Introducción a la impresión 3D en medicina y las impresoras 3D para el sector sanitario
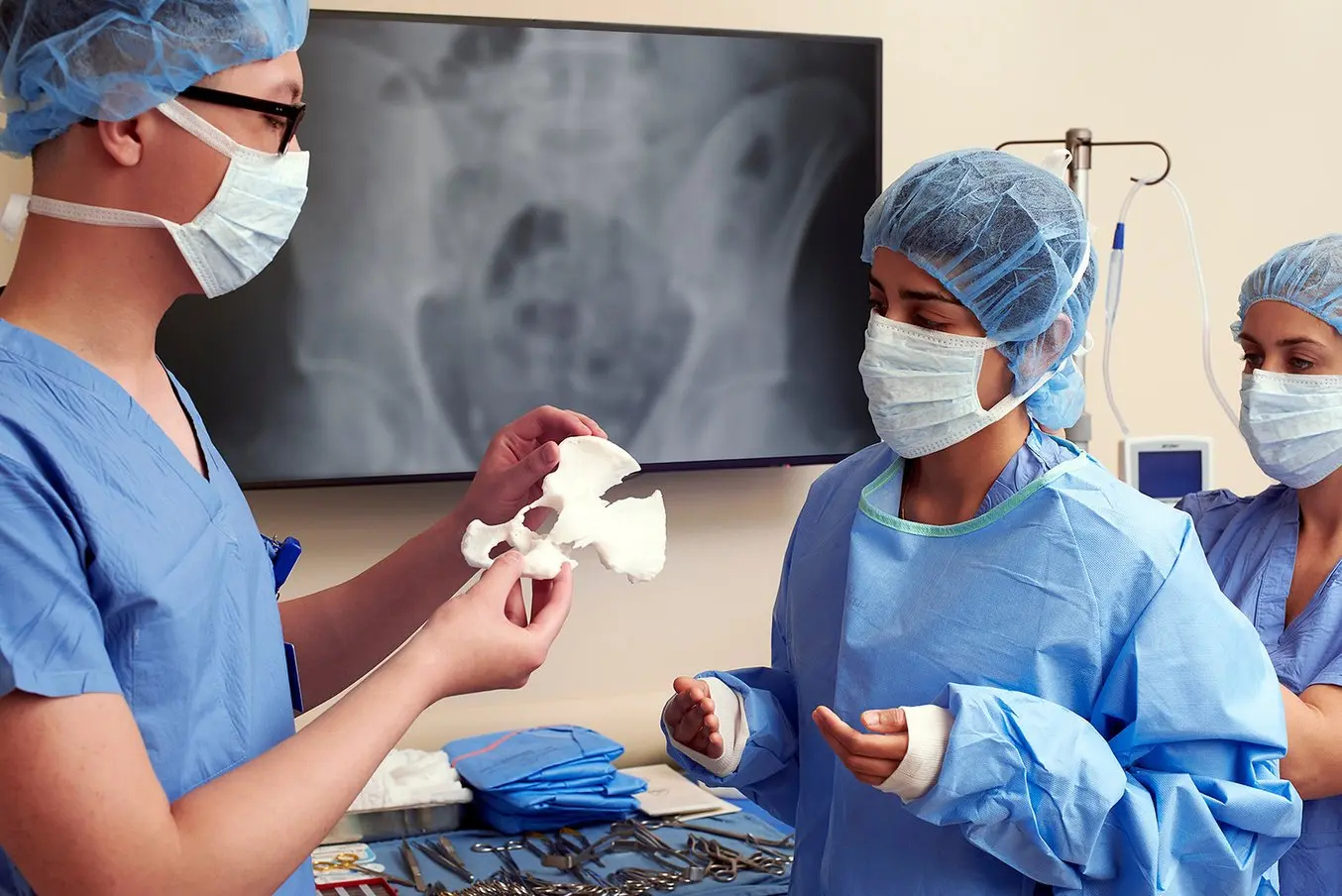
La medicina de precisión personalizada está en auge. Nuevas herramientas y tecnologías avanzadas acercan a los médicos a los pacientes, creando tratamientos y dispositivos personalizados para adaptarse lo mejor posible a cada persona.
Los avances en la tecnología de impresión 3D médica han hecho enormes contribuciones a diversos campos del sector sanitario. Para los pacientes, las nuevas herramientas y métodos terapéuticos desarrollados mediante la impresión 3D pueden ofrecer nuevos niveles de comodidad y personalización en el tratamiento. Para los médicos, el acceso actual a esta tecnología permite contar con una comprensión mayor de casos complejos y proporciona nuevas herramientas que pueden generar cuidados de mayor calidad.
Desde modelos quirúrgicos adaptados a cada paciente hasta productos sanitarios impresos en 3D. Sigue leyendo para descubrir seis formas de las que está creciendo la impresión 3D en el sector sanitario, por qué muchos profesionales médicos están interesados en el potencial de la impresión 3D en el ámbito de la medicina y cómo los diferentes tipos de tecnología de impresión 3D se pueden utilizar para aplicaciones sanitarias específicas.
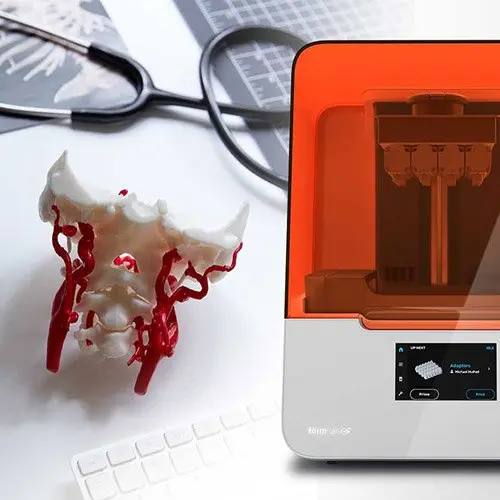
Introducción a la impresión 3D médica
Formlabs te ofrece una introducción con la que conocer las buenas prácticas de la impresión 3D médica y ver el último ecosistema de Formlabs Medical, ¡que incluye varios productos nuevos aptos para uso médico!
Impresión 3D en el sector de la sanidad
1. Modelos quirúrgicos adaptados a cada paciente
Los modelos anatómicos impresos en 3D a partir de datos de escaneos del paciente son herramientas cada vez más útiles para la medicina de precisión que se practica actualmente. A medida que los casos se vuelven más complejos y la eficiencia en el quirófano se vuelve más importante para los casos rutinarios, los modelos de referencia visuales y táctiles dan la capacidad de potenciar la comprensión y la comunicación dentro de los equipos quirúrgicos y con los pacientes.
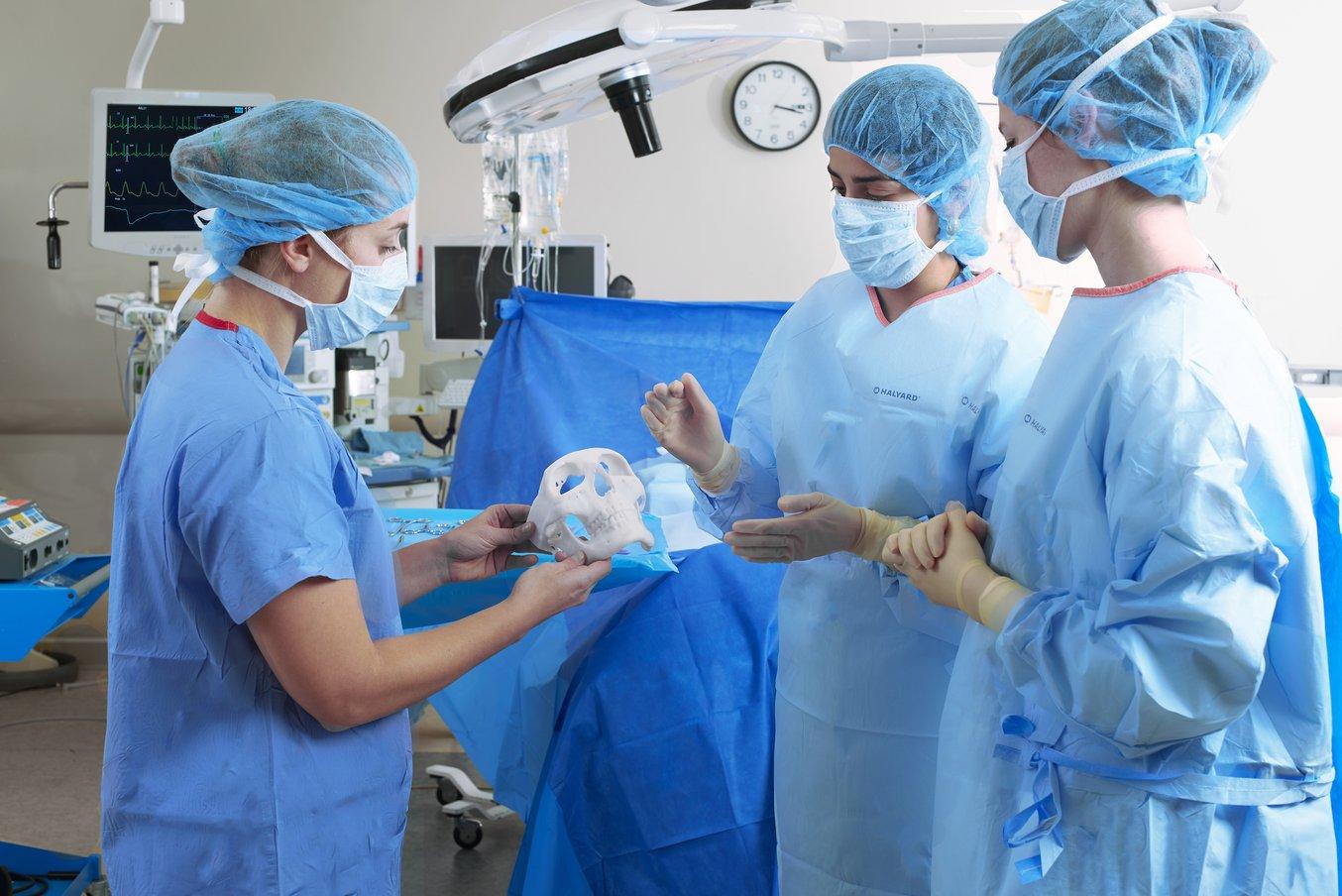
Cómo imprimir en 3D modelos anatómicos para la planificación preoperatoria con un mejor consentimiento por parte del paciente
Este libro blanco ofrece un tutorial práctico para que los médicos y técnicos empiecen a crear modelos anatómicos impresos en 3D a partir de escaneos del paciente, a revisar las buenas prácticas para preparar una tomografía computarizada o resonancia magnética, segmentar conjuntos de datos y convertir archivos a un formato imprimible en 3D.
Profesionales del sector sanitario, hospitales y organizaciones de investigación de todo el mundo están usando modelos anatómicos como herramientas de referencia para la planificación preoperatoria, para la visualización intraoperatoria y para el ajuste de equipo médico para operaciones tanto rutinarias como complejas que se han documentado en cientos de publicaciones.
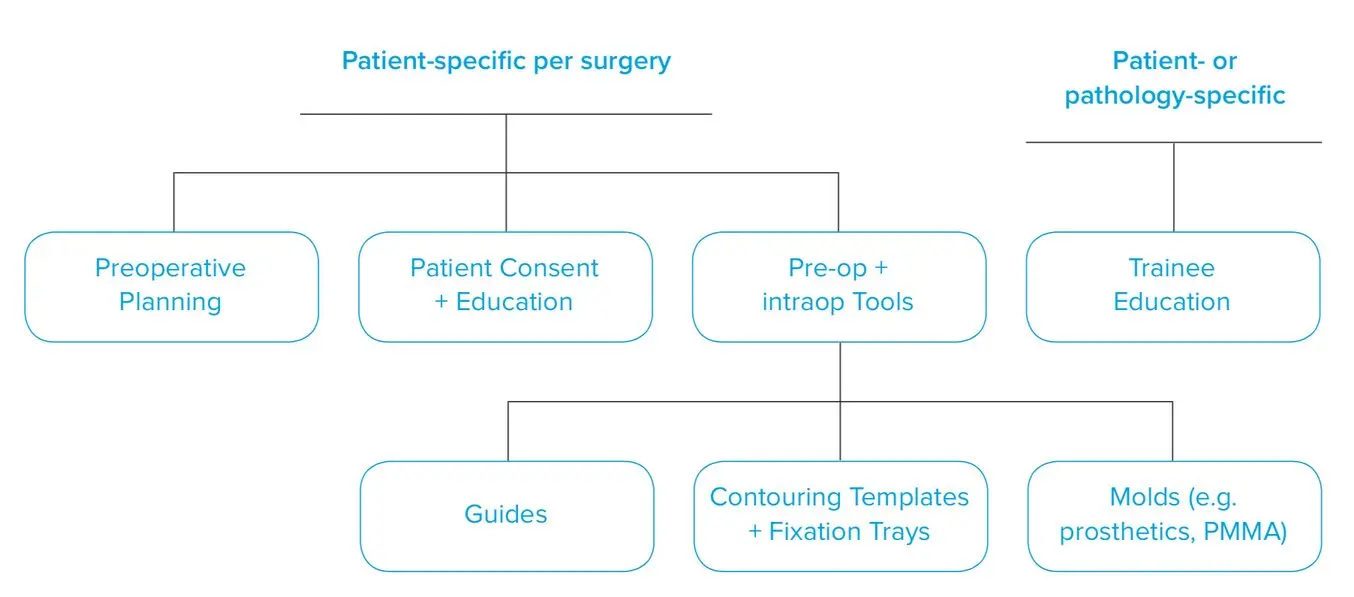
Gracias a la impresión 3D, producir modelos de referencia táctiles adaptados al paciente a partir de tomografías computarizadas y resonancias magnéticas es un proceso asequible y sencillo. Las publicaciones especializadas revisadas por pares muestran que proporcionan una visión adicional que ayuda a los médicos a prepararse mejor para las operaciones. Por consiguiente, con esta ayuda se obtiene una gran reducción de tiempo y de costes en el quirófano, al tiempo que se aumenta la satisfacción de los pacientes, se calman sus nervios y se reduce el tiempo de recuperación.
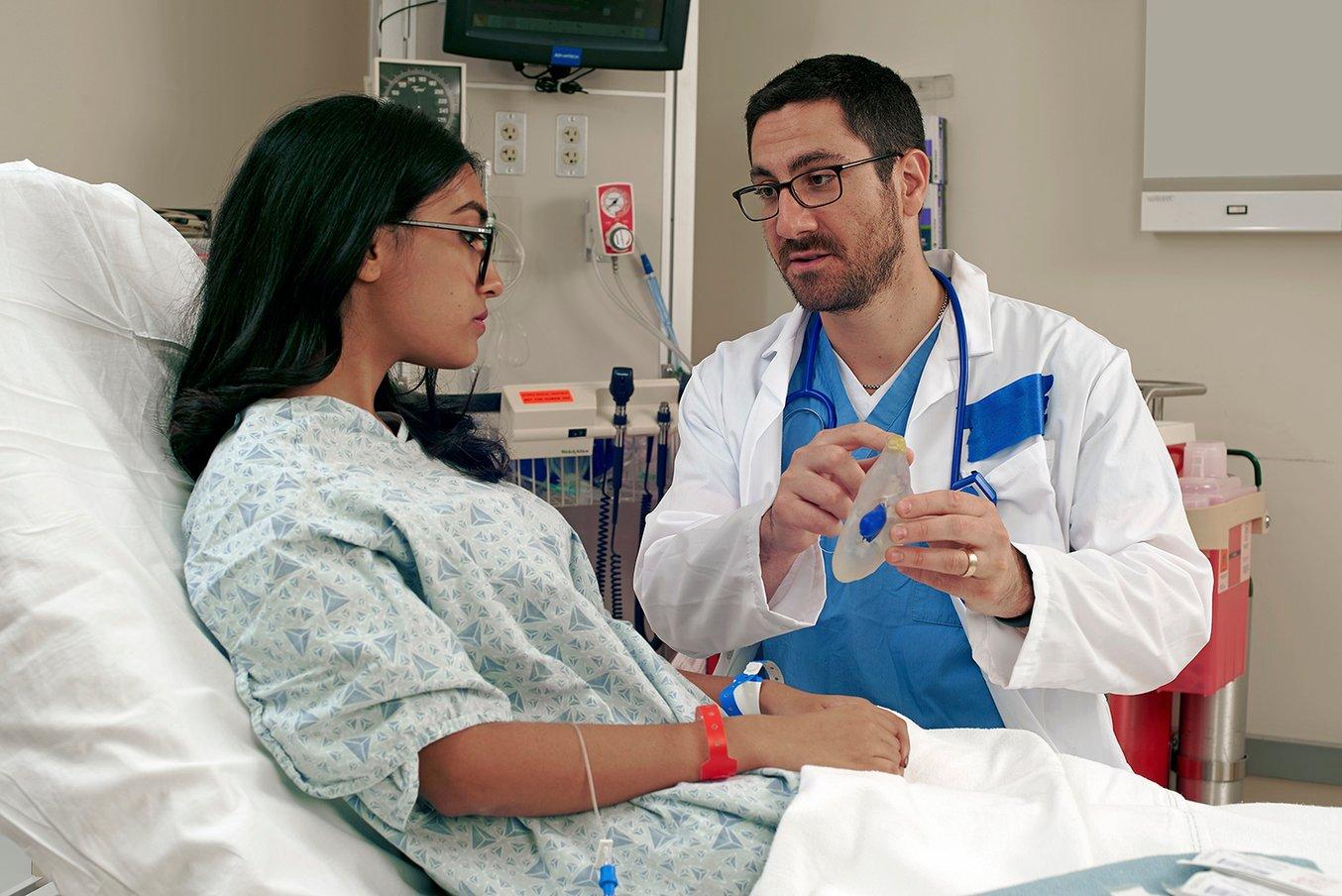
Los médicos pueden usar los modelos quirúrgicos adaptados al paciente para explicar la operación de antemano, con lo que el paciente tiene un consentimiento mejor informado y aumenta su tranquilidad.
Aprender de los modelos preoperatorios también puede influir en el desarrollo del tratamiento. Esto fue lo que le ocurrió al Dr. Michael Eames. Después de crear una réplica de los huesos del antebrazo de un paciente joven, el Dr. Eames se percató de que la herida era distinta de lo que pensaba.
El Dr. Eames se decidió por una nueva operación en los tejidos blandos. Una mucho menos invasiva, con un menor tiempo de rehabilitación y que provocaría unas cicatrices mucho más leves. Con la réplica impresa del hueso, el Dr. Eames explicó al paciente y a sus padres toda la intervención y obtuvo su consentimiento.
¿El resultado? Una intervención quirúrgica de menos de 30 minutos, en vez de la operación de tres horas que se había planeado en un principio. Esta diferencia de tiempo en el quirófano produjo un ahorro estimado de 5500 € para el hospital y supuso que el paciente tuviera que pasar menos tiempo de recuperación en asistencia posoperatoria.
"Todos y cada uno de nuestros cirujanos ortopédicos a tiempo completo y casi todos nuestros cirujanos a tiempo parcial han utilizado modelos impresos en 3D para atender a los pacientes del Centro Médico de Veteranos de San Francisco. Todos hemos visto que la impresión 3D mejora los resultados cuando llega el momento de la intervención".
Dr. Alexis Dang, cirujano ortopédico de la Universidad de California en San Francisco (UCSF) y del Centro Médico de Veteranos de San Francisco
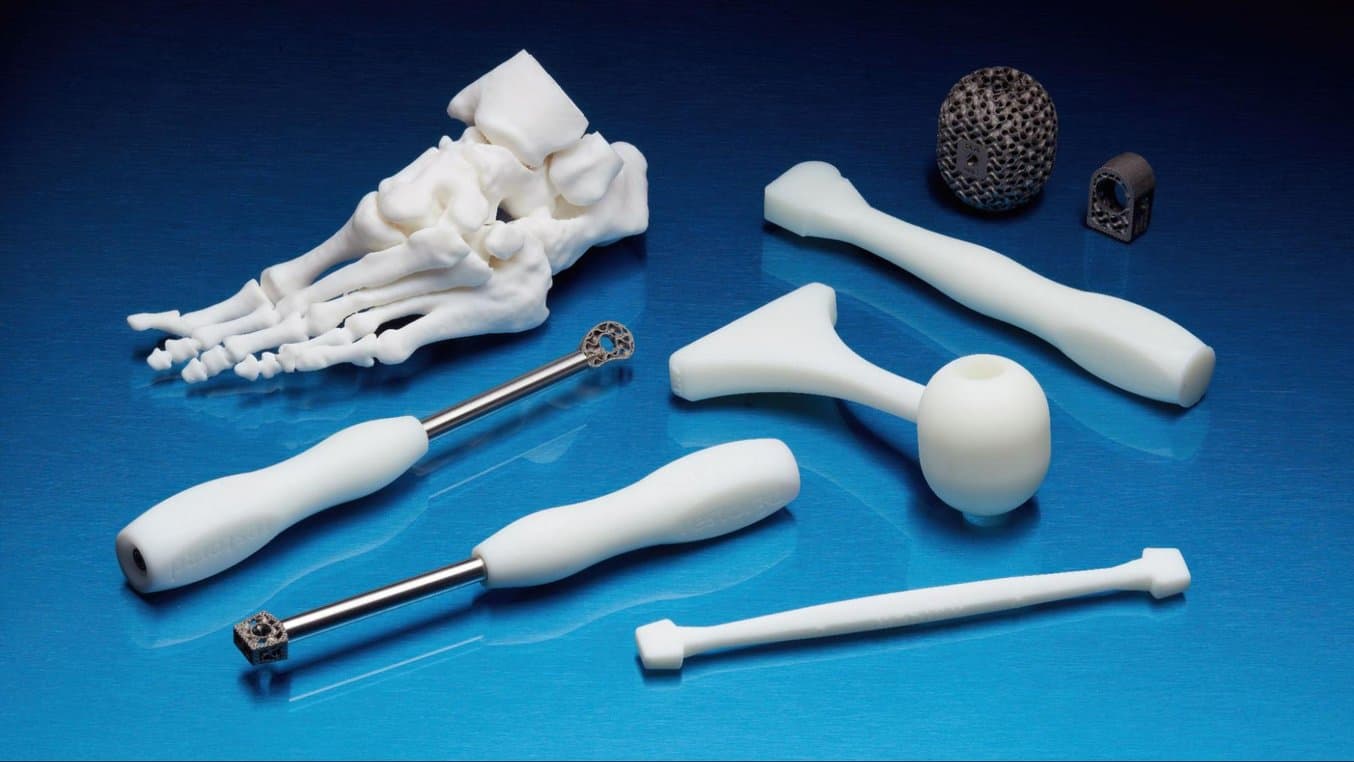
Cirugía personalizada con la impresión 3D: Preguntas y respuestas con Insight Surgery (anteriormente, 3D LifePrints)
Únete a esta sesión de preguntas con 3D LifePrints para descubrir su trabajo innovador y versátil en la creación de productos sanitarios adaptados a los pacientes.
El Dr. Frederik Verstreken del centro AZ Monica, en la región belga de Amberes, está especializado en cirugía de la mano, la muñeca y el antebrazo. Afirma que la combinación de la visualización, la planificación digital y los modelos anatómicos impresos en 3D da a los médicos la capacidad de ahorrar en torno a un 30-40 % del tiempo en el quirófano. Para casos de osteotomía complejos, a veces no era posible restaurar la anatomía, pero con los modelos quirúrgicos impresos en 3D, los médicos están mucho mejor preparados para realizar la operación que sin estas herramientas digitales, usan menos radiación y siguen obteniendo una precisión considerablemente mayor, con lo que los pacientes acaban recuperando el movimiento normal y perdiendo el dolor.
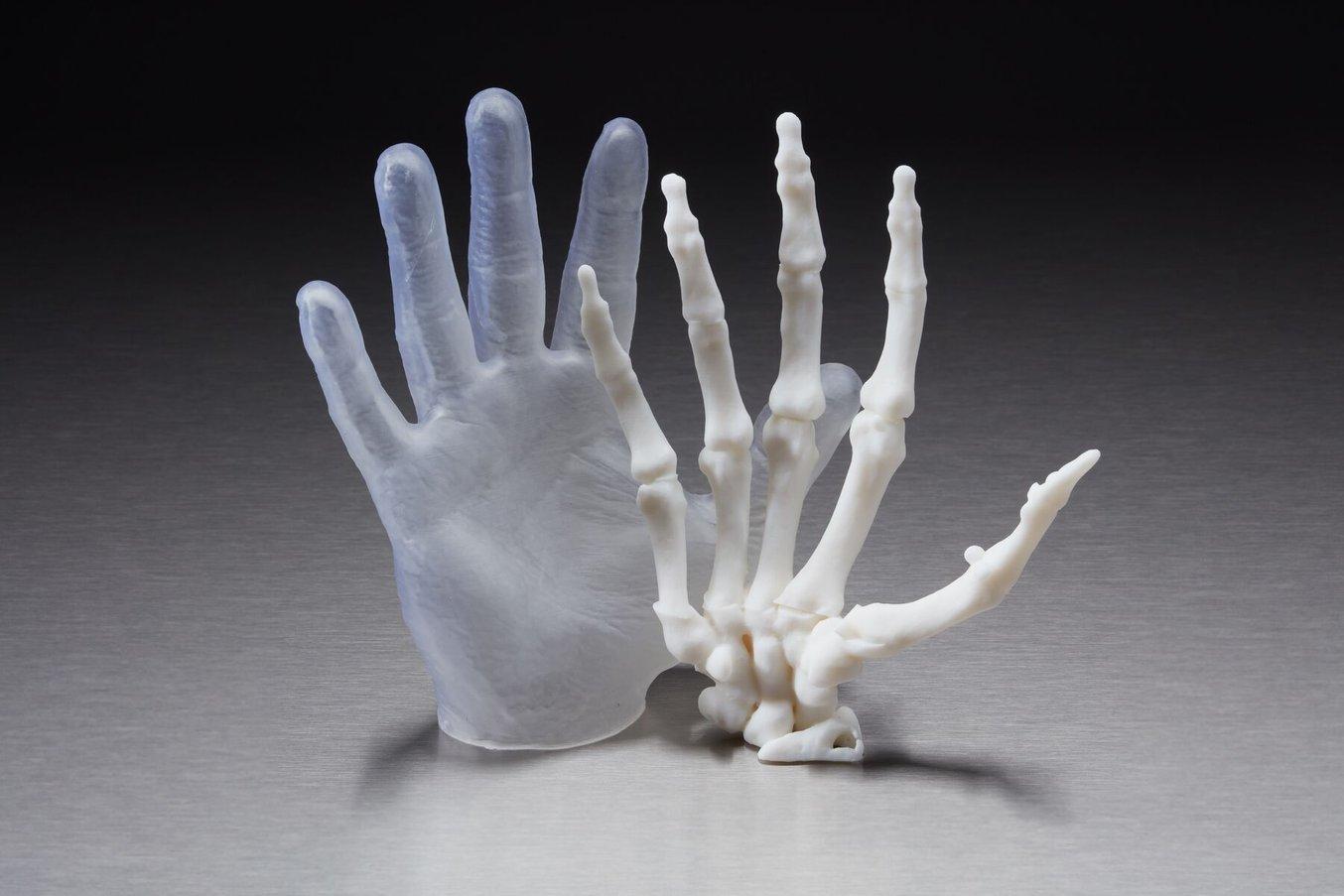
Modelo anatómico de una mano, que incluye la "piel" hecha con un material elástico de impresión 3D.
Todd Goldstein, instructor en el Instituto Feinstein de Investigación Médica, no deja lugar a dudas en su estimación de la importancia que ha cobrado la impresión 3D para su departamento. Calcula que si Northwell usa modelos impresos en 3D en el 10-15 % de sus casos, podría ahorrar 1750 000 $ al año.
Las guías quirúrgicas pueden ayudar a los cirujanos a entender la anatomía y la patología únicas de cada paciente, ayudando a analizar los riesgos, planificar el enfoque de la cirugía y familiarizarse con el caso antes de entrar en el quirófano. Elegir materiales pensando en propiedades específicas, como la elasticidad, puede permitir a los cirujanos practicar sus procedimientos con modelos, con lo que se acorta el tiempo que se pasa en el quirófano y se obtienen resultados mejores.
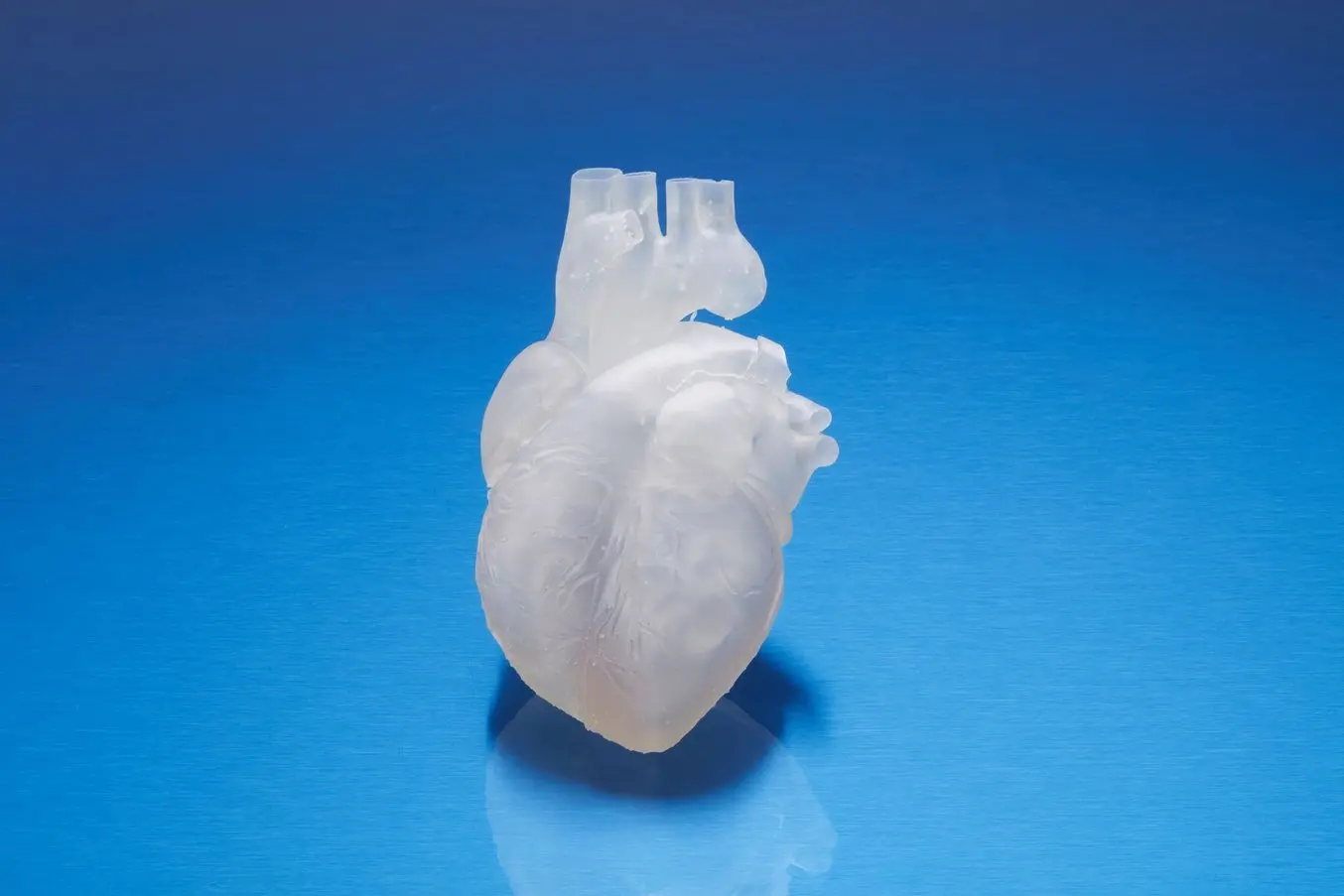
Cómo aprovechar los elastómeros biocompatibles de Formlabs para modelos de anatomía vascular
Descubre cómo los profesionales médicos pueden incorporar materiales elastoméricos y biocompatibles en procesos de impresión 3D innovadores con los nuevos materiales de Formlabs: la BioMed Flex 80A Resin y la BioMed Elastic 50A Resin.
2. Instrumentos quirúrgicos adaptados a cada paciente
Los nuevos materiales biocompatibles de impresión 3D médica han permitido que se desarrollen también nuevas herramientas y técnicas quirúrgicas con la finalidad expresa de mejorar aún más la experiencia clínica durante las intervenciones quirúrgicas. Los sistemas de instrumental tradicionales tardan en evolucionar, tienen costes iniciales considerables y a menudo presentan complicaciones en el proceso de trabajo quirúrgico. Las impresoras 3D y los materiales biocompatibles hacen que sea más fácil y rentable crear implantes, instrumentos quirúrgicos y guías de corte adaptados a procedimientos específicos y, a menudo, al paciente concreto en cuestión.
Imprimir en 3D guías quirúrgicas personalizadas puede ayudar a los cirujanos a entender la anatomía y la patología únicas de cada paciente, ayudando a analizar los riesgos, planificar el enfoque de la cirugía y familiarizarse con el caso antes de entrar en el quirófano. Las guías de corte bien diseñadas reducen el tiempo necesario para un caso y disminuyen el tiempo que los cirujanos dedican a utilizar un sistema de navegación intraoperatoria. Esto equivale a menos radiación para el paciente e incluso a pasar menos tiempo en el quirófano.
"Las guías nos dicen dónde hacer agujeros y dónde tenemos que hacer los cortes, para que cuando saquemos una placa, todo caiga en la posición correcta. Nuestra precisión es mucho mayor cuando usamos las guías que cuando no lo hacemos. Ahorramos al menos un 50 % del tiempo en comparación con hacerlo a mano y el resultado es mucho más preciso".
Frederik Verstreken, cirujano de mano y muñeca en el Hospital AZ Monica
El tiempo de entrega rápido de la impresión 3D permite realizar iteraciones rápidas de los diseños. Podemos recibir comentarios de los cirujanos y aplicar sus sugerencias rápidamente, volviendo a imprimir la herramienta o guía.
restor3d se ha propuesto como meta apoyar a los cirujanos y a los proveedores de asistencia sanitaria que reparan y reconstruyen el cuerpo humano, fomentando la innovación en el ámbito de la cirugía de precisión. restor3d aprovecha las capacidades de la impresión 3D para mejorar drásticamente la asistencia quirúrgica imprimiendo implantes de metal e instrumental polimérico adaptados a los procedimientos y, a menudo, a los mismos pacientes.
restor3d se ha establecido como un líder a la hora de usar la impresión 3D para innovar en el quirófano. Su kit de planificación preoperatoria líder en el sector, sus implantes precisos e innovadores y la solución completa que ofrece el kit de instrumental quirúrgico han ayudado a los hospitales a reducir los costes y mejorar la experiencia de los pacientes.
"Los cirujanos nos transmiten sus impresiones constantemente. La impresión 3D nos permite realizar rápidamente iteraciones del diseño para recibir las opiniones de los cirujanos y ofrecer una nueva solución con celeridad".
Nathan Evans, vicepresidente de Desarrollo de productos de restor3d
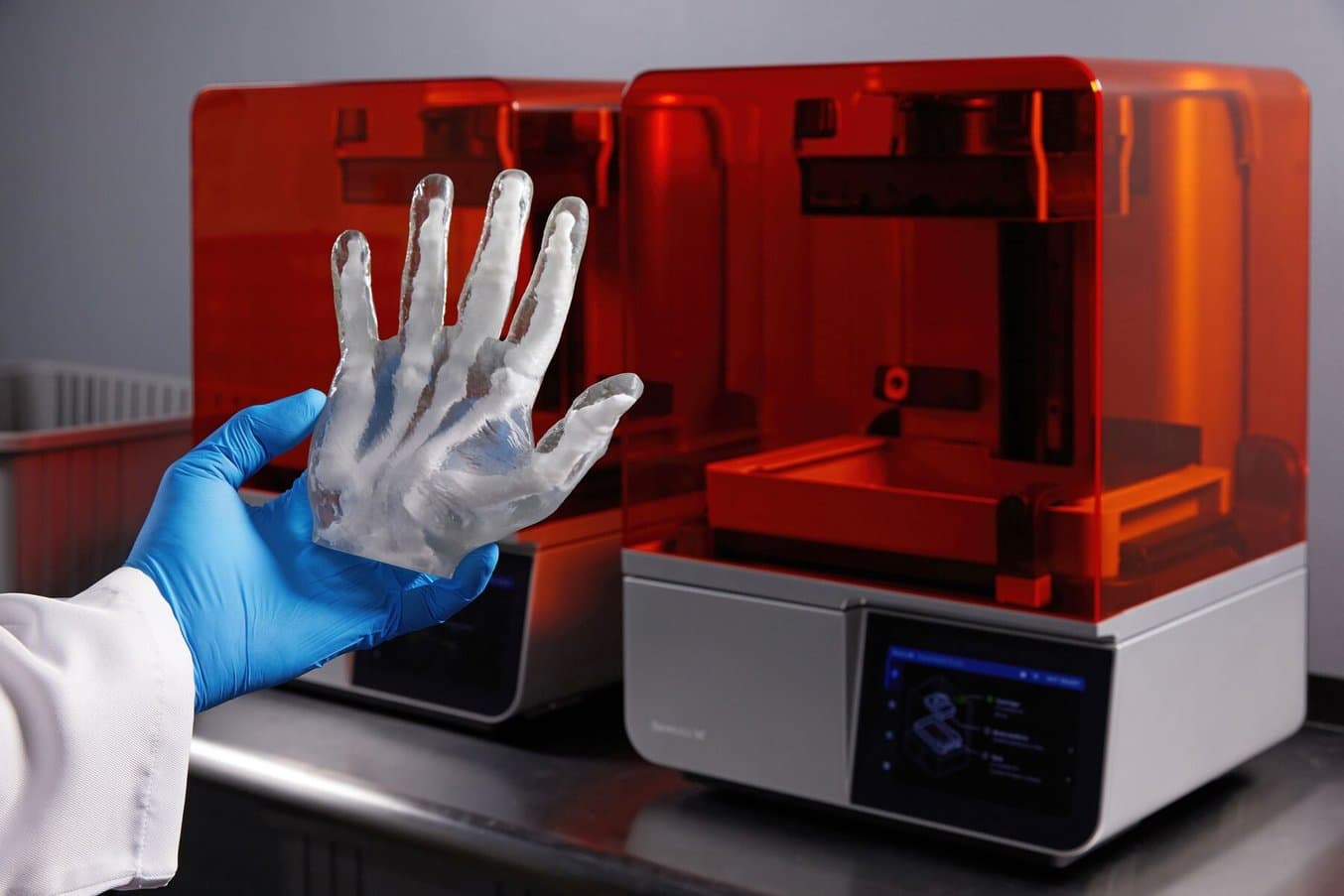
Resinas biocompatibles de Formlabs: Una guía exhaustiva para elegir el material adecuado
Actualmente, Formlabs ofrece más de 40 materiales únicos para la impresión 3D por estereolitografía (SLA). Este artículo ayuda a los usuarios a comparar y contrastar nuestros materiales biocompatibles para determinar cuál es el que se ajusta mejor al uso médico que quieren darle.
3. Nuevos productos sanitarios
La impresión 3D prácticamente se ha convertido en sinónimo de prototipado rápido. La facilidad de uso y el bajo coste de la impresión 3D in situ también han revolucionado el desarrollo de productos y muchos fabricantes de herramientas médicas han adoptado la tecnología para producir nuevos productos sanitarios e instrumentos quirúrgicos.
Más del 90 por ciento de las principales 50 empresas de productos sanitarios usan la impresión 3D para crear prototipos precisos de dispositivos médicos, sujeciones con guía y fijaciones para simplificar los ensayos, así como para imprimir en 3D directamente productos sanitarios.
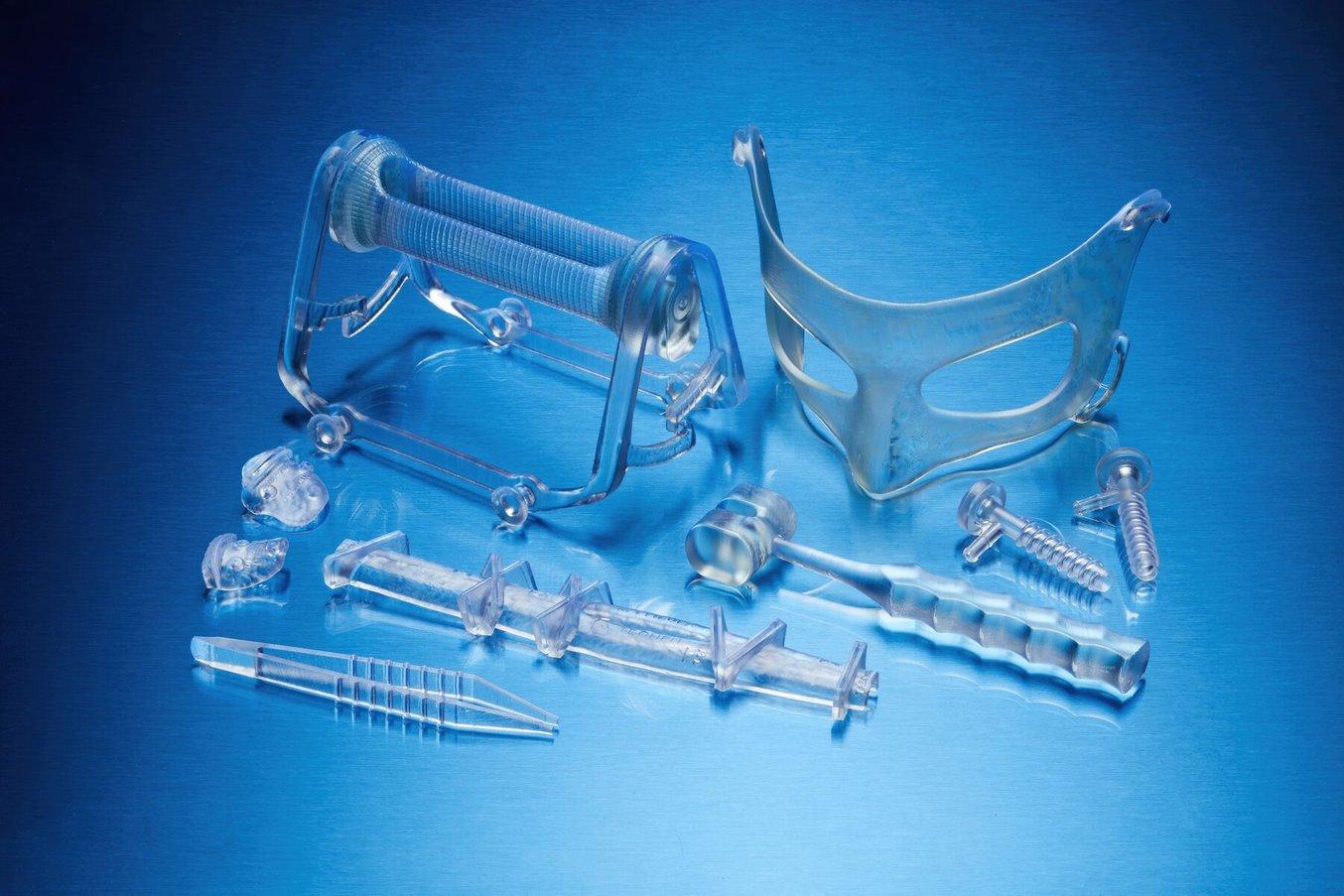
Creación de una nueva empresa de productos sanitarios con la fabricación aditiva de Formlabs
Conoce la inspiradora experiencia de tres empresas emergentes a la hora de construir un negocio totalmente nuevo y lanzar al mismo tiempo su primer producto sanitario. Nos explicarán por qué eligieron Formlabs para que formara parte de ese proceso y qué uso hicieron de la fabricación aditiva.
"Antes de que DJO Surgical incorporara la [impresora 3D de Formlabs], recurríamos casi exclusivamente a otras empresas de impresión para nuestros prototipos. Ahora, utilizamos cuatro impresoras de Formlabs, y su impacto en nuestro trabajo ha sido considerable. Nuestro ritmo de impresión 3D se ha duplicado, los costes se han reducido un 70 por ciento y el nivel de detalle de las impresiones nos permite tener una buena comunicación de los diseños con los cirujanos ortopédicos".
Alex Drew, un ingeniero de proyectos mecánicos de DJO Surgical
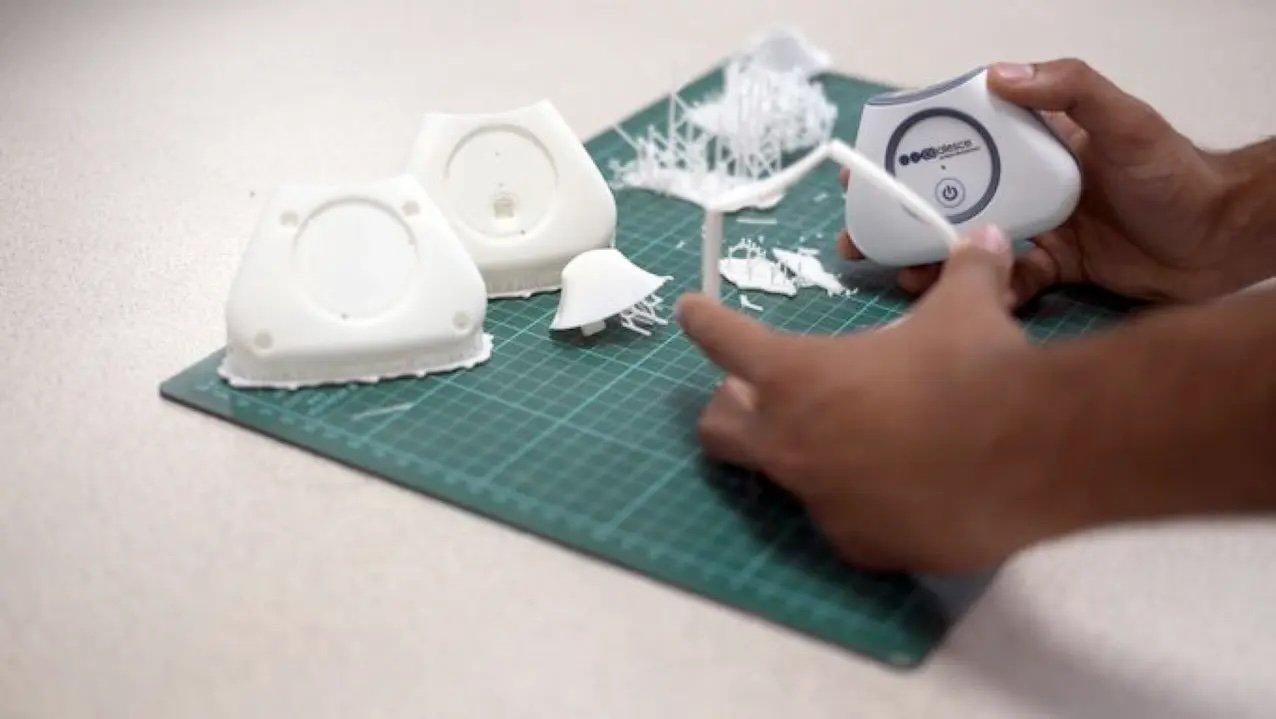
Las empresas de productos sanitarios como Coalesce usan la impresión 3D para crear prototipos precisos de dichos productos.
La impresión 3D puede acelerar el proceso de diseño haciendo que las iteraciones de diseños complejos se realicen en días, en lugar de semanas. Cuando Coalesce recibió el encargo de crear un inhalador capaz de evaluar digitalmente el perfil del flujo inspiratorio de un paciente con asma, externalizar el proyecto a un proveedor de servicios habría provocado que cada prototipo tuviera tiempos de espera largos. Los archivos de diseño habrían tenido que refinarse laboriosamente a lo largo de varias iteraciones antes de enviarlos a terceros para su construcción.
En vez de eso, la impresión 3D SLA de escritorio permitió a Coalesce mantener todo el proceso de prototipado dentro de la propia empresa. Los prototipos eran aptos para su uso en estudios clínicos y su aspecto era idéntico al de un producto terminado. De hecho, cuando se hizo una demostración del dispositivo, los clientes confundieron el prototipo con el producto final.
En general, trabajar in situ supuso una enorme reducción del 80-90 % de los tiempos de espera de los prototipos. Es más, las piezas solo tardaron ocho horas en imprimirse y se les pudo aplicar el acabado y la pintura en unos pocos días, mientras que el proceso habría llevado una semana o dos con un contratista externo.
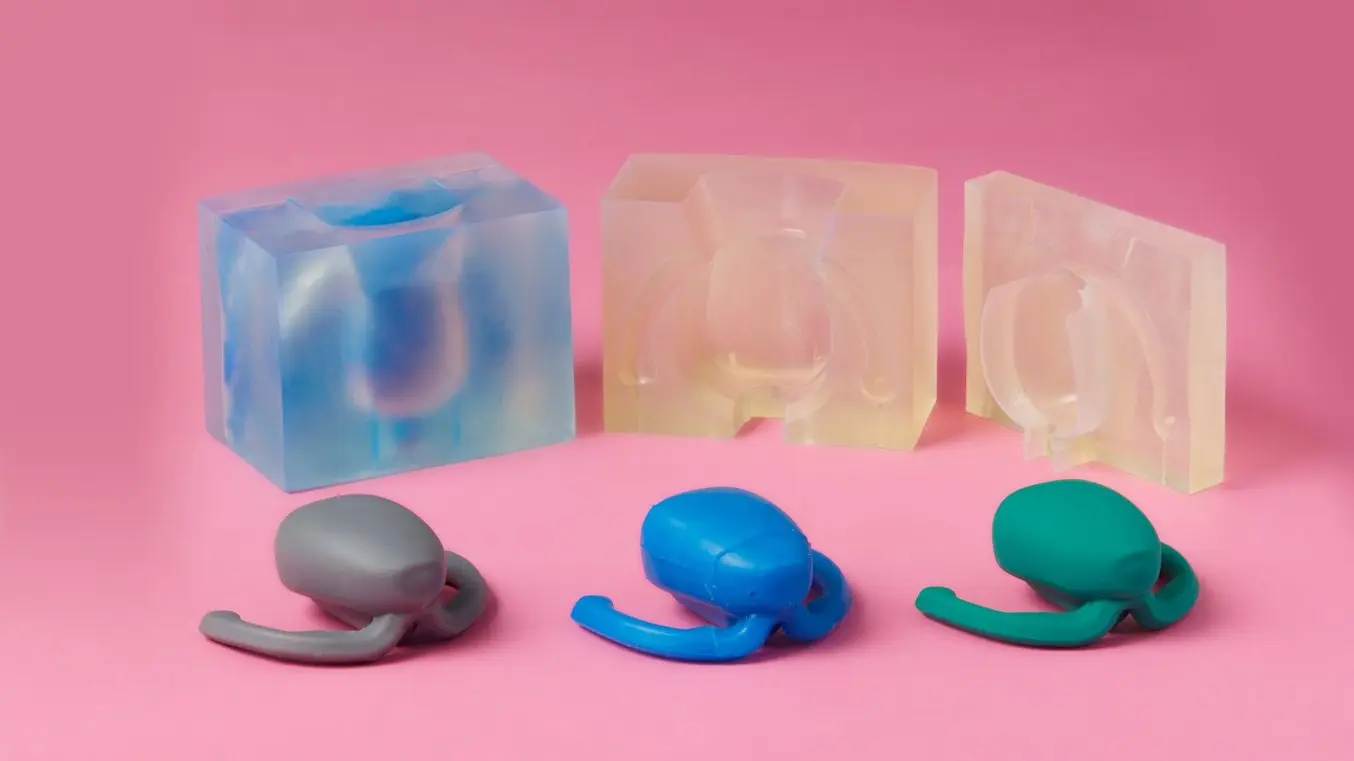
Creación de productos sanitarios con silicona
El objetivo de esta guía es ayudar al usuario a decidir cuál es el mejor método de producción de piezas de silicona para su uso previsto y ofrece instrucciones paso a paso tanto para imprimir con la Silicone 40A Resin como para moldear silicona utilizando herramientas impresas en 3D mediante SLA (que incluyen moldes de inyección de dos piezas, sobremoldes y moldes de compresión).
Shavini Fernando usó la impresión 3D para desarrollar OxiWear, un accesorio ponible en la oreja para monitorizar los signos vitales y enviar avisos de emergencia. Su equipo utilizó la impresión 3D SLA para prototipar el dispositivo y crear sujeciones con guía antiestáticas.
Nos dice: "Al ser una empresa nueva que acababa de empezar, imprimir en 3D in situ fue crucial para nosotros, ya que redujo mucho los costes a lo largo del ciclo de vida del desarrollo y nos permitió probar múltiples diseños de prototipos al mismo tiempo. Antes de imprimir en 3D, cada vez que había que externalizar un prototipo nos costaba 200 $. En comparación, cada dispositivo que imprimimos en la Form 3B nos cuesta calderilla".
4. Prótesis personalizadas avanzadas y asequibles
En todo el mundo, más de 50 millones de personas han necesitado la amputación de un miembro por motivos médicos. Para los pacientes que se enfrentan a la recuperación tras una emergencia médica, entrar por primera vez en el mundo de las prótesis puede ser doloroso. La mayoría quiere volver a su vida normal: conducir un coche, ejercitarse en el gimnasio, limpiar la casa. Sin embargo, la mayoría de las prótesis tradicionales son toscas, caras y frágiles. Aproximadamente el 10 % de los pacientes que requieren una prótesis avanzada de brazo puede permitírsela actualmente.
Las prótesis simples solo están disponibles en unas pocas tallas, de modo que los pacientes deben apañárselas con la que mejor les venga. Los dispositivos biónicos hechos a medida y diseñados para limitar los movimientos y agarres de miembros reales, que se valen de los músculos del miembro residual de una persona para controlar su funcionamiento, son tan caros que solo son accesibles para los pacientes que cuenten con los mejores seguros médicos de los países desarrollados. Esto afecta especialmente a las prótesis para niños. A medida que los niños crecen, es inevitable que sus prótesis se les queden pequeñas y requieran recambios costosos. El principal escollo es la falta de procesos de fabricación que puedan producir piezas personalizadas de forma asequible. Sin embargo, los fabricantes de prótesis cada vez optan más por aprovechar la famosa libertad de diseño de la impresión 3D para mitigar esas barreras económicas que impiden recibir el tratamiento.
Una de las empresas que está intentando revolucionar el mercado es PSYONIC, creadora de la Ability Hand. La Ability Hand es una prótesis diseñada y fabricada in situ con máquinas de CNC y métodos de fabricación híbrida, que promete volver a hacer que la vida y la movilidad de los pacientes sea la que era. PSYONIC utiliza la impresión 3D para prototipar rápidamente, hacer que sus productos sean más económicos y accesibles y crear piezas de uso final duraderas a partir de materiales resistentes a los impactos.
Iniciativas como e-NABLE permiten que se formen comunidades enteras en todo el mundo alrededor de las prótesis impresas en 3D. Están impulsando un movimiento independiente en la producción de prótesis, compartiendo información y diseños de código abierto libremente en Internet, para que los pacientes puedan obtener una prótesis que esté bien adaptada a ellos por precios tan bajos como 50 €.
Otros inventores, como Lyman Connor, van un paso más allá. Con solo un pequeño parque de cuatro impresoras 3D de escritorio, Lyman pudo completar y ajustar sus primeras prótesis de producción. ¿Cuál era su meta final? Crear una mano personalizable completamente biónica que vender a un precio considerablemente inferior a las decenas de miles de euros por los que se venden estas prótesis tan avanzadas en el mercado.
Por otro lado, unos investigadores del MIT también han identificado la impresión 3D como un medio óptimo para producir encajes de prótesis más cómodos.
Huelga decir que el bajo coste de la producción de estas prótesis, junto con la libertad que implican los diseños personalizados, ha sido revelador. Las prótesis hechas mediante la impresión 3D se pueden elaborar en apenas dos semanas y después pueden someterse a ensayo y mantenerse a un coste muy inferior al de sus equivalentes tradicionales.
A medida que los costes siguen decreciendo y mejoran las propiedades de los materiales, es indudable que la impresión 3D tendrá un papel cada vez más importante en este ámbito de la sanidad.
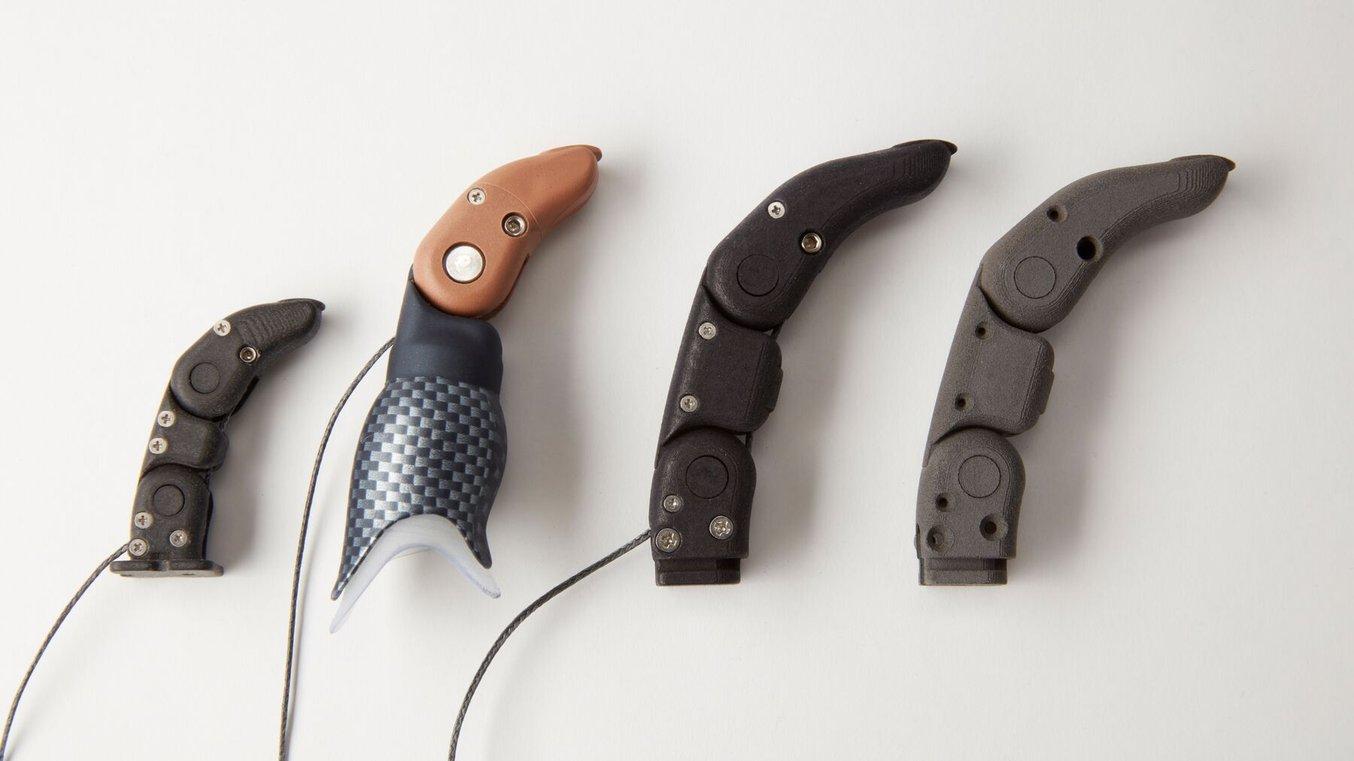
La impresión 3D en el sector de las órtesis y prótesis
Este libro blanco es una introducción al uso de la tecnología de impresión 3D para crear órtesis y prótesis de última generación.
5. Órtesis personalizadas
Muchas de las mismas barreras económicas que impiden recibir prótesis también se encuentran en ámbitos como el de las órtesis. Como muchos otros productos sanitarios adaptados al paciente, las órtesis personalizadas a menudo resultan inaccesibles por su elevado precio y por tardar semanas o meses en fabricarse. Con la impresión 3D, eso ya no tiene por qué ser así.
Muchos profesionales sanitarios ya están adoptando la impresión 3D para producir soluciones ortopédicas personalizadas. Al seguir procesos de trabajo de eficacia probada, la impresión 3D puede ahorrar tiempo y recursos, permitiendo producir órtesis adaptadas a los pacientes en tiempo récord.
Los procesos de trabajo digitales para las órtesis personalizadas engloban nuevas opciones de diseño, ensayo y fabricación para reducir los costes de la personalización y acelerar los ciclos de producción, con lo que se obtienen tiempos de espera menores, productos que se ajustan mejor a sus usuarios y resultados mejorados con los pacientes. Las órtesis impresas en 3D ofrecen una solución eficaz que hace posible una personalización de forma rápida y económica.
Kriwat GmbH, un proveedor médico especializado en ortopedia que tiene su sede principal en la ciudad alemana de Kiel, se enfrentaba a una escasez de mano de obra especializada. Por si esto no fuera poco, los procesos de trabajo tradicionales creaban un entorno lleno de polvo y vapores químicos. Para abordar estos problemas, Lais Kriwat, técnico maestro de calzado ortopédico, desarrolló un proceso de trabajo digital para la producción de plantillas ortopédicas utilizando dos impresoras 3D SLS Fuse 1+ 30W y el Nylon 11 Powder.
El proceso de trabajo digital redujo los costes de material y de mano de obra. Lais calcula que los costes de producción disminuyeron entre un 15 % y un 17 % gracias a la impresión 3D. También se aceleró la producción, con lo que sus trabajadores pudieron atender a más pacientes. "Ahora tenemos la capacidad de crear una órtesis que se ajusta perfectamente a un paciente en menos de 24 horas", dice Lais Kriwat.
Las posibilidades que se alcanzan con la libertad de diseño de la impresión 3D SLS incluyen la redistribución de la presión al andar, productos individuales de alta categoría, ciertos soportes que no se pueden fabricar con los métodos tradicionales y productos más delgados que siguen ofreciendo un apoyo óptimo para el pie en deportes como el atletismo y el fútbol.
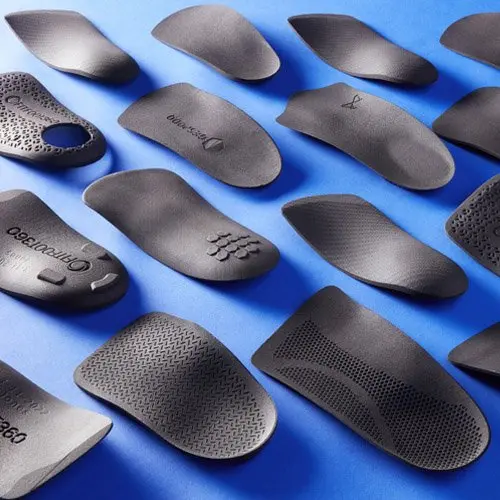
Impresión 3D de bases rígidas para plantillas ortopédicas con la Fuse 1+ 30W y el Nylon 11 Powder
Este estudio investiga las propiedades de los materiales y los métodos de fabricación utilizados para hacer plantillas ortopédicas personalizadas: la Fuse 1+ 30W y el Nylon 11 Powder de Formlabs, el HP 3D de alta reutilización PA 11 y el polipropileno fabricado de forma tradicional.
Matej y su hijo Nik son un ejemplo del poder de las órtesis personalizadas impresas en 3D. Nik nació prematuro en 2011 y las dificultades de su parto provocaron que padeciese parálisis cerebral, un trastorno que afecta a casi 20 millones de personas en todo el mundo. A Matej le parecía admirable la voluntad inquebrantable de su hijo de superar las limitaciones que su trastorno le imponía, pero debía elegir: una órtesis prefabricada que sería inadecuada e incómoda para su hijo o una costosa solución a medida que tardaría meses o semanas en llegar, para quedarse rápidamente desfasada al crecer el niño.
Decidió ocuparse él mismo del asunto y buscó nuevas soluciones para alcanzar su objetivo. Con la libertad que ofrecían tecnologías digitales como el escaneo 3D y la impresión 3D, los fisioterapeutas de Matej y Nik pudieron experimentar con comodidad y desarrollar un proceso de trabajo innovador completamente nuevo para crear órtesis de pie y tobillo.
La órtesis diseñada a medida e impresa en 3D que produjeron proporcionó a Nik el apoyo, la comodidad y la corrección exactas que necesitaba y donde las necesitaba, con lo que Nik pudo dar sus primeros pasos sin ayuda de nadie. Esta órtesis personalizada aportaba el acabado muy ajustado de las órtesis de alta gama, por un precio bastante inferior y sin que fueran necesarias más modificaciones.
La impresión 3D permite producir órtesis adaptadas a los pacientes con procesos de trabajo optimizados que ahorran tiempo y recursos. Para los pacientes, esto supone menos citas en la ortopedia, esperas más cortas y una personalización precisa que aumenta su comodidad. En comparación con los métodos de fabricación tradicionales, los procesos de trabajo 3D ahorran tiempo y recursos de material, al mismo tiempo que reducen los gastos y hacen posible un entorno de trabajo más cómodo.
6. Bioimpresión, ingeniería de tejidos, órganos impresos en 3D y más allá
La bioimpresión 3D es el uso de procesos de fabricación aditiva para depositar materiales conocidos como "biotintas", con los que se crean estructuras similares a tejidos que puedan usarse en ámbitos médicos. La ingeniería de tejidos es el conjunto de tecnologías en auge (entre las que se encuentra la bioimpresión) cuyo objetivo es desarrollar tejidos y órganos de sustitución en el laboratorio para usarlos en el tratamiento de lesiones y enfermedades.
Los investigadores están utilizando la bioimpresión en el desarrollo de tejidos y órganos cultivados en el laboratorio. Hacer posible dicho desarrollo crearía avances en la medicina regenerativa y en las pruebas de seguridad. Además, la capacidad de bioimprimir órganos podría aumentar significativamente las probabilidades de éxito de los transplantes. Dado que la bioimpresión usa células extraídas del paciente que requiere el tratamiento, elimina la posibilidad de un rechazo por parte del sistema inmunitario, uno de los grandes problemas de las operaciones de transplante de órganos hoy en día.
En la Universidad de Osaka, los investigadores han utilizado tinta a base de células y un soporte de impresión para crear formas específicas, como la de una nariz. Una vez que están impresas, las células siguen siendo viables durante un máximo de dos semanas, lo que supone un avance considerable en el trabajo de desarrollar órganos cultivados en laboratorio.
Actualmente, la regeneración de la piel y la curación de las heridas se realizan mediante dolorosos injertos de piel. Poder imprimir piel ofrece una alternativa que fomentaría la regeneración de la piel y la curación de las heridas. En 2023, investigadores del Instituto Wake Forest de Medicina Regenerativa consiguieron bioimprimir piel de grosor completo que mostraba una gran capacidad de curación al transplantarla en situaciones preclínicas.
El Dr. Atala, el principal autor del artículo, dijo: "Estos resultados muestran que la creación de piel humana de grosor completo mediante bioingeniería es posible, y que fomenta una curación más rápida y resultados con un aspecto más natural".
Los científicos del Instituto Terasaki de Innovación Biomédica han desarrollado una biotinta para imprimir que puede potenciar la formación de tejido muscular esquelético. Se espera que este tipo de tecnología se pueda usar para ayudar a personas que sufran lesiones o pérdidas musculares.
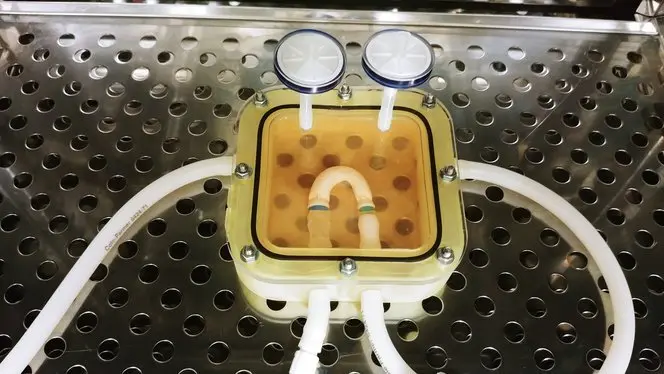
Una cámara de biorreactor impresa en 3D con una aorta en miniatura creciendo en su interior, generada mediante ingeniería de tejidos. El tejido se cultiva en el biorreactor para obtener el funcionamiento mecánico y biológico del tejido orgánico.
La impresión 3D ha demostrado que es capaz de responder a los desafíos de la producción de vasos sanguíneos sintéticos recreando las formas, dimensiones y geometrías precisas del vaso sanguíneo necesario. La capacidad de adaptar las soluciones impresas a las necesidades específicas de los pacientes ha resultado reveladora.
Citando al Dr. Pashneh-Tala: "[Crear vasos sanguíneos mediante la impresión 3D] ofrece el potencial de mejorar nuestras opciones quirúrgicas e incluso diseños de vasos sanguíneos a medida para los pacientes. Sin acceso a una impresión 3D asequible de alta precisión, crear estas formas no sería posible".
La bioimpresión está evolucionando rápidamente a medida que los investigadores expanden las fronteras de lo que se puede hacer con ella. Desde huesos y sangre hasta piel y músculos; los avances en bioimpresión están allanando el camino para que haya mejoras de la asistencia a los pacientes en el futuro.
Impresión 3D médica
En lo que respecta a las impresoras 3D médicas, no todos los métodos dan el mismo resultado. Es importante elegir la tecnología de impresión 3D adecuada para casos de uso específicos.
Las tecnologías de impresión 3D médica más populares incluyen la estereolitografía (SLA), el sinterizado selectivo por láser (SLS) y el modelado por deposición fundida (FDM) para las piezas de plástico, y el sinterizado directo de metal por láser (DMLS) y la fusión selectiva por láser (SLM) para los metales.
Estereolitografía (SLA)
Las impresoras 3D SLA usan un láser para curar resina líquida y convertirla en plástico endurecido en un proceso conocido como fotopolimerización. La SLA es uno de los procesos más populares entre los profesionales de la medicina por su alta resolución, su precisión y la versatilidad de sus materiales.
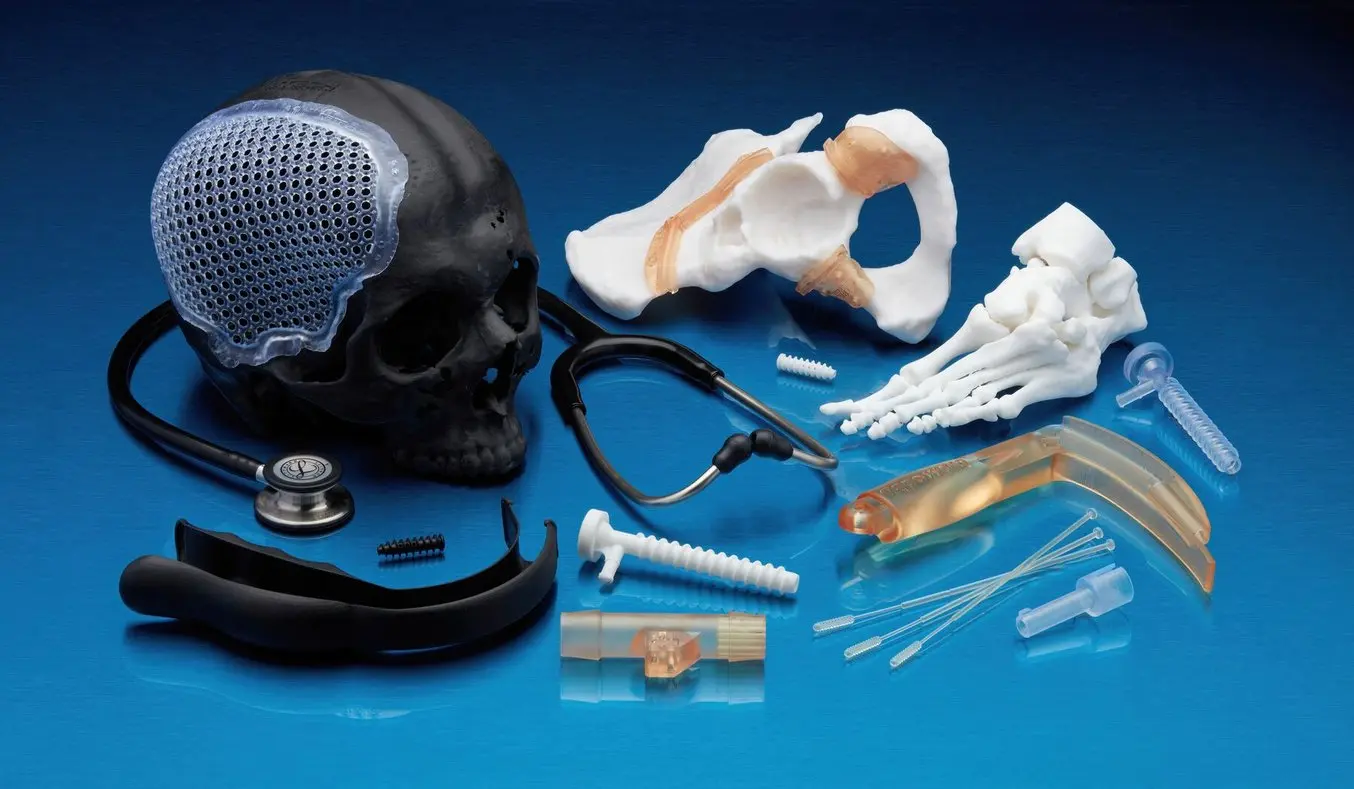
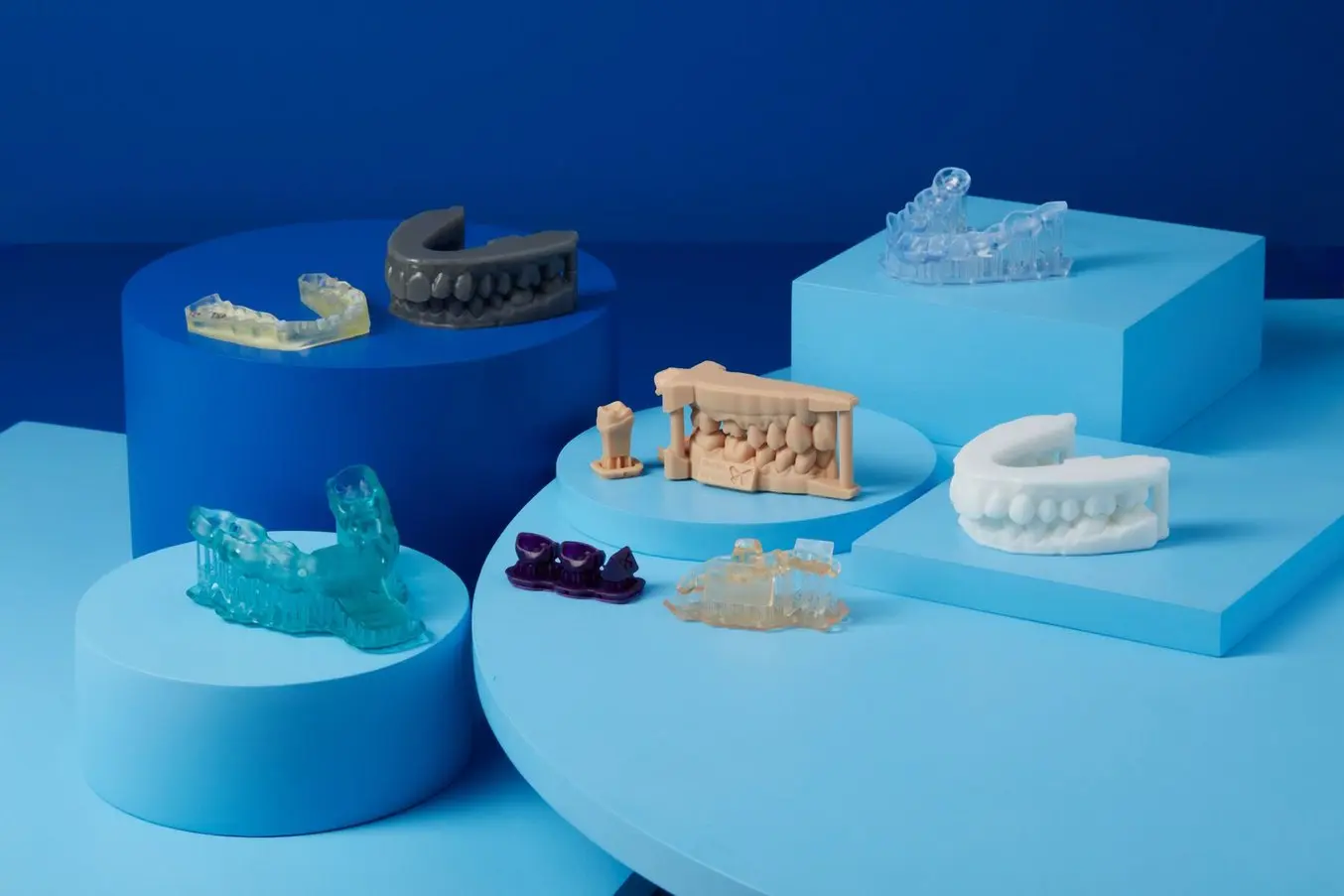
La impresión 3D SLA ofrece una amplia selección de materiales de impresión 3D, que incluye materiales biocompatibles, para diversas aplicaciones médicas y odontológicas.
Ventajas de la SLA
Las piezas realizadas mediante SLA tienen la mayor resolución y precisión, los detalles más nítidos y el acabado más liso de todas las tecnologías de impresión 3D. Sin embargo, la principal ventaja de la SLA reside en su versatilidad. Las fórmulas de resina para SLA ofrecen una gran variedad de propiedades ópticas, mecánicas y térmicas capaces de igualar las de los termoplásticos estándar, industriales y para ingeniería.
La impresión por SLA es una excelente opción para prototipos de productos sanitarios con un alto nivel de detalle que requieren tolerancias ajustadas y superficies lisas, así como para moldes, utillaje, patrones, y piezas de uso final funcionales. La SLA también ofrece la selección más amplia de materiales biocompatibles para aplicaciones odontológicas y médicas, como instrumentos quirúrgicos y aparatos médicos que requieren un contacto con la piel o las membranas mucosas.
Desventajas de la SLA
La gran versatilidad de la SLA hace que su precio sea ligeramente más caro que el del FDM, pero sigue siendo más asequible que cualquier otro proceso de impresión 3D. Las piezas de resina para SLA también requieren un posacabado después de la impresión, que incluye lavar las piezas y poscurarlas.

Solicita una pieza de muestra gratuita
Comprueba la calidad de la SLA de Formlabs de primera mano. Enviaremos una pieza de muestra gratuita a tu lugar de trabajo.
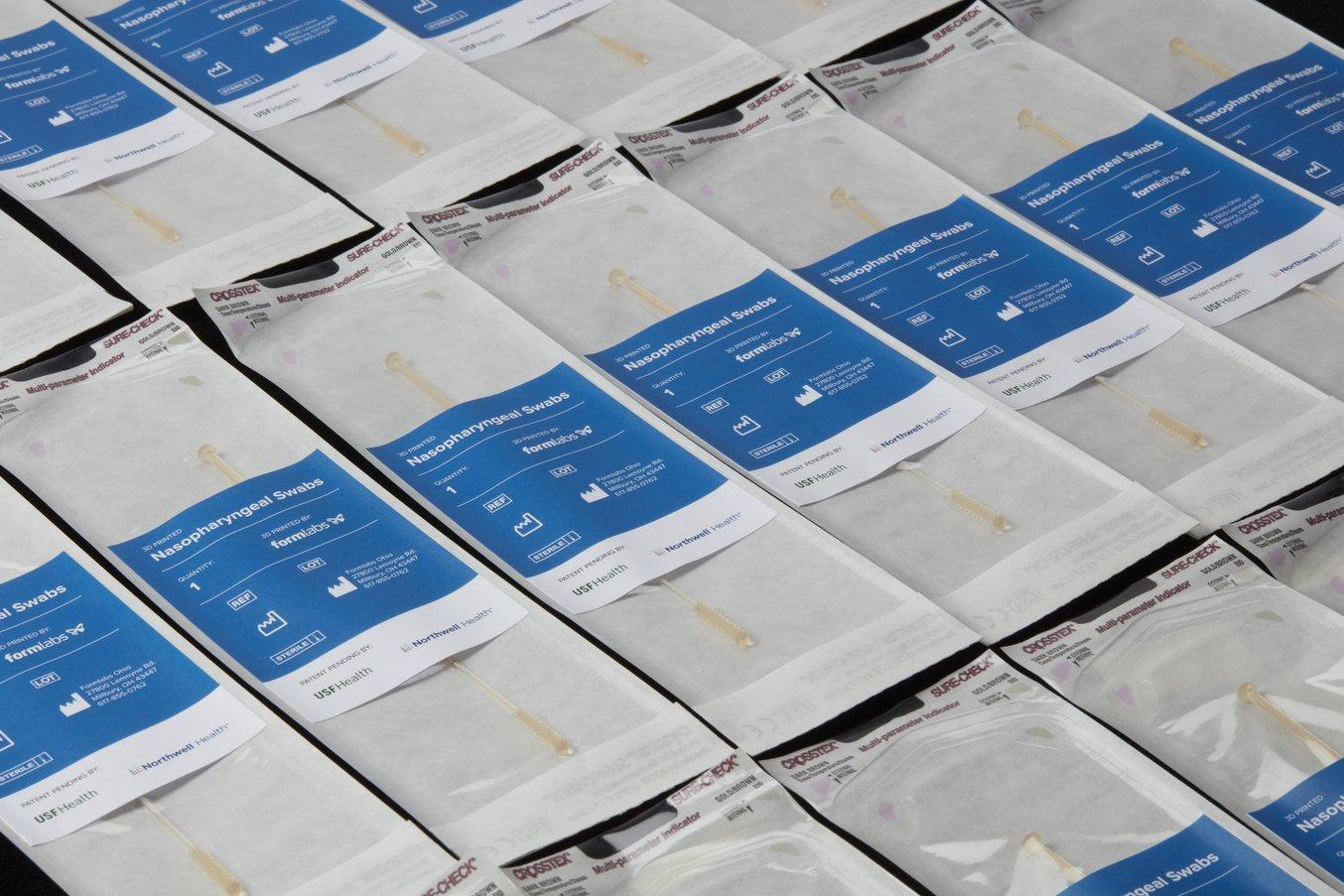
Guía de Formlabs de gestión del control de calidad para innovadores del sector sanitario
Esta guía describe los pasos que pueden dar los profesionales sanitarios para mantener, supervisar y mejorar la calidad de las piezas impresas en 3D mediante SLA.
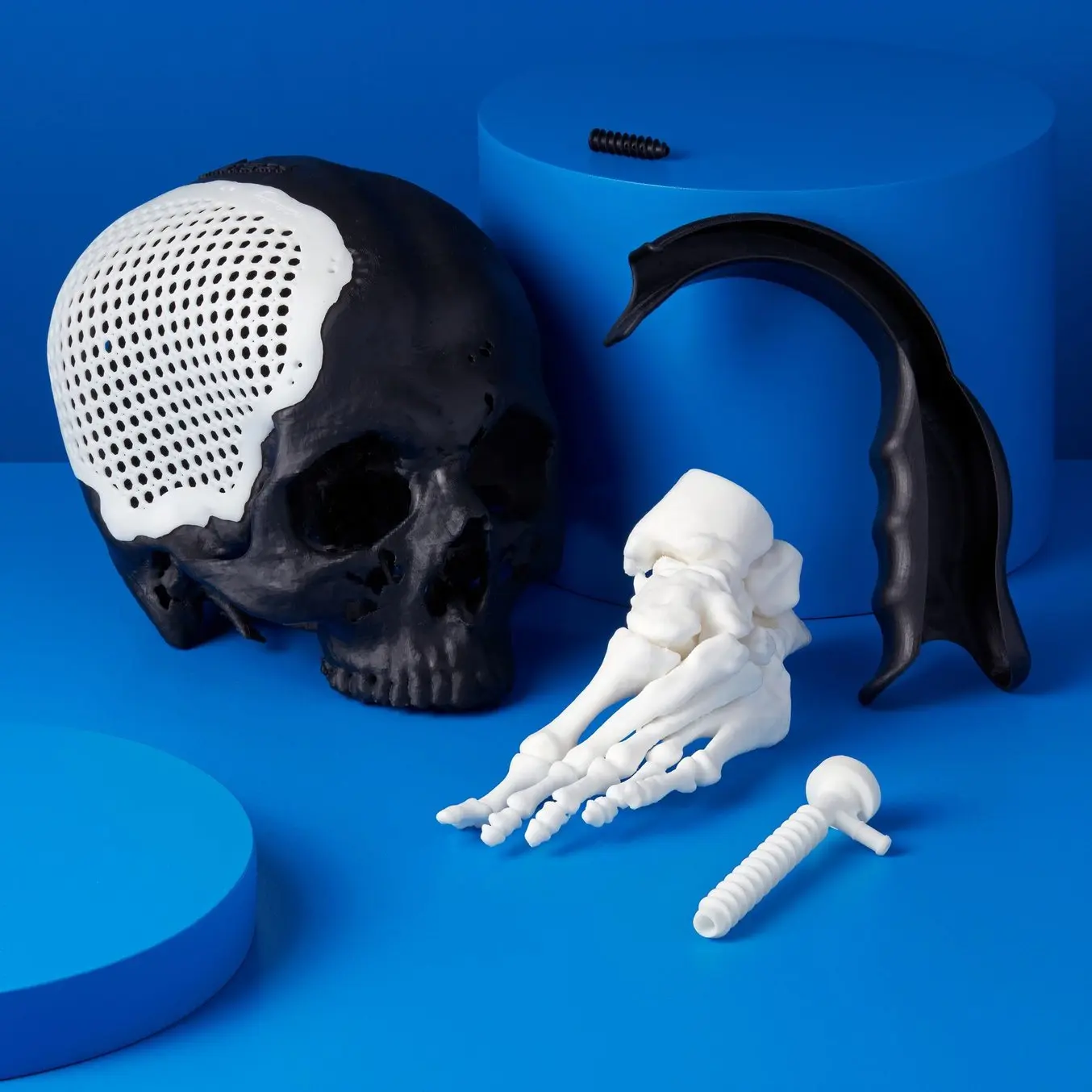
Productos sanitarios impresos en 3D para la cirugía de precisión: Perspectivas clínicas, comerciales y reglamentarias
Únete a Formlabs y Nelson Labs para realizar un análisis profundo de la biocompatibilidad, que incluye una introducción a nuestros nuevos materiales y buenas prácticas que los expertos del sector ofrecen a los fabricantes médicos.
Sinterizado selectivo por láser (SLS)
Las impresoras 3D SLS usan un láser de alta potencia para fundir pequeñas partículas de polvo de polímero. El polvo sin fundir sirve como soporte para la pieza durante la impresión y elimina la necesidad de agregar expresamente estructuras de soporte, por lo que el SLS es una opción especialmente eficaz para piezas mecánicas complejas.
La capacidad del SLS para producir piezas con excelentes capacidades mecánicas lo convierte en la tecnología de fabricación aditiva con polímeros más común para aplicaciones industriales. En función del material, las impresiones SLS también pueden ser biocompatibles y esterilizables, lo que las hace ideales para productos sanitarios, prototipos, guías quirúrgicas, tecnología ponible y órtesis.
Ventajas del SLS
Dado que la impresión por SLS no requiere estructuras de soporte específicas, es ideal para geometrías complejas, como relieves interiores, socavados, paredes delgadas y relieves cóncavos de piezas. Las piezas producidas mediante SLS tienen excelentes características mecánicas, con una resistencia similar a la de las piezas moldeadas por inyección.
La combinación de un bajo coste por pieza, una alta productividad, materiales establecidos y biocompatibilidad hace que el SLS sea una elección popular entre los desarrolladores de productos sanitarios para el prototipado funcional.
Desventajas del SLS
Las impresoras 3D SLS tienen un precio de entrada más alto que las tecnologías de FDM o SLA. Aunque hay varios materiales disponibles, el catálogo de materiales para el SLS es más limitado que los del FDM y la SLA. Las piezas salen de la impresora con un acabado de la superficie ligeramente rugoso, por lo que requieren pasos de posacabado como un granallado para obtener un acabado liso.

La impresión 3D SLS es ideal para prototipos funcionales resistentes y piezas de uso final, como prótesis y órtesis.
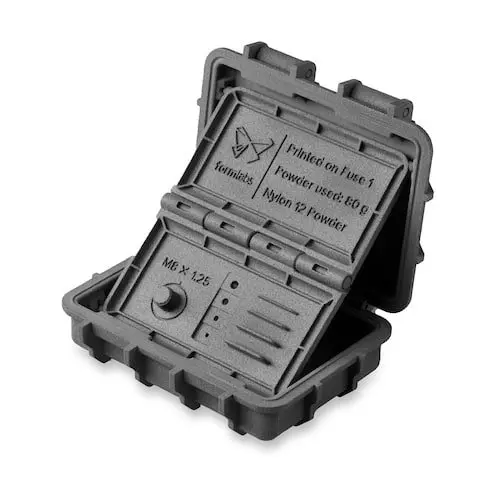
Solicita una pieza de muestra gratuita
Experimenta la calidad de la impresión SLS de Formlabs de primera mano. Enviaremos una pieza de muestra gratuita a tu lugar de trabajo.
Modelado por deposición fundida (FDM)
La impresión 3D FDM, también conocida como fabricación con filamento fundido (FFF), construye piezas derritiendo y extruyendo un filamento termoplástico que un extrusor deposita capa por capa en el área de impresión.
El FDM es la forma más extendida de impresión 3D al alcance del consumidor, fomentada por la aparición de las impresoras 3D para aficionados. Sin embargo, las impresoras FDM industriales también son populares entre los profesionales.
Ventajas del FDM
La impresión por FDM funciona con varios termoplásticos estándar, como el acrilonitrilo butadieno estireno (ABS), el ácido poliláctico (PLA) y sus diversas mezclas. Esto genera un precio inicial y de los materiales más bajo. El FDM se ajusta mejor a modelos de prueba de concepto básicos y al prototipado de bajo coste para piezas sencillas. Algunas materiales de FDM también son biocompatibles.
Desventajas del FDM
El FDM es la técnica que menor resolución y precisión tiene comparada con otras tecnologías de impresión 3D para plástico como la SLA y el SLS. No es la mejor opción para imprimir diseños complejos o piezas con relieves complicados, como los modelos anatómicos. Obtener un acabado de gran calidad requiere procesos de pulido químicos y mecánicos en los que hay que invertir mucho tiempo y trabajo manual. Algunas impresoras 3D FDM industriales usan soportes solubles para mitigar algunos de estos inconvenientes y ofrecen una mayor variedad de termoplásticos para ingeniería, pero estos tienen un precio elevado. Además, el FDM tiende a ser más lento al crear impresiones grandes que la SLA o el SLS.
Sinterizado directo de metal por láser (DMLS) y fusión selectiva por láser (SLM)
Las impresoras 3D de sinterizado directo de metal por láser (DMLS) y fusión selectiva por láser (SLM) funcionan de forma parecida a las impresoras SLS, pero en lugar de fundir polímeros en polvo, unen partículas de polvo metálico capa a capa utilizando un láser.
Las impresoras 3D DMLS y SLM pueden crear productos de metal resistentes, precisos y complejos, lo que hace que este proceso sea ideal para diversas aplicaciones sanitarias.
Ventajas del DMLS y la SLM
La mayor ventaja de estos procesos son los materiales, obviamente, ya que las impresoras 3D DMLS y SLM son capaces de producir productos sanitarios y componentes de uso final a partir de metal. Estos procesos pueden reproducir geometrías complejas y los productos acabados son resistentes, duraderos y biocompatibles. Se pueden utilizar para fabricar implantes genéricos (de cadera, rodilla, vertebrales, etc.), implantes a medida para el tratamiento de tumores y traumatismos, prótesis dentales y productos de tecnología médica y ortopédica.
Desventajas del DMLS y la SLM
Aunque los precios de las impresoras 3D de metal han empezado a bajar, con costes que van de 200 000 € a más de un millón de euros, estos sistemas siguen sin ser accesibles para la mayoría de los negocios. Los procesos de impresión 3D de metal también conllevan un proceso de trabajo arduo y complejo.
Por otro lado, la impresión 3D SLA es adecuada para procesos de trabajo de fundición de metal que produzcan piezas de metal a bajo coste, con una mayor libertad de diseño y en menos tiempo que con los métodos tradicionales.
Compara las impresoras 3D médicas
Estereolitografía (SLA) | Sinterizado selectivo por láser (SLS) | Modelado por deposición fundida (FDM) | Impresión 3D de metal (DMLS, SLM) | |
---|---|---|---|---|
Volumen de impresión | Hasta 300 × 335 × 200 mm (impresoras 3D de escritorio y para el banco de trabajo) | Hasta 165 × 165 × 300 mm (impresoras 3D para el banco de trabajo industriales) | Hasta 300 × 300 × 600 mm (impresoras 3D de escritorio y para el banco de trabajo) | Hasta 400 × 400 × 400 mm (DMLS/SLM industrial de gran tamaño) |
Gama de precios | Las impresoras profesionales pueden adquirirse desde 2399 € y las impresoras de trabajo de gran formato a partir de 8999 €, mientras que las máquinas industriales de gran tamaño están disponibles desde 80 000 €. | Los sistemas de sobremesa industriales pueden adquirirse desde 23 899 € y las impresoras industriales tradicionales están disponibles desde 100 000 €. | Las impresoras más asequibles y los equipos de impresión 3D tienen un precio inicial de unos cientos de euros. Las impresoras de escritorio de gama media y de mayor calidad pueden adquirirse desde 2000 € y los sistemas industriales están disponibles desde 15 000 €. | Desde 200 000 € |
Materiales | Variedades de resina (plásticos termoendurecibles). Resinas estándar, para ingeniería (similares al ABS y al polipropileno, flexibles, resistentes a la temperatura), para aplicaciones de fundición, dentales y médicas (biocompatibles). Silicona pura y cerámica. | Termoplásticos para ingeniería (incluyen materiales biocompatibles). Nylon 11, nylon 12, materiales compuestos de nylon reforzados con vidrio o carbono, polipropileno, TPU (elastómero). | Termoplásticos estándar, como el ABS, el PLA y sus diversas mezclas. | Acero inoxidable, acero de herramientas, titanio, cromo-cobalto y aluminio. |
Aplicaciones ideales | Modelos anatómicos (biocompatibles), instrumentos quirúrgicos (biocompatibles), productos sanitarios (biocompatibles), aparatos dentales (biocompatibles), prototipado rápido, utillaje rápido, accesorios para la fabricación y piezas de uso final. | Modelos anatómicos (biocompatibles), instrumentos quirúrgicos (biocompatibles), productos sanitarios (biocompatibles), órtesis y prótesis, prototipado rápido, utillaje rápido, accesorios para la fabricación y piezas de uso final. | Modelos de prueba de concepto básicos. Prototipado económico de piezas simples. | Piezas resistentes y duraderas con geometrías complejas, implantes, prótesis dentales, componentes médicos y ortopédicos hechos de metal. |
Materiales para las aplicaciones médicas de la impresión 3D
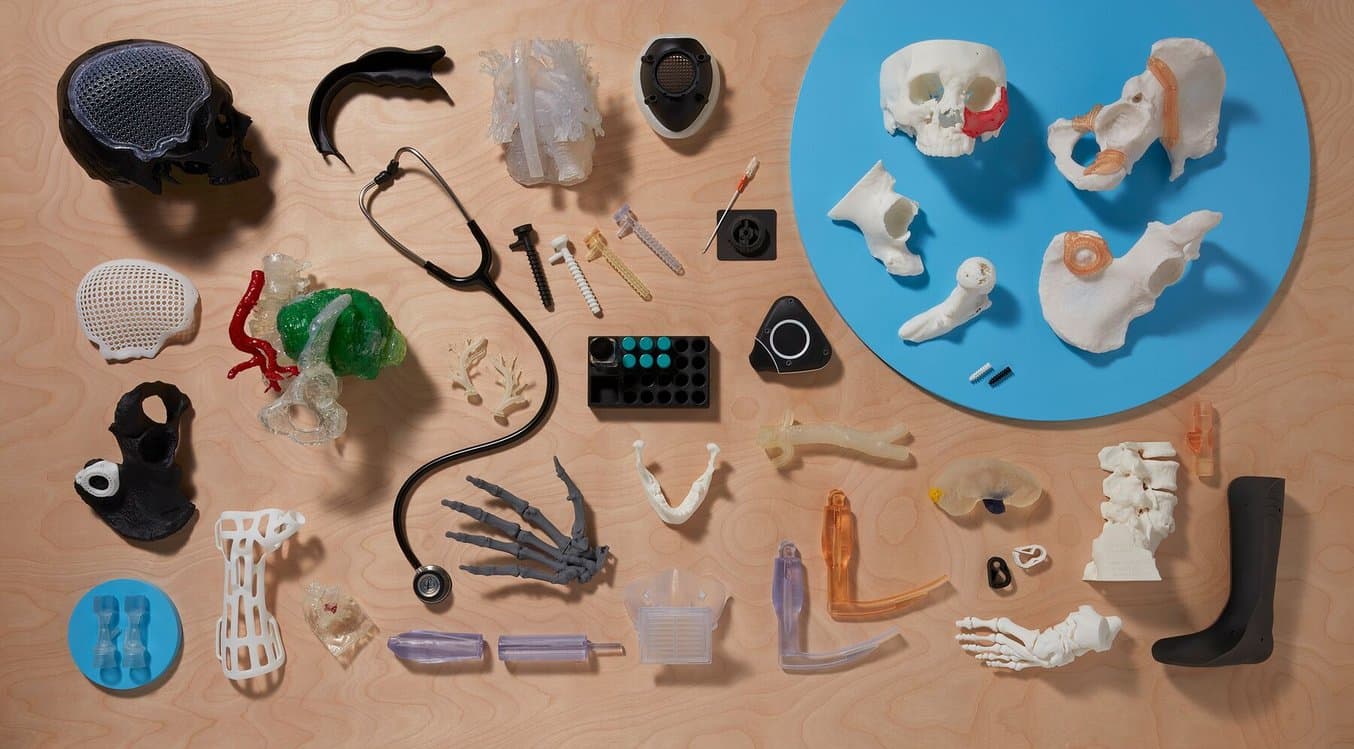
El catálogo de materiales de Formlabs incluye resinas para la impresión SLA y polvos para la impresión SLS, que están optimizados para diversas aplicaciones médicas.
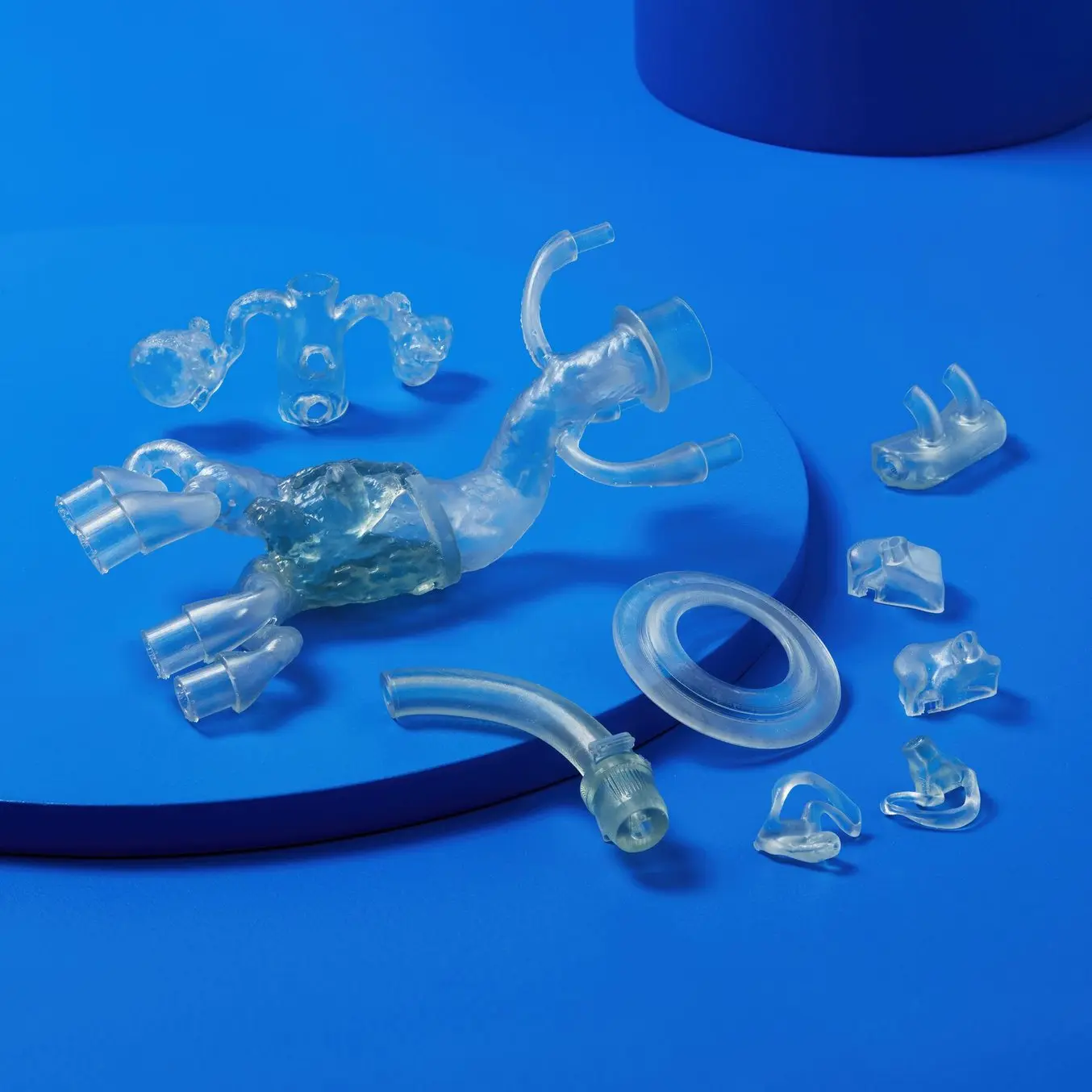
Dominar los materiales para imprimir en 3D productos sanitarios
En este seminario web, el ingeniero médico de Formlabs Shiden Yohannes explora los diversos materiales que están disponibles para la impresión 3D y sus propiedades únicas, con el fin de guiarte para que tomes decisiones informadas que se ajusten a tus necesidades.
Resinas para SLA
La SLA admite un amplio abanico de usos en sectores como la ingeniería, la fabricación y la sanidad. Se han desarrollado resinas para SLA con propiedades específicas, que incluyen opciones que son elásticas, duraderas y biocompatibles.
Las resinas BioMed de Formlabs están diseñadas para profesionales de la sanidad que buscan materiales médicos que sirvan para una amplia gama de aplicaciones en las que el rendimiento y la biocompatibilidad son cruciales. Los materiales de la familia de resinas BioMed se desarrollan y fabrican en unas instalaciones con certificación ISO 13485 y son compatibles con los métodos de desinfección y esterilización comunes.
Elegir la resina apropiada depende de la aplicación que se le vaya a dar, los requisitos mecánicos del material y el caso de uso. Las resinas BioMed de Formlabs incluyen opciones rígidas y elásticas, entre las que se cuentan algunas que están pensadas para un contacto de larga duración con la piel o con las membranas mucosas.
Además, se ha desarrollado todo un catálogo de materiales diseñados específicamente para satisfacer las necesidades de los profesionales de la odontología. Son resinas como la Premium Teeth Resin, pensada para la impresión directa de dientes de prótesis, y la Dental LT Comfort Resin, para férulas oclusales. Hay un catálogo completo de materiales e información acerca de las aplicaciones de las resinas para odontología de Formlabs, que está disponible en Formlabs Dental.
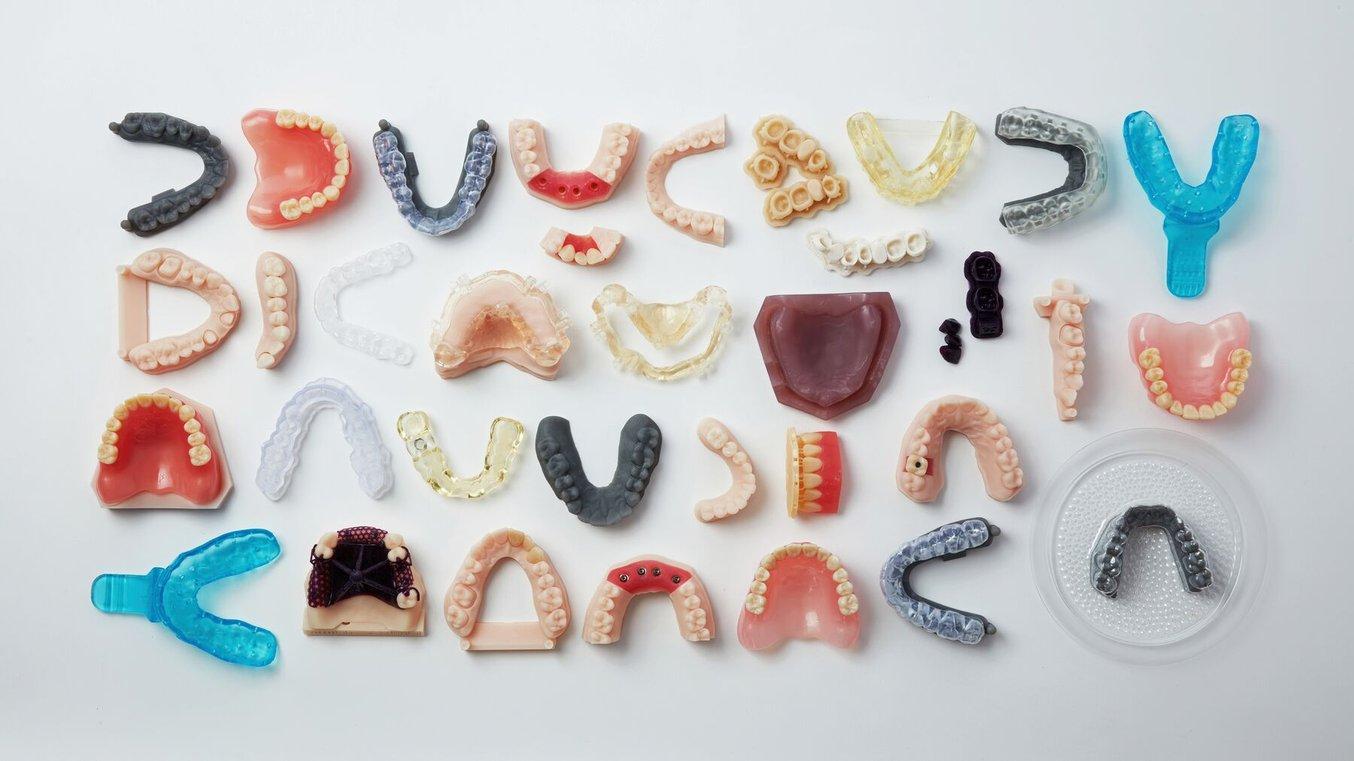
Se pueden imprimir más de 17 aplicaciones dentales con resinas de Formlabs formuladas específicamente para el mercado de la odontología.
Diversificar los tipos de resinas médicas puede ayudar a los profesionales de la sanidad con toda una serie de tareas esenciales: la creación de productos sanitarios, la planificación de procedimientos quirúrgicos, el desarrollo de implantes personalizados y la ejecución de investigaciones. La resinas BioMed dan a los profesionales sanitarios un abanico de opciones de materiales que expanden las capacidades de la impresión 3D. La siguiente tabla compara las propiedades y las aplicaciones de las resinas BioMed de Formlabs.
Material | Descripción | Aplicaciones |
---|---|---|
BioMed White Resin | Rígida y opaca, de color blanco. Aprobada para un contacto de larga duración (más de 30 días) con la piel y un contacto de corta duración (menos de 24 horas) con hueso, tejidos, dentina y membranas mucosas. | Productos sanitarios de uso final y componentes de los mismos; modelos y moldes de calibrado de implantes adaptados a los pacientes; guías de corte y perforación; herramientas y plantillas quirúrgicas; moldes, sujeciones con guía fijaciones biocompatibles; modelos anatómicos que se puedan usar en el quirófano. |
BioMed Black Resin | Rígida, de color negro mate. Aprobada para un contacto de larga duración (más de 30 días) con la piel y un contacto de corta duración (menos de 24 horas) con membranas mucosas. | Productos sanitarios de uso final y componentes de los mismos; moldes, sujeciones con guía y fijaciones biocompatibles; piezas de uso final que requieren estar en contacto con los pacientes; productos de consumo. |
BioMed Amber Resin | Rígida y semitransparente. Aprobada para un contacto de larga duración (más de 30 días) con la piel y un contacto de corta duración (menos de 24 horas) con hueso, tejidos, dentina y membranas mucosas. | Productos sanitarios de uso final, modelos de calibrado de implantes, guías de corte y perforación. |
BioMed Clear Resin | Rígida y transparente. Aprobada para un contacto de larga duración con la piel (más de 30 días) o las vías de gases respiratorios y las membranas mucosas (más de 30 horas). También está aprobada para un contacto de corta duración (menos de 24 horas) con hueso, tejidos y dentina. | Productos sanitarios de uso final, incluidos productos de las vías de gases respiratorios; moldes, sujeciones con guía y fijaciones, modelos para visualización y calibrado de implantes; dispositivos de cultivo celular y bioprocedimientos. |
BioMed Durable Resin | Resistente a los impactos, a la rotura y la abrasión. Transparente. Aprobada para un contacto de larga duración con la piel (más de 30 días) y las membranas mucosas (más de 30 horas), o un contacto de corta duración (menos de 24 horas) con hueso, tejidos, y dentina. | Instrumentos adaptados a los pacientes, instrumentos de un solo uso; productos sanitarios de uso final y componentes que requieren biocompatibilidad y resistencia a los impactos. |
BioMed Elastic 50A Resin | Blanda y similar a la silicona. Translúcida. Aprobada para un contacto de larga duración (más de 30 días) con la piel o un contacto de corta duración (menos de 24 horas) con membranas mucosas. | Productos sanitarios cómodos que requieran un contacto de larga duración con la piel; modelos de tejidos blandos biocompatibles que los cirujanos puedan usar como referencia en el quirófano. |
BioMed Flex 80A Resin | Similar a la goma dura. Translúcida. Aprobada para un contacto de larga duración (más de 30 días) con la piel o un contacto de corta duración (menos de 24 horas) con membranas mucosas. | Productos sanitarios y componentes de los mismos biocompatibles y flexibles; productos sanitarios que requieran un contacto de corta duración con membranas mucosas, modelos de tejidos duros para ayudar en operaciones quirúrgicas. |
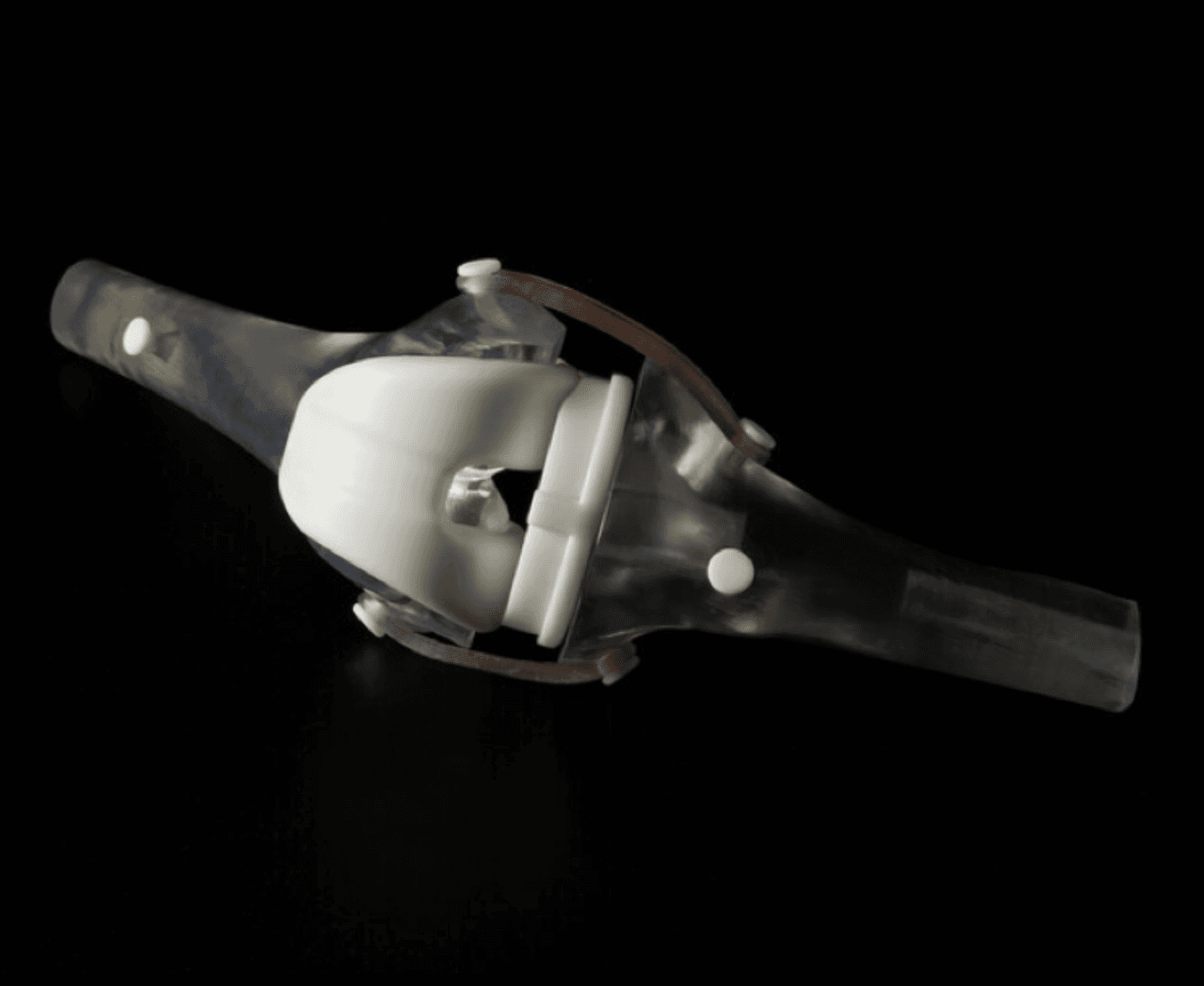
Creación de modelos de simulación de huesos para corte y perforación
Los modelos de simulación ósea impresos en 3D están revolucionando la formación médica, la planificación quirúrgica, la investigación y el desarrollo de productos sanitarios. Esta guía de aplicación describe las opciones de materiales de simulación ósea para la impresión 3D por estereolitografía (SLA) y todo el proceso de fabricación in situ de modelos anatómicos con propiedades similares a las de los huesos, destinados al corte y la perforación.
Polvos para SLS
Los polvos para SLS pueden ser biocompatibles, seguros para la piel y esterilizables; los diseños realizados con ellos pueden tener detalles precisos y paredes delgadas. Estas propiedades los hacen ideales para aplicaciones sanitarias como productos sanitarios, prototipos, prótesis, instrumentos quirúrgicos y órtesis.
El material más común para SLS es el nylon, un popular termoplástico para ingeniería con excelentes propiedades mecánicas. El nylon es ligero, resistente y flexible, así como estable frente a impactos, productos químicos, calor, luz UV, polvo y suciedad. Las piezas de nylon impresas en 3D también pueden ser biocompatibles y no sensibilizantes, lo que significa que pueden estar listas para llevarlas como prendas y son seguras de usar en muchos contextos.
El Nylon 12 Powder ofrece un equilibrio entre resistencia y detalle, con una resistencia a la tracción de 50 MPa. Al ser capaz de crear conjuntos complejos y piezas resistentes con una gran estabilidad ambiental, el Nylon 12 Powder es ideal para el prototipado de alto rendimiento, la fabricación de bajo volumen y sujeciones con guía, fijaciones y utillaje permanentes. Las piezas son biocompatibles y esterilizables, lo que convierte al Nylon 12 Powder en un material ideal para aplicaciones médicas, como guías quirúrgicas.
El Nylon 11 Powder es un material ideal para órtesis tenaces con gran ductilidad y estabilidad a largo plazo, como las bases de plantillas ortopédicas. Descubre más acerca de la durabilidad de este material en este análisis de rendimiento.
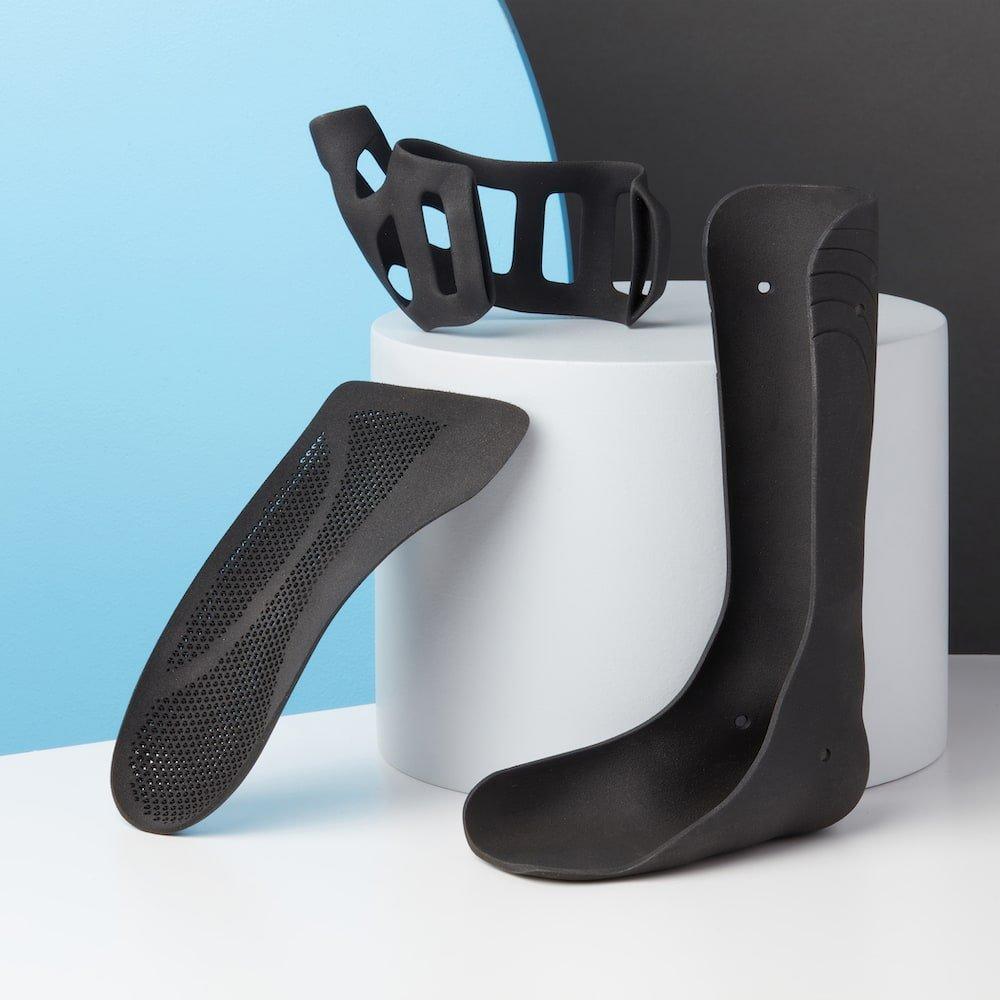
Órtesis impresas con el Nylon 11 Powder.
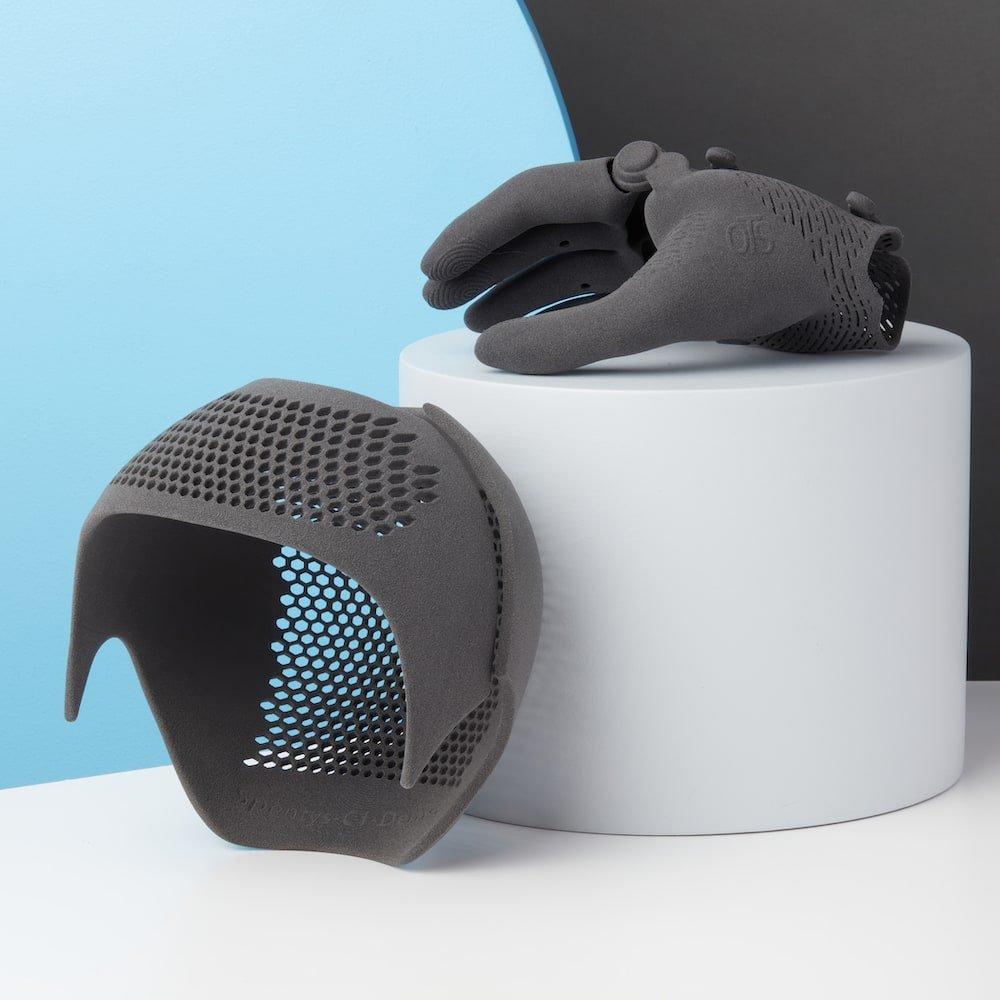
Un casco de remodelación craneal y un prototipo de una prótesis, impresos con el TPU 90A Powder.
El Polypropylene Powder se puede usar para producir prototipos funcionales y piezas de uso final resistentes. La gran ductilidad que ofrece permite doblarlo y flexionarlo repetidamente sin sacrificar durabilidad. Las piezas impresas con el Polypropylene Powder son resistentes a los productos químicos, soldables y estancas, por lo que son ideales para órtesis, prótesis, fijaciones, herramientas y sujeciones con guía.
El TPU 90A Powder es un elastómero flexible que combina la alta resistencia al desgarro y el gran alargamiento de rotura de los materiales de goma con la libertad de diseño y la durabilidad de la impresión 3D SLS. El TPU o poliuretano termoplástico es un termoplástico elastomérico muy utilizado. En el sector de la ortopedia, este material seguro para la piel se usa a menudo para prototipos de productos sanitarios, productos sanitarios de uso final y componentes de estos últimos, almohadillas ortopédicas, revestimientos protésicos, férulas, cascos de remodelación craneal y plantillas deportivas y correctoras.
La siguiente tabla desglosa algunas de las propiedades y las aplicaciones de los polvos para SLS de Formlabs.
Material | Descripción | Aplicaciones |
---|---|---|
Nylon 12 Powder | Gran resistencia a la tracción y durabilidad, biocompatible, esterilizable. | Productos sanitarios de uso final y componentes de los mismos; modelos y moldes de calibrado de implantes adaptados a los pacientes; guías de corte y perforación; herramientas y plantillas quirúrgicas; moldes, sujeciones con guía fijaciones biocompatibles; modelos anatómicos que se puedan usar en el quirófano. |
Nylon 11 Powder | Muy dúctil y robusto. Más flexible, menos frágil y mejor para imprimir paredes delgadas que el Nylon 12 Powder. Biocompatible, esterilizable. | Órtesis y prótesis, prototipos resistentes a los impactos, productos sanitarios, piezas de uso final. |
Polypropylene Powder | Dúctil y duradero, resistente a productos químicos, estanco, soldable. | Órtesis y prótesis, estuches y carcasas estancos; fijaciones, herramientas y sujeciones con guía fuertes y resistentes a los productos químicos. |
TPU 90A Powder | Elastómero tenaz, seguro para la piel, resiliente ante la deformación, con un gran alargamiento de rotura y resistencia al desgarro. | Suelas, férulas, aparatos ortopédicos y prótesis. Dispositivos ponibles y elementos de tacto blando. Almohadillas, amortiguadores y pinzas. |
Las propiedades de los materiales pueden variar según el diseño de las piezas y los métodos de fabricación. Es responsabilidad del fabricante determinar la idoneidad de las piezas impresas para su uso previsto.
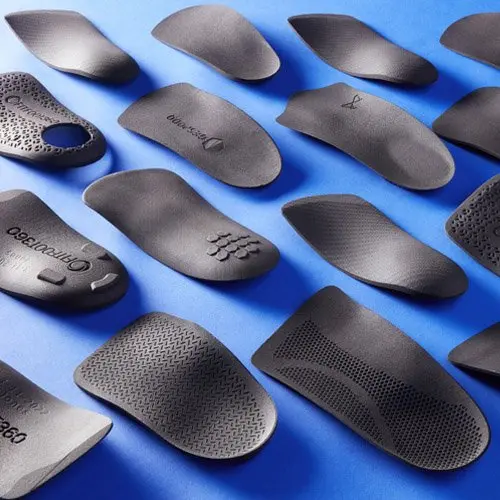
Impresión 3D de bases rígidas para plantillas ortopédicas
Descubre cómo producir bases fuertes y dúctiles para plantillas ortopédicas que superen los 4 millones de ciclos de flexión, con el ecosistema SLS compacto y asequible de Formlabs. Esta guía exhaustiva te ayudará a empezar a producir bases para plantillas ortopédicas con la Fuse 1+ 30W.
Empieza a trabajar con la impresión 3D médica
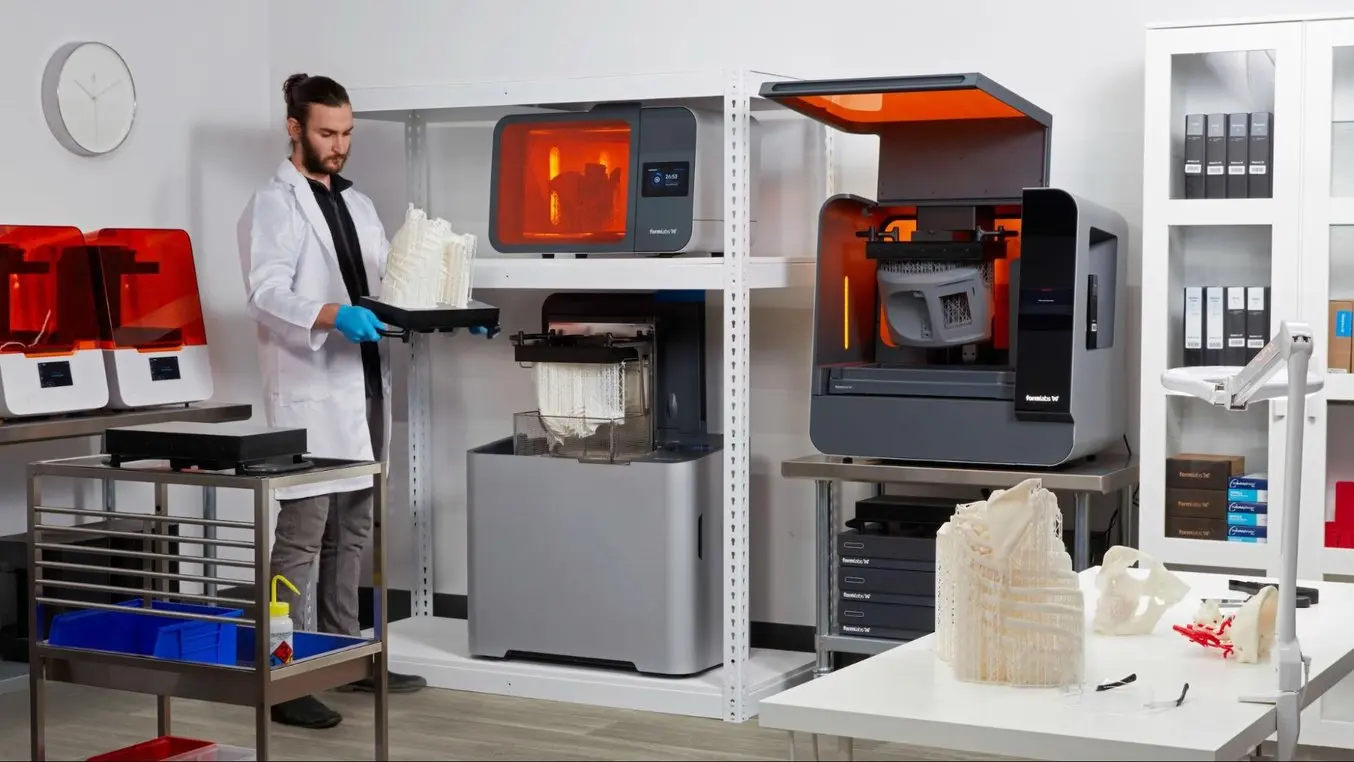
Los procesos de impresión 3D médica precisos y asequibles están democratizando el acceso a la tecnología y dando a los profesionales del sector sanitario la capacidad de desarrollar nuevas soluciones clínicas y fabricar rápidamente dispositivos personalizados. También permiten a los médicos enviar tratamientos nuevos a cualquier lugar del mundo. A medida que las tecnologías y los materiales de impresión 3D para la medicina sigan mejorando, allanarán el camino para la asistencia personalizada y aplicaciones médicas muy eficaces.
Todos los centros médicos deberían tener acceso a las herramientas más modernas para mejorar la asistencia y proporcionar la mejor experiencia posible para el paciente. Comienza ya a usarlas o expande la producción de tus instalaciones con Formlabs, un socio fiable que está a la vanguardia de la impresión 3D médica.
Ponte en contacto con nuestros expertos médicos para saber más acerca de cómo la impresión 3D puede ofrecer un tratamiento mejor y complementar tu actual proceso de diseño y fabricación de productos sanitarios.