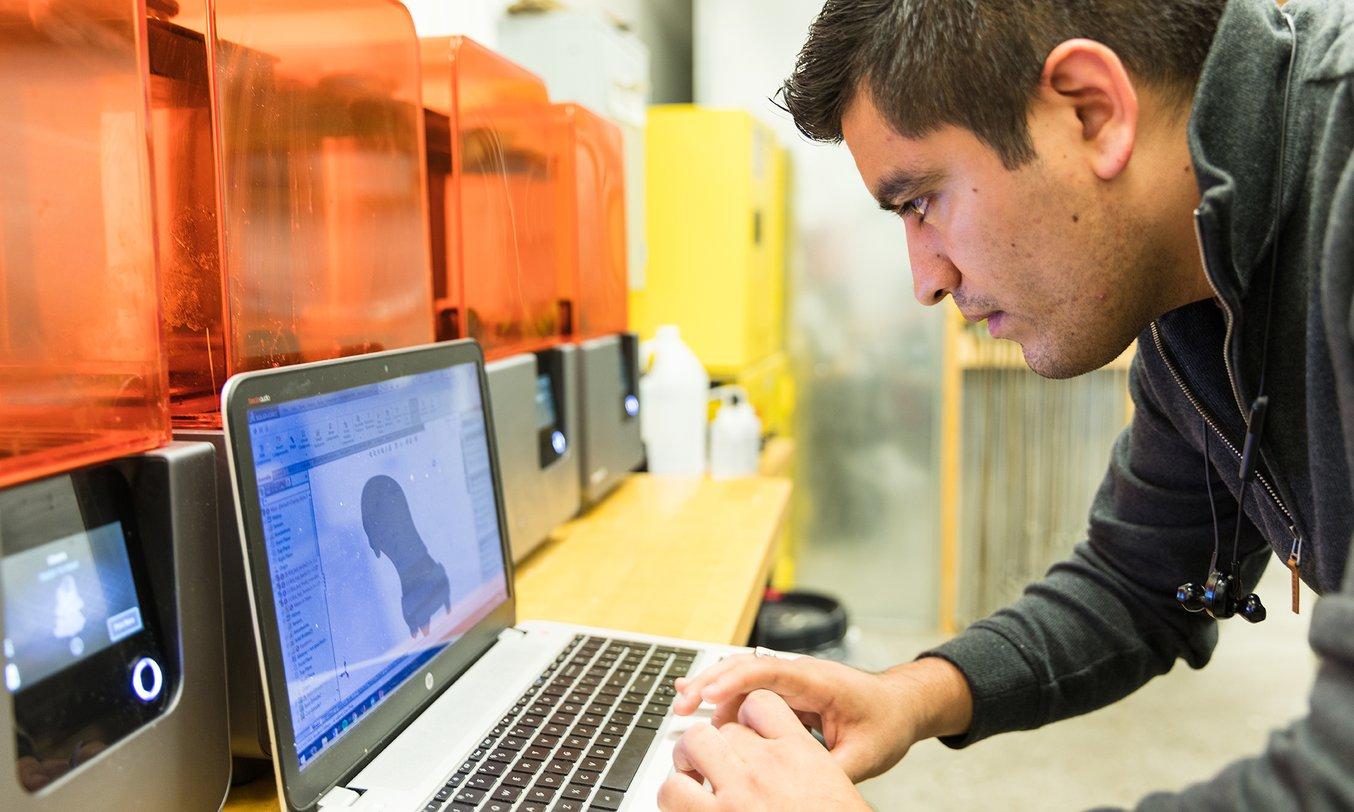
Richard Huizar hat immer schon gerne Dinge gebaut. Daher studiert er Maschinenbau und strebt eine Berufslaufbahn im Produktdesign an.
Im Seminar „Design Studio: Objects and Interaction“ am Massachusetts Institute of Technology (MIT) eignet sich Huizar die Fertigkeiten an, die er zur Umsetzung seines Berufsziels benötigt. Das Seminar befasst sich sowohl mit den Grundlagen des Designs als auch mit fortgeschrittenen Prototyping-Technologien, um Studierende dazu anzuregen, über den Tellerrand ihrer Fachbereiche hinauszuschauen.
Ausbildung zukünftiger Designer
PDas Seminar „Design Objects and Interaction“ ist Teil des Studiengangs Design als Nebenfach und soll die Studierenden dazu anregen, sich ganzheitlich mit dem Thema Design zu befassen. Der Lehrplan beinhaltet moderne Technologie und Tools, die den Studierenden nicht nur bei der Umsetzung ihrer Konzepte helfen, sondern sie auch befähigen und inspirieren sollen, Designs zu erstellen, die zuvor nicht möglich gewesen wären.
Für die Prüfung und den Bau ihrer Designs machen die MIT-Studierenden von fortschrittlicher Prototyping-Technik Gebrauch. Dazu gehörte auch eine Serie von Form 2-Stereolithographie-3D-Druckern. Hier erfahren Sie Näheres zum Thema 3D-Druck im Bildungsbereich.
„Wir müssen darüber nachdenken, wie Design in 30 Jahren aussehen wird“, so Marcelo Coelho. Er unterrichtet das Seminar gemeinsam mit Jessica Rosenkrantz, Mitbegründerin von und Creative Director bei Nervous System. “Wir bilden die Designer der Zukunft aus.”
Die 25 Teilnehmerinnen und Teilnehmer am Seminar „Design Objects and Interaction“ verwendeten:
- 4 Form 2 3D-Drucker
- 2 Finish Kits
- 4 l Transparentes Kunstharz
- 2 l Flexibles Kunstharz
Im Spannungsfeld von Technologie und Design Thinking
Die Studierenden erhielten einen Überblick über die Grundkompetenzen, die von modernen Designern erwartet werden, sowie die Aufgabe, ein Textil und Wearable zu entwickeln, das nur über 3D-Druck realisierbar ist.
Lucia Liu, MIT-Studierende im 3. Jahr mit Hauptfach Maschinenbau, ließ sich von natürlichen Zellstrukturen inspirieren und codierte einen Algorithmus für ein zellförmiges Textilmuster.

„Der 3D-Druck ermöglichte es mir, Design auf eine andere Art anzugehen,“ so Liu. „Die Fähigkeit der 3D-Drucker, organische Strukturen genauso problemlos zu erstellen wie geometrische Formen, hat mich wirklich inspiriert. Mein Ziel war es, ein 3D-gedrucktes Wearable zu entwickeln, das zeigt, wie sich mit verschiedenen Zellformen verschiedene Funktionen erfüllen lassen.”
Liu erstellte mit dem Form 2 Iterationen von Prototypen kleiner Gelenkmechanismen in ihrem Textil. Diese sollten unter Berücksichtigung der Mindesttoleranzen und -abstände des Form 2 so klein wie möglich ausfallen. Sie druckte das ganze Textil als ein einziges, vorkonfiguriertes Teil.


In Huizars Projekt spiegelt sich seine Fußballbegeisterung wider. Sein Ziel war es, maßgefertigte Stollen zu entwickeln, deren Zapfen an der Unterseite je nach dem Laufstil und den Techniken des Fußballspielers ausgetauscht werden können.
Nach seinen ersten Erfahrungen mit CAD war sich Huizar nicht sicher, wie gut sich sein Design in ein endgültiges Produkt umsetzen lassen würde.
„Wenn man das Design nur auf dem Bildschirm sieht, erhält man keinen Eindruck davon, wie gut es letztendlich am Fuß sitzen wird,“ so Huizar. „Nach dem Druck konnte ich das besser beurteilen und die Größe, Steifigkeit und Dicke anpassen. Das ist mit CAD allein nicht möglich. Man braucht einfach etwas Greifbares.“
Coelho erläuterte, dass eine der größten Herausforderungen im Seminar genau dieser Prozess war: ein CAD-Design für einen funktionalen physischen Gegenstand zu entwickeln.
„Viele Studierende erstellen ein Modell, ohne wirklich eine Vorstellung davon zu haben, wie es in der Realität aussehen wird, wie es sich biegen lässt, wie die Einzelkomponenten zusammenpassen,“ meint Coelho. „Durch den 3D-Druck des Modells erhalten die Studierenden die Möglichkeit, pragmatische Lösungen zu erarbeiten. Es ist gewissermaßen ein Realitätscheck.“

Rapid Prototyping im Klassenzimmer
Huizar und Liu hatten beide bereits in früheren Seminaren Zugang zu 3D-Druckern gehabt. Mit Desktop-3D-Druckern, die mit Stereolithographie-Technologie (SLA) arbeiten, hatten sie jedoch noch keine praktischen Erfahrungen gesammelt.
Liu hatte zuvor mit einem Kommilitonen zusammengearbeitet, der ihre Designs für sie auf einem 3D-Drucker druckte.
„Die Technologie war für mich zunächst ein wenig beängstigend, weil ich sie nicht selbst angewandt habe,“ berichtete Liu. „Mittlerweile habe ich mich mit dem Verfahren vertraut gemacht und praktische Erfahrungen gesammelt, und ich finde ich es sehr anwenderfreundlich.“

Huizar druckte den Großteil seiner Stollen mit dem transparenten Kunstharz von Formlabs. Die Komponenten, die eine gewisse Elastizität erforderten, druckte er mit dem flexiblen Kunstharz. Sein Schuhdesign setzte sich aus drei Schichten zusammen: einer oberen Schicht, die fest bleibt und an dem weichen Material des jeweiligen Schuhs befestigt wird, eine zweite Schicht mit beweglichen Teilen (den Gelenken) und eine untere Schicht, die die flexiblen Teile miteinander verbindet und einkeilt, so dass aus allem ein Teil wird.

Fordern Sie einen kostenlosen Probedruck der Kunstharze von Formlabs an.
„Dank der Präzision des Form 2 konnte ich Teile anfertigen, die perfekt zusammenpassen,“ erklärt Huizar. „Ich wusste, dass ich auf dieser Grundlage im Spanungs- oder Spritzgussverfahren Teile mit Präzisionswerten anfertigen konnte, die mit denen der 3D-gedruckten Modelle sehr vergleichbar waren.“

3D-Druckermanagement mit Dashboard
Eine erfolgreiche Einbindung anspruchsvoller Technologie in Unterrichts- und Laboranwendungen setzt voraus, dass sich die Geräte leicht verwalten lassen. Mit Dashboard von Formlabs können Anwender und Administratoren mehrere Drucker und Verbrauchsmaterialien überwachen.
Dashboard ist ein cloudbasiertes Tool zur Optimierung der Gerätenutzung.Dashboard verfolgt den Druckvorgang, sendet eine Benachrichtigung, wenn ein Druck fertiggestellt ist, stellt die Druckhistorie eines Teams zusammen und überwacht den Materialverbrauch, um eine zeitnahe Nachbestellung zu gewährleisten.
„Das Dashboard ist enorm hilfreich,“ so Coelho. „Die Studierenden sehen, welche Geräte in Betrieb sind, was gerade passiert und wann sie als nächstes drucken können. Es vereinfacht die Verwaltung der Geräte erheblich.“

Vorbereitung auf die Zukunft
Huizar und Liu sind sich einig, dass ihnen der Zugang zur 3D-Drucktechnik und anderen fortschrittlichen Technologien auf ihrem Weg zum beruflichen Erfolg helfen wird.
„Wir sollten in Bezug auf Technologie, die für unsere zukünftige berufliche Entwicklung sehr nützlich sein kann, keine Berührungsängste haben,“ meint Liu. „Die Möglichkeit, mich mit neuen Technologien vertraut zu machen, hat mir Gebiete und Anwendungen eröffnet, die ich früher nicht in Erwägung gezogen hatte.“
„Hochschulen sollen Studierende auf die Zukunft vorbereiten, nicht nur in Bezug auf das, was Technologien heute möglich machen, sondern welche Potenziale sie auf lange Sicht eröffnen,“ meint Huzier.
„Man kann einen Maschinenbauabschluss machen und über die aktuellen und früheren Fertigungsmethoden Bescheid wissen und diese ein Stück weit verbessern, was auf jeden Fall eine gute Sache ist, aber umwälzendere Veränderungen sind nur möglich, wenn man diese alten Muster hinter sich lässt und nach neuen Fertigungsmethoden oder Vorgehensweisen sucht. Das ist aber nur möglich, wenn man Zugang zu diesen Technologien hat.“
Webinar: Vorteile des 3D-Drucks im Unterricht
Möchten Sie mehr darüber erfahren, wie der 3D-Druck den Bildungssektor verändert und wie Sie selbst einsteigen können? Schauen Sie sich das Video unseres Webinars an to learn how educators at universities and colleges around the country benefit from access to 3D printing technology.

Wenn Sie mehr über den 3D-Druck erfahren und sich ein Bild von den Möglichkeiten eines 3D-Druckers von Formlabs machen möchten, fordern Sie einen kostenlosen Probedruck an.