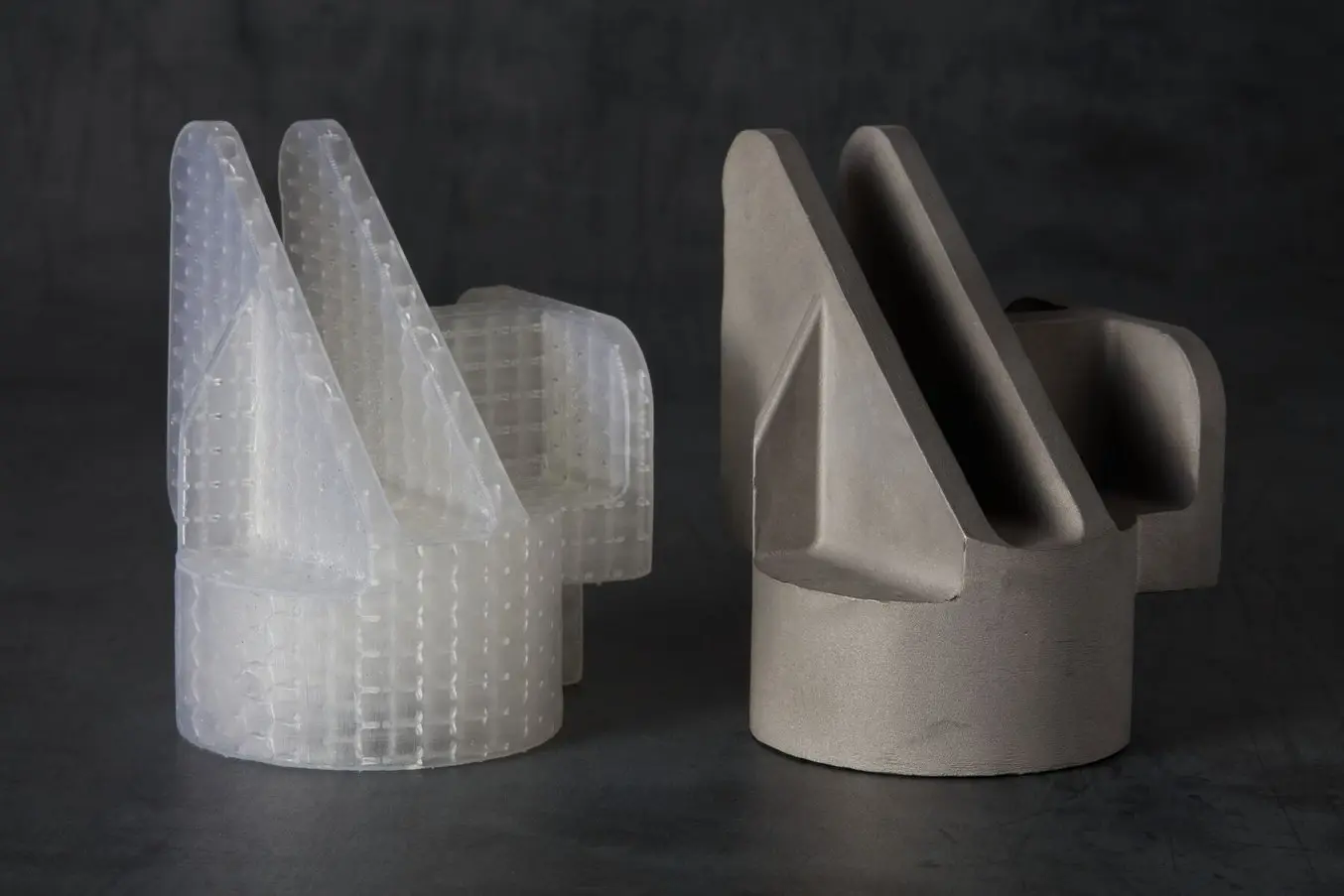
Investment casting pattern 3D printed in Clear Cast Resin and the cast metal part.
Metal casting is an age-old metalworking process in which molten metal cools and solidifies in a mold to form metal parts. Despite its ancient roots, metal casting is still one of the most popular processes for companies looking to produce metal parts.
This article will cover what metal casting is, how it works, and walks you through the most common metal casting processes and the benefits manufacturers can attain by combining modern digital tools like 3D printing with traditional casting workflows.
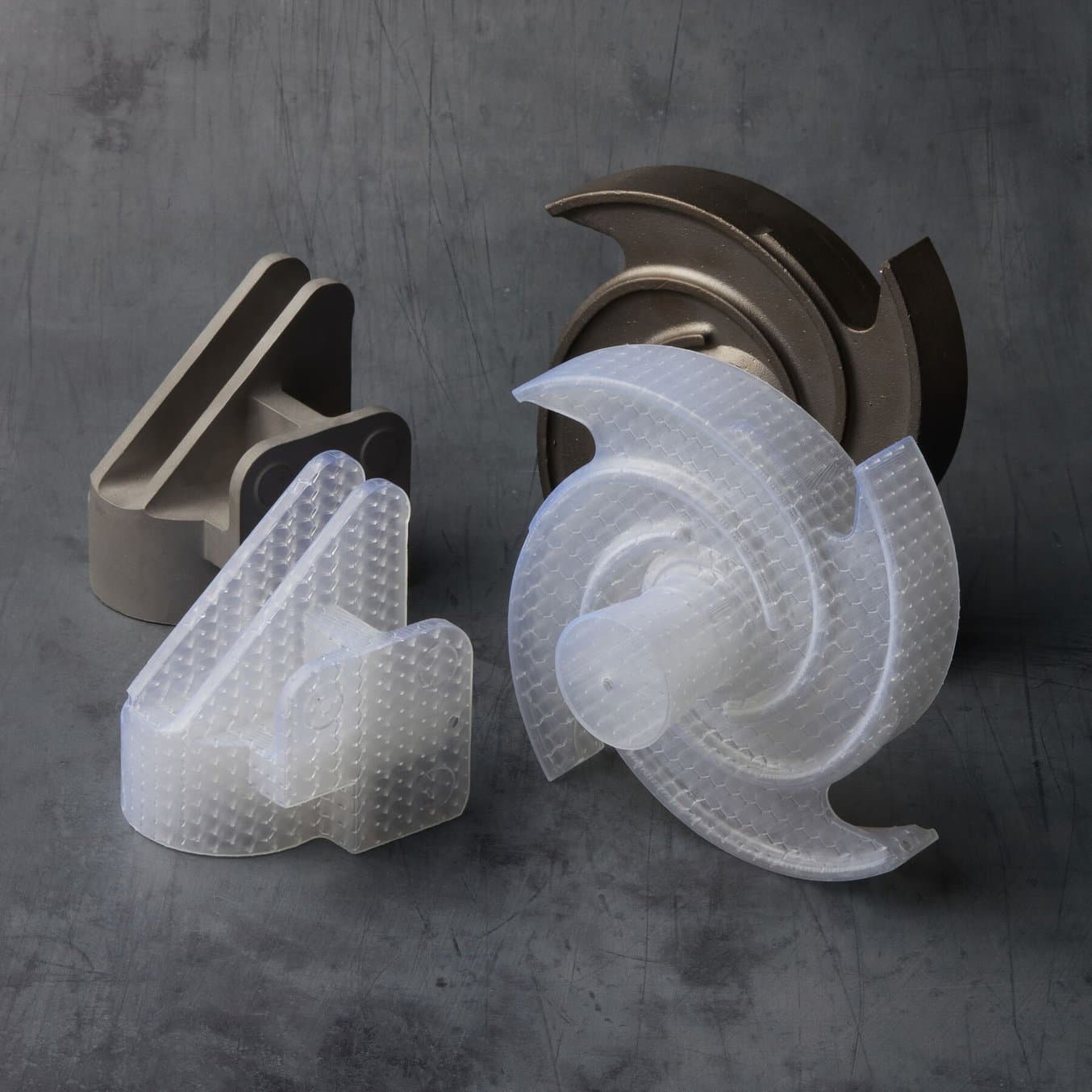
Precision and Cost-Efficiency in Casting: Leveraging 3D Printing for Metal Parts
This webinar will walk you through the methods by which several established foundries were able to cast metal parts using patterns 3D printed on Formlabs’ 3D printers. Learn how foundries are cutting costs, reducing lead times, and improving the quality of their metal parts by integrating Formlabs’ Clear Cast Resin and Materialise Magics’ Lattice with traditional casting methods.
Metal Casting Process Overview
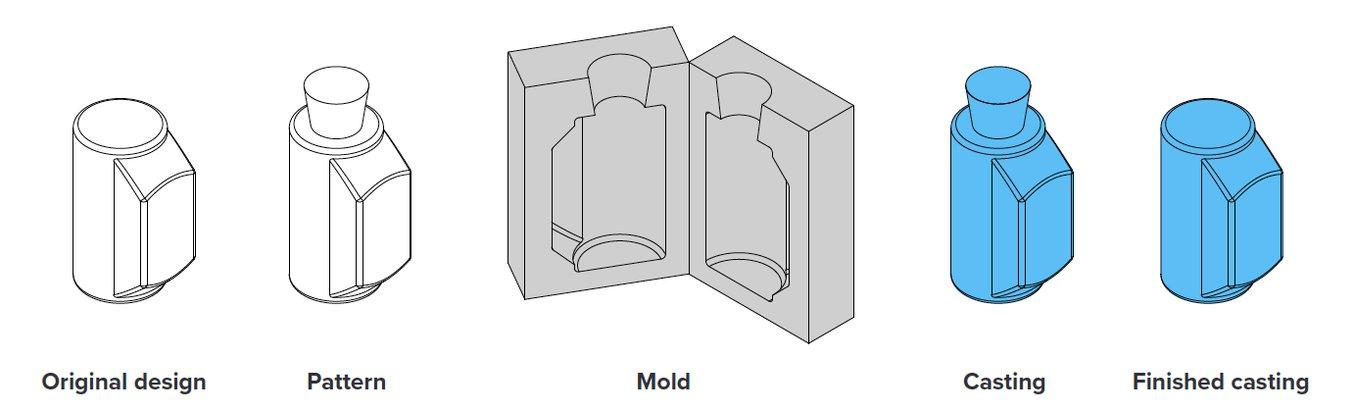
Metal casting step-by-step from the original design through final casting.
Since the advent of metal casting, the methods have evolved and varied. Its core techniques, however, have remained constant. Here is a general step-by-step process for metal casting:
Step 1: Patternmaking
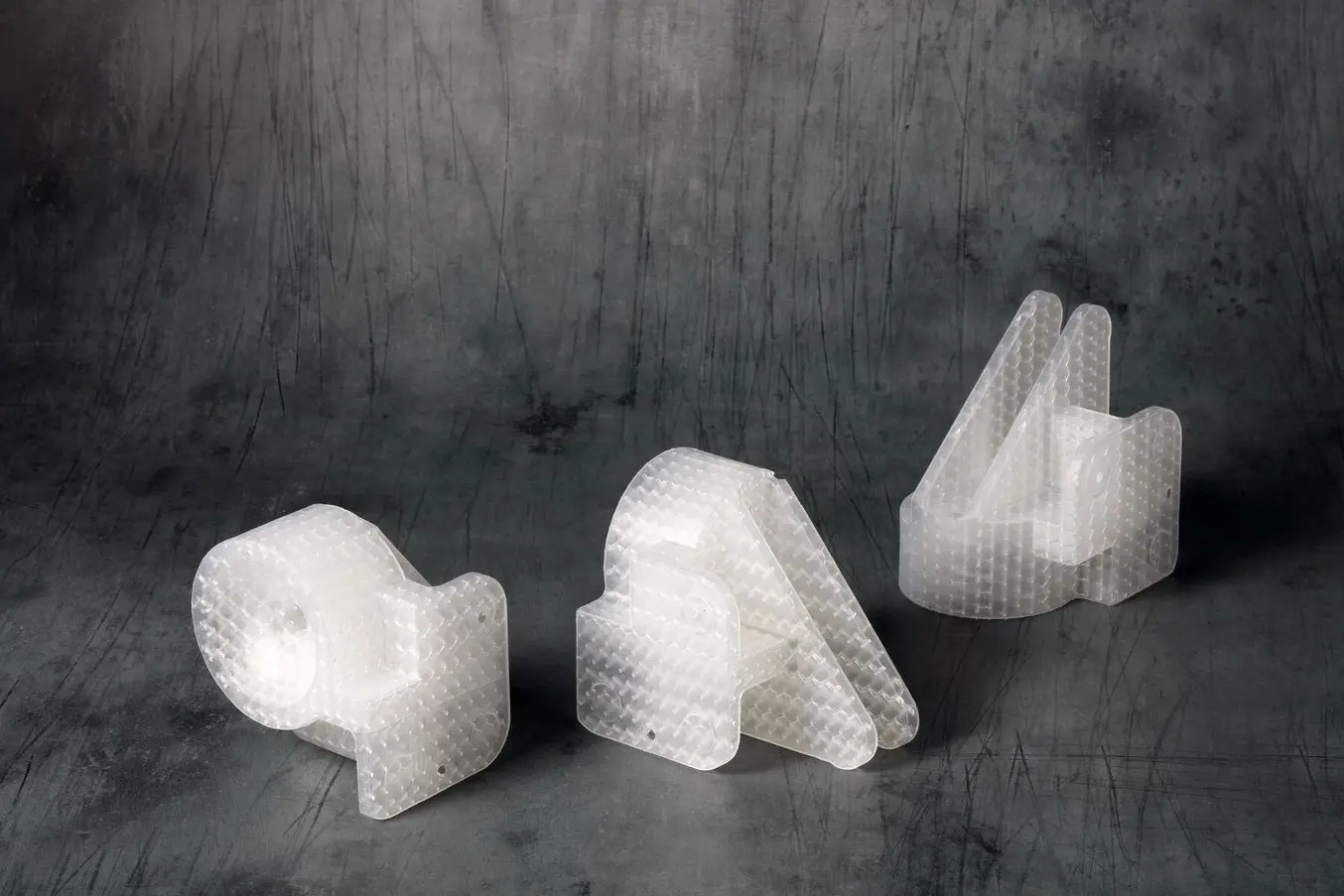
Industrial investment casting patterns 3D printed in Clear Cast Resin.
In order to begin the metal casting process, a manufacturer first must develop a representation of the desired pattern. This pattern is essential in designing the mold used for the cast. It is traditionally made from wood, foam, plastic, or wax and ensures that the mold accurately produces the finished metal part. Today, 3D printing is also a common method to produce patterns, which allows designers to create accurate patterns directly from digital CAD software tools.
A pattern is not an exact replica of the desired part. It has additional elements that make the casting process possible, including gates that allow molten metal to flow at a steady rate and vents for gas to escape. Additionally, patterns are also larger than the parts they represent to account for the shrinkage that occurs during cooling.
When the casting piece is hollow, the manufacturer also creates a core of sand or metal to shape the internal form. This core gets removed upon completion of the casting.
Step 2: Moldmaking
The next step is creating a casting mold, which can be either reusable (non-expendable) or non-reusable (expendable). Non-reusable molds are usually made out of sand, plaster, wax, or by 3D printing, and just as the name suggests, they get destroyed in the casting process. Reusable molds are made out of metal and other durable materials and can be reused for multiple casting cycles.
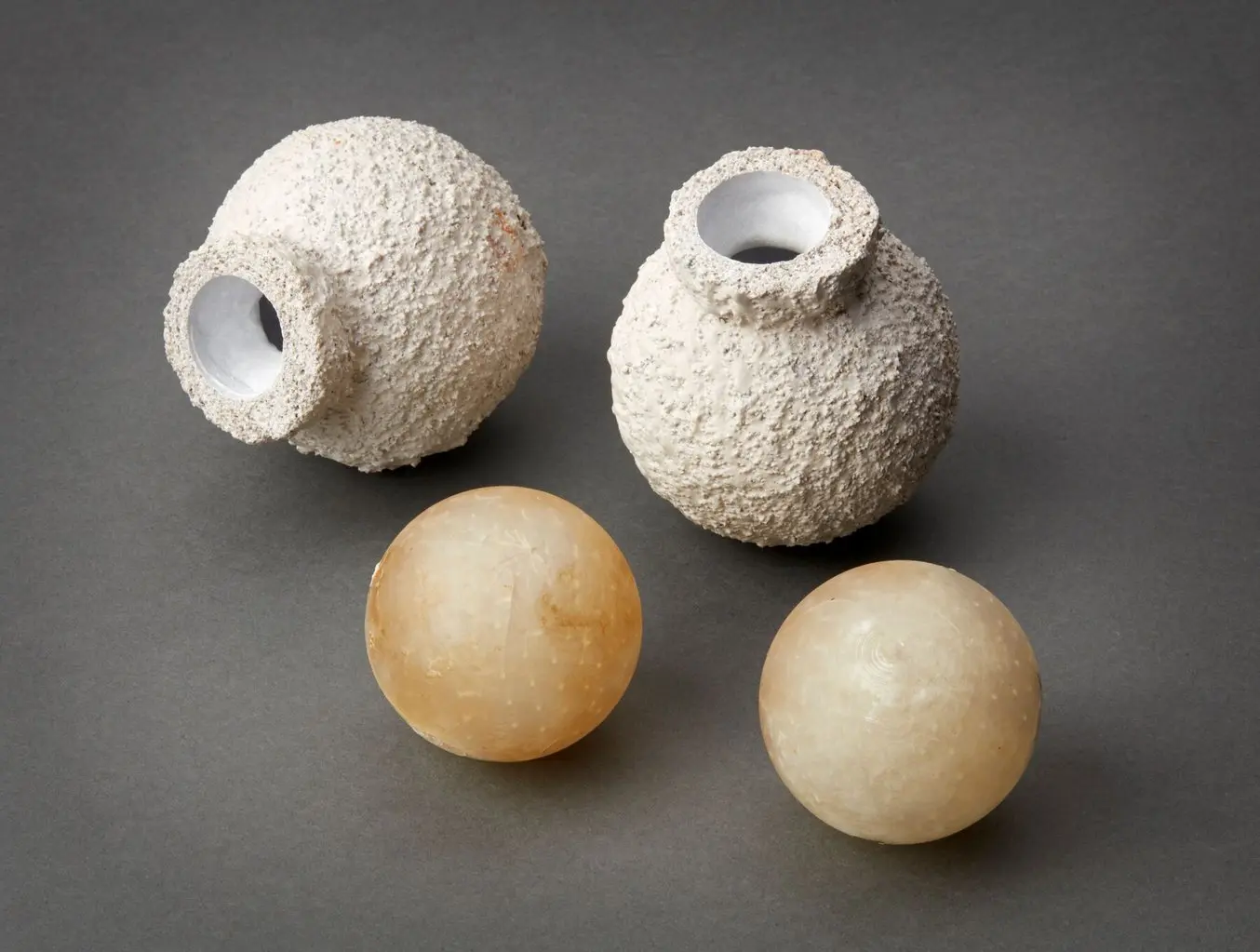
Ceramic shells after burnout and 3D printed patterns in Clear Resin.
Step 3: Melting and Pouring Molten Metal
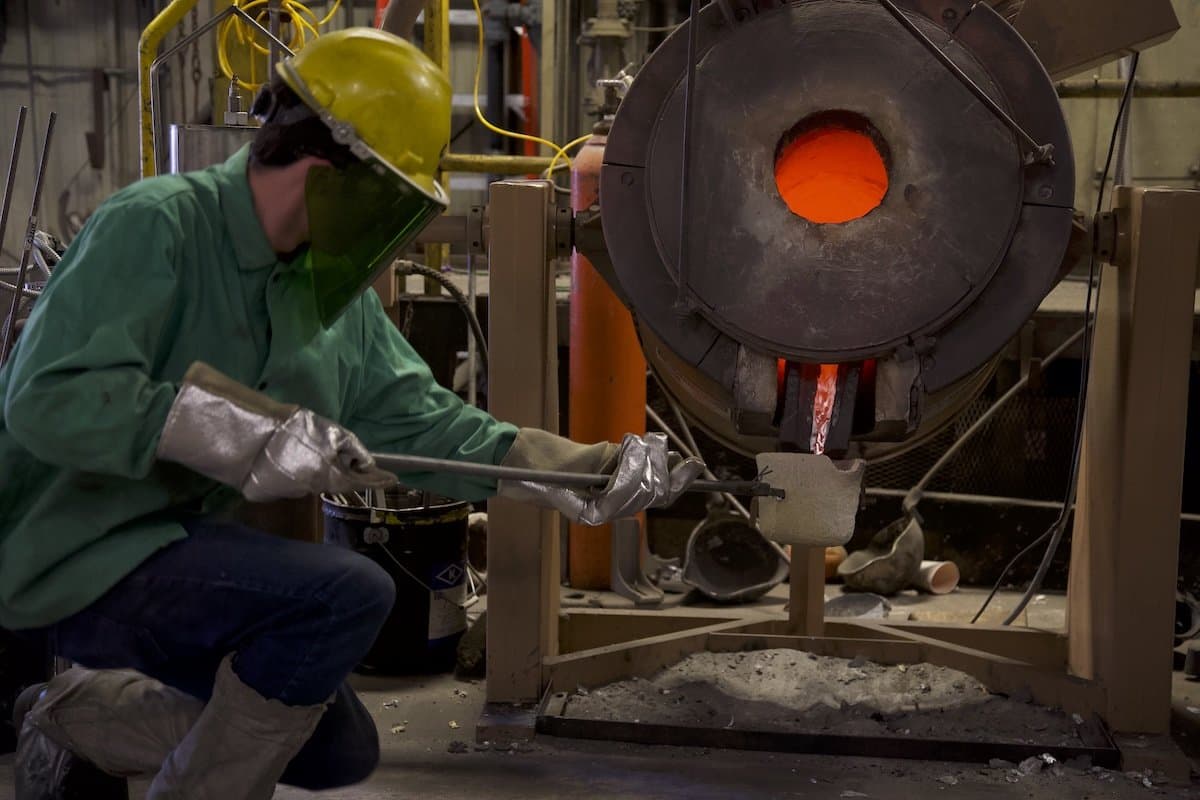
Pouring molten aluminum into a hollow investment.
During this step, the metal gets heated in a furnace until it melts. Depending on the application, manufacturers can use a variety of different metals, with the most commonly cast metals being iron, aluminum, aluminum alloy, steel, copper, and zinc, as well as precious metals like gold and silver. Once the metal melts, the manufacturer pours it into the mold cavity and allows it to cool and solidify.
Step 4: Mold Removal and Cleaning
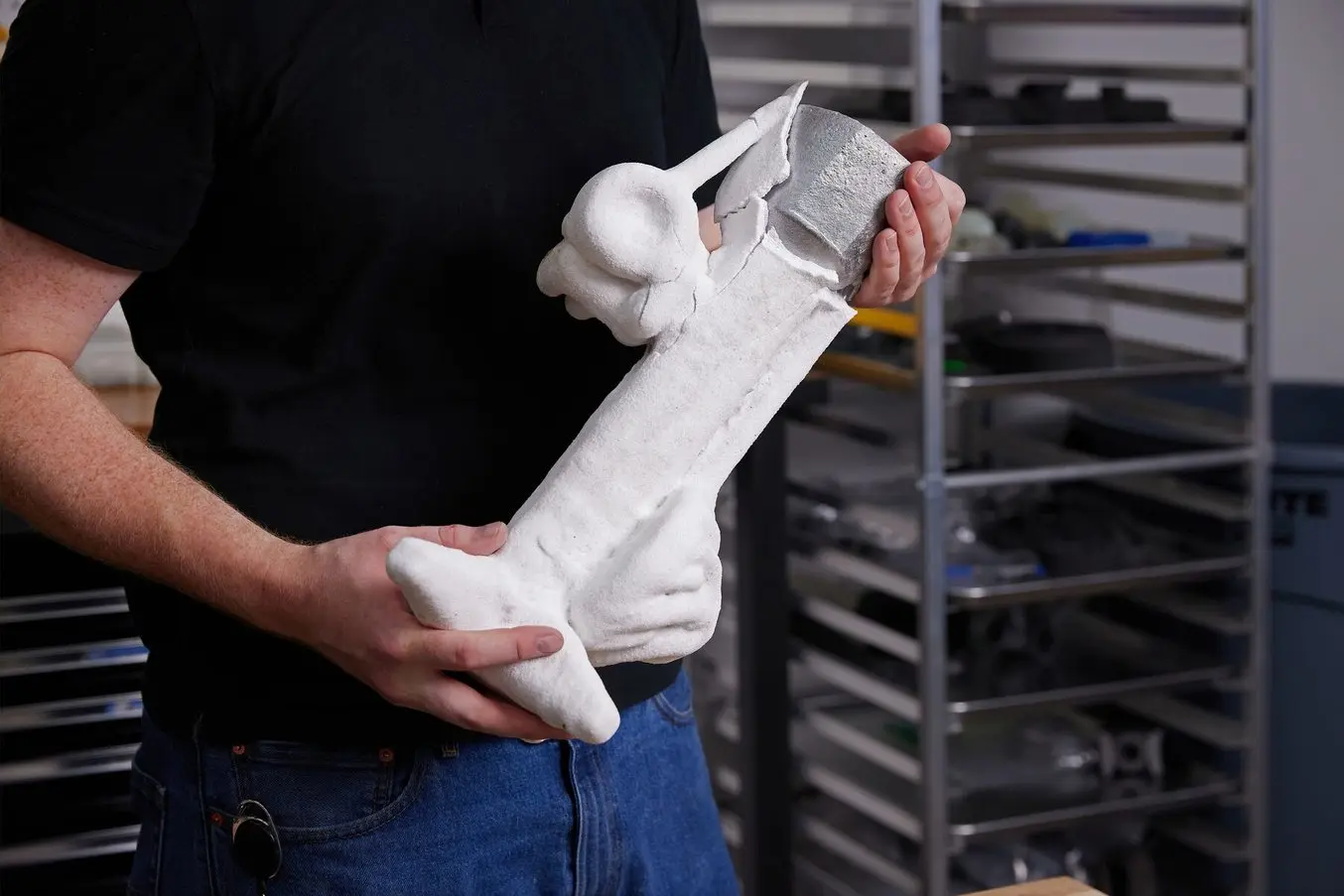
Metal casting post-production.
Once the metal cools down and solidifies, the parts get removed from the mold. Depending on the mold type, this can be done by vibrations in a shakeout process, washing away the investment material, or by ejector pins. Then, excess material, such as vents, gates, and feeders, are removed from the parts. Finally, the parts get filed, grated, machined, or sandblasted to smooth the surface and reach the final shape requirements.
Types of Metal Casting Processes
Though all metal casting techniques share the same core process, there are various methods better suited for different applications. Some of the most common methods include die casting, investment casting, and sand casting.
Die Casting
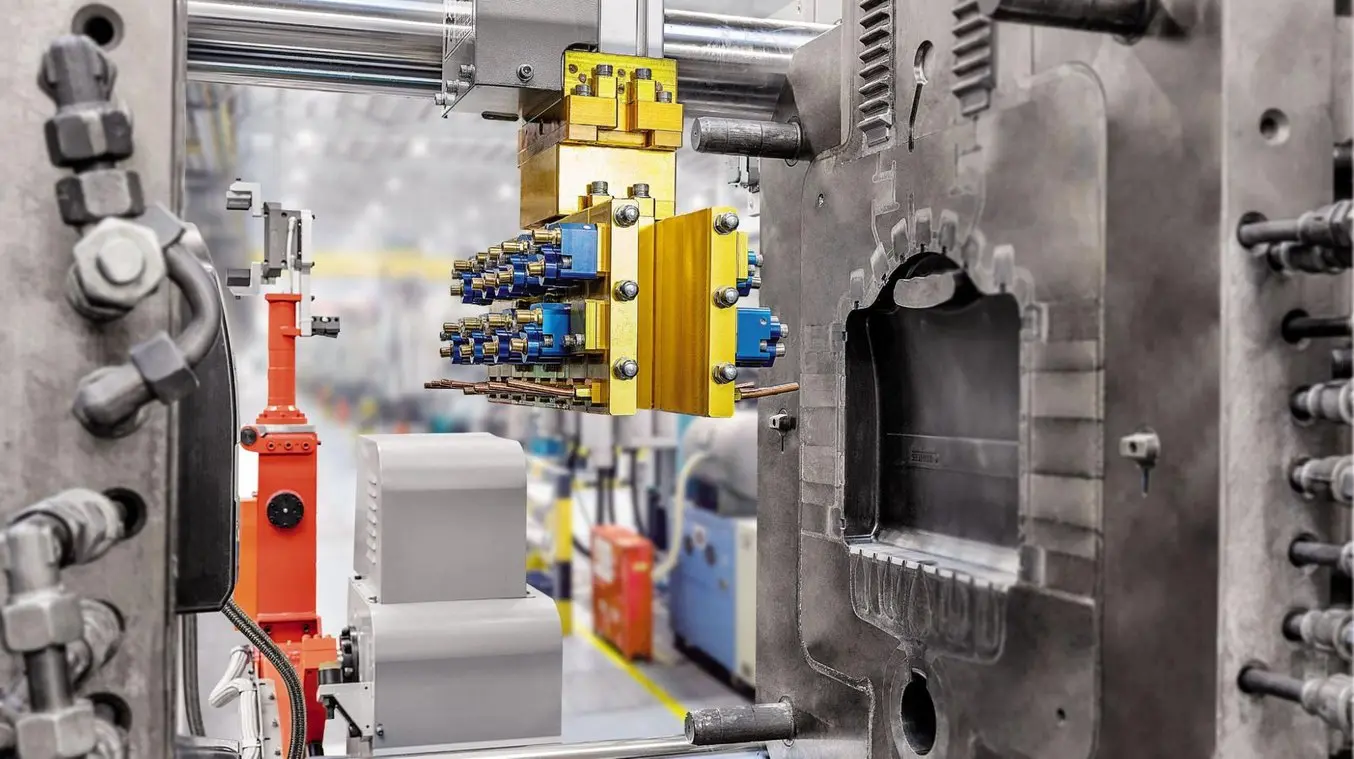
Die casting uses a steel mold and high pressure. (Source: buhlergroup.com)
Die casting is a metal casting process in which a manufacturer pushes molten metal into a steel mold cavity at a high pressure to quickly produce metal parts. In die casting, the manufacturer fixes two halves of a die or reusable mold together and uses a nozzle to inject pressurized molten metal into the die. When the metal cools, the die opens, and ejector pins push out the cast.
The two most common die casting processes are hot-chamber and cold-chamber casting. While the specifics of these processes vary, there are several shared characteristics of the die casting process as a whole.
Hot-Chamber Die Casting
Hot-chamber die casting is the most common of the two main die casting processes. Hot-chamber die casting machines have a built-in furnace to heat the metal within the machine. Once the metal reaches a molten state, the machine lowers a cylindrical chamber into the molten metal. The gooseneck shape of the metal injection system allows the chamber to quickly fill itself, and then push the material into the mold with air pressure or a piston.
Immersing the injection mechanism to fill it allows for rapid and streamlined mold injection in this casting process. Because the chamber is subject to direct heat from the molten metal, however, hot-chamber die casting systems are at risk for corrosion, making them a less viable option for metals with high melting points. Instead, it is better suited for materials with low melting points and high fluidity, like lead, magnesium, zinc, and copper.
Cold-Chamber Die Casting
By contrast, the cold-chamber die casting process works more slowly to avoid corrosion. With this method, a foundry worker ladles molten metal into the injection system. A piston then pushes the metal into the mold.
This process limits the corrosion that is more common in hot-chamber die casting. It is an ideal option for metals with high melting points, like aluminum and aluminum alloy.
Advantages of Die Casting
The die casting process is rapid and produces highly detailed parts. It is ideal for the production of high volumes of complex parts and can also produce strong parts with smooth surface finishes. Die casting’s capacity to produce a high volume of parts makes it a crucial process in the automotive and aerospace industries.
Disadvantages of Die Casting
As die casting tooling and equipment are expensive, this process is not cost-effective for smaller production runs. In addition, the malleability of metals used in the process can impact the complexity of the product.
Investment Casting
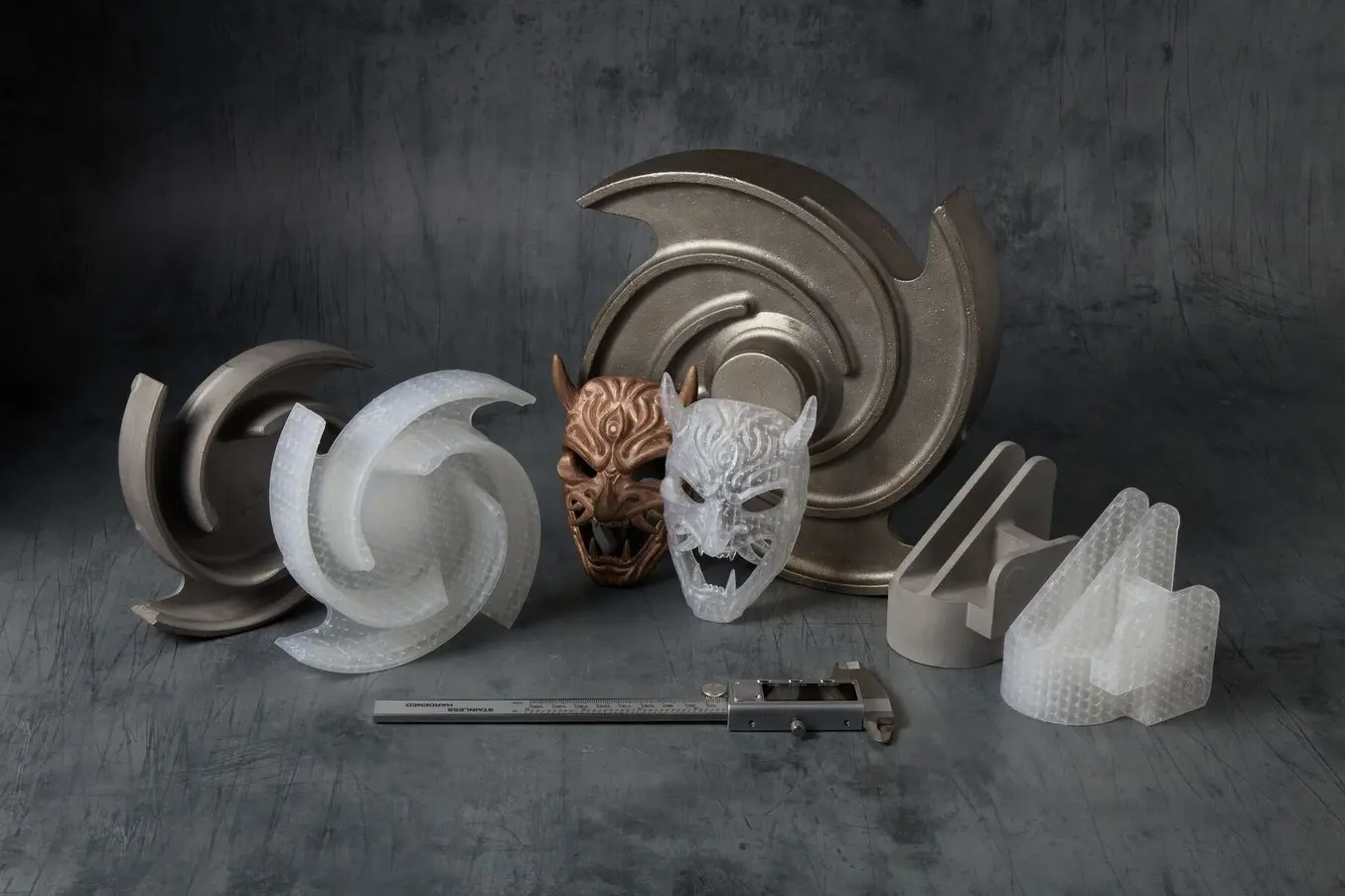
Cast parts from 3D printed patterns produced with Clear Cast Resin on a Formlabs resin 3D printer.
Investment casting, also known as lost-wax casting, is a process that uses wax, slurry, and molds to produce complex parts. It is one of the oldest metal casting techniques but is still valued for its ability to create precise metal parts with intricate shapes.
This process is still widely used for producing jewelry, dentistry, and art. Its industrial form, investment casting, is a common way to create precision metal parts in engineering and manufacturing.
Investment casting patterns are typically made out of wax or 3D printed polymers. The patterns are assembled into a tree-like structure and dipped into a slurry of silica, or put into a flask and surrounded by the liquid investment plaster. After the investment material dries, the flask is placed upside down into a kiln, which melts the pattern, leaving a negative cavity in the shape of the original model. Metal is melted and then poured, using gravity or vacuum pressure to pull the metal into the cavity. The casted parts are filed, ground, machined, or sandblasted to achieve final geometry and surface finish.
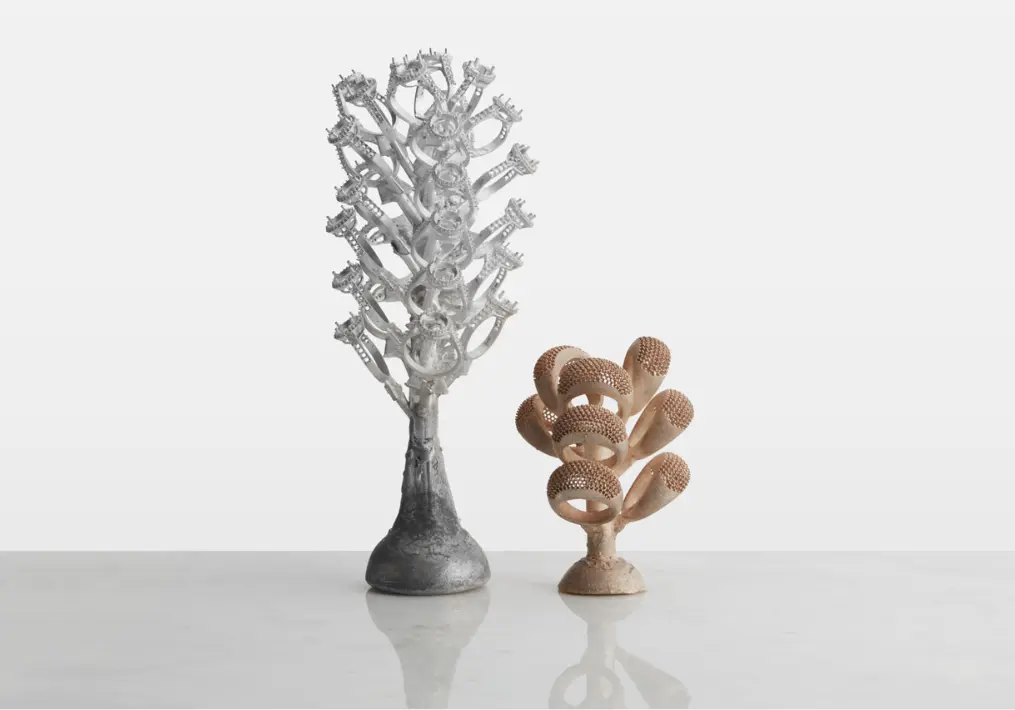
Sprue trees with cast rings.
Clear Cast Resin, Castable Wax Resin, Castable Wax 40 Resin, and True Cast Resin can all be used to 3D print parts for investment casting. Material selection depends on the features of an individual part. Castable Wax Resin is suitable from lightweight to medium jewelry, True Cast Resin for medium-weight jewelry and engineering components up to 5 mm thick, and Clear Cast Resin for parts over 3 mm thick.
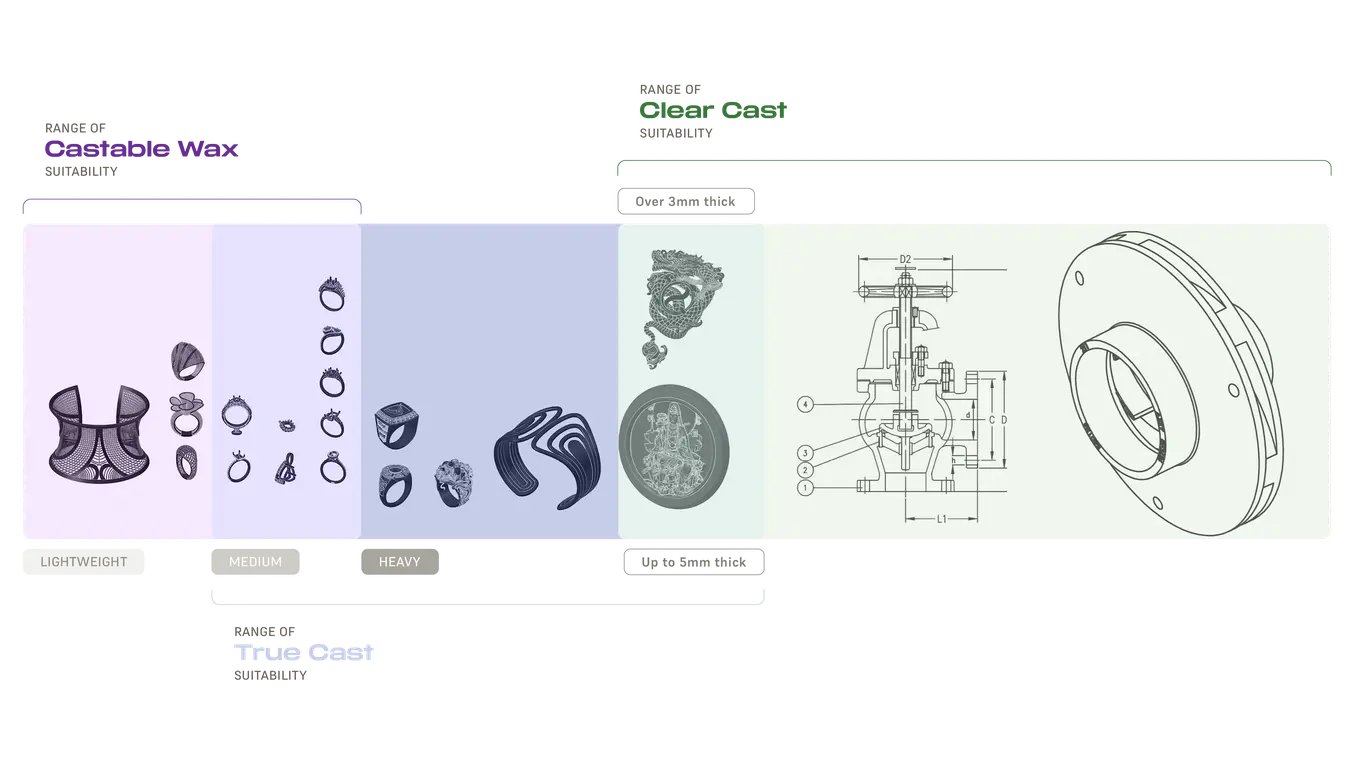
Advantages of Investment Casting
Investment casting is a versatile process. It allows manufacturers to produce accurate and repeatable parts out of nearly any metal available for casting and complicated shapes that would be difficult or impossible with other casting methods. Casted parts also have excellent surface qualities and low tolerances, with minimal surface finishing or machining required.
These features make investment casting ideal for complex parts in automotive, aerospace, and industrial applications, medical tools, dental implants, as well as fine jewelry and art.
Disadvantages of Investment Casting
Investment casting is a complex and labor-intensive process. It requires specialized equipment, costly refractories and binders, as well many manual operations to make a mold. It can be difficult to cast parts that require cores and the process is better suited to small parts.
Sand Casting
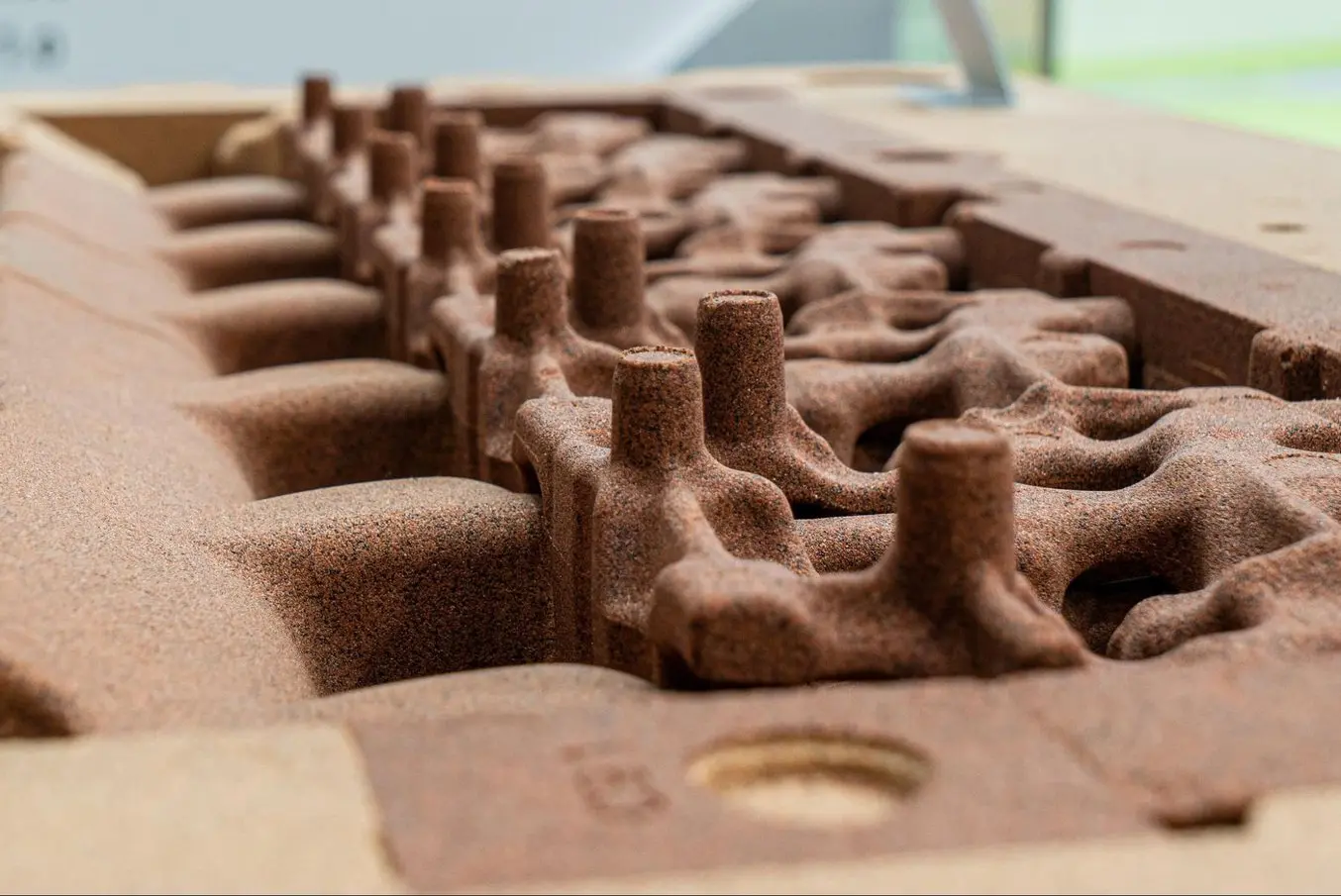
One half of a sand casting mold.
Sand casting is a metal casting method that was first in use 3,000 years ago but remains the most widely used casting method to this day. This process allows manufacturers to cast metal without relying on machining.
In the sand casting process, the manufacturer first creates a foundry pattern, or replica of the casting, most commonly from wood or plastic. The pattern is oversized to allow for shrinkage. Parts with features on one side only require an open-faced mold. For parts with multiple detailed surfaces, the manufacturer separates the foundry pattern into two mold boxes to form a closed cavity mold. The top half is called a cope and the bottom a drag.
Once the manufacturer creates the pattern, they tightly pack sand around the pattern. Then, they add sprues and gates to ensure that the molten metal flows smoothly through the mold cavity. The manufacturer removes the pattern then clamps the two halves of the sand mold together. Once the metal melts to a molten state, it is poured into the mold and left to cool. From here, the sand mold is removed using vibrations or high-pressure water. Finally, the manufacturer refines the part by removing sprues and gates, and polishing the cast metal part.
Advantages of Sand Casting
Sand casting is an adaptable process that functions outside the limitations of machinery. Because of this, it can create complex parts of virtually any size. Sand is inexpensive and plentiful, which lowers the setup cost and makes modifications possible. It is the only practical or economical way to produce very large castings. The lead time of sand casting is also short, making it a viable process for short production runs.
Sand casting’s versatility makes it a manufacturing option across a wide array of industries. It can produce medical equipment, automobile parts, electronic equipment, gas tanks, and engine blocks, and more.
Disadvantages of Sand Casting
Sand casting creates highly porous, textured metals. The shrinkage and rough surface finish also lower the dimensional accuracy of parts. This results in a low-strength final product that requires time-consuming post-processing to achieve a higher quality finish.
Selecting the Right Metal Casting Process
In order to choose the right industrial metal casting process, several factors must be considered. We’ve created this comparison table to help you compare die casting, investment casting, and sand casting in terms of types of metals, production volume, costs, production time, part complexity, and for which industries they are generally used.
Die Casting | Investment Casting | Sand Casting | |
---|---|---|---|
Compatible metals | Aluminum, copper, lead, magnesium, zinc | Most metals | Most metals |
Production volume | High volume | Low to high volume | One-off to medium volume |
Unit costs | Low | Moderate to high | Moderate |
Tooling costs | High | Moderate | Low |
Cycle time | Rapid | Long | Moderate |
Industries | Automotive, aerospace, consumer products, furniture, power tools | Automotive, aerospace, jewelry, medicine, dentistry, art | Automotive, aerospace, industrial equipment, electronics, consumer products |
Metal Casting With 3D Printing
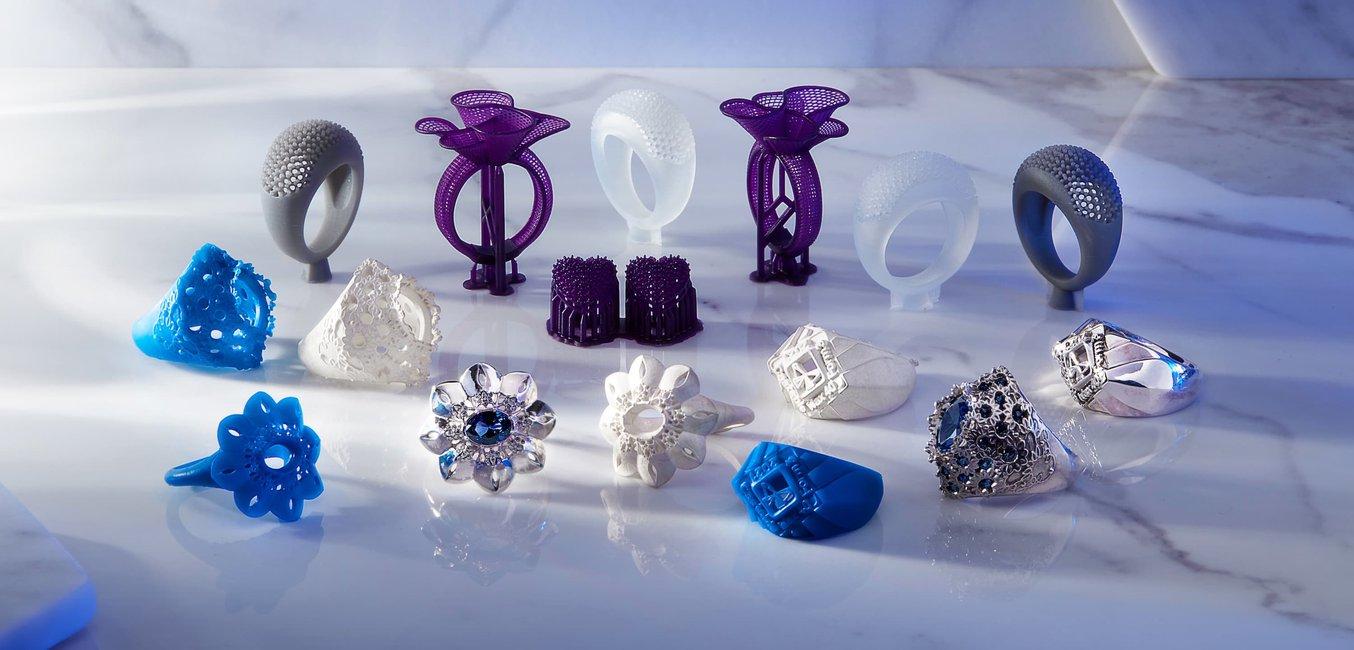
3D printed jewelry patterns and cast metal rings.
Engineers, designers, jewelers, and hobbyists can capitalize on the speed and flexibility of 3D printing by combining castings processes like indirect investment casting, direct investment casting, pewter casting, and sand casting with 3D printed patterns or casting metal into 3D printed molds. Cast metal parts using 3D printed rapid tooling can be produced in a fraction of the time invested in traditional casting and at a significantly lower cost than metal 3D printing.
Stereolithography (SLA) 3D printers offer high precision and a broad material library that is well-suited for casting workflows and can produce metal parts at a lower cost, with greater design freedom, and in less time than traditional methods.
Indirect Investment Casting
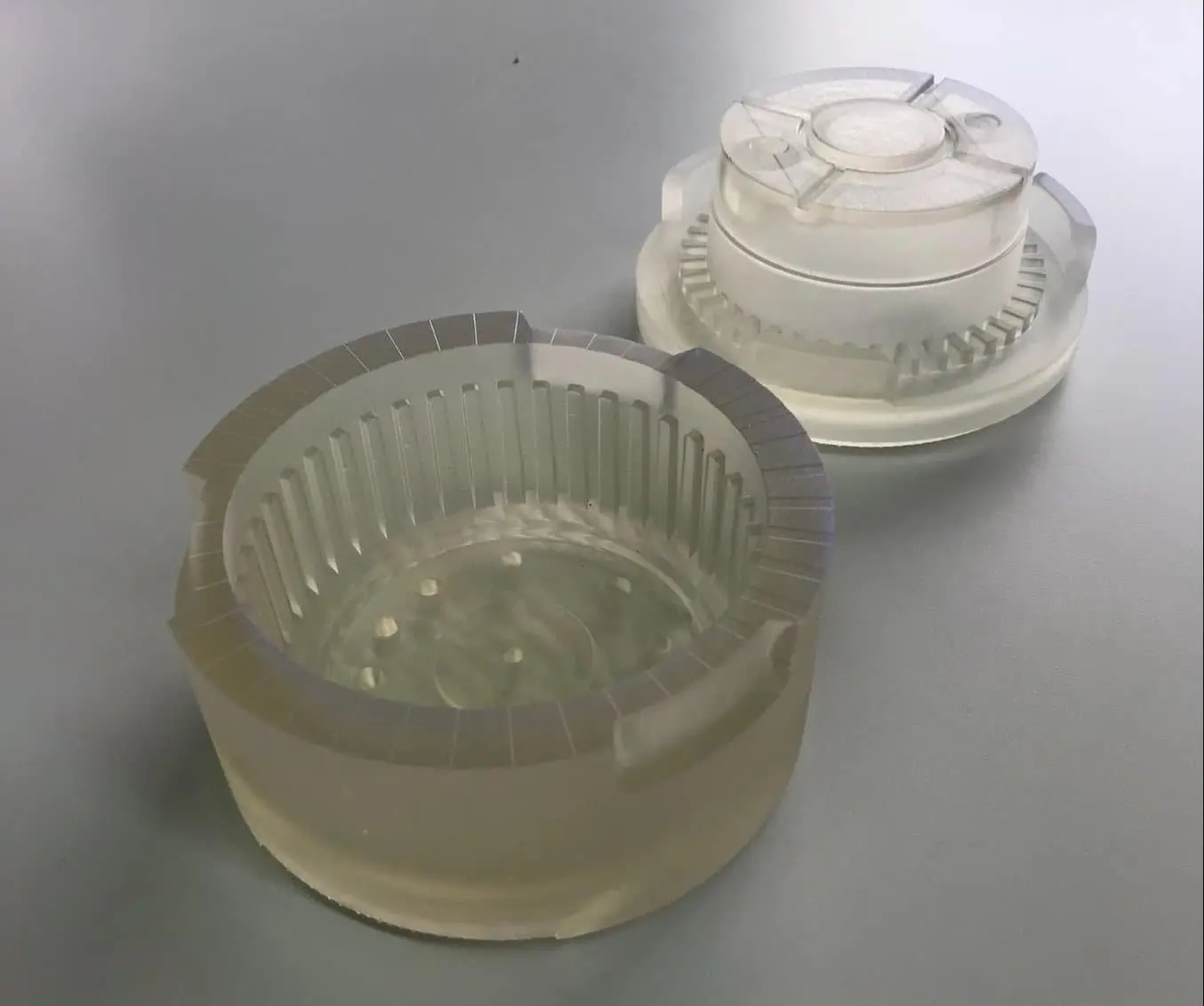
A 3D printed mold in Clear Resin for wax injection.
The process of making patterns from molds or tooling is referred to as indirect investment casting because it requires creating molds for producing the patterns in addition to final investment molds.
Rigid molds for wax (often referred to as tools) are commonly fabricated by machining aluminum or steel. Machined metal molds cost thousands of dollars to produce and take weeks of machining and polishing work before first shots can be run and pattern parts evaluated within a casting process.
With 3D printing, manufacturers can directly 3D print the mold for their pattern using materials like High Temp Resin or Rigid 10K Resin, resins with high-temperature resistance. For an optimal surface finish of molded parts, treat the interior surfaces of the mold by sanding and polishing for a smooth look, or bead blasting if a uniform matte look is desired. To ensure the final cast parts are dimensionally accurate, compensate for shrinkage by scaling up the printed mold. The exact shrinkage of the wax and the casting process can be obtained from supplier specifications.
3D printed molds for metal casting shorten the time between concept and first tests to a matter of days because manufacturers can directly print the tooling necessary for running and evaluating parts.
While molded pieces must follow design rules for moldability (e.g., no undercuts, draft is beneficial, etc.), you can achieve increased pattern complexity by using assembly jigs to combine multiple components into a single structure.
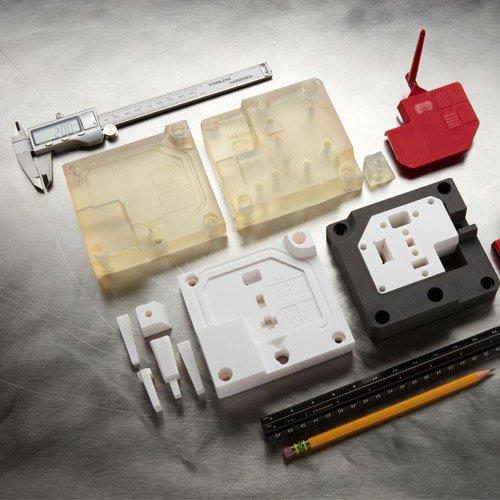
Moldmaking with 3D Prints: Techniques for Prototyping and Production
Download our white paper to learn about six moldmaking processes that are possible with an in-house SLA 3D printer, including injection molding, vacuum forming, silicone molding, and more.
Direct Investment Casting
Direct investment casting is a version of investment casting where the process moves directly from pattern creation to surrounding the pattern with investment material. It is ideal for producing parts with geometries that are too complex to be molded or for parts with extensive undercuts and fine surface texture details, where molding is possible but carries high tooling costs.
Traditionally, patterns for direct investment casting are carved by hand or machined if the part is a one-off or expected to be only a handful of units. With 3D printing, however, manufacturers can directly 3D print the patterns, removing the design and time constraints common in other processes.
With 3D printers, engineers, designers, and jewelers can directly 3D print patterns in order to achieve shorter lead times and geometric freedom that exceeds the design for manufacturability constraints of molding processes. Formlabs developed a range of castable 3D printing materials suitable for direct investment casting, particularly for industrial investment casting and casting jewelry.
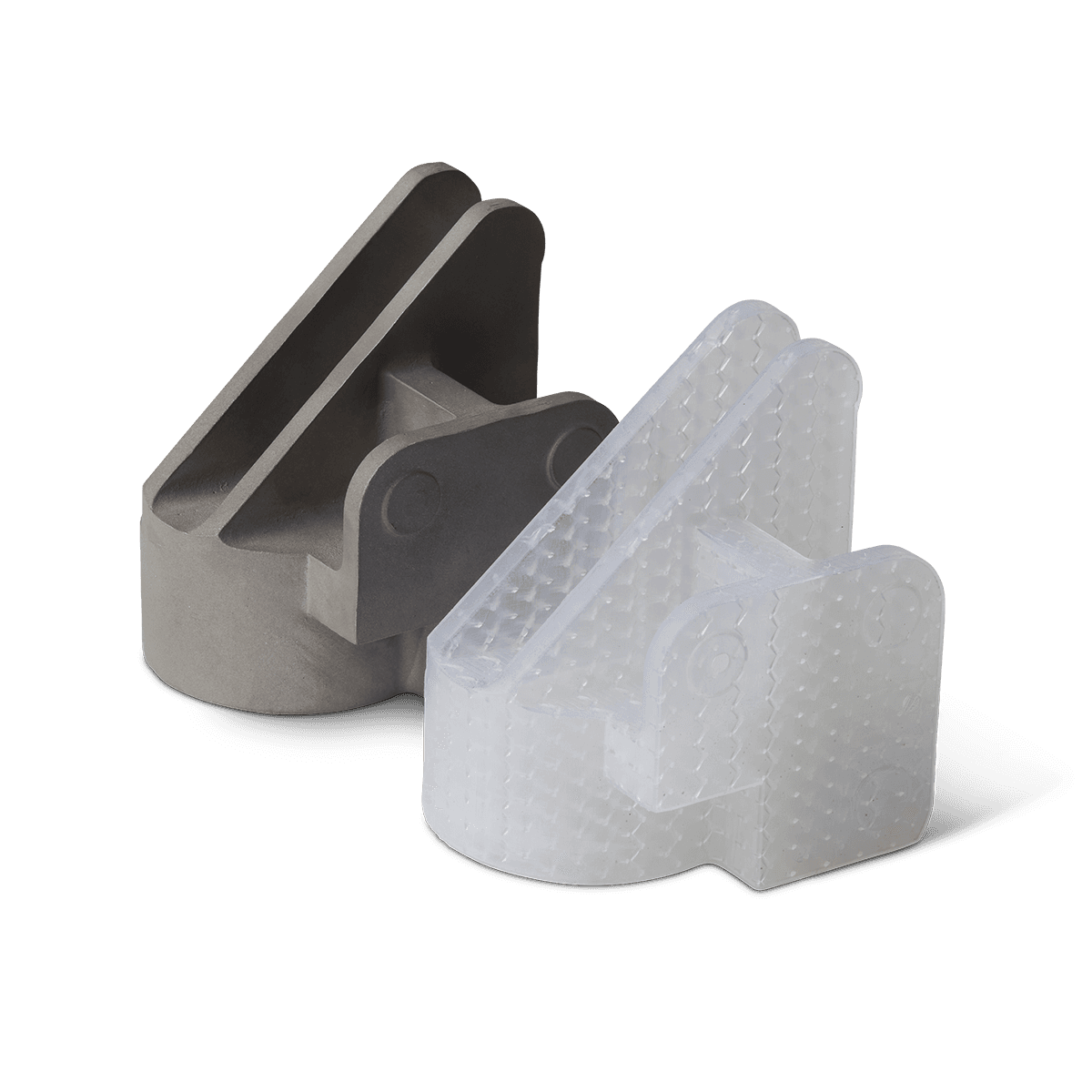
Industrial Investment Casting With 3D Printed Patterns Using Formlabs Clear Cast Resin
This white paper presents the methods by which several established foundries were able to cast metal parts using 3D printed patterns produced by Formlabs’ stereolithography (SLA) 3D printers.
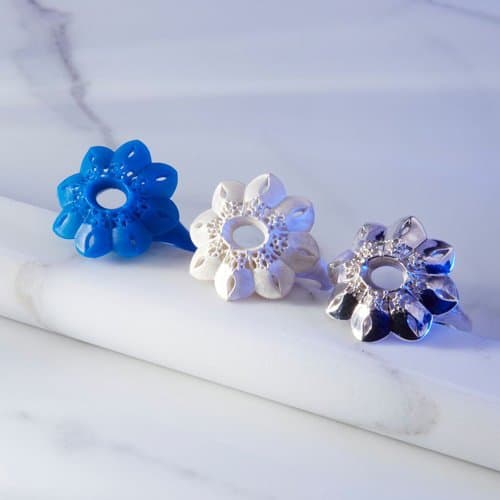
Introduction to Casting for 3D Printed Jewelry Patterns
The way jewelers work is changing, and castable photopolymer resins are leading the way. In this guide, learn how to cast fine jewelry pieces 3D printed on Formlabs printers.
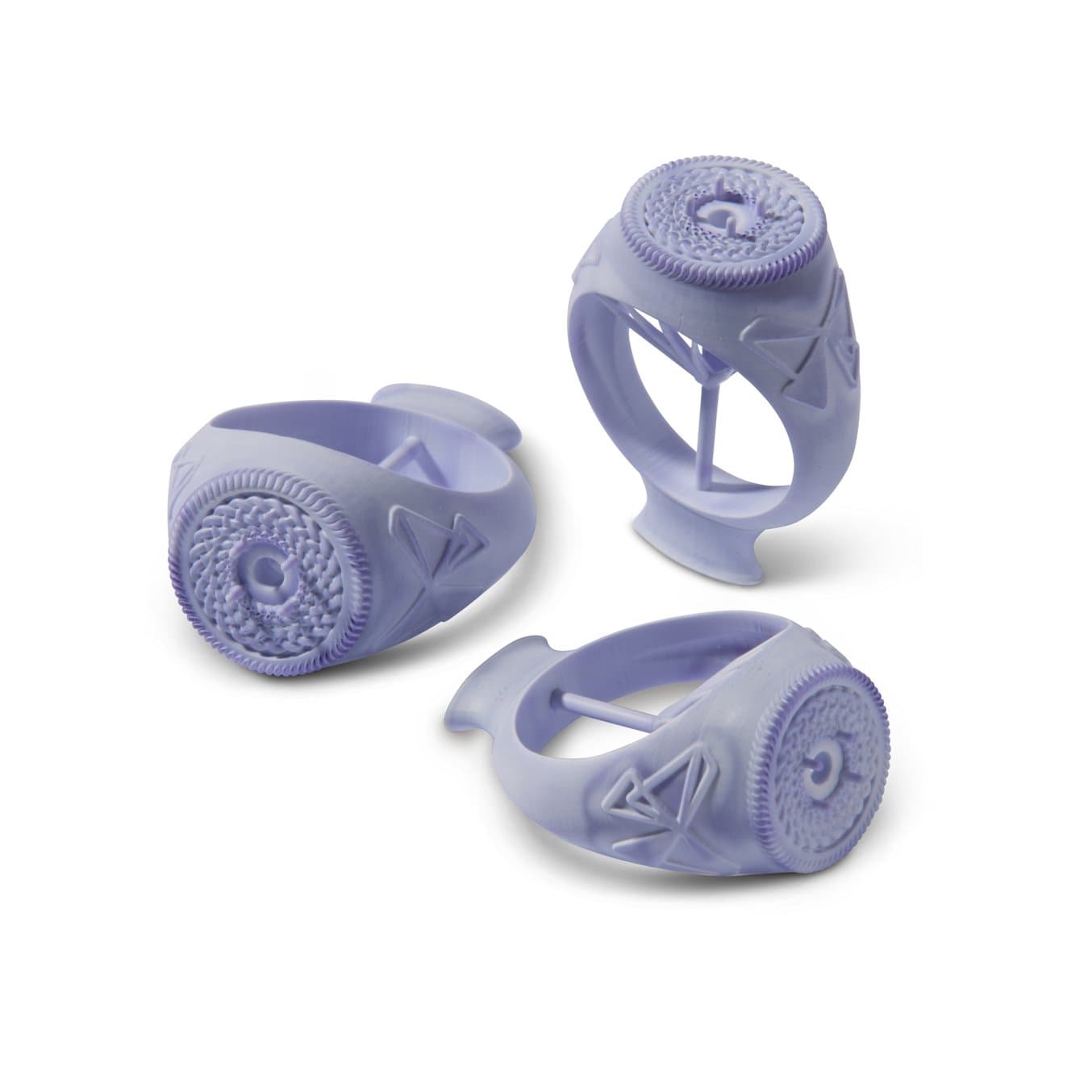
Request a Free Sample Part
See and feel Formlabs quality firsthand. We’ll ship a free sample part to your office.
Sand Casting
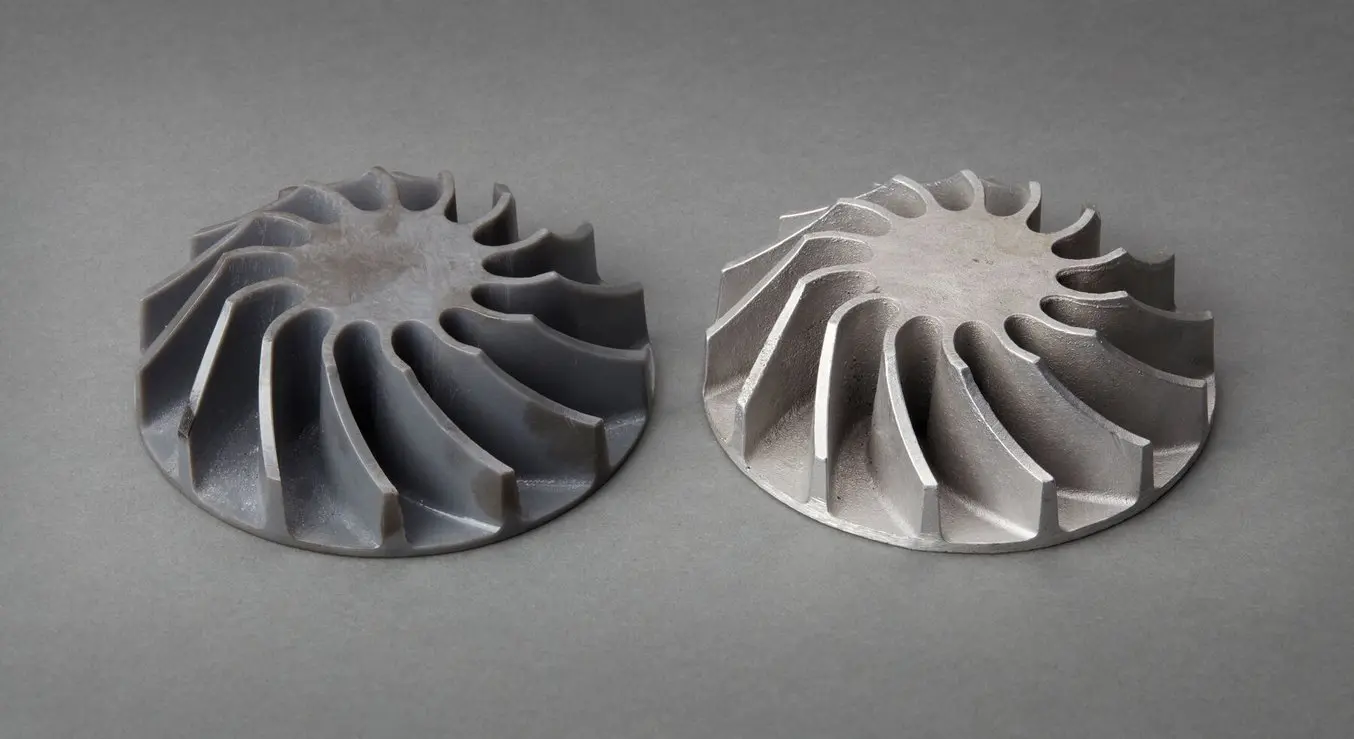
Grey Resin printed pattern and finished aluminum casting from an open-faced sand mold.
Similar to investment casting, 3D printing can be used to create patterns for sand casting.
In comparison to traditional materials like wood, 3D printing allows manufacturers to create complex shapes and go straight from digital design to casting.
Pewter Casting
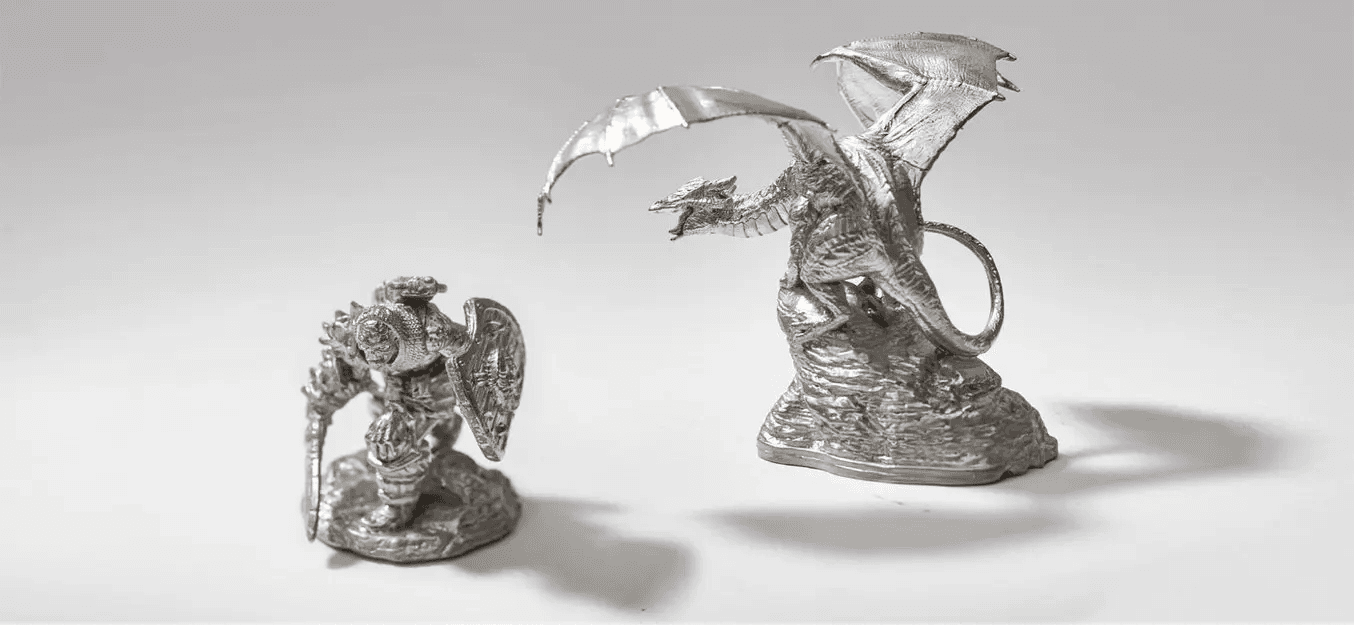
Metal Miniatures made with pewter casting and 3D printing.
Pewter is a malleable metal alloy with a low melting point that can be used for making fully metal objects for decorative applications such as detailed metal miniatures, jewelry, scale models, and replicas of antiques.
With recent developments in temperature-resistant 3D printing materials, like High Temp Resin for Formlabs SLA 3D printers, it’s now possible to 3D print molds for direct pewter casting.
There are two options for mold designs: a sacrificial or pull-apart mold. In a sacrificial mold, there is a shell designed to be broken apart in the process. Pull-apart molds function with separate halves so the mold can be reused.
Compared to directly printing metal, the casting pewter in 3D printed molds offers significantly better detail and surface finish at a small fraction of the cost. Compared to wax casting, directly 3D printing a mold has fewer steps and requires less manual effort, while preserving the most possible detail.
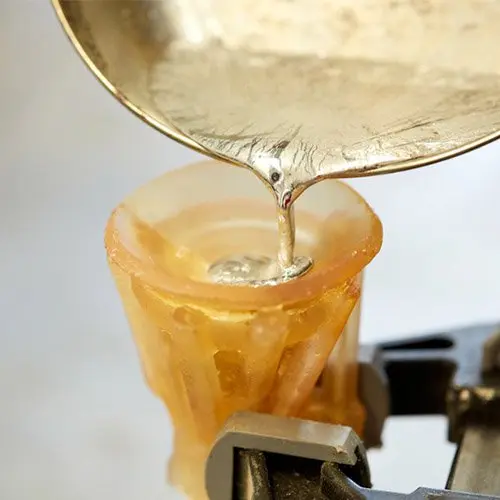
Metal, Ceramic, and Silicone: Using 3D Printed Molds in Advanced Hybrid Workflows
Watch our webinar to learn how moldmaking using 3D printed masters and reusable or sacrificial molds can allow you to produce parts in porcelain, precious and non-precious metals, silicone and biocompatible flexible materials, and more.
When to Combine 3D Printing and Metal Casting
Businesses looking to boost design freedom or cut costs and lead times have a strong solution in metal casting with 3D printing.
Certain types of complex metal castings, such as large shapes with cross-sections and pieces with multiple cores, are difficult to create using traditional metal casting methods. 3D printing allows manufacturers to produce these complex designs. For example, foundries or jewelers can create intricate and custom designs that might be impossible without a 3D printed pattern.
3D printing also eliminates reliance on multiple machines or service providers to create parts. Instead, companies just need a digital file, a 3D printer, and printing material. This can cut costs and waste, as all the material used goes into the final product.
Finally, the combination of 3D printing with metal casting can cut costs and lead time. Rather than waiting weeks for expensive tooling before being able to cast a final product, a 3D printer can create a pattern or mold in hours.
Diversified Metalsmiths, Inc. has incorporated modern technologies into their metal casting workflow to reduce costs, improve lead times, and increase agility. With the Form Series stereolithography (SLA) 3D printers and Clear Cast Resin, Diversified has been able to print patterns in-house quickly and affordably, without changing up their casting workflow or relying on external providers.
“Our main reason for purchasing the 3L was pattern cost… Even amortizing the 3L and associated equipment, we will at a minimum break even on costs for our current order, and save over $200 per part on upcoming orders. There is very little difference in our process, both before and after casting, between the PMMA and Clear Cast Resin SLA patterns."
John Farr, VP of Technology, Diversified Metalsmiths
3D Printer for Metal Casting
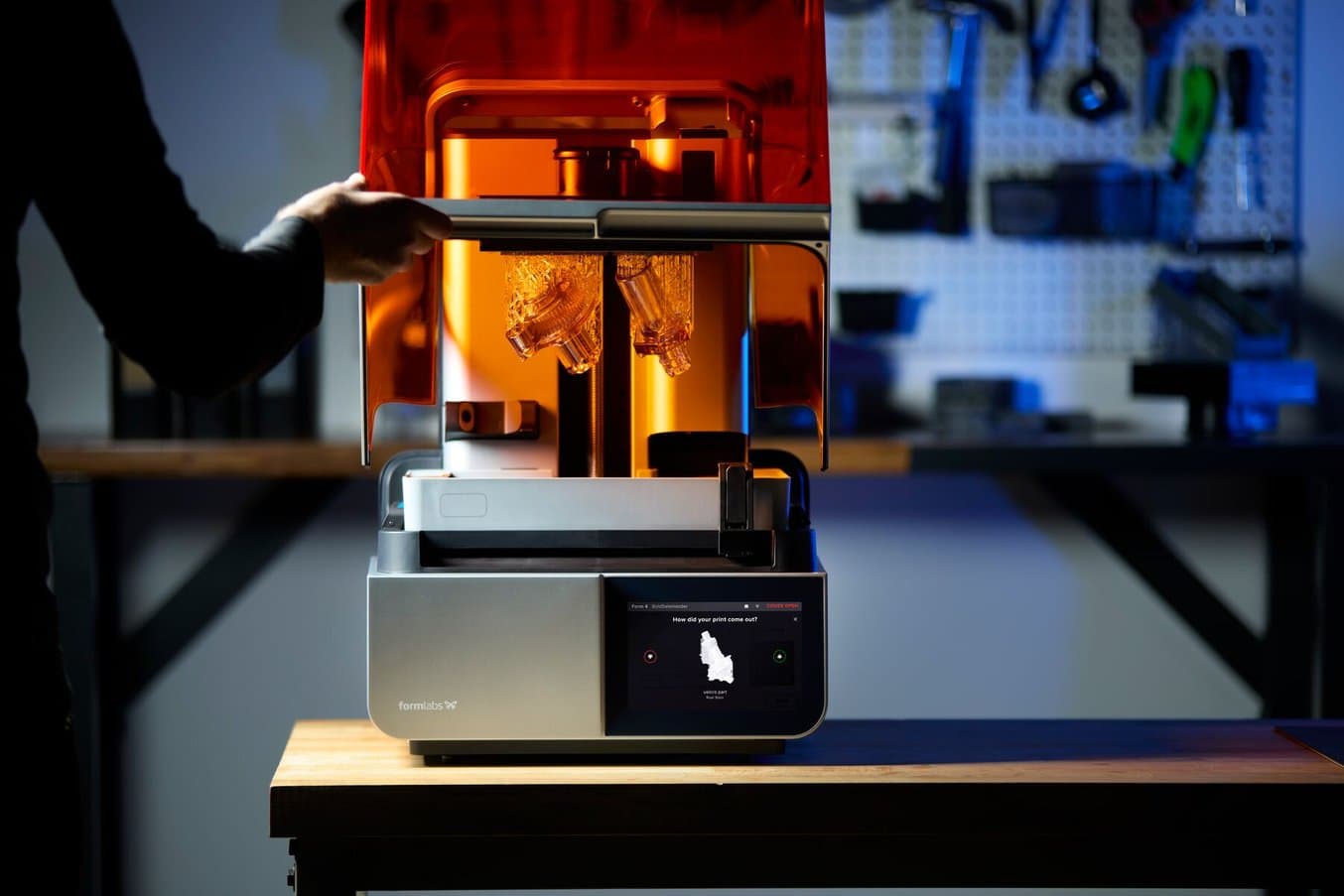
Metal casting combined with 3D printing helps companies quickly and efficiently create metal parts. With a Formlabs SLA 3D printer, you can expedite the metal casting process and cut costs along the way.
Learn more about Formlabs resin 3D printers or contact our 3D printing experts if you have any questions.