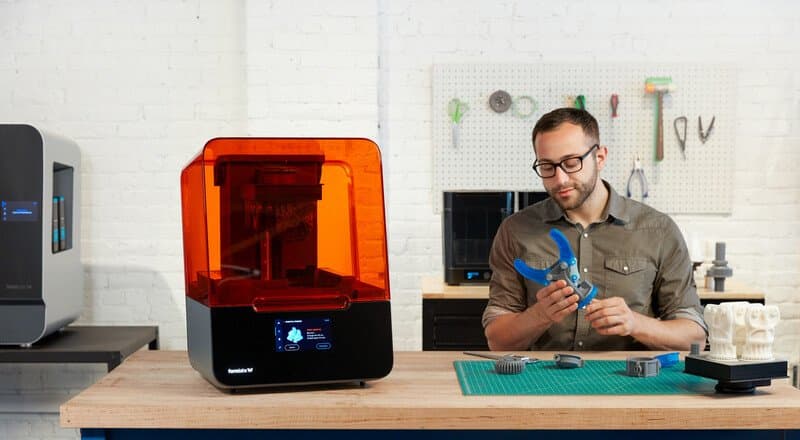
La Form 3, che utilizza la tecnologia Low Force Stereolithography (LFS), è stata lanciata quest'anno. E da allora è stata testata da critici, dai nostri ambasciatori Formlabs e da migliaia di utenti.
Per questo articolo abbiamo parlato con tre clienti che stanno usando molto la loro nuova Form 3. Continua a leggere per scoprire come se la cava la Form 3 con la prototipazione in-house e con le parti per uso finale spedite direttamente ai clienti.
Stampa e spedizione di parti per uso finale
Dan e Ruth Stewart sono i fondatori di Stewart Dollhouse Creations, un'azienda a conduzione familiare che si occupa della creazione di miniature. All'inizio le miniature venivano create con argilla polimerica, ma, con l'espansione dell'azienda, e dovendo affrontare problemi di adattamento della produzione alla domanda, la coppia è ricorsa alla stampa 3D. Negli anni la Stewart Dollhouse Creations ha acquistato ben quattro stampanti Form 2, prima di investire in una Form 3.
Stewart Dollhouse utilizza la fotogrammetria, una tecnica speciale che unisce diverse foto 2D in dati 3D per immortalare la geometria delle parti da stampare. Per ritoccare i dettagli più sottili utilizza invece software come Rhino o ZBrush. Una volta terminato il design, è il momento di mettere al lavoro la flotta di stampanti 3D Formlabs per produrre le parti finali. Dopo il lavaggio e la polimerizzazione le parti vengono impacchettate e spedite ai clienti, spesso senza neanche rimuovere i supporti. I supporti leggerissimi della Form 3 sono molto apprezzati dai clienti, perché rendono più facili le fasi di finitura e verniciatura.
Secondo Dan, l'aggiunta della Form 3 alla loro flotta di stampanti 3D è stata assolutamente indolore, visto che condivide piattaforma di stampa e cartucce di resina con la Form 2, un fattore che ha facilitato la transizione verso una flotta di stampanti miste.
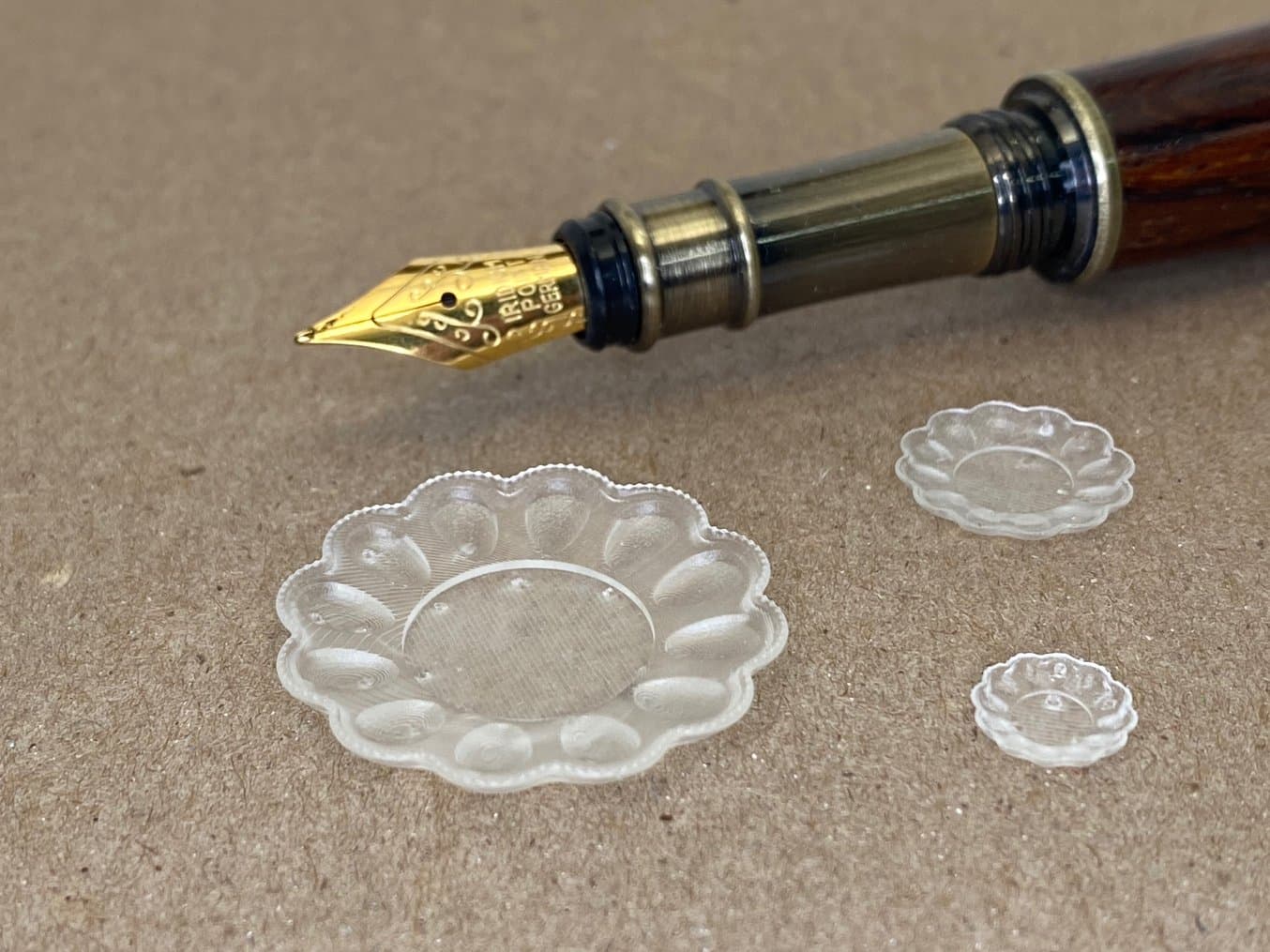
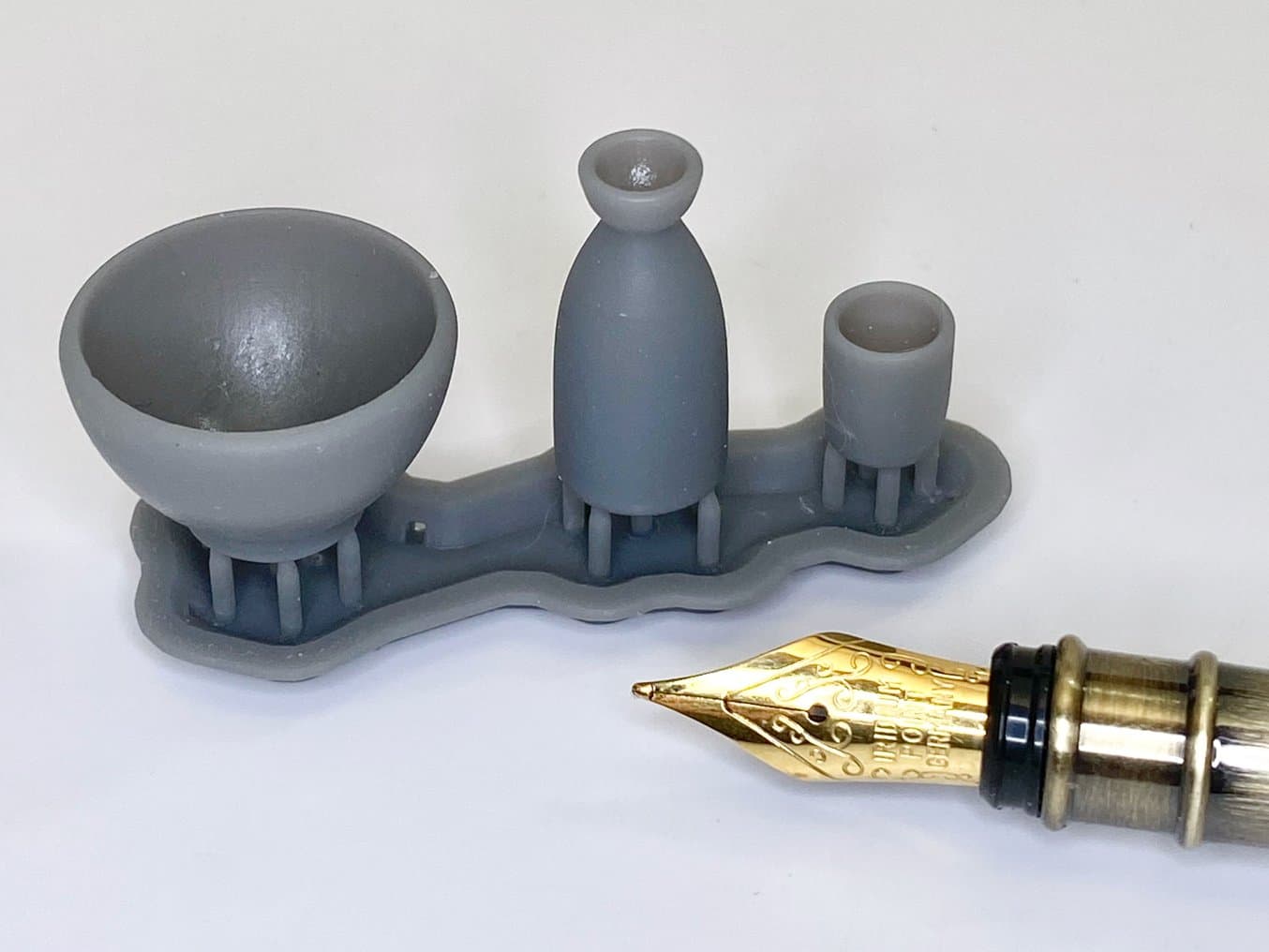
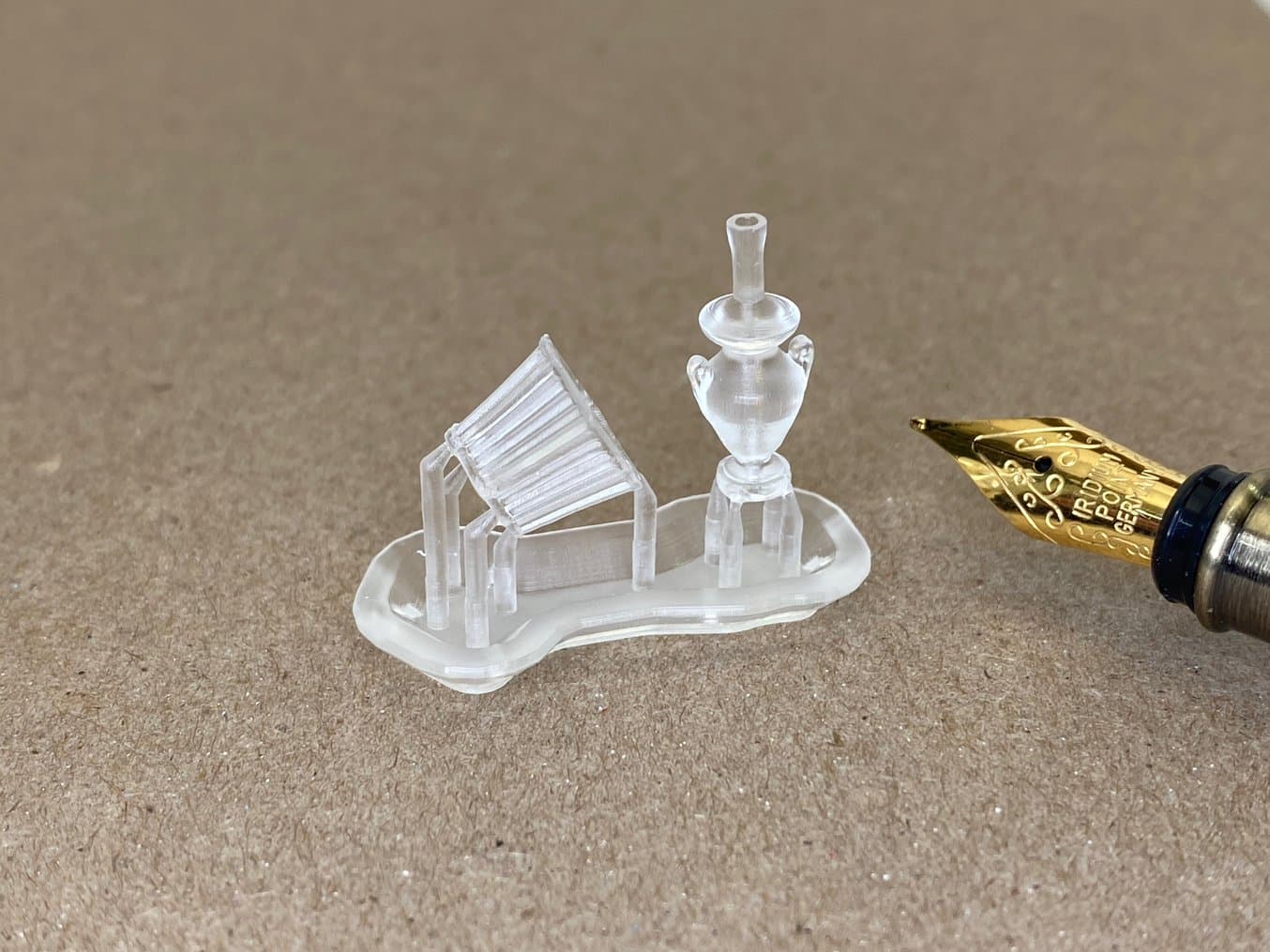
Prototipazione di dispositivi medici
Recentemente un'azienda di consulenza per il design di dispositivi medici dell'area di Minneapolis ha ampliato la sua flotta di stampanti Form 2 con una Form 3. L'azienda è in espansione e voleva continuare a poter contare sulla qualità e l'affidabilità delle stampanti Formlabs anche in questa nuova fase.
Per l'azienda è necessario che i modelli abbiano lo stesso aspetto e le stesse proprietà dell'ABS. La finitura superficiale e l'affidabilità delle stampanti rivestono una speciale importanza in questo caso, e l'azienda ha potuto notare miglioramenti su entrambi i fronti da quando ha introdotto le Form 3. Secondo il team di ingegneri: "La finitura superficiale con strati dello spessore di 100 micron della Form 3 è comparabile agli strati di 25 micron della Form 2".
"La finitura superficiale con strati dello spessore di 100 micron della Form 3 è comparabile agli strati di 25 micron della Form 2".
L'azienda utilizza la Grey Resin sulla Form 3 per stampare prototipi funzionali come serpentine, parti filettate e parti complementari. Il team ha già eseguito diverse iterazioni e sta procedendo rapidamente verso il design finale.
Dalla modellazione a deposizione fusa a stampe perfette con la Form 3
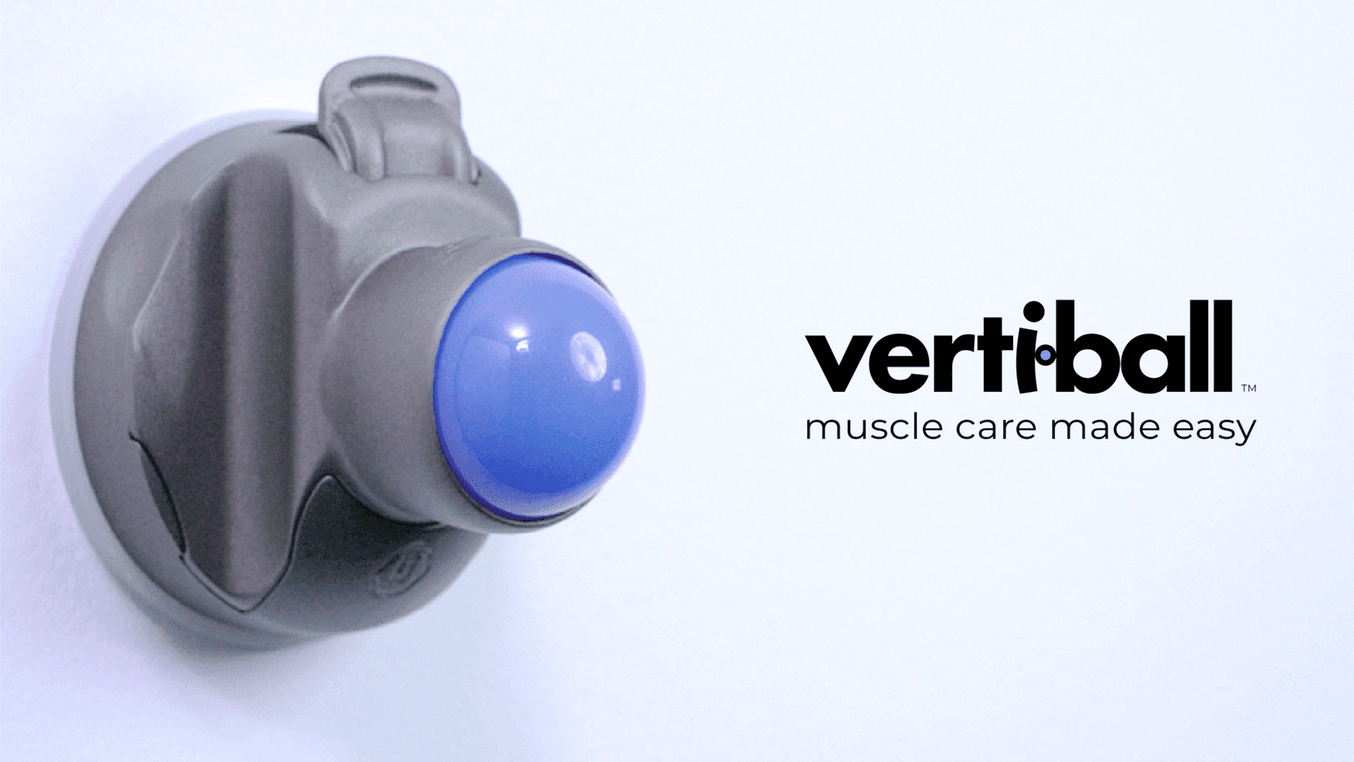
Curtis Kennedy è l'inventore di Vertiball, un sistema per massaggi muscolari montabile creato per alleviare tensioni, dolori e strappi. Curtis iniziò a progettare il prodotto quando era ancora uno studente presso la University of New Brunswick utilizzando una delle tante stampanti 3D a modellazione a deposizione fusa disponibili in università.
Purtroppo, però, a causa della natura anisotropica della tecnologia FDM, molti dei suoi prototipi si separavano in corrispondenza delle linee degli strati dopo solo tre usi. Nonostante queste difficoltà, dopo centinaia di prototipi è riuscito a investire in attrezzature per produrre la Vertiball.
Le sue parti prodotte in massa, però, non si montavano come si aspettava: il problema era che una delle parti più importanti non era precisa perché si restringeva durante il processo di stampa FDM, il che significava modificare le attrezzature, un'operazione lunga e costosa.
Curtis sapeva di aver bisogno di una stampante molto precisa, che garantisse finiture superficiali equiparabili a quelle delle parti stampate a iniezione. Dopo aver adattato il file CAD, Curtis richiese a Formlabs un campione personalizzato per verificare il nuovo design. Quel campione era proprio ciò di cui aveva bisogno e, a distanza di otto mesi, sta ancora utilizzando quella parte. Grazie a questa parte stampata in stereolitografia (SLA), ha potuto ricalibrare le attrezzature e soddisfare gli ordini.
Dopo questa esperienza con Formlabs, Curtis si è convinto ad acquistare una Form 3, che ha avuto un notevole impatto nella progettazione di alcuni dei suoi moduli per la Vertiball. Curtis ci ha raccontato che l'esperienza utente con la Form 3 è completamente diversa da qualunque altra stampante che aveva usato in precedenza. "L'interfaccia utente è intuitiva, PreForm è facile da usare, e impostare la stampante è estremamente semplice. Le dimensioni dei punti di contatto delle strutture di supporto sono veramente una svolta. Ho avuto pochissime stampe non riuscite. È praticamente perfetta."
Prova in prima persona la Form 3
Vedere come altri hanno usato la loro stampante SLA Form 3 è perfetto come primo passo per capire se è adatta per la tua azienda o per il tuo flusso di lavoro, ma non c'è niente di meglio che toccare con mano il prodotto stampato. Se ti interessa vedere da vicino la qualità della Form 3, richiedi gratuitamente un campione di stampa qui sotto.