The European Organization for Nuclear Research, also known as CERN, is a research center for high-energy physics that operates the largest particle physics laboratory in the world. CERN is home to the world's largest and most powerful particle accelerator, the Large Hadron Collider (LHC).
One of the most grandiose and expensive scientific instruments ever built, the LHC will help humanity answer some of the fundamental open questions in physics, which concern the basic laws governing the interactions and forces among the elementary objects, the deep structure of space and time, and in particular the interrelation between quantum mechanics and general relativity.
Massimo Angeletti, a mechanical engineer, is a member of the Experimental Physics Detector Technology (EP-DT) department involved in the construction, assembly, and installation of particle detectors. Read on to find out how this CERN department uses 3D printing for rapid prototyping and research and development.

An example of 3D printed support structures printed in Black Resin. Their purpose is to hold three bent thin chip sensors (ALPIDE MAPS sensors, 40 µm thick ) in position during a test with particle beams.
Rapid Prototyping of Particle Detectors
The department in which Massimo works has been using 3D printing for more than six years for different applications, using two Form 2 and a Form 3L stereolithography (SLA) 3D printers that are now key tools for the research and development of the new generation of particle detectors that will be installed in the LHC.
By rapid prototyping with 3D printers in house, they have been able to cut down on development times, reduce costs and find new layout solutions not reachable with traditional machining. Before in-house production, they had to rely on suppliers and wait for weeks for the even fairly simple 3D printed parts to reach CERN. Formlabs printers and materials are mainly used for prototypes, but also for molds and tools used during detectors assembly and testing.
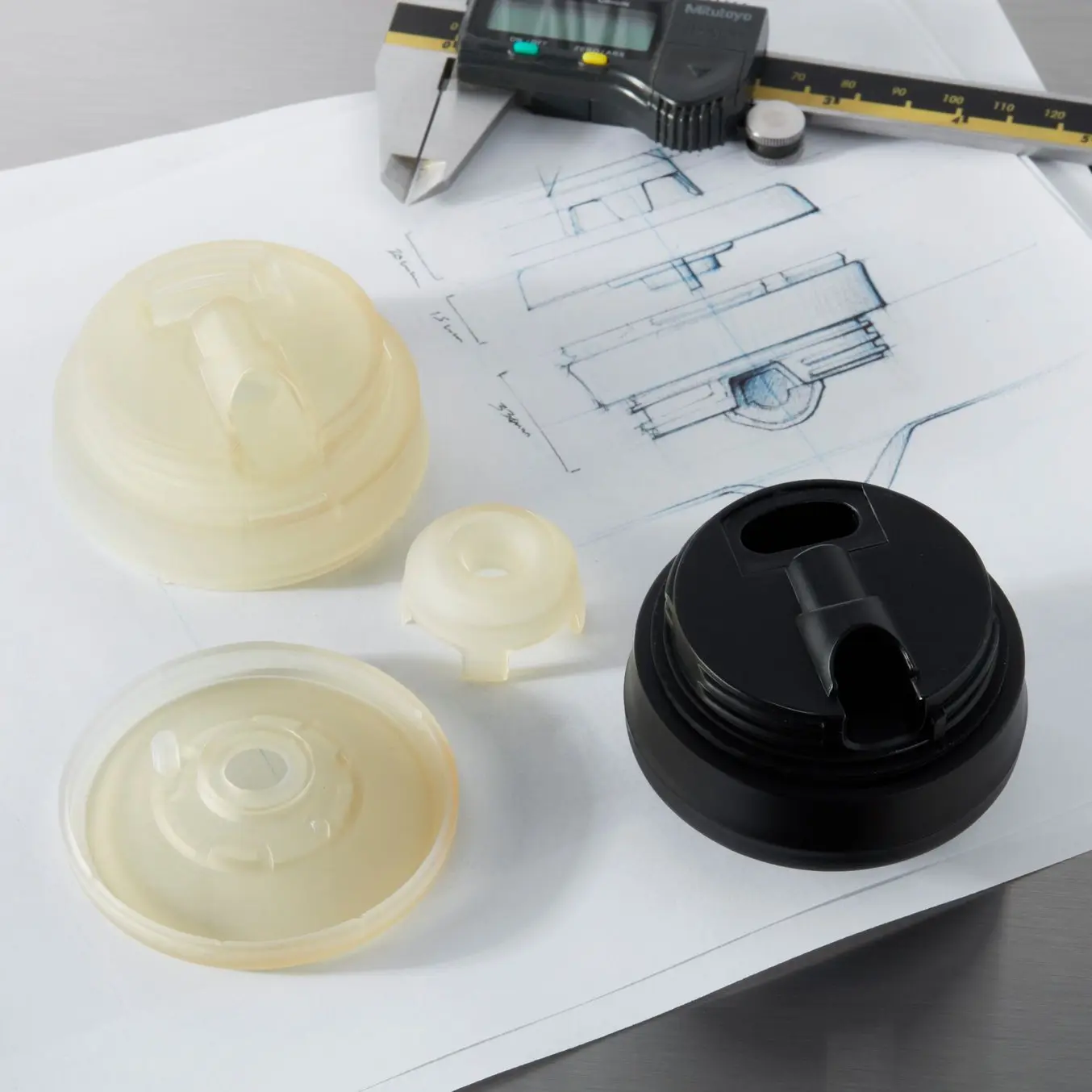
Guide to Rapid Prototyping for Product Development
In this guide, you’ll learn how rapid prototyping fits into the product development process, its applications, and what rapid prototyping tools are available to today’s product development teams.
Massimo's team also tested FDM technology printers but realized that surface quality, dirt resistance, and durability of parts was significantly less than that of parts printed in SLA. Due to the high-precision of the parts required, these properties were of utmost importance to the CERN team, and so they decided to use SLA for their prototypes.
Thanks to the training offered by Formlabs, researchers are able to safely and independently operate the printers. In most cases, they are the ones who create designs using CAD modeling programs and send them to the printer, which helps to speed up the workflow.
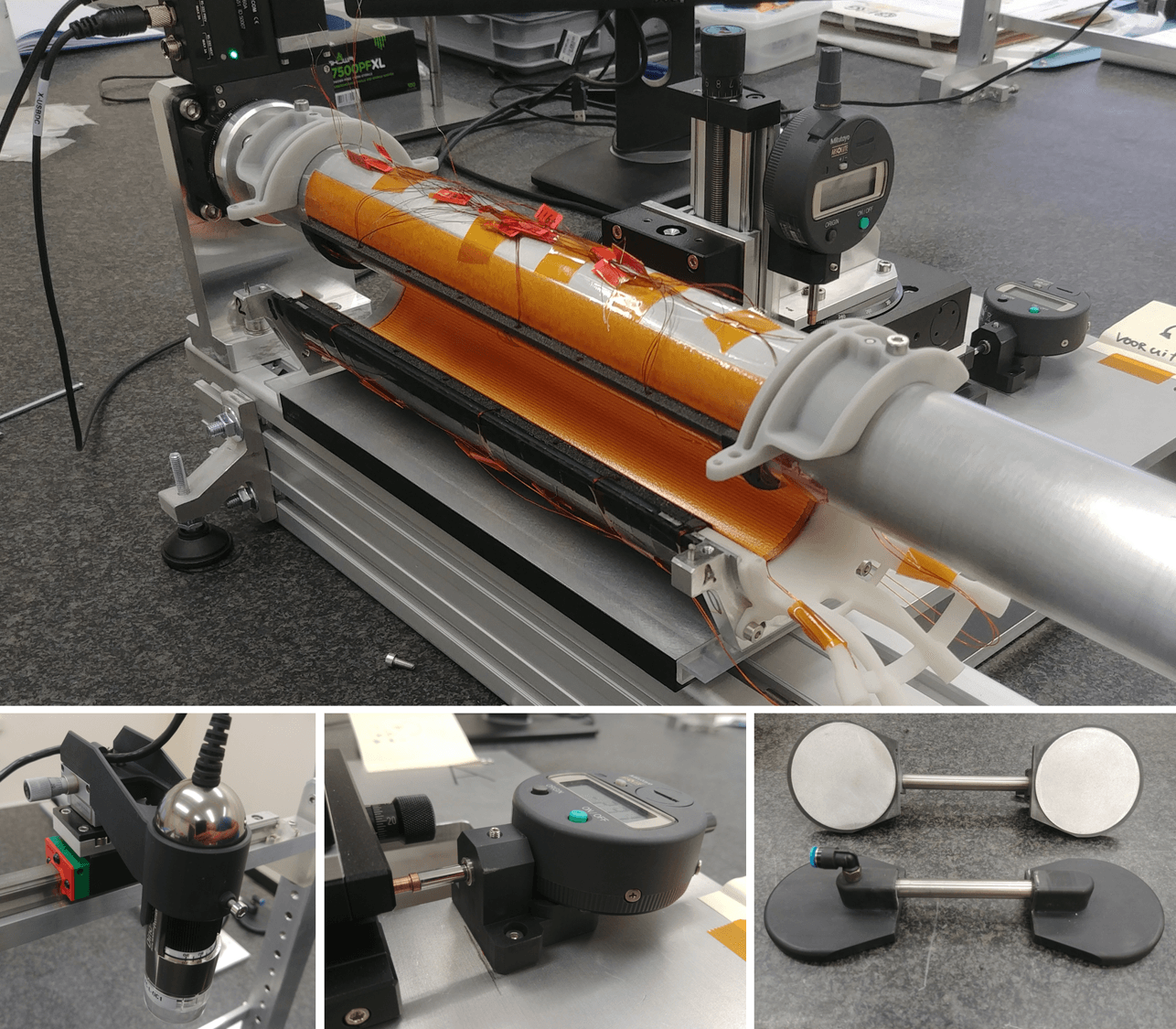
Several 3D printed parts in Black Resin utilized for the assembly of a real scale detector prototype (60 x 60 x 300 mm3). The prototype in the top picture is a model of a new category of particle tracking detector based on large thin MAPS sensors (90 x 280 mm2, 30-40 µm thick) that is under development for ALICE, one of the Large Experiment at LHC.
The unique design freedom offered by additive manufacturing makes it possible to produce complex three-dimensional shapes. This is well aligned with the novel trend of developing customized, versatile, and intricate particle detector structures.
To date, 3D printed polymeric materials are being increasingly used inside LHC experiments. However, the tight requirements, coming from exposure to radiation doses in the experimental area, which can change the mechanical properties, require a specific qualification of the printed materials.
“For this reason, we would like”, Angeletti explains, “to further characterize the Formlabs materials for high radiation environments such to extend their use in functional parts of the detectors in the experimental area”.
The resins most commonly used during the prototyping process of the particle detectors currently are Black Resin and Clear Resin, but CERN’s team is also testing Rigid 4000 Resin and Rigid 10K Resin to possibly manufacture end-use parts in the future.
"3D printers make everything easier and faster. You own the process from start to finish. You create the files on your own and send them to the printer, and that is certainly satisfying. 3D printing also allows a lot of iteration. Within a few days, you have the final piece that would have been delivered weeks later if it had been sent to third-party entities. It's unbelievable."
Massimo Angeletti, mechanical engineer, CERN
The Future of 3D Printing in Research
"It would be really nice", Angeletti explains, "to deeply implement 3D printed parts and minimize standard manufacturing". In fact, he sees the future with a detector almost entirely 3D printed, other than electronics such as the sensors and their components. Once tested for high radiation experiments, Angeletti is also hoping to utilize new radiation-qualified photopolymers inside possible future experiments.
From millifluidic devices to electroplated beam splitters and high-performance antennas, calibration units, and the study of corals, scientists around the globe use 3D printing to accelerate research, lower the cost, and speed up the development of advanced experimental setups, and fabricate custom scientific devices.
Explore the different 3D printers, materials, and applications to learn how to make 3D printing your ultimate tool for research and education.