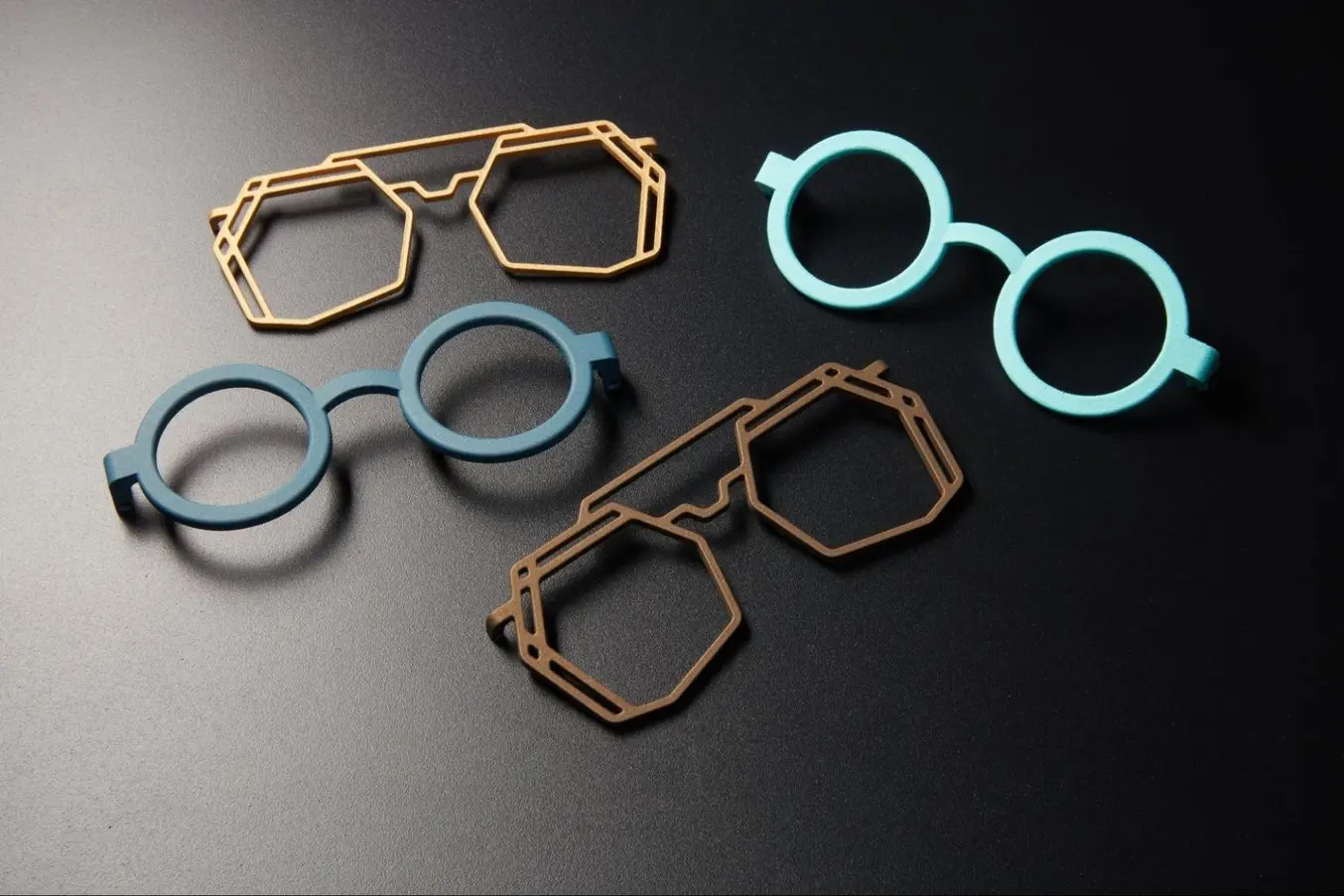
Gli occhiali, che siano modelli da lettura, protettivi oppure da sole promossi dalle celebrità, sono il raro esempio di un prodotto che può essere personalizzato all'infinito sia in termini di stile che di funzionalità. Le aziende produttrici apportano modifiche sia alle caratteristiche principali, come ad esempio il materiale, sia a dettagli più minuziosi, come le differenze a livello di micron nello spessore delle lenti.
Grazie ai progressi in termini di risoluzione, precisione, versatilità dei materiali e processi di finitura, la stampa 3D rappresenta un metodo conveniente per la progettazione e la produzione di occhiali.
Questa guida illustra le considerazioni su design e materiali per la stampa 3D di occhiali, i casi di studio di aziende produttrici del settore che già sfruttano questa tecnologia e i calcoli del ritorno d'investimento, tutte informazioni che potranno aiutarti a realizzare uno studio di fattibilità. Per un rapporto completo e approfondito, scarica il whitepaper sugli occhiali stampati in 3D.
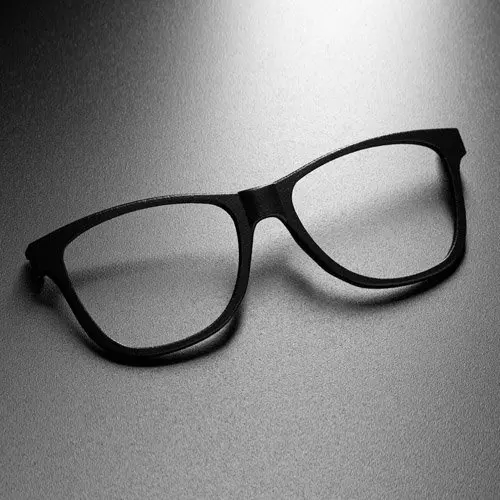
Produzione di occhiali stampati in 3D sull'ecosistema SLS serie Fuse di Formlabs
Questo whitepaper illustra le considerazioni su design e materiali di diverse aziende che producono montature di occhiali stampate in 3D.
Introduzione: l'avvento degli occhiali stampati in 3D
Grazie al lavoro di piccole aziende e grandi marchi che sfruttano la libertà di design, la capacità di produrre in piccoli lotti e i vantaggi in termini di sostenibilità offerti dalla stampa 3D, l'adozione di occhiali stampati in 3D da parte di utenti finali è aumentata in modo significativo negli ultimi cinque anni.
Che si tratti di protezione sul posto di lavoro, di prestazioni funzionali oppure di moda, la stampa 3D ha fatto capolino nel settore degli occhiali e ha cambiato il modo in cui designer e aziende pensano alla produzione.
Uno dei principali vantaggi della stampa 3D è che permette di ridurre le fasi di assemblaggio senza rinunciare a un elevato livello di uniformità e qualità. Secondo alcune aziende del settore, la produzione di montature in acetato richiede fino a sessanta passaggi individuali.
Questa immagine mostra come la stampa 3D offre una riduzione significativa della complessità di assemblaggio e della manodopera associata:
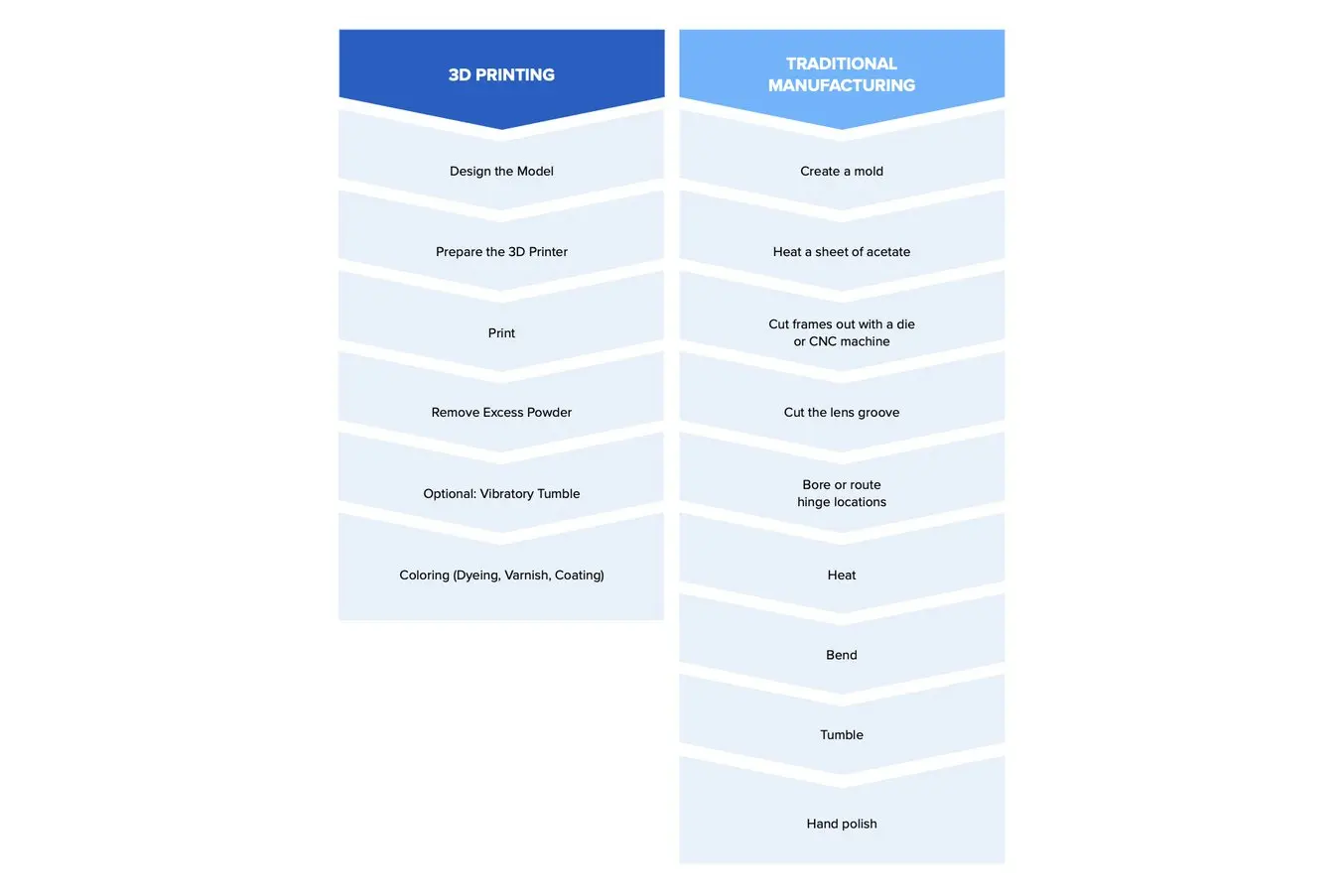
La stampa 3D a sinterizzazione laser selettiva (SLS) è la tecnologia di produzione additiva più comune per le applicazioni industriali, scelta da ingegneri e produttori di diversi settori perché permette di realizzare parti funzionali robuste.
Le stampanti 3D SLS utilizzano un laser ad alta potenza per fondere piccole particelle di polvere di polimeri. La polvere non fusa sostiene le parti durante il processo di stampa ed elimina la necessità di strutture di supporto dedicate. Ciò rende la sinterizzazione laser selettiva ideale per geometrie complesse, tra cui dettagli interni, sottosquadri, pareti sottili e dettagli in negativo. Le parti prodotte con la stampa SLS hanno caratteristiche meccaniche eccellenti, con una resistenza simile a quella delle parti stampate a iniezione, il che rende il processo ideale per la stampa 3D di occhiali.
Continua a leggere per scoprire come la stampa 3D può aumentare la velocità di commercializzazione, ridurre la manodopera ed eliminare la necessità di quantità minime d'ordine per montature e stanghette degli occhiali.
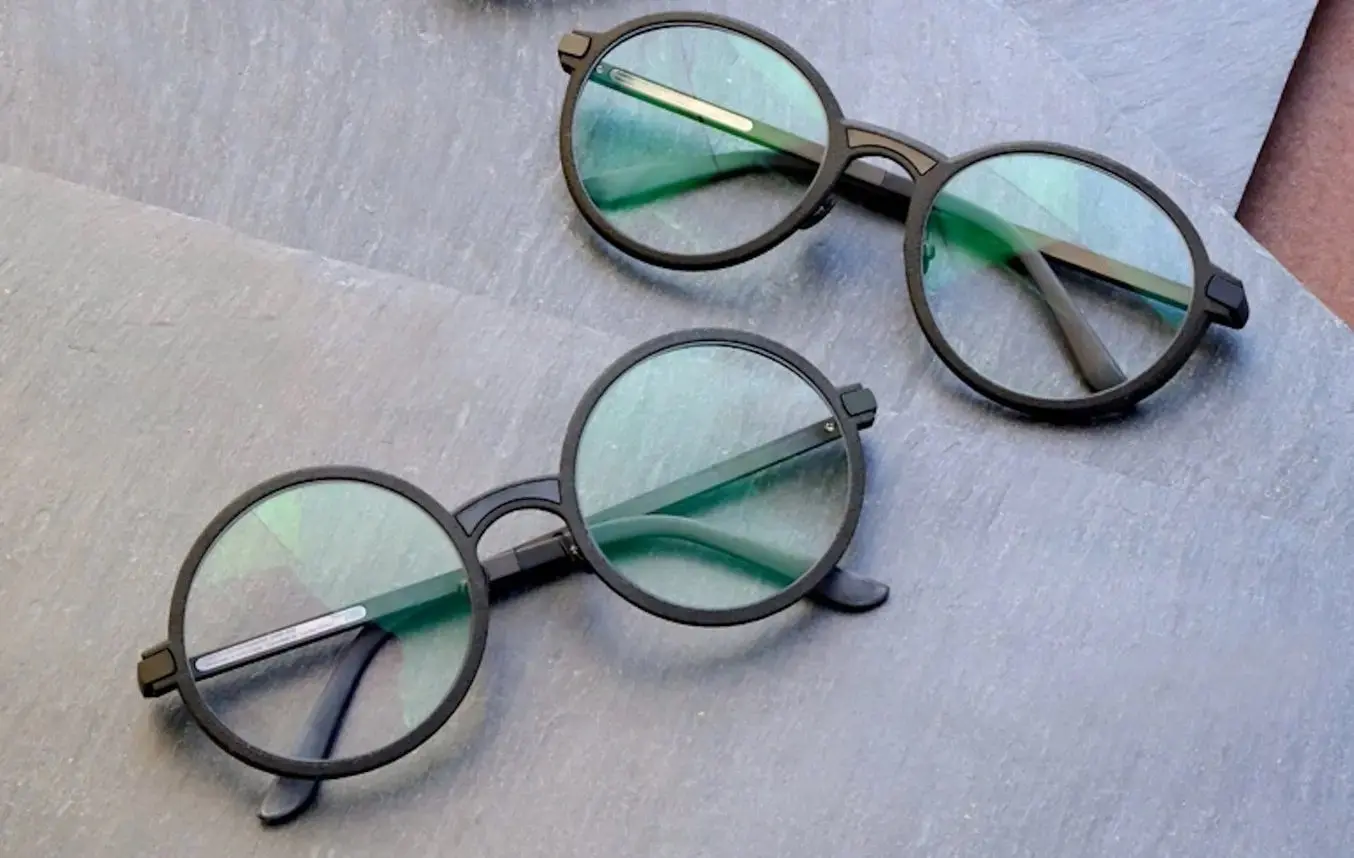
L'azienda produttrice svizzera Marcus Marienfeld utilizza la stampante 3D SLS Fuse 1+ 30W per produrre occhiali stampati in 3D.
Perché produrre occhiali con la stampa 3D?
1. Sostenibilità produttiva
Le montature di occhiali vengono prodotte principalmente tramite stampaggio a iniezione, fustellatura o fresatura CNC di precisione, tecniche che costringono i produttori a sostenere costi significativi per stampi e apparecchi. Esternalizzare la produzione di stampi o di parti realizzate tramite lavorazione meccanica può richiedere settimane e costare migliaia di dollari. Per giustificare la spesa, l'azienda deve impegnarsi a fabbricare quantità estremamente elevate di prodotto, il che può comportare una riduzione dei profitti e un elevato volume di scorte invendibili.
Questo sistema è insostenibile sia dal punto di vista finanziario sia da quello ambientale. Per contro, la stampa 3D permette di ottenere mezzi di produzione propri senza investire in stampi, riducendo al contempo il rischio di avviare una nuova linea di prodotti da zero. Grazie alla stampa 3D in-house, le aziende produttrici produrre piccoli lotti su richiesta senza costi di stampaggio iniziali, senza essere vincolate da quantità minime d'ordine elevate. In questo modo, possono evitare di produrre su larga scala articoli che potrebbero non avere successo.
Al giorno d'oggi, la maggior parte degli occhiali viene creata tramite stampaggio a iniezione o un processo sottrattivo: da fogli di acetato di grandi dimensioni viene ritaglia la forma della montatura, lasciando tutto il materiale risultante come scarto.
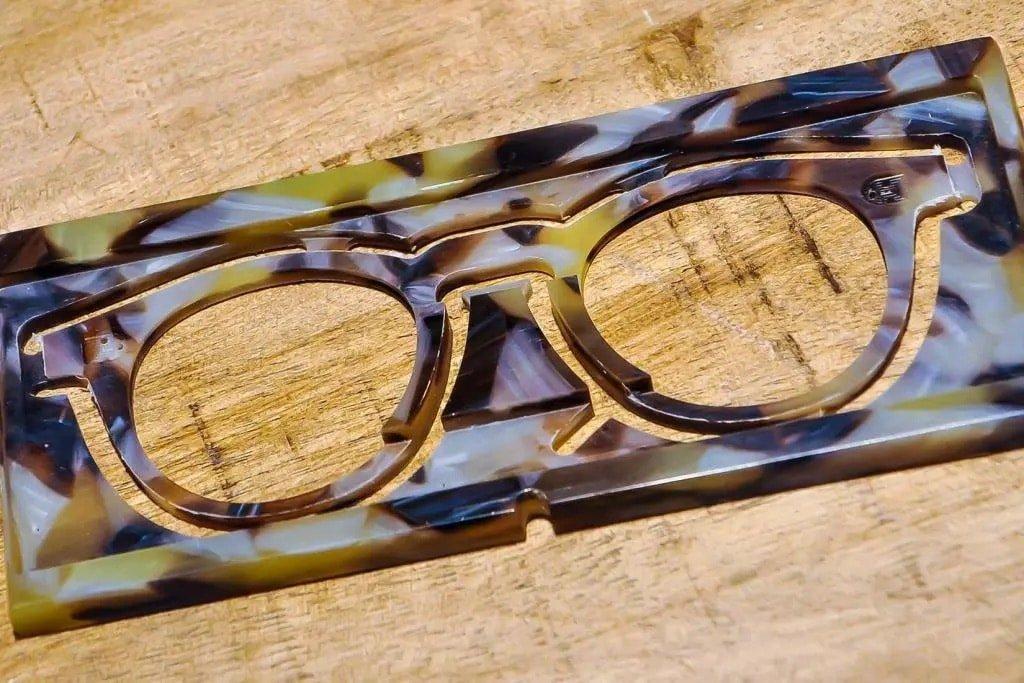
Una tradizionale montatura in acetato realizzata mediante processo di taglio. Fonte: Visio Optical
La stampa 3D è invece un processo additivo, ovvero le parti vengono create strato su strato a partire da una base di materiale. Con l'ecosistema SLS di Formlabs, il materiale in polvere non utilizzato può essere riciclato e poi riutilizzato nella stampa successiva, il che consente uno spreco minimo o pari a zero.
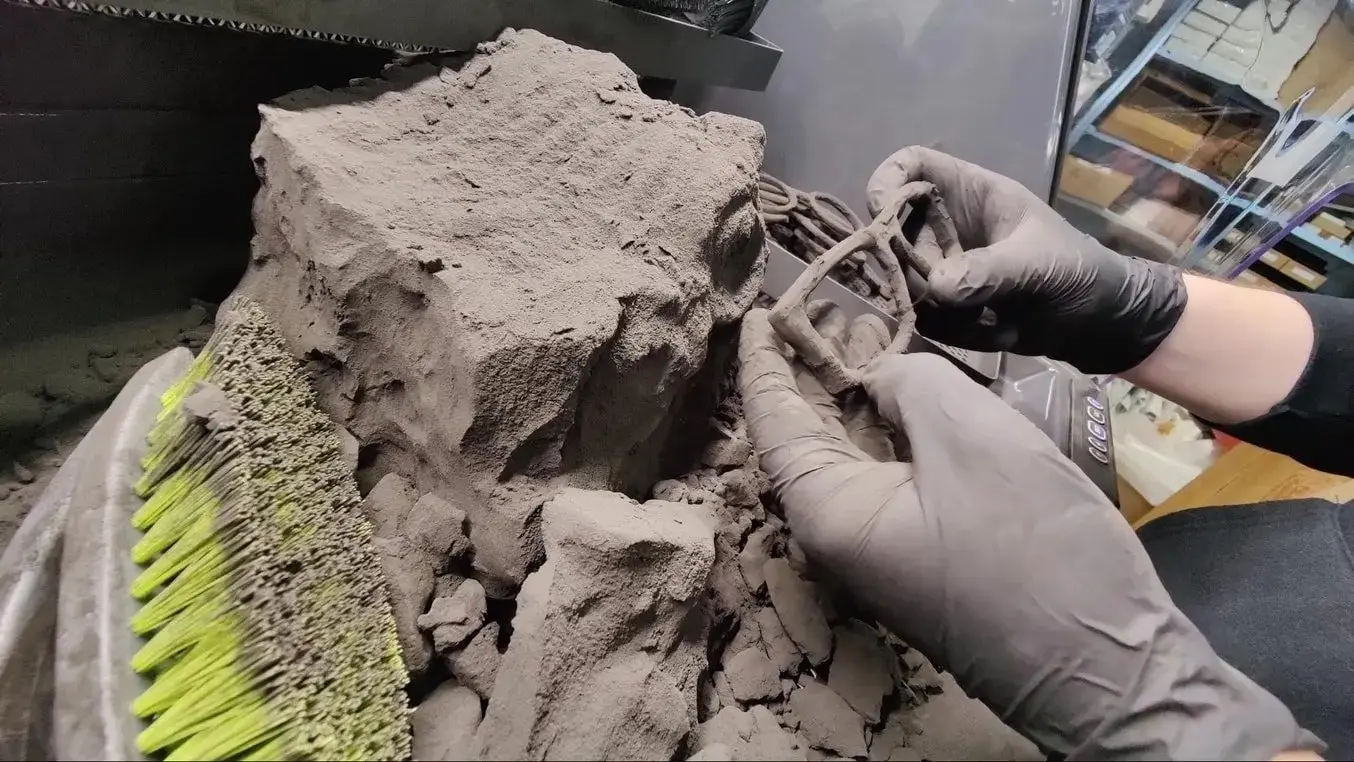
Rimozione dalla camera di stampa della Fuse 1+ 30W di montature di occhiali stampate in 3D con la Nylon 11 Powder.
L'ingombro ridotto e la fascia di prezzo accessibile dell'ecosistema SLS Fuse consentono alle aziende produttrici di acquistare più apparecchi per più sedi, distribuendo così la capacità produttiva nelle regioni fisicamente vicine ai consumatori e riducendo la dipendenza dalla produzione all'estero, che può essere rallentata dalle complicazioni della catena di fornitura globale. Una produzione distribuita riduce anche l'impatto ambientale associato alla sovrapproduzione e alla spedizione.
2. Libertà di design
A differenza di altre tecnologie di stampa 3D di polimeri, le parti prodotte con la stampa 3D SLS non richiedono strutture di supporto, poiché sono sostenute dal letto di polvere circostante. Senza strutture di supporto, canali di colata o restrizioni per angoli di sformo e sottosquadri comuni ai processi di stampaggio o taglio tradizionali, la stampa 3D SLS offre una libertà di design quasi illimitata, consentendo di realizzare design avanzati che in precedenza erano troppo costosi o addirittura impossibili da produrre.
Le restrizioni della produzione non impediscono più ai designer di creare i modelli con funzionalità, vestibilità ed estetica straordinarie. Gli occhiali stampati in 3D consentono di rispondere alle tendenze in modo più rapido che mai, permettendo ai marchi di conquistare segmenti di mercato nuovi ed emergenti.
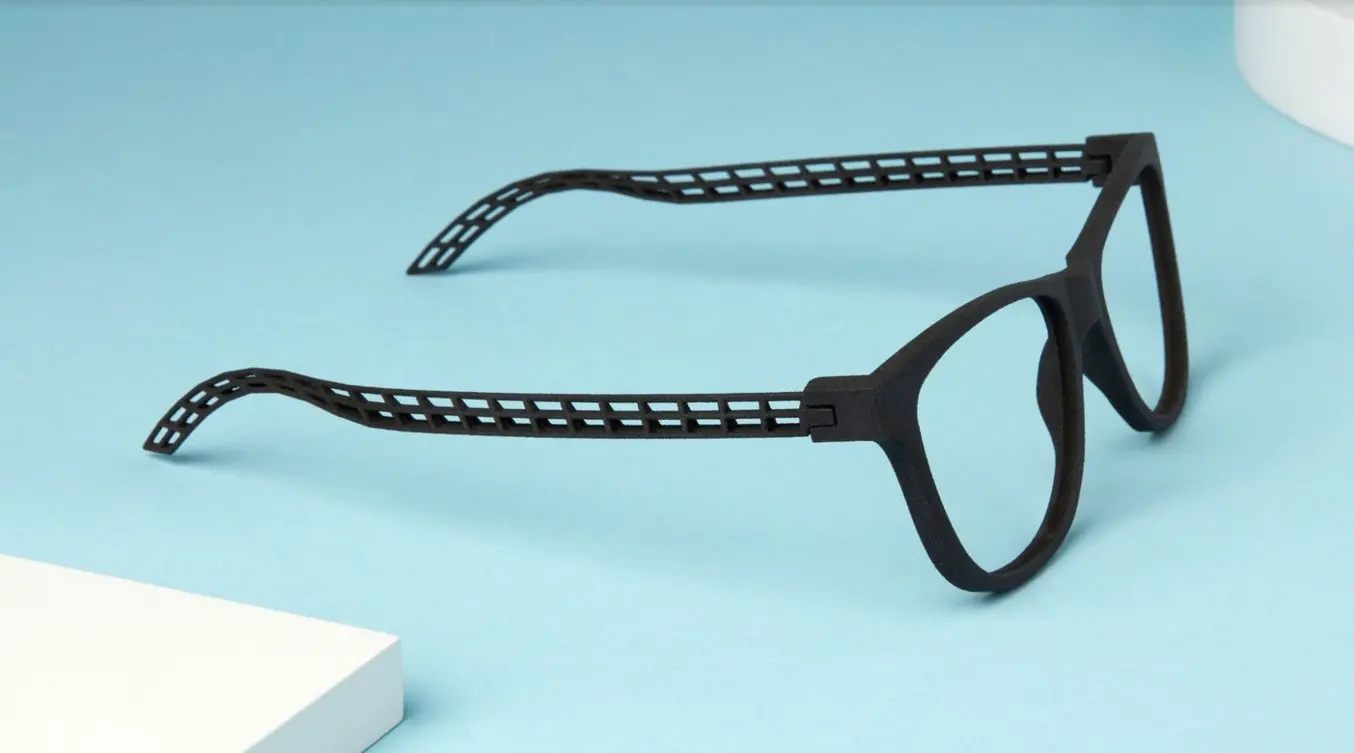
Stanghetta stampata in 3D con un design complesso, difficile o addirittura impossibile da produrre in modo efficace con gli strumenti tradizionali.
3. Personalizzazione
Senza limiti in fatto di apparecchi o quantità minime d'ordine, la personalizzazione del prodotto è finalmente a portata di mano. Le aziende possono scegliere dimensioni e design su misura per fornire ai clienti un prodotto completamente unico o con una migliore vestibilità.
La stampa 3D viene già utilizzata per personalizzare plantari, action figure, dispositivi di audiologia e altri tipi di prodotti. In genere, hanno maggior successo quando i consumatori ritengono che il prodotto sia di qualità più elevata poiché è più funzionale o più affine ai propri gusti. Con l'ampia varietà di età, etnie e caratteristiche facciali presenti nel mondo, i designer sono costretti ad abbandonare la mentalità della taglia unica e ad abbracciare l'universo della personalizzazione.
"Con la stampa 3D posso farlo senza problemi. Chi ha dimestichezza con la progettazione CAD può facilmente apportare modifiche al modello 3D, caricarlo sul software e stamparlo direttamente. Con la fresatura, invece, servirebbe ogni volta sviluppare uno strumento personalizzato e costoso per fissare i diversi elementi nell'apparecchio."
Marcus Marienfeld, designer e produttore di occhiali
Come produrre occhiali stampati in 3D
1. Progettazione
La creazione di occhiali per utilizzo finale con la stampa 3D offre vantaggi e sfide unici. In questa sezione, prenderemo in considerazione trama delle parti, opzioni per le cerniere, progettazione di geometrie che non possono essere realizzate mediante stampaggio e personalizzazione.
Trama
Le parti realizzate mediante produzione additiva sono formate tramite stratificazione, il che significa che alcune superfici potrebbero presentare linee degli strati visibili. Questo effetto può essere ridotto ottimizzando orientamento e design della parte e aggiungendo un'ulteriore fase di post-elaborazione per levigare la superficie.
L'aggiunta di goffratura o debossing alla superficie di montature e stanghette è una strategia ben nota per mascherare le linee degli strati sugli articoli per utilizzo finale stampati in 3D. Per un risultato ottimale, Formlabs consiglia una goffratura con un rilievo minimo di 0,35 mm e un debossing con una profondità minima di 0,15 mm.
Infine, le linee degli strati di una parte possono essere usate come strumento per aumentare la presa e la frizione, evitando così che gli occhiali scivolino sul naso.
Opzioni per le cerniere
Le cerniere degli occhiali stampati in 3D possono essere realizzate principalmente in quattro modi:
-
Viti tradizionali
-
Inserti termofissati
-
Accoppiamento a scatto
-
Cerniere stampate in posizione finale
Sebbene sia possibile aggiungere una filettatura alle cerniere in fase di progettazione, le filettature a vite tradizionali delle montature degli occhiali sono in genere troppo piccole per poter essere realizzate in modo uniforme tramite stampa 3D. Per questo motivo, usa almeno una filettatura M6.
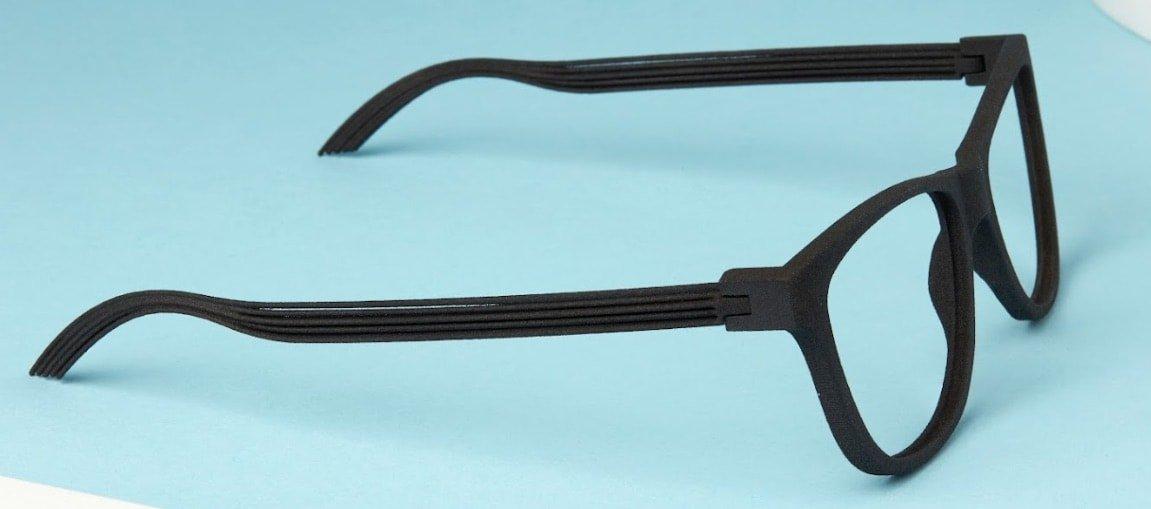
Occhiali stampati in 3D assemblati con una filettatura stampata e una vite di metallo.
Sia la Nylon 11 Powder sia la Nylon 12 Powder consentono l'uso di inserti termofissati e filettature maschiate, che possono durare più a lungo ed essere più resistenti di altre opzioni. Leggi questa guida dettagliata.
Infine, data l'assenza di strutture di supporto, la stampa 3D SLS consente l'uso di geometrie stampate in posizione finale. È possibile progettare e stampare le montature con le stanghette già fissate, senza la necessità di ulteriori assemblaggi. Formlabs consiglia un gioco di 0,3 mm per i dettagli più piccoli di 20 mm2 e un gioco di 0,6 mm per i dettagli più grandi di 20 mm2. Leggi la guida di progettazione SLS completa.
Geometrie che non possono essere realizzate mediante stampaggio
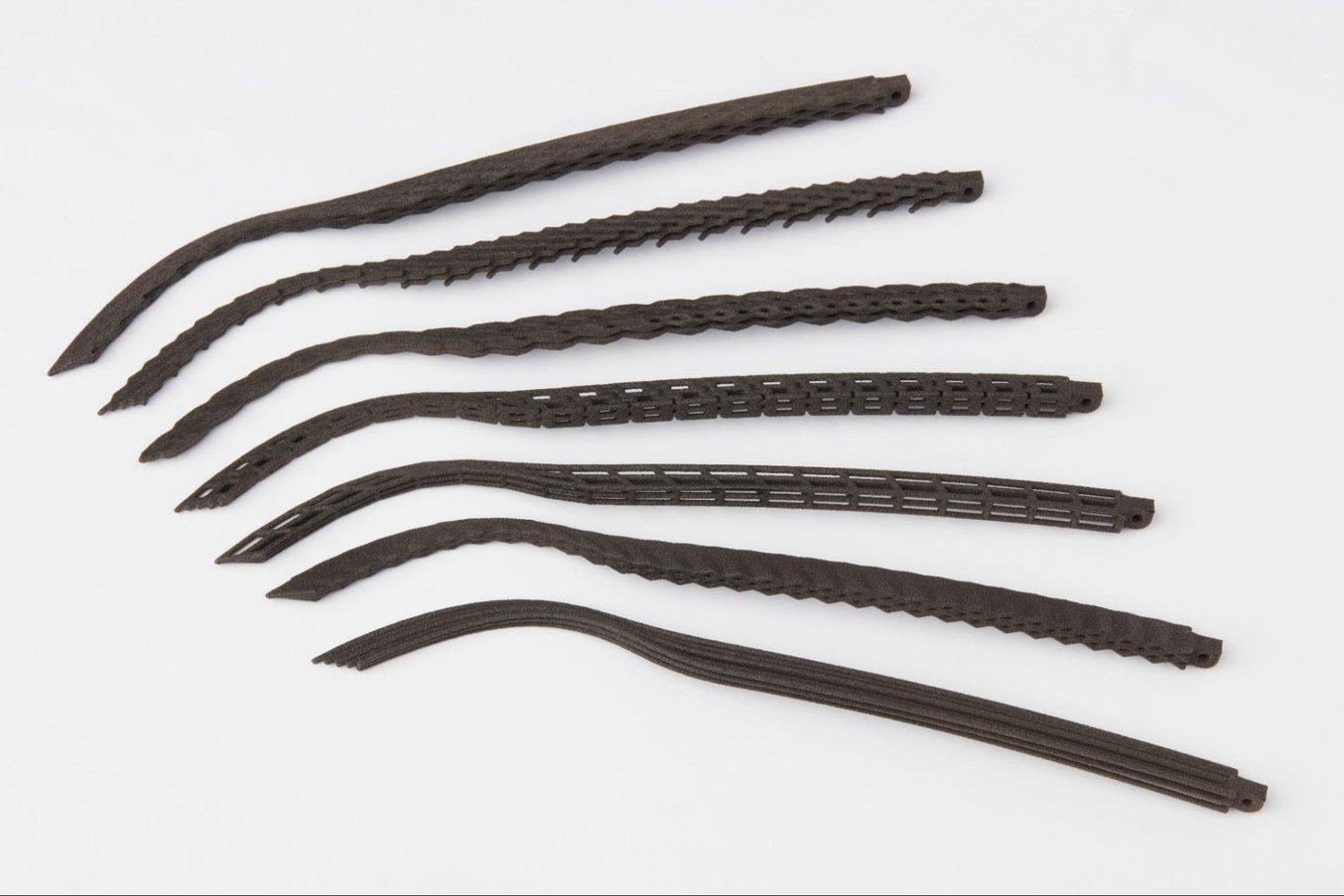
Stanghette per occhiali stampate in 3D con la Nylon 11 Powder, progettate con opzioni di reticolazione nel software nTopology.
La stampa 3D, diffusa principalmente nelle applicazioni più alla moda, ha consentito ai designer di creare modelli di occhiali che non possono essere realizzati mediante stampaggio o taglio. Poter creare geometrie più particolari, come le stanghette nell'immagine qui sopra, consente di offrire ai consumatori nuove possibilità di espressione o un maggior livello di comfort, alleggerendo in modo considerevole i componenti.
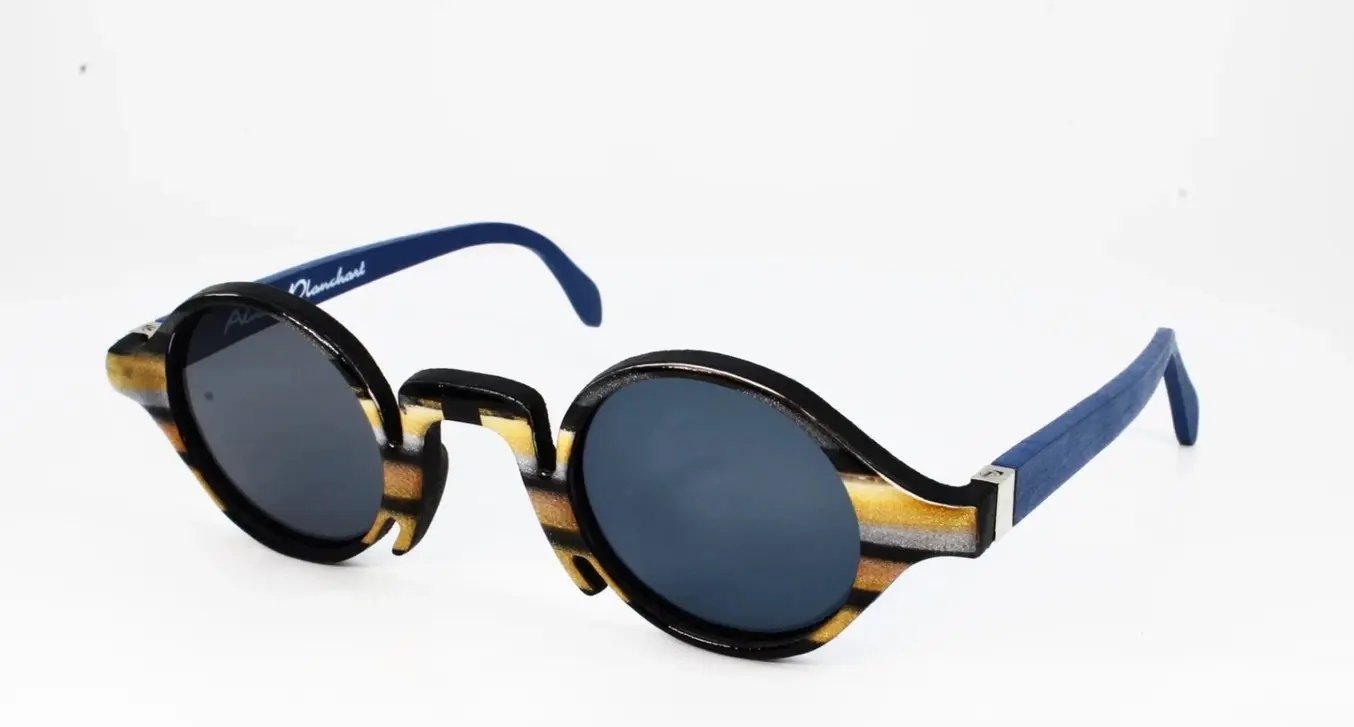
Montature e stanghette per occhiali stampate in 3D su una stampante Fuse 1+ 30W, progettate e prodotte da Alvaro Planchart.
2. Stampa 3D
Stampante 3D per occhiali
Grazie all'hardware affidabile, ai materiali di qualità industriale e all'interfaccia utente intuitiva, l'ecosistema SLS serie Fuse offre una soluzione di produzione accessibile e scalabile. Nelle sezioni di seguito troverai suggerimenti e consigli specifici per la stampa 3D di occhiali con tecnologia SLS.
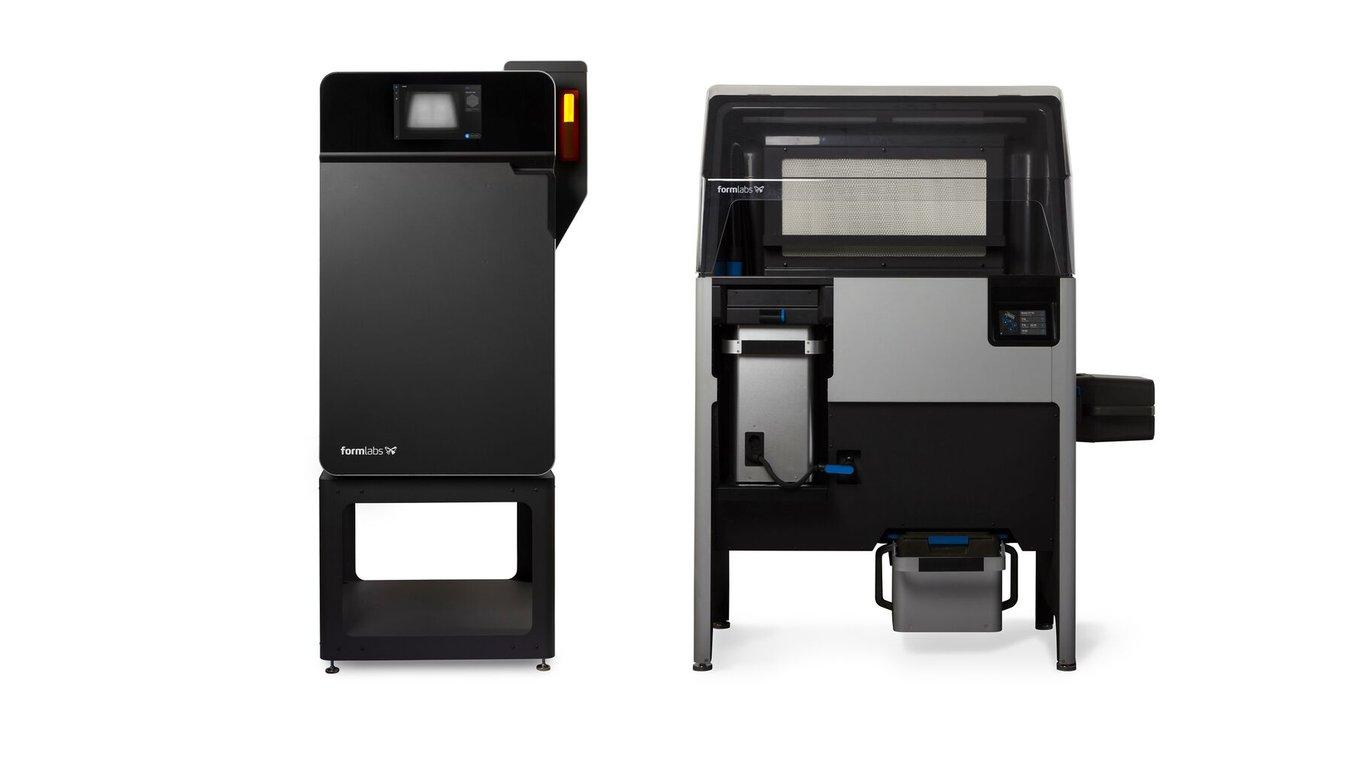
La stampante 3D SLS Fuse 1+ 30W (a sinistra) e l'unità di post-elaborazione Fuse Sift (a destra).
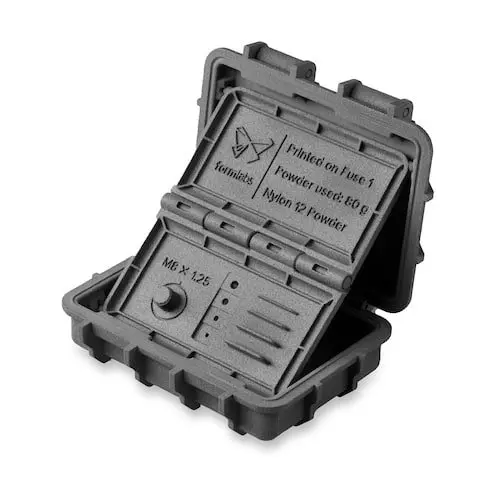
Richiedi un campione SLS gratuito
Guarda e tocca con mano la qualità di Formlabs. Saremo lieti di inviare presso la tua azienda una parte SLS stampata con la Fuse 1+ 30W come campione gratuito.
Materiali per la stampa 3D di montature di occhiali
Il sistema Fuse 1+ 30W supporta due materiali idonei alla produzione di occhiali: la Nylon 11 Powder e la Nylon 12 Powder. Sono entrambi materiali termoplastici, proprio come l'acetato, il che significa che gli ottici possono riscaldare le montature e le stanghette per adattarle meglio al viso dopo la stampa.
Se si confrontano le prestazioni funzionali con quelle dell'acetato, del TR90 e del policarbonato, entrambi i materiali SLS sono estremamente simili, anche se la Nylon 11 Powder viene preferita da alcuni clienti per il suo allungamento a rottura superiore e per i vantaggi in termini di sostenibilità.
Acetato di cellulosa* | Grilamid TR90** | Nylon 11 Powder | Nylon 12 Powder | |
---|---|---|---|---|
Carico di rottura a trazione | 30 MPa | 60 MPa | 49 MPa | 50 MPa |
Modulo di elasticità | 1700 MPa | 1500 MPa | 1600 MPa | 1850 MPa |
Allungamento a rottura | 30% | 50% | 40% | 11% |
Resistenza alla flessione | 40 MPa | N/A | 55 MPa | 66 MPa |
Nei test funzionali reali, la Nylon 11 Powder ha dimostrato una duttilità e una resistenza agli urti straordinarie.
Per garantire sostenibilità e lunga durata di un prodotto che viene esposto ai fattori esterni, è necessario tenere conto di ulteriori proprietà ambientali e dei materiali.
Grazie alla minore densità, al basso assorbimento d'acqua e all'elevata resistenza al calore e all'infiammabilità, la Nylon 11 Powder e la Nylon 12 Powder sono le candidate perfette per applicazioni più funzionali, ad esempio per la fabbricazione di occhiali protettivi utilizzati negli stabilimenti di produzione o per l'uso sul campo. Questi materiali consentono di creare montature leggere in grado di resistere a condizioni ambientali difficili.
Per concludere, la Nylon 11 Powder di Formlabs è un materiale rinnovabile con origine 100% biologica: poiché viene prodotta a partire da semi di ricino, rappresenta un'opzione più sostenibile rispetto ad alcune plastiche derivate dal petrolio. In confronto alla Nylon 12 Powder, la Nylon 11 Powder garantisce una riduzione del 60% dell'impatto in termini di carbonio.
Finitura superficiale
La finitura superficiale delle montature di occhiali stampate in 3D dipende in larga misura dal design del modello: diversi orientamenti producono finiture superficiali diverse. Formlabs ha condotto test approfonditi e ha riscontrato che, utilizzando la Nylon 11 Powder e la Nylon 12 Powder, un orientamento di stampa di 45° permette di ottenere una finitura superficiale estetica ottimale su una montatura rotonda di esempio. Il lato rivolto verso il fondo della camera di stampa avrà una finitura superficiale leggermente più liscia.
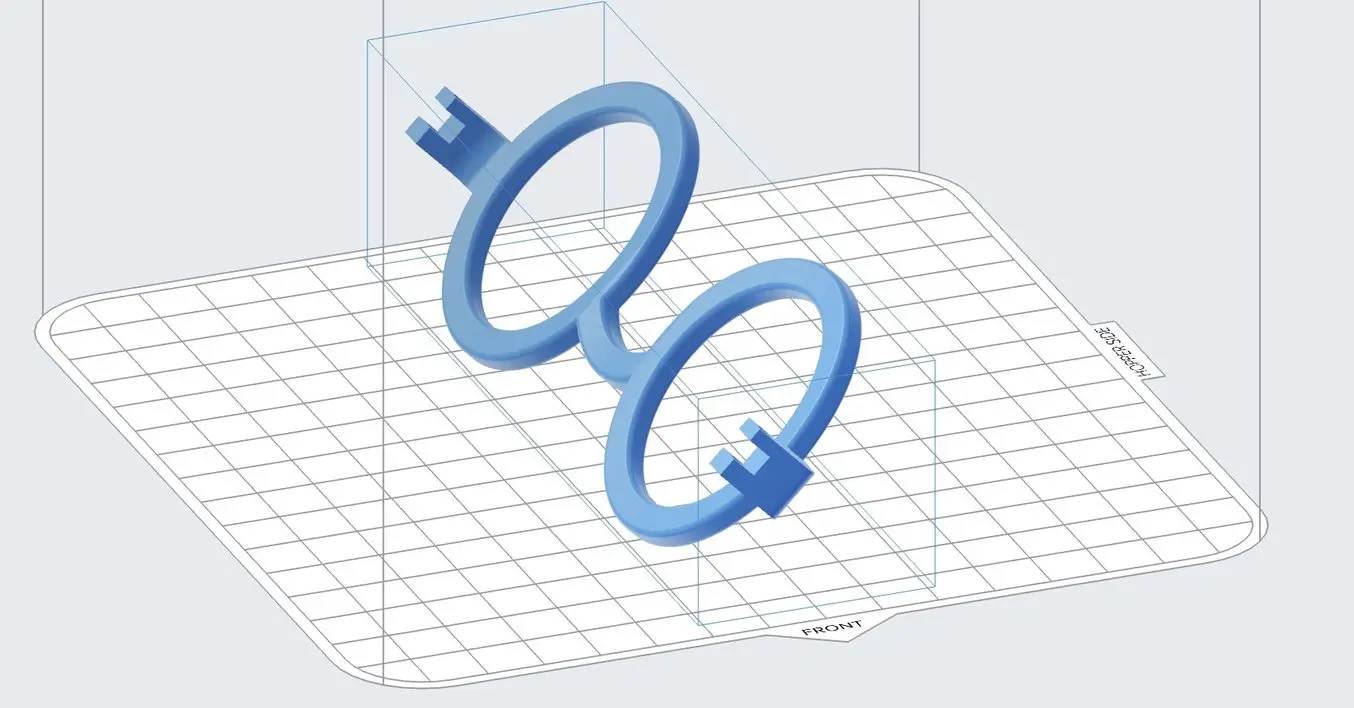
Parte anteriore di una montatura orientata con un angolo di 45° in PreForm per ottenere la finitura superficiale estetica ottimale.
Capacità di stampa
Se orientate con un angolo di 45°, nella camera di stampa della Fuse 1+ 30W è possibile posizionare 82 montature di esempio. A marzo 2023, l'uso della Nylon 12 Powder offre una densità di stampa del 10% e un tempo di stampa di 21 ore.
Formlabs lavora per migliorare costantemente le impostazioni di stampa. Contatta Formlabs per ricevere l'analisi più aggiornata su costi e tempi di stampa oppure per richiedere un'analisi personalizzata del design della tua parte.
Nylon 12 | Nylon 11 Powder | |||
---|---|---|---|---|
Numero di parti per stampa | 82 | 60* | ||
Densità di stampa** | 10% | 10% | ||
Tempo di stampa | 21 ore | 22,5 ore | ||
Produzione annuale massima per apparecchio | 19 680*** | 14 400*** |
* Il rendimento è calcolato in base al design di una montatura standard di Formlabs. Il numero di parti è stato ridotto per ottenere un tempo di stampa inferiore a 24 ore; ciò ha dato come risultato un rendimento di produzione più elevato. Con la Nylon 11 Powder è possibile stampare 82 montature alla volta, ma con un tempo di stampa superiore a 24 ore.
** Scopri di più sulla densità di stampa e sul tasso di rigenerazione qui.
*** Supponendo una stampa al giorno, cinque giorni a settimana, 48 settimane all'anno. È necessaria una seconda camera di stampa per cambiare rapidamente e avviare nuove stampe.
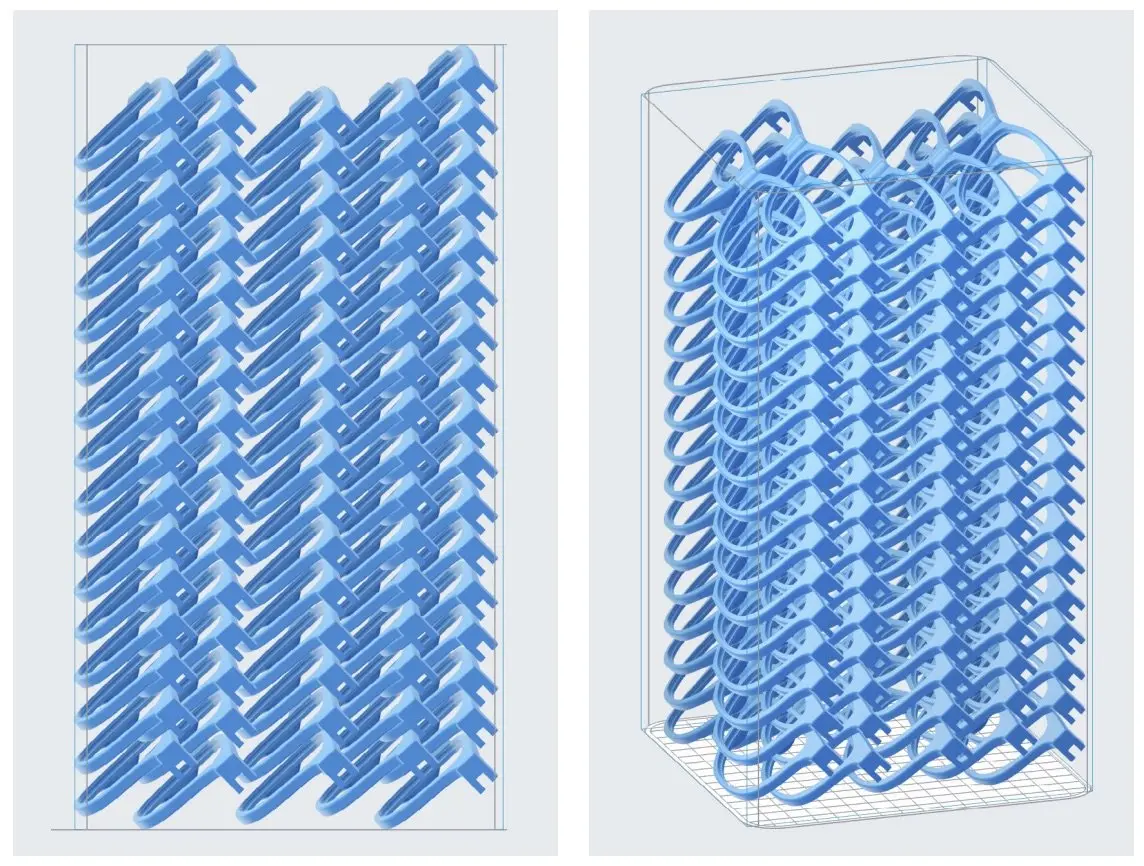
82 modelli di montatura posizionati in PreForm, il software di preparazione della stampa gratuito di Formlabs.
3. Opzioni di finitura
La finitura estetica naturale della Nylon 11 Powder e della Nylon 12 Powder è di colore grigio opaco, con una maggiore ruvidità rispetto all'acetato lucidato. Per ottenere una finitura più simile a quella degli occhiali tradizionali in acetato o in TR90, è opportuno prendere in considerazione diverse opzioni di finitura.
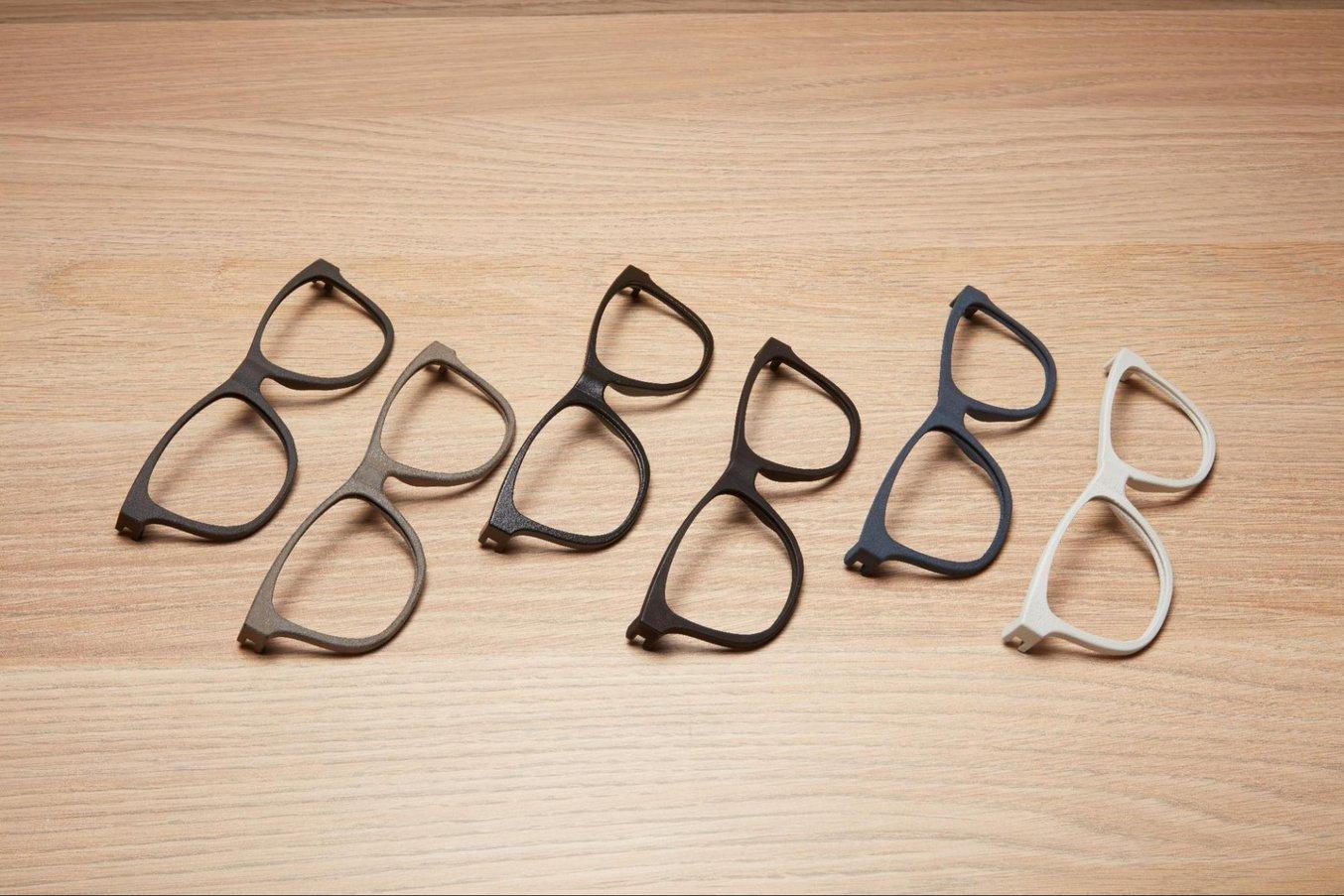
Montature stampate con la Nylon 11 Powder, da sinistra a destra: grezza, appena uscita dalla stampante; burattata; levigata a vapore; tinta di nero; tinta di blu; con applicazione di Cerakote bianco.
Preparazione della superficie della parte
Così come le montature tradizionali in acetato vengono spesso burattate con un materiale legnoso, per le montature stampate in 3D è particolarmente vantaggioso inserirle per qualche ora in un buratto vibrante. Usando un materiale ceramico con un lubrificante, Formlabs ha riscontrato una riduzione dell'80% della ruvidità superficiale, con conseguente sensazione di morbidezza al tatto. Formlabs impiega il buratto vibrante Mr. Deburr 300DB, un'opzione a basso costo e intuitiva.
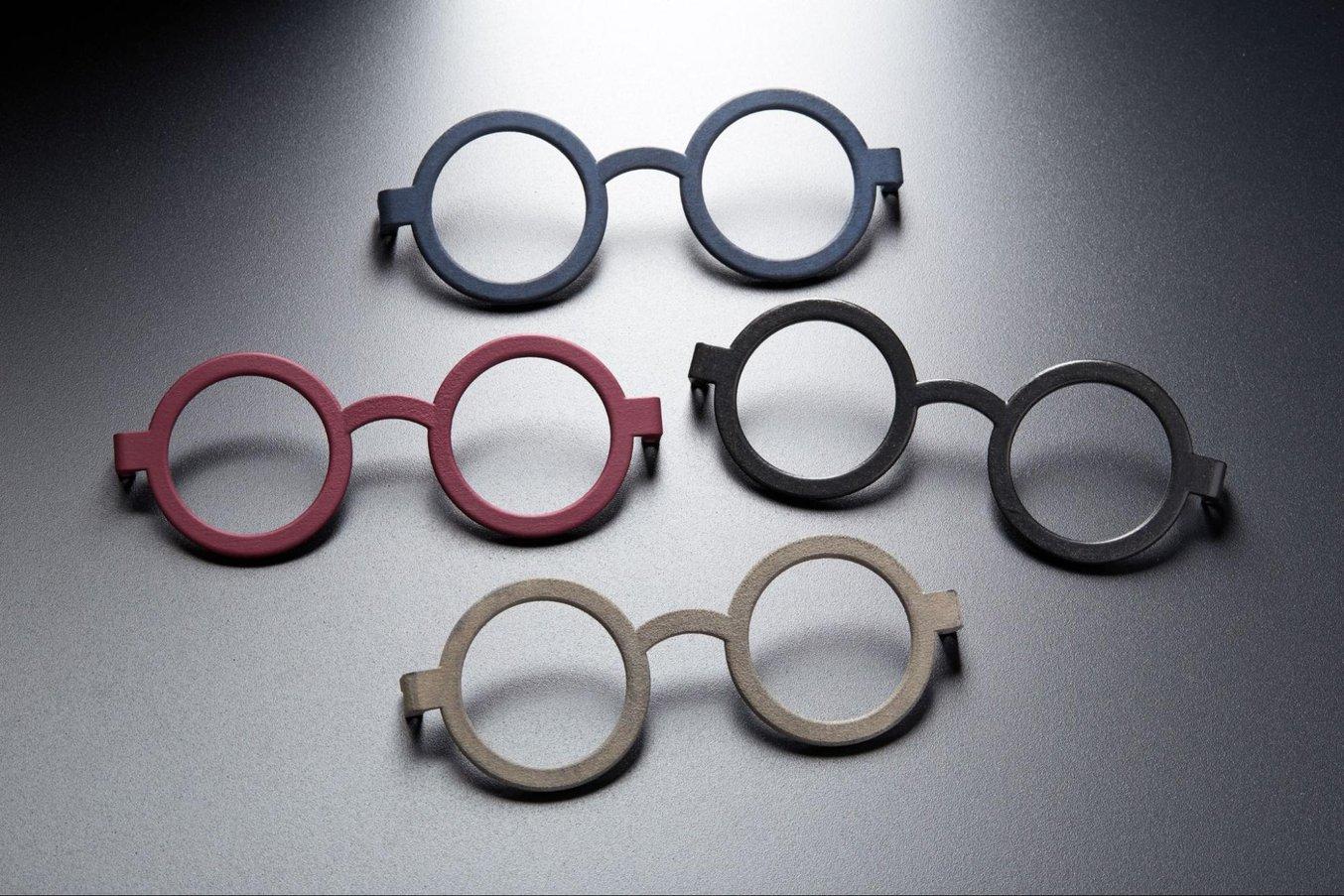
Montature stampate in Nylon 11 Powder: (in basso) burattata; (a sinistra) con applicazione di Cerakote; (a destra) levigata a vapore; (in alto) con applicazione di Cerakote.
Opzioni di colorazione
Un'opzione semplice e conveniente per la colorazione della parte è utilizzare un sistema di tintura a bagno d'acqua. Le parti vengono immerse in un bagno d'acqua riscaldata con un colorante che penetra in tutte le superfici della parte, alterandone in modo permanente il colore. Per via del colore grigio della polvere, è impossibile ottenere opzioni di colore molto chiare, come il bianco o il giallo brillante, attraverso un processo di tintura.
Tuttavia, colori come il nero, il rosso, il verde, il viola e il blu sono ottenibili anche con un set di tintura di base composto da una piastra calda, una pentola e la tintura per nylon RIT. In alternativa, sono disponibili soluzioni industriali di aziende come Dyemansion, che offrono una maggiore uniformità di colore e un esatto abbinamento cromatico.
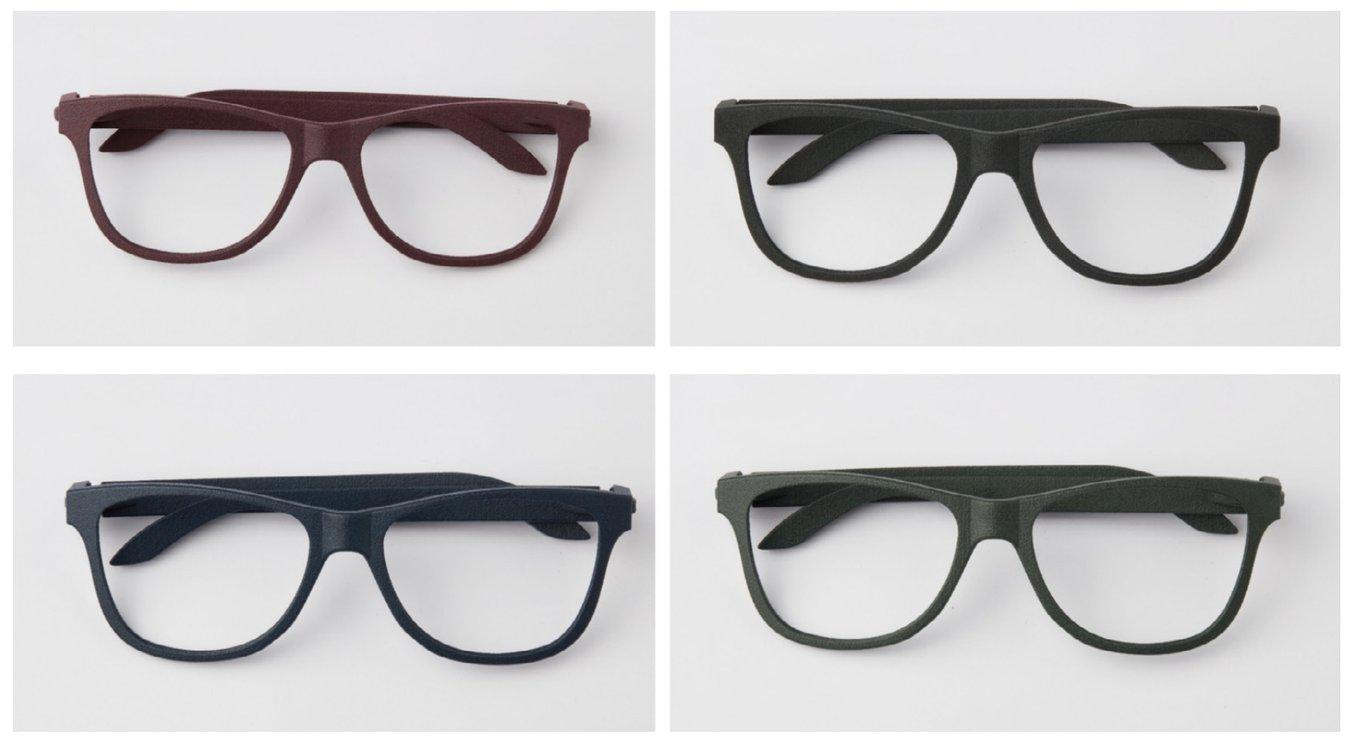
Montature stampate con la Nylon 11 Powder e tinte in un bagno d'acqua.
Formlabs utilizza anche il rivestimento Cerakote per migliorare le proprietà meccaniche della parte e consentire un'ampia varietà di colorazioni. Cerakote è un rivestimento ceramico a film sottile, con spessore da 0,00635 mm a 0,0254 mm e che non richiede un primer.
Una volta applicato, le parti realizzate con la stampa 3D SLS possono contare su un miglioramento della resistenza alle sostanze chimiche e ai graffi. Cerakote può essere utilizzato anche per ottenere una finitura superficiale lucida, con colori che vanno da quelli pastello a quelli metallizzati, incluse tutte le tonalità intermedie. Inoltre, una volta rivestite, le parti possono essere sottoposte a lavorazione con un laser per ottenere motivi accattivanti o per inserire informazioni, come loghi o numeri di serie.
Grazie a specifici programmi di polimerizzazione personalizzabili, Cerakote può essere impiegato anche per ottenere una finitura lucida.
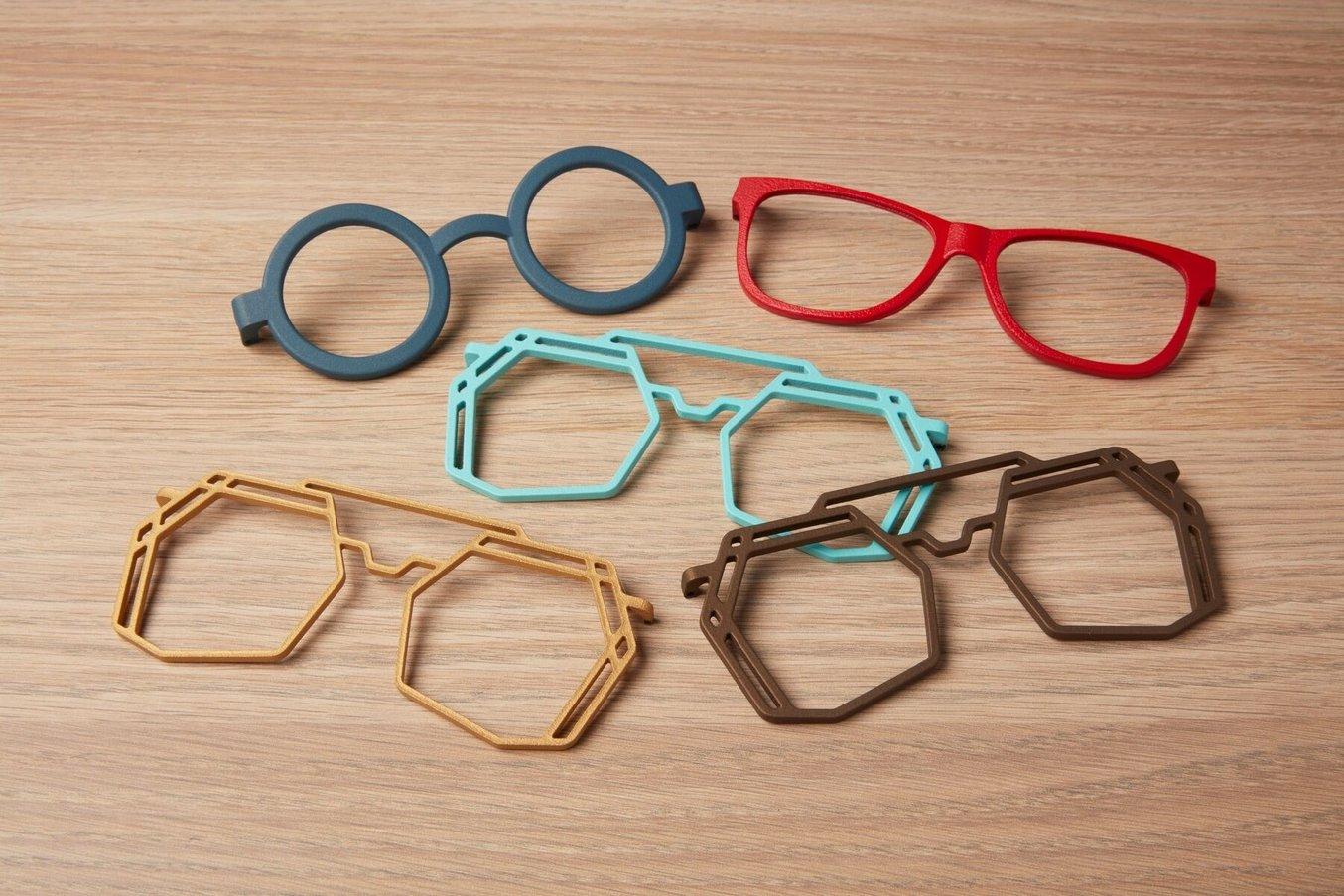
Montature stampate con la Nylon 11 Powder e rivestite con Cerakote serie H.
Sulle parti realizzate con la stampa 3D SLS è possibile effettuare anche l'idroimmersione. Per saperne di più, leggi questo articolo di blog. I processi di stampa e verniciatura sono altresì compatibili con la tecnologia SLS.
Infine, la levigazione a vapore è un processo che serve a sigillare chimicamente e a levigare la superficie delle parti realizzate tramite stampa 3D SLS. Questa tecnica assicura una superficie simile a quella ottenuta dallo stampaggio a iniezione, ma con una ruvidità notevolmente migliorata e una resistenza all'umidità e alla proliferazione batterica. Inoltre, consente al contempo di ottenere finiture superficiali lucide.
Formlabs utilizza le tecnologie di produzione additiva per realizzare componenti per occhiali levigati a vapore. Inoltre, le parti possono essere tinte in un bagno d'acqua prima o dopo la levigazione a vapore, sigillando così il colore della parte con una maggiore lucentezza.
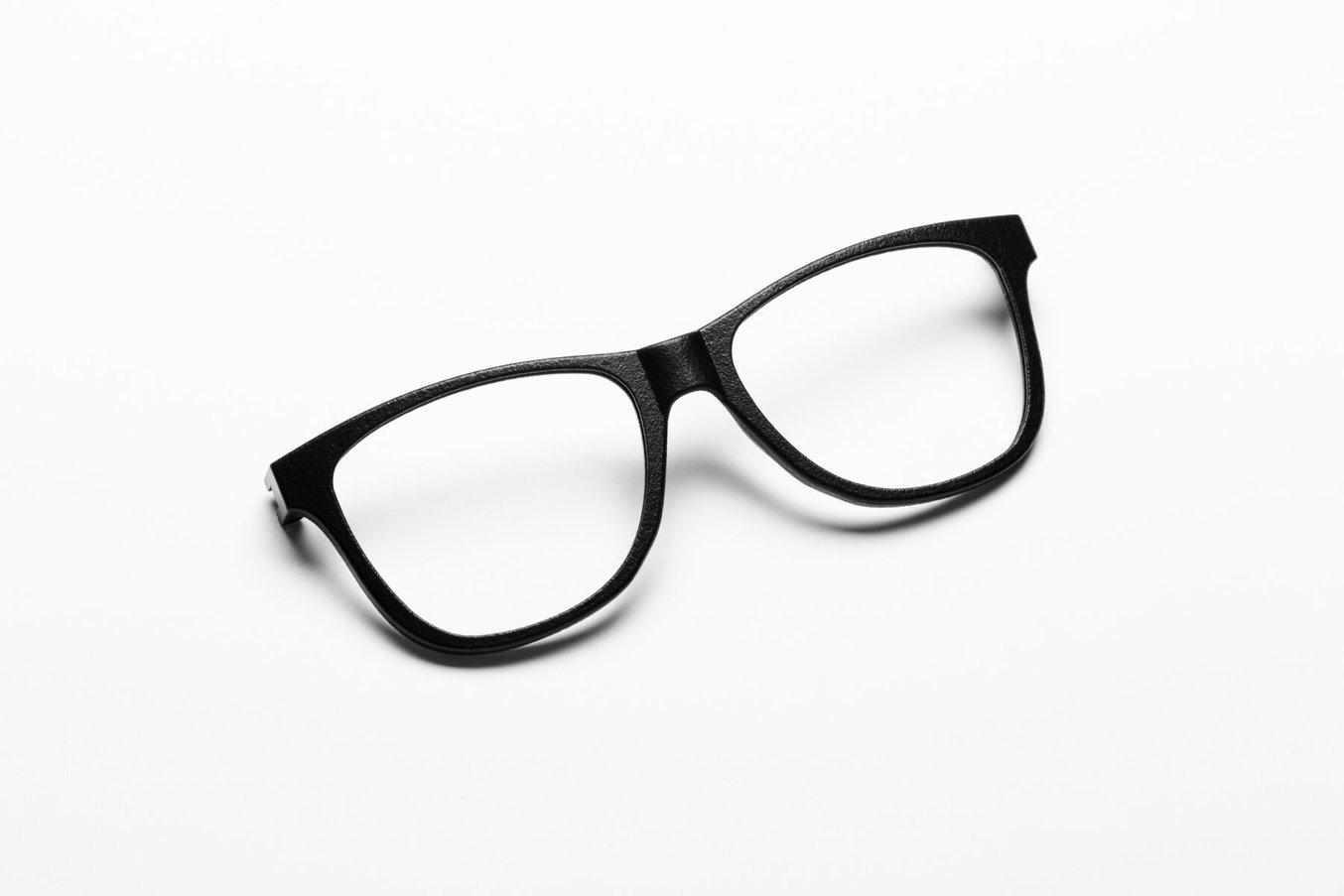
Montature realizzate con la Nylon 11 Powder dopo la levigazione a vapore.
Tocca i risultati con mano
Sebbene Formlabs abbia esplorato e sviluppato molte opzioni per migliorare la finitura superficiale delle parti realizzate tramite stampa 3D SLS, vi sono ancora molte altre strade da percorrere. Molti clienti hanno ordinato un campione gratuito dei loro occhiali e in seguito applicato le loro tecniche di finitura proprietarie (diversi materiali di burattatura, verniciatura, rivestimenti ecc.) per ottenere un aspetto estetico unico.
Contatta il nostro team vendite per ordinare un campione gratuito del tuo design. In alternativa, ordina un campione standard realizzato con la Nylon 11 Powder o la Nylon 12 Powder su cui provare tecniche di finitura riservate o proprietarie.
Altri usi della stampa 3D nel settore degli occhiali
Prototipazione
Sia il sistema SLS Fuse 1+ 30W che il sistema SLA Form 3+ possono essere utilizzati per realizzare prototipi di occhiali per testarne le dimensioni, la vestibilità e il design complessivo.
Usa i materiali in nylon sul sistema Fuse 1+ 30W per creare prototipi funzionali che possono essere indossati e testati per lunghi periodi di tempo. Scegli il sistema Form 3+ per creare prototipi estetici con una traslucenza simile a quella dell'acetato e del policarbonato. I prototipi realizzati tramite la stampa SLA possono essere indossati per settimane, ma non sono adatti all'uso prolungato, a meno che non siano dotati di un rivestimento che blocca i raggi UV.
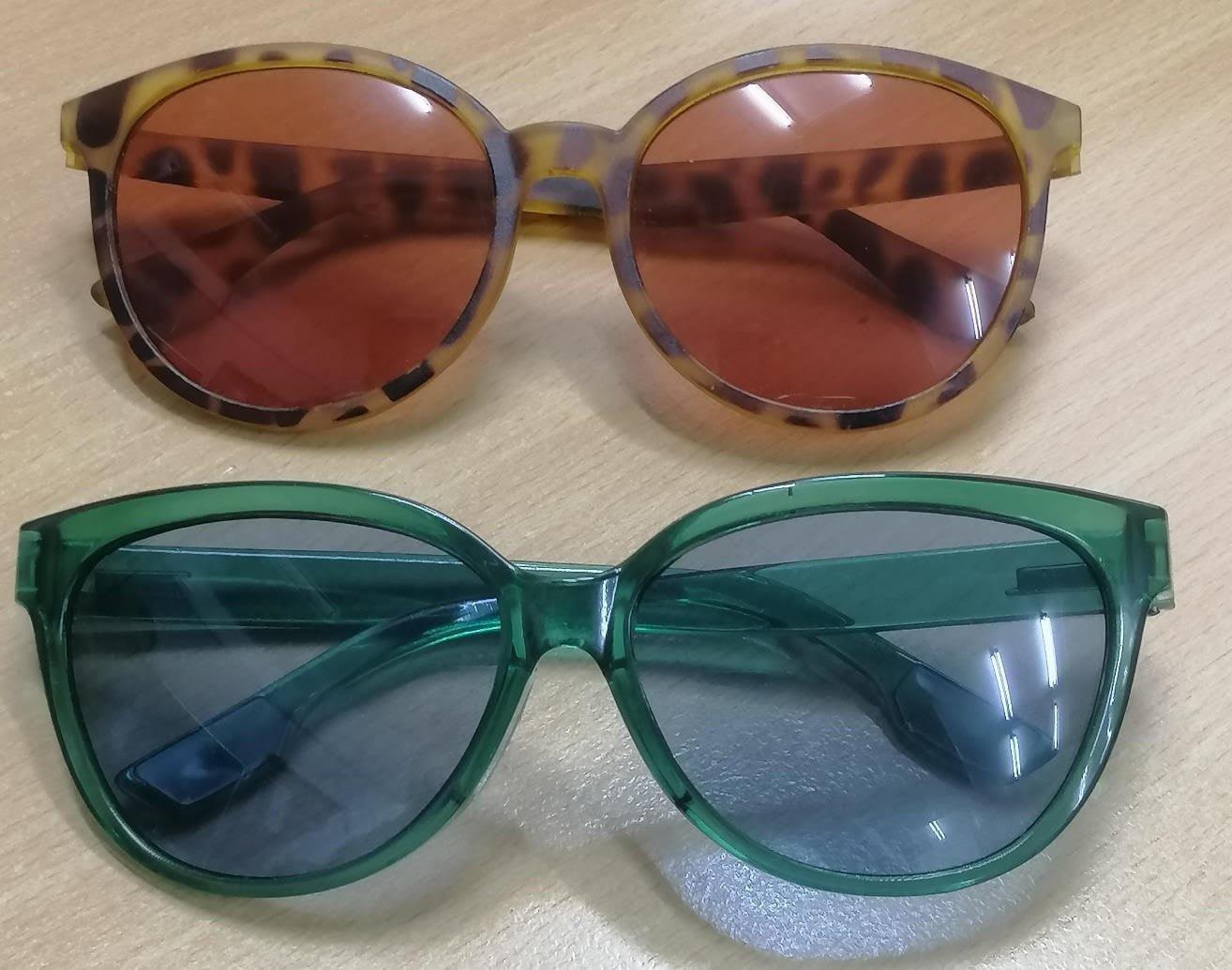
Plastinax utilizza la stampante SLA Form 3+ per produrre prototipi estetici per materiali parzialmente traslucidi.
Collaudo sugli utenti
La Fuse 1+ 30W permette di creare occhiali pronti per essere testati e valutati, così da ottenere rapidamente feedback sulla vestibilità, verificare la vita utile ed eseguire iterazioni di dimensioni e design.
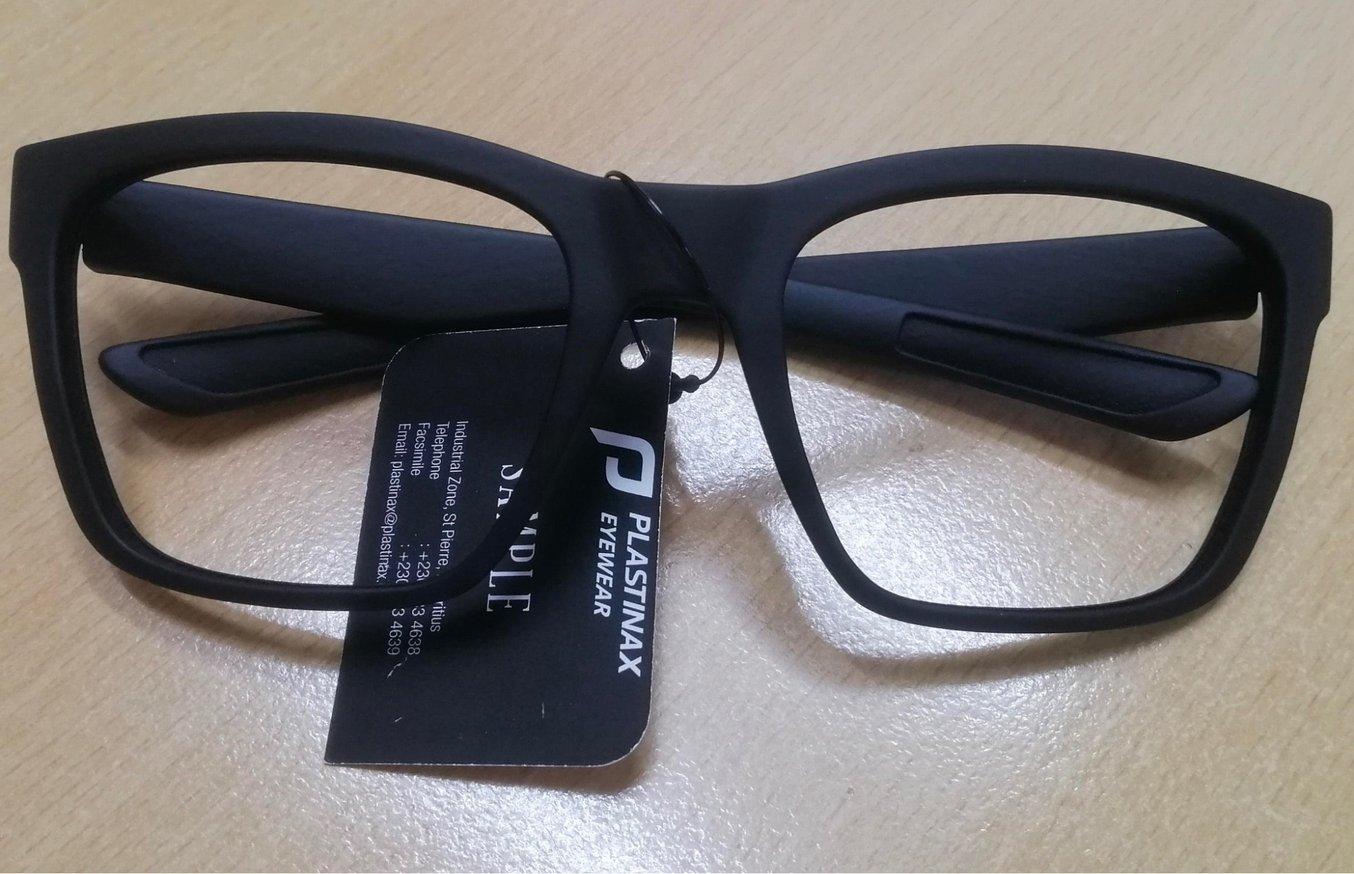
Montature realizzate con la Nylon 12 Powder, stampate e finite da Plastinax.
Occhiali intelligenti
La stampa 3D permette di realizzare design complessi senza difficoltà. Aggiungere alloggiamenti per componenti elettronici o i complessi assemblaggi necessari per i dispositivi indossabili non comporta alcun problema per la stampante 3D. La stampa 3D SLS è la soluzione ottimale per creare alloggiamenti complessi per occhiali intelligenti, che altrimenti sarebbero difficili da produrre con costosi stampi a iniezione a più componenti.
Dime e fissaggi
Grazie all'elevata resistenza agli urti, la Nylon 12 Powder e la Nylon 11 Powder sono particolarmente indicate per la realizzazione di dime e fissaggi personalizzati. Questi materiali sono abbastanza resistenti da piegare alcuni metalli utilizzati nelle montature e nelle stanghette tradizionali, come il titanio, con pressioni superiori a 90 kg.
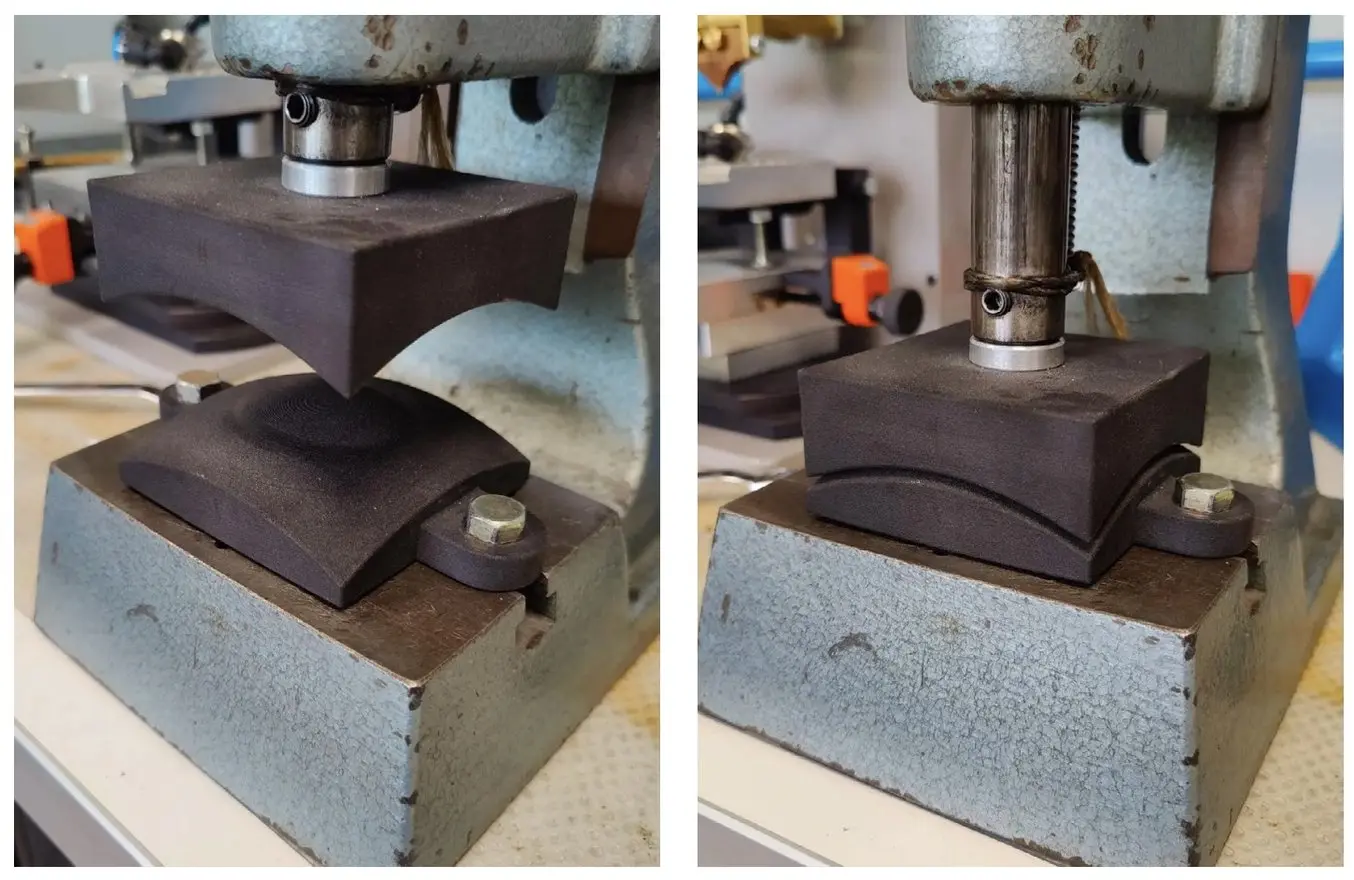
Marcus Marienfeld utilizza la Fuse 1+ 30W e la Nylon 11 Powder per piegare montature e stanghette.
Stampaggio a iniezione e formatura sottovuoto in piccoli lotti
L'uso delle stampanti 3D SLA Form 3+ o Form 3L e della Rigid 10K Resin per produrre stampi a iniezione è comune in molti settori. Grazie all'elevata resistenza al calore e alla finitura superficiale raffinata, la Rigid 10K Resin può essere utilizzata per stampare a iniezione montature e stanghette in piccoli volumi, nonché per realizzare stampi per la produzione di imballaggi sottovuoto.
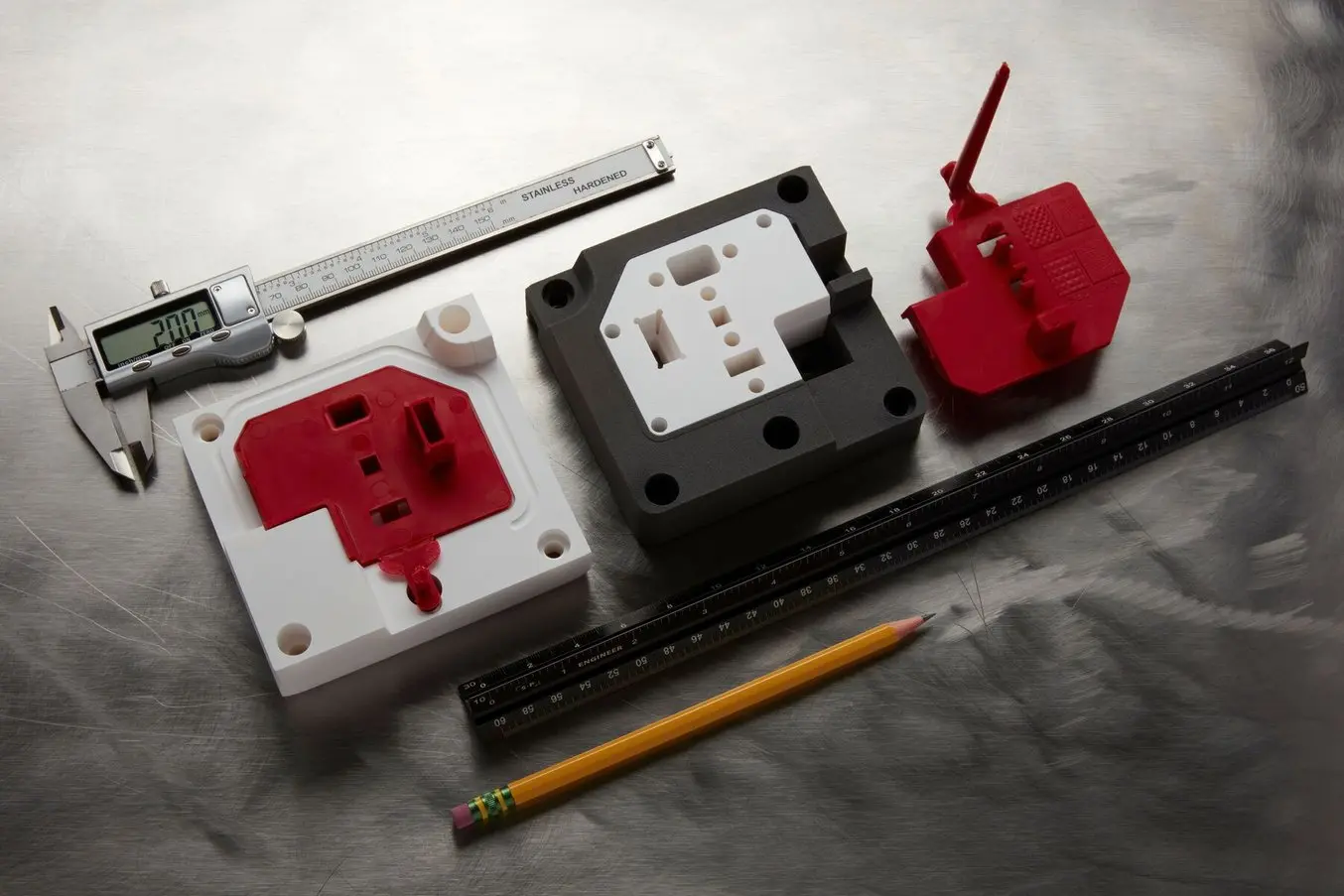
Stampi a iniezione realizzati in 3D con la Rigid 10K Resin.
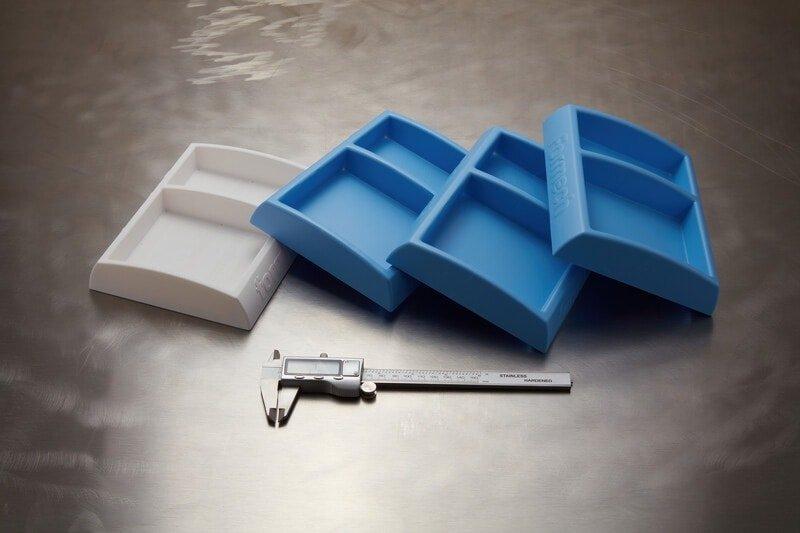
Stampi per imballaggi prodotti con termoformatura, realizzati in 3D con la Rigid 10K Resin.
Realizzazione di uno studio di fattibilità
Grazie alla stampa 3D, realizzare prodotti o lanciare nuove linee di articoli diventa ogni giorno più accessibile e conveniente. Una singola stampante 3D Fuse 1+ 30W permette di realizzare oltre 19 000 montature o 50 000 stanghette all'anno, con un programma di produzione non ottimizzato di cinque giorni.
Capacità annuale di montature realizzate con la Nylon 12 Powder | Costo per parte della polvere sinterizzata | Costo per parte rettificato** | ||
---|---|---|---|---|
1 Fuse 1+ 30W | 19 680 | 0,66 $ | 1,92 $ | |
5 Fuse 1+ 30W | 98 400 | Contatta Formlabs | Contatta Formlabs | |
10 Fuse 1+ 30W | 196 800 | Contatta Formlabs | Contatta Formlabs | |
* Supponendo una settimana lavorativa di cinque giorni con cinque stampe a settimana, per 48 settimane all'anno.
** Costo per parte rettificato in base alla perdita di materiale dovuta alla densità di stampa più bassa. Scopri di più sul tasso di rigenerazione.
Opzione 1: possedere i propri mezzi di produzione
Il modo più efficiente e conveniente di produrre occhiali stampati in 3D è possedere gli apparecchi di produzione. Ciò comporta l'acquisto di un ecosistema Fuse 1+ 30W.
I vantaggi della produzione con stampa 3D integrata verticalmente includono l'ottimizzazione del ritorno d'investimento, il controllo più rigoroso della qualità, la possibilità di modificare il design e di passare dalla prototipazione alla produzione sullo stesso apparecchio e la possibilità di utilizzare l'ecosistema per altri scopi, come la creazione di dime e fissaggi.
Progettato per essere il più accessibile possibile, l'ecosistema Fuse 1+ 30W vanta un funzionamento plug-and-play intuitivo: la maggior parte delle persone impara a usarlo in poche ore. Inoltre, non ha requisiti particolari in fatto di stabilimento, quindi consente una rapida installazione e una facile scalabilità man mano che la domanda cresce.
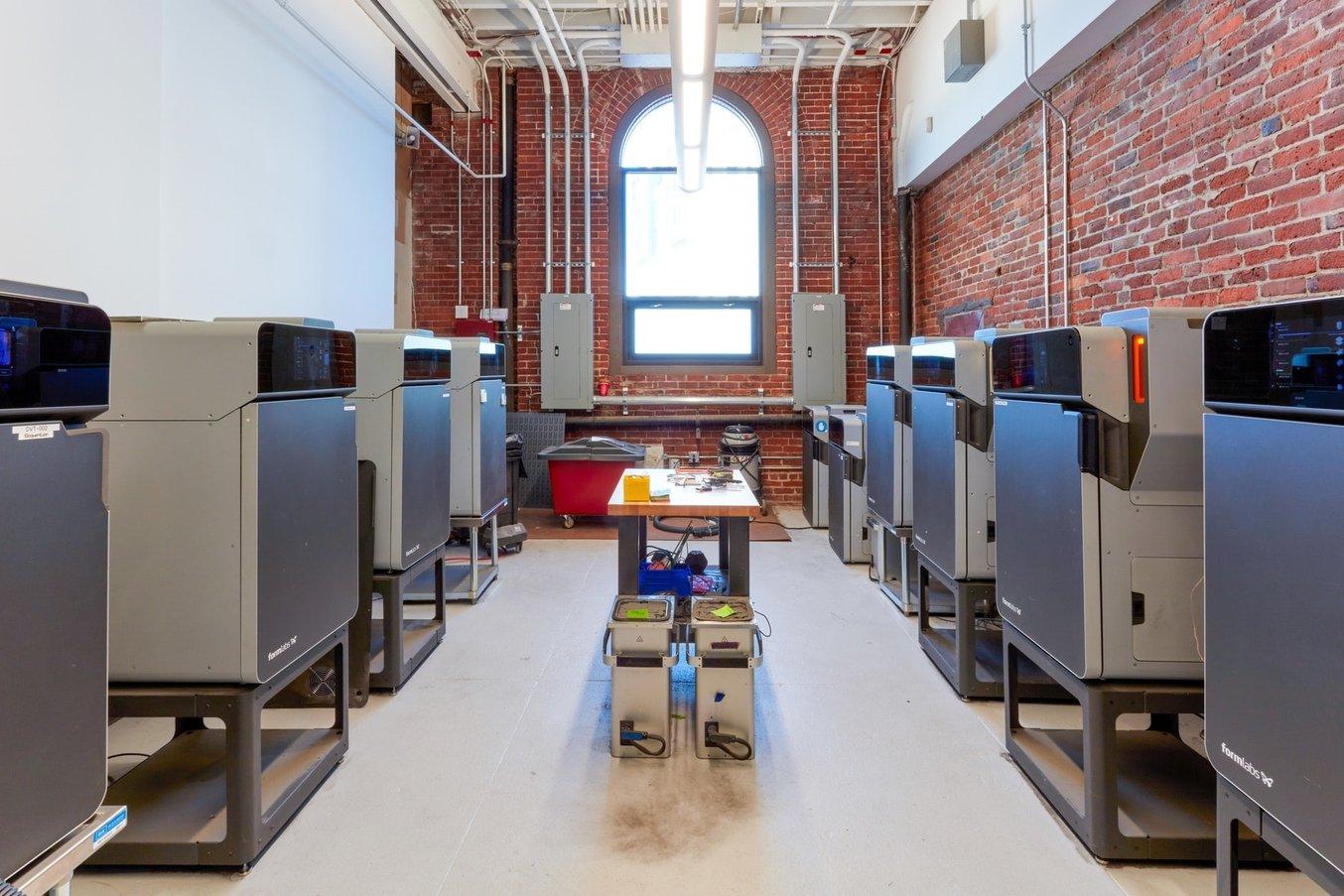
Con la serie Fuse, è facile scalare il proprio ecosistema man mano che la domanda cresce.
È anche importante ricordare che non è necessario acquistare una nuova Fuse Sift per ogni stampante Fuse 1+ 30W aggiuntiva. La maggior parte dei clienti dispone di una stazione di post-elaborazione ogni quattro stampanti.
Il costo per integrare un ecosistema di stampa SLS Formlabs completo, che comprende una Fuse 1+ 30W, un'unità di post-elaborazione Fuse Sift, due camere di stampa, due cartucce, 24 kg di Nylon 12 Powder e due anni di assistenza clienti da parte di esperti è di 53 350 $.
Opzione 2: esternalizzare a un fornitore di servizi
In tutto il mondo vi sono numerosi fornitori di servizi in grado di offrire una gamma variabile di soluzioni pronte all'uso, da quelli che si occupano solo della stampa 3D dei componenti a quelli che offrono servizi di progettazione, stampa, post-elaborazione e imballaggio.
Quando si lavora con un fornitore di servizi, il costo per parte è più elevato. Tuttavia, l'esternalizzazione può essere una buona opzione per chi non ha lo spazio o il capitale da investire in apparecchi di produzione, ma anche per chi vuole condurre un esperimento a volumi ridotti.
Contatta Formlabs per ricevere un elenco di fornitori di servizi approvati.
Inizia a realizzare occhiali stampati in 3D
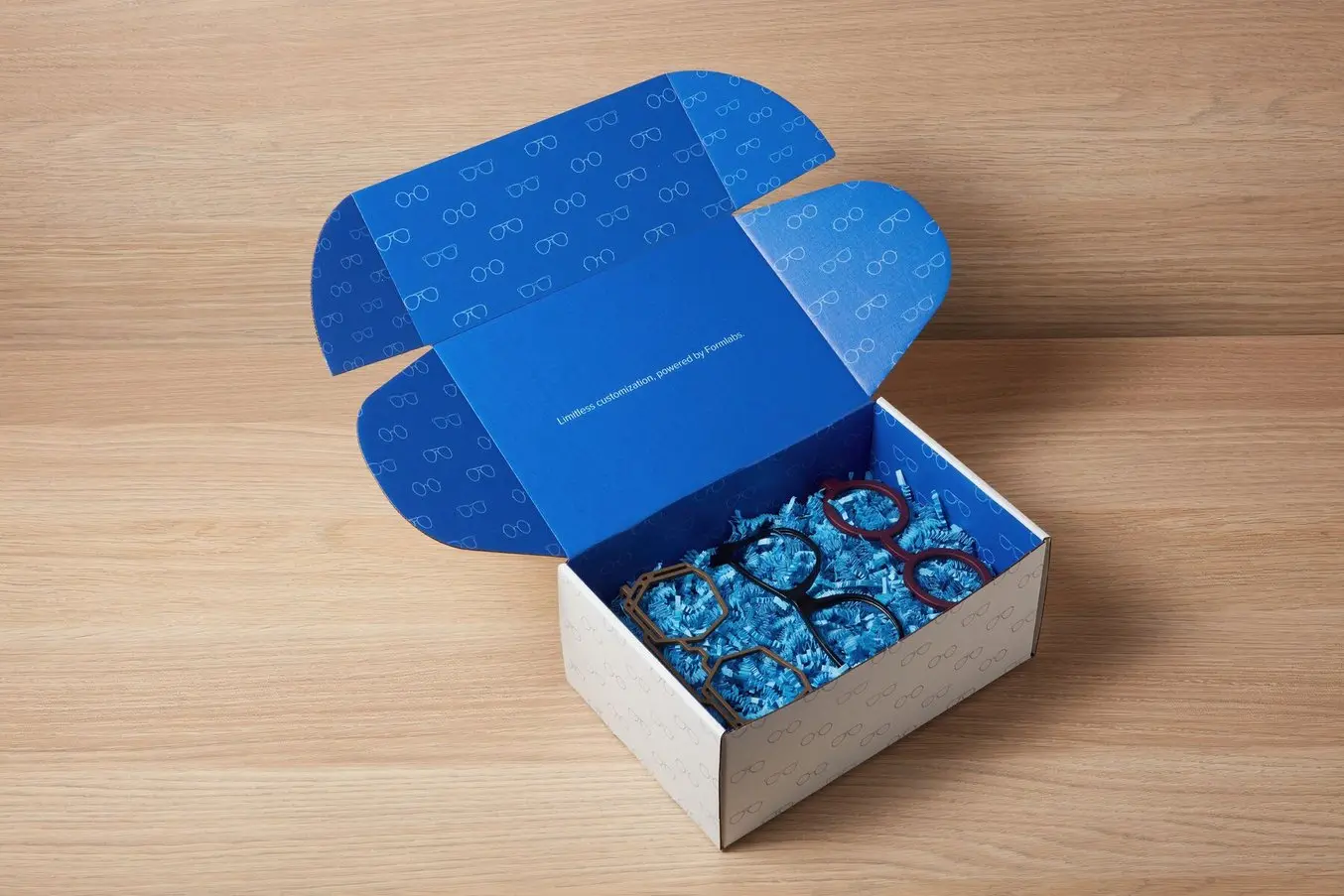
Vuoi ricevere uno dei nostri campioni di occhiali standard o far stampare un modello progettato da te? Contatta il team di Formlabs specializzato in occhiali.