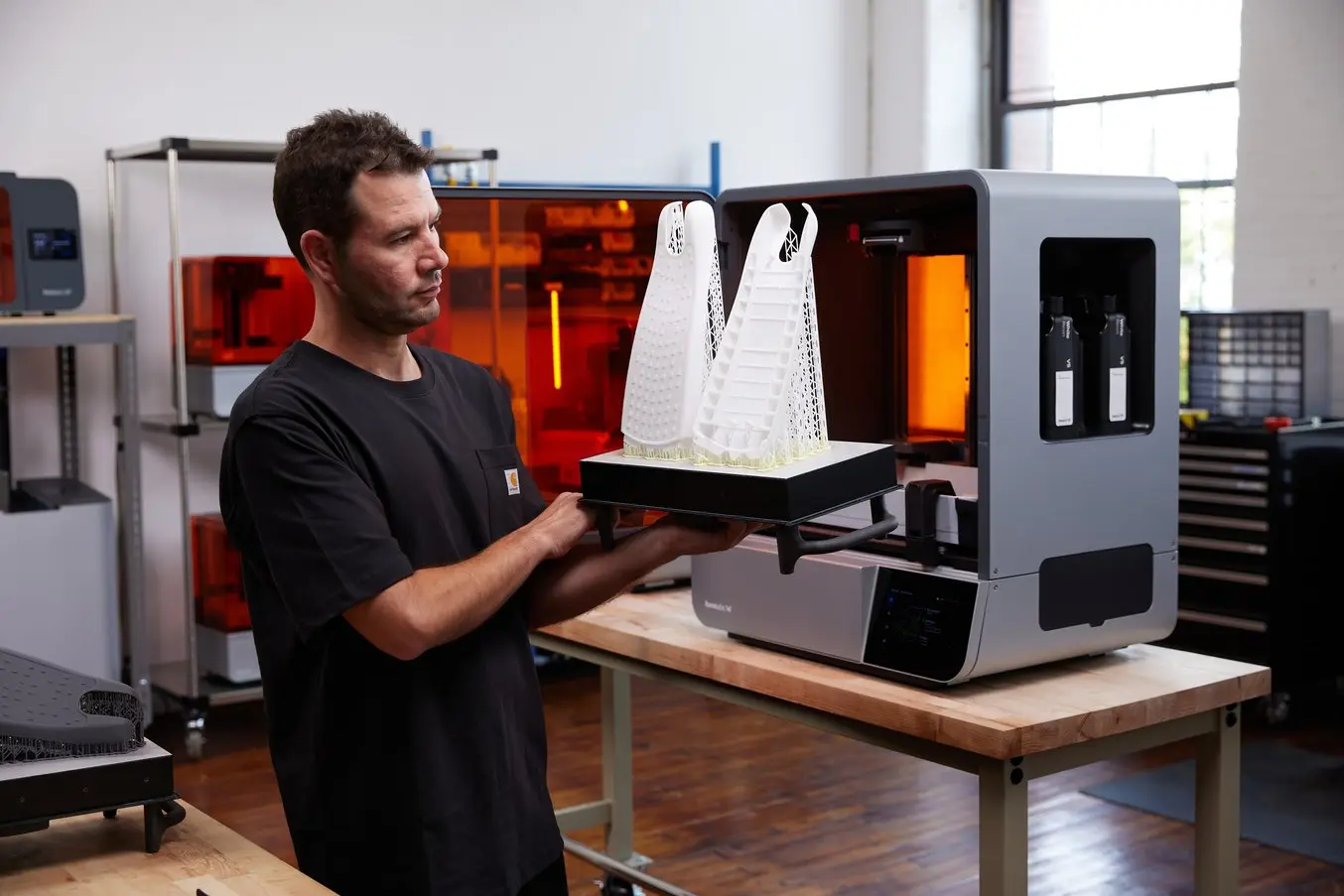
In the past decade, technological advances have made resin 3D printing, also known as vat photopolymerization, one of the foremost methods for producing highly detailed 3D printed parts for rapid prototyping, rapid tooling, manufacturing aids, and even end-use parts due to its high accuracy, fast printing speed, wide range of materials, and isotropic mechanical properties.
As resin 3D printer manufacturers have introduced innovations in hardware, software, and materials science, different types of resin 3D printing processes have proliferated.
For many years, the two main types of resin 3D printers were broadly defined as stereolithography (SLA) and digital light processing (DLP). More recently, subsets of those technologies have been introduced and further delineated, including liquid crystal display (LCD) and masked stereolithography (MSLA) 3D printing.
While all of these resin 3D printing technologies were once complex and cost-prohibitive, today’s compact desktop and benchtop resin 3D printers can produce industrial-quality parts at an affordable price point and with excellent mechanical and aesthetic properties.
This guide will cover the details and advantages of each type of resin 3D printing process, as well as discuss their costs and the applications where each type of printer might perform best.
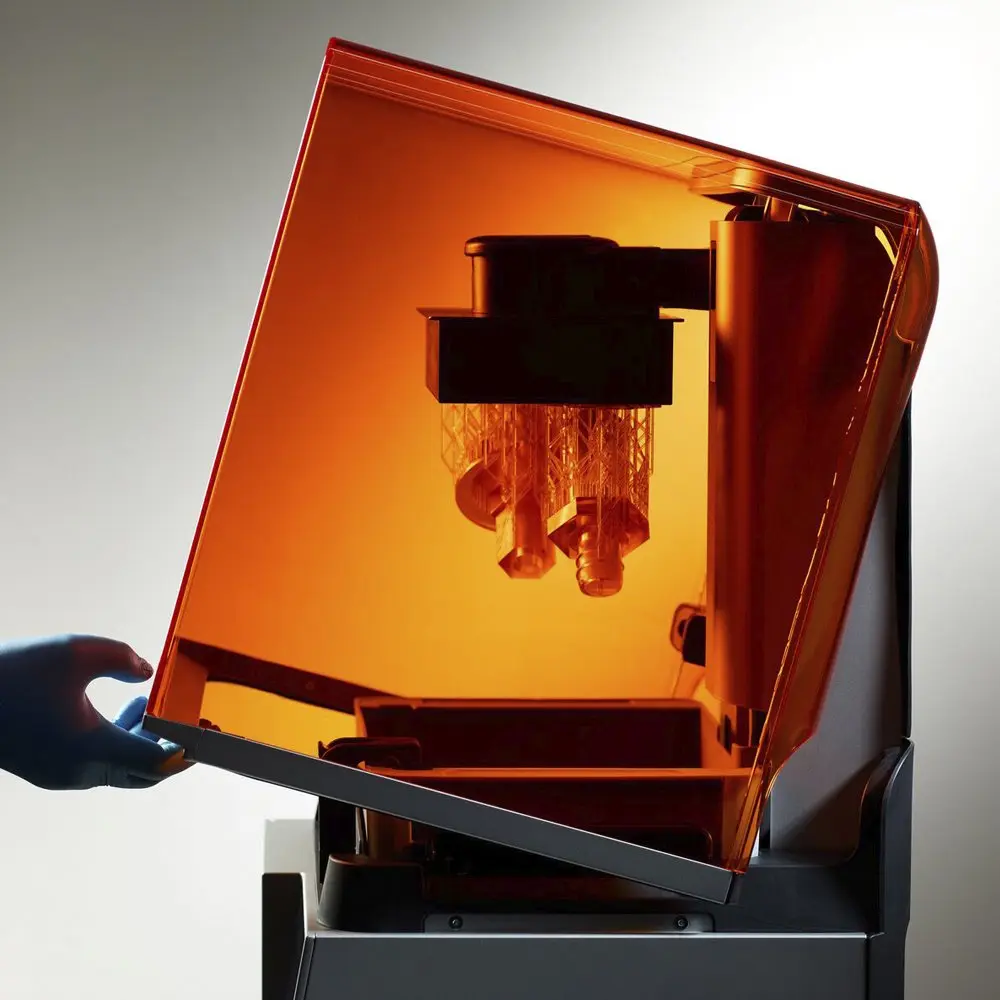
Guide to Stereolithography (SLA) 3D Printing
Looking for a 3D printer to realize your 3D models in high resolution? Download our white paper to learn how SLA printing works and why it's the most popular 3D printing process for creating models with incredible details.
What is SLA 3D Printing?
Traditional SLA printers were built around large vats filled with liquid resin where the top layer was selectively cured by the laser positioned above the tank. These systems were large, prohibitively expensive, and required complex infrastructure, limiting their use to the likes of Fortune 500 companies.
Formlabs introduced inverted stereolithography 3D printing in 2011 with the Form 1. With the inverted SLA process, a light source (a laser in Form 1) cures the cross-section of the part through a transparent-bottomed resin tank, meaning only a thin layer of resin needs to be dispensed and available for curing at any time. This technology makes it possible to fabricate resin parts using a much smaller printer that fits on a desktop.
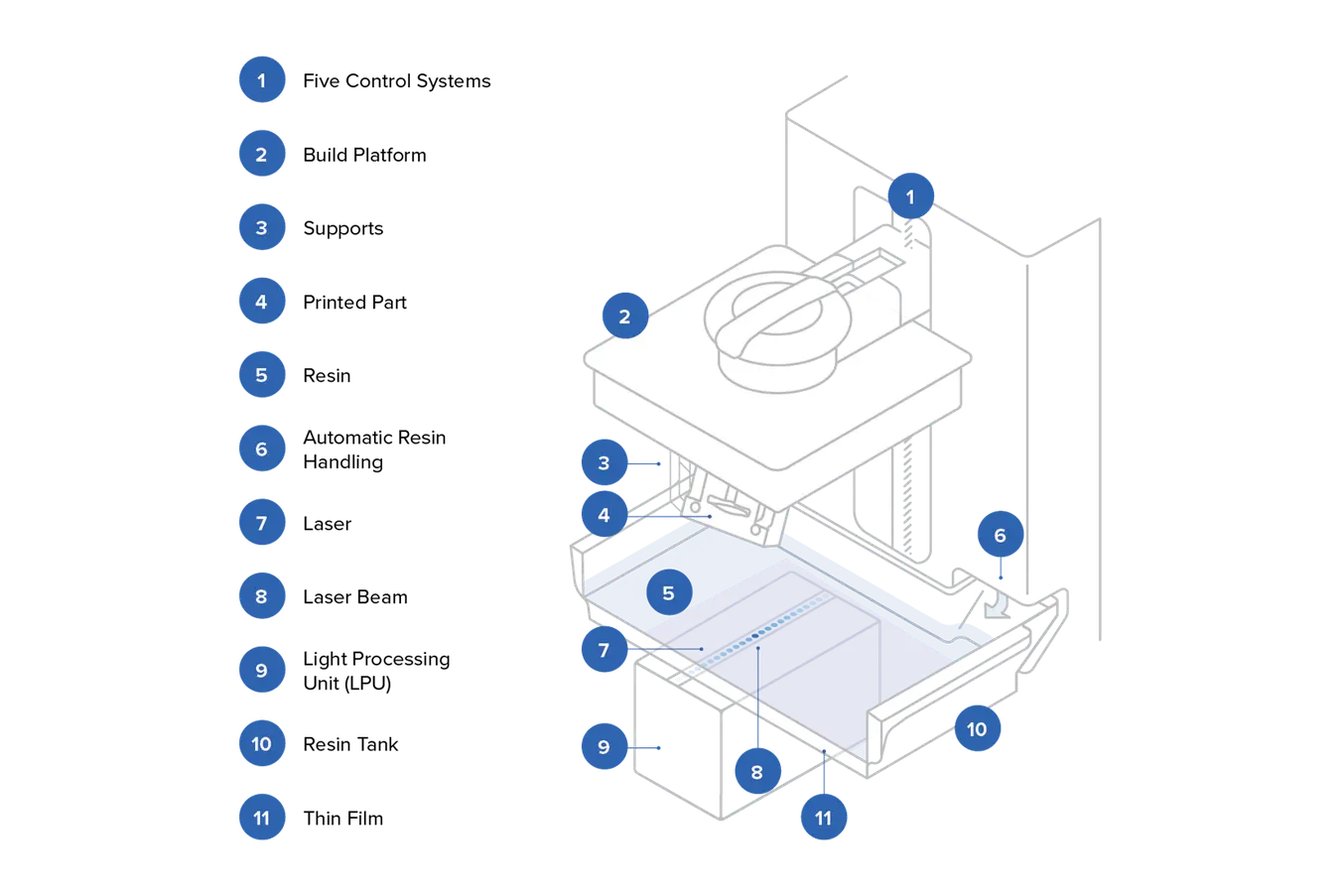
A graphic representation of Formlabs’ Low Force Stereolithography™ (LFS) Print Engine, an advanced form of SLA 3D printing.
With the introduction of Form 2 in 2015 and the subsequent release of a wider range of materials, SLA 3D printing became much more reliable and useful for professionals in a range of different environments.
In 2019, Formlabs introduced Low Force Stereolithography (LFS) with Form 3 and Form 3L SLA 3D printers, which use a flexible-bottomed resin tank to peel the cured part away from the bottom of the tank, which drastically reduces the forces exerted on parts during the print process.
This advanced form of stereolithography delivers vastly improved surface quality and print accuracy. Lower print forces also allowed for light-touch support structures that tear away with ease, enabled larger build volume, and opened up possibilities for advanced, production-ready materials.
What is DLP 3D Printing?
Digital light processing (DLP) 3D printing is a resin 3D printing process that uses a light projector rather than a laser to cure liquid resin one layer at a time.
DLP printers’ light source is projected using a series of micromirror devices laid out in a matrix on a semiconductor chip. These micromirror devices each represent a single voxel (or 3D pixel) of the part. The number of micromirror devices and size of the build area determines the resolution of the part.
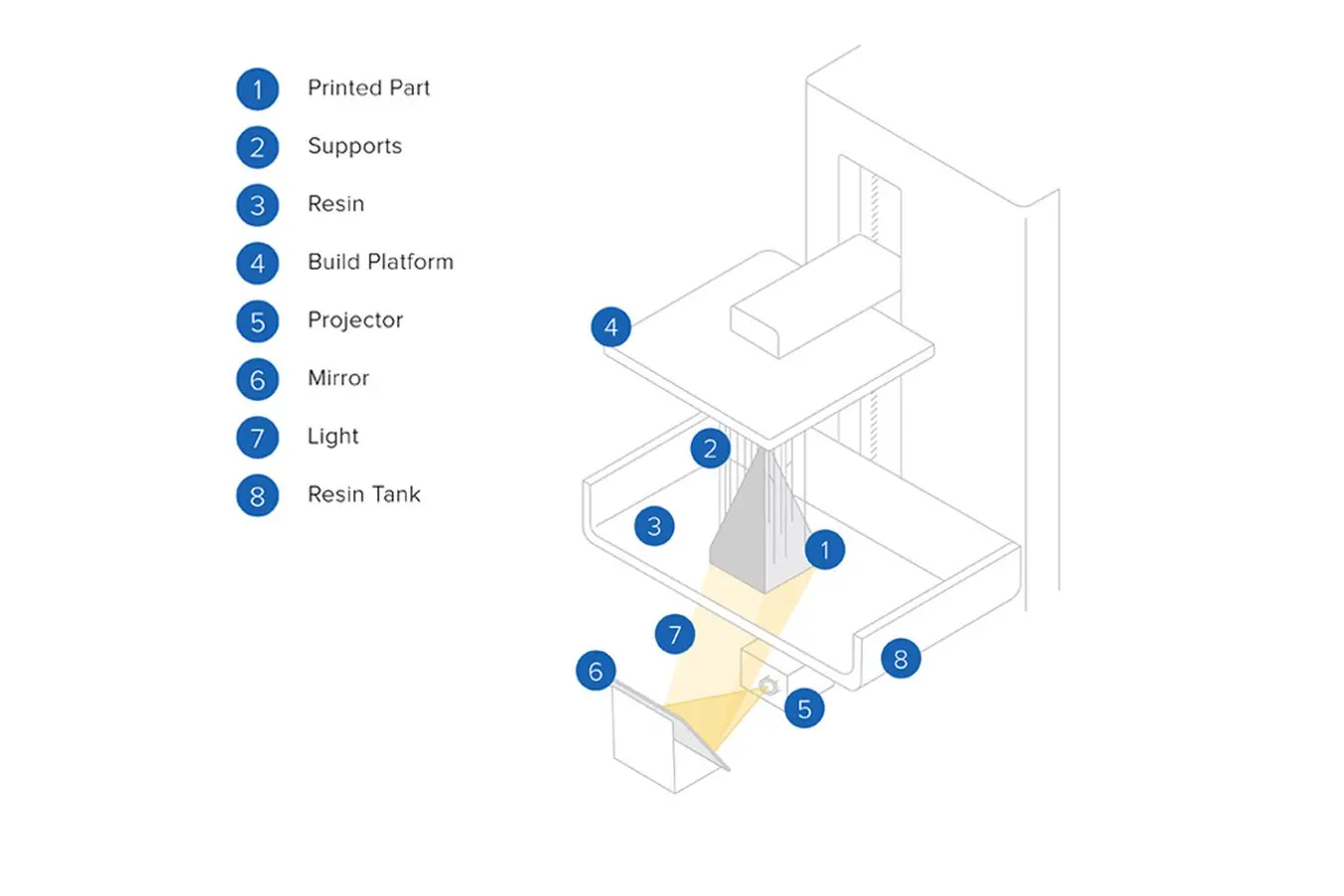
A graphic representation of digital light processing (DLP) 3D printing.
Because the light is projected in an instant over the complete cross-section of the part, each layer cures very quickly. As a result, DLP 3D printers generally offer faster printing speed.
In the same way that inverted SLA 3D printing enabled the creation of desktop units rather than large, top-down traditional printers, inverted DLP printers have become more affordable and accessible thanks to more compact desktop units.
What is MSLA 3D Printing (or LCD 3D Printing)?
Masked stereolithography (MSLA) 3D printing technology refers to any photopolymerization process where a light source is selectively covered, or masked. It is often used interchangeably with LCD 3D printing, because MSLA printers generally use LCD screens to mask the light and cure only the desired cross-section of the part. However, MSLA can refer to other technologies as well, because it means masked resin 3D printing, regardless of the type of light source or masking technique.
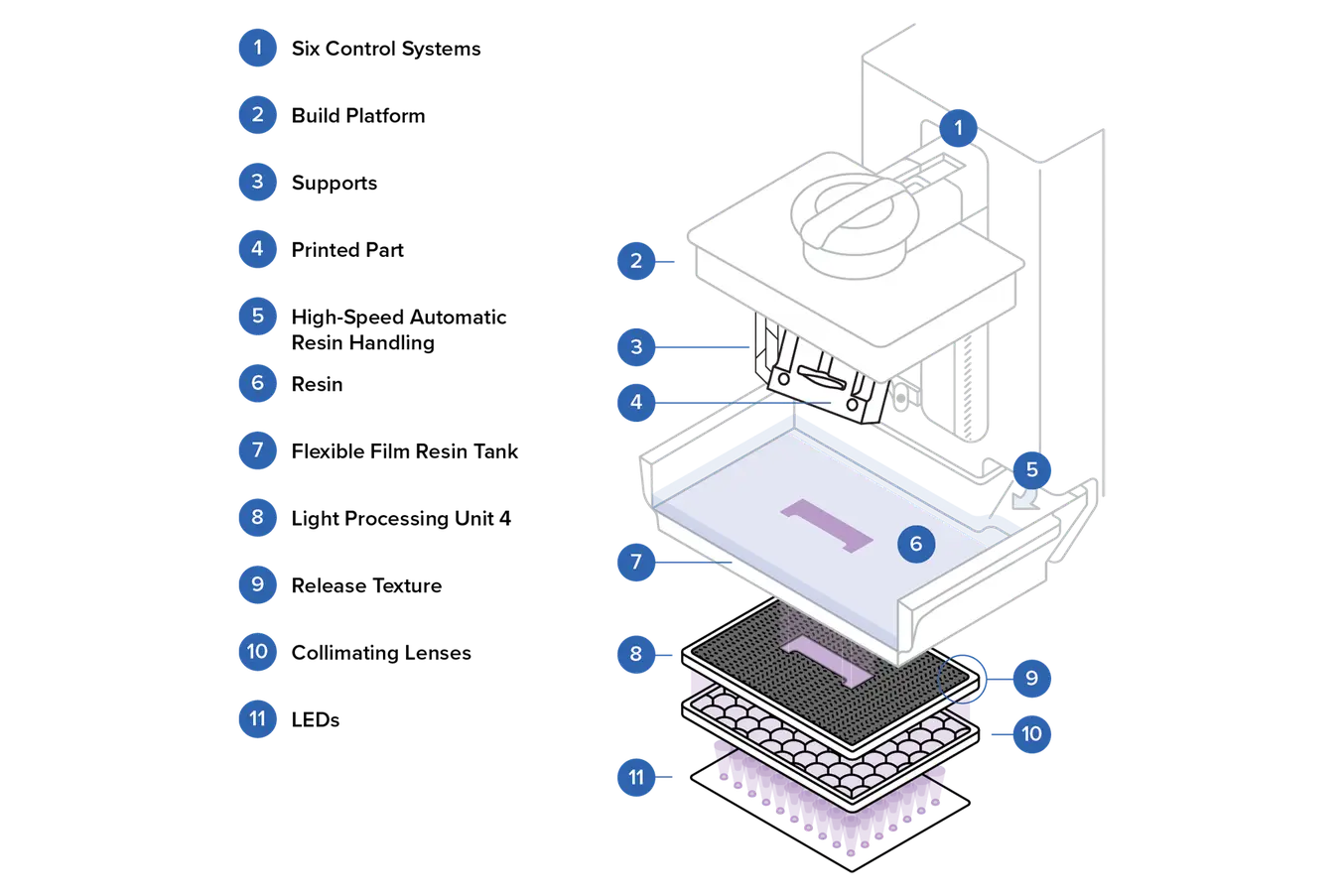
A graphic representation of Formlabs’ Low Force Display™ (LFD) Print Engine, an advanced form of MSLA 3D printing.
The use of LCD screens in resin 3D printing came after the development of laser-powered SLA and DLP 3D printing, enabled by the rapid development of display technologies due to their prevalence in other types of electronics. More recently, it has become possible to design LCDs with small pixel sizes and high transmission of 405 nm wavelength light — the wavelength typically used to cure liquid resin.
As the LEDs project light at the same time, MSLA 3D printers cure each layer of the resin almost instantly and offer fast printing speeds comparable to DLP 3D printers.
The more dense the LCD screen, the smaller the pixels are, and the higher the possible resolution of the part will be. However, there is a tradeoff to smaller pixels. Higher pixel density (smaller pixels) results in lower light transmission, lowering the optical power delivered to the liquid resin and lowering print speed.
Formlabs’ Low Force Display™ (LFD) Print Engine is an advanced form of MSLA 3D printing, developed for Form 4 and Form 4L. LFD introduces a brand new technology stack including a backlight unit, light processing unit, release texture, and integrated camera, and significant improvements with updates to the flexible film tank, resin cartridge, automatic resin handling, and intelligent control systems to deliver the speed, reliability, and part quality that professionals need, all in a single printer.
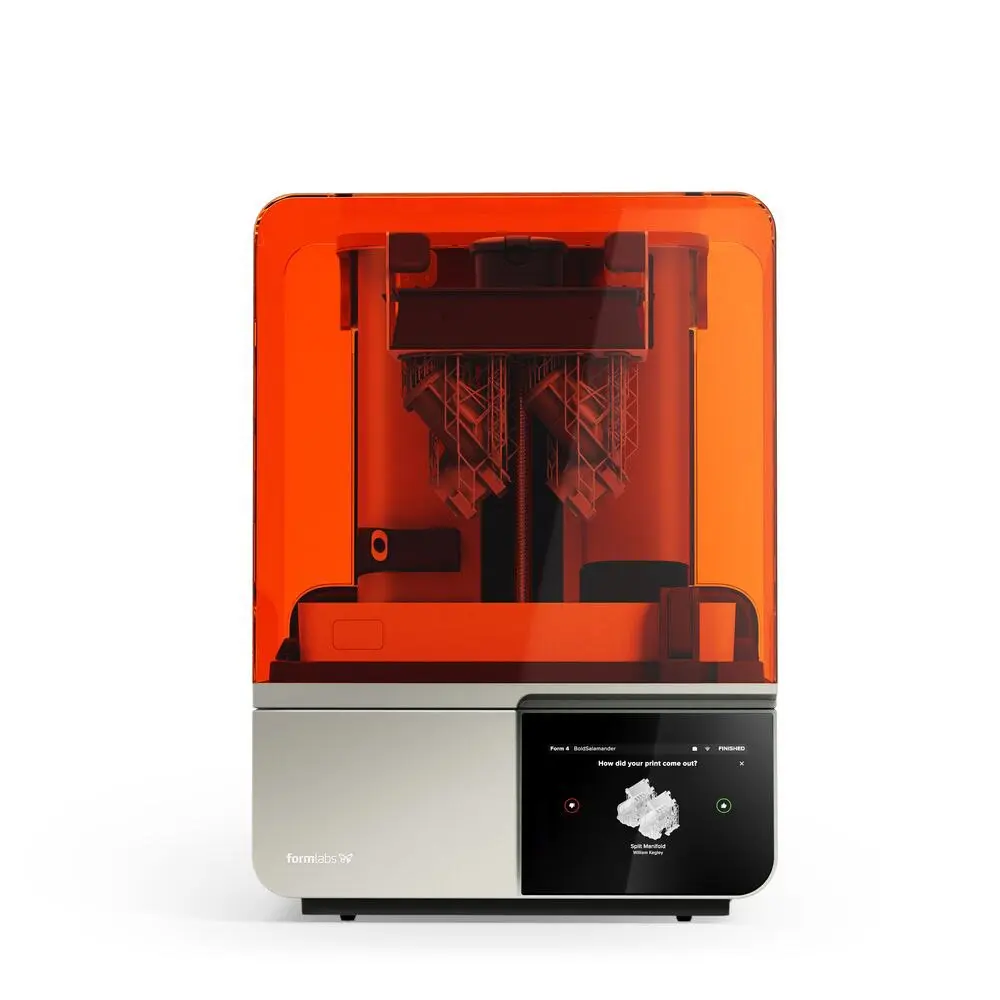
Product Demo: Form 4
See how Form 4 can enable new levels of productivity and innovation through its unmatched speed, accuracy, and reliability.
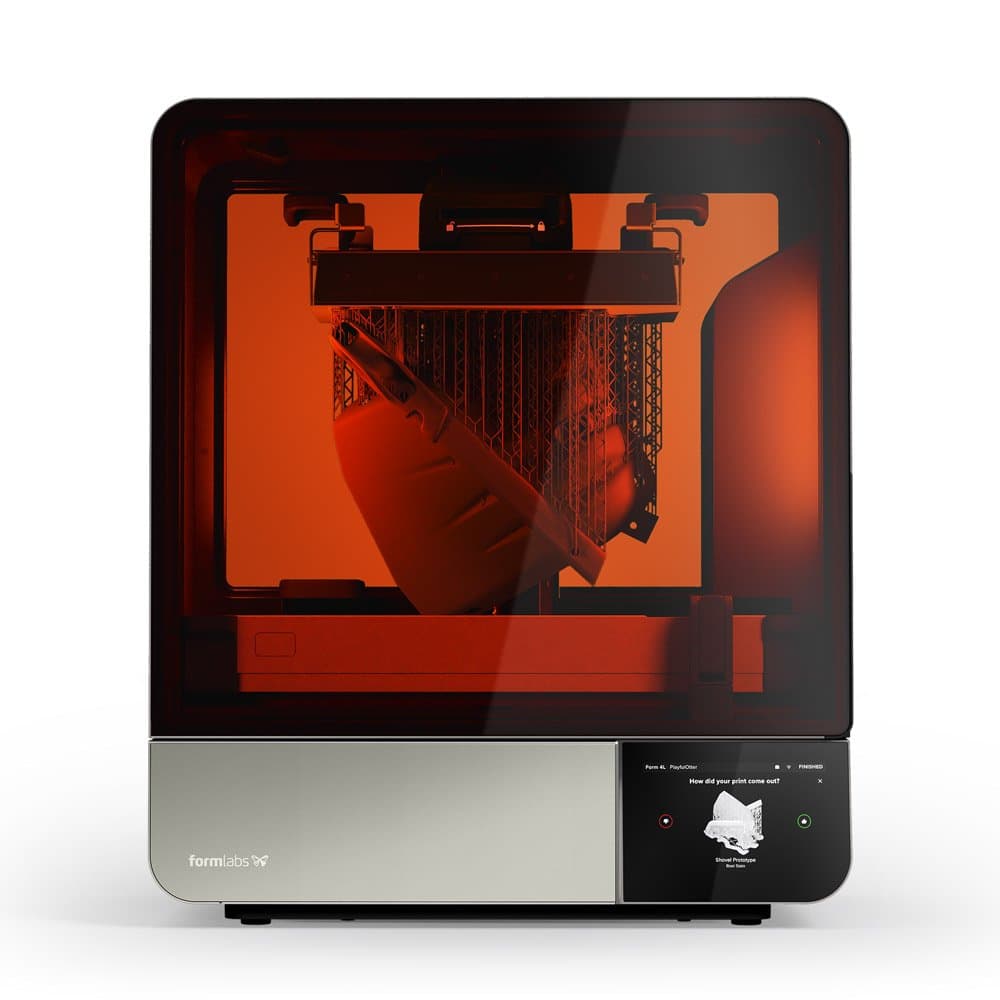
Product Demo: Form 4L
See how Form 4L, our next-generation large-format resin 3D printer, takes the speed, accuracy, and reliability of Form 4 to a completely new scale.
Comparing SLA, DLP, MSLA/LCD 3D Printing Processes
Laser-powered SLA, DLP, and MSLA/LCD 3D printers are all stereolithography processes because they all use a light source to cure liquid resin. Some of the differences between these resin 3D printing technologies are due to the accuracy, resolution, quality, and durability of that light source, light processing solution, and other technologies built around them. Other differences such as workflow or applications differ more from manufacturer to manufacturer, depending on the software, accessories, and materials available for each system.
Resolution
Resolution in 3D printing can be difficult to characterize and standardize between machines and manufacturers. Ultimately, the quality and accuracy of a print depends on many factors, namely: the size, shape, and power distribution of the light curing the resin, and the scattering, bleeding, and polymerization characteristics of the resin. For example, some resins scatter light more than others, which can cause extra resin to cure and create less detailed features in a print.
Resolution — once referred to as ‘dots per inch’ or DPI on paper-and-ink printers — is easily understood as ink covering the X and Y axes. When 3D printing became more widely adopted, the addition of the Z-axis further complicated the definition and measurement standards for 3D printing resolution.
To determine the highest resolution 3D printing technology and manufacturer, both the ability to specifically trace a part in the XY planes and the minimum Z-axis layer height should be considered. The ability to specifically trace the intended pattern, however, relies on several factors.
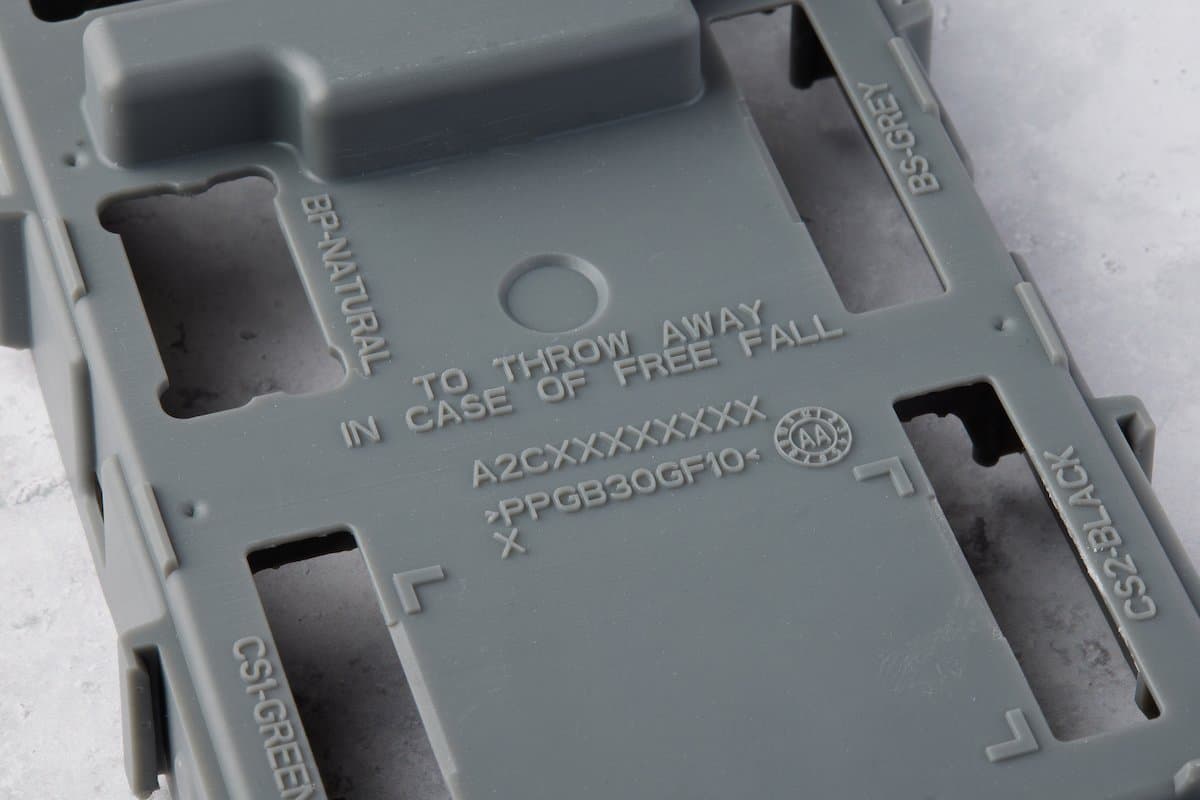
Resin 3D printers have excellent resolution, far superior to other 3D printing processes like fused deposition modeling (FDM) 3D printers. For applications like rapid prototyping or molding, resolution can mean the difference in a successful end product or design review.
Resolution for laser-powered SLA 3D printers is determined by four factors: spot size of the laser, the power distribution of the laser spot, the precision with which the galvanometers position the light in the XY plane, and the Z-axis minimum layer height.
Laser spot size, at first glance, seems to indicate the minimum feature size possible — but that is not the case. Though it’s true that if the entire part consists of a single, round dot or sphere, then the minimum feature size is determined by the laser spot size — it cannot cure something smaller than itself. However, a dot or tiny spherical part is not realistic. For realistic parts, the laser can trace shapes and features that are smaller than its spot size, because it can move in the XY plane in increments smaller than its own spot size — tracing the ‘outside’ of a very small feature.
As an example, Form 3+ has a laser spot size of 85 microns, but an XY resolution of 25 microns. Here, XY resolution refers to how precisely the printer can draw in the XY (horizontal) plane.
Resolution of DLP 3D printers is determined by the pixel size (both X and Y measurements), the power and uniformity of the light, the use of anti-aliasing, and the Z-axis minimum layer height, similar to laser-powered SLA printers.
The smaller the pixel size, the greater the resolution — similar to familiar technologies such as TVs or handheld electronics. In DLP 3D printing, XY resolution is defined by the pixel size, the smallest feature the projector can reproduce within a single layer. This depends on the resolution of the projector, the most common being full HD (1080p), and its distance from the optical window. As a result, most desktop DLP 3D printers have a fixed XY resolution, generally between 35 to 100 microns.
DLP 3D printers’ resolution diminishes as build volume grows bigger, because there are no projectors available with significantly more pixels. Therefore, manufacturers have to increase the distance from the light source with the same number of pixels, leading to decreased resolution and print quality.
Resolution of MSLA 3D printers is determined by pixel size of the LCD, the collimation and uniformity of the light source, the use of anti-aliasing, and the Z-axis minimum layer height.
Similar to DLP 3D printers, the smaller the pixel, the greater the resolution. But smaller pixels are only one factor. MSLA printers need to have highly collimated (meaning the rays are parallel) light that does not spread when passing through a pixel in the LCD screen. The light must also be extremely uniform so the resin is cured with the same optical power through every pixel in the LCD screen.
Luckily, Z-axis minimum layer height is less complicated — most resin 3D printers have a standard layer height of between 25 and 200 microns. For inverted resin 3D printers, layer height is determined by the vertical depth of the resin squeezed between the build platform and the bottom of the resin tank — effectively the height of the resin cured in each layer.
Long story short, does resolution actually matter in resin 3D printing? The answer is yes, but resolution itself is often just a vanity metric. It offers some indication, but it doesn’t necessarily correlate directly with accuracy, precision, and print quality. Higher resolution (smaller pixels or laser spot size in the XY dimension and smaller layers in the Z dimension) also generally comes with significant trade-offs in terms of speed or even reliability (as more layers can introduce more possibilities of error).
To see real-life examples, read our study that evaluates how SLA and MSLA 3D printers with different resolutions perform in terms of surface finish, dimensional accuracy, and minimum feature size.
Dimensional Accuracy and Precision
Because 3D printing is an additive process, each layer introduces an opportunity for dimensional inaccuracy. As each layer forms, minuscule deviations from the intended shape of the cross-section can compound, affecting overall accuracy. Accuracy depends on many different factors: the type of 3D printing process, hardware design, resin properties, print settings, and post-processing workflow. In general, resin 3D printers are the most accurate and precise 3D printing processes. Differences in accuracy and precision vary more in regards to model and manufacturer than technology.
In resin 3D printing, the first major factor impacting accuracy is the optical performance of the printer — specifically the size, shape, and uniformity of light curing the resin. Professional laser-powered 3D printers, such as Form 3+ and Form 3B+ use high-quality galvanometers and extensive calibration to ensure that the laser’s light hits the resin at precisely the intended spot, and follows along the laser path without deviation.
The accuracy of DLP 3D printers is affected by the resolution and power of the light projector and the quality and calibration of the micromirror devices. DLP printers are often limited in their accuracy by pixel distortion at the edges of the build where the micromirror devices have to project the light further from the light source.
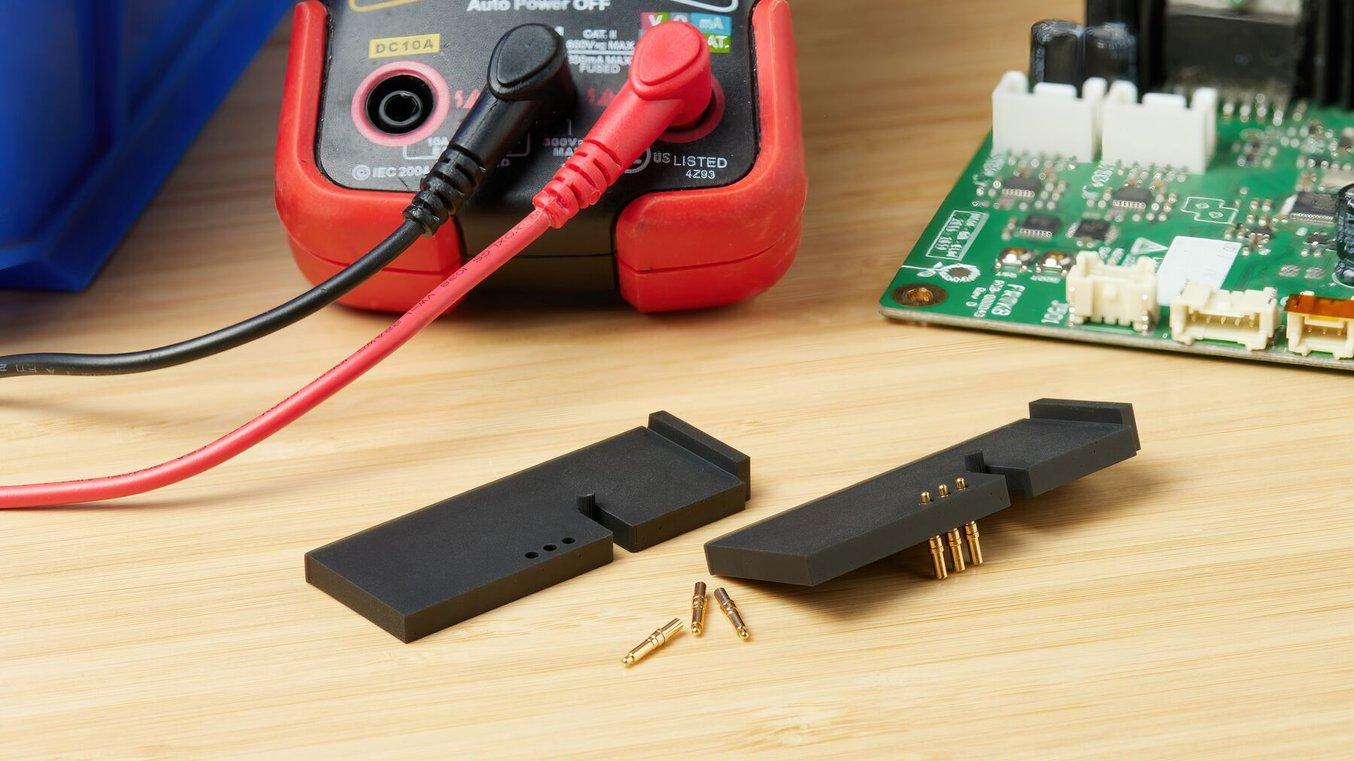
Dimensional accuracy and precision are important for 3D printed parts that will be part of assemblies or need to have insert features like these pin holes for an electronics circuit board assembly.
The accuracy of LCD and MSLA 3D printers is affected by the uniformity and collimation of the light source, and the pixel size and quality of the LCD screen. Most LCD printers have lenses over their light sources, but most are very basic and can lead to uneven light, dark spots, or distortion — creating inaccurate parts. The quality of the LCD screen is also crucial — greater quality means the LCD screen will respond to the software programming telling it where to cover the light and where to let it through.
Formlabs' Light Processing Unit 4 (LPU 4) includes a custom LCD screen with a 50 μm pixel size and pre-tuned anti-aliasing for excellent dimensional accuracy. Form 4’s Backlight Unit generates a uniform area projection of an ultra-high power light using 60 LEDs and a plano-convex lens array and optical baffle which creates highly collimated and uniform light, even at high power.
The second major factor impacting accuracy is the forces that a part experiences during printing. All inverted resin printers have two types of print forces. Peel forces occur during the peeling process of each layer as the build platform rises and the cured layer separates from the resin tank before starting a new layer. Squish forces occur on each layer when the build platform descends and squishes the print into the pool of liquid resin. These forces can cause layers to shift and deform, ultimately leading to lower dimensional accuracy.
Some printers use a basic flexible film resin tank that gently separates from cured layers and minimizes peel forces. Although these tanks reduce peel forces, they have two key problems. They use a non-durable film that is easy to damage and has to be replaced frequently. They are also prone to suction forces, where the flexible film suctions onto the LCD screen and causes a spike in peel forces.
Form 4 and Form 4L, professional MSLA printers, use a dual-layer flexible film tank that minimizes peel forces and is extremely robust to damage. Form 4 and Form 4L also feature a proprietary, microtextured optical film, called the Release Texture, that provides airflow between the resin tank and LCD screen, preventing suction forces and increasing accuracy.
The Release Texture of Form 4 MSLA 3D printers provides airflow between the resin tank and LCD screen, preventing suction forces and increasing accuracy.
The last major factor impacting accuracy is the properties of the liquid resin inside the printer. The process of curing liquid resin depends on many variables, including resin temperature, homogeneity, scattering, viscosity, and more. Small changes to any of these variables can cause more or less resin to cure, which can cause up to hundreds of micrometers of deviation in the size or shape of cured layers. Most resin 3D printers do not control these variables, resulting in frequent and unpredictable changes in dimensional accuracy.
Form 4 and Form 4L address this problem in several ways. First, they precisely control the temperature and homogeneity of the liquid resin using precision heaters, infrared temperature sensing, and a high-speed resin mixer. Formlabs also develops and manufactures its own materials, and tightly controls the reactivity, viscosity, and scattering properties of every material. Moreover, Form 4 and Form 4L use advanced slicing software, printer hardware calibrations, and validated print settings to automatically compensate for the properties of individual materials.
Once again, the accuracy and precision of a 3D printer are not solely dependent on the technology, but the exact hardware design, liquid resin properties, print settings and calibrations, and post-processing workflow.
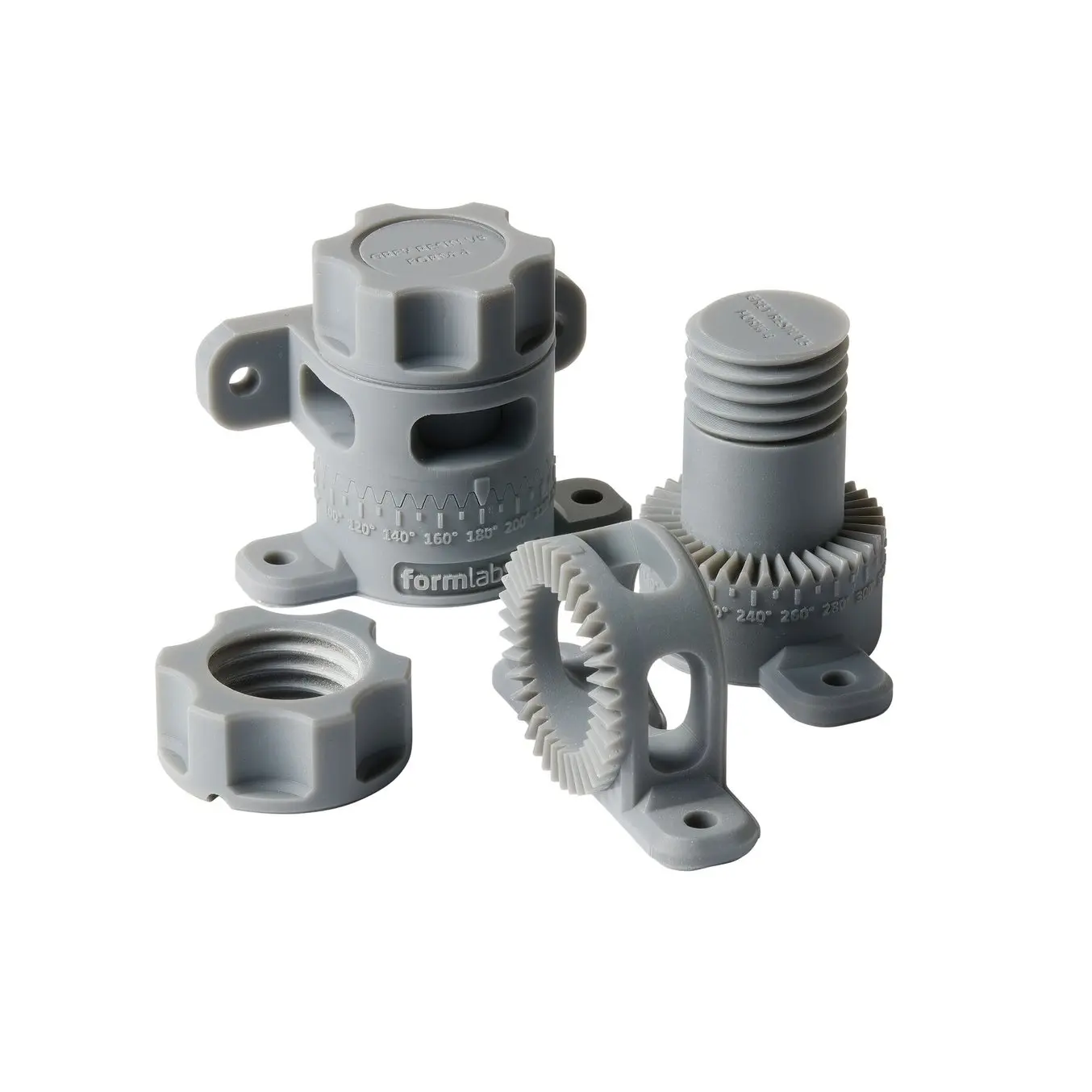
Form 4 Series Design Guide
A successful 3D print starts with a well-designed model. Follow our best practices to optimize designs and reduce failures.
Build Volume
Before the introduction of inverted SLA 3D printing, resin 3D printers had large build volumes and were very expensive. Inverted resin 3D printing then made the technology more accessible, but these machines were often much smaller as large builds would have been extremely difficult to print successfully due to the high peel forces.
Now the combination of inverted SLA (which allows for just as much resin as you need instead of large vats), and new peel technologies makes it possible to print larger build volumes without spending $100,000+ on a traditional large-format resin 3D printing system. For industries like consumer goods, product design, and healthcare, large-format resin printers are an ideal solution and enable applications like human-scale parts.
Those looking to evaluate which size resin printer is best for them should first consider the application. There are three main product categories for laser-powered resin printers — desktop, benchtop, and industrial-sized systems.
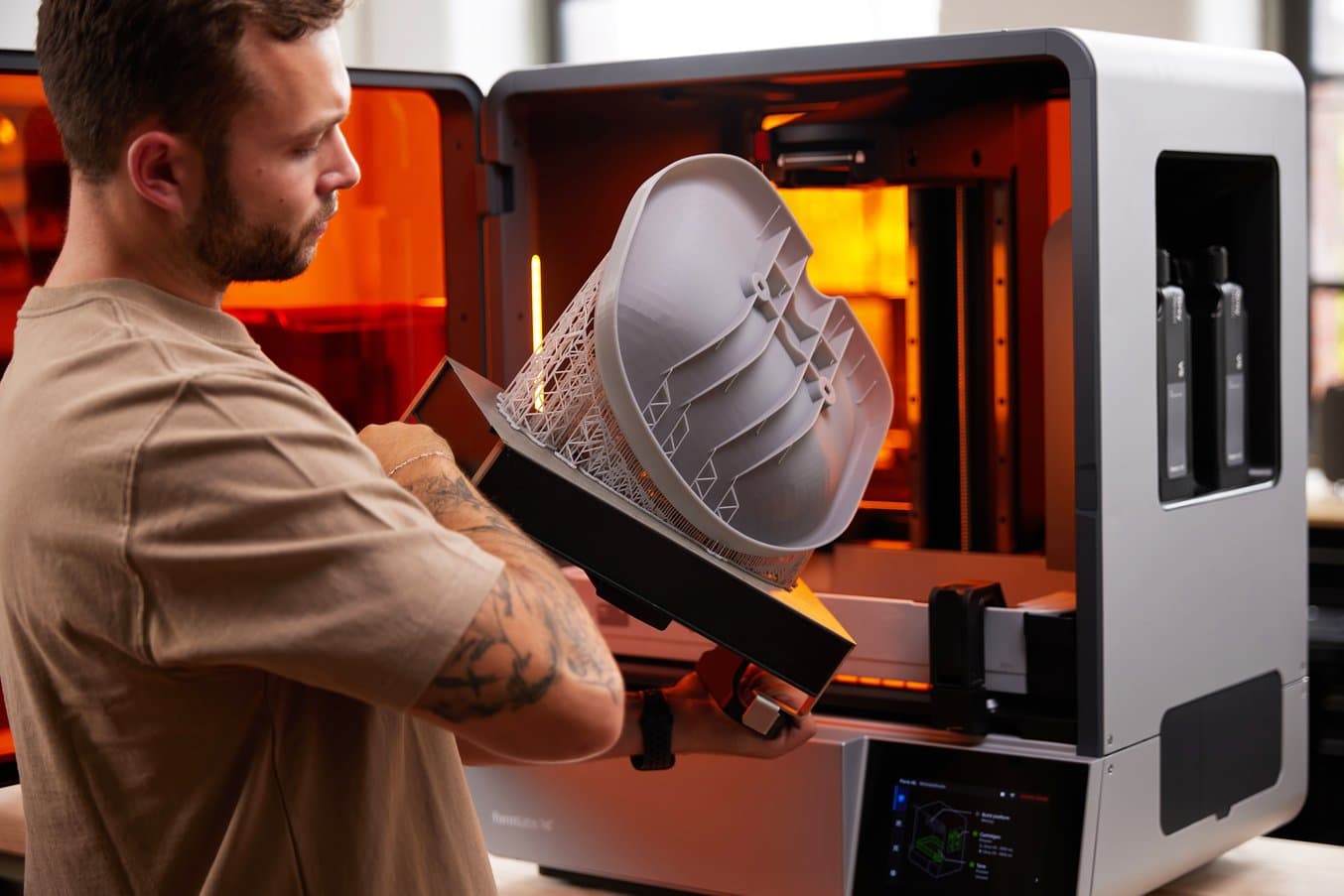
Benchtop resin 3D printers like Form 4L offer the combination of human-scale parts with the dimensional accuracy, range of material properties, and surface finish of resin 3D printing.
Industrial-sized systems were more common in previous decades for large corporations who could afford both the high cost of purchase and maintenance as well as the higher square footage and infrastructure requirements of top-down stereolithography printing.
Desktop-sized resin 3D printers were enabled by the invention of inverted SLA 3D printing, and as the technology was adopted by more manufacturers, smaller printers with cuboid build space of around 10-20 cm in each direction became the norm. For example, Formlabs' Form 3+ offers a 14.5 × 14.5 × 19.3 cm build volume, while Form 4 offers 30% larger build volume at 20.0 × 12.5 × 21.0 cm.
Benchtop resin 3D printing similarly was made possible by the combination of inverted SLA technology and improved peeling techniques. Benchtop 3D printers such as the Form 4L, which offers a 35.3 × 19.6 × 35.0 cm build volume, have the ability to do human-scale rapid prototyping of consumer goods, as well as create end-use products by direct 3D printing or through the use of 3D printed rapid tooling.
With DLP 3D printers, there is a direct trade-off between resolution and build volume. The resolution depends on the projector, which defines the number of pixels/voxels available. If one moves the projector closer to the optical window, the pixels get smaller, which increases the resolution, but limits the available build area. Some manufacturers use higher resolution 4K or 8K projectors, but these are very expensive, inflating the costs of the end product.
Large-format DLP printers still mostly use top-down technology, instead of inverted, which requires large amounts of resin to be available at once. As a result, desktop, small-format DLP 3D printers are generally optimized for specific use cases. They have a smaller build volume and offer a high resolution to produce small, detailed pieces like jewelry, while others can produce bigger parts but at a lower resolution.
Because LCD 3D printers rely on an array of LEDs and a similar-sized masking LCD screen, the accuracy and precision benefits remain the same as build volume gets larger. A large-format LCD or MSLA resin 3D printer will have the same accuracy as a smaller version, provided they are using an LCD screen with the same pixel size and a LED light source with the same uniformity and collimation.
Unlike laser-powered SLA 3D printers, however, this does slightly increase the cost for every added LED and square cm of LCD screen added. A laser-powered resin printer can use the same laser for any size build volume, because its galvanometers can simply direct its path to farther reaches of the platform for larger sizes. However, in the interest of print speed, many benchtop large format laser-powered resin printers, like Form 3L, add a second laser unit, which increases the cost similarly to how a larger LED array and LCD screen might.
Surface Finish
Resin 3D printers are known for creating parts with smooth surface finishes that require minimal post-processing to achieve the look of injection molded plastics. Resin 3D printing, whether using a projector, series of LEDs, or laser, can cure liquid resin with much better surface finish than an FDM printer can extrude filament. Depending on the design, all resin and FDM printers might need to print parts with supports, which can leave behind touchpoints or artifacts on the surface that may need to be lightly sanded or clipped.
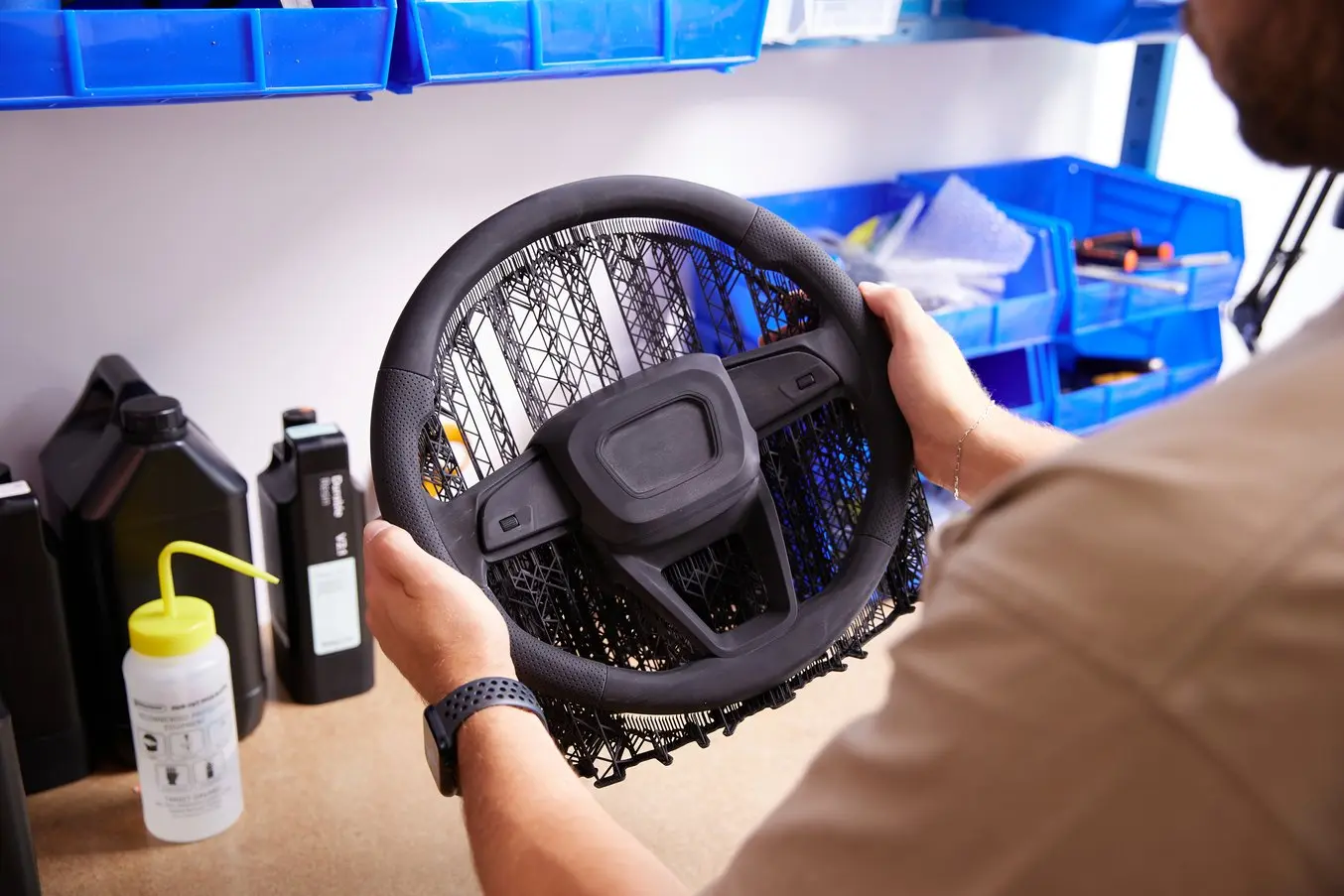
The surface finish possible on the Form 4L makes human-scale prototyping more realistic — this steering wheel prototype has the texture of what will eventually be an end-use fabric cover built into its 3D model.
Resin 3D printers’ layers are chemically as well as physically bonded to each other in the Z-axis, so the differentiation between vertical layers is very hard to detect, leading to a smoother appearance.
For clear materials, such as Clear Resin, this smooth surface translates to better transparency of the parts themselves, making it an ideal technology for parts requiring optical translucency or showcasing internal features.
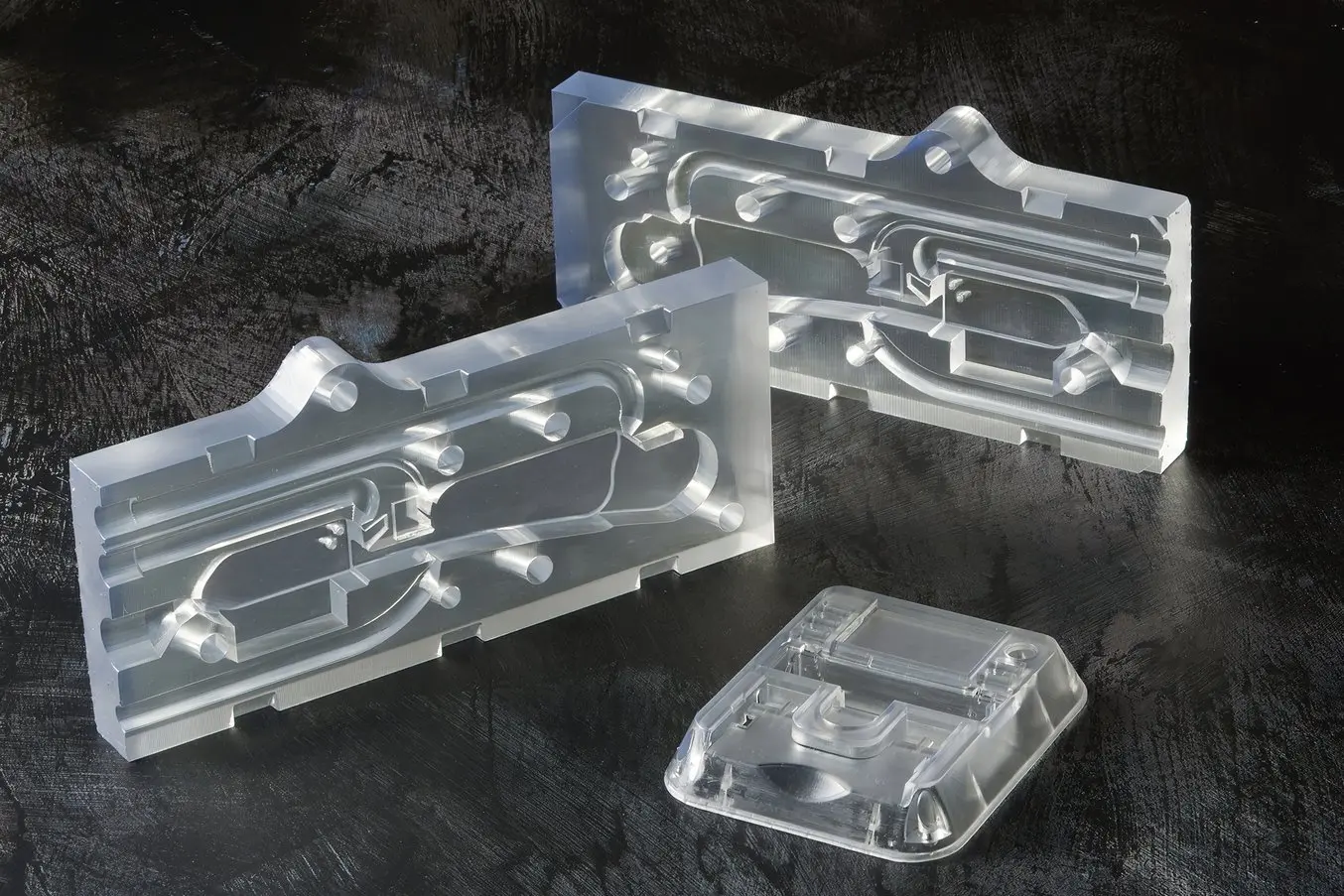
Smooth surfaces allow for near-complete optical transparency. For two-part molds, this transparency makes it easy to observe and troubleshoot the molding process as it happens within the part.
Laser-powered 3D printers like the Form 3+ and Form 3L are popular for their almost perfectly smooth surfaces. Because a laser has a round spot size, curved edges are truly rounded, and the overall appearance of the parts is very smooth.
DLP and LCD 3D printers also generally have incredibly smooth surface finishes and require very little sanding or polishing to look like injection molded plastics. However, both DLP and LCD printers are projecting light through voxels or pixels, which are rectangular. Historically, these voxels would cause a visible ‘stepping’ or ‘aliasing’ artifact in the X and Y axis, typically called voxel or pixel lines.
Recently, DLP and LCD 3D printers have started using high-resolution projectors or LCD screens with very small pixels, plus anti-aliasing techniques where certain pixels are partially turned on. As a result, modern DLP and LCD 3D printers deliver a surface finish that is mostly indistinguishable from laser-powered SLA printers.
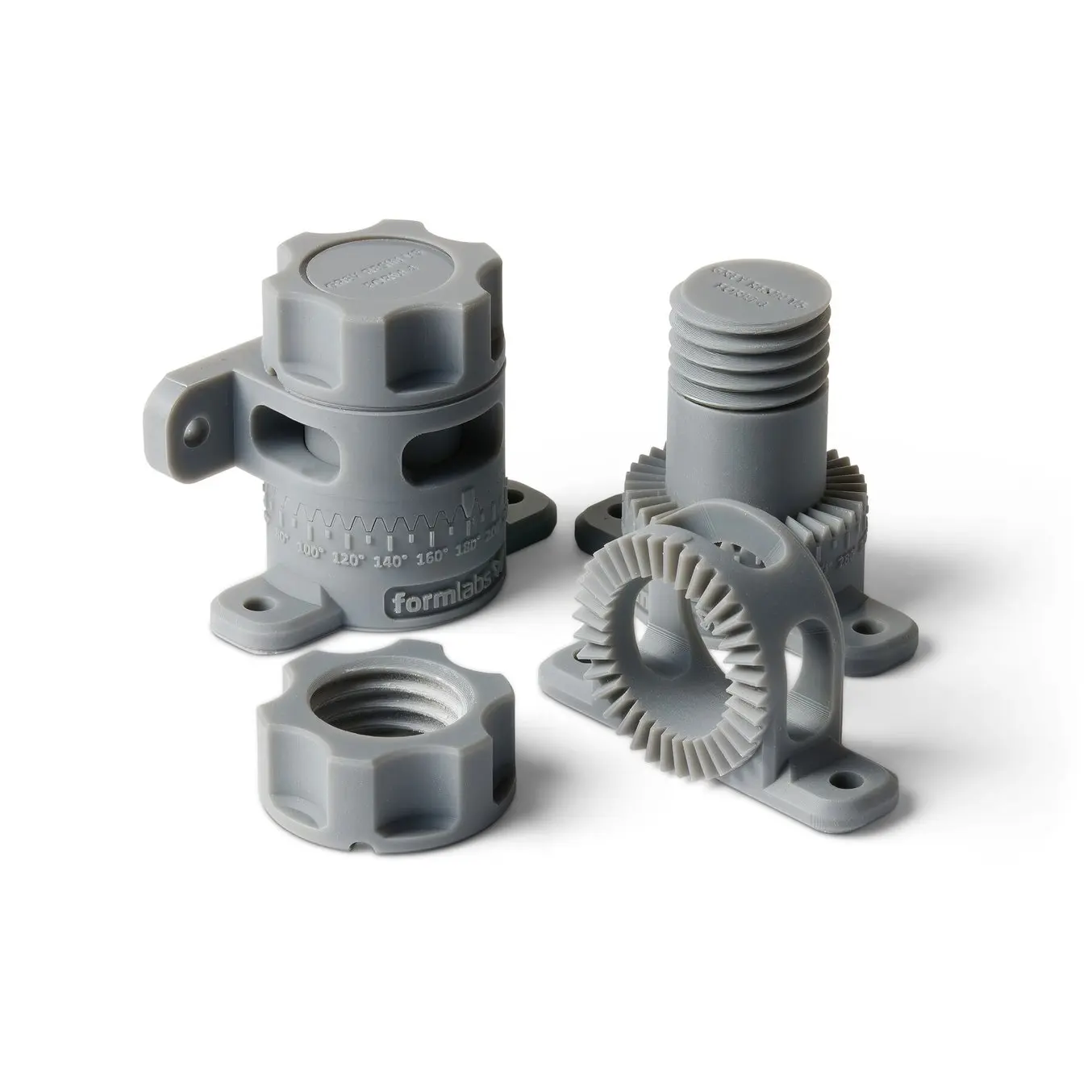
Request a Free Sample Part
See and feel Formlabs quality firsthand. We’ll ship a free 3D printed sample part to your office.
Speed and Throughput
As more businesses turn to 3D printing for production as well as rapid iteration, 3D printing speed becomes a greater consideration when choosing a technology. The right 3D printer is one that produces high-quality parts quickly, without compromising on accuracy, reliability, or materials performance. FDM and SLS processes have significantly improved print speed, but resin 3D printers got even faster, making them the fastest additive manufacturing process. New print engines like LFD take that even further and can produce most parts in just a few hours, or small parts in minutes of cycle time.
For small parts, laser-powered resin printers are comparable in speed to DLP and LCD 3D printers — when the laser doesn’t have to cover a large area to cure the resin, it can quickly accomplish each layer. However, for medium to large parts, or batch production, laser-powered 3D printers can be significantly slower than their DLP or MSLA counterparts.
DLP printers have been popular in industries where fast printing has an effect on the bottom line, like dental labs. However, they are more prone to optical distortion across the build area and require advanced calibration for high accuracy. They are also typically more expensive than LCD 3D printers for similar performance.
Advanced MSLA technology, like Form 4 and Form 4L, offers the fastest and most reliable 3D printing solution overall. Curing each layer all at once is the biggest factor driving that speed, but other factors, such as the Form 4’s dual-layer flexible film resin tank, Release Texture, high-speed automated resin filling, and fast resin heating, also decrease overall print time.
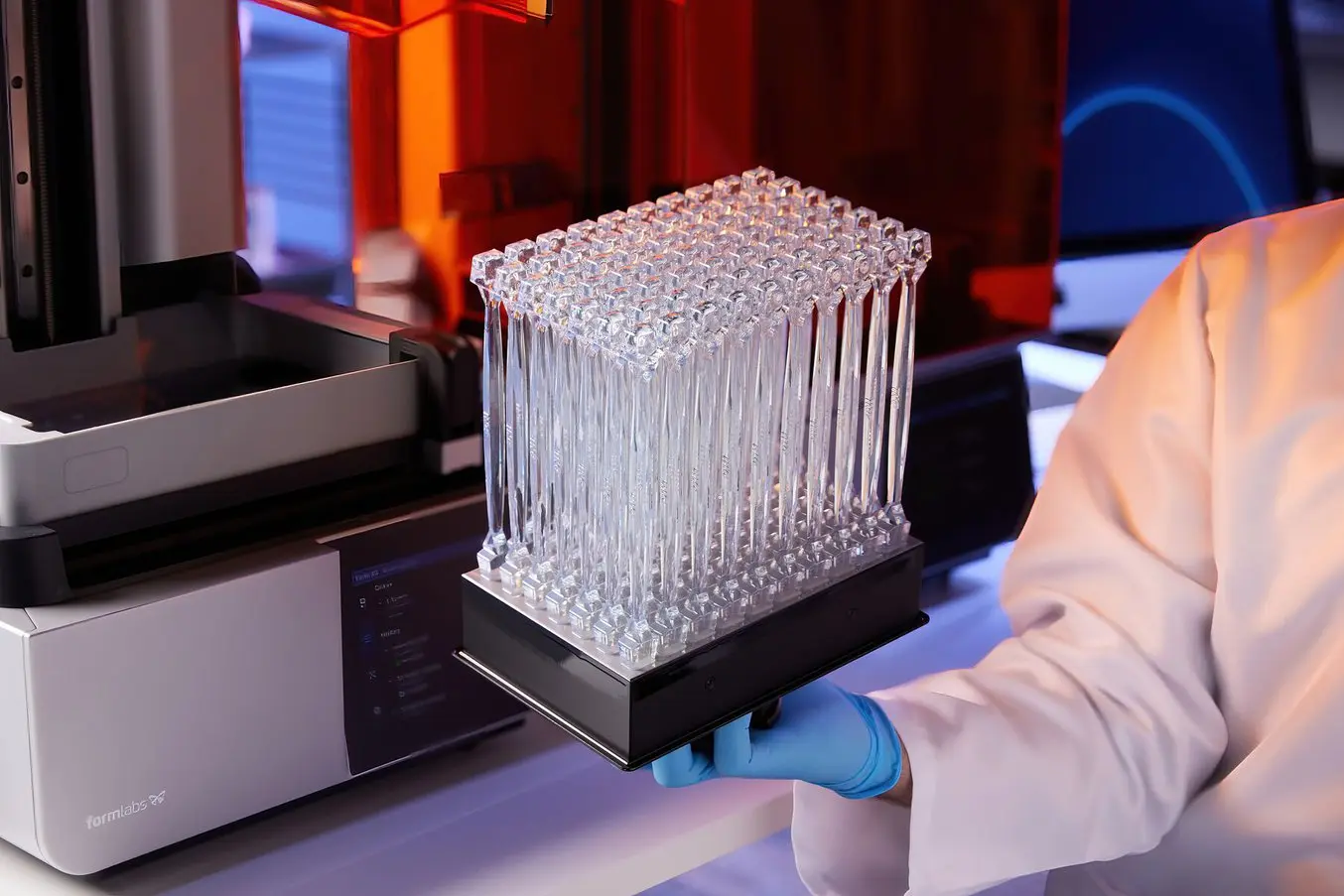
Form 4 can finish a fully packed build in 2-5 hours, depending on the material. The throughput possible with a fleet of affordable, fast, and easy-to-use 3D printers like Form 4 can match the output of traditional processes like injection molding.
When considering MSLA printers for production, the quality and reliability of the components are important considerations. Most LCD printers have a reputation for a short lifetime, as generic LCD screens are not made for the type of conditions found in 3D printers. On Formlabs Form 4 and Form 4L, the Light Processing Unit has a lifetime of 600,000–1,900,000 layers — and both can be replaced by the user easily and at low cost.
Scaling throughput is easy with desktop resin 3D printers. Their accessible size simplifies the process of adding more units and scaling up to produce more parts. There are also options to add automation for some units. Formlabs resin printers offer advanced workflow tools such as Form Auto for Form 3/B/+ that automate part removal to enable 24/7 printing. Automation tools like the Formlabs Automation Ecosystem reduce the number of touchpoints necessary for the print process, simplifying workflows where many smaller, mostly similar items (like dental or ortho models) need to be printed nearly continuously.
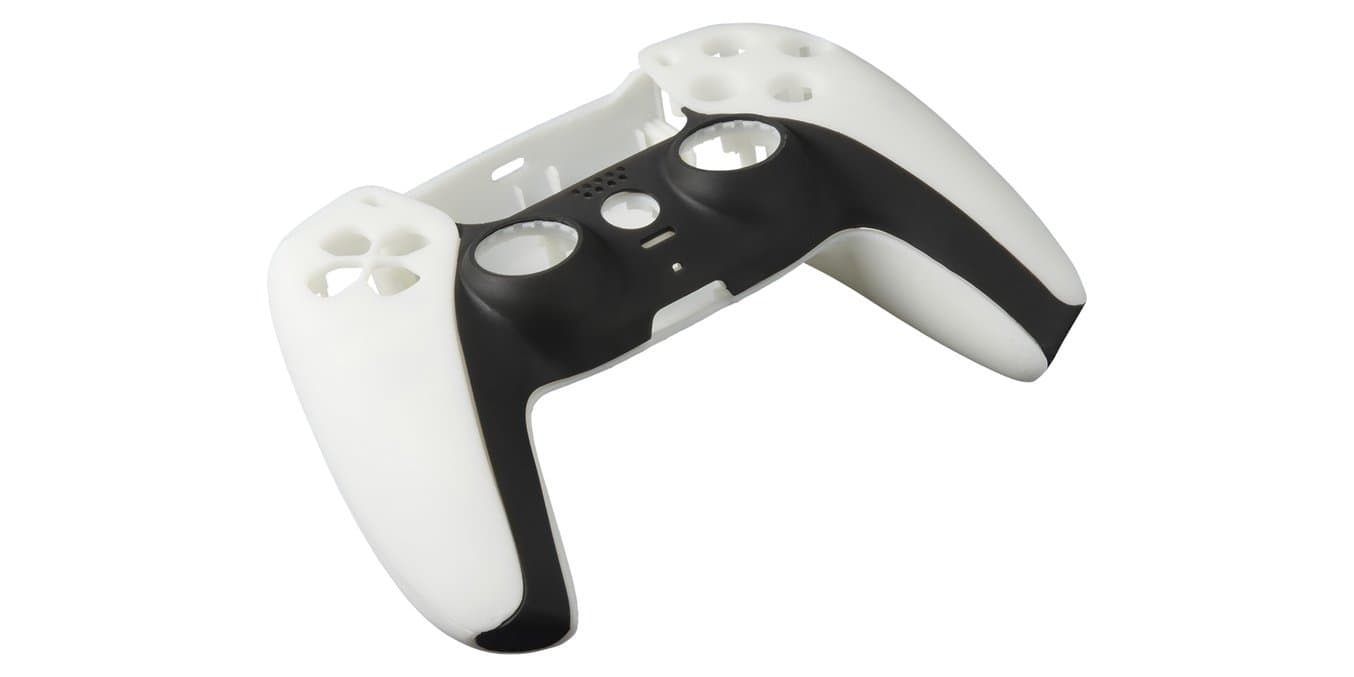
Print Speed Comparison: Gaming Controller
FDM 3D Printing | SLA 3D Printing | SLS 3D Printing | |
---|---|---|---|
1 assembly (3 parts) | 10 h 32 min | 2 h 36 m | 3 h 52 min printing (6 h 52 min cooling) |
5 assemblies (15 parts) | 52 h 40 min | 13 h | 9 h 38 min printing (13 h 47 min cooling) |
Compared printers and printing parameters:
- FDM 3D printer: Bambu Lab X1, PLA Basic, 120 microns layer height, 15% infill density
- SLA 3D printer: Form 4, Grey Resin, 100 microns layer height
- SLS 3D printer: Fuse 1+ 30W, Nylon 12 Powder, 110 microns layer height
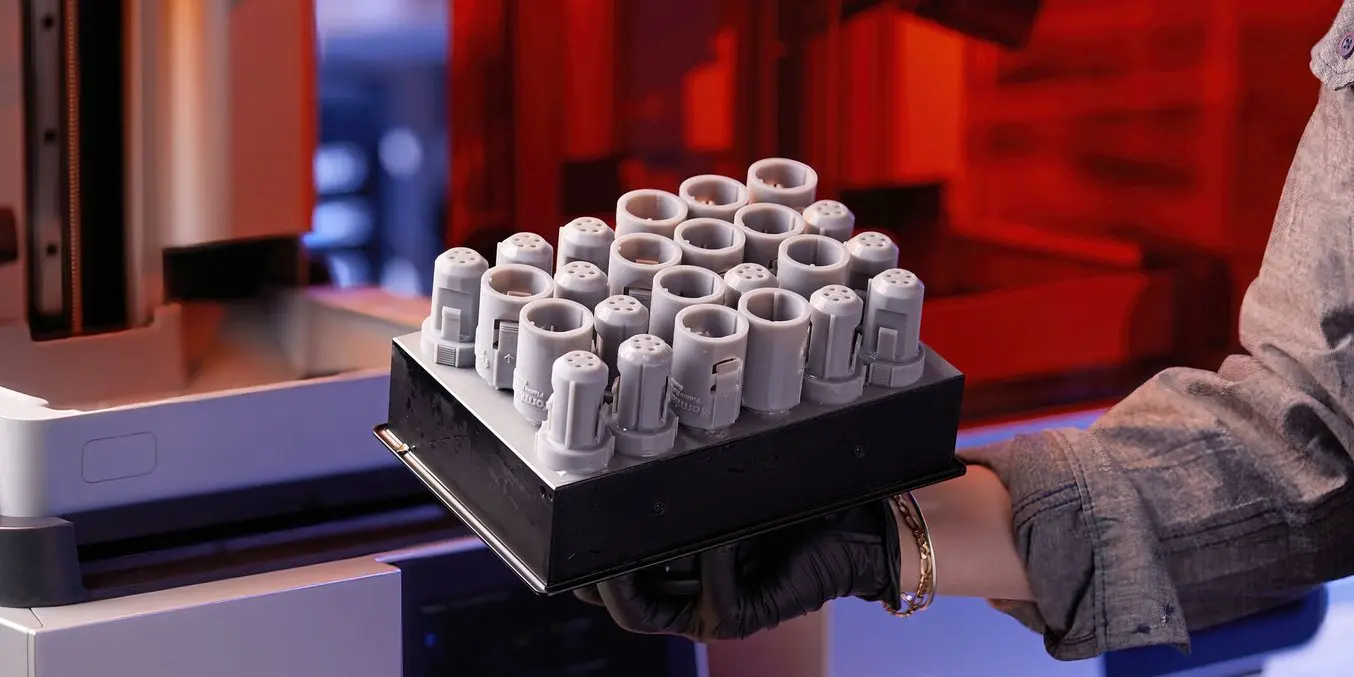
Print Speed Comparison: Electrical Connector
FDM 3D Printing | SLA 3D Printing | SLS 3D Printing | |
---|---|---|---|
1 assembly (2 parts) | 2 h 38 min | 1 h 3 min | 3 h 30 min printing (6 h 27 min cooling) |
50 assemblies (100 parts) | 84 h | 13 h 2 min | 12 h 59 min printing (13 h 49 min cooling) |
Compared printers and printing parameters:
- FDM 3D printer: Bambu Lab X1, PLA Basic, 120 microns layer height, 15% infill density
- SLA 3D printer: Form 4, Grey Resin, 100 microns layer height
- SLS 3D printer: Fuse 1+ 30W, Nylon 12 Powder, 110 microns layer height
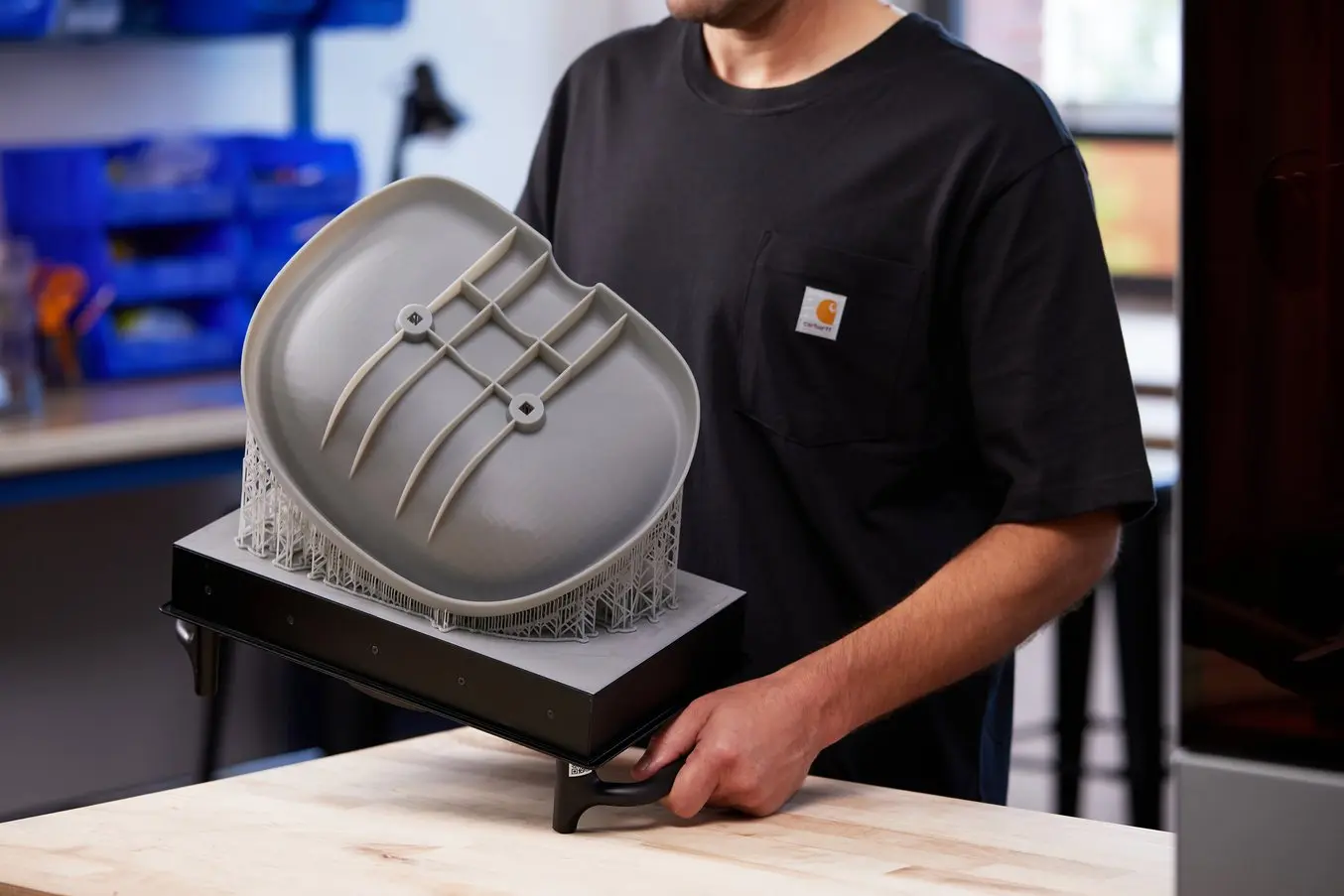
Print Speed Comparison: Radio Flyer Seat Prototype
FDM 3D Printing | SLA 3D Printing | |
---|---|---|
1 prototype | 42 hr 3 min | 2 hr 37 min |
Compared printers and printing parameters:
- FDM 3D printer: Ultimaker S7, PLA, 100 microns layer height, 20% infill density
- SLA 3D printer: Form 4, Fast Model Resin, 200 microns layer height
Curious to check the print speed for your own parts? Download PreForm, Formlabs’ free print preparation software to calculate print times when printing on Formlabs SLA and SLS 3D printers.
Workflow and Ease of Use
Different manufacturers will offer various workflow solutions to make resin 3D printing easier.
Some printers come with proprietary software to prepare 3D models for printing, such as PreForm for Formlabs SLA 3D printers, while other manufacturers might require the user to purchase slicing software to orient parts, create support structures, slice models, and upload their files themselves. Features differ by software tool, for example, PreForm offers a one-click print setup, powerful manual controls to optimize support density and size, adaptive layer thickness, or functions to save material and time. Luckily, the software can be easy to download and test before purchasing a 3D printer.
Getting started with resin 3D printing can be quite easy — many resin 3D printers, especially desktop-sized units, are designed to be unboxed within just a few minutes and start printing almost immediately. Parts of the process like the user interface and sensors within the printer make not only the first print simple, but continued maintenance as well.
Some lower-cost resin 3D printers require further calibration steps to ensure the material will print successfully at the designated layer height. These steps might include manually pouring in resin, choosing print settings (without the benefit of a validated, repeatable workflow), and tweaking print settings to ensure part success.
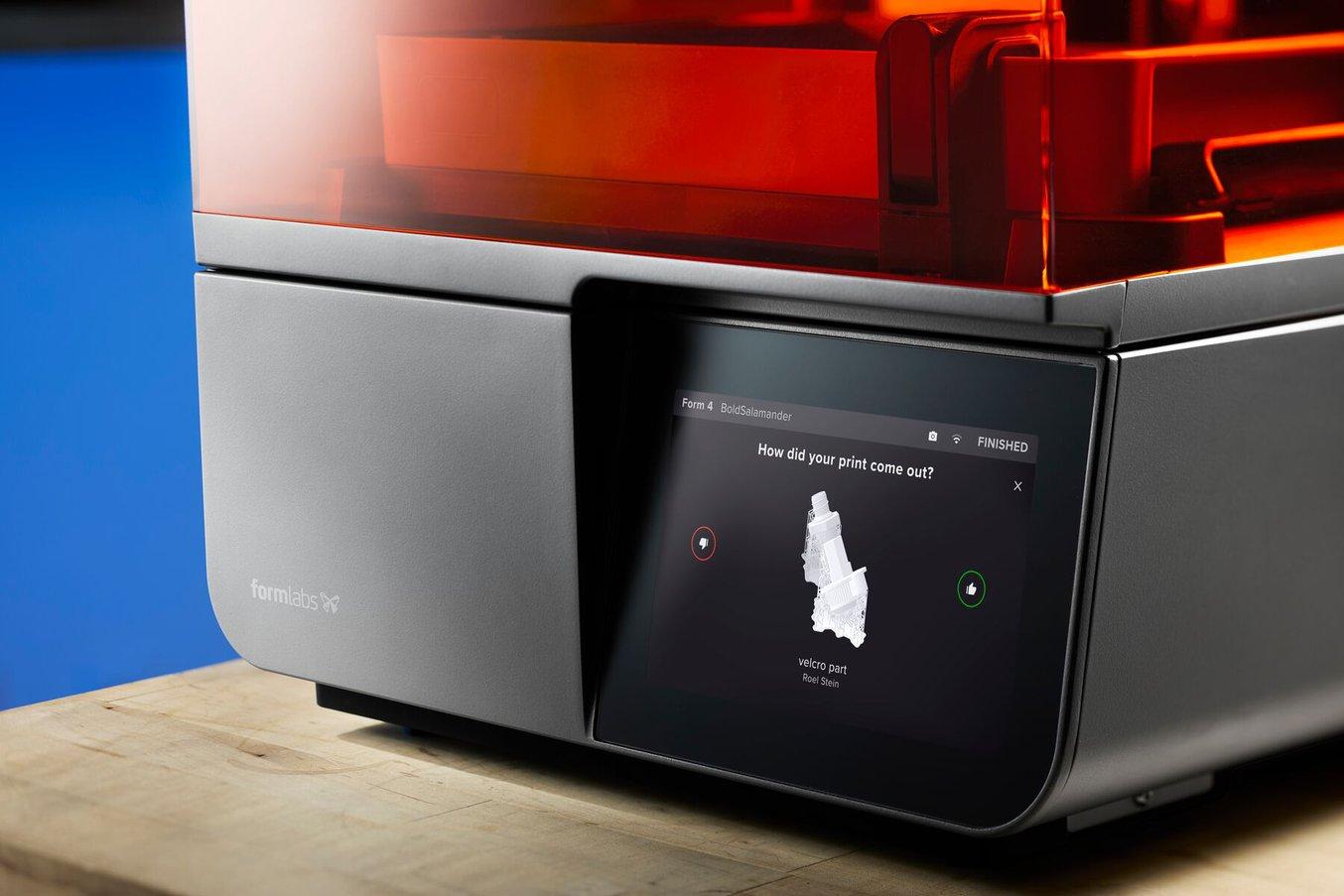
An improved user experience on Form 4 includes a touchscreen that's both easier to read and to interact with.
Form 4 and Form 4L’s improved touchscreen, intelligent control systems, and fast automatic resin dispensing enable a smooth workflow that users can ‘set and forget,’ so they can focus on their design and testing while Form 4/L delivers parts. The advanced cartridge system automatically refills the tank with liquid resin, which requires less attention and facilitates printing overnight. Validated material settings for multiple layer heights grant peace of mind to users, who can choose a material and layer height knowing they have been tested rigorously and that the printer will complete the part successfully.
Another major factor to consider when choosing a 3D printing system is the post-print workflow. When the print is complete, the part will need to be washed, potentially post-cured, and then post-processed, whether with a simple support removal, or a more advanced post-processing method. Form 4’s lower peel forces enable supports with tiny touchpoints that are easy to remove. These light-touch supports enable faster post-processing times and an easier workflow.
Different manufacturers offer a range of solutions, such as Formlabs' end-to-end workflow using automated agitation of IPA in Form Wash, preprogrammed post-cure settings for over 40 materials in Form Cure, and a set of advanced Finishing Tools to polish, shine, and prepare parts for use.
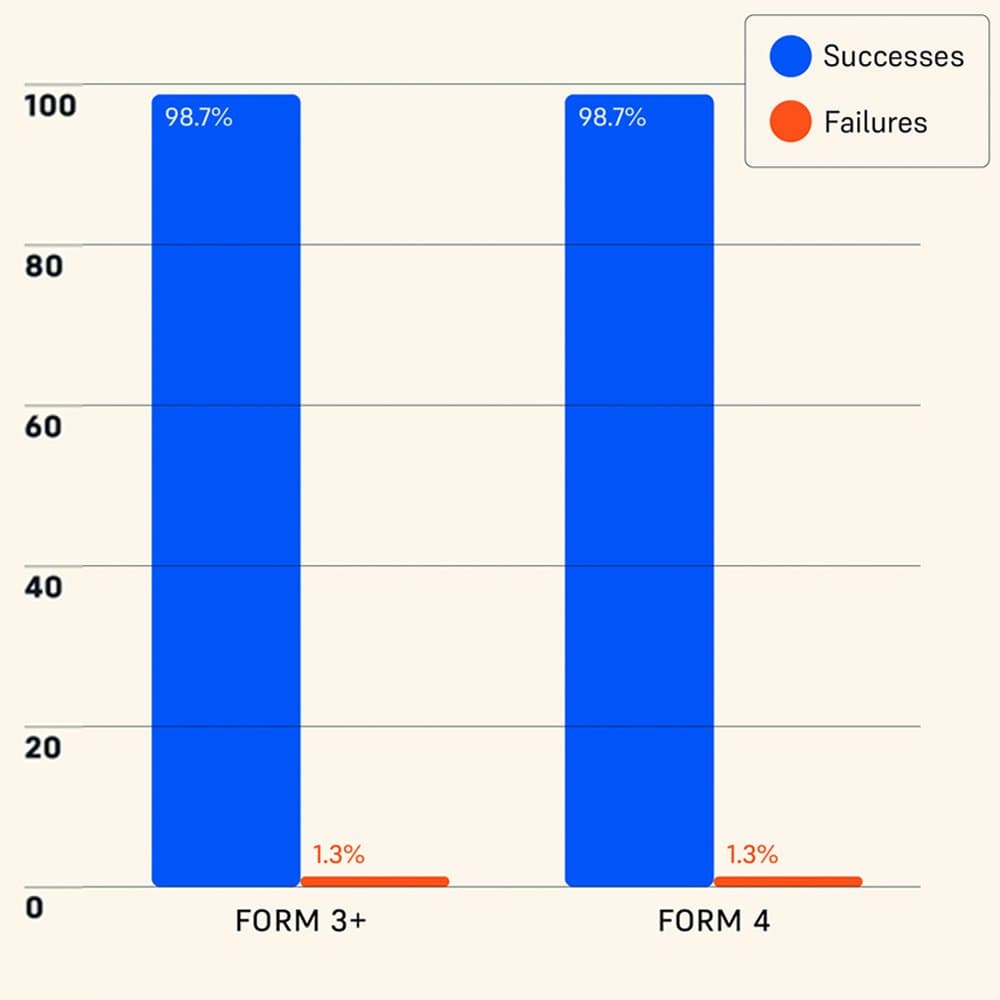
Independently Tested Reliability of Form 4 and Other Resin 3D Printers
Formlabs Form 4 was measured to have a 98.7% print success rate by an independent global leader in product testing. Read a complete description of the test methodology and see the results in our white paper.
Materials and Applications
Regarding the easy switching between materials, most resin printers are “plug and play,” with easily swappable build platforms and resin tanks. Just like with accuracy and precision, the available materials differ more from machine to machine than between technologies. Many manufacturers make their own resins, but many do not, preferring to white-label other company’s materials or simply offer an open system capable of accepting many different types of resins.
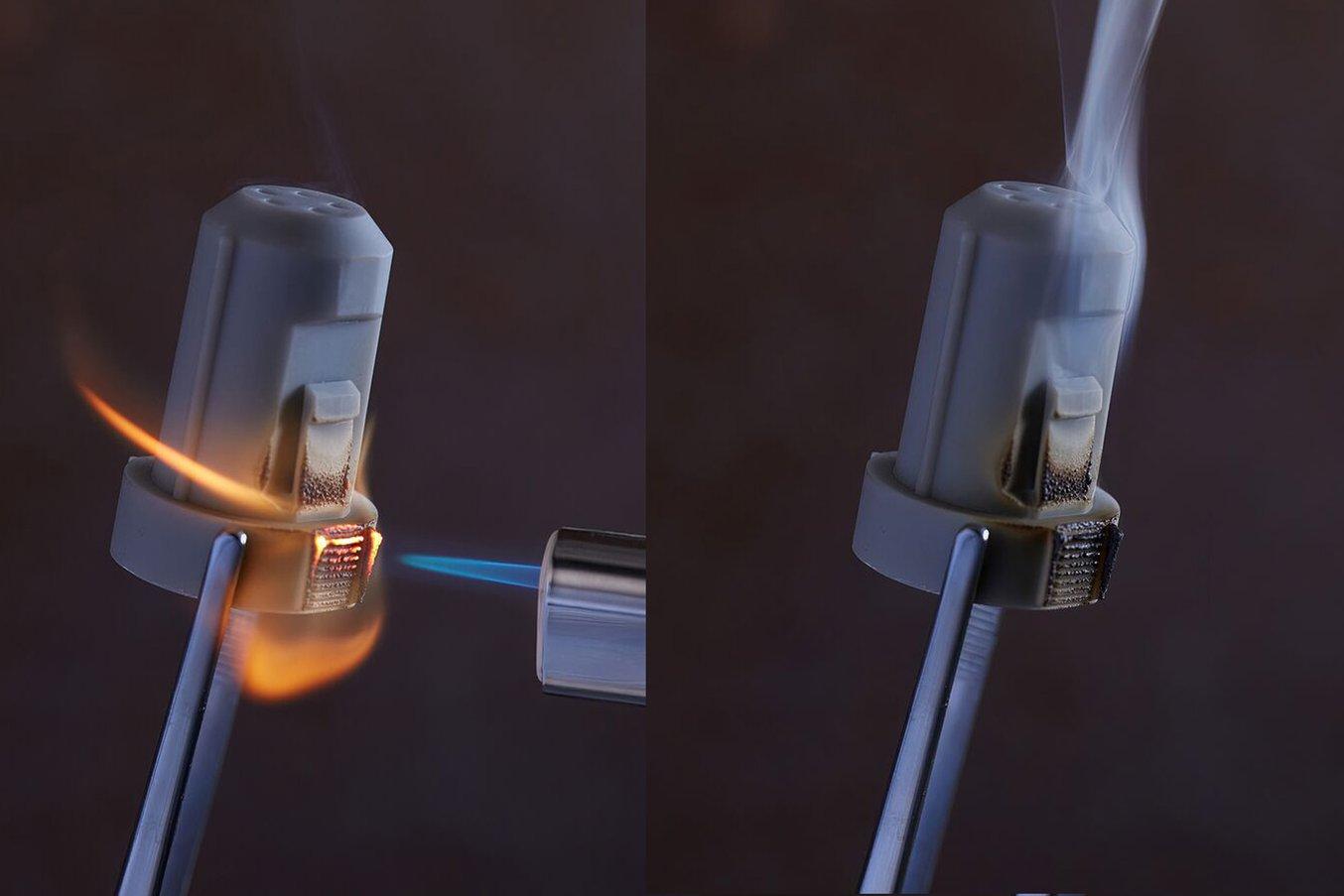
Formlabs' Flame Retardant Resin is a specialty UL 94 Blue Card certified material for creating self-extinguishing and halogen-free parts.
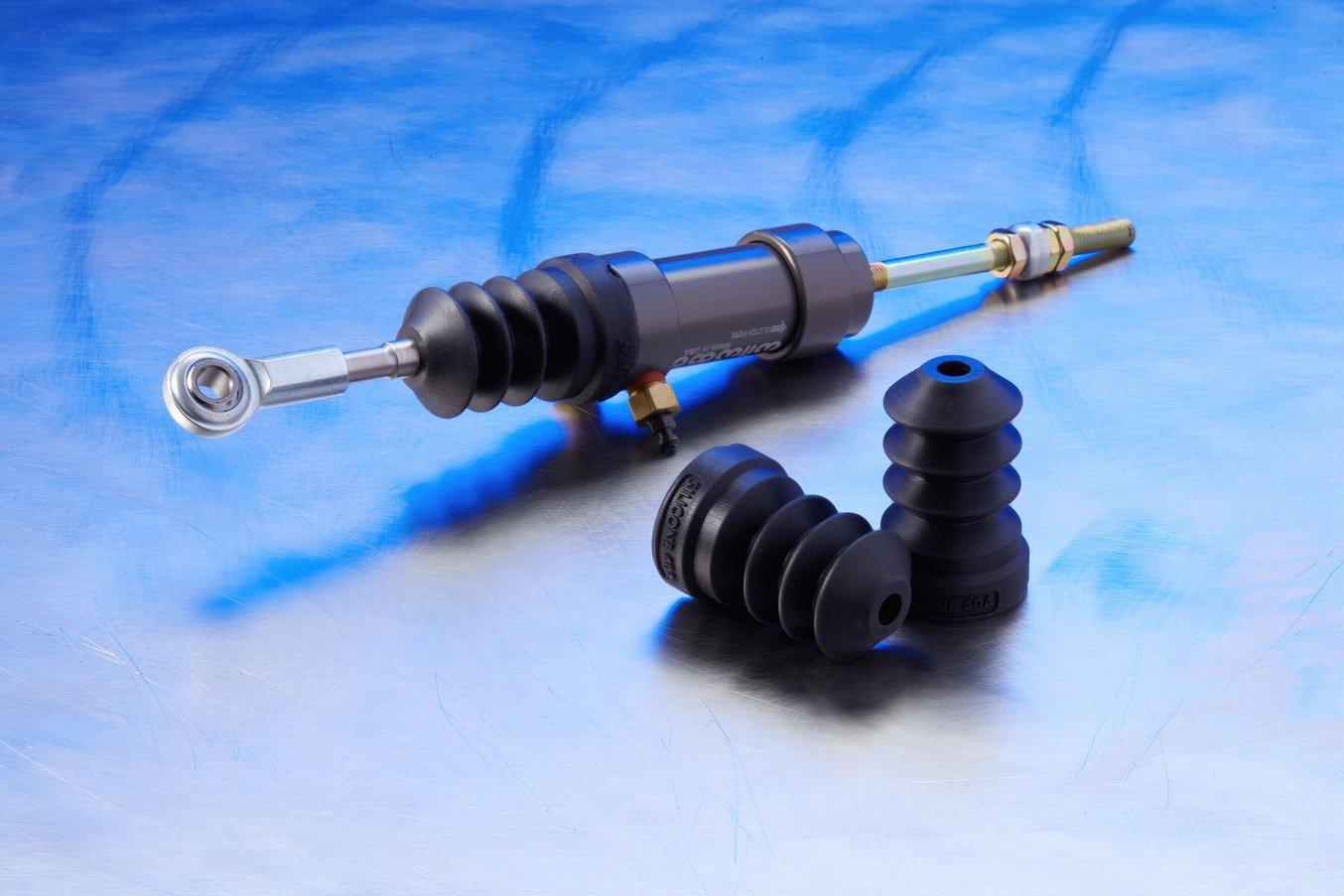
Silicone 40A Resin is a true silicone, with mechanical properties that are familiar to engineers and product designers.
The advantages to open systems are easy to identify — it puts more control in the hands of the user to choose whatever material they’d like. However, the trade-off is that these open systems don’t calibrate material settings specifically for their printers, so accuracy, reliability, and material properties often suffer. Formlabs offers both an extensive library of 40+ unique, custom-formulated resins and the ability to use third-party certified materials through Open Platform. Some of these unique materials are designed for specific and extreme applications, such as open-flame environments, watertight chambers, or injection molding.
Materials are often the deciding factor for opening the door to different applications. Some applications, like electronics manufacturing, require unique formulas and a third-party certification process — like resins that can dissipate electrostatic discharge. Others, like manufacturing aids, require resins that are strong and durable. Many manufacturers offer resins that can fulfill these properties, though strength and durability will vary between manufacturers. When choosing a resin 3D printer, consult the technical data sheets of their materials to determine if the uniquely formulated resins can hold up under your intended use, and safety data sheets to make sure that the resins are safe to use.
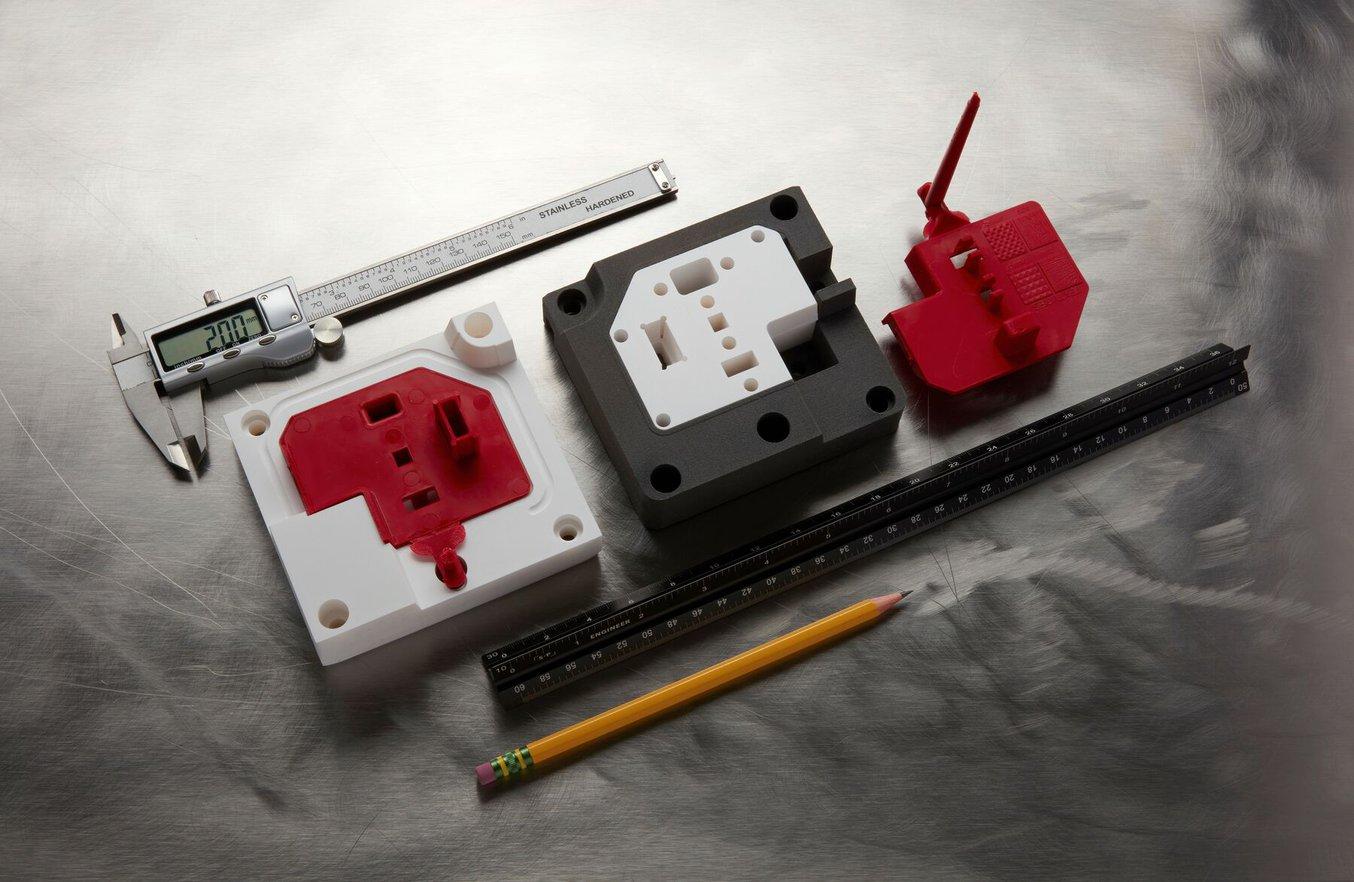
Rigid 10K Resin is a highly glass-filled and extremely stiff material that is similar to glass and fiber-filled thermoplastics. It is ideal for rapid tooling applications like injection molding, blow molding, or thermoforming.
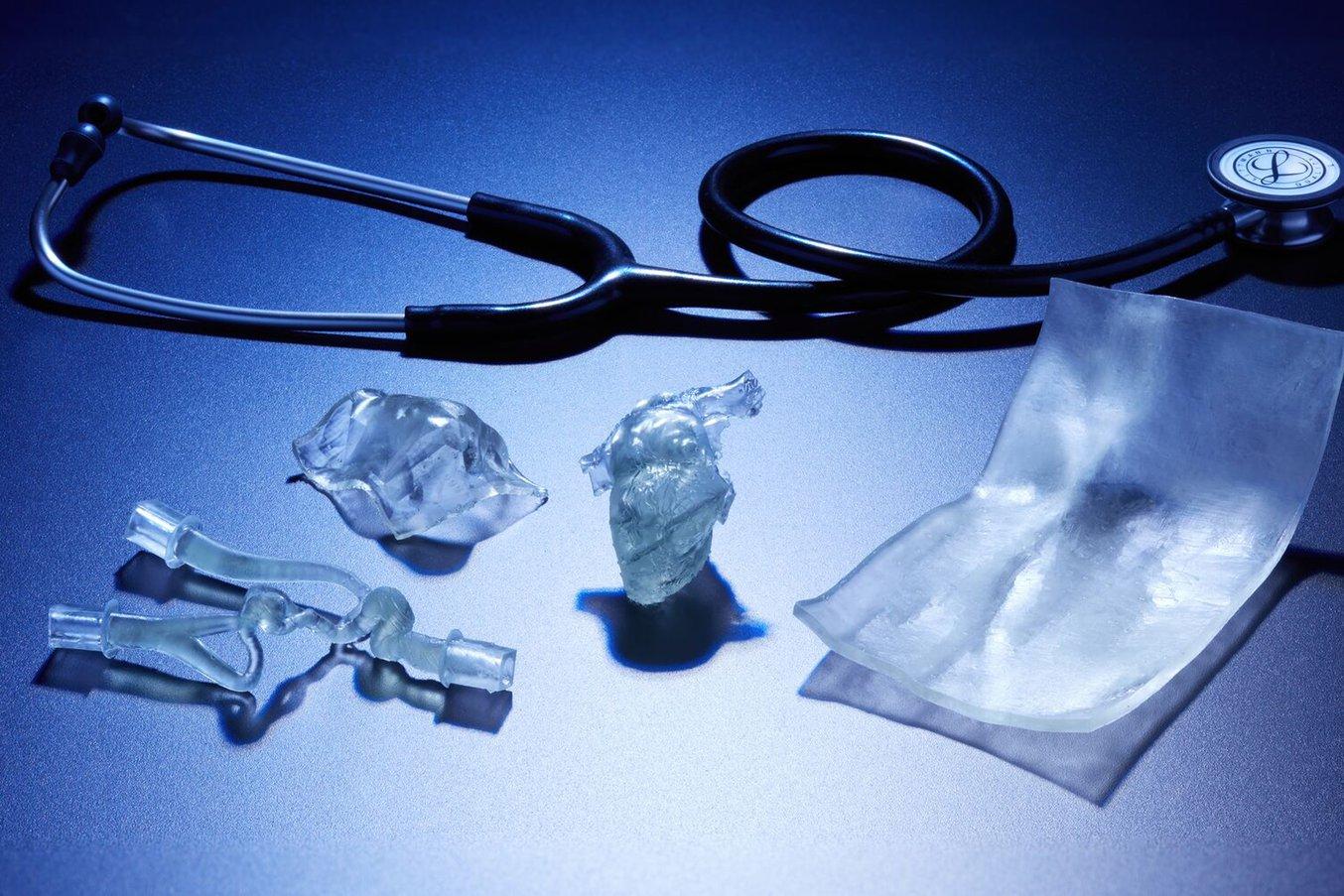
BioMed Elastic 50A Resin enables healthcare providers to 3D print soft, elastic, biocompatible parts with complex shapes such as patient-specific medical devices or soft tissue medical models.
Cost
Resin 3D printers have traditionally been more expensive than FDM 3D printers, but less expensive than SLS printers, though exceptions exist. In recent years, however, prices have come down and resin printers today offer the best value for a wider range of applications.
At the lower end of the range, low-cost LCD 3D printers are available for $200 to $1000. These machines might be suitable for hobbyists or beginners, but they require calibration and fine-tuning for each resin type, and they are generally not reliable or durable, which will often lead to higher costs in terms of maintenance, sunk time, failed parts, and wasted material.
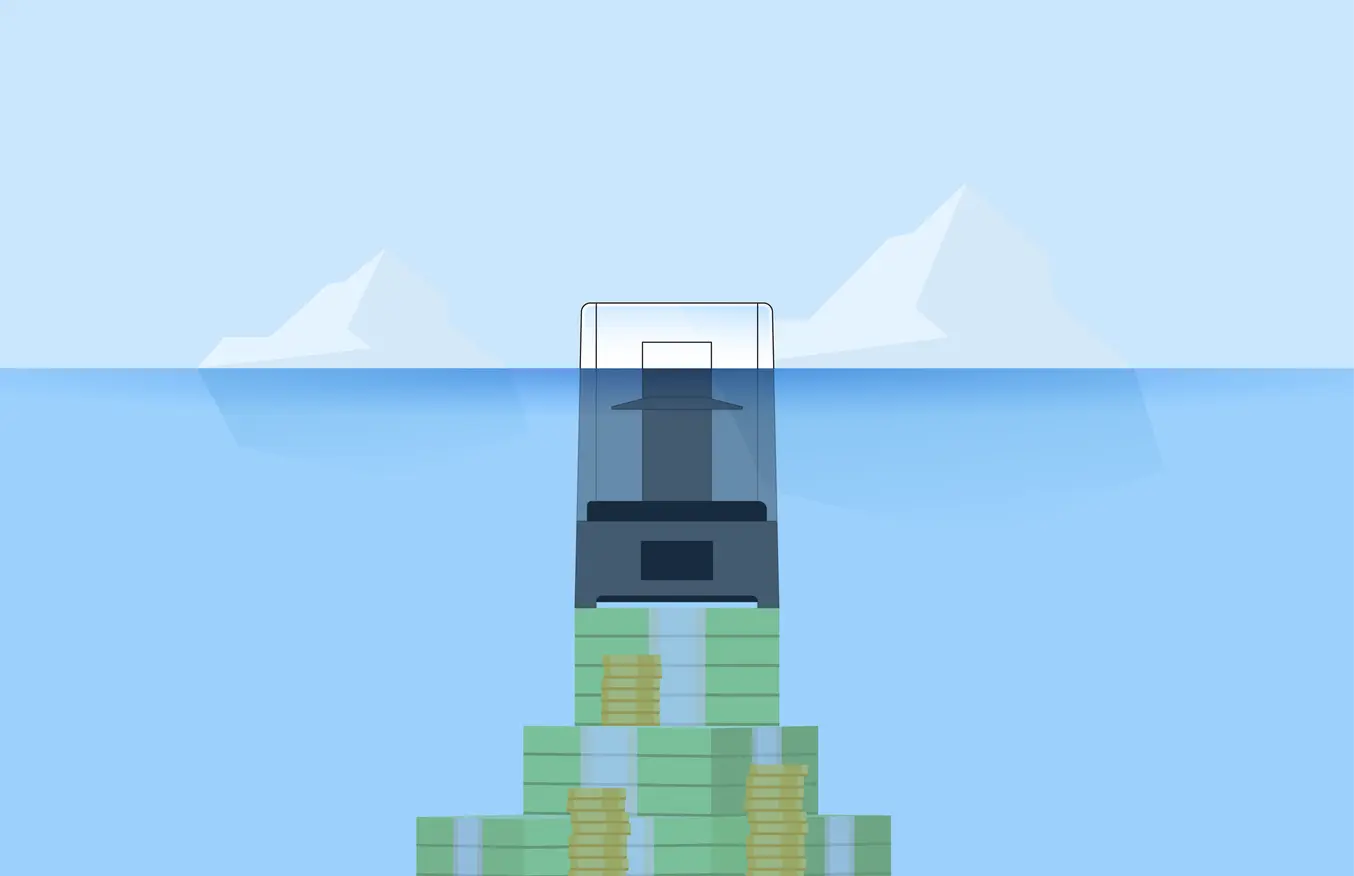
Uncovering the Hidden Costs of Low-Cost Resin 3D Printers
When selecting a 3D printer, it is critical to understand all costs associated with the system to optimize resource allocation and maximize productivity. This report compares the cost and experience of operating low-cost resin printers and a Formlabs SLA 3D printer, demonstrating how hidden costs are dramatically different between these products.
Professional resin 3D printers include SLA technologies including laser-powered SLA, DLP, or LCD/MSLA. Prices are generally in the $2500 to $10,000 range, while large-format resin 3D printers are typically more in the $5,000 to $25,000 range. There are many factors that influence the price in this range, from the more reliable and powerful light sources (whether LEDs, lasers, or projectors) to the light processing solution, overall build quality, software, accessories, and service plan.
Similarly, materials costs differ between manufacturers. As mentioned above, many manufacturers outsource or simply white-label their materials from other suppliers, which can add additional upcharge costs for materials. Low-cost materials, like low-cost resin printers themselves, can have adverse effects on your part quality and create hidden costs, as can using materials that have not been validated and calibrated for a specific machine. Some low-cost materials also create strong odors or have ingredients that make them less expensive to produce but are not certified for safe handling and use.
Formlabs materials are validated for specific use cases and precisely engineered to perform optimally in a range of environments and applications. By investing time and labor into print settings for each layer height and each material, Formlabs ensures that each of the 40+ resins is safe and easy to use.
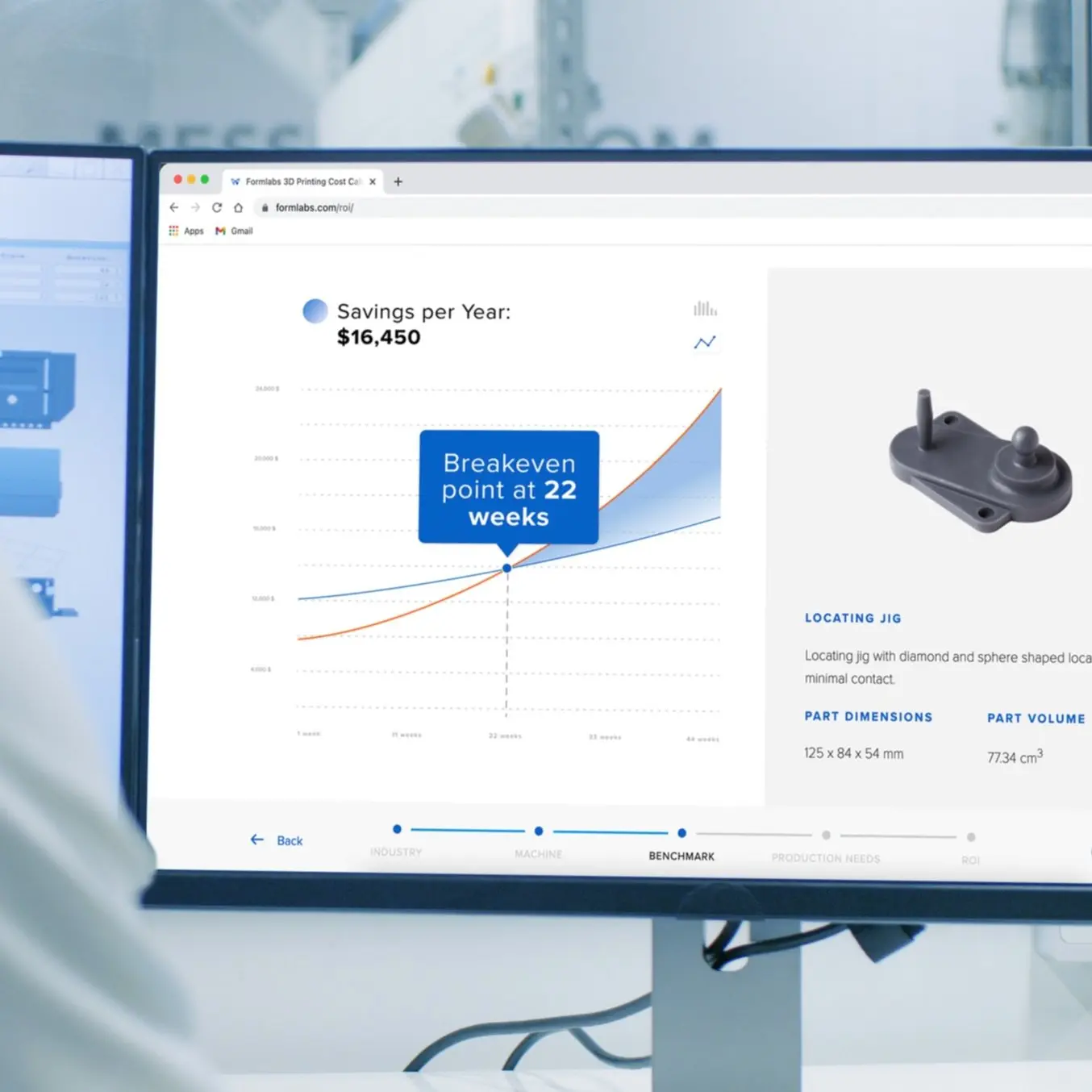
Calculate Your Time and Cost Savings
Try our interactive ROI tool to see how much time and cost you can save when 3D printing on Formlabs 3D printers.
Get Started With Resin 3D Printing
When deciding between laser-powered SLA, DLP, LCD, and MSLA technologies, take your intended application (and thus ideal materials) into account, as well as other factors like speed, accuracy, and resolution.
Though these resin 3D printing processes have some differences, the big differences in machine performance are most often due to differences in the manufacturer’s choices rather than inherent strengths and weaknesses of the process.
Resin 3D printing as a broad category produces parts that are extremely precise and accurate, with smooth surface finishes, faster than any other technology. These parts can cover a wide range of applications due to their unique resin formulations. Professional resin 3D printers like Formlabs’ Form 4, combine the fast speed of resin 3D printing with the surface resolution and accuracy of high-end industrial 3D printers, and offer a wide range of advanced materials, showing the best features of what the technology has to offer.
Learn more about Form 4 and Form 4L or dive into our materials catalog to explore Formlabs' 40+ resins.