New Balance und Formlabs arbeiten zusammen, um Performance und Individualisierung bei Sportschuhen voranzutreiben
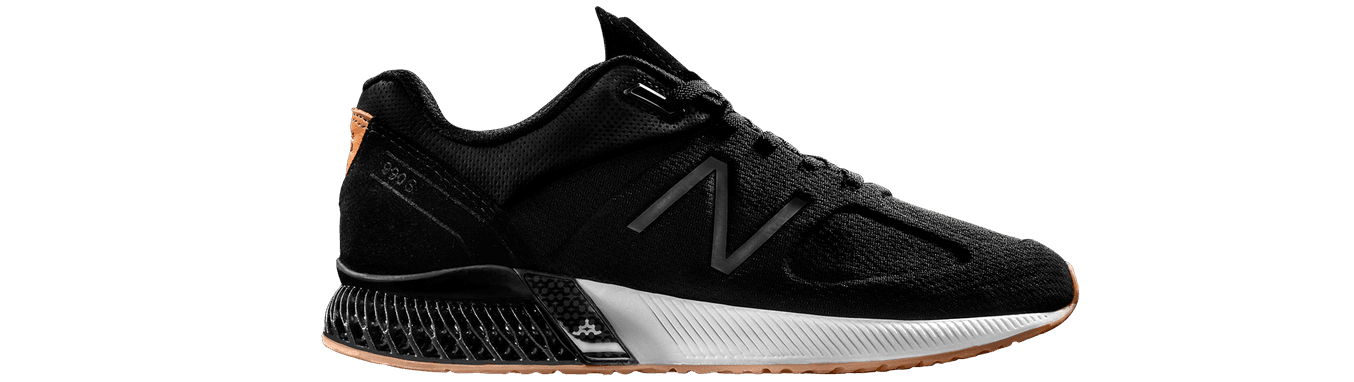
Performance liegt in den Details. Bei Schuhen sind das Design und Materialien, deren Möglichkeiten beide jeweils durch die Fertigung begrenzt werden.
Im Jahr 2017 begann New Balance eine Zusammenarbeit mit Formlabs, um ein 3D-Druck-Fertigungssystem zu entwickeln, das innovative Möglichkeiten bei den genannten Aspekten eröffnet - unbegrenzte Designfreiheit zur Schaffung leistungsoptimierter Strukturen, einen Weg zur skalierbaren Herstellung von Komponenten und eine ganze Bandbreite an neuen Materialien.
Diesen Sommer macht das Unternehmen einen gewaltigen Schritt nach vorn, indem es diese Vision mit der Ankündigung von TripleCell zur Wirklichkeit werden lässt. Bei dem Projekt handelt es sich um eine Premiumtechnologieplattform, die durch Formlabs Stereolithografie-(SLA)-3D-Drucker und Rebound Resin, ein vollständig neues Material, unterstützt wird.
„TripleCell ermöglicht es uns, auf bahnbrechende Weise Daten zu nutzen, um jeden Millimeter der Sohle für das Lauferlebnis zu beeinflussen. Formlabs ist bei diesem Projekt ein entscheidender Partner. Wir können wirklich für Disruption in der Branche sorgen, und das nicht nur in Sachen Performance, sondern auch bei der Individualisierung für Sportler und den Markteinführungszeiten“
Katherine Petrecca, New Balance General Manager Footwear des Innovation Design Studio
Lesen Sie weiter, um mehr über die Materialien und die Zusammenarbeit beim 3D-Druck-Arbeitsprozess zu erfahren, die hinter TripleCell stecken, und die Herangehensweise, die New Balance in eine Position versetzt hat, zum Marktführer bei der innovativen Herstellung von Sportschuhen zu avancieren.
Die Suche nach Invidividualisierungsmöglichkeiten in einer komplexen Lieferkette
Schuhe sind von Haus aus komplexe Produkte. Schuhe sind ein Geschäft mit großem Inventar und hohen Volumina, bei dem oft immer noch viel Handarbeit und Handwerkskunst erforderlich ist. New Balance führt jedes Jahr tausende Designs ein, und ein einziges Modell umfasst Hunderte von SKUs an Farb- und Größenkombinationen, bei denen Komponenten mit verschiedenen Materialien, Toleranzen und Werkzeugprogrammen hergestellt werden.
Da die Nachfrage nach Individualisierung wächst, wir alles nur noch komplizierter. Der moderne Verbaucher wünscht sich individualisierte Produkte, die von überall aus über eine Vielzahl von Endgeräten bestellt und schnell geliefert werden können.
Bislang konnten die meisten Unternehmen hochgradig individualisierte Produkte nur als Unikate anbieten, wobei sie 3D-Druck nutzen, um stark individualisierte Sportschuhe Dienst für Profisportler anzufertigen. Im Jahr 2013 nahm der erste Sportler mit individuell gedruckten Schuhen an einem Wettkampf teil. Kurz danach gab es auch in der Leichtathletik, beim Football, Baseball und bei anderen Sportarten Premieren.
Parallel dazu entwickelte sich auch die 3D-Drucktechnologie weiter. Im Jahr 2012 brachte Formlabs den Form 1 mit dem Ziel auf den Markt, leistungsstarke, zuverlässige Stereolithographie (SLA) erschwinglich, zugänglich und skalierbar zu machen. Der Form 2 kam 2015 auf den Markt, und seitdem haben Anwender über 40 Millionen Teile auf diesen Geräten gedruckt. Jetzt öffnen der Form 3 und Form 3L die Tür für weitere Möglichkeiten bei der Fertigung mit 3D-Druck, darunter auch für großformatige Teile.
Heute ist 3D-Druck auf dem besten Weg kundenindividuelle Massenproduktion für mehr Unternehmen zur Wirklichkeit werden zu lassen. In verschiedenen Branchen gibt es Pionierprodukte wie etwa die Gillette’s Razor Maker™ Plattform, die eines der ersten Beispiele für 3D-gedruckte Endprodukte für den Verbraucher ist.
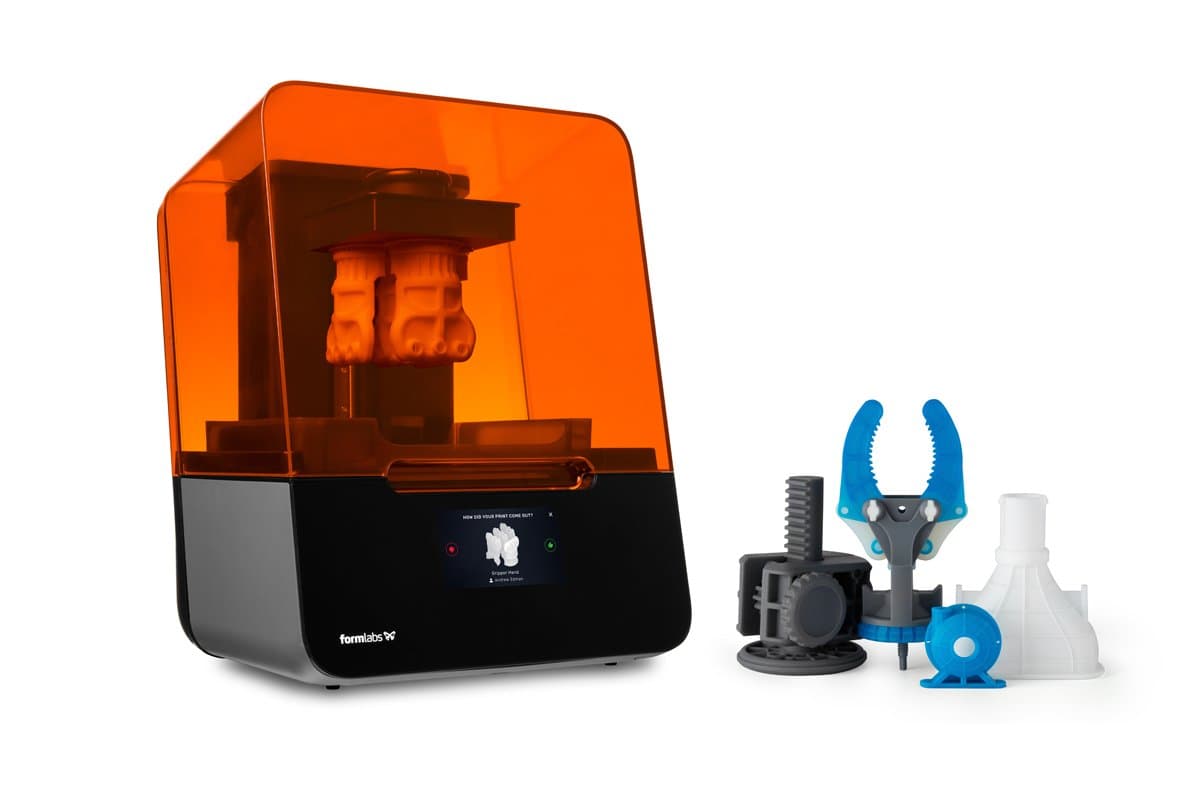
Einführung in den 3D-Druck mit Desktop Stereolithographie (SLA)
Laden Sie unser erweitertes Whitepaper über Stereolithographie herunter, um zu erfahren, wie SLA-Drucktechnologien funktionieren, warum Tausende von Fachleuten diesen Prozess heute verwenden und wie dieser 3D-Druckprozess Ihrer Arbeit zugute kommen kann.
Einen kompletten Schuh schneller als je zuvor designen
Neben der Zusammenarbeit mit Profisportlern hat New Balance 3D-Druck bereits seit einiger Zeit für die Prototypenfertigung genutzt. Heute fertigt das Unternehmen jährlich Tausende von 3D-gedruckten Prototypen. New Balance beobachtete die Weiterentwicklung der 3D-Druck-Branche genau.
„Wir sahen die Innovationen bei 3D-Druckern und Materialien und stellten uns vor, wie sich das in der Zukunft für Konsumgüter einsetzen ließe“, berichtet Petrecca.
„Wenn man Technologien wie 3D-Druck nutzen kann, um zu einem stärker ausgeprägten On-Demand-Herstellungsmodell überzugehen, ist das bahnbrechend. Daraus ergeben sich sowohl für den Verbraucher als auch für New Balance als Hersteller Vorteile. Mit Hinblick auf den Verbrauchern sind die Design- und Herstellungsmöglichkeiten mit 3D-Druck deutlich größer als beim Spritzguss und beim Formpressen. Wir haben so viele Möglichkeiten, Teile zu machen, die besser sind als die, die wir heute aus Schaum und Kunststoff herstellen.“
Die meisten Schaumkomponenten in modernen Schuhen werden durch unterschiedliche Spritzguss- oder Formpressverfahren hergestellt, was die Designmöglichkeiten erheblich einschränkt. Der Übergang zum Einsatz von 3D-Druck bei der Prototypenfertigung und der Produktion hat jedoch neue Möglichkeiten eröffnet, die mit herkömmlichen Fertigungsverfahren unmöglich waren.
„Bislang konnten wir nur das Äußere des Schuhs entwickeln und uns auf die Materialeigenschaften verlassen, um alle Performance-Vorteile zu erhalten, die wir wünschten. Das, was man noch am ehesten als Individualisierung betrachten kann, sind verschiedene Teile aus Schaum, die zusammengeklebt oder -gepresst werden, wobei viele Montageschritte erforderlich sind“, so Dan Dempsey, New Balance Senior Additive Manufacturing Engineer bei New Balance.
„Durch den Einsatz Additiver Fertigung können wir die Gitterstruktur verändern, um lokale Eigenschaften in einer einzigen Form zu ändern, wodurch wir das gesamte Volumen des Schuhs beeinflussen können; wir können ein System von innen nach außen gestalten..“.
Echter 3D-Druck ermöglicht das Design eines gesamten Teils, um Strukturen herzustellen, die über Schaum hinausgehen. Die TripleCell-Produkte von New Balance werden die besten Beispiele in der Branche für Data-to-Design sein, da sie über nahtlose Übergänge zwischen unterschiedlichen Eigenschaften in der Sohle verfügen.
Diese neue Designmethode sorgt für ganz neue Möglichkeiten in Sachen Performance. Und das ist genau das, was TripleCell erreicht: nathloses Tuning der gesamten Sohle, wobei ein Bereich mit hoher Dämpfung innerhalb desselben Designs und desselben Materials in einen Bereich mit hoher Stabilität übergehen kann. Die Prototypenfertigung und die Herstellung von Teilen mit 3D-Druck verändern auch den gesamten Arbeitsablauf bei der Produktentwicklung, wodurch die Markteinführungszeiten verkürzt werden.
„Der herkömmliche Zeitplan für unseren Produktzyklus von den ersten Entwürfen bis zur Markteinführung beträgt 15 bis 18 Monate. Und wenn wir Werkzeuge bauen und auf Schaum- oder Gummiteile warten, reden wir von Lieferzeiten zwischen 4 und 6 Wochen" erklärt Petrecca. „Wenn wir keine Formen mehr benötigen, können wir bei der Entwicklungszeit ganze Monate einsparen. Dank der TripleCell-Technologie können wir mehrere Designs ohne Probleme gleichzeitig entwickeln und den herkömmlichen iterative Testablauf neu erfinden. Wir konnten tausende von Optionen erzeugen und bearbeiten, bevor wir zu den für den Laufsport ausgerichteten Hochleistungsstrukturen gelangten, die Sie heute sehen.
Die Entwicklung von Rebound Resin und einem nahtlosen 3D-Druck-Fertigungssystem
Als das Team von New Balance mit dem Projekt begann, wusste es, dass ein sehr spezifisches Material nötig sein würde, das allerdings in der additiven Fertigungsbranche jedoch noch nicht existierte, sowie ein hervorragender Partner, der das gesamte System umsetzen könnte. Im Jahr 2017 gab das Unternehmen eine Zusammenarbeit mit Formlabs bekannt, wodurch die 3D-Drucktechnologie bei der Großserienfertigung von Schuhen im Werk in Massachusetts ihren Einzug feierte.
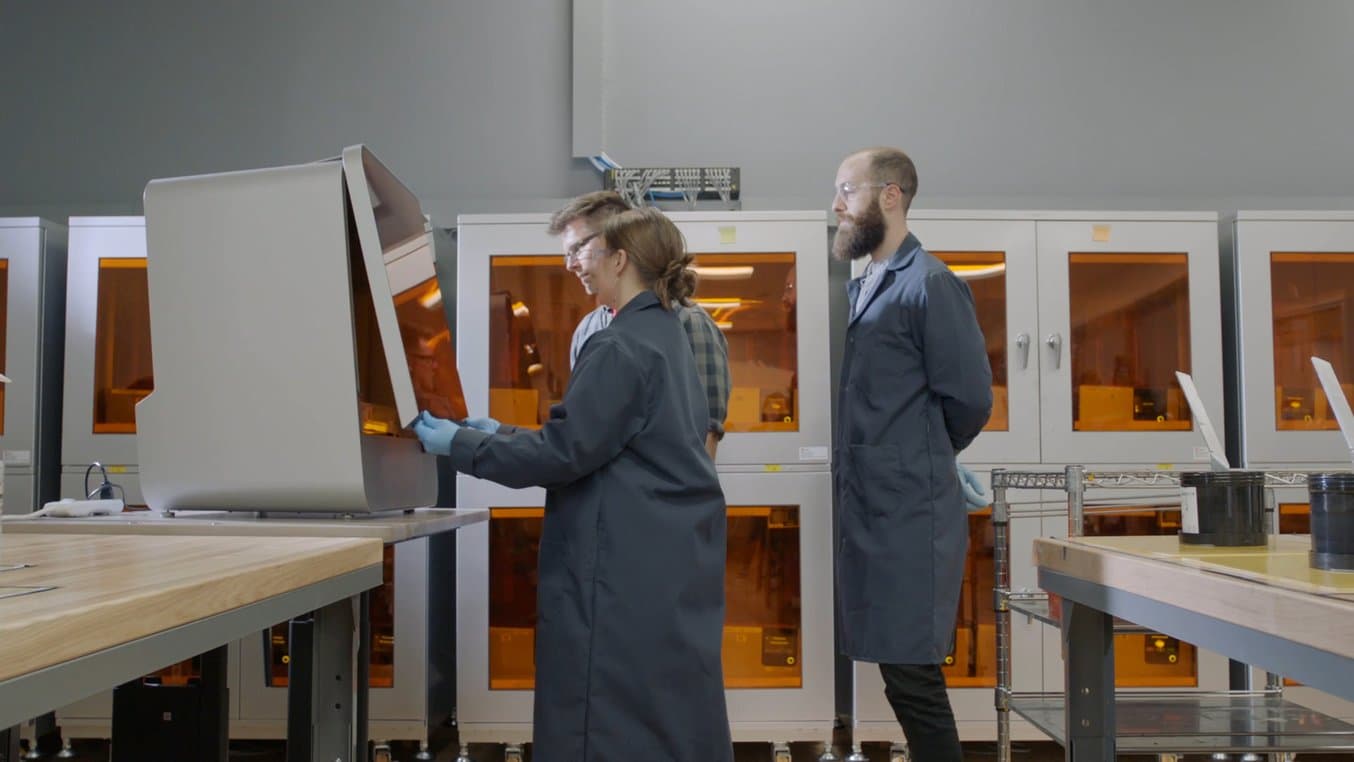
„Alles steht und fällt mit den Eigenschaften, die man aus den Materialien, die man herstellt, herausholen kann. Man kann den schnellsten Drucker der Welt oder einen Drucker für eine Million Dollar einsetzen, aber das spielt gar keine Rolle, wenn die Materialeigenschaften nicht der Anwendung standhalten, für die sie bestimmt sind“, so Dempsey.
New Balance und Formlabs haben von Grund auf ein exklusives kundenspezifisches Material entwickelt, das allen erforderlichen Fertigungs- und Endnutzungsanwendungen standhält. Das Endergebnis ist Rebound Resin.
Dieses Material, das entwickelt wurde, um federnde, widerstandsfähige Gitterstrukturen zu erzeugen, bietet eine deutlich höhere Energierückgabe, Reißfestigkeit und Dehnung als alle anderen SLA-Materialien von Formlabs.
„Die 3D-gedruckten TripleCell-Komponenten bieten eine viel lebendigere, federartige Dämpfung als alle Schaumsohlen, die Sie bislang ausprobiert haben, und können auf Anfrage in unseren Werken in Massachusetts hergestellt werden“, so Petrecca.
Rebound Resin wurde entwickelt wurde, um federnde, widerstandsfähige Gitterstrukturen zu erzeugen, und bietet eine deutlich höhere Energierückgabe, Reißfestigkeit und Dehnung als alle anderen SLA-Materialien von Formlabs.
„Alles steht und fällt mit den Eigenschaften, die man aus den Materialien, die man herstellt, herausholen kann. Man kann den schnellsten Drucker der Welt oder einen Drucker für eine Million Dollar einsetzen, aber das spielt gar keine Rolle, wenn die Materialeigenschaften nicht der Anwendung standhalten, für die sie bestimmt sind“
Dan Dempsey, New Balance Senior Additive Manufacturing Engineer
Die Grenzen von Schuhdesign und -fertigung erweitern
Die TripleCell-Partnerschaft ist ein weiterer Meilenstein bei 3D-Druckanwendungen, die von der Prototypenfertigung bis zur skalierbaren Herstellung gehen.
Diese bahnbrechende digital hergestellteTechnologie wird jetzt exklusiv in den amerikanischen Werken von
New Balance skalierbar gefertigt. Nächstes Jahr möchte New Balance die Produktion auf über 10 000 TripleCell-Paare pro Jahr hochfahren und das Wachstum innerhalb der Fabriken ausweiten.
Für die Zukunft bietet TripleCell die Grundlage zur Nutzung einzigartiger Sportlerdaten und Leistungseinblicke, um individuelle Schuhe in unbegrenzten Kombinationen zu schaffen und diese auf Anfrage herzustellen, wodurch sich Entwicklungszeiten reduzieren und Markteinführungszeiten verkürzen lassen.
„Wo wir heute stehen, zeigt nur, wie wir intern und mit Formlabs gearbeitet haben. Sie haben unser
Programm wirklich angetrieben“, sagt Petrecca. „Wir haben gezeigt, dass wir Additive Fertigung nach obenaufwärts skalieren und sinnvoll in einer Produktionsumgebung einsetzen können. Unseren zukünftigen Projekten sind fast keine Grenzen gesetzt.
Behind-the-Scenes Insights: New Balance's TripleCell Platform and Gillette's Razor Maker
For more behind-the-scenes insights from New Balance’s approach to 3D printing and work with Formlabs, watch our 2019 Formlabs User Summit panel 3D Printing as Business Transformation, featuring New Balance and Gillette.