500 pièces en deux jours : des essais de perçage pour Airbus sauvés par l’impression 3D
En fabrication avancée, l’une des plus grandes difficultés est de garantir un assemblage parfait des structures complexes telles que les robots, les ensembles à assistance numérique et les technologies d’usinage. L’Advanced Manufacturing Research Centre (AMRC) abrite la Factory 2050, une structure d’un budget de 43 millions de livres. Cette dernière accueille l’Integrated Manufacturing Group, un groupe de recherche collaborant avec des partenaires industriels pour fusionner ces technologies avancées et développer des systèmes intégrés.
Le groupe de recherche a récemment travaillé sur un projet pour Airbus, premier fabricant européen en aérospatiale, impliquant le perçage et l’usinage haute tolérance de composants en fibre de carbone, en aluminium et en titane.
Les exigences du secteur de l’aérospatiale sont extrêmement strictes, il était donc capital d’empêcher toute contamination croisée des trous durant ces essais. Dès le début du projet, l’équipe a réalisé que la solution prévue n’était pas suffisante pour résoudre le problème, et l’usinage ou le moulage par injection de pièces de rechange aurait signifié des semaines de retard.
George Sleath, ingénieur de projet du groupe Integrated Manufacturing, nous a expliqué que l’équipe a utilisé l’impression 3D pour produire rapidement 500 bouchons de perçage haute précision, réduisant ainsi le délai de réalisation de plusieurs semaines à trois jours seulement.
Sleath et l’équipe d’ingénieurs ont travaillé avec la station de fabrication additive en accès libre de l’AMRC pour fabriquer les pièces requises. Lisez notre étude de cas pour découvrir l’accès libre à l’impression 3D et l’aide qu’il apporte à des centaines d’ingénieurs sur l’ensemble du site.
Des essais avec différentes méthodes pour éviter la contamination croisée
« L’une des exigences capitales du processus de perçage était d’exclure toute contamination dans les trous. Cela signifie qu’après avoir percé un trou, avant de passer au suivant, nous devions couvrir le premier pour éviter que tout élément issu du perçage contamine le second trou. Lorsque nous avons réalisé que nous devions répondre à cette exigence et utiliser un bouchon pour les trous, il ne nous restait plus que peu de temps pour fournir une solution », a ajouté Sleath.
Tout d’abord, les ingénieurs ont essayé d’utiliser une pièce en aluminium dotée d’un petit joint torique en caoutchouc mais cette solution ne permettait pas de résoudre le problème de façon satisfaisante. Le projet entier en a été freiné, ce qui n’était pas acceptable au vu du temps imparti pour conclure le projet.
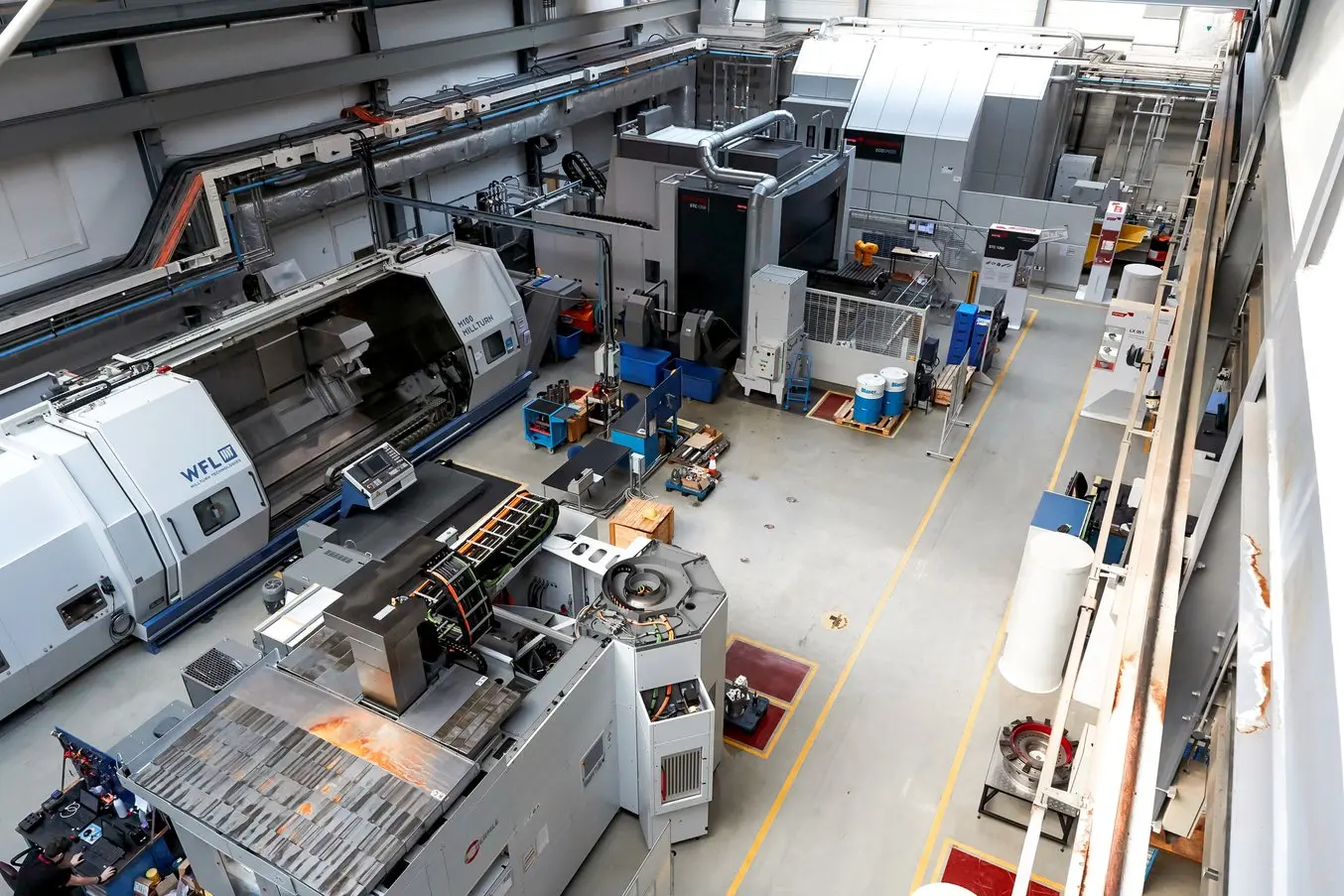
L’équipe a ensuite conçu un nouveau design : un petit disque avec un canal usiné sur le pourtour extérieur pour accueillir le joint torique. La pièce était soumise à des exigences de tolérance relativement strictes ; si le canal usiné était trop grand et que le joint s’enfonçait dans le côté de la pièce, le joint n’était plus constitué par le joint torique mais par le plastique. La plage de tolérance acceptable était de la moitié de l’épaisseur du joint torique, environ un demi-millimètre.
La variété des pièces présageait également de complications pour la fabrication. « Nous devions produire de multiples variations car nous devions percer des trous de différentes tailles et nous avions donc besoin de différents bouchons de perçage. Du point de vue de la conception virtuelle, changer une dimension ne prend pas beaucoup de temps, mais si vous prévoyez de fabriquer les pièces moulées par injection, vous devez produire un moule pour chaque nouveau bouchon, » a expliqué Sleath.
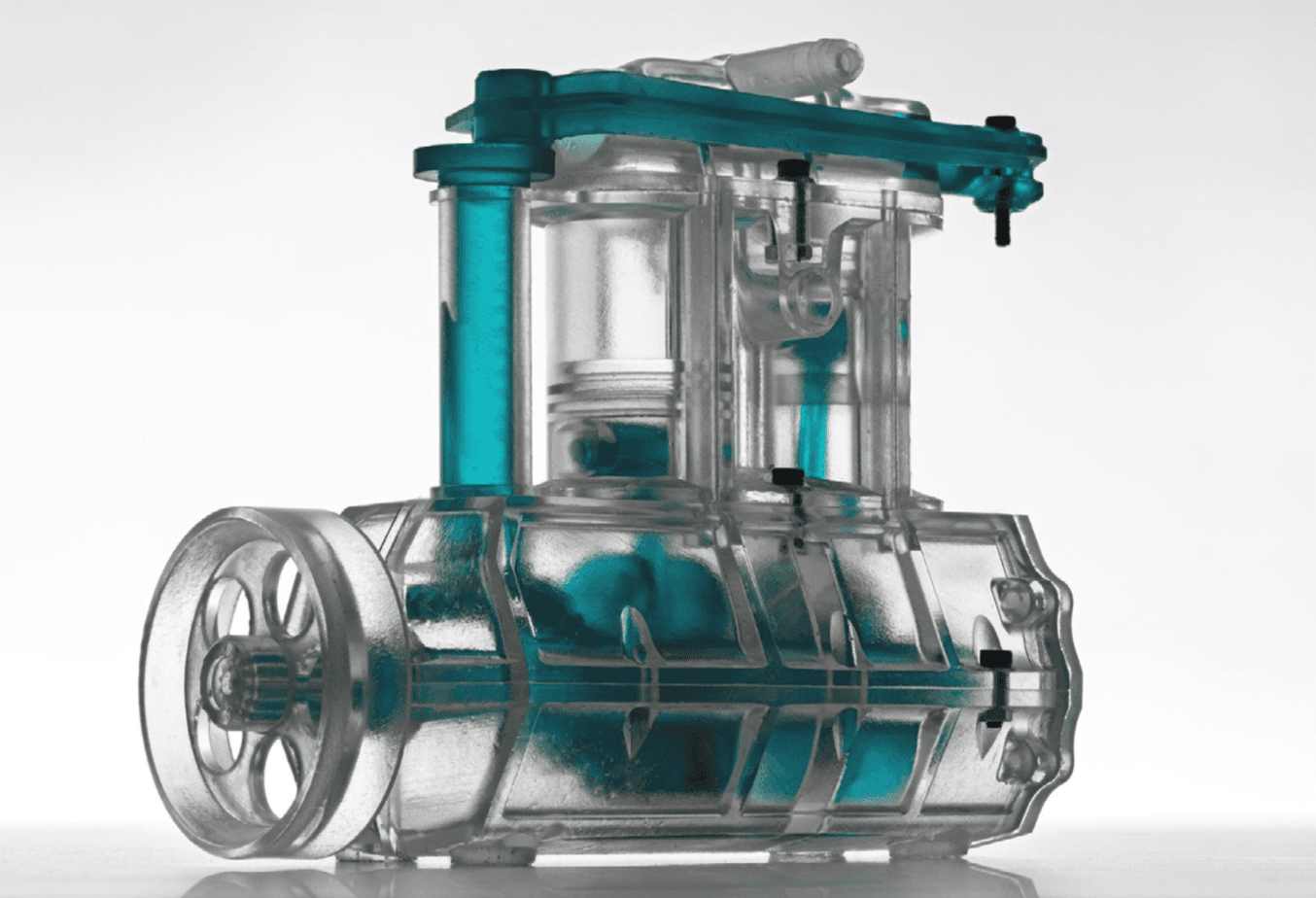
Livre Blanc : Tolérances d'usinage
Téléchargez notre livre blanc pour en savoir plus sur la tolérance et l’adéquation dans la conception d’assemblages fonctionnels imprimés en 3D.
Téléchargez le Livre Blanc
Impression en 3D de 500 bouchons protecteurs en deux jours
L’équipe avait besoin d’environ 500 de ces petits bouchons en dix jours, ce qui exclut de fait toute option de fabrication, sauf l’impression 3D.
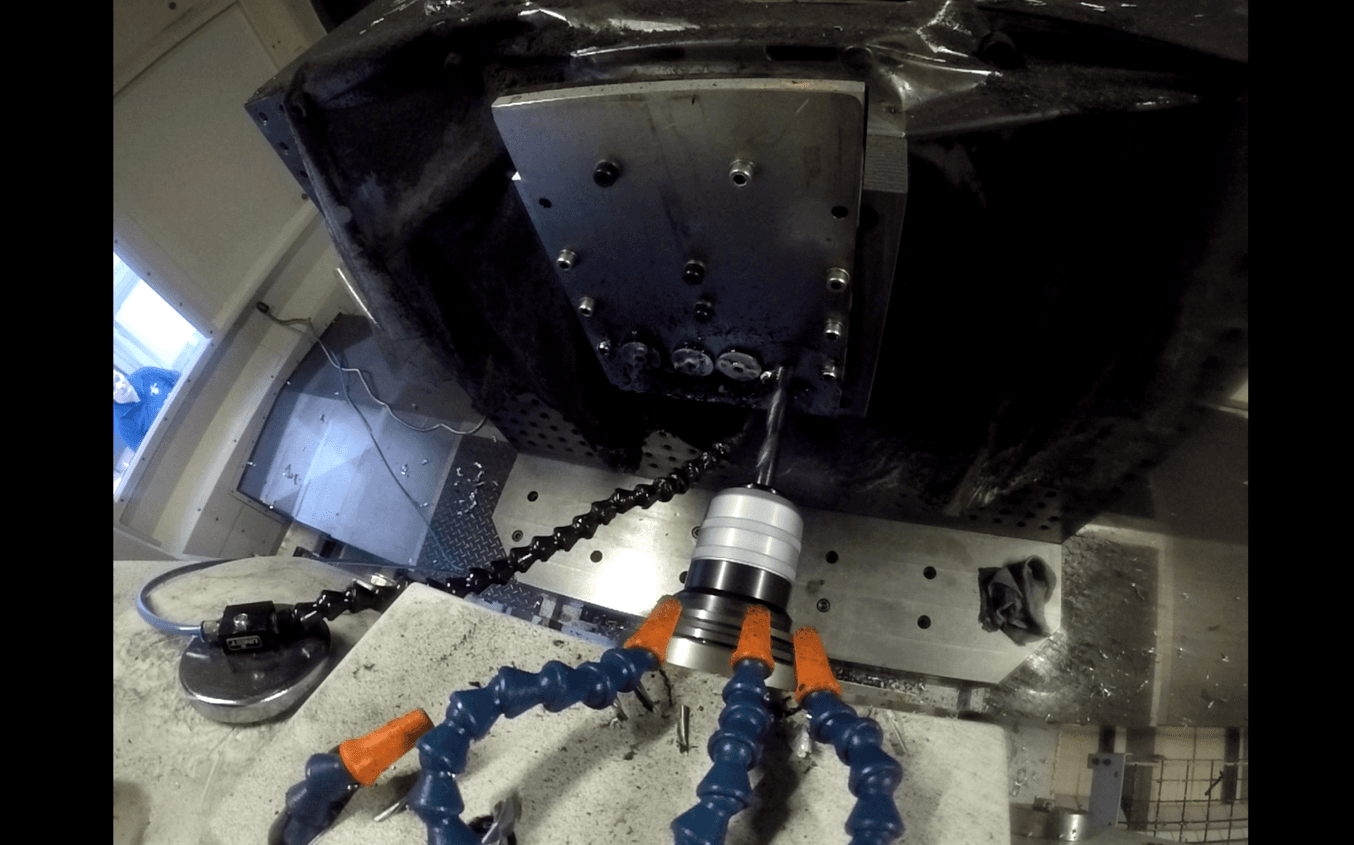
À ce moment-là, Sleath n’était pas sûr des capacités internes de l’AMRC et a demandé des devis à trois centres d’impression externes. Mais au vu de la plus-value estimée des pièces à imprimer dans le projet, les devis étaient bien trop élevés.
« J’ai ensuite parlé avec Mark Cocking de notre groupe Conception et Prototypage et je lui ai demandé quelles quantités il était possible de fabriquer en interne. J’ai attendu sa réponse durant 24 h mais lorsqu’elle est arrivée, il m’a dit « Oui, nous en avons déjà imprimé la moitié. » 250 de ces bouchons de perçage imprimés en 24 h, c’était une vitesse de production incroyable, », a déclaré Sleath.
"250 de ces bouchons de perçage imprimés en 24 h, c’était une vitesse de production incroyable"
George Sleath - AMRC
Finalement, Cocking a réussi à imprimer tous les composants en deux jours.
« Cela voulait non seulement dire que nous avions les pièces plus tôt que prévu et que nous pouvions les utiliser, mais nous avons même pu passer à autre chose et arrêter de nous inquiéter pour la date de livraison de ces pièces, » a ajouté Sleath.
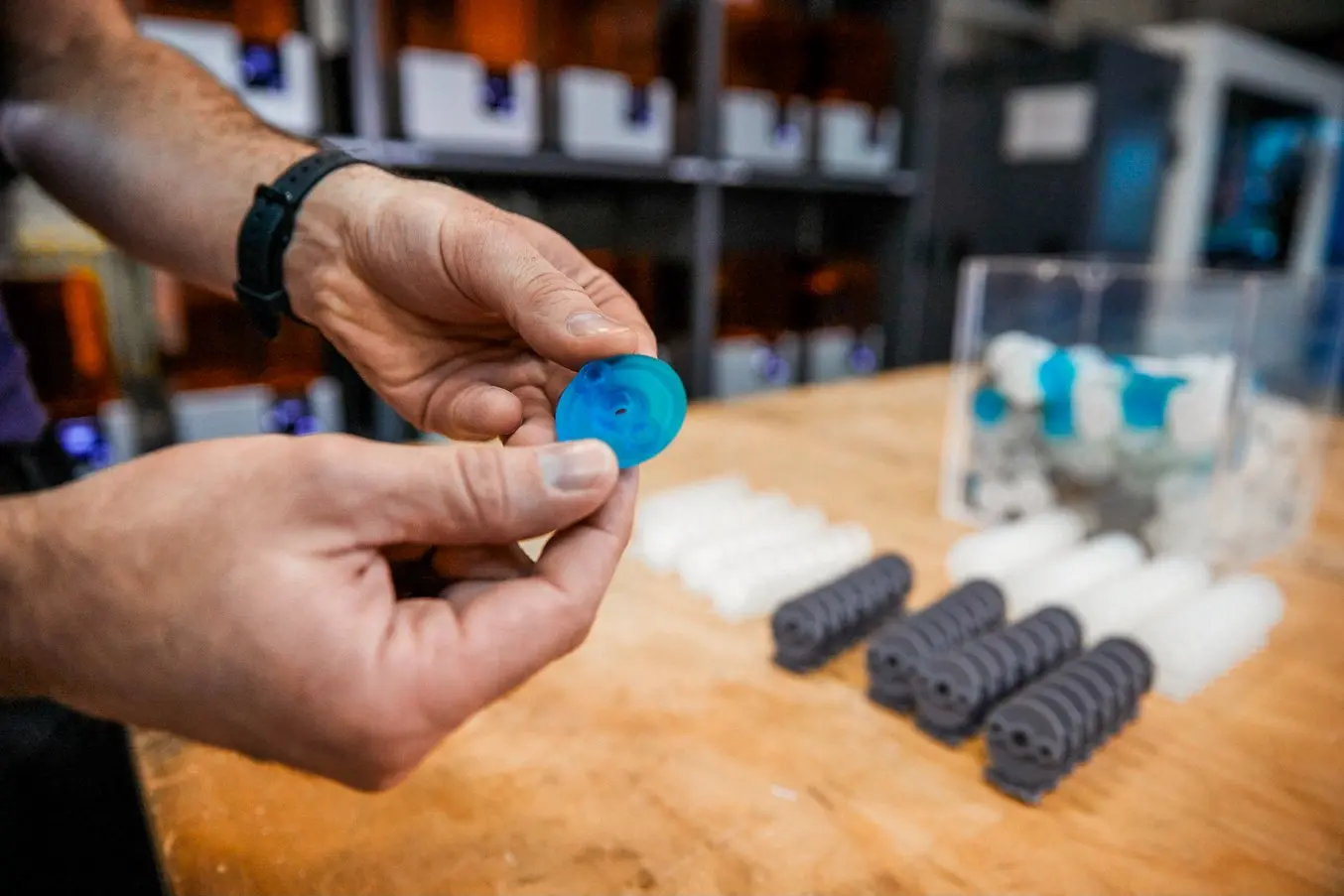
La station d’impression 3D en interne offre la flexibilité et l’espace nécessaires pour les répétitions
Durant l’impression des pièces en 3D, les ingénieurs ont également été en mesure d’inclure une géométrie dans la pièce qu’ils ont pu reproduire dans un outil par impression 3D, permettant ainsi d’installer les bouchons rapidement.
« Les retours que j’ai reçus de la part des opérateurs chargés d’installer les bouchons sont fantastiques. La grande majorité des pièces a fourni exactement le résultat attendu et aucune ne s’est cassée durant l’opération, » a déclaré Sleath.
Outre la rapidité de la production et les faibles coûts, l’impression 3D en interne présente un avantage supplémentaire non négligeable : la flexibilité.
« Si le design n’avait pas fonctionné lors des essais, nous aurions pu reprendre et corriger la conception rapidement. Il en aurait été autrement si nous avions dû envoyer le premier design à un bureau externe et que nous avions réalisé qu’une modification mineure était nécessaire alors que le prestataire nous renvoyait les 500 pièces sur plusieurs semaines, » a poursuivi Sleath.
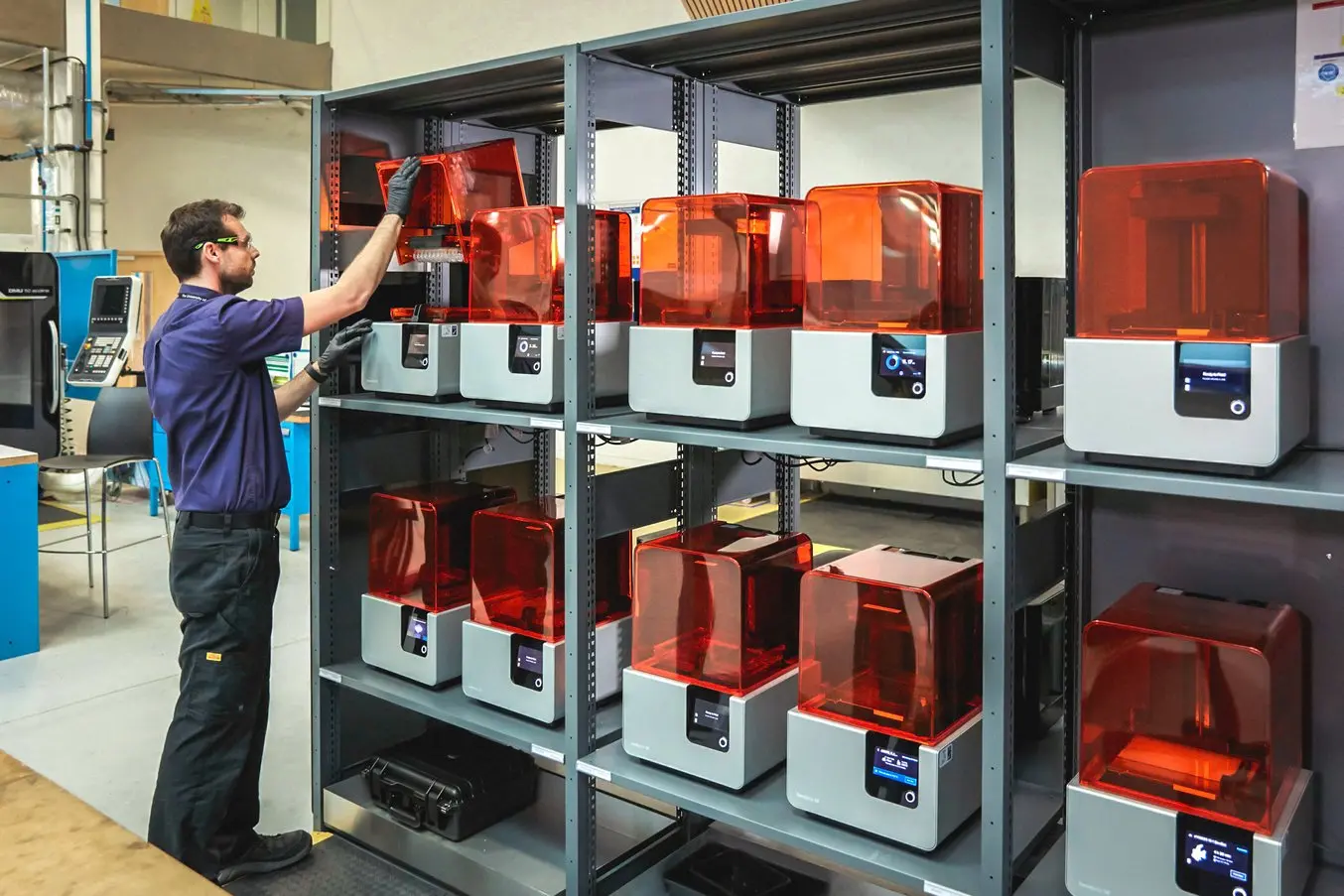
Découvrez la station d’impression 3D et l’assistance qu’elle fournit à des centaines d’ingénieurs de l’AMRC
« J’aime utiliser l’impression 3D pour répéter les essais rapidement durant la phase de conception. Par exemple, j’imprime une pièce en 3D et j’observe les résultats qu’elle donne sur le terrain, puis je renvoie rapidement un nouveau design à l’imprimante. Parfois, j’arrive à tester deux ou trois designs par jour grâce à la vitesse du processus et à son faible coût. Avec le nouveau projet de libre accès de l’AMRC, auquel le site entier travaille pour que tous puissent en profiter, je pense que tout le monde va commencer à utiliser l’impression 3D bien plus souvent, » a ajouté Sleath.
Découvrez la station d’impression 3D de l’AMRC et les autres applications telles que les attaches de capteur thermorésistantes pour le soudage, les attaches très complexes d’un organe de préhension et les cylindres d’enroulement filamentaire personnalisés pour la fabrication de composites.
Vous souhaitez en savoir plus sur les imprimantes et les technologies utilisées dans la station d’impression 3D de l’AMRC ? Explorez la Form 3, la Form 3L et la sélection de résines techniques Formlabs pour voir si elles s’appliquent à votre propre projet, ou demandez un échantillon 3D gratuit pour découvrir nos matériaux directement.