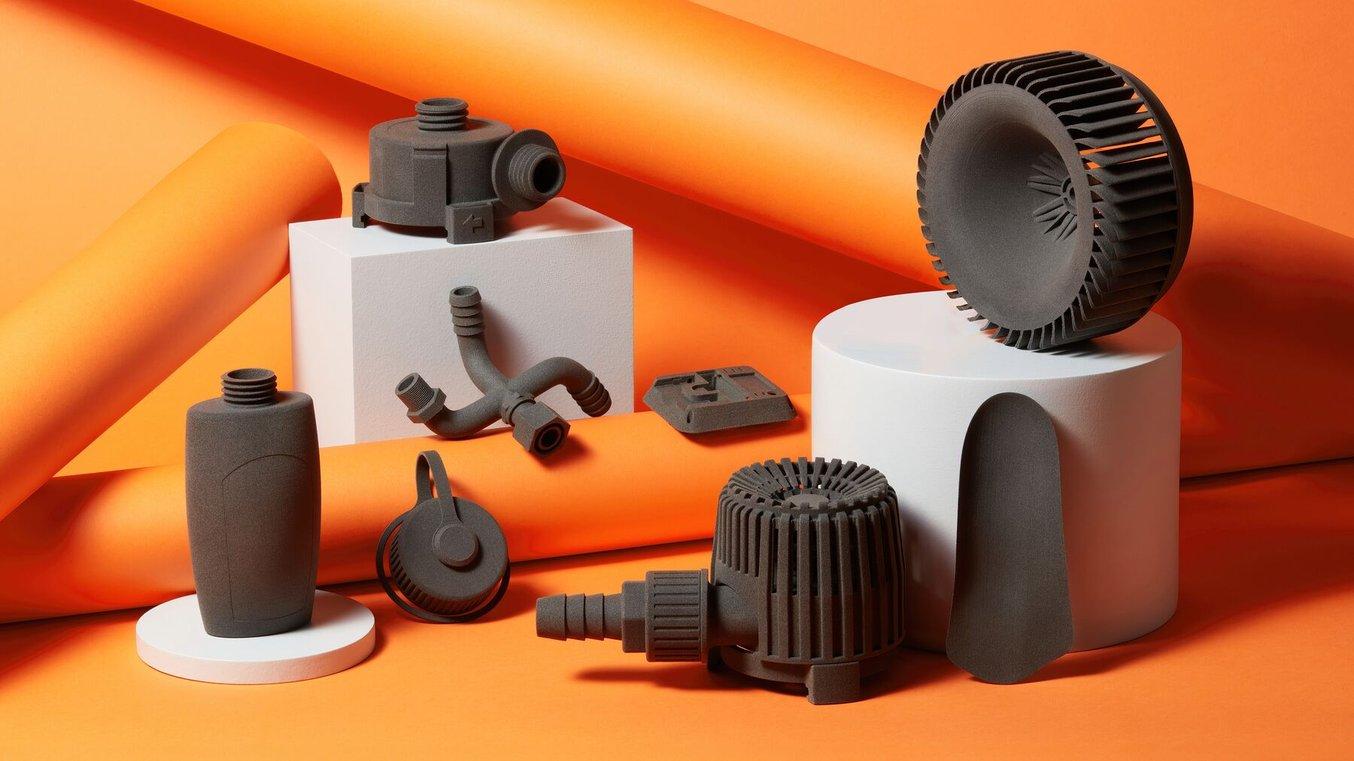
As 3D printing technologies become more advanced, engineers, manufacturers, and designers in every industry are starting to rely on 3D printed parts in each stage of the design to manufacturing process. Being able to use one material, like polypropylene, throughout that process provides huge benefits — lower costs and less chance of having to rework tooling, continuous adherence to regulatory standards, and a smooth path to validation for the manufacturing workflow.
Materials that are familiar to the industry but still provide the benefits of 3D printing are in high demand. Polypropylene, the second-most commonly produced commodity plastic in the world, is a thermoplastic that nearly everyone in the engineering and manufacturing industries understands and interacts with daily.
The ability to 3D print polypropylene means that users have access to the design freedom, rapid turnarounds, and supply chain flexibility inherent to 3D printing, while still being able to rely on familiar, standardized material properties. This guide will cover common applications for polypropylene as well as the advantages and disadvantages of creating polypropylene parts through traditional molding, FDM, SLS, MJF, and SLA 3D printing technologies.
What is Polypropylene?
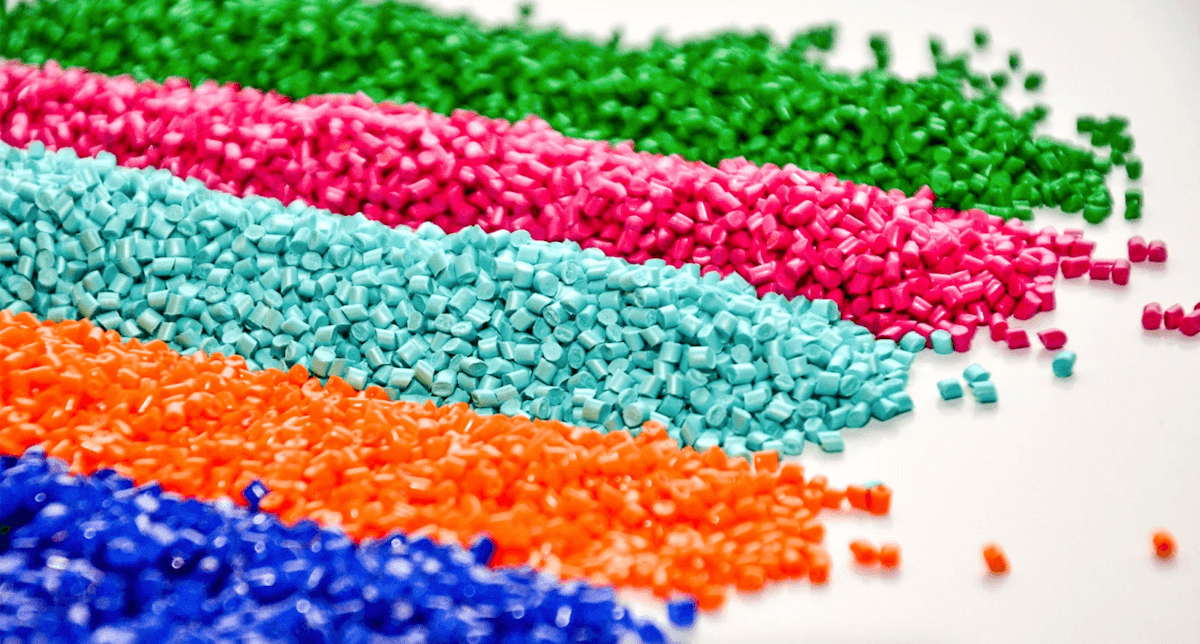
Polypropylene is highly colorfast, meaning that dyeing techniques are straightforward and pellets can be easily saturated with pigment. This characteristic makes it a good material choice for mass production of consumer goods. (image: All3dp.com)
Polypropylene (PP) is a polyolefin similar to polyethylene. It is a thermoplastic used in the manufacturing and consumer goods industries for the mass production of common items like plastic bottles. Polypropylene is formed by chain-growth polymerization of a single propylene monomer. It is extremely similar to another common commodity plastic, polyethylene. The two materials are sometimes combined during recycling processes to produce recycled polyolefin fibers. Though polypropylene was first developed in 1951 by American employees of Philips Petroleum, research and development are ongoing, and there is much promising research on bio-based polypropylene materials as well as novel recycling techniques.
Polypropylene Applications
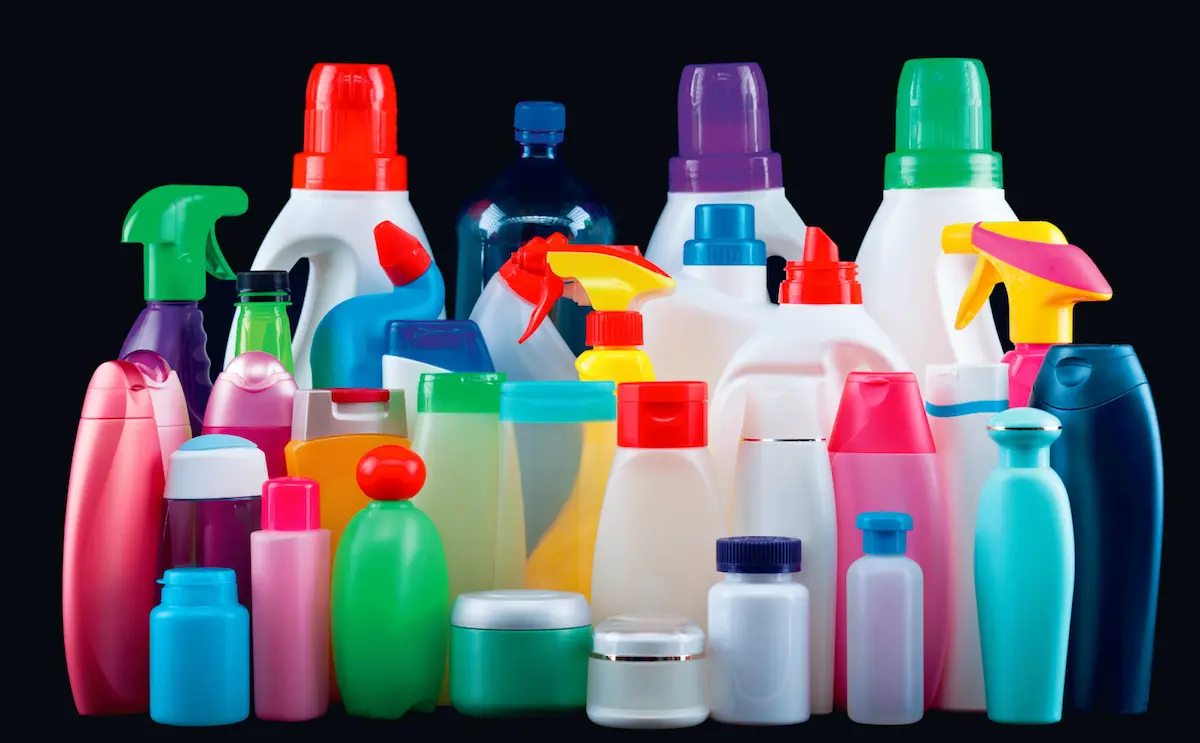
Polypropylene is one of the most common commodity plastics in the world; its ductility and low cost make it ideally suited for consumer goods packaging applications, such as bottles for cosmetics, cleaning products, and pharmaceuticals. (image: Adreco Plastics)
Polypropylene’s ductility, lightweightness, and chemical and water resistance make it ideal for consumer goods where walls are thin, but strength is necessary, such as in plastic food containers. Its most common use is for bottles of liquids like shampoo, motor oil, cleaning solutions, and others, as well as for laboratory tubes and bottles, food and pharmaceutical containers, and medical devices. A common use case for polypropylene materials is in the fabrication of plastic window shades.
Polypropylene’s ductile qualities make it ideal for the production of parts that have living hinges, such as the lids of candy containers or shampoo bottles. PP resists fatigue and can be used repeatedly even in these applications.
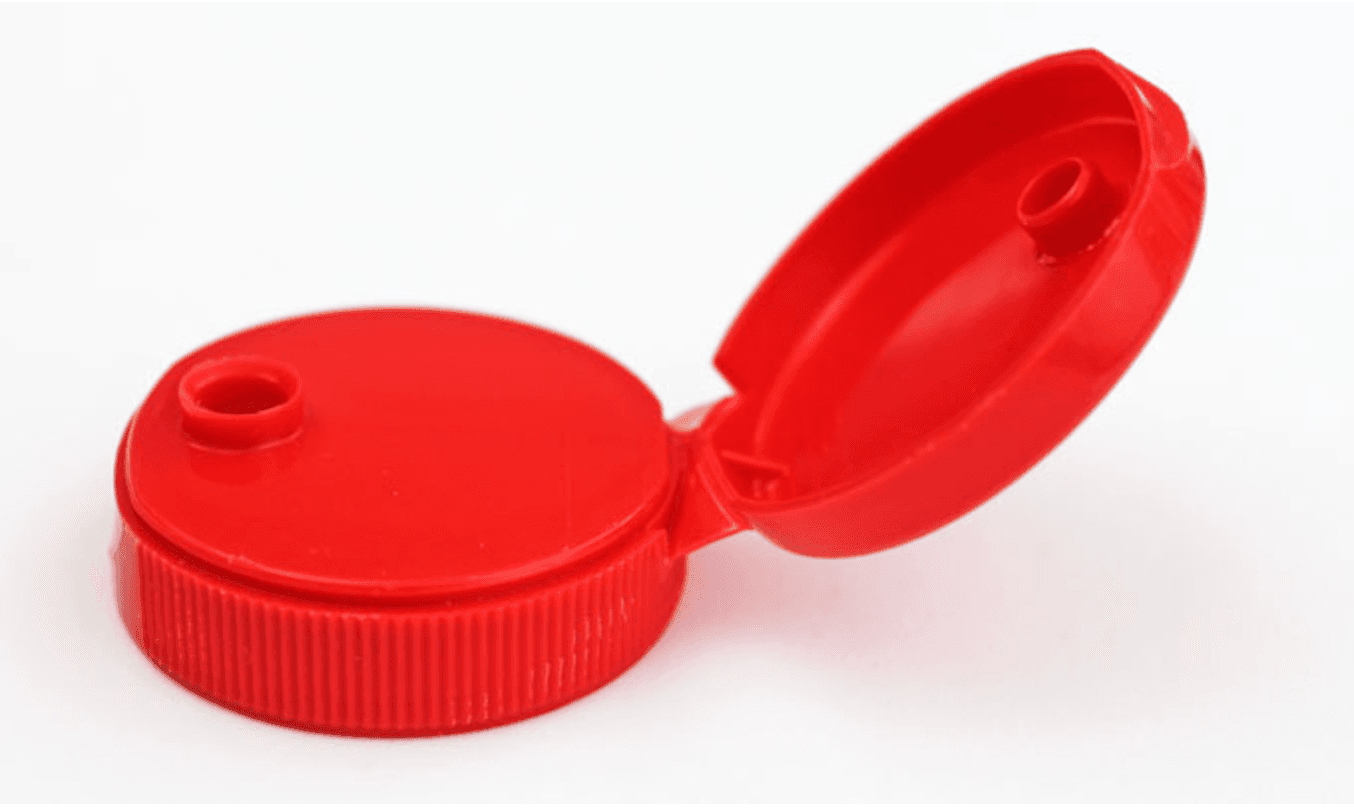
Polypropylene’s ductility makes it a good choice for design features such as living hinges, where components’ connections must be repeatedly bent without tearing. (image: RevPart)
Polypropylene Material Properties
Polypropylene materials are lightweight, watertight, chemically resistant, and ductile. The density of polypropylene is low, typically between 0.895 and 0.93 g/cm3, making it one of the lowest-density plastics available and thus well-suited for lightweight applications.
Polypropylene has good thermal resistance as well as hydrophobic and oleophobic qualities, leading to its common use in the food packaging industry. When combined with other compounds, polypropylene can become quite tough and be used for engineering applications where repeated pressure or impact occurs. The heat deflection temperature (HDT) of many forms of polypropylene materials is about 100 °C at 0.45 MPa, which, though not extremely high, makes it suitable for a wide range of applications.
Polypropylene Fabrication Methods
Polypropylene is most often molded, typically by injection molding molten polypropylene pellets, or thermoformed using sheets of polypropylene material. These methods of fabrication are extremely inexpensive per part for mass production and represent the vast majority of polypropylene production parts.
However, traditional mass manufacturing processes pose some serious disadvantages, such as the high up-front costs of tooling and the associated risk of obsolescence, lead times and necessary outsourcing, and the limits it puts on the product design and development process.
3D printing polypropylene has become more popular as hardware, software, and materials in the 3D printing industry have advanced. 3D printed polypropylene parts can exhibit the same material properties as injection-molded polypropylene parts, and offer the benefits inherent in additive manufacturing: design freedom, customization, efficiency, reduced waste, avoidance of obsolete tooling, and supply chain agility.
Polypropylene 3D Printing Technologies
There are multiple possibilities for 3D printing polypropylene materials, including selective laser sintering (SLS) or multi-jet fusion (MJF) with polypropylene powder, and fused deposition modeling (FDM) with polypropylene filament. There are also polypropylene-like materials available on stereolithography (SLA) printers that can accurately simulate polypropylene material properties.
Selective Laser Sintering (SLS) | Multi-Jet Fusion (MJF) | Fused Deposition Modeling (FDM) | Stereolithography (SLA) | |
---|---|---|---|---|
Resolution | ★★★★☆ | ★★★★☆ | ★★★☆☆ | ★★★★★ |
Accuracy | ★★★★★ | ★★★★★ | ★★★★☆ | ★★★★★ |
Surface Finish | ★★★★☆ | ★★★★☆ | ★★☆☆☆ | ★★★★★ |
Throughput | ★★★★★ | ★★★★★ | ★★★☆☆ | ★★★★☆ |
Complex Designs | ★★★★★ | ★★★★★ | ★★★☆☆ | ★★★★★ |
Ease of Use | ★★★★☆ | ★★★☆☆ | ★★★★★ | ★★★★★ |
Material Properties | ★★★★★ | ★★★★★ | ★★★☆☆ | ★★★☆☆ |
Materials Available | Polypropylene, nylon | Polypropylene, nylon | Polypropylene, nylon | Polypropylene-like materials: Tough 1500 Resin, Durable Resin |
Cost | Benchtop industrial SLS 3D printers start just under $30,000 for the printer and $60,000 for the entire ecosystem, including powder management and cleaning stations. Traditional industrial SLS printers start at around $200,000. | Starting at $350,000. | Budget printers capable of printing PP start at $1,000, mid-range printers around $3,500, and industrial systems from $15,000. | Professional SLA 3D printers cost around $2,500 to $10,000, and large-format resin 3D printers are in the $5,000 to $25,000 range. |
Pros | High-quality parts Design freedom No need for support structures High throughput Simplified workflow Small footprint Low maintenance | Large build volume High-quality parts Design freedom No need for support structures High throughput | Low-cost consumer machines and materials Fast for simple, small parts Wide variety of colors | Affordable High-Quality Parts Design Freedom |
Cons | Moderate build volume | Expensive machinery Large footprint Facility requirements Requires a dedicated operator | Low accuracy Lower quality parts Anisotropic Limited design freedom Requires supports | Not true polypropylene |
Applications | Functional prototyping Short-run, bridge, or custom manufacturing | Functional prototyping Short-run, bridge, or custom manufacturing | Low-cost rapid prototyping Basic proof-of-concept models | Functional prototyping |

How to Choose a 3D Printing Technology
Having trouble finding the best plastic 3D printer for your needs? In this video guide, we compare FDM, SLA, and SLS technologies across popular buying considerations.
Selective Laser Sintering (SLS) 3D Printing Polypropylene
Selective laser sintering (SLS) is fast becoming one of the most popular methods for 3D printing durable, end-use quality parts. SLS technology uses a high-powered laser to fuse small particles of polymer powder together. The unfused powder supports the part during printing and eliminates the need for dedicated support structures.
Polypropylene powders for SLS 3D printers are not available from all manufacturers, so it’s important to confirm when choosing an SLS 3D printer that it does offer PP powder as part of its material library.
Polypropylene Powder for SLS 3D Printing
Polypropylene powder, while not the most common material used for SLS 3D printing (which is nylon), is still a very popular material offered by industrial SLS 3D printer manufacturers.
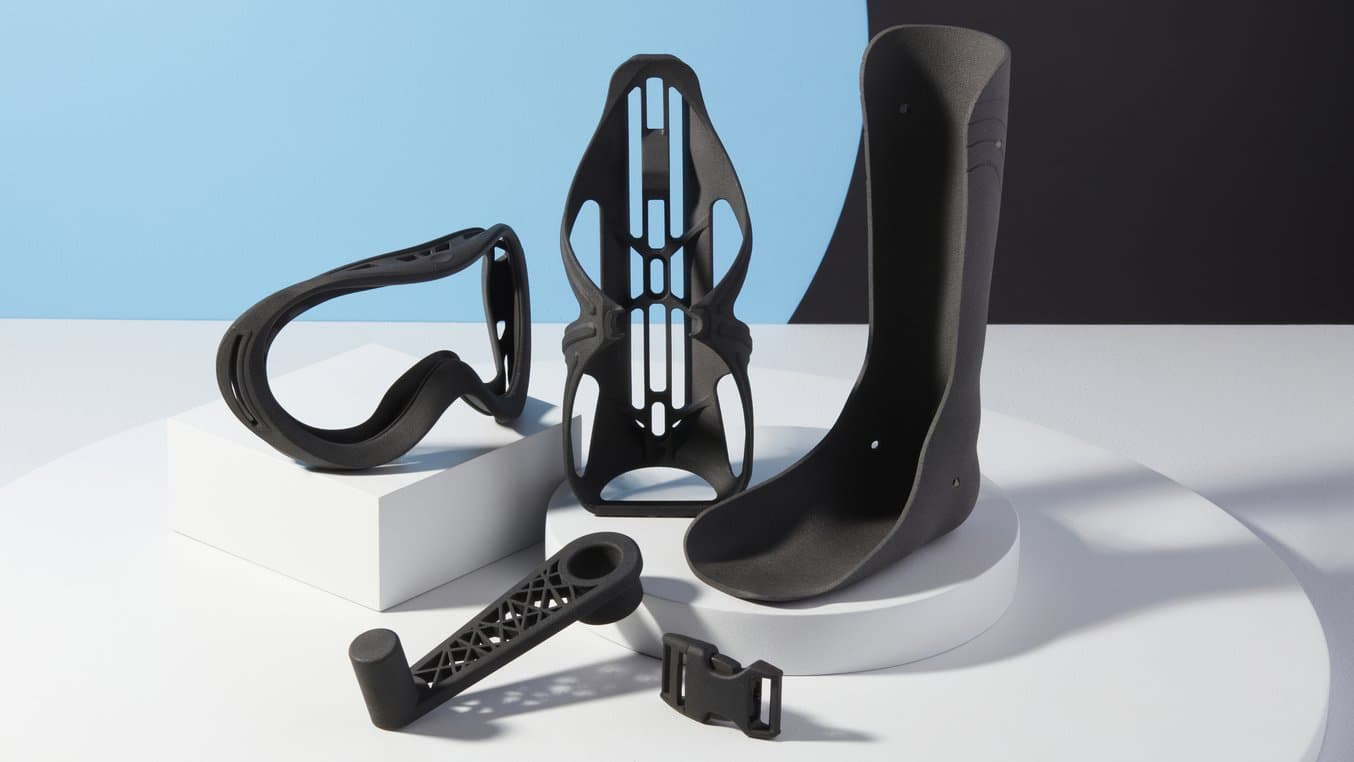
Nylon 11 Powder offers similar properties to polypropylene.
Formlabs currently offers Nylon 12 Tough and Nylon 11 Powder for 3D printing parts with polypropylene-like properties. Nylon 12 Tough Powder is less ductile than polypropylene, but is considerably tougher. For the highest possible elongation at break and toughness, choose Nylon 11 Powder (for best results, Nylon 11 Powder requires inert atmospheric control).
How to Print Polypropylene-Like Parts With SLS Technology
3D printing parts with SLS technology can produce single prototypes or low- to mid-volume production runs. The SLS workflow involves a pre-print step to pack parts efficiently within the powder bed.
Packing density and refresh rate are important factors to increase efficiency and lower cost per part. This step can be made simpler — especially for higher volume production — by employing a packing algorithm such as Formlabs’ PreForm packing algorithm, or Autodesk’s NetFabb solution. Formlabs Nylon 12 Tough Powder has a refresh rate of 20%, meaning that 80% of every build chamber can be recycled powder. This means that less powder overall is used, and the cost per part stays quite low.
When the print has completed, there are additional post-processing steps: powder removal and media blasting. Some SLS printer manufacturers offer complete ecosystems for these steps, while others do not, so additional, third-party equipment might be necessary for depowdering and blasting process. Formlabs Fuse Sift and Fuse Blast make it easy to post-process SLS parts, improving powder usage efficiency and the cleanliness of your SLS printing space.
Post-processing solutions such as vapor smoothing, vibratory tumbling (also known as vibratory finishing), ceramic coating, or dyeing can improve both the aesthetics and mechanical performance of SLS 3D printed parts.
Pros and Cons of SLS 3D Printing Polypropylene
Polypropylene 3D printed parts from an SLS 3D printing system are close to isotropic, which means they display similar material properties under stress along all axes. This isotropic quality makes it possible to have 3D printed polypropylene parts function in end-use environments, where force or impact can come from multiple — or unforeseen — directions. FDM printers cannot create isotropic parts, and so FDM 3D printed polypropylene filaments will produce parts that can split under impact along their layer lines.
SLS 3D printing is a powerful way to prototype, and because polypropylene is so commonly used for consumer goods, SLS 3D printing polypropylene creates opportunities for reimagining consumer products, increasing iterative frequency, and giving small or medium-sized businesses the tools to create parts and bring them to market without outsourcing large parts of their workflow. With end-use quality 3D printed polypropylene parts, the design to manufacturing process is tighter, more efficient, and more cost-effective.
Multi Jet Fusion (MJF) 3D Printing Polypropylene
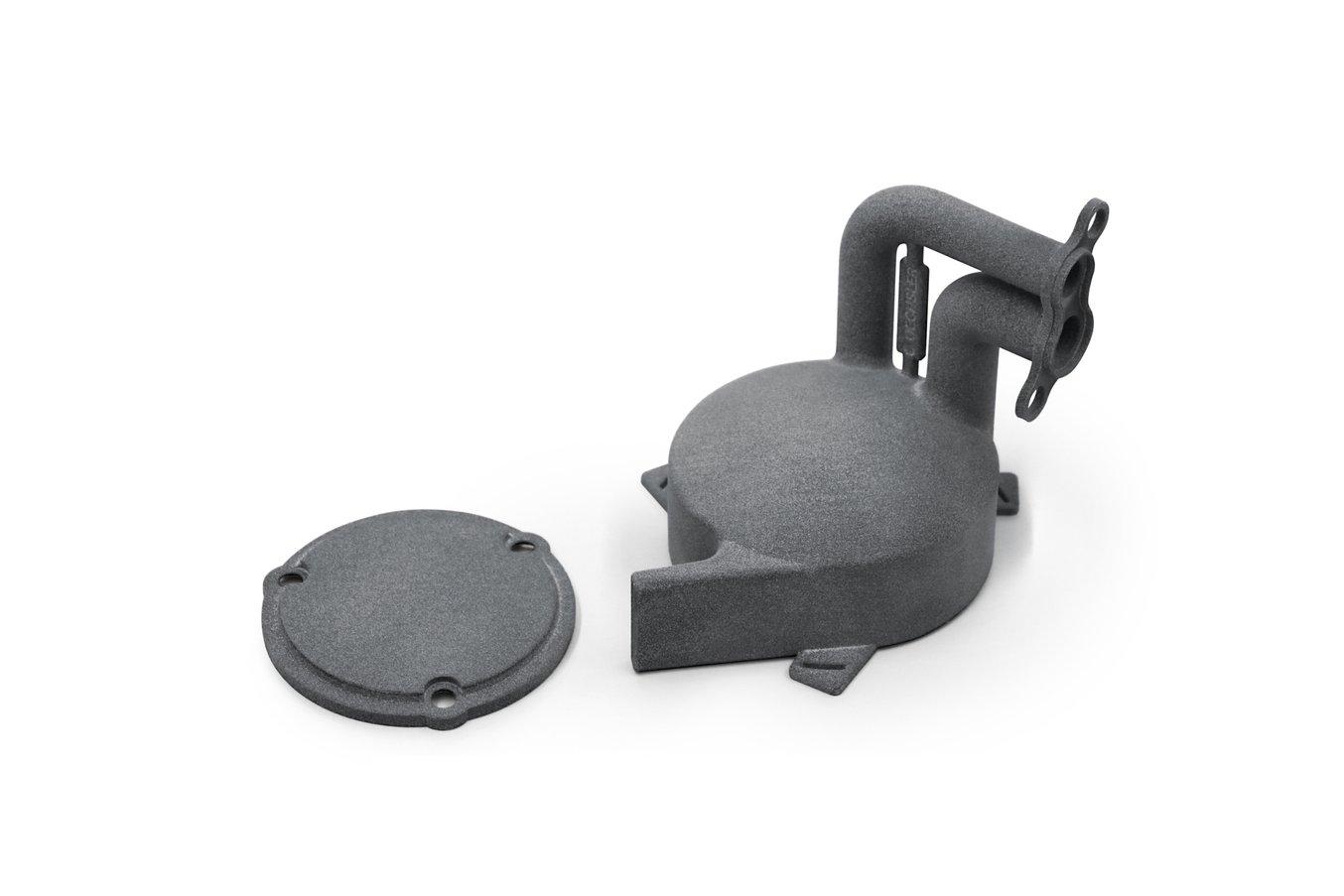
MJF printers by HP are well-suited for low- to mid-volume production runs for polypropylene parts. (image: Make Parts Fast)
Multi Jet Fusion is a powder bed fusion additive manufacturing process patented and solely provided by Hewlett Packard (HP). MJF 3D printers produce parts by dispensing a liquid binding agent onto a bed of polymer powder particles to bring them to a semi-solid state before curing the layer with an infrared heat source and beginning the next layer.
Polypropylene Powder for MJF 3D Printing
HP has offered an MJF polypropylene powder material since 2020. MJF customers leverage PP powder’s ability to create true polypropylene parts in order to create continuity in the prototyping and design stages, so that when prototyping turns to mass production, the polypropylene material properties can remain the same throughout. HP’s polypropylene powder offers an elongation at break of 20% and an ultimate tensile strength of 30 MPa, making it similar in performance to the Formlabs Polypropylene Powder for the Fuse Series, but with a slightly less favorable elongation at break.
How to Print Polypropylene Parts With MJF Technology
Only one of the five HP MJF printer models is compatible with their PP powder, so customers should confirm that the right model before purchase.
Printing polypropylene powder parts on the HP MJF printers requires many of the same steps as SLS 3D printing polypropylene. Because many of the MJF printers are larger than the Fuse Series, a packing algorithm should be used to avoid unnecessary powder waste. MJF printers require dedicated electrical circuits, large floor areas, and often a dedicated operator who has been trained in running the machine.
After printing, parts undergo depowdering and media blasting steps, and can then be post-processed with a range of options to achieve an end-use quality finish. These post-processing methods can help take polypropylene parts from prototype to final production quality.
Pros and Cons of MJF 3D Printing Polypropylene
MJF 3D printing polypropylene delivers parts that accurately represent the material properties of injection molded polypropylene, an important quality for anyone looking to maintain one material throughout the design and production stages. MJF printers create high-quality parts reliably and can be used for production volumes due to their larger build chambers.
However, MJF printers are costly, and can often cost upwards of $340,000, including annual service contracts, dedicated infrastructure requirements, and expensive powder.
Fused Deposition Modeling (FDM) 3D Printing Polypropylene
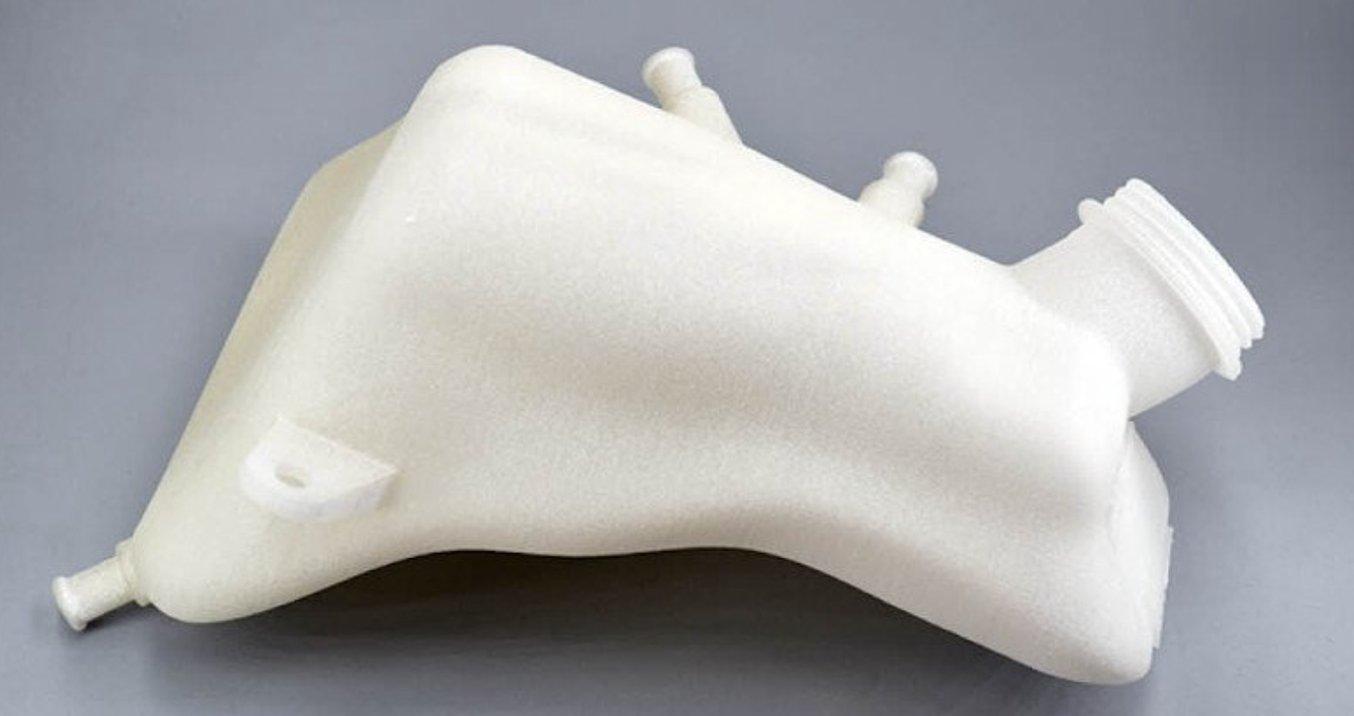
FDM polypropylene filament can be used for quick prototypes, like this engineering component printed on an FDM printer. (image: Sculpteo)
FDM 3D printing is the most well-known 3D printing process due to its ubiquity and low barrier to entry. Known as the ‘hot glue gun’ method, FDM printers melt and extrude plastic filament in the shape of the part, laying down the material layer by layer. FDM 3D printing polypropylene filament is available for many manufacturers, but FDM 3D printed polypropylene parts can rarely match the material properties of traditionally fabricated polypropylene parts.
Polypropylene Filament for FDM 3D Printing
Many manufacturers offer polypropylene filament options, but they are more expensive than other, more common FDM 3D printing materials such as ABS or PLA filament. The higher HDT of polypropylene means that FDM 3D printers need to maintain a high temperature for both the extruder and print chamber, so it is important to confirm compatiblity before choosing an FDM printer or buying filament to create polypropylene parts.
FDM 3D printed polypropylene isn’t suitable for more advanced applications like end-use parts, where SLS and MJF 3D polypropylene powder excels. There are budget printers capable of printing PP starting at $1,000, mid-range printers that cost approximately $3,500, and industrial systems that start at around $15,000.
How to Print Polypropylene Parts With FDM Technology
Polypropylene filament is harder to print with than standard FDM materials. It requires an extruder temperature of around 240 °C with a bed temperature of 85-120 °C. Printing polypropylene parts on an FDM printer also requires the printer to have a cooling fan — polypropylene filament can warp during the cooling or setting stage, and a fan can help mitigate the risk of this by evenly distributing the cooler air around the part.
Pros and Cons of FDM 3D Printing Polypropylene
FDM 3D printing polypropylene is a good method for creating quick, inexpensive early-stage prototypes or ‘looks-like’ models. The accessibility of many FDM 3D printers, both in cost and workflow, makes it a good technology for hobbyists looking to design consumer goods, or product designers who want an early physical model before starting more intensive design stages.
FDM 3D printers do not create isotropic or watertight parts, so FDM polypropylene parts can’t effectively function as bottles, enclosures, or tubing, which are common polypropylene applications.
Stereolithography (SLA) 3D Printing With Polypropylene-Like Materials
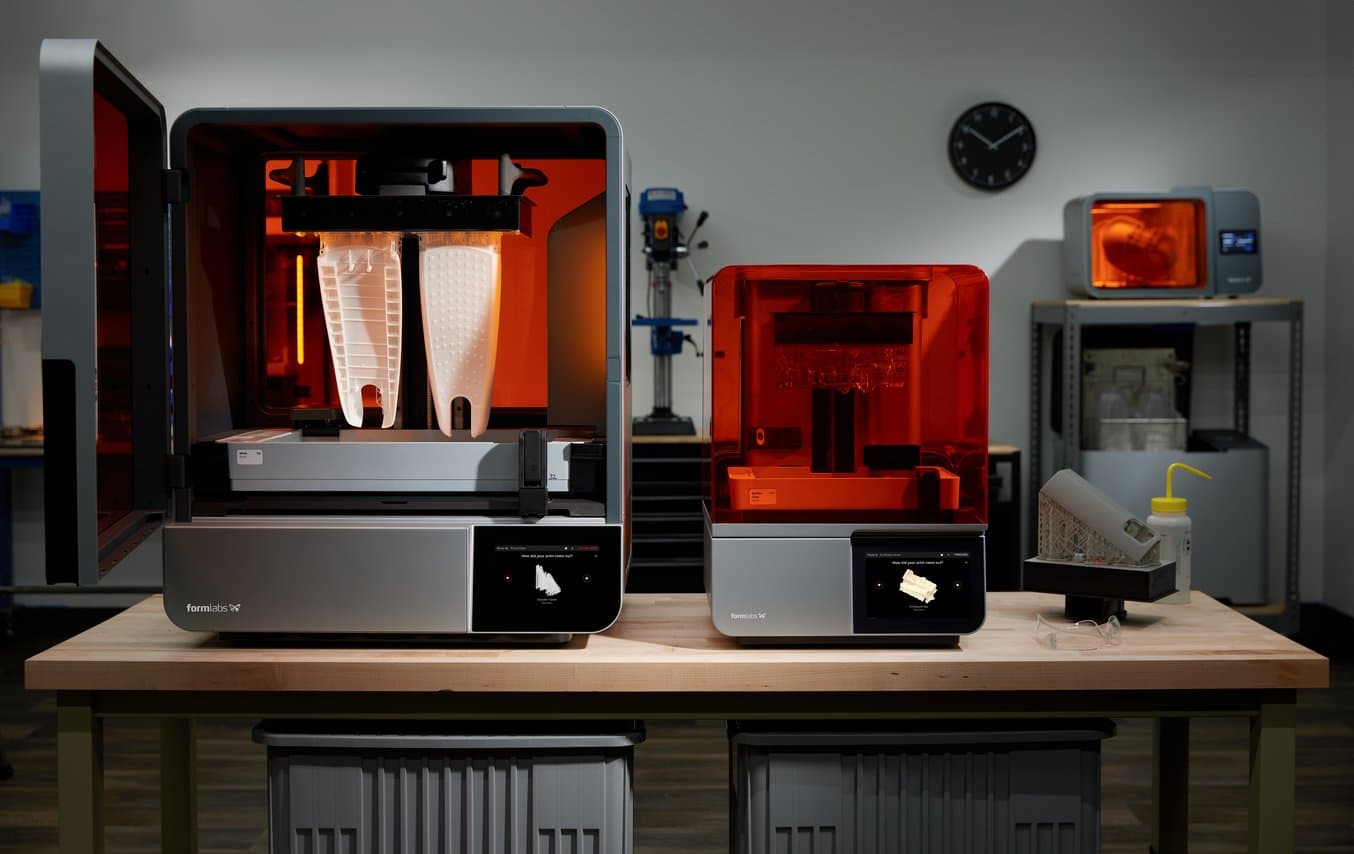
SLA printers like the Form 4L (left) and the Form 4 (right), are great complements to the product development workflow. Printing with a polypropylene-like resin, such as Tough 1500 Resin, could be a quick way to produce early prototypes before moving onto functional testing or larger runs with injection molded polypropylene.
Stereolithography (SLA) 3D printing technology uses a laser or light source to cure liquid resins one thin layer at a time, creating a part that is isotropically and chemically bonded between layers as well as physically. SLA 3D printer manufacturers produce their own materials — industry-standard materials such as ABS, PLA, or nylon don’t have one-to-one equivalents in SLA resin materials libraries, so there is no ‘true’ polypropylene resin on the market.
However, many manufacturers offer resins that can match nearly all polypropylene material properties, and service as adequate replacements in the design and prototyping workflows before mass manufacturing with traditionally fabricated polypropylene parts.
Polypropylene-Like Resins for SLA 3D Printing
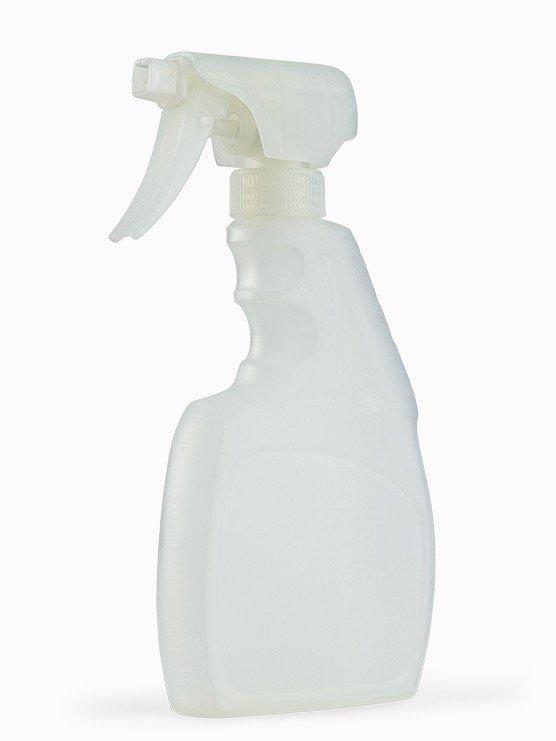
Formlabs' Durable Resin is a good substitute for polypropylene during the prototyping process. With an elongation at break of 55%, Durable Resin is a good choice for consumer goods packaging, like this bottle.
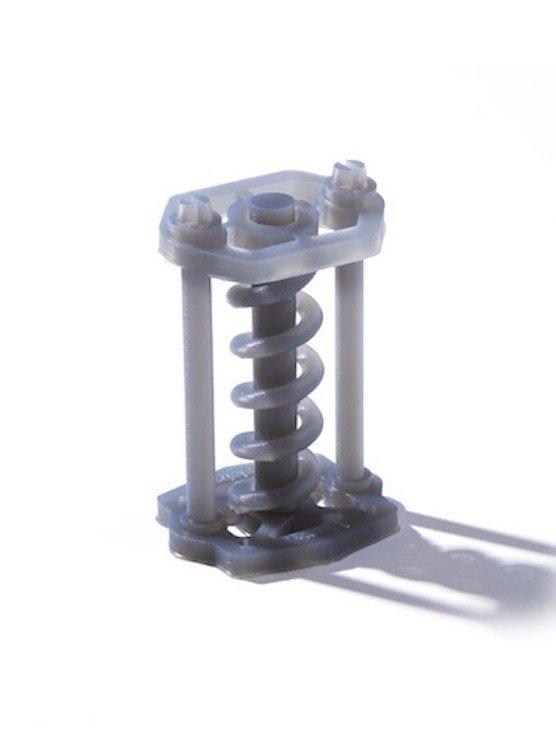
Formlabs' Tough 1500 Resin has a higher tensile strength (33 MPa) than Durable Resin and is slightly more flexible than injection molded polypropylene.
Formlabs offers multiple resins that are ideally suited for prototyping in applications where polypropylene will eventually be used, such as consumer goods packaging. Because there are many different grades of polypropylene, there is more than one resin that can take its place in certain applications.
Tough 1500 Resin offers very similar material properties to injection molded polypropylene. With an ultimate tensile strength of 33 MPa and an elongation at break of 51%, it’s slightly more flexible than injection molded polypropylene.
Durable Resin offers similar elongation, at 55%, but a lower ultimate tensile strength at 28 MPa, and more often is used in place of polyethylene materials.
How to Print Polypropylene-Like Resins With SLA 3D Technology
The workflow for printing polypropylene-like materials with SLA technology depends on the printer manufacturer. Printer workflows and costs can range from entry-level costs and easy workflows to complex workflows and high-cost machines. Formlabs' Form Series SLA printers are inexpensive and the workflow is intuitive and clean.
Once choosing a resin to simulate polypropylene, insert the resin cartridge into the back of the printer and start the print. After the print is done, parts will need to be washed, and, if using Tough 1500 Resin or Durable Resin, will need a post-cure. These two steps can be streamlined using the Formlabs post-processing solutions the Form Wash or Form Wash L and the Form Cure or Form Cure L.
Pros and Cons of SLA 3D Printing With Polypropylene-Like Resins
SLA 3D printing with PP-like materials is ideal for high-quality functional prototypes and prototyping parts normally produced with polypropylene. For SLA customers who are already printing with SLA printers, using Tough 1500 Resin or Durable Resin to simulate polypropylene parts is an easy and inexpensive way to achieve similar mechanical performance. Switching between resins is simple and requires no cleaning step.
The major downside to printing with these resins is that they are not true polypropylene materials, so there will be some gap in the continuity between design and production if using these for prototyping or design.
Getting Started With 3D Printed Polypropylene
3D printing polypropylene solutions are becoming more widely available as 3D printer manufacturers of SLS, MJF, FDM, and SLA technologies are introducing more polypropylene filaments and powders, as well as resins that can mimic polypropylene properties.
To get started with 3D printing polypropylene parts, first consider what features you need from a 3D printer and for your unique workflow. For fast, inexpensive early-stage prototyping, polypropylene filament for FDM 3D printing may be the most efficient option. For higher-quality functional prototypes, SLA printing with a resin such as Tough 1500 Resin or Durable Resin is a good way to achieve many of polypropylene’s benefits. For true polypropylene that is watertight and creates parts that can endure functional testing and end use, SLS and MJF 3D printing are the best choices.
The Fuse Series SLS ecosystem makes creating industrial-quality polypropylene-like parts accessible. Have some questions about the right solution? Get in touch with our experts.