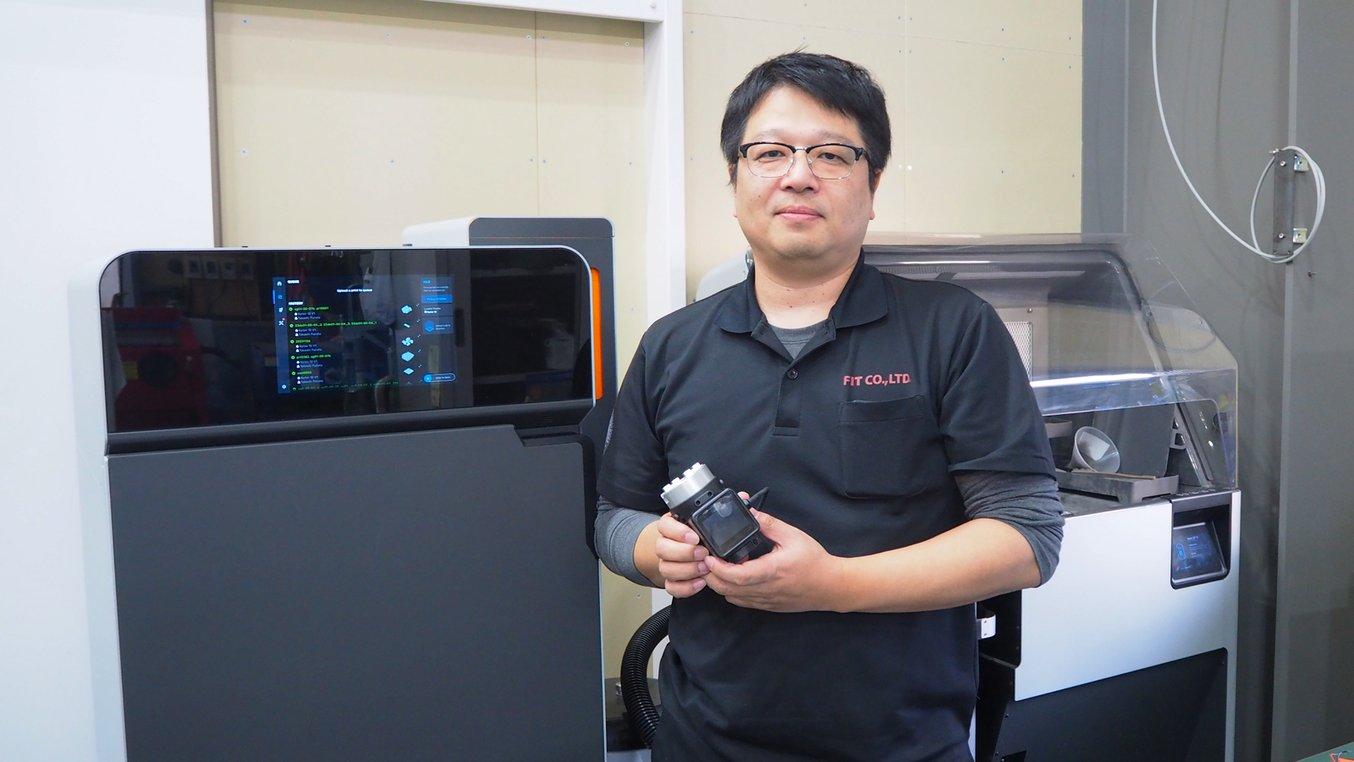
Der erfolgreiche Einsatz von Automatisierung – sowohl im Bereich Hardware als auch Software – ist der Schlüssel für Hersteller, die auf einem globalisierten und wettbewerbsintensiven Markt erfolgreich bleiben wollen.
Robotikanwendungen sind einer der komplexesten Faktoren in dieser Gleichung. Ihre Bauteile müssen stark genug sein, um das Gewicht der Produkte zu bewältigen, die sie handhaben, und gleichzeitig leicht genug, um sie zu manövrieren. Außerdem müssen Robotikkomponenten individuell hergestellt werden, um sicherzustellen, dass sie präzise mit Produkten unterschiedlicher Form umgehen können.
FIT Co. mit Sitz in Gifu, Japan, fand eine Lösung, die es dem Unternehmen ermöglichte, nicht nur erfolgreich Bauteile für Robotikanwendungen zu fertigen, sondern auch ein ganzes Geschäft rund um End-of-Arm-Tooling (EOAT) aufzubauen. ARMA, die neue Robotik-Abteilung von FIT, hat sich die einzigartigen Möglichkeiten der Technologie des selektiven Lasersinterns (SLS) der Fuse-Serie zunutze gemacht, um Bauteile für Robotikanwendungen herzustellen, die herkömmliches End-of-Arm-Tooling aus Metall nicht nur ersetzen, sondern auch verbessern können.
Anforderungen an End-of-Arm-Tooling
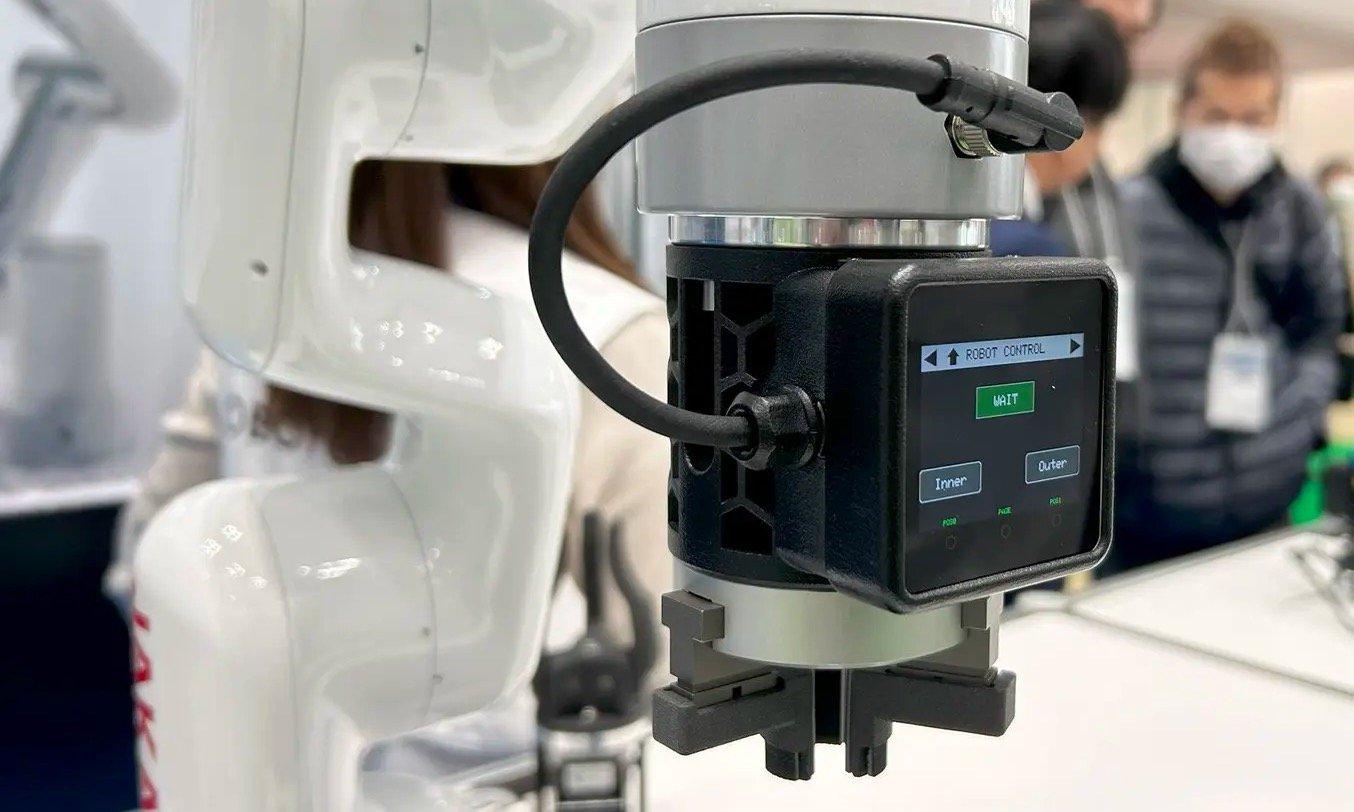
Diese Greiferkomponente, die ARMA mit dem SLS-3D-Drucker der Fuse-Serie aus Nylonpulver gedruckt hat, ist stark, robust und leicht. Mit 3D-Druck hergestellte End-of-Arm-Tooling-Komponenten wie dieser Greifer ermöglichen es Unternehmen, nach Bedarf Robotiklösungen für eine Vielzahl von Produkten mit unterschiedlichen Formen und Gewichten zu erstellen.
Da Online-Shopping und Vertriebsmodelle mit großen Lagerhäusern zum vorherrschenden Standard geworden sind, um Produkte zum Verbraucher zu bringen, stehen Pick-and-Place-Roboter heute besonders hoch im Kurs. Die breite Palette an Produkten – Hunderttausende verschiedener SKUs – kann jeweils unterschiedliche Gewichte, Formen und Verpackungen aufweisen, was eine Anpassung der Robotergreifer unabdingbar macht. Jedes einzelne Teil individuell zu entwerfen ist jedoch mit komplexen Konstruktionsarbeiten verbunden.
Obwohl sich die Branche der Robotik rasant entwickelt, stützt die sich bei allen Bauteilen, einschließlich End-of-Arm-Tooling, häufig noch auf traditionelle Verfahren der Metallverarbeitung. Roboter müssen schließlich stark und langlebig sein und über die nötige Geschicklichkeit verfügen, um Produkte unterschiedlicher Form und Größe zu greifen.
Mit herkömmlichen Fertigungsmethoden wie Zerspanung oder Guss ist es schwierig, diese Anforderungen zu erfüllen. Daher wird EOAT oft aus mehreren, miteinander verbauten Komponenten hergestellt. Je mehr Bauteile, desto mehr erhöht sich für Robotik-Hersteller jedoch auch das Risiko von Lieferkettenproblemen
Mit SLS-3D-Druck kann ARMA Bauteile mit größerer Designfreiheit gestalten. Dank des selbststützenden Pulverbetts der Drucker der Fuse-Serie können Teile ohne Stützstrukturen hergestellt werden und komplexe Formen wie Gitter, interne Kanäle, Wabenmuster oder generative Designs sind problemlos möglich. Durch die Nutzung dieser Designmöglichkeiten optimiert ARMA die Teile mit Fokus auf Leichtigkeit bei gleichzeitiger Festigkeit und Beweglichkeit.
Durch den Einsatz der Fuse-Serie und den 3D-Druck mit Nylon 12 Powder war ARMA in der Lage, das Gewicht von Greifern und Endeffektoren um 40 % zu verringern. Sowohl das Ersetzen von Bauteilen aus Metall durch Nylon als auch die Verwendung von wabenförmigen Strukturen in den Teilen trugen zum Erfolg der Teile bei. „Für die Greifer von ARMA ist die Festigkeit, die Nylon 12 Powder bietet, mehr als ausreichend“, so Takashi Furuta, Geschäftsführer von FIT und ARMA.
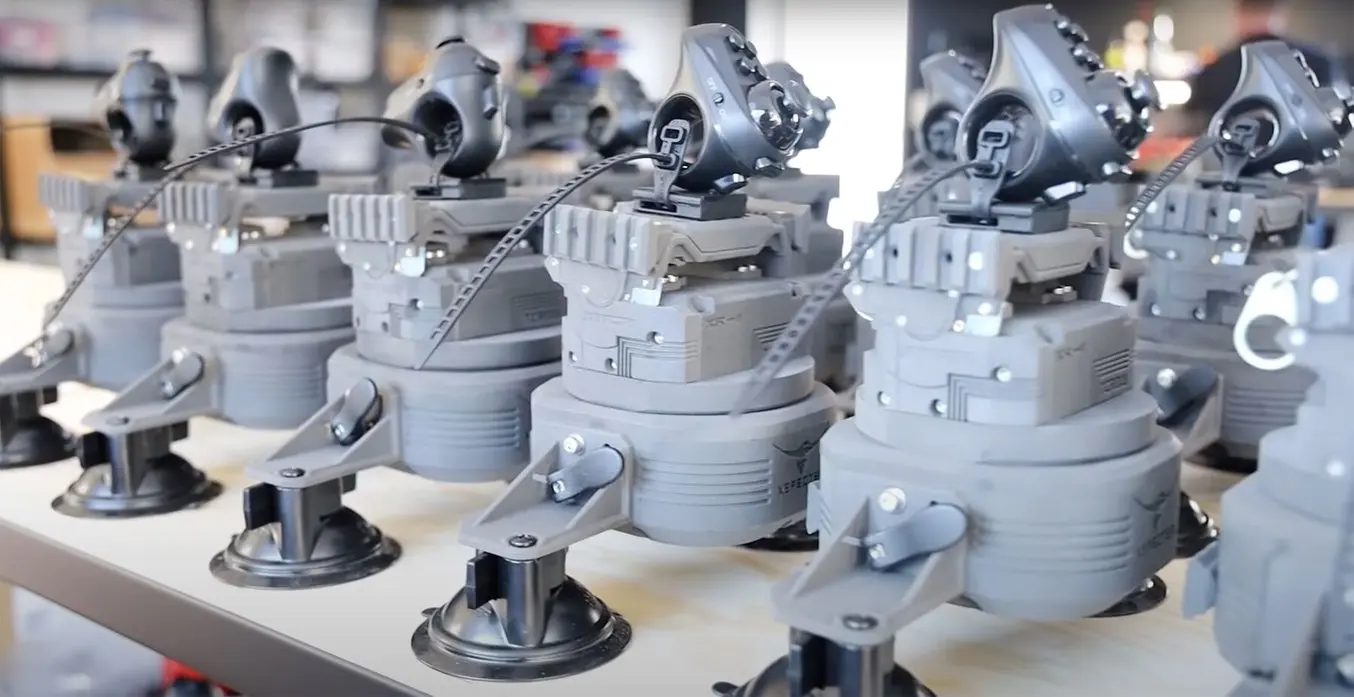
SLS-Produktion für die Endverwendung
3D-Druck für die Endverwendung ist nicht nur möglich, sondern dank des SLS-Ecosystems der Fuse-Serie auch noch erschwinglicher, agiler und leichter skalierbar denn je. Besuchen Sie unsere Seite zum Thema SLS für die Produktion und vergleichen Sie Produktionsverfahren, informieren Sie sich über unsere Mengenrabatte auf Pulver und entdecken Sie die Produktionsabläufe 15 verschiedener Hersteller, die derzeit die Fuse-Serie nutzen.
Die Vorteile eines multimethodischen Ansatzes
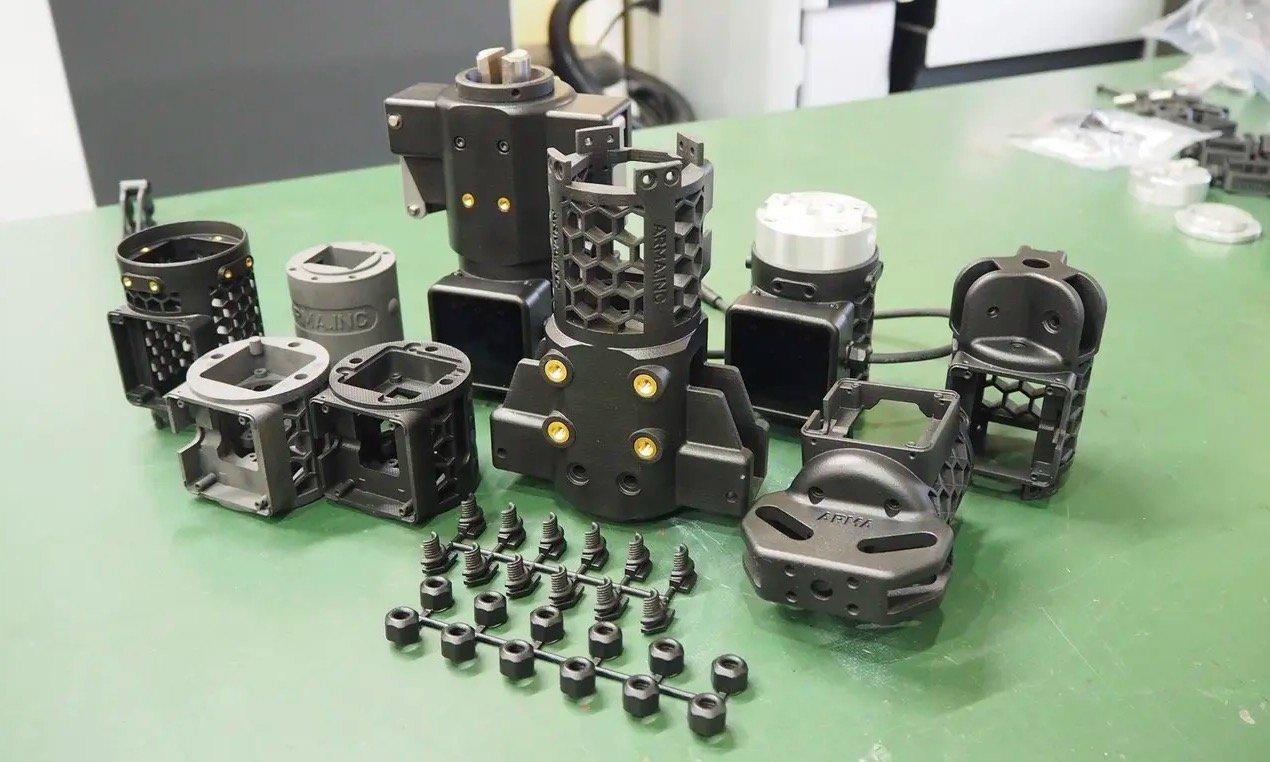
Diese Bauteile wurden von Furutas Team auf dem Fuse 1 aus Nylon 12 Powder gedruckt, und einige wurden chemisch dampfgeglättet, um ihre Ästhetik und Haltbarkeit zu verbessern und Produkte in Endproduktqualität zu erstellen.
Für Furuta war die Kombination traditioneller Fertigungsmethoden mit modernen Werkzeugen ein voller Erfolg. Seit 2016 ist der 3D-Druck in die Design- und Fertigungsprozesse seines Unternehmens integriert. Das Unternehmen produziert viele Metallbauteile und nutzt verschiedene 3D-Drucktechnologien. Dabei bringen die verschiedenen 3D-Druckverfahren unterschiedliche Vorteile mit sich. „Wir nutzen FDM für die schnelle Herstellung einzelner Teile. Für die Fertigung großer Stückzahlen verwenden wir den Fuse 1“, erläutert Furuta.
Als FIT im Jahr 2022 mit dem Druck auf der Fuse-Serie begann, erkannte Furuta, dass die Festigkeit und Oberflächenbeschaffenheit der fertigen SLS-Teile seinem Unternehmen neue Möglichkeiten eröffnen würde. „[Andere Technologien] können mit der Qualität von Fuse 1 nicht mithalten, insbesondere wenn es um Designfreiheit, Isotropie, Oberflächenbeschaffenheit und Festigkeit geht“, urteilt Furuta.
Dank der Maßgenauigkeit der Fuse-Serie ist das Design von Teilen für Baugruppen für Furuta eine Leichtigkeit, da er auf die Zuverlässigkeit und die konsistenten Toleranzen der Drucker vertrauen kann. Das Team kombiniert die im SLS-Verfahren gedruckten Bauteile aus Nylon 12 Powder mit herkömmlichen Metallkomponenten, um Robotiksysteme zu erstellen, die leichter sind als frühere Iterationen, aber dennoch extrem stark und robust – und das alles zu geringeren Kosten als bei herkömmlicher Bearbeitung.
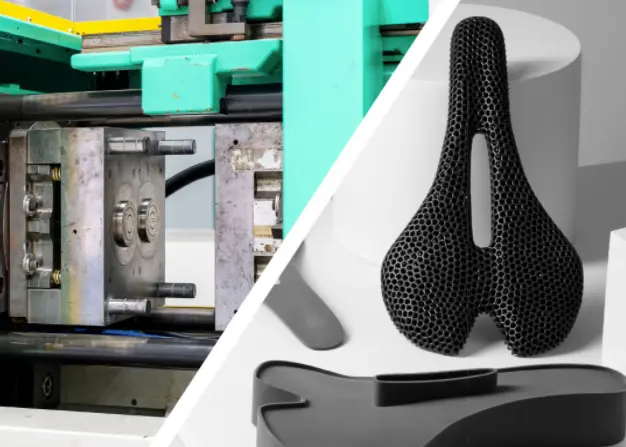
SLS-3D-Druck oder Spritzguss: Wann sollte man Spritzgussteile durch 3D-Druck ersetzen?
Dieses Whitepaper zeigt die Kostendynamik für Anwendungsfälle aus der Praxis und stellt Leitfäden vor für den Einsatz von SLS-3D-Druck, Spritzguss oder einer Kombination beider Verfahren.
Vapor Smoothing für ästhetische Qualität und einfache Montage
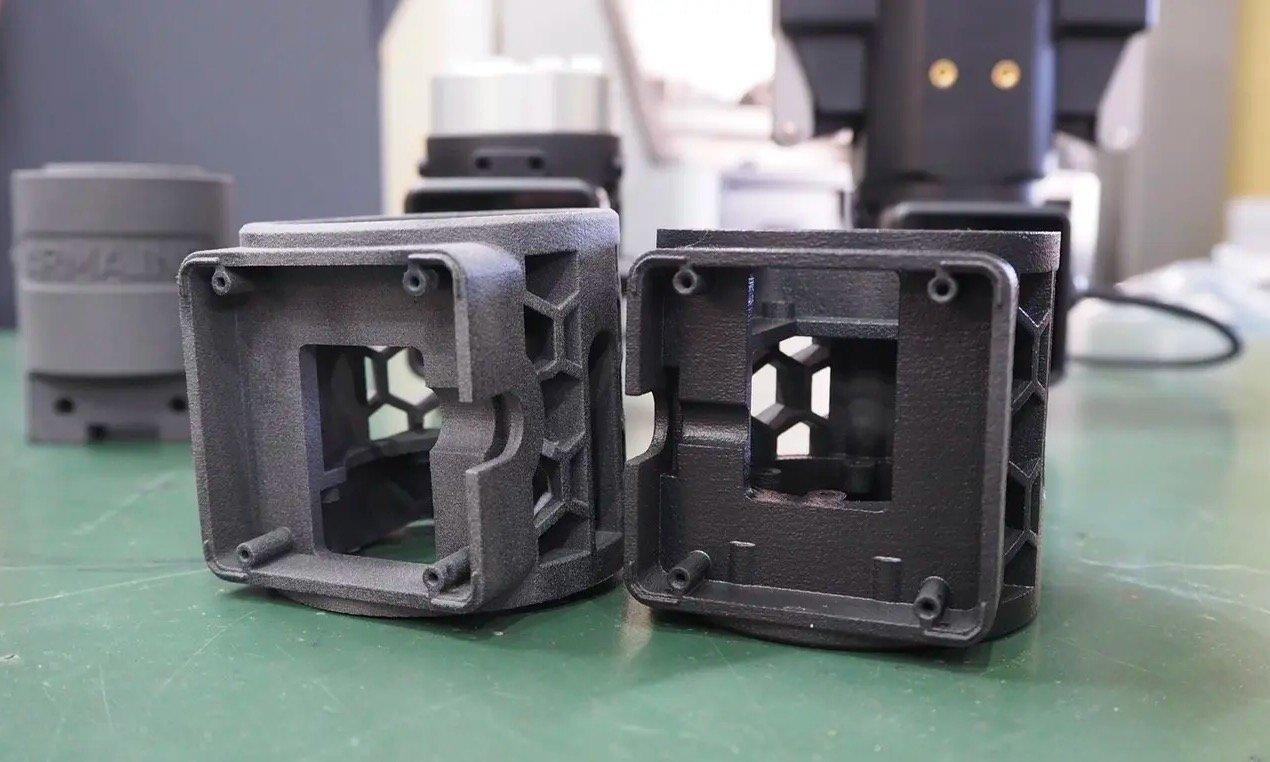
Vapor Smoothing oder chemische Dampfglättung kann die Oberflächenqualität von SLS-3D-Druckteilen verbessern und ihre Eignung für Endanwendungen verbessern, in denen sie Licht, Flüssigkeiten oder Chemikalien ausgesetzt sein können.
SLS-Teile sind hinsichtlich ihrer Festigkeit für den Endverbrauch geeignet, aber viele Kunden ziehen es vor, fortgeschrittene Nachbearbeitungsmethoden zu verwenden, um die Oberfläche der Teile zu verbessern und die mit der SLS-Technologie verbundene Oberflächenrauheit zu reduzieren.
ARMA nutzt dafür Vapor Smoothing bzw. chemische Dampfglättung: eine Technik, bei der die Teile in ein verdampftes chemisches Lösungsmittel getaucht werden, welches das 3D-Druckmaterial kontrolliert chemisch schmelzt, winzige Hohlräume auffüllt und so eine glatte, glänzende Hülle um das Teil erzeugt. Der Glättungseffekt ist dabei nicht nur auf sichtbare Geometrien beschränkt, sodass dieses Verfahren sich auch für komplexe Teile mit internen Kanälen oder Vertiefungen gut eignet. ARMA verwendet die Anlage AMT PostPro SF50, um eine glatte Oberflächenbeschaffenheit zu erzielen, was es noch einfacher macht, Bauteile aus Nylon 12 Powder in Baugruppen zu integrieren.
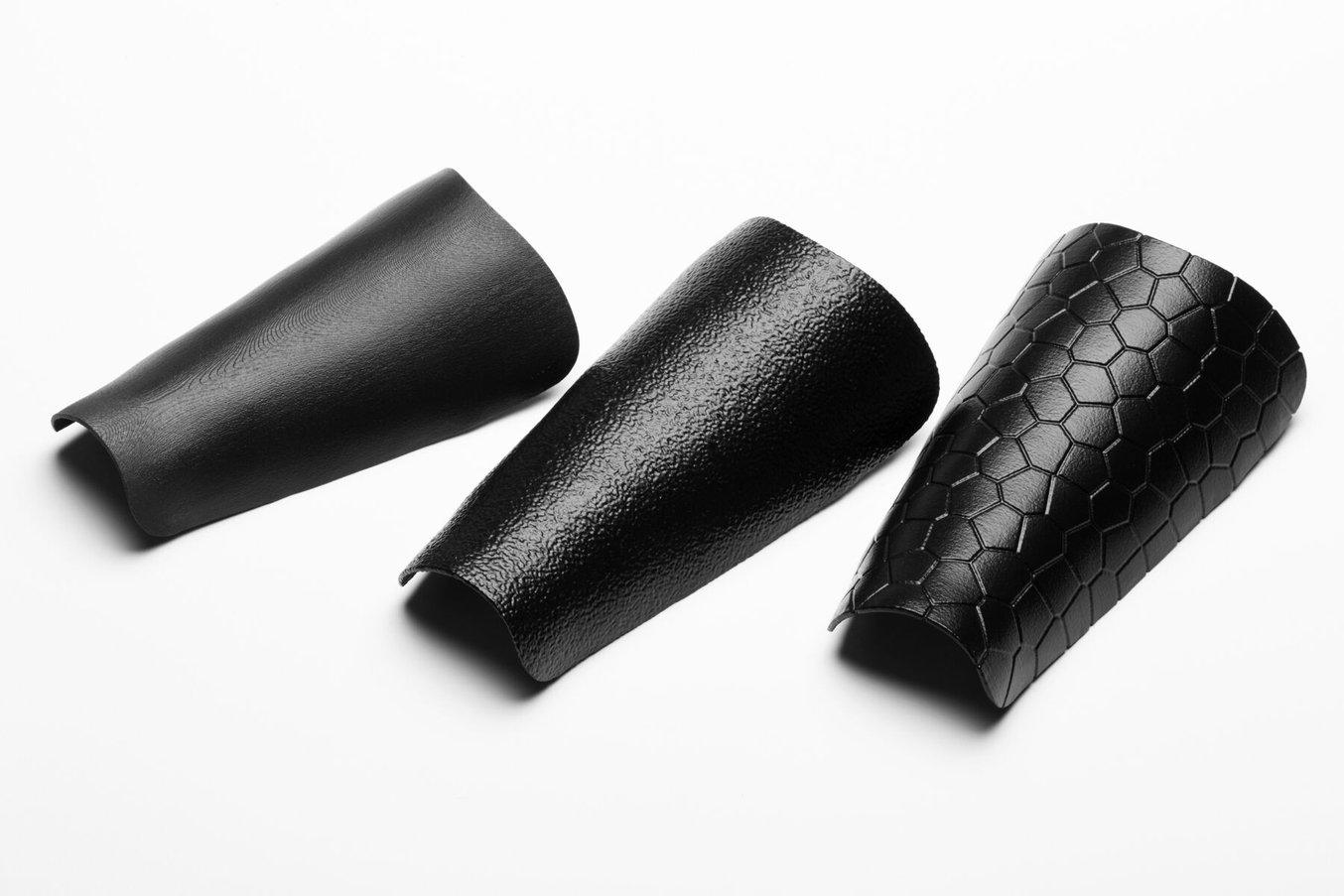
Steigerung der Oberflächenqualität von SLS-Druckteilen durch Dampfglättung: Eine gemeinsame Studie von Formlabs und AMT
In diesem Whitepaper untersuchen wir das Verfahren und die Vorteile des Dampfglättens bzw. Vapor Smoothing und demonstrieren Ergebnisse aus Tests mit Formlabs-SLS-Pulvern und der chemischen Dampfglättungsanlage von AMT.
Robustere Lieferketten durch weniger Einzelkomponenten
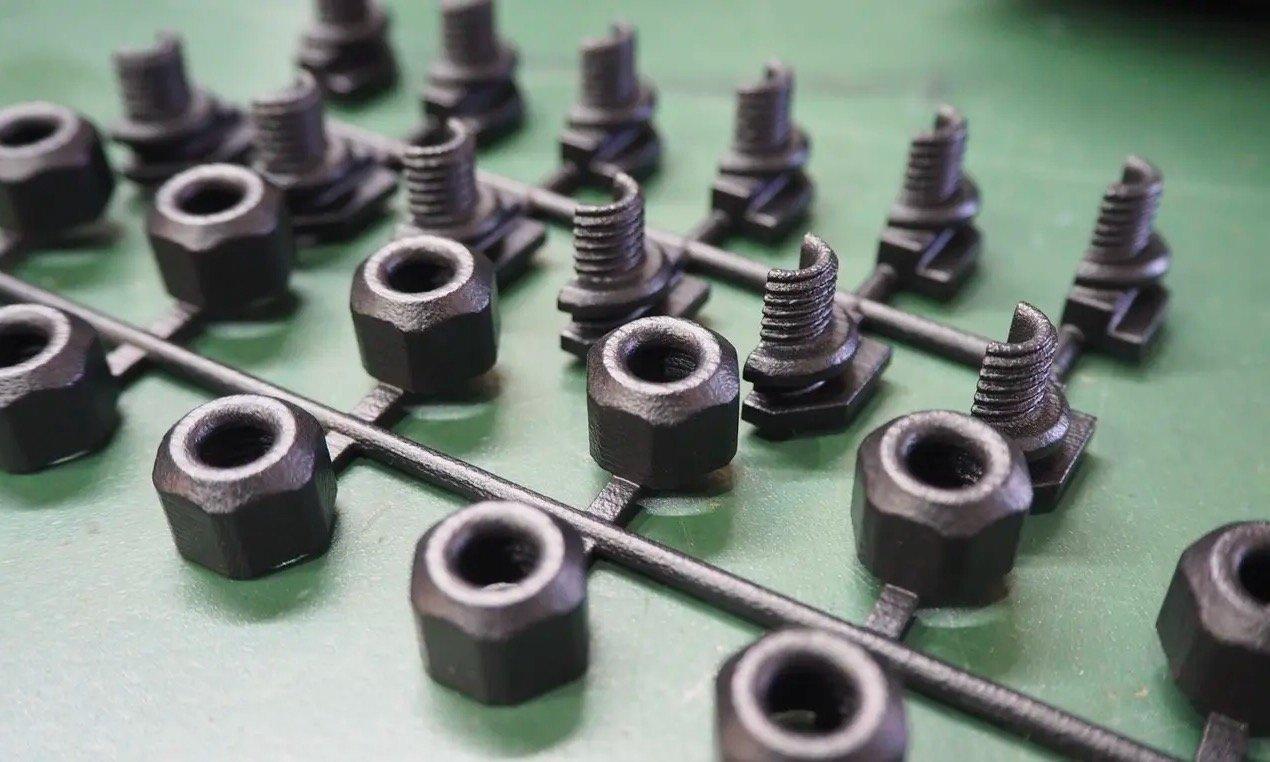
Da die Druckbetten von SLS-Druckern selbststützend sind, ist das kreative Design von einteiligen Lösungen ohne Montage kein Problem. Dadurch verringert sich die Abhängigkeit von externen Zulieferern von Einzelteilen und die Lieferkette von ARMA wird gestrafft und geschützt.
Durch die Begrenzung der Anzahl der Komponenten, aus denen End-of-Arm-Greifer oder sonstige Robotik-Bauteile bestehen, kann ARMA das Risiko von Engpässen in der Lieferkette mindern, die sich auf die Fertigung oder den Vertrieb seiner Produkte auswirken. Die Einführung des betriebsinternen 3D-Drucks mit der Fuse-Serie ist für ARMA eine Möglichkeit, die Kontrolle über die eigene Fertigung zu übernehmen. „Die Greifer und Endeffektoren, die wir auf dem Fuse 1 herstellen, sind so konzipiert, dass sie kundenspezifisch angepasst werden können, da die Bedürfnisse je nach Unternehmen und Produktionsstandort variieren“, erklärt Furuta. Wenn jede dieser kundenspezifischen Bestellungen die Montage mehrerer Bauteile und die Verwendung unterschiedlicher Materialien erfordert, können die Durchlaufzeiten für die Auftragserfüllung schnell aus dem Ufer laufen.
Das Fuse-SLS-Ecosystem ist kompakt, erfordert nur wenig Infrastruktur und kann in Büro- oder Fabrikumgebungen verwendet werden. Daher lässt sich die Produktionslösung problemlos in den eigenen Betrieb integrieren – selbst für Unternehmen wie ARMA, das seinen Kundenstamm gerade erst aufbaut. Für kleinere Produktionsvolumen, bei denen Massenfertigungsverfahren zu kostspielig und kompliziert wären, ist der SLS-3D-Druck die perfekte Lösung.
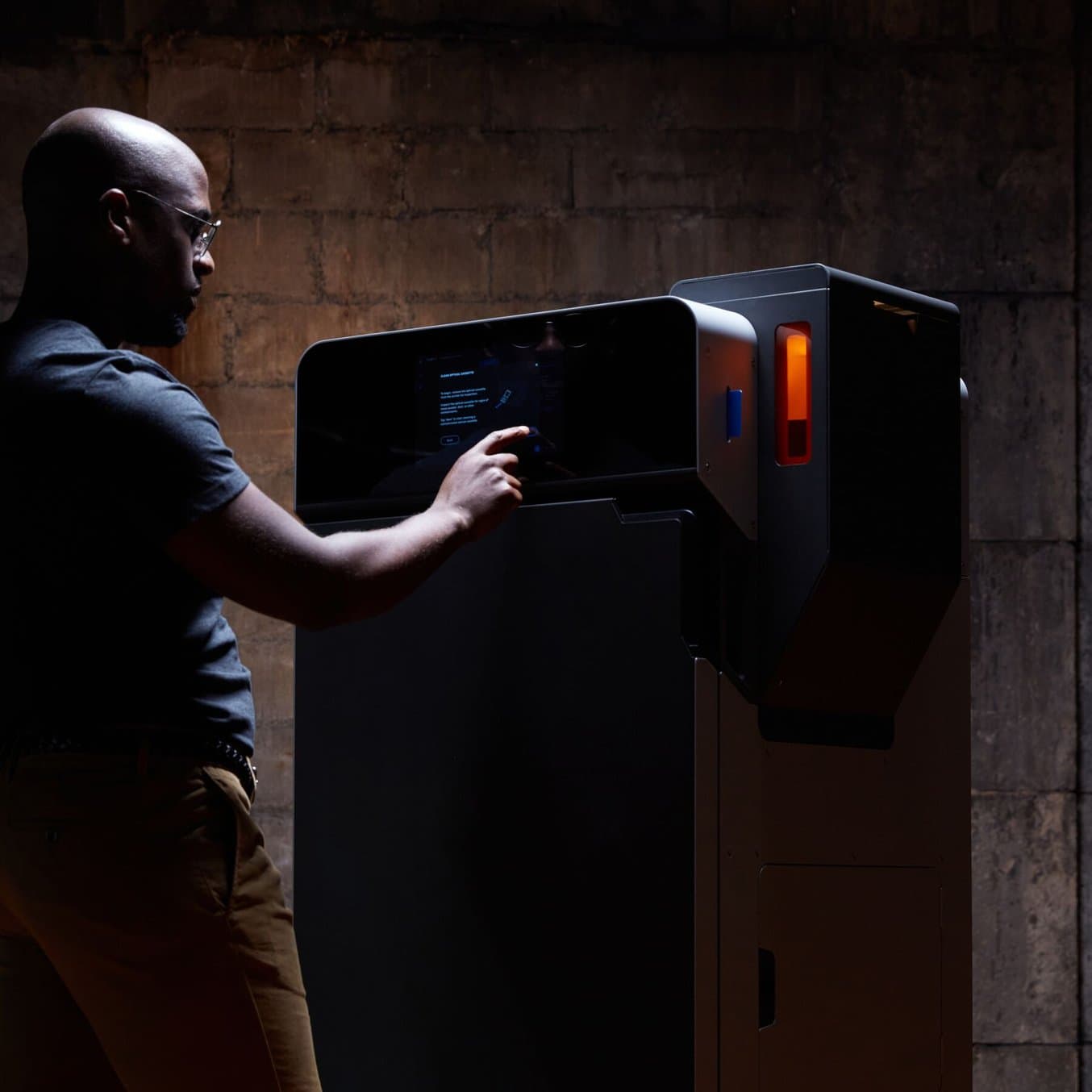
Outsourcing oder betriebsintern: Wann sollte man SLS-3D-Druck in den eigenen Betrieb holen?
In diesem Whitepaper untersuchen wir den Mehrwert betriebsinterner SLS-3D-Drucker im Vergleich zum Outsourcing von SLS-Teilen an einen Fertigungsdienstleister.
ARMA vereint Funktionalität und Ästhetik
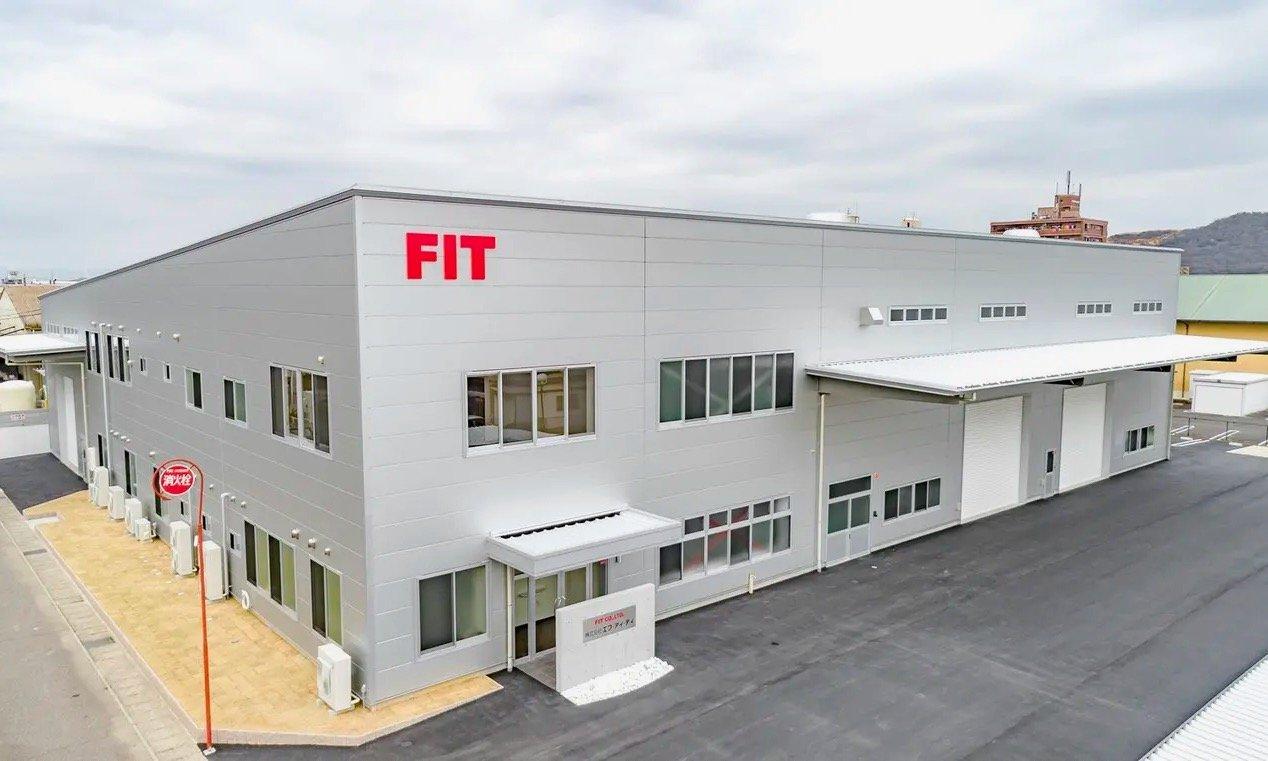
Die Integration der Fuse-Serie in seine Prozesse hat FIT zu einem so starken Wachstum verholfen, dass das Unternehmen in der Lage war, eine ganze Abteilung – ARMA – auf die Fertigung von End-of-Arm-Tooling zu spezialisieren.
Die Frage nach dem Fuse entlockt selbst dem eher zurückhaltenden Furuta ein Lächeln. „Es macht Spaß“, antwortet er schlicht. Das Durchbrechen von Design-Einschränkungen mit der SLS-Technologie und die effiziente industrielle Leistung des gesamten SLS-Ecosystems sind für Furuta, der stets bestrebt ist, klobige Bauteile in reibungslos integrierte und hochleistungsfähige Robotiksysteme zu optimieren, sehr attraktiv. Mit dem Fuse-Drucker will Furuta nach eigenen Angaben „die Funktionalität weiter verbessern und unnötige Funktionen eliminieren“.
Der SLS-3D-Druck erweitert die Grenzen des Machbaren in der Fertigung starker, langlebiger Endbauteile als Ersatz von Metallkomponenten. Indem Sie Produktionskapazitäten ins eigene Haus verlagern und Ihre Lieferkette selbst kontrollieren, werden Sie flexibler, risikoresistenter und besser positioniert, um neue Potenziale auszuschöpfen.
Sehen Sie sich Anwendungsbeispiele für 3D-Druck in der Fertigung an oder erfahren Sie mehr über die SLS-3D-Drucker und Nachbearbeitungslösungen der Fuse-Serie.