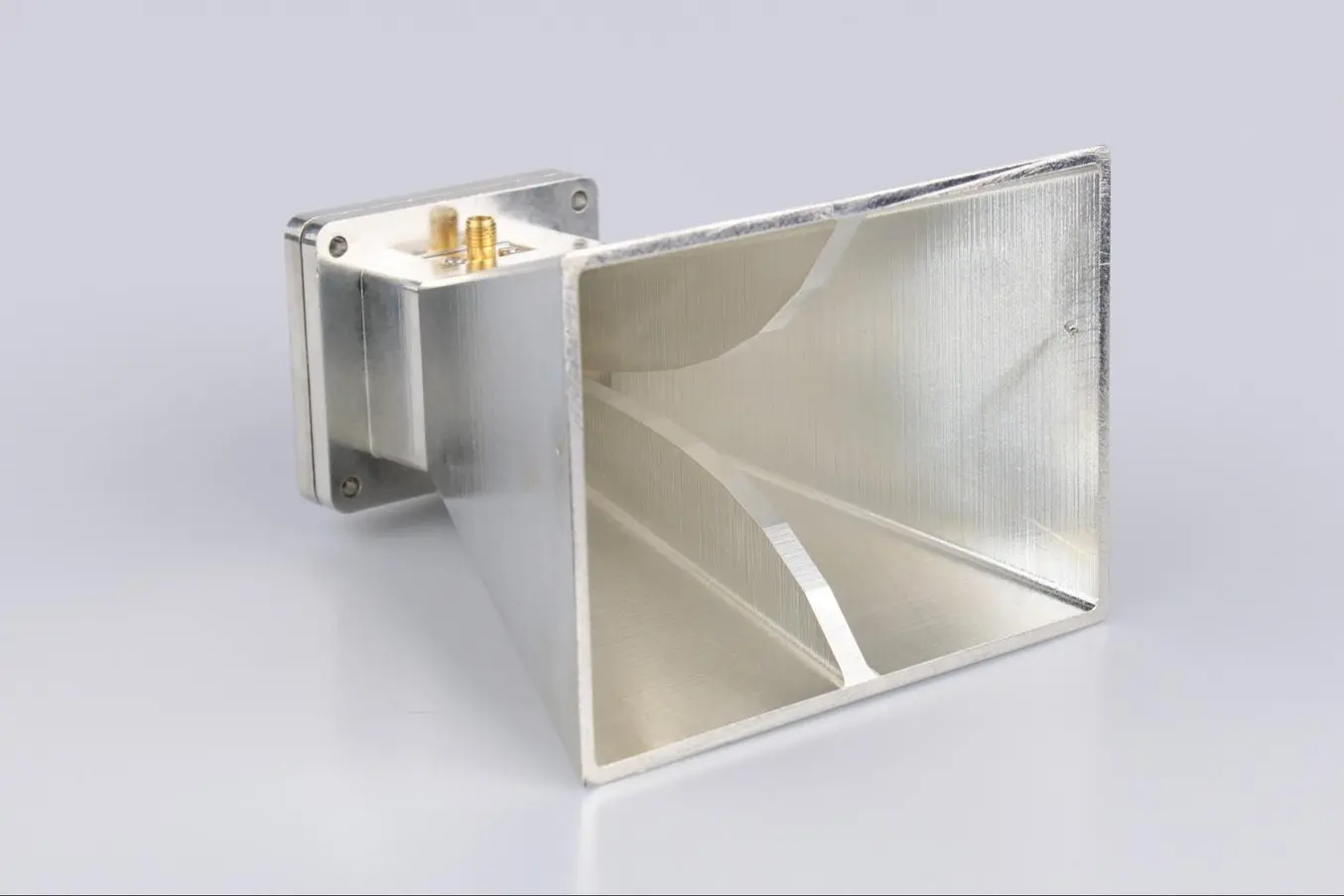
Elliptika è un'azienda specializzata nella progettazione e nello sviluppo di prodotti e soluzioni a radiofrequenze e microonde con sede a Brest, in Francia. Realizza filtri e antenne personalizzati all'avanguardia, che vengono usati nell'ambito di ricerca e sviluppo per il settore automobilistico, della difesa, medico e dell'istruzione da aziende come Thales.
Per assicurarsi che le antenne soddisfino stringenti requisiti come compattezza e prestazioni elevate, riducendo al minimo i costi e realizzando i progetti in breve tempo, l'azienda ha dovuto superare i limiti delle tecniche di produzione tradizionali.
Continua a leggere per scoprire come Gwendal Cochet e Alexandre Manchec, designer di radiofrequenze di Elliptika, utilizzano la stampa 3D e la galvanizzazione per realizzare antenne ad alte prestazioni, riducendo di oltre il 90% il tempo e i costi di produzione.
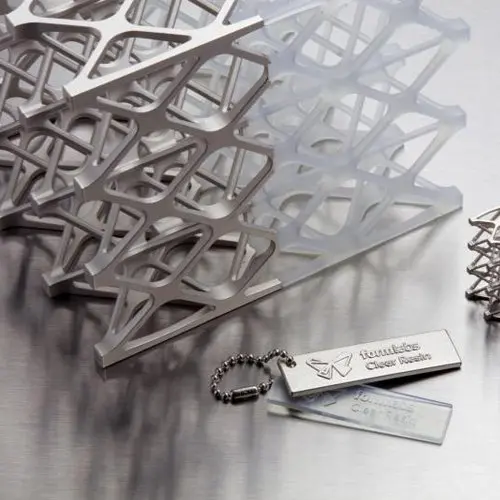
La tecnica più vicina alla stampa 3D di oggetti metallici con una stampante da 3500 $
Scopri in questo webinar come la galvanizzazione amplia le possibilità della stampa 3D a resina per realizzare parti per uso finale ad alta rigidità e resistenti all'usura. Se la stampa SLA consente la creazione di parti personalizzate complesse, la galvanizzazione trasforma le parti stampate in stereolitografia per ottenere proprietà simili a quelle dei metalli, come modulo elevato, conduttività elettrica e finiture estetiche.
Guarda il webinarCome funziona la galvanizzazione di parti stampate in 3D
Le antenne necessitano di un elevato grado di conduttività elettrica per propagare le onde radio. Anche se le parti stampate in 3D in plastica non conducono l'elettricità, offrono un’infinita libertà di design e materiali con buone proprietà termiche e meccaniche. Per raggiungere la conduttività desiderata, questi vantaggi possono essere coniugati grazie alla galvanizzazione, fornendo ottime soluzioni per la realizzazione di antenne personalizzate.
Dopo aver lavorato con diversi processi di produzione additiva, il team di Elliptika ha individuato nella stampa 3D stereolitografica (SLA) il metodo che meglio si adatta alla galvanizzazione.
"La superficie dei componenti a radiofrequenze deve essere liscia, per evitare perdite dovute alla ruvidità. Ad esempio, utilizzare una stampante a modellazione a deposizione fusa (FDM) con strati spessi è un problema. Oltre alle maggiori perdite, la ruvidità delle parti causa difficoltà durante il processo di galvanizzazione, impedendo al metallo di aderire in modo efficace. Con le parte stampata in stereolitografia non abbiamo problemi simili" spiega Cochet.
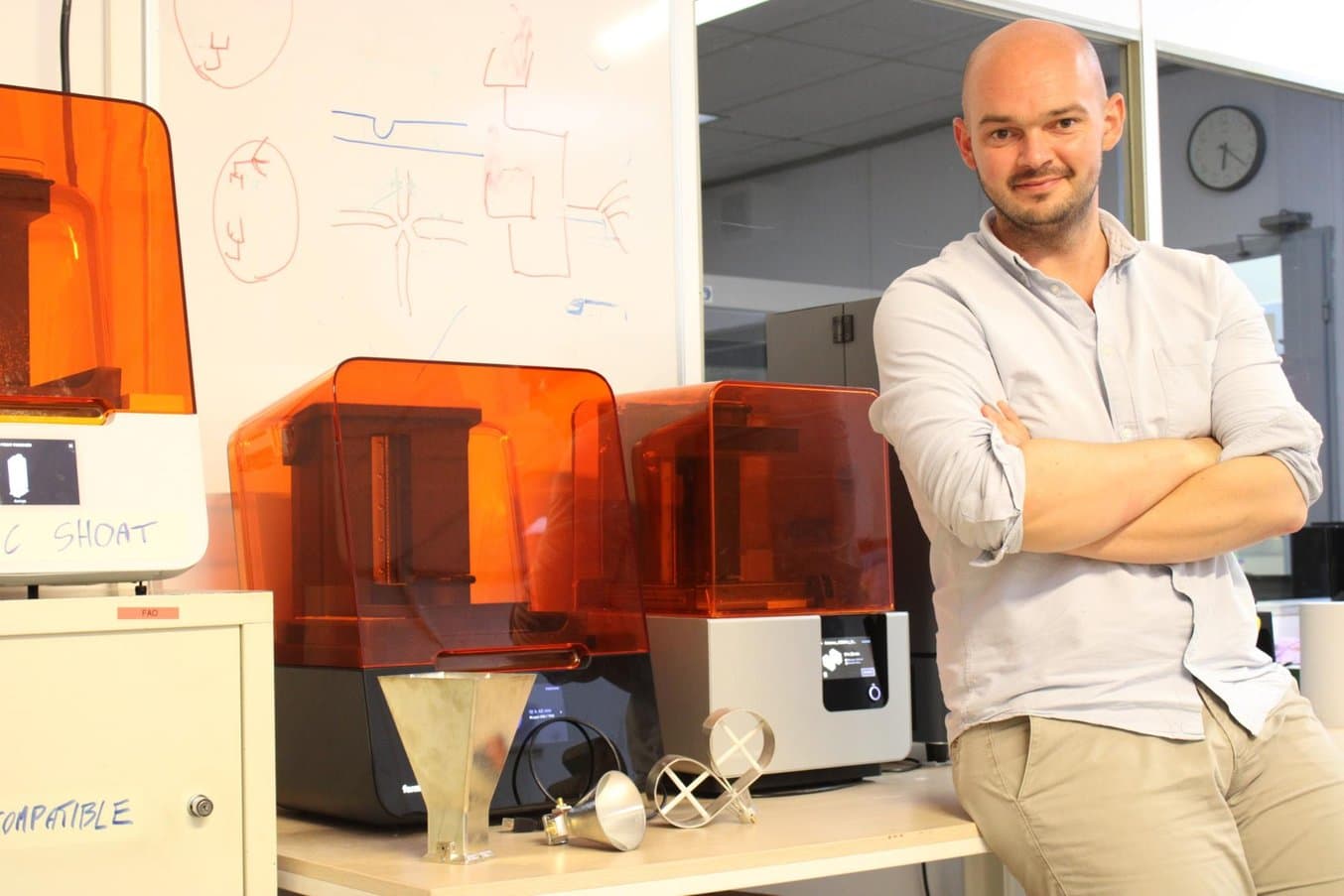
Inizialmente il team ha usato una stampante SLA Form 2, poi ha acquistato il modello successivo, la Form 3, e di recente ha aggiunto sette stampanti Form 3B per sostenere progetti legati alla pandemia di COVID-19. L'azienda si serve soprattutto della White Resin per realizzare parti per la galvanizzazione, ma per le parti meccaniche ha utilizzato sia la Tough Resin che la High Temp Resin.
Ecco come funziona il processo di galvanizzazione:
"In seguito alla stampa 3D della parte, è necessario rimuovere il supporto, pulirne la superficie e polimerizzarlo. Poi la parte stampata è sottoposta a un processo chimico per placcare un sottile strato di rame (3 µm circa). Infine, la parte può ricevere la finitura superficiale, ad esempio uno strato più spesso di stagno" spiega Cochet.
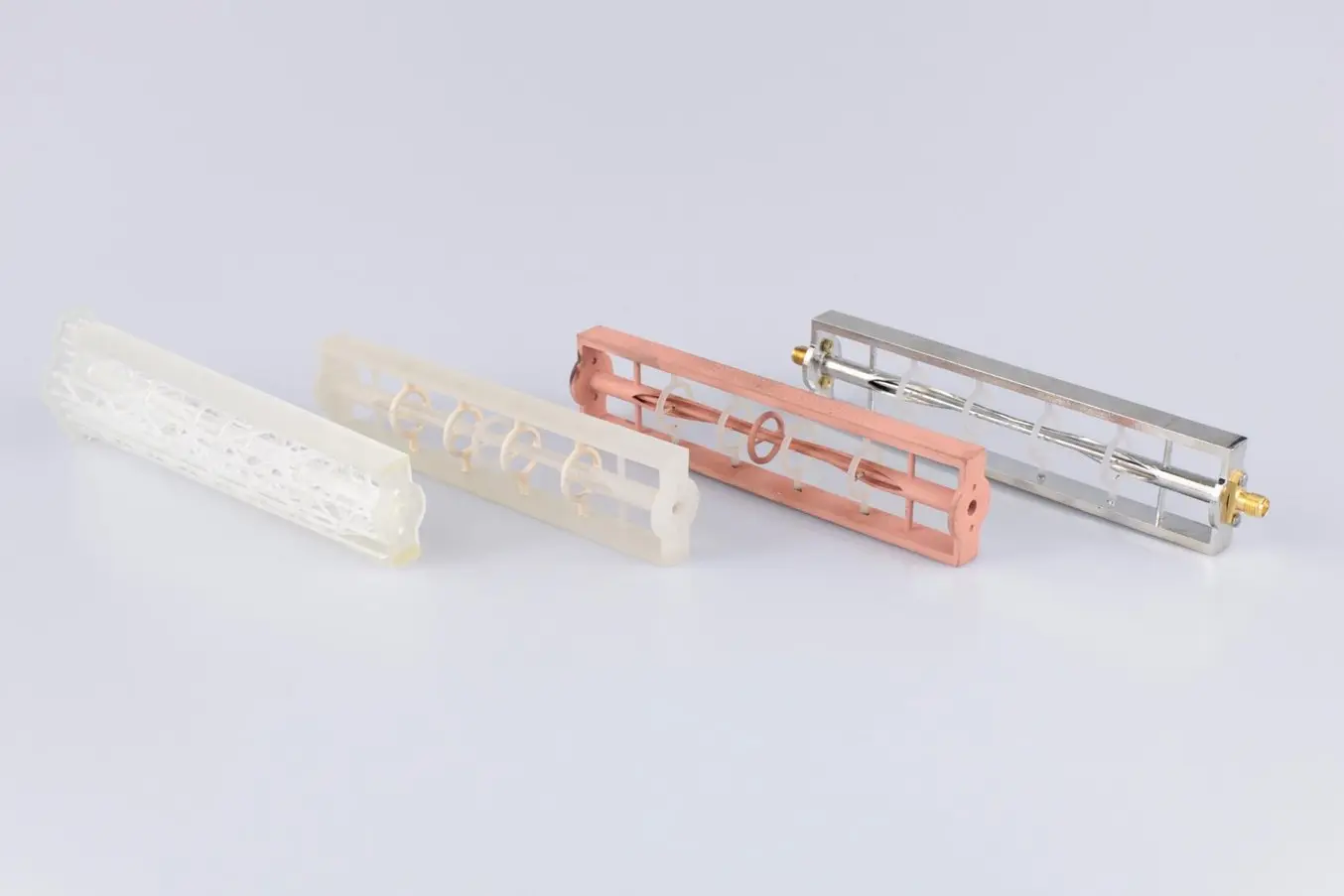
Le diverse fasi della galvanizzazione, da sinistra a destra: la parte stampata in 3D in plastica, una parte sottoposta a polimerizzazione post-stampa in seguito alla rimozione dei supporti, una parte galvanizzata con il rame e una parte finale galvanizzata con un rivestimento in stagno.
Ridurre di oltre il 90% il tempo e i costi di produzione
Poiché la maggior parte delle antenne viene utilizzata nell'ambito di ricerca e sviluppo, di solito Elliptika necessita soltanto di piccoli lotti di produzione, da una a 20 unità circa.
"La stampa 3D è molto interessante per noi, perché ci permette di produrre antenne complesse a un prezzo molto competitivo. Non vogliamo lavorare con altre soluzioni come la lavorazione meccanica o lo stampaggio a iniezione" afferma Alexandre.
Con i processi tradizionali, la produzione di un'antenna può richiedere fino a tre mesi, cioè il tempo necessario alla produzione di attrezzature e il continuo scambio di comunicazioni sui dettagli del design con il fornitore di servizi.
"Con la stampa 3D in-house, otteniamo parti funzionanti in due giorni. Un giorno per la stampa, uno per la placcatura, e sono pronte. Così è tutto molto più veloce. Anche il prezzo fa una gran differenza, perché fabbricare un’antenna costa circa 3000 €, se si esternalizza il lavoro. La stampa invece costa più o meno 20 €. Per noi il costo di realizzazione dell'antenna [tenendo conto anche del prezzo della stampante 3D] è ottimizzato in un solo progetto" afferma Cochet.
Produzione di un'antenna | Costo | Tempo di realizzazione |
---|---|---|
Stampa 3D SLA | 20€ | 2 giorni |
Esternalizzazione | 3,000€ | Fino a 3 mesi |
La personalizzazione e lo sviluppo rapido aprono nuove opportunità di mercato
La stampa 3D e la placcatura hanno aperto nuove opportunità di mercato, oltre a nuove possibilità per l'azienda.
"Prima della stampa 3D, producevamo solo antenne e filtri in PCB. Ora realizziamo anche parti volumiche. Era già possibile, ma non per un'azienda piccola come la nostra. Dobbiamo sviluppare nuove antenne rapidamente per i nostri clienti e, prima di introdurre la stampa 3D, il processo risultava troppo lungo e costoso" spiega Cochet.
"La personalizzazione per noi è molto semplice, così i nostri clienti possono avere un prototipo con specifiche particolari in breve tempo e a un prezzo conveniente. Inoltre, a volte hanno esigenze molto importanti per quanto riguarda il peso o il volume. In questi casi, possiamo costruire un'antenna in uno spazio molto ristretto, cosa che non era possibile nel caso di antenne ottenute tramite lavorazione meccanica. Quando si produce un'antenna con lavorazione meccanica, di solito è necessario creare varie parti da assemblare, componendo un oggetto molto più grande di una singola parte stampabile in 3D" afferma Cochet.
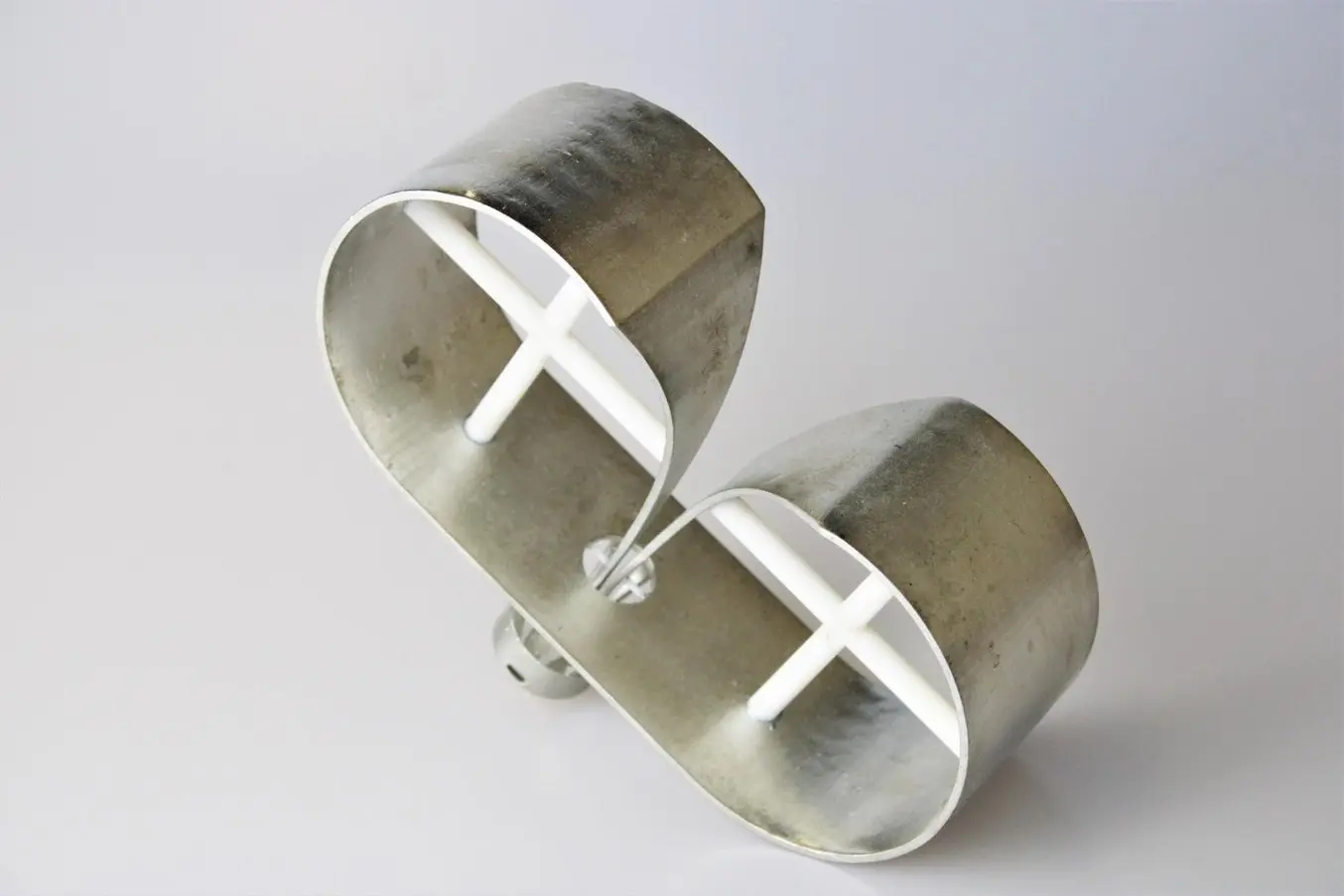
Un'antenna a cono TEM stampata in 3D e galvanizzata in modo selettivo, progettata da Julien Haumant, ingegnere del dipartimento di ricerca e sviluppo di Elliptika.
"Ad esempio, una delle nostre antenne è molto complessa, perché ha delle parti curve. Grazie alla stampa 3D, il dispositivo può essere fabbricato in un unico pezzo, che pesa solo 75 grammi. Per creare un dispositivo con queste proprietà tramite la lavorazione meccanica, sarebbero necessari molti pezzi diversi, e il peso sarebbe superiore, mentre le dimensioni sarebbero dieci o venti volte maggiori" aggiunge Cochet.
Scopri di più sulle applicazioni della galvanizzazione
Galvanizzare parti stampate in 3D ha molte applicazioni: Volkswagen e Autodesk hanno adottato queste tecnologie per produrre una serie spettacolare di coprimozzi per un veicolo dal concept futuristico, alcuni ricercatori in Svizzera hanno creato dispositivi sperimentali come beam splitter, mentre varie aziende placcano parti stampate in 3D per creare oggetti complessi con la resistenza del metallo a un prezzo conveniente.
Guarda il nostro webinar formativo gratuito con Sean Wise, presidente e fondatore di RePliForm, per scoprire come è riuscito, insieme al suo team, a sfruttare la galvanizzazione per ampliare lo spettro delle applicazioni della stampa 3D. Scoprirai anche la galvanizzazione e le sue applicazioni specifiche nella stampa 3D SLA, nonché i vari processi utili a realizzare una stampa 3D galvanizzata completa.