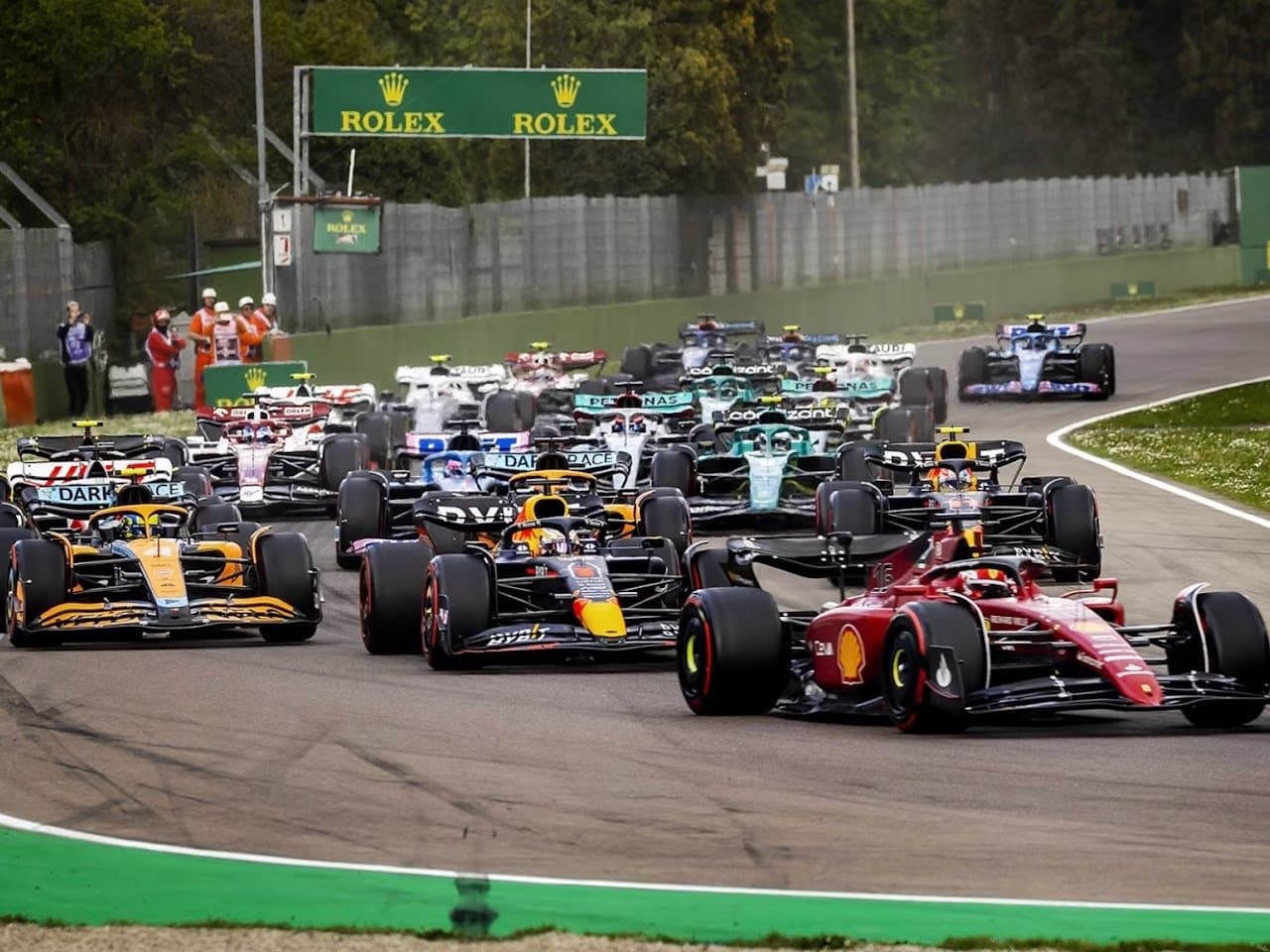
Foto mit freundlicher Genehmigung von Formula1.com
Angesichts der enormen Aufmerksamkeit, die spektakuläre internationale Autorennen wie die Formel 1 auf sich ziehen, herrscht ein ständiger Druck, die Rennwagen noch schneller und leistungsstärker zu machen. Schon jetzt beschäftigen die Formel-1-Teams einige der talentiertesten Fachleute für Maschinenbau, doch manchmal beanspruchen selbst diese die Hilfe externer Spezialisten, um noch ein paar PS mehr dazuzugewinnen.
Einer dieser Spezialisten ist Mackart Additive, ein Subunternehmen für Maschinenbau und Fertigung mit Sitz in Staffordshire im Herzen Englands. Dank seinen mehr als zwei Jahrzehnten Erfahrung in der Konstruktionstechnik und additiven Fertigung hat Mackart seine Kapazitäten im 3D-Druck über die traditionelle Domäne des Rapid Prototyping hinaus ausgedehnt. Derzeit stammen etwa 80 % von Mackarts Aufträgen von F1-Teams – denn diese Kunden streben ständig danach, die Leichtigkeit, Leistung, Zuverlässigkeit und Aerodynamik ihrer Fahrzeuge weiter zu steigern. Das Team von Steven McCarthy ist ein Meister im 3D-Druck komplexer Werkzeuge für Bauteile aus kohlenstofffaserverstärktem Kunststoff (CFK), die neue, zuvor unerreichbar geglaubte Maßstäbe setzen.
Mithilfe seiner neun Stereolithografie-Drucker (SLA) aus der Serie Form 3 und dem Form Auto sowie weiteren Druckern der Technologien Schmelzschichtung (FDM) und Verbundstoff-3D-Druck fertigt Mackart kohlenstofffaserverstärktes Werkzeug und Silikonwerkzeug sowie 3D-gedruckte Bauteile für die Endverwendung. In Zusammenarbeit mit Formlabs' offiziellem Partner Solid Print3D hat Mackart seinen Durchsatz bis auf ein echtes Produktionsniveau hochskaliert.
"Für uns ist der 3D-Druck nicht nur ein Hilfsmittel für Rapid Prototyping – er ist ein effizientes Fertigungsverfahren."
Steven McCarthy, Geschäftsführer und Gründer, Mackart Additive
Komplexes Werkzeug für Carbonfaserteile aus dem 3D-Drucker
McCarthy war früher als Ingenieur im Bereich Luft- und Raumfahrt tätig, hat mit Mackart jedoch seit der Gründung im Jahr 2016 mit zahlreichen verschiedenen Branchen kooperiert, von Herstellern von Sanitärausstattung bis hin zu internationalen Motorsport-Titanen.
Eines der Materialien, das im Bereich der Motorrennen am häufigsten zum Einsatz kommt und in jüngsten Jahren auch in der Automobilbranche zum gängigen Werkstoff avancierte, ist kohlenstofffaserverstärkter Kunststoff (CFK). Bauteile aus CFK halten den hohen Temperaturanforderungen der Rennbahn stand und bieten dabei eine beispiellose spezifische Festigkeit, die die Leistung von Rennwagen in jeder Hinsicht steigert.
Carbonfaserverstärkte Teile werden normalerweise durch Prepreg-Laminierung gefertigt, indem vorimprägnierte Kohlenstofffasergewebe mit der korrekten Menge ungehärteten Kunstharzes verarbeitet werden. Diese Prepreg-Halbzeuge werden dann in oder auf das Formwerkzeug laminiert und mittels Hitze und Druck in einem Autoklav ausgehärtet.
Konventionellerweise werden die Formwerkzeuge hierfür aus Metall zerspant, damit sie der Hitze und dem Druck des Autoklavs standhalten. Subtraktive Verfahren haben jedoch mehrere Nachteile – sie verschwenden Material, sind langwierig, teuer und behindern damit den iterativen Designprozess. Angesichts der Fortschritte in den Druckmaterialien und der Hardware hat sich der 3D-Druck zur brauchbaren Option für die Herstellung robuster Werkzeuge für derartige Anwendungen etabliert.
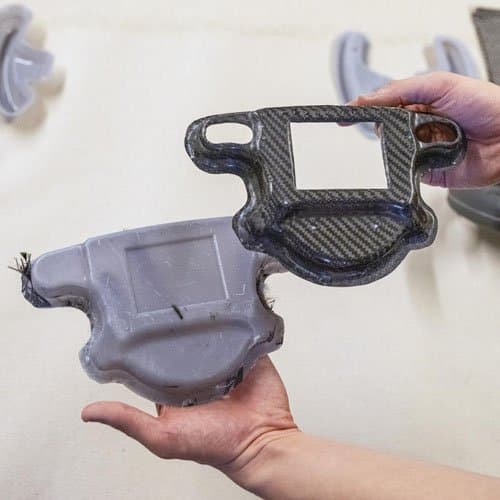
Fertigung von Kohlenstofffaserteilen mit 3D-gedruckten Formen
In diesem Whitepaper zur Herstellung von Kohlenstofffaserteilen erhalten Sie Designleitfäden für Verbundwerkstoffformen sowie schrittweise Anleitungen für die Prepreg- und Handlaminierung.
Carbonfaser-Werkzeug durch die Kombination mehrerer Technologien
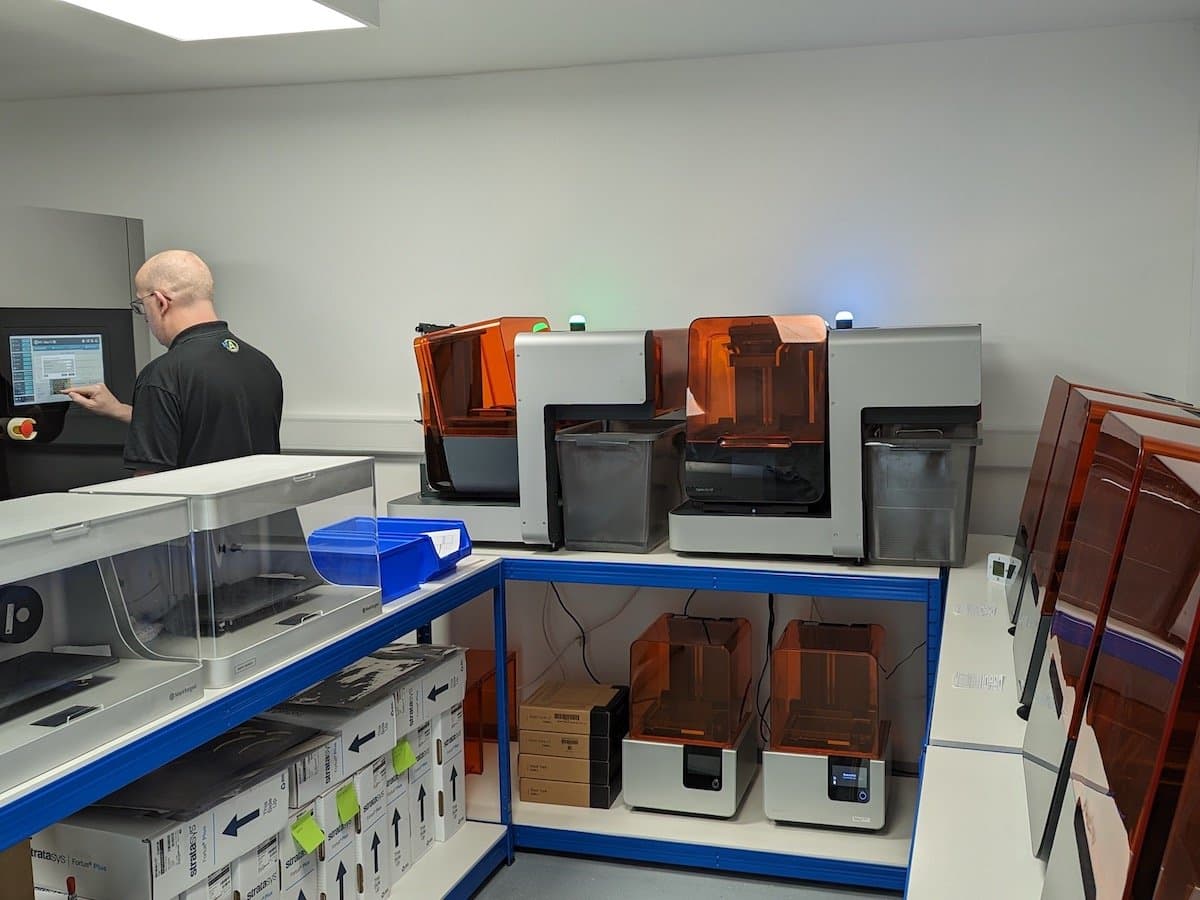
Das 3D-Drucklabor von Mackart Additive nutzt mehrere Technologien und Prozesse in Kombination, unter anderem auch zwei Form Auto. So fertigt das Unternehmen fortschrittliche Teile für eine große Bandbreite industrieller Anwendungen.
Der Schlüssel zum Erfolg liegt bei industriellem Fertigungswerkzeug in der Optimierung des Druckdesigns und der Ausrichtung – und die Anpassung dieser Parameter hat das Team von Mackart bis zur Perfektion gebracht. Mithilfe einer Kombination verschiedener 3D-Drucktechnologien und Materialien, die jeweils aufgrund ihrer spezifischen Eigenschaften gewählt werden, entwirft und fertigt das Unternehmen komplexe CFK-Formen und -Formkerne.
Nachdem das Team zuerst Grey Resin und Grey Pro Resin verwendet hatte, testete es Rigid 4000 Resin und Rigid 10K Resin und stellte fest, dass deren glatte Oberflächengüte und Steifigkeit bei den letztendlichen CFK-Teilen die besten Ergebnisse erzielen. „Wir haben einfache Presswerkzeuge aus Rigid 4000 Resin getestet und die Ergebnisse waren erstklassig. Mittels Laser-Metrologie untersuchten wir die Teile und sie wiesen eine überragende Maßgenauigkeit auf. In einigen Fällen betrug die Abweichung von der nominalen CAD-Geometrie bloß Mikrometer“, berichtet McCarthy.
Zur Herstellung großformatiger Werkzeuge teilt das Team diese häufig in kleinere Bauteile auf, die dann über sorgfältig ausgewählte Verbindungselemente zusammengefügt werden. „Bei größerem Werkzeug, das nicht ins Bauvolumen der Drucker passt, bauen wir oft Flanschverbindungen zur späteren Montage ein. Wir können Baugruppen aus drei oder vier Komponenten produzieren, um damit Werkzeuge von fast 450 mm Länge zu erstellen“, so McCarthy.
Technologievergleich: Werkzeug für kohlenstofffaserverstärkte Teile
Durchlaufzeit | Vorteile | Nachteile | |
---|---|---|---|
3D-gedrucktes Werkzeug | 1 Woche | Gestaltungsfreiheit Kontrolle über Durchlaufzeit/Lieferkette Kosteneffizient bei geringen Mengen | Wärmeausdehnung ist zu beachten Größeneinschränkungen Weniger Produktionsläufe pro Teil |
Konventionell gefertigtes Werkzeug | 3–4 Wochen | Tausende von Produktionsläufen Haltbarkeit Größe | Lange Lieferzeiten Designeinschränkungen |
Justierung der Parameter und Optimierung des Prozesses
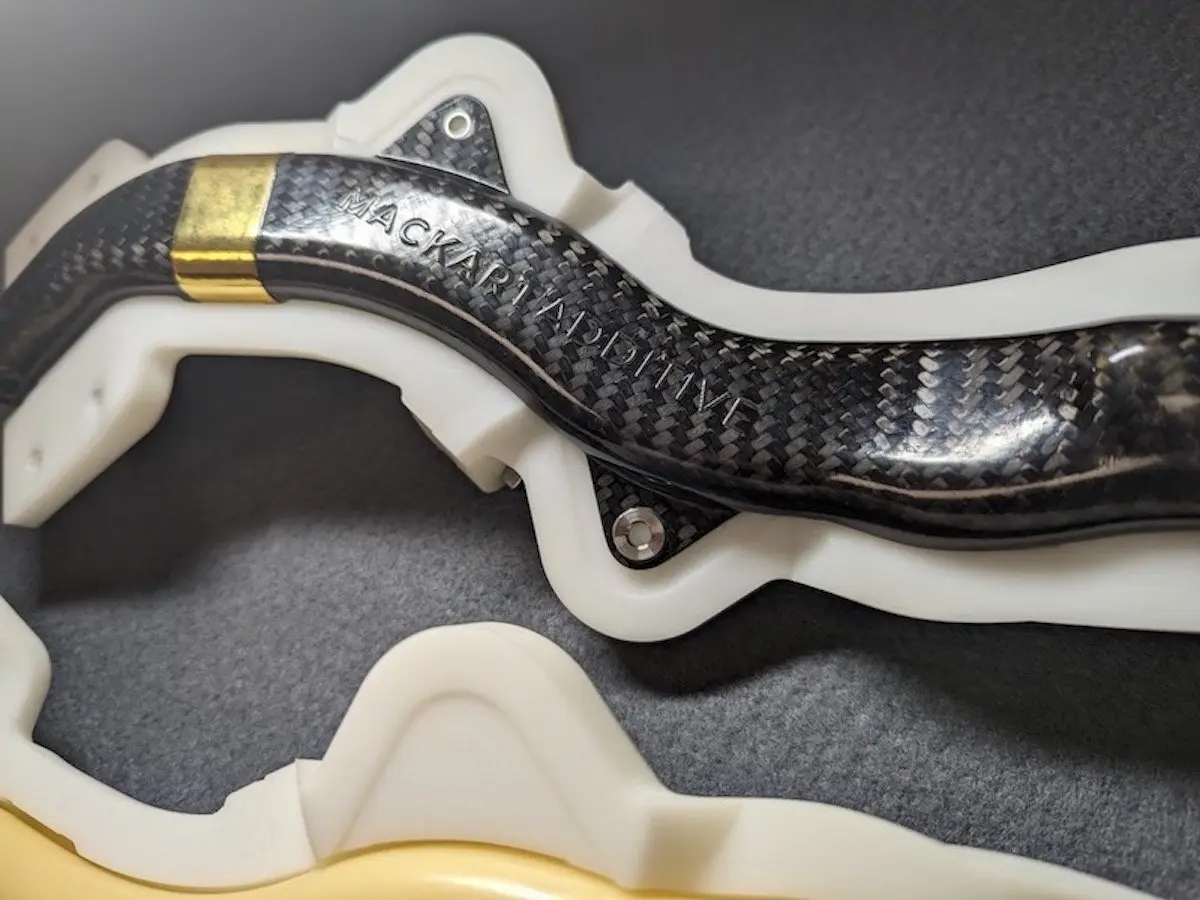
Dieses kohlenstofffaserverstärkte Lüftungsbauteil wurde mithilfe von 3D-gedrucktem Rapid Tooling hergestellt, bestehend aus einer äußeren Hülle, die aus Rigid 10K Resin auf dem Form 3+ gedruckt wurde, sowie einem inneren Formkern, das auf einem großformatigen SLA-3D-Drucker gedruckt wurde.
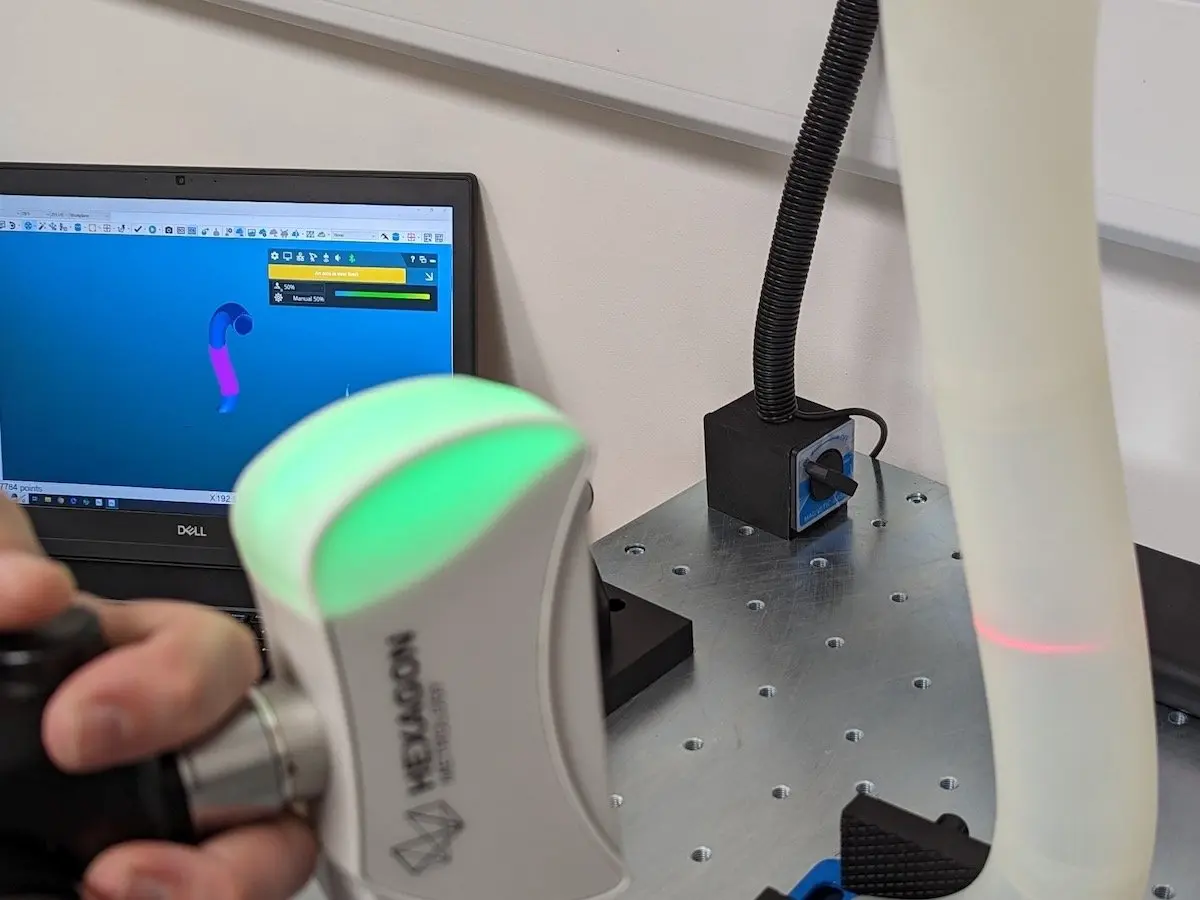
McCarthy erstellt einen 3D-Scan eines Formkerns, der aus Durable Resin auf dem Form 3 gedruckt wurde und in einem Fertigungsprozess eines CFK-Lüftungskanals für einen Formel-1-Wagen zum Einsatz kommt.
Während des Aushärtungsprozesses mit dem Autoklav kann die Temperatur die Glasübergangstemperatur des Werkzeugmaterials übersteigen. Die Leistung von Rigid 10K Resin konnte hier jedoch überzeugen und das Bauteil weist auch nach wiederholter Benutzung keinen Verschleiß oder Maßabweichungen auf. „Rigid 10K Resin ist ein härteres Material und bietet eine etwas bessere Oberflächenqualität. Tatsächlich ist es ein wunderbarer Ersatz für Aluminium“, urteilt McCarthy. Um die Teiloberfläche für den Kontakt mit Kohlenstofffasergeweben zu optimieren, putzt das Team von Mackart die Oberfläche der Formenteile aus Rigid 10K Resin leicht ab, damit die Glaspartikel entfernt werden, die sich aus der einzigartigen Photopolymerumwandlung beim Druck von Rigid 10K Resin ergeben.
Außerdem hat das Team die Kompensationsfaktoren für den Materialverzug beim Autoklavieren so justiert, dass das fertige CFK-Bauteil den Toleranzen entspricht. „Wenn das Teil nicht zu kompliziert ist, können wir die Toleranzen vollkommen einhalten. Bei größeren Werkzeugen ist es eine Frage des Prozentsatzes“, so McCarthy.
Für die interne Form komplexer CFK-Komponenten wie Rohren und Kanälen werden üblicherweise lösliche Formkerne genutzt. Bei kleineren Komponenten (die in das Konstruktionsvolumen des Druckers passen) können jedoch entnehmbare Formkerne gefertigt werden, wodurch die Komplexität und der Zeitaufwand der herkömmlichen, löslichen Variante aus dem FDM-Druck vermieden werden. Mackart hat mit Durable Resin überragende Erfolge für diesen Anwendungsfall erzielt. Für größere, entnehmbare Formkerne, die das Konstruktionsvolumen des Druckers übersteigen, nutzt Mackart alternativ den betriebsinternen SLA-Druck mit tiefem Tank.
Der Teufel liegt im Detail
Für Branchen wie den Motorsport ist die additive Fertigung eine perfekte Lösung, denn hier können kleinste Designänderungen, auch wenn sie nur ein paar Mikrometer betragen, einen Sekundenvorsprung ausmachen oder den letzten Vorstoß über die Ziellinie ermöglichen. Der Luftstrom um den Wagen herum und durch ihn hindurch ist hierbei der Dreh- und Angelpunkt.
„Der 3D-Druck liefert eine wunderbare Lösung für den Motorsport, denn er bietet eine geometrische Freiheit ganz ohne die Einschränkungen subtraktiver Verfahren. Da Platz im Inneren eines Rennwagens ein Luxusgut ist, erlaubt diese Gestaltungsfreiheit es den Teams, die gesamte Aerodynamik zu optimieren. Ohne die Möglichkeit, starre CFK-Komponenten (die mit 3D-gedrucktem Werkzeug hergestellt werden) zu bearbeiten und ohne Abstriche um das Fahrzeug herum zu formen, hätten wir in den vergangenen paar Rennsaisons vielleicht nicht dieselben Leistungssteigerungen beobachtet. Dass wir Werkzeug herstellen können, mit dem wir dieses Potenzial ausschöpfen können, verdanken wir dem Werkzeugbau mit 3D-Druck, optimiert durch eine sorgfältige, gut entwickelte Designtechnik“, erklärt McCarthy.
In der Vergangenheit erforderte die Fertigung relativ komplexer Geometrien aus kohlenstofffaserverstärktem Kunststoff mittels traditionellem, subtraktiv gefertigtem Werkzeug stets die Integration von verlorenem, überschüssigem Material in die Komponenten, damit das Gussputzen in der letzten Phase der Passung möglich war. Die Genauigkeit und Stabilität der 3D-gedruckten Formwerkzeuge haben dies größtenteils überflüssig gemacht. „Es gibt jetzt gleich beim ersten Mal einen Erwartungsmaßstab dafür, was „richtig“ ist, und diesem werden wir mit den fertigen CFK-Komponenten regelmäßig gerecht. Was wir gut können, ist wirklich komplexe, genaue Geometrien umzusetzen“, sagt McCarthy.
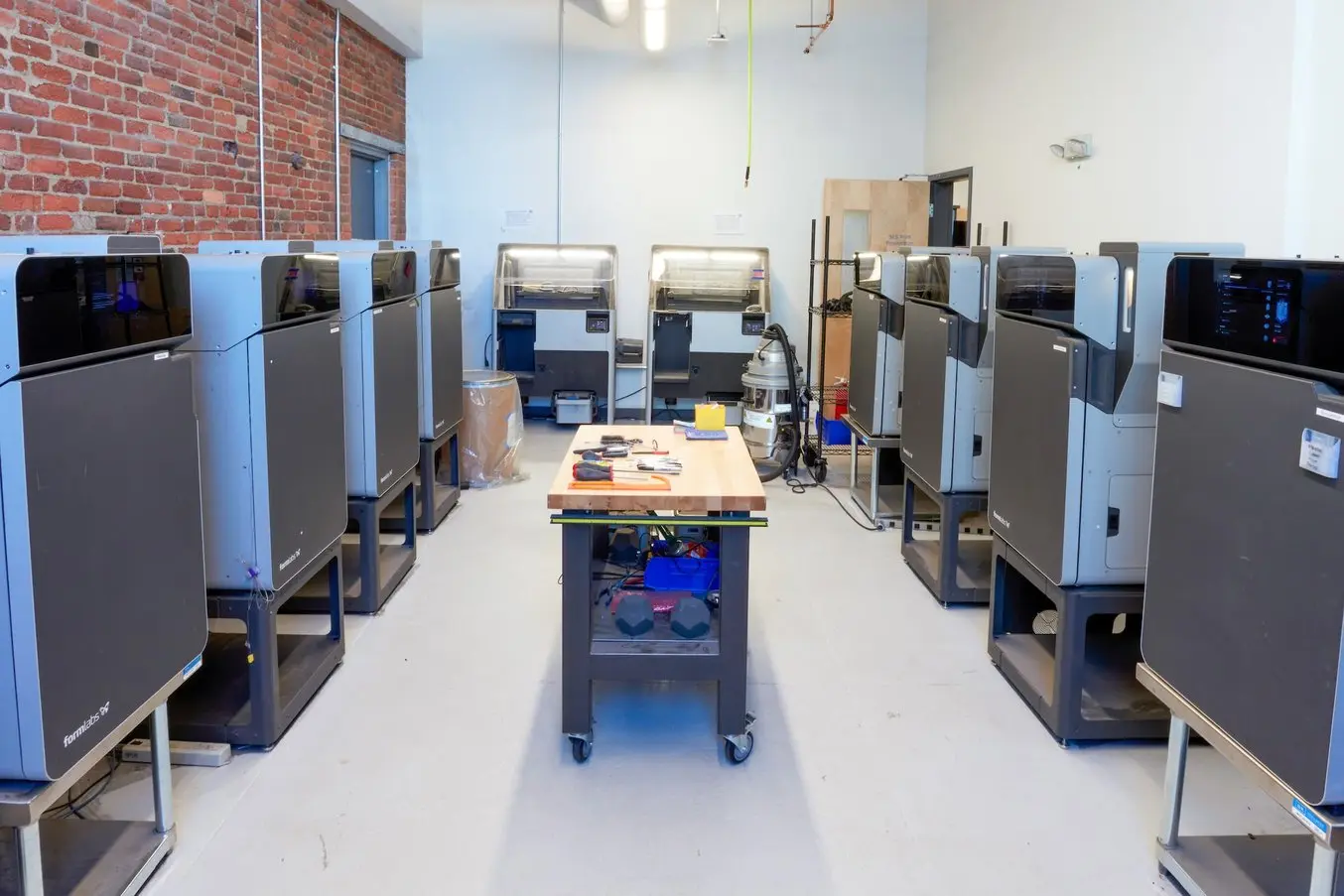
Die Verwaltung von 3D-Druckerflotten
Die Verwaltung mehrerer SLA- und SLS-3D-Drucker muss nicht zwingend kompliziert sein, jedes Unternehmen kann in nur ein oder zwei Tagen eine ganze Flotte von SLA- und SLS-Druckern in Betrieb nehmen. In diesem Leitfaden stellen wir vier verschiedene Fertigungsszenarien mit mehreren Druckern vor, um Ihnen bei der Zusammenstellung eines effizienten Prozesses für jegliches Bauteil oder Produktionsvolumen zu helfen.
Mit dem Form Auto auch über Nacht in vollem Gange
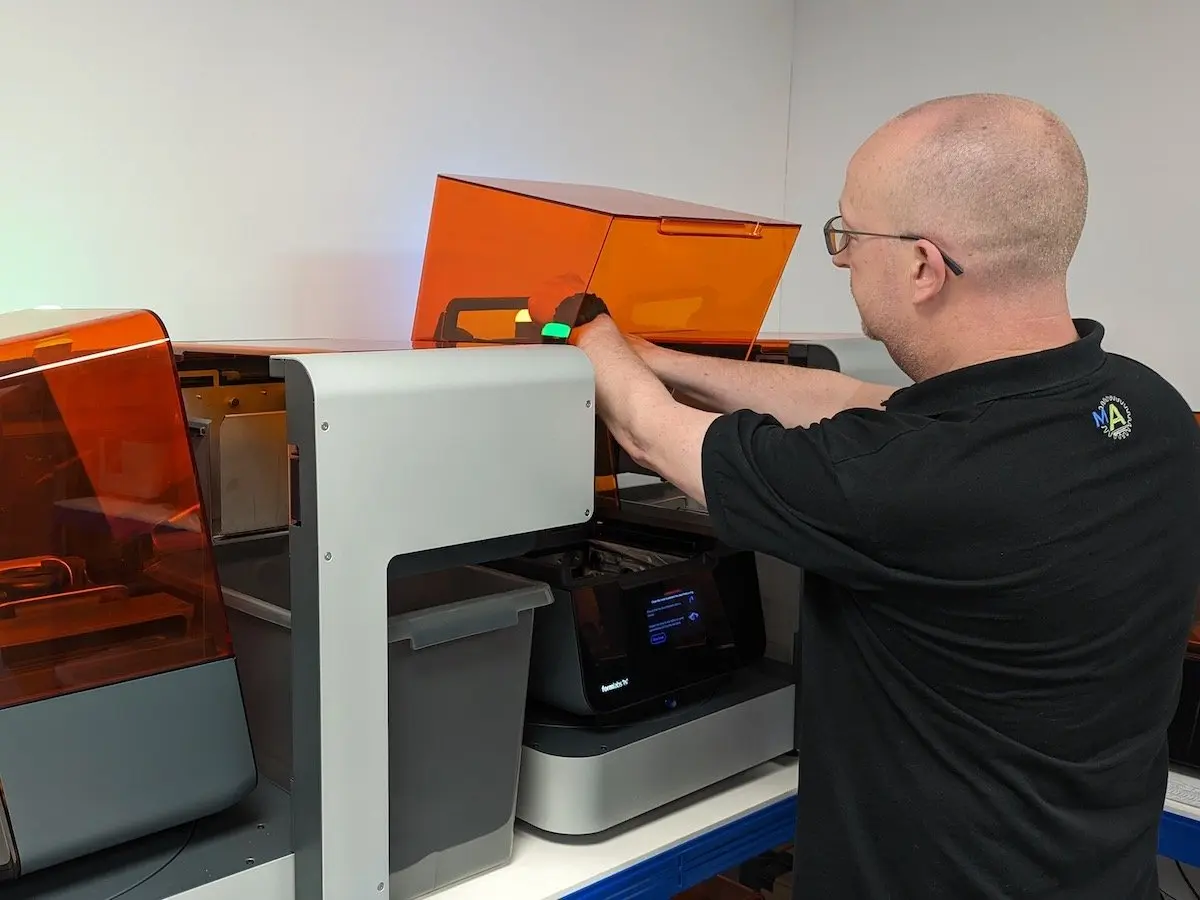
Der Form Auto ist mit bestehenden Druckern des Typs Form 3 und Form 3+ kompatibel, sodass Drucklabore ihre Geräte mit wachsender Nachfrage schrittweise aufrüsten können.
Mackart gehört zu den Erstanwendern des automatisierten Ecosystems von Formlabs; das Team nahm den Form Auto Anfang 2023 in Betrieb und optimiert seitdem stetig seine Automatisierungsprozesse. „Das gibt uns die Möglichkeit, unsere Kapazitäten zu maximieren – der Vorteil des Form Auto ist, dass man eine Nachtschicht hinzufügen kann“, berichtet McCarthy.
Zwei der neun Form 3+ wurden mit einem Form Auto ausgestattet und sind dadurch durchgängig in Betrieb. Der Form Auto arbeitet auch über Nacht und am Wochenende, um den Druckbetrieb am Laufen zu halten, wenn das Team Feierabend hat.
„Der Form Auto erledigt die Nachtschicht und die Wochenendschicht und man braucht keine Wechsel von Konstruktionsplattformen einzuplanen. Er läuft einwandfrei und eignet sich super für kleine Bauteile und mittelgroße Produktionsserien bis zu 1000 Teilen und mehr.“
Steven McCarthy, Geschäftsführer und Gründer, Mackart Additive
Das Team von Mackart hat immer mit verschiedenen Projekten zugleich zu tun. Während das Team noch intensiv mit der Arbeit an neueren, komplexeren Teilen beschäftigt ist, kann der Form Auto einen Teil ihrer repetitiven Aufgaben übernehmen und die Leerlaufzeiten der Drucker reduzieren. „Unsere Durchlaufzeit hat sich dadurch verkürzt und die Produktivität hat sich erhöht“, so McCarthy.
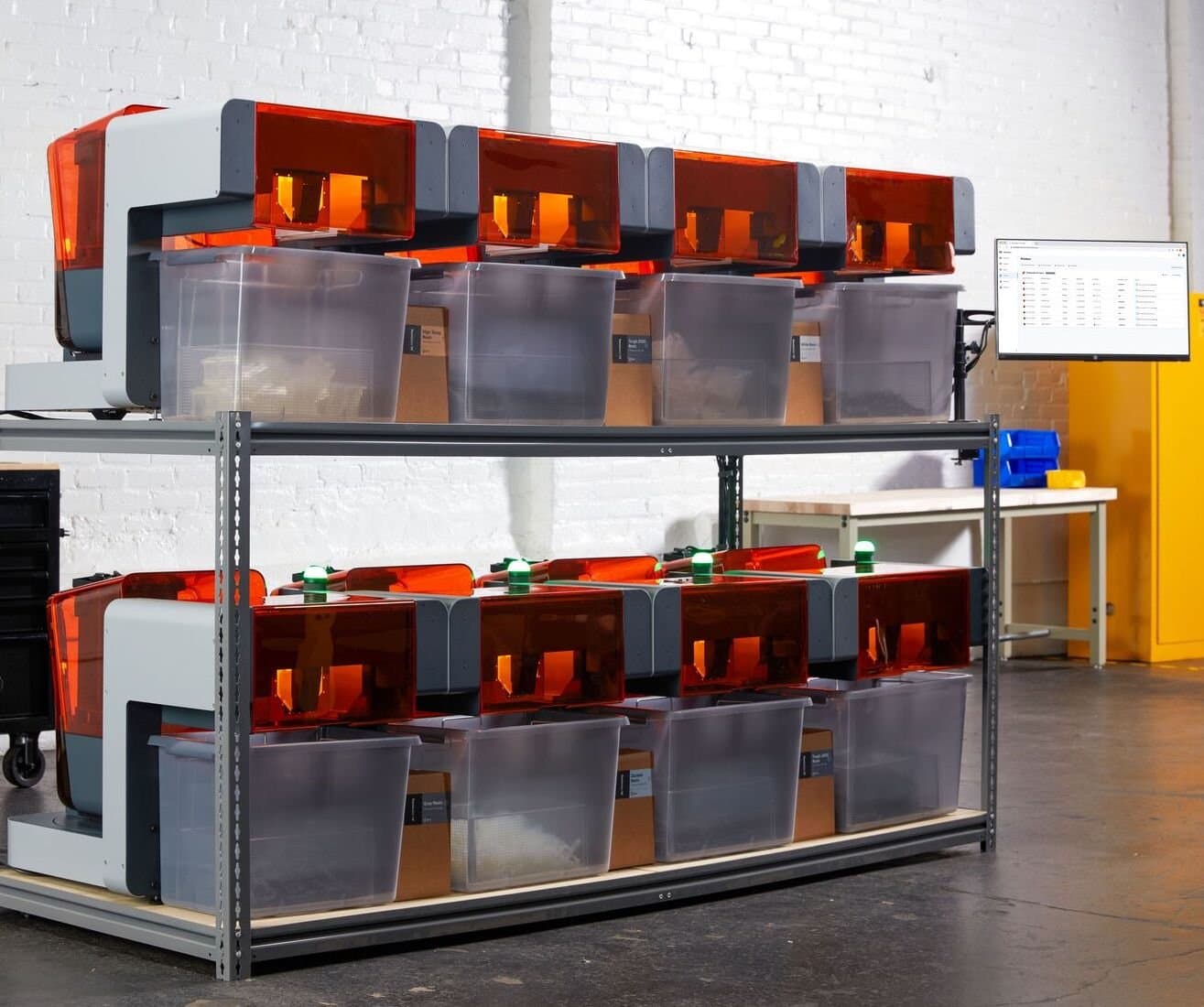
Einführung in das automatisierte Ecosystem von Formlabs
Lernen Sie Formlabs' automatisiertes Ecosystem kennen: Angefangen von der ununterbrochenen Teileproduktion rund um die Uhr, die Durchsatz und Produktivität neu definiert, bis hin zur automatisierten 3D-Druckerflotte.
Oldtimer-Bauteile für 10 000 £ weniger
Einige der repetitiven Arbeitsschritte fallen bei kleinen Teilen an, die in größeren Mengen produziert werden müssen, wie etwa Ersatzteile für Oldtimer. Diese Bauteile wären ursprünglich spritzgegossen worden, doch ein großer Teil der Gussformen ist im Laufe der Zeit verloren gegangen und längst nicht mehr auf Lager. Um dieses Problem zu lösen, wandte sich ein Kunde an Mackart.
Früher haben die Bauteile als Lagerartikel vermutlich etwa 0,20 £ pro Stück gekostet. Mit 3D-Druck sind die Teile für ungefähr fünf- bis zehnmal so viel erhältlich, dafür fallen jedoch die Kosten neuer Formwerkzeuge, die Mindestproduktionsmengen des Spritzgusses und die Einrichtungskosten weg – Kostenpunkte, die sich bei der Produktion individueller Komponenten nur schwer amortisieren ließen.
3D-gedruckte Bauteile bieten hierfür nun eine taugliche Lösung. „Werden die Teile 3D-gedruckt, stellt sich das Problem der Amortisation der Produktionskosten von Spritzguss überhaupt nicht – über Reverse Engineering entwerfen wir, was immer der Kunde braucht, und dieser kann ein einzelnes Teil davon erwerben, ohne 10 000 £ oder mehr für eine neue Spritzgussform und all die anderen prozessbedingten Zusatzkosten ausgeben zu müssen. Damit hat der Kunde dann eine unbegrenzte Beschaffungsquelle für jede beliebige Stückzahl“, so McCarthy.
In der Automobilbranche kann die Beschaffung einzelner Teile oder auch nur kleiner Mengen von Teilen extrem teuer sein, weshalb die Restauration und Wartung von Oldtimern leicht zum Luxushobby wird. Dank des 3D-Drucks kann Mackart seiner Kundschaft auch für kleine Mengen günstige Preise bieten. „Es ist eine viel flexiblere, wirtschaftlichere Lösung, und da ist der Form Auto eine große Hilfe. Er wird einsatzbereit geliefert, erfordert minimale Wartung, und man kann 1000 Teile am Stück produzieren, wofür man nichts weiter tun muss, als hin und wieder eine neue Harzkartusche einzusetzen“, erzählt McCarthy.
Hat sich der Prozess bewährt, geht es an die Kapazitätssteigerung
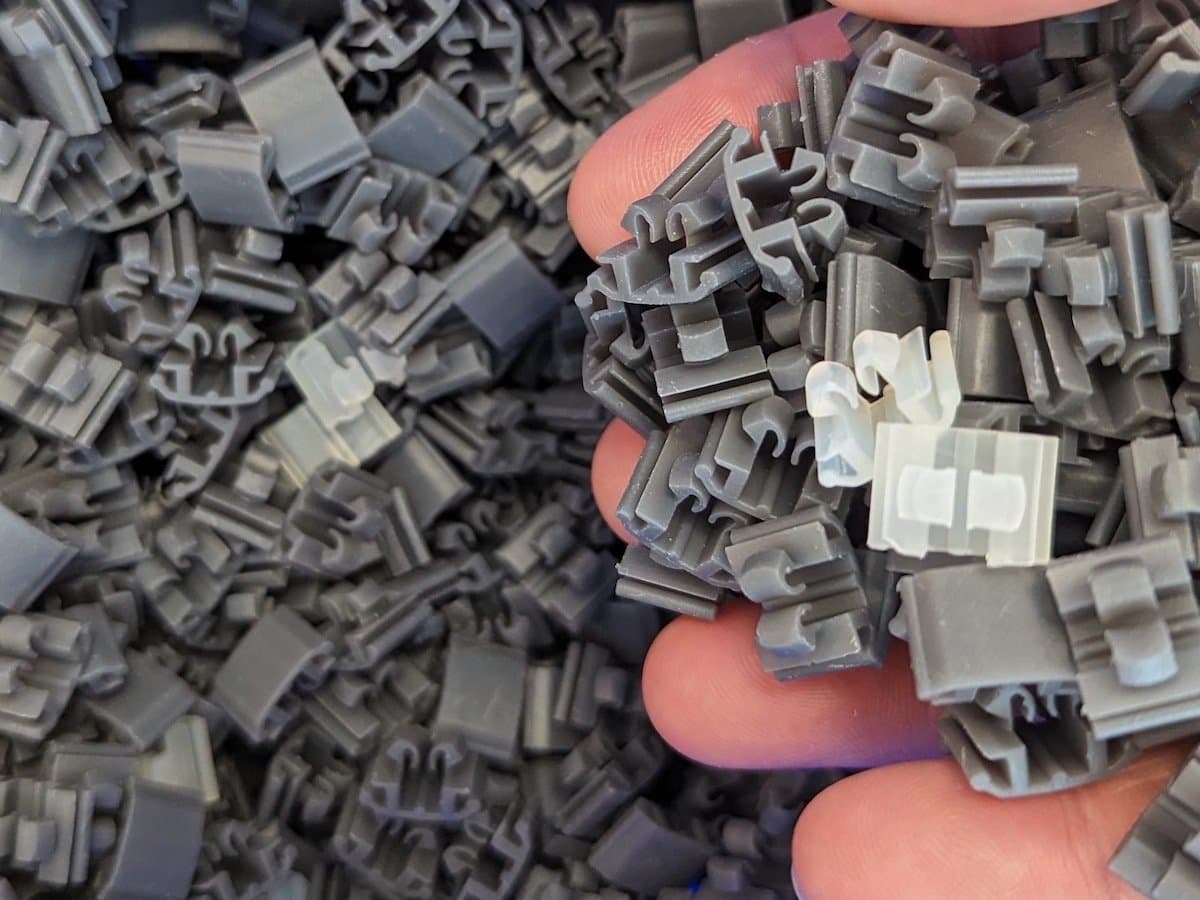
Der Form Auto unterstützt Mackart perfekt dabei, Hunderte oder Tausende von kleinen Teilen zu fertigen, wie zum Beispiel diese Verbindungsclips für den Oldtimer-Markt.
Mackart hat viel Zeit in die Optimierung seiner Prozesse investiert und sichergestellt, dass es seinen Kunden aus verschiedensten Branchen hochwertige Designs liefert. Der Schlüssel hierzu war die Kombination mehrerer Technologien und die Nutzung verschiedener 3D-Druckverfahren und Materialien, je nach ihrer Eignung.
Indem das Team den Form Auto hinzufügte, konnte es seine Kapazitäten steigern und seine Produktion um eine weitere Arbeitsschicht erweitern, die ohne manuelle Eingriffe auskommt. Für die Zukunft ist McCarthy zuversichtlich, dass das Unternehmen mit steigender Nachfrage seine 3D-Druckerflotte dazu nutzen kann, neue Branchen und Anwendungsbereiche zu erobern, mit derselben Präzision und Leistungsstärke, die es zu einem bewährten Partner für einige der führenden Formel-1-Teams der Welt gemacht haben.
Wir bedanken uns bei unserem Vertriebspartner im Vereinigten Königreich, Solid Print3D, der Mackart bei der Arbeit mit 3D-Drucklösungen von Formlabs berät und unterstützt. Um mehr über Anwendungen des 3D-Drucks in der Automobilindustrie zu erfahren, besuchen Sie unseren Branchenüberblick oder lassen Sie sich von unserem Team zu Ihrem spezifischen Anwendungsfall beraten.