Validierungstests in der Produktentwicklung: Vom Konzeptnachweis zum EVT, DVT und PVT zur Massenproduktion
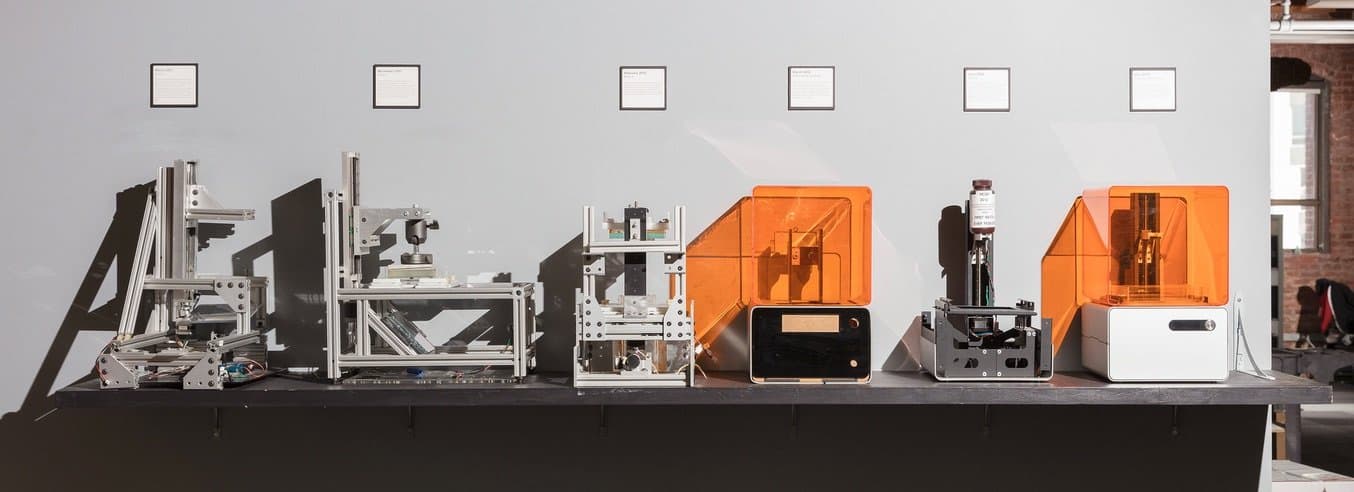
Eine einfache Daumenregel besagt, dass Änderungen an einem Produkt umso kostspieliger sind, je länger sich seine Entwicklung hinzieht. Eines der zentralen Ziele jeder Initiative zur Entwicklung eines neuen Produkts lautet daher: Probleme frühestmöglich lösen, um Risiken kostspieliger Iterationen in nachgelagerten Phasen zu verringern.
Genau da kommt das Konzept der Validierungstests ins Spiel. Dahinter verbirgt sich eine strukturierte Methodik mit klar voneinander abgegrenzten Phasen, anhand derer geprüft wird, ob ein bestimmtes Teil den für seine jeweilige Entwicklungsphase festgelegten Anforderungen genügt und somit die nötige Reife erreicht hat, um in die nächste Phase voranzuschreiten. Im Verlauf dieses Prozesses entwickeln Design- und Ingenieursteams Prototypen in unterschiedlichsten Ausführungen. Jede dieser Phasen bietet Raum, um Erkenntnisse zu sammeln, Ideen auszuloten und diese anzupassen, wobei das Produkt die für die jeweilige Phase definierten Kriterien erfüllen muss, bevor es in die nächste übergehen und schließlich erfolgreich in Massenproduktion gehen kann.
Im Folgenden beleuchten wir Ansätze zur Optimierung von Entwicklungsprozessen auf dem Weg zur Massenproduktion und gehen auf die verschiedenen Phasen der Produktreife mit Blick auf Zielsetzungen und Aktivitäten, gelöste Probleme, erstellte Prototypen und Abschlusskriterien ein.
Was spricht für Validierungstests?
Kaum ein Produktdesign ist direkt vom ersten CAD-Modell an produktionsbereit. Auch ein simples Kunststoffteil nicht, kann doch selbst dieses unschöne Einfallstellen, Fließspuren oder Schwachstellen als Folge ungleichmäßiger Abkühlung in der ersten geformten Charge aufweisen. Womöglich stellt sich aber auch ein Bereich als zu klein für die gesetzlich vorgeschriebenen Etiketten heraus, oder es bestehen unter bestimmten Bedingungen Probleme mit den Toleranzen an der Verbindungsstelle zu einem anderen Teil. Vielleicht ergibt sich vonseiten einer zentralen Nutzergruppe aber auch eine neue Anforderung von höchster Priorität, aufgrund derer das Designteam einen weiteren Entwicklungszyklus anstoßen muss.
Im Designprozess sind kontinuierliche Erweiterungen, Feinjustierungen und Richtungsanpassungen wie diese ebenso erforderlich wie die Vorarbeit, bei der es Aspekte wie die serienmäßige Umsetzbarkeit, voraussichtliche Kosten, kundenseitig eingeholtes Feedback sowie Angelegenheiten rund um geistiges Eigentum und Zertifizierungsstandards zu eruieren und zu klären gilt.
Mit jedem weiteren Prozessschritt in Richtung Produktion steigen die Kosten für solche Iterationen in exponentiellem Maße. Denn zu Beginn des Entwicklungsprozesse sind es vielleicht 50 $ an Materialkosten, die für eine Reihe von vom Designteam angefertigten Skizzen und Schaumstoffmodellen anfallen. Eine stärker ausdifferenzierte, etwa mittels Rapid Prototyping im 3D-Drucker gefertigte Produktausführung einschließlich zugekaufter Teile und einer Umspritzung im Vakuumspritzgussverfahren kann dagegen bereits mit rund 500–1000 $ zu Buche schlagen. Anpassungen der Werkzeugausstattung in der Produktionsphase wiederum können die Kosten bereits auf bis zu 50 000 $ in die Höhe treiben und zudem Verzögerungen von mehreren Wochen oder sogar Monaten nach sich ziehen.
Bei komplexen Produkten gehen die Produktionskosten nicht selten in die Millionen. Und blickt man auf noch anspruchsvollere Projekte wie etwa Flugzeuge, dann sind dort nicht zuletzt auch Tausende an Mitarbeitern involviert, während sich die Fixkosten für die Herstellung gut und gerne auf Summen von mehreren Milliarden belaufen. Um solcherlei Verzehn- oder Verhundertfachungen der Kosten oder andere Katastrophen bestmöglich zu vermeiden, wägen Designer und Ingenieure für jeden einzelnen ihrer Schritte die Wahrscheinlichkeit seiner Iteration gegenüber der seiner Erfolgs ab. Und genau hierfür sind Validierungstests essenziell wichtig. Denn durch sie bleibt gewährleistet, dass ein Design die zur jeweiligen Entwicklungsphase passenden Anforderungen erfüllt. Die Abgrenzung der einzelnen Phasen anhand klarer Abschlusskriterien und zu erreichenden Ergebnissen stellt dabei eine optimale Ressourcennutzung sowie sukzessive Qualitätsverbesserungen sicher.
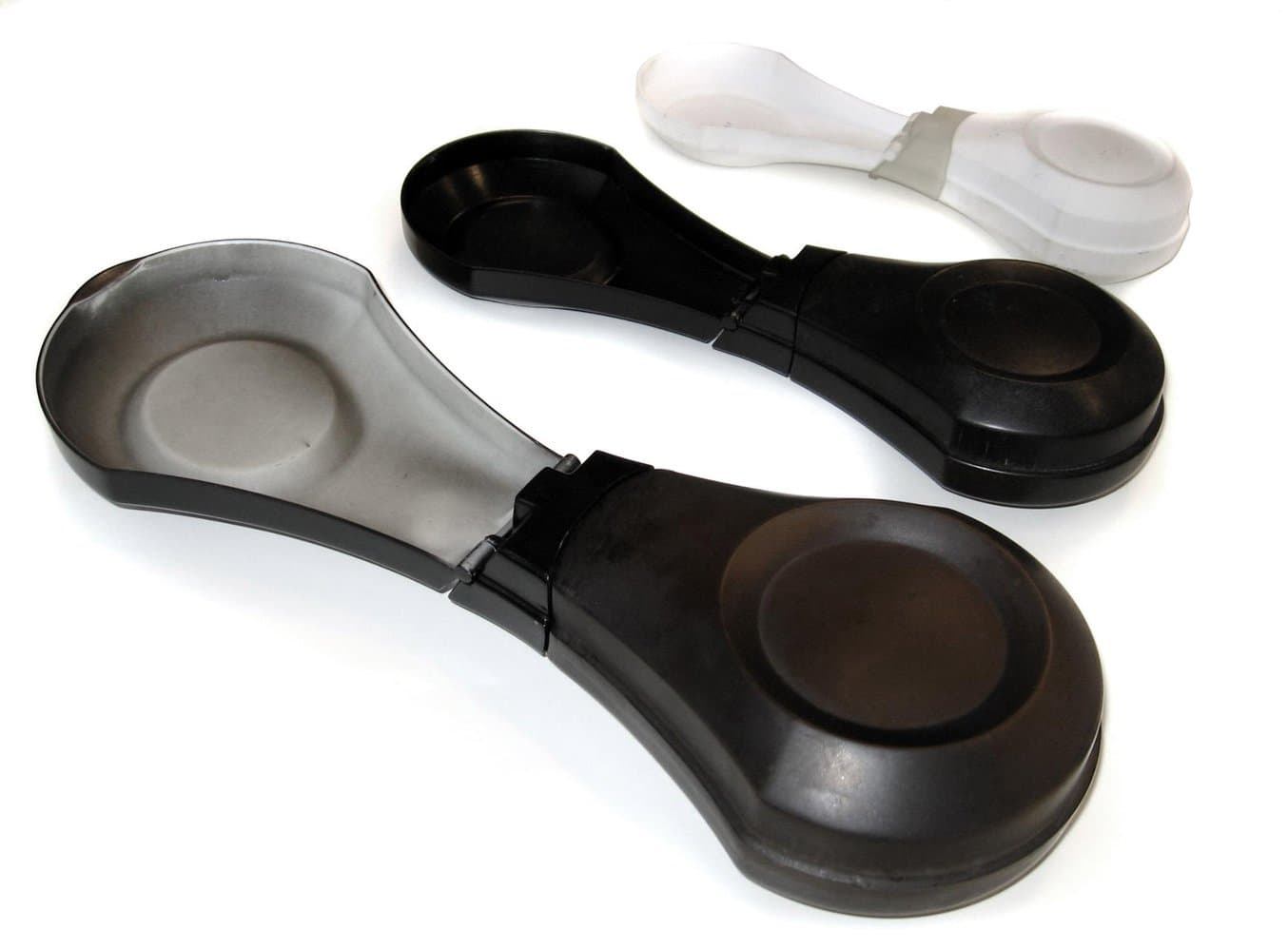
Die verschiedenen Phasen der Reife eines Verbraucherprodukts, ausgenommen des ersten Modells. Hinten: EVT-Modell, hergestellt mittels SLS- und SLA-3D-Druck. Mitte: Probeexemplar eines DVT-Modells, hergestellt mit Kunststoffwerkzeugen. Vorne: PVT-Modell, hergestellt mit Metallwerkzeugen. Zur Verfügung gestellt von IDZone Product Design
Phasen der Produktreife
Konzeptnachweis und Prototypenentwicklung
Den Startschuss zur Neuproduktplanung (NPP) gibt die Unternehmensführung, die für das jeweilige Projekt das Marktpotenzial ermittelt und die Produktpositionierung ausarbeitet, eine technologische Beurteilung vornimmt sowie eine Lieferkettenstrategie definiert und die Ressourcenzuteilung bestimmt. Von da ab wird der Entwicklungsprozess in der Regel in ein Produktteam übergeben, das diese Punkte allesamt in einem Lastenheft (auch „Anforderungespezifikation“) zusammenfassen und in brauchbare Konzepte überführen muss.
Der erste Schritt besteht in einem Konzeptnachweis – manchmal auch Machbarkeitsnachweis/Machbarkeitsstudie oder PoC (von Englisch „Proof of Concept“) –, der als früher Test einer Idee, eines Verfahrens oder eines Produkts verwendet wird, um dessen Potenzial und Machbarkeit unter realen Gegebenheiten zu prüfen. Aus diesen Konzepten entstehen im weiteren Verlauf die Prototypen, die als bereits voll funktionsfähiges Modell des Produkts genau aufzeigen, wie dieses in Bezug auf Mechanik, Design, Nutzererlebnis usw. funktioniert.
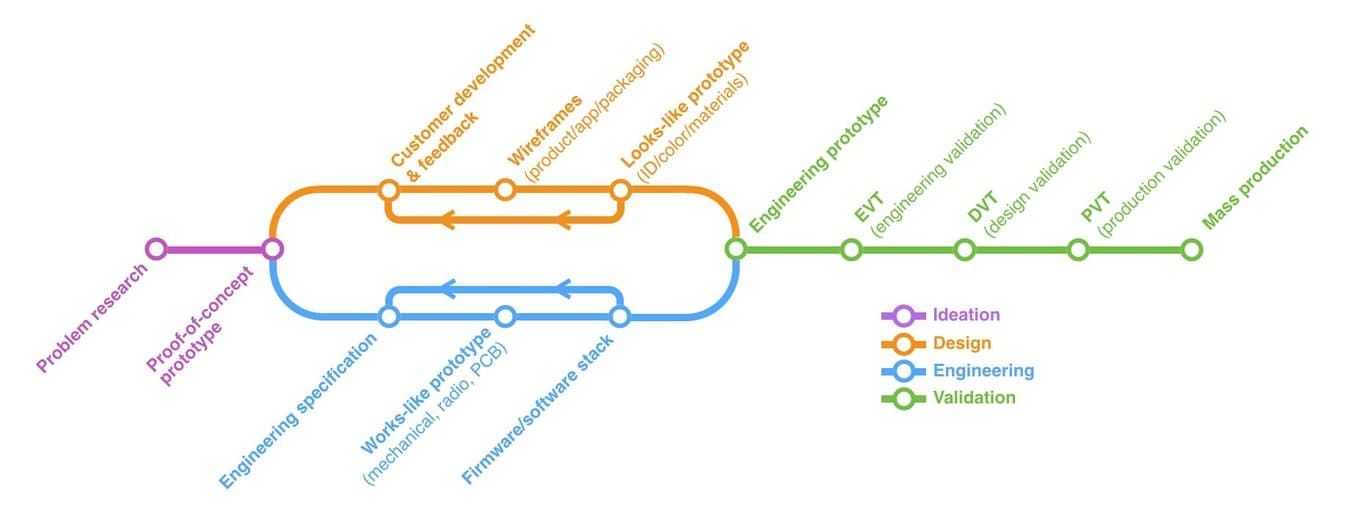
Die verschiedenen Phasen der Produktentwicklung auf dem Weg zur Massenproduktion. (Quelle)
Ein Prototyp ist eine Ausführung des Produktdesigns, über die sein Nutzen in Bezug auf bestimmte Anforderungen präsentiert und beurteilt werden kann. Dabei können Prototypen etwa in Form früher, von Hand hergestellte Modelle etwa aus Ton, Karton, Schaumstoff oder Holz in Erscheinung, genauso aber auch als höchst detailtreue, funktionsfähige Prototypen aus dem 3D-Drucker oder einer Fertigungsanlage. Bestimmte Prototypen repräsentieren nur einen Teil der Produktanforderungen. Diese Modelle bilden etwa die Optik oder Funktionalität des Designs ab oder dienen zur Veranschaulichung einer einzelnen Form oder Funktion, um über diese bestimmte nachgelagerte Funktionalitäten zu testen. Ein Modell, das sämtliche Anforderungen und Funktionalitäten des Designs aufweist, wird als technischer Prototyp bezeichnet.
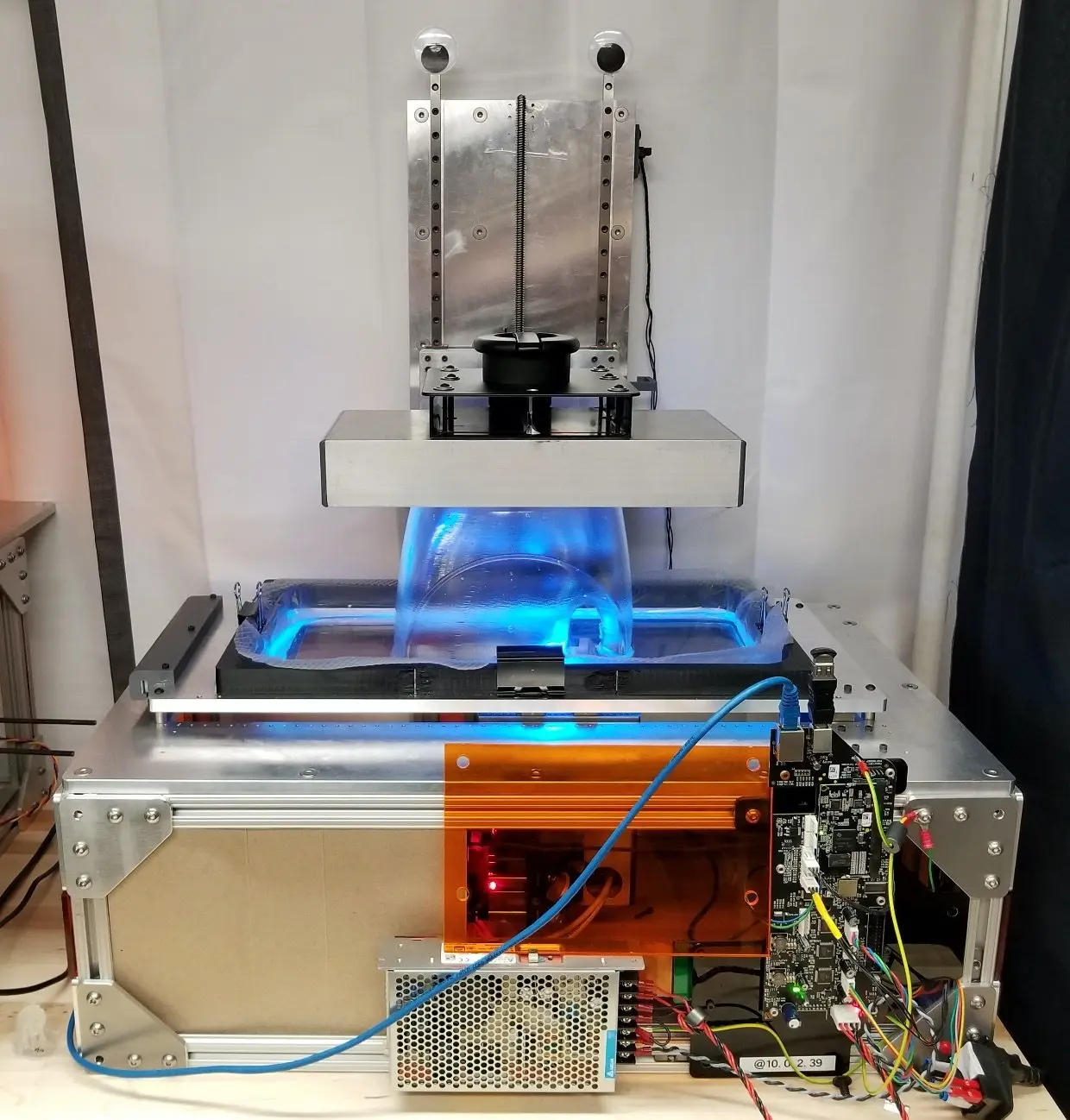
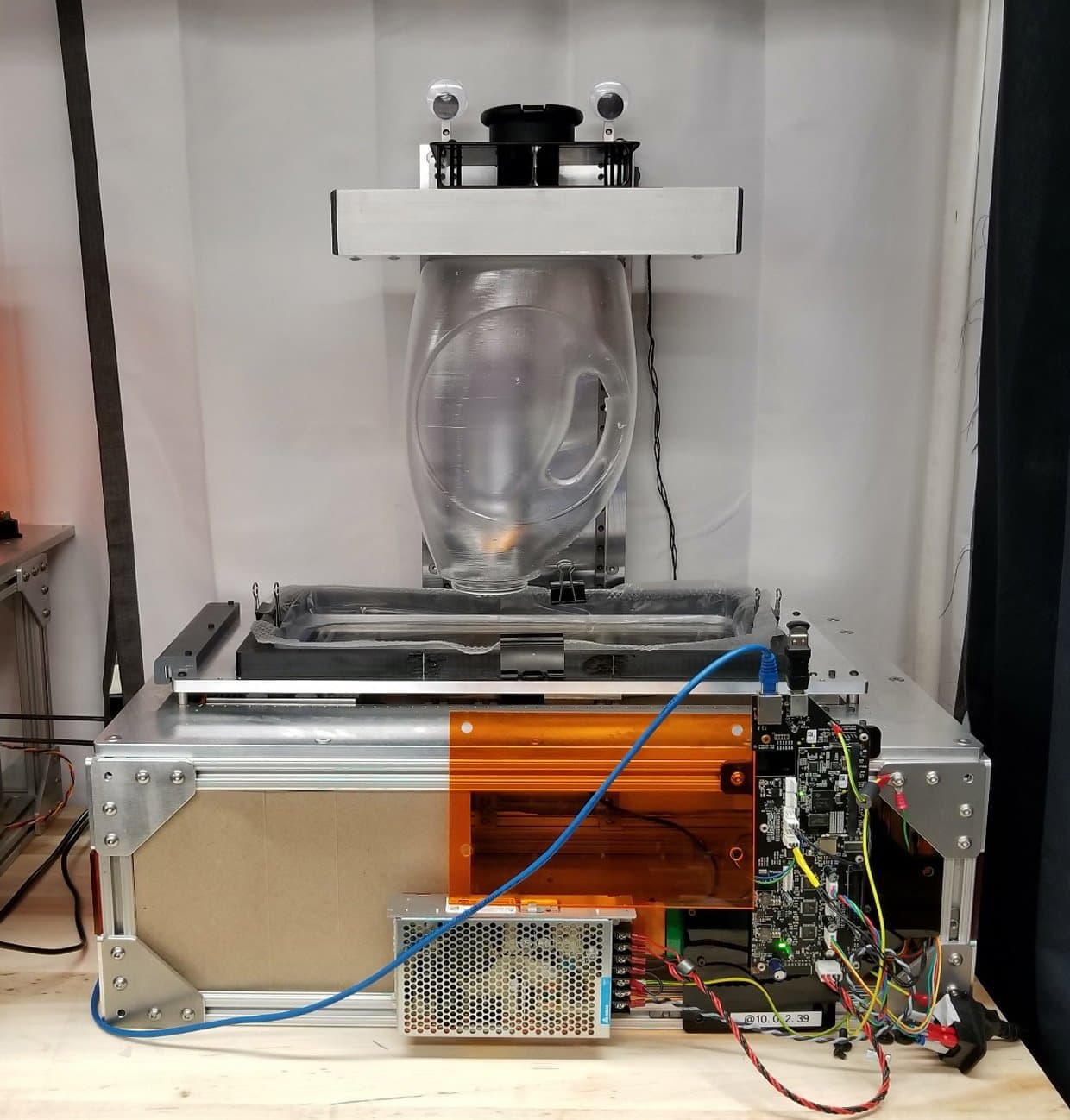
Frühe, bereits funktionsfähige Prototypen des Form 3L Großformat-SLA-3D-Druckers.
Im Entwicklungsverlauf entstehen Modelle, die das Produktdesign statt in seinem eigentlichen Formfaktor quasi in überdimensionaler Form abbilden und sämtliche funktionalen Komponenten in „Platzhalterversionen“ umfassen, um so die Funktionsweise des Produkts demonstrieren zu können. Die Elektronik wird dabei in Form rudimentärer Arbeitsversionen mithilfe von Hardwarebaukästen oder auch unter Verwendung eines Arduino oder Raspberry Pi umgesetzt.
Analytische oder virtuelle Prototypen sind Produktausführungen in nicht-materieller Form wie etwa 3D-Modelle. Verwendet werden diese für das Rendering, mathematische Simulationen oder auch Finite-Elemente-Analysen (FEA). Daneben gilt aber auch eine Skizze bereits als grobe Form eines virtuellen Prototypen.
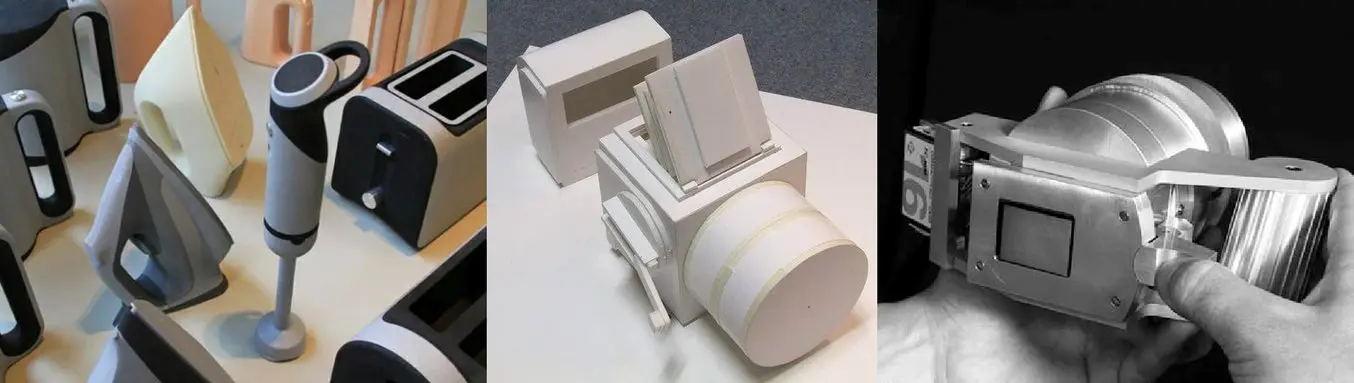
Testfähige Alpha-Prototypen in verschiedenen Detailausführungen: Links: Schaumstoffmodelle von Küchengeräten zur Abbildung der Optik. Zur Verfügung gestellt von Superior Prototype. Mitte: Modelle aus Schaumstoff/Pappkarton zur teilweisen Abbildung von Form und Interaktivität. Zur Verfügung gestellt von Frits van Beek. Rechts: Maschinell gefertigter, bereits in Teilen interaktiver Prototyp einer Digitalkamera im Alpha-Stadium: Das Design ist in dieser Form noch nicht für die Produktion vorgesehen. Zur Verfügung gestellt von Joep Frens.
Die Phase der Prototpenentwicklung ist unabdingbar für die Klärung von Detailfragen rund um Benutzerfreundlichkeit, Optik und versteckte Nutzeranforderungen, Feedback und Einschätzungen von anderen Designern, Produktmanagern und Fachexperten sowie rechtliche Belange und technische Einschränkungen. Bei einem komplexen elektromechanischen Produkt umfasst der Designprozess eine Vielzahl von Konzepten, für die jeweils diverse Skizzen für Sondierungsfragen erstellt werden, ebenso wie mehrere physische Produktausführungen und zahlreiche gerenderte 3D-Modelle.
Als etwa das Designteam von IDEO im Jahr 1987 die erste ergonomische Computer-Maus für Microsoft entwickelte, waren allein für ihre Form nicht weniger als 80 Schaumstoffmodelle nötig. Bei stärker risikobehafteten und komplexeren Prozessen sind aber zum Beispiel auch geradezu unfassbare 5127 Prototypen möglich, wie sie James Dyson in 15 Jahren Entwicklungsarbeit für den ersten sogenannten „Zyklonstaubsauger“ benötigte. Um die Entwicklung neuer Produkte zu beschleunigen und nicht im berüchtigten „Sumpf aus Hardware“ unterzugehen, braucht es mit Blick auf Prototypen einen konzentrierten Fokus auf die zentralen Anforderungen des Produkts. Dabei ebenso entscheidend ist es, potenziell in späteren Phasen auftretende Risiken einfließen zu lassen und in diesem Zuge auch Nutzertests zur Sondierung einzuplanen.
Zusammengefasst besteht in der Phase der Prototypenentwicklung das Ziel darin, einen technischen Prototypen zu erhalten, der so funktioniert und aussieht wie das finale Produkt. So dient diese Phase als Nachweis dafür, dass die eingesetzte Technologie den Anforderungen der Kunden entspricht, dass das Produkt fertigungstechnisch umsetzbar ist und zudem so funktioniert wie vorgesehen. Sobald dies nachgewiesen ist, geht es in den darauffolgenden Validierungsphasen an die Sicherstellung, dass das Produkt in großem Maßstab in Produktion gehen kann.
Technische Validierung
In der Phase der technischen Erprobung, auch „Engineering Validation Test“ oder kurz EVT genannt, dreht sich alles um den grundlegenden Funktionsumfang des Produkts und dessen Optimierung. Im Unterschied zum noch stark eingeschränkten „Alpha“-Prototypen aus der Entwicklungsphase entsteht hier nun ein technischer oder „Beta“-Prototyp, dessen Funktionsumfang bereits weitestgehend komplett ist. Definiert wird dieser in der Regel in einer sogenannten Konstruktionsmatrix. Der technische Prototyp ist eine in den Grundzügen gebrauchsfertige Version des kommerziellen Endprodukts, die nach den Prinzipien des sogenannten Design for Manufacturing (DFM), also dem „produktionsgerechten Gestalten“ konstruiert wird. Dieser Prototyp dient für Tests unter ausgewählten Nutzergruppen, zur Vorlage bei Werkzeugspezialisten, um in späteren Phasen die Produktion zu planen, sowie als Vorführteil in ersten Vertriebsmeetings.
Anhand einer sogenannten „Make-or-Buy-Analyse“ wird für alle Einzelkomponenten der Baugruppe beurteilt, ob diese in Eigenregie gefertigt oder extern bezogen werden, wobei für Sonderanfertigungen noch eine spezifische Prüfung und Auswahl vorgenommen wird. All dies wird dann in einer Stückliste für Angebotsanfragen bei Vertragsherstellern festgehalten, damit diese die für die erste Produktionslinie und Probeexemplare nötige Werkzeugausstattung vorbereiten. Bei Produkten mit elektronischen Komponenten werden zudem heißverprägte Leiterplatten entwickelt, wofür industrielle Verfahren zum Einsatz kommen. An dieser Stelle werden außerdem Leistungstests sowie Test zu Temperaturbeständigkeitstest und elektromatischen Störungen durchgeführt.
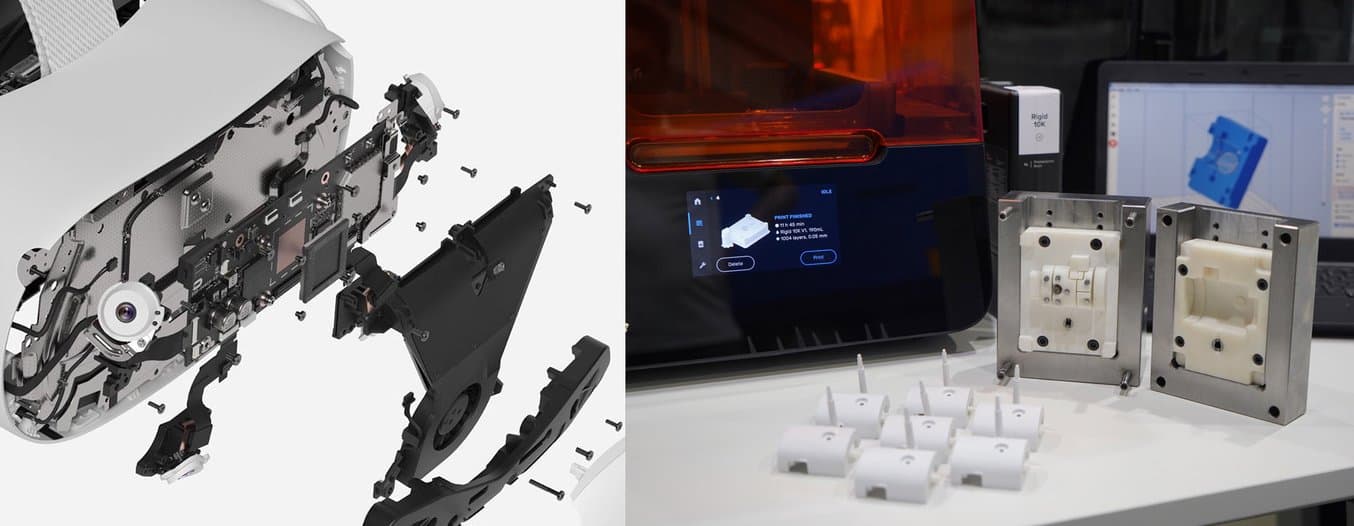
In der Phase der technischen Validierung typische Aktivitäten. Links: Darstellung eines für die Produktion vorgesehenen Produktdesigns in Form einer Explosionszeichnung. Zur Verfügung gestellt von Oculus. Rechts: Produktion kleiner Volumina von Spritzgrussformen mithilfe von Formen aus dem 3D-Drucker.
Gefertigt werden dann ca. 20 bis 50 Einheiten des Prototyps, dies entweder anhand von Präzisionsverfahren wie additiver Fertigung und CNC-Bearbeitung oder unter Verwendung von Kunststoffwerkzeugen. Letztere kommen dabei zum Einsatz, um eine Serie von Spritzgussteilen aus Silikon- oder 3D-gedruckten Formen herzustellen. Das übergeordnete Ziel dieser Phase besteht darin, sämtliche produktionstechnischen Aspekte im Design festzuhalten und am Ende eine kleine Stückzahl produktionstauglicher technischer Prototypen anzufertigen.
Designvalidierung
Der Designvalidierungstest (DVT) läutet die Phase ein, in der das Produkt zur eigentlichen Serienreife gelangt. Während bei der technischen Validierung der Fokus auf Design for Manufacturing in Bezug auf die Architektur liegt, geht es bei der Designvalidierung um die Detailarbeit auf dem Weg zur ersten Serie in Massenproduktion. Prägend für diese Phase sind umfassende Experimente und Optimierungsschritte. So werden etwa bei Leiterplatten intensive Fehlerdiagnosen und Maßnahmen zur Reduktion von Rauschspannungen vorgenommen und so das Tel von Iteration zu Iteration immer weiter perfektioniert. Für die einzelnen in Eigenregie gefertigten Teile wird beim Vertragshersteller die Entwicklung eines ersten Metallwerkzeugs veranlasst, um den Output in Serienproduktion zu bestimmen. Dabei kommen unter Umständen Aluminiumformen zum Einsatz, mit deren Hilfe das Design im Hinblick auf Oberflächenbeschaffenheit, Material, Toleranzen und Formenkonfigurationen (z. B. für Schieber und Klemmen), Verbindungsmethoden und Verfahrensparameter optimiert wird.
Gefertigt werden in der Regel zwischen 50 und 200 Exemplare, bei umfangreicheren Projekten sind aber auch 1000 und mehr nicht unüblich. Diese werden dann an das Designteam für betriebsinterne Prüfungen und letzte technische Anpassungen geliefert bzw. wird auch eine gewisse Stückzahl direkt als Beta-Produktausführung an potenzielle Kunden oder Expertentester übergeben. Diese ersten produktionsfertigen Exemplare werden verschiedensten Tests unterzogen, darunter beispielsweise solchen in der Klimakammer, zur Beständigkeit gegenüber Temperaturextremen und Chemikalien oder gemäß Anforderungen für Zertifizierungen etwa von FDA, FCC, UL, EC oder RoHS. Dazu kommen etwa auch Alterungs-, Strahlungs- und kosmetische Tests sowie solche zur Prüfung der Widerstandsfähigkeit gegenüber Verschleiß, Aufprall und mehr. Flankiert wird das Ganze durch ausgedehnte Nutzertests, die in realistischem Kontext unter einem signifikanten Anteil der Population durchgeführt werden.
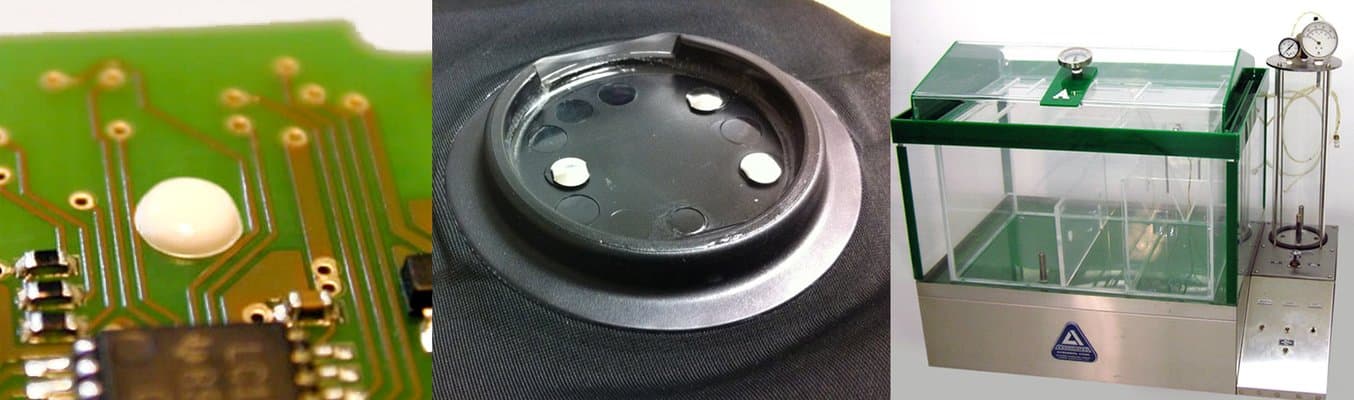
In der Phase der Designvalidierung liegt der Fokus ganz auf der Optimierung. Links: Leiterplatte, bei denen heißverprägte, integrierte Nieten die Verbindung zum Kunststoffgehäuse herstellen. Zur Verfügung gestellt von Hartmann. Mitte: Experiment, bei dem ein spritzgegossenes Kunststoffgehäuse in ein Stoffsubstrat eingefasst wird. Zur Verfügung gestellt von Bemis Sewfree. Rechts: Klimakammer für Korrosionstests durch Salzsprühnebel. Zur Verfügung gestellt von Associated Environmental Systems.
Zur Beschleunigung der Produktentwicklung besteht auch die Möglichkeit, die Phase der Designvalidierung zu beschleunigen, indem die Investition in Metallwerkzeuge ans Ende der Phase der technischen Validierung vorgezogen wird. Auf diese Weise ist der technische Prototyp direkt produktionstauglich, erfüllt damit also das Abschlusskriterium der technischen Validierung, während er zugleich auch dem Abschlusskriterum der Designvalidierung entspricht, für das die Ausstattung an Metallwerkzeugen einsatzbereit und die Beurteilung der Ausbeute in Serienproduktion abgeschlossen sein muss. Die Strategie, bereits in so einem frühen Stadium im Umfang der für die Phase der Produktvalidierung benötigten Ressourcen zu investieren, birgt jedoch enorme Risiken. Von derartigen Abkürzungen ist daher in den meisten, wenn nicht gar in allen Fällen abzuraten.
Produktvalidierung
Der Produktvalidierungstest (PVT) markiert die letzte Phase, bevor schließlich der Startschuss zur Massenproduktion in Serie fällt. Alle Metallwerkzeuge sind nun fest konfiguriert, entsprechend sind weder am Produktdesign noch an den Formen für die Produktion weitere Änderungen möglich. Halte- und Aufspannvorrichtung sowie Werkbänke müssen bereit und validiert sein, um den Produktionspiloten (PP) einzuleiten. Die Anstrengungen richten sich in dieser Phase auf die Optimierung und Stabilisierung von Produktion und Fertigungsstraßen in Bezug auf die Geschwindigkeit der Anlagen sowie die Schulung der Bediener, die Ausschussquote sowie die Ausbeute pro Tag.
Zur Identifikation von Risiken wie etwa der Abhängigkeit von einem einzelnen Vertragshersteller für den Bezug einer bestimmten Komponente werden Protokolle für das Risikomanagement wie etwa FMECA, FAI sowie weitere Qualitätskontrollmechanismen herangezogen. Bei Elektronikprodukten erfolgen zudem der erste Startvorgang sowie eine Prüfung der Firmware, außerdem werden in dieser Phase Produktverpackung und -handbücher gestaltet bzw. erstellt. Die Tätigkeiten in dieser Phase entfallen größtenteils auf den Vertragshersteller.
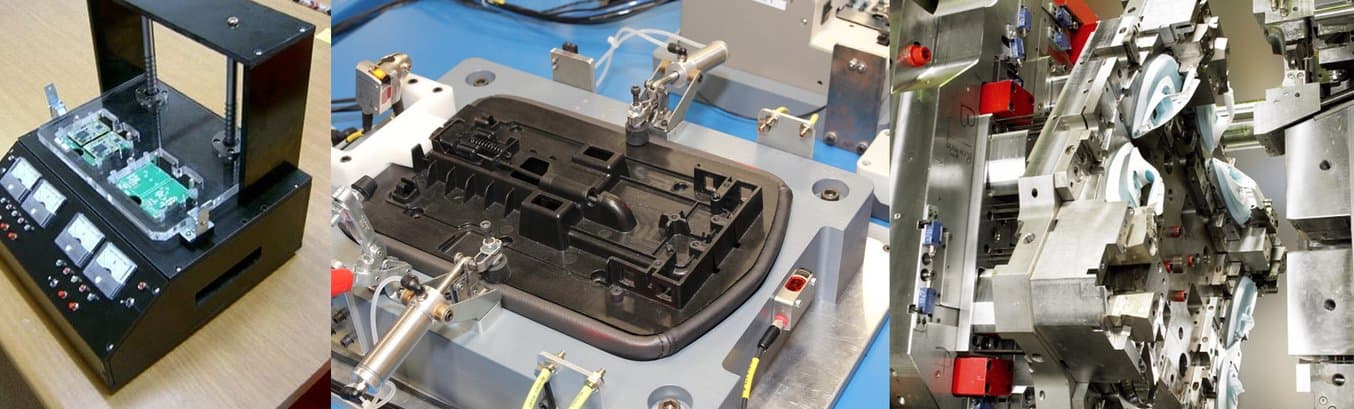
In der Phase der Produktvalidierung liegt der Fokus auf der Prozess- und Qualitätskontrolle zur Optimierung der Fertigungsstraße. Links: Haltevorrichtung für Plattentests mit Kapazität für mehrere Leiterplatten. Zur Verfügung gestellt von Korea Jig. Mitte: Multistations-Montagevorrichtung für ein Verbraucherprodukt. Zur Verfügung gestellt von Aerosport Additive. Rechts: Komplexes Rotations-Spritzgießwerkzeug für den Formenbau aus verschiedenen Materialien. Zur Verfügung gestellt von Grosfilley In-Mold & Rotative Solutions.
Die produzierte Stückzahl liegt in der Phase der Produktvalidierung in der Regel bei 500 aufwärts bzw. bei mindestens 5 % der Menge des ersten Produktionslaufs. Die Ziele bestehen darin, bei Produktionsgeschwindigkeiten auf Serienniveau die in der Vorphase ermittelte Ausbeute zu erzielen und die Produkte marktfähig zu machen. An dieser Stelle arbeiten Unternehmen zudem häufig einen Vertriebsplan aus und beginnen mit dem Verkauf an die Erstkunden. Die Phase der Produktvalidierung markiert zugleich auch die letzte Möglichkeit für Feinjustierungen am Produktionsprozess. Daher wird ihr Abschlusskriterium bzw. ihre Abgrenzung zur nächsten Phase in einigen Fällen an Status gebunden, due abhängig von zentralen Produktionskennzahlen auf rot, orange oder grün lauten. Steht dann alles auf grün, steht der Serienproduktion nichts mehr im Wege.
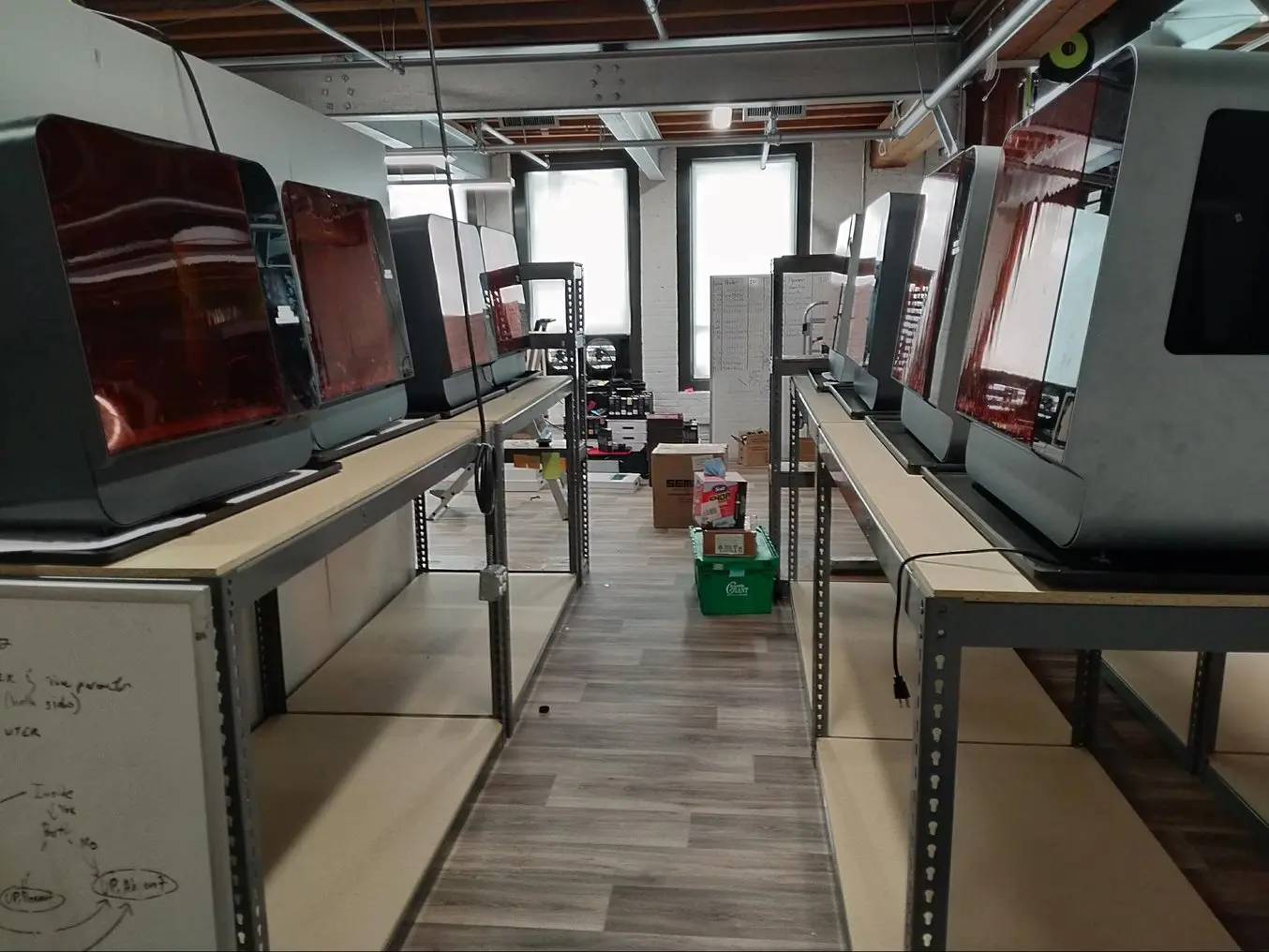
Für die Produktvalidierung gefertigte Form 3L Drucker vor der Qualitätskontrolle am Formlabs-Hauptsitz. Auch in der Phase der Produktvalidierung ist es gängige Praxis, produktionsfertige Produkte vom Vertragshersteller anzufordern, damit das Ingenieursteam vor der Auslieferung an Kunden noch einmal ihre Qualität prüft. Dies erst recht in Zeiten einer weltweiten Pandemie, die eine in persona durchgeführte Qualitätskontrolle am Standort des Vertragshersteller nicht zulässt.
Massenproduktion
Die letzte Station auf dem Weg durch die Phasen der Produktreife markiert die Skalierung auf Serien- bzw. Massenproduktion (MP). Für den ersten Lauf wird in der Regel eine Stückzahl von mindestens 5000 angesetzt, was bei besonders gefragten Verbraucherprodukten wie der PlayStation, dem iPad und iPhone oder dem Rubiks-Zauberwürfel aber auch direkt auf mehrere Millionen hinaufgehen kann.
In einigen Fällen richtet man in dieser Phase auch Nachbauten der ursprünglichen Fertigungsstraße ein, um so mehrere Anlagen im Parallelbetrieb laufen zu lassen. Mittels Analyse von Ausschuss und Ausbeute bei einer kleinen Stichprobe der Produktion lässt sich dabei das Qualitätsniveau halten. Gehen erste Retouren ein, wird durch eine EFFA-Analyse sichergestellt, dass alle fehlerhaften Produkte direkt zurück an das Ingenieursteam gehen. Bei der Absicherung der Qualität hilft die Einbeziehung von Fertigungsstätten und Auftragnehmern: Ihnen ist zu vermitteln, dass unerwartete Änderungen an Werkzeugausstattung und Prozessparametern Qualitätsschwankungen bedeuten können. Im Mittelpunkt von alldem steht es, die Ausbeute zu verbessern, Kosten zu reduzieren und bei entsprechender Nachfrage die Kapazitäten auszuweiten. Hierbei unterstützen Marketing- und Begleitmaterial, Werbeaktivitäten sowie Prognosen zu erwarteten Absatzvolumen, für die die Teams aus Marketing und Vertreib verantwortlich zeichnen.
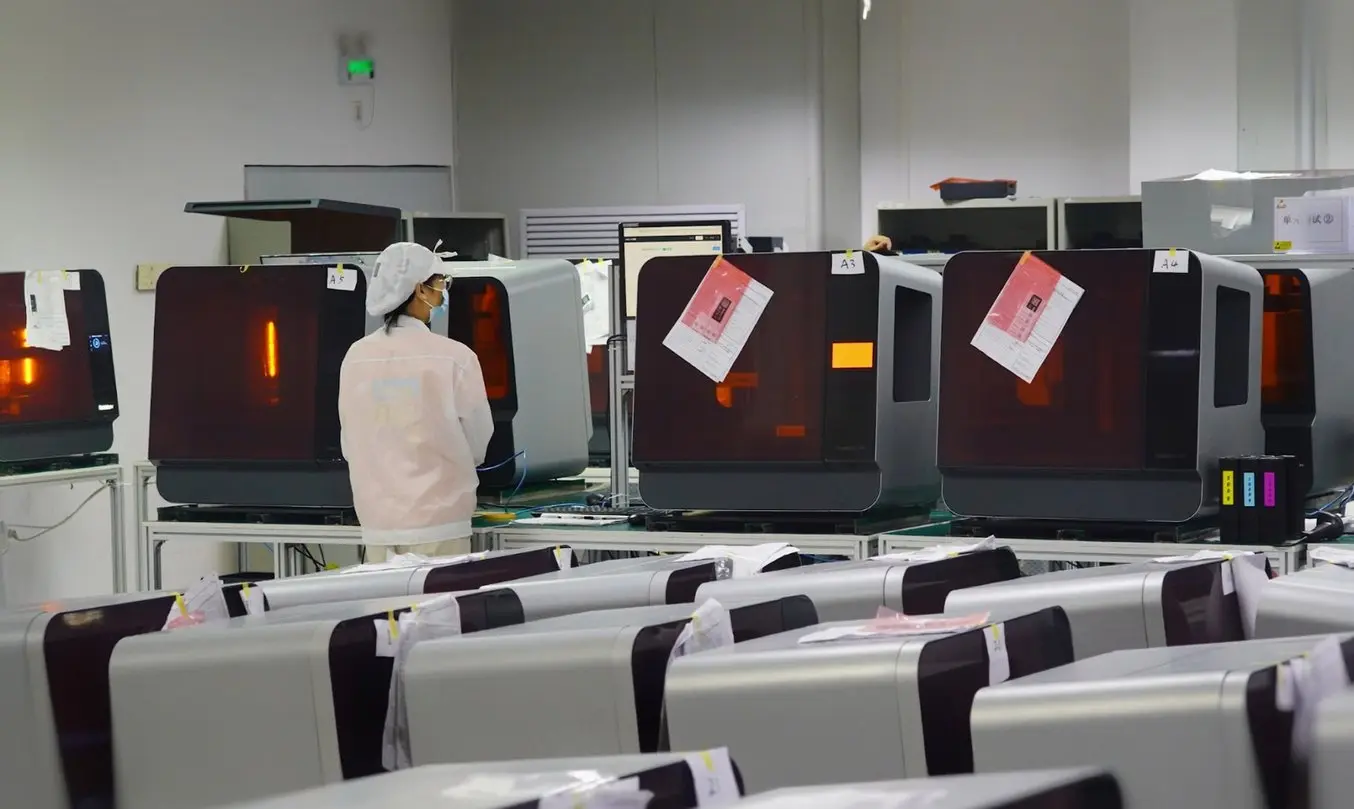
Nach der Qualitätskontrolle in Serie produzierte Form 3L Drucker am Standort des Vertragsherstellers.
The Different Stages of the New Product Development Process for Hardware
Phase | NPP | PoC | EVT | DVT | PVT | MP |
---|---|---|---|---|---|---|
Reifegrad | Business Case | Alpha-Prototyp | Beta-Prototyp | Vorserie | Kommerzielles Endprodukt | Kommerzielles Endprodukt |
Dauer | 2–4 Monate | 3 Monate bis 3 Jahre und mehr | 2–4 Monate | 3 Monate | 1 Monat | Mehr als 3 Monate |
Fokus | Ermittlung des Marktpotenzials, Lastenheft | Nachweis der Attraktivität für Nutzer | Produktionstaugliches Gerät | Skalierfähigkeit | Bereitschaft für MP | Qualitätssicherung |
Stückzahl | 0 | 5 | < 50 | < 500 | 500 oder mehr | 5000 oder mehr |
Vertrieb | Positionierung | Marketingplan | Absatzprognose | Vorbereitung auf Marktstart | Vertriebsplan | Werbeaktivitäten |
Kundenfeedback | Befragungen, Fokusgruppen | Nutzertests zur Sondierung | Nutzertests in Laborumgebung | Nutzertests vor Ort | Feldanalyse | Kontinuierliches Feedback |
Standort | Betriebsintern | Betriebsintern + Designpartner (optional) | Betriebsintern + Entwicklungspartner (optional) | Vertragshersteller + betriebsinterne Validierung | Vertragshersteller | Vertragshersteller |
Fazit
Ganz gleich, ob falsche Entscheidungen oder übersehene Kerndetails: In einer zu weit fortgeschritten Phase der Produktentwicklung können Missgeschicke dieser Art hohe Kosten und erhebliche Verzögerungen nach sich ziehen. Außerdem drohen empfindliche Reputationsverluste bei Auslieferung von fehlerhaften Produkten – selbst wenn es sich womöglich nur um Beta-Prototypen handelt. Daher gilt für komplexe Produkte, Systeme und Services jedweder Art, Form und Verwendung: Für ihre Entwicklung braucht es eine strukturierte Methodik mit klar voneinander abgegrenzten Phasen. Denn so bleibt das Vorhaben Stets optimal auf Kurs in Richtung Serienproduktion und zugleich der Ressourcenaufwand auf ein Mindestmaß beschränkt.
Zusammenfassen lassen sich die einzelnen Phasen der Produktreife wie folgt: Bei den Phasen Konzeptnachweis und Prototypenentwicklung wird ein Produktkonzept im Hinblick auf seine Brauchbarkeit, seinen Nutzen für Kunden sowie dahingehend untersucht, ob es sich entwicklungstechnisch umsetzen lässt. In der darauffolgenden Phase der technischen Validierung zielt das Entwicklerteam darauf ab, die nötige Gewissheit zu liefern, dass das Design wie vorgesehen funktionieren wird. Im Anschluss daran wird das Design in der Phase der Designvalidierung im Sinne einer erfolgreichen Überführung in Serienproduktion untersucht und dabei einer Vielzahl unterschiedlichster Tests unterzogen, während die Phase der Produktvalidierung dazu dient, die Produktionsstraße so auzusteuern, dass sie die anvisierten Kennzahlen erfüllt. In der Serien- bzw. Massenproduktion liegt der Fokus dann auf Vertrieb und Qualitätsabsicherung, auf künftigen Designanpassungen sowie irgendwann auch darauf, das Ende des Produktlebenszyklus einzuleiten.
Eine detaillierte Aufstellung aller Anforderungen in einem Lastenheft, eine gut durchdachte Methodik für die Prototypenfertigung sowie detaillierte Analysen in den Frühphasen der Produktentwicklung sind absolut entscheidend, um umfangreiche Anpassungen im späteren Verlauf zu vermeiden. So essenziell wichtig, wie diese Aspekte sind, so erhaben ist dafür aber auch der Moment, wenn der erste Karton vom Fließband kommt und der Blick hinein das Ergebnis aus Monaten oder gar Jahren harter Arbeit offenbart.
Der 3D-Druck kann dabei helfende Hand und Multifunktionswerkzeug zugleich sein, auf die Entwicklerteams über den gesamten Entwicklungsprozess hinweg zurückgreifen können. Von höchst detailtreuen Prototypen über Rapid Tooling bis hin zu Halte- und Spannvorrichtungen für die Fertigungsstraße: Mit 3D-Druckern können Sie Ihre Entwicklungsprozesse auf vielfältigste Weise beschleunigen und sind damit bestens aufgestellt, die Fertigung Ihrer Produkte zu maximalem Erfolg zu verhelfen.