, und es hat ein Rezept für 3D-Druck gefunden, das andere Unternehmen nutzen können. Die Design and Prototyping Group des AMRC hat vor kurzem eine neue additive Fertigungsstation mit einer Flotte von 12 Form 2 Stereolithografie (SLA) 3D-Druckern installiert, die hunderten von Ingenieuren am Standort freien Zugang zum 3D-Druck bei ihren verschiedenen Projekten bietet.
„Es hat unsere Tätigkeiten deutlich rationalisiert. [Zu jedem Zeitpunkt] laufen hunderte Projekte mit hunderten Ingenieuren. Da unsere Mitarbeiter jetzt Zugriff zum 3D-Druck haben, wurde bei jedem Projekt, bei dem additive Fertigung erforderlich ist, die Fertigungsdauer von Komponenten von etwa anderthalb Wochen auf einige Stunden reduziert“, berichtet Mark Cocking, der technische Leiter für Polymeradditive der Design and Prototyping Group des AMRC.
Erhalten Sie mit der Video-Story einen Einblick in das AMRC und erfahren Sie von Cocking und den Ingenieuren, die in dem Forschungszentrum arbeiten, mehr über die verschiedenen Anwendungen, die 3D-Druck in einer Fertigungsumgebung ermöglicht.
Freier Zugang zu 3D-Druck, um Innovationen zu fördern und Durchlaufzeiten zu reduzieren
Die Design and Prototyping Group des AMRC arbeitet mit Forschern des gesamten Standorts zusammen, um alles von Konzeptdesigns bis hin zu vollständig funktionalen Prototypen für verschiedene Branchen zu entwickeln.
„Einige der Teile, die wir herstellen, dienen nur zur Vorführung von Konzepten, aber sehr oft stellen wir auch Haltevorrichtungen und andere maßgefertigte Komponenten her, die für verschiedene Forschungsprogramme in Maschinen verbaut werden“, erzählt Cocking.
Um die Vielzahl der Anforderungen von der Kernenergie bis hin zur Verbundwerkstoff-Forschung abzudecken, ist das Forschungszentrum mit verschiedenen Anlagen wie industriellen Laserschneidsystemen, CNC-Fräsmaschinen, CT-Scannern und mehreren Metall-Lasersintersystemen sowie Schmelzschicht-(FDM)- und SLA 3D-Druckern ausgerüstet.
Erfahren Sie mehr über die drei verbreitetsten Technologien zum 3D-Druck von Kunststoffen, die aktuell genutzt werden: die Schmelzschichtung (FDM), die Stereolithografie (SLA) und das Selektives Lasersintern (SLS).
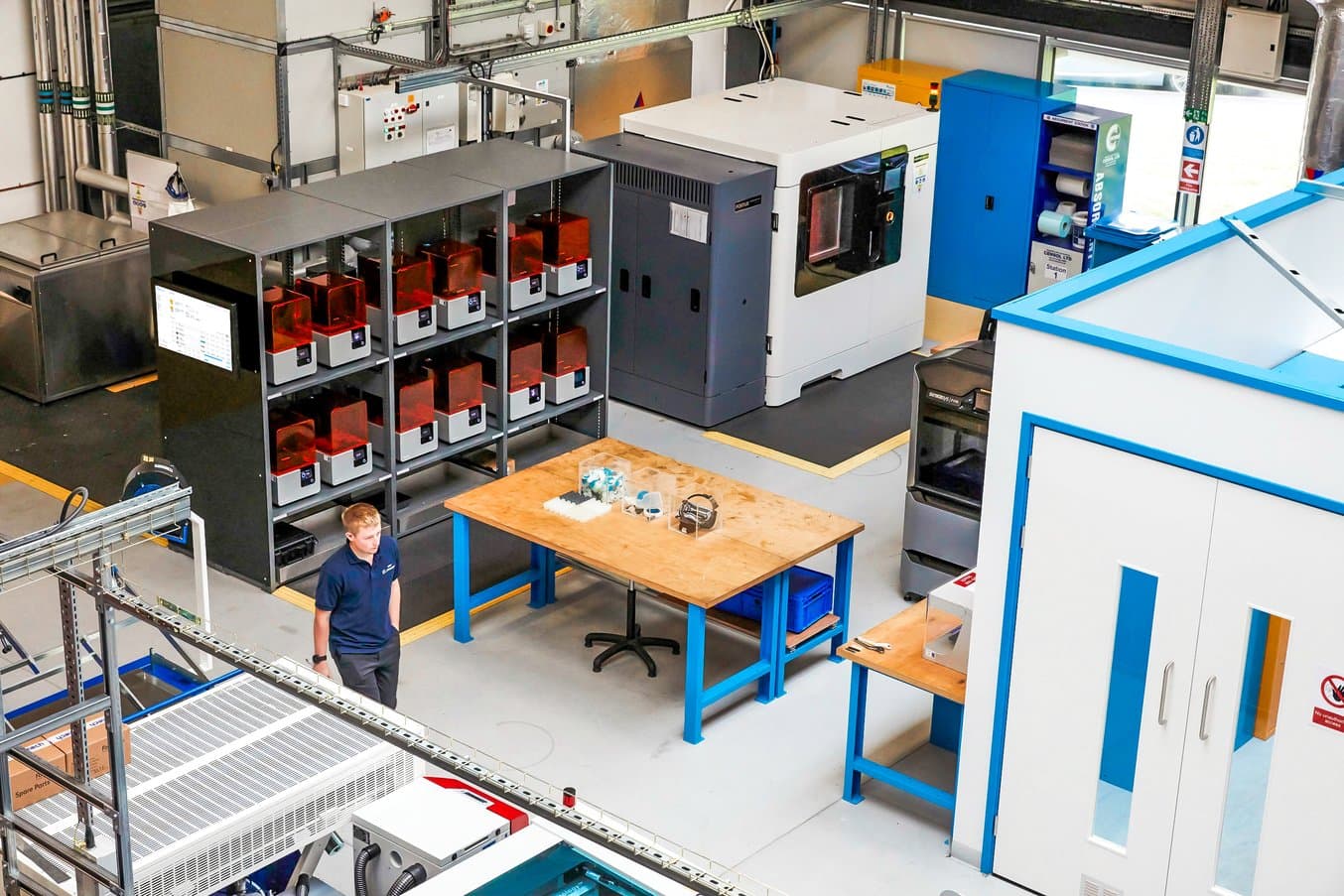
Zuvor setzte das Zentrum einen einzigen Industrie SLA 3D-Drucker ein, für dessen Einsatz aufgrund der Komplexität des Prozesses nur eine Handvoll Mitarbeiter geschult waren. Alle Aufträge im AMRC, bei denen additive Fertigung eingesetzt werden musste, wurden von diesen Personen bearbeitet, wodurch der Arbeitsprozess verlangsamt und die Innovation beeinträchtigt wurde.
„Es war viel besser für unseren Standort, dieses Wissen zugänglich zu machen und viele Anwender zu schulen und es ihnen zu ermöglichen, das System zu nutzen und ihr Wissen dann durch die Anwendung zu erweitern. Wir haben herausgefunden, dass sie durch die Möglichkeit, diese Geräte zu nutzen, immer mehr Konzepte für die additive Fertigung von Komponenten entwickeln können“, so Cocking.
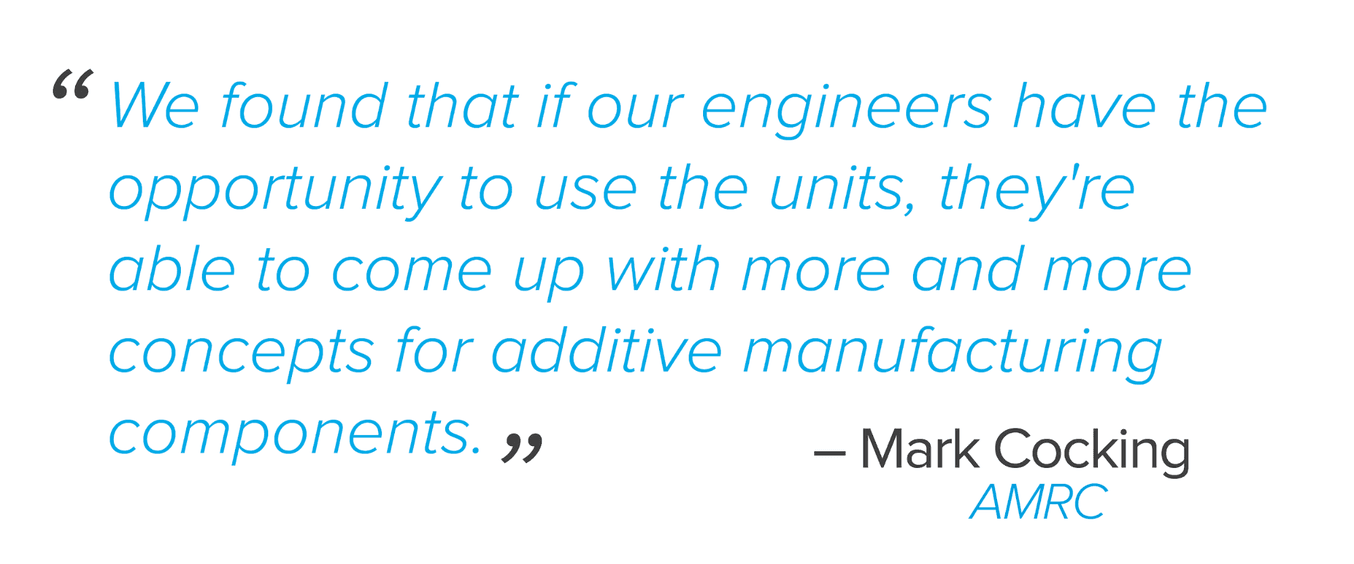
„Ingenieure müssen sich nicht mehr mit Papierkram herumschlagen, um eine Idee zu einem Druckteil werden zu lassen; sie können einfach hierherkommen und das im Handumdrehen tun. Dadurch fallen Barrieren bei der internen Konzeptentwicklung weg und es sind mehr Innovationen möglich. Sie können Teile innerhalb von Stunden entwickeln, die ein Partner noch am selben Tag oder vielleicht am nächsten Nachmittag auf dem Besprechungstisch vor sich liegen hat.“
Wie man eine Druckerfarm für hunderte von Ingenieuren einrichtet und betreibt
Die Design and Prototyping Group verfügt aktuell über 12 Form 2 3D-Drucker, die als Station eingerichtet sind. Cocking hat die Drucker auf einer Seite aufgestellt, um den Zugang zu den verschiedenen Kunstharzen und den Druckteilen zu erleichtern, und auf der anderen Seite einen Nassbereich mit vier Form Wash und vier Form Cure Einheiten für das Reinigen und Nachhärten eingerichtet. Es gibt einen Abschnitt auf dieser Seite mit Lagerfläche für Konstruktionsplattformen, PSA, Anweisungen, Risikobewertungen und einer Pufferzone für Druckteile, die durch das System laufen.
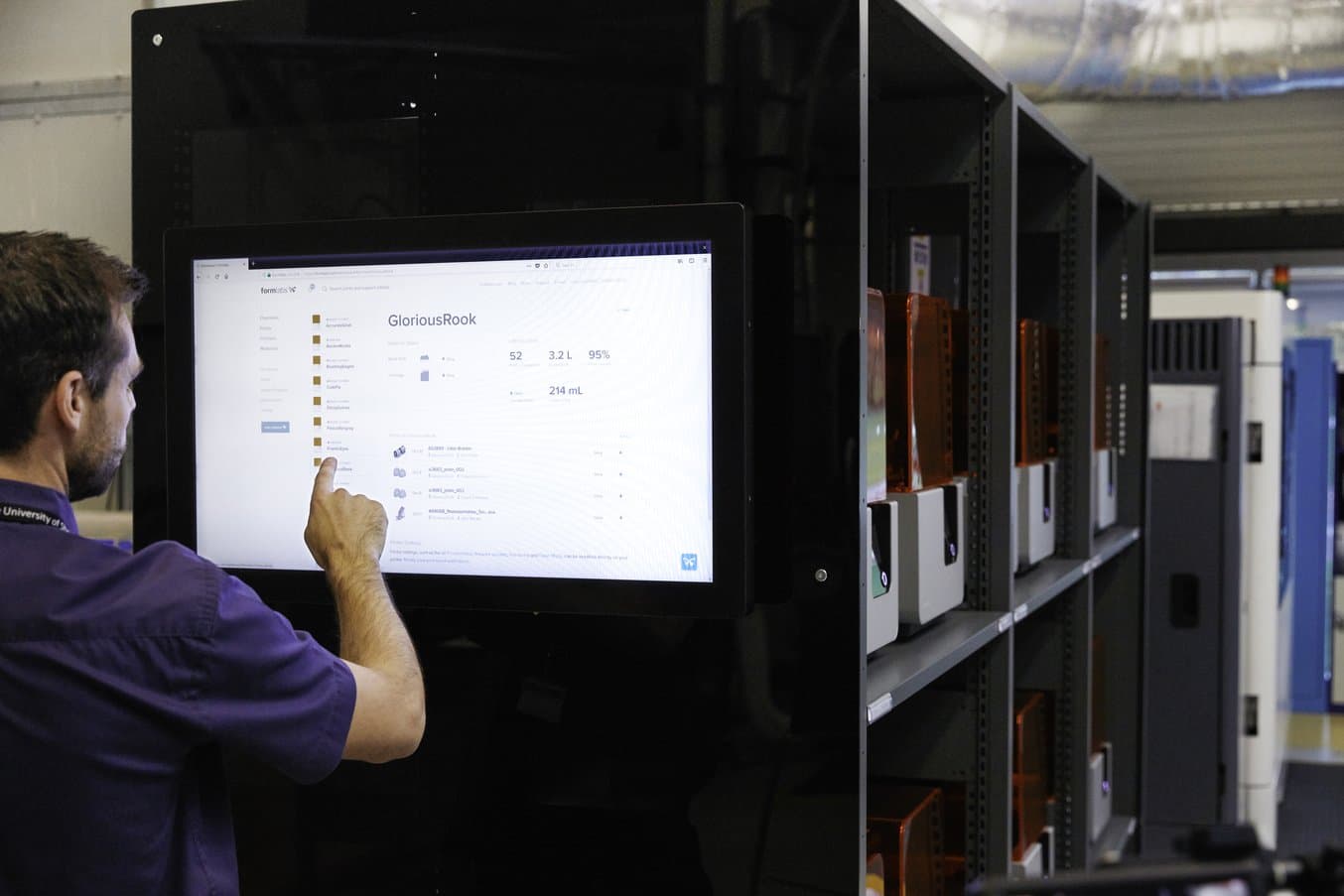
Ein einziger Techniker verwaltet den Bereich und kümmert sich um die Drucker. Der Techniker bedient die 12 Geräte über einen Touchscreen an der Seitenwand der Station, auf dem die Dashboard Software von Formlabs läuft. Sie bietet Informationen zum Druckstatus und dem Materialfüllstand. Wenn die Mitarbeiter zum Zentrum kommen, um die Geräte zu nutzen, müssen Sie einfach nur den Druckknopf drücken.
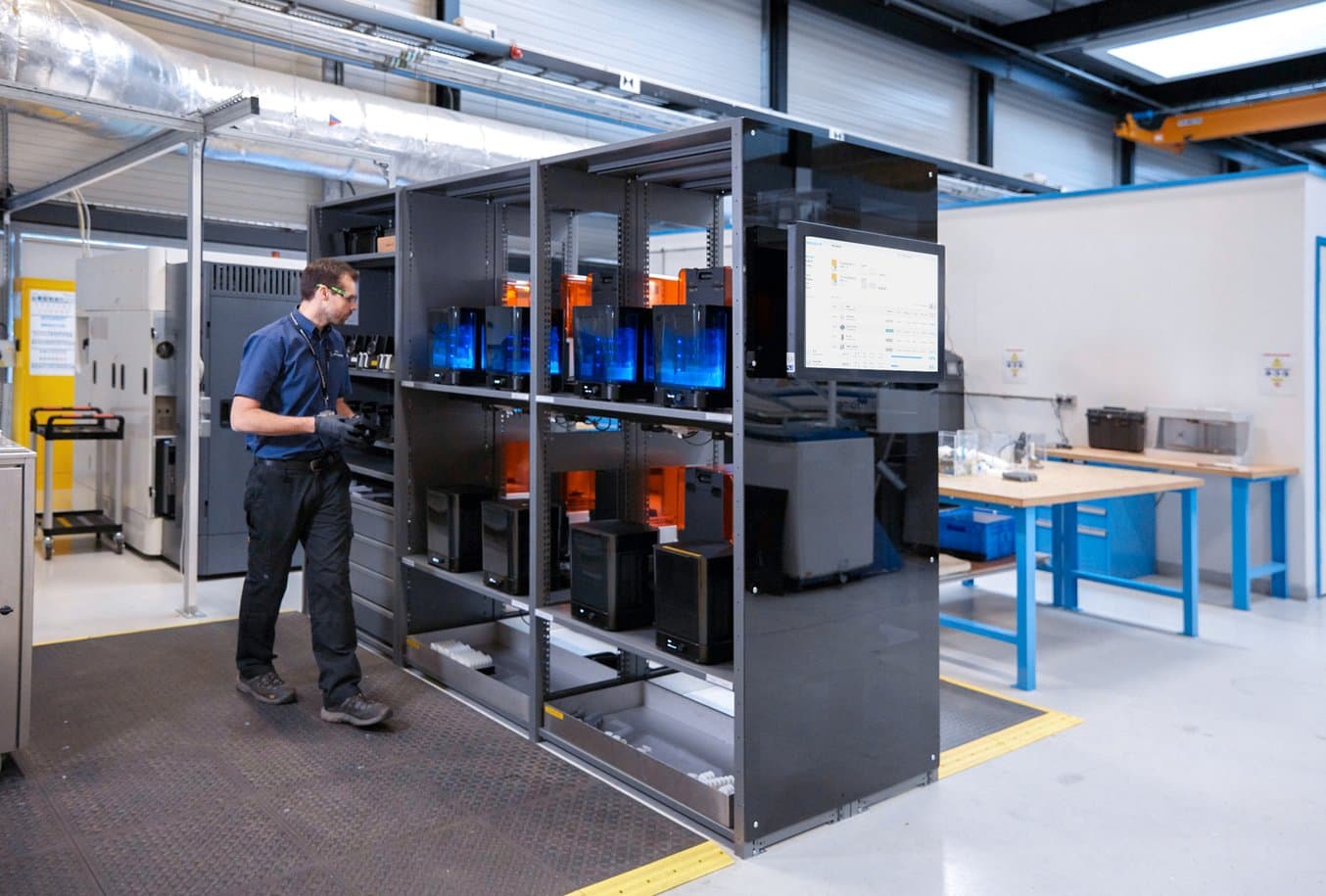
Mitarbeiter können sich für einen Schulungkurs anmelden und zum Zentrum kommen, um sich 45 Minuten bis eine Stunde lang mit der Software und dem Druckprozess zu beschäftigen. Zum Ende dieser Schulung werden sie bereits ihren ersten Druckauftrag gestartet haben. Wenn nach der Schulung der Auftrag fertig ist, kommen sie zurück, nehmen die Konstruktionsplattform mit den Druckteilen aus dem Drucker, lassen sie durch das Reinigungs- und Nachhärtesystem laufen und nutzen die Nachbearbeitungsstation, um die Stützstrukturen zu entfernen und Risikobewertungen zu lesen. Sobald sie diesen Druckprozess absolviert haben, erhalten sie die Berechtigung, die Geräte zu nutzen, wann immer sie möchten.
„Ich brauchte Geräte, an denen Mitarbeiter einfach geschult werden können und die erfolgreich einzusetzen sind, sodass sie sie erneut benutzen wollen. Der Form 2 ist das erste kleine SLA-Gerät, das ich eingesetzt habe und bei dem ich mir dachte, ‚ja, das ist wirklich revolutionär.‘ Das Gerät lässt sich so einfach bedienen“, sagt Cocking. „Die Software ist sehr intuitiv und Ingenieure lernen sie sehr schnell. Sie verstehen sie leicht und verinnerlichen die Grundlagen, und von da ab können sie selbst lernen und ihre additiven Erfahrungen ausweiten. Bislang wurden etwas über 100 Ingenieure an der Form 2 Station geschult.“
PreForm bereitet 3D-Modelle für Formlabs 3D-Drucker vor. Laden Sie die Software herunter und probieren Sie sie aus; es ist kein Drucker erforderlich.
Der Austausch von Wissen erfolgt meist organisch durch mündliche Weitergabe. Ingenieure, die die 3D-Drucker einsetzen, bringen Teile zurück in ihre Abteilungen und verwenden diese bei Konzeptmodellen, Prototypen oder verbauen sie in Maschinen. Andere Ingenieure aus ihrer Abteilung lernen, wie die Teile hergestellt werden, entwickeln ein Interesse und so erhält das Zentrum zwangsläufig immer mehr Schulungsanfragen.
Eine Vielzahl von Anwendungen im AMRC wird durch 3D-Druck unterstützt
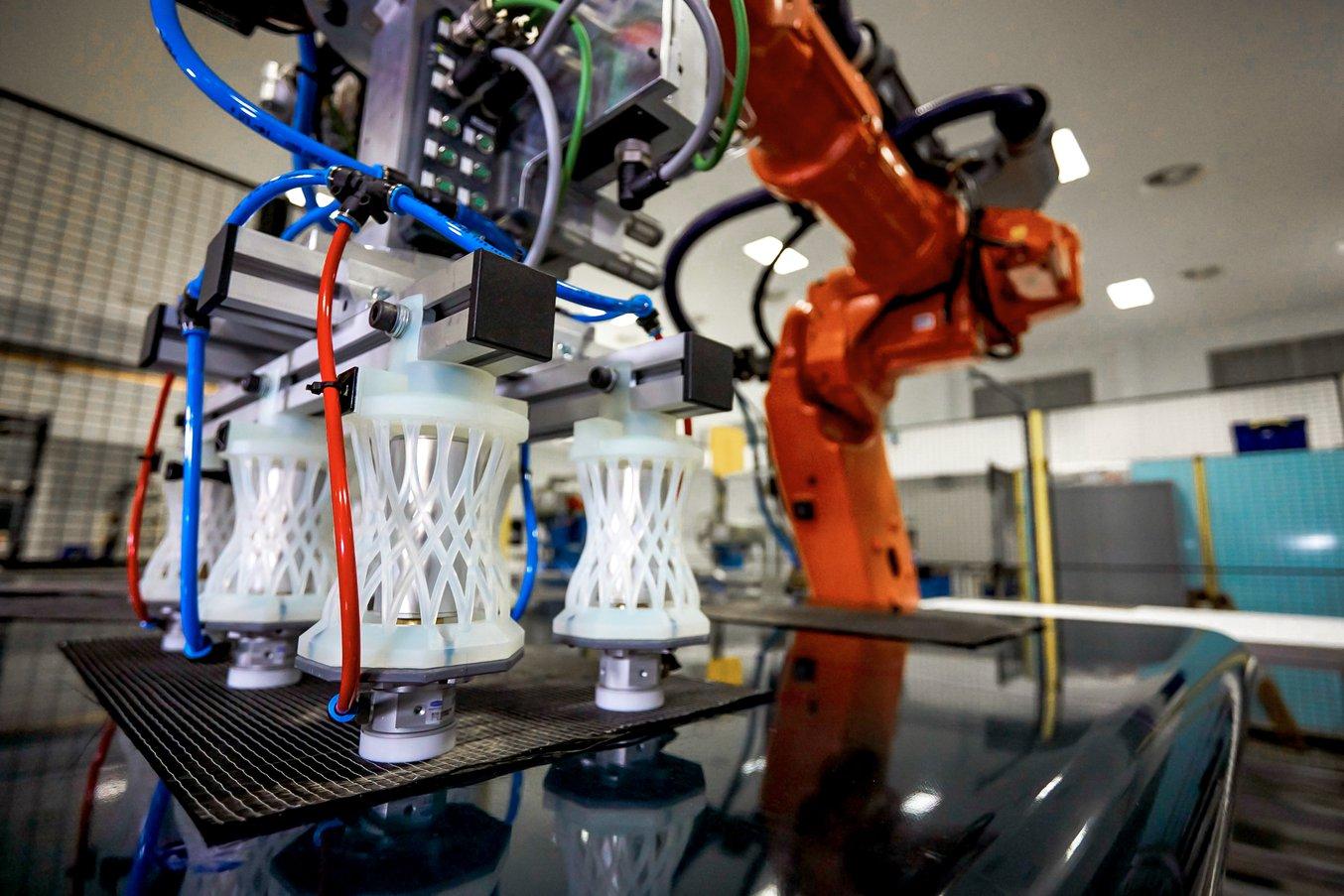
Seit ihrer Einrichtung hat die 3D-Druckstation dutzende von Forschungsprojekten am ganzen Standort unterstützt.
Lernen Sie einige dieser Anwendung genauer kennen:
- Schutzkappen für Bohrversuche: Die 3D-Druckstation hat 500 hochgenaue Bohrkappen hergestellt, die essenziell waren, um die Querkontamination bei Bohrversuchen für Airbus zu verhindern. Die Durchlaufzeit konnte von Wochen auf nur zwei Tage reduziert werden.
- Halterung für Robotergreifer: Forscher haben hochkomplexe Halterungen für einen Pick-and-Place-Roboter entwickelt und gedruckt, die sich mit einem anderen Fertigungsverfahren nur sehr schwer herstellen ließen. Der Roboter automatisiert die Fertigung von Verbundwerkstoffen.
- Halterung für Temperatursensor: In einem Roboterschweißprojekt für die Kernenergieindustrie haben Forscher ein Dutzend 3D-gedruckte Teile wie Unterlegscheiben, Halterungen und ein Sensormontagesystem entwickelt, die den hohen Temperaturen in unmittelbarer Nähe zur Schweißnaht standhalten müssen.
- Rolle für Faserwicklung: Verbundwerkstoff-Forscher haben maßgefertigte Rollen für eine Faserwickelmaschine hergestellt, die zur Fertigung von Kraftstoffrohren, Schläuchen, Behältern und Wellen für die Luft- und Raumfahrt und die Automobilindustrie eingesetzt wird.
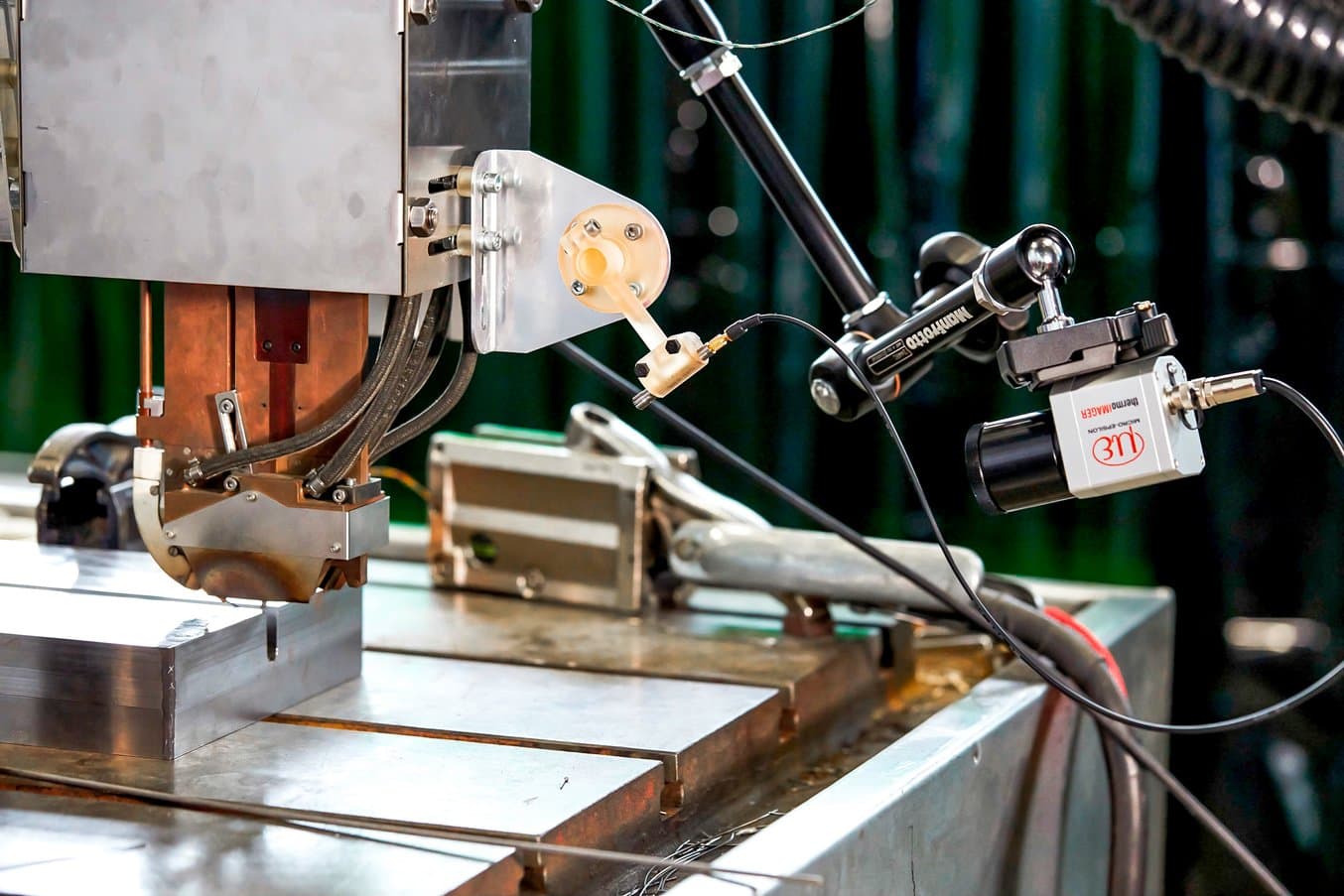
Anwendungen der Rezepte der 3D-Druckstation an neuen Standorten und für neue Industriepartner
Cocking und die Design and Prototyping Group planen bereits die Ausweitung der Kapazitäten zur additiven Fertigung am AMRC.
„Einige unsere Gebäude sind eher abgelegen und sind weiter von diesem Hauptcampus entfernt. Wir planen, das Modell dieser Station zu verwenden, es zu vervielfältigen und Satelliteneinheiten in verschiedenen Gebäuden auf dem Standort zu platzieren, damit Mitarbeiter direkt in ihrer Abteilung Zugriff auf Drucker haben und nicht erst hierher kommen müssen“, erklärt Cocking.
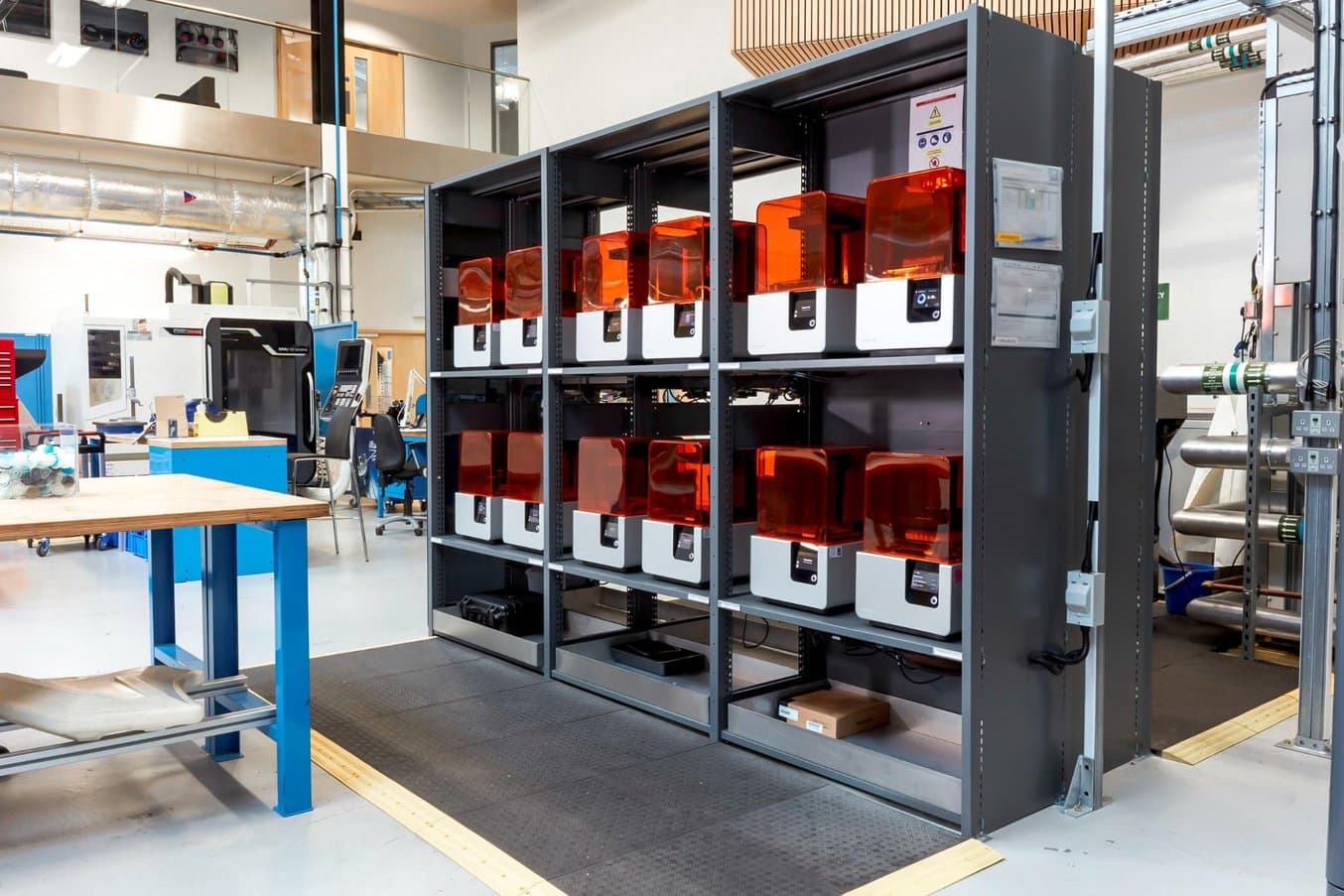
„In meinen 12 Jahren in der Branche habe ich gelernt, dass es von großem Vorteil für die Industrie wäre, vor Ort über Geräte zur additiven Fertigung zu verfügen, sodass ihre Ingenieure leicht darauf zugreifen können“, so Cocking.
„Sie könnten die Durchlaufzeiten bei maßgefertigten Komponenten von Wochen auf Stunden reduzieren. Da ich maßgefertigte Komponenten bereits selbst bestellt habe, verstehe ich die Durchlaufzeiten und kenne die Auswirkungen, die sie auf die Innovation, aber auch zuletzt auf den Markteinführungstermin eines Produkts haben. Sie können die Produkteinführung um Monate nach vorn verlegen, wenn Sie nur Zugriff auf additive Fertigung haben.“
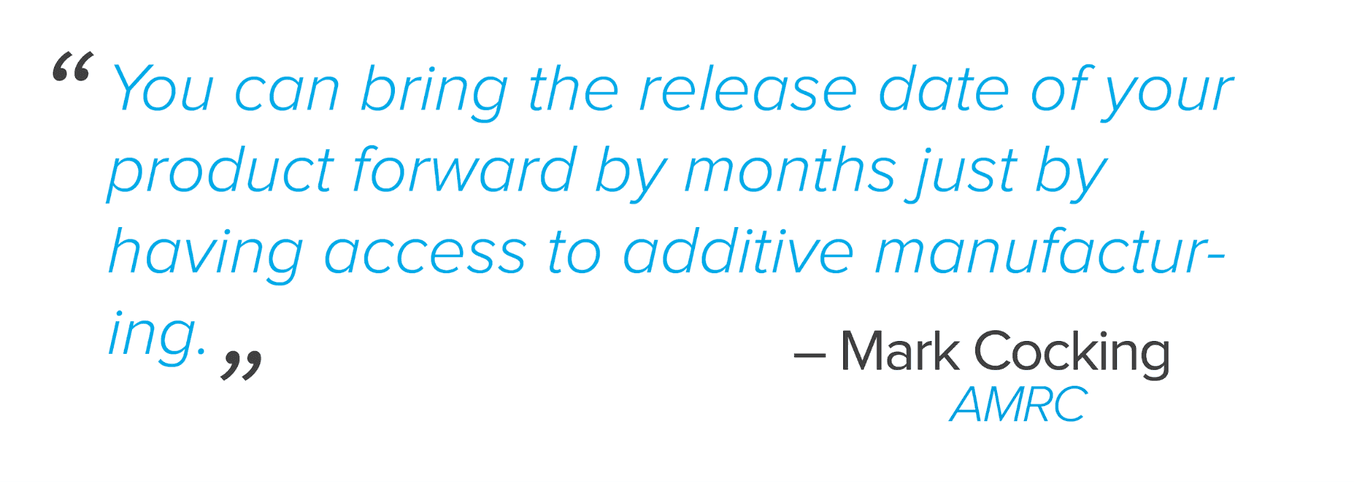
Die Industriepartner des AMRC scheinen derselben Meinung zu sein, da der Erfolg der frei zugänglichen Plattform auch ihre Aufmerksamkeit gewonnen hat.
„Einige unserer Partner sind jetzt interessierter daran, eine exakte Kopie dieser Station anzufertigen und sie in ihrem eigenen Werk einzusetzen. Sie wünschen etwas, das benutzerfreundlich und skalierbar ist. Man kann mit 12 Druckern anfangen, aber man kann daraus mit wachsender Nachfrage ziemlich einfach viele verschiedene Stationen machen. Die additive Fertigung von Chargen ist durch Plattformen mit mehreren Druckern möglich. Es ist schon heute möglich, und das zu einem guten Preis“, so Cocking.
Lernen Sie den Form 2 für Maschinenbau- und Fertigungsanwendungen kennen
„Ich stelle einen Wandel fest, bei dem nicht mehr nur kleine Konzeptmodelle hergestellt werden, sondern immer mehr Fertigteile. Momentan drucken wir viele Geometrien, die denselben Tests unterzogen werden wie Spritzgussteile“, erklärt Cocking.
Unterschiedliche Projekte und Herausforderungen verlangen nach Teilen mit vielen verschiedenen Materialeigenschaften. Ingenieure des AMRC können auf eine große Palette an technischen Kunstharzen zugreifen, die von hoher Festigkeit zu Elastizität oder Temperaturbeständigkeit über alle Materialeigenschaften verfügen, die nötig sind, um komplexe Probleme zu lösen und Prozesse von der Prototypenfertigung bis zur Produktion zu verbessern.
Lernen Sie den Form 3 , den großformatigen Form 3L und die Bibliothek an technischen Kunstharzen von Formlabs für Ihr eigenes Projekt kennen, oder fordern Sie einen kostenlosen Probedruck an, um sich selbst einen Eindruck von den Materialien zu verschaffen.