The automotive industry is undergoing rapid transformation as consumer sentiment and regulatory mandates create mounting pressure to transition away from fossil fuels and to electric vehicles. Ford is leading the charge, much as it did through the production of the Model T and the introduction of the assembly line over 100 years ago, and plans to sell exclusively EVs in Europe by 2030.
Ford Motor Company is the sixth largest automaker in the world, producing over 4 million vehicles a year and employing over 175,000 staff worldwide. At the heart of Ford's European operations is Ford Cologne, established in 1930 and best known for assembling the Ford Fiesta.
Adjacent to the factory, PD Merkenich serves as a development center, responsible for designing all passenger vehicles for the European market from the ground up, including successful models such as the Fiesta, Focus, Kuga, and now the all-electric Explorer, the first EV for the European market, which recently entered serial production in the Cologne assembly plant. The team also supports the development of commercial vehicles, collaborating with Ford’s Dunton Technical Centre in the UK.
But how does Ford keep up with the intense competition and increasingly shorter development cycles? Read on to get a glimpse into PD Merkenich’s Rapid Technology Center, which is instrumental in creating rapid prototypes for product development.
The Tools to Produce Full-Scale Automotive Prototypes
“Prototyping is very important in the development process. It gives you, the engineer, the possibility to verify the design. If you need to rework your injection molding tool or production tool later on, this is very expensive. It takes a lot of time, so you will have downtime at the production in the worst case. This can be avoided using prototyping and applying all the technologies that are available,” said Sandro Piroddi, Supervisor of the Rapid Technology Center at Ford.
Producing full-scale vehicle prototypes requires a wide range of tools. The Rapid Technology Center is a sprawling facility that is equipped with the latest fabrication methods: it has its own injection molding machines, forming tools, and a wide range of subtractive manufacturing tools, for example, milling machines that can fit even the largest chassis panels.
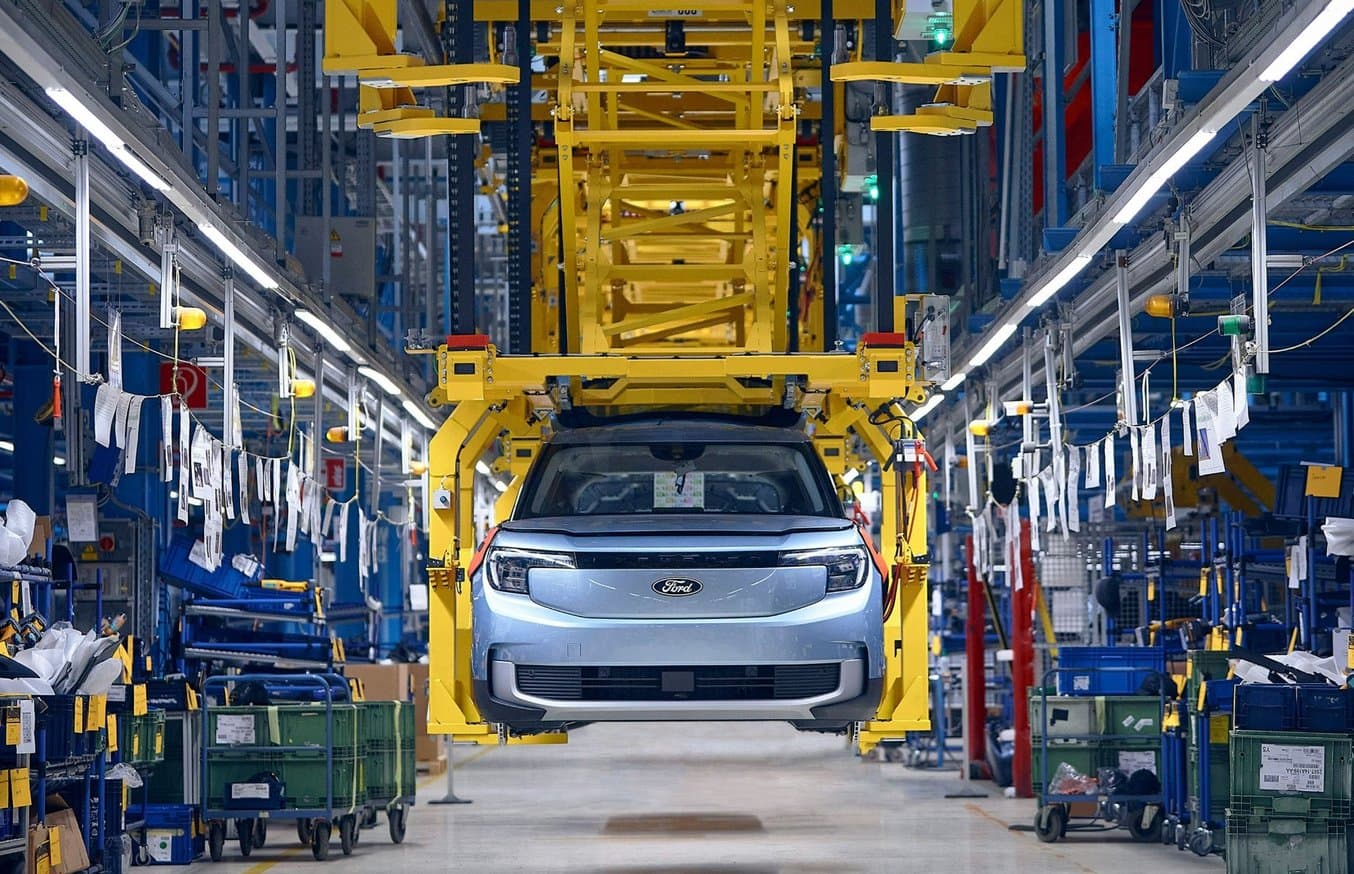
The all-electric Explorer has recently entered serial production in the Cologne assembly plant.
Of course, the list wouldn’t be complete without additive manufacturing. PD Merkenich was actually the first workshop in Europe to utilize a stereolithography (SLA) 3D printer in 1994 and since then has expanded its fleet to a suite of fused deposition modeling (FDM), SLA, and selective laser sintering (SLS) polymer 3D printers, as well as metal 3D printing.
While the first concept models are still developed from clay, as the product development moves into later stages and each component gets closer to its final shape, it’s increasingly important to be able to test both form and function with materials and processes that are as close to production as possible.
"Additive manufacturing is very important in the development process. It gives you the opportunity to produce parts very quickly, very efficiently, and reduce costs. You also have the possibility to react on a short-term basis. Looking at the development in the direction of electrification, the development times are getting shorter, so that means the time you have to develop parts and verify parts of vehicles is getting shorter and therefore it's very important to have this technology in the development process. It makes you much more competitive compared to competitors."
Sandro Piroddi, Supervisor of the Rapid Technology Center, Ford
Due to increasingly compressed development schedules, the Rapid Technology Center constantly seeks advancements within the additive manufacturing field that can empower them to expedite the delivery of components.
Developing Design Prototypes With SLA 3D Printing
SLA 3D printers are used mainly in the workshop for design prototypes that require good surface quality and need to be rapidly produced for quick iterations. PD Merkenich’s first Formlabs printer was a Form 2, but they quickly scaled up their fleet to multiple desktop units and a Form 3L large-format SLA 3D printer. Most recently, they were one of the first companies to get their hands on Form 4, Formlabs’ latest MSLA 3D printer.
“The Form 4 is very fast, I think it is the best machine that I’ve seen until now in terms of speed. It's really a very good upgrade compared to the previous models. It’s easier to operate, so it's much easier for the operators in our workshop to learn how to work with the machine and get parts with good quality,” said Bruno Alves, Additive Manufacturing Expert and Tooling Specialist at Ford.
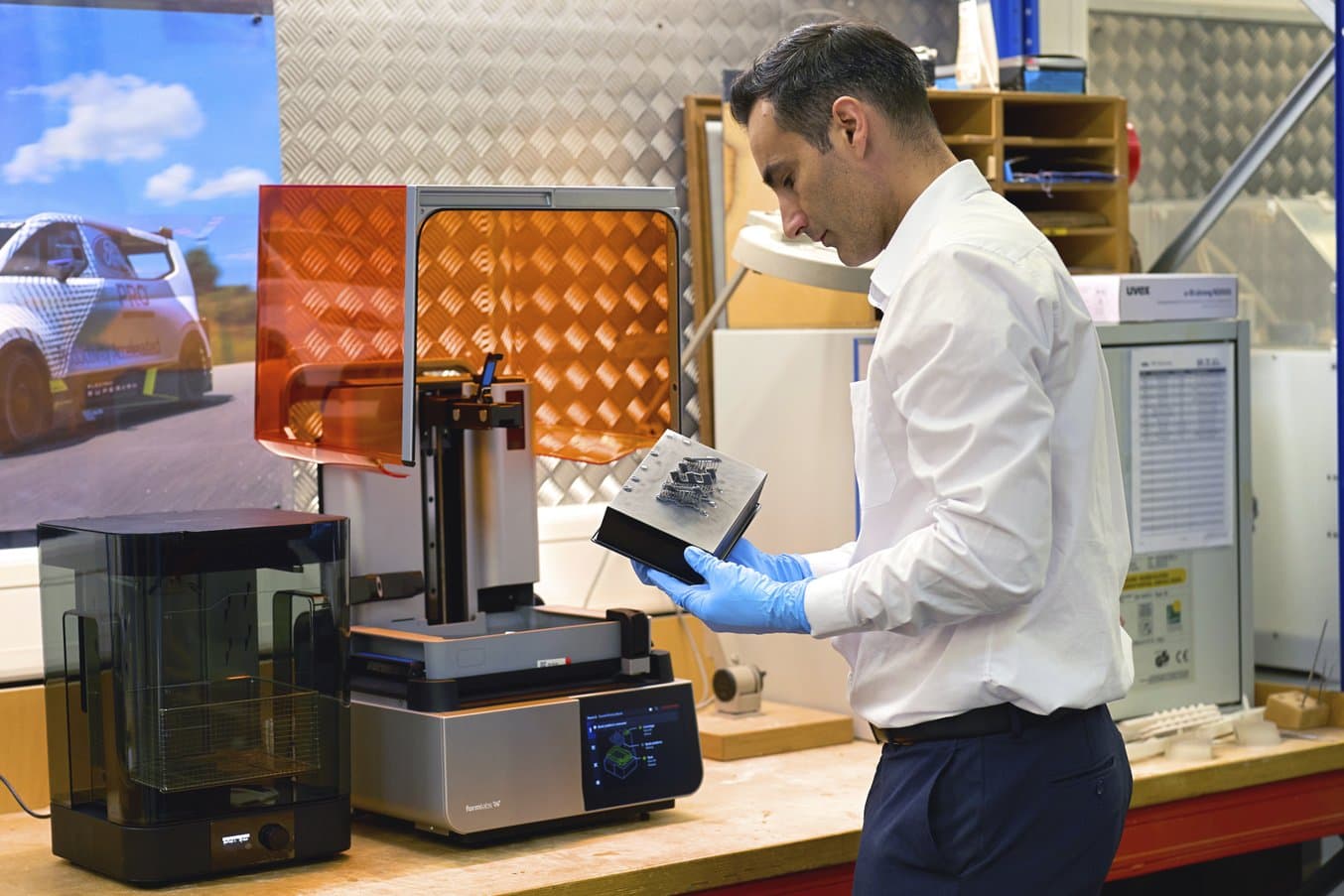
PD Merkenich was one of the beta testers of the new Form 4. The blazing fast speed of the new printer will empower the workshop to deliver new prototypes in just hours.
“Working with Form 4, it's really a game-changer. The speed of the printer will change our workflow. We can deliver more parts, the throughput is higher. We are much more flexible if we have short-time requests. Now we can do these using Form 4.”
Sandro Piroddi, Supervisor of the Rapid Technology Center, Ford
“Some years ago it was days, now we are just printing parts in some minutes. So the engineers are not afraid to make new designs, new iterations, because they know now that they will get the parts very fast,” added Alves.
The rapid print speed now enables the RTC team to fulfill more requests in under 24 hours — even ones coming from the UK, where they can deliver parts quickly through overnight shipment.
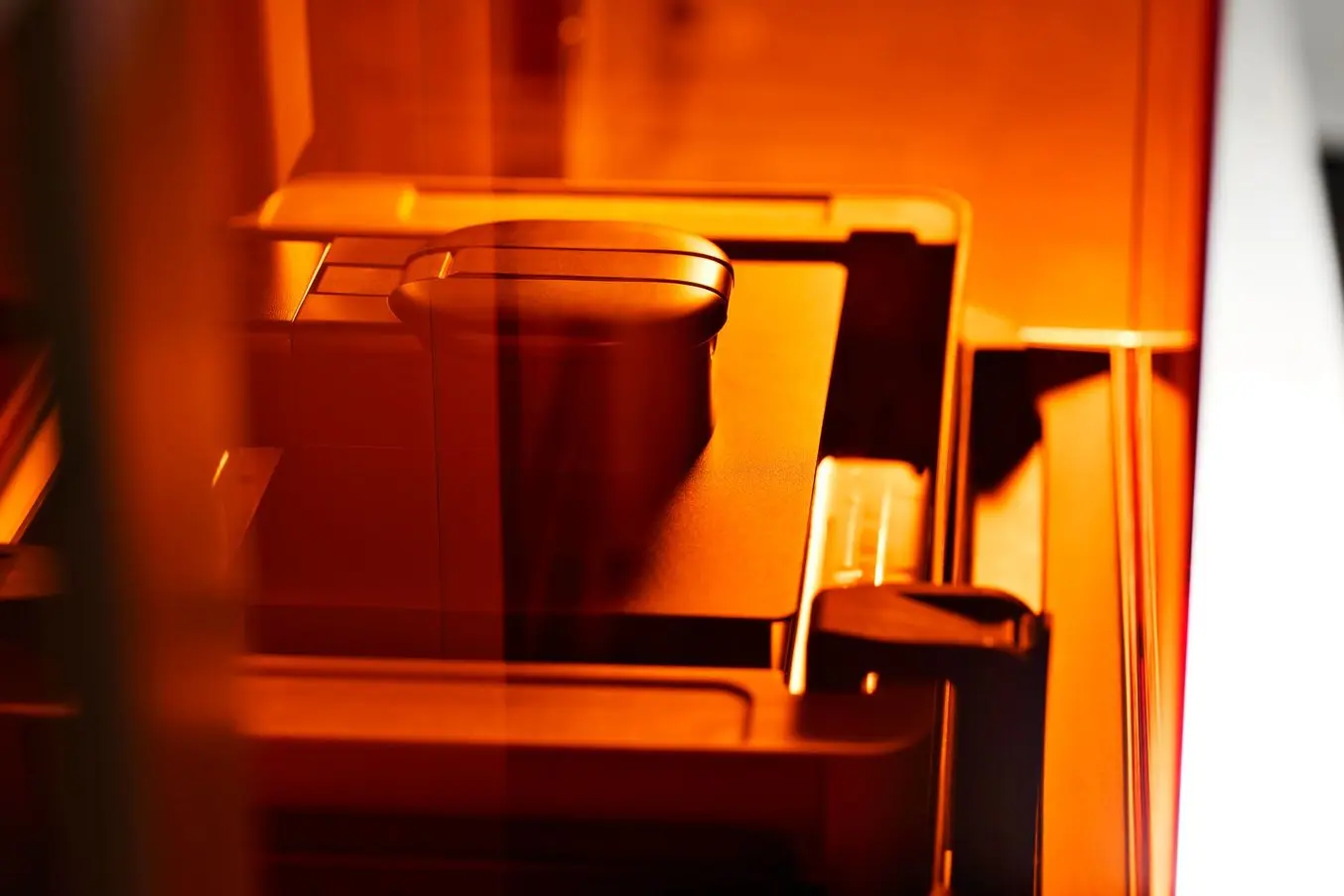
Product Demo: Form 4
See how Form 4 can enable new levels of productivity and innovation through its unmatched speed, accuracy, and reliability.
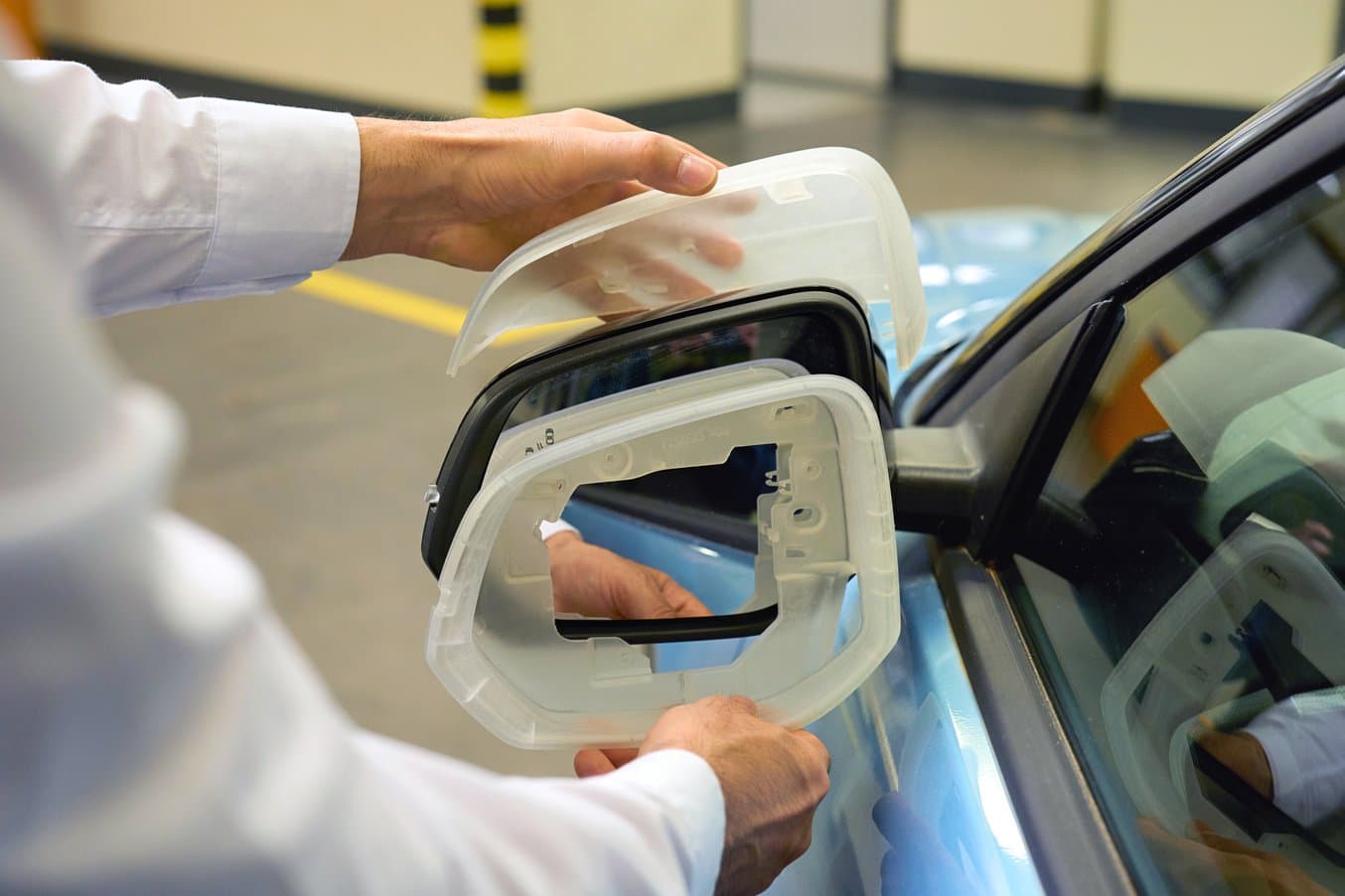
The team used SLA 3D printing to prototype many parts for the new Explorer, for example, the rearview mirror assembly.
For the new Explorer, the team leveraged SLA 3D printing to validate the design of many exterior and interior parts.
“The Form 3L enables us to print big parts, for example, exterior body parts for the vehicle. We printed this mirror cap to validate a design. 3D printing is suitable for this application because it's fast and we can have very good quality compared to mass production parts,” said Alves.
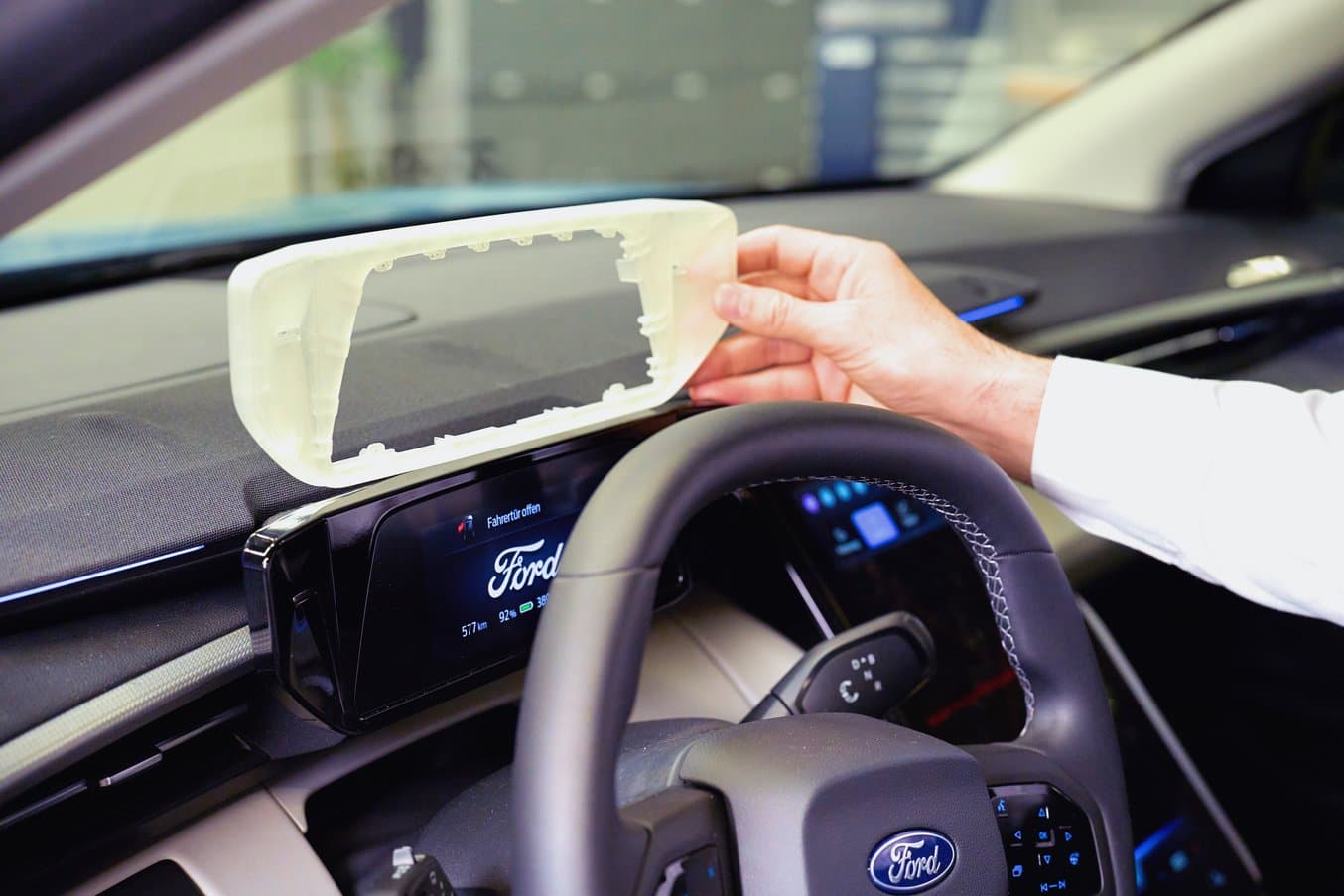
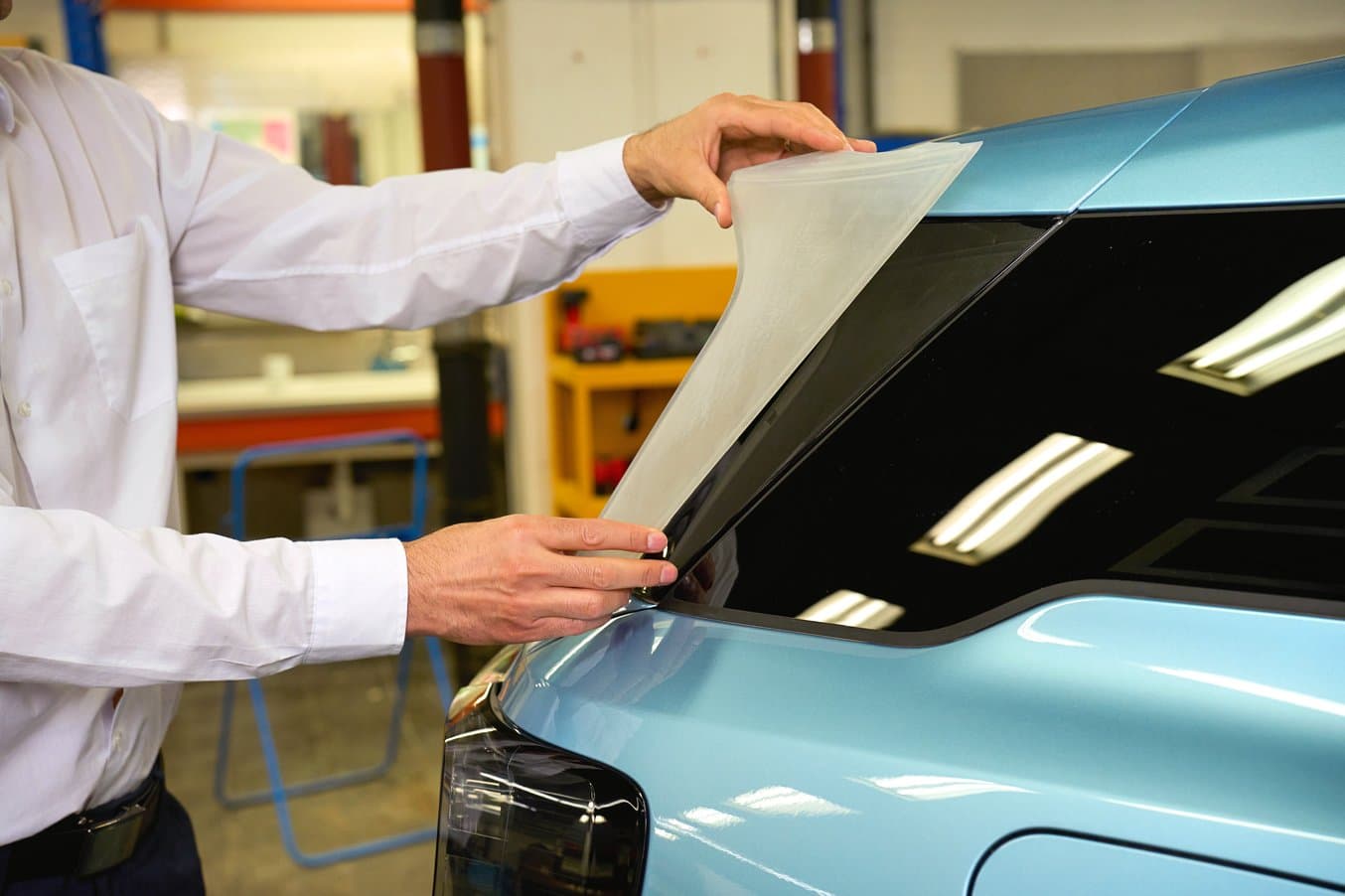
The large build volume of Form 3L enables the team to produce large prototypes in one piece.
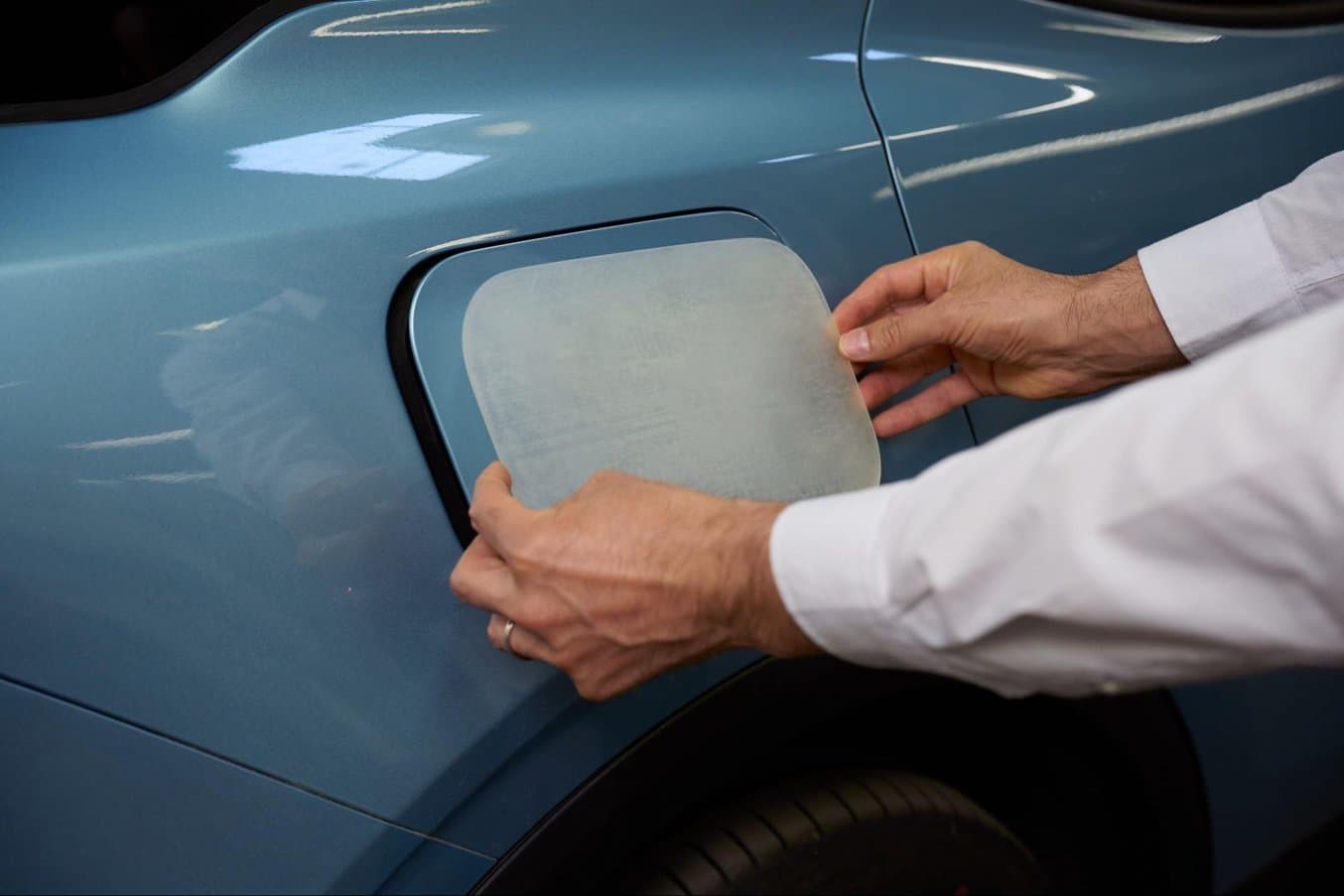
These parts were printed in Clear Resin and media blasted in Fuse Blast.
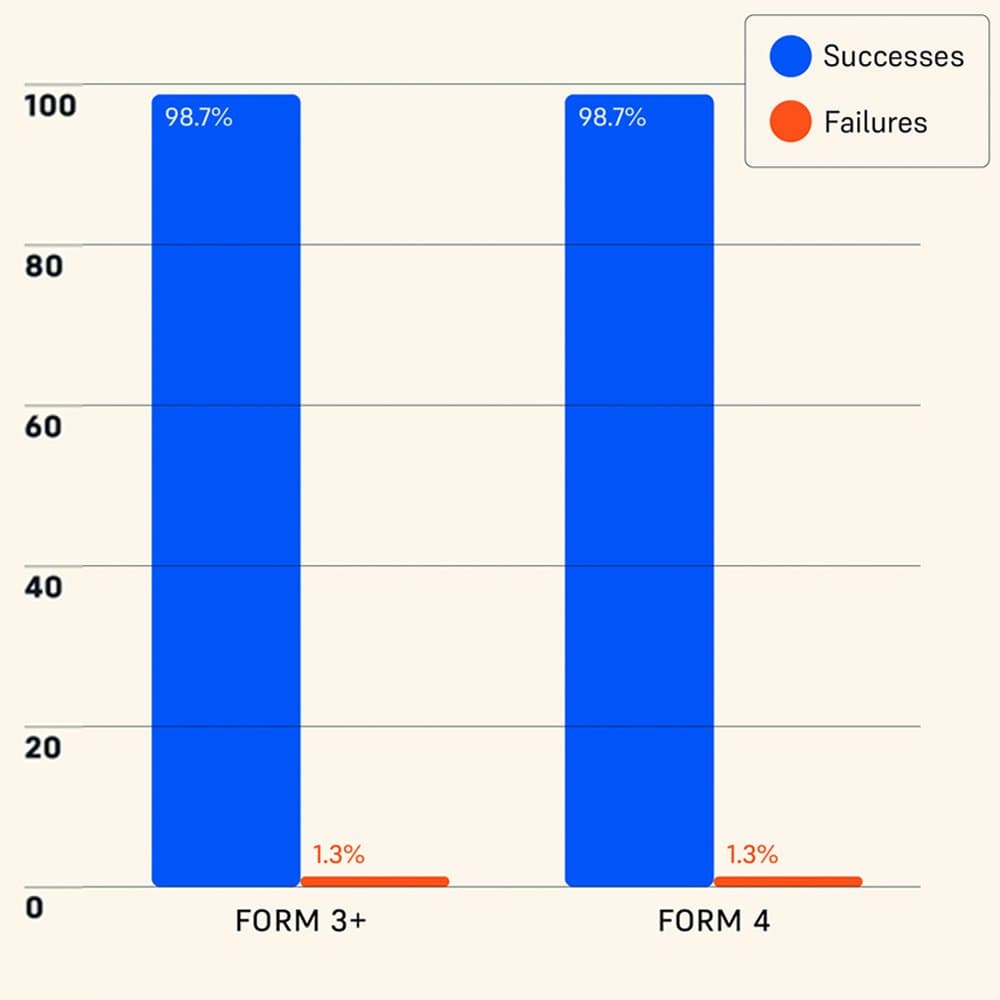
Independently Tested Reliability of Form 4 and Other Resin 3D Printers
Formlabs Form 4 was measured to have a 98.7% print success rate by an independent global leader in product testing. Read a complete description of the test methodology and see the results in our white paper.
Testing Mechanical Parts With SLS 3D Printing
The workshop also operates a large suite of SLS 3D printers that are used for testing mechanical parts.
“We are always trying to test and validate materials that are more similar to the ones used in mass production. The Fuse 1+ uses material PA-12 [nylon] that is very similar to injection molded mass production parts,” said Alves.
While the team also has large-format SLS 3D printers in-house that can print large body panels as well, they prefer to run the Fuse 1+ 30W for any part that fits into its build volume.
“The Fuse 1+ is much faster than the competitors. It's also very easy for our workers to operate the machine. At the end of the day, what really matters for us is that it’s very easy to deliver the parts faster.”
Bruno Alves, Additive Manufacturing Expert and Tooling Specialist, Ford
The team was also one of the beta testers for the Fuse Blast automated cleaning and polishing solution that completes the SLS workflow and simplifies post-processing.
“The Blast speeds up our process tremendously because the operator doesn't need to clean the parts manually now. They just put them inside the box and start the machine. Previously, they were doing it manually and it was really time-consuming. So in that time now the operators could be doing other things and we speed up the process,” said Alves.
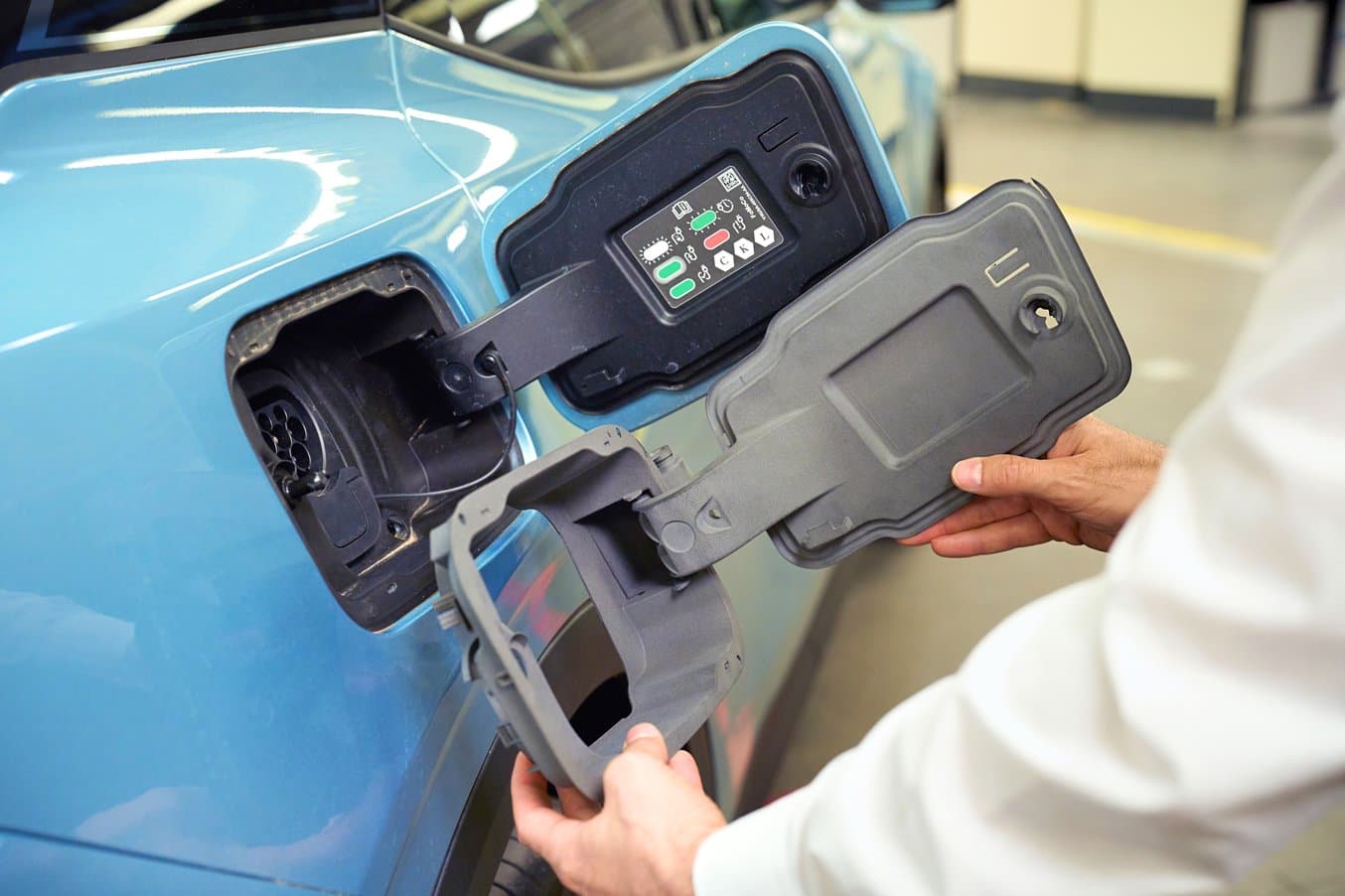
The charging port is a complex assembly that would have been impossible to prototype with any other method.
The self-supporting nature of SLS 3D printing makes it easier to produce complex designs. For the new Explorer, the team used the Fuse 1+ 30W to produce various mechanical parts and assemblies.
“For this charging cover, it was important to use SLS, based on the fact that we needed a functional part that would enable us to test the mechanisms. It's a really complex design that we are not able to produce in any other way. We cannot mill this part. We cannot use injection molding to produce just some samples. So the best way is to print in a material that we can test physically,” said Alves.
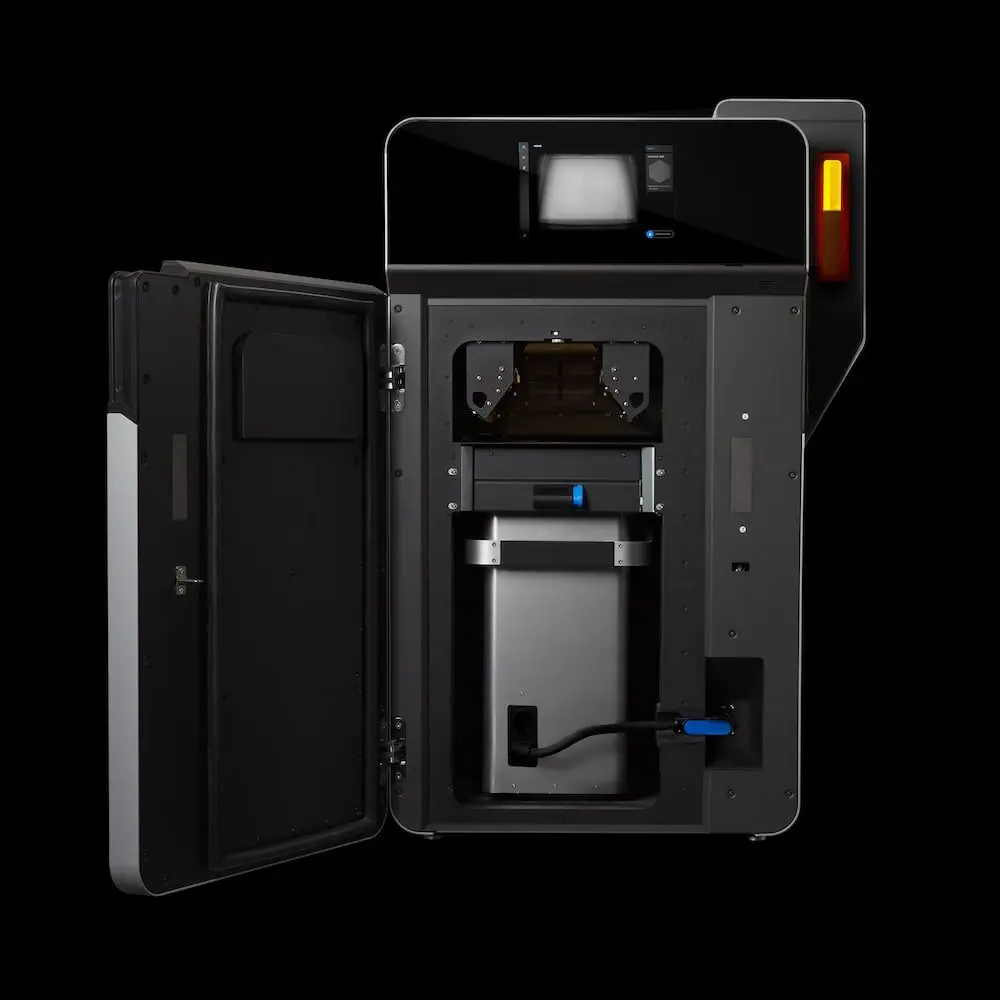
Rapid SLS Production of High Performance Parts with the New Fuse 1+ 30W
Watch our product demo for a walkthrough of the Fuse 1+ 30W and SLS 3D printing with Formlabs experts.
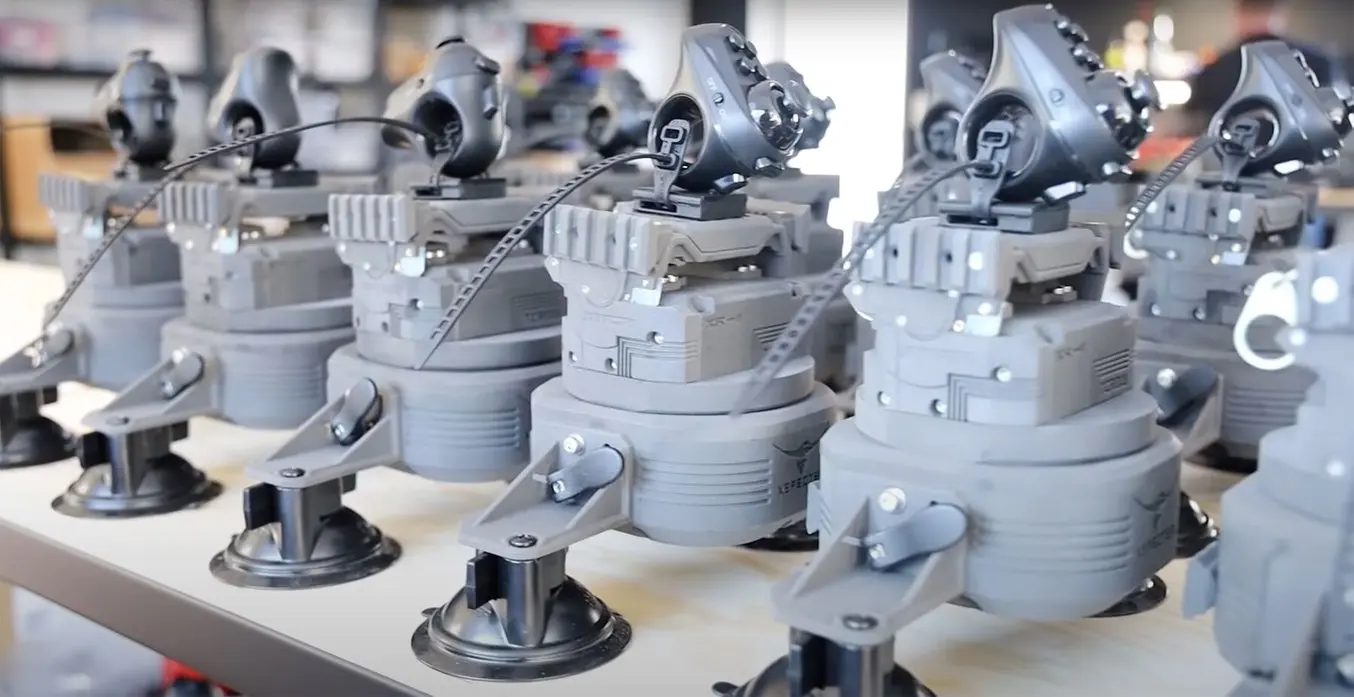
SLS for End-Use Production
3D printing for end-use production is not only possible, it's more affordable, agile, and scalable than ever with the Fuse SLS Ecosystem. Visit our SLS for Production page to compare production methods, learn about bulk powder pricing, and see production in action for 15 different manufacturers currently using the Fuse Series.
Injection Molding in House With 3D Printed Mold Inserts
Having diverse technologies in-house also enables the Rapid Technology Center to create hybrid workflows, for example, by combining traditional manufacturing processes with 3D printed rapid tooling.
Depending on the intended application, the team can select the most suitable production process and material, aiming to optimize the cost, speed, and overall efficiency of the workflow. In crash tests, for example, components must be constructed from the same material and process as in mass production. For plastic components, this typically involves injection molding, a process that traditionally requires costly and time-consuming metal tooling.
“We see a lot of potential using 3D printing inserts for injection molding based on the fact that we can iterate the design very fast. We print cavities in cores and then we can change them in the tool and inject the parts,” said Alves.
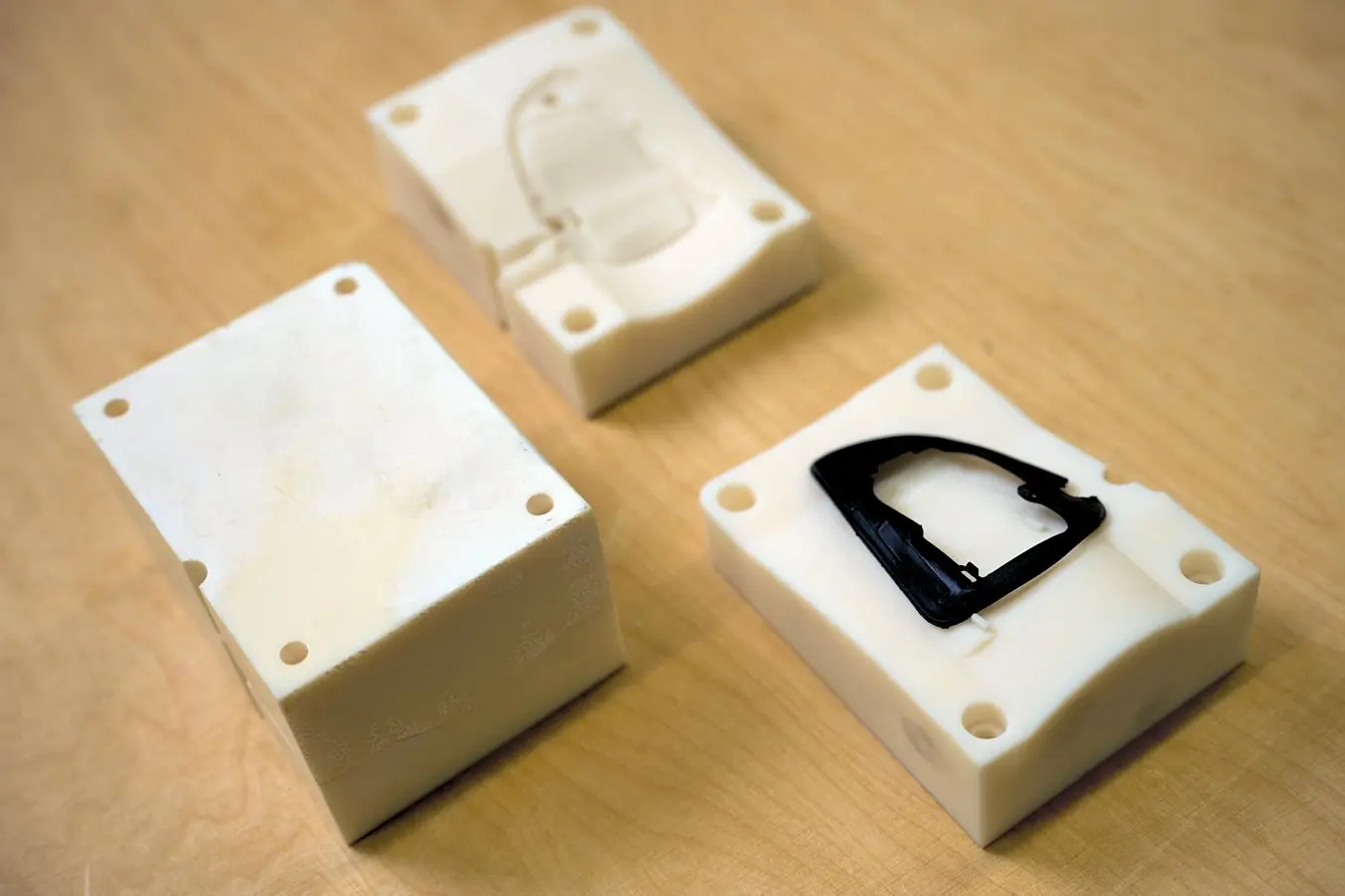
The team produced the injection molding inserts in Rigid 10K Resin on SLA printers.
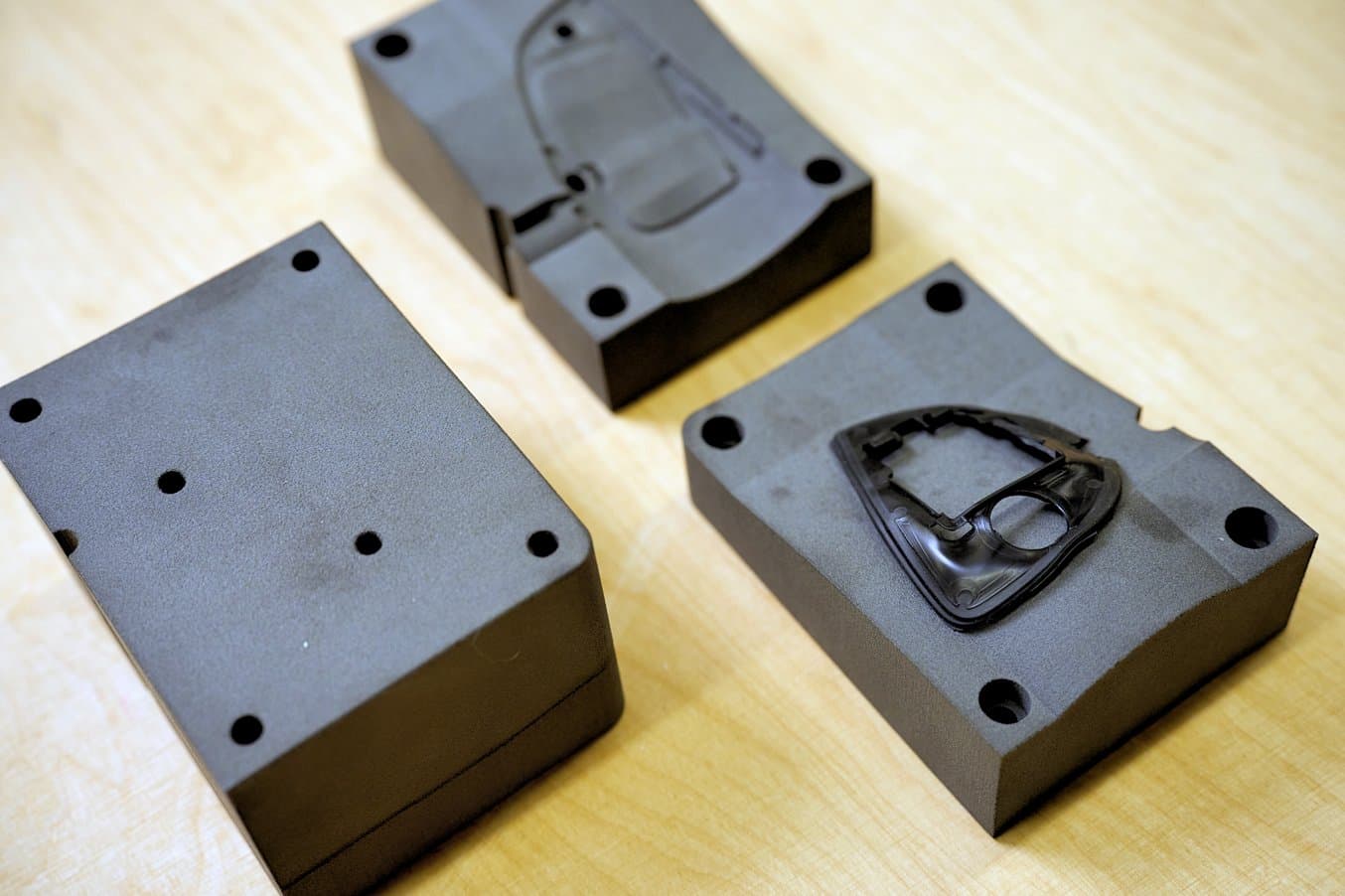
For the same application, they use used Nylon 12 Powder on SLS printers.
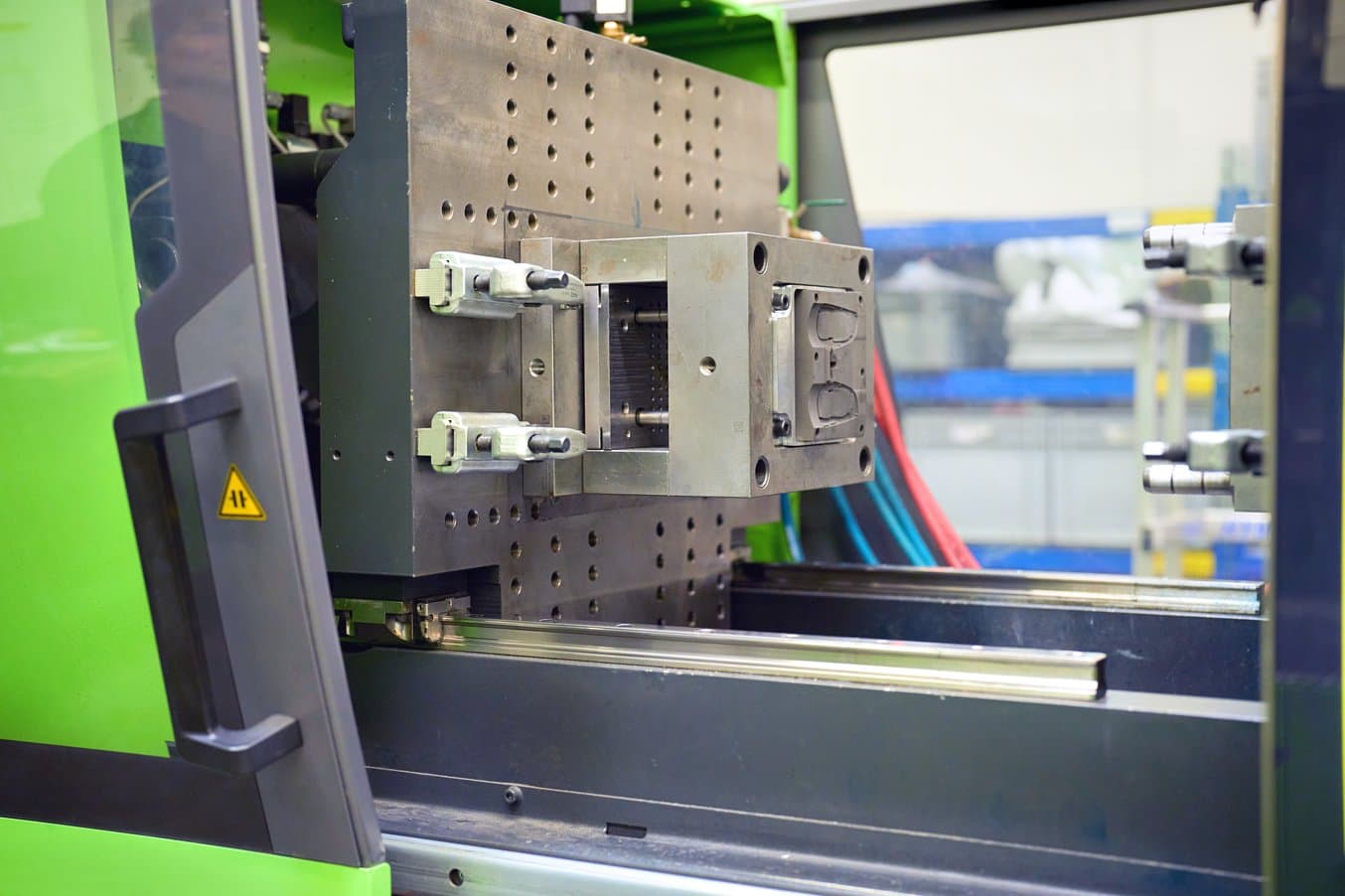
3D printing enables the team to produce inserts for molding different designs and rapid iterations quickly using their in-house industrial injection molding machine.
For the new Explorer, the team produced rubber components for the door handle assembly using 3D printed mold inserts in their in-house injection molding machine.
“This was a complex process because we are using several inserts and there are also several different designs that could have several iterations each. Normally, external injection molding will take maybe two or three months. Internally, using additive manufacturing, we can speed up the process to maybe two weeks, three weeks maximum. For this project, if we had to use external tools, it would have been much more time-consuming and we would not have been able to deliver the parts on time,” said Alves.
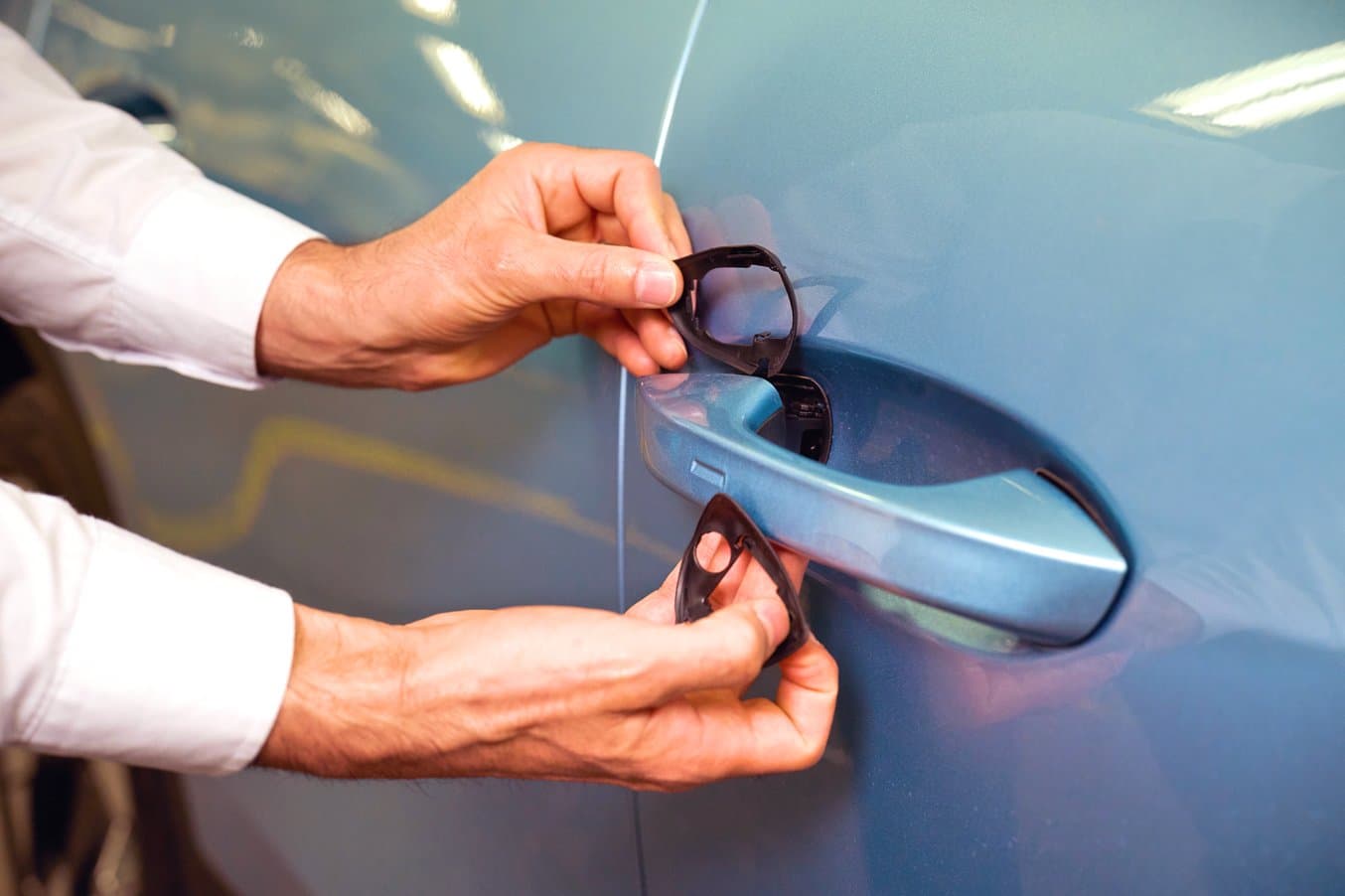
Each door handle design includes two of these rubber components for damping and insulation. For the four-door SUV, this means eight unique components for each design iteration.
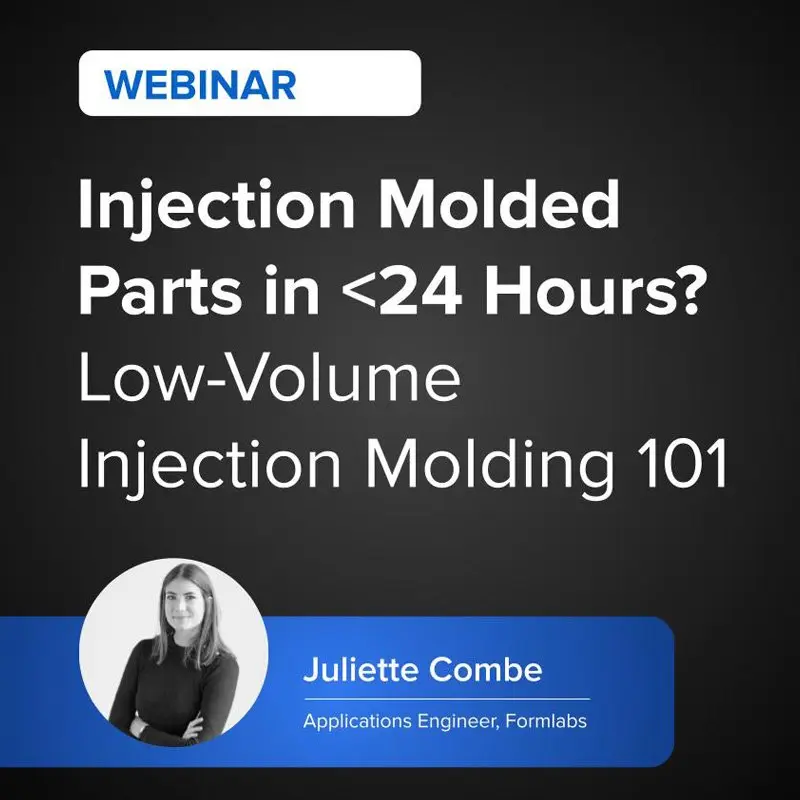
Injection Molded Parts in <24 Hours? Low-Volume Injection Molding 101
In this webinar, we'll show you how to use stereolithography (SLA) 3D printed molds in the injection molding process to lower costs, reduce lead times, and bring better products to market.
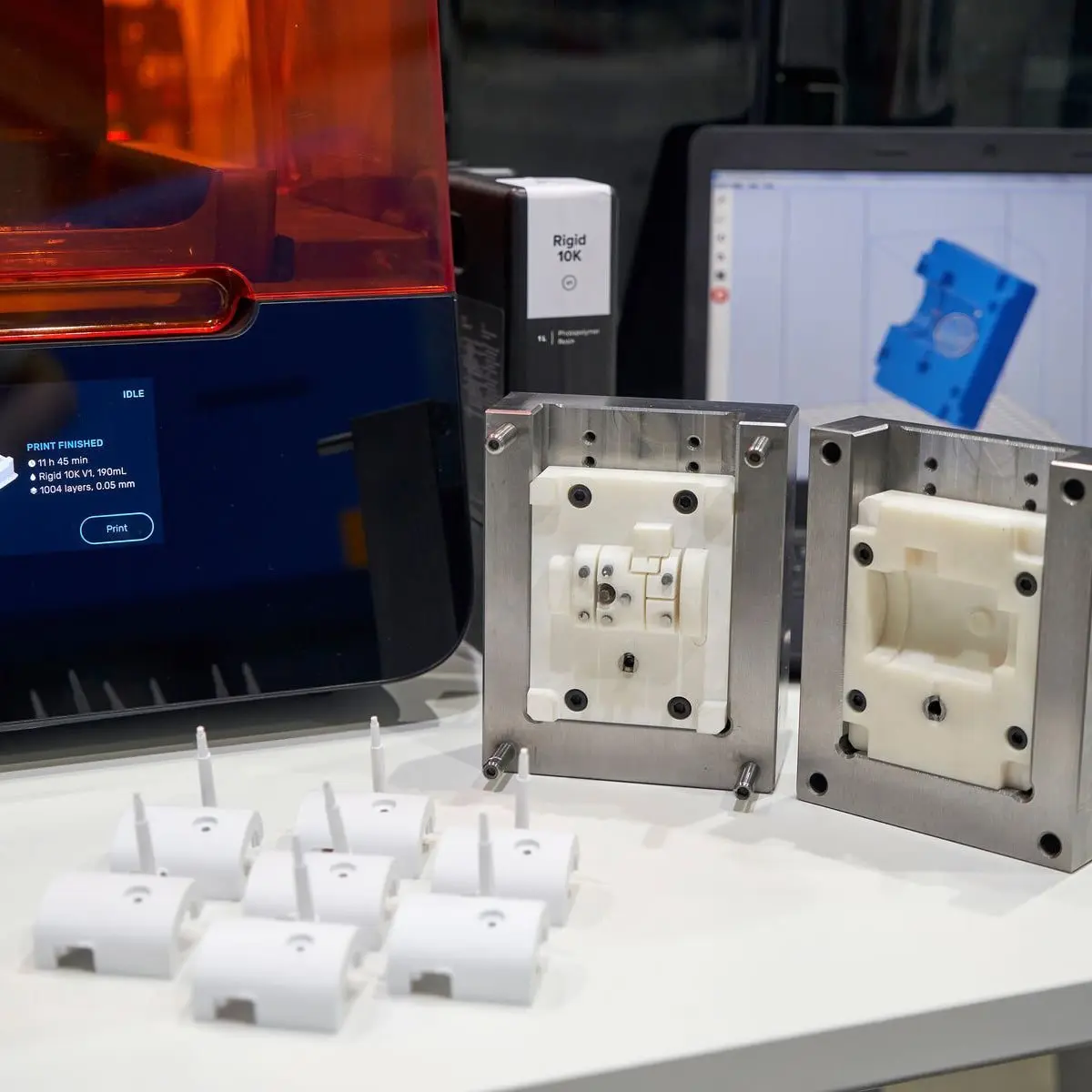
Low-Volume Rapid Injection Molding With 3D Printed Molds
Download our white paper for guidelines for using 3D printed molds in the injection molding process to lower costs and lead time and see real-life case studies with Braskem, Holimaker, and Novus Applications.
Accelerating Towards Electrification
Ford's commitment to an entirely electric lineup by 2030 sets an ambitious roadmap for the PD Merkenich facility. To hit the necessary milestones, the company will have to continue finding cutting-edge technologies and trying new, innovative workflows. Remaining competitive requires them to push the boundaries and integrate new materials, processes, and machinery like in-house tooling and 3D printing.
“Our competitors are speeding up the developing process. We need to speed up as well. So the solution is to test new materials, new processes, and new machines coming to market. Currently, if we didn’t have access to additive manufacturing, we would not be able to compete with the competitors, we would not be able to be so fast. 3D printing allows us to, in a shorter time, have the best product that we can offer for the clients,” said Alves.