Plastinax produce occhiali e prodotti correlati per alcuni dei marchi più importanti al mondo dal 1976. L'azienda collabora con clienti internazionali per la progettazione di occhiali da sole, montature e occhiali protettivi, che poi produce in grandi volumi utilizzando lo stampaggio a iniezione, per un totale di 80 000-100 000 montature al mese. I tempi di consegna brevi e la reattività sono di fondamentale importanza. Per rimanere competitiva sul mercato mondiale, Plastinax deve infatti accelerare i tempi di progettazione e produzione in modo che le montature possano essere spedite dalla sede in Mauritius alla clientela in tutto il mondo.
Plastinax, controllata di ENL Group, sfrutta le stampanti 3D stereolitografiche (SLA) e a sinterizzazione laser selettiva (SLS) di Formlabs per produrre piccoli lotti di prototipi funzionali di montature da sottoporre alla clientela, che può così valutarli e fornire un riscontro prima di passare alla produzione. L'azienda adesso utilizza anche le attrezzature stampate in 3D per la produzione ponte o in volumi ridotti di componenti per occhiali, sfruttando la stampante 3D SLS Fuse 1 e la Nylon 12 Powder.
Questo workflow di stampa 3D ha permesso a Plastinax di rispondere più rapidamente alle richieste e di ampliare la gamma di design realizzabili. Steeven Devasagayaum, ingegnere progettista presso Plastinax, ci ha parlato dell'integrazione della Form 2 e della Fuse 1 nel workflow dell'azienda, spiegandoci come la stampa 3D ha cambiato l'approccio alla progettazione e alla produzione.
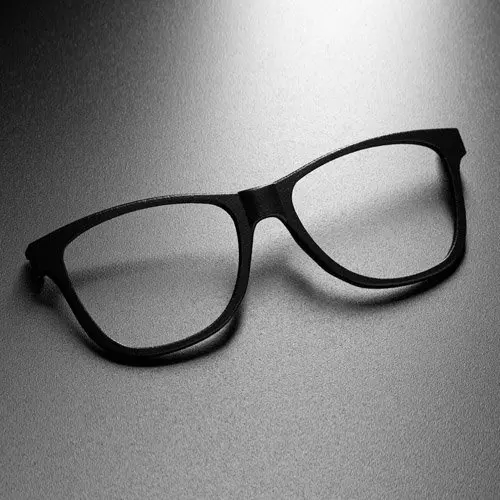
Produzione di occhiali stampati in 3D sull'ecosistema SLS serie Fuse di Formlabs
Questo whitepaper illustra le considerazioni su design e materiali di diverse aziende che producono montature di occhiali stampate in 3D.
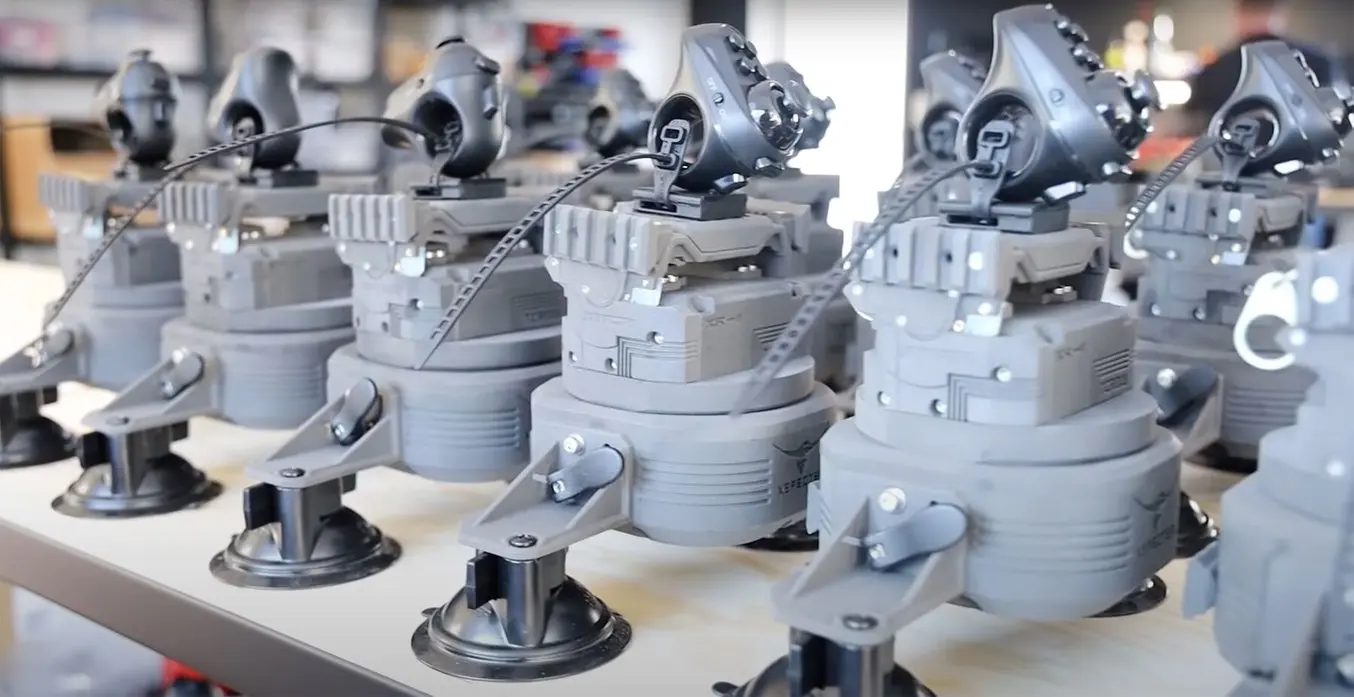
Produzione SLS per utilizzo finale
La stampa 3D per utilizzo finale non è solamente possibile, ma ora, grazie all'ecosistema SLS Fuse, è anche più economica, agile e scalabile che mai. Visita la nostra pagina dedicata alla produzione SLS per confrontare i metodi, scoprire di più sui prezzi all'ingrosso della polvere e vedere come 15 aziende utilizzano già la serie Fuse.
Produzione su larga scala nell'isola di Mauritius
Plastinax ha iniziato a produrre montature per occhiali negli anni '70 per grandi marchi statunitensi, europei e di altri Paesi del mondo. Come per molti altri settori, all'epoca il processo di progettazione era lento e per lo più manuale, nonostante già allora questo ambito facesse leva sulla creatività e sulla differenziazione attraverso design complessi o branding particolari.
Dal suo ingresso in Plastinax nel 2006, Devasagayaum ha aiutato il team a passare dalla prototipazione manuale all'esternalizzazione di modelli stampati in 3D. Grazie a questo nuovo workflow, non solo è diventato possibile eseguire iterazioni di modelli iniziali più simili ai prodotti finali realizzati tramite stampaggio a iniezione, ma anche il processo di progettazione è stato velocizzato. Dopo il passaggio dalla presentazione del progetto o dal disegno tecnico al prototipo realizzato a mano, l'azienda ha potuto implementare scansione e disegno 3D esternalizzati.
L'ulteriore passaggio di stampa 3D di modelli era utile per creare prototipi più simili alle parti per utilizzo finale, ma non era ideale nel caso fosse necessario apportare piccole modifiche, poiché la consegna di un'ulteriore serie di prototipi poteva richiedere anche più di una settimana. Le tempistiche dell'esternalizzazione rappresentavano un ostacolo per la competitività di Plastinax.
La stampa 3D si sposta in-house
Il team di ricerca e sviluppo di Plastinax ha iniziato a cercare una stampante 3D SLA da implementare in-house per accorciare i tempi di realizzazione. Tuttavia, gli apparecchi sul mercato erano costosi ed esternalizzare la prototipazione rapida era più conveniente che investire in una delle apparecchiature disponibili all'epoca.
Nel 2016, Plastinax ha deciso di adottare la stampa 3D in-house acquistando una Form 2. Un anno dopo, l'azienda ha introdotto una seconda unità per soddisfare la crescente richiesta di prototipi rapidi. "Questi apparecchi ci hanno cambiato la vita, permettendoci di progettare e ottenere prototipi nel giro di poche ore. Potevamo finalmente dimostrare alla nostra clientela internazionale di essere reattivi e di poter apportare modifiche nell'arco di una settimana. Sono i migliori apparecchi in termini di rapporto qualità-prezzo e soprattutto di affidabilità", afferma Devasagayaum.
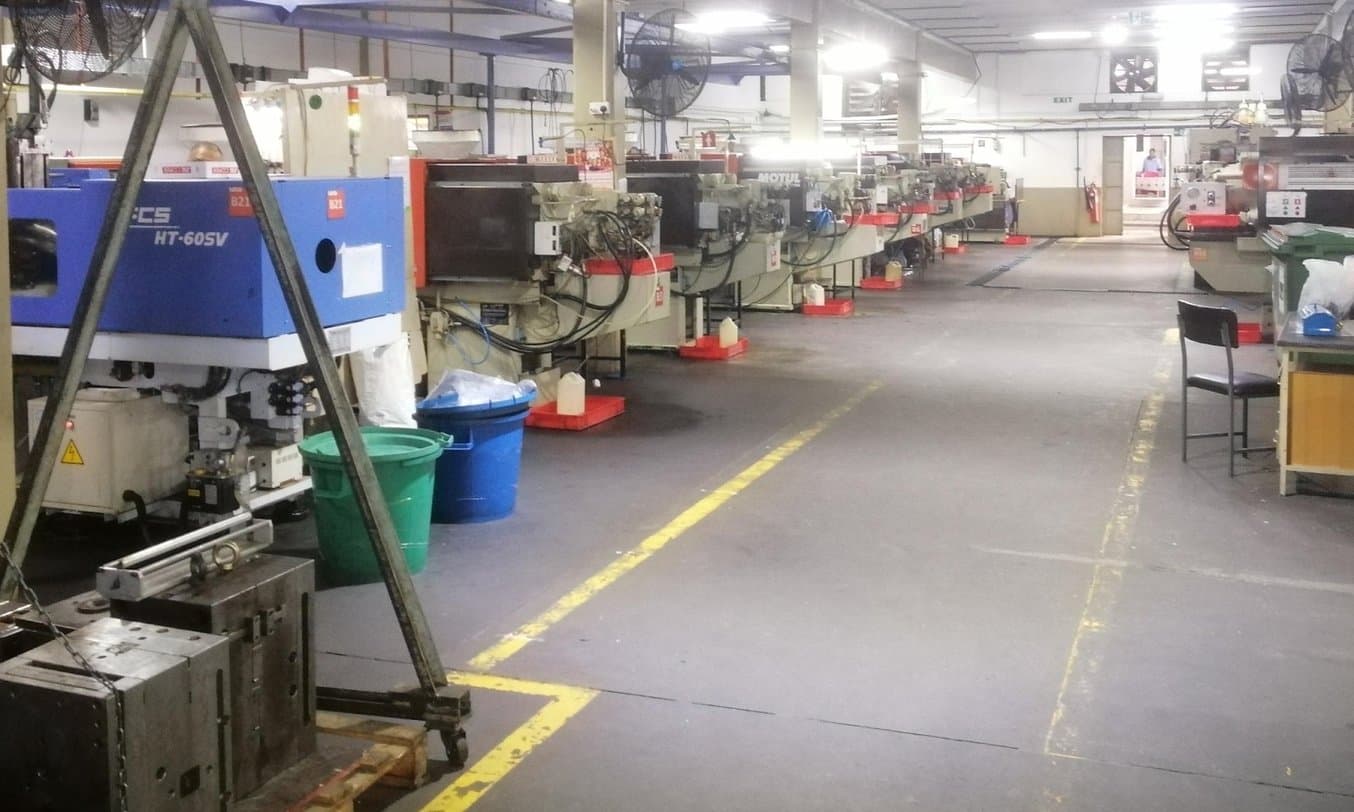
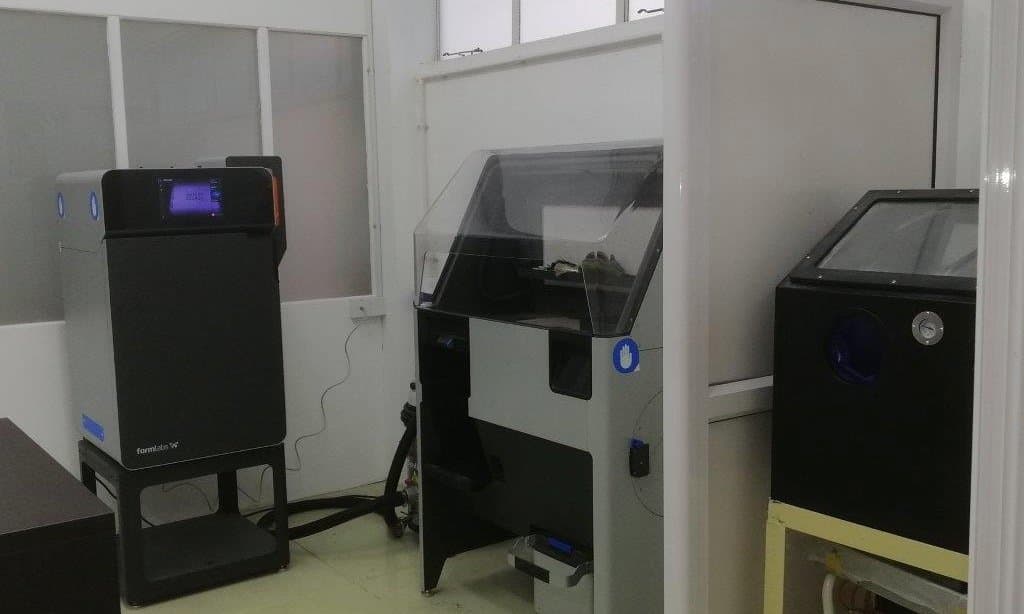
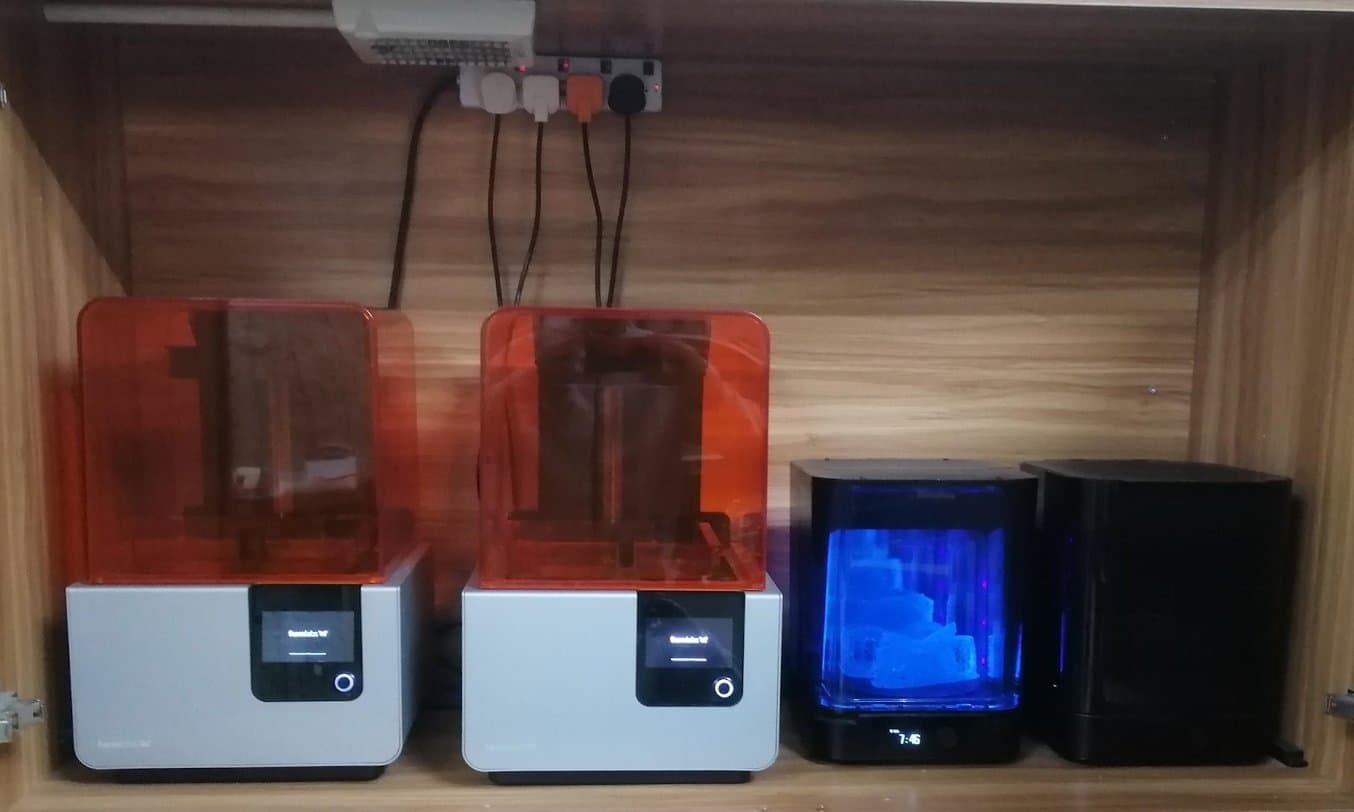
Sfruttando la potenza industriale di un impianto di produzione su larga scala (a sinistra), Plastinax produce più di un milione di paia di occhiali all'anno. Grazie alla presenza in-house di stampanti 3D come quelle della serie Fuse (al centro) e le Form 2 (a destra), l'azienda riesce a eseguire iterazioni più accurate e continuare a far crescere la propria attività.
Aumento della produzione grazie alla stampa SLS
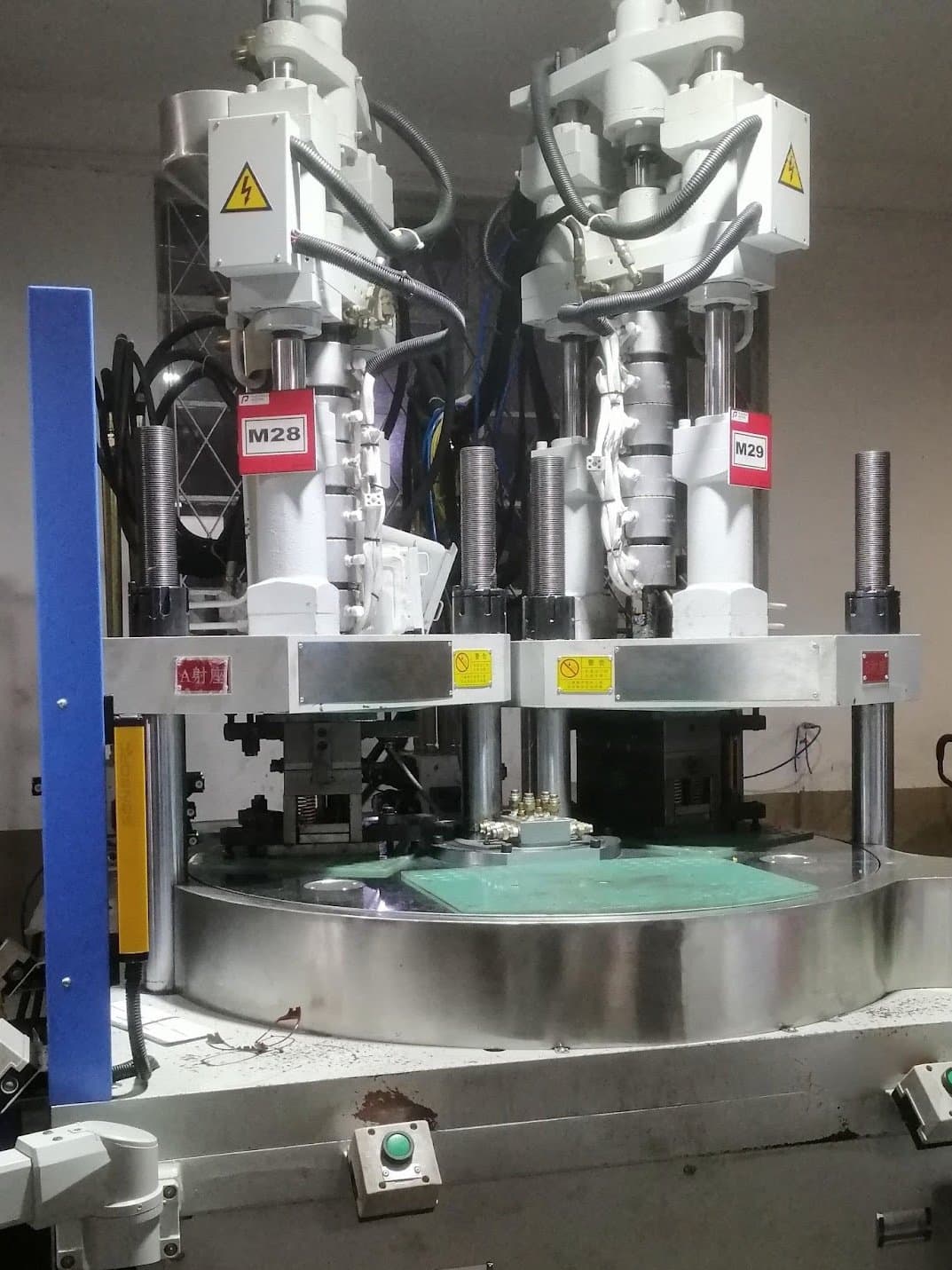
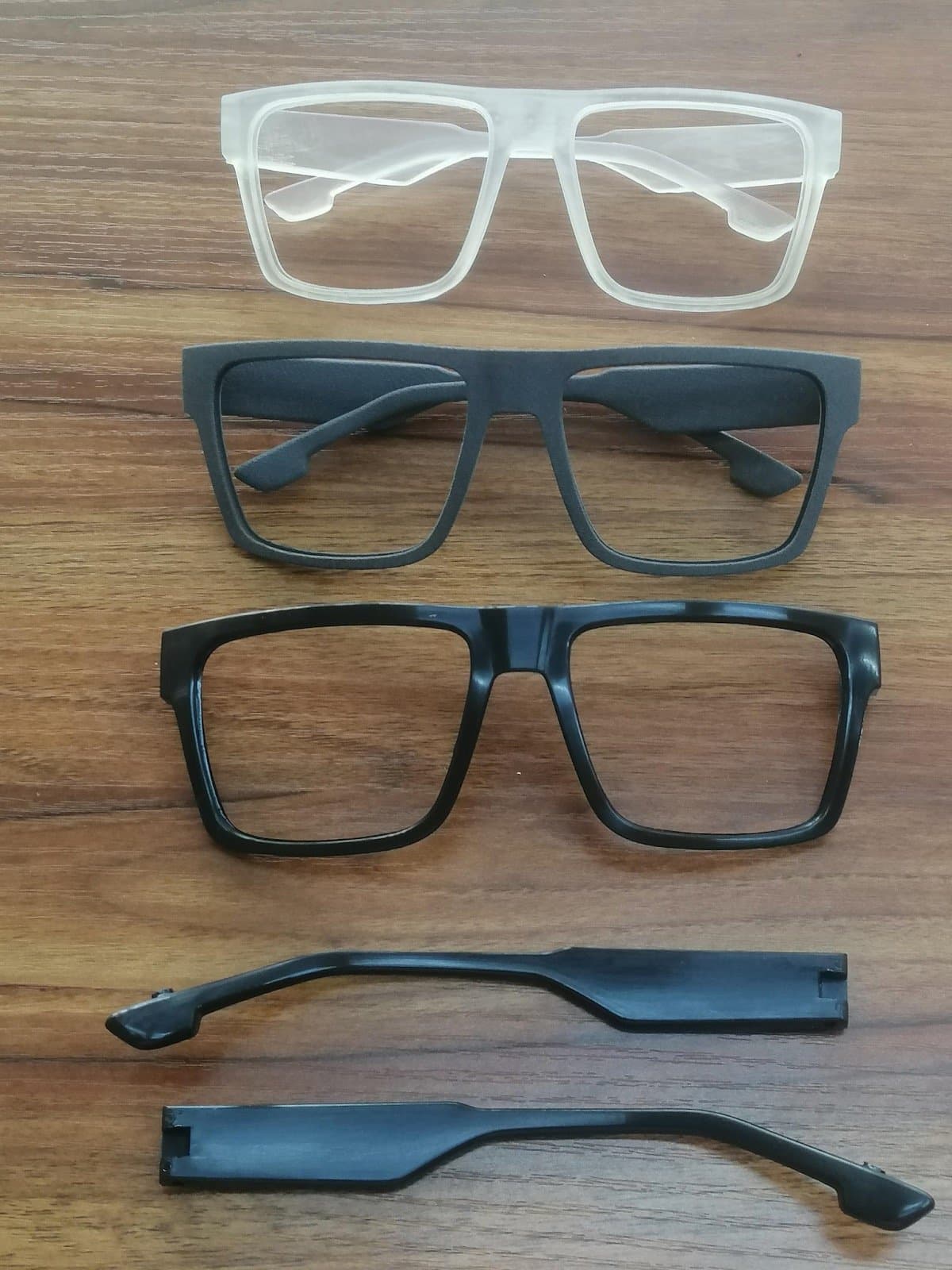
Plastinax è ora in grado di sfruttare sia lo stampaggio a iniezione con le sue apparecchiature industriali (a sinistra) che la stampa 3D con materiali SLA e SLS (a destra, modelli in alto e al centro), così da realizzare montature che hanno le stesse caratteristiche estetiche e funzionali del prodotto per utilizzo finale (a destra, modello in basso).
Plastinax ha aumentato sia la produzione che il numero di resine utilizzate, dalla Clear Resin per la creazione di montature traslucide di design fino alla Grey Pro Resin, utilizzata per i test funzionali. Nel 2021, un cliente ha mostrato al team alcuni prototipi stampati in 3D in nylon da un'azienda della concorrenza con sede in Asia orientale, sottolineando la loro lunga durata. "Da quel momento, abbiamo iniziato a cercare un apparecchio che potesse creare un prodotto simile. Dovevamo compiere un altro passo verso l'innovazione introducendo in azienda attrezzature affidabili e ad alte prestazioni in modo da essere il più competitivi possibile. Lavoravamo con Formlabs già da sei anni e visto che l'assistenza e il servizio clienti erano stati eccezionali, abbiamo deciso di acquistare una Fuse 1", racconta Devasagayaum.
Piccoli cambiamenti, grandi risultati
Per un produttore a contratto internazionale come Plastinax, il successo si basa sulla capacità di assicurarsi una commessa e dimostrare che il proprio prodotto finale è migliore di quello della concorrenza. Inviare ai clienti un solo design realizzato in un materiale di alta qualità non sempre è sufficiente. Steeven Devasagayaum si affida alla Fuse 1 per apportare microscopiche modifiche richieste dai clienti.
"Nel settore degli occhiali, sono le piccole differenze che contano, persino quelle di qualche decimo di millimetro. Mi è stato chiesto, ad esempio, di modificare di un solo grado l'angolo del ponte di un paio di occhiali, e queste stampanti possono farlo. Una volta pronte, inviamo al cliente le varie versioni", afferma Devasagayaum.
Il letto di polvere autoportante della tecnologia SLS consente di posizionare le parti nella Fuse 1 in modo efficiente, nidificandole o impilandole per sfruttare al massimo ogni granello di polvere. Questa soluzione permette di stampare più di dieci montature alla volta. Ciò semplifica il workflow e consente di sottoporre facilmente più parti insieme alla post-elaborazione nella Fuse Sift. La capacità di offrire simultaneamente diverse variazioni sul design è uno degli elementi che permette a Plastinax di assicurarsi ordini dopo un solo colloquio con il cliente. Una volta Plastinax è potuta intervenire dopo l'errore di un'azienda della concorrenza, che aveva inviato montature con lenti di dimensione errata. "Siamo riusciti a trovare le dimensioni giuste e stampare le montature in 3D in poche ore, per poi inviarle al cliente il giorno successivo", racconta Devasagayaum.
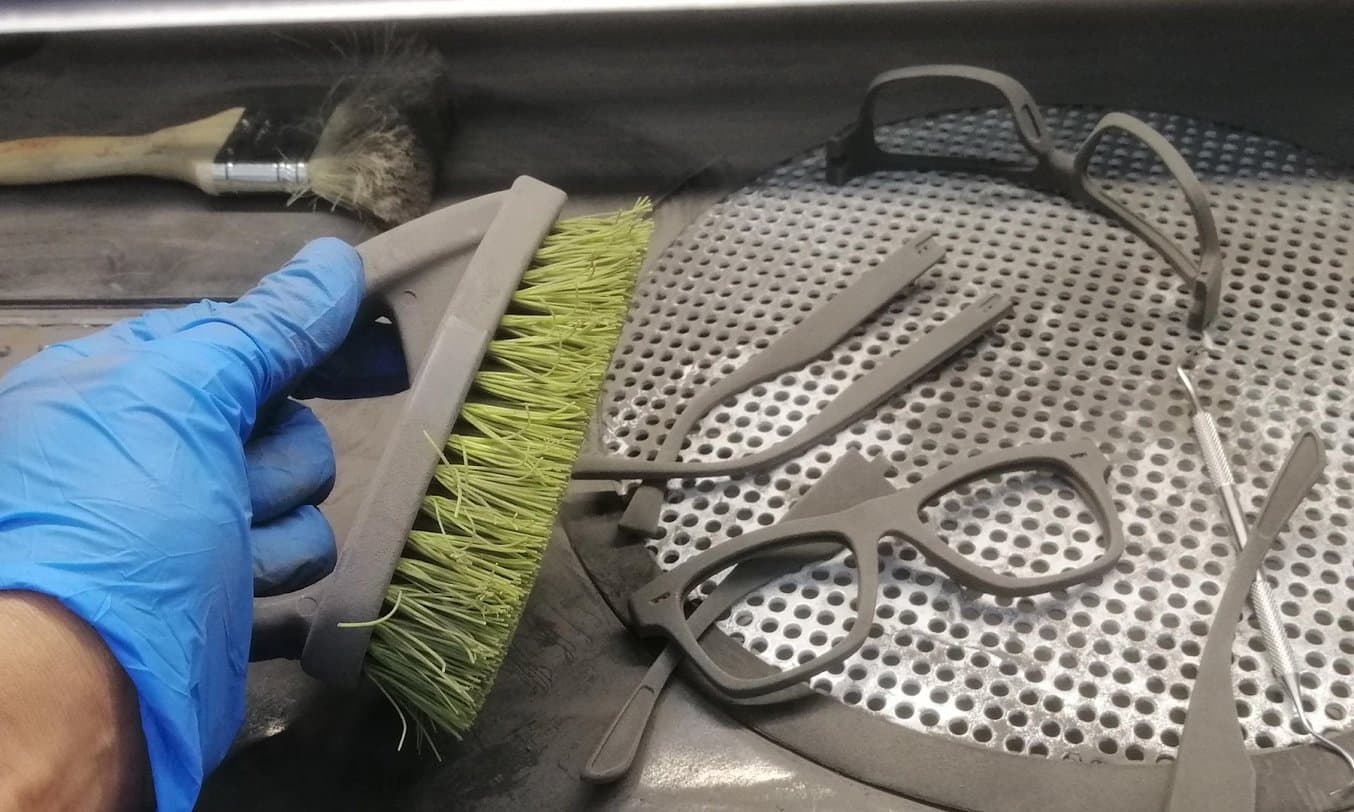
La Fuse Sift semplifica il workflow di Plastinax e consente la creazione rapida di prototipi per valutare aderenza, funzionamento e aspetto estetico.
Workflow di stampa SLA e SLS semplificato
Poter contare su una soluzione industriale avanzata in-house aiuta a mantenere il workflow efficiente. Devasagayaum utilizza sia la stampa SLA che quella SLS nel processo di progettazione. L'ingombro ridotto delle stampanti semplifica il passaggio da una tecnologia all'altra nel corso della giornata. Mentre la Fuse 1 crea prototipi funzionali che riportano precisamente minuscole differenze di grandezza, la Form 2 può stampare due montature in Clear Resin che verranno verniciate per mostrare varie opzioni per la finitura superficiale finale.
"Entrambe le tecnologie sono utili nel nostro processo di progettazione. La Nylon 12 Powder è simile alla poliammide di cui saranno costituite le montature finali realizzate tramite stampaggio a iniezione. Inoltre, è possibile applicare alle parti in Clear Resin alcune vernici e trame per mostrare le finiture superficiali che possiamo creare. Abbiamo la possibilità di sfruttare sia la finitura superficiale della stampa SLA, che la stabilità e la resistenza del nylon."
Steeven Devasagayaum, ingegnere progettista presso Plastinax
Grazie alla somiglianza tra nylon e poliammide, per la clientela è più semplice farsi un'idea del peso e della resistenza che avranno le montature finali realizzate tramite stampaggio a iniezione. Per un cliente che aveva richiesto la realizzazione di un paio di occhiali protettivi, Devasagayaum ha stampato svariati prototipi rapidi da mostrare al team marketing del cliente. Poiché gli occhiali dovevano essere durevoli, resistenti agli urti e leggermente flessibili, la stampa 3D SLS era la scelta perfetta. "Abbiamo potuto verniciarli rapidamente e dopo questa fase avevano lo stesso aspetto delle versioni finali in plastica realizzate tramite stampaggio", afferma Devasagayaum.
La flessibilità intrinseca delle parti in Nylon 12 Powder è utile anche per inserire ed estrarre le lenti di prova nei prototipi. Plastinax è in grado di offrire prototipi perfettamente funzionali con lenti di diverso spessore per svariate montature, fornendo ai clienti modelli dalle caratteristiche estetiche e funzionali identiche a quelle che avranno le montature realizzate tramite stampaggio a iniezione.
L'azienda ha ora la possibilità di stampare fino a 28 prototipi alla volta utilizzando la Fuse 1 nei casi in cui siano necessarie quantità più elevate di parti, come per le fiere di settore. "Possiamo facilmente creare in-house prototipi rapidi dalle caratteristiche estetiche e funzionali uguali a quelle del prodotto finale. Ricorrendo all'esternalizzazione, ci vorrebbero almeno dieci giorni", afferma Devasagayaum.
Oltre alla prototipazione, Plastinax si affida alle stampanti della serie Fuse anche per l'implementazione di nuovi workflow per la creazione di attrezzature. La leggera flessibilità del nylon e l'elevata precisione dimensionale offrono la possibilità di ideare, testare e produrre attrezzature resistenti utili nelle linee di produzione. Ad esempio, Devasagayaum stampa strumenti di formatura di lenti e basi per il taglio delle stesse, nonché per l'inserimento di cerniere di metallo flessibili nelle aste o per il mantenimento della montatura in posizione durante la realizzazione di cavità per l'applicazione di loghi metallici personalizzati.
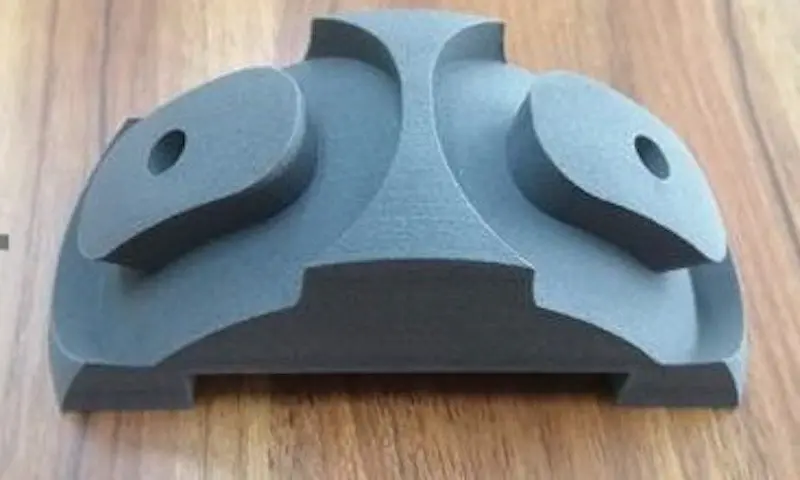
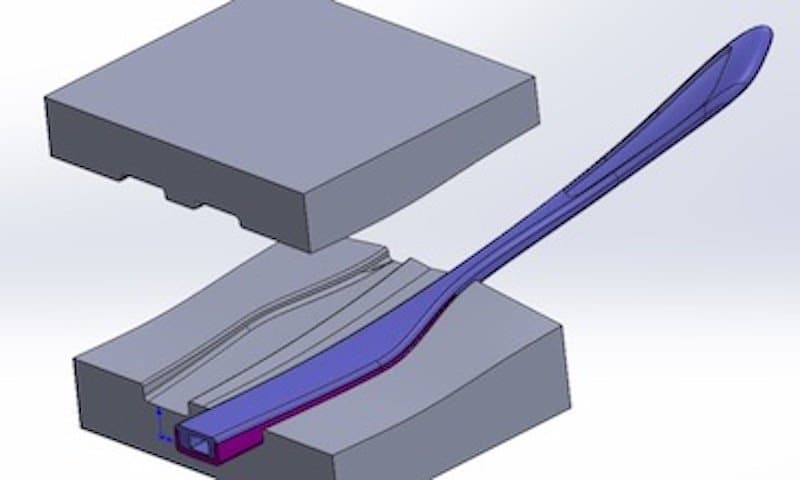
Plastinax crea attrezzature per la formatura di lenti (a sinistra) o basi per l'inserimento di cerniere di metallo flessibili nelle aste degli occhiali o per la realizzazione tramite CNC di cavità sulle montature per l'applicazione di loghi metallici personalizzati.
Uno sguardo rivolto al futuro
Il settore degli occhiali è destinato a essere protagonista nell'ambito della personalizzazione. Gli occhiali sono tra i pochi prodotti a essere usati sia come accessorio estetico che come elemento necessario nella vita di milioni di persone con problemi di vista. Entrambi questi aspetti possono trarre vantaggio dalla personalizzazione, sia essa basata sull'adattamento alla forma del viso o su decisioni estetiche personali.
Plastinax sa che poter personalizzare i propri prodotti sarà di grande importanza nel prossimo futuro e considera come opzioni valide a tal fine sia il workflow SLA che quello SLS. La creazione rapida di attrezzature per lo stampaggio a iniezione tramite stampa 3D SLA con materiali come la Rigid 10K Resin è un'alternativa alla creazione di attrezzature in metallo. Inoltre, Devasagayaum sta già considerando di sfruttare la produzione in serie di piccoli lotti di montature per utilizzo finale realizzate tramite stampa diretta con la Fuse 1. "Le possibilità sono infinite. La Form 2 e la Fuse 1 hanno rivoluzionato il nostro modo di lavorare", afferma.
Per maggiori informazioni sulla stampa 3D di montature per occhiali, dai un'occhiata al nostro manuale operativo oppure contatta il nostro team vendite per scoprire come portare la stampa 3D SLS e SLA in-house.