Reinere Teile in kürzerer Zeit: Wie der Fuse Blast die SLS-Produktivität bei Autotiv erhöht
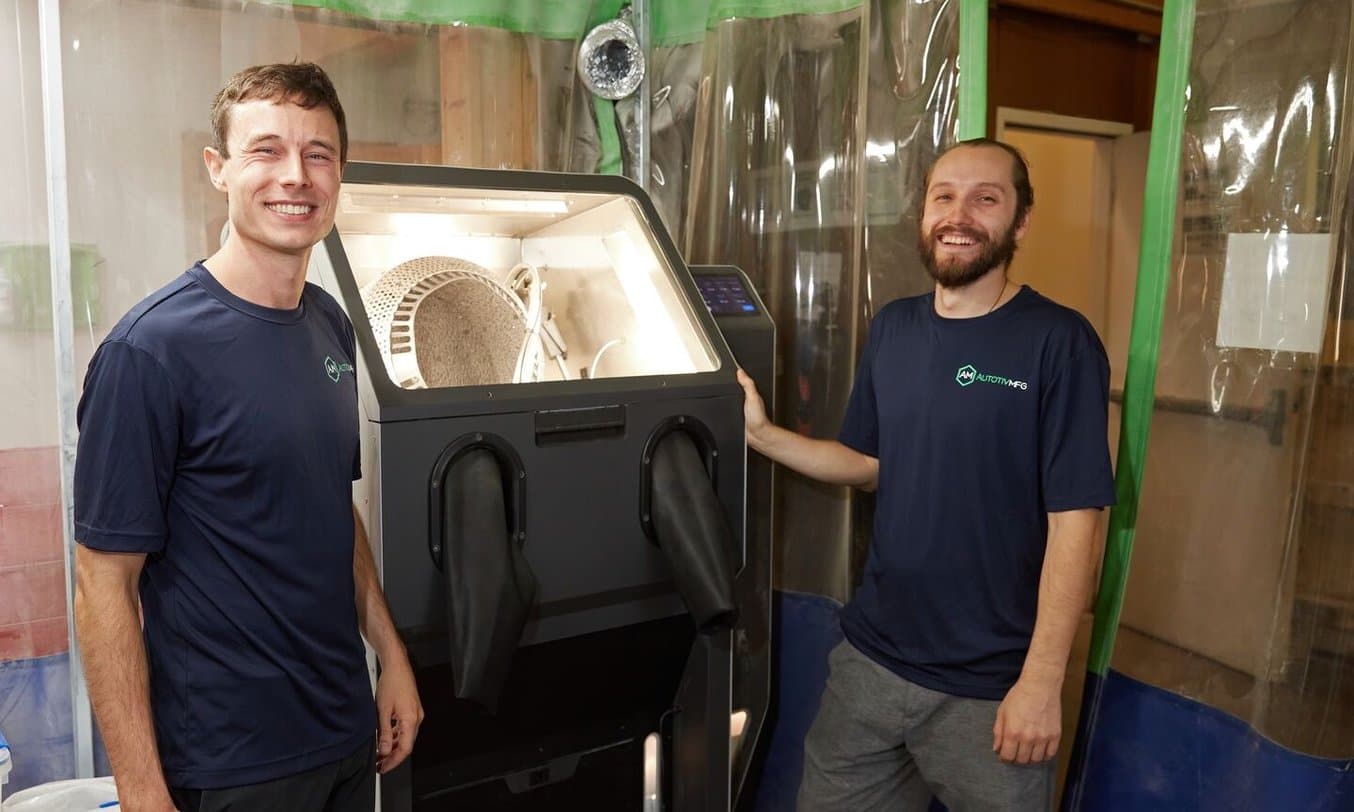
Evan LaBelle, Geschäftsführer und Mitgründer von Autotiv (links), und Betriebsleiter Chris Haak (rechts) mit ihrem Fuse Blast.
Effizienz steht für Autotiv an erster Stelle. Das Startup mit Sitz in Salem, New Hampshire (USA), ist als Vertragshersteller auf 3D-Druck und fortgeschrittene Nachbearbeitungstechniken spezialisiert und legt den Fokus darauf, seinen Kunden so schnell wie möglich fertige Teile zu liefern. Dies hat sich als immer schwieriger erwiesen, je mehr das Unternehmen gewachsen ist – denn bei der SLS-Produktion können durch die arbeitsintensiven Nachbearbeitungsschritte erhebliche Engpässe entstehen, die zu längeren Durchlaufzeiten führen.
Um seine hohen Standards beizubehalten, trotz der stetig wachsenden Auftragsmenge für SLS-Druck, verbrachte das Team von Autotiv Stunden oder sogar ganze Tage mit dem manuellen Sandstrahlen von SLS-Teilen. Durch die Anschaffung des automatisierten Reinigungssystems Fuse Blast ist das Team nun jedoch in der Lage, seine Zeit höherwertigen Aufgaben zu widmen.
Evan LaBelle, Geschäftsführer und Mitgründer von Autotiv, und Betriebsleiter Chris Haak haben uns einen Blick hinter die Türen ihres Betriebs gewährt und uns Einblick darin gegeben, wie sie eine schlanke Fertigungsumgebung erschaffen haben, indem sie sorgfältig das richtige Werkzeug für jede Aufgabe wählen und Prozesse automatisieren, wann immer möglich.
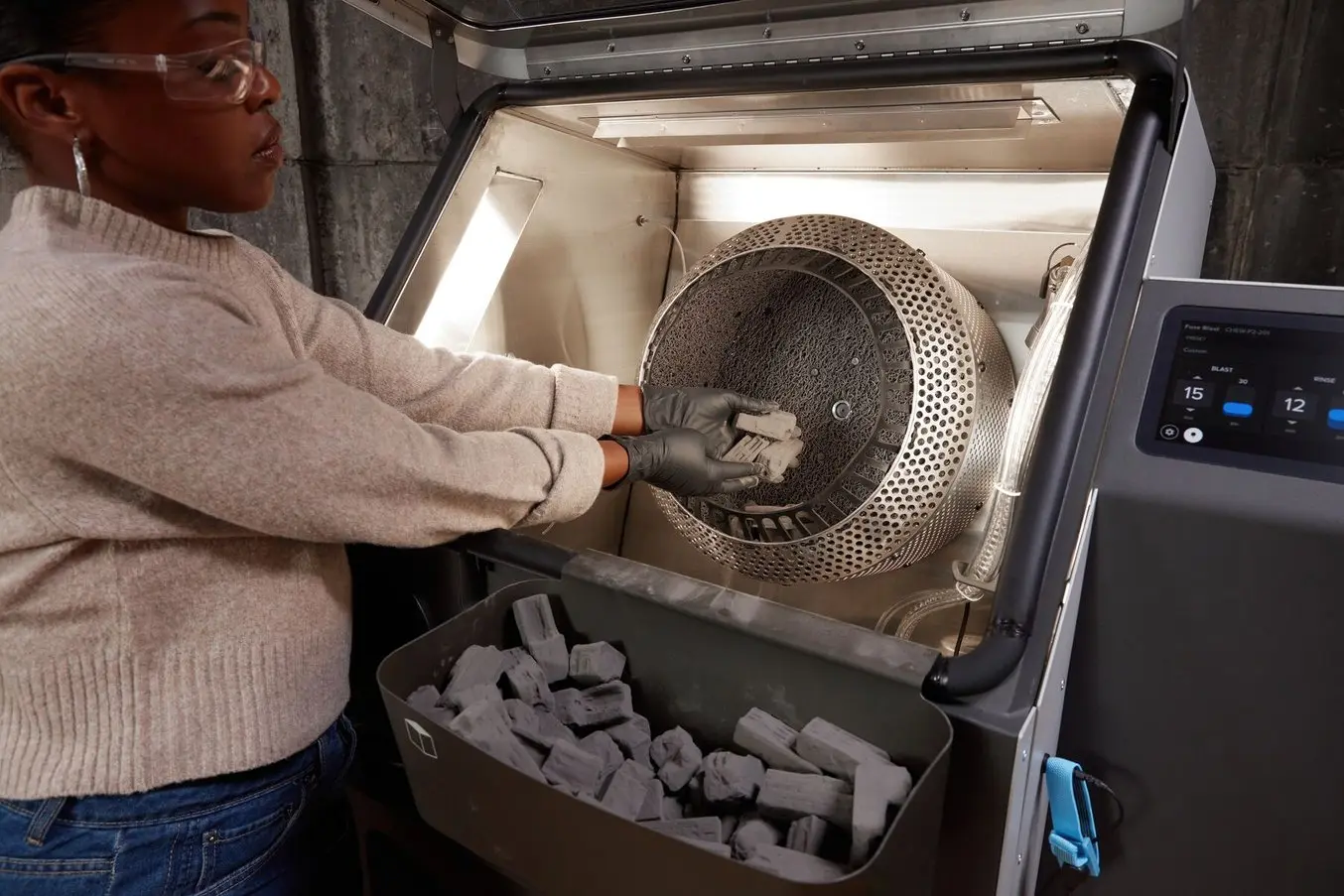
Neue, automatisierte Nachbearbeitung und schnellerer Druck mit den SLS-3D-Druckern der Fuse-Serie
Entdecken Sie die neuesten Innovationen von Formlabs: Software-Verbesserungen für das SLS-System der Fuse-Serie und den neuen Fuse Blast, eine automatisierte Lösung zur Reinigung und Politur von SLS-Teilen ohne manuelle Arbeiten in nur 15 Minuten. Registrieren Sie sich, um die 15-minütige Einführung und Produktdemo anzusehen.
SLS auf Produktionsniveau und der Zeitfresser Sandstrahlen
Seit der Eröffnung im Jahr 2015 setzt Autotiv ausschließlich auf Mundpropaganda und Stammkundschaft, um sein Geschäft zu vergrößern. „Wir haben keine Marketing-Leute oder Vertriebsmitarbeiter, sondern bauen ganz auf uns und unseren Fokus auf Druck und Nachbearbeitung auf hohem Niveau“, erzählt und LaBelle. Diese Strategie hat sich ausgezahlt. Im letzten Jahr hat Autotiv einen steilen Anstieg von Aufträgen mit hohen Stückzahlen verzeichnet, unter anderem für bis zu sechstausend Teile.
Von einsatzbereiten Plug-and-Print-Dateien bis hin zu Prototypenkonzepten, die Absprachen erfordern, hat Autotiv es Tag für Tag mit immer wieder neuen Teilen, Mengen, Branchen und Anwendungen zu tun. Nach LaBelles Schätzung handelt es sich bei etwa 75 % der Aufträge um SLS-Teile, sowohl Prototyping als auch Serienproduktion. Die anderen 25 % verteilen sich auf die 3D-Druckverfahren Schmelzschichtung (FDM) und Stereolithografie (SLA) sowie Nachbearbeitungstechniken wie Färben oder Beschichten.
Die SLS-Produktion hochfahren
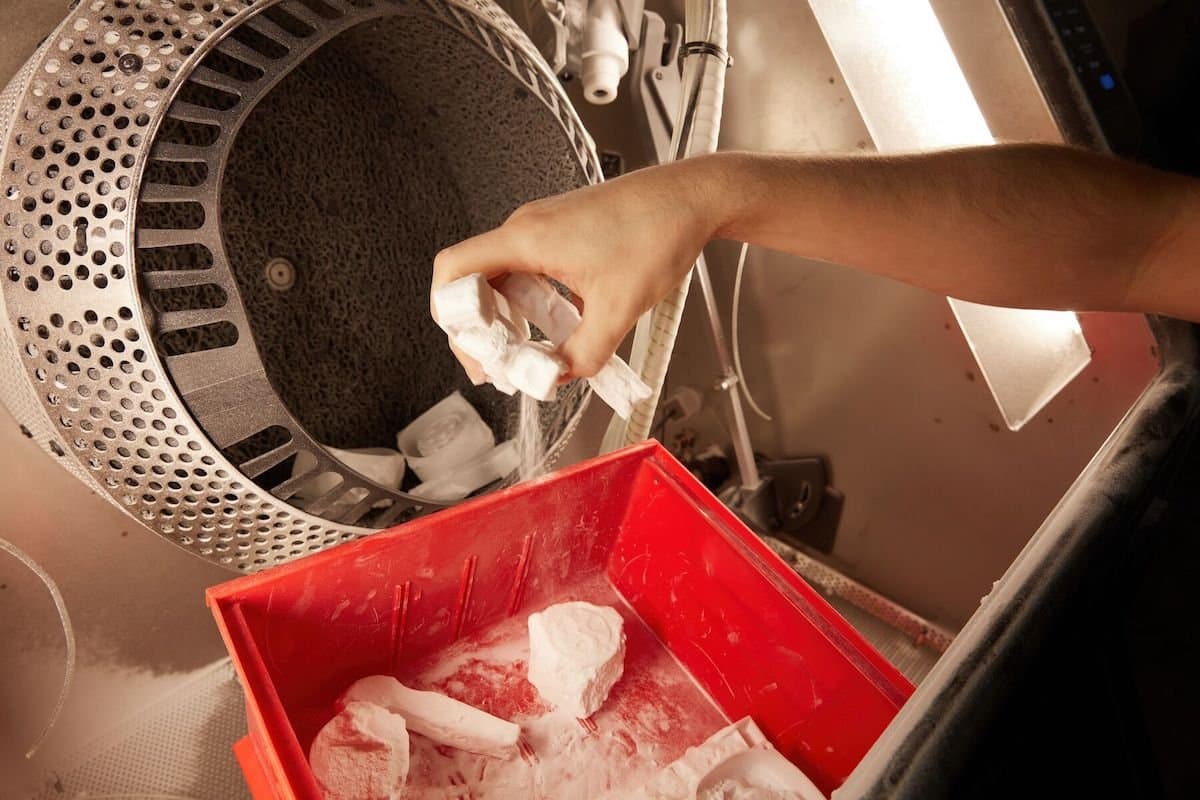
Der Großteil der Aufträge von Autotiv fällt auf die SLS-Produktion von Teilen aus PA 12 im großformatigen SLS-Drucker des Unternehmens. Die Reinigung von kleinen Bauteilen wie diesen beanspruchte früher einen bedeutenden Teil von Haaks Arbeitszeit.
Vor zwei Jahren investierte Autotiv in einen großformatigen SLS-Drucker, den es für rund 300 000 $ erwarb. Der Drucker hat ein Fertigungsvolumen von 325 x 325 x 425 mm, das es dem Team ermöglicht, problemlos große Objekte zu drucken oder aber ganze Chargen kleinerer Teile in einem vollständig gefüllten Fertigungsvolumen zu produzieren. Weil der Großteil der Fertigungsanfragen Teile aus PA 12 betrifft, rentiert es sich für das Unternehmen am meisten, seinen Drucker durchgängig für Drucke mit PA 12 zu nutzen und sich auf sein Zulieferernetzwerk zu stützen, um bei Bedarf andere auf SLS-Geräten gedruckte Materialien zu beziehen.
Je mehr sich die Aufträge auf Serienproduktionsniveau häuften, desto mehr stieß Autotiv auf Probleme bei der Nachbearbeitung. Der großformatige Drucker wurde zusammen mit einem Gerät für die Pulververwaltung ähnlich dem Fuse Sift geliefert, mit welchem die Druckteile aus dem Pulverkuchen entnommen werden und Pulver recycelt wird. Die anschließende Reinigung der Teile blieb jedoch Autotiv überlassen, selbst wenn dies bedeutete, Stunden vor dem manuellen Strahlgerät zu verbringen, um Pulver in Kleinstarbeit von der Druckteiloberfläche zu entfernen.
„Je nach Auftragsmenge standen wir dort zwei bis drei Stunden am Tag, vielleicht etwas mehr. Es konnte auch mal den ganzen Tag dauern, sodass wir uns abwechselten, wenn wir mehrere Hundert oder Eintausend Teile zu bearbeiten hatten. Es war auf jeden Fall ein Arbeitsfresser.“
Chris Haak, Betriebsleiter bei Autotiv
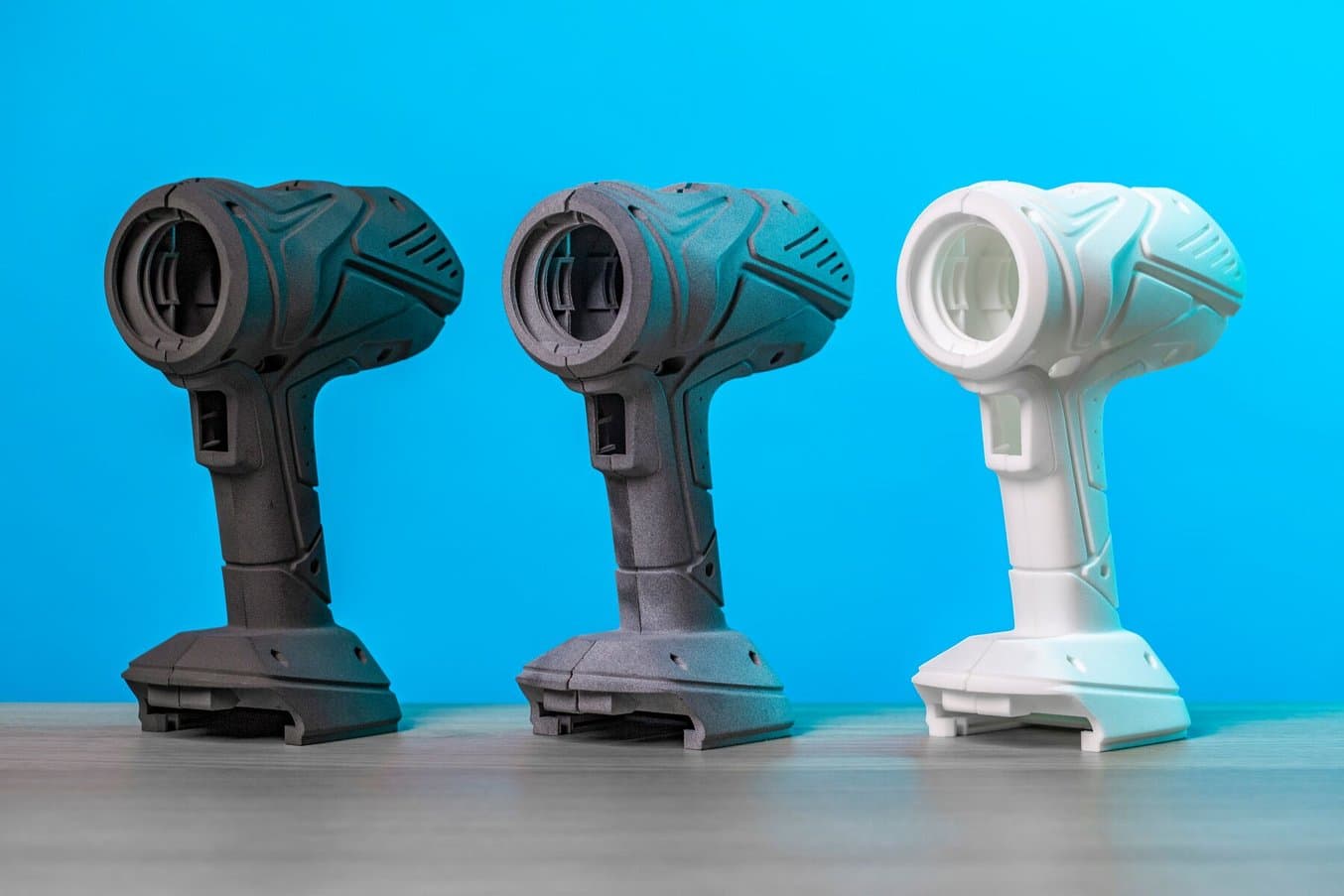
SLS-3D-Drucker der Fuse-Serie vs. konventionelle Pulverbettfusionsanlagen
In diesem vergleichenden Leitfaden behandeln wir die wesentlichen Unterschiede zwischen kompakten SLS-Druckern wie dem Fuse 1+ 30W von Formlabs, der leicht in bestehenden Büro- oder Fertigungsanlagen untergebracht werden kann, und Maschinen mit großer Stellfläche, die für die Integration in bestehende Prozesse mehr Planung und Vorbereitung erfordern.
Physische Belastung
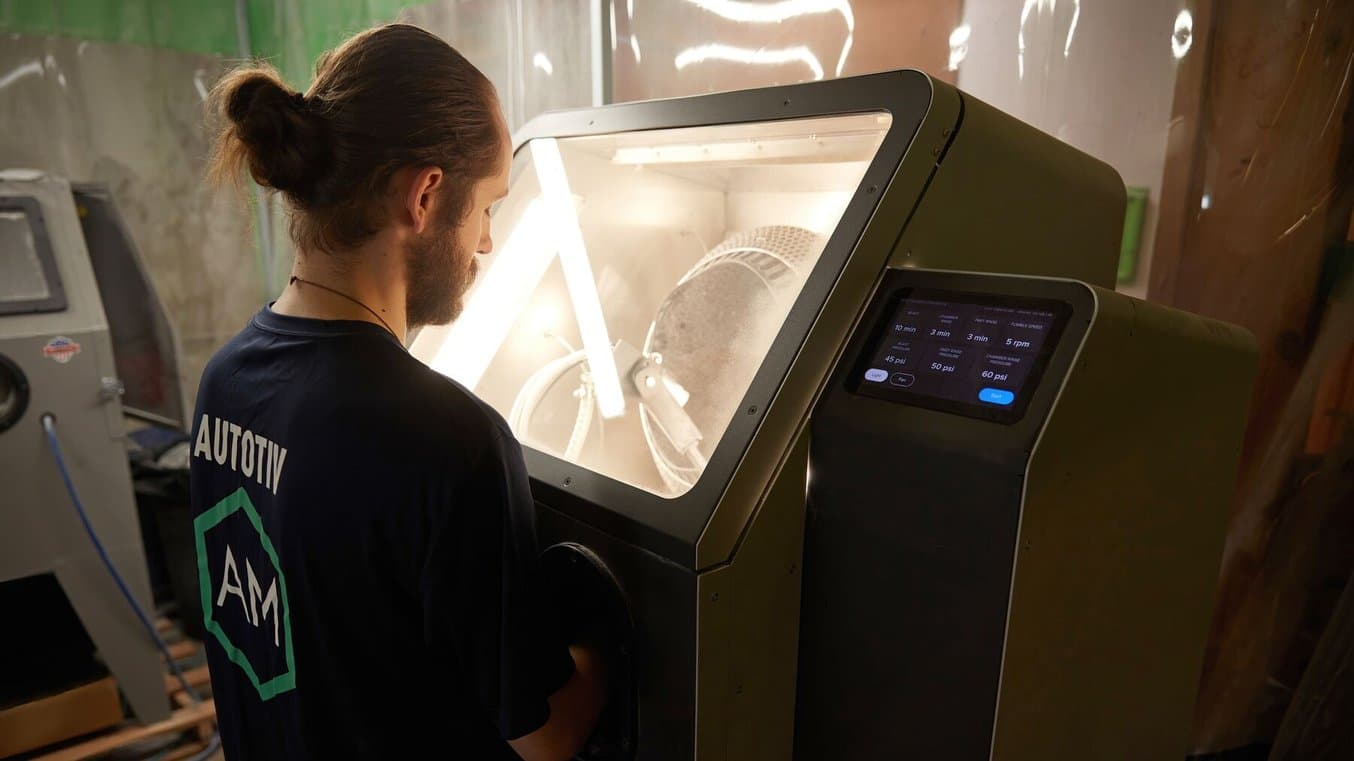
Teile, die nach dem Färben eine zusätzliche manuelle Politur benötigen, bearbeitet Haak zwar noch immer über den Handschuhkasten der Strahlkabine, doch der Großteil der Arbeit ist heute automatisiert. Dies mindert auch die physische Belastung, die das stundenlange Stehen vor dem Strahlgerät mit sich bringt.
Da Autotiv sich zum Ziel gesetzt hat, bestimmte SLS-Aufträge innerhalb von 24 Stunden abzuschließen, muss das Team einen strikt reglementierten Zeitplan für Druck, Reinigung und Verpackung einhalten. Auch wenn sich mehrere Aufträge in einem großen Fertigungsvolumen zum Druck über Nacht bündeln lassen, muss das Team dennoch den Überblick darüber behalten, welcher Auftrag die kürzeste Durchlaufzeit hat. „Wir mussten aufpassen, dass wir die richtigen Teile in der richtigen Reihenfolge reinigten, damit die Aufträge fristgerecht fertig wurden“, so Haak.
Aufgrund der strengen Fristen war der Zeitplan für das Bestrahlen der Teile nicht flexibel, selbst wenn dies dem Team physisch viel abverlangte. Das stundenlange Bearbeiten von Druckteilen und das Bedienen der Strahldüse, insbesondere in einem engen Raum mit der ständigen Hitze und dem Lärm der Sandstrahlanlage, machten dem Team zu schaffen.
„Das machte einen großen Teil des Arbeitstages aus, hier mehrere Stunden stehen zu müssen, ganz zu schweigen von der Belastung und der Erschöpfung von Körper und Muskeln. Tatsächlich musste ein Mitarbeiter sogar zum Arzt, weil er beim Sandstrahlen seine Schulter überstrapaziert hatte.“
Chris Haak, Betriebsleiter bei Autotiv
3D-Drucker und Strahlgerät von verschiedenen Herstellern
Zuerst zögerte das Autotiv-Team, die Nachbearbeitungslösung von Formlabs in einen Arbeitsprozess mit dem Drucker eines anderen Herstellers zu integrieren. Haak und LaBelle waren mit SLS-Druckteilen von Formlabs vertraut und beobachteten, dass der Pulverkuchen der von Autotiv gefertigten Teile einen höheren Kraftaufwand bei der Entpulverung erforderte als ein typischer Druck mit Nylon 12 Powder von Formlabs.
„Ich musste mir selbst ein Bild davon machen, aber tatsächlich verflog jede Besorgnis schon bei der allerersten Anwendung. Das Gerät fügt sich gut in jegliche Produktions- oder Büroanlage ein, es ist ziemlich vielseitig und eignet sich für viele verschiedene Arten von Kunden. Solche, die ein kleineres System der Fuse-Serie betreiben, und auch solche mit einem größeren SLS-System.“
Chris Haak, Betriebsleiter bei Autotiv
Da Autotiv seinen großformatigen SLS-Drucker jeden Abend und auch am Wochenende in Betrieb hat, brauchte es eine Sandstrahllösung, die ebenso viel leisten konnte. Der Fuse Blast war eine erschwingliche Option, die sich leicht in die Abläufe des Teams integrieren ließ.
Während die ursprüngliche Strahlkabine des Unternehmens in einem abgeschirmten Bereich aufgestellt war, um die Pulverkontamination des gesamten Arbeitsbereichs zu verhindern, ist dies beim Fuse Blast nicht notwendig. Das Autotiv-Team konnte den Fuse Blast in der Nähe seiner Pulverrückgewinnungsstation unterbringen, und es bot sich an, die beiden Geräte nah beieinander in diesem geschlossenen Bereich zu behalten. Zukünftig könnte das Team jedoch auch auf die Flächen jenseits dieses abgeschirmten Bereiches skalieren, da es sich beim Fuse Blast um ein geschlossenes System handelt, das eine saubere, pulverfreie Umgebung sichert.
Automatisiertes Sandstrahlen liefert bessere Ergebnisse
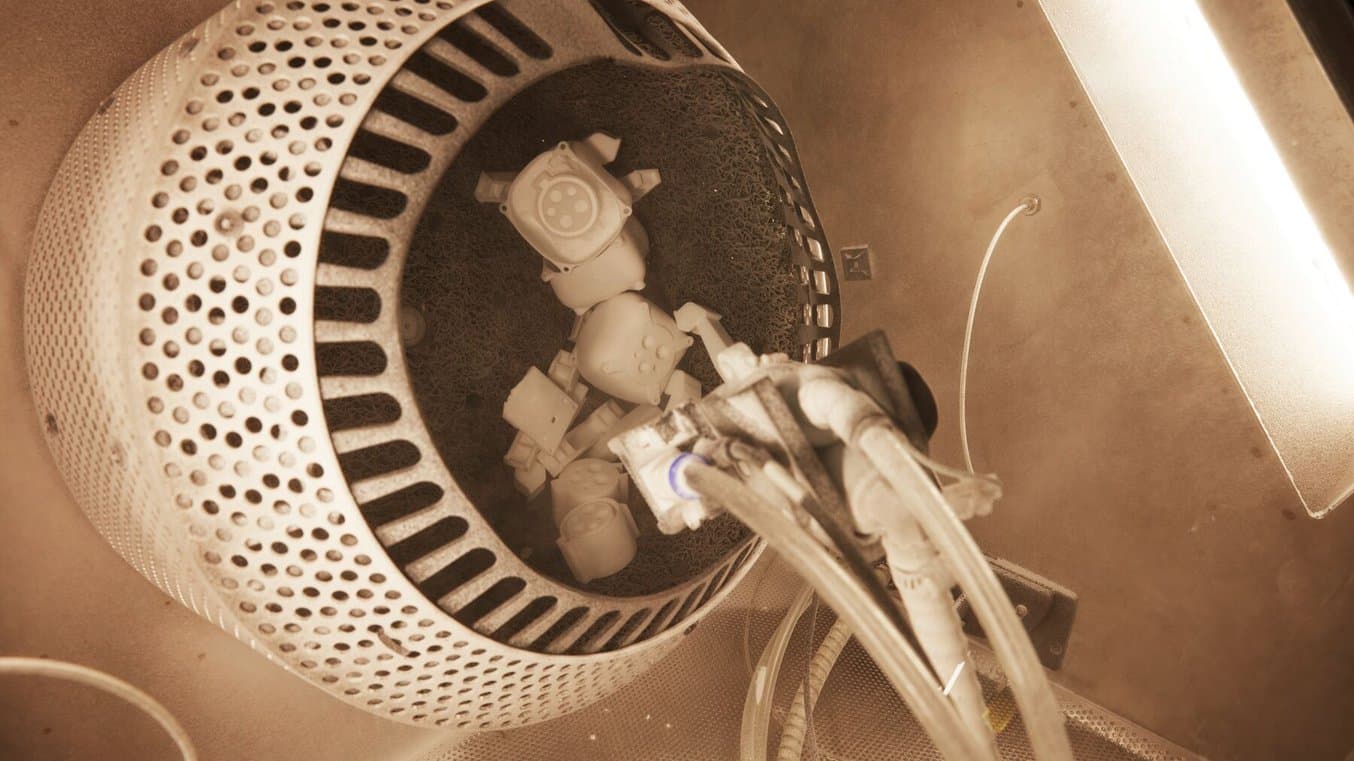
Der Fuse Blast ist besser darin, kleine Teile oder filigrane Details vor Schäden zu bewahren, als manuelle Strahlgeräte – in der Trommel werden die Teile sanft genug bewegt, um Schäden vorzubeugen, während die Strahldüse überschüssiges Pulver entfernt.
Das manuelle Sandstrahlen kostete das Autotiv-Team wertvolle Arbeitszeit, in der es die Teile von Hand bearbeitete, aber es schuf auch noch einen weiteren Zeitfresser: das Nachdrucken beschädigter Teile. Erschöpfung und die Herausforderung, die Strahldüse über Stunden hinweg von Hand zu bedienen, führten oft dazu, dass den Mitarbeitenden kleinere Teile aus den Händen geschleudert wurden und gegen die Kabinenwand schlugen.
„Früher sind kleine Teile leicht zerbrochen oder sie flogen einem durch den Strahldruck aus der Hand, wurden gegen die Rückwand der Strahlkabine geschleudert und zersplitterten. Mit dem Fuse Blast ist so etwas noch nie passiert. Tatsächlich ist er etwas sicherer, weil man in einer kontrollierten Umgebung arbeitet, und er hat im Inneren auch ein ziemlich weiches Netz“, so Haak.
Das manuelle Sandstrahlen kann auch dazu führen, dass Teile „verbrennen“ oder Kratzer erhalten, wenn der Luftstrahl zu lange auf eine Stelle gerichtet wird, was schon innerhalb von Sekunden passieren kann. Das manuelle Bestrahlen erfordert geschultes Personal, das mit dem Verfahren, dem Druck und den Anforderungen des Teils vertraut ist. Der Fuse Blast automatisiert den Prozess und hält die Teile kontinuierlich in Bewegung, während sie mit einem niedrigeren Strahldruck bestrahlt werden.
Weniger zerbrochene oder „verbrannte“ Teile bedeuten weniger Nachdrucke und damit mehr Zeit für die finale Politur, das Färben und das Versenden der fertigen Aufträge. Haak und LaBelle haben festgestellt, dass sie mit dem Fuse Blast sogar ein satinähnliches Finish erzielen können, wenn das Gerät als zusätzlicher Schritt nach dem Färben eingesetzt wird. Das Team von Autotiv nutzt die manuelle Strahloption für einige Minuten, um Teile konzentriert zu bestrahlen und so fleckige Flächen oder unebene Farben zu behandeln, nachdem die Teile aus der Färbeanlage kommen. „Wir beobachten eine Verbesserung der Oberflächenbeschaffenheit, weil die Teile in der Trommel ständig bewegt werden. Das ergibt ein nahezu satinartiges Finish auf den schwarz gefärbten Teilen, die wir bei uns drucken, nachbearbeiten und färben“, berichtet Haak.
Kleine Teile und komplexe Geometrien lassen sich nun leichter bearbeiten, und das Team von Autotiv kann sich ruhigen Gewissens anderen Aufgaben widmen, während eine vorprogrammierte Reinigung im Gang ist. „Bei der manuellen Reinigung entgehen uns womöglich Einschlüsse, Löcher und Ecken, was wir vor dem Versand überprüfen müssen. Mit dem Fuse Blast sind wir in der Lage, viel schneller zu prüfen, weil wir bei der Reinigung der Teile tatsächlich mehr Vertrauen in die Maschine als in uns selbst haben. Sie liefert eine ebenso gute wenn nicht sogar bessere Leistung beim Säubern dieser kleinen Details“, so Haak.
In-Line-Ionisierung sorgt für fühlbare Reinheit
Vor der Ankunft des Fuse Blast säuberte Haak die Druckteile nach dem Sandstrahlen manuell mithilfe von Druckluft, um Pulverreste von der Oberfläche zu entfernen. „Selbst dann hatten wir immer noch statische Ladung. Das heißt, selbst nachdem wir sie bestrahlten und zur Weiterverarbeitung und Prüfung in einen Behälter legten, zogen die Teile noch Staub an“, erinnert sich Haak.
Bei der Prüfung der Teile offenbarte sich zwangsläufig ihre staubige Oberfläche, sodass sie zurück in die Nachbearbeitung geschickt wurden, bevor sie versandt werden konnten. Dadurch verlor Autotiv wertvolle Zeit und die Projekte seiner Kundschaft verzögerten sich.
Der In-Line-Ionisator des Fuse Blast behebt die statische Aufladung der Teile, was zum Ergebnis hat, dass Pulver und Strahlmittel von den Teilen auf den Boden der Strahlkabine fallen.
„Die Teile kommen heraus und sind direkt fühlbar sauber. Wenn man sie in die Hand nimmt, kann man die Oberfläche fühlen – es ist einfach nur das SLS-Teil, da ist nichts anderes auf der Oberfläche.“
Chris Haak, Betriebsleiter bei Autotiv
Weniger Kontamination, geringere Strahlmittelkosten
Durch die passive Strahlmittelfilterung des Fuse Blast werden Strahlmedium und Pulver kontinuierlich voneinander getrennt, damit die Strahldüse ausschließlich unkontaminiertes Strahlmittel zieht und die Teile schneller gereinigt werden. Sein manuelles Strahlgerät nutzte das Autotiv-Team jeden Tag und verbrauchte alle drei bis vier Wochen etwa 20 kg an Strahlmittel, bevor dieses ausgetauscht werden musste. Mit dem Fuse Blast hat das Team diese Zahl nahezu halbiert. Um seinen relativ festen Pulverkuchen zu bearbeiten, verwendet Autotiv einen Strahldruck von 3,1 bar – Anwender, die den empfohlenen Druck von 2 bar ansetzen, können mit einer vier- bis achtmal längeren Haltbarkeit des Strahlmittels rechnen als beim manuellen Sandstrahlen. „Wir füllen etwa 11 kg Strahlmittel in den Fuse Blast und wechseln es alle vier Wochen aus. Man kann also sagen, die Lebensdauer des Strahlmediums wird praktisch verdoppelt“, so LaBelle.
Höhere Produktivität für stetiges Wachstum bei Autotiv
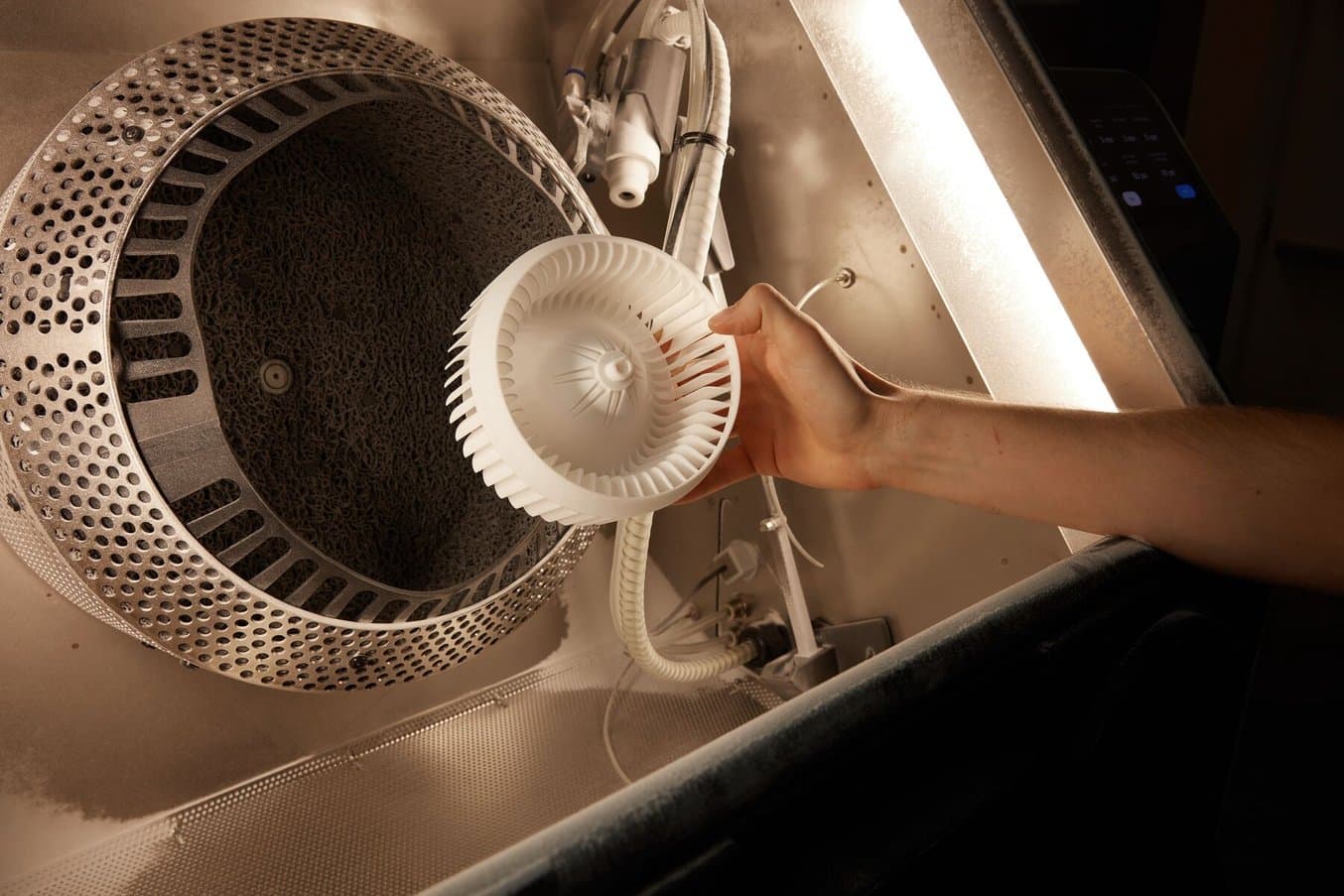
Durch den In-Line-Ionisator fällt das Pulver von der Teiloberfläche ab, sodass diese fühlbar rein wird.
Bei Autotiv lautet die Devise: „Alle packen mit an“. Die gesamte Belegschaft, angefangen von LaBelle bis zu den neuesten Teammitgliedern, wechselt sich ab, wenn es zur Sache geht. Als das Team noch Stunden oder sogar ganze Tage mit dem manuellen Sandstrahlen verbrachte, teilte es sich die Arbeit, damit niemand zu lange am Stück an der Maschine stehen musste. Mit dem Fuse Blast gewinnt es diese Stunden nun wieder zurück und kann sie den zahlreichen höherwertigen Aufgaben widmen, die in dem wachsenden Unternehmen anfallen. „Der Fuse Blast bringt uns eine starke Verbesserung hinsichtlich der Zeit und Produktivität, die das Team für andere Aufgaben zur Verfügung hat“, so Haak. Obwohl das Unternehmen seine Teile nicht auf einem Formlabs-Drucker fertigt, ließ sich der Fuse Blast nahtlos in seinen Arbeitsprozess integrieren.
„Es ist im Grunde Plug-and-Play. Man muss nichts feinjustieren. Man befüllt ihn einfach mit Strahlmittel und drückt auf Start, und 10 bis 15 Minuten später bekommt man seine gereinigten Teile.“
Evan LaBelle, Geschäftsführer und Mitgründer von Autotiv
Die Bandbreite der Unternehmen, die aktuell Teile von Autotiv anfordern, ist groß. Alle Branchen von Robotik über Automobilindustrie hin zur Verbraucherelektronik sind dabei, den SLS-3D-Druck auf irgendeine Weise in ihre Fertigungs- und Entwicklungsprozesse zu integrieren. Angesichts des Wachstums, das sich daraus für Autotiv ergibt, ist der Fuse Blast eine große Hilfe bei der Handhabung der steigenden Auftragsmenge. „Ich kann mir vorstellen, damit zu skalieren“, meint auch Haak.
Um mehr über SLS-3D-Druck zu erfahren oder den Fuse Blast kennenzulernen, kontaktieren Sie unser SLS-Team.