Formlabs’ New Form 4: Unmatched Speed, Accuracy, and Reliability to Redefine 3D Printing
Formlabs is proud to announce Form 4, our next-generation resin 3D printer that redefines the industry standard for speed, accuracy, reliability, and material versatility.
Form 4 and its biocompatible version, Form 4B, represent the next evolution in stereolithography (SLA) 3D printing technology, built upon years of groundbreaking hardware, software, and materials science innovations. With unprecedented speed, Form 4/B delivers the majority of parts in under two hours, in all materials, without ever compromising on dimensional accuracy or surface finish.
Form 4 combines a new print engine with updates to the Formlabs materials library — 23 unique resins on Form 4 and 37 on Form 4B available at launch — as well as new accessories and post-processing solutions, and an improved user experience. These updates reaffirm that Formlabs’ resin 3D printing ecosystem is the most powerful tool available for any professional to turn their ideas into reality.
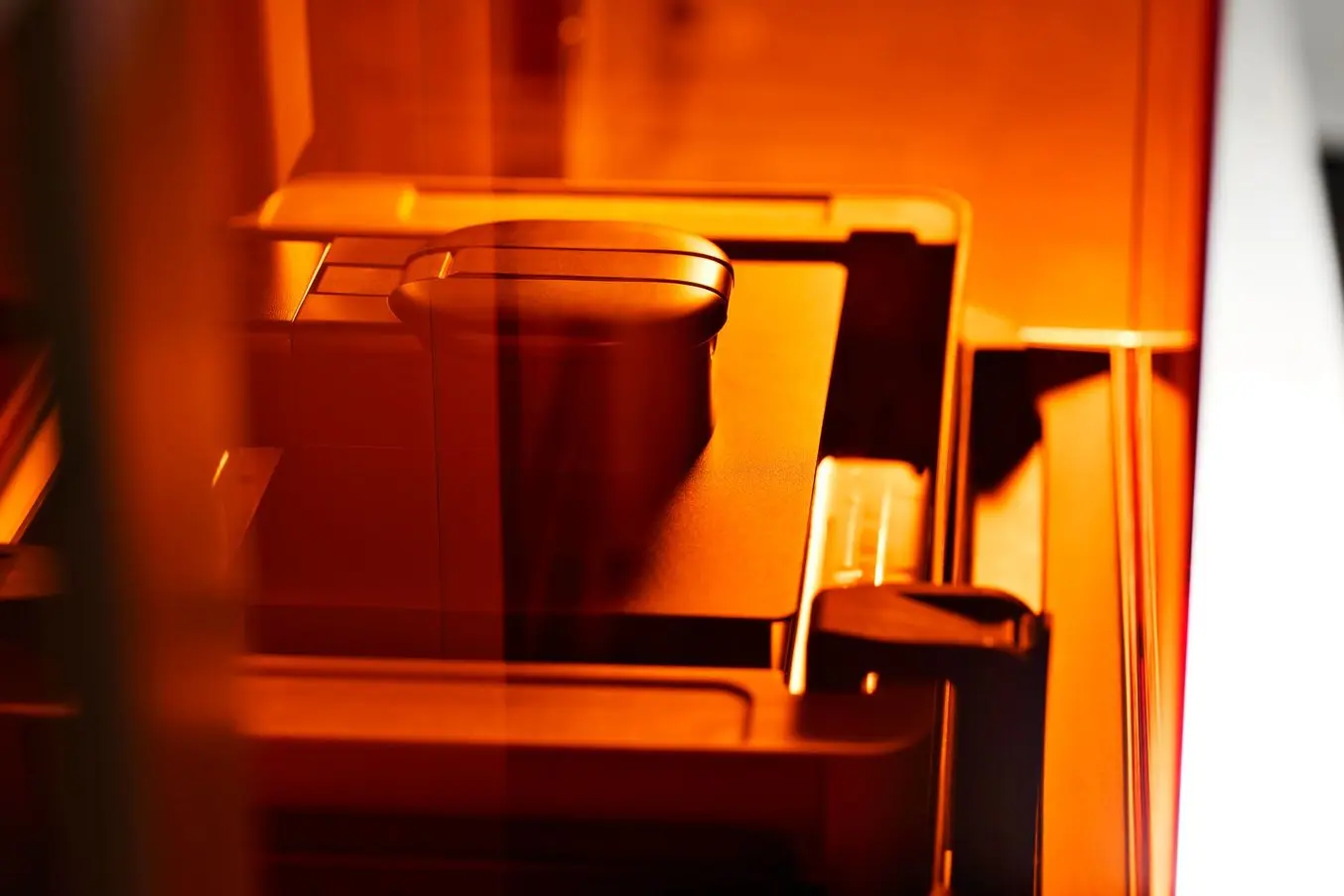
Product Demo: Form 4
See how Form 4 can enable new levels of productivity and innovation through its unmatched speed, accuracy, and reliability.
The Next Step in SLA Evolution
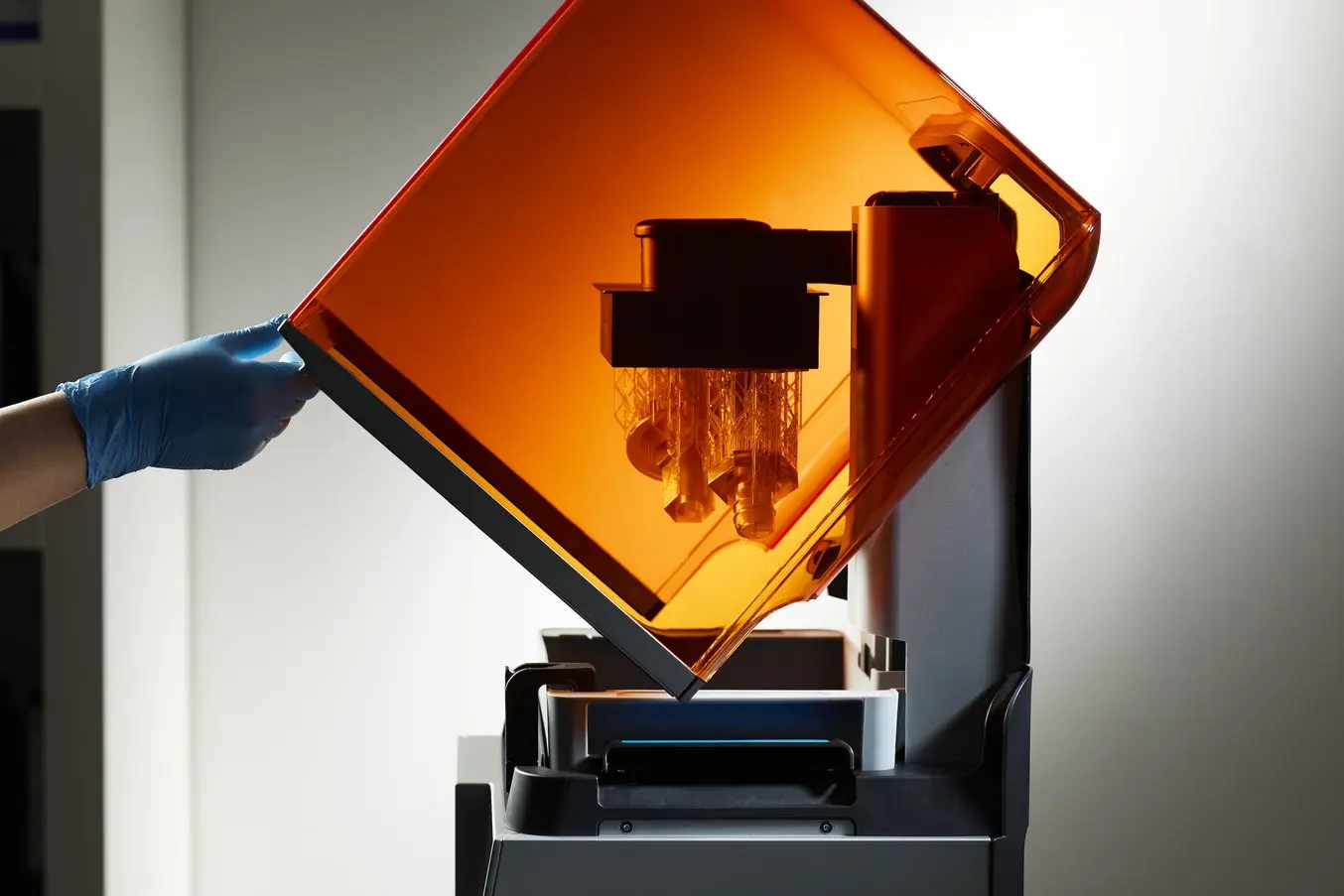
Form 4 takes the best qualities of the leading resin printers in the world and enhances them, for blazing-fast speeds, a 30% larger build volume, and better-than-ever tolerances and accuracy.
Since 2011, Formlabs has been dedicated to producing powerful 3D printing tools for engineers, product designers, manufacturers, researchers, healthcare professionals, and more. By making advanced 3D printing technology accessible, early versions of our printers powered innovations in every industry, and removed the cost and time limitations of traditional manufacturing.
But designing products and working with physical things is still incredibly difficult — every idea will have to overcome innumerable hurdles before reaching the end-user, and scaling production represents additional obstacles. Though 3D printing removes many barriers inherent in the fabrication process, even in-house fabrication of prototypes, tooling, and low-volume end-use parts can be too slow or too costly.
A 3D printer needs to be a tool that can match the speed of a product designer’s ‘lightbulb moments,’ the daily demand for assembly line fixturing, or production at scale. By working with over 50,000 companies who have leveraged Formlabs printers for years, we identified pain points in the 3D printing process, and have worked to continuously improve our products to address them.
Form 4 creates new opportunities in every application, accelerating the iterative speed of a design team, increasing the volume of a production-scale manufacturer, and expanding the material versatility of a service bureau.
Print speeds of up to 100 mm per hour1, a 30% larger build volume, new advanced materials, and updates to the workflow make Form 4 the most powerful professional fabrication tool available.
1Using Fast Model v1 Resin and 200um layer height. Based on actual print times from a collection of test parts covering common engineering, product design, manufacturing, and dental applications.
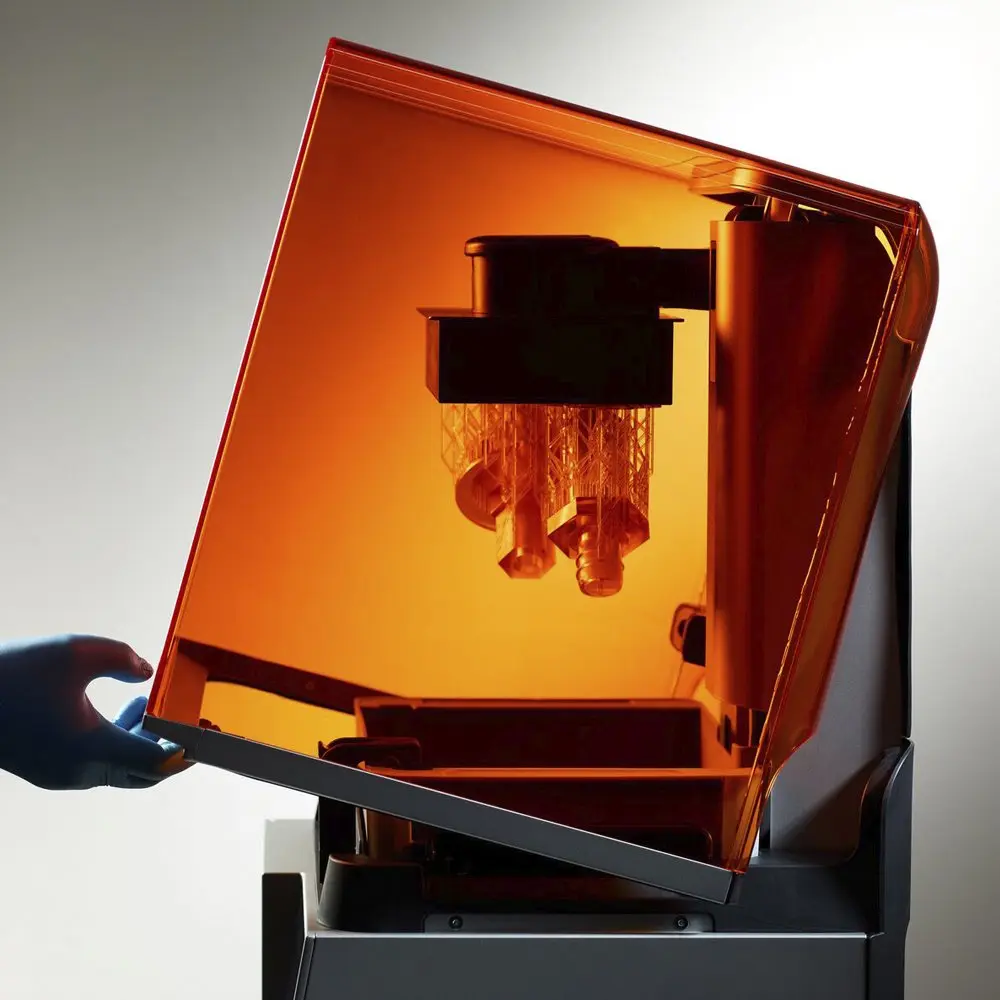
Guide to Stereolithography (SLA) 3D Printing
Looking for a 3D printer to realize your 3D models in high resolution? Download our white paper to learn how SLA printing works and why it's the most popular 3D printing process for creating models with incredible details.
From Ideation to Validation Before Lunch
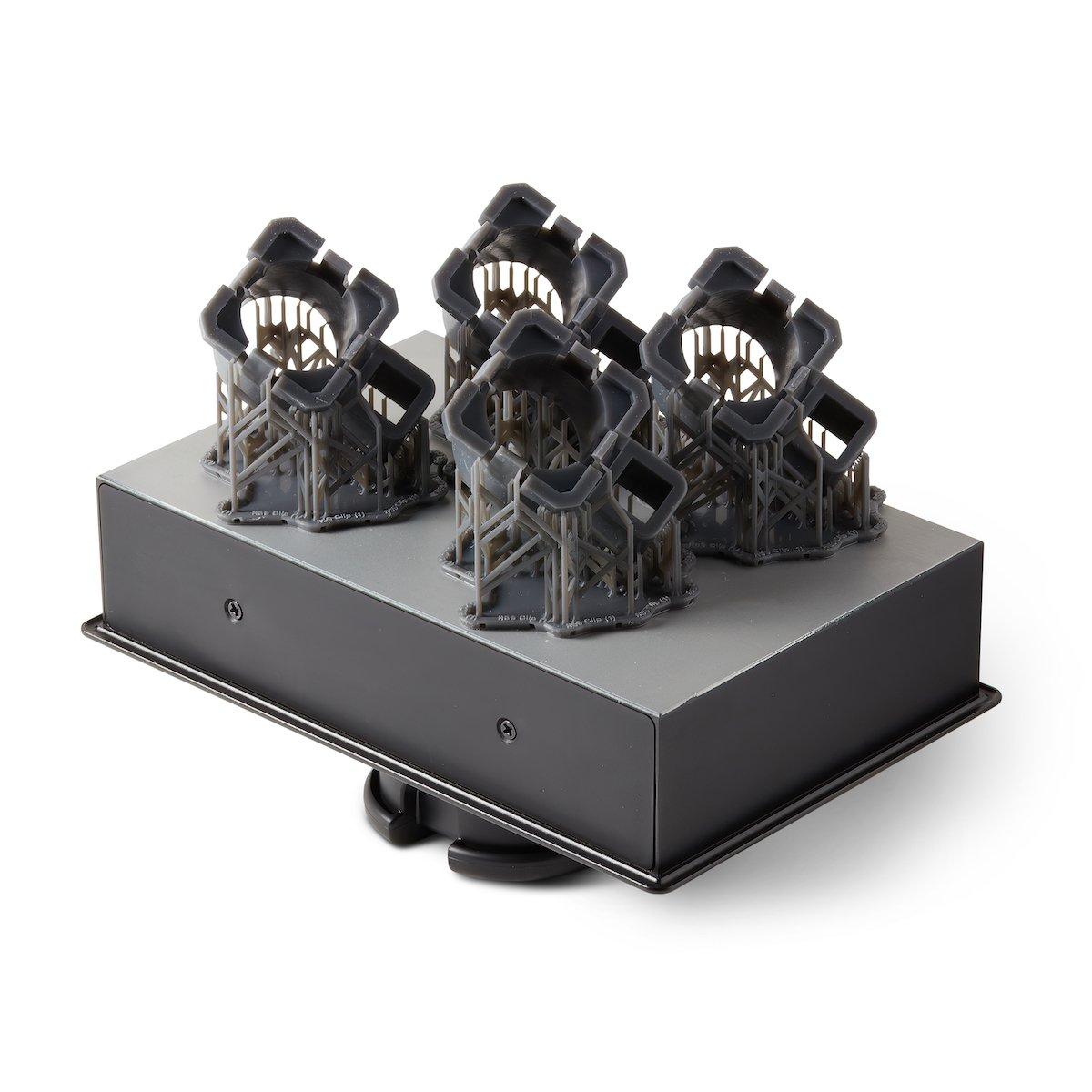
These switch clips were printed in Tough 2000 Resin on Form 4 in one hour and 53 minutes, compared to four hours and 47 minutes on the Form 3+.
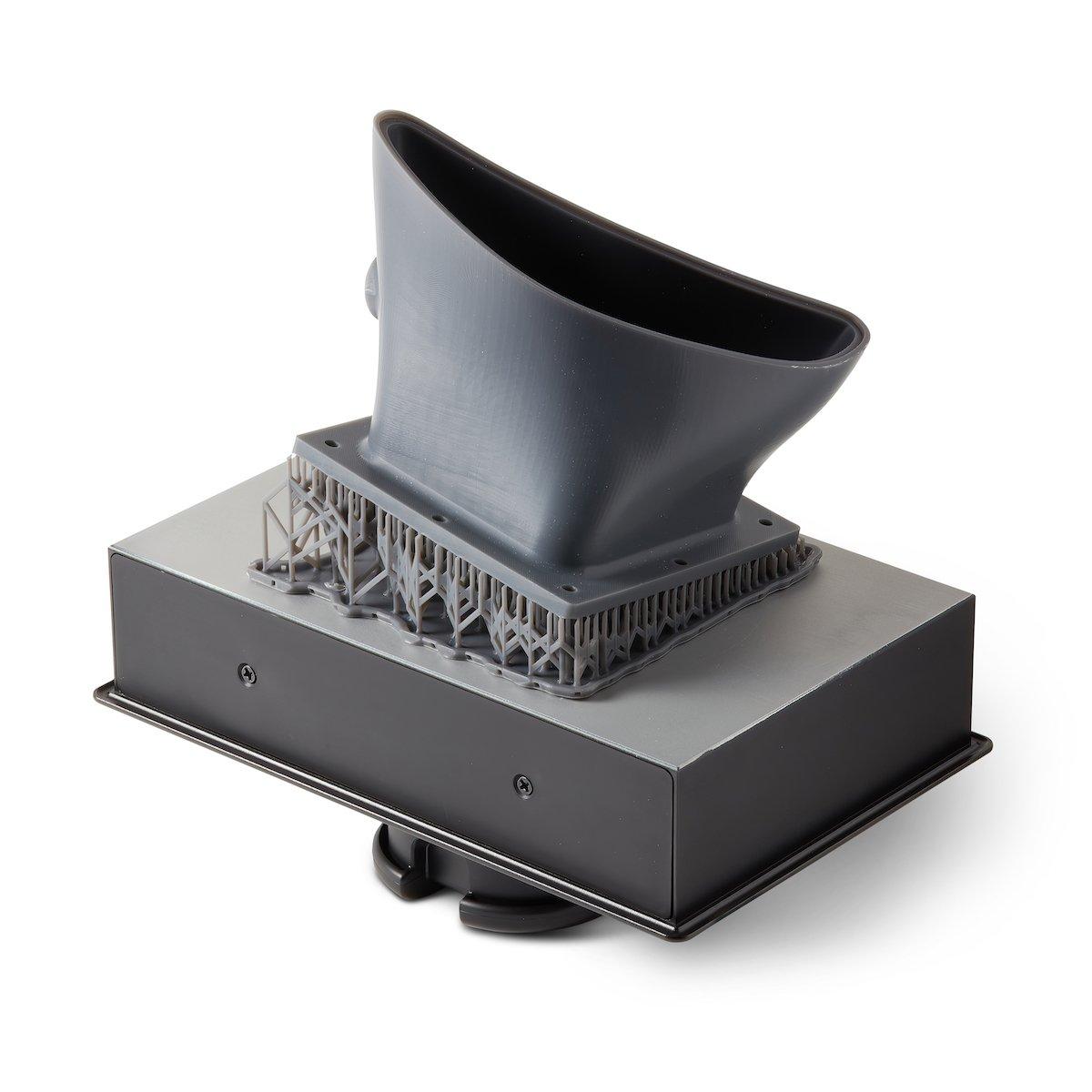
This large airflow test snout was printed in Grey Resin V5 on Form 4 in two hours and 56 minutes, compared to almost nine hours on Form 3+.
Form 4 enables every individual, team, and organization to get more done. Productivity is never limited by a lack of good ideas — it’s limited by the ability to execute. With faster printing speeds than ever before, products can go through design, print, and testing multiple times a day.
Prints on Form 4 are completed two to four times faster than with any other Form Series resin 3D printer, even for tall parts or batch printing. This new capability outpaces professional 3D printers across every technology and discipline.
Form 4’s speed is driven by the new Low Force Display™ print engine, a powerful combination of high-power LEDs and masking lenses that cure each layer of resin instantly — regardless of part size or quantity. Print speeds are no longer affected by how much of the build platform is covered, so multiple parts can print at once without extending your print time.
How Form 4 Transforms OXO’s Workflow
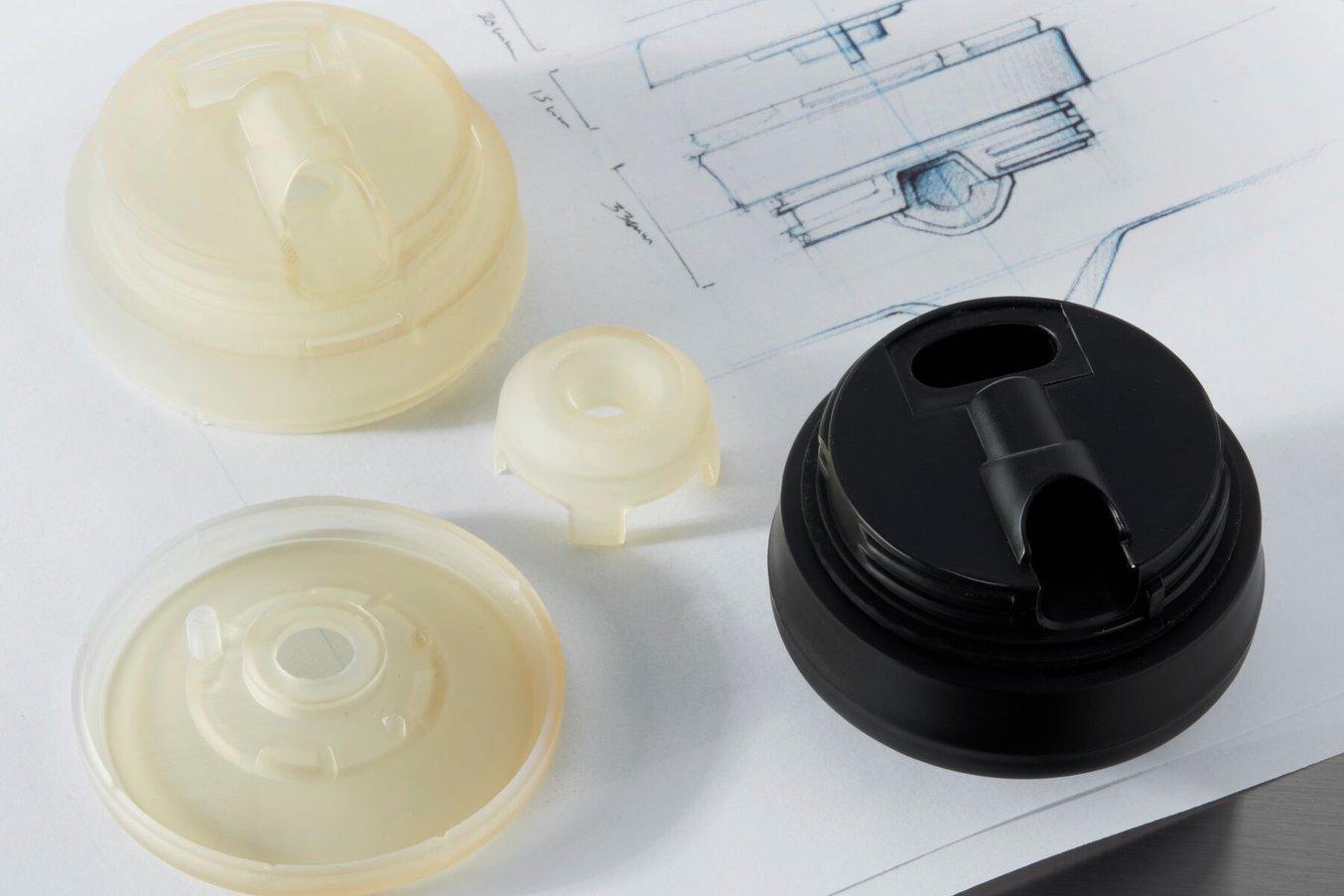
OXO’s product development process has to match the breakneck pace of the consumer goods market and ensure they reach market before their many competitors in the kitchen goods and appliances market.
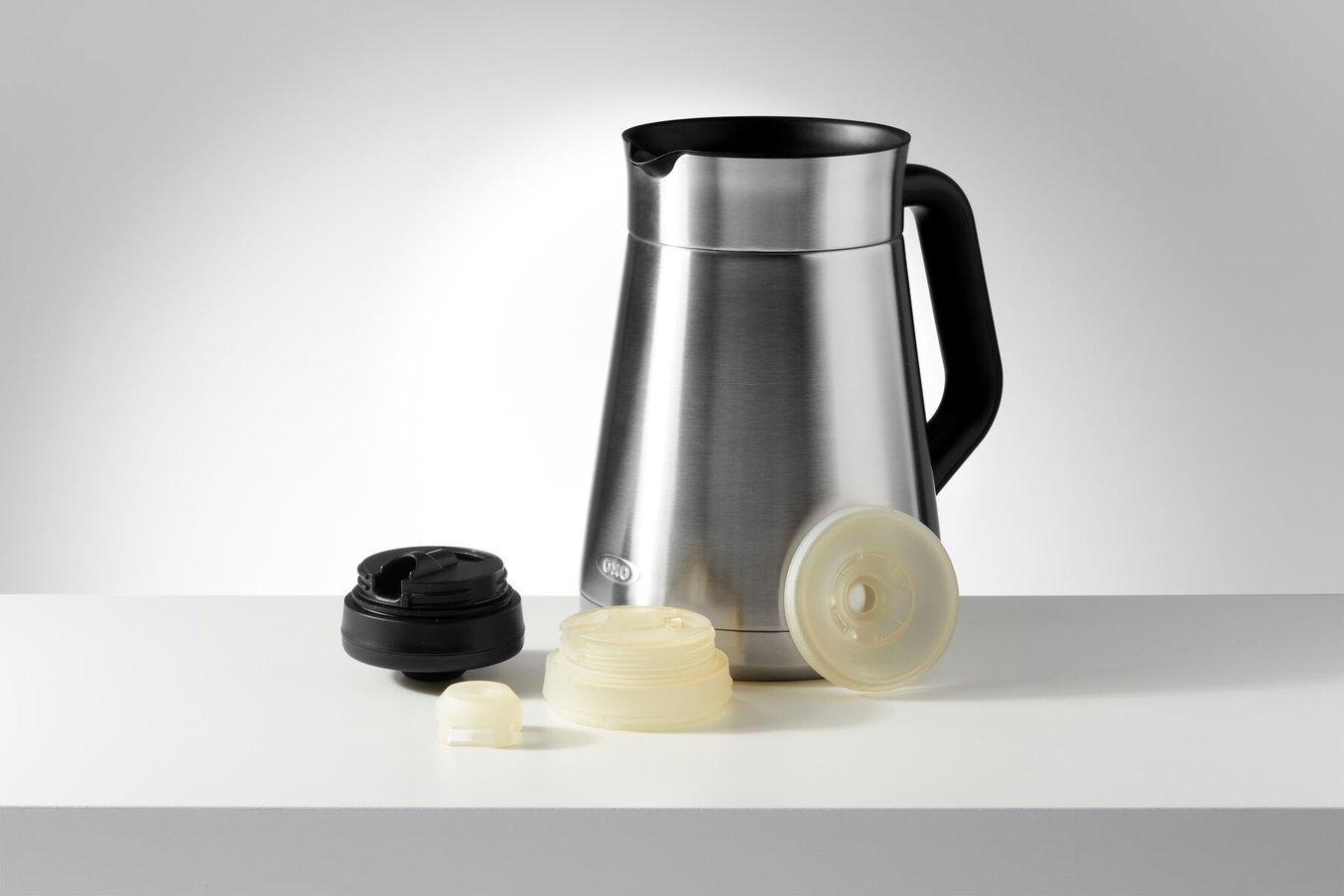
Caps like these, prototyped multiple times a day on Form 4, represent months of engineering and design work. Doubling the number of design improvements they can make a day, Form 4 helps OXO create beautiful, functional, and long-lasting products.
At OXO, Jesse Emanuel runs the rapid prototyping lab for teams of industrial designers, validation engineers, and the global manufacturing team. OXO’s product catalog is vast, covering everything from hand implements like vegetable peelers to more complex cooking equipment like food processors and coffee machines.
To create tools that customers will come to rely on for years, Emanuel and his fleet of 3D printers are printing between 100 and 200 resin parts each week. Every team needs parts — basic form models for the industrial designers to validate a new idea, end-use functional testing models for the product team to dial in for mass production, and presentation-ready parts for marketing and sales to present to OXO’s many distributors. Speed, quality, and material versatility are necessary in a 3D printer, and the Form 4 came at the perfect time.
“Form 4 has transformed our workflow. In the past, our queue has often been an issue based on time. With Form 4, it throws that out the window — we’re no longer constrained by time.”
Jesse Emanuel, Test Engineer, OXO
Kitchen products need to be simple, streamlined, easy to use, and have the right ‘feel’ in the hand. Those qualities make iteration just using CAD nearly impossible — OXO designers have to hold something to get a read on it. With Form 4, “People are able to do on-the-fly daytime iterations. In the past we had to wait overnight to see most updated product iterations. Now, we can get three or four prints off the Form 4 in a day,” says Emanuel.
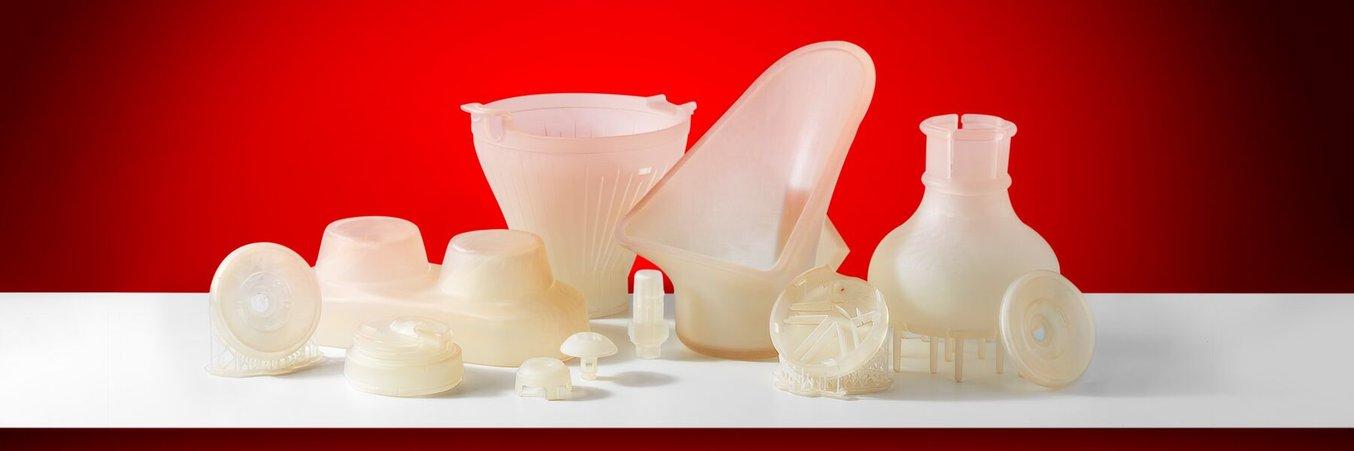
Many of OXO's product lines require prototypes, like these printed in High Temp Resin to go through extensive testing in high temperature conditions.
The scale of OXO’s product catalog necessitates a product development tool with speed, versatility, and high-volume capacity. Form 4 ensures that Emanuel and the rest of the team can try out new ideas (almost) as fast as they can think of them.
Being able to match Formlabs resins to common industrial plastics makes design and testing easier for OXO. “A huge reason we use SLA over FDM is materials options,” says Emanuel. They rely on Tough 2000 Resin for ABS-like parts and Tough 1500 Resin for polypropylene, as well as Silicone 40A Resin for true silicone validation models, High Temp Resin for prototypes that will be tested in boiling water, and Rigid 10K Resin for injection molds.
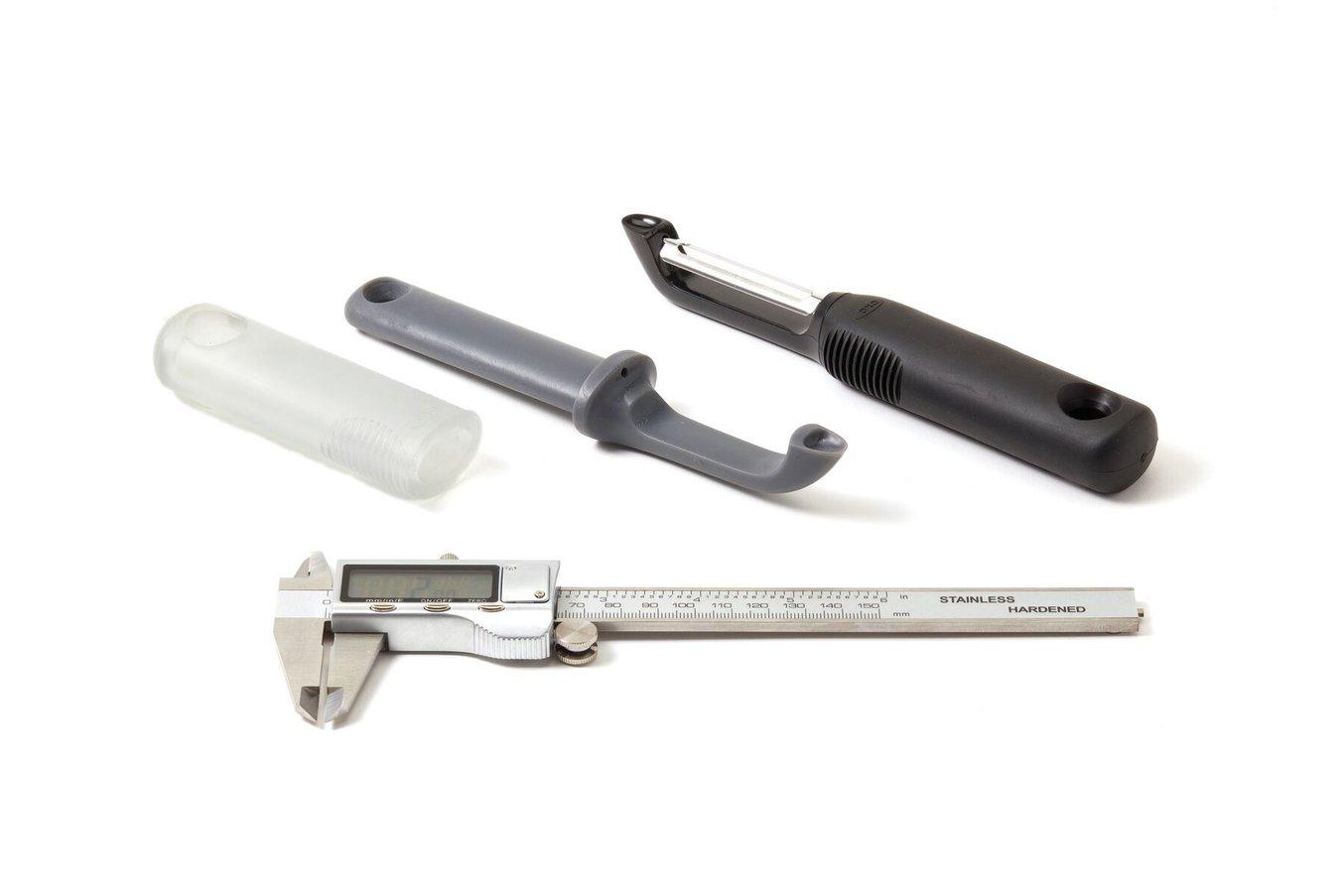
The OXO vegetable peeler, found in almost every kitchen across the country, was prototyped on Form 4. Each vertically printed peeler takes only three hours and 20 minutes to complete, and build platforms can hold more than eight different iterations at once.
“For all of our products, we have a huge myriad of different components and products we use. We run about 12-15 different Formlabs materials that we use for a variety of reasons.” Form 4 has allowed an already high-performing team to increase their iterative speed. As OXO’s product development process continues accelerating, Form 4 enables new levels of productivity and efficiency. To learn more about OXO, read the full user story.
Industry-Leading Dimensional Accuracy
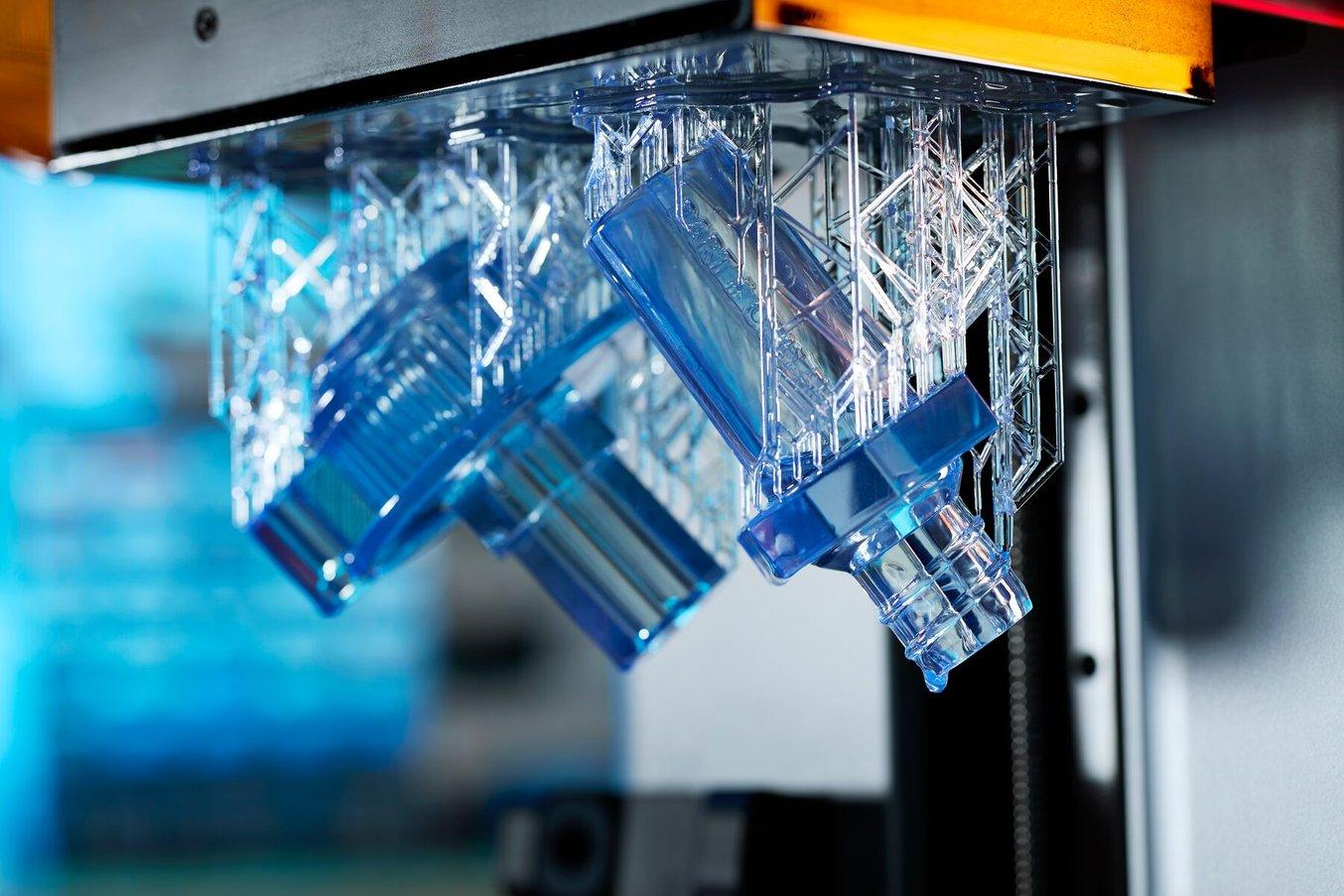
With Form 4’s tight, consistent tolerances, parts come out of the printer with crisp edges, clear, well-defined planes, and perfectly smooth surfaces.
3D printed parts need to be precise to be useful. Whether they’re prototypes that need to look like an injection molded plastic, or fixtures that need to mate with existing components on an assembly line, tolerances matter. Speed should never come at the cost of accuracy and precision.
Form 4 not only matches the industry standard for tolerances, it goes beyond. With superior and repeatable tolerances, parts printed in every resin on Form 4 will match your design parameters, every time. Form 4’s Light Processing Unit (LPU) delivers a 50 µm XY resolution so that multi-part assemblies glide together without friction, manufacturing aids integrate seamlessly into the workflow, and end-use parts match the repeatable precision of mass-produced plastics made through injection molding.
With repeatable tolerances that match initial designs, parts can remain the same through each stage of product development. Quickly printed as a mockup, functionally tested as a later-stage prototype, or produced as a stop-gap option, the appearance and performance of every part will stay the same. Surface finishes that are indistinguishable from injection molded plastics make the design to mass-production workflow simpler. With the accuracy of Form 4, you can focus on the product, not planning contingencies for dimensional variation.
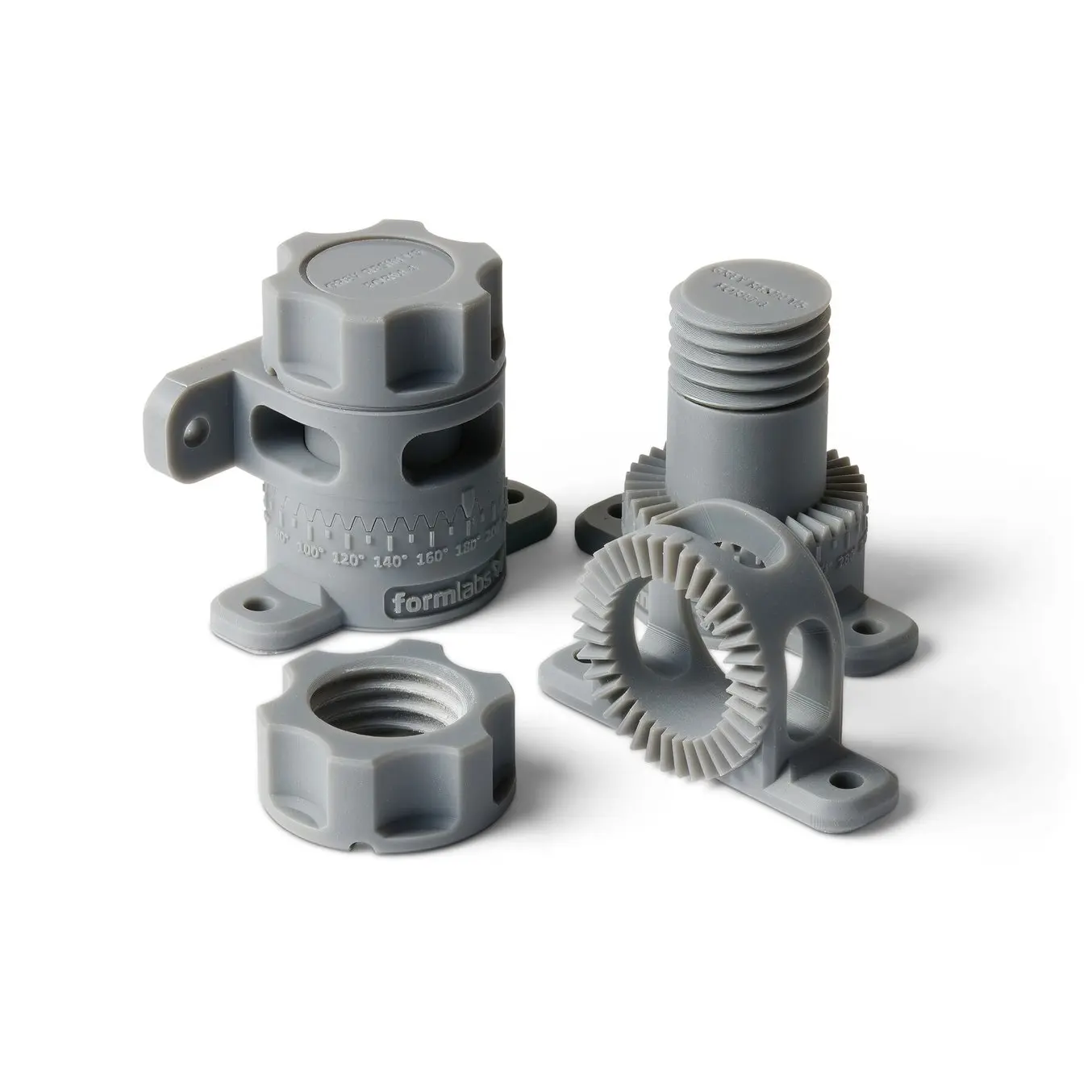
Request a Free Sample Part
See and feel Formlabs quality firsthand. We’ll ship a free 3D printed sample part to your office.
15 Minutes to Your First Print: Any User, Any Application
Before earlier iterations of the Form Series introduced accessible, high-quality 3D printing, SLA workflows were often complicated. Some required dedicated operators, complex infrastructure, and large spaces for top-down resin printing.
With the Form Series, Formlabs proved that accessible 3D printing meant more than just affordable prices — it also meant that the workflow could be easy to learn and that the printer could fit into your existing space, including offices, homes, classrooms, and machine shops. Form 4 takes that one step further, simplifying the printer set-up, monitoring, and material change-over, so that anyone can start printing within 15 minutes.
In addition to the speed improvements made possible by the print engine and material settings, new automatic resin handling features reduce the time it takes for prints to start. Automatic resin dispensing uses a series of smart sensors to maximize uptime, so that changeover time between prints is negligible and you can focus on the parts, not the process.
Form Series printers are being used in applications as complex as bioengineered cell scaffolding, metal turbine fabrication through investment casting, and surgical implants. When 3D printing is part of a process that complex, the actual printing should be the easiest step, and Form 4 makes that possible. From receiving your printer to starting your first print, spend only 15 minutes on set-up and watch your ideas take shape in minutes.
Ease of Use, Step by Step
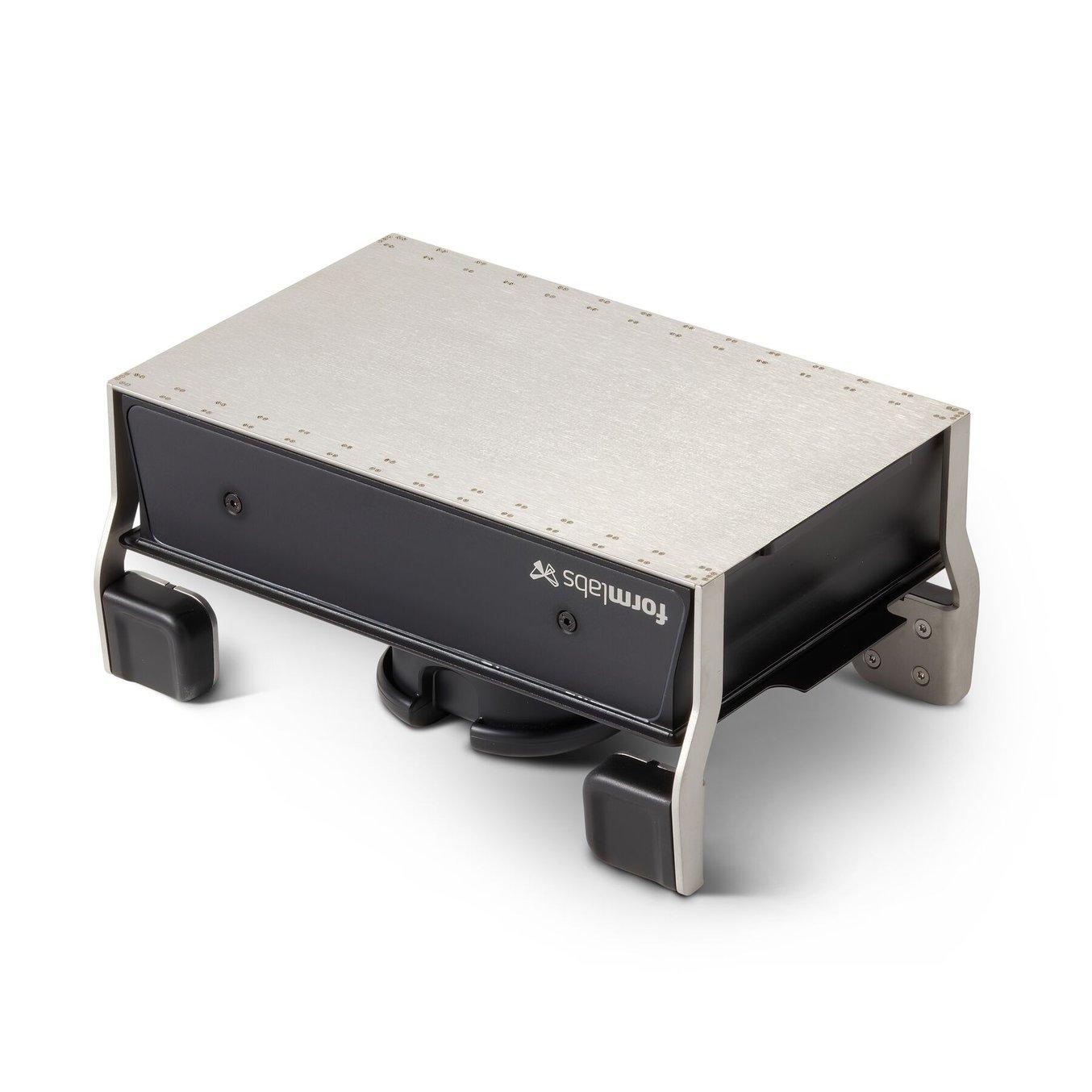
The full Formlabs ecosystem is designed to maximize efficiency and reduce the potential for print errors. Formlabs free print preparation software, PreForm, automatically analyzes the part and determines the optimal orientation and support placement. Formlabs software engineering team continuously improves software settings to ensure that print speed, materials settings, and automatic orientation and support are perfected.
From the moment the printer finishes your part, the workflow is designed for ease, repeatability, and efficiency. The Quick Release Technology of the Build Platform Flex enables quick removal of the part and reduces instances of breakage. Parts are then automatically washed in the new Form Wash, with improved isopropyl alcohol agitation for a faster, cleaner process. The new Form Wash can adapt to fit build platforms from any Formlabs desktop printer. After washing, if parts need a post-cure step, the precision Form Cure settings ensure that parts can reach their optimal mechanical properties.
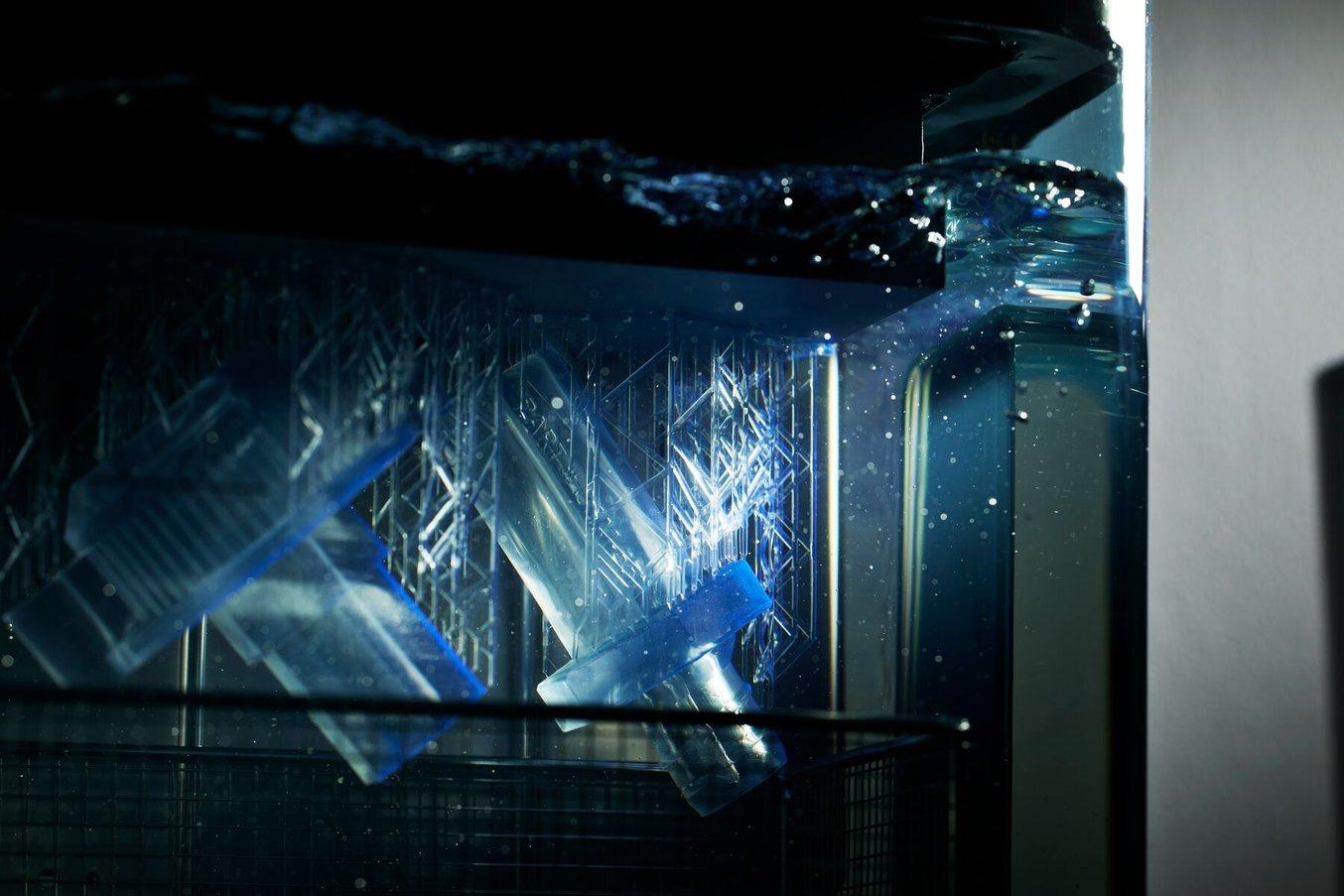
The second generation Form Wash is adaptable for multiple build platform sizes and improves the liquid agitation process, so parts get cleaner, quicker.
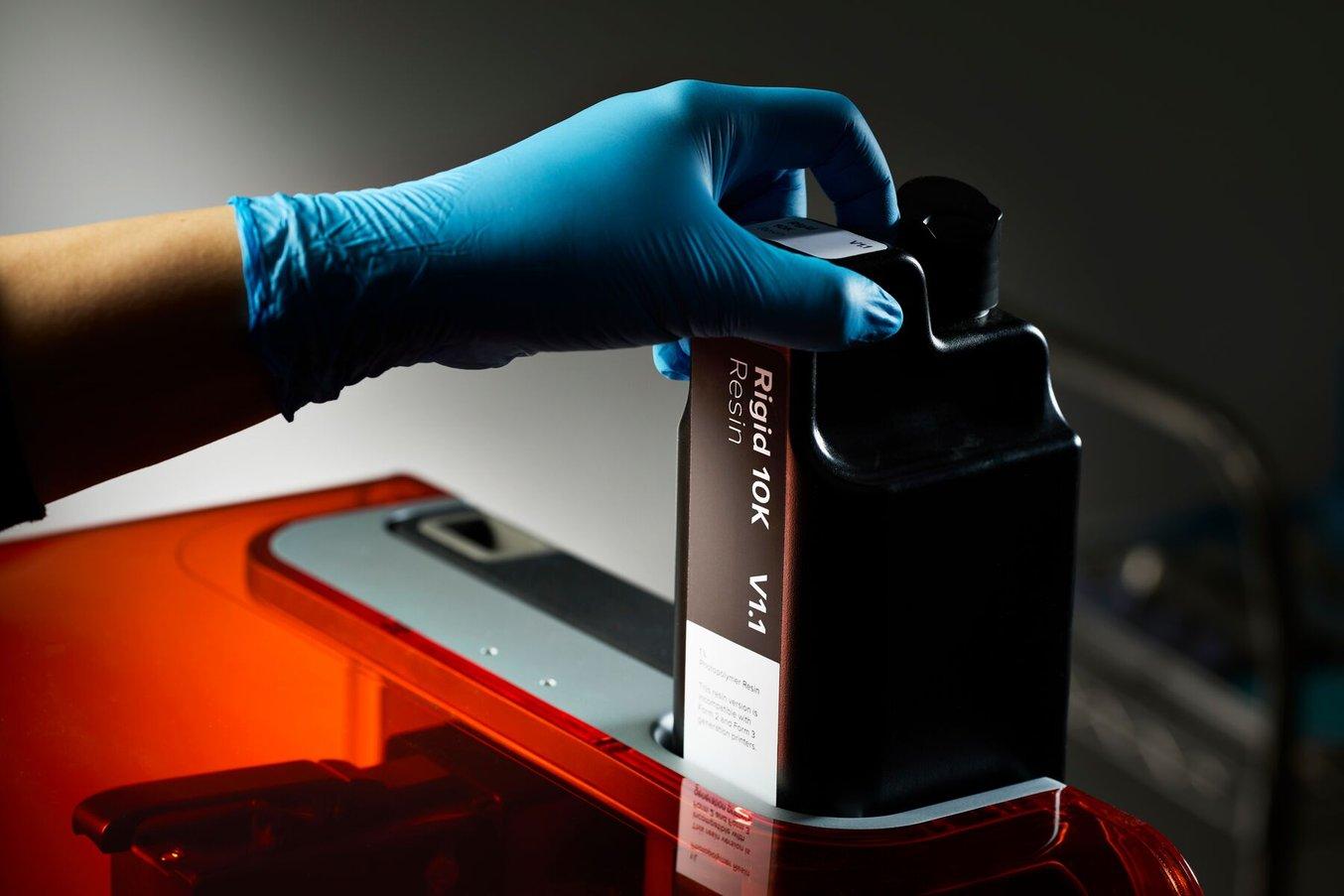
The new resin cartridge design uses less plastic and still delivers one full liter of material, making storage and maintenance that much easier.
High-Volume Reliability and Consistent Success
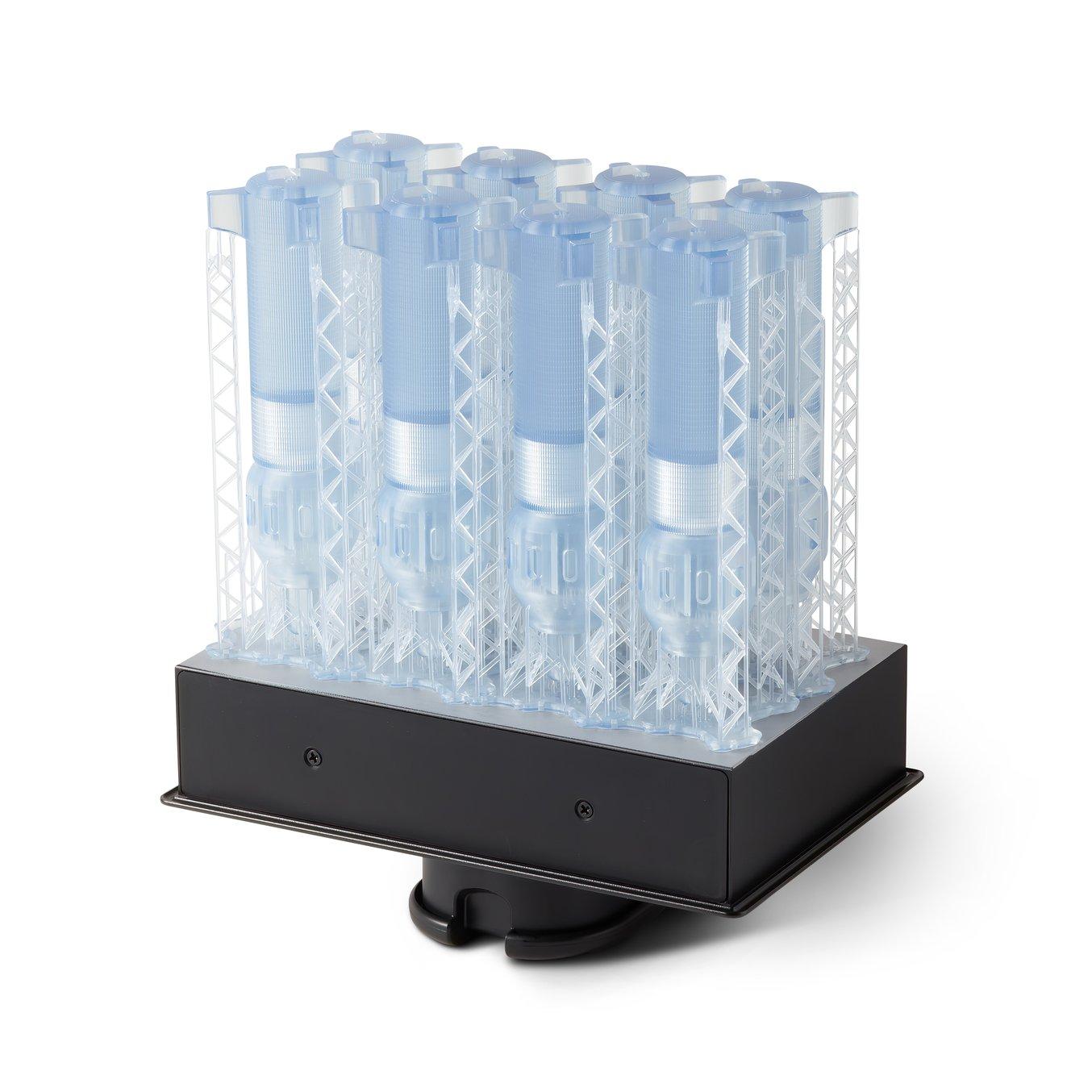
This entire build volume — eight single-use surgical ratchets — prints in only five hours and 45 minutes, compared to over 25 hours on the Form 3+. Now, surgeons and medical services can produce a full build three times a day, without extending their work day.
For the Form Series, accessibility also means reliability. Even for customers printing all day, every day, the printer won’t let you down. The Form Series set a high standard for print success and repeatable, reliable, high-volume use, but Form 4 surpasses it.
Form 4’s reliability is in part due to the time spent in the manufacturing process on quality control — each printer will undergo 60 checkpoints for functionality before it leaves the factory, ensuring that every unit will be the most consistent, high-performing part of your workflow. Furthermore, Formlabs’ print optimization team has spent years printing thousands of parts to dial in the settings for each material, so that even complex geometries in different materials will print with industry-leading reliability.
Both the central printer engine and components like the Resin Tank and Build Platform have been re-engineered to function more smoothly and last longer, even in high-volume applications. Resin Tanks can be relied upon for over 75,0002 layers, extending the uptime of the printer and reducing operational costs and the number of touchpoints necessary to continue high-volume production.
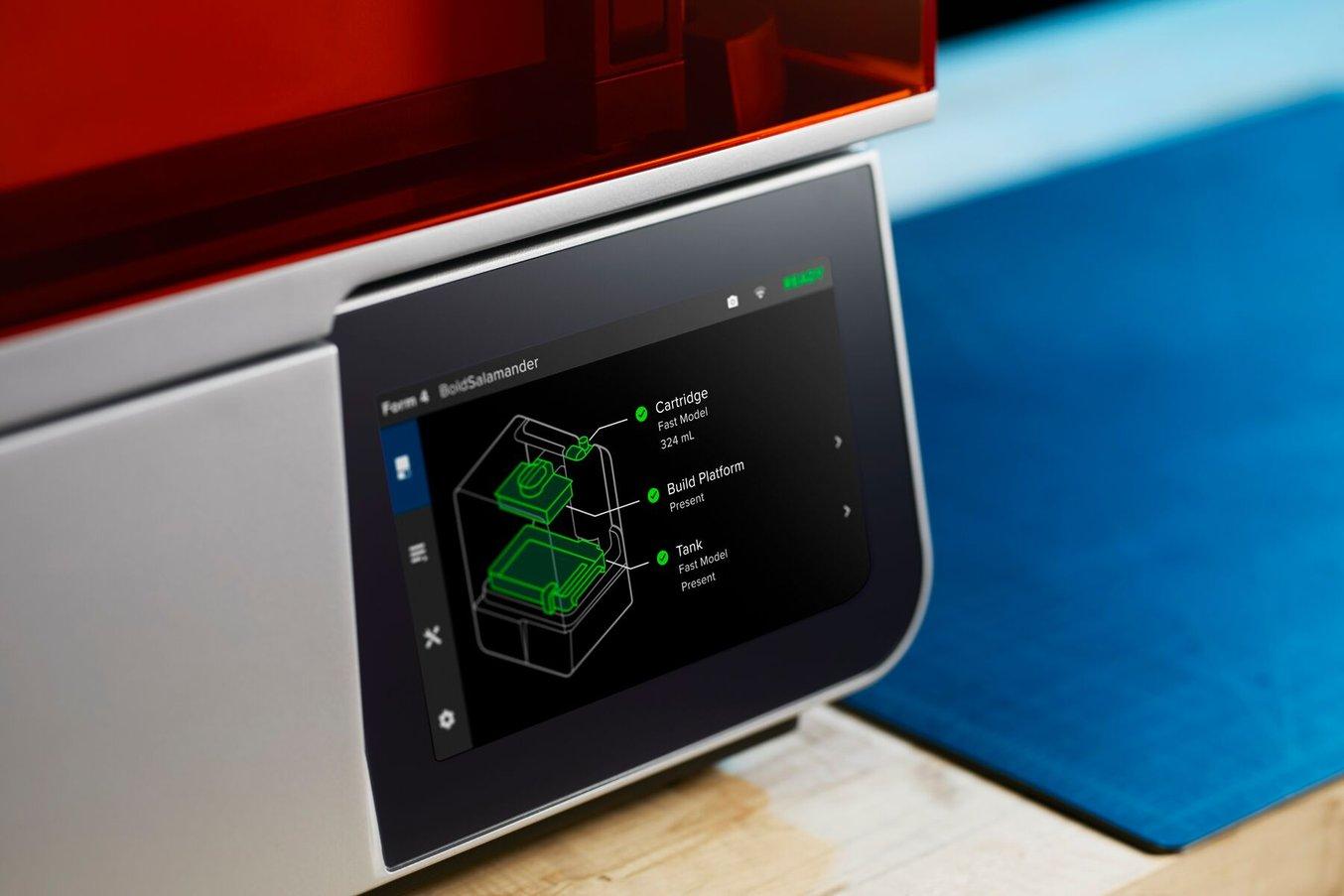
Form 4’s improved sensor system responds quickly to any potential issue with the print process, giving customers ample time to make changes to the workflow and ensure smooth printing.
Form 4’s automatic diagnostics and integrated sensors alert you to potential issues with each print, giving customers a chance to avert the consequences of a poorly set-up job and to understand how to optimize their printer usage. The integrated sensor system ensures that Form 4 will remain up and running, even in high-volume applications, for years to come. Reliability shouldn’t dip as the printer gets more use — Form 4 is a tool that improves as your own process evolves.
2 With any Formlabs material. The exact lifetime of an individual resin tank depends on layers printed, physical wear, and accidental damage.
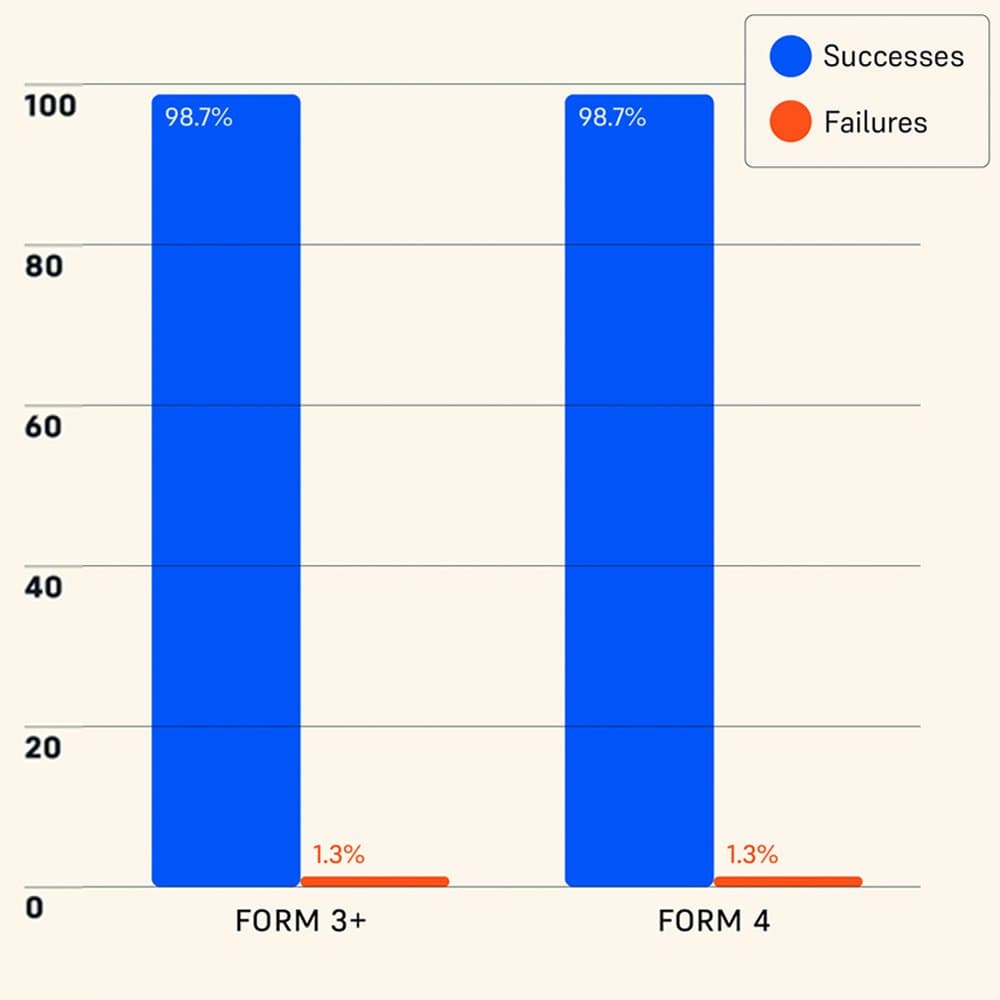
Independently Tested Reliability of Form 4 and Other Resin 3D Printers
Formlabs Form 4 was measured to have a 98.7% print success rate by an independent global leader in product testing. Read a complete description of the test methodology and see the results in our white paper.
Unlock New Applications Through the Expansive Materials Catalog
Formlabs printers combine high-precision hardware engineering and groundbreaking software to create a workflow that delivers complex shapes with tight tolerances, every time. But Formlabs’ library of more than 23 purpose-built resins, including true silicone, technical ceramic, polyurethane, and unique formulations like Tough 1500 Resin, Rigid 10K Resin, and Flame Retardant Resin, is what unlocks potential for new applications and new industries.
With the introduction of Form 4, six new materials are now available, and at a discounted price:
Form 4’s upgraded automatic resin dispensing and heating capabilities make it possible for Formlabs to develop materials that were previously out of reach, like those with very high viscosity or that are highly filled. These new materials are updated formulas of some of the most widely-used materials in the world for resin 3D printing. The features that have made materials like Grey Resin or Clear Resin so popular are enhanced in the new versions, so that part detail is sharper and the aesthetic qualities are elevated. Clear Resin V5 delivers almost completely transparent parts, and Black Resin V5’s surface is smooth and completely matte.
When Form 4’s previous iteration, Form 3, was announced in 2019, Formlabs offered 20 unique resins. Since then, we've nearly doubled our resin catalog, with 37 materials available on Form 4B, and more to come. Integrating the Form 4 ecosystem into your workflow means unlocking future, innovative materials that can take toughness, durability, heat, and aging resistance to the next level.
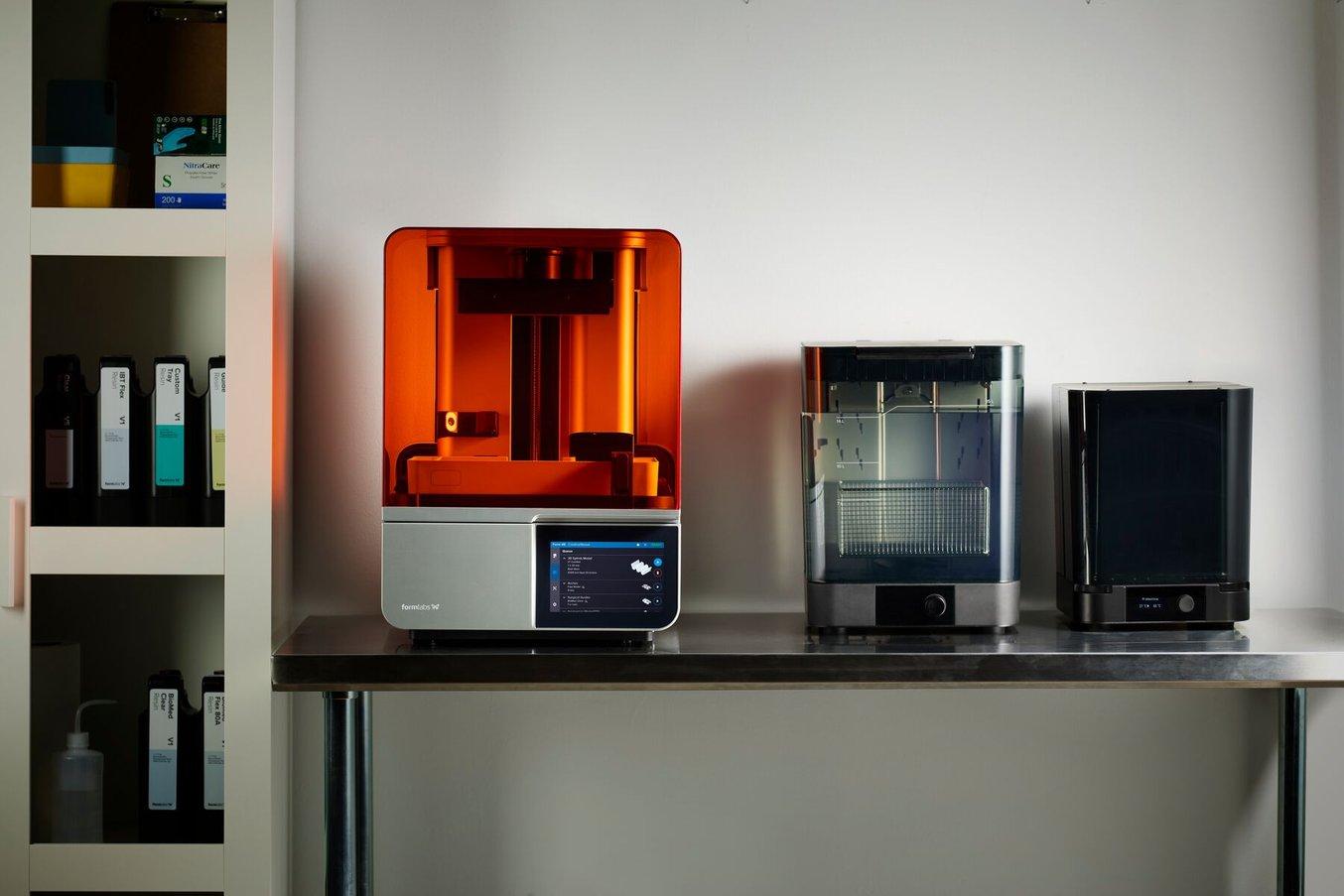
Together, Form 4, Form Wash, and Form Cure complete the Formlabs resin 3D printing ecosystem, making it easy to print with any of Formlabs materials by relying on preprogrammed settings that ensure each material reaches its optimal material properties.
For customers looking to experiment with resins not currently available in the Formlabs library, Open Platform will be available for Form 4 — so users can opt for even more versatility with certified third-party materials, customizable print settings, and complete freedom to print with any 405 nm photopolymer resin.
Formlabs customers are in environments where heat deflection temperatures, elongation, flexural modulus, and tensile strength are the difference between using a 3D printed part and using a traditionally fabricated component. For years, material limitations meant that in these situations, customers couldn’t take advantage of the on-demand power, affordable cost, and design freedom of 3D printing. Materials make the difference. Form 4 has been developed alongside our library of purpose-built resins, so that pre-programmed settings deliver parts that perform, every time.
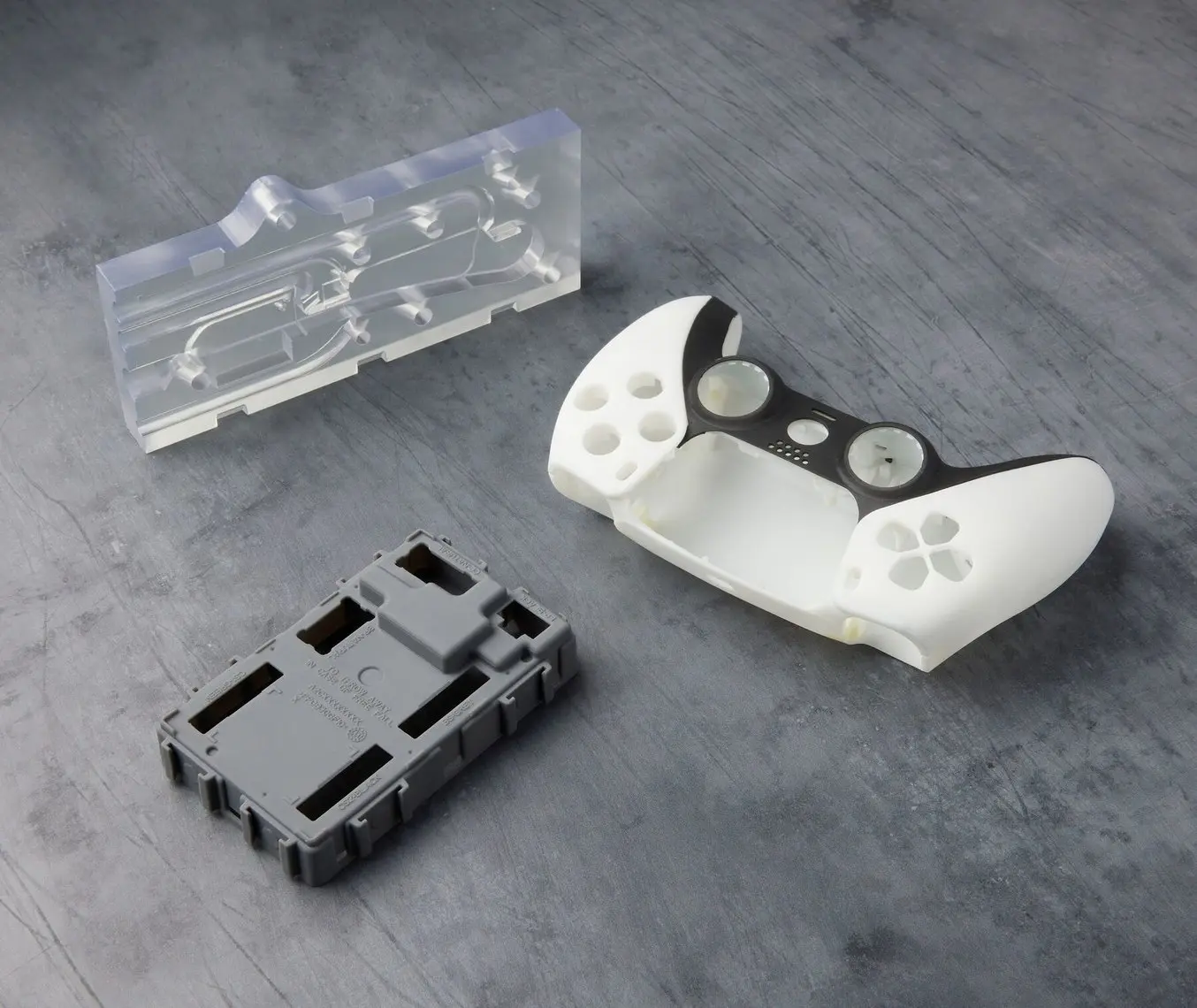
Form 4 Materials Guide
Learn more about all the high performance materials available on Form 4 and how to leverage the right material for your application.
How Form 4 Elevates Workflows Across Industries
Form 4 Accelerates Ascent at Black Diamond Equipment
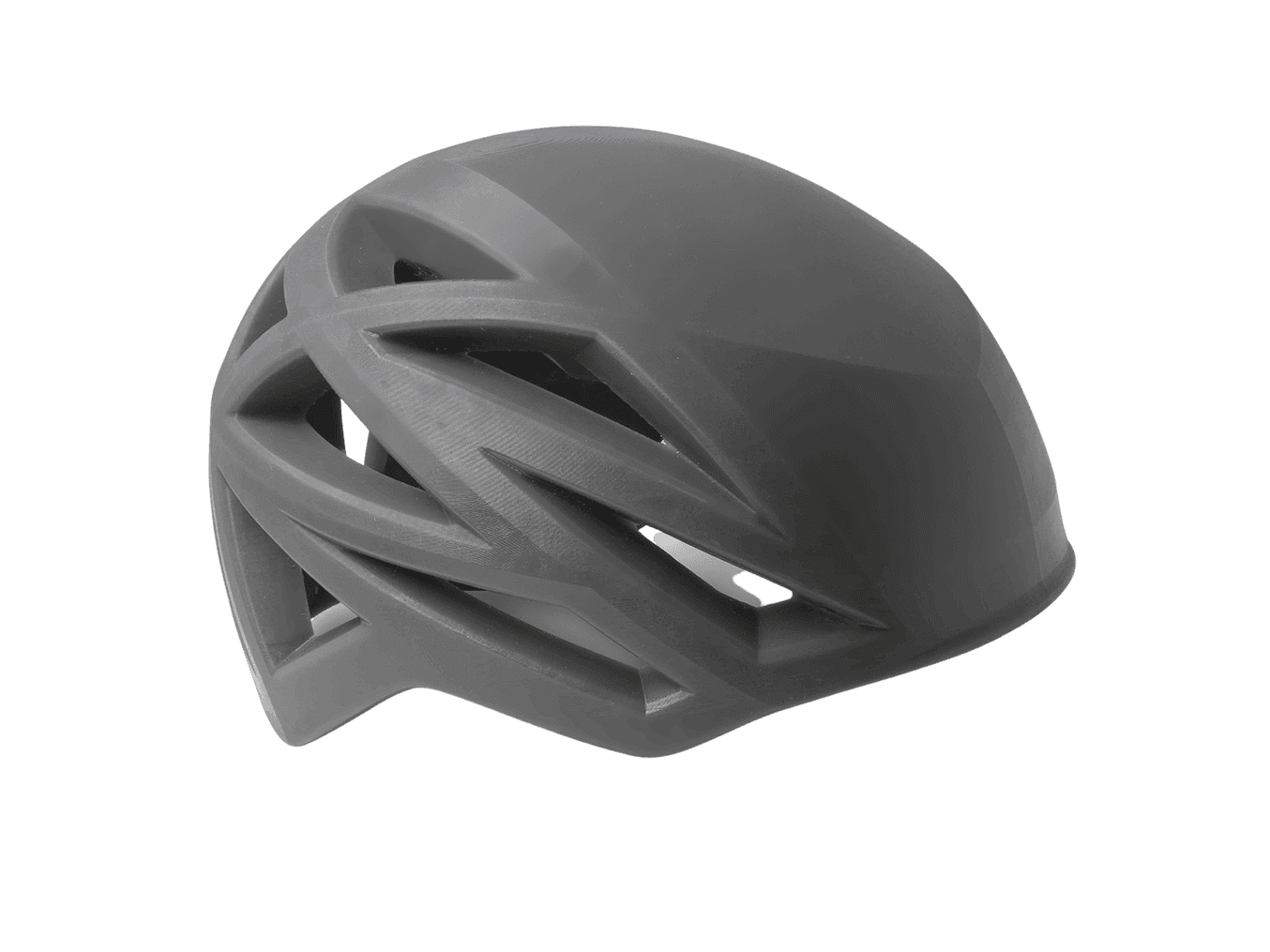
Black Diamond prides themselves on producing the highest quality gear for people who love the outdoors — Form 4 helps them iterate more thoroughly, delivering products that help keep people safe and improve performance.
Black Diamond Equipment has one deal-breaking requirement for people to work on their design team — unbridled, infectious enthusiasm for the gear they’re making. Product Design Lab manager Matt Tetzl spoke with us about their design process and how using Form 4 has helped them spend more time testing their products in the Wasatch Mountains, and less time waiting in the lab for prints to finish.
Familiar Formlabs Ecosystem Streamlines Adoption
Tetzl has been printing every day on Formlabs printers for years, but adding a new printer can always present challenges. Not so with Form 4 — Tetzl got it unboxed and running its first print in under 30 minutes.
“It’s been mostly plug and play, very straightforward. It feels just as approachable as all the other Formlabs systems — 99% of the time I know I’ll have a successful print. And the other 1%, I know I can fix it myself, and get it working same-day. It’s super nice to have that reliability.”
Matt Tetzl, Prototyping Manager, Black Diamond
Though reliability makes integration easy, speed is what’s affected resin printer utilization at Black Diamond the most. One project, designing lenses for a headlamp, was already moving at a breakneck pace; designers were requesting new iterations every day. Form 4 accelerated that even further. “We did three iterations in a single day to get three different parts before our meeting in the afternoon.” Operating as an internal service bureau for multiple design departments, Tetzl has been able to stick to a 24-hour delivery guarantee. Now, he’s been able to go above and beyond. “Form 4 bridges that gap, and makes it same-day delivery.”
Though designers are familiar with the necessity of tradeoffs in product development — size or packability, lightweight or strength — Form 4 has accelerated development with no diminishing dimensional accuracy. “We need parts to match the original CAD design, to fit smoothly into assemblies, and to print multi-part molds that fit together tightly. Grey Resin V5 molds have been fitting perfectly,” Tetzl says.
Grey Resin V5 Fatigue Testing and Surface Finish
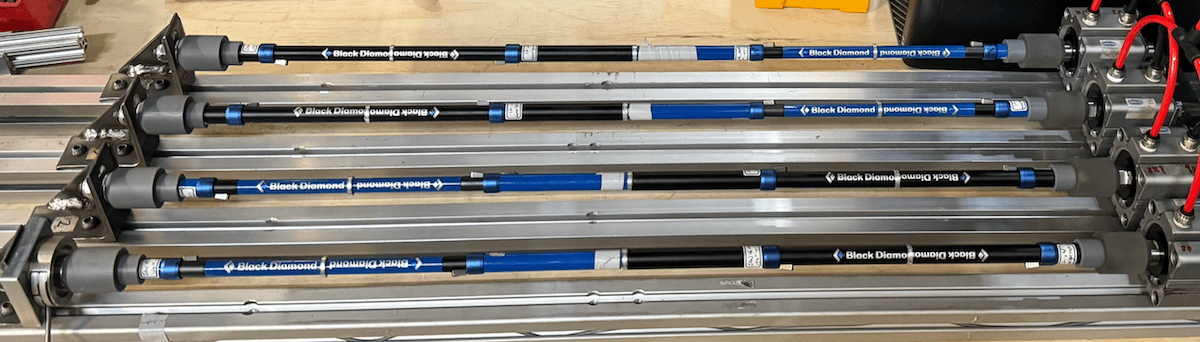
Grey Resin V5 stands up to considerable force, even for testing cycles of 2.5 million. Being able to quickly produce parts for validation cycles means Black Diamond can try out new ideas without risking coming up against a deadline.
For Black Diamond’s trekking poles, fatigue testing has to go above and beyond what another company might call pushing the limit and Grey Resin V5 was up to the challenge. Tetzl printed a Fixture to hold the button assembly that controls the telescoping action of a collapsible trekking pole in Grey Resin V5 on Form 4. The pole was then put through a simulated fatigue test where a customized jig pushed the button with considerable force against the housing over and over again. Even after exhaustive testing with some pretty serious weight, Tetzl was impressed by the durability of the new resin formulation, saying, “For 55 pounds per cycle, we completed 2.5 million cycles, and it showed no wear or deformation.”
Speed, dimensional accuracy, and surface finish improvements have helped Tetzl answer increasing volume for SLA parts from the Black Diamond design teams. Form 4 helps the team iterate more thoroughly, and nearly eliminates the time they used to spend waiting for prints, so they can get out on the trails for functional testing early and often — the optimal result.
Form 4B Advances Medical Device Development at restor3d
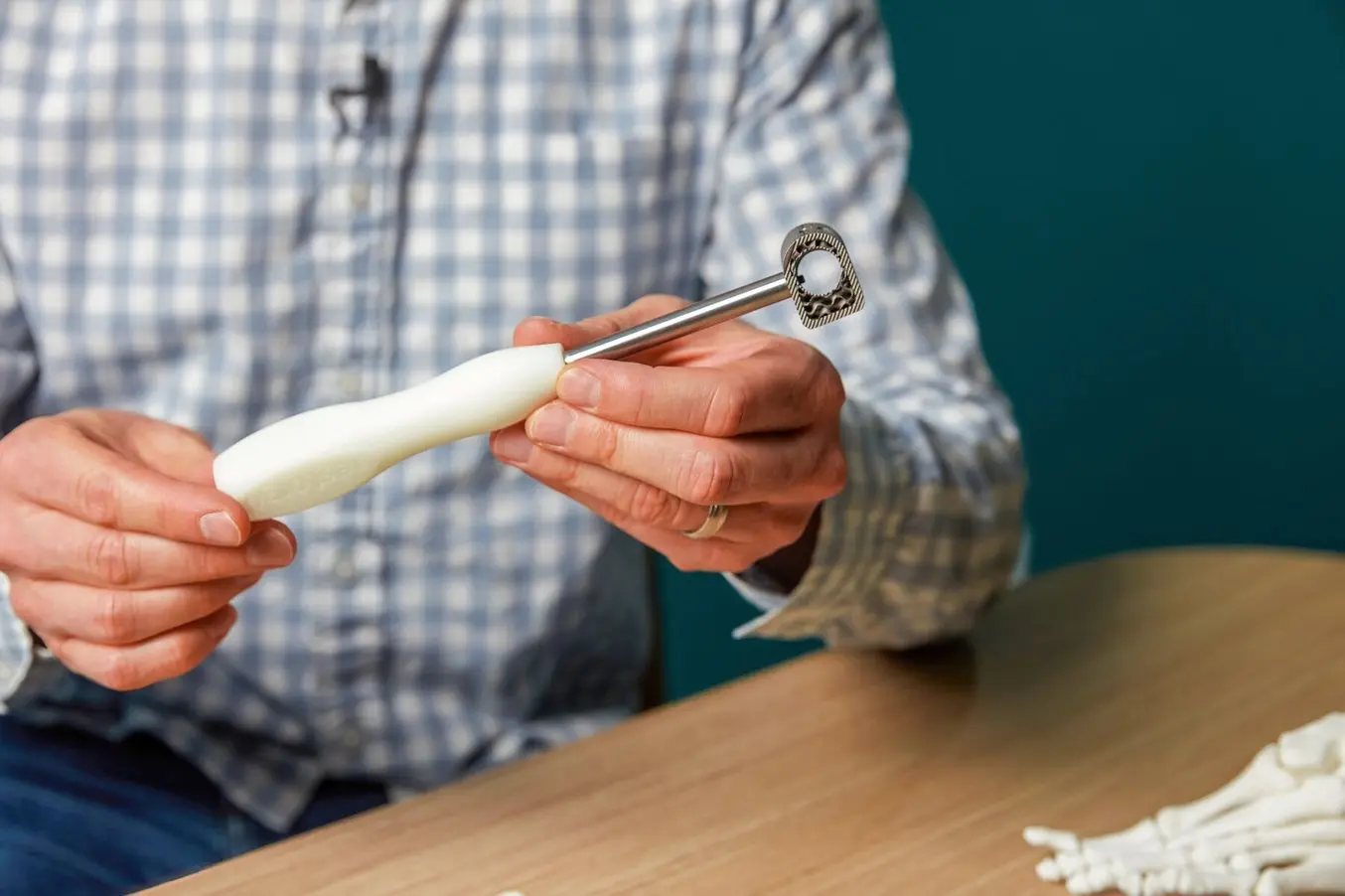
From the development of medical devices and patient-specific surgical guides to dental appliances, Form 4B brings speed and accuracy to life-altering procedures.
Medical device development and manufacturing require stringent quality controls. At restor3d, a medical device leader focused on patient-specific solutions utilizing additive manufacturing, advanced polymer additive manufacturing is being used to create off-the-shelf and patient-specific surgical instrumentation. Additive manufacturing manager Elena Tercheria specializes in polymers production which she and her team manufacture via 3D printers.
Tercheria’s main fleet of 3D printers consists of Form 3, Form 3+, and Form 3B 3D printers, where she sends about 90% of products printed in polymers, using a specially-formulated resin that surgeons can see under X-ray. Having used the Form 3/B/+ and competitors’ printers for years, the first thing she noted about Form 4B was print speed.
“The print speed improvement struck us the most. In my eight years’ experience with additive manufacturing, I haven’t seen SLA machines print parts that quickly. Almost every build, the Form 4B has been faster."
Elena Tercheria, Additive Manufacturing Manager, restor3D
When working with surgeons preparing for surgery, agility is key. In the event of an unplanned need for replacement parts, additional copies, or even last-minute redesigns, “the accelerated build duration [of the Form 4B] will help us be much more agile with recovery in these situations.” Additionally, “we love the improved accuracy of the time estimate. Just seeing the machine mix every layer and still attain a drastic decrease in the build duration is powerful.” Initially, the restor3d team expected the resin mixing frequency to affect build time, but consistently the print “finished in almost the exact time quoted. That’s a big deal for us, we will be able to dependably plan and schedule machine availability in advance.”
When considering speed, post-processing is a key component to understanding the total turnaround time. With the launch of the Form 4/4B come updates to Form Wash and Form Cure. Tercheria says, “The improvements with the Form Wash have been great: the larger impeller allows much better agitation for removing residual uncured resin from parts. A big thumbs up from us on the new Form Wash.”
Surface finish quality minimizes the need for post-processing, saving time and improving the accuracy of production. Resins for the Form 4/4B have been reformulated for improved print quality. “Honestly, there's hardly any layer lines,” says Tercheria. “Sidewalls look really smooth – they almost don't look 3D printed.”
Form 4B enables the printing of biocompatible resins in healthcare settings. From the development of medical devices and patient-specific surgical guides to dental appliances, the Form 4B brings speed and accuracy to life-altering procedures.
The Next Evolution in Industrial 3D Printing
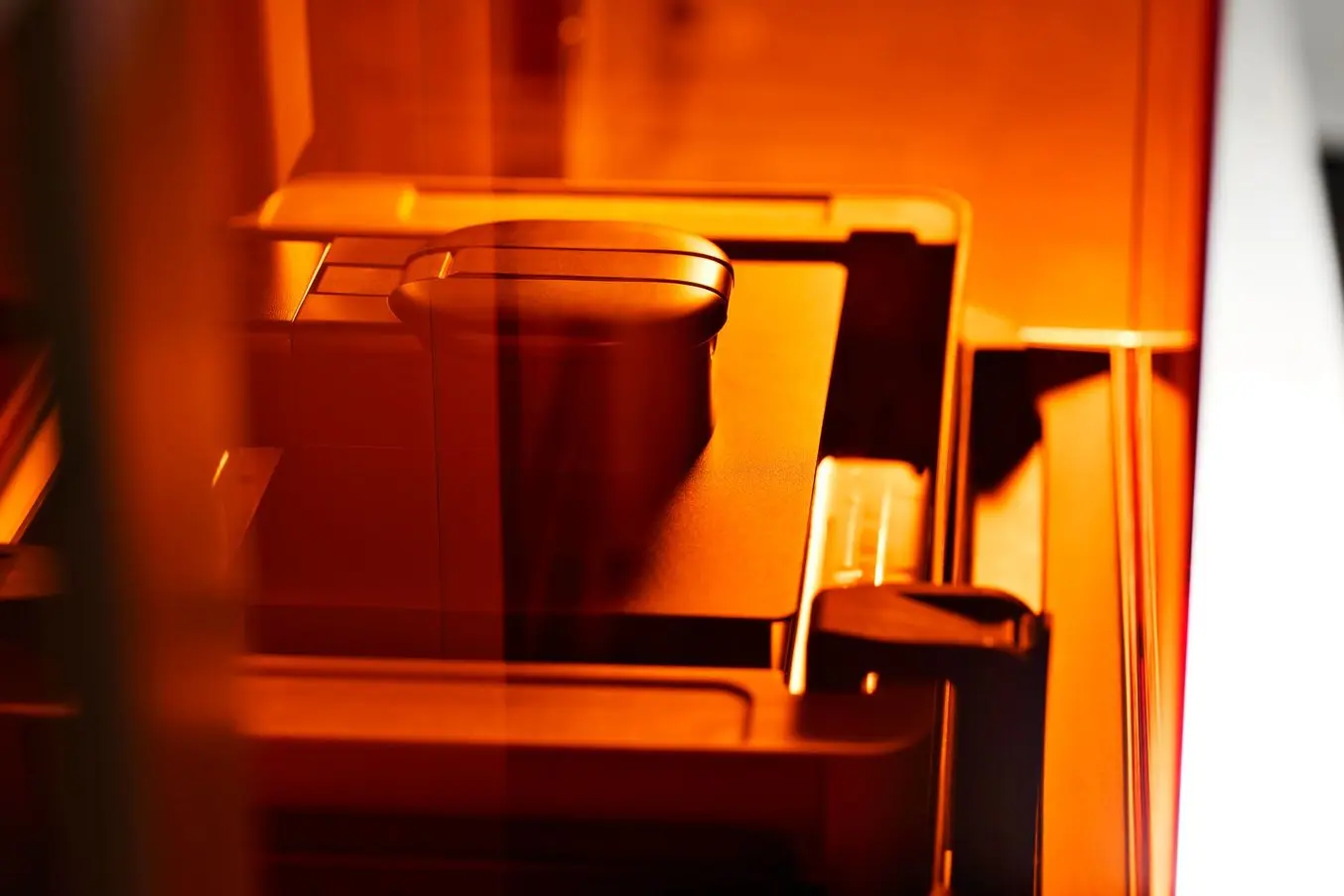
Form 4 and Form 4B represent the next evolution in stereolithography (SLA) 3D printing technology, built upon years of groundbreaking hardware, software, and materials science innovations.
Form 4 is setting a new standard for professional 3D printing. By combining the most diverse materials library available with a powerful new print engine, Form 4 printers enable new levels of creativity and productivity.
Iterate three times as fast, multiple times a day, so every possible angle is explored. Produce consistent parts at high volumes, without worrying about downtime or reliability issues. Take on more volume and respond to more requests to increase productivity across your organization.
With two to four times faster print speeds, a 30% larger build volume, unmatched reliability and precision, and the most rigorous quality engineering process in the industry, there is no limit to what Formlabs customers can achieve with Form 4.