Die Mission von Glassboard ist klar formuliert: die ehrgeizigsten Unternehmen der Welt bei der Entwicklung von Produkten zu unterstützen, die Kunden begeistern. Das Team möchte nicht einfach bloß CAD-Dateien und Präsentationen erstellen; es hat sich vorgenommen, als Produktentwickler ganzheitlich zu arbeiten und Unternehmen bei der Produktion, Preisverhandlung sowie der Aufstellung der Lieferketten zu unterstützen, um ein Produkt auf den Markt zu bringen.
Da Glassboard Design in einer Reihe von Branchen tätig ist, stellt 3D-Druck für das Unternehmen ein unschätzbares Hilfsmittel bei der Erschaffung innovativer Produkte dar. Vice President of Operations Grant Chapman erklärt: „Glassboard ist ein Allround-Produktentwickler, doch wir versuchen genug Fachkenntnis im Unternehmen zu haben, um jegliches Projekt angehen zu können. Wir stecken nicht nur in einem Branchenzweig. Wir beschäftigen uns nicht nur mit der Radsportbranche, nicht nur mit der Gesundheitsbranche und nicht nur mit Verbraucherelektronik. Wir machen von allem ein bisschen. Und Formlabs bietet ein Werkzeug, das uns durch all diese Branchen begleitet, sowie eine Vielfalt an Materialien, die uns ermöglicht zu tun, was wir wollen.“
Lernen Sie in diesem Beitrag das Team von Glassboard kennen und erfahren Sie, wie das Unternehmen den Form 2 und den Form 3BL nutzt, um Barrieren zwischen den Zielen seiner Kunden und ihren technischen Möglichkeiten zu durchbrechen und dabei innovative Produkte zu erschaffen.
Das richtige SLA-Material für jedes Projekt
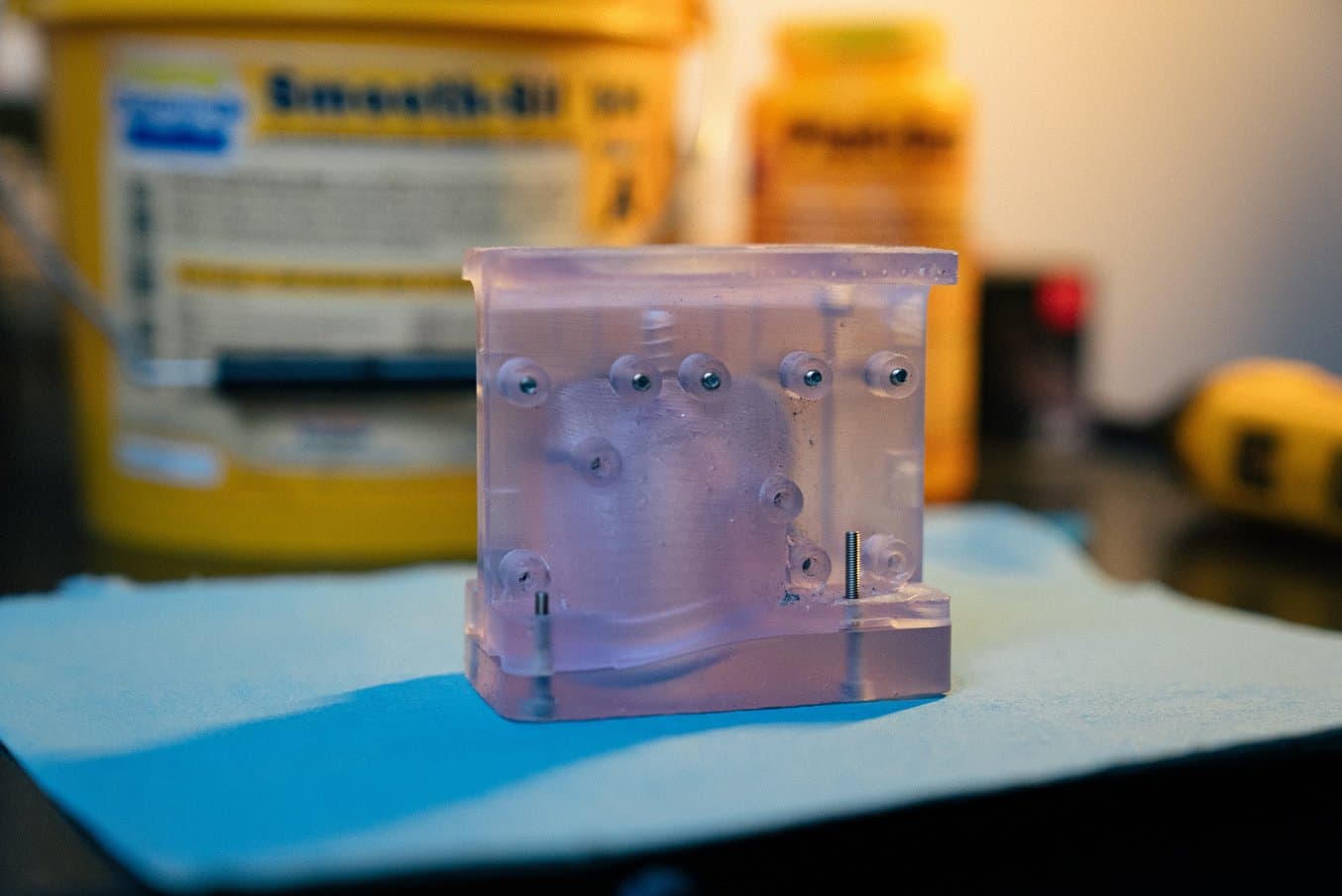
BioMed Clear Resin wird verwendet, um transparente Formen zu erstellen, die auf Luftblasen oder sonstige Mängel überprüft werden können.
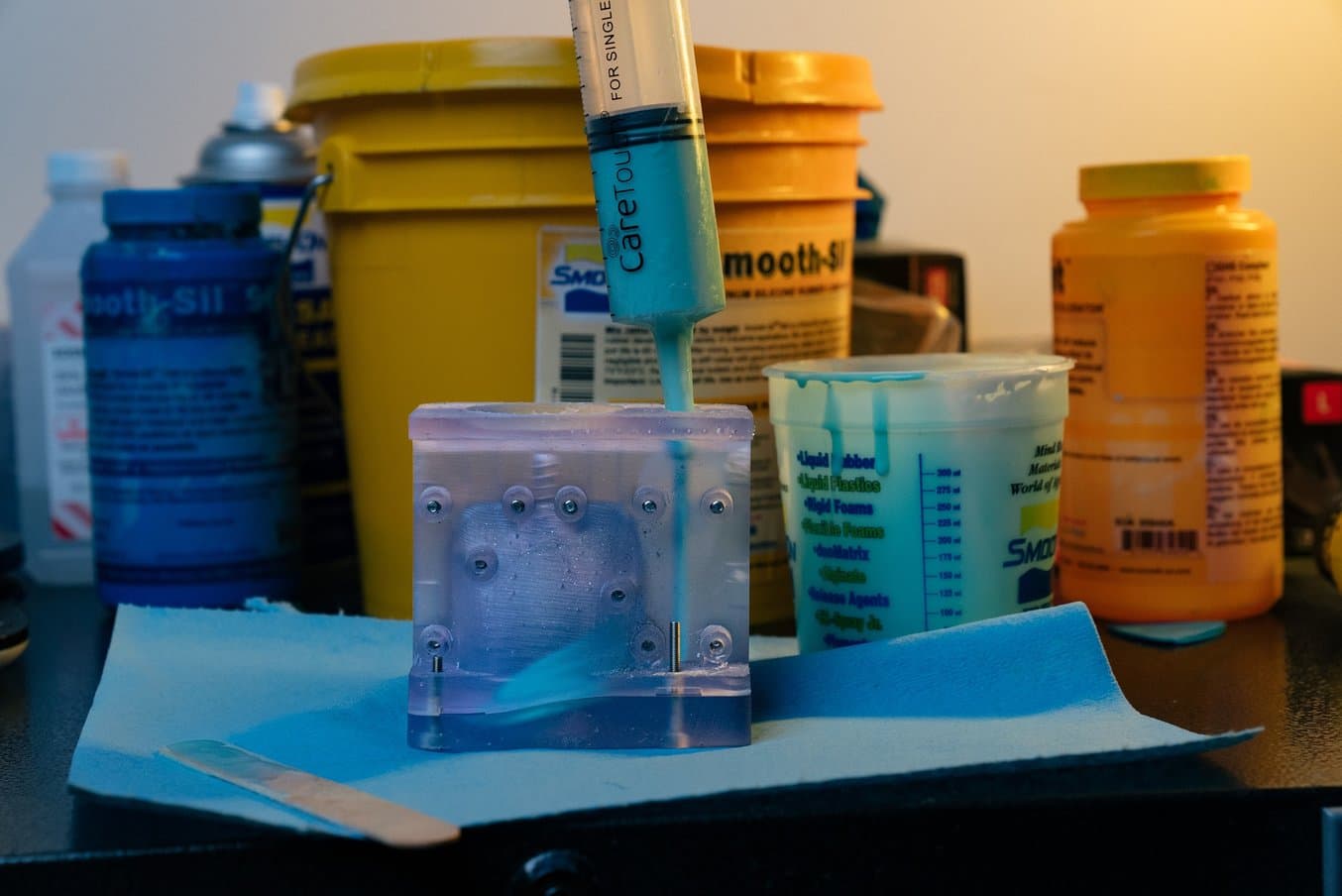
Glassboard nennt ganz offen den Grund, warum es 3D-Drucker von Formlabs nutzt: Es gibt für alles das passende Material.
Das Team von Glassboard arbeitet mit einer breiten Palette von Produkten, wobei jedes Projekt einen anderen Arbeitsablauf oder eine andere Technik erfordert, um den perfekten Prototyp zu kreieren: von Spritzguss über Thermoformen bis zu Silikonformenbau. Deshalb braucht das Team einen 3D-Drucker, der Schritt hält und Lösungen liefert. „Je mehr sich die Materialbibliothek vergrößert, desto besser wird mein Leben. Es ist eine lineare Funktion“, so Chapman.
Diese Problematik wurde erst kürzlich in einem gemeinsamen Projekt von Glassboard mit Sunny, einem Hersteller von Menstruationsprodukten, deutlich. Sunny versucht eine neue Menstruationstasse auf den Markt zu bringen und suchte nach einer innovativen Lösung, damit das Produkt sich abhebt.
Dem Team von Glassboard war klar, dass diese Art von Produkt – ein flexibles Verbraucherprodukt zur Anwendung am menschlichen Körper – ausgiebiges Prototyping und Tests erfordern würde. Chapman wandte sich an zwei seiner zuverlässigsten Mitarbeiter – seine zwei SLA-3D-Drucker von Formlabs – und begann mit Elastic 50A Resin und Flexible 80A Resin zu drucken, um die Tasse nachzubilden.
„Für das Produkt von Sunny haben wir die Bandbreite der Kunstharze von Formlabs wirklich ausgenutzt. Von den biegsamsten, elastischsten und gummiartigsten bis hin zu den steifen Materialien über fast alles, was dazwischen liegt, haben wir bei diesem Produkt alles verwendet.“ - Grant Chapman
Bei anderen Projekten brauchte das Team ein Material, das Schlagprüfungen standhält – genau entgegengesetzt zu den Anforderungen eines empfindlichen Medizinproduktes. Das Team wählte hierfür Tough 2000 Resin und druckte daraus Teile, die durch strapaziöse Sturz- und Festigkeitstests beansprucht wurden. „Wir arbeiten auch noch an einem Sicherheitsprodukt, das mit Tough 2000 Resin seine Schlagprüfungszertifizierung bestanden hat, nachdem es mehreren Stürzen standhielt. Alle anderen Kunststoffe in diesem Produkt waren vakuumgeformte Polycarbonat-Teile, deren Formwerkzeuge ebenfalls auf dem Form 3BL gedruckt wurden“, berichtet Chapman.
Ohne die umfangreiche Materialbibliothek hätten viele dieser Projekte Chapman zufolge nie das Licht der Welt erblickt oder wären nie so gut gelungen. „Der Prototyp dieses Sicherheitsprodukts existiert nur dank der Möglichkeiten des 3BL, und er hat es schon in Prototypform durch die tatsächlichen Zertifizierungstests geschafft, mit Polymeren für die Produktion also erst recht“, fügte er hinzu.
Die folgenden drei Kunstharze verwendet Glassboard Designs am liebsten, um Probleme in der Produktentwicklung zu lösen:
- Tough 2000 Resin: „Es dreht sich alles um Funktionalität. Es kommt echtem Kunststoff so nah, dass man damit sogar Prototypen von funktionsfähigen Teilen wie Schnappverbindungen und Biegescharnieren herstellen kann“, erklärte uns das Team.
- Draft Resin, weil es „dafür, wie genau es ist, einfach unglaublich schnell druckbar ist, und dabei immer noch gut aussieht“, wie Senior Product Development Engineer Ben Ettinger beschreibt.
- Und schließlich einer der persönlichen Favoriten Chapmans, Rigid 10K Resin: „Als ihr Rigid 10K herausgebracht habt, habe ich gedacht, ich träume, denn die technischen Daten schienen zu gut, um wahr zu sein. Ich habe sofort einen Liter zum Testen bestellt, die Ergebnisse sind da... es ist wirklich das Beste.“
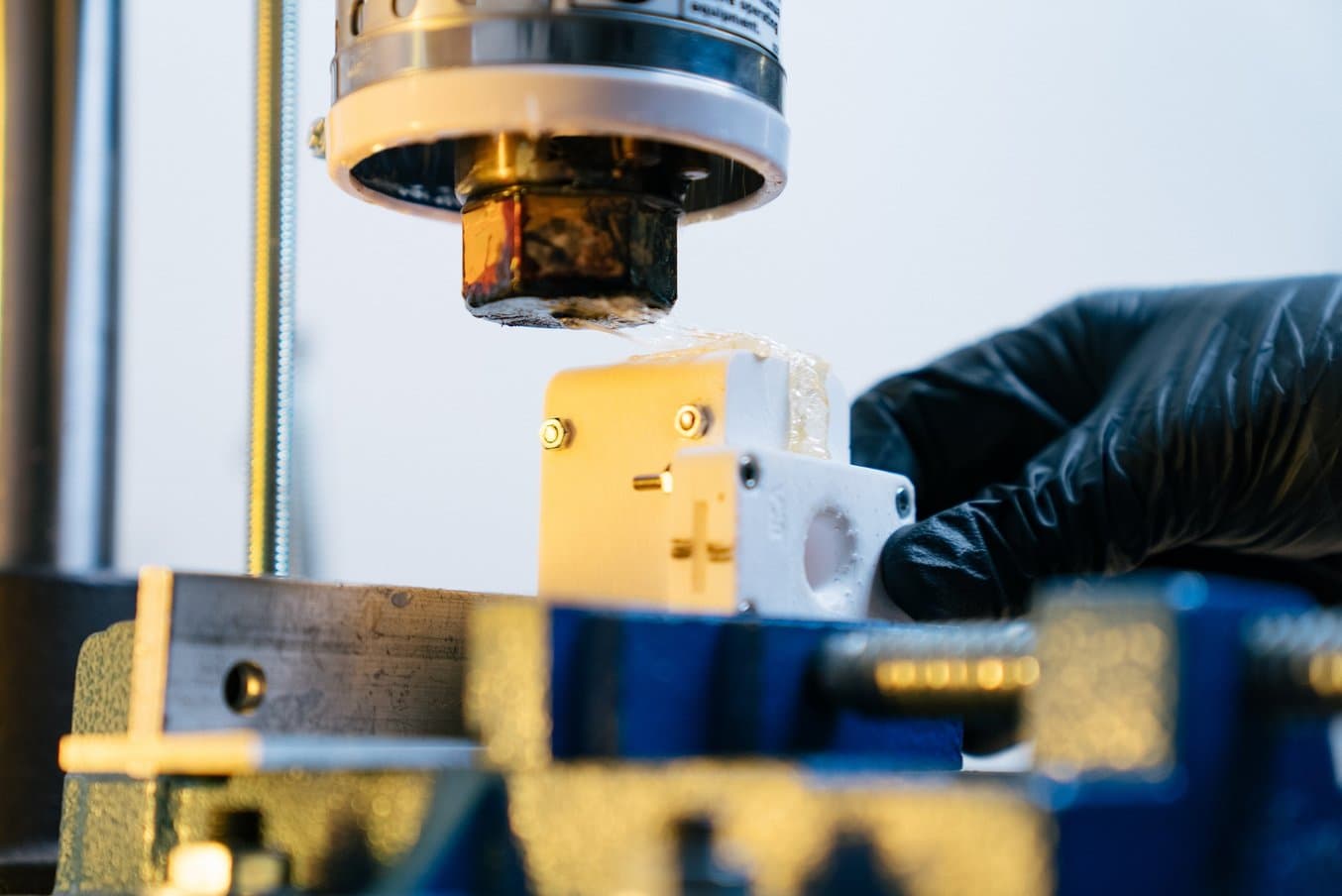
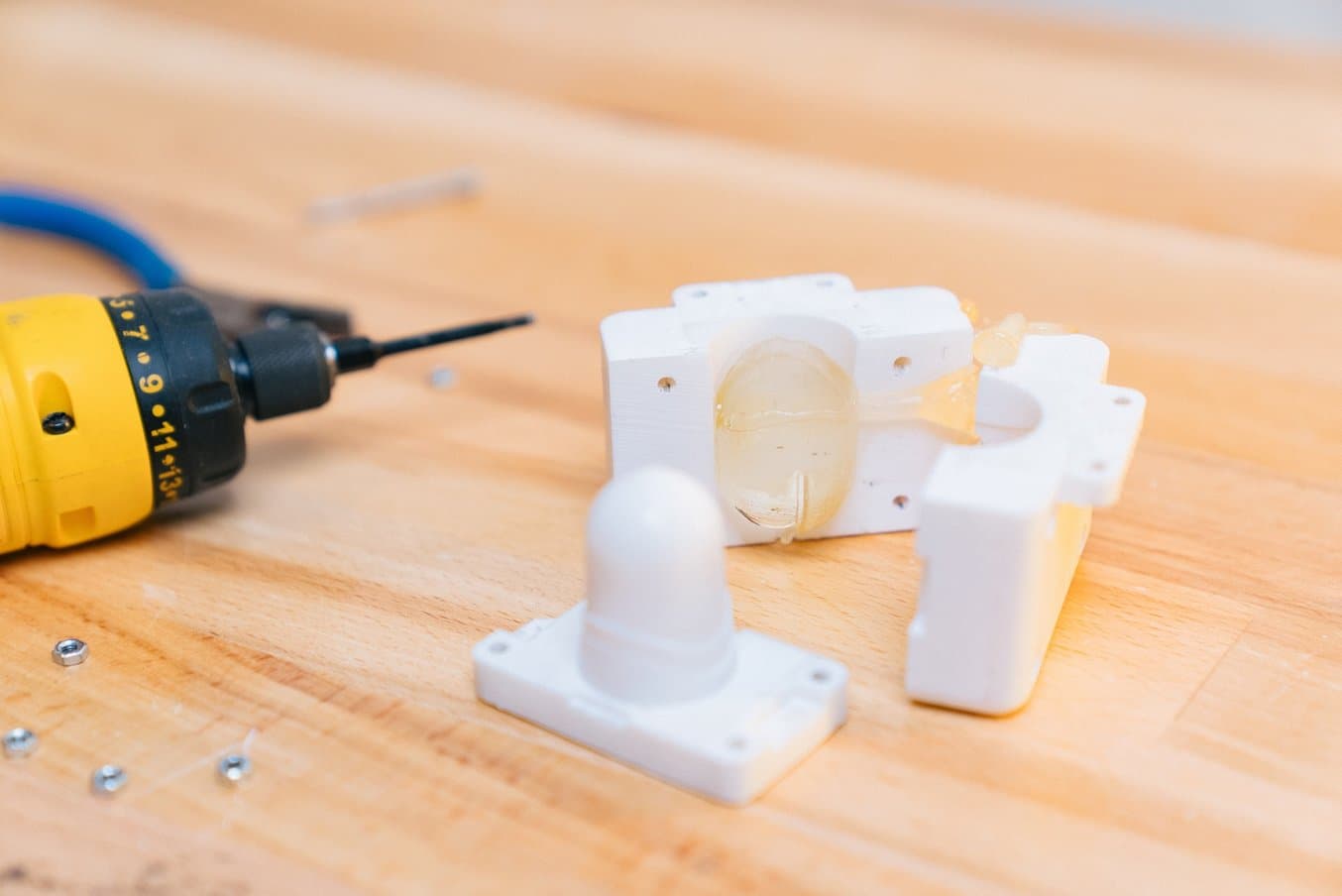
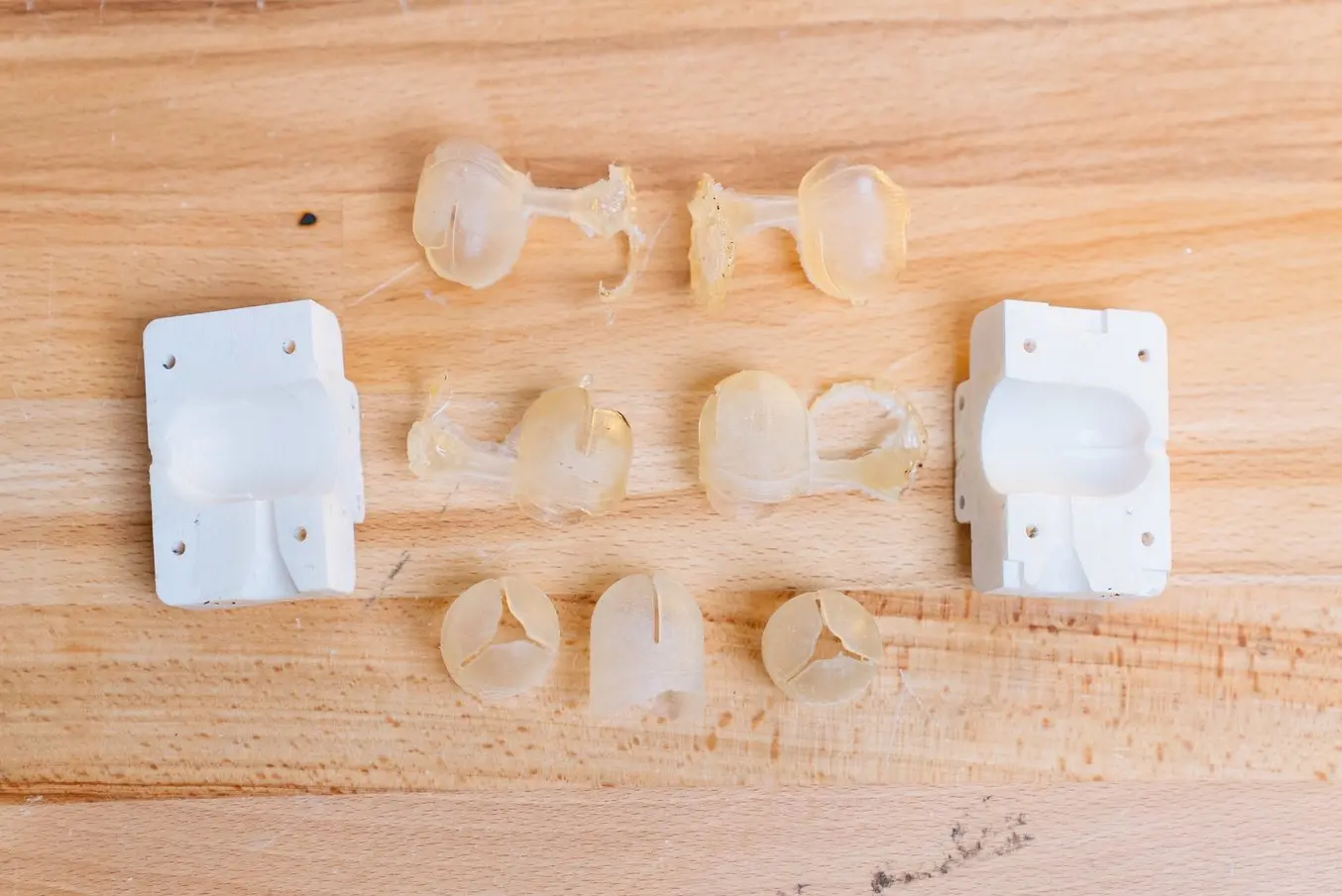
3D-gedruckte Spritzgussformen sind ein elementarer Teil von Glassboards Entwicklungsprozess.
Die Vorteile der Materialbibliothek bei der Produktentwicklung sind offensichtlich: Der Form 2 und der Form 3BL sind vielseitige Geräte, die mit Chapmans und Ettingers Fantasie wie auch den Ansprüchen ihrer Kunden Schritt halten können. Chapman erklärt: „Unsere anderen Werkzeuge sind alle spezialisierter und können nur eine Sache gut. Ihr aber habt für alle Zwecke das passende Kunstharz. Was für ein verrücktes Kunstharz werdet ihr euch als Nächstes ausdenken? Egal, was es ist, es wird großartig werden. Es wird für eine Branche oder einen Fachbereich geeignet sein, den wir bisher nicht erreichen konnten, oder für eine Art von Material, für das wir bisher keine Prototypen herstellen konnten, und es wird uns ermöglichen, wirklich tolle Sachen zu machen.“
Form 3BL und Produktentwicklung
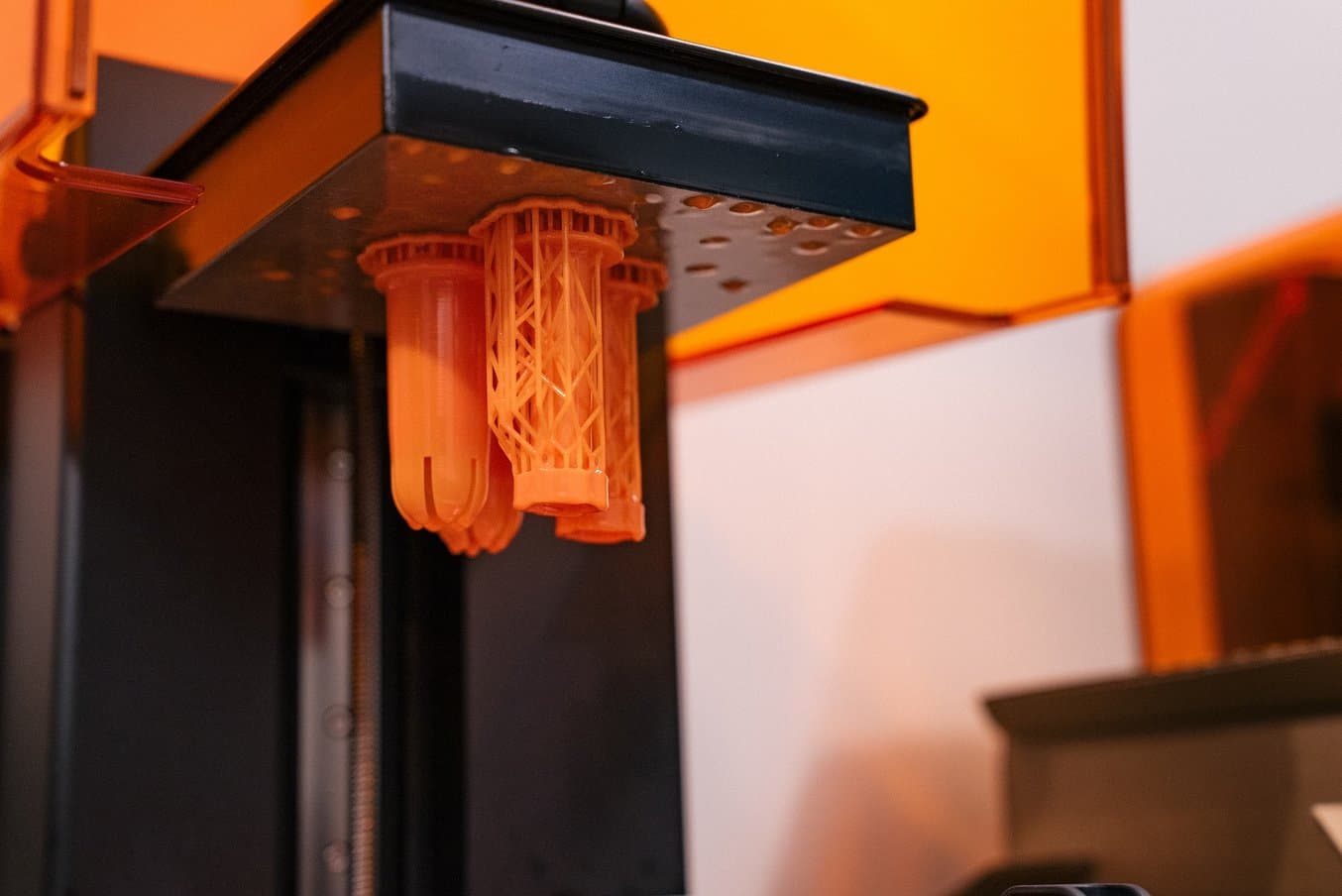
Glassboard setzt die Drucker Form 2 und Form 3BL ein.
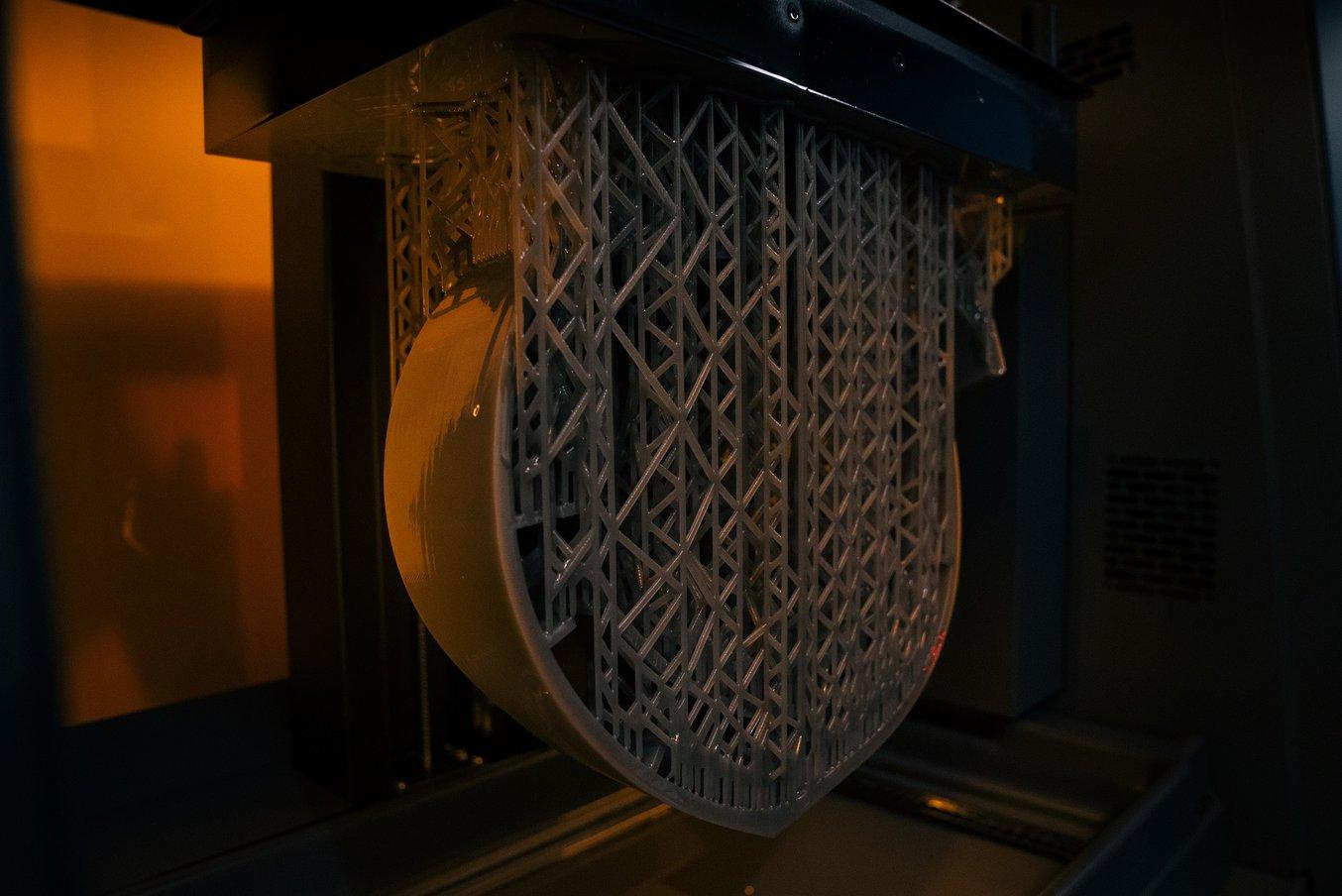
Dank seines frühen Erfolgs mit dem Vakuumformen hat das Team dessen Nutzung auf andere Projekte ausgeweitet. „Bei einem anderen Produkt haben wir viel mit Vakuumformen gearbeitet. Wir haben angefangen, auf dem Form 3BL aus Draft Resin Formwerkzeuge für das Vakuumformen von sehr großen Teilen zu drucken. Früher wären diese Formen in mehreren Abschnitten auf einem Form 2 gedruckt und dann zusammengefügt worden, was zusätzliche Druckzeit erfordert hätte. In der Vergangenheit haben Designer das Vakuumformen nur für die Produktion von Verpackungen, Badewannen oder Außenhüllen von Helmen in Betracht gezogen. Doch langsam lernen wir, dass man mit Vakuumformen auch viel komplexere Teile herstellen kann, wenn man bereit ist, kniffligere Werkzeuge oder Lüftungen zu entwerfen. Außerdem erlaubt es uns, bei der Prototypenentwicklung mit Thermoplasten in Produktionsqualität zu arbeiten ohne auf Spritzguss zurückgreifen zu müssen. Ich glaube, wir sind gerade erst dabei, diese Technologie zu erschließen, und es lohnt sich, im Auge zu behalten, was wir im nächsten Jahr damit hervorbringen werden.“
Grant Chapman
„Die Herstellung von Teilen mit Vakuumformen ist wirklich ein Vorgang von 24 Stunden; Formwerkzeuge werden über Nacht gedruckt, am Morgen gehärtet und bis zum Ende des Tages werden die Thermoplastplatten geformt und nachbearbeitet. Und dann hat man das fertige Teil in der Hand und kann es testen. Genau das ist für mich die Definition von Rapid Prototyping.“
Ein unerwarteter Anwendungsfall für den Form 3BL war die Nutzung der größeren Konstruktionsplattform für den Druck einer Vielzahl kleiner Teile zugleich. Ursprünglich hatte das Team erwartet, den Drucker vorwiegend zur großformatigen Prototypenfertigung für Teile und große Formen zu verwenden, doch wie uns Chapman erklärte, begann das Team aufgrund der hochwertigen Präzision der Low Force Stereolithography, den Form 3BL in einigen Fällen als Ersatz für den Form 2 einzusetzen. „Ein Kunde, für den wir auch zweiteilige Urethanformen herstellen, brauchte über Nacht einige Prototypen eines kleinen flexiblen Teils. Statt dieselbe Form zu verwenden, sie zu säubern und neu zu befüllen, haben wir letztendlich einfach über Nacht 30 Formen auf dem Form 3BL gedruckt und waren in der Lage, sie alle zusammenzusetzen, am nächsten Tag zu befüllen und alles auszuliefern. Und das hat drei oder vier Drucke auf dem Form 2 auf einen einzigen Druck über Nacht auf dem Form 3BL reduziert“, so Chapman.
Er fügte hinzu: „Wir sind vom 3BL bisher mehr als beeindruckt, und die Softwareänderungen, die wir selbst in den letzten fünf Monaten schon beobachtet haben, die Einführung der neuen Stützstruktureinstellungen der Kunstharze von der Beta-Version zur Veröffentlichung, haben einen Unterschied wie Tag und Nacht ausgemacht. Es ist einfach eine tolle Verbesserung der Lebensqualität bei der Entfernung von Stützstrukturen, und das in einer so kurzen Entwicklungszeit. Ich bin mit dieser Produktreihe also sehr zufrieden.“
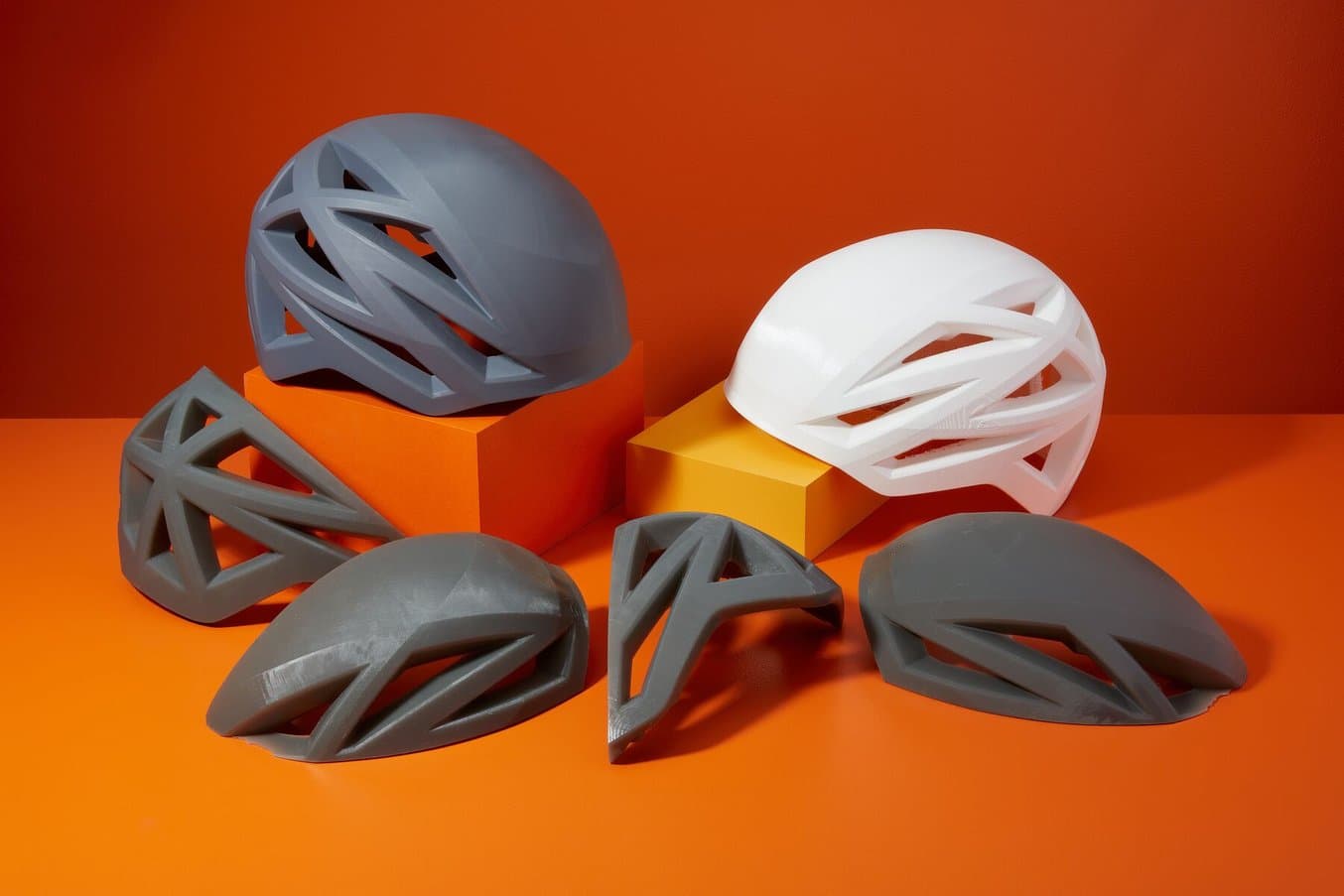
Großformatiger Druck macht den Unterschied
In diesem kostenlosen Bericht vergleichen wir betriebsinternen großformatigen 3D-Druck mit dem Form 3L mit anderen Produktionsmethoden, vor allem mit Outsourcing und der Verwendung von FDM-Druckern. Außerdem stellen wir die Kosten der verschiedenen Verfahren einander gegenüber und erörtern, wann die Anschaffung eines betriebsinternen Form 3L sich anbietet.
Betriebsinternes Thermoformen mit Erfolg
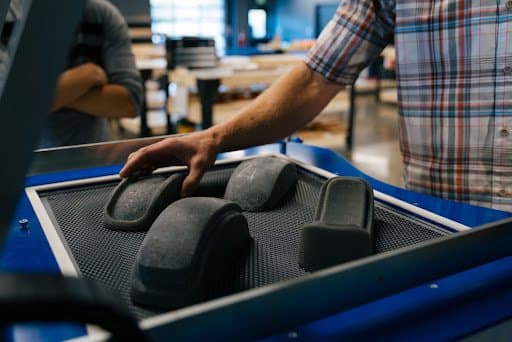
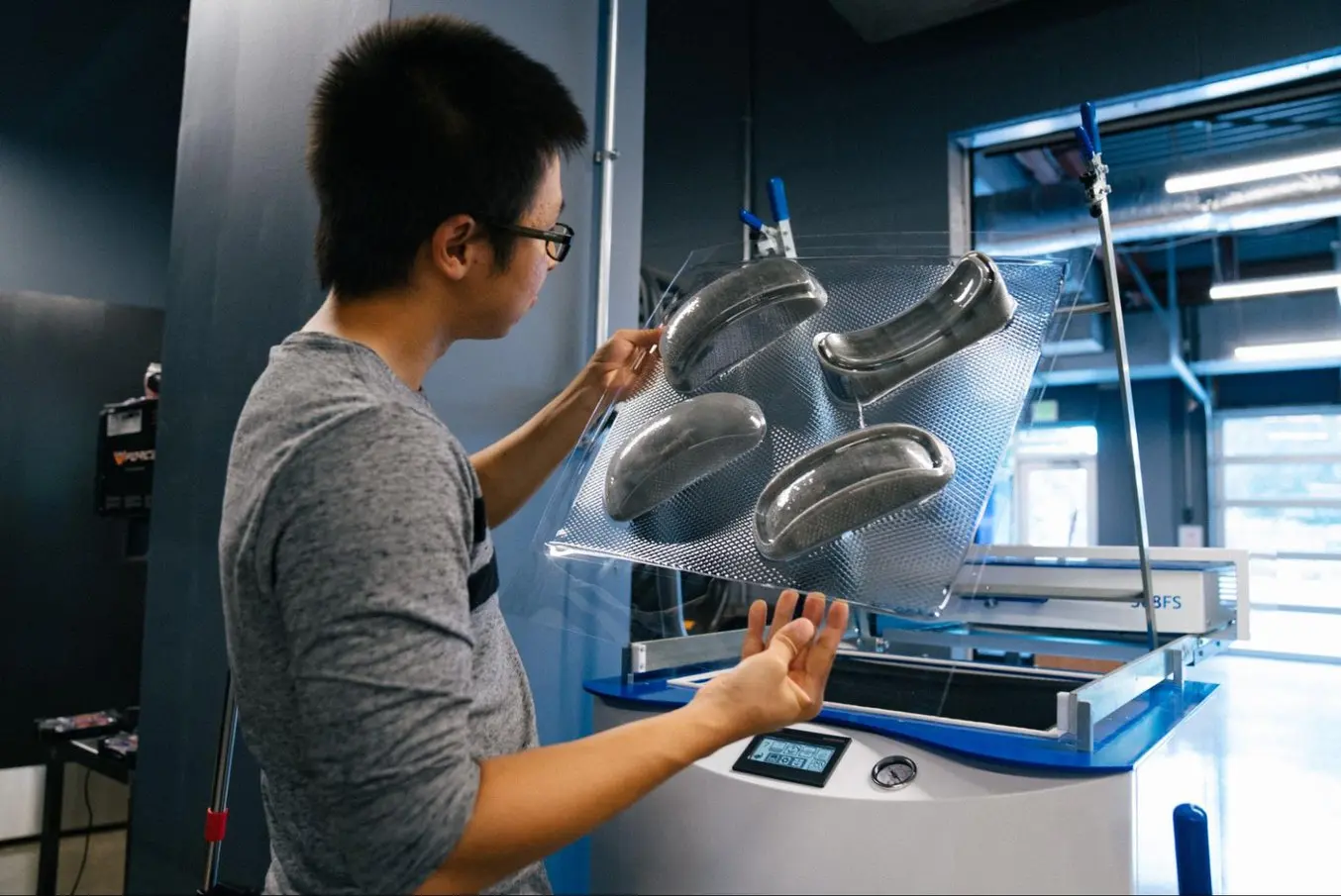
Glassboard berichtete uns von zwei weiteren Projekten, die deutlich machen, wie der Designprozess durch den 3D-Druck verbessert wurde: eine Prüftablette und ein Helm. Das Team produzierte hohle Formen mit Querstreben im Inneren zur Steigerung der Festigkeit und zur Reduktion des Bruchrisikos des Formwerkzeugs beim Vakuumformen. Für das Vakuumformverfahren weisen die Oberflächen der Formen kleine Luftlöcher von 1,5 mm Durchmesser auf. Bei der Prüftablette handelt es sich um eine einfache Geometrie mit einer Wanddicke zwischen 0,5 mm und 0,8 mm und Entformungsschrägen von mindestens zwei Grad. Der Helm hat eine Wanddicke von 4 mm und beinhaltet anspruchsvollere Merkmale, insbesondere Hinterschneidungen. Die Form wurde mehrteilig entworfen, damit sie vom thermogeformten Produkt getrennt werden kann.
Die Formwerkzeuge wurden über Nacht auf dem Form 3L bei 200 Mikrometern Schichtdicke aus Formlabs' Draft Resin gedruckt. Aufgrund der Größe des Helms wählte das Team Draft Resin als Material, um die Iterationen zu beschleunigen, da es die höchste Druckgeschwindigkeit aller Formlabs-Kunstharze hat. Nach dem Entfernen der Stützstrukturen waren etwa 20 Minuten Schleifen und Glätten erforderlich, um die Teile fertigzustellen. Eine Politur oder der Einsatz von Formentrennmittel waren nicht nötig. Kleinere Teile druckt Glassboard gewöhnlich aus Grey Resin, um ein Verziehen insbesondere von Teilen mit langen dünnen Abschnitten zu vermeiden.
Das Team stellte 15 Prüftabletten und zwei Helme her. Das Umformen der Platten im Vakuumformgerät verlief ohne Schwierigkeiten: Die Platten schmolzen oder verformten sich nicht und es entstanden keine Risse oder Verbrennungen an den Formwerkzeugen. Es wurden keine Ausfalltests mit den Formen durchgeführt, doch Glassboard geht davon aus, dass sie bei Einhaltung der Abkühlzeit von 8–10 Minuten noch vielen weiteren Zyklen standhalten würden. Durch die Nutzung eines 3D-Druckmaterials mit höheren thermischen Eigenschaften, wie etwa Rigid 10K Resin, ließe sich die Abkühlzeit auf zwei bis drei Minuten verkürzen.
Zuvor hatte das Team die Werkzeugbestückung ausgelagert. Durch den betriebsinternen 3D-Druck mit Formlabs-Druckern reduzierte es die Kosten auf einen Bruchteil und verkürzte die Durchlaufzeit von Wochen auf Tage.
WERKZEUG VIA OUTSOURCING | WERKZEUG VIA BETRIEBSINTERNEM 3D-DRUCK | |
---|---|---|
Erforderliche Ausrüstung | PC-Platten für das Thermoformen | PC-Platten für das Thermoformen, Form 3L, Draft Resin |
Zeitaufwand für den Formenbau | Zwei bis vier Wochen | Ein Tag |
Kosten des Formenbaus | 5000–10 000 USD | > 400 USD |
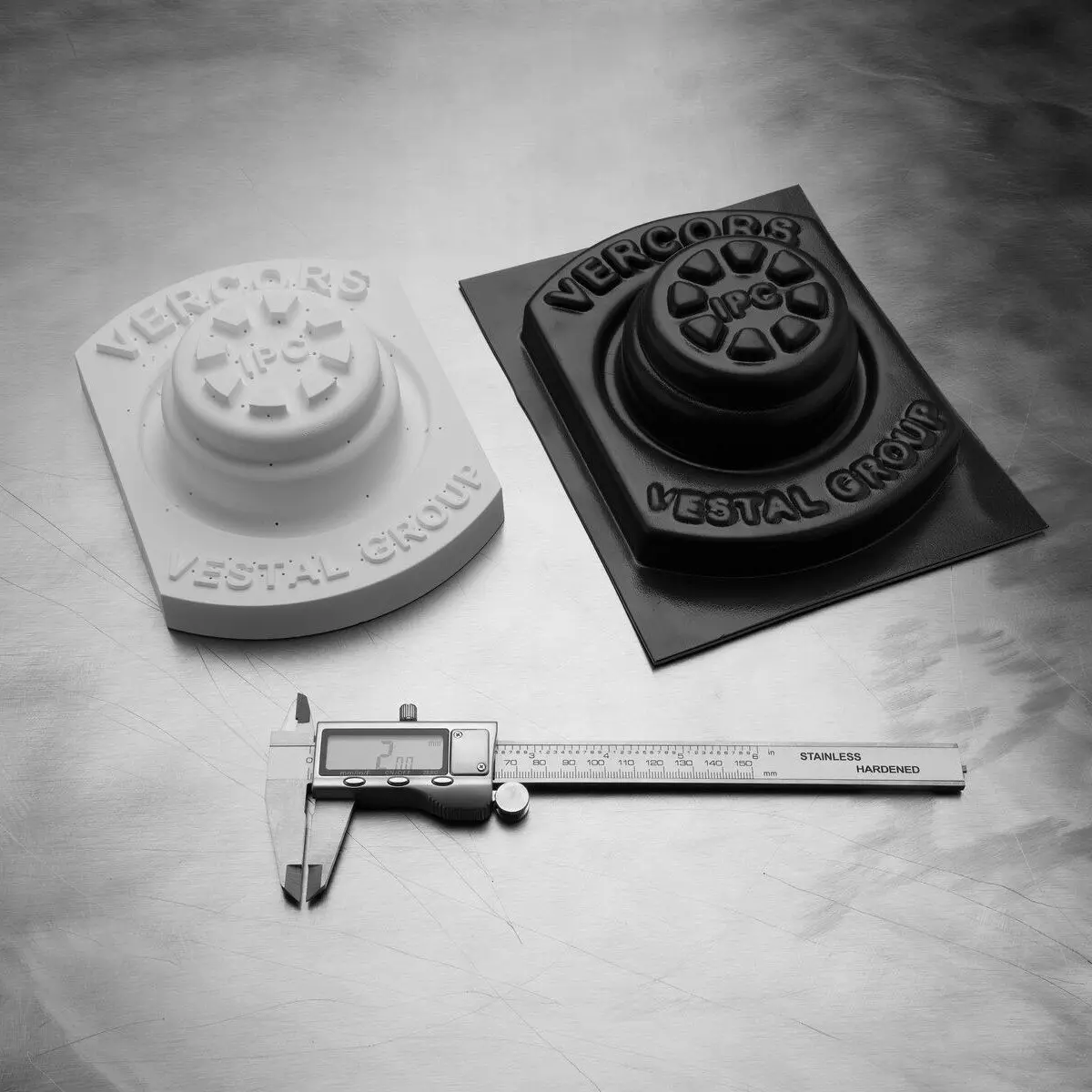
Schnelles Thermoformen in Kleinserie mit 3D-gedruckten Formwerkzeugen
Laden Sie unser Whitepaper herunter und erfahren Sie mehr über die schnelle Erstellung komplexer Formwerkzeuge mittels 3D-Druck. Wir geben außerdem Tipps und Richtlinien zur Vorbereitung der Bestandteile der Form.
Biokompatible Materialien von Formlabs für die Produktentwicklung
Grant Chapman
„Zugang zu Materialien zu haben, die man den Menschen guten Gewissens auch für Hautkontakt bereitstellt, das ändert grundlegend die Ausgangslage für das Erstellen von Prototypen, die zum Testen angefasst und gefühlt werden müssen.“
Dental LT Clear Resin (V2) ist nicht nur für die Prototypenherstellung von biokompatiblen Teilen hervorragend geeignet, sondern auch für den Formenbau, und das Team verwendet seinen Form 3BL auch für die Herstellung großformatiger Formen. Chapman erzählte uns: „Das Herausragende an Dental LT Clear Resin (V2) ist, dass es für Schleimhäute sicher ist, sodass wir es ohne große Bedenken in einer Anwendung nutzen können, wo der Endkunde möglicherweise Hautkontakt braucht, wie etwa bei platingehärteten Silikonformen oder direkt 3D-gedruckten Teilen. Ein anderer Vorteil von Dental LT ist, dass es einfach sehr genau druckt und das Entfernen der Stützstrukturen überaus einfach ist. Das ist bei diesem Material ein weiterer Bonus.“
Auch das Erstellen transparenter Formen mit Dental LT Clear Resin (V2) war ein Pluspunkt, fügte Chapman hinzu: „Es ist außerdem noch transparent. Wenn wir Formen befüllen, sehen wir, ob unbeabsichtigt Luftblasen oder Lücken entstehen, und können sie herausziehen oder absaugen.“

Kostenlosen Probedruck anfordern
BioMed Clear Resin ist ein hartes, starkes Material für biokompatible Anwendungen, bei denen es über längere Zeit zum Kontakt mit Haut oder Schleimhäuten kommt. Sehen und fühlen Sie selbst die Qualität von Formlabs. Wir senden Ihnen einen kostenlosen Probedruck an Ihren Arbeitsplatz.
ei vielen Verbraucherprodukten versuchen die Designer nicht, das Rad neu zu erfinden und technische Probleme zu lösen. Im Fall von Sunny existiert das Produkt schon von Vornherein. Die Frage ist, wie sich verglichen mit existierenden Apparaten ein besseres Kundenerlebnis erreichen lässt, und genau da können Iterationen von kleinen Merkmalen bei einem neuen Produkt über Erfolg oder Misserfolg entscheiden.
„Das ist es, was sie so wertschätzen: der Ablauf von ihrem Feedback zu Designiterationen und Updates bis hin zu neuen Prototypen, die sie wiederum testen können, um die Feedbackschleife weiter aufrechtzuerhalten. Ich glaube, das ist wahrscheinlich der zufriedenstellendste Teil des ganzen Prozesses gewesen“, erklärt Ettinger.
Auf Zuverlässigkeit kommt es an
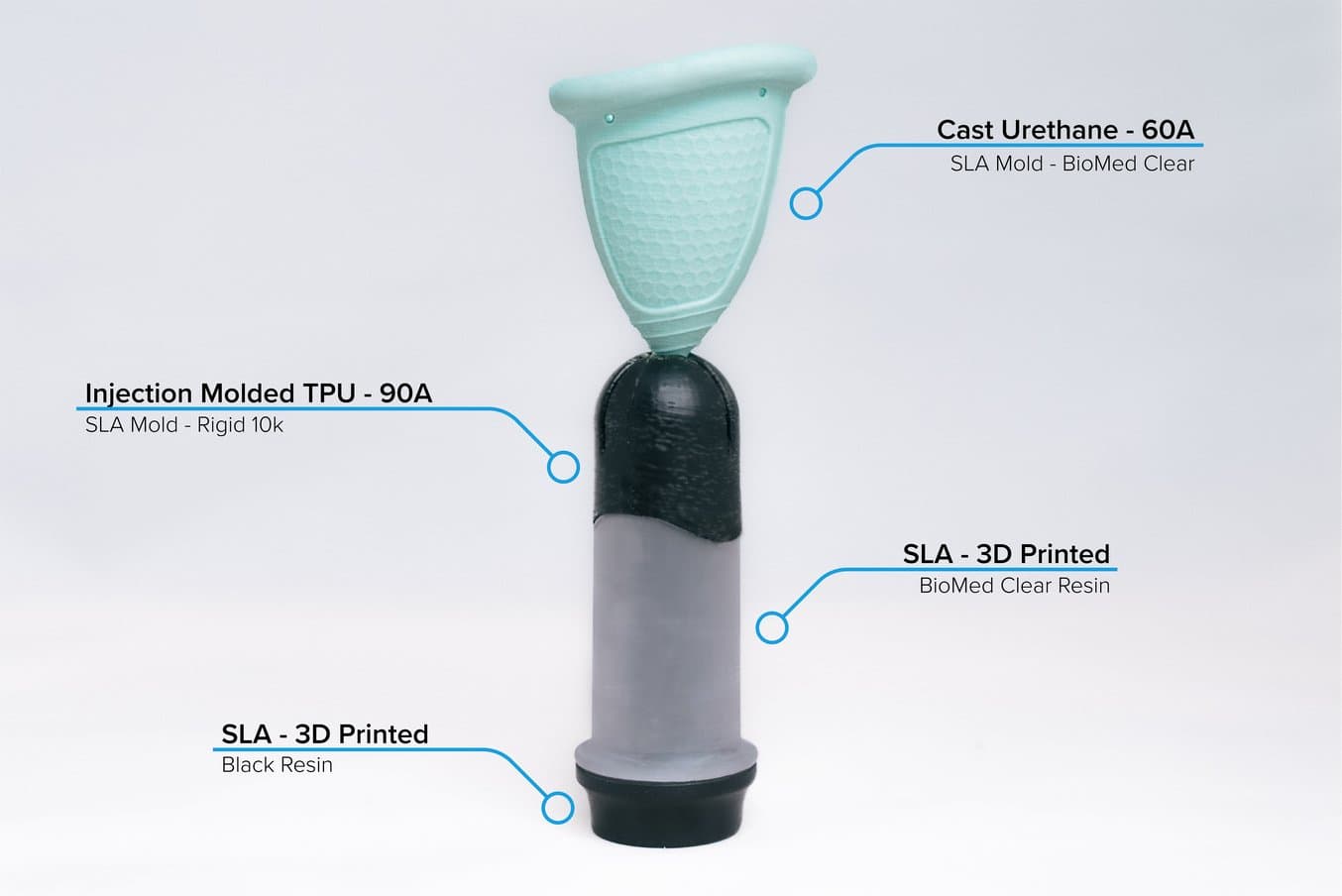
Die verschiedenen Teile für die Entwicklung des Applikators und der Tasse für Sunny.
Was für Herausforderungen sich auch stellen, das Team von Glassboard macht keine Ausflüchte, und deshalb braucht es ein Werkzeug, das mit ihm mithalten kann. Zuverlässigkeit ist für den Erfolg und schnelle Durchsätze im Sunny-Projekt unabdingbar. Da dutzende Prototypen gedruckt werden mussten, hätten fehlgeschlagene Drucke das Projekt zurücksetzen können.
„Zuverlässigkeit ist ein immens wichtiger Punkt“, erläutert Chapman. „Und es geht hier nicht um die zwei Stunden, die eine Reparatur dauern würde, wenn ein Drucker kaputt ginge, sondern dass uns, wenn ein Drucker über Nacht kaputtgehen würde, das Teil fehlen würde, das an dem Tag an den Kunden versendet werden sollte, um dessen Frist einzuhalten. Und genau darum ist Zuverlässigkeit wirklich essenziell. Es geht nicht um die ausgefallene Zeit. Es geht um die verfehlte Chance eines Drucks, den man einem Kunden versprochen hat und auf dessen Fertigstellung man zählt. Wenn ein Drucker versagt oder einen Defekt hat, dann verpasst man eine Frist, und genau deshalb ist Zuverlässigkeit so wichtig.“
Letztendlich hat das Team für den Applikator und die Tasse von Sunny insgesamt mehr als 100 Prototypen hergestellt. Weil das Produkt mit Haut in Kontakt kommt, noch dazu in einem so empfindlichen Bereich, war dem Team klar, dass sich das Design nicht in bloß ein paar Drucken perfektionieren lassen würde. Das Produkt muss gut aussehen, gut sitzen und für eine Vielzahl von Körpern funktionieren. Deswegen seien schnelle Iterationen laut Chapman so wichtig: „Bei fast all unseren betriebsintern entwickelten Produkten ist unser Ziel, Prototypen so schnell und so einfach wie möglich herzustellen. Und das geht in die Frage über, wie wir das Produkt in einem Zustand testen können, der dem Produktionszustand so nah wie möglich kommt, noch bevor der Kunde die Werkzeugbestückung beginnen muss und bevor wir mit dem Hersteller in Verbindung treten müssen. Wie lässt sich also im Prototypenstadium so viel wie möglich testen?“
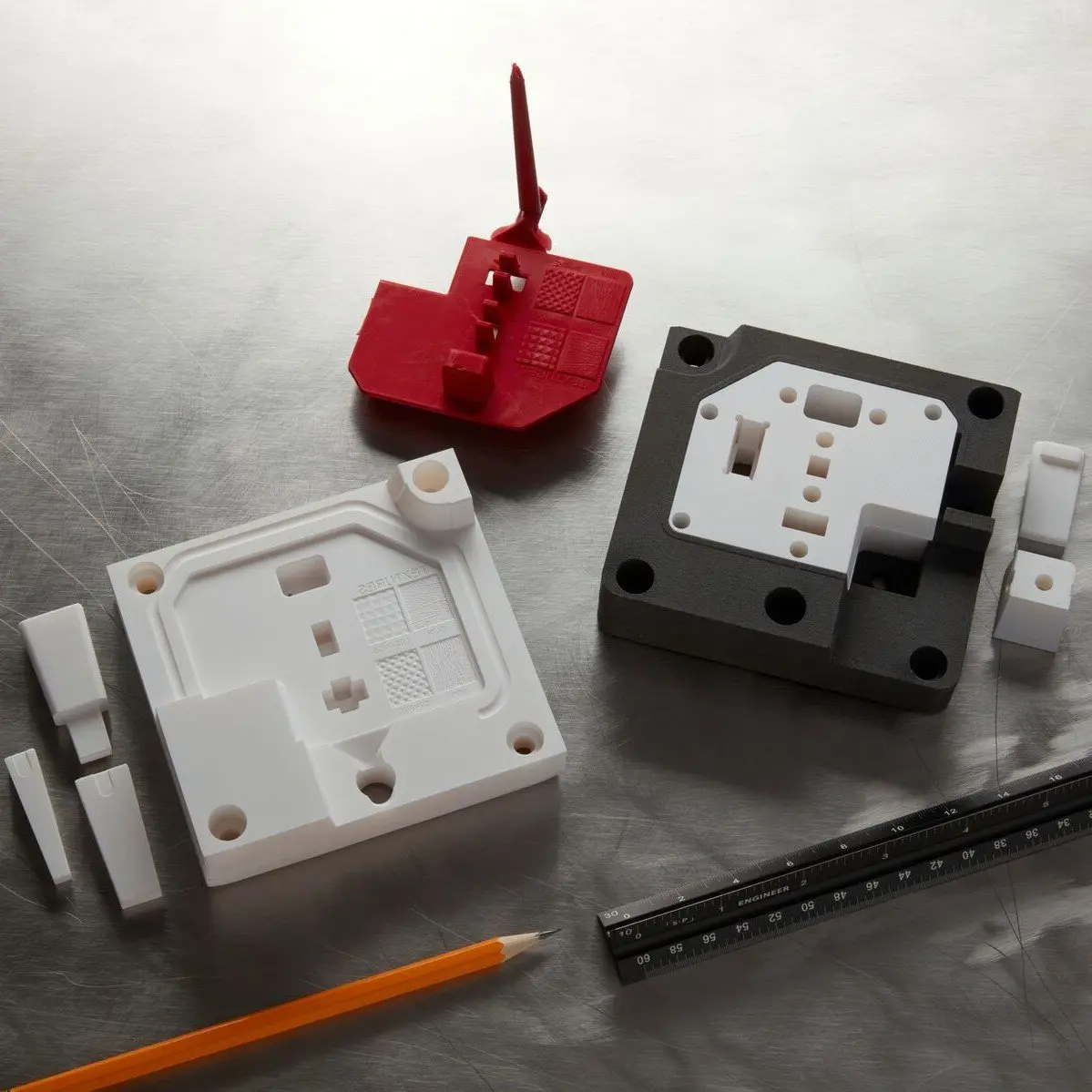
Leitfaden zum Rapid Tooling
In diesem Whitepaper sprechen wir über die Kombination von Rapid Tooling mit traditionellen Herstellungsverfahren wie Spritzguss, Vakuumformen oder anderen Gießverfahren, um die Flexibilität, Agilität, Skalierbarkeit und Kosteneffizienz zu steigern.
Erfahren Sie mehr über 3D-Druck für das Produktdesign

Seine Ansichten zur Nutzung von 3D-Druck fasste Chapman so zusammen: „Das ist ein Werkzeug, von dem ich wünschte, ich hätte es schon vor Jahren zu nutzen gelernt, denn jetzt ist es eines unser Standardhilfsmittel.“ Aufgrund ihrer Vielseitigkeit und Verlässlichkeit wird Glassboard den Form 2 und den Form 3BL in Zukunft vermutlich in jedem Projekt einsetzen.
Um mehr über Glassboard zu erfahren und die zukünftigen Projekte des Unternehmens zu verfolgen, besuchen Sie die Website des Unternehmens.
Um zu erfahren, wie großformatiger 3D-Druck auch für Ihre Produkte eingesetzt werden kann, besuchen Sie unsere Seite über den Form 3L. Oder fordern Sie über den untenstehenden Link einen kostenlosen Probedruck an, gedruckt auf dem Form 3L.