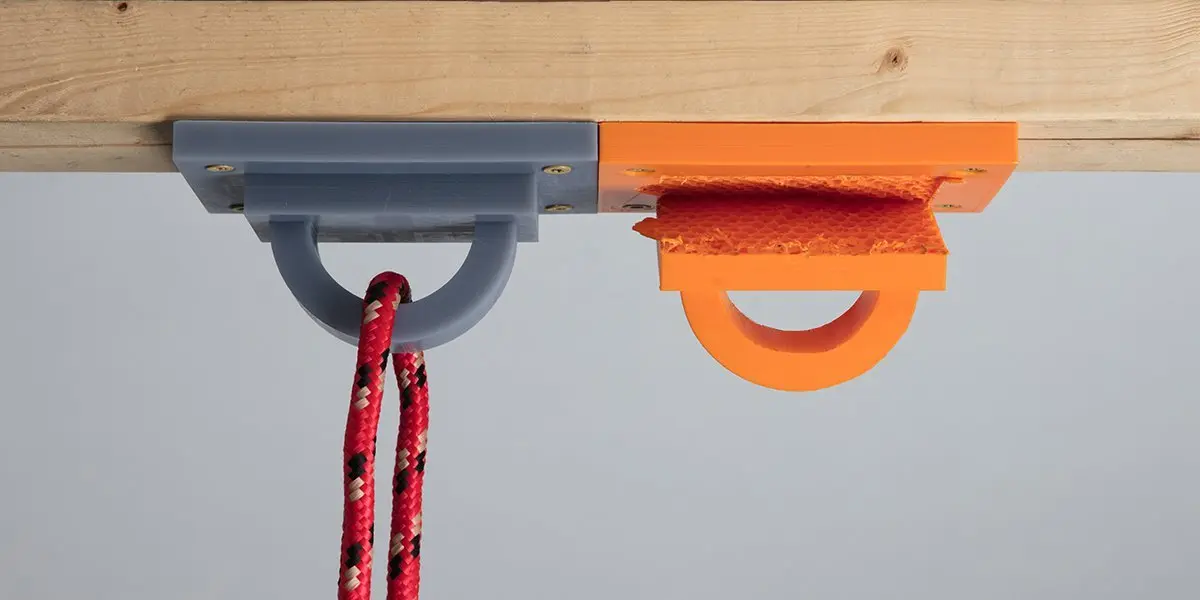
Es gibt viele Aspekte, die bei der Vorbereitung eines Objekts für den 3D-Druck berücksichtigt werden müssen. Dazu gehört die Ausrichtung des Objekts auf der Konstruktionsplattform: Ist die Oberfläche groß genug, damit das Teil haften bleibt? Ist die Zahl der ungestützten Überhänge so klein wie möglich? Und ist der Abstand zwischen den einzelnen Objekten groß genug?
Zu diesen Erwägungen kommt noch eine weitere, falls das Teil erheblicher Belastung standhalten soll: die Anisotropie.
Anisotropie bedeutet in diesem Kontext, dass sich die physikalischen Eigenschaften je nach Richtung unterscheiden. So kann ein 3D-Druck beispielsweise in X-, Y- und Z-Richtung unterschiedliche Bruchdehnung oder Steifigkeit aufweisen.
Isotropie und Anisotropie sind Konzepte, die beim Thema 3D-Druck häufig besprochen werden, doch in einigen Fällen basieren die grundlegenden Annahmen auf Verallgemeinerungen.
Häufig werden nur Schmelzschichtung-Drucker (FDM) betrachtet, bei denen Polymere geschmolzen und zu soliden Fertigteilen gehärtet werden. Anschließend wird das Konzept der strukturellen Anisotropie intuitiv auf andere Drucktechnologien wie den kunstharzbasierten Stereolithografie-3D-Druck (SLA) übertragen.
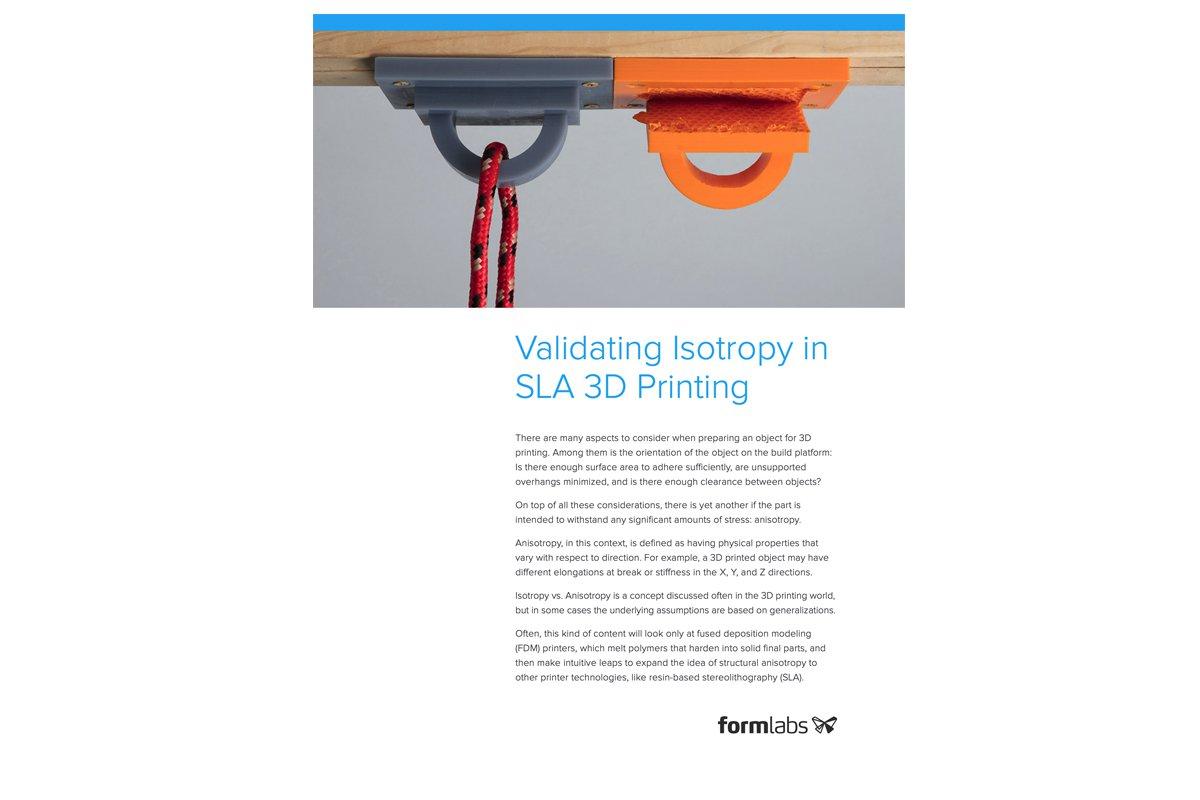
Validierung von Isotropie beim SLA 3D-Druck
Sie haben gerade keine Zeit zum Lesen? Laden Sie das PDF des Beitrags herunter.
*Auf Englisch.
Als PDF herunterladenWeshalb FDM-Teile anisotrop sind
3D-Drucker bauen Teile Schicht für Schicht auf. Allerdings kommen je nach Technologie unterschiedliche Methoden zum Einsatz. Dies hat wiederum eine bedeutende Auswirkung auf die Molekularstruktur der Teile.
Beispielsweise schmelzen FDM-Drucker Kunststoffschichten auf vorhergehende Schichten. Dies sorgt für mechanische (nicht chemische) Adhäsion. Wie in diesem Experiment demonstriert wurde, haften die FDM-Schichtoberflächen nicht vollständig aneinander. Selbst wenn die vorherige Schicht teilweise geschmolzen ist, haften die umliegenden Schichten nur zum Teil an ihren Nachbarn.
Darum haben die so hergestellten FDM-Objekte unterschiedliche mechanische Eigenschaften je nach der Richtung der mechanischen Beanspruchung, die auf sie wirkt. Sie sind ebenfalls weniger dicht als ähnliche Objekte, die mit anderen Methoden wie Spritzguss hergestellt werden. Aus demselben Grund lassen sich wasserdichte Objekte mit FDM-Druck nur schwer herstellen: FDM-Drucke sind voller mikroskopischer Hohlräume und Löcher.
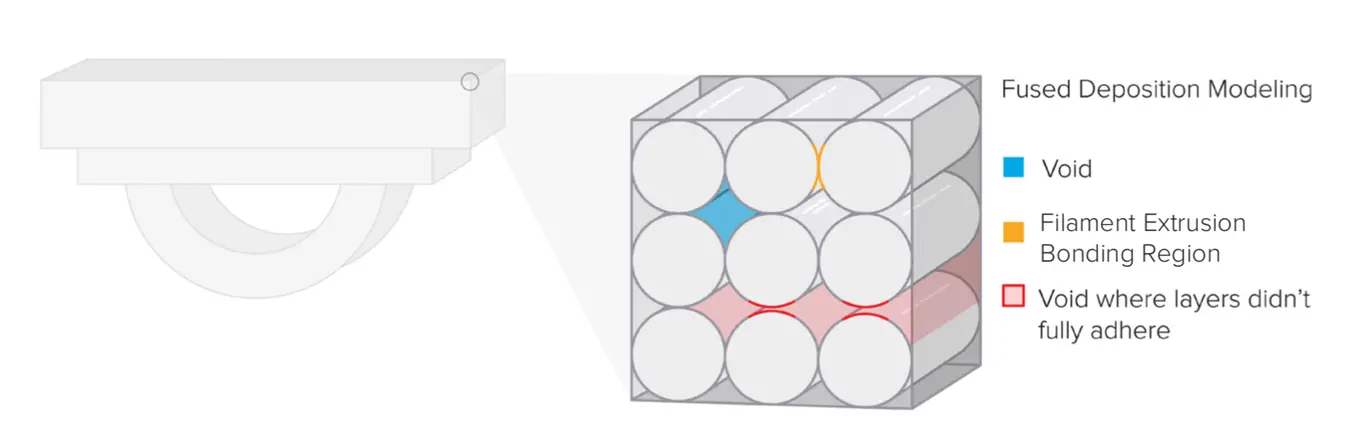
FDM 3D-Drucker bilden Schichten, indem sie Linien aus PLA oder ABS auftragen. Dieser Prozess führt dazu, dass die Schichten miteinander nicht so stark verbunden sind wie die einzelnen Linien (Filamentextrusion) in sich selbst. Es gibt Hohlräume zwischen den abgerundeten Linien und so ist es möglich, dass die Schichten nicht vollständig aneinander haften.
Wenn man diese Anordnung auf der molekularen Ebene betrachtet, gibt es einen klaren Unterschied zwischen den Kräften innerhalb der einzelnen Schichten und den Kräften, die die Schichten zusammenhalten: Jede aufgetragene Linie aus PLA oder ABS besteht aus stark vernetzten Polymerketten, die eng miteinander verbunden und somit ziemlich fest, belastbar und steif sind.
Wenn zusätzliche Linien neben oder auf vorhergehende Linien aufgetragen werden, ist es sehr schwierig – ja geradezu unmöglich –, dasselbe Maß an Vernetzung zwischen den einzelnen Linien zu erzielen. So entstehen Verbindungen zwischen den Fasern, die deutlich weniger fest und steif sind.
Das bedeutet, dass bei einem bestimmten Auftragungsmuster das Teil in der Richtung der aufgetragenen Linie am stärksten ist und schwächer entlang der Achsen, die vor allem aus diesen Haftregionen zwischen den einzelnen Fasern bestehen, nämlich entlang der zwei Raumachsen, die im rechten Winkel zur Linienachse verlaufen.
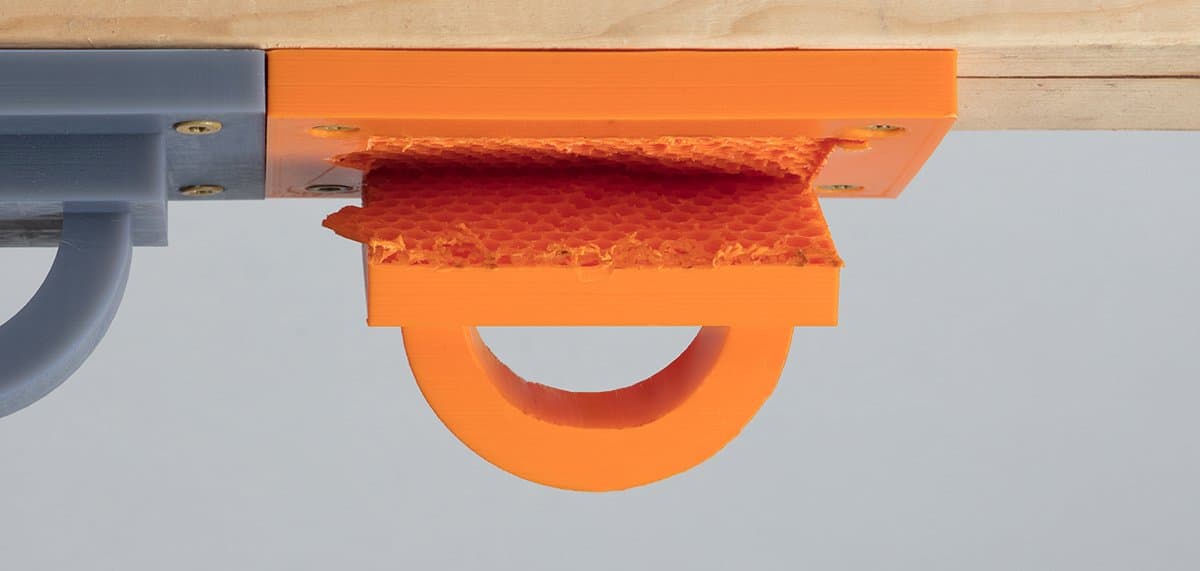
FDM-Drucke sind anisotrop – unter Gewichtseinwirkung kann es bei FDM-Druckteilen zum Versagen kommen, wenn sie nicht korrekt ausgerichtet sind oder nicht unter Berücksichtigung der Anisotropie modelliert wurden.
Kurzum: FDM-Drucke sind nicht gleich fest in alle Richtungen und können nicht isotrop sein, weshalb die Ausrichtung beim Gestalten und Drucken von lasttragenden Teilen eine Rolle spielt.
Weshalb SLA-Teile isotrop sind: Theorie
Beim kunstharzbasierten SLA 3D-Druck gibt es keinen Unterschied zwischen den chemischen Bindungen, die die einzelnen Schichten bilden, und den Kräften, die die Schichten zusammenhalten.
Während der Schichtbildung reagieren die Kunstharzmonomere miteinander und gehen kovalente Bindungen ein. Dies bewirkt einen hohen Grad an lateraler Festigkeit, aber die Polymerisierungsreaktion wird nicht bis zum Abschluss weitergeführt. Stattdessen wird der Druckvorgang so moduliert, dass die Schicht in einem semi-reaktiven Zustand verharrt, der als „grün“ bezeichnet wird.
Dieser grüne Zustand unterscheidet sich auf eine sehr wichtige Weise vom vollständig ausgehärteten Zustand: Auf der Oberfläche befinden sich noch immer polymerisierbare Gruppen, mit denen nachfolgende Schichten kovalente Bindungen eingehen können.
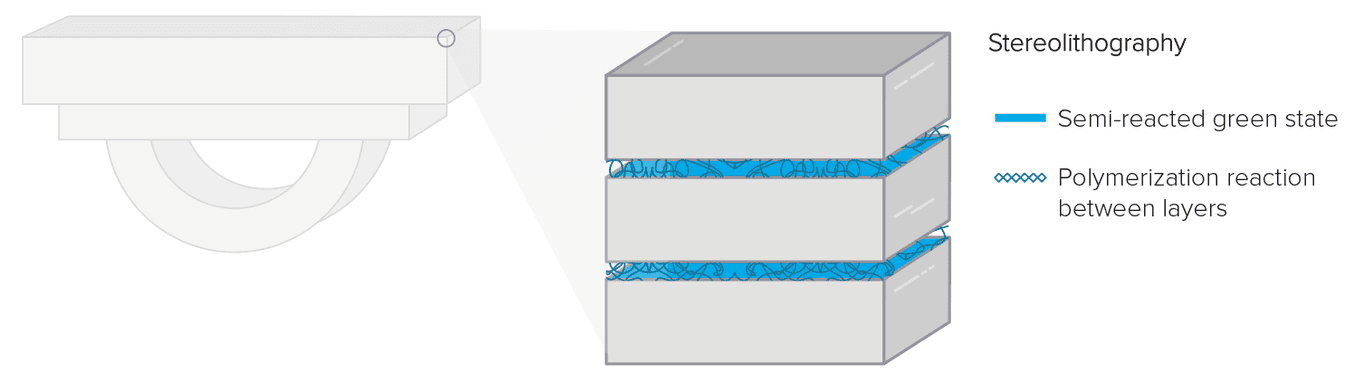
Bei SLA-Druckteilen gibt es durch chemische Bindungen keinen Unterschied zwischen der Z-Achse und der XY-Ebene. Jedes auf einem SLA-Gerät gedruckte, durchgängige Teil ist ein fortlaufendes Polymernetzwerk.
Bei der Aushärtung der nächsten Schicht werden die Gruppen der vorherigen Schicht in die Polymerisierungsreaktion einbezogen und gehen nicht nur lateral kovalente Bindungen ein, sondern auch mit der vorherigen Schicht. Diese Querverbindung ist typisch für alle SLA-Druckprozesse.
Das bedeutet, dass es auf Molekularebene im Hinblick auf die chemischen Bindungen kaum einen bis keinen Unterschied zwischen der Z-Achse und der XY-Ebene gibt. Jedes auf einem SLA-Gerät gedruckte, durchgängige Teil ist ein einzelnes Molekül. Da die SLA-Linien vollständig mit ihren Nachbarn verbunden sind, gibt es keine Hohlräume oder mikroskopischen Risse, wie bei FDM typisch. Diese Druckteile sind wasserdicht und volldicht.
SLA-Druckteile, die auf diese Weise entstehen, sind faktisch isotrop.
So viel zur Theorie, wie steht es mit der Praxis?
Wie sieht das in der Praxis aus? Müssen Sie sich wirklich keine Gedanken darüber machen, wie Sie das SLA-Druckteil ausrichten, wenn es etwas Spannung standhalten soll? Wir haben beschlossen, die Theorie auf die Probe zu stellen, und verwenden dazu einen Form 2, Clear Resin und unsere betriebseigene Zugprüfmaschine.
Wir verwendeten eine Zugprüfmaschine, um die Unterschiede zwischen Zugfestigkeit und Elastizitätsmodul bei FDM- und SLA-Drucken zu messen.
Damit die gesamte Bandbreite an Winkeln berücksichtigt wird, haben wir fünf Zugproben nach ASTM Type IV in Schritten von 15 Grad von 0 (flach auf der XY-Ebene) bis 90 Grad (vertikal) gedruckt. Jede Zugprobe wurde in Isopropylalkohol (IPA) gewaschen, nachgehärtet und in der Zugprüfmaschine eingespannt.
Die Zugprüfmaschine streckt die Proben mit konstanter Geschwindigkeit, bis diese brechen. Dabei wird aufgezeichnet, wie viel Kraft die Proben entgegensetzen. Auf Grundlage dieser Daten kann eine Vielzahl an Materialeigenschaften bestimmt werden, von denen die wichtigsten die maximale Festigkeit und der Elastizitätsmodul sind.
Maximale Belastung
Die maximale Belastung ist die höchste Zugkraft, der die Probe standhält, bevor sie bricht. Dies ist für gewöhnlich das, was gemeint ist, wenn von einem „festen Material“ gesprochen wird.
Es ist leicht zu erkennen, wie die maximale Zugbelastung als Maß für die Anisotropie verwendet werden kann: Ein Teil mit schwachen chemischen Bindungen zwischen den Schichten würde eine deutlich geringere Festigkeit aufweisen, wenn die Zugkraft im rechten Winkel zur XY-Ebene angewendet wird.
Tatsächlich ist genau das in einem vorherigen Experiment mit FDM-Drucken passiert, wobei die Streckfestigkeit in Z-Achsenrichtung etwa 55 Prozent des Werts der X-Achse betrug.
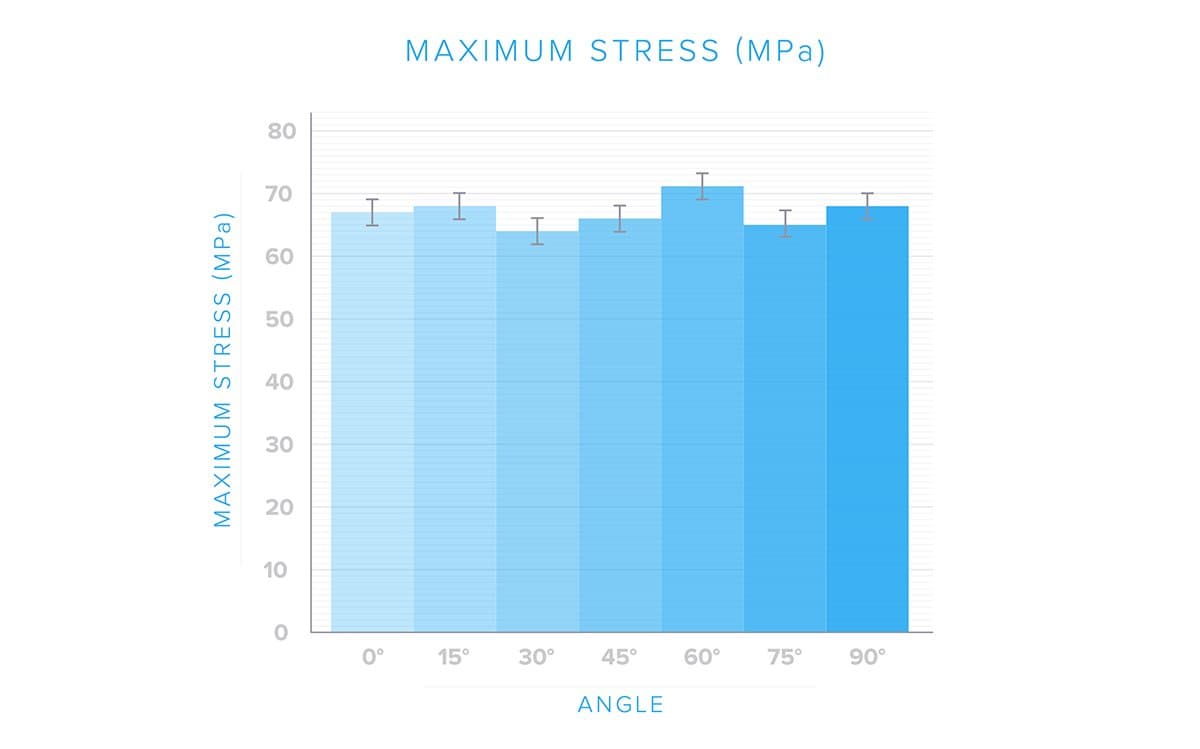
Die maximale Zugbelastung beim Teil blieb bei allen Winkelvarianten gleich. Das bedeutet, dass das Teil mit Hinblick auf die Zugfestigkeit isotrop ist.
Wären die SLA-Druckteile anisotrop gewesen, hätten wir einen Rückgang der Zugsbelastung erwarten müssen, je mehr sich der Druckwinkel 90 Grad nähert.
Um unsere Erkenntnisse zur Festigkeit zu validieren, haben wir auch den Elastizitätsmodul für die einzelnen Winkel erfasst.
Elastizitätsmodul
Der Elastizitätsmodul ist eine Messgröße für die Steifigkeit und gibt das Maß der Flexibilität eines Objektes an. Er ist besonders wichtig für Ingenieure, die auf Grundlage erwarteter Belastungen und Verformungen Designentscheidungen treffen müssen.
Wie bei der Streckfestigkeit wird auch hier erwartet, dass schwächere Bindungen zwischen den Schichten zu einem Rückgang des Elastizitätsmoduls führen, wodurch dieser sich als weiterer interessanter Messwert zur Untersuchung der Isotropie bei SLA-Druckteilen eignet.
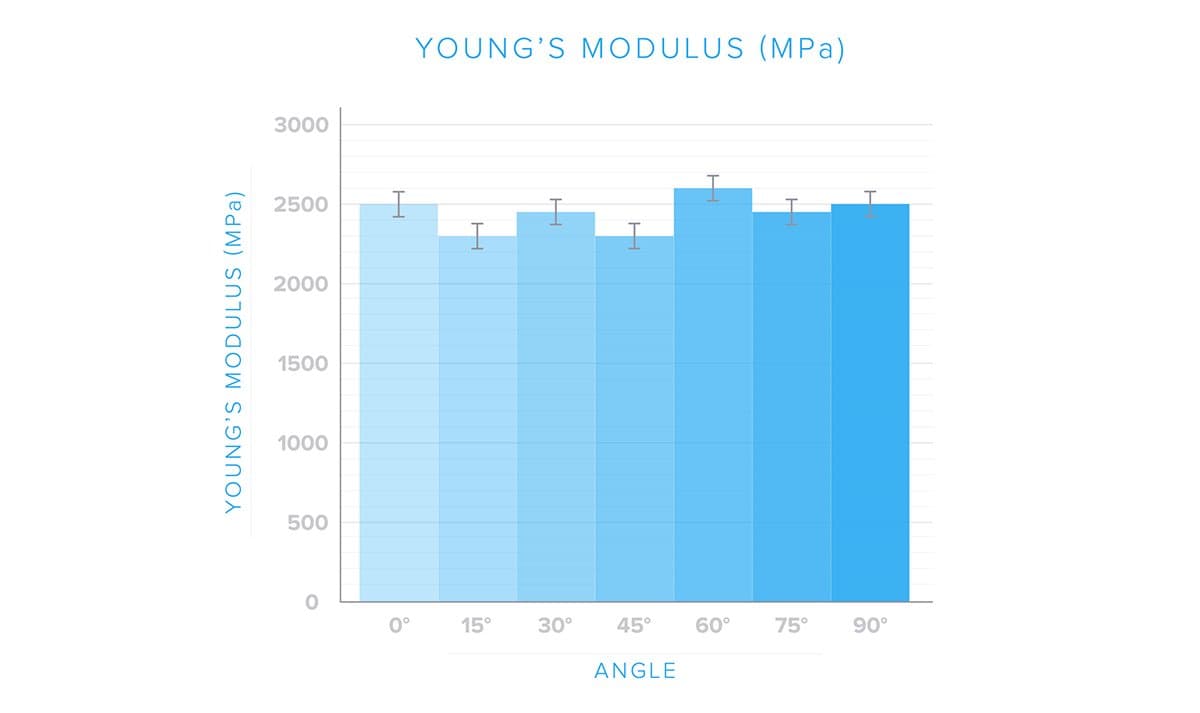
Genau wie die maximale Festigkeit bleibt der Elastizitätsmodul unabhängig vom Druckwinkel etwa gleich. Somit ist der Elastizitätsmodul ebenfalls isotrop im Hinblick auf den Druckwinkel.
Wie erwartet, liegen die Daten des Elastizitätsmoduls ebenfalls grob auf einer horizontalen Linie und weisen so erneut darauf hin, dass die Druckausrichtung keine Auswirkung auf die Materialeigenschaften von SLA-Druckteilen hat. Dies unterstützt die Hypothese, dass SLA-Druckteile tatsächlich isotrop sind.
Das Urteil: SLA-Teile sind isotrop
Aus den Ergebnissen ergibt sich diese Schlussfolgerung: SLA 3D-Drucker produzieren Teile, die in Z-Richtung genauso fest und belastbar sind wie in X- und Y-Richtung, unabhängig davon, wie sie gedruckt werden. Dadurch eignet sich SLA besonders für die Prototypenentwicklung im Maschinenbau, bei der es auf die Materialeigenschaften ankommt.
Besuchen Sie unsere Materialseite, um mehr über Formlabs Kunstharze zu erfahren, und fordern Sie einen kostenlosen Probedruck an, um sich selbst von der SLA-Qualität zu überzeugen.