IGESTEK mit Sitz im spanischen Bilbao ist eines der führenden Unternehmen mit einer Spezialisierung auf die Entwicklung leichtgewichtiger Lösungen für die Automobilindustrie mithilfe von Kunst- und Verbundwerkstoffen.
Das Unternehmen entwickelt und integriert verschiedene Hybridverfahren zur Herstellung von Verbundwerkstoffkomponenten, die dann von namhaften Automobilzulieferern und Erstausstattern (OEMs) implementiert werden, um Hochleistungsteile für Autos und Motorräder zu fertigen.
Das Team bei IGESTEK verwendet 3D-Druck im gesamten Produktentwicklungsprozess, von der Verifizierung der Geometrien in der Konzeptionsphase bis zu funktionsfähigen Prototypen in der Designphase. 3D-Druck kommt auch zum Einsatz für die Herstellung von Rapid Tooling, z. B. für Einsätze beim Kunststoffspritzguss oder für Tiefziehwerkzeuge für Verbundwerkstoffe.
Im Folgenden erfahren Sie, wie IGESTEK die Entwicklung beschleunigt, Kosten senkt und schnell auf auftretende Probleme reagiert.
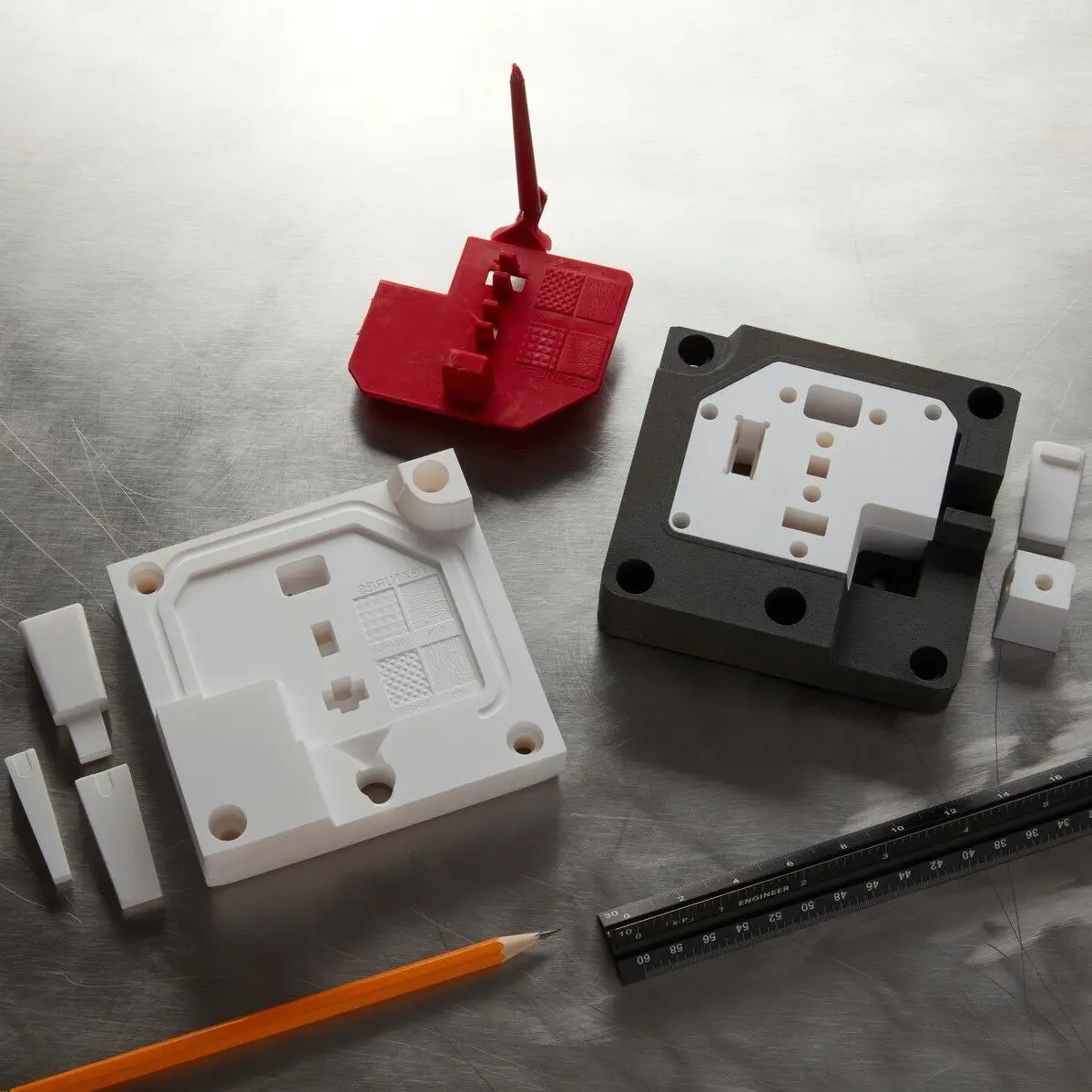
Leitfaden zum Rapid Tooling
In diesem Whitepaper sprechen wir über die Kombination von Rapid Tooling mit traditionellen Herstellungsverfahren wie Spritzguss, Vakuumformen oder anderen Gießverfahren.
Die Iteration einer Fahrzeugkomponente mit generativer Gestaltung und dem Form 3L
Eines der jüngsten Innovationsprojekte von IGESTEK ist die Befestigung eines Stoßdämpfers als Teil der Radaufhängung. Diese Komponenten sind Teil der Aufhängung des Fahrzeugs und sollen als solche die Vibrationen des rollenden Fahrzeugs abfangen und den Fahrkomfort der Insassen verbessern.
Die generative Gestaltung der Stoßdämpferaufhängung wurde mit Autodesk Fusion 360 entwickelt. Die Software stellte basierend auf einer begrenzten Menge an Anforderungen verschiedene Lösungen zur Verfügung.
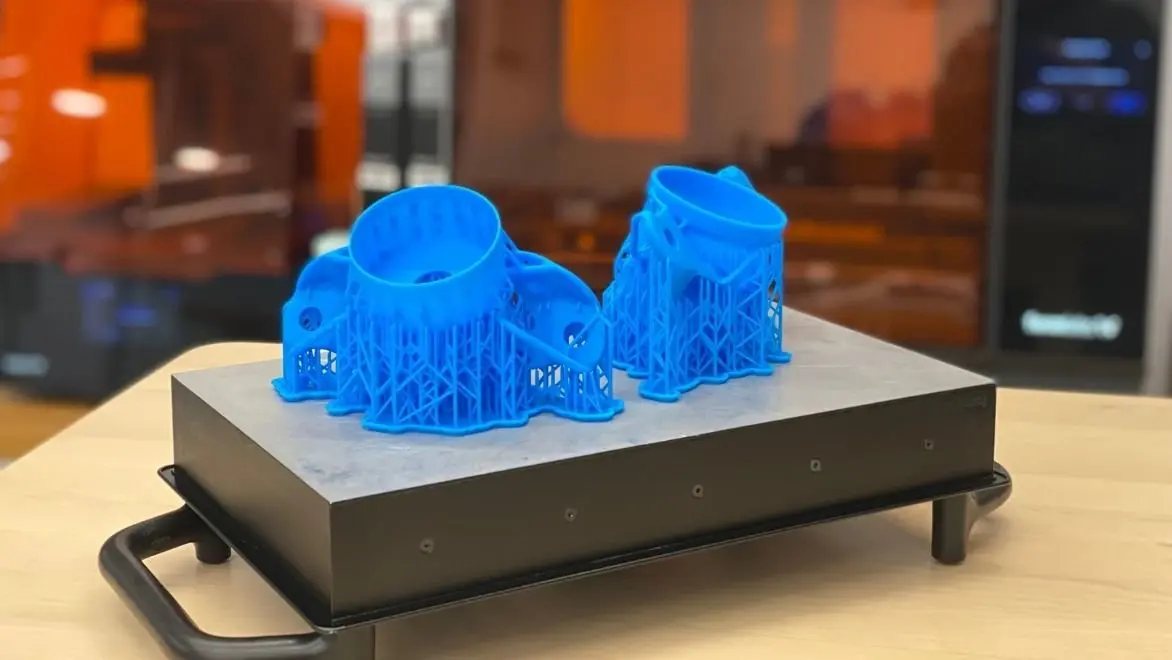
Dank des großen Konstruktionsvolumens des Form 3L druckt IGESTEK mehrere Iterationen derselben Komponente gleichzeitig.
Die vielversprechendsten Designs druckte das Team dann betriebsintern mit dem großformatigen Stereolithografie-3D-Drucker (SLA) Form 3L, um die Geometrie zu validieren. Dank des großen Konstruktionsvolumens druckte man bis zu drei verschiedene Iterationen gleichzeitig. SLA-3D-Druck erlaubt die Umsetzung der komplexen Geometrien, die die generative Gestaltung hervorbringt. So validiert man die Baugruppen und Kinematikprozesse anhand funktionsfähiger Prototypen ganz ohne Investitionen in teure Werkzeugbestückung.
Das Endergebnis dieses F+E-Prozesses war dann eine Architektur mit mehreren Materialien, die metallische 3D-Drucke der generativen Geometrien mit leichteren Verbundwerkstoffen kombiniert, um bestmögliche Leistung anzubieten – und das mit 40 % weniger Gewicht als bei den aktuell auf dem Markt erhältlichen Lösungen.
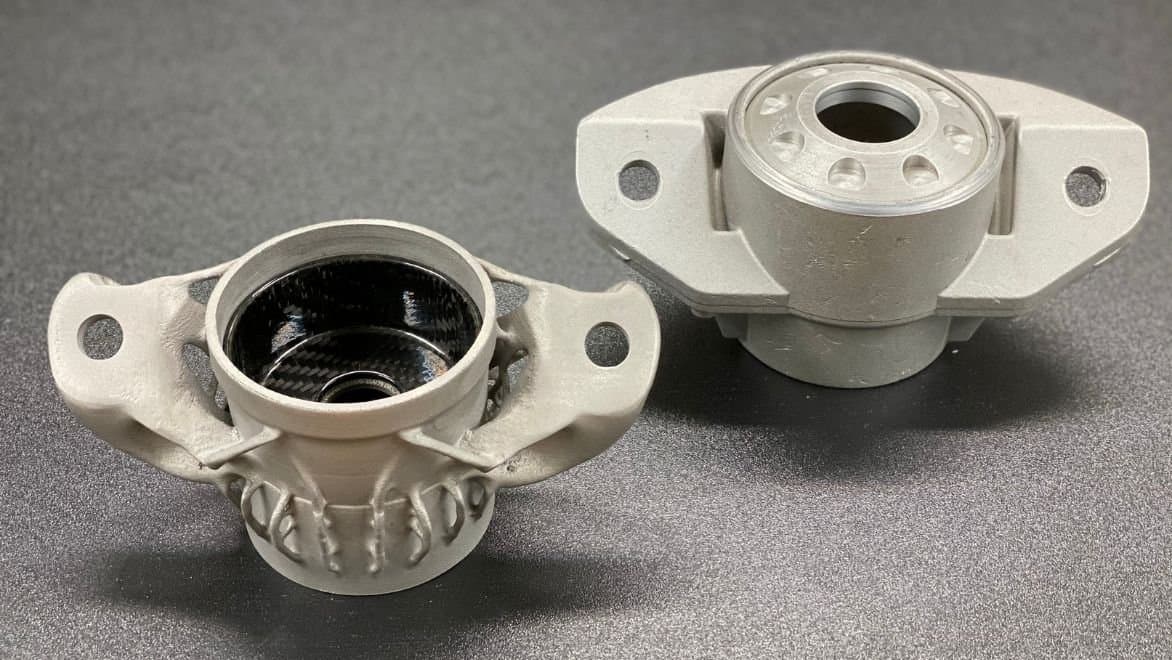
Das Endergebnis, hergestellt mit einer Kombination aus Metall-3D-Druck und Verbundwerkstoffen.
Der Einsatz unterschiedlicher 3D-Druckmaterialien zur Herstellung eines Tiefziehwerkzeugs
Das Team von IGESTEK nutzt den 3D-Druck auch über die Prototypenentwicklung hinaus, z. B. zur Anfertigung von Rapid Tooling zur Produktion der Verbundwerkstoffteile, wie etwa beim Tiefziehen von Prepreg-Teilen aus Kohlenstofffaser.
„Formlabs-Kunstharze wie Rigid 10K Resin und High Temp Resin sind äußerst hilfreich im Maschinenbau. Wir arbeiten bei unseren Verbundwerkstoffen für gewöhnlich mit druckbasierten Thermoformtechnologien. Damit es der Presse auch standhält, muss das Werkzeug starr und hitzebeständig sein, denn [zur Formung des Verbundwerkstoffteils] wird Druck eingesetzt gemeinsam mit hohen Temperaturen von 180 bis 200 Grad“, berichtet Nerea Romero, Innovation Manager bei IGESTEK.
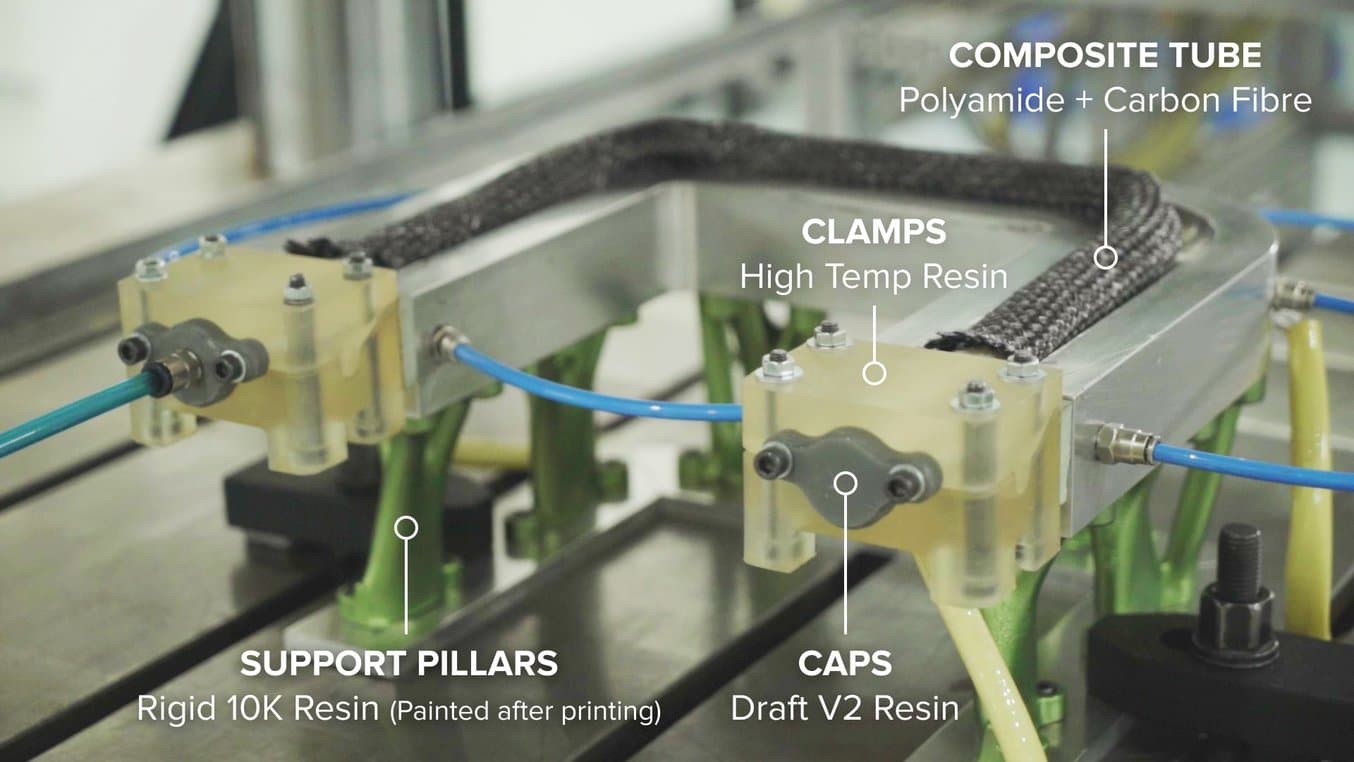
Dieser Thermoformaufbau für Verbundwerkstoffrohre wurde dank einer Vielzahl an 3D-Druckteilen umgesetzt.
Ein zeitnahes Beispiel ist ein Werkzeug, das das Team zur Herstellung von Verbundwerkstoffrohren entwickelte. Die Stützen des Aufbaus wurden aus Rigid 10K Resin angefertigt, da diese hohe Steifigkeit voraussetzen. Die Klemmen mussten hohen Temperaturen und starkem Druck widerstehen, wofür sich High Temp Resin anbot. Und mit Draft Resin produzierte man in Windeseile die Endkappen des Werkzeugs.
„[Ohne 3D-Druck] müssten wir alles aus Metall herstellen, was eindeutig länger dauern würde und teurer wäre. 3D-Druck liefert uns schnelle Antworten auf unsere Forschungsfragen. Falls irgendetwas nicht funktioniert, dann drucken wir einfach einen anderen Prototypen und verbessern es“, so Romero.
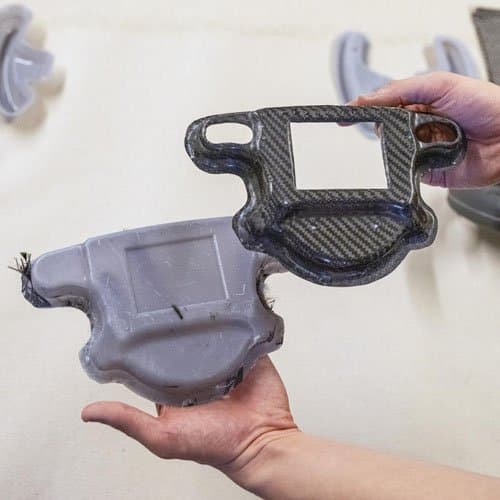
Fertigung von Kohlenstofffaserteilen mit 3D-gedruckten Formen
Laden Sie dieses Whitepaper zur Erstellung von Kohlenstofffaserteilen herunter. Es erläutert Designleitfäden für Verbundwerkstoffformen sowie schrittweise Anleitungen für die Prepreg- und Handlaminierung.
Spritzguss mit 3D-gedruckten Formeinsätzen
Darüber hinaus verwendet das Team von IGESTEK 3D-gedruckte Formeinsätze beim Spritzguss von Kunststoffteilen. Üblicherweise wurden diese Einsätze mittels Zerspanung von Aluminium oder Stahl hergestellt – einfache Teilen betriebsintern und komplexe Teile via Outsourcing. Das zieht jedoch hohe Kosten nach sich sowie lange Durchlaufzeiten, insbesondere bei Einzelstücken oder Kleinserien für Prototypen.
Ein Beispiel aus der jüngsten Vergangenheit, ein Spritzgusseinsatz zur Fertigung einer externen Autoverkleidungskomponente, zeigt, wie das Team mithilfe von 3D-Druck die Kosten und Durchlaufzeit auf weniger als ein Drittel des Ursprungswertes verringern konnte.
Spritzgussformeinsatz | 3D-gedruckt | Zerspantes Metall |
---|---|---|
Kosten | 300€ | 1000€ |
Durchlaufzeit | 10 Stunden | 30 Stunden |
Die Form hat zwei Hohlräume: einen mit einem Metalleinsatz und den anderen mit einem maßgefertigten, 3D-gedruckten Einsatz, der ein Negativ des Designs darstellt. Bei der Prototypenentwicklung ist dies ideal, da das Team den 3D-gedruckten Einsatz leicht austauschen und so schnell verschiedene Iterationen testen kann.
„In der Prototypenphase benötigt man nur einige wenige Komponenten, die man mit anderen Komponenten zusammensetzt und so die allgemeine Symmetrie testet. Bei 20 oder 50 Komponenten beweist das schon, dass der Ansatz funktioniert“, erläutert Romero.
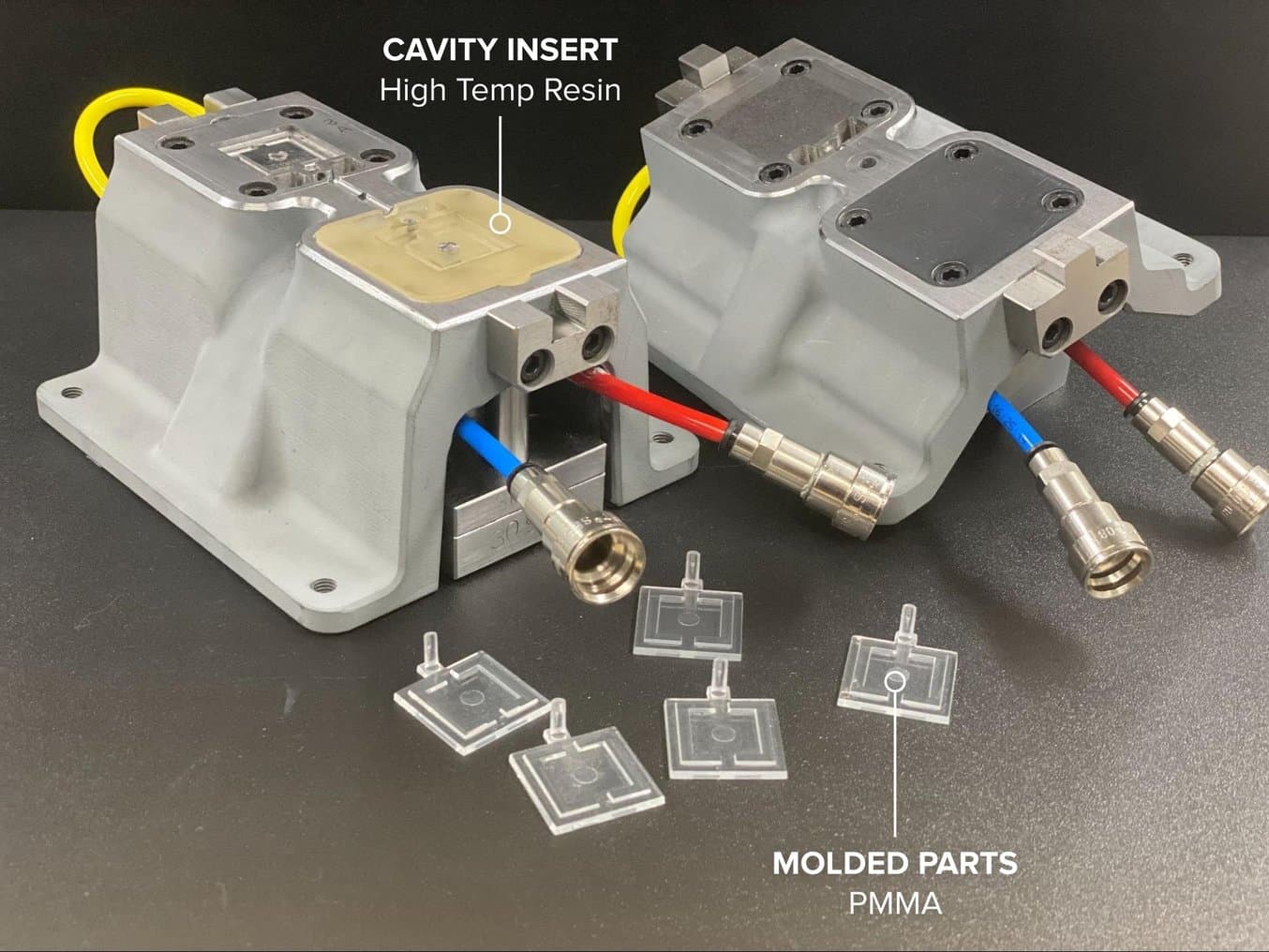
Spritzgussaufbau für eine Fahrzeugkomponente aus PMMA mit einem Einsatz aus High Temp Resin.
Die Anzahl der Gussteile aus einer 3D-Druckform hängt hauptsächlich von drei Faktoren ab: dem Gussmaterial, dem Spritzsystem und den Parametern des Gussverfahrens.
„Es hängt viel vom Material des Spritzgusses oder des Verbundwerkstoffs ab. Beispielsweise ist der Spritzguss mit faserverstärktem Kunststoff viel aggressiver als herkömmliche Materialien. Dabei wird [der Einsatz] schneller beschädigt. Dann bekommt man vielleicht 20 Komponenten. Aber wenn man noch mehr produzieren möchte, muss man den Einsatz austauschen“, sagt Romero.
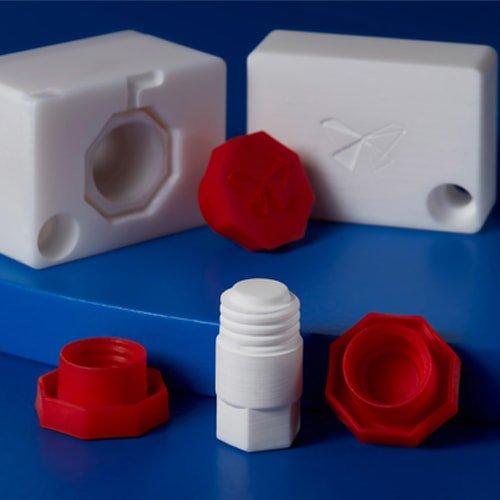
Schnelles Spritzgießen von Kleinserien mit Formen aus dem 3D-Drucker
Laden Sie dieses Whitepaper herunter und erfahren Sie mehr über die Methoden und Richtlinien zur Herstellung 3D-gedruckter Spritzgussformen, um die Kosten zu senken und Lieferzeiten zu verkürzen. Es enthält Fallstudien aus der Praxis von Braskem, Holimaker und Novus Applications.
Das nächste große Projekt
Das Team von IGESTEK arbeitet weiter an Innovationen. Es überlegt bereits, wie man die Grenzen des Möglichen bei den nächsten Projekten mit 3D-Druck noch weiter überwinden kann.
Zu den nächsten Projekten gehören auch großformatige Tiefziehformen, die das große Fertigungsvolumen des Form 3L ausnutzen, sowie die Arbeit mit anderen Materialien wie Flexible 80A Resin und Elastic 50A Resin, die der Werkzeugbestückung neue Eigenschaften verleihen.