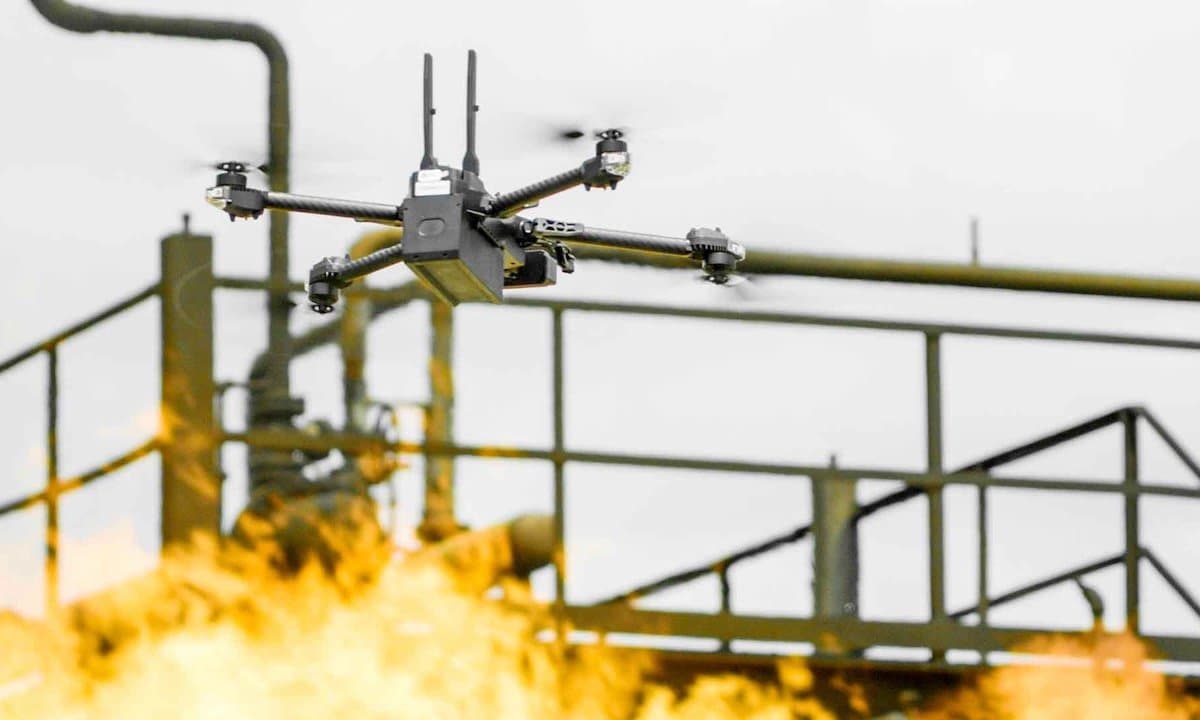
Skydios Produktreihe unbemannter Flugsysteme wird von professionellen Anwendern verschiedenster Branchen genutzt, von der Energieversorgung bis zur Katastrophenhilfe und darüber hinaus. Foto mit freundlicher Erlaubnis von Skydio.
Rund um den Globus versuchen Hersteller, auf den Vormarsch künstlicher Intelligenz zu reagieren und sich anzupassen, doch ein Drohnenproduzent hat in Sachen KI-gestützter Systeme den Maßstab gesetzt. Skydio ist ein führender Drohnenhersteller aus den USA und globaler Marktführer im Bereich autonomes Fliegen. Seine unbemannten Flugsysteme (UAS, für engl. unmanned aerial system) und neuartigen Dock-Produkte eröffnen neue Möglichkeiten für Branchen wie die Energieversorgung, das Transportwesen, öffentliche Sicherheit, Umweltforschung und mehr.
Die Ingenieur- und Designteams von Skydio setzen auf den SLA-3D-Drucker (Stereolithografie) Form 3+ von Formlabs, um in der Prototypingphase der Produktentwicklung so nah wie möglich an das endgültige Design für die Massenfertigung heranzukommen. Die Drucker vom Typ Form 3+ bewältigen alles von Funktionstests bis hin zu Werkzeug und Halterungen, dank der erheblichen Bandbreite an Materialien, die Formlabs bietet. Skydio bietet zwei Drohnentypen, die Skydio 2+ und die Skydio X2, eine leistungsstarke Drohne für Großunternehmen und den Verteidigungssektor. Darüber hinaus hat das Unternehmen das Skydio Dock herausgebracht, ein neues, innovatives Produkt, mit dessen Hilfe Drohnen an weit abgelegene Standorte entsendet werden können und das ohne menschliche Interaktion oder Überwachung Informationen überträgt.
Eric Weinhoffer, Senior Hardware Development Specialist bei Skydio, hat sich mit uns über den Design- und Produktionsprozess des Unternehmens unterhalten und erklärt, wie der 3D-Druck dem Hardware-Team dabei hilft, mit Skydios fortschrittlicher Softwareentwicklung Schritt zu halten.
Wie Skydio sich abhebt
In den Anfangstagen der Drohnenindustrie benötigten unbemannte Flugsysteme bzw. Luftfahrzeuge (UAV, für engl. unmanned aerial vehicle) einen Piloten, der das System aus der Ferne steuerte. Um eine verlässliche Verbindung herzustellen, musste der Pilot sich in physischer Nähe zur Drohne befinden, was deren Reichweite und Effektivität einschränkte. In den vergangenen paar Jahren haben Drohnenhersteller begonnen, ihre Systeme um bestimmte autonome Funktionen zu ergänzen, wodurch sie neue Anwendungsfälle erschließen und eine umfangreiche Informationsaufnahme durch die Drohnen möglich machen.
Skydio ist an der Konkurrenz vorbeigezischt, indem es sich zuerst auf die Softwareentwicklung konzentrierte – das Unternehmen führte ein vollkommen autonomes Flugsystem ein. „In der Vergangenheit erforderte die Steuerung dieser Drohnen sehr viel Können. Mit konventionellen Drohnen hatte man immer viele Abstürze, oder ein sehr minderwertiges Video. Unsere Drohnen stürzen nicht ab – sie liefern nicht nur die perfekte Aufnahme, sondern sie weichen auch Bäumen aus, navigieren intelligent und können Subjekte automatisch verfolgen. Wir sind im autonomen Fliegen weltweit führend“, so Weinhoffer.
Ein solcher Grad an Autonomie eröffnet eine völlig neue Vielfalt an Möglichkeiten für den Drohneneinsatz. Behörden für öffentliche Sicherheit können mit ihrer Hilfe Unfallstellen oder Tatorte überwachen, um Vorfälle digital zu rekonstruieren – und zwar ohne für die Kontrolle der Drohne Arbeitskräfte aufwenden zu müssen oder Dienstleister zu engagieren. Versorgungsunternehmen, Bauunternehmen und staatliche Agenturen nutzen die Drohnen von Skydio für umfassende Inspektionen ihrer Standorte und können Drohnen von einem fest installierten Dock entsenden – so richten sie ohne zusätzliche Ressourcen eine nahezu ununterbrochene Überwachung ein. Weil es bei diesen Anwendungen oft um schwer zugängliche Bereiche geht, müssen die Drohnen von Skydio robust und gut durchdacht sein. Der SLA-3D-Druck erlaubt es dem Unternehmen, sich so nah wie möglich an das endgültige spritzgegossene Bauteil anzunähern, wenn die Anforderungen an die Prototypen geprüft werden.
Ständige Kompromisse bei Gewicht, Geschwindigkeit und Reichweite
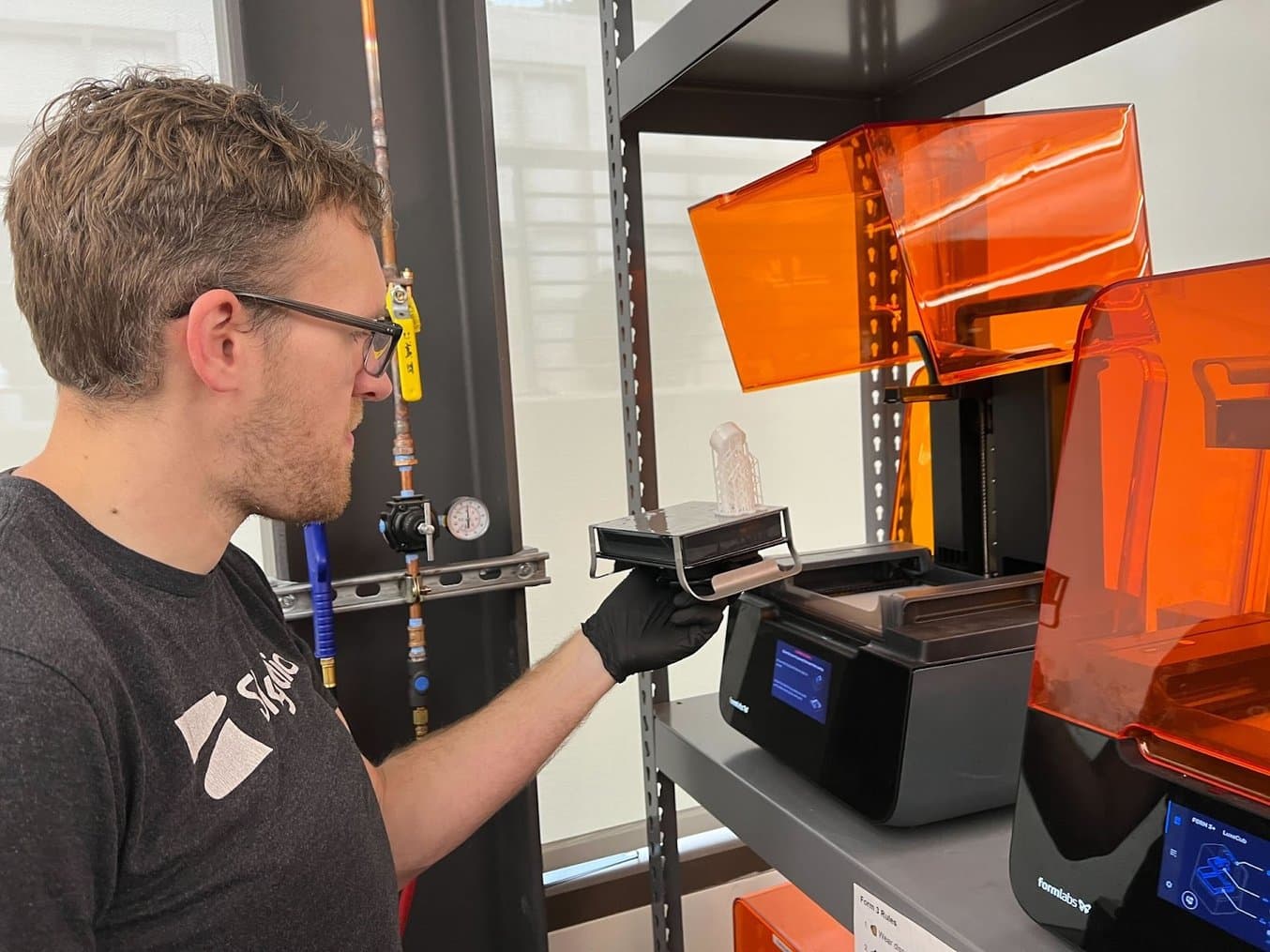
Weinhoffer und das für die Hardwareentwicklung zuständige Team stützen sich auf die Drucker vom Typ Form 3+ und eine Vielzahl von Formlabs-Kunstharzen, um mit dem rasanten Entwicklungsprozess von Skydios Software-Team mitzuhalten. Foto mit freundlicher Erlaubnis von Skydio.
Beim Drohnendesign muss man sich im Schließen von Kompromissen üben. Robust gebaute Drohnen können nicht so lange fliegen wie leichte. Sehr leichte Drohnen können die Rechenleistung nicht tragen, die für den autonomen Betrieb nötig ist – werden aber sämtliche notwendige Rechenkomponenten für das autonome Fliegen eingebaut, erhöht das die Masse und beeinflusst damit die Flugzeit. Es ist eine ewige Kette leichter Designänderungen, minimaler Anpassungen und ausgiebiger Tests. „Wir laden sehr viel Datenverarbeitungsleistung an Bord, um das autonome Fliegen zu unterstützen. Jede Entscheidung bedeutet Abstriche bei der Leistung, was jede Komponente der Hardware und Elektronik beeinflusst.“
Um kleine Änderungen an der Geometrie von Komponenten vorzunehmen und zu testen, wie diese die Flugzeit oder Stoßfestigkeit beeinflussen, zählt das Team auf den Druck über Nacht, auf den sich der Entwicklungsprozess stützt.
„Die Schnelligkeit des 3D-Drucks versetzt uns in die Lage, bestimmte Kompromisse in Betracht zu ziehen. Wir können zwei leicht unterschiedliche Geometrien miteinander vergleichen und ihre jeweiligen Nachteile testen.“
Eric Weinhoffer, Senior Hardware Development Specialist
Dass Skydio in der Lage ist, diese Entscheidungen und Prüfprotokolle schnell zu durchlaufen, hat es dem Unternehmen erlaubt, Fristen einzuhalten und sich Aufträge zu sichern. Für ein Großprogramm der US-Regierung meldeten sich zahlreiche Drohnenhersteller auf eine offene Ausschreibung. Die Bewerber mussten einen strengen und kompetitiven Zeitrahmen einhalten, um Produkte vorzustellen, die den Anforderungen der Regierung gerecht wurden. Skydio gelang es, die Ausschreibung zu gewinnen – dank seines schnellen Tempos bei der Hardwareentwicklung, das das Unternehmen zum Teil seinen Formlabs-Druckern verdankt.
„Wir hatten keinerlei Kontrolle über die Frist, und es war entscheidend, dass wir Hardware und Software zusammen entwickeln. Die Durchlaufzeiten zur Produktion der Bauteile bedeuteten für uns das größte Hindernis. Sofort nahmen wir den Form 3+ in Dauerbetrieb, und damit wurde es sehr einfach. Wir hatten die Hardware, die wir brauchten, direkt parat“, erzählt Weinhoffer.
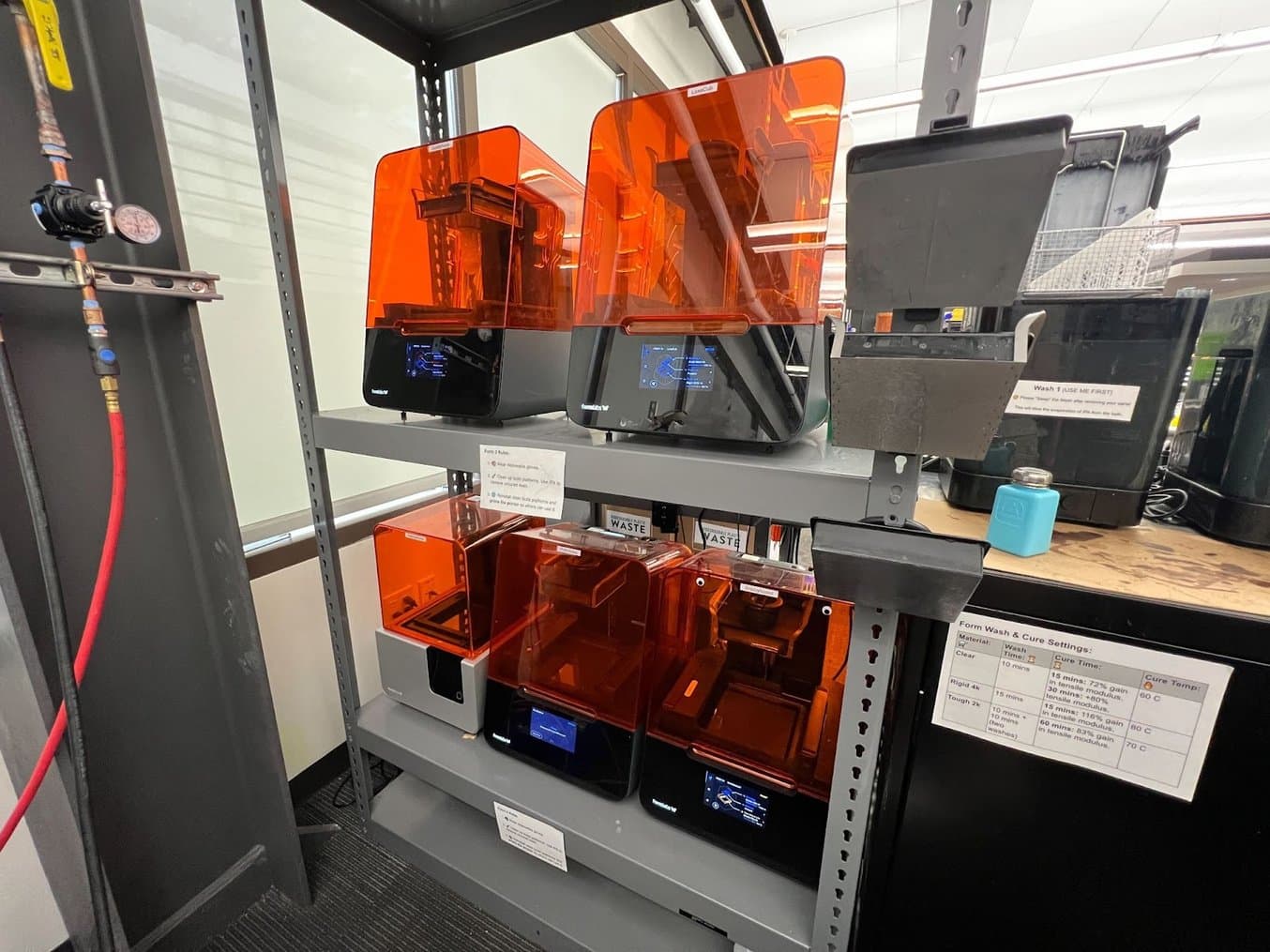
Das Hardware-Entwicklungsteam von Skydio hält seine SLA-Drucker leicht zugänglich bereit, damit sie dauerhaft in Betrieb bleiben können und das Team so dabei unterstützen, konstant Prototypen zu erstellen und zu testen. Foto mit freundlicher Erlaubnis von Skydio.
Finale Designs und Funktionstests
In externen Testszenarien wie im Fall der staatlichen Ausschreibung können provisorische 3D-gedruckte Teile dazu dienen, die Robustheit und Haltbarkeit sowie Festigkeit und Steifigkeit von Spritzgussteilen und zerspanten Teilen zu simulieren, was von kritischer Bedeutung ist. Skydio benutzt für schnelle Prüfungen von Form und Passung zwar auch Teile aus FDM-3D-Druckern (Schmelzschichtung), doch für die Funktionstests der finalen Prototypendesigns verlässt sich das Team auf die Geräte von Formlabs. „SLA ist hilfreich, denn hier zählen Schnelligkeit und die Fähigkeit, sich so nah wie möglich an das Produktionsbauteil anzunähern, in möglichst kurzer Zeit. Dass wir Teile erhalten, die den Eigenschaften des Produktionsmaterials so nahe kommen, ist unglaublich“, meint Weinhoffer.
Skydio verwendet Rigid 4000 Resin wegen seines Gleichgewichts zwischen Hitzebeständigkeit, Schlagfestigkeit und Festigkeit, und Tough 2000 Resin aufgrund seiner Ähnlichkeit zu spritzgegossenen Kunststoffen. Die transparente Optik von Clear Resin ist essenziell für den Einsatz in der Inspektionsphase, um zu erkennen, wie die Kabel innerhalb der elektroniklastigen Drohnen verlaufen. Für die schnelle Fertigung von Werkzeug oder funktionale Tests neuer Dichtungsdesigns greift das Team auf Elastic 50A Resin oder Durable Resin zurück.
„Die Formlabs-Teile haben direkt nach dem Druck die Optik und Haptik von massiven Gussteilen. Die Tatsache, dass wir nah an das endgültige Produktionsteil herankommen, ist ein immenser Vorteil. Wenn man das auf weitere Aspekte wie Passung und Oberflächenfinish überträgt, erhalten unsere Designer einen besseren Eindruck davon, wie sich ein Teil verhalten wird, oder sie können die Masse eines Teils in den Händen fühlen und Fallprüfungen oder Prototyp-Flüge durchführen. Die Teile geben uns die Sicherheit, sie in Flugtests einzusetzen.“
Eric Weinhoffer, Senior Hardware Development Specialist
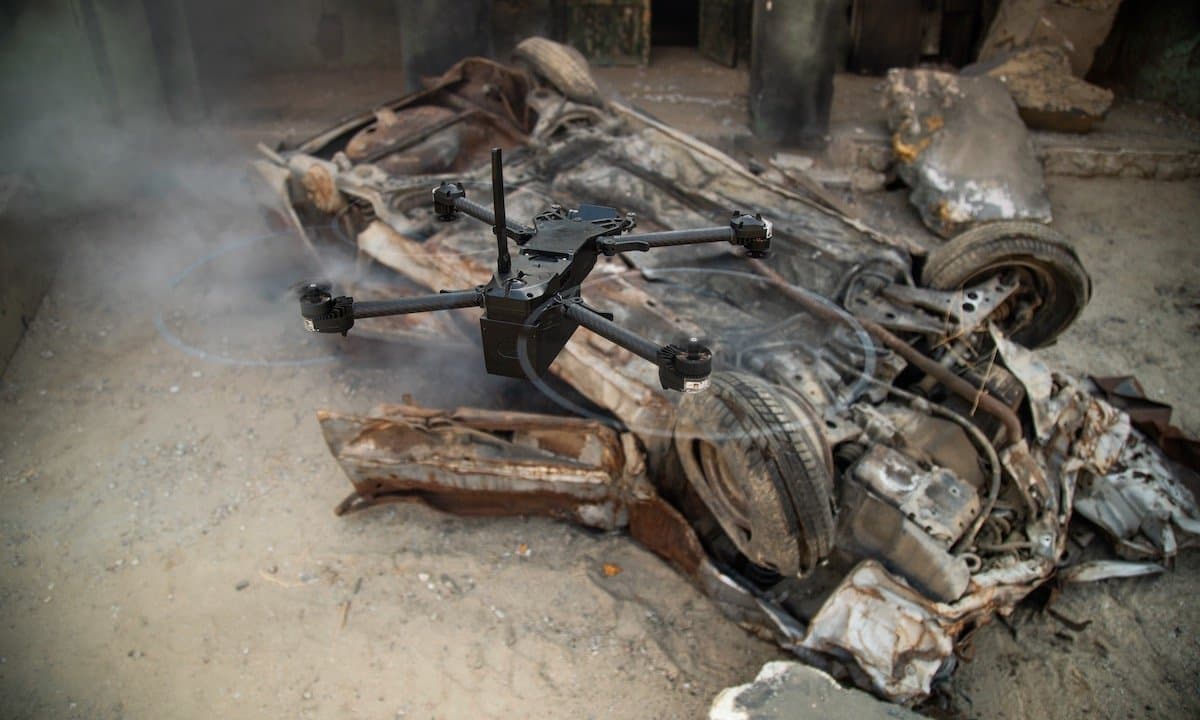
Rapid Tooling und Fertigungshilfen für große und kleine Zulieferer
Erfahren Sie in unserem Webinar, wie die additive Fertigung von Zulieferern der Luftfahrt für mehr als nur Rapid Prototyping eingesetzt wird. 3D-gedruckte Werkzeuge, Halterungen und Vorrichtungen verhelfen Unternehmen jeder Größenordnung dazu, Zeit und Kosten zu sparen und bessere Produkte auf den Markt zu bringen. Lernen Sie von Formlabs-Experten bewährte Fallstudien kennen, die die Grenzen der Luft- und Raumfahrt und der Fertigung ausweiten.
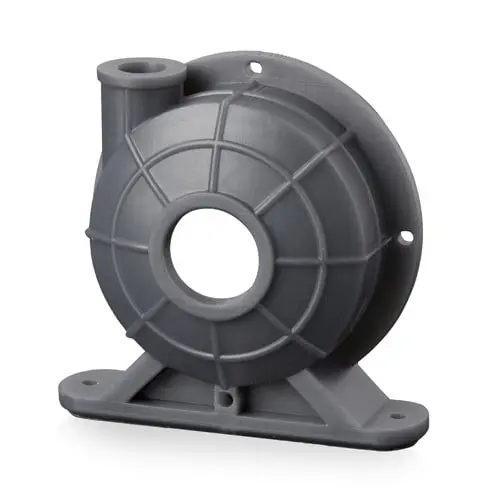
Kostenlosen Probedruck anfordern
Sehen und fühlen Sie die Qualität von Formlabs aus erster Hand. Wir senden Ihnen einen kostenlosen Probedruck an Ihren Arbeitsplatz.
Haltevorrichtungen für Funktionstests
Festigkeit ist sowohl für Prüfvorrichtungen als auch für im Fluggerät verbaute Teile entscheidend. Das Team entwickelt Testvorrichtungen für Drohnenkomponenten auf den Druckern des Typs Form 3+, wobei es von der mechanischen Festigkeit von Rigid 4000 Resin und der Schlagfestigkeit von Tough 2000 Resin profitiert.
Während der Radiofrequenz-Prüfphase im Zuge der Drohnenentwicklung platziert das Team Drohnenkomponenten in einer Antennenmesskammer, die externe Radiowellen abschirmt. Dafür war eine starke Haltevorrichtung nötig, die die Teile auf einem robotischen Drehteller fixiert. Diese durfte nicht aus Metall sein, um den Versuch nicht zu beeinträchtigen. Weinhoffer entwarf eine Vorrichtung, die aus Rigid 4000 Resin 3D-gedruckt und an der Kammer befestigt wurde, wo sie die Antennen in der richtigen Ausrichtung für den Versuch hält.
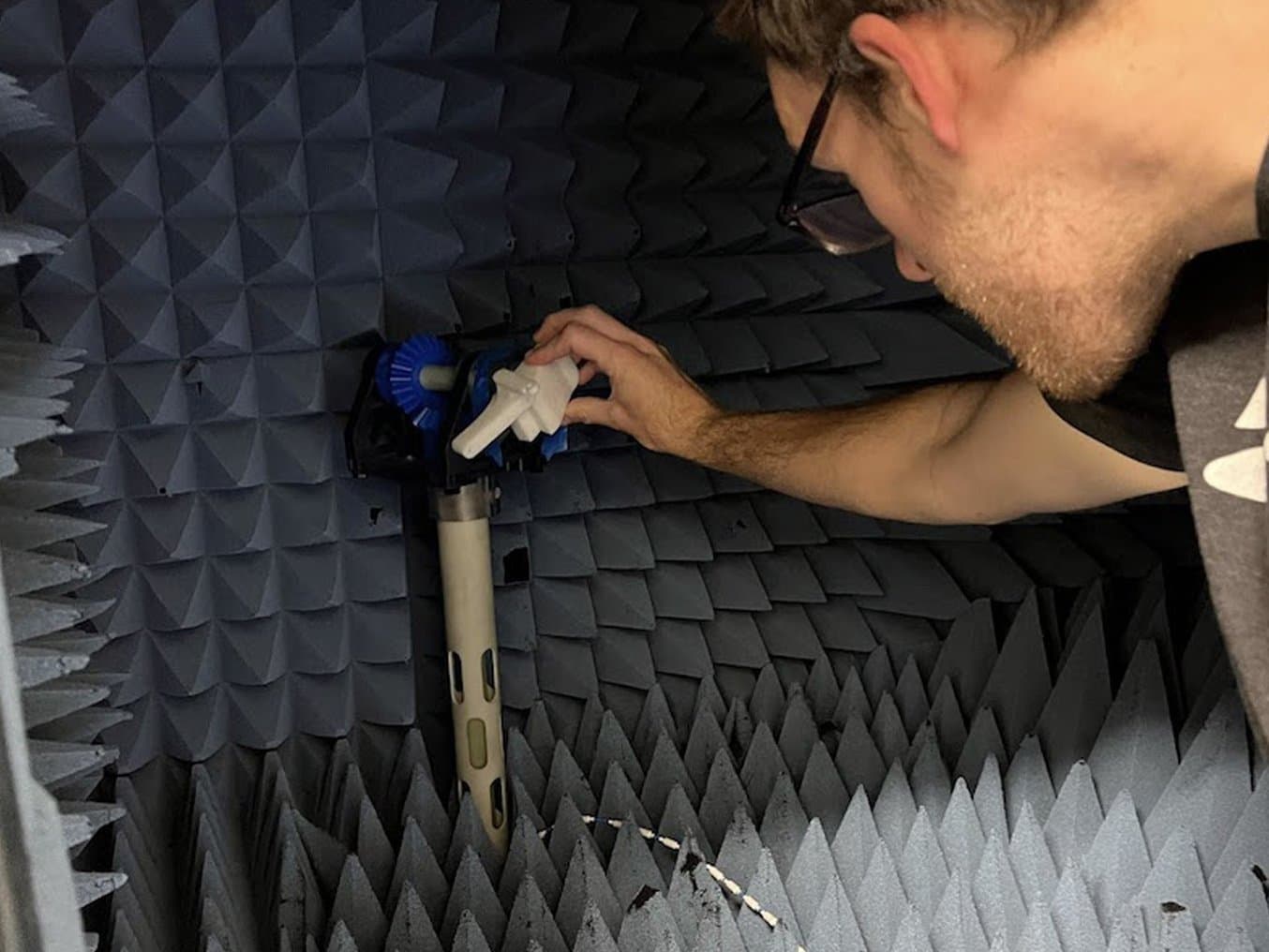
In einer Radiofrequenz-Kammer werden die endgültigen Teile durch 3D-gedruckte Vorrichtungen in Position gehalten. Metallhalterungen sind teuer und würden zudem die Radiofrequenztests beeinträchtigen. Deshalb sind auf Abruf verfügbare 3D-gedruckte Teile wie dieses Teil aus Rigid 4000 Resin unerlässlich. Foto mit freundlicher Erlaubnis von Skydio.
In einem anderen Fall brauchte das Team eine Lösung zur betriebsinternen Prototypenerstellung für Vibrationsisolatoren aus Gummi, denn Variationen dieser weichen Komponenten von Zulieferern anzufordern wäre teuer und zeitaufwendig gewesen. Inspiriert von einem Whitepaper von Formlabs druckte das Hardware-Entwicklungsteam mehrere Urformen, die eingesetzt wurden, um die Vibrationsisolation verschiedener Designs zu testen.
„Der weitaus größte Vorteil ist die Bandbreite an Materialien und Materialeigenschaften bei den Formlabs-Kunstharzen.“
Eric Weinhoffer, Senior Hardware Development Specialist
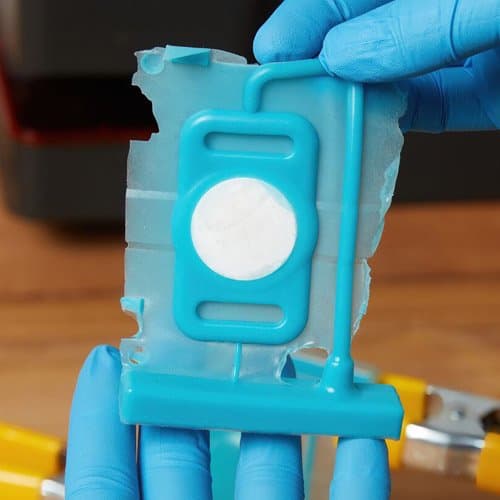
Herstellung von Silikonteilen mit 3D-gedruckten Werkzeugen
Dieser Bericht bietet eine schrittweise Anleitung zu 3D-gedruckten Formwerkzeugen für die Produktion von Silikonteilen, einschließlich bewährter Praktiken und Fallstudien von Kunden.
Weitläufiger Einsatz dank Benutzerfreundlichkeit
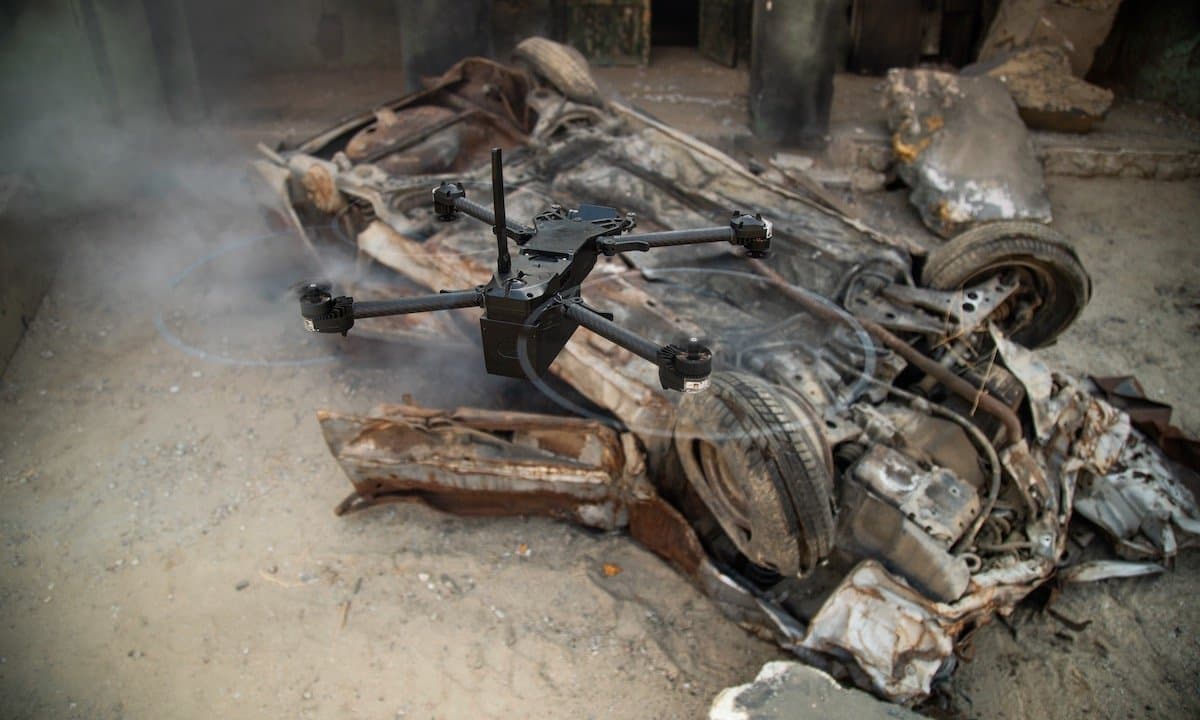
Drohnen helfen öffentlichen Sicherheitsbehörden dabei, Informationen von Unglücksstellen oder Tatorten zu sammeln, ohne ihre Mitarbeitenden zu gefährden.
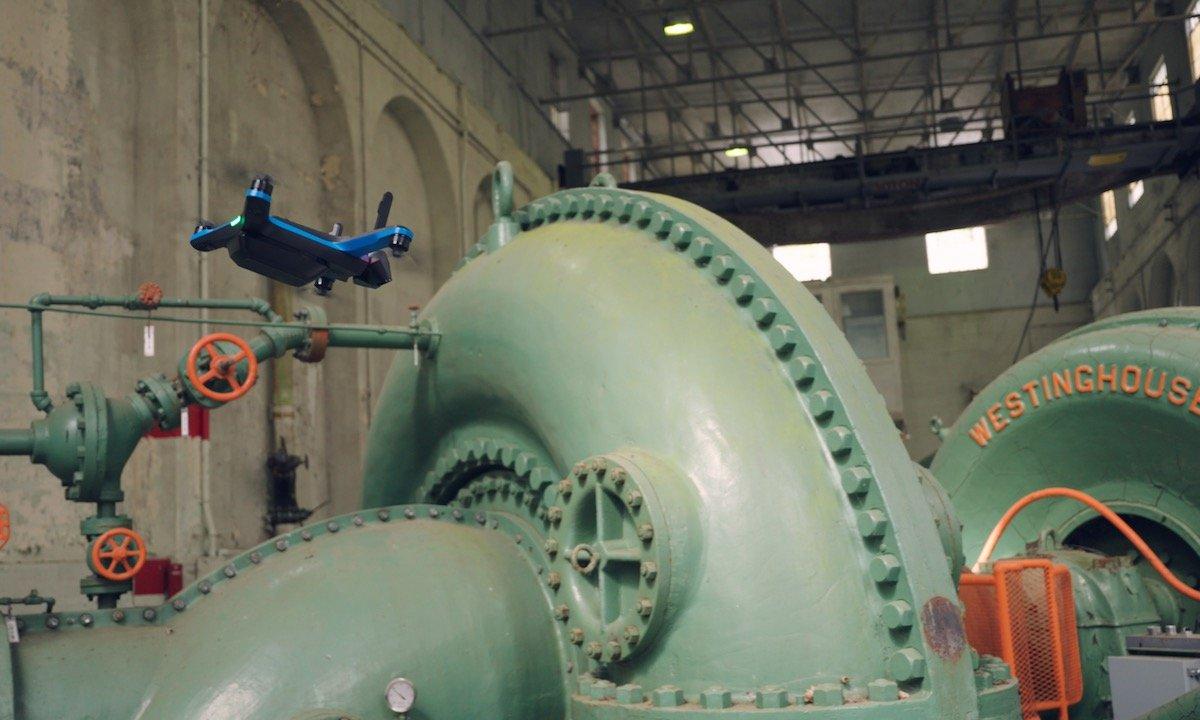
Ausrüstung für die Stromerzeugung befindet sich häufig in schwer zugänglichen Bereichen, doch die Drohnen und Docks von Skydio unterstützen Unternehmen dabei, ihre kritische Infrastruktur zu untersuchen, ohne Personal in der Nähe haben zu müssen. Fotos mit freundlicher Erlaubnis von Skydio.
Ein Grund dafür, weshalb Skydio eine so große Bandbreite von Branchen und Kunden anspricht, ist die Zugänglichkeit und Benutzerfreundlichkeit seiner Produkte – die autonome Flugfunktion ist fortschrittlich genug, um eine Drohnenentsendung frei von Sorgen und Planung zu ermöglichen. Die Strafverfolgung kann sich so statt auf das Fliegen darauf fokussieren, Informationen von Tatorten zu sammeln, und Bauunternehmen können für jahrelange Projekte eine Drohne und ein Dock einsetzen, ohne sich Gedanken über Lücken bei der Inspektion machen zu müssen. Dieselbe Philosophie verfolgt Weinhoffer auch beim 3D-Druck: Wenn eine Technologie nicht zugänglich ist, dann hat sie im Labor keinen großen Wert. „Die Formlabs-Drucker sind so einfach zu verwenden und so viele Mitglieder unseres Ingenieurteams können sie nutzen. Weitere Form 3+ hinzuzufügen und unseren Entwicklungsteams einen oder zwei Tage zusätzlich zu geben, in denen sie schnelle Fortschritte machen, das hat für uns einen riesigen Effekt“, so Weinhoffer.
Auf Skydios Pfad zu einer breiteren Produktpalette und zu stärker individualisierten Lösungen ist der 3D-Druck zu mehr als nur einem Hilfsmittel geworden – er hat es dem Hardware-Team möglich gemacht, mit dem halsbrecherischen Tempo der Softwareentwicklung Schritt zu halten.
Wenn Sie mehr darüber erfahren möchten, wie 3D-Drucker wie der Form 3+ es Herstellern in der Luftfahrt und Verteidigung ermöglichen, ihre Prozesse zu optimieren, wichtige Verträge zu sichern und die Kosten von Produktion und Entwicklung zu senken, dann besuchen Sie unsere Website rund um den Industriezweig oder kontaktieren Sie unser Expertenteam.