Wie Brose mit SLA- und SLS-Technologie seine Automobilproduktion auf Touren bringt
In jedem dritten Neufahrzeug, das heute vom Band läuft, ist mindestens ein Bauteil von Brose verbaut – einem der fünf größten familiengeführten Automobilzulieferer der Welt. Vor über 100 Jahren von Max Brose in Berlin gegründet, hat sich das Unternehmen vom Automobilzubehörhandel zum Marktführer für mechatronische Systeme entwickelt. Seine Produkte – hauptsächlich Sitz-, Heckklappen- und Türbaugruppen – entwickelt und produziert das Unternehmen für die größten Namen der Automobilbranche: BMW, Volvo, Ford, Mercedes, Jeep und andere.
Einer der Gründe für das stetige Wachstum von Brose und die langfristigen erfolgreichen Partnerschaften mit diesen Erstausrüstern (OEMs) ist das Engagement des Unternehmens für kontinuierliche Verbesserung und Innovation. Im Mittelpunkt zahlreicher Initiativen in der Konstruktion und Endfertigung steht der 3D-Druck. Dieser versetzt Brose in die Lage, auf jegliche Änderungen in der dynamischen Automobilbranche flexibel zu reagieren.
Wir haben dem Hauptsitz von Brose North America in Auburn Hills, Michigan, sowie der großangelegten Produktionsstätte in New Boston, Michigan, einen Besuch abgestattet, um ihre leistungsstarken 3D-Drucker der Technologien Stereolithografie (SLA) und selektives Lasersintern (SLS) in Aktion zu begutachten. Matthias Schulz, Leiter des Prototypings in der Abteilung für Sitze und Zuständiger für die additive Technologie in der Region, hat sich mit uns darüber unterhalten, wie Brose den 3D-Druck prozessübergreifend einsetzt, vom Design über die Fertigung bis hin zu den Endbauteilen, und das bei den engen Fristen der OEMs.
„Wir haben in der Automobilindustrie rasante Veränderungen erlebt, vor allem in den letzten fünf Jahren. Die Entwicklungszeit für neue Produkte wird immer kürzer. Daran müssen wir uns anpassen – wir müssen uns mehr und mehr auf additive Technologien stützen. Das ist in unserem Interesse, denn es verkürzt auch die Vorlaufzeiten für Werkzeuge etc., und hilft uns später bei der Produktion, sodass wir Teile schneller liefern können.“
Matthias Schulz, Leiter der Prototypenentwicklung für Sitze, Brose North America
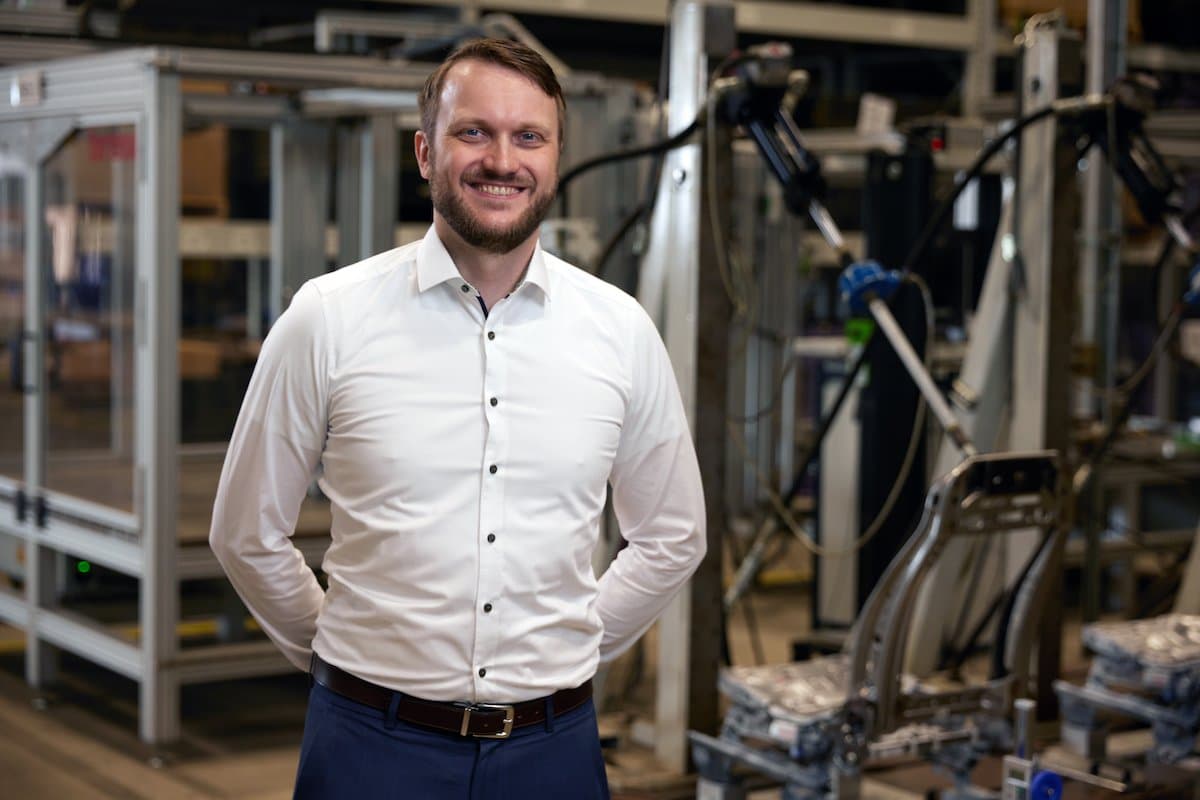
Webinar auf Abruf: SLS bei Brose für die Endproduktion von Automobilbauteilen
In diesem On-Demand-Webinar demonstriert Matthias Schulz, Leiter für das Sitz-Prototyping bei Brose North America, wie Brose die SLA- und SLS-Technologie einsetzt – von schnellen Schweißvorrichtungen bis hin zu Produktionsserien von 250 000 Endbauteilen.
Wenn Prototyping über Einzelanfertigungen hinausgeht
Die Prototypenentwicklung ist eine perfekte Anwendung für 3D-Druck – und auch dafür bekannt. Brose hat für sein Prototyping eine Reihe von FDM-Druckern (Schmelzschichtung), SLA- und SLS-3D-Druckern im Einsatz, doch seine Fertigungsmengen entsprechen nicht zwingend dem für Konzeptnachweise erwarteten Volumen. Bei Brose liegt das typische Fertigungsvolumen für Prototypen bei 500 bis 1000 Stück.
„Wir drucken in größerem Maßstab. 'Prototyping' bedeutet bei uns den Druck mehrerer hundert Teile, abhängig von der Anzahl der Tests, die wir durchführen müssen. Wir müssen nicht nur interne und externe Normen einhalten, sondern auch Bestimmungen auf Bundesebene. Dafür brauchen wir natürlich eine bestimmte Anzahl von Teilen, sodass wir für einen Prototyp meist sieben- bis achthundert Teile drucken“, erläutert Schulz.
Mindestbestellmengen machen SLA zur besten Option: Gummidämpfer zur Sitzlängeneinstellung
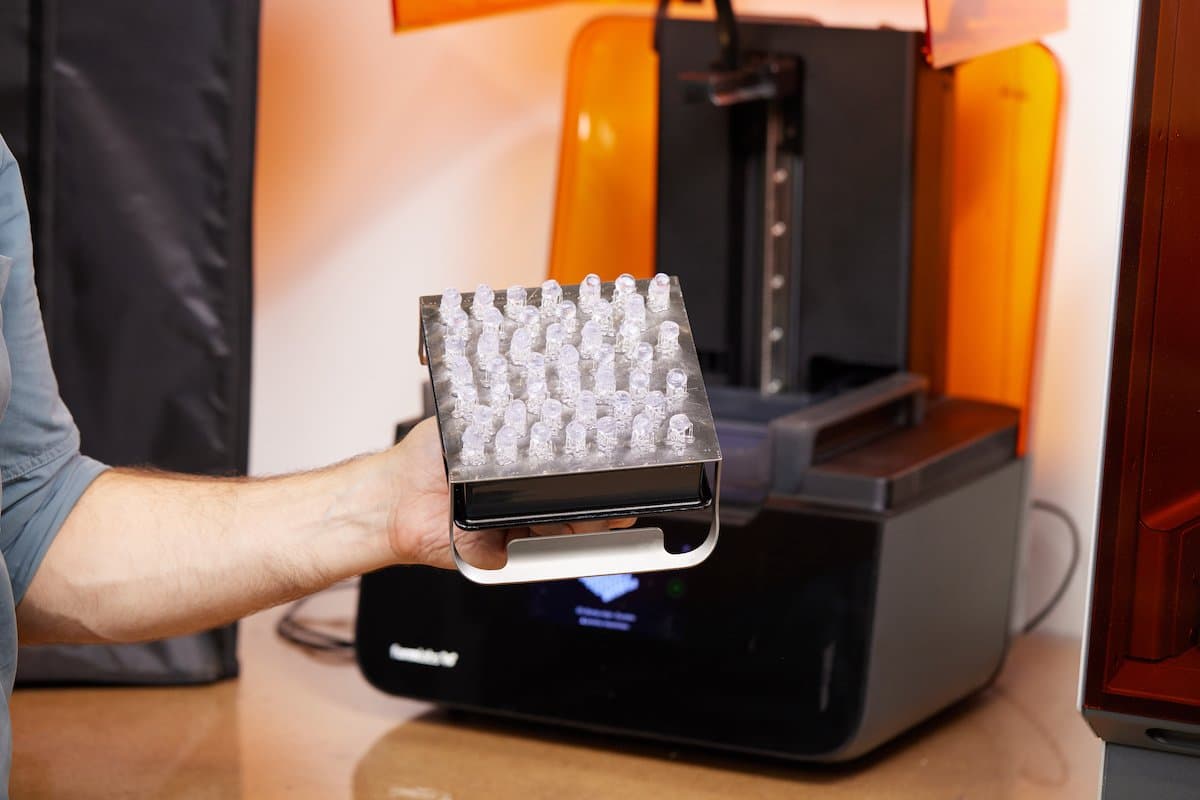
Bei diesen Prototypen handelt es sich um kleine Bauteile, die das Aufprallen der metallenen Sitzbaugruppe auf dem Sitzrahmen akustisch und haptisch dämpfen sollen. Das Outsourcing nach Übersee erforderte eine Mindestbestellmenge von mehreren Millionen Stück. Deshalb druckten Schulz und sein Team die Teile zu Testzwecken auf den Druckern der Form-Serie.
Bei einem Projekt benötigte das Prototyping-Team einen weichen Silikondämpfer, der in die Sitzbaugruppe eingebaut wird. Wenn sich der Sitz auf dem Rahmen nach vorne bewegt, dämpft dieses Bauteil das Geräusch und verbessert die haptische und akustische Rückmeldung beim Bewegen der Sitzeinheit. Für die Bestellung dieser Teile bei einem Brose-Serienzulieferer in Übersee lag die Mindestbestellmenge in Millionenhöhe – Brose benötigte allerdings nur ein paar hundert Stück für einen vorläufigen Designtest.
Abgesehen von den hohen Kosten der Beschaffung und Verschiffung mehrerer Millionen von Teilen aus Übersee hätte die Lieferzeit mehrere Wochen betragen. Zudem müssten Millionen von Teilen, die nicht benötigt wurden, eingelagert werden, bevor sie letztlich als Abfall enden. Statt die Teile zu bestellen, nutzte das Team also das vorhandene CAD, um in kürzester Zeit mehrere hundert Stück auf dem Form 4 zu drucken. Innerhalb einer Woche waren die Teile bereit, und die Lösung reduzierte die Gesamtkosten und Vorlaufzeiten des gesamten Projekts.
„Mit dem Form 4 waren wir in der Lage, die Teile zu wesentlich geringeren Kosten zu drucken, als wenn wir sie hierher geordert und die Mindestmenge bestellt hätten – was mehrere Millionen Stück bedeutet hätte. Wir hatten die Teile im Nu zur Verfügung und mussten auf nichts warten.“
Matthias Schulz, Leiter der Prototypenentwicklung für Sitze, Brose North America
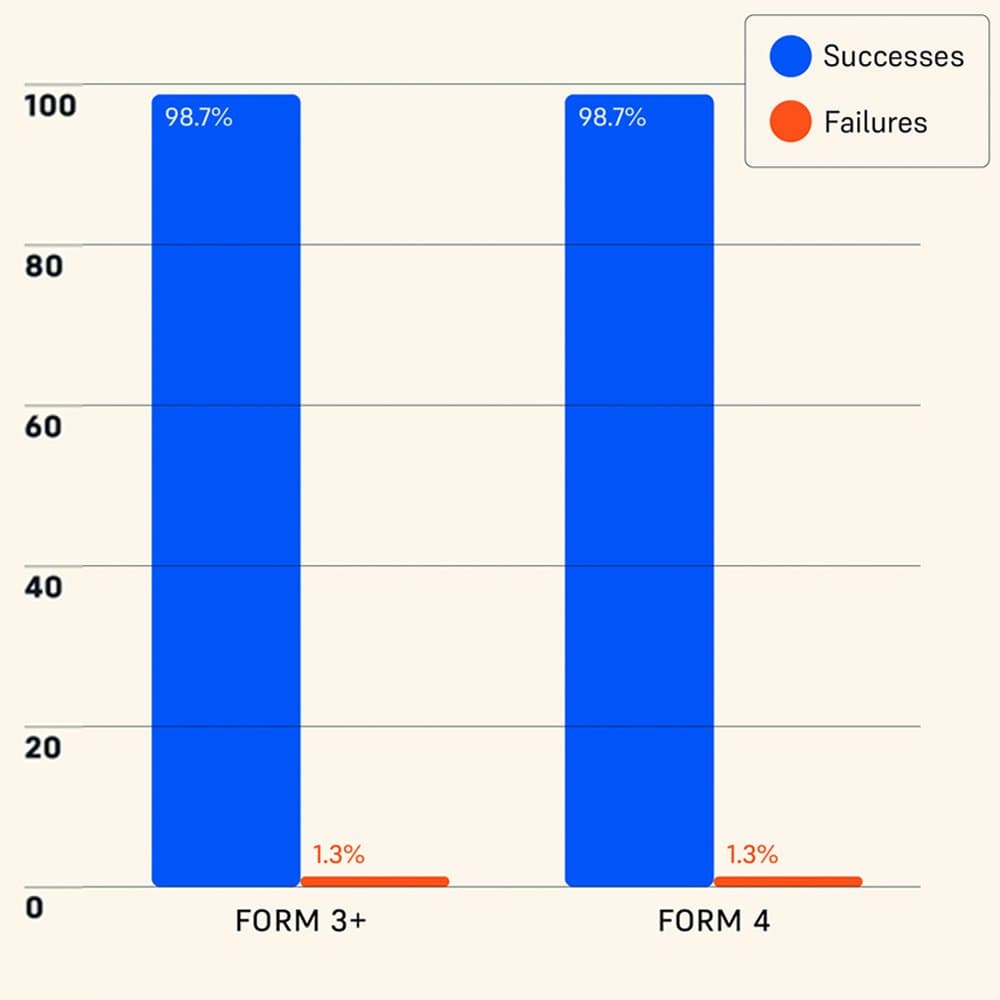
Zuverlässigkeit von Form 4 und anderen Kunstharz-3D-Druckern unabhängig getestet
Der Form 4 von Formlabs erreichte in einer Untersuchung eines unabhängigen, weltweit führenden Produkttesters eine Druckerfolgsrate von 98,7 %. Eine vollständige Beschreibung der Testmethode und die Ergebnisse finden Sie in unserem Whitepaper.
SLA und SLS vereint für Prototypen in großen Mengen
Wenn Bauteile an Komplexität, Größe und Stückzahl zunehmen, greift Brose für Prototyping wie auch Produktion auf seine Flotte von drei SLS-3D-Druckern der Fuse-Serie zurück. Dank des selbststützenden Druckbetts ermöglicht der SLS-3D-Druck vollgepackte Konstruktionskammern für den Druck auf Produktionsniveau. Darüber hinaus machen die Festigkeit und die mechanischen Eigenschaften von gesintertem Nylon die Technologie ideal für Endbauteile. Vor kurzem setzte Broses Team für additive Fertigung bei einem Projekt sowohl die SLA- als auch die SLS-Technologie ein, um den Prototyp einer Sitzfederungsmatte herzustellen.
Das Team druckte die lichtdurchlässigen, flexiblen Teile aus Durable Resin auf den SLA-3D-Druckern der Form-Serie und die Verbindungsrohre aus Nylon 12 GF Powder auf der Fuse-Serie. Jeder Mattenprototyp bestand aus sechs SLS-Teilen und drei SLA-Teilen. Insgesamt baute das Team 150 dieser Matten zusammen, um sie als Teil einer kompletten Sitzbaugruppe zu testen.
Dank seiner betriebsinternen Geräte für Rapid Prototyping war Brose in der Lage, eine wichtige Komponente seiner Sitzbaugruppe selbst zu entwerfen, zu testen und zu iterieren, ganz ohne Werkzeugbau oder Outsourcing. „Manchmal ist die Kombination von SLA und SLS die Lösung, wie bei dieser Sitzfederungsmatte. Umspritzwerkzeuge sind sehr komplex und teuer, deshalb haben wir die Teile für SLS so konstruiert, dass sie über den Draht einrasten, und die SLA-Teile als 'Grünteile' auf dem Draht installiert und so ausgehärtet“, berichtet Schulz.
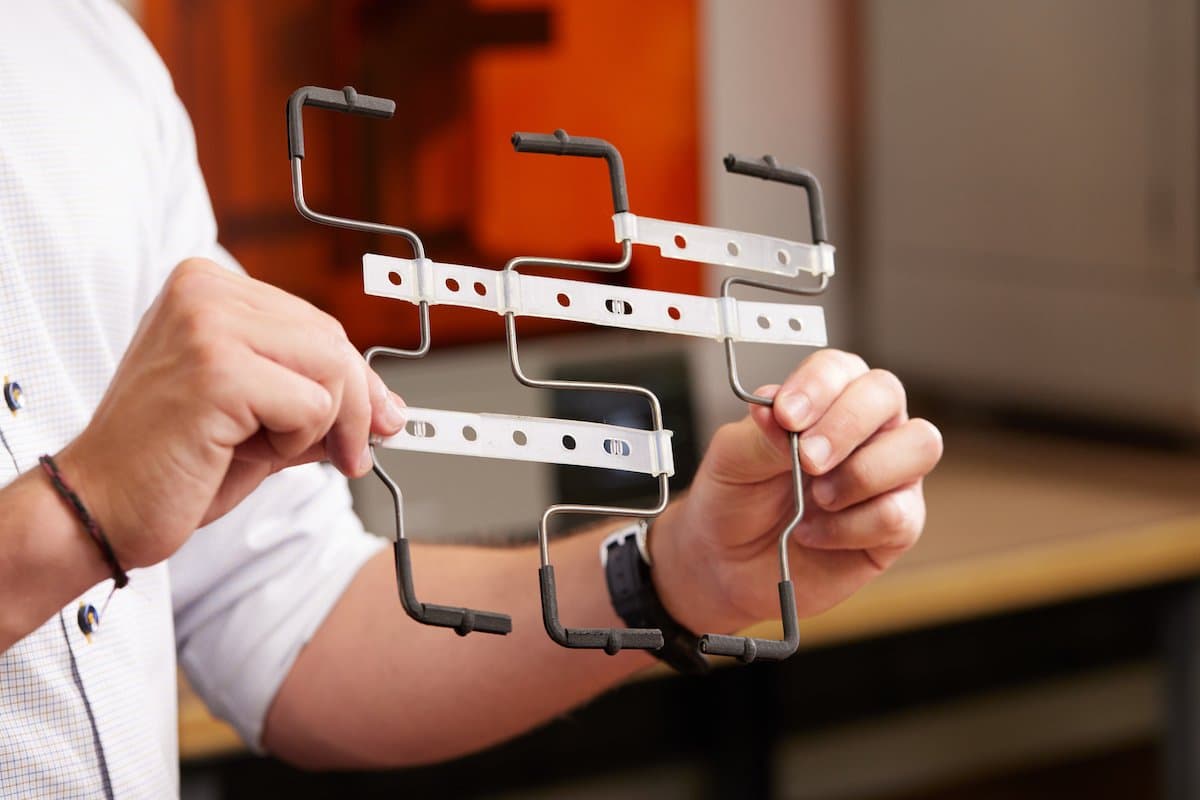
Diese Sitzfederungsmatte besteht sowohl aus SLA-Teilen (Durable Resin, lichtdurchlässig) als auch aus SLS-Teilen (Nylon 12 GF Powder, dunkelgrau). Für die Tests wurden 150 dieser Baugruppen benötigt, bestehend aus 900 SLS-Teilen und 450 SLA-Teilen.
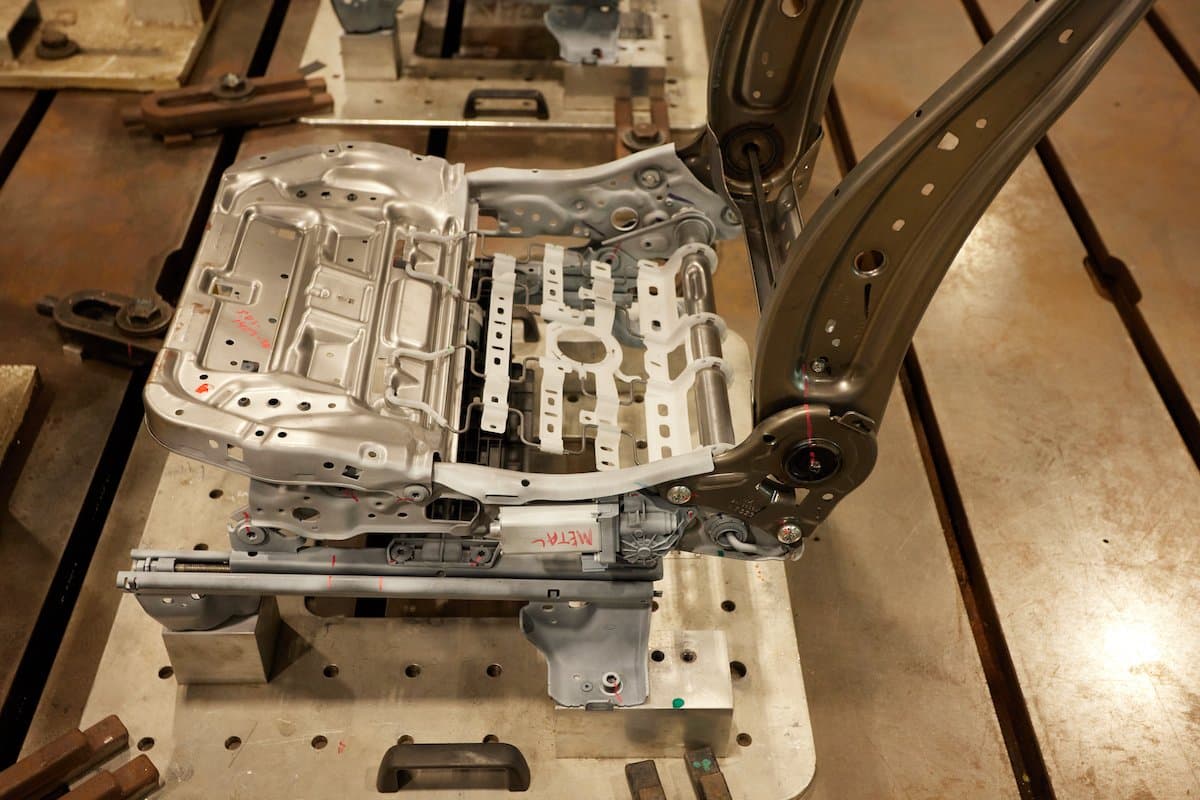
Prototypen und Produktionsteile für die Endverwendung (wie diese hier) werden Ermüdungstests unterzogen, die einen jahrelangen Gebrauch simulieren.
Fertigungshilfsmittel rationalisieren die Produktion
Die additive Fertigung wird bei Brose nicht nur für das Prototyping eingesetzt. Im Rahmen der 2022 gestarteten Initiative „Plant Goes Additive“ integriert das Unternehmen die Technologie in alle Abteilungen. Die Automobilproduktion steht niemals still und ist eine stark kontrollierte Branche – der gesamte Prozess ist schlank und auf Effizienz, Sicherheit und Produktqualität optimiert.
Roboterschweißvorrichtungen aus dem Form 4L binnen eines Tages
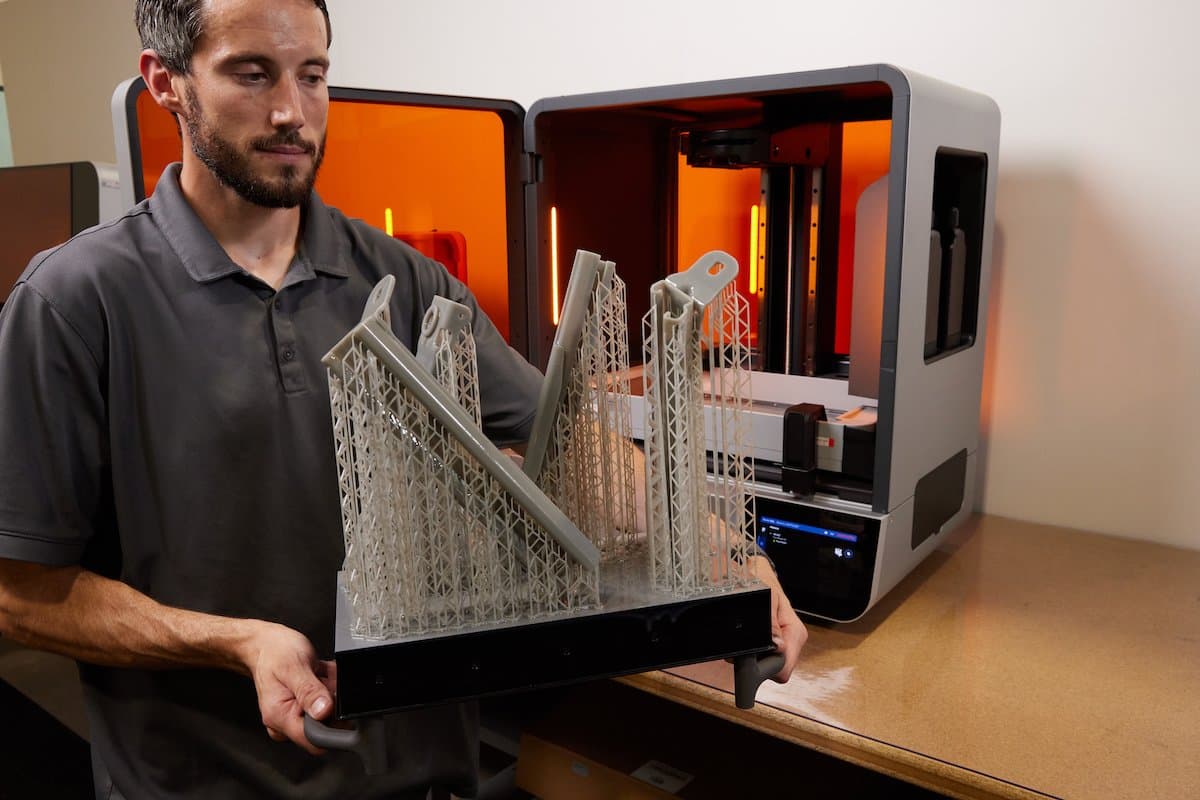
Der Form 4L liefert großformatige Teile noch am selben Tag, wie etwa diese Passungsvorrichtung zum Schweißen aus Fast Model Resin.
In jedem Glied der Lieferkette für die Automobilproduktion machen Metallteile einen Großteil des Gesamtprodukts aus. Daher spielt das Schweißen im Montageprozess natürlich eine große Rolle. Bei Brose North America, wo ein Team für additive Fertigung eine Flotte von SLA- und SLS-Druckern betreibt, müssen die Schweißroboter ständig zwischen verschiedenen Produktlinien wechseln. In einem Produktionswerk sind Schweißmaschinen auf eine einzige Produktlinie programmiert. Im Hauptsitz gibt es jedoch zwei robotische Maschinen, die für das Schweißen von Sitzprototypen aller Produktlinien zuständig sind.
Jedes Mal, wenn der Roboter auf eine neue Produktlinie umgestellt werden muss, muss die Schweißabteilung seine Parameter neu programmieren. Die Programmierung eines Schweißroboters mit Schienenprototypen aus Metall ist teuer, und oft stehen die Teile noch nicht zur Verfügung, wenn die Schweißstation für die Programmierung der Geräte bereit ist. Der 3D-Druck bietet hier eine schnelle und kostengünstige Lösung, denn die Teile zur Einrichtung der Fertigungszelle erfordern Schnelligkeit und Maßgenauigkeit.
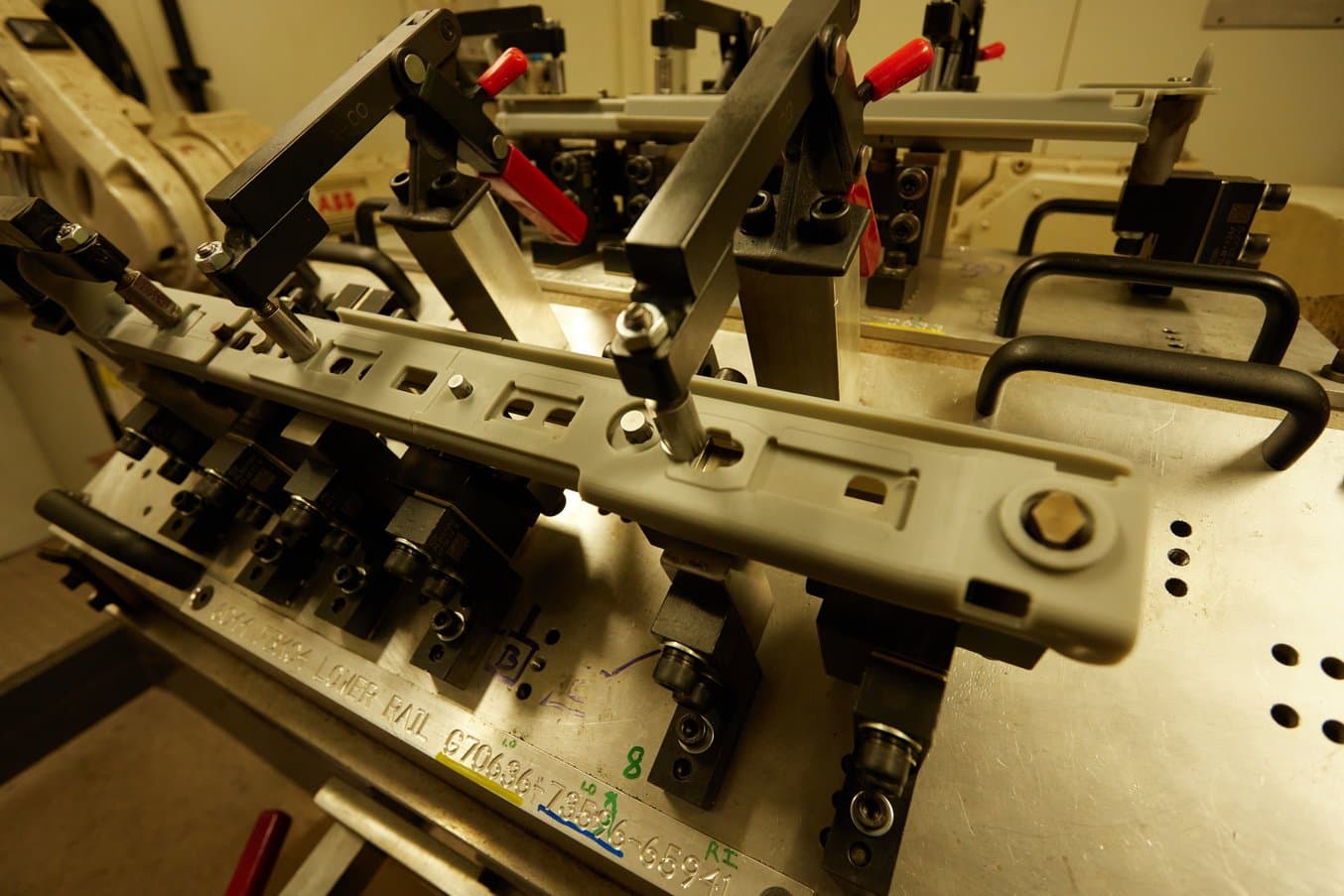
Diese Sitzkomponente wurde in weniger als drei Stunden auf dem Form 4L aus Fast Model Resin gedruckt, gewaschen, nachgehärtet und auf dem Schweißroboter montiert. Dadurch ist das Team in der Lage, den Roboter schnell auf die nötigen Bewegungen einzustellen.
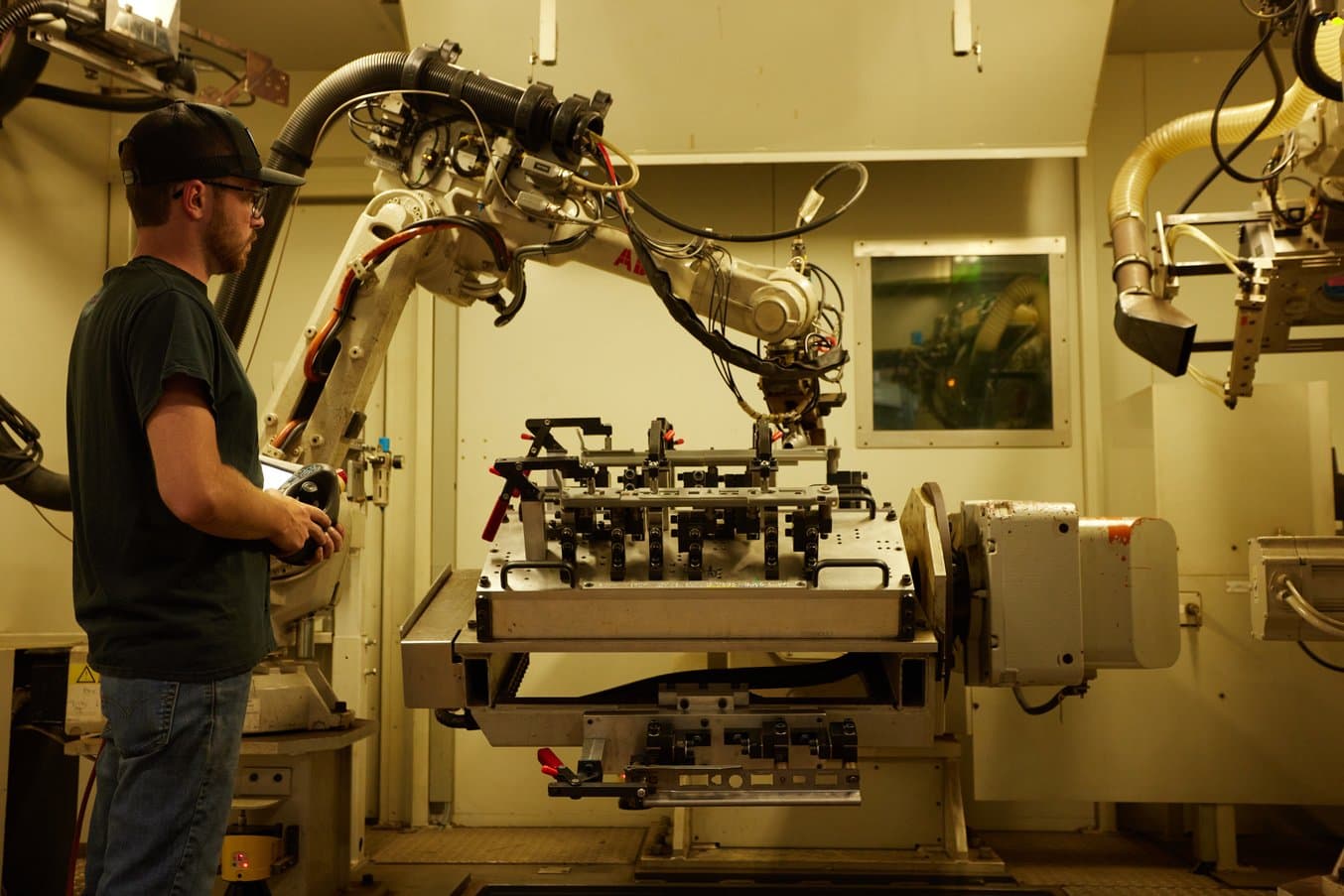
Passungsvorrichtungen wie diese helfen dem Schweißerteam, schnell und effizient zwischen Produktlinien zu wechseln. Sie sind hochpräzise, erschwinglich und können beliebig oft nachgefertigt werden, falls Änderungen oder Ersatzteile erforderlich sind.
Das Brose-Team öffnete sein Paket des neuen großformatigen Kunstharz-3D-Druckers Form 4L an einem Dienstagmorgen. Die Einrichtung beanspruchte nur 30 Minuten, und schon bald druckte das Team aus Fast Model Resin große Teile für die Einrichtung der Schweißzelle. Aufgeteilt in vier Einzelteile füllten diese Teile fast das gesamte Fertigungsvolumen aus. Trotz dieser Größe druckte der Form 4L die Vorrichtung in weniger als zwei Stunden, und nur 45 Minuten später, nach einem kurzen Waschgang und einer Nachhärtung, war sie auf dem Schweißroboter montiert.
„Mit dem neuen Form 4L von Formlabs können wir große Teile schnell drucken. Zum Beispiel nutzen wir den Form 4L zum Drucken von Teilen für unsere Schweißzelle in nur wenigen Stunden statt über Nacht. So kann das Schweißerteam von Brose den Roboter programmieren, bevor die gestanzten Metallbauteile eintreffen. Mit dem neuen Fast Model Resin erreichen wir den nötigen Detailgrad und die nötige Steifigkeit schneller als je zuvor.“
Matthias Schulz, Leiter der Prototypenentwicklung für Sitze, Brose North America
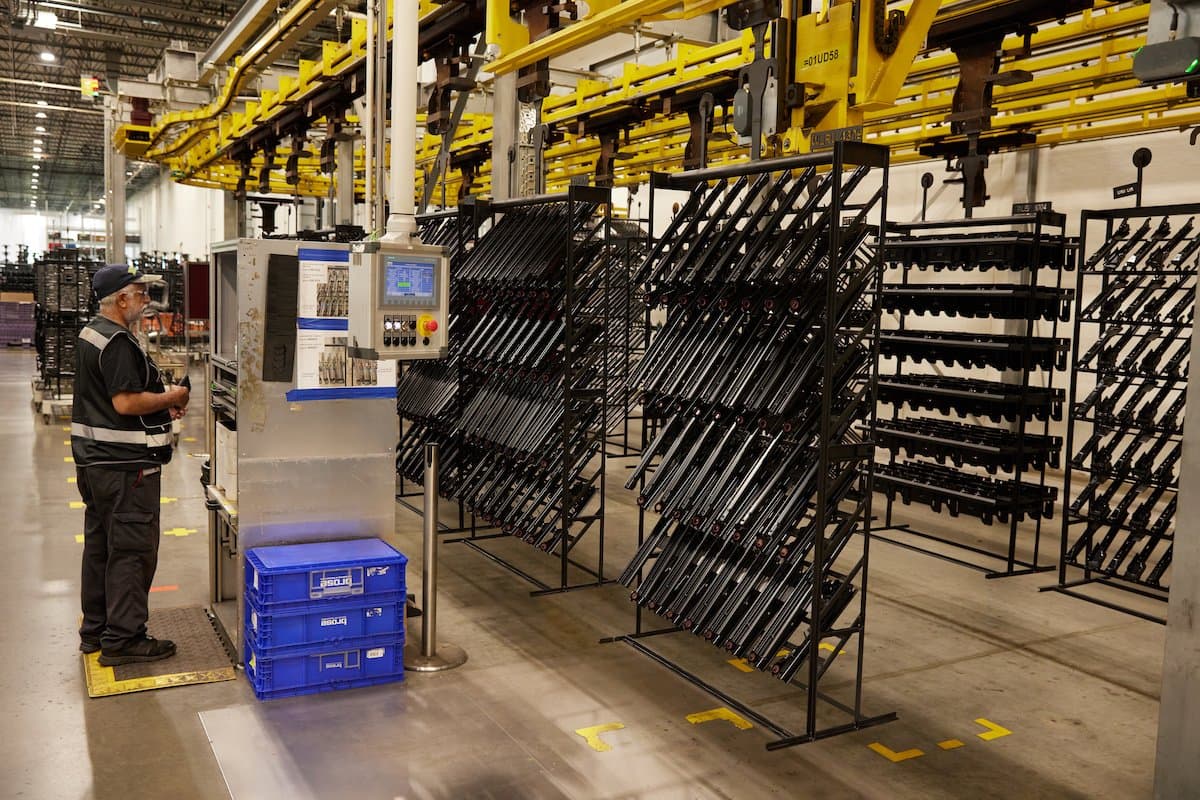
Beim Brose-Produktionswerk New Boston werden Tausende von Sitzschienen wie den oben abgebildeten zusammengeschweißt, um die Basis der Sitzbaugruppe zu bilden. Das Testen der Schweißparameter ist ein wesentlicher Bestandteil des Fertigungsprozesses.
Die Schweißparameter werden im nordamerikanischen Hauptsitz von Brose anhand von Prototypen und 3D-gedruckten Teilen ermittelt und dann für die Serienproduktion von geschweißten Sitzrahmen verwendet. Die Sitzschienen (oben) werden bei Brose New Boston mithilfe großer Schweißroboter montiert.
End-of-Line-Verbinder (EOL) senken Betriebskosten bei Brose New Boston
Im Brose-Werk in New Boston, etwa dreißig Minuten westlich des Stadtzentrums von Detroit, dient der 3D-Druck zur Herstellung maßgefertigter Fertigungshilfsmittel, die den Montageprozess rationalisieren. Vor ihrer Integration in die Produktion werden die 3D-gedruckten Teile strengen Tests unterzogen, aber sobald sie freigegeben sind, tragen sie dazu bei, den Ausschuss zu reduzieren, die Produktionsdauer zu verkürzen und die Maschinen durchgängig am Laufen zu halten.
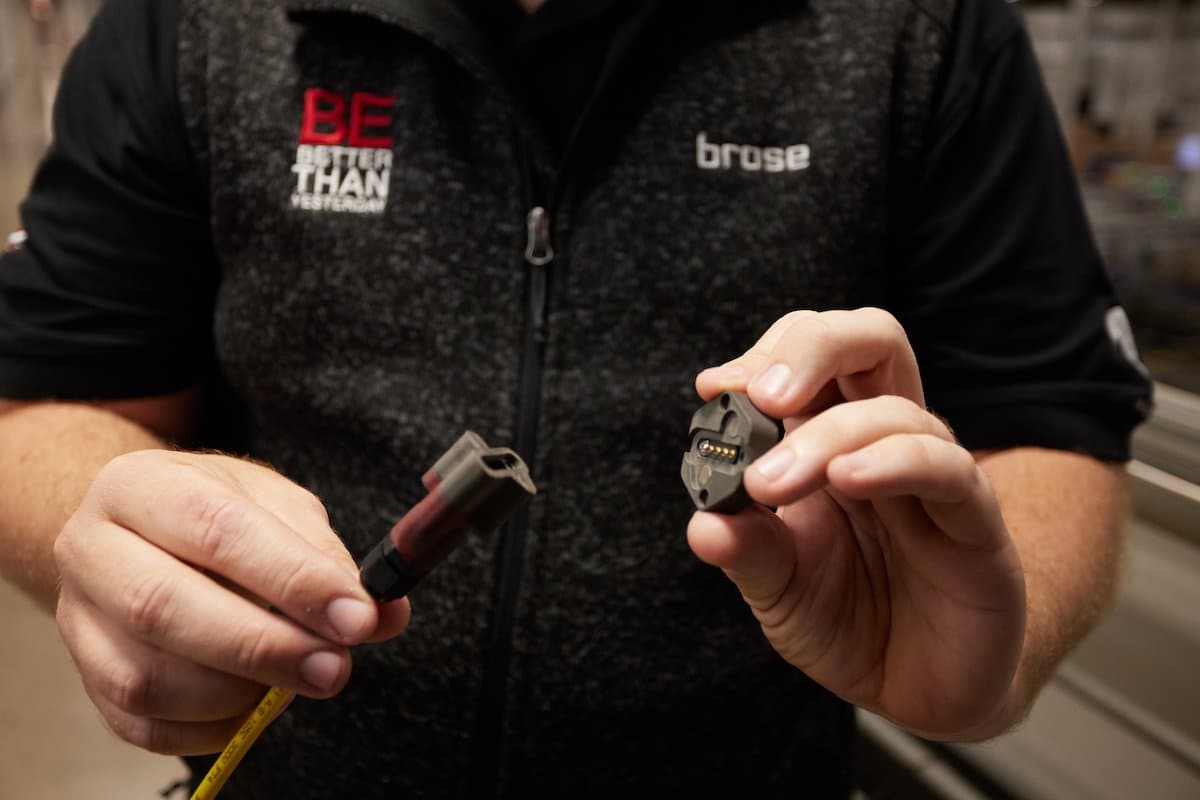
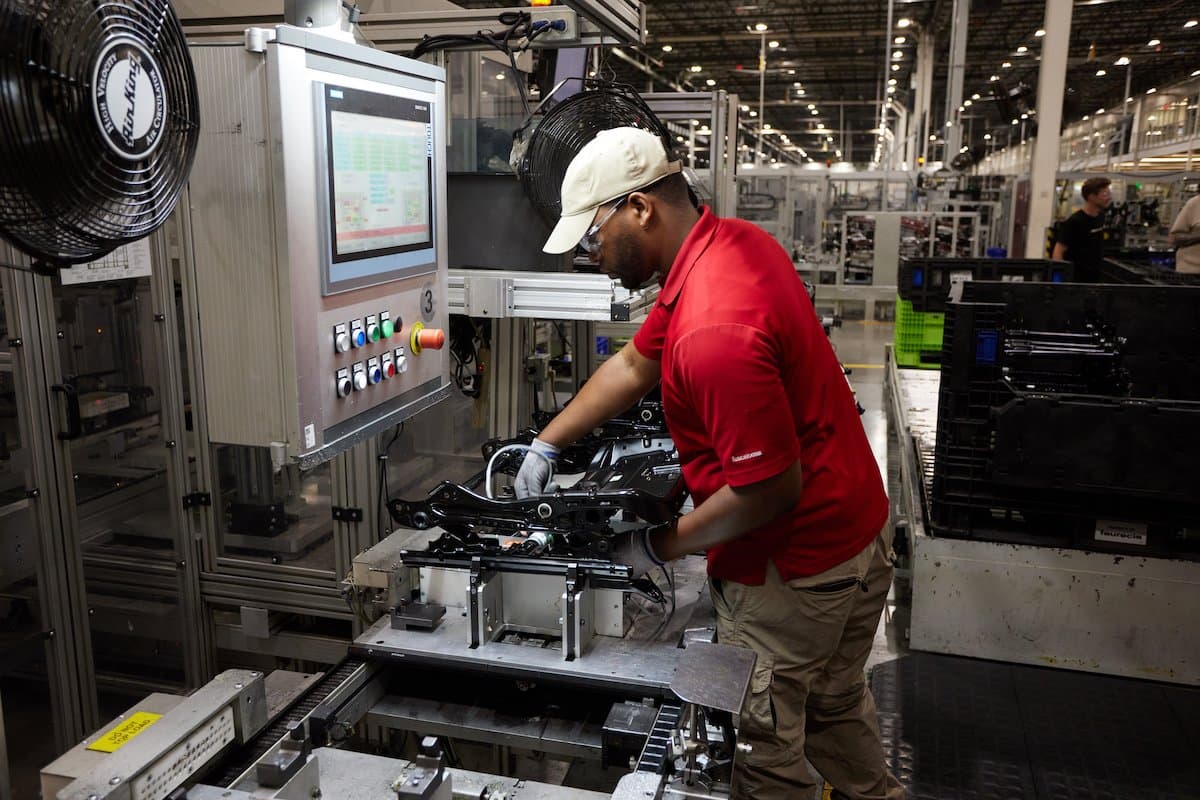
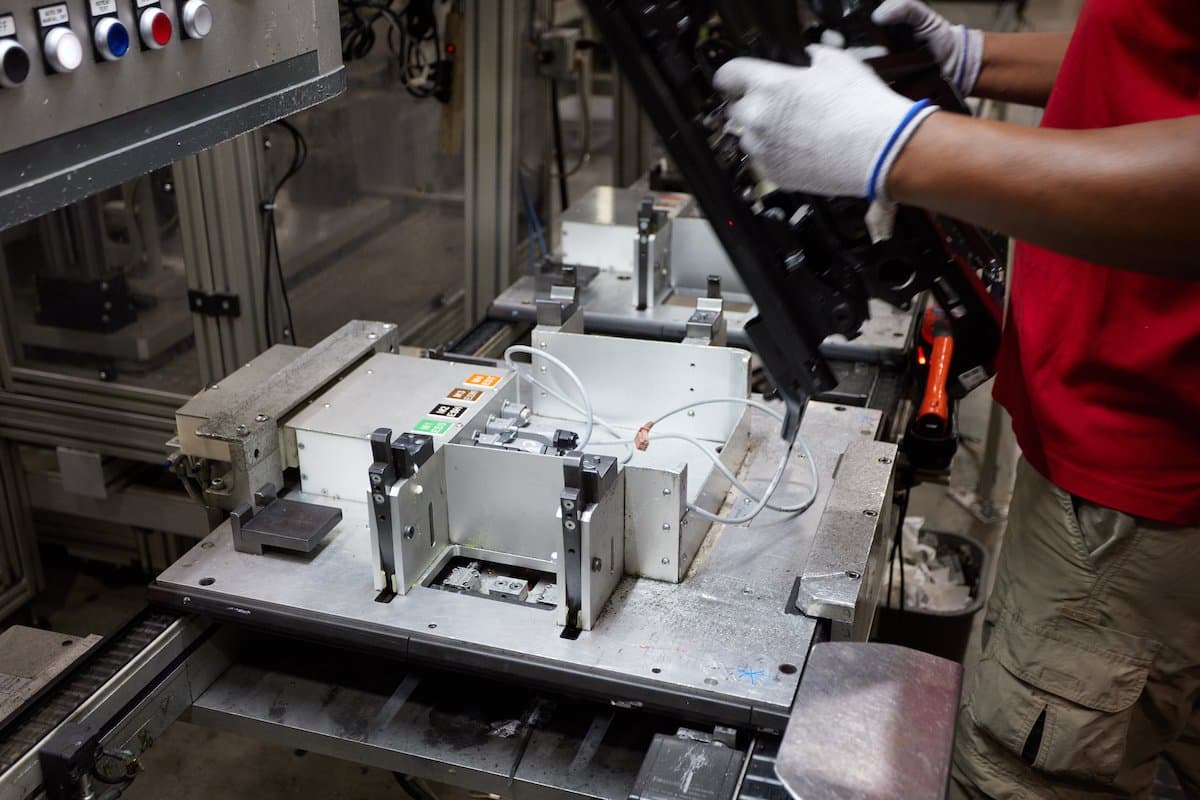

Dieser End-of-Line-Verbinder (EOL) wird in der letzten Phase der Montage des Autositzes eingesetzt. Nachdem der Sitzrahmen mit dem Strom verbunden und letzte Prüfungen durchgeführt wurden, wird das Teil für die nächste Phase des Prozesses entnommen. Hierbei wurde der elektrische Anschluss oftmals vergessen, sodass beim Entfernen des Sitzes das Kabel durchbrach, was einen Schaden von mehreren hundert Dollar am Montageband verursachte und die Produktion stoppte.
Gemeinsam mit dem Team von New Boston entwickelte das Team für additive Technologien eine magnetische Verbindungsleitung. Sie lässt sich leicht am Band und am Sitzrahmen befestigen, löst sich aber ohne Beschädigung ab, wenn der Sitzrahmen ohne manuelles Entfernen des Kabels weggezogen wird. „Wir nutzen 3D-gedruckte Fertigungshilfsmittel, um den Verschleiß von Maschinen zu verringern. Damit können wir Reparaturen an der Fertigungsstraße schneller durchführen. Das bedeutet weniger Ausfallzeiten in der Produktion und führt zu einem höheren Gesamtdurchsatz“, so Schulz.
Übergangsweise Serienproduktion von Automobilteilen für die Endverwendung
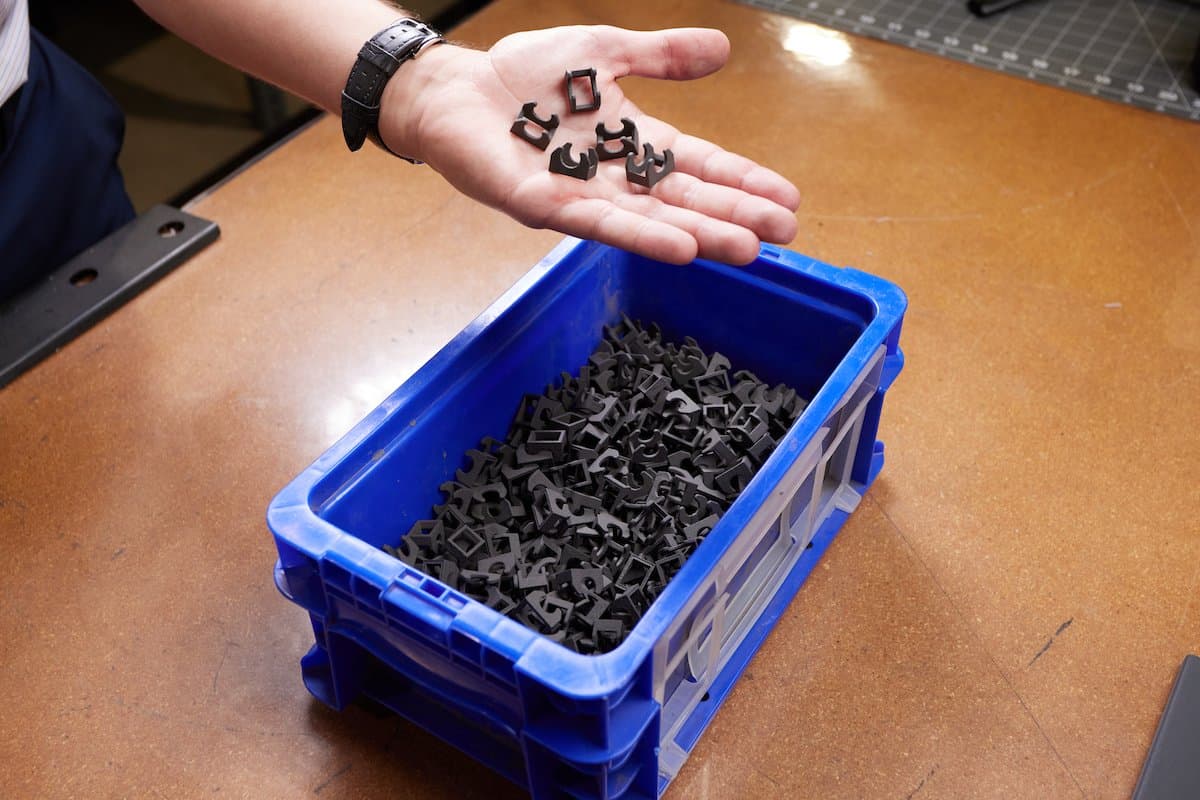
Für Sitzbaugruppen im BMW X7 wird Brose 250 000 dieser Clips 3D-drucken.
Wie Schulz uns erklärt, hat sich die Automobilindustrie besonders in den letzten fünf Jahren rapide verändert. Die zunehmende Verbreitung von Elektrofahrzeugen, die wachsende Nachfrage nach kundenspezifischen Funktionen und Probleme mit der Lieferkette haben OEMs dazu veranlasst, verstärkt in die additive Fertigung als zuverlässige Produktionsalternative zu investieren.
„Wir haben immer mehr Kunden, die additive Technologien nachfragen. Auch für die Benutzeroberflächen für den Endkunden spielt dies eine Rolle, denn es ist immer mehr Personalisierung in den Fahrzeugen gewünscht, weshalb additive Technologien von den OEMs immer stärker angefordert werden“, führt Schulz aus.
Für die Endverwendung war der 3D-Druck, insbesondere in der stark regulierten Automobilindustrie, nicht immer eine Option. Deshalb ist Broses Team für additive Fertigung erst dann zur Endfertigung übergegangen, als die Hardware und Materialien zuverlässig in der Lage waren, leistungsstarke Teile zu liefern.
„Wir entschieden uns, auf den Formlabs-Zug aufzuspringen. Die Materialauswahl und die Einheitlichkeit der Drucke haben sich so stark verbessert, dass die Technologie nun auch für den Einsatz in der Automobilindustrie bereit ist. Insbesondere bei den OEMs gibt es Sicherheits- und Haltbarkeitsbedenken. Wir versuchen, diese auszuschließen. Und in Zusammenarbeit mit Formlabs haben wir bewiesen, dass wir Teile wie die für den aktuellen BMW X7 in der Praxis implementieren können.“
Matthias Schulz, Leiter der Prototypenentwicklung für Sitze, Brose North America
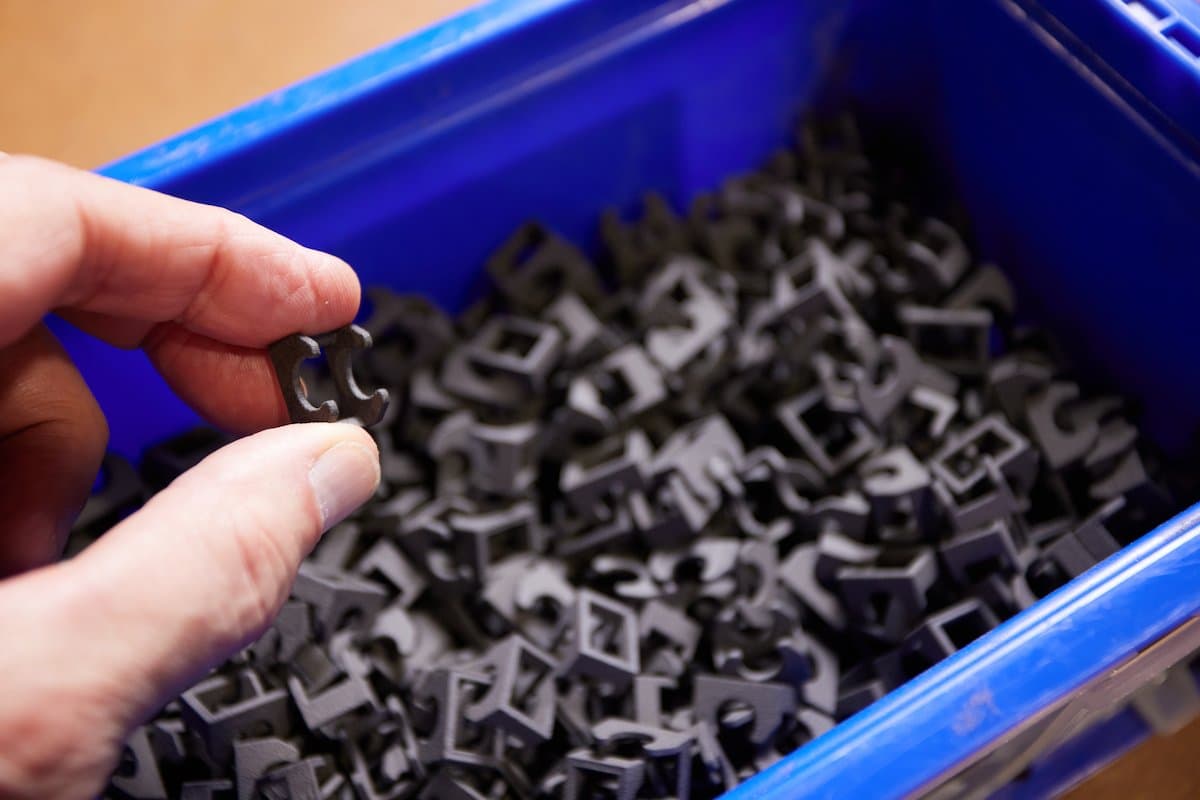
Anwendung: Sitzbauteile für BMW X7
Arbeitsablauf: 3D-Scan, Iteration, 3D-Druck auf den SLS-3D-Druckern der Fuse-Serie für die Endproduktion.
Stückzahl: 250 000
Details zum Druck:
- Drucker: Fuse 1 und Fuse 1+ 30W
- Material: Nylon 12 GF Powder
- Fertigungsvolumen: 1440 Teile pro Konstruktionskammer
- Teile pro Monat: 16 000
Warum 3D-Druck?
- 3D-Druck als Übergangslösung bis zur Verfügbarkeit von Produktionswerkzeug
Brose nutzt den 3D-Druck für die Endproduktion als kostengünstige und schnelle Alternative zur traditionellen Fertigung. Wenn ein Erstausrüster ein Bauteil anfordert, oder auch eine Änderung an einem bestehenden Teil, und die Massenproduktion mithilfe von Fertigungswerkzeug zu langwierig wäre, dann prüft das Team von Brose den 3D-Druck als mögliche Alternative. Eine zentrale Rolle spielt hierbei das Reverse Engineering und das Scannen vorhandener Komponenten.
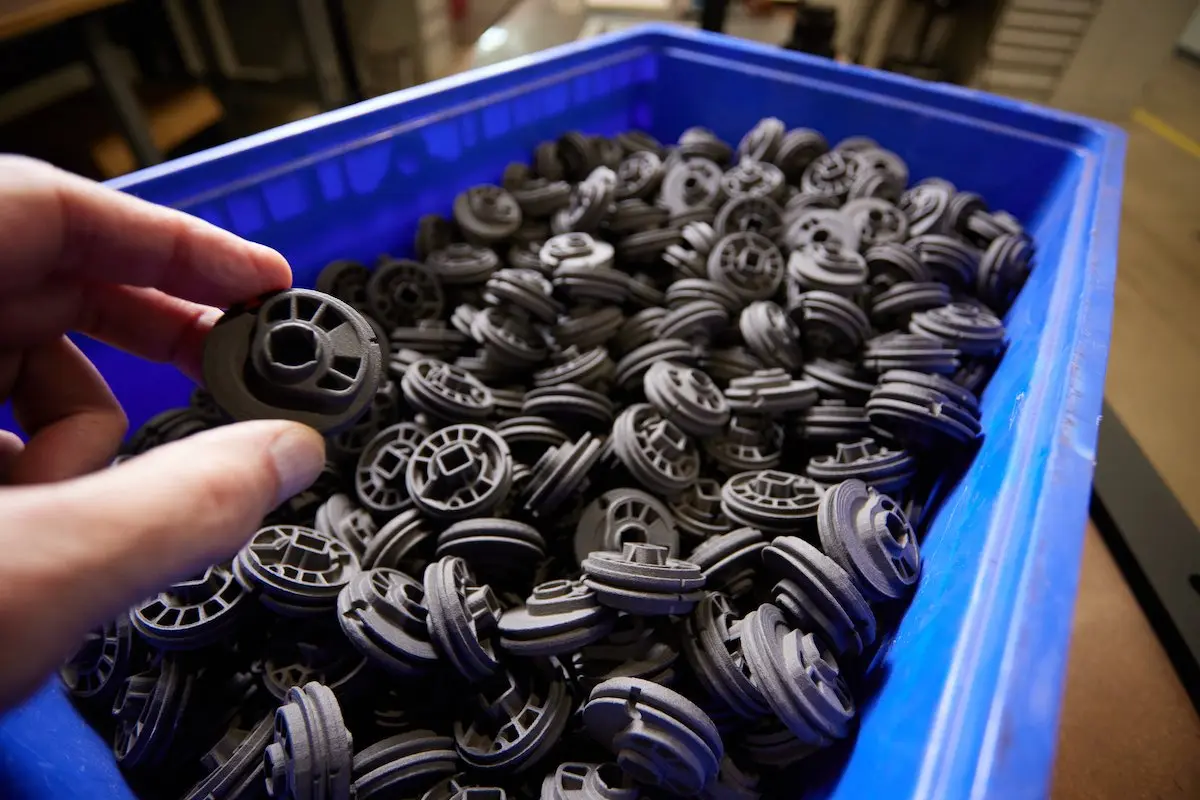
Anwendung: Bowdenzug-Auslösung
Arbeitsablauf: 3D-Scan, Iteration, 3D-Druck auf den SLS-3D-Druckern der Fuse-Serie für die Endproduktion.
Stückzahl: 20 000
Details zum Druck:
- Drucker: Fuse 1 und Fuse 1+ 30W
- Material: Nylon 12 GF Powder
- Durchsatz: 144 Teile pro Kammer, 1000 Teile pro Woche
Warum 3D-Druck?
- 3D-Druck als Übergangslösung bis zur Verfügbarkeit von Produktionswerkzeug
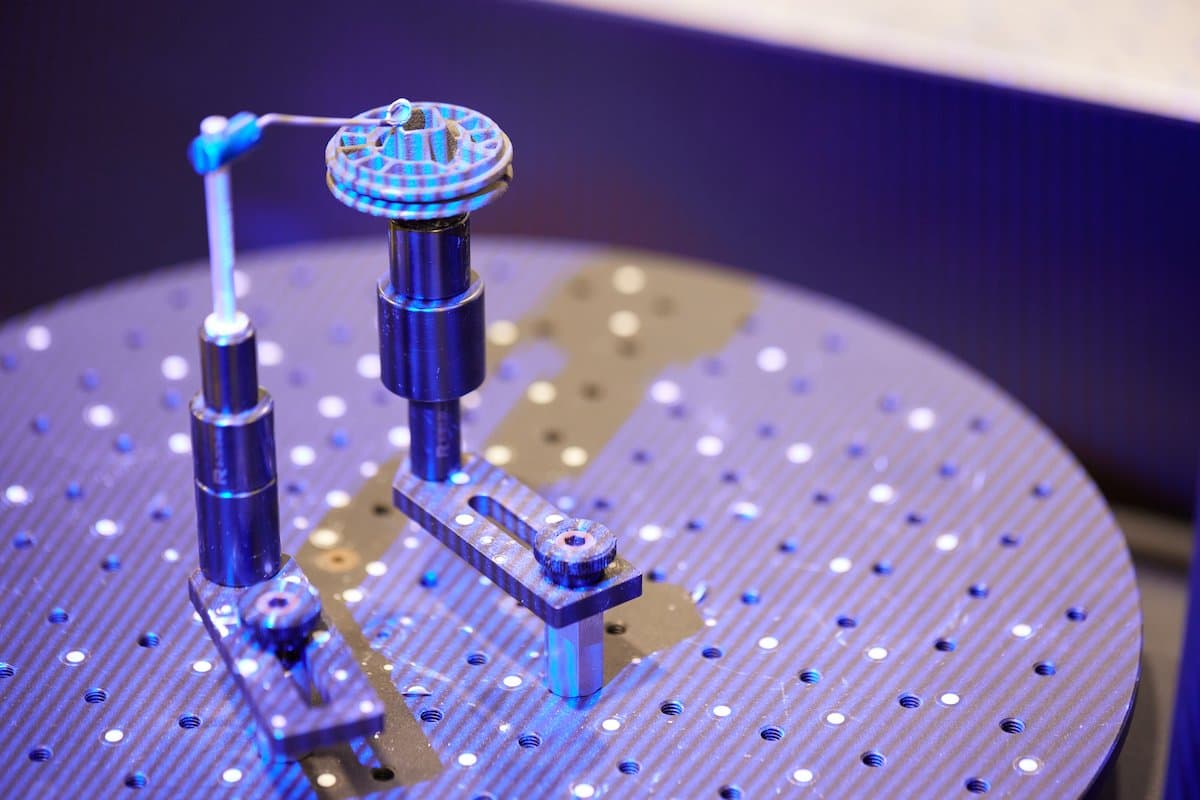
Häufig erstellt Brose Scans von bestehenden Bauteilen oder früheren Iterationen, um Änderungen im CAD vorzunehmen und die aktualisierte Version noch am selben Tag zu drucken.
Bei diesem Bauteil handelt es sich um eine Bowdenzug-Auslösung – Brose druckt davon 20 000 Stück auf den SLS-3D-Druckern der Fuse-Serie, um sie in die endgültige Sitzbaugruppe für einen großen, bekannten Erstausrüster einzubauen.
„Brose hat sich entschieden, den Formlabs-SLS-Druck in den Betrieb zu holen, weil die Technologie uns einen äußerst schnellen 3D-Druck mit weniger Nachbearbeitungsaufwand ermöglicht als beim SLA-Druck. Wir sind in der Lage, hohe Stückzahlen zu drucken, was für die Übergangsfertigung oder sonstige Endbauteile für OEMs eine Voraussetzung ist“, sagt Schulz.
Bei drei SLS-3D-Druckern der Fuse-Serie, die im Dauerbetrieb Prototypen, Fertigungshilfsmittel und Hunderttausende von Endbauteilen produzieren, stehen Zuverlässigkeit und Konsistenz an erster Stelle. Das Team nutzt hierfür Nylon 12 GF Powder, wegen seiner Maßgenauigkeit und seiner großen Ähnlichkeit mit spritzgegossenem Nylon, selbst bei Stückzahlen auf Produktionsniveau. Nach jedem Druckauftrag wird eine kurze Wartungsprüfung am Fuse 1 oder Fuse 1+ 30W durchgeführt, die nur etwa fünfzehn Minuten dauert und eine kontinuierliche, effiziente Produktion gewährleistet.
„Formlabs weiß, wie man einen Drucker baut, der einfach zu warten ist. Die Geräte sind sehr zuverlässig und wir erleben kaum Fehldrucke, sodass wir den Druck größerer Mengen von Teilen angehen und mit Gewissheit zur Produktion übergehen können“, urteilt Schulz.
Von Null auf Hundert: 3D-Druck gewinnt in der Automobilindustrie an Fahrt
In seinem Streben nach kontinuierlicher Verbesserung hat Brose in neue Technologien wie die additive Fertigung und die Automatisierung investiert, um seine Prozesse zu rationalisieren und allen Kunden innovative Lösungen zu bieten. Mit wachsender Bedeutung des 3D-Drucks im Unternehmen sind Vorreiter wie Schulz bestrebt, neue Wege zu finden, um die schnellen Durchlaufzeiten und (häufig) niedrigeren Kosten auszunutzen.
Schnelle, leistungsstarke Werkzeuge wie Form 4, Form 4L und die Fuse-Serie liefern Prototypen, Fertigungshilfen und Endbauteile in Stunden oder Tagen statt in Wochen oder Monaten. „Formlabs ist der richtige Partner für uns. Wir brauchten eine schlüsselfertige Lösung, mit der wir Teile in größeren Mengen und mit weniger technischer Unterstützung herstellen können. Die Software, der Support und die Drucker von Formlabs sind genau das Richtige für uns.“
Um mehr über den 3D-Druck in der Automobilindustrie zu erfahren, erkunden Sie unsere Website. Wenn Sie sich selbst von der Qualität des SLA- oder SLS-3D-Drucks überzeugen möchten, fordern Sie ein Probeteil an.