One in every three new vehicles coming off the assembly line today has at least one component manufactured by Brose — one of the five largest family-owned automotive suppliers in the world. Started over 100 years ago in Berlin by Max Brose, the company has grown from an automobile accessories trading business into a market leader in mechatronic systems. Their products — mostly seat, liftgate, and door assemblies — are designed and produced for the biggest names in the car world: BMW, Volvo, Ford, Mercedes, Jeep, and more.
Brose’s steady growth and their long-term successful partnerships with these OEMs are due in part to the company’s commitment to continuous innovation and improvement. 3D printing is at the core of multiple initiatives in Brose’s design and end-use manufacturing processes and has helped Brose adapt and respond to all the changes in the fast-paced automotive industry.
We visited Brose North America, their headquarters in Auburn Hills, Michigan, as well as Brose New Boston in New Boston, Michigan, one of their largest end-use manufacturing facilities, to see how they’ve put powerful stereolithography (SLA) and selective laser sintering (SLS) 3D printers into action. Seat Division Prototyping Manager Matthias Schulz who is leading Additive Technology as well in the region, spoke to us about how Brose uses 3D printing throughout their entire process, from design to manufacturing to end-use parts on tight timelines for OEMs.
“We have seen rapid changes in the automotive industry, especially in the last five years. The development times for new products are getting shortened by a lot. That requires us to act accordingly — we have to implement additive technology more and more. It's in our interest because it also shortens lead times for toolings, etc., and helps us later with production to deliver parts faster.”
Matthias Schulz, Manager, Seat Prototyping, Brose North America
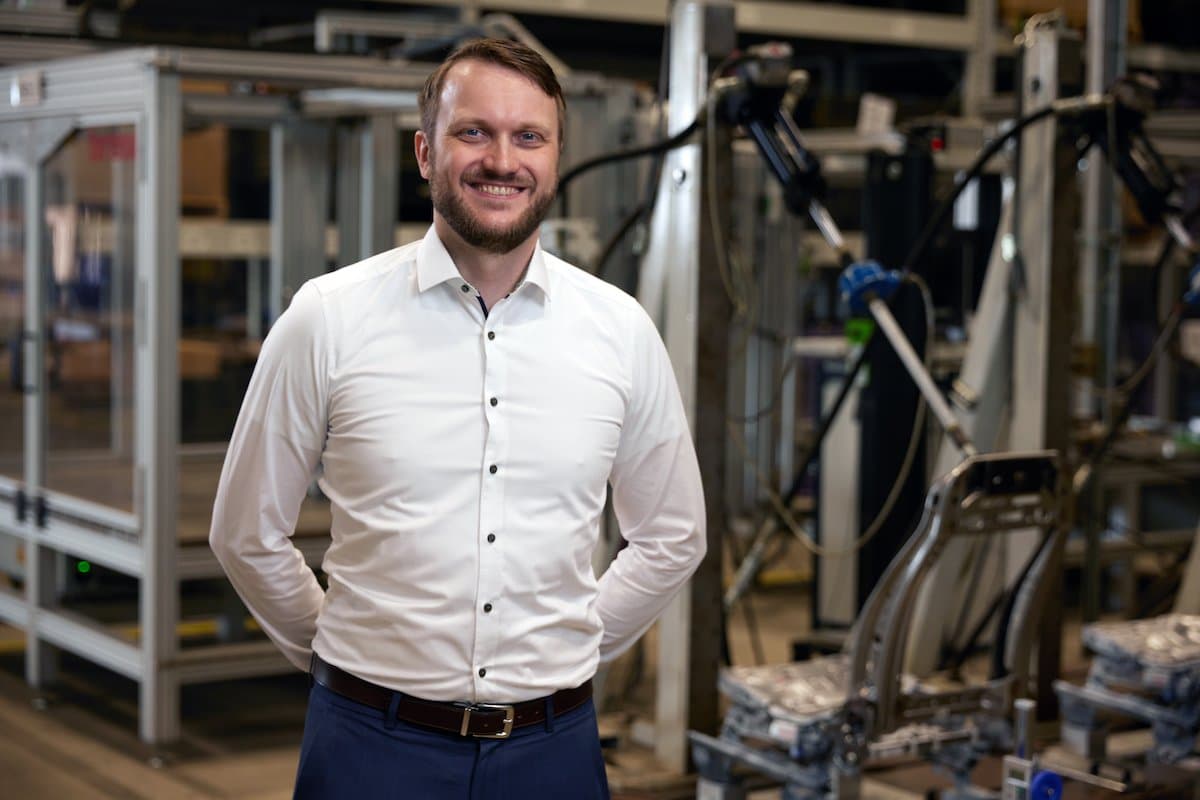
Webinar On-Demand: SLS at Brose for End-Use Automotive Production
In this on-demand webinar, Matthias Schulz, Manager of Seat Prototyping at Brose North America, demonstrates how Brose uses SLA and SLS technology for everything from quick welding jigs to production runs of 250,000 end-use parts.
When Prototyping Goes Beyond One-Offs
Prototyping as an application is a perfect — and familiar — fit for 3D printing. While Brose does employ a range of fused deposition modeling (FDM), SLA, and SLS 3D printers for prototypes, their volumes aren’t necessarily what one might expect for proof of concept parts. For Brose, a typical volume for prototypes is closer to 500 or 1000.
“We use 3D printing on a larger scale. ‘Prototyping’ means we have to print several hundred parts, mostly related to the number of tests that we have to do. Not only do we fulfill internal and external standards, but also federal requirements. Those, of course, require us to do a certain amount of parts, and that usually leads to seven to eight hundred parts that we have to print for a prototype,” says Schulz.
Overseas Order Quantities Make SLA The Best Option: Rubber Seat Length Adjuster Dampener
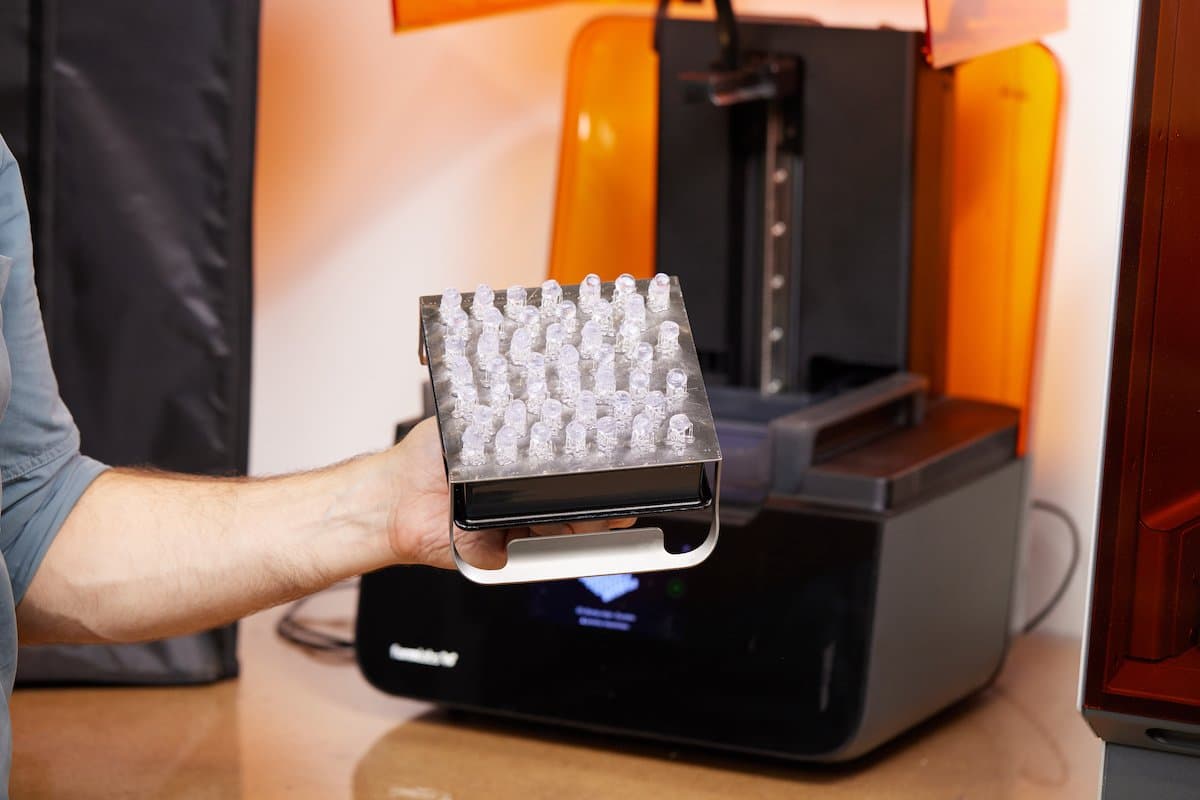
These prototypes are small dampeners made to reduce the sound and feel of the metal seat assembly hitting the seat frame. Ordering them from overseas required a minimum order quantity of several million, so Schulz and his team printed them on the Form Series printers for testing.
For one project, the prototype team needed to use a soft silicone dampener which is installed in the seat assembly. As the seat moves forward on its frame, the part dampens the sound and improves the haptic and acoustic feedback of the seat assembly movement. To order these parts from a Brose serial supplier overseas, the minimum order quantity was in the millions — and Brose only needed a few hundred for use in a preliminary design test.
Besides the high cost of ordering several million parts and shipping them overseas, the lead time was several weeks, and the millions of parts that weren’t needed would require storage before ultimately creating waste. Instead of ordering the part, the existing CAD was used to quickly 3D print several hundred of them on Form 4. They were ready in a week, and the solution reduced the overall costs and lead times of the entire project.
“We were able to print them on Form 4 at a much cheaper cost than flying those parts over here and ordering minimum order quantity stock — which required us to order several millions of those parts. We had them rapidly available and didn’t have to wait for anything.”
Matthias Schulz, Manager, Seat Prototyping, Brose North America
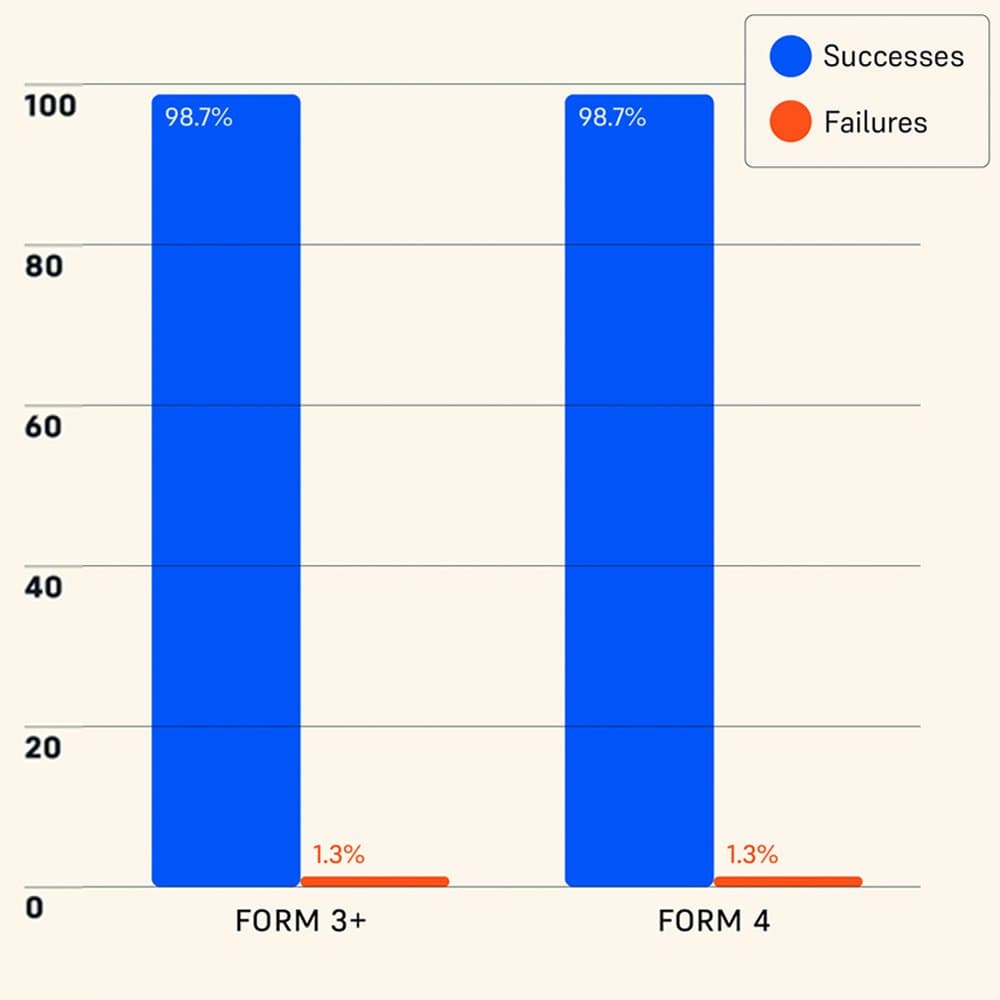
Independently Tested Reliability of Form 4 and Other Resin 3D Printers
Formlabs Form 4 was measured to have a 98.7% print success rate by an independent global leader in product testing. Read a complete description of the test methodology and see the results in our white paper.
Combining SLA and SLS for High-Volume Prototypes
When components increase in complexity, size, and required volume, Brose turns to his fleet of three Fuse Series SLS 3D printers for prototypes and production. SLS 3D printing with its self-supporting print bed enables fully packed production volume builds, and the strength and mechanical properties of sintered nylon make the technology ideal for end-use components. For a recent project, Brose’s Additive Technology team used both SLA and SLS technology to prototype a seat suspension mat.
They printed the translucent, flexible parts in Durable Resin on their Form Series SLA 3D printers, and the mat’s connection tubing in Nylon 12 GF Powder on their Fuse Series printers. For each mat prototype, there were six SLS parts and three SLA parts, but in total, the team assembled 150 of these full mats to be tested as part of complete seat assemblies.
With rapid prototyping tools in-house, Brose was able to design, test, and iterate a vital component of their seat assembly product without tooling or outsourcing. “Sometimes the combination of both SLA and SLS is the answer, like on this seat suspension mat. An overmold tool is very complex and expensive, so we designed the parts to snap over the wire for the SLS and installed the SLA parts in a “green state” on the wire and cured it that way,” says Schulz.
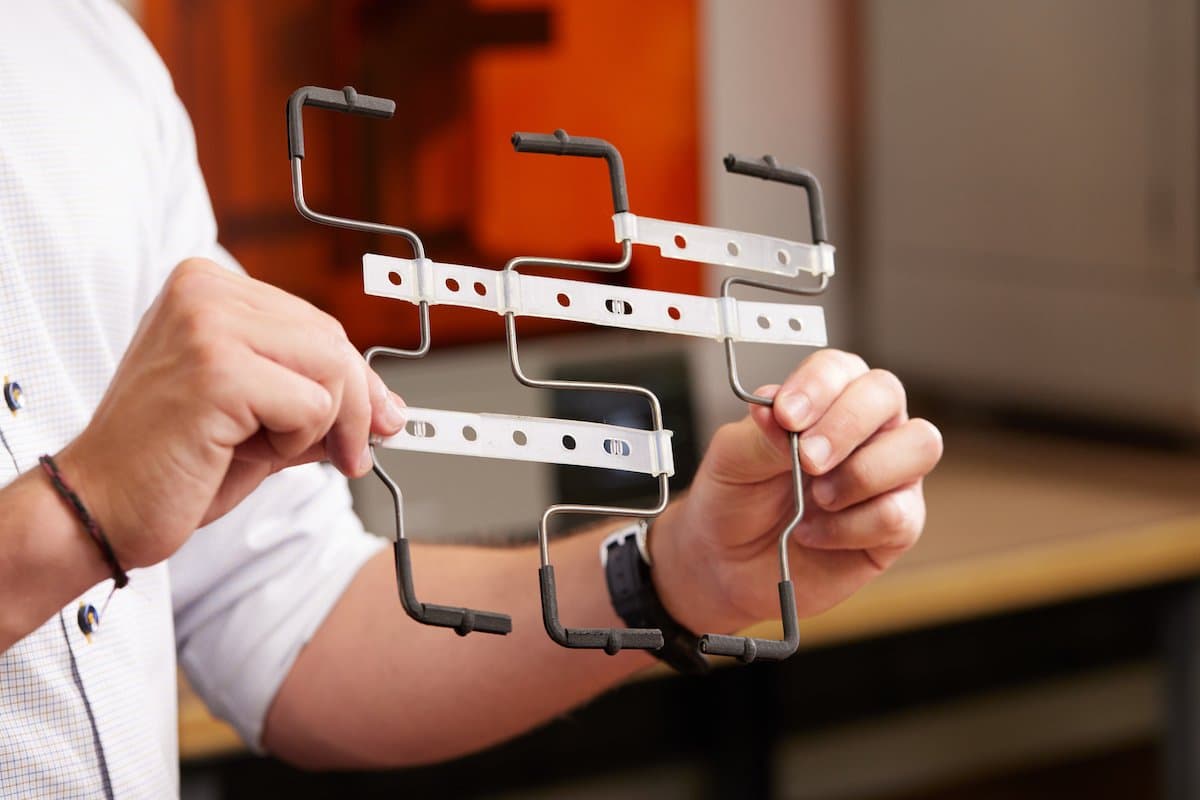
This seat suspension mat has both SLA parts (Durable Resin, translucent material) and SLS parts (Nylon 12 GF Powder, dark grey material). 150 of these full assemblies were needed for testing, including 900 SLS parts and 450 SLA parts.
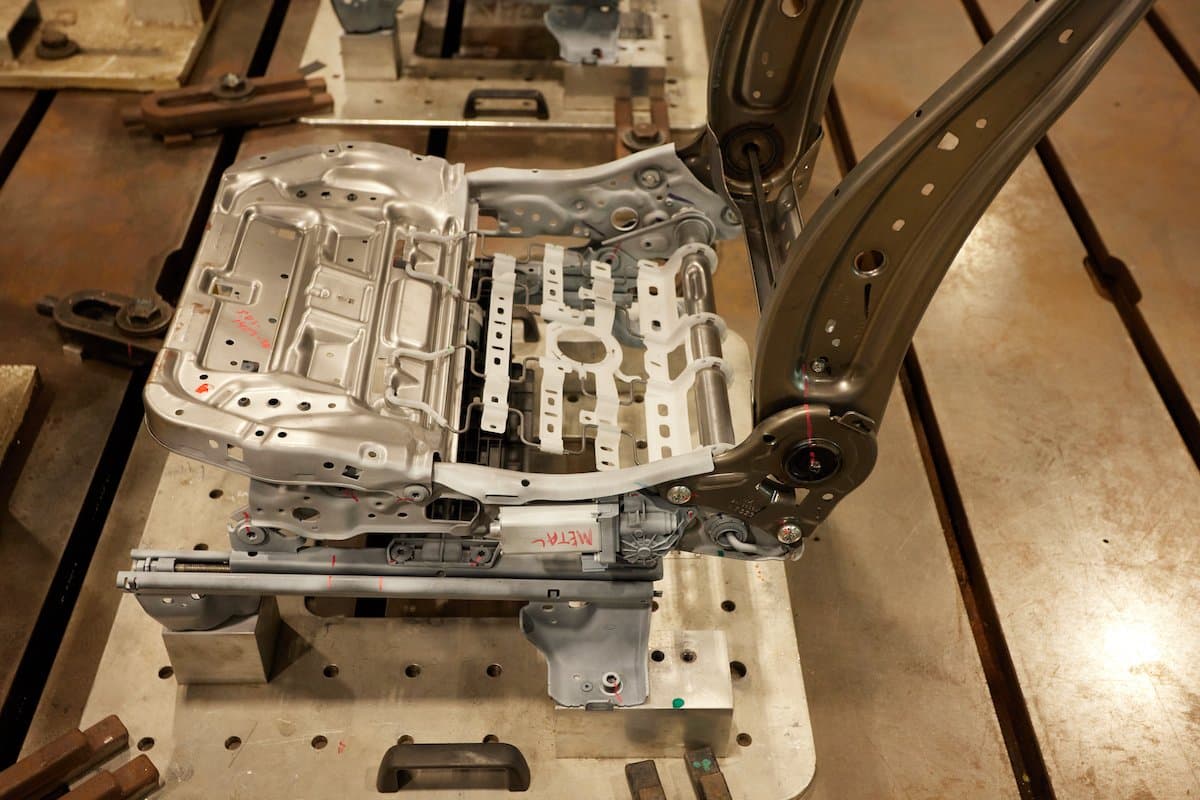
Prototypes and end-use production versions (like this above) go through fatigue testing that mimics years of use.
Manufacturing Aids Streamline Production
Additive manufacturing isn’t only being used as a prototyping tool at Brose — they’re integrating the technology across all departments as part of their Plant Goes Additive initiative, which launched in 2022. Automotive manufacturing is non-stop and highly controlled — every part of the process has been lean and optimized for efficiency as well as safety and product excellence.
Same-Day Robotic Welding Fixtures on Form 4L
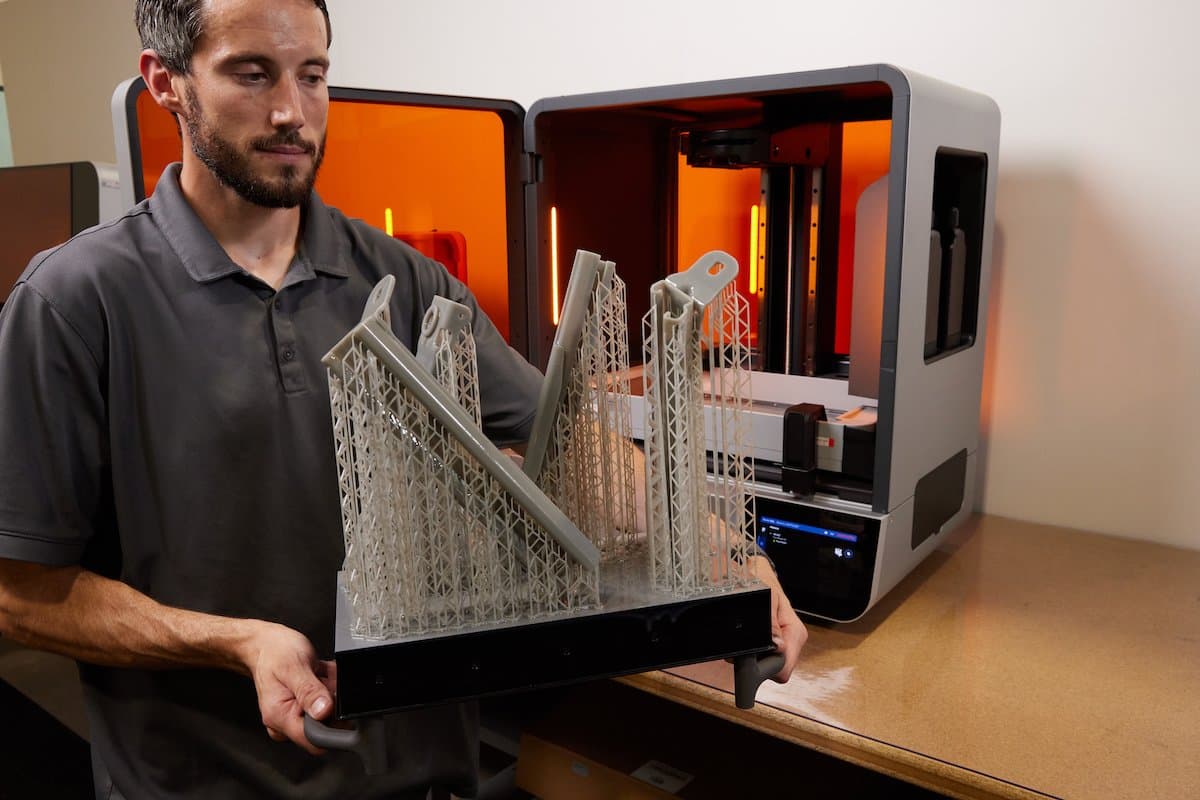
Form 4L makes same-day, large-format parts possible, like this welding fit fixture printed in Fast Model Resin.
At every stage in the automotive supply chain, metal parts are key components of the overall product. Welding is, understandably, a huge part of the assembly process. At Brose North America, where Brose’s Additive Technology team operates the fleet of SLA and SLS printers, their welding robots need to switch between different product lines constantly. At a plant, the welding machines stay programmed to one product line, but at headquarters, they have two robotic machines responsible for welding seat prototypes of every different product line.
Each time the robot has to switch to a new product line, the welding department has to reprogram its parameters. Programming a welding robot using prototype metal rails is expensive, and they are very often not available at the time the weld station is ready to teach the equipment. 3D printing offers a fast and inexpensive solution, as speed and dimensional accuracy are needed for those setup parts.
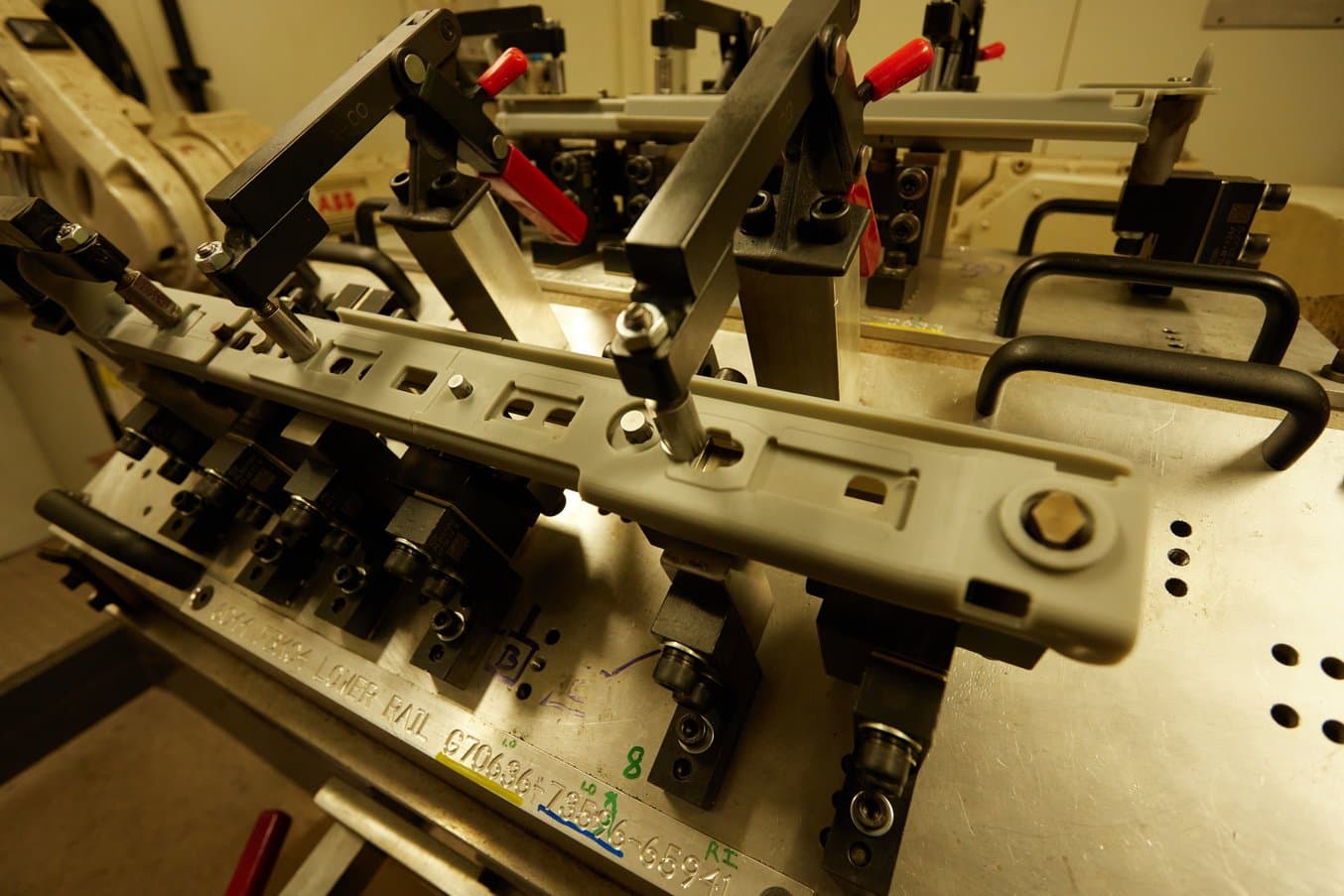
This seat part was printed on Form 4L in Fast Model resin, washed, cured, and assembled onto the robotic welding machine in under three hours. This allows the team to teach the robot movements quickly.
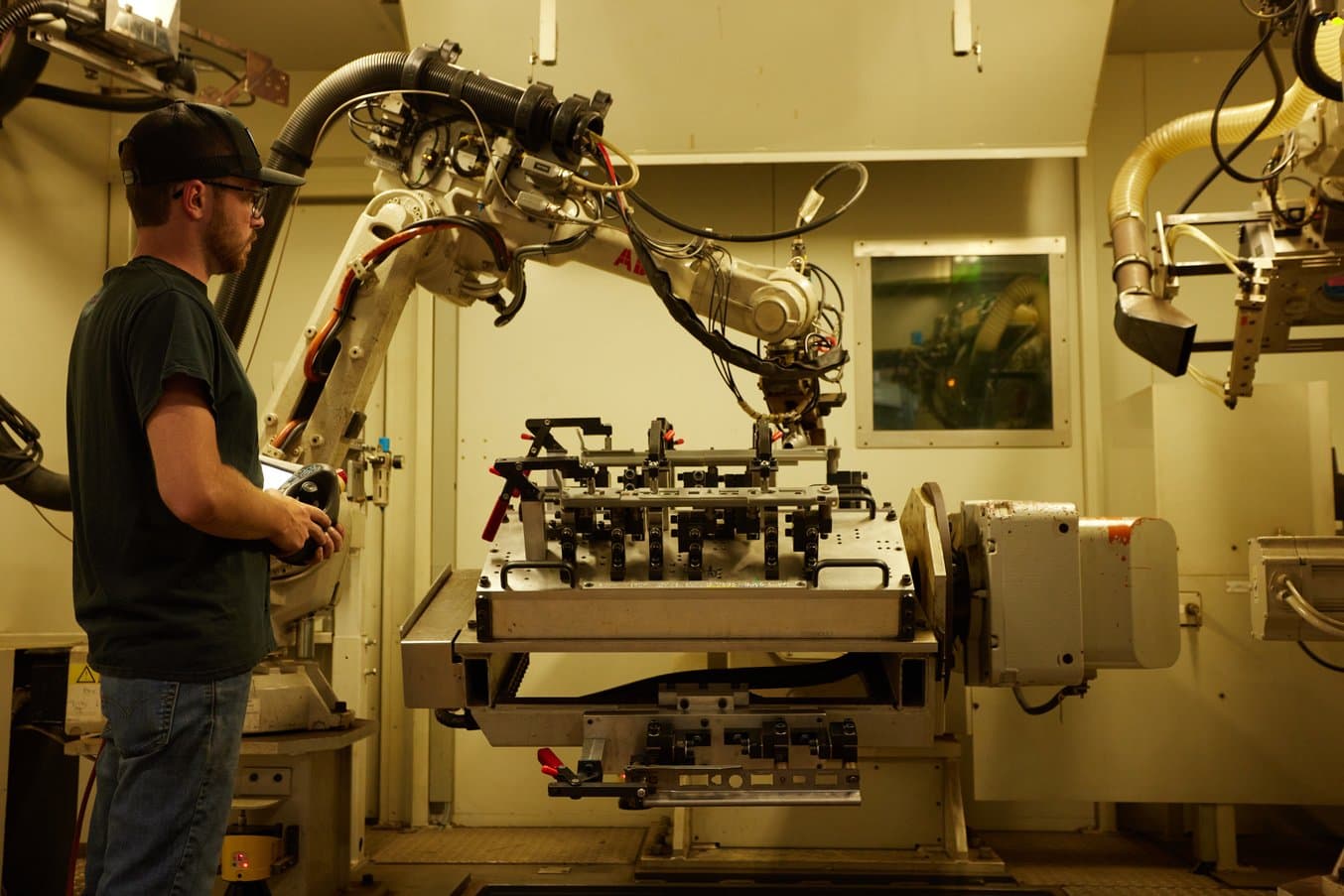
Fit fixtures like these help the welding team transition quickly and efficiently between product lines. They’re highly accurate, affordable, and endlessly replicable in case one needs changes or replacement.
The Brose team opened their newly arrived Form 4L large-format resin 3D printer on a Tuesday morning. The setup took just 30 minutes, and soon they were printing large welding setup parts using Fast Model Resin. The parts, divided into four pieces, nearly filled the entire build volume. Despite its size, the Form 4L printed it in under two hours, and after a quick wash and post-cure, the fixture was mounted on the welding robot just 45 minutes later.
“The new Formlabs 4L allows us to print large parts fast. For example, we use Form 4L to print setup parts for our weld cell in just hours instead of overnight. This allows the Brose welding experts to program the robot prior to the metal stamping components arriving. With the new Fast Model Resin, we receive the detail required and the rigidity needed in a faster time than ever before.”
Matthias Schulz, Manager, Seat Prototyping, Brose North America
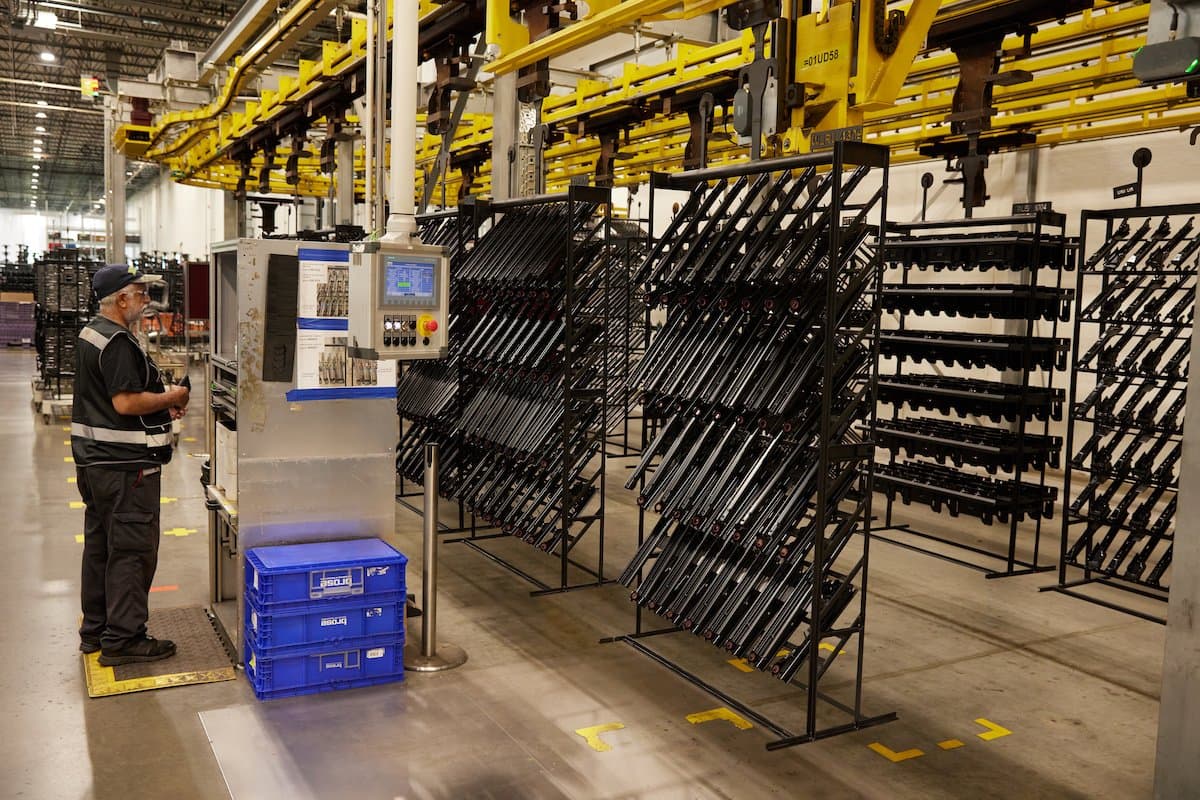
At Brose New Boston, thousands of seat rails, shown above, are welded together to form the base of the seat assembly. Testing welding parameters is integral to the manufacturing process.
The welding parameters determined at Brose North America headquarters with prototypes and 3D printed setup parts, will then be used for mass production of welded seat frames. The seat rails, above, will be assembled at Brose New Boston with large robotic welding machines.
End-of-Line (EOL) Connectors Reduce Operating Costs at Brose New Boston
At Brose’s New Boston plant, located about thirty minutes west of downtown Detroit, the team leverages 3D printing to create customized manufacturing aids that streamline the assembly process. While 3D printed parts undergo rigorous testing before being integrated into production, once approved, they help reduce waste, improve production timelines, and keep machinery running consistently.
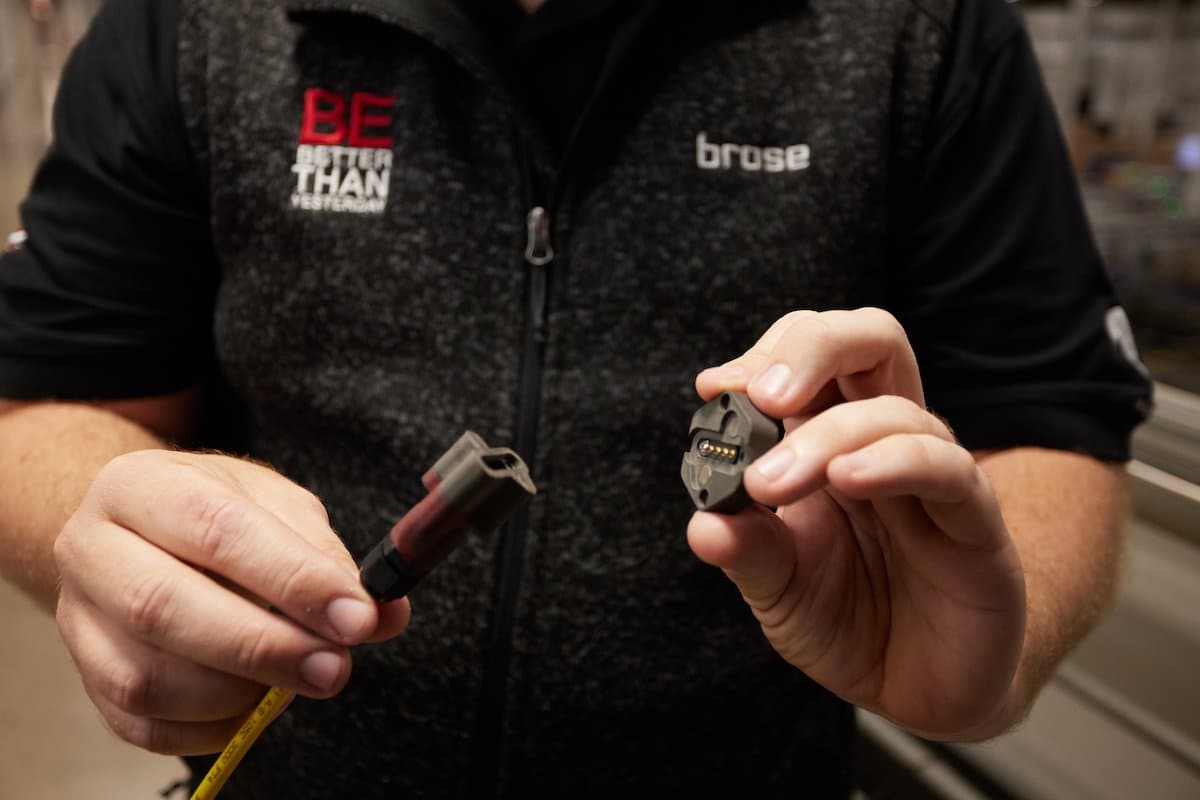
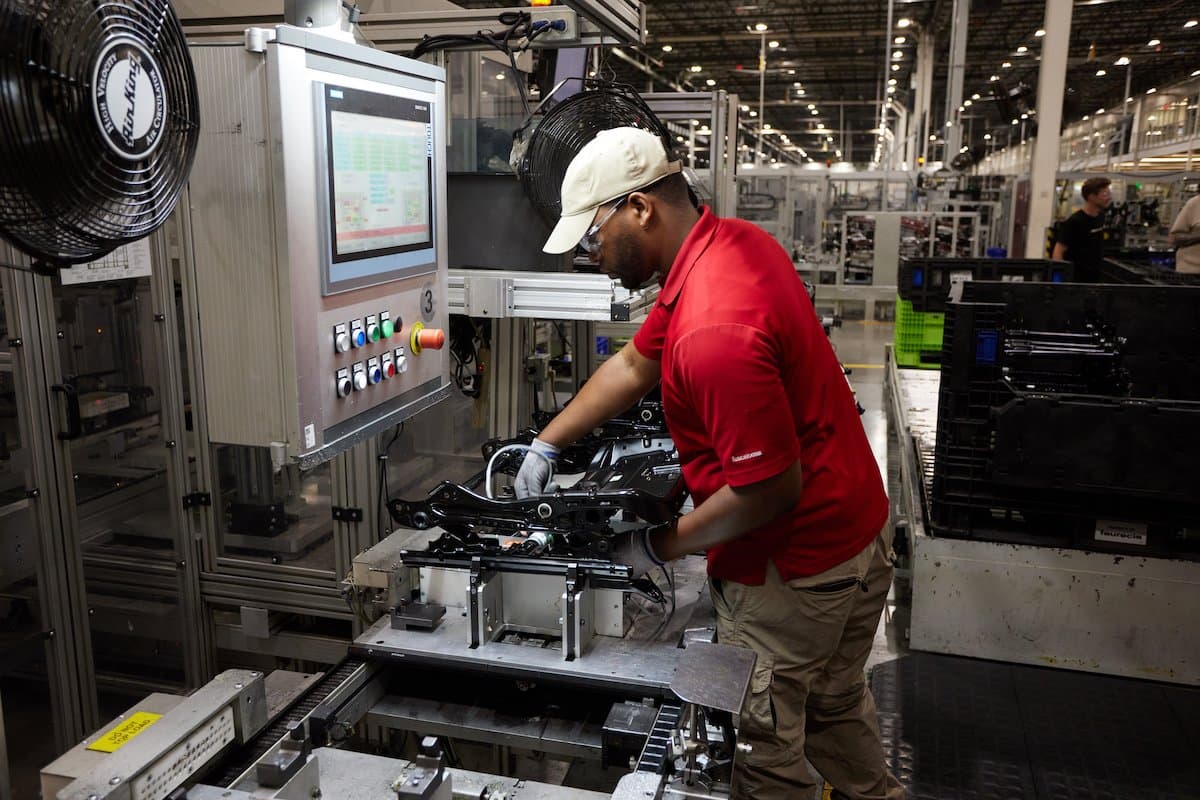
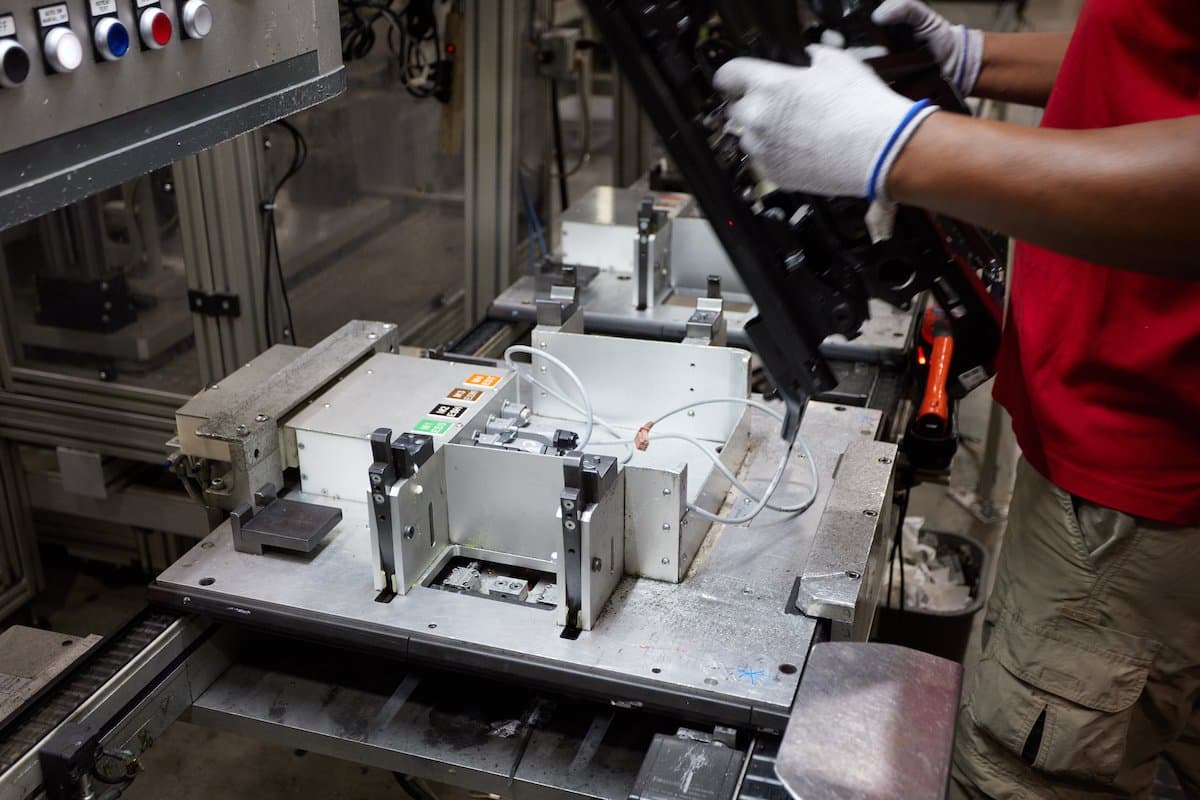

This end-of-line (EOL) connector piece has been implemented at the final stage in the seat assembly process. After the technician connects the seat frame to the electrical source and performs the final check, he removes it to move through the next process stage. Many times, technicians would forget the electrical connection, and in removing the seat, snap the cord, causing a couple hundred dollars of damage to the assembly line, and pausing production.
The additive technology team worked with the New Boston team to design a magnetic connector line. It easily attaches to the line and the seat frame, but snaps off without any damage if the technician pulls away the seat frame without manually removing the cord. “We use 3D printed manufacturing aids to reduce wear and tear on machinery. They allow us quicker repairs on the production line. This leads to less downtime in production and also helps us increase the overall output,” says Schulz.
Serial Gap Production for End-Use Automotive Parts
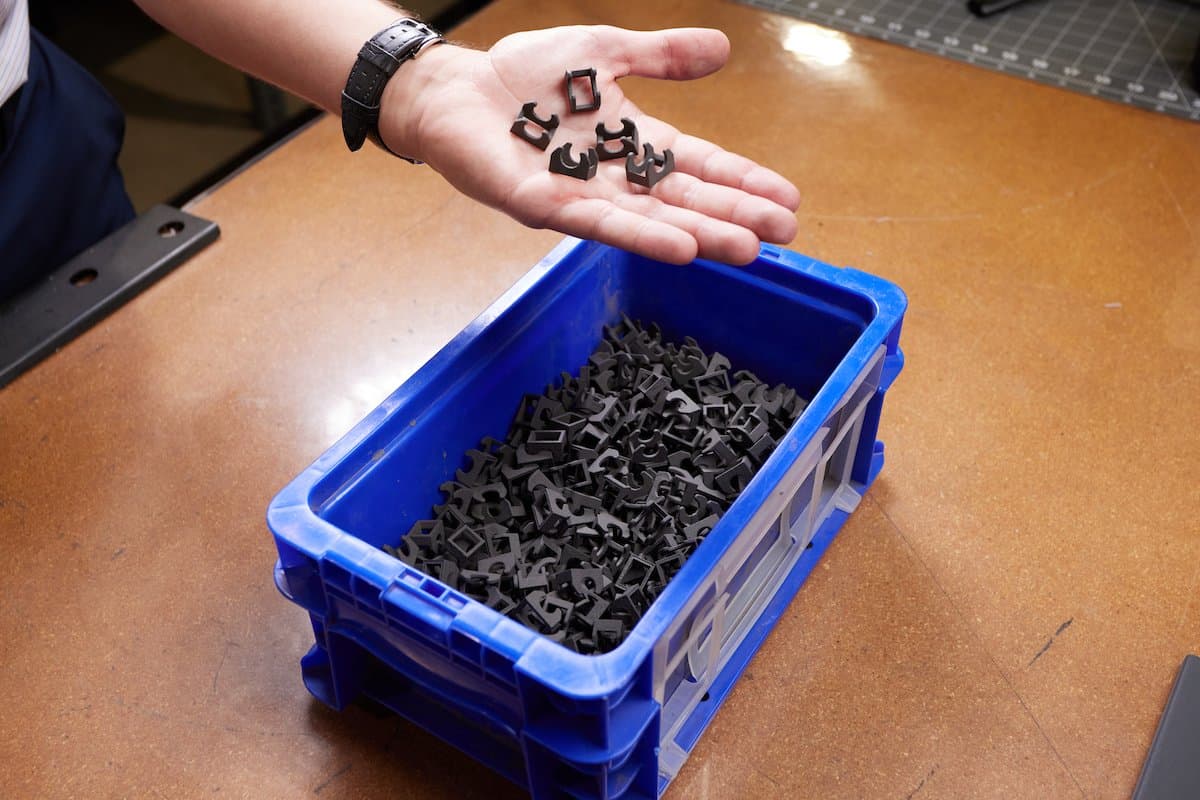
Brose will 3D print 250,000 of these clips for seat assemblies in the BMW X7.
As Schulz says, the automotive industry has been changing fast, especially in the last five years. The rise of EVs, the growing demand for customized features, and supply chain concerns have prompted OEMs to invest more heavily in additive manufacturing as a reliable alternative for production.
“We do have more and more customers requesting additive technology. It also plays a role with the customer interface for the end-use customer, because they would like to have more personalization in their vehicles, and therefore, additive technology is being asked for more and more by the OEMs,” says Schulz.
3D printing for end-use parts, especially in the highly regulated automotive industry, hasn’t always been possible. Brose’s additive manufacturing team has made sure they moved to end-use production only when the quality of the hardware and materials could deliver high-performance parts reliably.
“We decided to jump onto the Formlabs boat here. We did that because the material availability and the consistency of the prints were so much improved that the technology is now ready to be helpful in the automotive industry. The issue for us is that safety and durability concerns exist, especially with the OEMs. We’re trying to rule this out. And in collaboration with Formlabs, we have proven that we can implement parts like we do on the current BMW X7.”
Matthias Schulz, Manager, Seat Prototyping, Brose North America
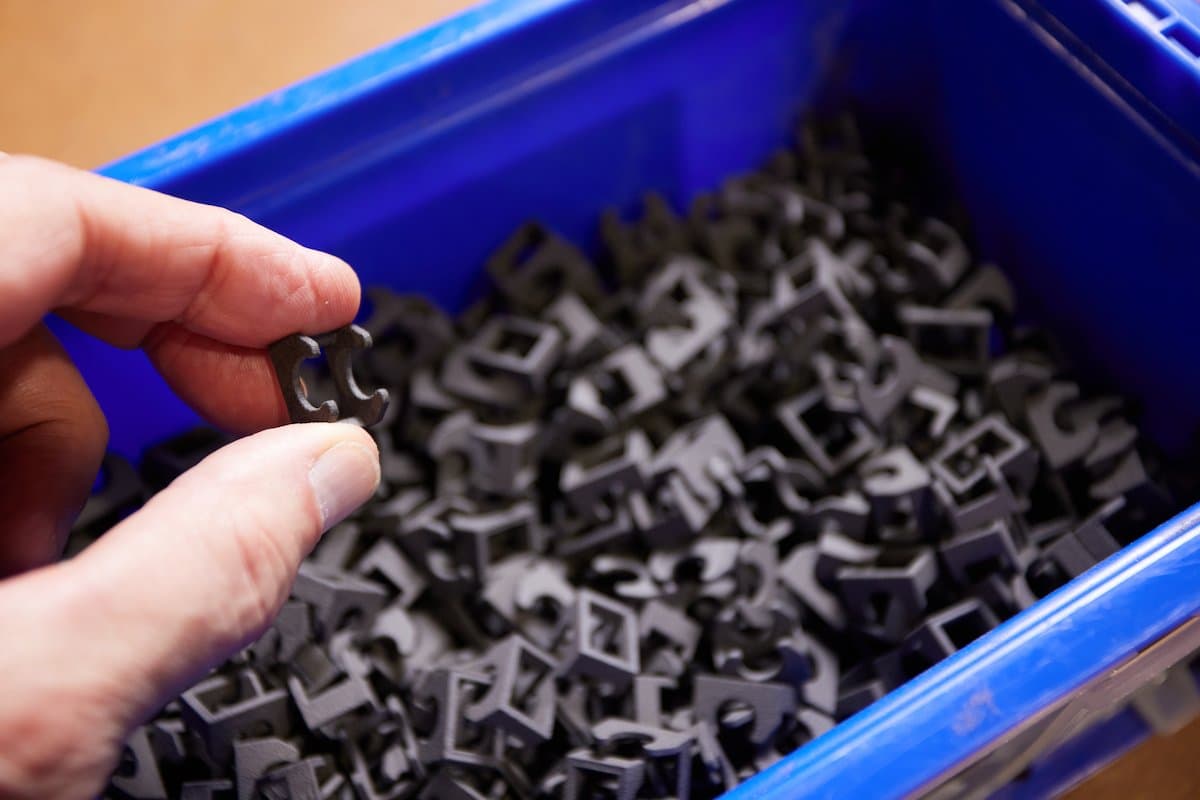
Application: BMW X7 Seat Components
Workflow: 3D scanning, iterating, then 3D printing on the Fuse Series SLS 3D printers for end-use production.
Volume: 250,000
Build Details:
- Printer: Fuse 1 and Fuse 1+ 30W
- Material: Nylon 12 GF Powder
- Build Volume: 1,440 parts per build chamber
- Parts Per Month: 16,000
Why 3D Printing?
- Gap printing to allow transition time for tooling availability
Brose uses 3D printing for end-use production as an affordable, fast alternative to traditional manufacturing. When an OEM requests a part, or a change to an existing part, that cannot be tooled and mass-produced fast enough, the additive division at Brose evaluates if 3D printing is suitable. A big part of that is reverse engineering and scanning existing components.
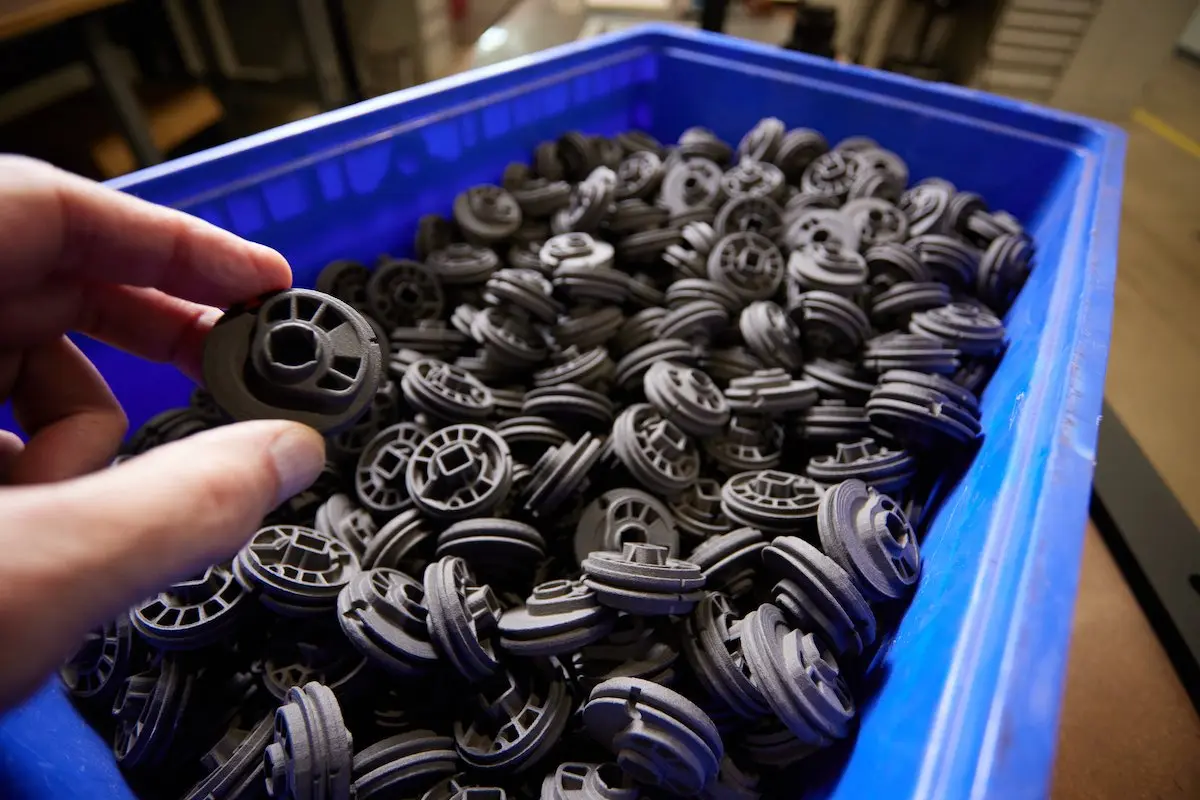
Application: Bowden Release
Workflow: 3D scanning, iterating, then 3D printing on the Fuse Series SLS 3D printers for end-use production.
Volume: 20,000
Build Details:
- Printer: Fuse 1 and Fuse 1+ 30W
- Material: Nylon 12 GF Powder
- Throughput: 144 parts per chamber, 1000 parts per week
Why 3D Printing?
- Gap printing to allow transition time for tooling availability
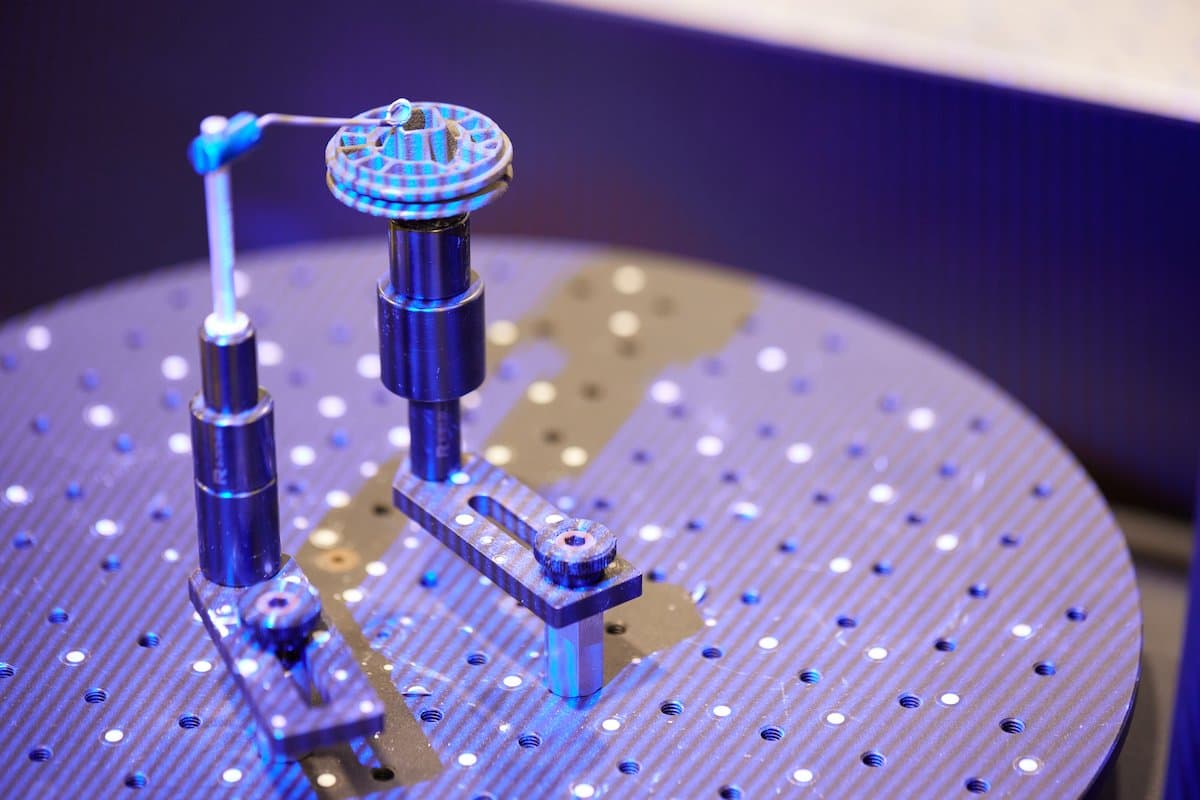
Brose will often scan existing components or previous iterations so they can make changes in CAD and 3D print the updated version on the same day.
This component is a Bowden release — 20,000 of these parts will be printed on Brose’s fleet of Fuse Series SLS 3D printers and included in the final seat assembly for a large, well-known OEM.
“Brose decided to bring SLS with Formlabs in-house because the SLS technology allows us fast and rapid 3D printing that has less post-processing requirements than we see on SLA. We can print high volume quantities, which is necessary for us to support gap printing or other OEM-related end-use customer parts,” says Schulz.
With three Fuse Series SLS 3D printers working nonstop to produce prototypes, manufacturing aids, and hundreds of thousands of end-use components, reliability and consistency are key. The team uses Nylon 12 GF Powder for its dimensional accuracy and close resemblance to injection molded nylon, even at production volumes. After each full build, a quick maintenance check on the Fuse 1 or Fuse 1+ 30W takes just about fifteen minutes, ensuring continuous, efficient production.
“Formlabs understands how to build a printer that is easy to maintain. The equipment is very reliable and we hardly see any failed prints, so we can commit to printing higher volume parts and have the confidence to go to production,” says Schulz.
0 to 60: 3D Printers Gain Speed in Automotive
Brose’s commitment to continuous improvement has led them to invest in new technologies like additive manufacturing and automation to streamline their processes and deliver innovative solutions for each of their customers. As 3D printing begins to take a bigger and bigger role at the company, champions like Schulz are committed to finding new ways to leverage its quick turnaround times and (frequently) lower costs.
With fast, powerful tools like Form 4, Form 4L, and the Fuse Series, prototyping, manufacturing aids, and end-use components can be turned around in hours or days, rather than weeks or months. “Formlabs is the right partner to work with. We needed a turnkey solution that could produce parts in higher volumes and with less engineering support. The software, support, and printers from Formlabs are the right fit.”
To learn more about 3D printing in the automotive industry, visit our website. To see the quality of SLA or SLS 3D printing for yourself, request a sample.