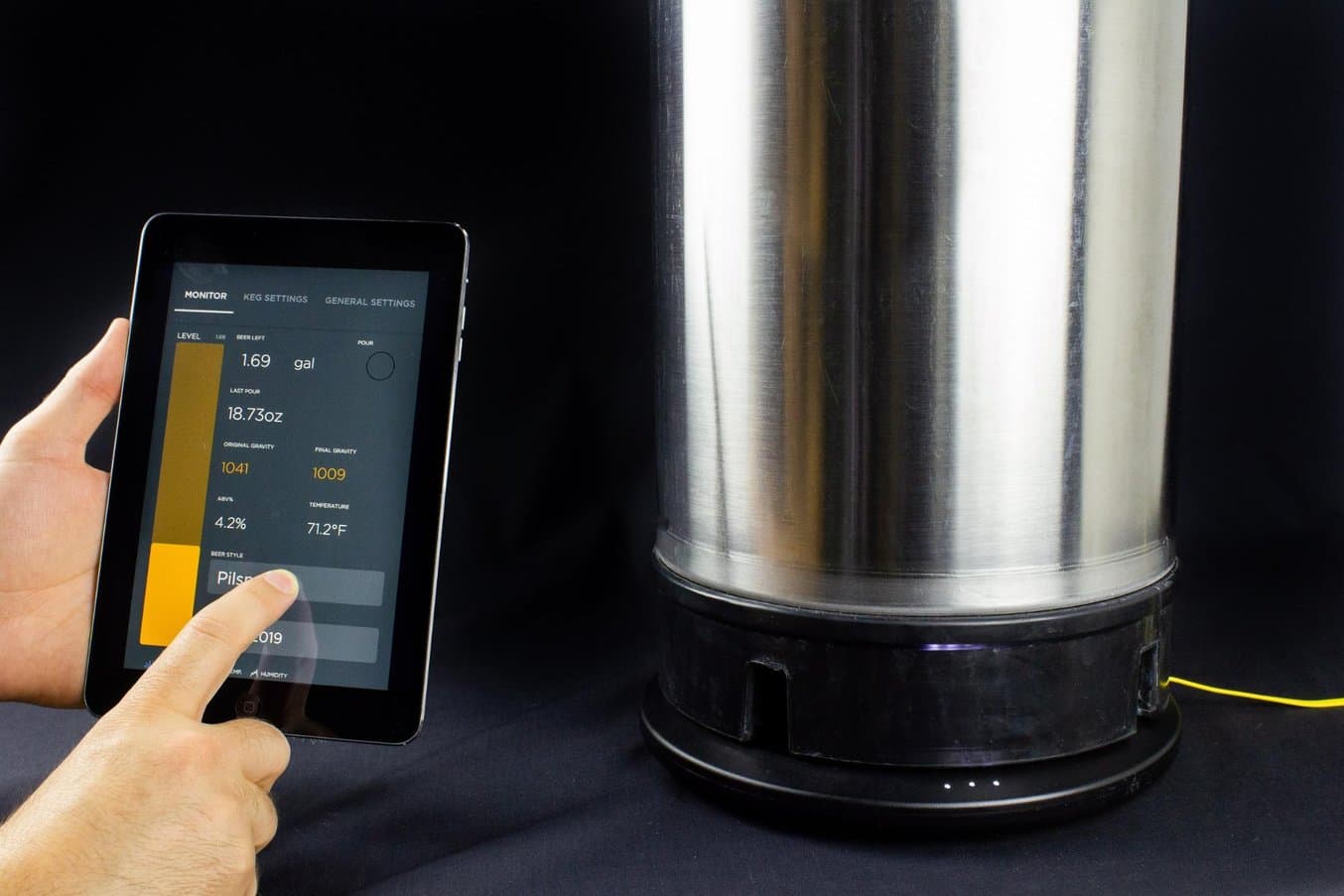
Plaato’s name might sound familiar to readers of our Blog; last year we shared their story about the development of a smart airlock for homebrewers that measures CO2 released during fermentation.
Since then, Michael Kononsky and his team has continued on their quest to empower brewers with data and launched a new product, Plaato Keg, a smart scale for monitoring beer kegs.
While the airlock required complex, optically clear parts, the development of their latest product brought about a host of new challenges. "We needed a waterproof device that will withstand a keg, which can be anywhere from 20 to 60 kilograms when they're full,” said Kononsky.
Read on to learn how Plaato’s team created more than 100 prototypes for beta testers worldwide and 3D printed new iterations both at their office and at their contract manufacturer to finalize the design for manufacturing (DFM) of their new product, which has already won two of the prestigious Red Dot Awards.
How to Empower Brewers With Data?
“We had a chat with one of our retailers, just fooling around a bit with some ideas and we said, ‘Okay, what about knowing how much you drink, knowing how much you have in your inventory. ‘Cause a lot of people have many different kegs and a kegerator, which is like a fridge for kegs. They have it in the basement, they don't know how much they have left or how old it is. So we made a couple of prototypes and our retailers loved it. They said they want to support that,” said Kononsky.
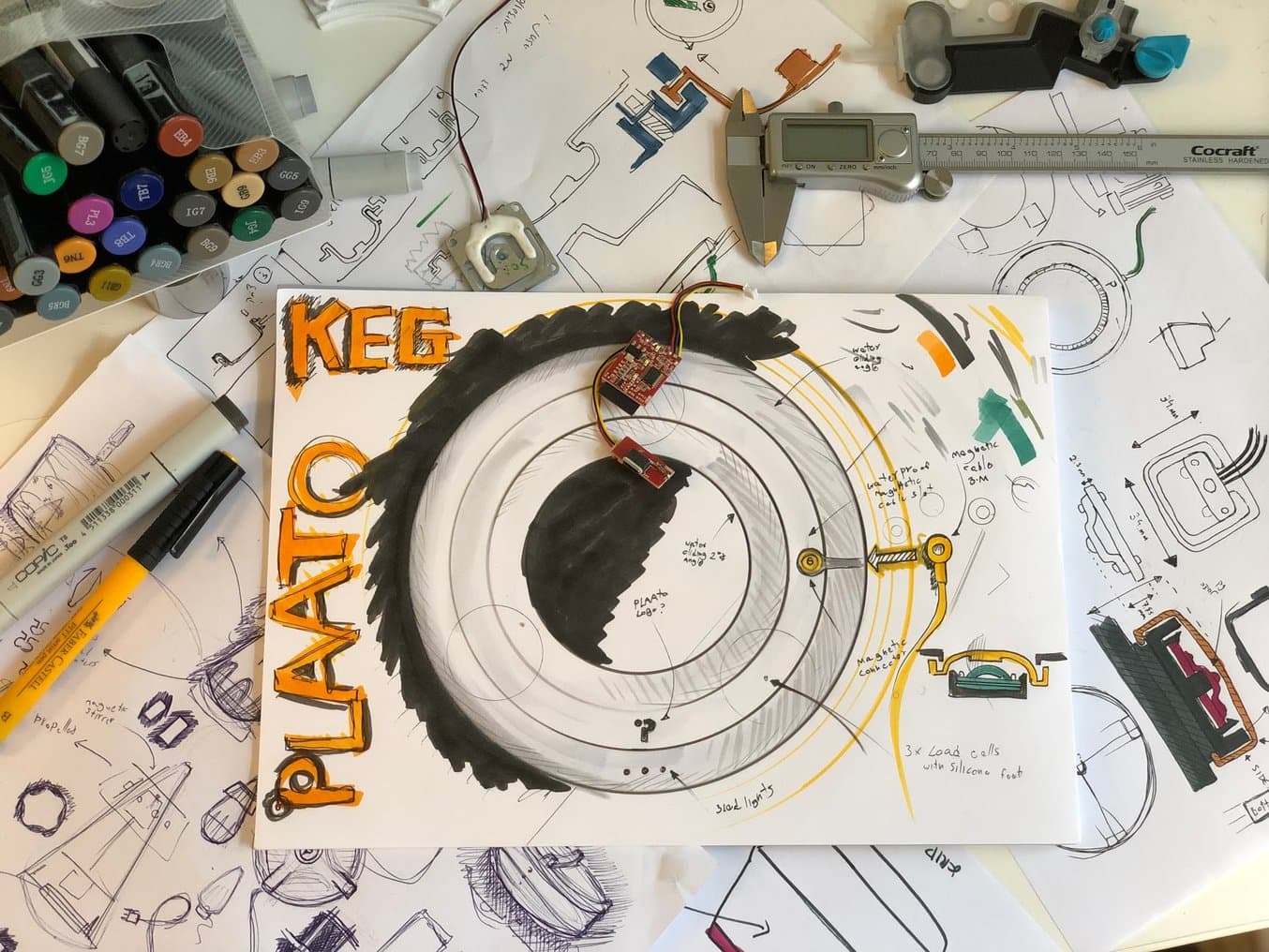
Design iterations of the Plaato Keg, including the connector and the load cells.
The current solutions on the market are all based on flow sensors that tend to get dirty and require users to install them and set up plumbing. Kononsky and his team thought that they could measure the volume in a more easy and clean way by converting weight and specific gravity.
"We just wanted to measure the beer without touching it and connecting it. Something stupid simple that the keg will just sit on, so you can just drop your keg on it and get the data in the cloud. Only in Norway, our tiny country, we estimate that there are around 14,000 kegerators and the average person has seven to eight kegs,” said Kononsky.
Developing and Testing a Resilient Product for Kegs
“We included the community in the development, we surveyed 300 of our existing airlock customers who showed interest in a product for kegs. We asked ‘What kind of kegs do you use? What are the problems? How do you use the kegs? Is it a wet environment? What kind of connectors and cable types can fit in your kegerator?’ We got pictures and measurements of thousands of different kegs, so we had to really optimize a product to that,” said Kononsky.
Kononsky and his team first started with laser cutting acrylic plates and linking them together, but they found it hard to match the shape of the kegs and the process was extremely time-consuming. Next, they used an FDM 3D printer with a nozzle custom-drilled to 1 mm to be able to churn out rough prototypes fast for quick market validation. Once they needed more sophisticated and detailed prototypes, they turned to stereolithography (SLA) 3D printing.
Plaato’s team used multiple techniques to create prototypes at different stages: laser-cut acrylic plates (clear) and FDM 3D printing (black, rough texture) at the beginning, and SLA 3D printing for detailed prototypes (white frame and the polished and painted black enclosure)
“We were making a thin product that had to be waterproof and be able survive an impact, so that was quite challenging. Rigid Resin was a game-changer. We could screw on all the sensors on it, we could make all the plastic bosses, and we could waterproof it. It gave us the detail level we needed so we could also communicate that with our manufacturers,” said Kononsky.
Rigid Resin was a game-changer.
Michael Kononsky, Plaato co-founder
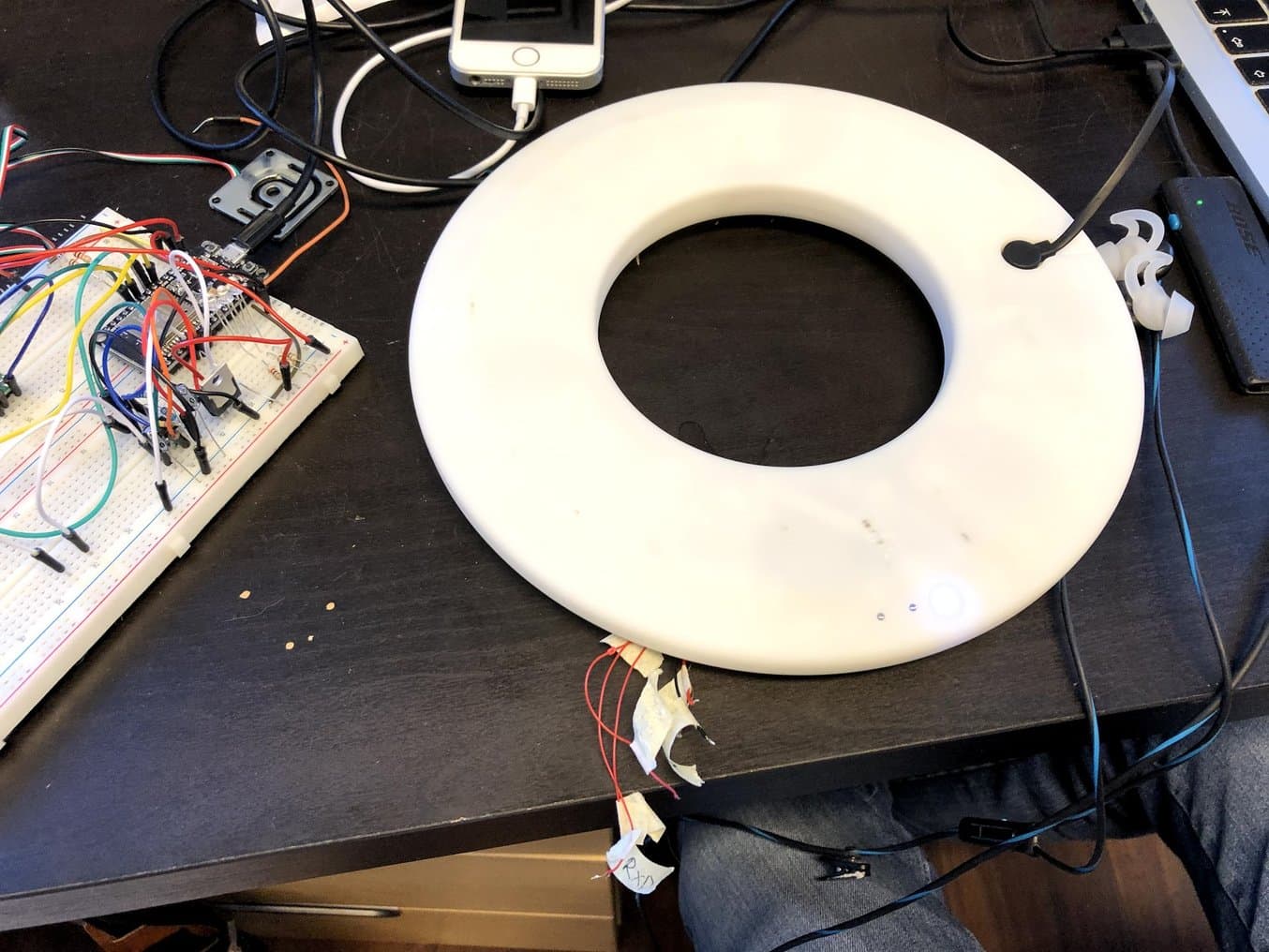
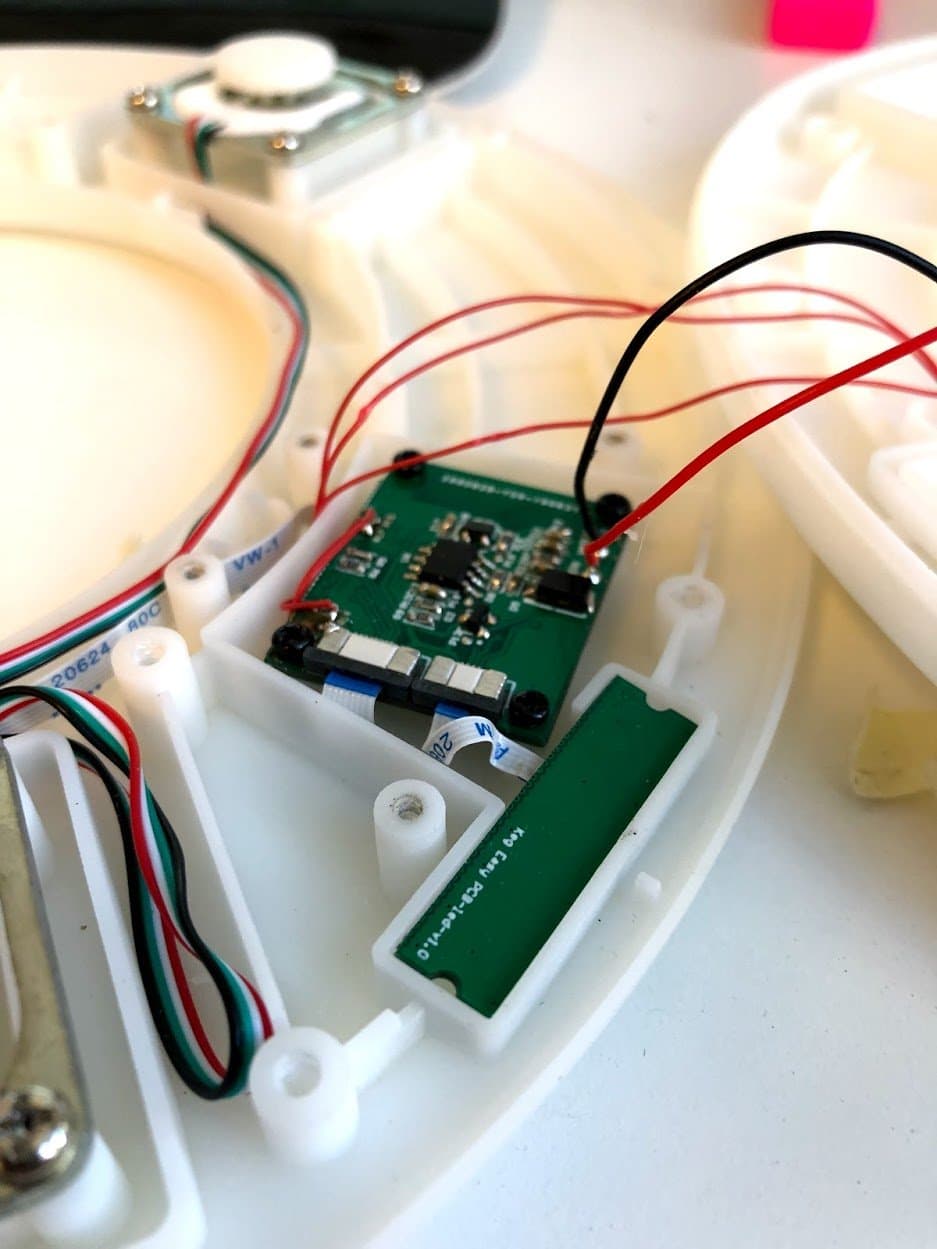
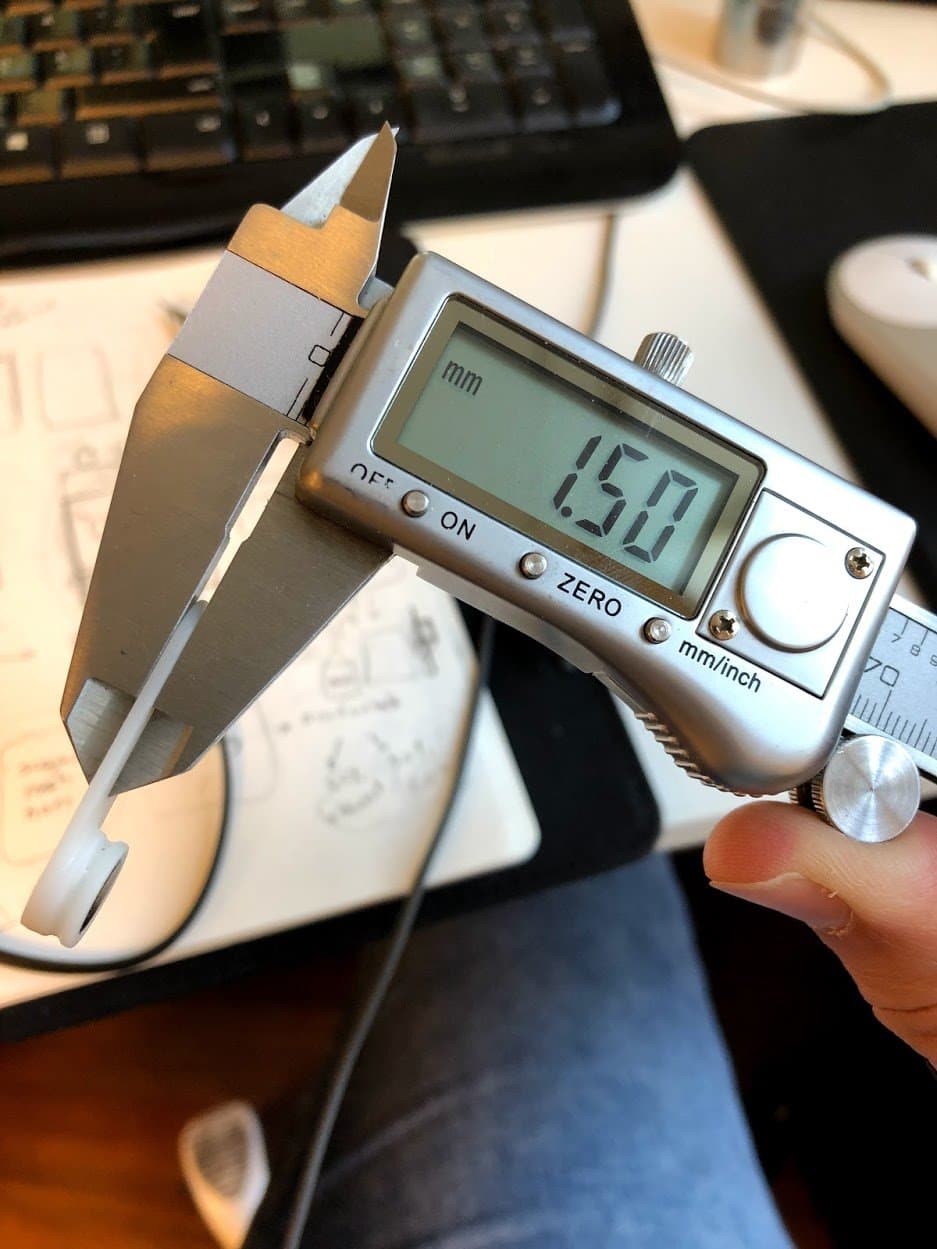
The engineers used Rigid Resin to create detailed prototypes with thin walls that included all the features of the final injection-molded design.
The PCBs, sensors, and other electronics are hosted in compartments that are screwed to the enclosure. These are not waterproof, so the team had to create custom gaskets and jackets around them are both anti-slip and protective. They had to be tight and have good tolerances to provide compression and waterproofing.
“We used Elastic Resin for fast prototyping. We just played with the thickness. It's very nice to get a batch of 20 different gasket types on a single tray, so one that is 1.1 millimeter, 1.2, 1.4, and so on. I can just test them all out and that's it. It saves a lot of money,” said Kononsky.
Altogether, Plaato’s team created about 35-40 prototypes on their Formlabs SLA 3D printer. They split the models into multiple smaller parts to fit them all into a single build that can be printed in nine hours.
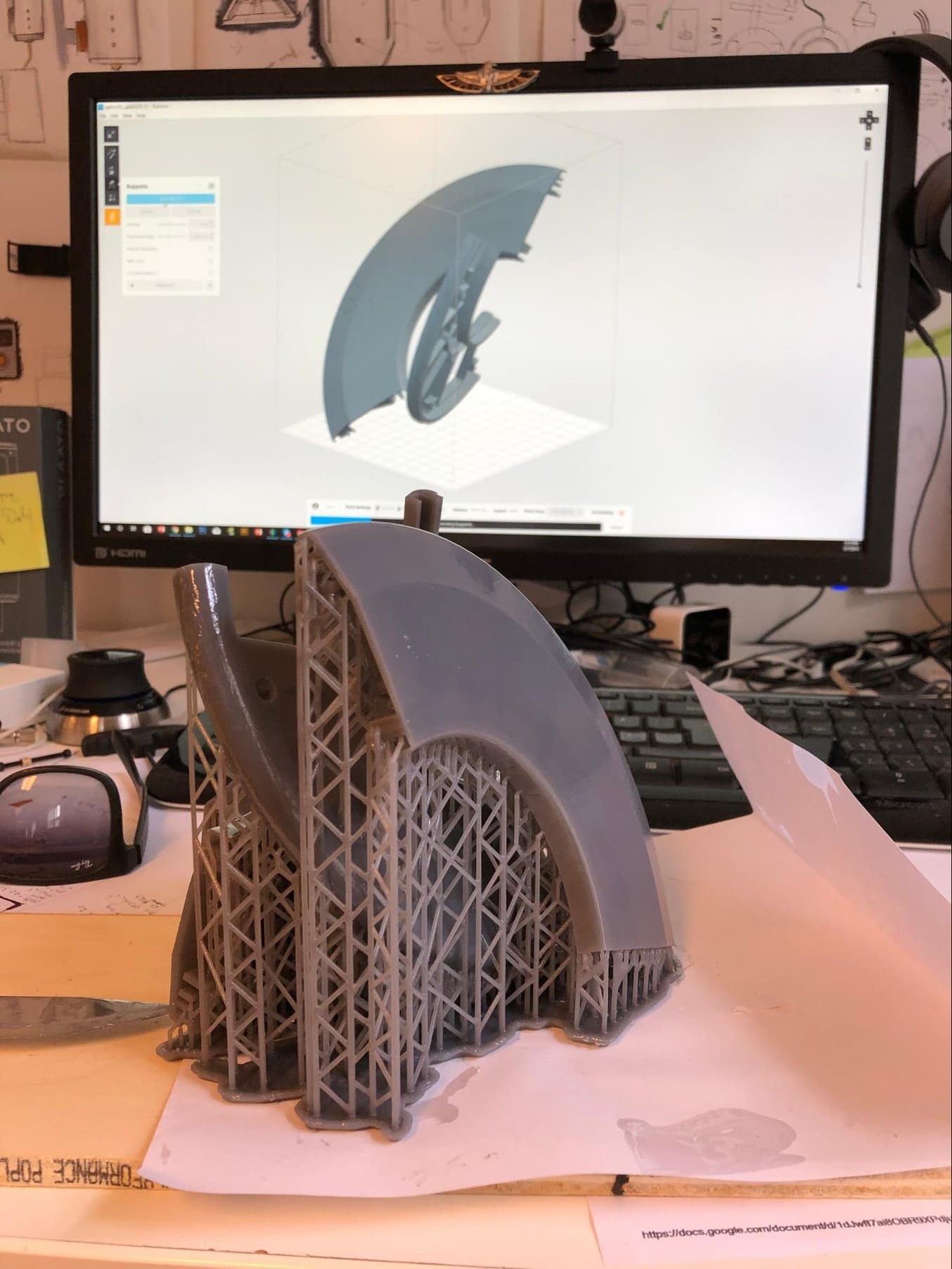
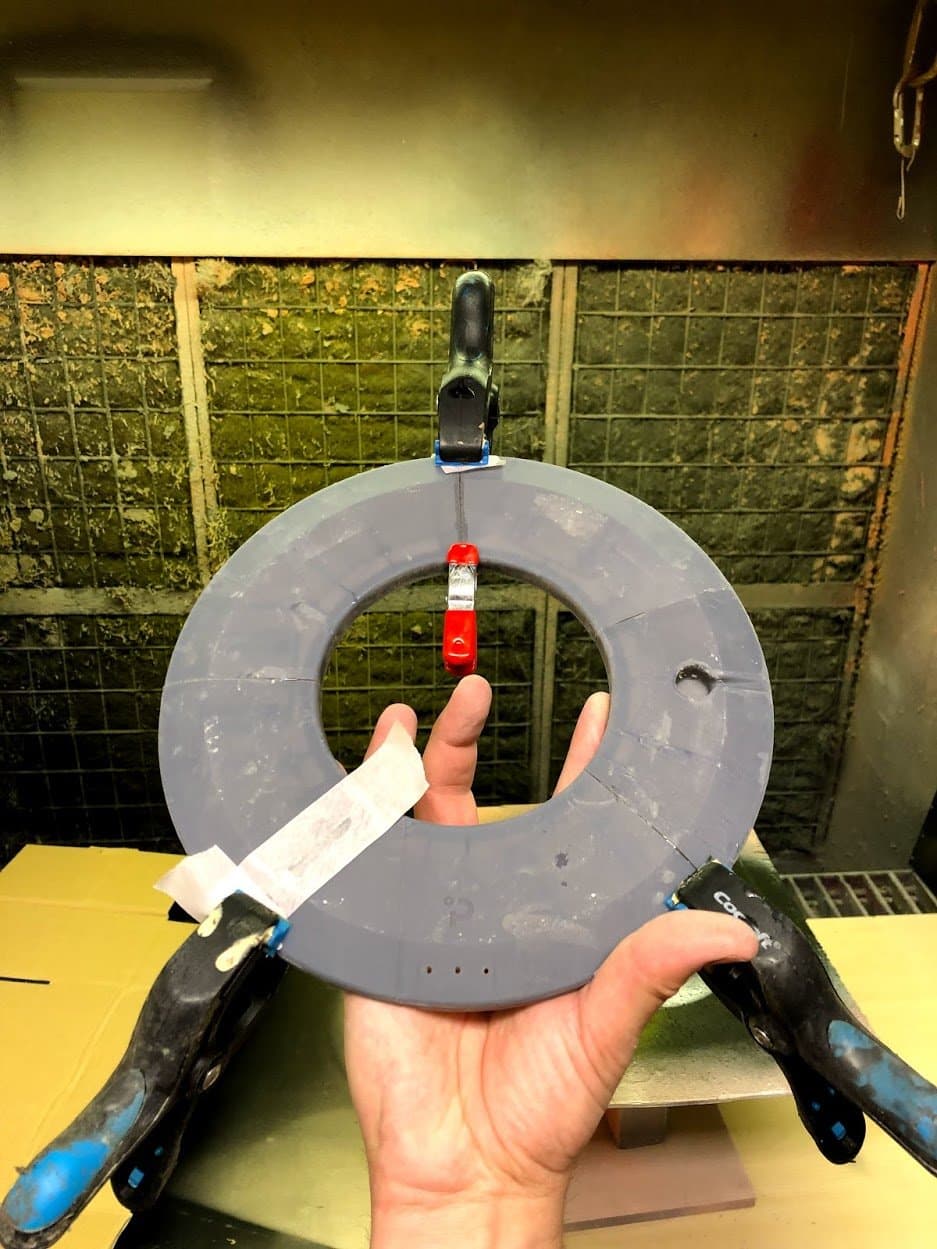
Plaato’s team split the models into multiple smaller parts to fit them into a single build.
“The cool thing about this printer is that I can leave it working overnight, so the last thing I'm doing before I leave for home is that I set up a print. When I come back in the morning, it has finished. I wash it, cure it, spend maybe one hour assembling it all together with the electronics and everything, and before lunch, we have a new iteration,” said Kononsky.
The team involved their community in the prototyping stages as well. From the first MVP prototypes to the ones that resembled the final product, they shipped around 100 prototypes to customers in the US, South America, Asia, Australia, Europe, and the Middle East. This provided valuable feedback that they could build into consecutive iterations, for example, the ideas for a warning system that tells users if they have a leak on the keg and a temperature sensor that alerts if the thermostat is on fire, which happens sometimes with self-made kegerators.
The 3D printed prototypes also helped to validate that Plaato’s design would be resilient enough to cope with the environment of the kegs.
“We dropped it like in a crash test, from 10 centimeters, 20, 30, 40. We dropped it from one meter as well and it survived it all. We knew, if that works with resin, then for sure it will work when injection molded, because we went with an impact-resistant polycarbonate, the same thing you use to make shields for the police. We actually managed to 3D print something that can stay over 48 hours under one meter of water and it will be completely perfect. That saved a lot of development time and a lot of very expensive solutions that we would have used if we went old school development,” said Kononsky.
Design for Manufacturing by 3D Printing Iterations at Home and in China
Kononsky and his team had a bit easier job this time, as they picked the contract manufacturer of the airlock to produce the new product as well. By using SLA 3D printing both at their office and at the contract manufacturer, they managed to speed up the validation process and ramp up manufacturing quickly.
“I like to kind of make 90-95% of the design before we contract with the manufacturer. I want to leave them some freedom because they know their machinery and they know their capabilities. We trust our partner to be professional, so I didn't want to lock them into very small details that might complicate the project for no good reason,” said Kononsky.
“Our manufacturing partner got himself a Form 2 as well, so it was very easy to communicate. As they have the same printer as we have, I could send them the files that I sliced myself for printing. Then I got their draft back, I printed it, I tested it, and it was great. That was a very interesting way of working, it was very good to develop it together.
Many companies just ship parts back and forth from their contract manufacturer overseas, but that makes locking these final details a painfully slow process.
“When I was a consultant that's what we did, but it’d take you four days back and forth [with expedited shipping]. Those are precious days, so you're relying more on screenshots and PowerPoints, but then you have some communication gaps. They could also just mill the whole parts, but it's not easy and we cannot match expectations in the same way. [3D printing] makes things a lot easier, you can just make the exact file you want. Especially some radiuses and compression levels are very difficult to communicate without it,” said Kononsky.
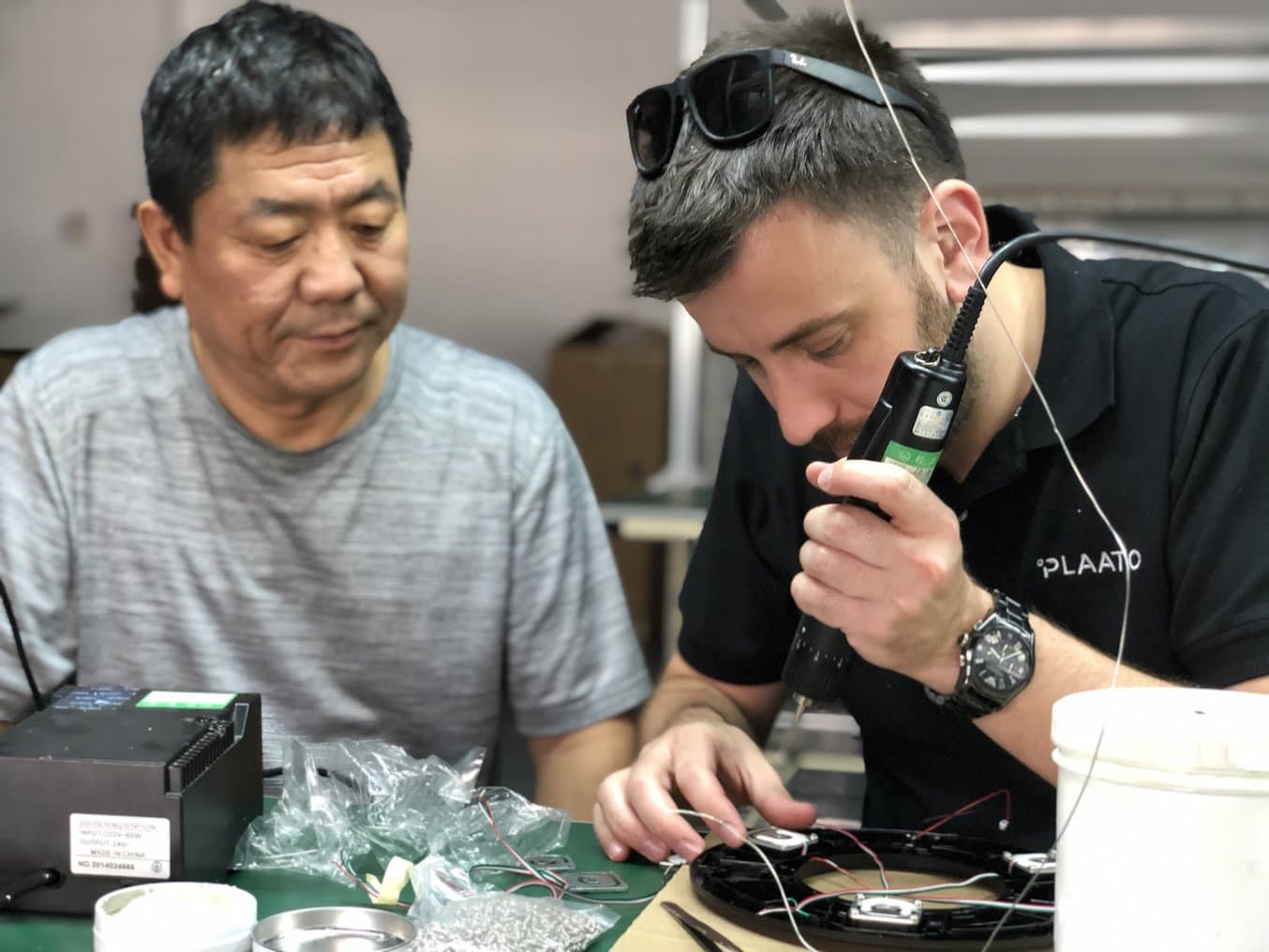
Using the 3D printer at their contract manufacturer, they also printed jigs and fixtures for the assembly line.
Having a 3D printer at their contract manufacturer also helped expedite tooling for the production line.
“We also printed a lot of the jigs for the assembly line for pushing some components in, securing them, [ensuring the correct] placements, and others. We printed all of those with the printer that we brought with us from the office of our manufacturer to the factory when my colleague and I went down there to the production line,” said Kononsky.
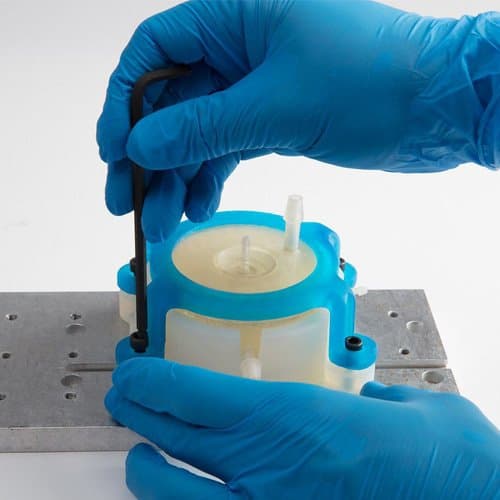
Designing Jigs & Fixtures with 3D Printing
Download our white paper for a comprehensive look at jig and fixture design basics, best practices for designing 3D printed jigs and fixtures, and tips for validating printed fixtures.
From a Successful Launch to New Applications
As a small company wary of making a huge gamble before entering the market, they turned to crowdfunding again and raised more than $150,000 through a campaign on Kickstarter.
The preorders of the backers have now been fulfilled and luckily for their industry, the COVID-19 pandemic has only encouraged more people to brew at home, so they quickly sold out of their first batch of the new product.
As a testimony to the innovative new design, the Plaato Keg has also won Red Dot Awards in two categories, for smart products, and for industrial design.
Some customers also found creative applications for the product. “We found out that many of the people who bought it were bars and all sorts of service providers that provide kegs and taps for office spaces. We have a company that owns 150 points of sale cold brew coffee taps. They said ‘Yeah, I just manage all the inventory from there. I'm not just driving around and I'm not waiting for people to call me when they’re out of coffee or beer on tap, I just know in advance, I can plan my day.’ And that's very cool because this kind of service was not there. They can give better service for their clients,” said Kononsky.
Explore Formlabs’ latest SLA 3D printer, the Form 3, and our growing collection of engineering resins to solve complex challenges in product development. Curious to see the quality firsthand?