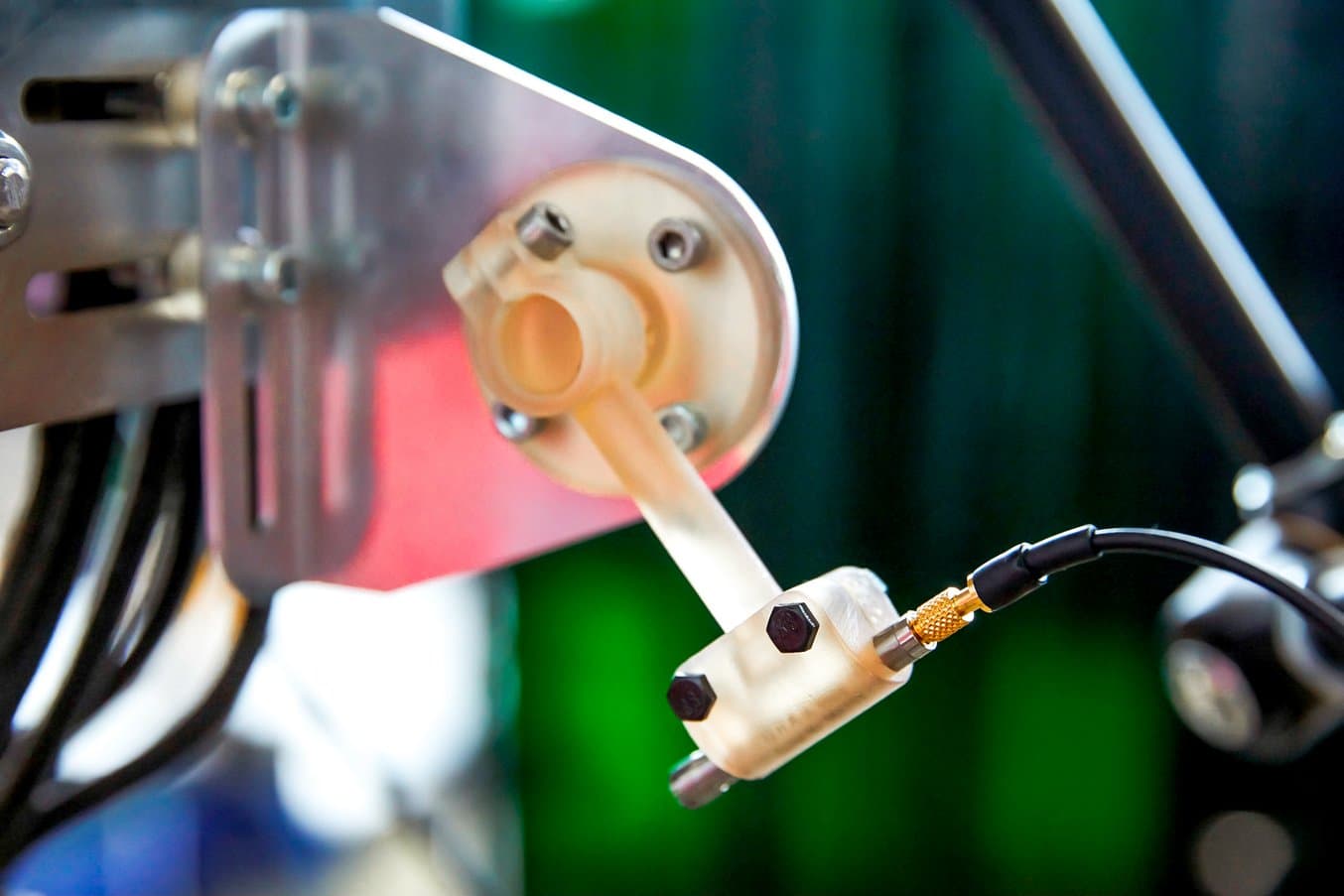
Das Nuclear Advanced Manufacturing Research Centre (Nuclear AMRC) ist ein gemeinsames Projekt von Hochschulen und Industrievertretern aus der gesamten Kernenergie-Lieferkette. In diesem Rahmen werden fortschrittliche Fertigungslösungen für die zivile Kernenergie erforscht, um britischen Herstellern bei Ausschreibungen im eigenen Land und weltweit zum Erfolg zu verhelfen.
Ein Projekt, an dem das Zentrum vor kurzem gearbeitet hat, ist die Entwicklung einer Roboterschweißlösung zum Schweißen von Druckbehältern im Kernenergiesektor. Dazu musste das Team mehrere Sensoren in die Ausrüstung für eine gefährliche Umgebung mit hohen Temperaturen integrieren.
Erfahren Sie von Matthew Smart, dem technischen Leiter des Projekts in der Bearbeitungsgruppe des Nuclear AMRC, wie das Team den 3D-Druck genutzt hat, um schnell verschiedene Designs zu iterieren, und dutzende Teile gefertigt hat, die hohen Temperaturen in der Nähe der Schweißnaht widerstehen.
Smart und das Ingenieurteam arbeiteten an der frei zugänglichen additiven Fertigungsstation des AMRC, um die erforderlichen Teile herzustellen. Lesen Sie unsere Fallstudie, um zu erfahren, wie der freie Zugang zu 3D-Druck hunderten von Ingenieuren an einem Standort helfen kann.
Wieso das Schweißen von Behältern in der Kernindustrie Monate dauern kann
Aktuelle Methoden zum Schweißen von Druckbehältern erfordern häufige Haltepunkte für die manuelle Inspektion, wozu Komponenten mehrfach abgekühlt und wieder erwärmt werden müssen. Es ist ein zeitaufwändiger Prozess; ein großer Behälter kann Monate in Anspruch nehmen. Mit dem Projekt des Nuclear AMRC soll diese Durchlaufzeit durch die Entwicklung eines Robotersystems reduziert werden, das Fehler im laufenden Prozess erkennen kann, sodass der Schweißvorgang nur angehalten werden muss, wenn tatsächlich ein Fehler auftritt.
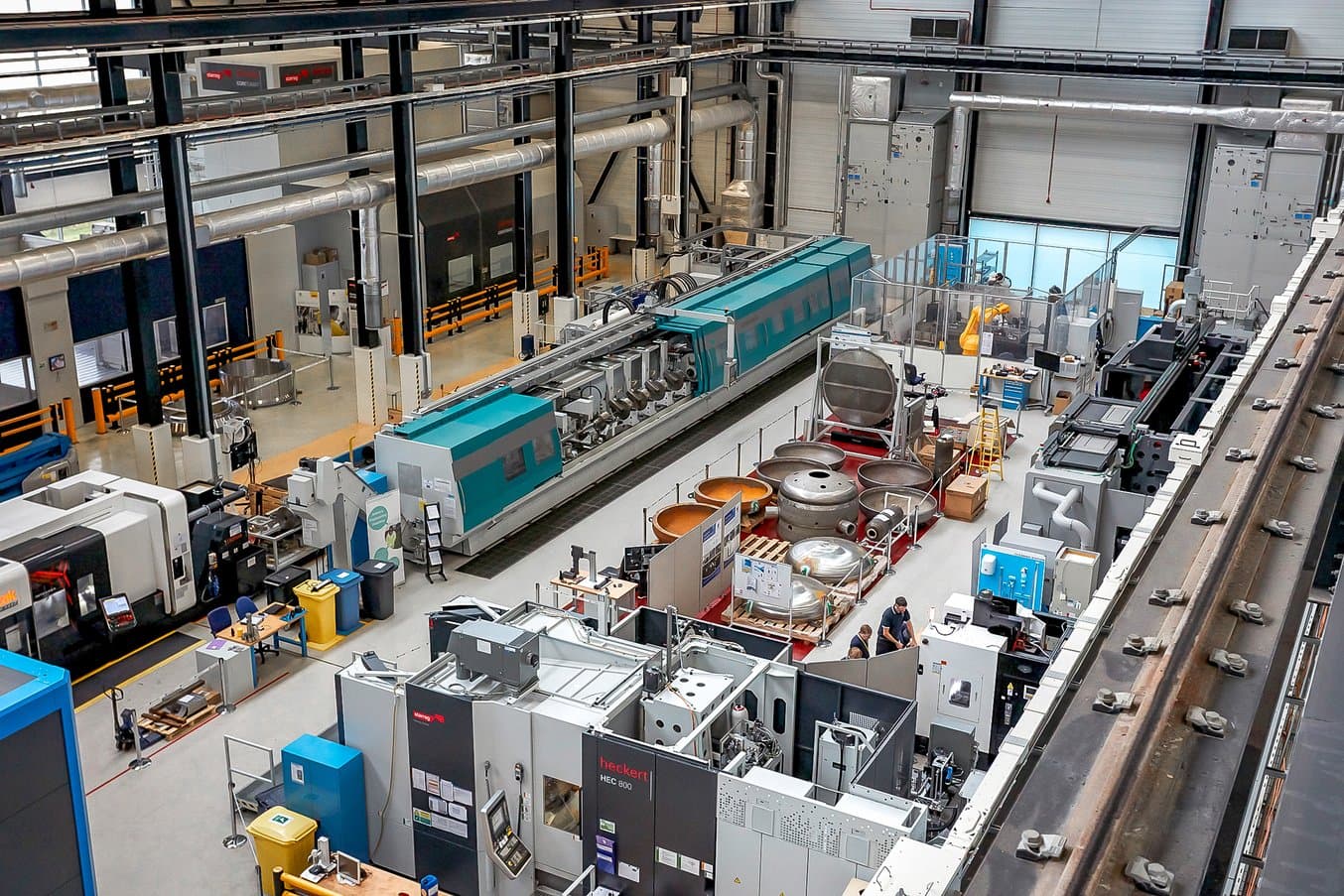
Um den Schweißprozess in Echtzeit zu analysieren, werden im Konzept der Forscher mehrere unterschiedliche Sensoren integriert, so etwa Laserscanner, akustische Überwachung, Prozessüberwachung von Spannung und Stromstärke, Wärmebildgebung und ein Kamerasystem.
„Die mechanische Integration all dieser verschiedenen Sensoren ist eine Herausforderung in dieser gefährlichen Umgebung. Wir müssen verschiedene Anordnungen und Ausrichtungen testen, um herauszufinden, wo die ganzen Sensoren hin sollen. Aber wir müssen bei der Testmethode und der Anwendung der Ausrüstung sehr flexibel sein, da es sehr teuer ist, Arbeitszeit für diese Maschine zu buchen“, so Smart.
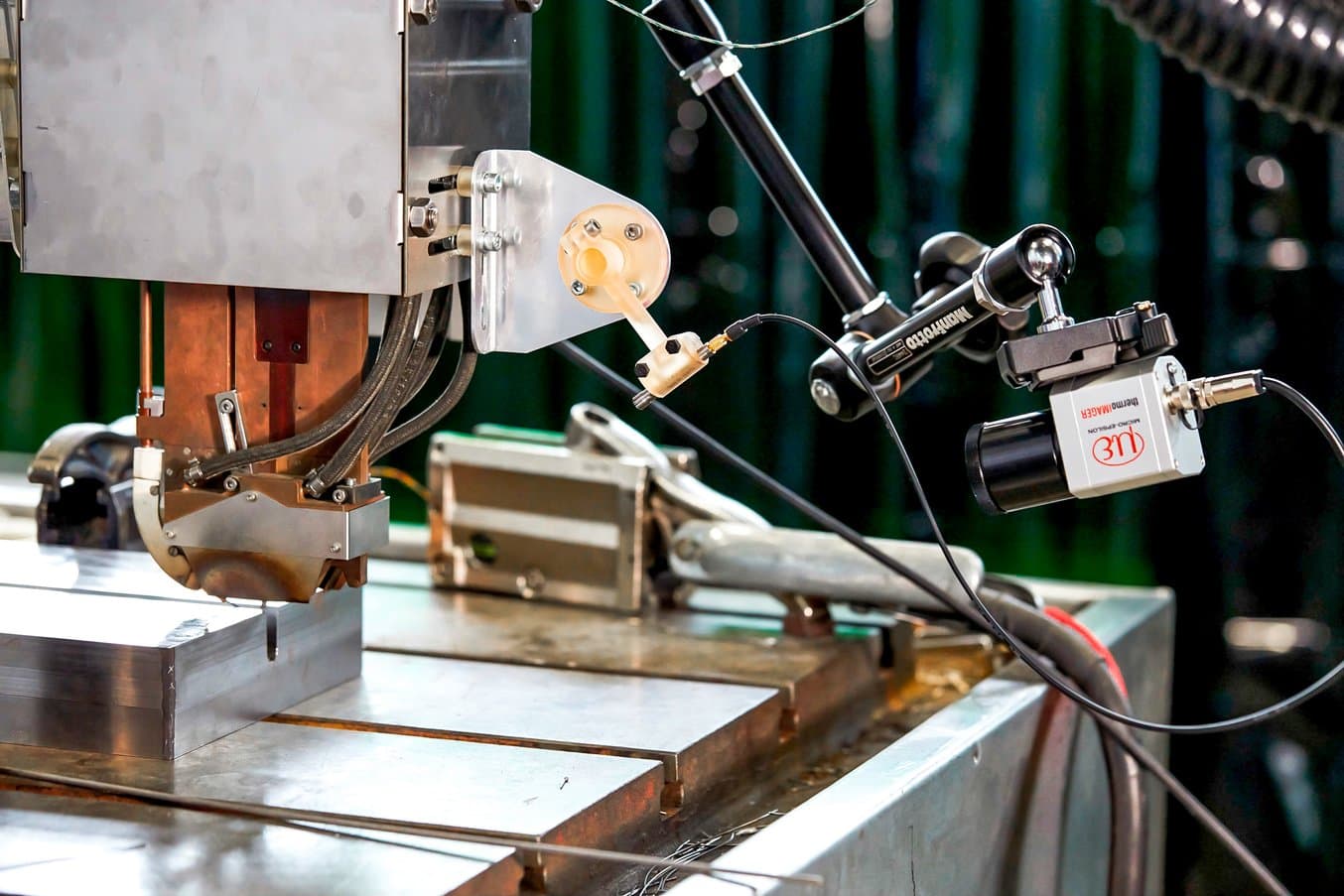
Schnelle Iteration von Sensorkonfigurationen und Montagestrategien mit 3D-Druck
Die aktuelle Sensoranordnung enthält etwa ein dutzend verschiedene 3D-gedruckte Teile, in erster Linie Unterlegscheiben, die Halterungen zusammenhalten, sowie ein Halterungssystem für die Mikrofone. Alle diese Teile müssen den hohen Temperaturen in unmittelbarer Nähe zur Schweißnaht widerstehen.
Formlabs High Temp Resin weist eine Wärmeformbeständigkeitstemperatur (HDT) von 238 °C bei 0,45 MPa auf, wodurch es sich ideal für Teile eignet, bei denen eine hohe Temperaturbeständigkeit ein Muss ist.
„Wenn wir diese Teile auf herkömmliche Weise herstellen hätten müssen, wäre der Designprozess deutlich anstrengender gewesen, wenn es darum geht, die Anforderungen zu erfüllen und alle Toleranzen genau festzulegen, bevor wir die Teile herstellen. Da die Halterungen 3D-gedruckt werden können, ist etwas Raum für Trial and Error. Wir können mehrere Versionen mit verschiedenen Toleranzen drucken und unterschiedliche Ausrichtungen und Größen testen. Wir können viel innovativer sein und Dinge schneller testen“, so Smart.
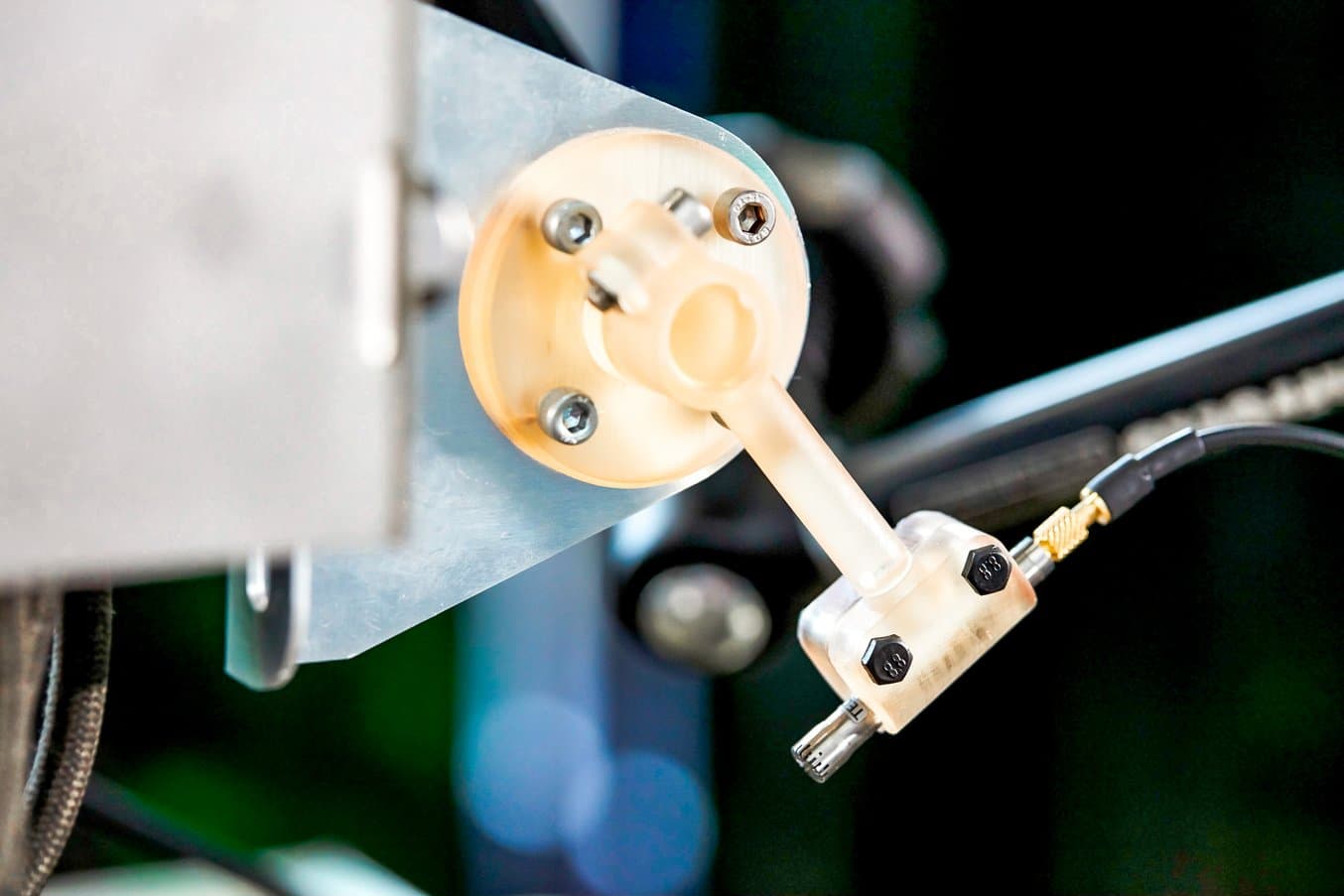
Da wir den 3D-Druck nutzen können, um die verschiedenen Sensorkonfigurationen und Montagestrategien schnell zu testen, konnte das Team sehr flexibel sein und erhebliche Zeit- und Kosteneinsparungen bei der Herstellung der Teile erzielen.
„Wir würden sonst Tage an Arbeitszeit für Ingenieurarbeiten damit verbringen, den ganzen Papierkram zu erledigen, das Material zu bestimmen, Designarbeiten durchzuführen und ein Unternehmen zu beauftragen. So sind es nur ein paar Stunden mit einem CAD-Programm und der Preis vom Kunststoff. Es ist im Vergleich zum herkömmlichen Verfahren nur ein Bruchteil des Aufwands“, so Smart.
„Man kann die Agilität nicht wirklich quantifizieren, da es uns einfach deutlich mehr testen und iterieren lässt. Nehmen wir an, man schickt ein Design zur Fertigung und es war ungeeignet, dann muss man es wieder durchgehen. Wir sprechen also von Wochen, wenn es darum geht, vom Test eines Prototypen zum nächsten zu gelangen. Mit 3D-Druck ist es eine Sache von zwei Tagen. Die Innovationsgeschwindigkeit lässt sich nicht quantifizieren.“
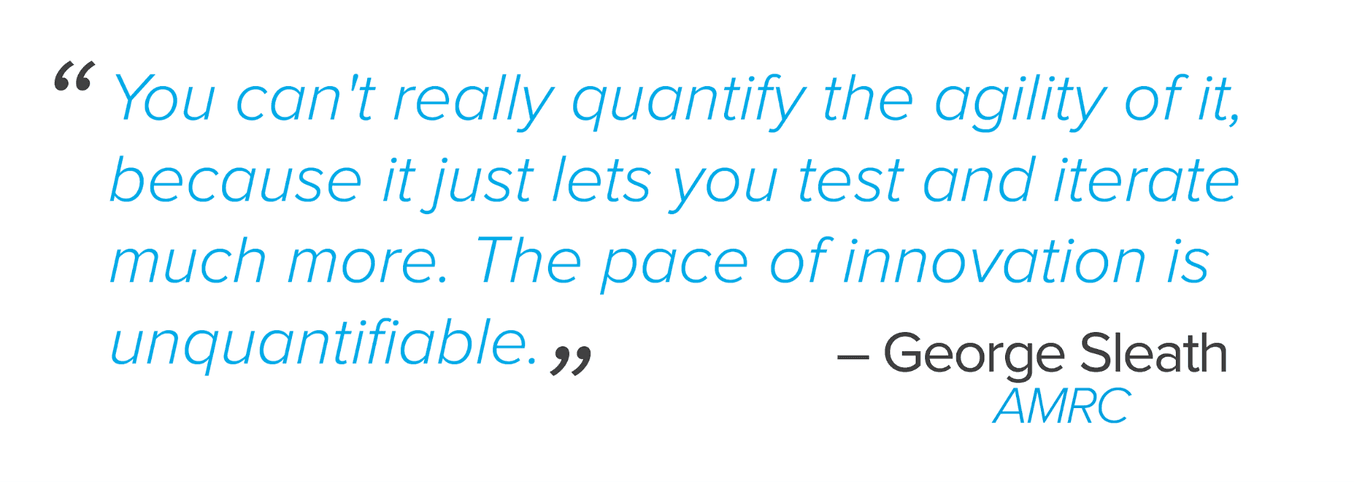
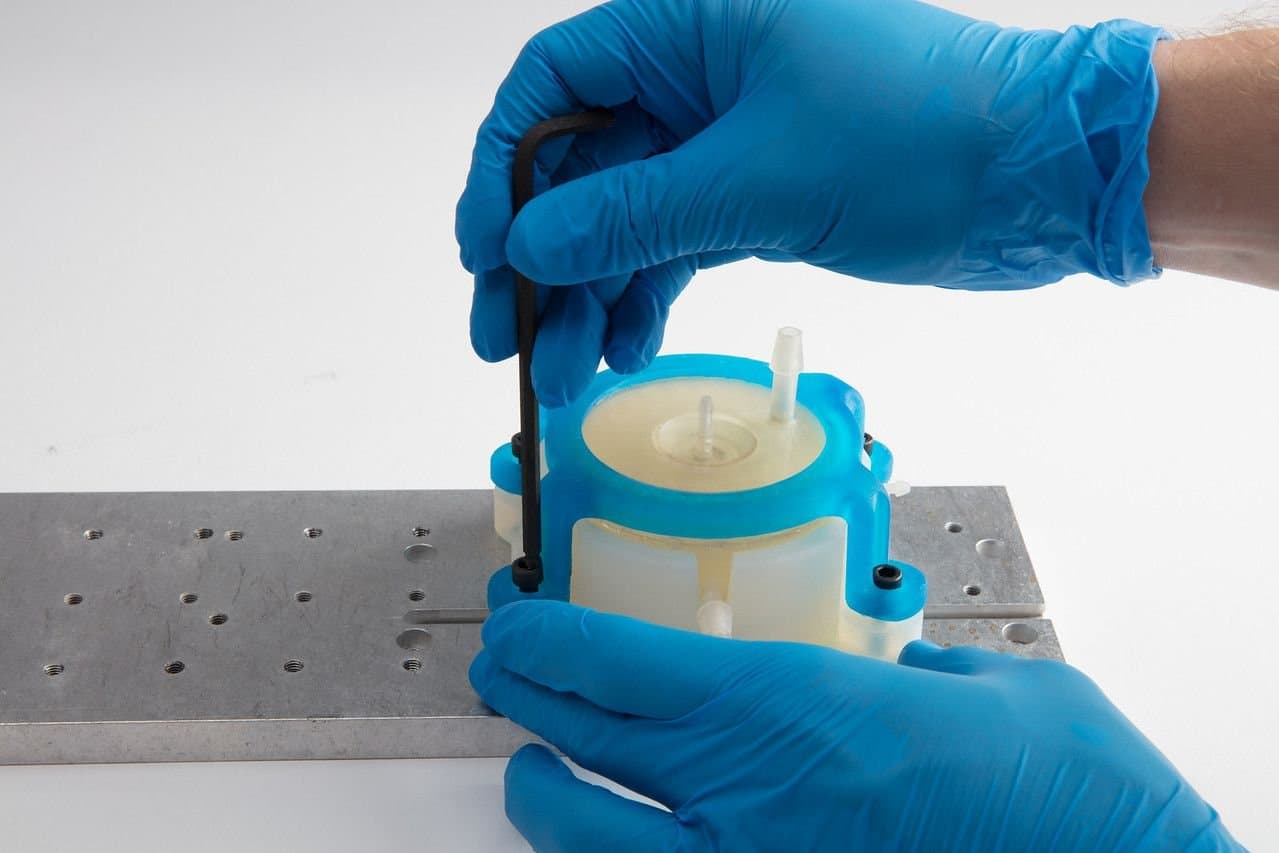
Designing Jigs & Fixtures with 3D Printing
Laden Sie unser Whitepaper herunter, um zu erfahren, wie Sie mit 3D-gedruckten Haltevorrichtungen Kosten reduzieren, die Entwicklungszeit verkürzen und besser optimierte Arbeitsprozesse schaffen können.
White Paper herunterladen
Eine eigene 3D-Druckstation verkürzt Durchlaufzeiten
Smart hat mit der Design and Prototyping Group des AMRC zusammengearbeitet, um die 3D-Druckteile herzustellen. Die Gruppe hat vor kurzem eine neue additive Fertigungsstation mit einer Flotte von 12 Form 2 Stereolithografie (SLA) 3D-Druckern installiert, die allen Ingenieuren am Standort freien Zugang zum 3D-Druck bietet.
„Wir arbeiten ziemlich eng mit der Design Group zusammen. Sie waren sehr zuvorkommend und haben uns einbezogen und uns gezeigt, was in Sachen Ausrüstung machbar ist und zur Verfügung steht und wie man das Design optimieren kann, damit es sich schnell und einfach mit den 3D-Druckern herstellen lässt. Dieser Zugang und das Wissen um die Fähigkeiten ist für die Nutzung in der Forschungsgruppe unabdingbar“, so Smart.
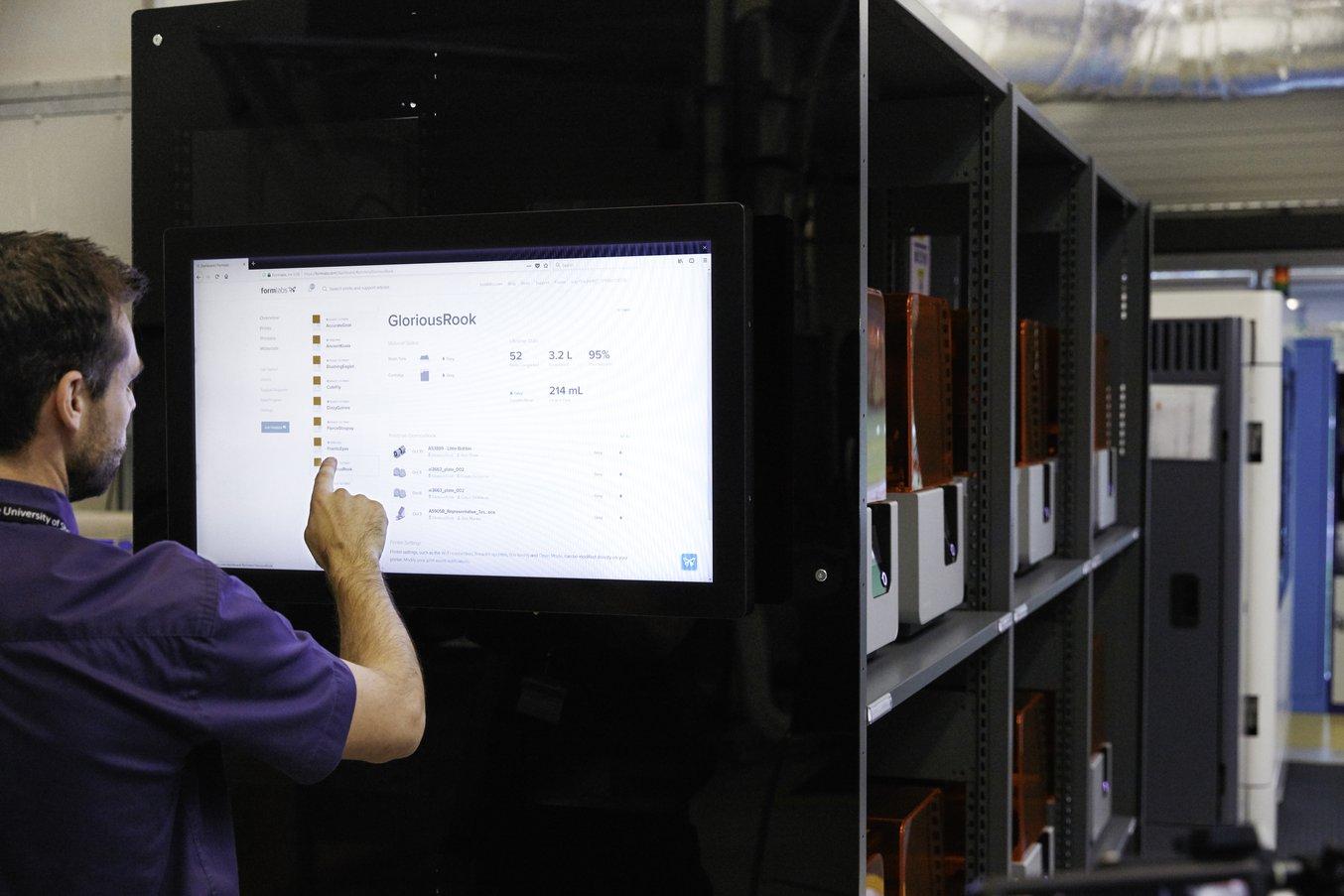
„Wenn es keine [3D-Druckstation] gäbe, wäre mir die Technologie zwar bekannt, ich hätte aber gar keine Kenntnis von dem, was machbar wäre und wie wir etwas designen müssten, das wir herstellen wollen. Ich wurde an einigen der Geräte geschult, und den freien Zugang zu haben, Komponenten zur Fertigung da runter zu schicken, ist unglaublich praktisch“, erzählt Smart.
Erfahren Sie, wie eine 3D-Druckstation hunderte von Ingenieuren im AMRC unterstützt
Erfahren Sie mehr über die 3D-Druckstation des AMRC und über andere Anwendungen wie den Seriendruck von 500 hochpräzisen Bohrkappen für Bohrversuche für Airbus, hochkomplexe Halterungen für einen Robotergreifer und maßgefertigte Faserwickelrollen für die Herstellung von Verbundwerkstoffen.
Möchten Sie mehr über die Drucker und die Technologie hinter der 3D-Druckstation des AMRC erfahren? Lernen Sie den Form 3, den großformatigen Form 3L, und Bibliothek an technischen Kunstharzen von Formlabs für Ihr eigenes Projekt kennen, oder fordern Sie einen kostenlosen Probedruck an, um sich selbst einen Eindruck von den Materialien zu verschaffen.