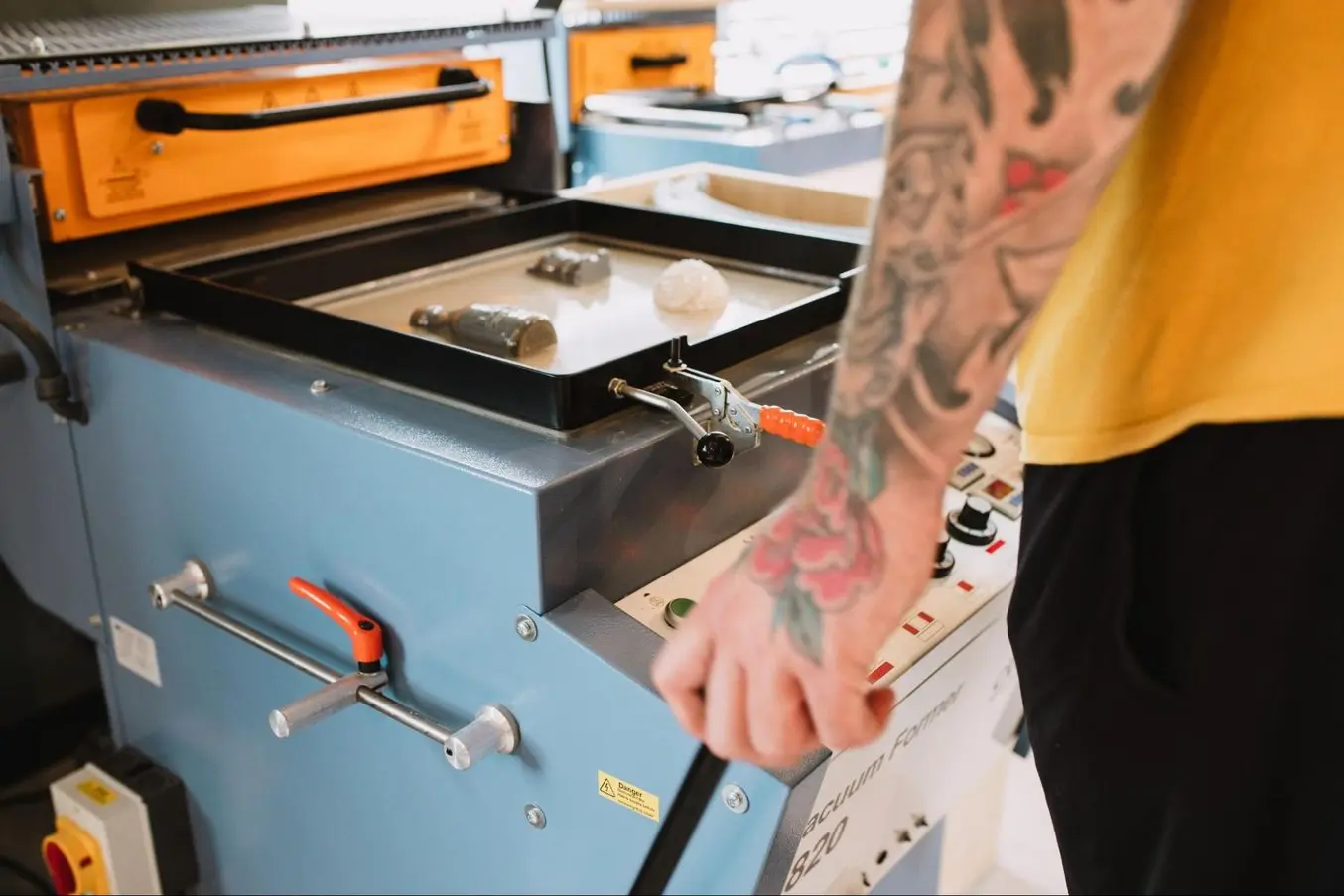
Kunststoff gibt es in verschiedenen Farben, Größen, Typen und mit verschiedenen Materialeigenschaften. Aufgrund seiner Vielfalt ist er ein wichtiges Material für Hersteller, die sowohl Prototypen als auch Endverbrauchsteile produzieren. Thermoformen ist ein Fertigungsverfahren, das eine vielseitige Lösung zur Verarbeitung von Kunststoffplatten bietet.
In diesem umfassenden Leitfaden erfahren Sie mehr über die verschiedenen Thermoformverfahren, die dazugehörigen Materialien und Geräte sowie darüber, wie Sie Formwerkzeuge für das Thermoformen erstellen, auch durch moderne Verfahren wie den 3D-Druck.
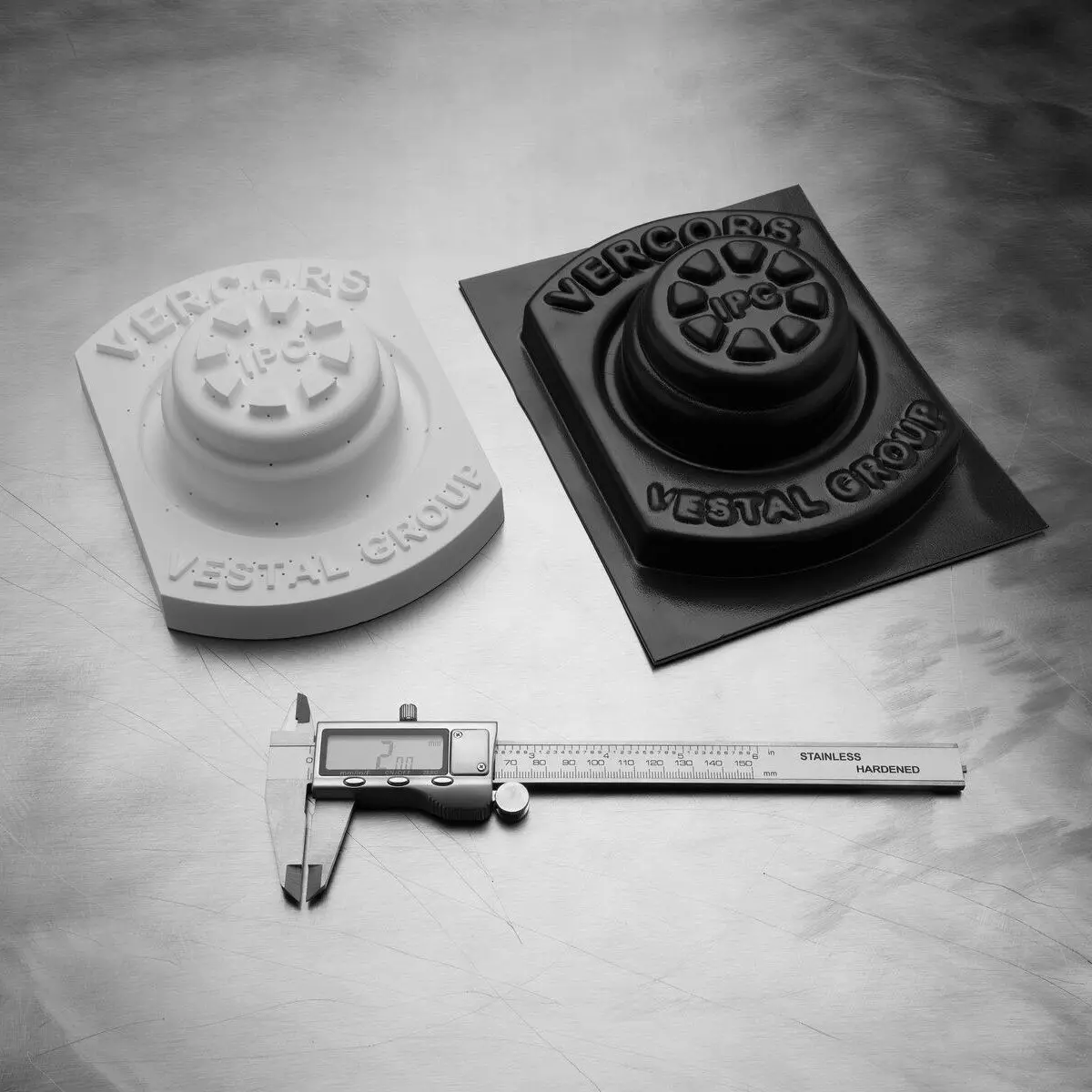
Schnelles Thermoformen in Kleinserie mit 3D-gedruckten Formwerkzeugen
Laden Sie unser Whitepaper herunter und erfahren Sie mehr über die schnelle Fertigung komplexer Formwerkzeuge mittels 3D-Druck. Wir geben außerdem Tipps und Richtlinien zur Vorbereitung der Bestandteile der Form.
Was ist Thermoformen?
Thermoformen, auch Tiefziehen genannt, ist ein Fertigungsverfahren für Kunststoff, bei dem eine Kunststoffplatte oder -folie erhitzt und mithilfe eines Formwerkzeugs in bestimmte Formen gebracht wird. Der so geformte Kunststoff wird dann abgekühlt und nachbearbeitet, bis das fertige Teil vorliegt. Der Prozess wird mithilfe einer Thermoformmaschine durchgeführt, welche die Thermoplastplatte erhitzt und die biegsame Platte dann über das Formwerkzeug zieht. Moderne Thermoformmaschinen führen im Allgemeinen auch den Nachbearbeitungs- und Schneidprozess aus, während Nachbearbeitung und Kühlen bei konventionellen Geräten oft extern erfolgen müssen.
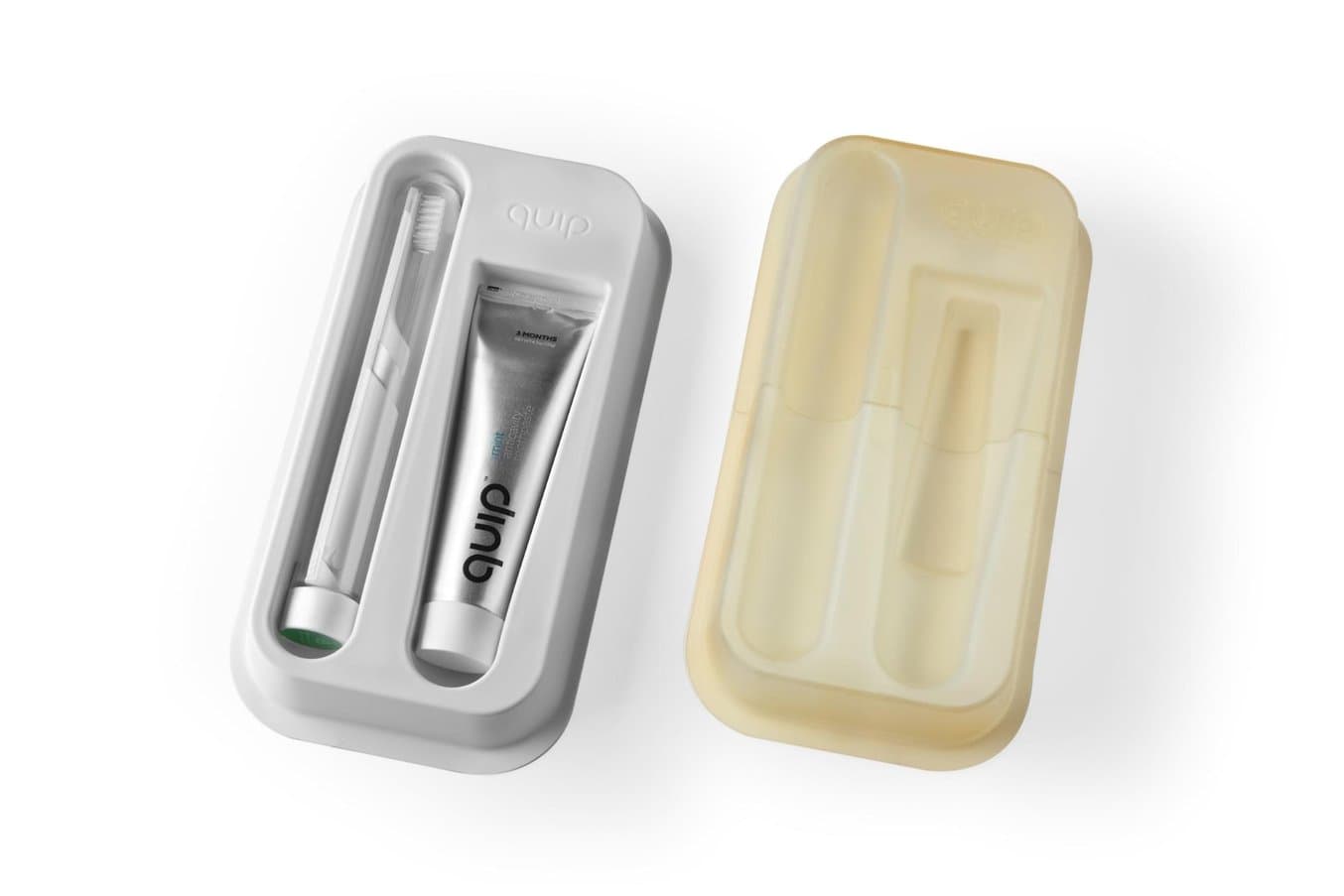
Das Thermoformen ist ein weit verbreitetes Verfahren zur Produktion von Kunststoffverpackungen.
Als Materialien für das Thermoformen werden Thermoplaste verwendet. Hierzu gehören ABS, Polystyrol, Polycarbonat, PETG usw. Die Wahl des Materials hängt vom Fertigungsprojekt und von den für das produzierte Teil erforderlichen Eigenschaften ab.
Thermoformen wird zur Herstellung von Verpackungen für landwirtschaftliche und pharmazeutische Produkte, Konsumgüter, Haushaltsgeräte und mehr verwendet. Auch bei der Herstellung von haltbaren Endverbrauchsteilen wie Flugzeugkomponenten, Fördergeräten, Innenteilen für Autos und medizinischen Geräten kommt es zum Einsatz.
Im Vergleich zu anderen herkömmlichen Fertigungsverfahren produzieren Hersteller kleine bis große Verpackungsmengen mit Thermoformen zu erschwinglichen Kosten. Ein weiterer wichtiger Vorteil des Thermoformens ist, dass hiermit fast alle Thermoplaste verarbeitet werden können, um in kürzester Zeit hochwertige Endverbrauchsteile herzustellen.
Das Thermoformverfahren hat aber auch Nachteile: Es eignet sich nur für dünnwandige Entwürfe, ergibt eine ungleichmäßige Wanddicke und bei der Herstellung von Teilen mit komplexer Geometrie ist die Vielseitigkeit begrenzt. Dieser Leitfaden unterstützt Hersteller dabei, diese Nachteile zu begrenzen und die Vorteile des Thermoformens voll auszunutzen, um die Produktivität zu erhöhen und Kosten zu senken.
Thermoformverfahren
Das Thermoformen ist ein umfassendes Fertigungsverfahren, das die verschiedenen Möglichkeiten zur Umformung erhitzter Kunststoffplatten umfasst. Entscheidet ein Hersteller sich für das Vakuum- oder das Druckformverfahren, dann nutzt er die Vorteile des Thermoformens.
Unter der Vielzahl an existierenden Thermoformverfahren sind folgende am weitesten verbreitet:
-
Vakuumformen: Bei diesem Thermoformverfahren wird zum Formen der Platten Unterdruck verwendet. Zuerst wird die Kunststoffplatte erhitzt, damit sie flexibel wird. Dann entzieht die Vakuumformmaschine Luft, um die Platte an die Form zu pressen. Vakuumformen ist bekannt für seine Kosteneffizienz und einen schnellen Fertigungsprozess.
-
Druckformen: Beim Druckformprozess werden die Kunststoffplatten ebenfalls erhitzt durch Einsatz von Vakuum gegen ein Formwerkzeug gepresst. Es gibt jedoch einen Zwischenschritt. Sobald die Luft abgesaugt ist, übt eine Presse Druck auf die Platte aus, damit der bearbeitete Kunststoff seine endgültige Form besser behält. Dieses Verfahren kommt zum Einsatz, wenn bei einem Thermoformprozess höhere Detailgenauigkeit erforderlich ist.
-
Mechanisches Formen: Bei diesem Prozess wird eine direkte mechanische Kraft angewandt, um die zuvor erhitzte Kunststoffplatte zu formen. Mithilfe eines Kernstopfens wird die biegsame Platte in den Raum zwischen Stopfen und Formwerkzeug gepresst und so das Oberflächenmuster auf die Kunststoffplatte geprägt. Mechanisches Thermoformen wird eingesetzt, wenn ein hohes Maß an Präzision und Detailgenauigkeit erforderlich ist.
-
Überlegformen: Beim Überlegformen wird die erhitzte Kunststoffplatte über ein Formwerkzeug mit bestimmten Mustern platziert. Das Muster der Form wird dann in den Kunststoff gepresst, um das Teil fertigzustellen. Das Überlegformen ist eines der günstigsten Thermoformverfahren, weil es nur wenig Werkzeugausstattung erfordert. Da die Dicke des Materials beibehalten werden kann, führt dieser Prozess nicht zu Schwächen in den Teilen.
-
Positiv-Negativ-Formung: Dieses Thermoformverfahren wird angewandt, wenn die fertigen Teile eine hohe Präzision aufweisen müssen. Beim Positiv-Negativ-Formen kommen eine positive und eine negative Form zum Einsatz, um die erhitzte Kunststoffplatte zu formen. Die Formmaschine drückt die Formwerkzeuge über und unter der Kunststoffplatte zusammen. Die Platte erhält dadurch die Form oder Kontur, die beide Formwerkzeuge vorgeben.
-
Twin-Sheet-Verfahren: In diesem Verfahren werden zwei Schichten von Kunststoffplatten geformt, um sie zu einem Teil zu kombinieren. Die Kunststoffplatten werden gleichzeitig erhitzt, geformt und zusammengefügt, sodass sie ein Objekt bilden. Das Twin-Sheet-Verfahren eignet sich besonders, um Teile mit Hohlräumen oder doppelten Wänden herzustellen.
-
Freiblasen: Das Freiblasverfahren ist eine Thermoformtechnik, bei der der erhitzte Kunststoff ohne Formwerkzeuge bearbeitet wird. Hier bläst die Formmaschine den Kunststoff mithilfe von Druckluft in eine Blasenform, bis die endgültige Form erreicht ist.
Thermoformverfahren | Kosteneffizienz | Produktionsvolumen | Anwendung |
---|---|---|---|
Vakuumformen | Sehr günstiges, schnelles Fertigungsverfahren | Niedrige bis hohe Produktionsvolumen | Für die Herstellung von Teilen, bei denen Präzision und Genauigkeit nicht entscheidend sind, z. B. Haushaltsgegenstände und Verpackungen |
Druckformen | Günstiges Fertigungsverfahren | Niedrige bis hohe Produktionsvolumen | Für die Herstellung von Teilen, bei denen Haltbarkeit und Einheitlichkeit wichtig sind |
Mechanisches Formen | Günstiges Fertigungsverfahren | Mittlere bis hohe Produktionsvolumen | Für die Herstellung von hochwertigen und präzisen Teilen |
Überlegformen | Sehr günstiges, schnelles Fertigungsverfahren | Mittlere bis hohe Produktionsvolumen | Große Komponenten und dicke Materialien mit einfachen gebogenen Formen |
Positiv-Negativ-Formung | Teures Fertigungsverfahren aufgrund der erforderlichen Werkzeugbestückung | Mittlere bis hohe Produktionsvolumen | Für die Herstellung langlebiger Teile und Komponenten wie Fahrzeugverkleidungen und Vorrichtungen |
Twin-Sheet-Verfahren | Günstiges Fertigungsverfahren | Mittlere bis hohe Produktionsvolumen | Für die Herstellung von Verpackungsgegenständen wie hohlen und doppelwandigen Teilen |
Freiblasen | Teurer als andere Optionen | Kleine Produktionsvolumen | Für die Herstellung von Oberlichtern, Kuppeln usw. |
Thermoformmaterialien
Thermoformen wird zur Herstellung von Lebensmittelverpackungen, Flugzeugkomponenten, Spielzeug, Paletten und anderen Kunststoffgegenständen eingesetzt. Daher steht vor einem Produktionszyklus eine Vielzahl von Kunststoffmaterialien zur Auswahl. Häufig genutzte Materialien für das Thermoformen sind:
-
Polypropylen (PP): Aufgrund von Preis und Menge ist PP das beliebteste Kunststoffmaterial für das Thermoformen. Es wird häufig zur Herstellung von Verpackungen, Beatmungsgeräten, Spielzeug und anderen Kunststoffgegenständen genutzt. Seine Eigenschaften wie ausgezeichnete Beständigkeit gegen Chemikalien, Ermüdung und Hitze, machen Polypropylen zu einer beliebten Wahl. Darüber hinaus ist PP ein sehr erschwingliches Material und für die unterschiedlichen hier beschriebenen Thermoformverfahren geeignet.
-
Polystyrol (PS): Dieses aromatische Kohlenwasserstoffpolymer bietet Herstellern einen transparenten, harten und spröden Kunststoff. Polystyrol wird häufig als Verpackungsmaterial verwendet, da es Eigenschaften wie Wasser- und Luftbeständigkeit bietet. Hersteller nutzen PS, um Lebensmittelverpackungen, CD-Hüllen und Haushaltsgegenstände zu fertigen.
-
Polyethylenterephthalat (PET): PET bietet sehr gute Resistenzeigenschaften gegen Alkohol und ätherische Öle, eine gute chemische Beständigkeit und ein hohes Maß an Schlagzähigkeit und Zugfestigkeit. Es wird gewöhnlich für kohlensäurehaltige Getränke, Wasserflaschen und andere Lebensmittelprodukte genutzt.
-
Weich-Polyethylen (LDPE): LDPE ist ein gegen Chemikalien und UV-Strahlen beständiger Thermoplast. Der Kunststoff ist flexibel und hat eine hohe Zugfestigkeit. Er wird für die Herstellung von Verpackungsfolie, DVDs, Kabelisolierungen, Behältern und chemikalienbeständigen Teilen verwendet.
-
Hart-Polyethylen (HDPE): HDPE ähnelt LDPE hinsichtlich seiner Grundeigenschaften und ist beständig gegen Chemikalien, UV-Strahlen und Wasser. Es ist ein langlebiger Thermoplast, der zur Herstellung von Verpackungsfolien, geblasenen Flaschen, Behältern, Rohren und Plastiktüten verwendet wird.
-
Polyvinylchlorid (PVC): PVC ist ein weiterer beliebter Kunststoff, der bei der Herstellung von Rohren, Fensterrahmen, Innenverkleidungen von Autos, Haushaltsgegenständen, Verpackungen und Schuhen genutzt wird. Es kann flexibel oder starr gefertigt werden, je nach Herstelleranforderung. PVC ist außerdem sehr dicht, haltbar und wasserresistent. Es ist jedoch zu beachten, dass PVC nicht vollkommen chemikalienbeständig ist und mit Chlor reagieren kann.
-
Polycarbonat (PC): Polycarbonate sind starke, belastbare Materialien, die großen Verformungen ausgesetzt werden können, ohne zu reißen oder zu brechen. Sie sind hitzeresistent, schwer entflammbar und haben gute elektrische Isolatoreigenschaften. Einige Arten von PC sind auch optisch transparent und für sichtbares Licht hochtransparent. Daher wird PC für Kunststoffgläser in Brillen, in medizinischen Geräten, Automobilkomponenten, Schutzausrüstung (Brillengläser, Schutzhelme), Panzerglas, Autoscheinwerfern und im Bauwesen verwendet.
-
Celluloseacetat: Für Hersteller, die ein umweltfreundliches thermoplastisches Material suchen, stellt Celluloseacetat eine Option dar. Dieser Thermoplast wird aus nachwachsenden Rohstoffen wie z. B. Zellstoff hergestellt. Celluloseacetat ist normalerweise farblos und transparent. Es wird für die Herstellung von Haushaltsgegenständen, Verpackungsfolien, Glasrahmen und Überzügen für Medikamente verwendet.
-
Polymethylmethacrylat (PMMA): Zu den Eigenschaften von PMMA gehören hohe Festigkeit, Witterungsbeständigkeit, Haltbarkeit und Transparenz. PMMA wird genutzt, um Linsen, Fahrzeugscheinwerfer und transparente Verpackungen herzustellen. Dank der Haltbarkeit von PMMA sind Endverbrauchsteile langzeitig nutzbar.
-
Acrylnitril-Butadien-Styrol (ABS): ABS ist ein starres, abrasionsbeständiges Material, das niedrigen Temperaturen gut standhält. Thermogeformtes ABS eignet sich zur Herstellung von Aufbau- und Verbindungstechnik, Lebensmittelbehältern und Haushaltsgeräten.
Weitere verfügbare Fertigungsmaterialien sind Polytetrafluorethylen (PTFE), Polyamide, High Impact Polystyrene (HIPS) und mehr. Die Materialwahl hängt von den Projektanforderungen und dem beabsichtigten Thermoformverfahren ab. Die Anwendungstabelle kann helfen, die richtige Wahl für Ihre Projekte zu treffen.
Anwendungen | Materialien | Gängige Thermoformverfahren |
---|---|---|
Verpackungen | ABS, PP, PMMA, PVC, PET, LDPE | Druckformen, Vakuumformen, Positiv-Negativ-Formung, Twin-Sheet-Verfahren, mechanisches Formen |
Haushalts- und Verbrauchsgegenstände | ABS, PS, PVC, PP, PC | Druckformen, Vakuumformen, mechanisches Formen |
Komponenten und Innenverkleidung von Autos | PC, PMMA, HDPE, LDPE | Überlegformen, Positiv-Negativ-Formung, Druckformen |
Gesundheitswesen und Medizinprodukte | Celluloseacetat, LDPE, PC | Druckformen, mechanisches Formen, Vakuumformen |
Bauwesen, Klimatechnik, Rohrleitungen | PVC, HDPE, PC | Mechanisches Formen, Druckformen, Vakuumformen, Überlegformen |
Thermoformen von Platten oder Folien
Bei Thermoformverfahren werden Halbzeuge verschiedener Dicken verwendet: Folien oder Platten. Beim Thermoformen von Folien werden dünne Kunststoffbahnen in Form von Folienrollen eingesetzt. Beim Thermoformen von Platten werden dickere Kunststoffplatten verwendet. Die Materialdicke ist ausschlaggebend bei der Wahl der Geräte für das Thermoformen.
Zur Fertigung dünnwandiger Gegenstände wie z. B. Kunststoffbechern und Lebensmittelverpackungen nutzen Hersteller Folien als Halbzeug. Im Umkehrschluss werden zur Herstellung von Paletten und Behältern Platten sowie zusätzliche Hilfsgeräte benötigt. Das Thermoformen von Platten ist ideal für geringe bis mittlere Produktionsvolumen geeignet, während Folien sich für hohe Produktionsvolumen anbieten.
Die folgende Übersicht stellt die Unterschiede des Thermoformens von Platten und von Folien dar:
Kunststoff-Thermoformen | Platten | Folien |
---|---|---|
Formteildicke | 1,5–9,5 mm | < 3 mm |
Maschinentyp | Plattenzuführung | Folienrollenzuführung |
Verwendete Thermoplaste | ABS, HDPE, Polypropylen | PETG, PET, PVC |
Produktionsvolumen | Niedriges bis mittleres Volumen | Mittleres bis hohes Volumen |
Anwendungsbeispiele | Gehäuse für Elektronik, Innenteile, Industriewerkzeuge, permanente Strukturkomponenten, Paletten, Wannen, Duschwannen, Koffer. | Starre oder halbstarre Einwegverpackungen, Einweggegenstände (Lebensmittelverpackungen, Einwegbecher, -teller und -schalen) sowie Verpackungen für kleine medizinische Geräte. |
Thermoformgeräte
Jedes Thermoformverfahren erfordert spezielle Geräte, z. B. werden für Vakuumformen, Druckformen, Twin-Sheet-Verfahren oder Überlegformen unterschiedliche Geräte benötigt.
Thermoformgeräte können in Unterkategorien unterteilt werden, die durch ihre Anwendungsfälle definiert werden. So kann zwischen Desktop-, Industrie- und selbstgebauten Thermoformgeräten unterschieden werden. Je nach Anwendungsfall können professionelle Hersteller und Heimwerker aus diesen Optionen wählen.
Folgende Produktspezifikationen sollten bei der Wahl des passenden Thermoformgeräts berücksichtigt werden:
-
Formfläche: Die Formfläche bezeichnet das Konstruktionsvolumen, in dem das Kunststoffmodell oder -design geformt wird. Die Formfläche enthält die entworfene(n) Form(en), den Kernstopfen bzw. den Mechanismus zur Übertragung von Mustern auf die vorher erhitzte Kunststoffplatte.
-
Ziehtiefe: Das Konzept der Ziehtiefe (oder „Ziehverhältnis“) ist beim Thermoformverfahren entscheidend. Die Ziehtiefe ermöglicht dem Hersteller Rückschlüsse auf die notwendige Dicke der Kunststoffplatten für die jeweiligen Projekte. Kennt der Hersteller die Ziehtiefe der Geräte, kann er die Dicke des Kunststoffteils ermitteln sowie die Oberfläche, die die Kunststoffplatte während des Thermoformprozesses abdecken sollte.
-
Geräteabmessungen: Die Abmessungen der Thermoformausrüstung bestimmen die Größe von Komponenten oder Kunststoffteilen, die produziert werden können. Desktop-Thermoformgeräte sind kompakt und bieten daher begrenzte Teilabmessungen, während industrielle Lösungen viel größer sind.
-
Klemmkraft: Manche Thermoformmaschinen (etwa solche für das Druckformen, Twin-Sheet-Verfahren und das Positiv-Negativ-Formen) klemmen die Kunststoffplatte fest, um das fertige Teil zu formen. Die Klemmkraft ist ein wichtiger Faktor, da sie die Auswahl des Materials beeinflusst.
-
Werkzeugwechsel: Die vorhandenen Werkzeugwechseloptionen einer Thermoformmaschine geben Herstellern einen Hinweis darauf, wie schnell Werkzeugwechsel ausgeführt werden können. Schnellere Werkzeugwechsel erhöhen die Effizienz und Wirtschaftlichkeit der Geräte in der Produktion.
Arten von Thermoformgeräten
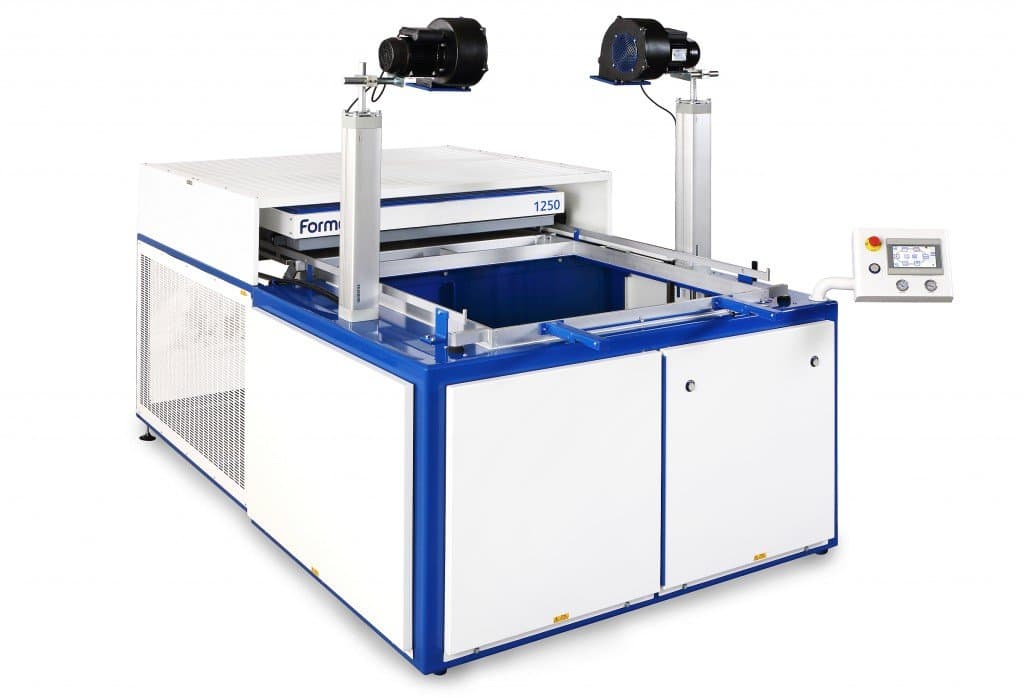
Großformatige industrielle Vakuumformmaschine von Formech
Sobald die Eigenschaften bekannt sind, wählt der Hersteller eine Thermoformmaschine aus einer der folgenden Kategorien:
-
Industrielle Thermoformgeräte: Hierbei handelt es sich um großformatige Geräte für mittlere bis hohe Produktionsvolumen. Industrielle Vakuumformmaschinen sind mit einer breiteren Palette von Materialien und Kunststoffdicken kompatibel, bieten eine größere Ziehtiefe und haben stärkere Vakuumkräfte bzw. einen höheren Druck, um komplexe und filigrane Details zu schaffen und eine dem Spritzguss ähnliche Teilqualität zu erreichen. Beispiele für industrielle Thermoformgeräte sind die Geräte von GN, Ridat, Formech und Belovac. Die Kosten für industrielle Thermoformmaschinen beginnen bei rund 10 000 USD und gehen noch weit darüber hinaus.
-
Desktop-Thermoformgeräte: Desktop-Thermoformgeräte haben kleinere Abmessungen, eine eingeschränkte Materialauswahl und üben geringere Kräfte aus. Hersteller, Produktentwickler und Hobbyanwender verwenden Desktop-Thermoformgeräte für Prototyping, Sonderanfertigungen und Kleinserienproduktion. Die Preise für Desktop-Thermoformgeräte beginnen bei unter 1000 USD und eine breite Auswahl an Geräten ist für unter 10 000 USD erhältlich. Formech, Mayku und Smartform sind einige Beispiele für Anbieter.
-
Selbstgebaute Thermoformgeräte: Heimwerker, die mit dem Thermoformen experimentieren möchten, können sich Geräte für die Kleinserienproduktion selbst zusammenbauen. Selbstgebaute Geräte sind meist günstiger, aber auch arbeitsaufwendiger als Standardgeräte, und der Eigenbau erfordert Fachwissen.
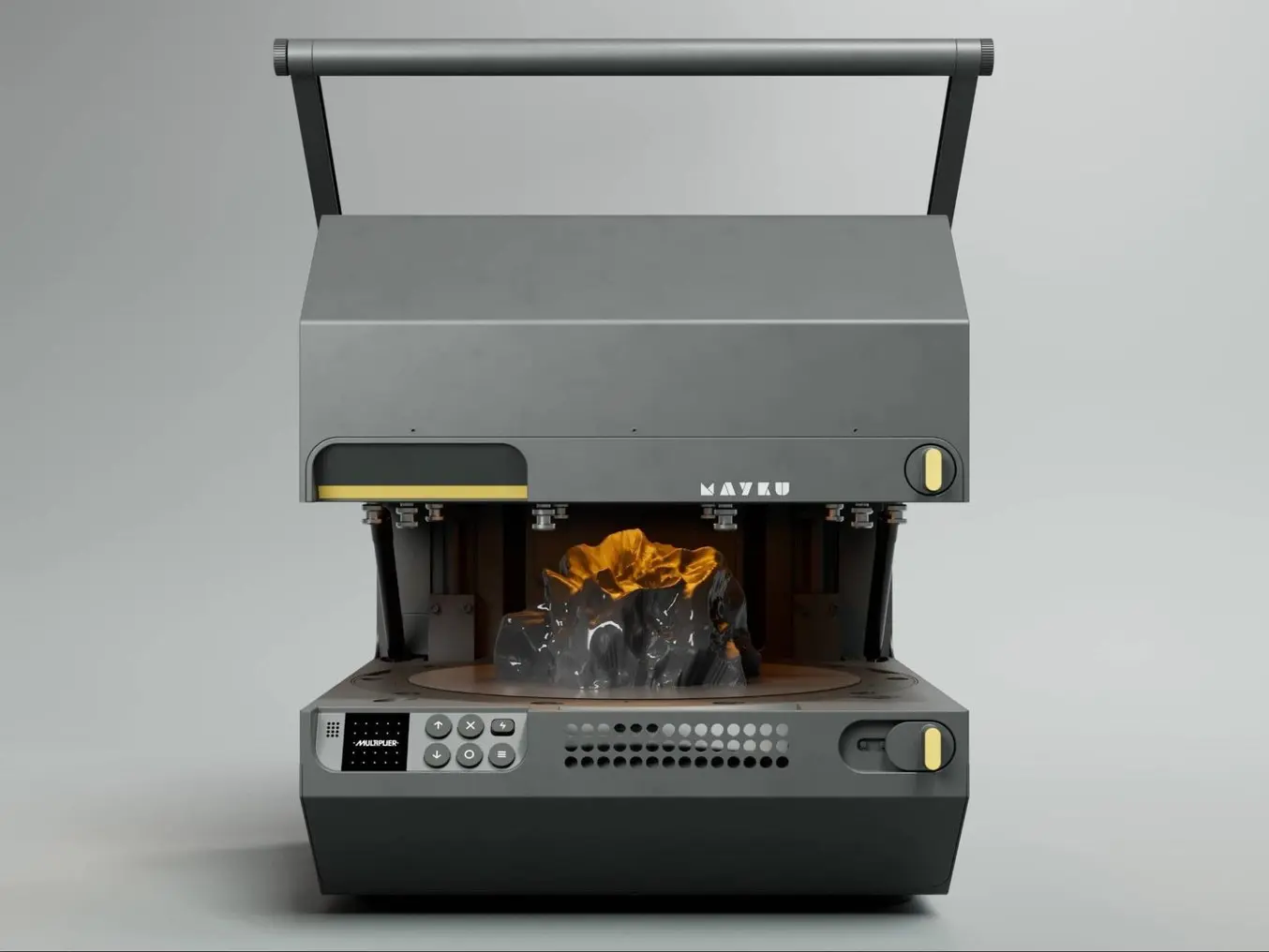
Ein Desktop-Druckformgerät von Mayku.
Thermoformwerkzeuge
Die meisten Thermoformverfahren, einschließlich Vakuumformen, Druckformen, Positiv-Negativ-Formung, mechanisches Formen und Twin-Sheet-Verfahren, verwenden strukturierte Formwerkzeuge, um der Kunststoffplatte ihre endgültige Geometrie zu verleihen.
Die für Thermoformprozesse erforderlichen Formwerkzeuge können mit verschiedenen Fertigungsverfahren erzeugt werden, etwa durch manuelle Holzbearbeitung, CNC-Bearbeitung von Kunststoff, Strukturschaum, glasfaserverstärktem Kunststoff, technischen Verbundwerkstoffen oder Metallen, 3D-Druck von Polymeren oder Gießen von Gips oder Metall.
Der Formentwurf und das richtige Verfahren für den Formenbau hängen vom Design der Teile und den folgenden Faktoren ab:
-
Produktionsvolumen: Holz-, Gips-, Verbundwerkstoff- und 3D-gedruckte Kunststoffformen sind für Sonderanfertigungen, Prototypen und Kleinserien im Allgemeinen die kostengünstigste Option, wobei 3D-gedruckte, zerspante oder gegossene Polymer- und Verbundwerkstoffformen auch für mittlere Produktionsvolumen ideal sind. Für hohe Produktionsvolumen sind Metallformen die gängigste Wahl, aufgrund ihrer verbesserten Wärmeleitfähigkeit und Festigkeit. Sie bieten eine bessere Kontrolle der Oberflächentemperatur der Form, eine größere Einheitlichkeit der Teile, verringerte Zyklen und eine bessere Haltbarkeit.
-
Design der Teile: Der manuelle Formenbau aus Holz mag eine gute Lösung für einfache Formen sein, aber für Teile mit komplexen Geometrien, die Präzision und Genauigkeit erfordern, sind Gussverfahren oder digitale Werkzeuge wie Zerspanungstechnik oder 3D-Druck deutlich besser geeignet.
-
Thermoformtemperatur: Je nach Material muss die Form eine höhere Wärmebeständigkeit aufweisen. Die Schaffung von Kühlkanälen in der Form kann die Kühlgeschwindigkeit erhöhen, die Einheitlichkeit verbessern und den Produktionszyklus verkürzen.
-
Kräfte beim Thermoformen: Das Werkzeug sollte den Kräften, die beim Thermoformen auftreten, standhalten (z. B. Vakuumkräfte, Druck oder mechanische Einwirkungen). Das Ausmaß dieser Kräfte hängt vom Material, der Kunststoffdicke, den Anforderungen an die Qualität, der Oberflächenbeschaffenheit und dem Detailgrad des fertigen Teils ab.
-
Bestandteile der Form: Die Form sollte kritische Bestandteile wie Belüftungslöcher und Entformungsschrägen aufweisen, damit die Luft beim Formprozess zirkulieren und das Teil entformt werden kann.
-
Oberflächenbeschaffenheit der Form: Anforderungen an die Formteilqualität wie Oberflächenbeschaffenheit, Detailgrad, Maßgenauigkeit und Stabilität sind bei der Fertigung des Werkzeugs zu berücksichtigen.
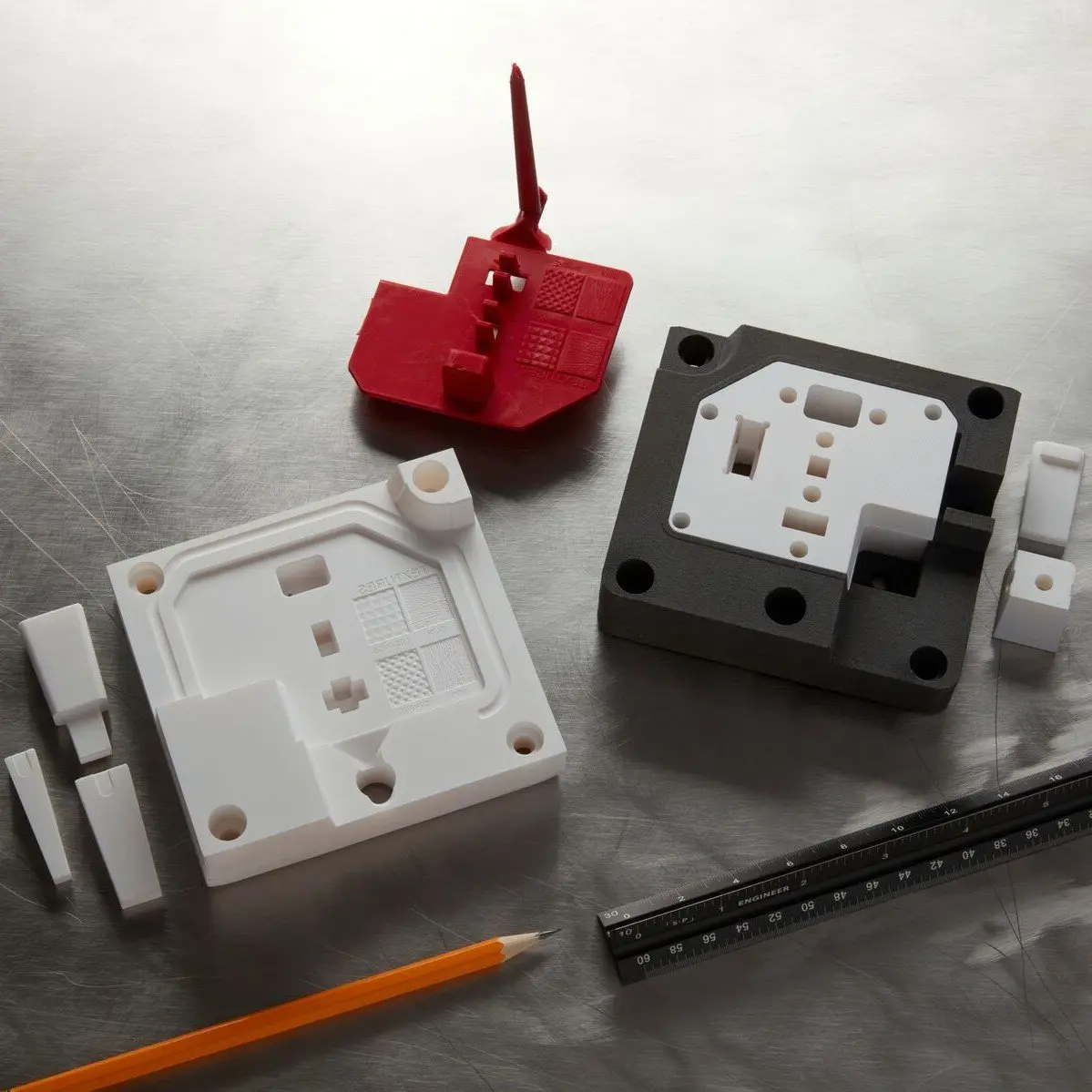
Leitfaden zum Rapid Tooling
In diesem Whitepaper sprechen wir über die Kombination von Rapid Tooling mit traditionellen Herstellungsverfahren wie Spritzguss, Thermoformen oder anderen Gießverfahren.
Herstellung von Thermoformwerkzeugen mit 3D-Druck
Traditionelle Methoden zur Formenherstellung sind oft kostspielig, arbeitsintensiv und haben lange Durchlaufzeiten. Das kann die Effizienz von Thermoformverfahren einschränken.
Viele Unternehmen nutzen vermehrt den Stereolithografie-3D-Druck (SLA), um Formen für Thermoformverfahren zu erstellen, da dieser insbesondere bei kleineren Auflagen, Sonderanfertigungen und Prototypenentwicklung eine schnelle Durchlaufzeit zu einem niedrigen Preispunkt bietet – dies ist auch als Rapid Tooling bekannt. Der 3D-Druck ermöglicht außerdem eine unübertroffene Gestaltungsfreiheit bei der Herstellung komplexer und filigraner Formen. Verwenden Sie den Desktop-SLA-Drucker Form 3+ für kleinere Formen und den großformatigen SLA-Drucker Form 3L für Formgrößen von bis zu 33,5 × 20 × 30 cm.
Die Entwicklung von Thermoformwerkzeugen mithilfe des 3D-Drucks bietet unter anderem folgende Vorteile:
-
Geschwindigkeit: In den meisten Fällen können 3D-Drucker kleine bis mittelgroße Thermoformwerkzeuge in weniger als 24 Stunden erstellen.
-
Kosteneffizienz: Mittels 3D-Druck senken Hersteller die Kosten für den Formenbau und steigern somit deutlich die Kosteneffizienz des Thermoformens für kleinere Auflagen und Sonderanfertigungen.
-
Komplexe Formendesigns: Mit 3D-Druck entfallen die Herausforderungen bei der Entwicklung von Formen mit komplexen Geometrien, wie sie von herkömmlichen Fertigungsverfahren bekannt sind. So ermöglicht der 3D-Druck z. B. den Einsatz von Designmerkmalen, die sich nur schwer maschinell bearbeiten lassen. Der Umformungsprozess kann außerdem durch das Hinzufügen von Lüftungsöffnungen für einen besseren Zug oder Druck verbessert werden. Hersteller können professionelle 3D-Drucker auch nutzen, um komplexe Formwerkzeuge für Thermoformprozesse wie das Twin-Sheet-Verfahren und das Positiv-Negativ-Formen zu entwickeln.
-
Schnelle Prototypenfertigung von Formen: Der 3D-Druck gibt Herstellern ein Werkzeug in die Hand, mit dem sie Formendesigns schnell und kostengünstig testen und iterieren. Die 3D-gedruckten Formen können dann direkt in der Herstellung von Sonderanfertigungen und kleinen Stückzahlen verwendet werden (z. B. für Bridge Manufacturing), bis das endgültige Formwerkzeug geliefert wird.
-
Erweiterte Materialoptionen: Der 3D-Druck bietet eine breite Palette von Materialien, sodass Hersteller mit Formen unterschiedlicher Qualität, Hitzebeständigkeit, Haltbarkeit und Kosten experimentieren können.
-
Oberflächenbeschaffenheit: Mit SLA- und kunstharzbasierten 3D-Drucktechnologien lassen sich eine glatte Oberflächenbeschaffenheit und ein hoher Detailgrad erreichen.
-
Benutzerfreundlichkeit: Kunstharz-3D-Drucker für Desktop und Benchtop können nahtlos in jeden Thermoformprozess integriert werden, da sie einfach zu implementieren, zu bedienen und zu warten sind. Dadurch können das CNC und die Arbeitszeit von qualifizierten Bedienern in der Zwischenzeit für andere wichtige Aufgaben freigestellt werden.
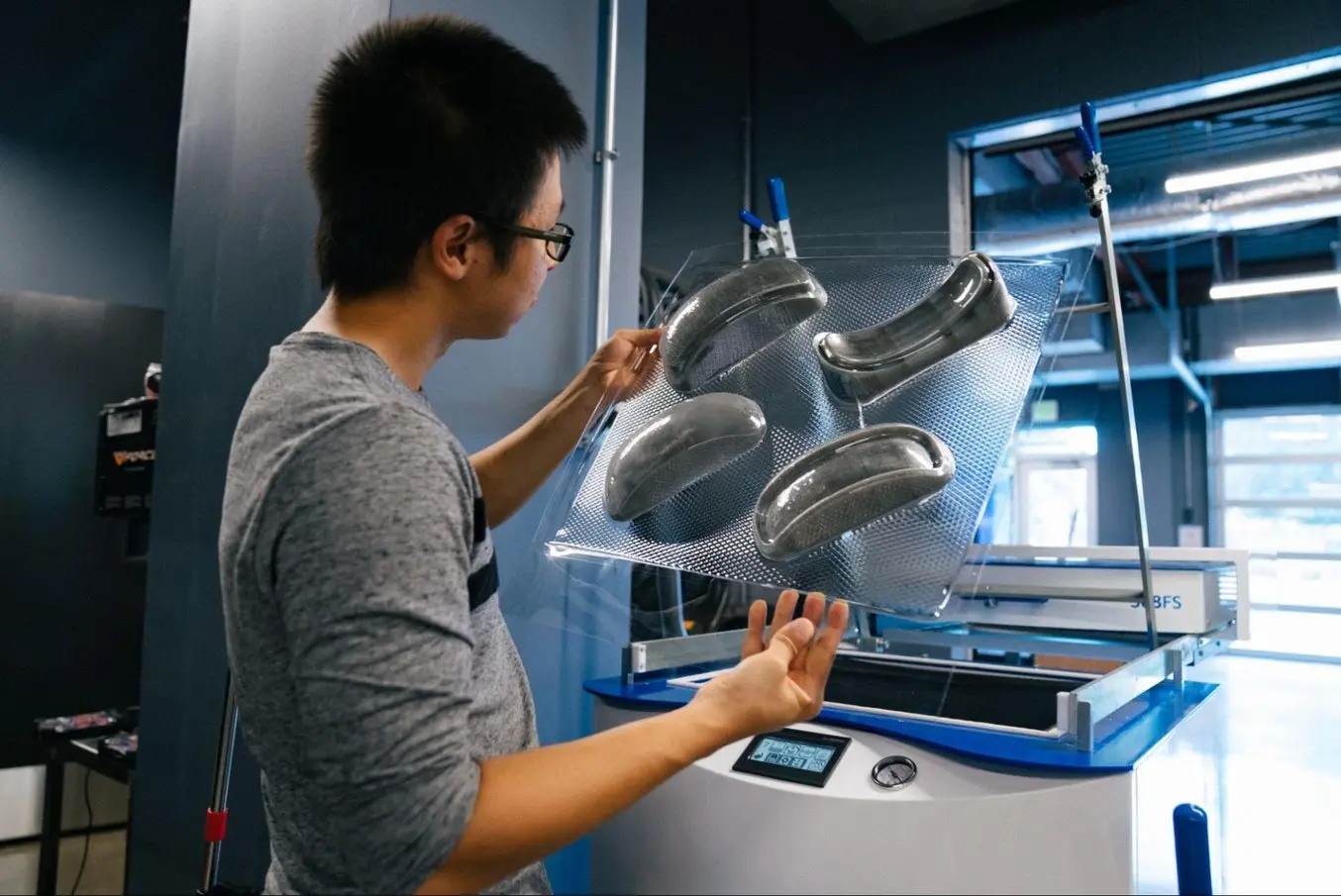
Das Produktentwicklungsunternehmen Glassboard verwendet 3D-gedruckte Formen zum Thermoformen von Prototypen aus Polycarbonat wie Helmschalen oder Verpackungsteilen.
Bei der Entwicklung von thermoplastischen Prototypen nutzt das Produktentwicklungsunternehmen Glassboard die hohe Druckgeschwindigkeit von Draft Resin zur schnellen Produktion von Thermoformwerkzeugen für Prototypen aus Polycarbonat wie Helmschalen oder Verpackungsteilen. So wird eine komplizierte Formgeometrie möglich, die mit traditionellen Verfahren nur schwer herzustellen wäre, beispielsweise kleinste Details oder Löcher zur besseren Vakuumverteilung auf der Oberfläche.
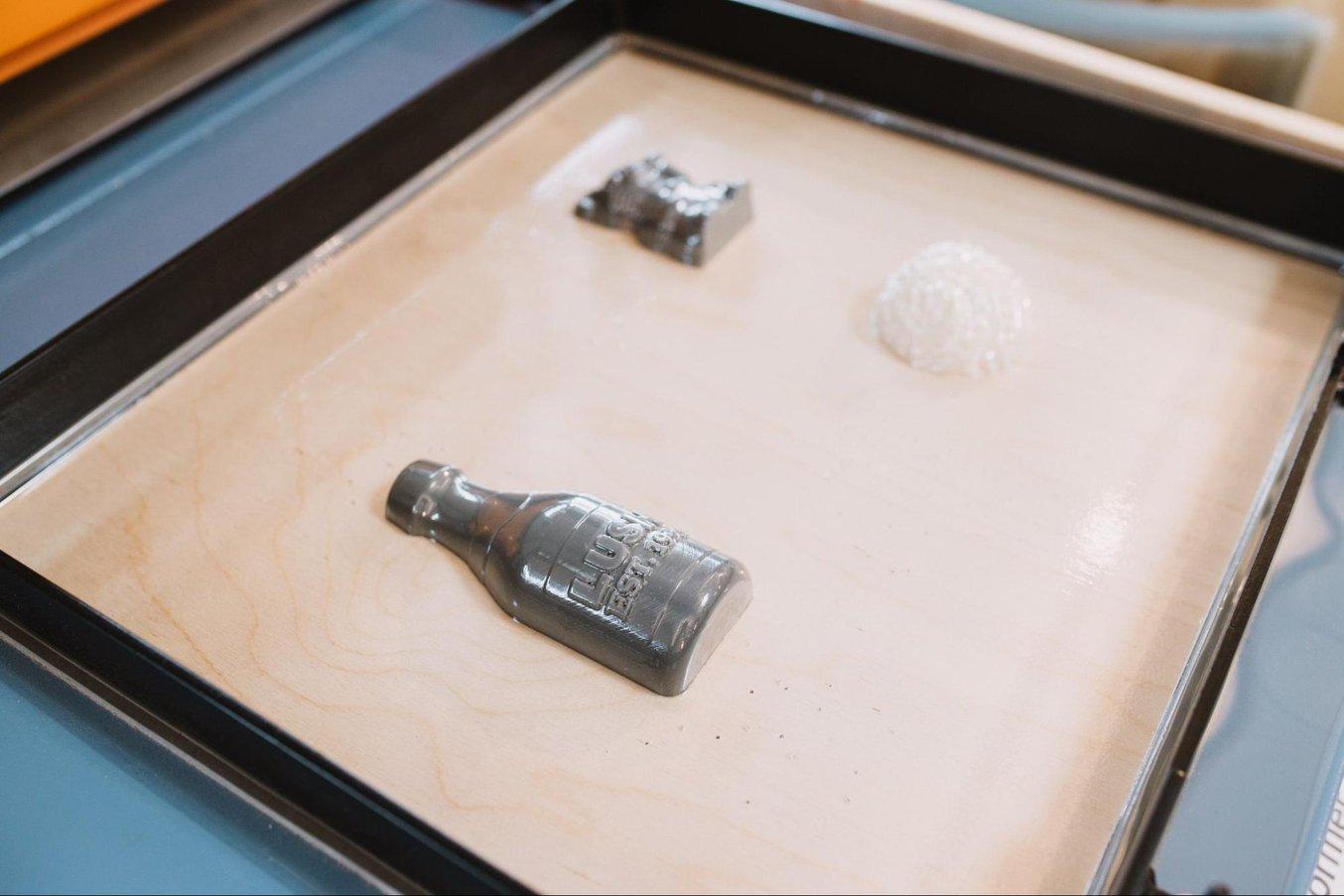
Der Kosmetikhersteller Lush nutzt den 3D-Druck, um innerhalb von 24 Stunden detailreiche und texturierte Formwerkzeuge für das Vakuumformverfahren herzustellen.
Früher fertigte der Kosmetikhersteller Lush die Urformen für seine überaus beliebten Produkte von Hand. Seit Kurzem verwendet das Team jedoch 3D-Druck zur Herstellung von Vakuumformwerkzeugen mit detaillierten Designs und Texturen. Dadurch lassen sich Konzepte bereits in weniger als 24 Stunden umsetzen und mehr als eintausend Designs pro Jahr testen.
3D-gedruckte Formen für das Thermoformverfahren eignen sich außerdem ideal für die kostengünstige Herstellung maßgefertigter oder individualisierter Endverbrauchsteile. So sind Vakuumformen und Druckformen mit 3D-gedruckten Modellen beispielsweise für transparente Aligner in der Kieferorthopädie die gängigen Produktionsweisen.

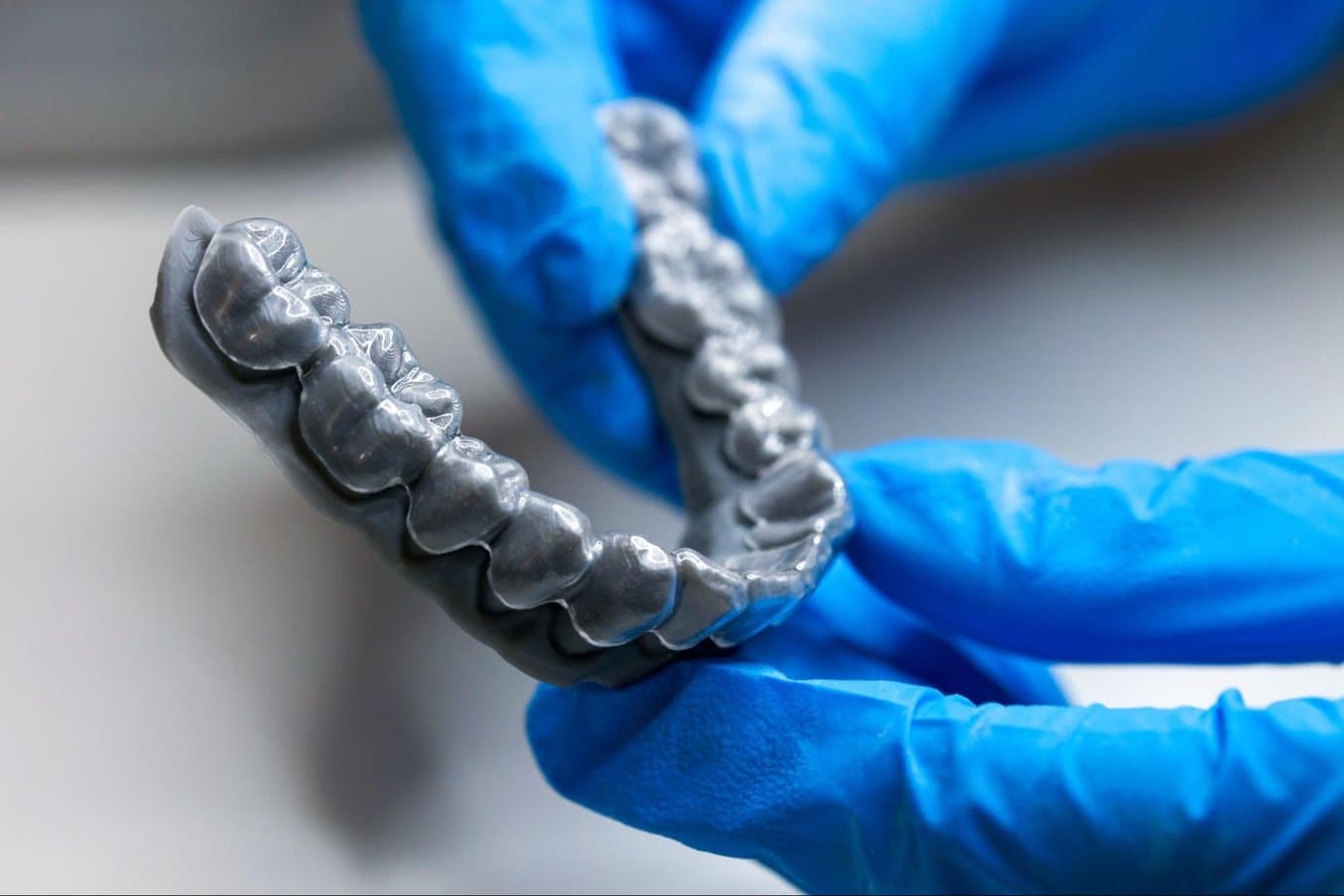
Vakuumformen und Druckformen mit 3D-gedruckten Modellen sind die gängigen Produktionsweisen für transparente Aligner in der Kieferorthopädie.
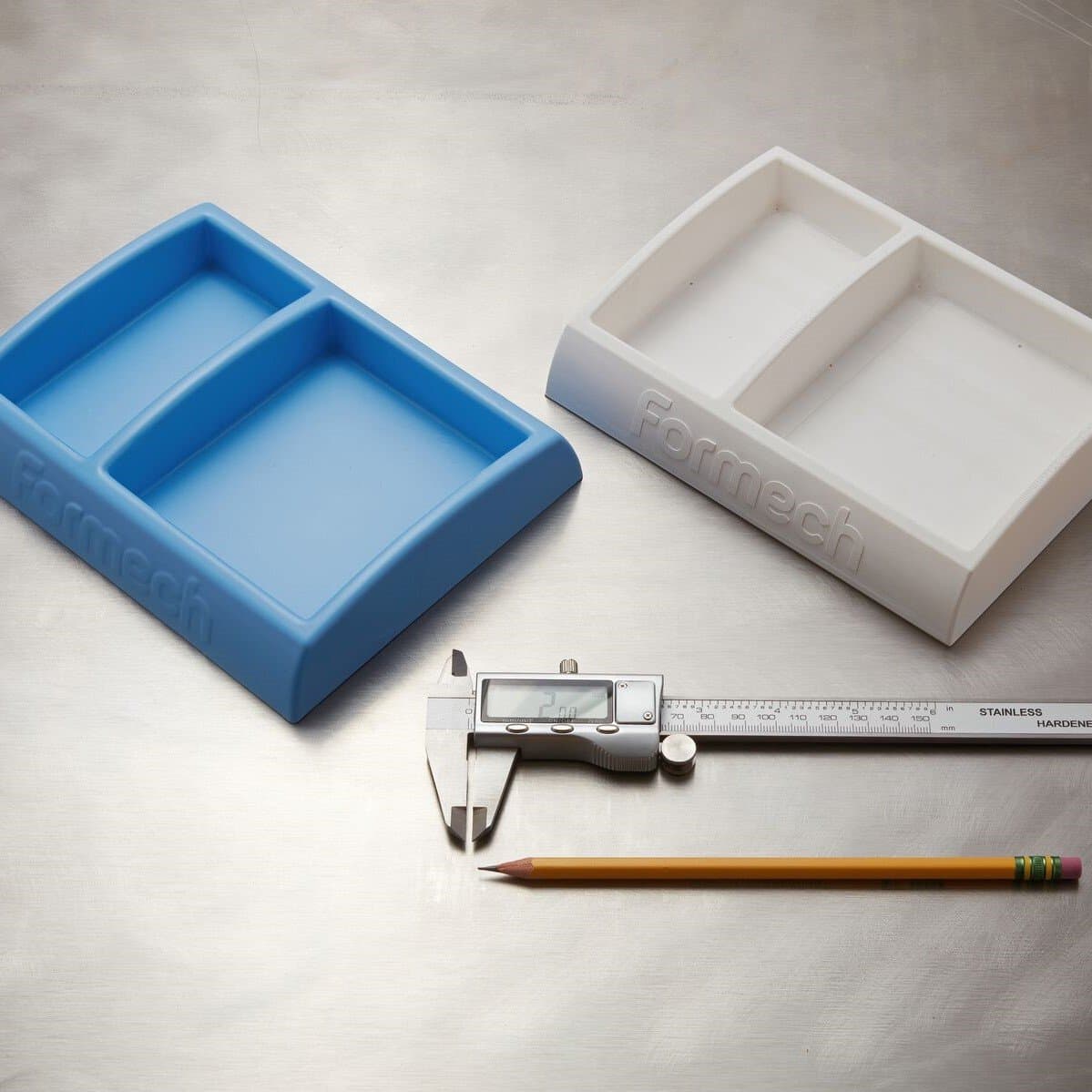
Schnelles Thermoformen mit 3D-gedruckten Formwerkzeugen: Ein praktischer Leitfaden
Beschleunigen Sie die Produktentwicklung, reduzieren Sie Kosten und Durchlaufzeiten und produzieren Sie maßgefertigte oder limitierte Produkte mit Leichtigkeit durch Thermoformen in Kombination mit 3D-gedrucktem Rapid Tooling.
So erstellen Sie Thermoformwerkzeuge mit 3D-Druck
Durch die Integration des 3D-Drucks zur Beschleunigung des Thermoformprozesses verändert sich der oben beschriebene traditionelle Arbeitsablauf. Mit 3D-Druck umfasst der Arbeitsablauf die folgenden Schritte:
-
Entwerfen Sie die Form mithilfe einer CAD-Anwendung.
-
Wählen Sie das passende Kunstharz aus unserer umfassenden Materialbibliothek aus und drucken Sie das Teil mit einem SLA-3D-Drucker von Formlabs.
-
Setzen Sie die 3D-gedruckte Form in die Thermoformmaschine ein und führen Sie den Produktionsprozess durch.
-
Entfernen Sie das Teil und führen Sie alle etwaigen Nachbearbeitungsschritte durch, um den produzierten Artikel einsatzbereit zu machen.
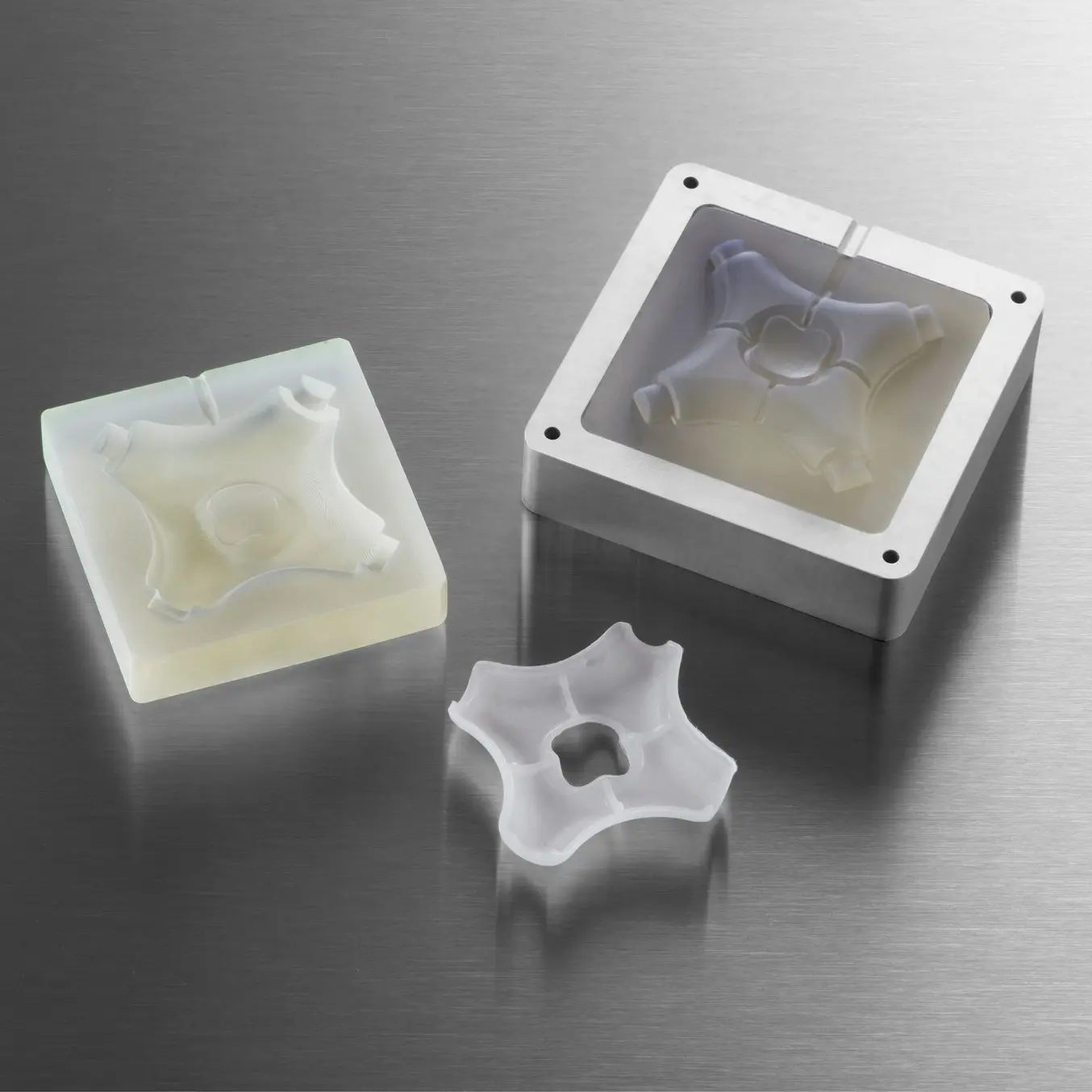
Formenbau durch 3D-Druck: Techniken für Prototyping und Produktion
Laden Sie unser Whitepaper über sechs Arten von Gussformen und Formwerkzeugen herunter, die sich mit einem betriebsinternen SLA-3D-Drucker herstellen lassen, für Spritzguss, Vakuumformen, Silikonformenbau und mehr.
Legen Sie los mit dem 3D-Druck von Thermoformwerkzeugen
Durch Kombination des Thermoformverfahrens mit 3D-gedruckten Formen erreichen Sie in Ihrem Produktionsprozess eine bessere Flexibilität, Agilität, Skalierbarkeit und Kosteneffizienz. Validieren Sie Ihre Designs und Materialwahl, noch bevor Sie zur Massenproduktion übergehen, und produzieren Sie individualisierte Endverbrauchsteile oder Sondereditionen mithilfe des Thermoformverfahrens und 3D-gedruckten Formen.
Laden Sie sich unser Whitepaper herunter, um mehr über Designleitfäden, detaillierte Arbeitsabläufe, die Bedingungen des Umformungsprozesses und reale Fallstudien des Thermoformens mit 3D-gedruckten Formen zu erfahren.