How Rosenberger Optimizes Traditional Manufacturing and Lead Times With 3D Printed Tooling and End-Use Parts
Today, our constant internet connectivity — through our phones, cars, refrigerators, and more — makes it easy to forget the technological complexity and innovation that make it possible to connect the world in real-time.
The Rosenberger Group, as one of the biggest global players in this space, is one of the manufacturers that make this connectivity possible. Since 1958 they’ve manufactured high-frequency fiber optic and high-voltage connectivity solutions that power our global network.
To maintain their success in a constantly changing industry (and to be a key driver of that change), Rosenberger has to stay up to date with the latest technologies from other manufacturers, including 3D printing. They’ve incorporated additive technology into their workflow for years, and have worked with Formlabs since 2017.
Today, Equipment Designer Manuel Kaspreiter oversees a fleet of Formlabs 3D printers, including seven Form Series stereolithography (SLA) 3D printers and three Fuse Series selective laser sintering (SLS) 3D printers. Kaspreiter spoke to us about how Rosenberger leverages SLA and SLS technology at every stage of production, from early design iterations to end-use production and manufacturing aids.
Overcoming Initial Skepticism
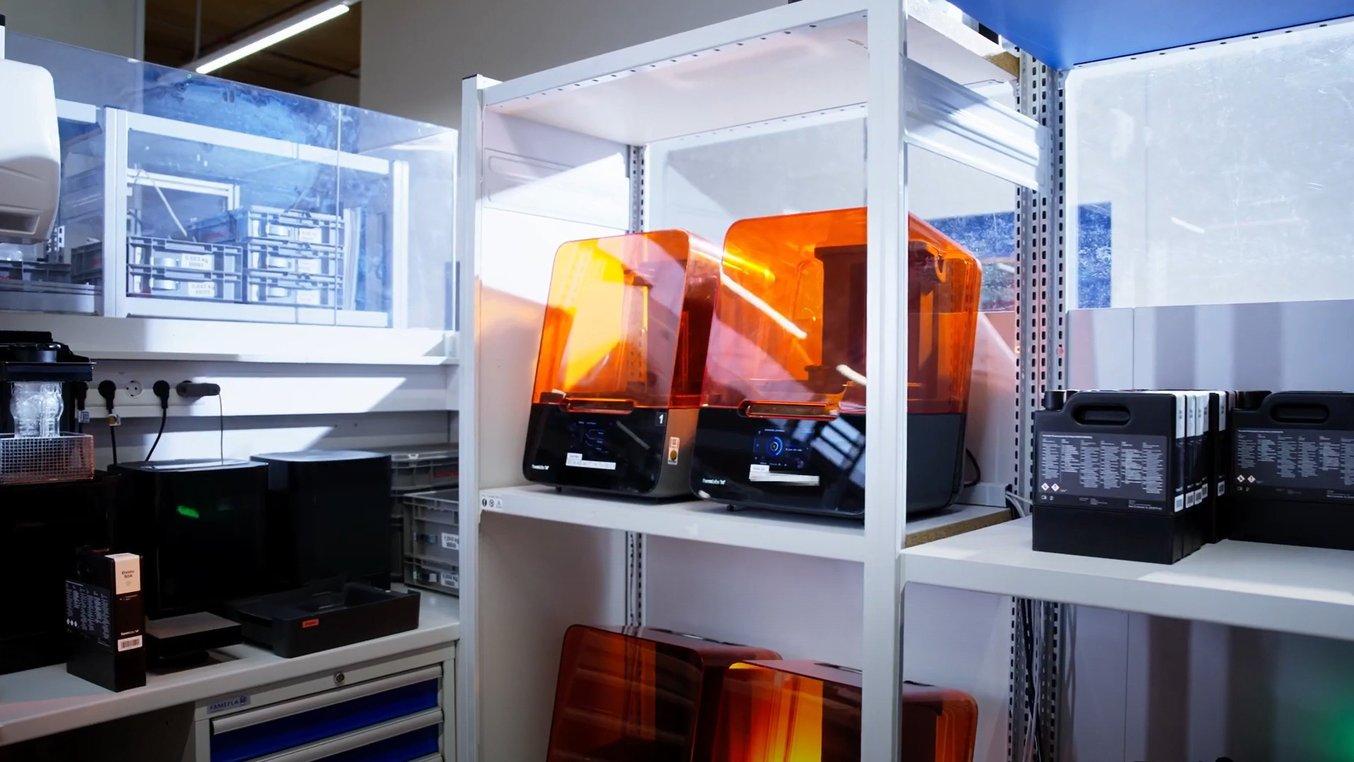
The Form 3+ 3D printers are in almost continuous use at Rosenberger for the production of tools, prototypes, replacement parts, and manufacturing aids.
While 3D printing has now been enthusiastically embraced across departments and functions within Rosenberger, Kapsreiter had to overcome some initial skepticism when introducing the technology. Most employees were only familiar with fused deposition modeling (FDM) 3D printing technology and associated it with low accuracy, rough surface texture, and anisotropy. To get past their initial pushback, Kapsreiter started with SLA 3D printed parts that showcased the smooth surface finishes and machining-grade tolerances.
"Many associate 3D printing with FDM printing, which puts them off. We had to convince people that SLA and SLS are not comparable to FDM... If you need parts with a high surface quality, then SLA really is a good option. Printed in the right material and properly oriented in PreForm, the SLA 3D printed parts can keep up with injection-molded parts," says Kapsreiter.
The quality of the SLA and SLS 3D printers was enough to let the technology speak for itself — today, Rosenberger's 3D printers are in continuous operation fulfilling requests from across the company. Kapsreiter produces parts for prototypes, tools, replacement parts and manufacturing or assembly aids.
"Our colleagues, but also the industry in general, have come to realize that we can be faster and more agile with 3D printing than with machining in order to develop solutions."
Manuel Kapsreiter, Equipment Designer, Rosenberger
Replacements and Improvements for Industrial Production Lines
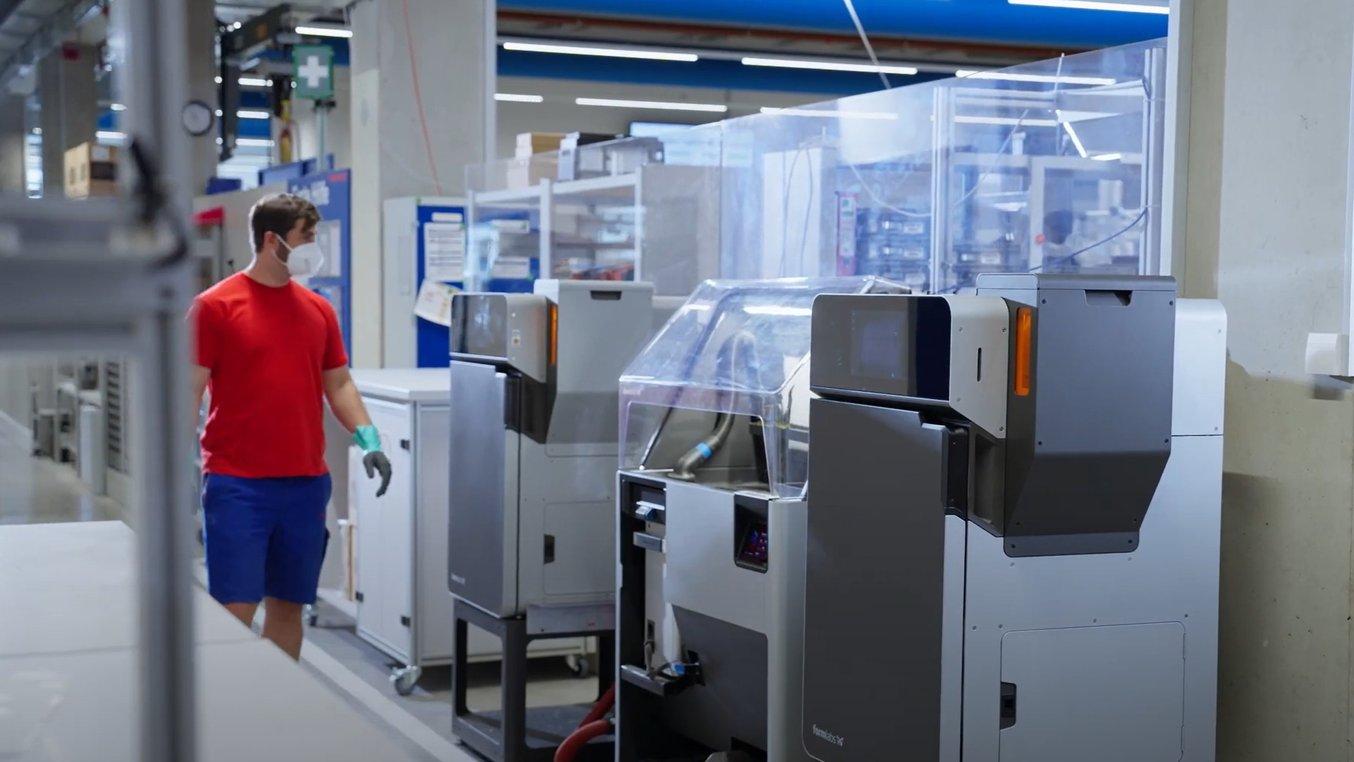
Rosenberger's two Fuse 1+ 30W SLS 3D printers produce on-demand replacement parts for their industrial machinery. These replacement parts were previously milled, but can be made 80% faster with SLS 3D printing.
The production of Rosenberger's diverse products requires a wide range of machines, and the maintenance required to keep them running poses a challenge to the manufacturing operations team. By nature, replacement parts are incredibly time-sensitive. If a machine goes down, production grinds to a halt. The longer production is down, the worse it is for the company’s bottom line.
Rosenberger had always relied on traditional CNC milling for on-demand replacement parts, but as material science has advanced and 3D printers have become faster and more powerful, the technology makes it more efficient and affordable to use 3D printing for quick replacements.
"Compared to milling, we get parts 80% faster with 3D printing and can respond to requirements overnight."
Manuel Kapsreiter, Equipment Designer, Rosenberger
Improved Efficiency Through Custom Manufacturing Aids
As employees have become comfortable and knowledgeable about the power of in-house 3D printing, it’s not only when something breaks that the Form 3 Series and Fuse Series are called into action.
Recently, a production employee noticed that water wasn’t flowing efficiently through an industrial washer, and approached the toolmaking team to design a solution. SLA 3D printing and Formlabs’ versatile material library made it possible to iterate a new design quickly, tweaking the exact angle of the apertures inside the washer so that the water could be directed through a ball-like component. Once installed, the device immediately improved the performance of the washer and reduced energy and water usage.
Once the part was designed, iterated, and tested, Kapsreiter moved to production, printing one for every industrial washer they had to maximize the cost savings and productivity of the factory floor. The unique geometry and low quantity (only 40 are necessary) make it impossible injection mold and difficult to machine, so on-demand 3D printing makes sense for this component moving forward.
"The ball is hollow inside and has holes in all directions and angles. This is a geometry that cannot be produced in any other way. Without 3D printing, it would be much more time-consuming, much more complicated to produce, and not as good a result."
Manuel Kapsreiter, Equipment Designer, Rosenberger
Quick improvements like these, suggested by technicians from all over the factory, can make a huge difference to the company’s operation and productivity. Without additive manufacturing, designers would have to resort to complex casting processes or the milling of several parts, which would have to be laboriously assembled in a further step. Today, they can skip these expensive procedures. With Form 3+, production is faster, more cost-effective, and requires fewer manual steps, as the transparent sphere is printed in one piece. The team only uses CNC milling for the final drill holes, which is no problem thanks to the high toughness, rigidity and strength of Clear Resin.
By avoiding milling, casting, and lathing operations, Rosenberger not only reduces the manufacturing costs and time, but also optimizes the operation of traditional machines. Every process that is shifted towards 3D printing "saves capacities of more expensive production machines, which can then be used for specialized applications that are not suitable for 3D printing. This achieves a more optimal utilization of the existing equipment," explains Kapsreiter.
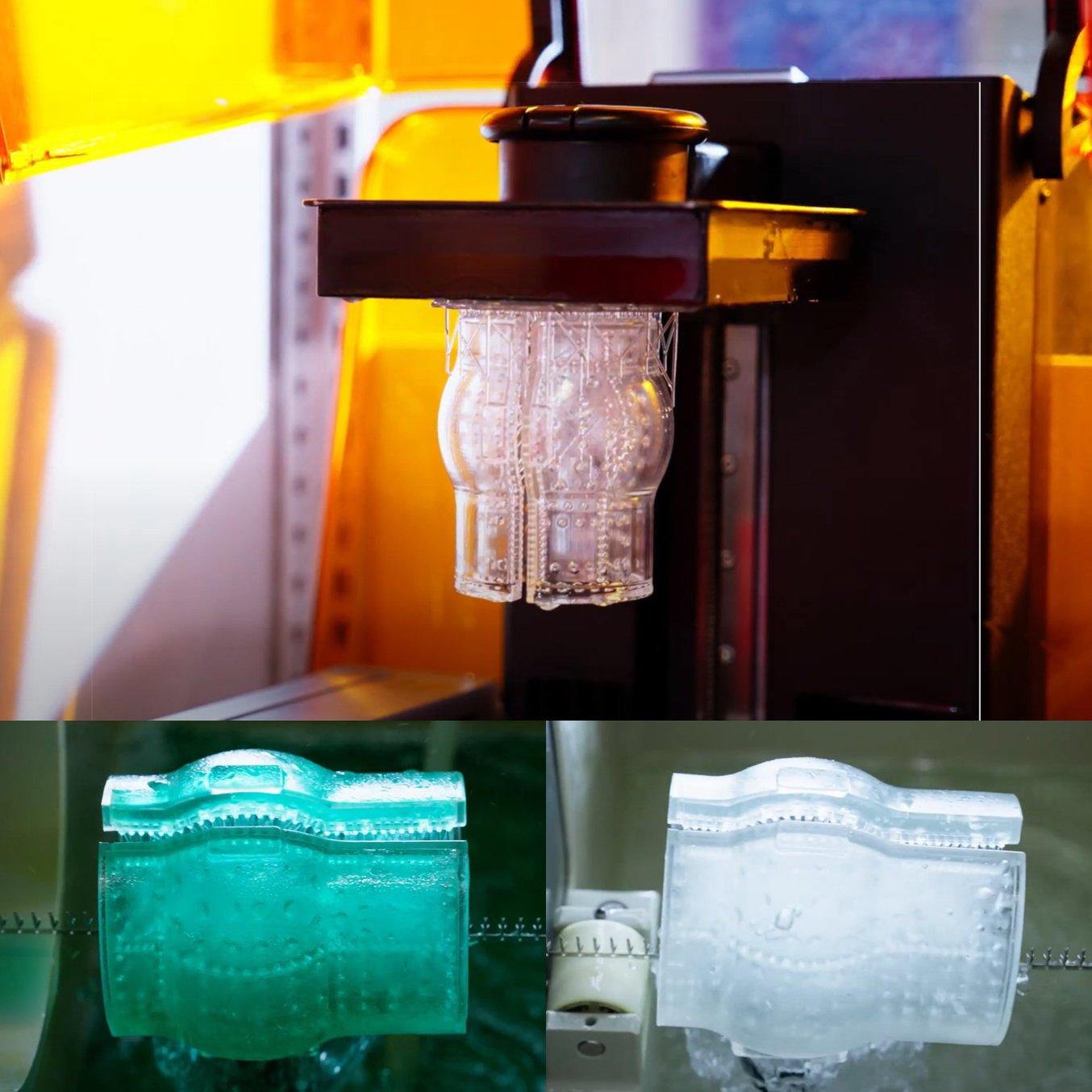
Rosenberger's tooling department uses Form 3+ to print parts with complex geometries such as this wash ball made of Clear Resin, which would be difficult and expensive to produce using traditional methods.
"The production employee who requested the wash ball is absolutely delighted. He has already initiated several other projects where he sees the potential to improve tasks with 3D printed components," says Kapsreiter.
This kind of innovative thinking is exactly what Rosenberger's additive experts are trying to encourage across the company. 3D printing education empowers employees to recognize inefficiencies in their workflows and suggest solutions, saving the company's resources and reducing waste in every department.
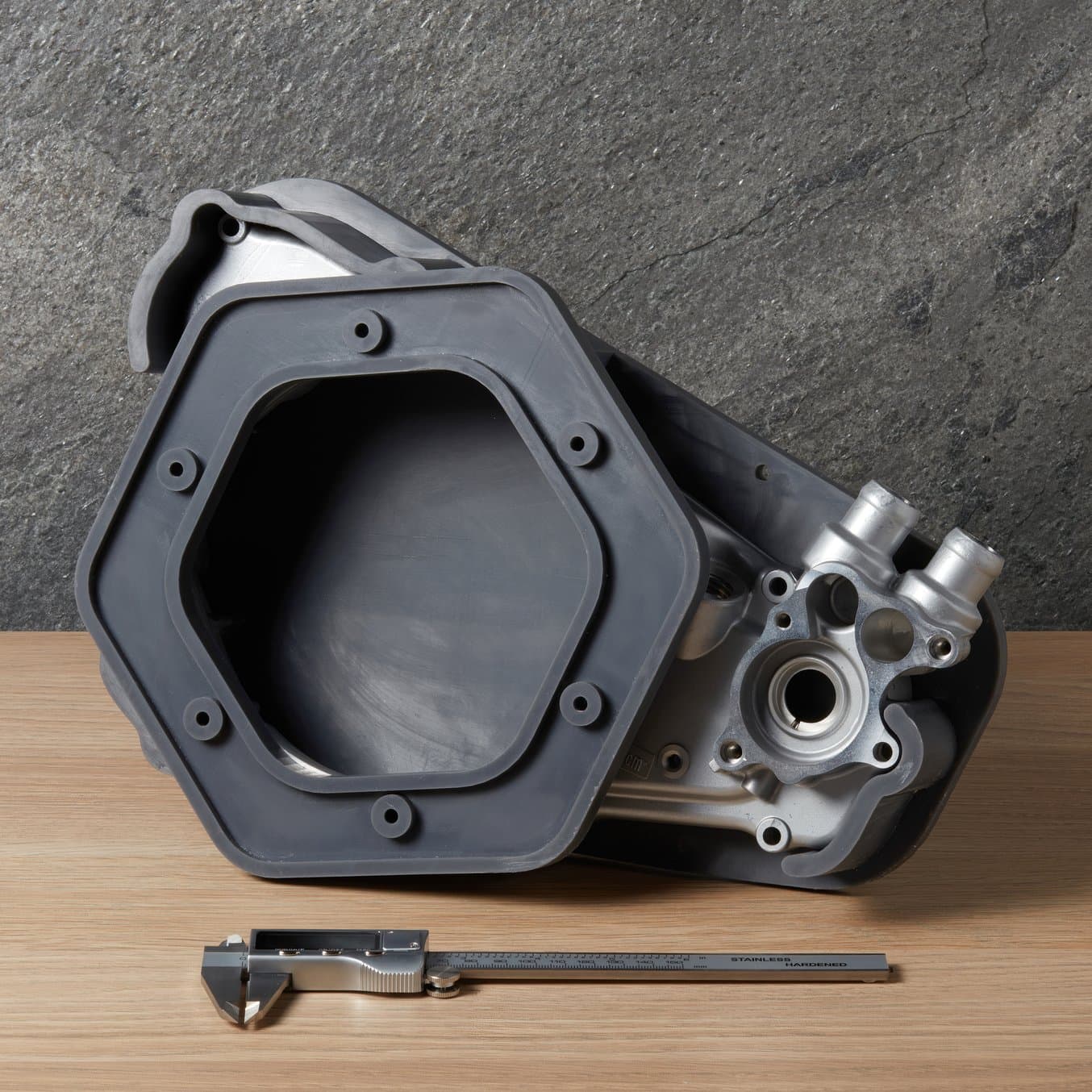
How to 3D Print In-House Jigs, Fixtures, and Other Manufacturing Aids
This white paper outlines the principles behind creating effective jigs, fixtures, and other manufacturing aids in-house.
Increased Throughput – Cost-Effective 3D Printing Series Production
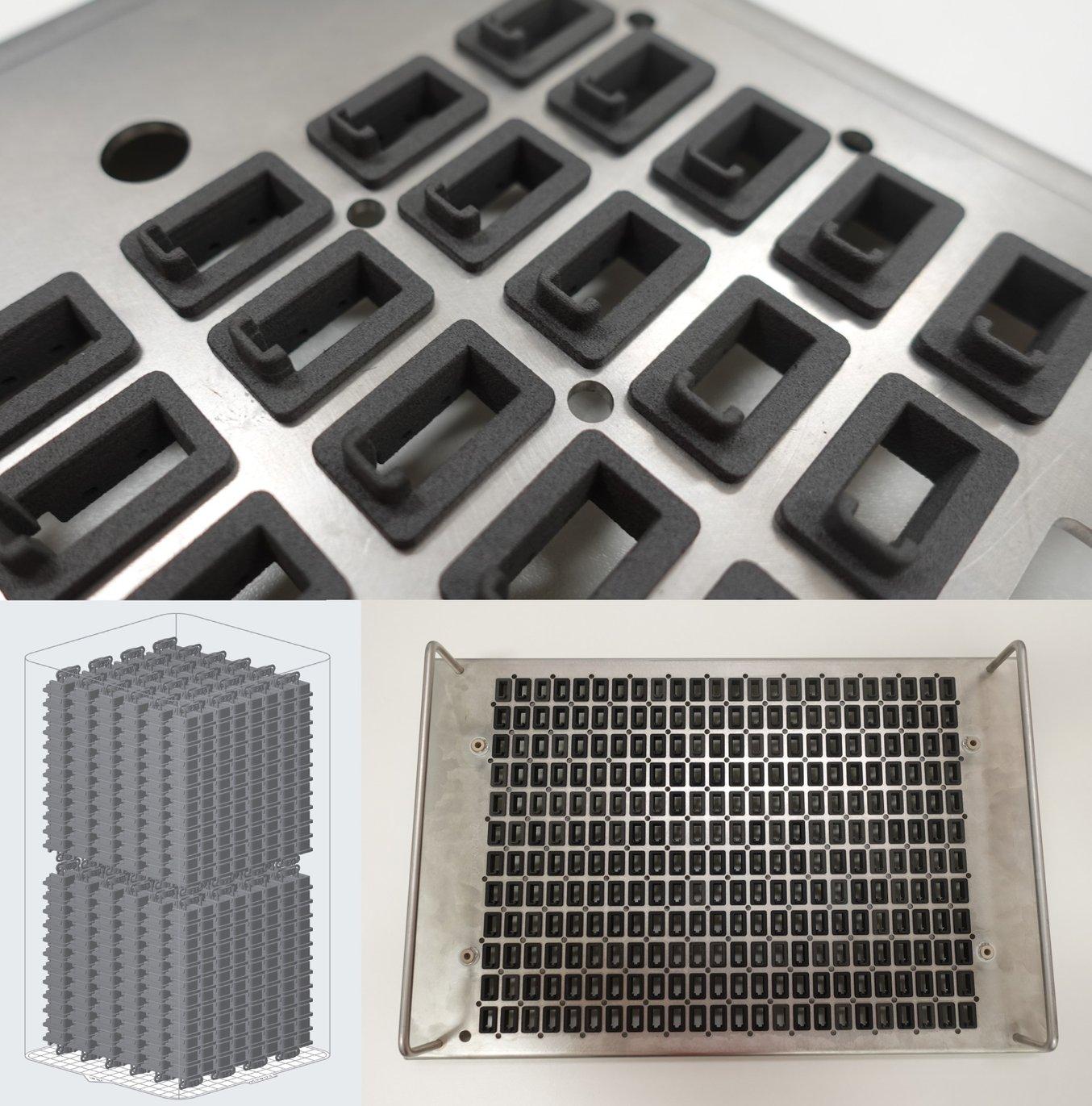
The large build volume and high throughput of the Fuse 1+ 30W enables Rosenberger to produce SLS parts in large quantities at low cost, such as these clips printed in Nylon 12 Powder for use in a washing line.
Both SLA and SLS 3D printing can provide enormous benefits for manufacturing aids, but it’s SLS 3D printing that shines in applications where higher volumes of parts are necessary.
In one cleaning process, a Rosenberger employee noticed that a washing system was only cleaning small batches, despite having the necessary volume capacity for larger batches. He designed a carrier system in which larger batches, placed on a stainless steel plate, could be immersed in the ultrasonic bath. Kapsreiter’s team designed and printed 8500 clips in Nylon 12 Powder to attach the plate. "Our Fuse 1+ 30W ran for five weeks," Kapsreiter recalls. With the help of high-throughput SLS printing, they were able to increase the efficiency of the entire process.
Especially when combined with the Fuse Sift, the Fuse 1+ 30W can handle large-scale production with low effort and low cost per part. The 7.5-liter build chamber of the Fuse 1+ 30W can accommodate several parts at the same time, as SLS printing does not require any support structures, which saves additional material and manual processing.
Rosenberger's tooling department uses the Fuse Sift to remove unsintered powder from the printed parts, 60% of which is recycled. Recently, the team also began using a fully automated sandblasting system — similar to the newly released, innovative Fuse Blast from Formlabs — to clean batches of prints in a closed process, further accelerating the production of large quantities.
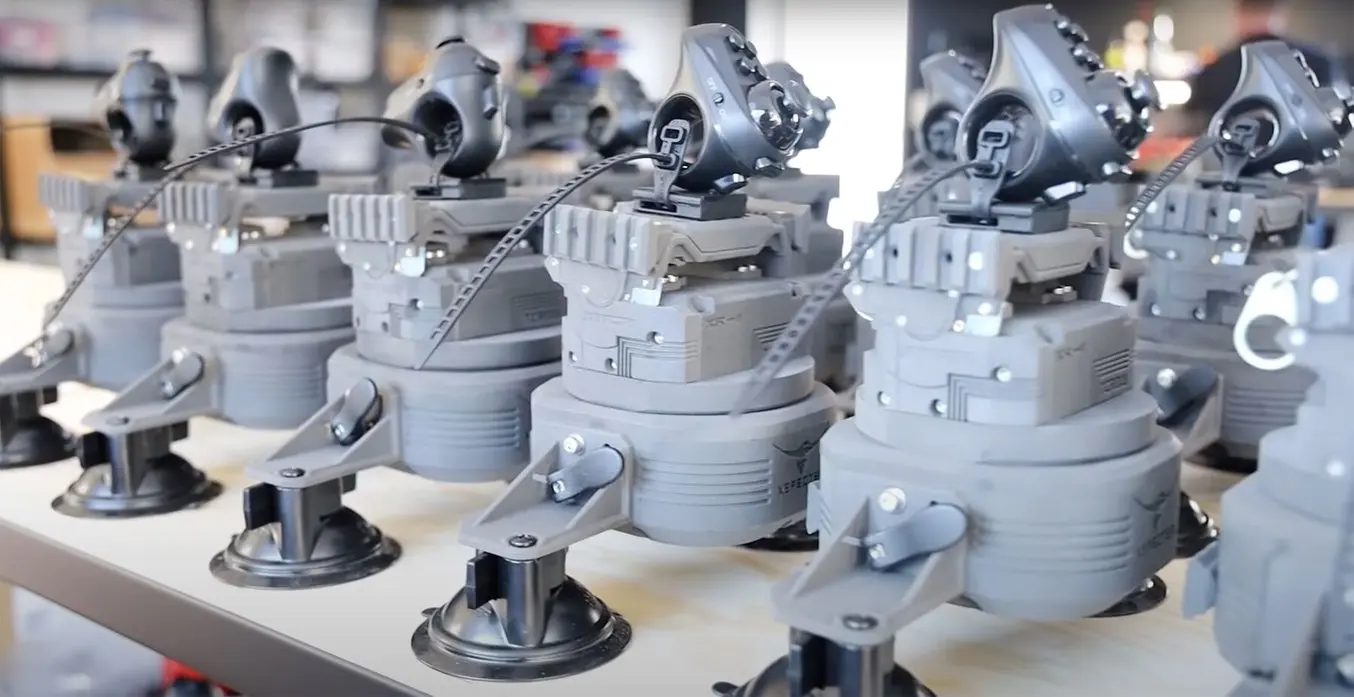
SLS for End-Use Production
3D printing for end-use production is not only possible, it's more affordable, agile, and scalable than ever with the Fuse SLS Ecosystem. Compare production methods, learn about bulk powder pricing, and see production in action for 15 different manufacturers currently using the Fuse Series.
Accelerating Innovation
Before 3D printing, Rosenberger had to use time-consuming injection molding services for prototypes as well as production parts. Due to the high costs and long wait times, employees were hesitant to try new things, and generally refrained from requesting multiple iterations or low volumes of test parts. With the tooling department’s increased 3D printing capacity, employees from every team are able to see their ideas come to life without worrying about potential costs. Form Series and Fuse Series 3D printers can cost-effectively produce quick models and test parts for every application and help customers see their projects through every stage of development.
"In the past, sample tools were made to produce very small quantities by injection molding. 3D printing lets us dispense with expensive metal tools, which makes prototyping much cheaper. The great thing is that you can now also produce sample parts using 3D printing that would not have been made before. This allows us to show customers the state of development — not only on the computer, but also physically. You can look at it in CAD and try to simulate it, but physically holding the part in your hands and testing it at the place of use gives you a completely different feel for it," explains Kapsreiter.
"The big advantage of 3D printing is its accessibility. The fact that you can get a physical item quickly and at low cost has greatly lowered the threshold for trying out new things. Because it's so cheap, you can make a mistake, learn from it and make improvements the next time you try it. And that is a great strength of 3D printing."
Manuel Kapsreiter, Equipment Designer, Rosenberger
Choosing the Right Technology and Material
The particular challenge for Rosenberger's tooling department is the need to constantly produce unique parts in a short time. Complex processes or failed prints slow them down, so an intuitive interface and easy workflow are important. They need to rely on the printer to deliver consistent results, every time, without tweaking or adjusting the worfklow.
"It was always important for us that the prints offered dimensional accuracy, were robust, had good mechanical properties and were reliable... Form 3 is very reliable — there's no comparison to other systems. As we have a very large variety of parts which we hardly ever print twice, it is always important to us that the labor time per print is relatively low. And these were precisely the arguments in favor of the Formlabs system."
Manuel Kapsreiter, Equipment Designer, Rosenberger
Operating cross-sectionally, Rosenberger's tooling department not only has to produce parts quickly, but also support a variety of different areas with different requirements. The expectations regarding print quality, precision, and material properties are high so that prints can be used in Rosenberger's professional production. It is therefore essential for the team's work to be able to draw on a broad portfolio of materials. A key argument for Formlabs 3D printers for Kapsreiter was "the wide range of materials that are available and with which we can cover many different applications."
Rosenberger bases its decision between SLA and SLS on the required production volume and the required material properties of the parts to be printed. The team uses Form 3+ primarily when smooth surfaces and a high level of detail are required. For larger components, large batches, or when they need properties similar to injection molding, the team prefers the large build volume and cost-effective thermoplastic printing materials of the Fuse 1+ 30W. Rosenberger's toolmakers most frequently print with:
- Tough 2000 Resin, due to its high similarity to ABS, stability and resistance to fracture, for example for casing prototypes with latching lugs or mounting brackets
- Rigid 4000 Resin, due to its high stability and rigidity, for example for punches for toggle presses in assembly
- Rigid 10K Resin, due to its very high stability, very high rigidity and heat resistance, for example for wear-resistant parts such as sliding plates
- Grey Resin, due to the low price for prototypes
- Flexible 80A Resin, due to its pliability, for example for waterproof seals for plugs, housings, and tools as well as robot gripping units
- ESD Resin, due to the deep black color for illustrative purposes
- High Temp Resin, due to its superior heat resistance, for example for soldering devices
- Clear Resin, due to its transparency, for example for wash balls and transparent covers
- Nylon 12 Powder, due to the low price and large build volume of the Fuse 1+ 30W, for example for large components or batches of smaller parts
In addition to the variety of materials, print quality, reliability and intuitive operation, the low upfront costs were also critical factors in Rosenberger's decision in favor of the Formlabs ecosystem.
"The printers [from Formlabs] are simply very affordable. Of course, this is an argument that the competition really has to swallow."
Manuel Kapsreiter, Equipment Designer, Rosenberger
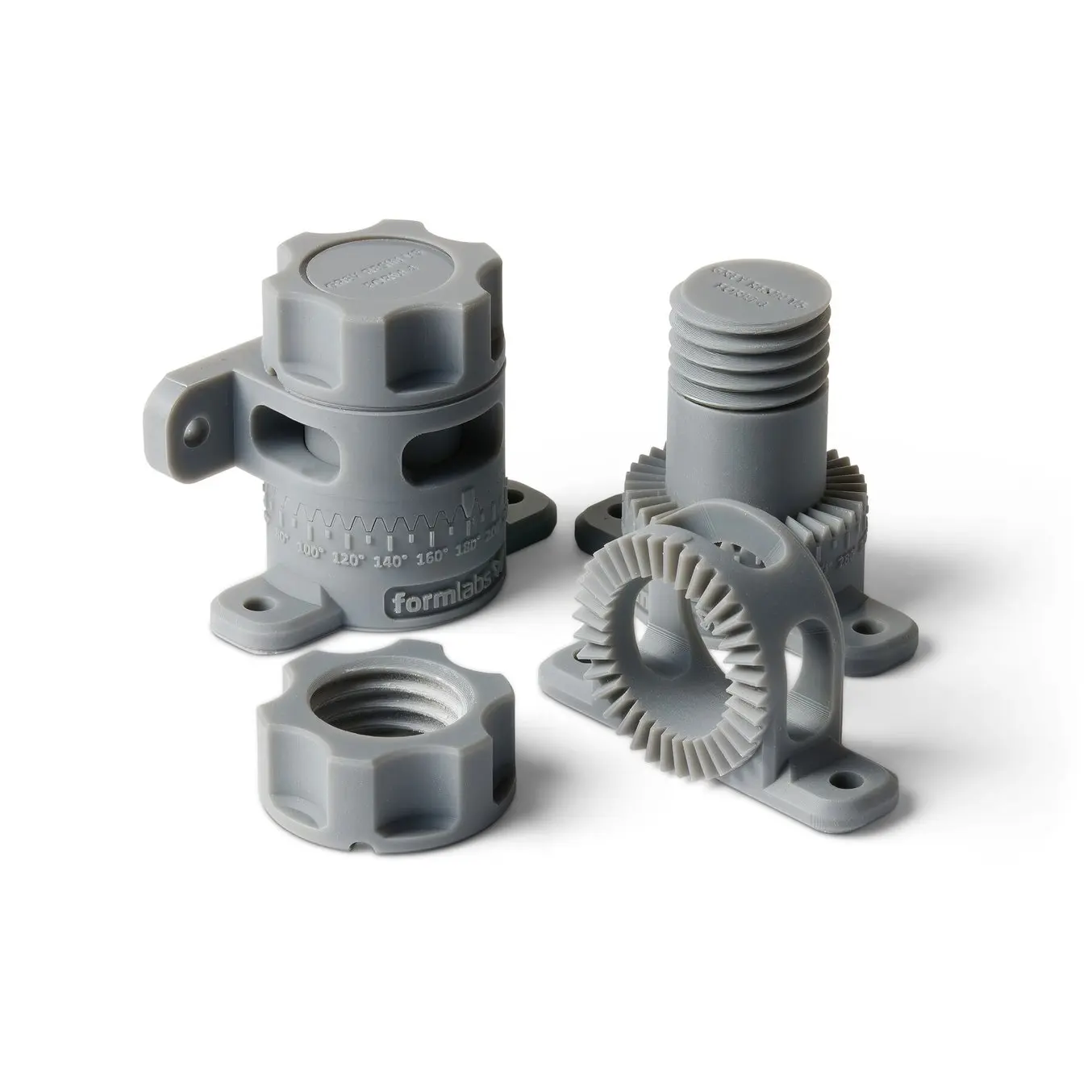
Request a Free Sample Part
See and feel Formlabs quality firsthand. We’ll ship a free 3D printed sample part to your office.
Continuous Expansion of 3D Printing at Rosenberger – From Fridolfing to the World
Running the workshop and coordinating the large number of employee requests required the team set up new workflows.
With the help of a self-developed ticketing system, Rosenberger's tool shop receives 3D printing requests from all areas of the company. Once printing and post-processing are complete, the parts are sent on their way – sometimes to distant company locations in Asia. After Kapsreiter’s 3D printing program demonstrated such tangible success, other areas of the company have begun to take notice.
"Our site in Augsburg has purchased a printer within a year and a second one a few months later. You could call it the success story from Fridolfing. Of course, other locations also see the advantages, and they naturally followed suit."
Manuel Kapsreiter, Equipment Designer, Rosenberger
After six years of positive experiences at Rosenberger, Kapsreiter recommends that all industrial companies reconsider any preconceptions they may have about additive manufacturing, having initially faced some skepticism himself. Thanks to its versatile applications, low manufacturing costs and fast turnaround times, 3D printing is a valuable addition to industrial production facilities.
"3D printing is simply an additional tool, with additional possibilities and additional strengths, and it's the right development for the vast majority of companies. You shouldn't neglect it, but rather choose the best possible option for you. For most people, it will be a wake-up call when they realize how much they can print and how much time they can save," says Kapsreiter.
Today, the Rosenberger tooling team receives a steady stream of print orders. More and more employees in production and assembly want to implement their ideas for process optimization with 3D printing. For Manuel Kapsreiter, it is therefore clear that 3D printing at Rosenberger is a success story that he is determined to continue. To this end, he wants to increase internal additive manufacturing capacities "because demand simply keeps rising."