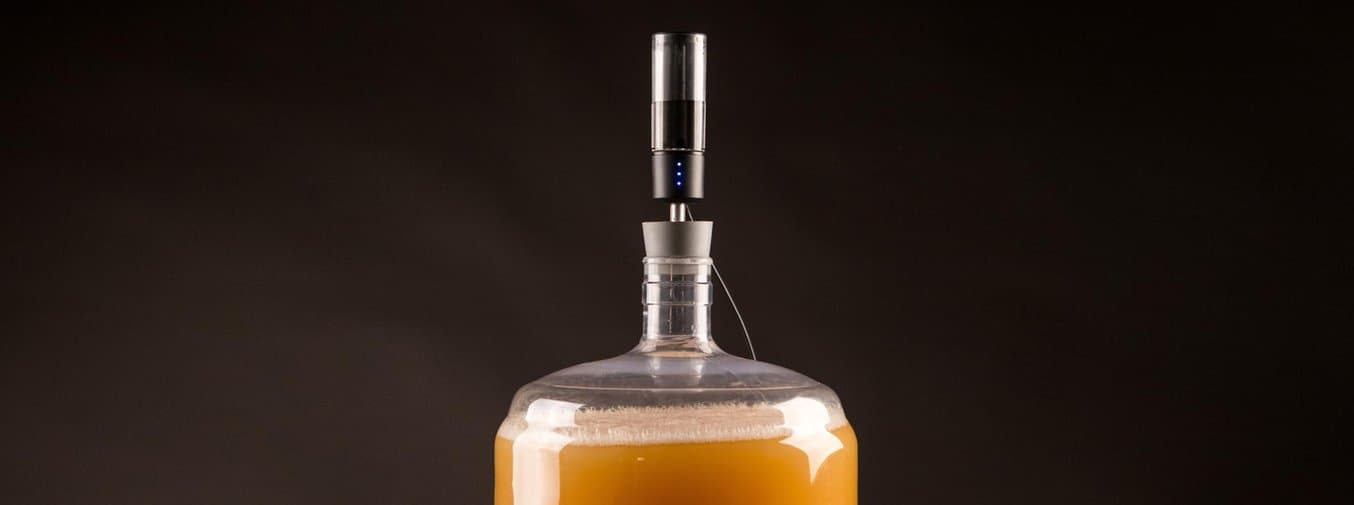
Michael Kononsky, a product designer by trade, and Pål Ingebrigtsen, an engineer, met at a startup event in Norway in 2015. Working in their first jobs just after graduation, both were thirsty for brewing something new.
Eager hobbyist beer brewers themselves, the duo saw a business opportunity in the worldwide emergence of craft breweries and the increasing popularity of homebrewing—today in the US alone there are already over 1 million homebrewers.
More than 1,000 prototypes later, Plaato, the first brewing product that measures CO2 released during fermentation to empower brewers with data, was born.
In this post, Kononsky shares how the Plaato team developed a novel design that won the prestigious Red Dot Award, prototyped optically clear parts with 3D printing, and set up production in Asia.
Empowering Homebrewers With Data
The craft of beer brewing goes back thousands of years. Over time, industrial breweries have thoroughly refined the process to fully leverage modern technology to analyze and control every aspect of brewing. But homebrewing is still a hit-or-miss hobby for most, with often varying results.
Kononsky and Ingebrigtsen wondered if they could couple their skills and new technology to make the greatest product ever for homebrewers.
“We thought that it’d be great to gather data from beer brewing, because the fermentation process, where the magic really happens, is a complete mystery box. You close the bucket for two weeks and then you don't know what's going on inside. You don't know if it's good, if it's bad, if it's too warm or too cold,” Kononsky said.
“Then you open it and say, ‘oh damn, this is infected,’ or ‘oh yeah, that was great.’ But then, you never manage to recreate it and you can’t share the recipe with a friend because you don't really have the proper tools to do that.”
Kononsky discovered research from the 1980s that proved it’s possible to calculate the specific gravity, fermentation activity, and alcohol percentage in the liquid from the CO2 released during fermentation. He figured that if they could count the “bubbles” and estimate their volume with machine learning, they could transform this biological data into digital data and see if the fermentation is too aggressive or if it’s too slow, and also know how different types of sugars and yeasts affect the fermentation curve.
“Basically, we monitor the beer like you monitor a person in the hospital. It's not making a better beer for you, but it makes you a better brewer because it's a tool that empowers you with information. After every batch you make, you have a report showing you what was bad or what was good and that will allow you to recreate or iterate on the results, and share it with your peers to discuss and analyze it,” Kononsky said.
Prototyping an Optically Clear Airlock
Kononsky and Ingebrigtsen looked at many different methods and even found perfect flow meters that can measure the CO2, but the brewing environment brought up unique challenges.
“[For brewing], a product should withstand spillage, corrosion, and accidental dropping. You have to have everything cleaned and sanitized, as you’re always risking contamination and infection. We had to develop a method that monitors fermentation activity without putting any sensors inside the brew because it's so sensitive to invasive measurements. Basically, we needed to create a product that measures the activity without touching the beer,” Kononsky said.
To answer these unique parameters, the entrepreneurs decided to develop an optically clear airlock.

There are only a few ways to prototype optically clear parts; Kononsky tried CNC machining and outsourcing to service providers, but found both methods slow and expensive. “We calculated that for the price of 3-4 iterations, we can buy a new Formlabs 3D printer,” said Kononsky.
Read our tutorial that walks through finishing methods to create transparent 3D printed parts.

Having a 3D printer at their desk allowed the team to test multiple iterations a day, at low cost.
“We printed all day every day until we managed to get something right because the threshold of trying something new was so low. The unit cost for these clear parts is almost insignificant. It added a lot of value, it's like having another designer in the team.” said Kononsky.
“I think we had around 1,000 different clear part prototypes—we produced six prototypes a day, then iterated the design in Solidworks based on the conclusions, while having a new part already printing. We measured the bubbles, measured the flow, tweaked the parameters, and used some machine learning and empirical learning. Working so closely with the parts, you actually understand the material and its properties.”
Kononsky and Ingebrigtsen required highly accurate prototypes that can be taken apart, cleaned, washed, and reassembled to click exactly at the same spot so that the sensitive sensor would give the correct reading in their next test.
“It's the same working principle like a pen, with a cup that you click on and that stays at the exact same spot. We managed to solve it with a combination of the Clear Resin for the clear part, and the Tough Resin for the bottom. Clear parts are very rigid, while the Tough bottom parts had some flexibility to allow for a tiny groove, some ribs, and a double-click ring. We managed to simulate the final product’s behavior; it worked 100% correctly just like the plastic [injection] molded part,” said Kononsky.
Download our white paper for a breakdown of how to measure and apply tolerances for each type of engineering fit, with specific recommendations for Formlabs Tough Resin and Durable Resin. The resource also includes links to downloadable test models and suggestions for lubricants, bonded components, and machining.
The Benchmark for Production

After a successful crowdfunding campaign to fund the expensive molds and tooling, the team continued with ramping up production in Asia, where they used the prototype as a reference point.
“Basically it was our pre-golden sample. With injection molding, you have to account for some shrinkage that you don't have with 3D printing. Also, the surface tension and the plastic properties were a bit different. But we had a benchmark in our hands, so we could work together with the engineers and iterated the mold a couple of times to reach the same tolerances that we got from the 3D printer. We just had to replicate the properties based on the printed prototype, not the other way around. So it was not a black hole that we were guessing and trying, we really had the benchmark that worked as an anchor,” said Kononsky.

From Homebrewing to Microbreweries
The entrepreneurs recently received the prestigious Red Dot Award as a recognition for the “aesthetically sophisticated design of Plaato that brings the airlock traditionally used in beer brewing into the digital age.”

With 4,000 units already shipped, Kononsky and Ingebrigtsen are now focusing on optimizing production to make it more cost-effective and expanding the product line with a new commercial version or their airlock for small- to medium-scale breweries that will meet the demand of higher volume fermentation.
Accelerate Product Development With the Form 2
“I'm telling my team all the time, I have no idea what I would have done without the Form 2 printer. I seriously think we wouldn't have managed to understand even our production abilities. We would have a big bulky part with some window made of glass, nothing close to these proportions and size,” said Kononsky.
Rapid prototyping in-house on the Form 2 has helped thousands of engineers and designers solve complex problems, saving time and costs at every stage of product development.
Explore the Form 2 and Formlabs’ collection of engineering resins, and request a free 3D printed sample part to see our materials firsthand.