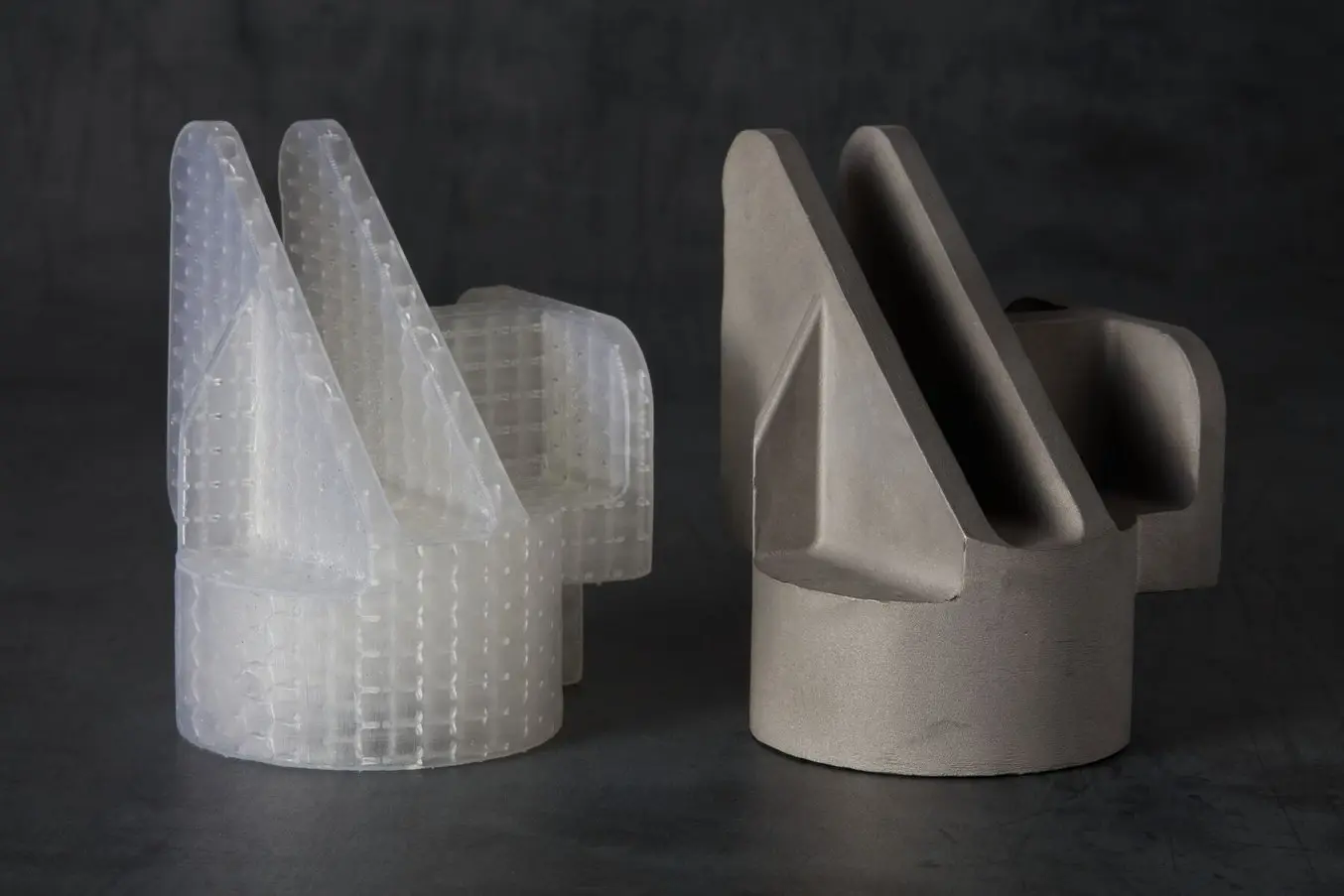
Modello per fusione a cera persa stampato in 3D con la Clear Cast Resin e parte in metallo fusa.
La fusione del metallo è un processo di lavorazione antichissimo che prevede l'inserimento di metallo fuso in uno stampo, all'interno del quale si raffredderà e si solidificherà creando una parte finale. Nonostante le sue origini antiche, la fusione del metallo rimane ancora oggi uno dei processi più diffusi tra le aziende che producono parti metalliche.
In questo articolo vedremo cos'è e come funziona la fusione del metallo, e ti guideremo attraverso i processi di fusione del metallo più diffusi. Inoltre, ti mostreremo i benefici che si possono ottenere combinando strumenti digitali moderni come la stampa 3D ai workflow di fusione.
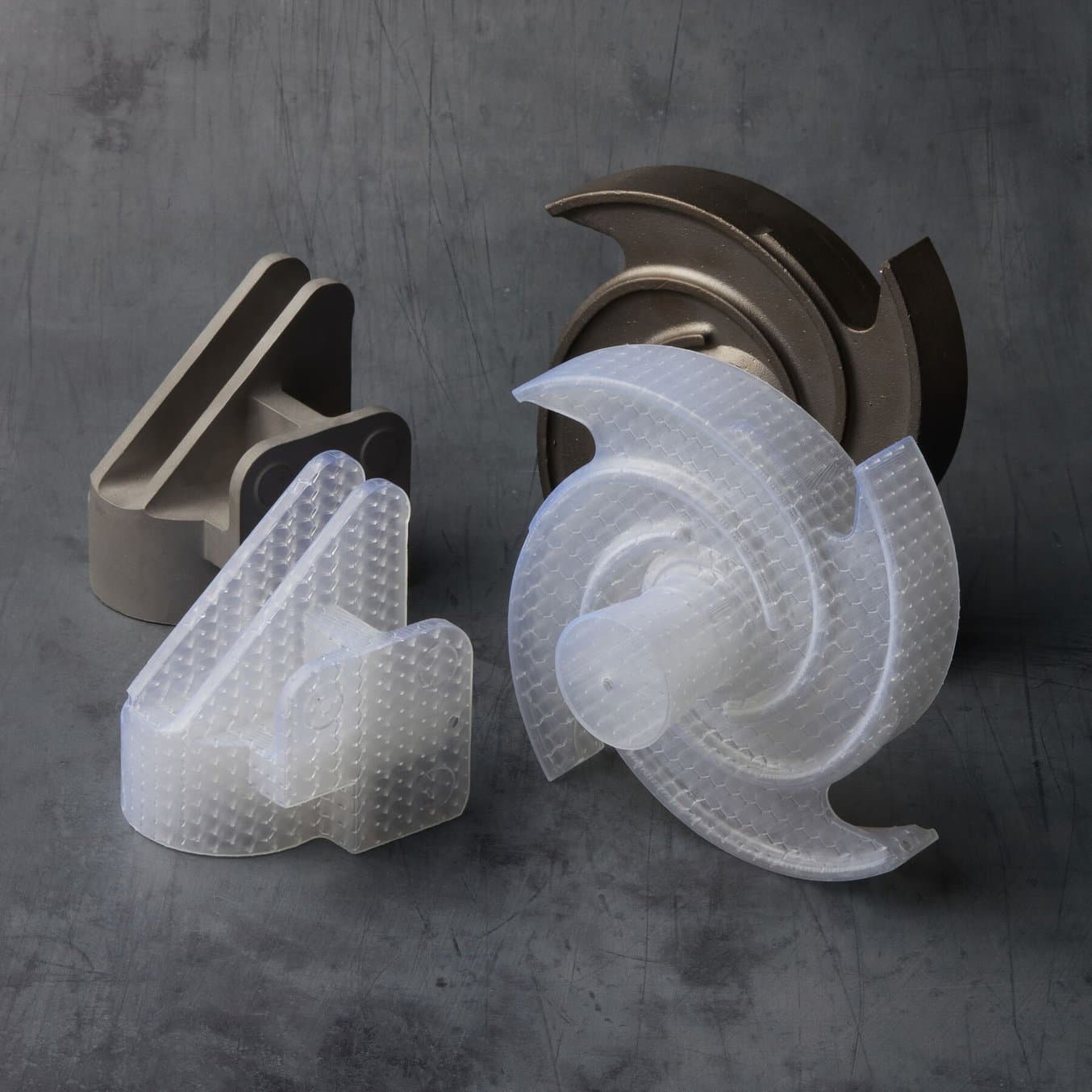
Fusione di parti in metallo precisa e conveniente grazie alla stampa 3D
Questo whitepaper presenta i metodi che hanno permesso a diverse fonderie leader di eseguire la fusione di parti in metallo utilizzando modelli 3D realizzati con stampanti Formlabs. Scopri come le fonderie riescono a risparmiare, ridurre i tempi di produzione e migliorare la qualità delle parti in metallo grazie all'integrazione nei processi di fusione tradizionali della Clear Cast Resin di Formlabs e del modulo di reticolazione di Materialise Magics.
Panoramica del processo di fusione del metallo
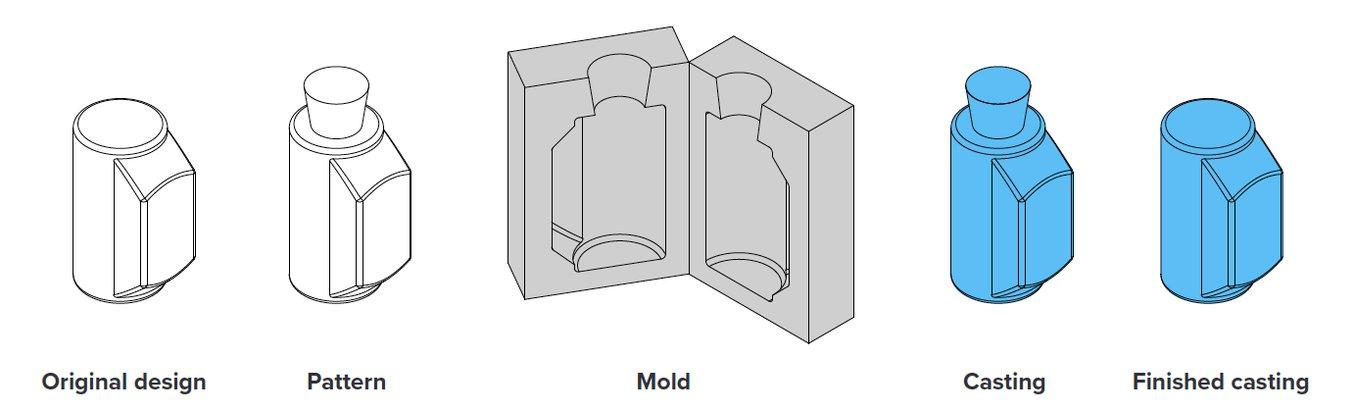
Le fasi della fusione del metallo, dal progetto originale fino alla fusione finale.
Dall'avvento della fusione del metallo, i metodi si sono evoluti e sono cambiati. Tuttavia, le tecniche principali sono rimaste le stesse. Vediamo di seguito uno per uno i passaggi di un procedimento generale per la fusione del metallo:
1° passaggio: realizzazione del modello
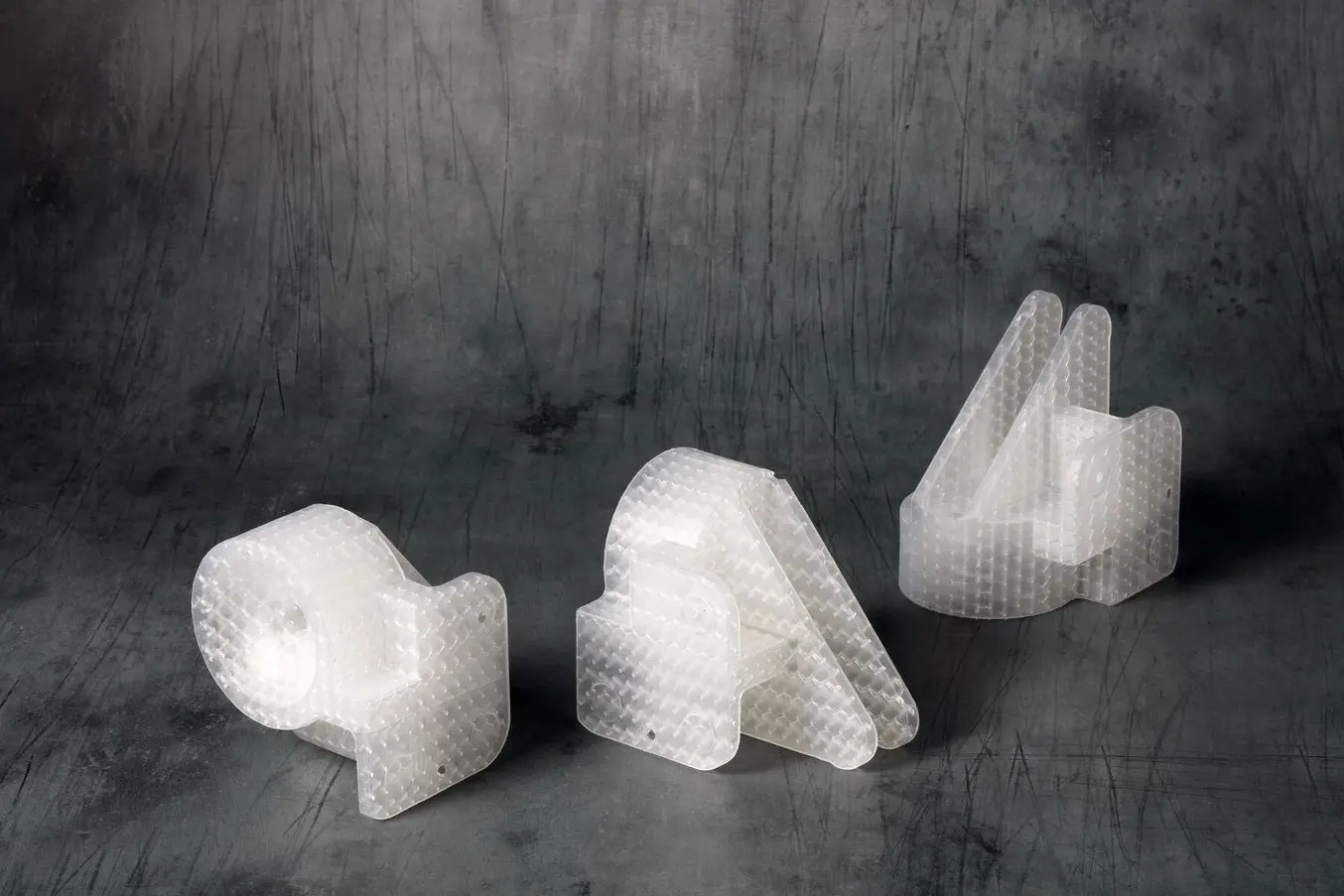
Modelli per fusione a cera persa industriale stampati in 3D con la Clear Cast Resin.
Per iniziare il processo di fusione del metallo, è necessario prima creare una rappresentazione del modello che si desidera ottenere. Questo modello è essenziale per la progettazione dello stampo da usare durante la fusione. Solitamente è realizzato in legno, schiuma, plastica o cera e serve ad assicurarsi che lo stampo riproduca in modo fedele la parte in metallo finita. Oggi, la stampa 3D è un metodo di produzione dei modelli molto comune, che permette ai team di progettazione di creare modelli accurati direttamente da strumenti software CAD digitali.
Il modello non è la replica esatta della parte desiderata, in quanto include alcuni elementi addizionali che rendono possibile il processo di fusione, tra cui aperture per permettere al metallo fuso di fluire in modo uniforme e sfiati per permettere la fuoriuscita dei gas. Inoltre, i modelli devono essere più grandi delle parti che rappresentano per via del restringimento che avviene durante il raffreddamento.
Quando la parte fusa è cava, è necessario creare anche un nucleo di sabbia o metallo per modellare la forma interna. Questo nucleo viene rimosso una volta completata la fusione.
2° passaggio: creazione degli stampi
Il passaggio successivo consiste nella creazione di uno stampo per la fusione, che può essere riutilizzabile (non sacrificabile) o non riutilizzabile (sacrificabile). Gli stampi non riutilizzabili vengono generalmente realizzati in sabbia, gesso o cera, oppure mediante stampa 3D. Proprio come suggerisce il nome, vengono distrutti durante il processo di fusione. Gli stampi riutilizzabili sono realizzati in metallo o in altri materiali resistenti e possono essere riutilizzati per molti cicli di fusione.
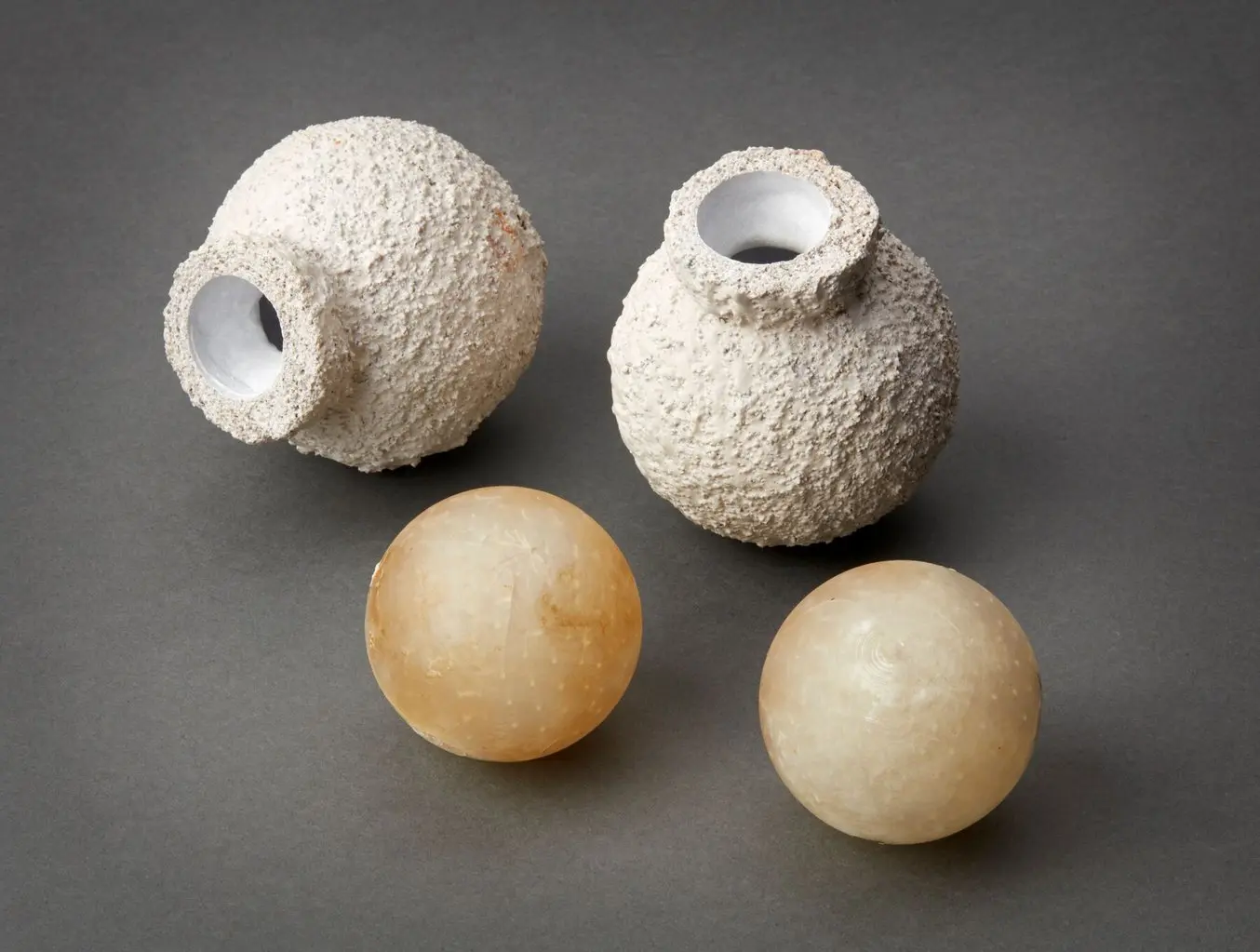
Gusci ceramici dopo la combustione e modelli stampati in 3D con la Clear Resin.
3° passaggio: fusione e versamento del metallo fuso
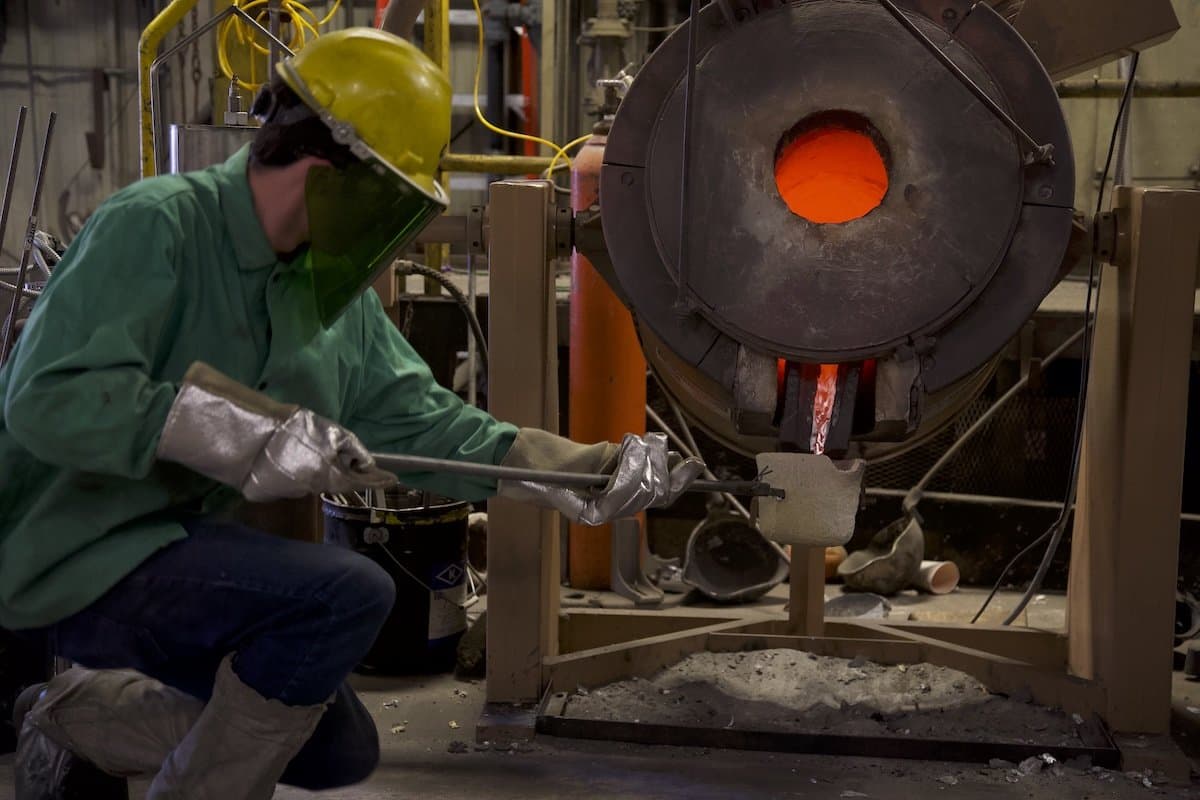
Versamento dell'alluminio fuso in uno stampo cavo.
Durante questo passaggio, il metallo viene scaldato in un forno di cottura finché non si scioglie. In base all'applicazione, si possono utilizzare diversi metalli. I metalli più comuni per la fusione sono il ferro, l'alluminio, le leghe di alluminio, l'acciaio, il rame e lo zinco, oltre ai metalli preziosi come l'oro e l'argento. Una volta sciolto, il metallo viene versato nella cavità dello stampo e viene lasciato a raffreddare e solidificare.
4° passaggio: rimozione dallo stampo e pulizia
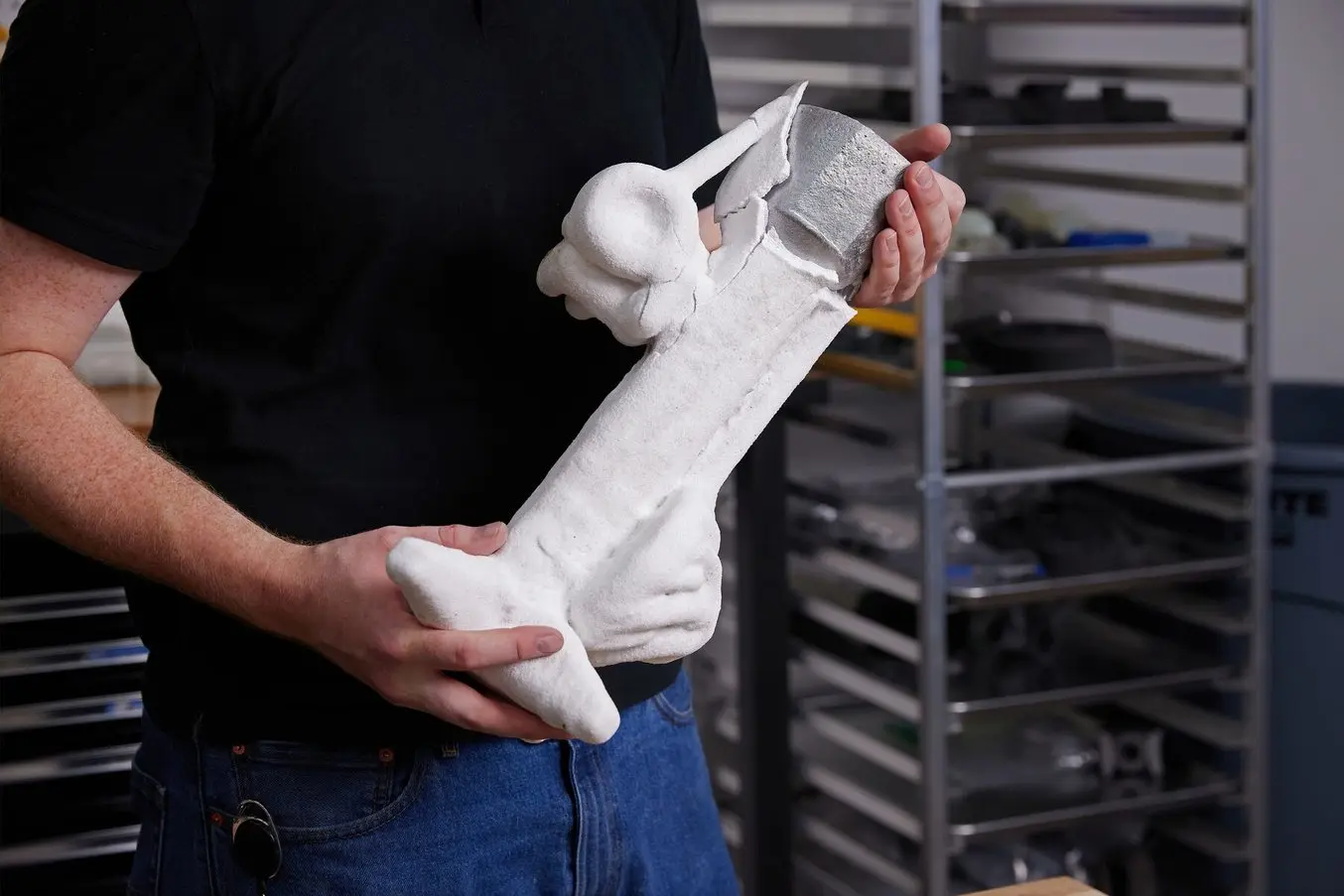
Interventi di post-produzione successivi alla fusione del metallo.
Quando il metallo si è raffreddato e solidificato, le parti vengono rimosse dallo stampo. A seconda della tipologia di stampo, la rimozione può avvenire attraverso le vibrazioni, con il processo di scuotimento, lavando via il materiale di rivestimento oppure mediante perni di espulsione. A questo punto bisogna rimuovere dalle parti il materiale in eccesso, come gli sfiati, le aperture e i canali d'immissione. Infine, le parti vengono limate, raschiate, lavorate o sabbiate per renderne più liscia la superficie e ottenere i requisiti della forma finale.
Tipi di procedimento di fusione del metallo
Tutte le tecniche di fusione del metallo si basano sullo stesso procedimento principale, ma ci sono metodi differenti che si adattano meglio alle diverse applicazioni. Tra i metodi più comuni ci sono la pressofusione, la fusione a cera persa e la fusione in sabbia.
Colata a pressione
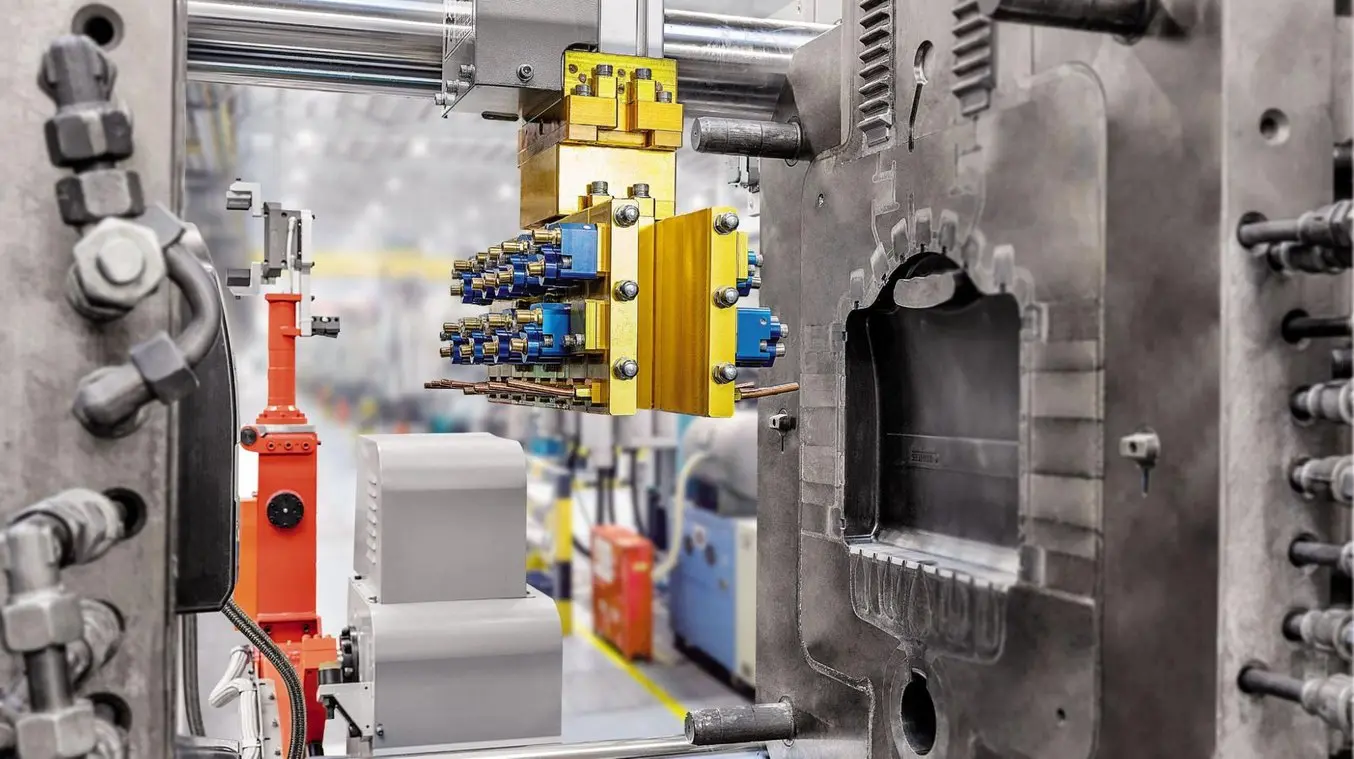
Per la pressofusione viene usato uno stampo in acciaio con un'elevata pressione. (Fonte: buhlergroup.com)
La pressofusione è un processo di fusione del metallo in cui il metallo fuso viene spinto all'interno di uno stampo cavo in acciaio a una pressione elevata, in modo tale da produrre velocemente le parti in metallo. Nella pressofusione, si fissano assieme due metà di una matrice o di uno stampo riutilizzabile e, attraverso un ugello, si inietta il metallo fuso ad alta pressione all'interno dello stampo. Quando il metallo si raffredda lo stampo si apre e i perni di espulsione spingono fuori la parte.
I due procedimenti di pressofusione più comuni sono quelli a camera calda e a camera fredda. Le specifiche di questi processi sono diverse, ma il procedimento di pressofusione nel suo insieme ha diverse caratteristiche in comune.
Pressofusione a camera calda
La pressofusione a camera calda è la più diffusa tra questi due procedimenti. Gli apparecchi per la pressofusione a camera calda dispongono al loro interno di un forno di cottura integrato per scaldare il metallo. Una volta che il metallo ha raggiunto lo stato fuso, l'apparecchio vi immerge all'interno una camera cilindrica. La forma a collo d'oca del sistema di iniezione del metallo permette alla camera di riempirsi rapidamente e fa sì che il materiale venga spinto all'interno dello stampo con la pressione dell'aria o con un pistone.
In questo procedimento di fusione, il riempimento mediante immersione del meccanismo di iniezione permette di iniettare il materiale all'interno dello stampo in modo facile e veloce. Tuttavia, poiché la camera è esposta in maniera diretta al calore del metallo fuso, i sistemi di pressofusione a camera calda sono a rischio di corrosione e quindi difficilmente praticabili per i metalli con punti di fusione elevati. Sono invece più adatti a materiali con punti di fusione bassi e ad alta fluidità, come il piombo, il magnesio, lo zinco e il rame.
Pressofusione a camera fredda
Il procedimento di pressofusione a camera fredda invece funziona più lentamente, così da evitare la corrosione. Questo metodo prevede l'inserimento manuale del metallo fuso all'interno del sistema di iniezione da parte dei lavoratori della fonderia. Successivamente, un pistone spinge il metallo all'interno dello stampo.
Il processo limita la corrosione, che è più frequente nella pressofusione a camera calda. Questa opzione è ideale per i metalli con punti di fusione elevati, come l'alluminio e le leghe di alluminio.
Vantaggi della pressofusione
Il procedimento di pressofusione è rapido e produce parti estremamente dettagliate. È ideale per la produzione di volumi elevati di parti complesse ed è anche in grado di produrre componenti con finitura superficiale liscia. La possibilità di produrre volumi elevati grazie alla pressofusione rende questo procedimento cruciale nei settori automobilistico e aerospaziale.
Svantaggi della pressofusione
Le attrezzature e i macchinari per la pressofusione sono molto costosi, quindi questo procedimento non è conveniente per produzioni con volumi più ridotti. Inoltre, la malleabilità dei metalli usati nel processo può influire sulla complessità del prodotto.
Fusione a cera persa
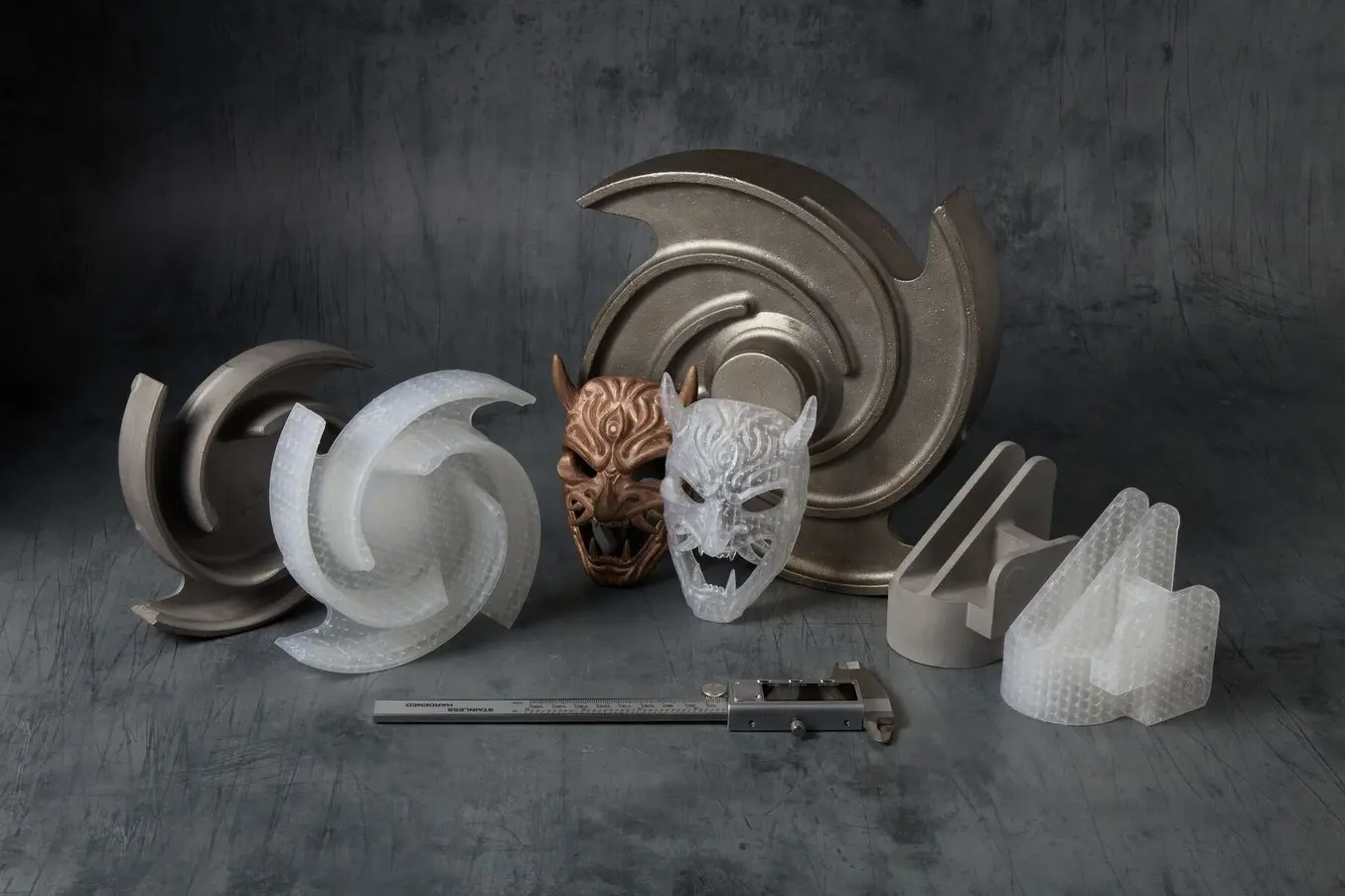
Parti fuse da modelli stampati in 3D con la Clear Cast Resin su una stampante 3D a resina di Formlabs.
La fusione a cera persa è un processo che usa cera, impasti e stampi per produrre parti complesse. Si tratta di una delle più antiche tecniche di fusione del metallo, utilizzata ancora oggi in quanto consente di creare parti precise con forme elaborate.
Questo processo viene usato su larga scala nella gioielleria, nell'odontoiatria e nell'arte. Nella sua forma industriale è un metodo comune per creare parti metalliche di precisione per l'ingegneria e la produzione.
I modelli per la fusione a cera persa sono di solito realizzati in cera o in polimeri stampati in 3D. I modelli vengono assemblati in una struttura ad albero e immersi in un impasto di silice, oppure posizionati all'interno di un cilindro e circondati dal materiale di rivestimento liquido. Una volta seccatosi il materiale di rivestimento, il cilindro viene capovolto all'interno di una fornace che scioglie il modello, lasciando una cavità in negativo con la forma del modello originale. Il metallo viene fuso e poi versato, sfruttando la gravità o la pressione sottovuoto per spingere il metallo all'interno della cavità. Le parti fuse vengono limate, levigate, lavorate o sabbiate per ottenere la geometria e la finitura superficiale finali.
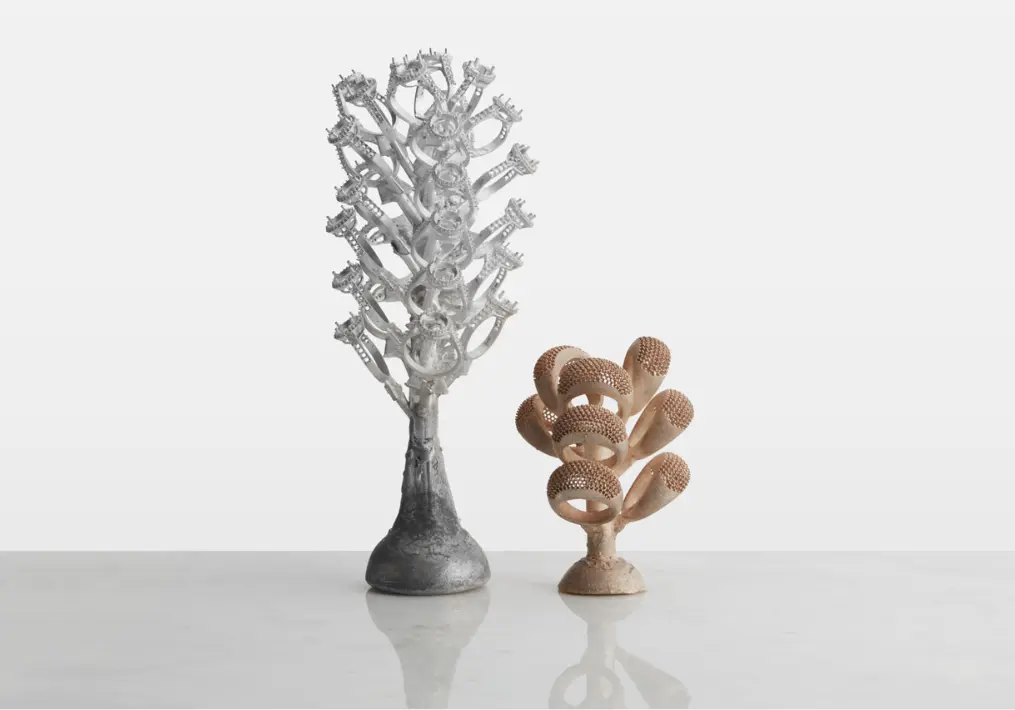
Alberi di fusione con anelli colati.
Clear Cast Resin, Castable Wax Resin, Castable Wax 40 Resin e True Cast Resin possono essere utilizzate tutte per stampare in 3D parti per la fusione a cera persa. La scelta del materiale dipende dalle caratteristiche della singola parte. La Castable Wax Resin è adatta ad articoli di gioielleria di peso medio e ridotto, la True Cast Resin ad articoli di gioielleria di medio peso e componenti ingegneristici con spessore massimo di 5 mm e la Clear Cast Resin a parti di spessore superiore a 3 mm.
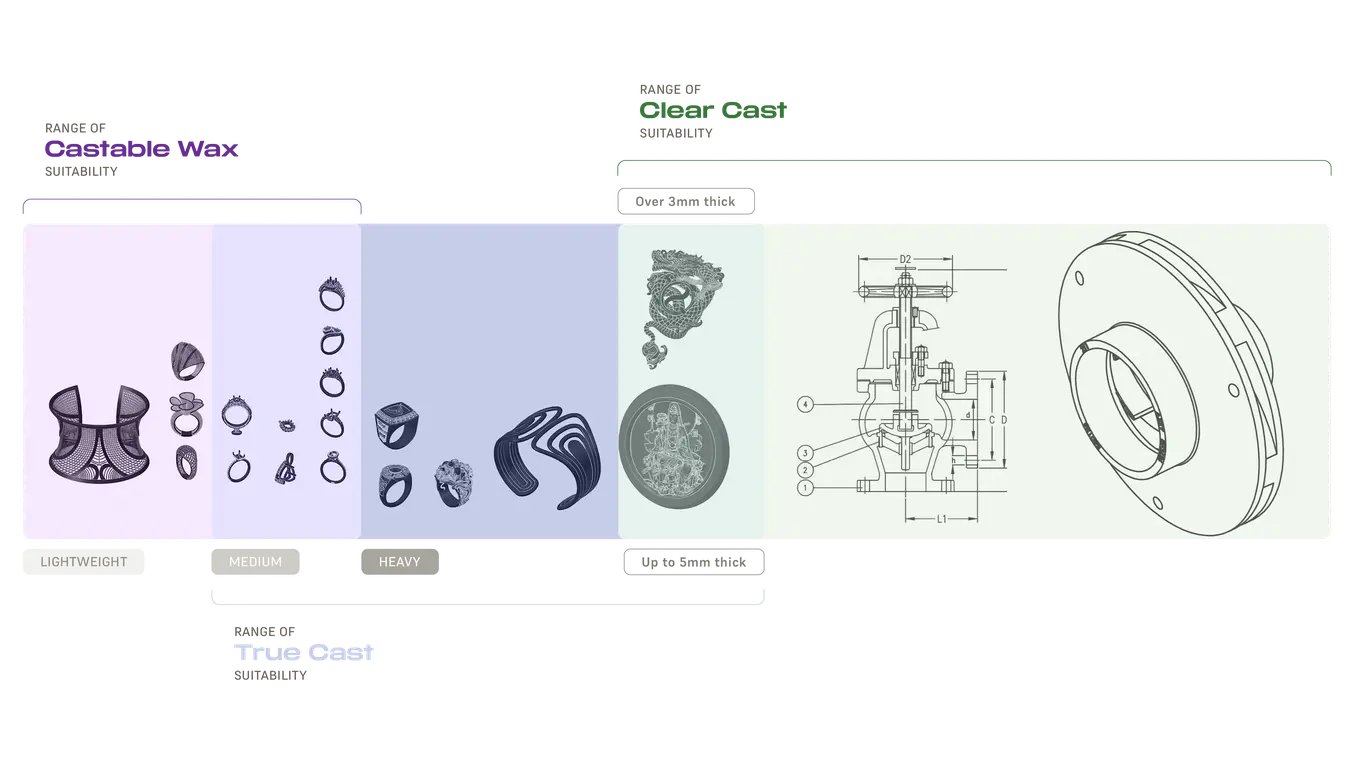
Vantaggi della fusione a cera persa
La fusione a cera persa è un procedimento versatile. Consente alle aziende produttrici di realizzare parti accurate e ripetibili con quasi tutti i metalli disponibili per la fusione, nonché di ottenere forme complesse che sarebbero difficili o impossibili da realizzare con altri metodi di fusione. Le parti fuse presentano inoltre una finitura superficiale eccellente e basse tolleranze, e per questo richiedono solo interventi minimi di rifinitura o lavorazione meccanica.
Queste caratteristiche fanno della fusione a cera persa la tecnica ideale per realizzare parti complesse per i settori automobilistico, aerospaziale, industriale, degli strumenti medici, degli impianti odontoiatrici, nonché della gioielleria e dell'arte.
Svantaggi della fusione a cera persa
La fusione a cera persa è un processo complesso e laborioso. Richiede attrezzatura specializzata, materiali refrattari e leganti costosi. Inoltre molte delle operazioni per creare uno stampo sono manuali. La fusione di parti che richiedono un nucleo può risultare difficile, perciò il processo è più indicato per le parti piccole.
Fusione in sabbia
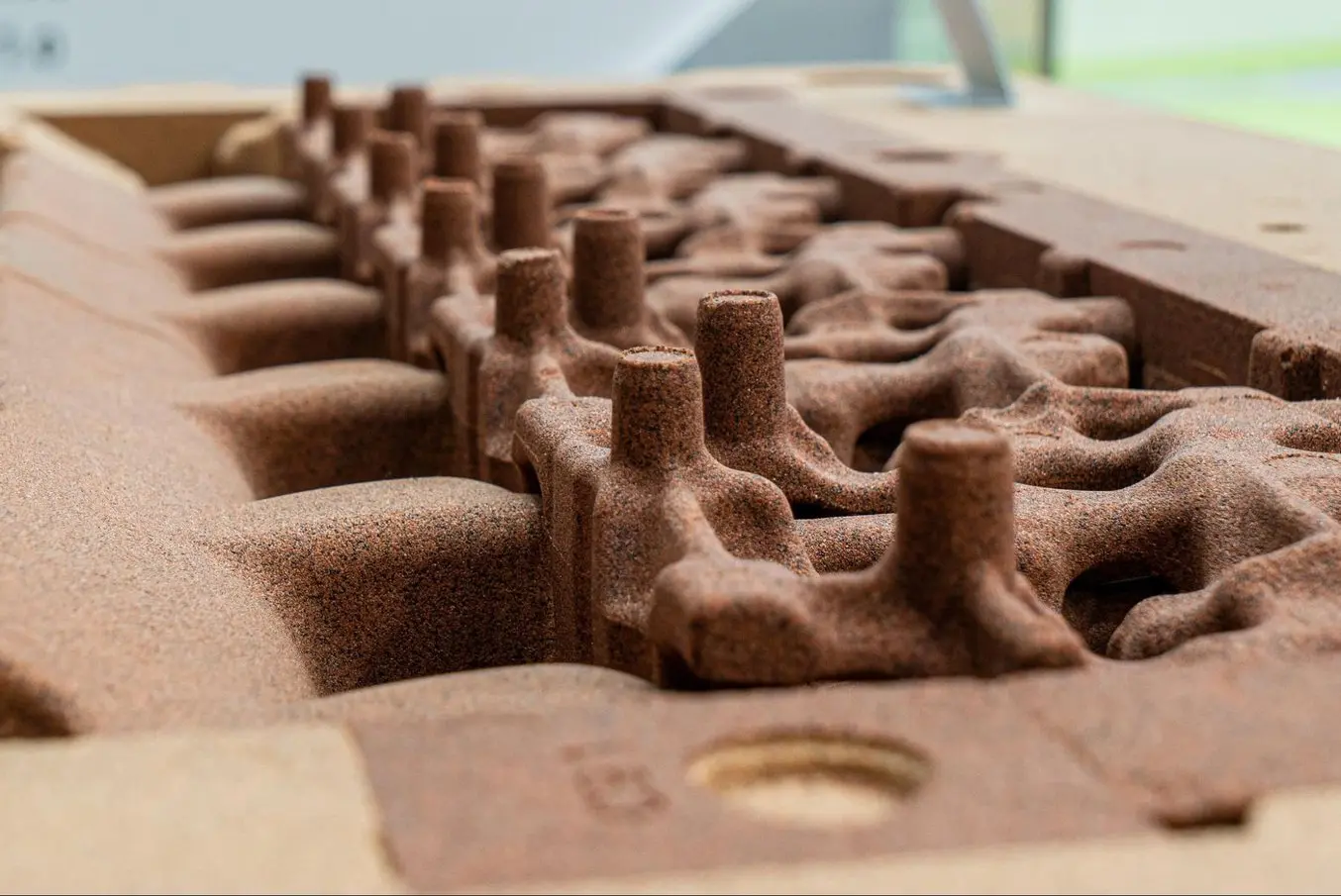
Una metà di uno stampo per la fusione in sabbia.
La fusione in sabbia è un metodo di fusione del metallo utilizzato per la prima volta 3000 anni fa, ma che rimane ancora oggi il procedimento più usato. Questo metodo permette di fondere il metallo senza affidarsi alla lavorazione meccanica.
Il primo passaggio del procedimento di fusione in sabbia è la creazione di un modello da fonderia, ovvero una replica della colata, in genere realizzata in legno o plastica. Il modello è sovradimensionato per tenere conto del restringimento. Le parti che presentano caratteristiche su un solo lato richiedono uno stampo aperto. Per le parti con dettagli su diverse superfici, il modello da fonderia viene diviso in due stampi per formare uno stampo a cavità chiusa. La metà superiore viene chiamata "cope" e quella inferiore "drag".
A questo punto si compatta la sabbia attorno al modello e si aggiungono canali di colata e aperture per permettere al metallo fuso di fluire in modo uniforme attraverso la cavità dello stampo. Quindi si rimuove il modello e si serrano le due metà dello stampo in sabbia. Il metallo fuso viene poi versato nello stampo e lasciato a raffreddare. A questo punto, il modello in sabbia viene rimosso tramite vibrazioni o con acqua ad alta pressione. Infine, la parte in metallo viene prima rifinita, rimuovendo canali di colata e aperture, e poi lucidata.
Vantaggi della fusione in sabbia
La fusione in sabbia è un procedimento adattabile che funziona indipendentemente dai limiti dei macchinari. Proprio per questo è in grado di creare parti complesse praticamente di qualsiasi dimensione. La sabbia è facilmente reperibile ed economica, quindi i costi di implementazione sono ridotti ed è possibile apportare modifiche. È l'unico modo pratico ed economico per produrre parti fuse di dimensioni molto grandi. Anche i tempi di realizzazione della fusione in sabbia sono brevi, il che lo rende un processo adatto a cicli di produzione brevi.
La versatilità fa della fusione in sabbia un'opzione di produzione adatta a una vasta gamma di settori. Può essere utilizzata per produrre attrezzature mediche, parti automobilistiche, apparecchi elettronici, serbatoi per il gas, blocchi motore e molto altro.
Svantaggi della fusione in sabbia
La fusione in sabbia crea metalli molto porosi e ruvidi. Il restringimento e la finitura superficiale grezza riducono l'accuratezza dimensionale delle parti. Questo si traduce in un prodotto finale a bassa resistenza, che richiede lunghi interventi di post-elaborazione per ottenere una finitura superficiale di qualità superiore.
Come selezionare il giusto procedimento di fusione del metallo
Per scegliere il procedimento industriale di fusione del metallo più adatto vanno presi in considerazione diversi fattori. Abbiamo creato questa tabella per aiutarti a confrontare la pressofusione, la fusione a cera persa e la fusione in sabbia in termini di tipi di materiali, volumi di produzione, costi, tempi di realizzazione, complessità delle parti e settori nei quali vengono utilizzati maggiormente.
Colata a pressione | Fusione a cera persa | Fusione in sabbia | |
---|---|---|---|
Metalli compatibili | Alluminio, rame, piombo, magnesio, zinco | La maggior parte dei metalli | La maggior parte dei metalli |
Volume di produzione | Grandi volumi | Da piccoli a grandi volumi | Da singoli pezzi a volumi medi |
Costo per parte | Basso | Da moderato a elevato | Moderato |
Costo delle attrezzature | Alto | Moderato | Basso |
Tempo di ciclo | Breve | Lungo | Moderato |
Settori | Automobilistico, aerospaziale, prodotti di consumo, arredamento, utensili elettrici | Automobilistico, aerospaziale, gioielleria, medicina, odontoiatria, arte | Automobilistico, aerospaziale, attrezzature industriali, elettronica, prodotti di consumo |
Fusione del metallo con la stampa 3D
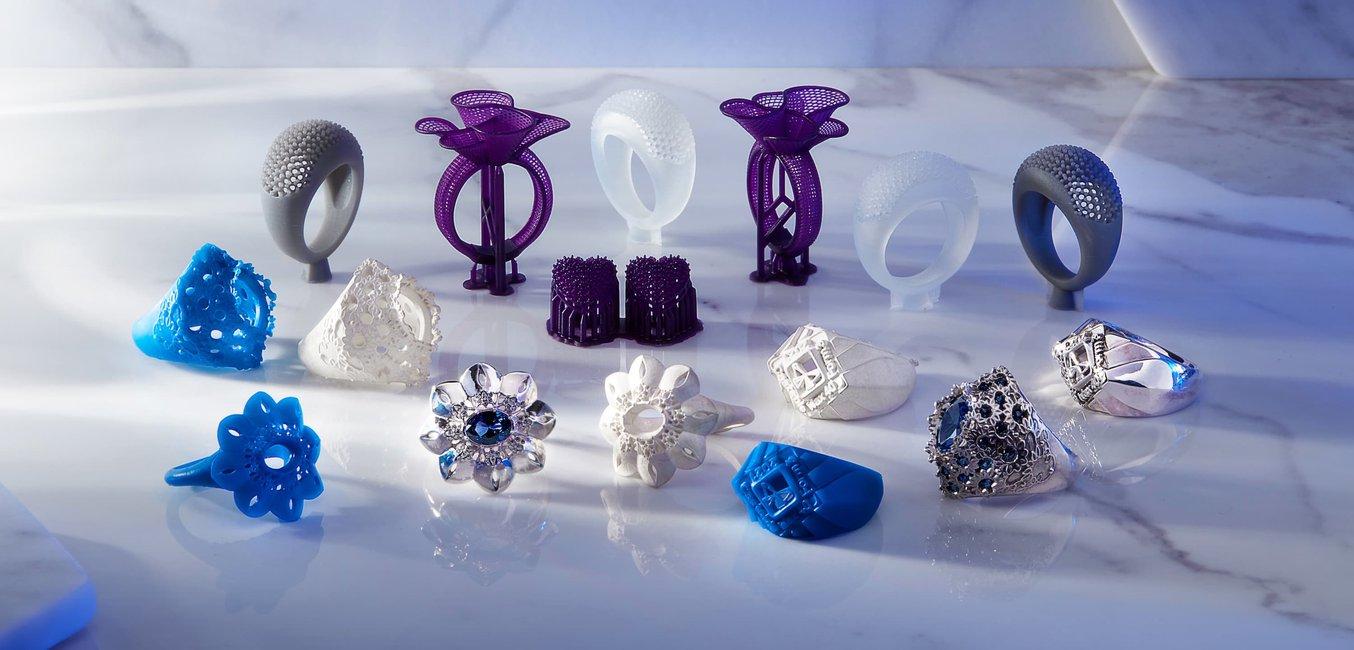
Modelli di gioielli stampati in 3D e anelli metallici fusi.
I team di ingegneria, progettazione e produzione di gioielli, così come gli utenti amatoriali, possono sfruttare la velocità e la flessibilità della stampa 3D per combinare i processi di fusione con modelli stampati in 3D per la fusione indiretta a cera persa, la fusione diretta a cera persa, la fusione in peltro e la fusione in sabbia. In alternativa, possono colare il metallo fuso direttamente in stampi realizzati in 3D. Le parti in metallo fuso realizzate utilizzando attrezzature create rapidamente mediante la stampa 3D hanno tempi di realizzazione molto inferiori rispetto alla fusione tradizionale e un costo significativamente ridotto rispetto alla stampa 3D in metallo.
Le stampanti 3D stereolitografiche (SLA) offrono alta precisione e un ampio catalogo di materiali adatti ai workflow di fusione. Inoltre, permettono di produrre parti in metallo a un costo inferiore, con una maggiore libertà di design e in tempi più brevi rispetto ai metodi tradizionali.
Fusione indiretta a cera persa
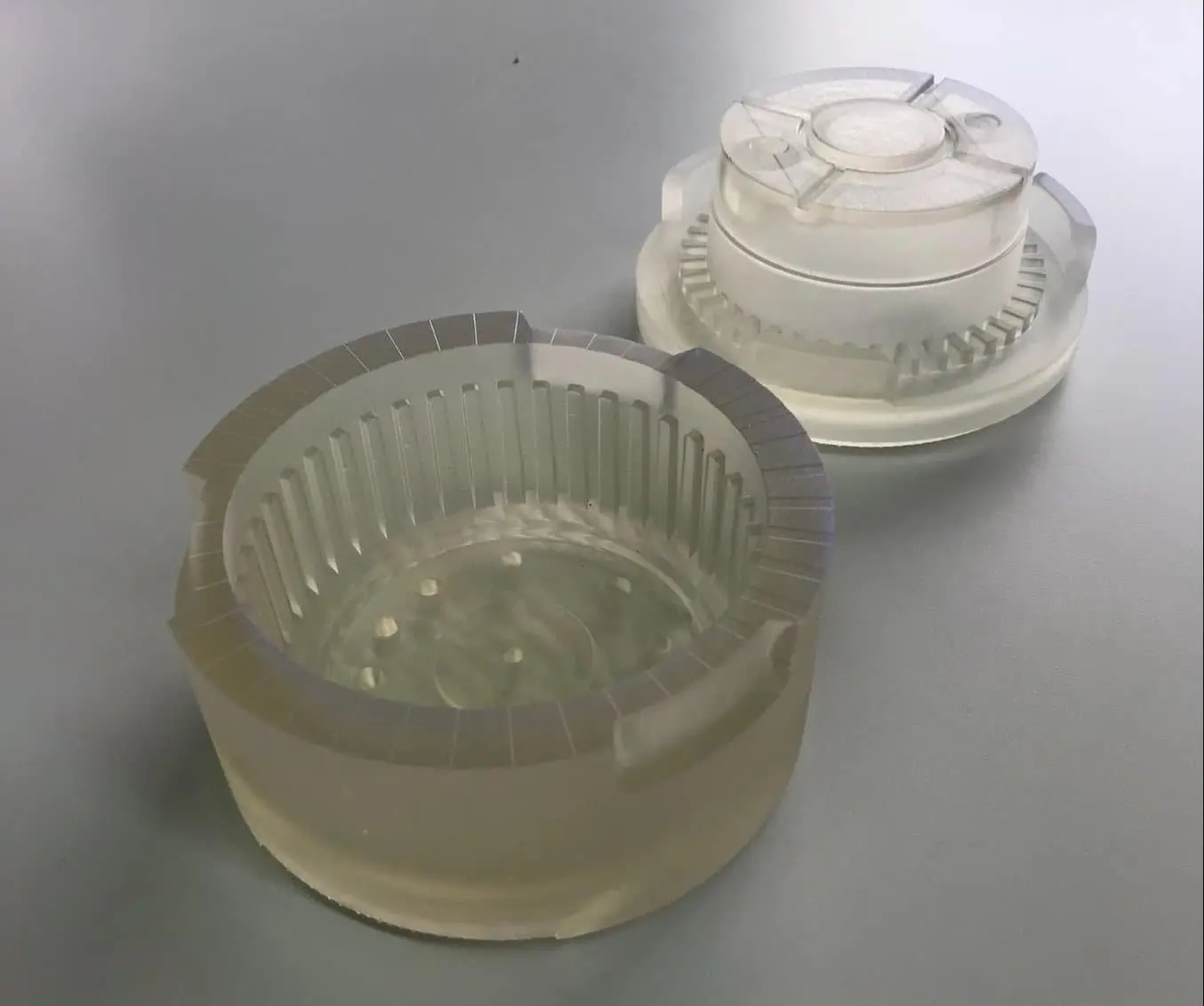
Stampo per iniezione di cera stampato in 3D con la Clear Resin.
Il processo di creazione di modelli mediante stampi o attrezzature viene chiamato fusione indiretta a cera persa, in quanto, oltre agli stampi di fusione finali, richiede la creazione di un'altra serie di stampi per produrre i modelli.
Gli stampi rigidi per la cera normalmente vengono prodotti mediante la lavorazione meccanica di alluminio o acciaio. La produzione di questi stampi in metallo costa migliaia di euro e richiede settimane di lavorazione meccanica e rifinitura prima che gli stampi possano essere usati e prima che si possano valutare le parti modello realizzando un procedimento di fusione.
Con la stampa 3D, le aziende produttrici possono stampare direttamente lo stampo del loro modello usando materiali come la High Temp Resin o la Rigid 10K Resin, che resistono alle alte temperature. Per una finitura superficiale ottimale, si consiglia di levigare e lucidare le superfici interne se si ha bisogno di uno stampo liscio, o di sabbiarle per renderle uniformemente opache. Per assicurarsi che le parti fuse finali siano delle dimensioni corrette, si consiglia di creare uno stampo leggermente più grande per compensare il restringimento. Le percentuali di restringimento della cera durante il procedimento di fusione si possono trovare nelle specifiche del fornitore.
Con gli stampi 3D per la fusione del metallo, il tempo che passa tra l'idea e i primi test si riduce a pochi giorni, perché le aziende produttrici possono stampare direttamente le attrezzature necessarie per la produzione e la valutazione delle parti.
Anche se le parti ottenute da stampi devono seguire specifiche regole di progettazione per lo stampaggio (evitare sottosquadri, introduzione di angoli di sformo, ecc.), si possono ottenere modelli più complessi usando dime di assemblaggio per combinare diversi componenti in un'unica struttura.
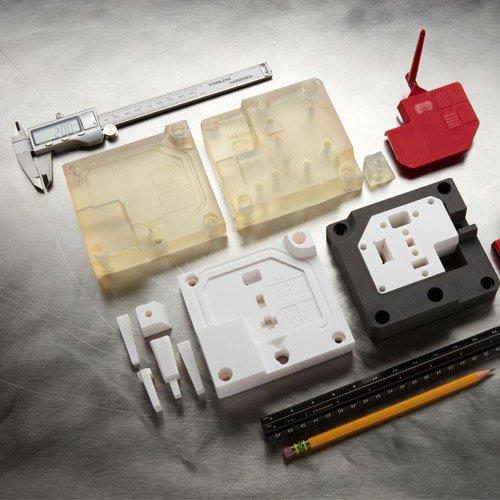
Realizzazione di stampi con la stampa 3D: tecniche di prototipazione e produzione
Scarica il nostro whitepaper per scoprire sei processi di stampaggio che si possono seguire con una stampante 3D SLA in-house, tra cui lo stampaggio a iniezione, la formatura sottovuoto, lo stampaggio in silicone e tanti altri.
Fusione diretta a cera persa
Il procedimento di fusione diretta a cera persa è una versione del processo di fusione a cera persa nel quale si passa direttamente dalla creazione di un modello alla copertura del modello stesso con un materiale di rivestimento. È ideale per la produzione di parti le cui geometrie sono troppo complesse da realizzare con uno stampo, nonché di parti con ampi sottosquadri e dettagli superficiali di piccole dimensioni, per cui lo stampaggio sarebbe possibile, ma richiederebbe investimenti considerevoli per le attrezzature.
Tradizionalmente, quando si producono solo poche unità, i modelli per la fusione diretta a cera persa vengono intagliati a mano o realizzati tramite lavorazione meccanica. Tuttavia, grazie alla stampa 3D, è possibile stampare direttamente i modelli, eliminando i limiti di progettazione e di tempo comuni agli altri processi.
Con le stampanti 3D, i team di ingegneria, design e produzione di gioielli possono stampare direttamente i modelli in 3D per ridurre i tempi di produzione e avere la libertà di creare geometrie che vanno oltre i limiti di design per la fabbricazione imposti dai processi di stampaggio. Formlabs ha sviluppato una serie di materiali per la stampa 3D adatti alla fusione diretta a cera persa, indicati in particolare per la fusione a cera persa industriale e la fusione per la gioielleria.
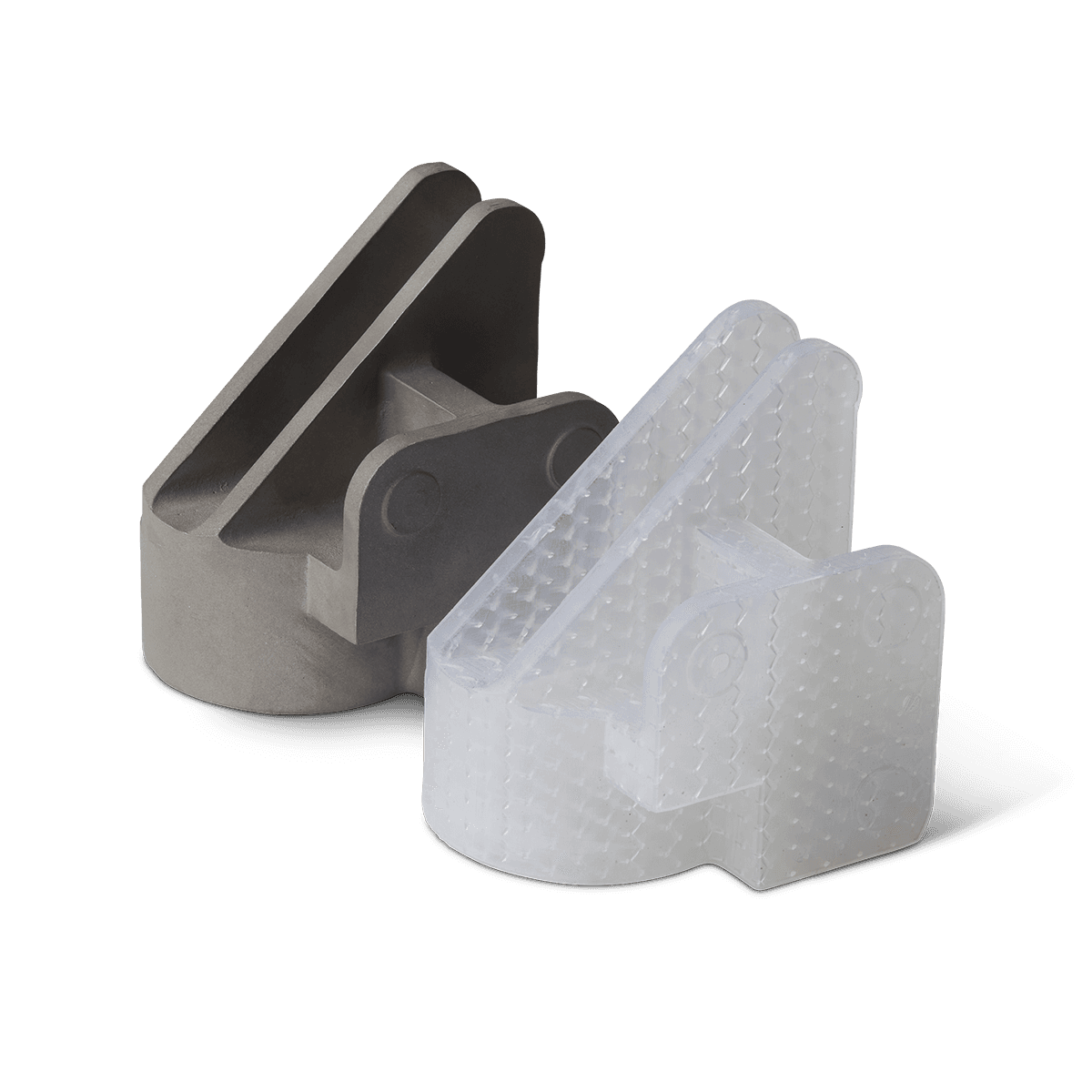
Fusione a cera persa industriale con modelli stampati in 3D usando la Clear Cast Resin di Formlabs
Questo whitepaper presenta i metodi che hanno permesso a diverse fonderie leader di eseguire la fusione di parti in metallo utilizzando modelli stampati in 3D su stampanti stereolitografiche (SLA) di Formlabs.
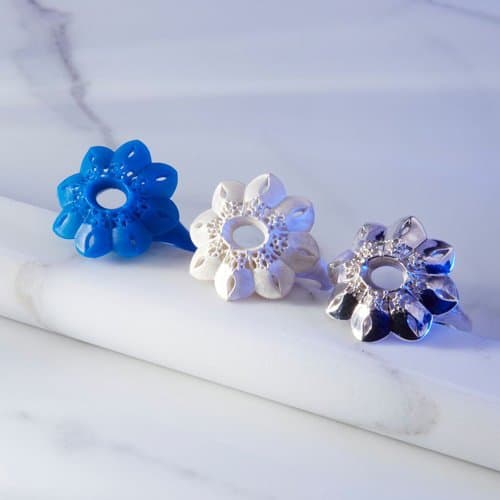
Introduzione alla fusione per modelli di gioielli stampati in 3D
I metodi di lavorazione nell'ambito della gioielleria stanno cambiando e le resine fotopolimeriche calcinabili rappresentano l'ultima avanguardia. In questa guida imparerai come realizzare raffinati pezzi di gioielleria da modelli stampati in 3D con le stampanti Formlabs.
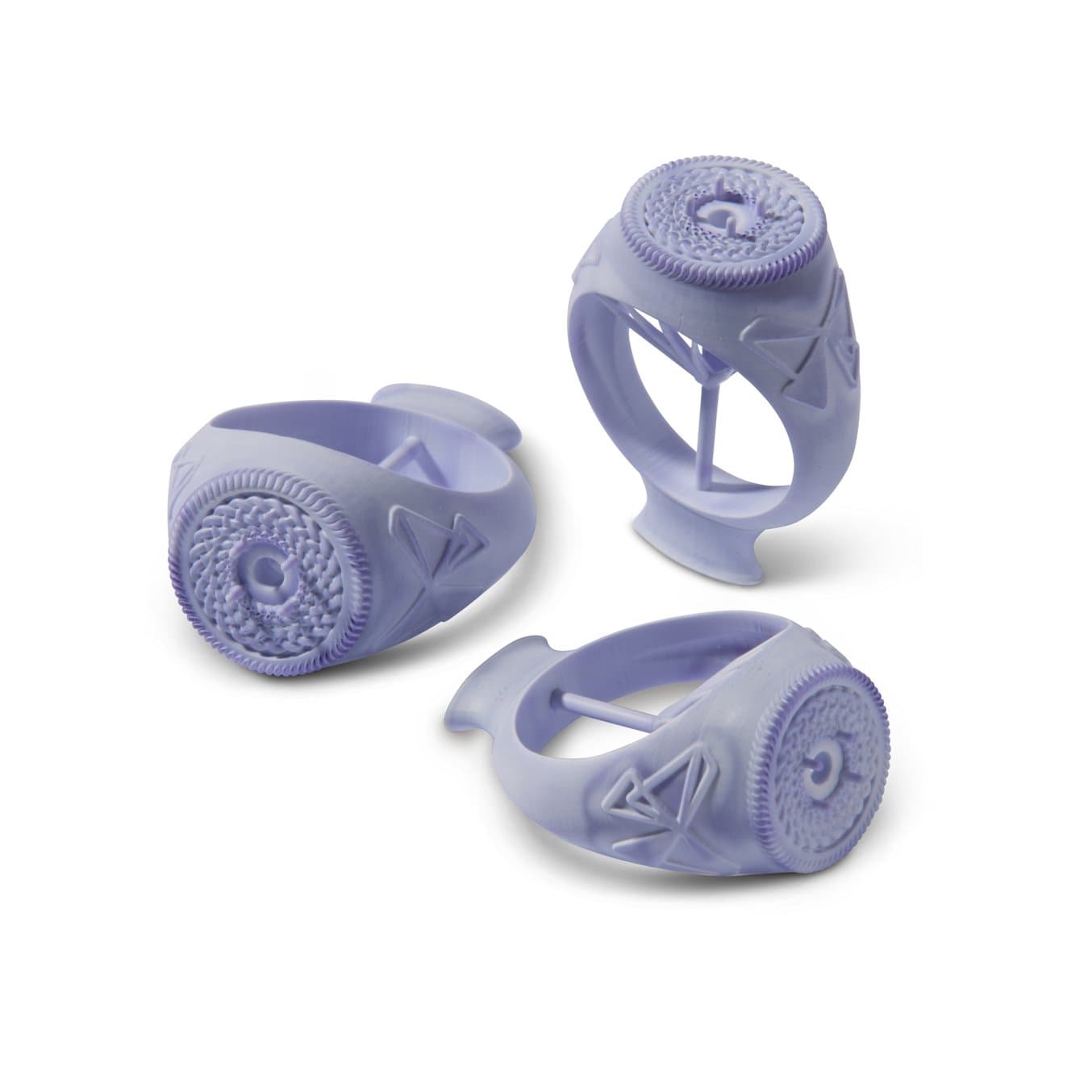
Richiedi un campione gratuito
Guarda e tocca con mano la qualità di Formlabs. Saremo lieti di inviare presso la tua azienda un campione gratuito.
Fusione in sabbia
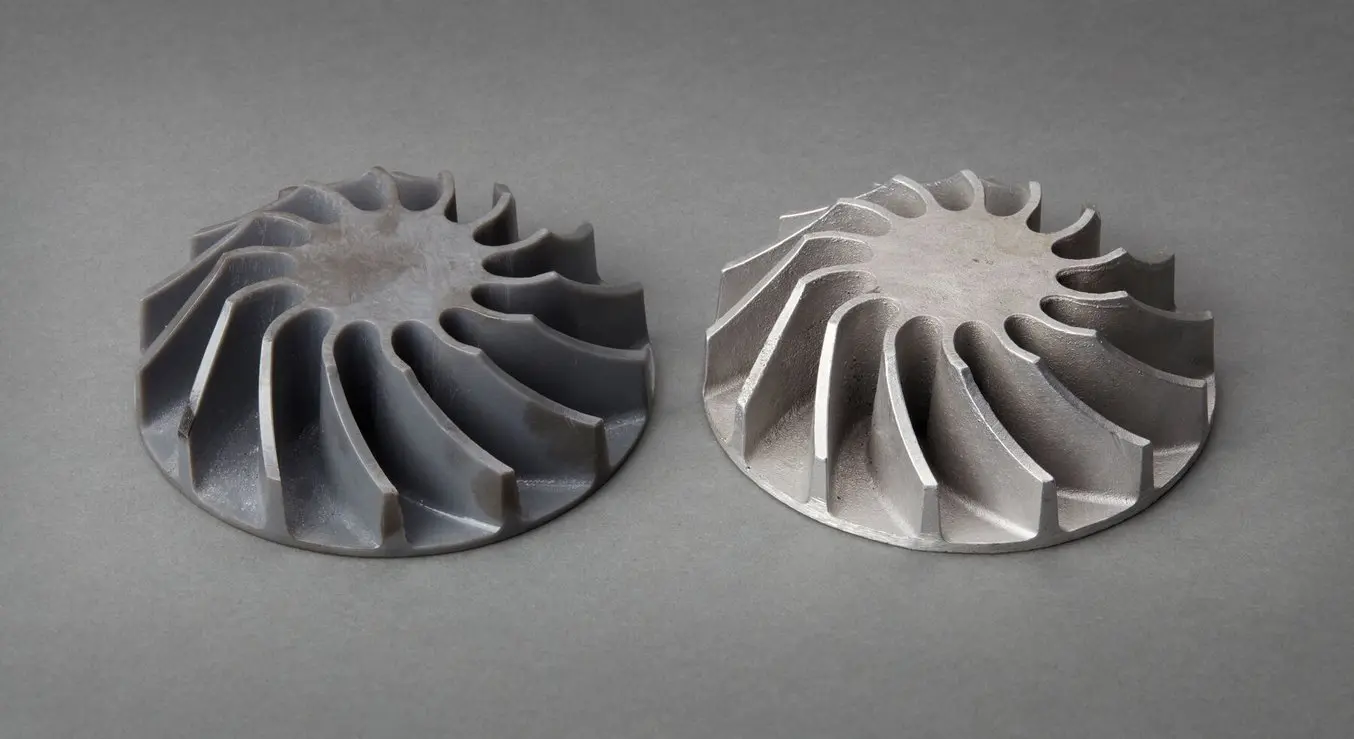
Modello stampato con la Grey Resin e fusione finale in alluminio creata con uno stampo in sabbia a una sola faccia.
Analogamente a quanto detto riguardo alla fusione a cera persa, la stampa 3D può essere usata per creare modelli per la fusione in sabbia.
Se paragonata ai materiali tradizionali come il legno, la stampa 3D permette di creare forme complesse e di passare direttamente dalla progettazione digitale alla colata.
Fusione in peltro
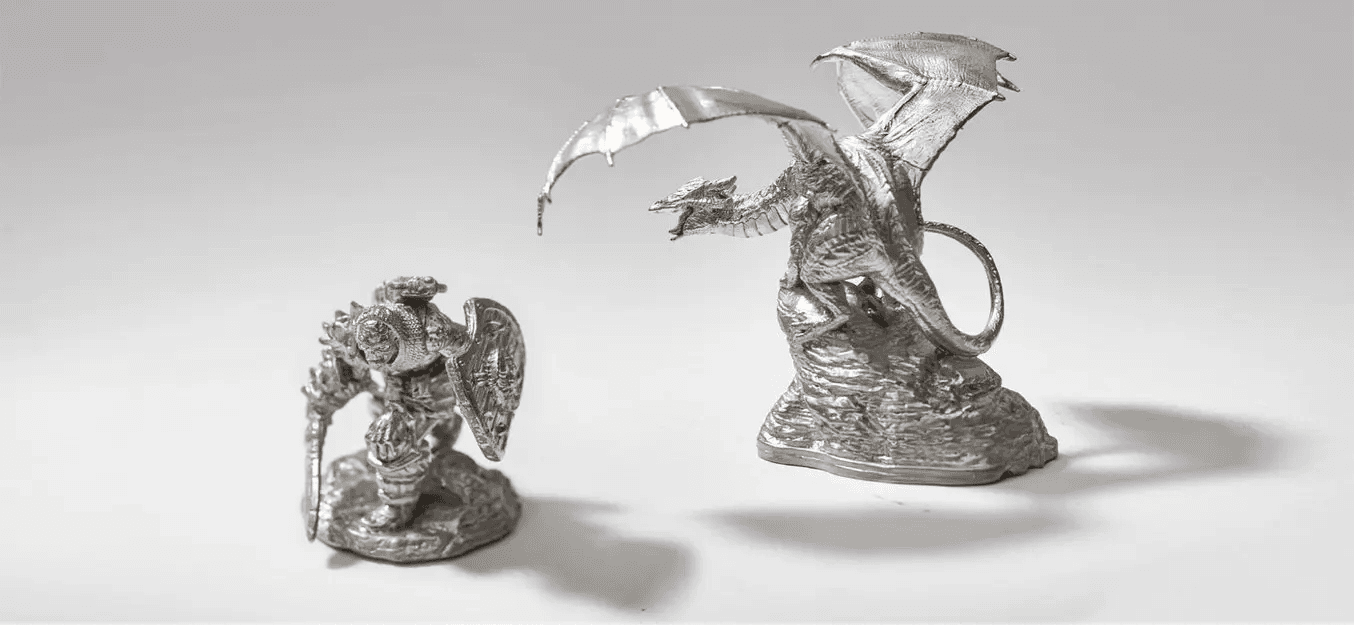
Modellini in metallo realizzati con fusione in peltro e stampa 3D.
Il peltro è una lega metallica malleabile con un punto di fusione basso che può essere usata per realizzare oggetti decorativi in metallo come miniature ricche di dettagli, gioielli, modelli in scala e repliche di oggetti antichi.
Grazie ai recenti sviluppi nel campo dei materiali per la stampa 3D resistenti alle temperature, come la High Temp Resin per le stampanti 3D SLA di Formlabs, è ora possibile realizzare stampi per la fusione diretta del peltro.
Ci sono due opzioni per progettare gli stampi: usa e getta o apribili. Gli stampi usa e getta hanno un guscio progettato per rompersi durante il procedimento. Invece gli stampi apribili sono composti da due metà e questo permette di riutilizzare lo stampo.
In confronto alla stampa diretta dei metalli, la fusione del peltro all'interno di stampi realizzati con la stampa 3D offre un grado di dettaglio e una finitura superficiale nettamente superiori a un costo decisamente inferiore. Rispetto alla fusione a cera, stampare direttamente uno stampo in 3D comporta meno passaggi e meno sforzi, conservando allo stesso tempo il maggior numero di dettagli possibile.
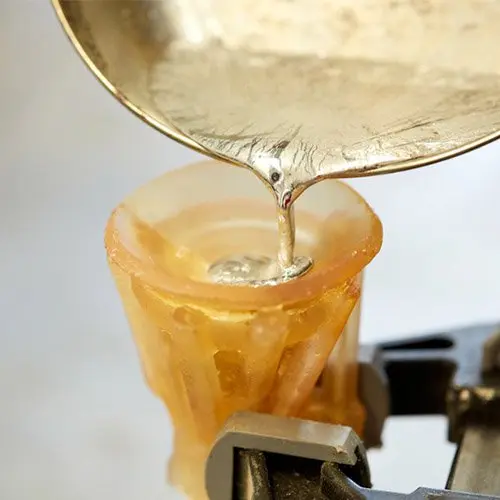
Metallo, ceramica e silicone: l'utilizzo di stampi realizzati in 3D nei flussi di lavoro ibridi avanzati
Guarda il nostro webinar per scoprire come gli stampi prodotti usando master ottenuti con la stampa 3D e gli stampi riutilizzabili o usa e getta possono aiutarti a fabbricare parti in porcellana, metalli preziosi e non, silicone, materiali flessibili biocompatibili e non solo.
Quando combinare la stampa 3D con la fusione del metallo
Le aziende che vogliono aumentare la propria libertà di progettazione o ridurre i costi e i tempi di realizzazione hanno a disposizione una soluzione perfetta: la fusione del metallo combinata alla stampa 3D.
Alcune tipologie complesse di fusione del metallo, come le forme di grandi dimensioni con sezioni trasversali o le parti con diversi nuclei, sono difficili da realizzare con i metodi tradizionali di fusione del metallo. La stampa 3D permette di produrre questi design complessi. Ad esempio, le fonderie o le aziende produttrici di gioielli possono creare design complessi e personalizzati che sarebbero impossibili da realizzare senza un modello stampato in 3D.
Inoltre, con la stampa 3D si possono creare le parti senza dover dipendere dai fornitori di servizi e senza bisogno di un gran numero di macchinari. Alle aziende basta avere un file digitale, una stampante 3D e il materiale per la stampa. Questo riduce i costi e gli sprechi, perché viene utilizzato solo il materiale necessario a creare il prodotto finale.
Infine, la combinazione di stampa 3D e fusione del metallo riduce i tempi e i costi di produzione. Invece di utilizzare apparecchiature costose e aspettare settimane per poter testare la colata del prodotto finale, con la stampante 3D si possono creare modelli e stampi in poche ore.
Diversified Metalsmiths, Inc. ha incorporato tecnologie moderne nel suo workflow di fusione dei metalli per ridurre i costi, migliorare i tempi di produzione e aumentare l'agilità. Utilizzando le stampanti 3D stereolitografiche (SLA) della serie Form e la Clear Cast Resin, Diversified ha potuto stampare modelli in-house in modo rapido ed economico, senza necessità di modificare il workflow di fusione o ricorrere all'esternalizzazione.
"Il motivo principale per cui abbiamo acquistato la Form 3L è il costo dei modelli. Anche ammortizzando la spesa per la stampante e l'attrezzatura associata, come minimo arriveremo a pareggiare i costi dell'ordine in corso, mentre sui prossimi prevediamo di risparmiare oltre 200 dollari per parte. Non ci sono grandi differenze tra i modelli in PMMA e quelli in Clear Cast Resin in termini di processo di produzione, né prima né dopo la fusione."
John Farr, vicepresidente del dipartimento di tecnologia, Diversified Metalsmiths
Stampante 3D per la fusione dei metalli
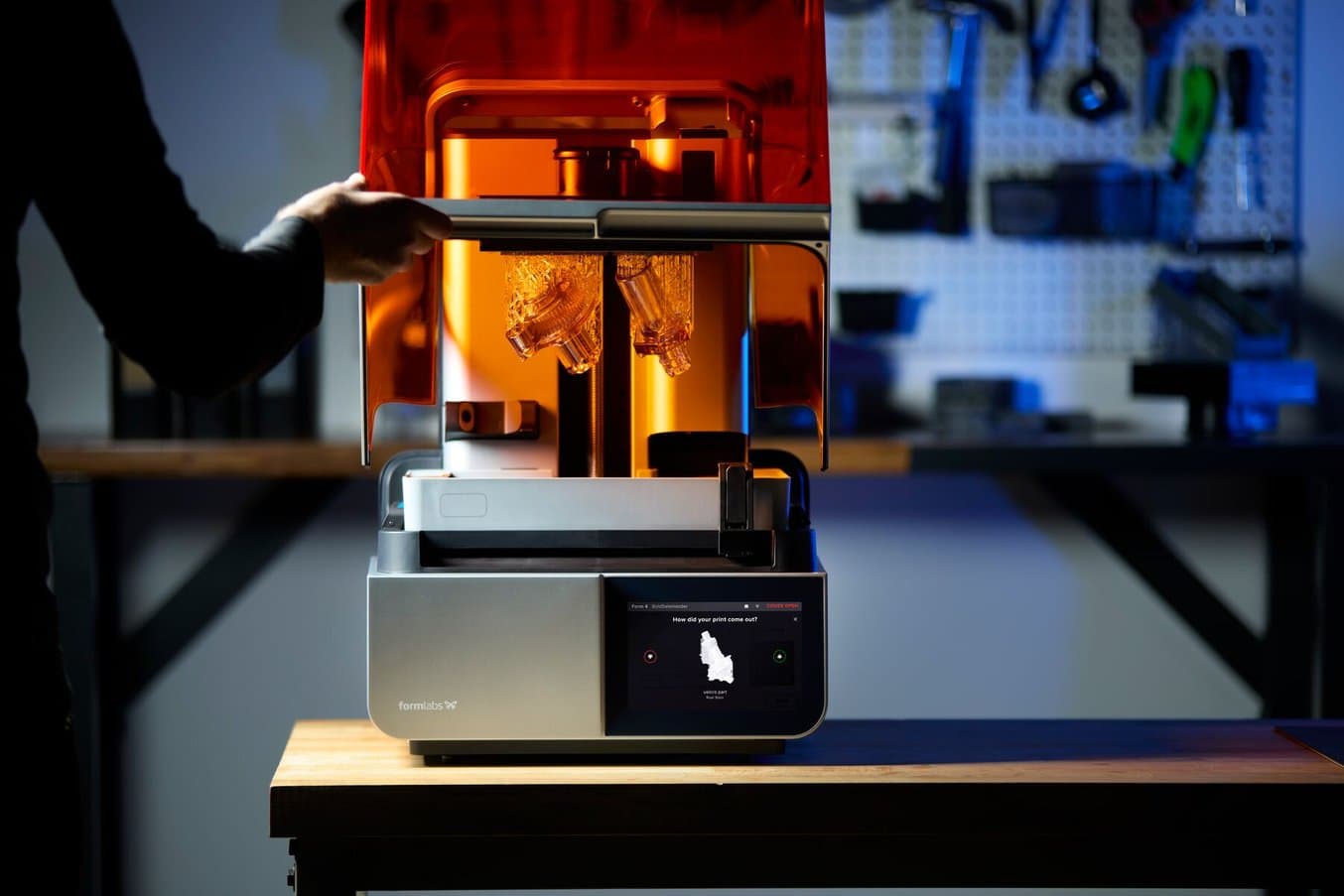
La fusione dei metalli combinata alla stampa 3D permette alle aziende di creare parti in metallo in modo rapido ed efficiente. Con una stampante 3D SLA Formlabs puoi velocizzare il processo di fusione dei metalli e ridurre i costi.
Scopri di più sulle stampanti 3D a resina di Formlabs oppure contatta i nostri esperti di stampa 3D in caso di domande.