MOSOLF Special Vehicles GmbH is a leading special vehicle manufacturer based in Kippenheim, Germany. With close to 50 employees, the company produces around 1000 special and emergency vehicles per year. Among their customers are the German state and federal police forces, the defense sector, disaster control and technical relief organizations, municipalities, and industrial customers, all of whom require vehicles with high degrees of customization and advanced performance.
In the automotive industry, most parts are manufactured through mass production processes like injection molding, which are cost-effective for standard production runs of hundreds of thousands of units. MOSOLF’s clients, however, require a diverse range of custom and low-volume parts, where tooling costs render traditional manufacturing methods economically unfeasible. For MOSOLF, 3D printing presents an ideal solution.
“I estimate that every third police van [in Germany] now contains additively manufactured parts. At MOSOLF, we are now so far advanced with 3D printing that there is no vehicle that leaves our yard without an additively manufactured part in it. We now 3D print around 5,000 parts per year, but we are on an upward trend, which means that we have at least three parts in every vehicle if not more.”
Carsten Busam, Head of Project Planning, MOSOLF Special Vehicles GmbH
Read on to learn how MOSOLF uses selective laser sintering (SLS) 3D printing with the Fuse Series to produce a wide range of end-use parts for police vans and other special and emergency vehicles.
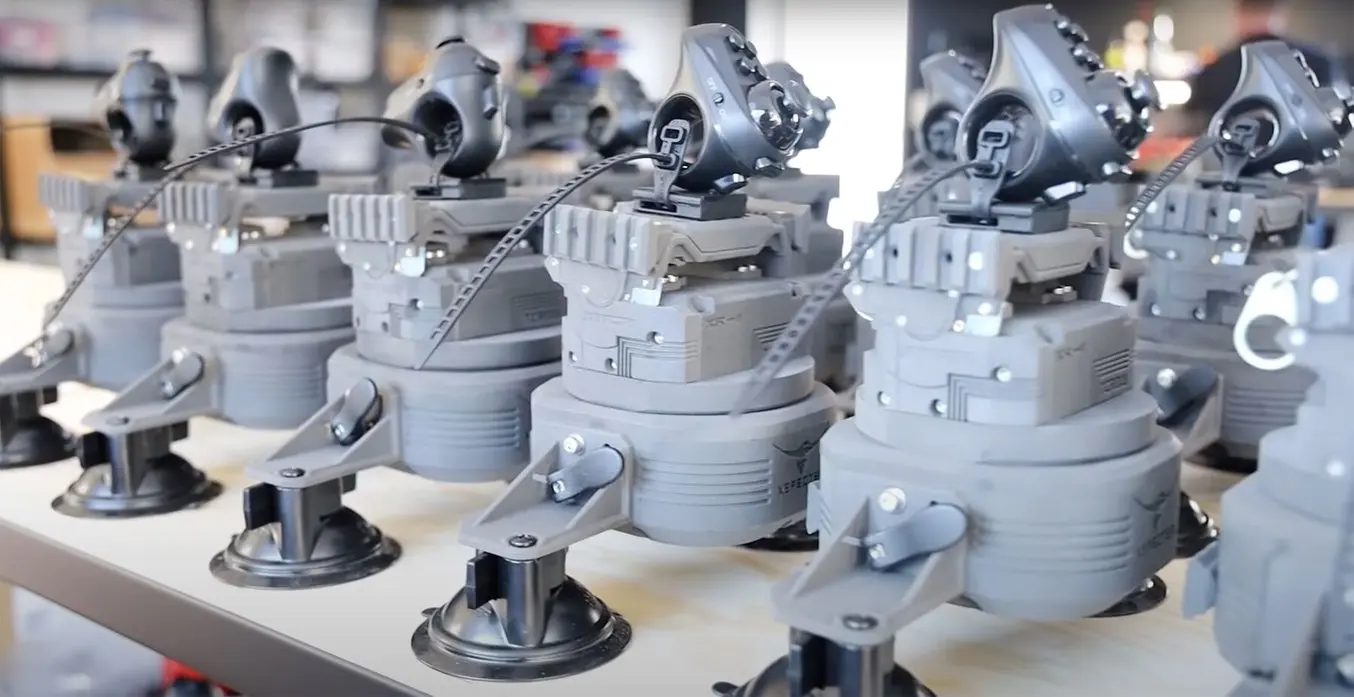
SLS for End-Use Production
3D printing for end-use production is not only possible, it's more affordable, agile, and scalable than ever with the Fuse SLS Ecosystem. Compare production methods, learn about bulk powder pricing, and see production in action for 15 different manufacturers currently using the Fuse Series.
Custom Solutions to Fit the Needs of 17 Police Forces in Germany
“Our biggest challenge is the variety,” says Busam. Each state and branch of the police force purchases several different types of vehicles — and each individual vehicle can then require customized features depending on its specific purpose. The components that have to be built in also vary — for example, different forces use radio or signaling systems from different manufacturers. This means that each vehicle requires a large quantity of custom parts.
“We manufacture vehicles for 17 police forces in Germany and everyone has their own idea of what the ergonomics should look like and how they want it to be operated. Accordingly, the quantities are usually comparatively high when it comes to the basic design, but when you add the degree of customization, they are small again,” said Busam.
MOSOLF’s team builds on series vehicles, which means that they take commercially available cars, trucks, and vans, and retrofit them to spec. The team has to find the appropriate installation location for each requested feature and make sure that it’s ergonomic, durable, and aesthetic. In older models, finding installation sites was easier — they have multiple empty spaces within a dashboard or console for MOSOLF to adapt. Newer models have proven to be a challenge.
“Vehicles are becoming increasingly cluttered with displays. There are no longer any service bays in the vehicles. There are some storage compartments and a charger for the cell phone, but it is a challenge to find installation spaces where all the controls can be accommodated. Especially in concealed vehicles, where you shouldn't be able to see that it's in fact a police vehicle,” said Busam.
MOSOLF’s journey with 3D printing started in 2016 when the Bavarian police force placed an order for their entire fleet of vehicles and motorcycles to be fitted with new, digital radios.
“We had to find an individual solution for each vehicle and each motorcycle. Had we formed all parts from sheet metal, it'd have been incredibly time-consuming or the solutions wouldn’t have been particularly pretty, so we took the first step into the 3D world.”
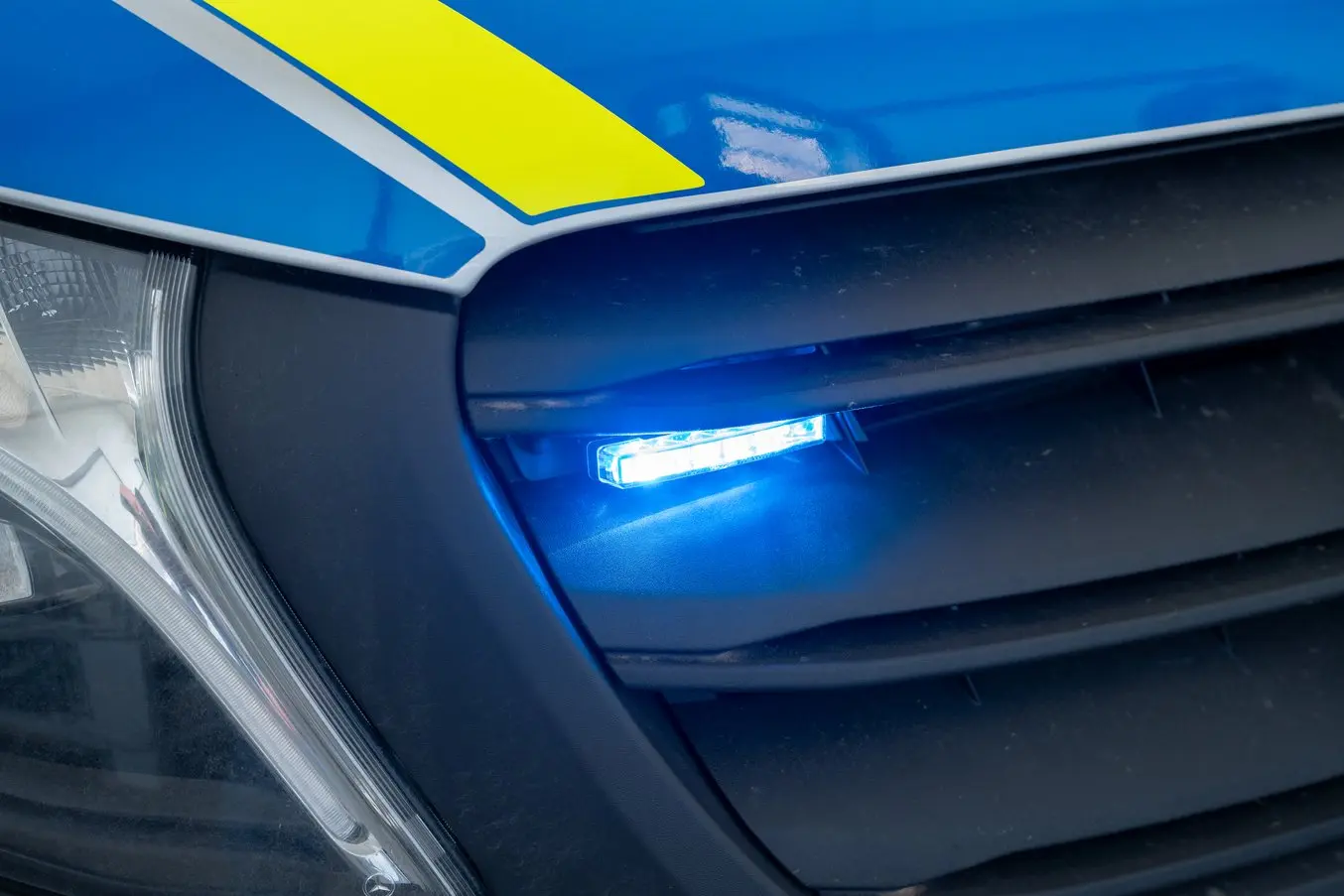
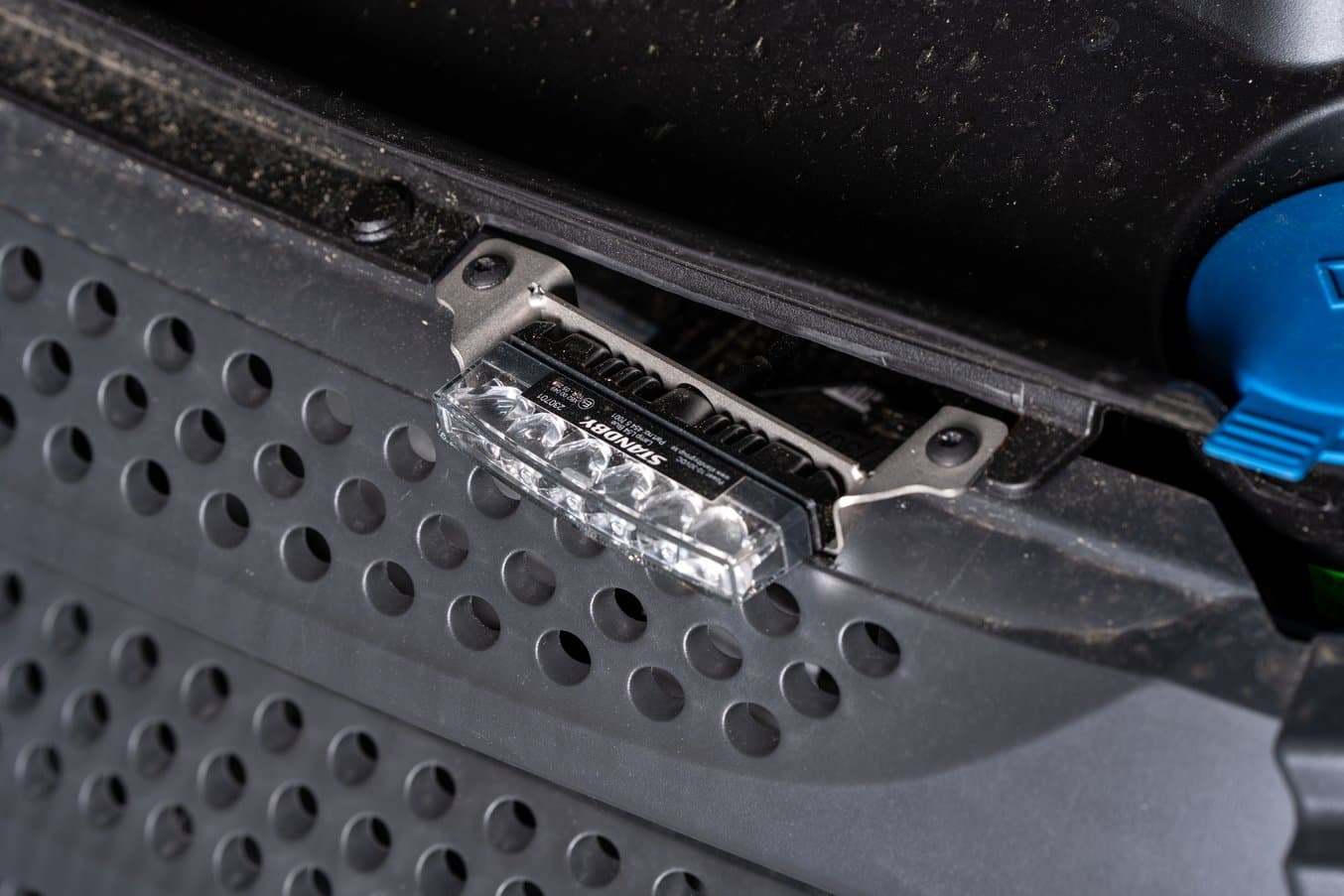
Custom mount for the LED front flash lights on police vans. The team traditionally used sheet metal forming to produce these parts.
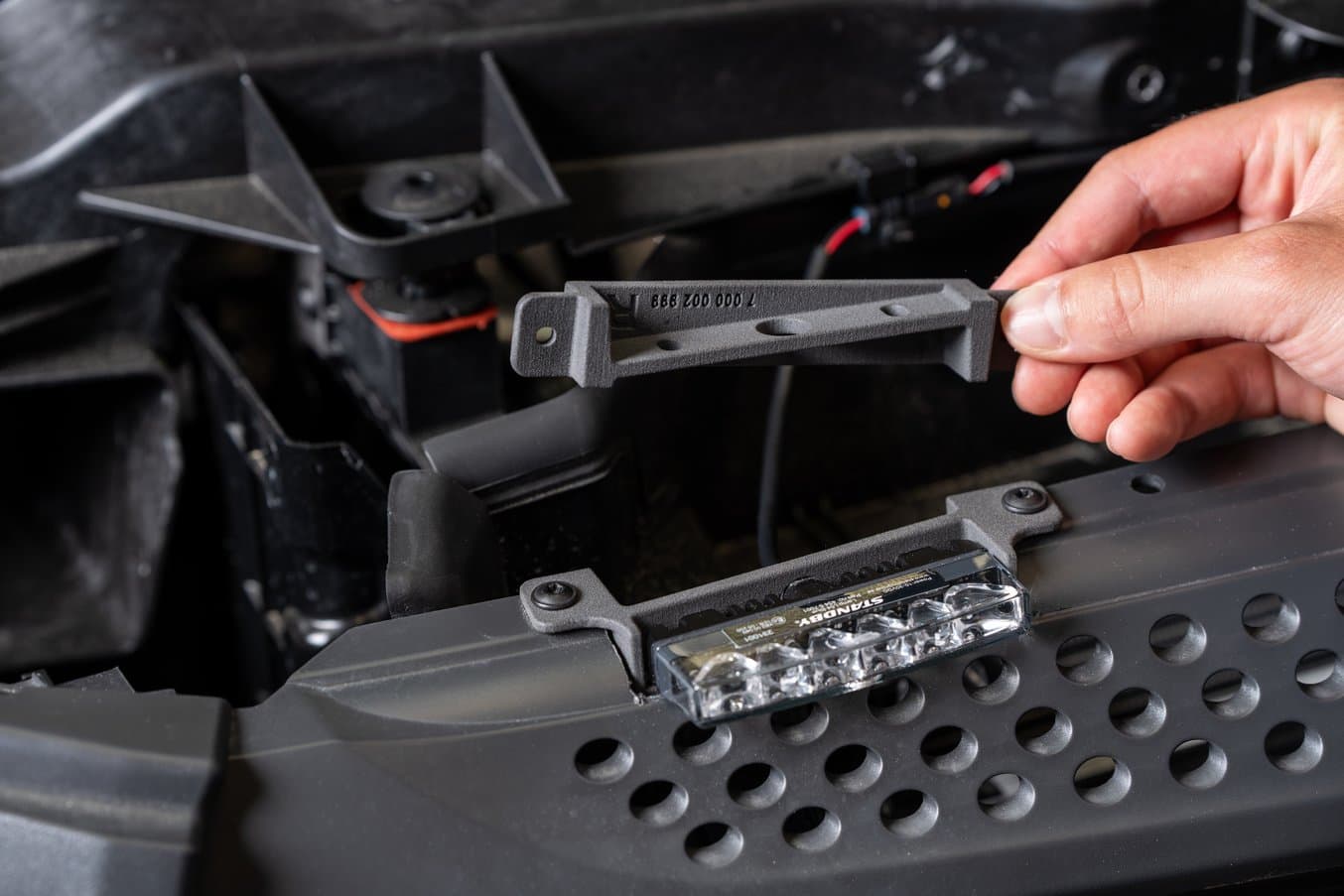
SLS 3D printing now offers a substantially faster, easier, and more cost-effective solution.
The team first produced parts with fused deposition modeling (FDM) 3D printing, which at the time was the most accessible technology that fit their needs, but they quickly ran into limitations. FDM was hard to scale to quantities large enough to fulfill the order, and the parts themselves weren’t industrial-grade quality.
SLS 3D printing would have been the logical next step, but with solutions starting at around €200,000, this was beyond the reach of small businesses — until Formlabs’ Fuse Series was released.
“SLS printing is ideal for MOSOLF because it offers super quality, high accuracy, high material performance and it can produce many components at once. It is cost-effective because the whole system is very, very affordable,” said Gerhard Duda, CEO and Founder of 3D-WERK Black Forest GmbH, Formlabs Partner, who has worked with MOSOLF’s team since the beginning to find the best solutions for their applications.
“The Fuse Ecosystem was the right one for us because it is the most manageable for us in terms of handling and workflow,” added Busam.
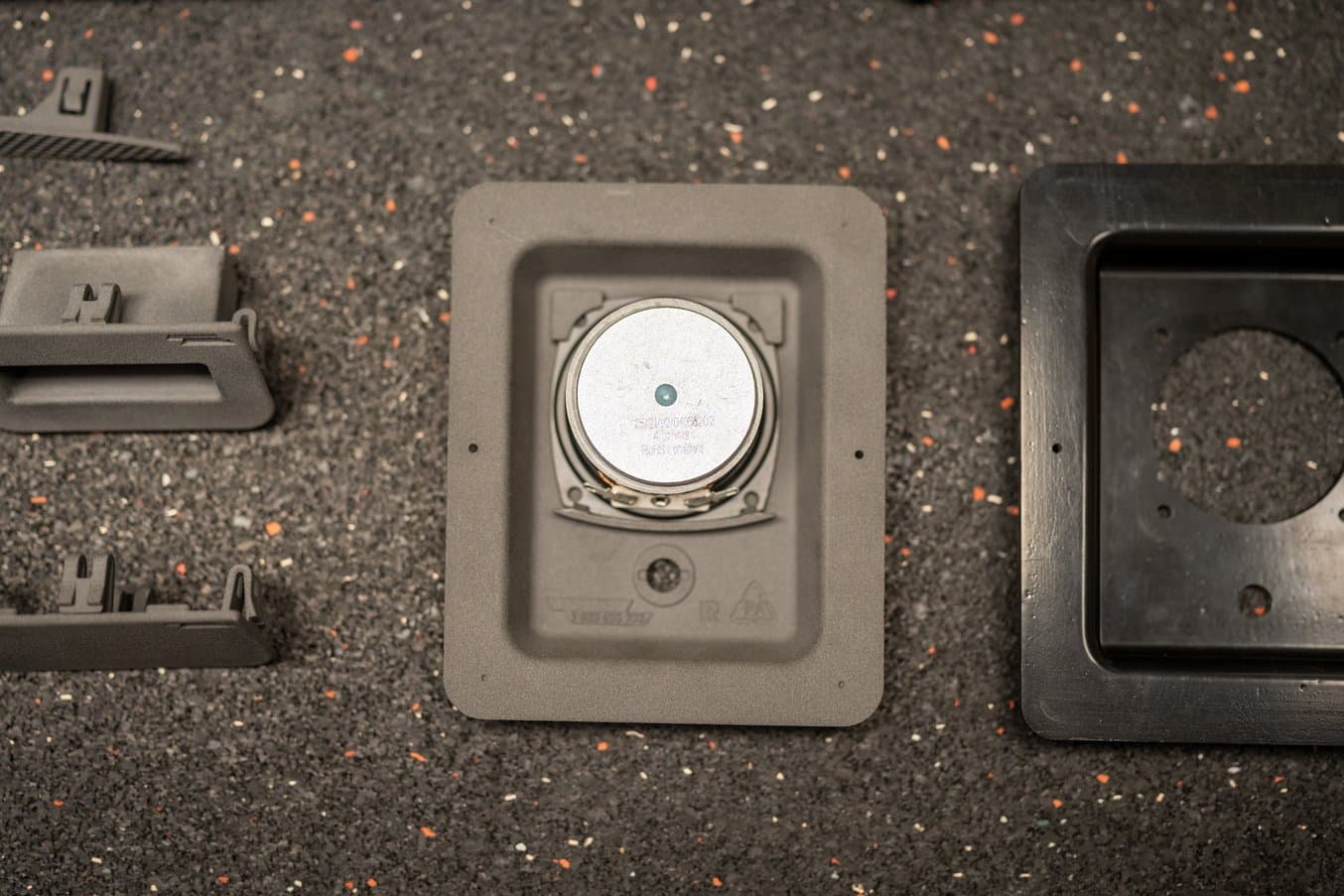
This speaker cover has been designed to save 70% of the pre-installation costs. The speaker body simply clips into the insert, without any need for bonding or mechanical fastening.
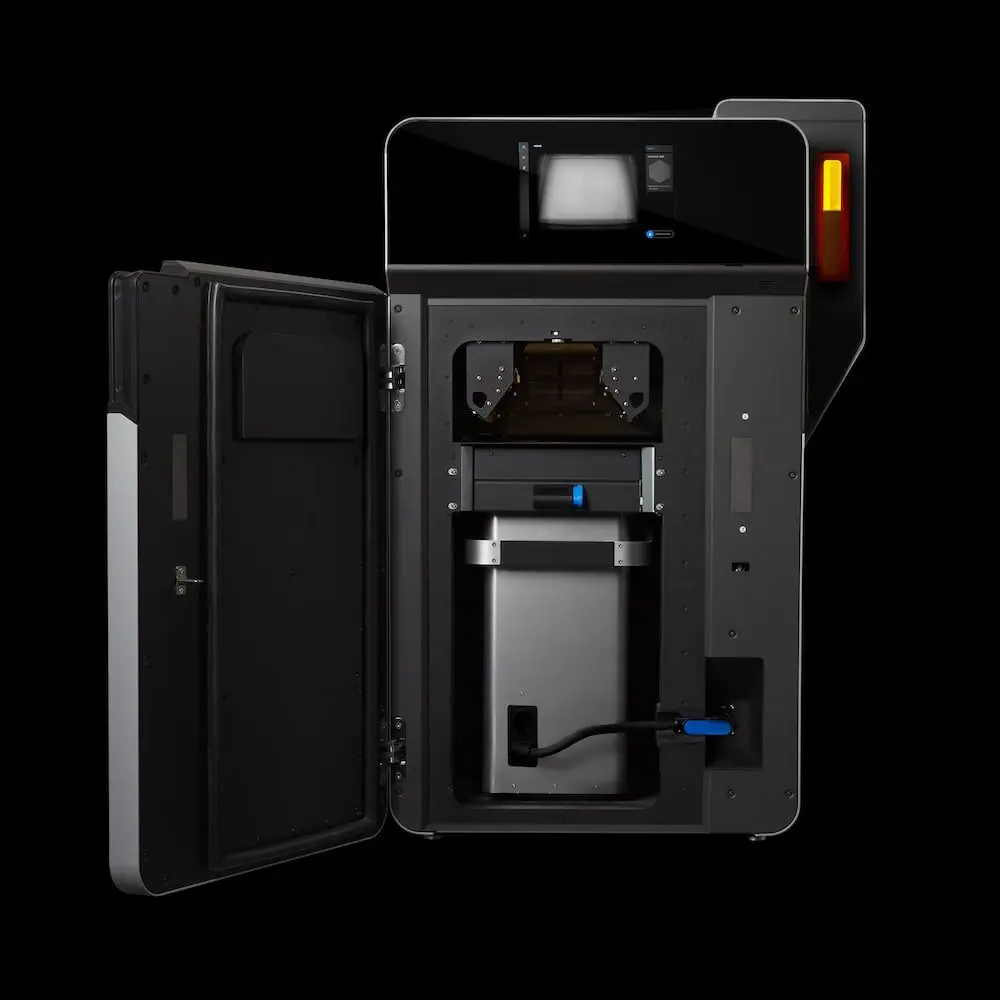
Rapid SLS Production of High Performance Parts with the New Fuse 1+ 30W
Watch our product demo for a walkthrough of the Fuse 1+ 30W and SLS 3D printing with Formlabs experts.
Custom End-Use Parts Within 24 Hours With SLS 3D Printing
Compared to traditional mass production processes like injection molding, thermoforming, or sheet metal forming, the biggest benefit of additive manufacturing is that it can produce custom or low volume end-use parts without expensive tooling.
“We use SLS technology and especially the Fuse 1+ 30W for different components, from the smallest, simplest designs to the complicated console that is installed on the vehicle. We have been using this technology extensively and the Fuse fulfills about 80% of our needs,” said Tiberiu Morariu, the Prototyping, Design, and Technical Conception lead at MOSOLF
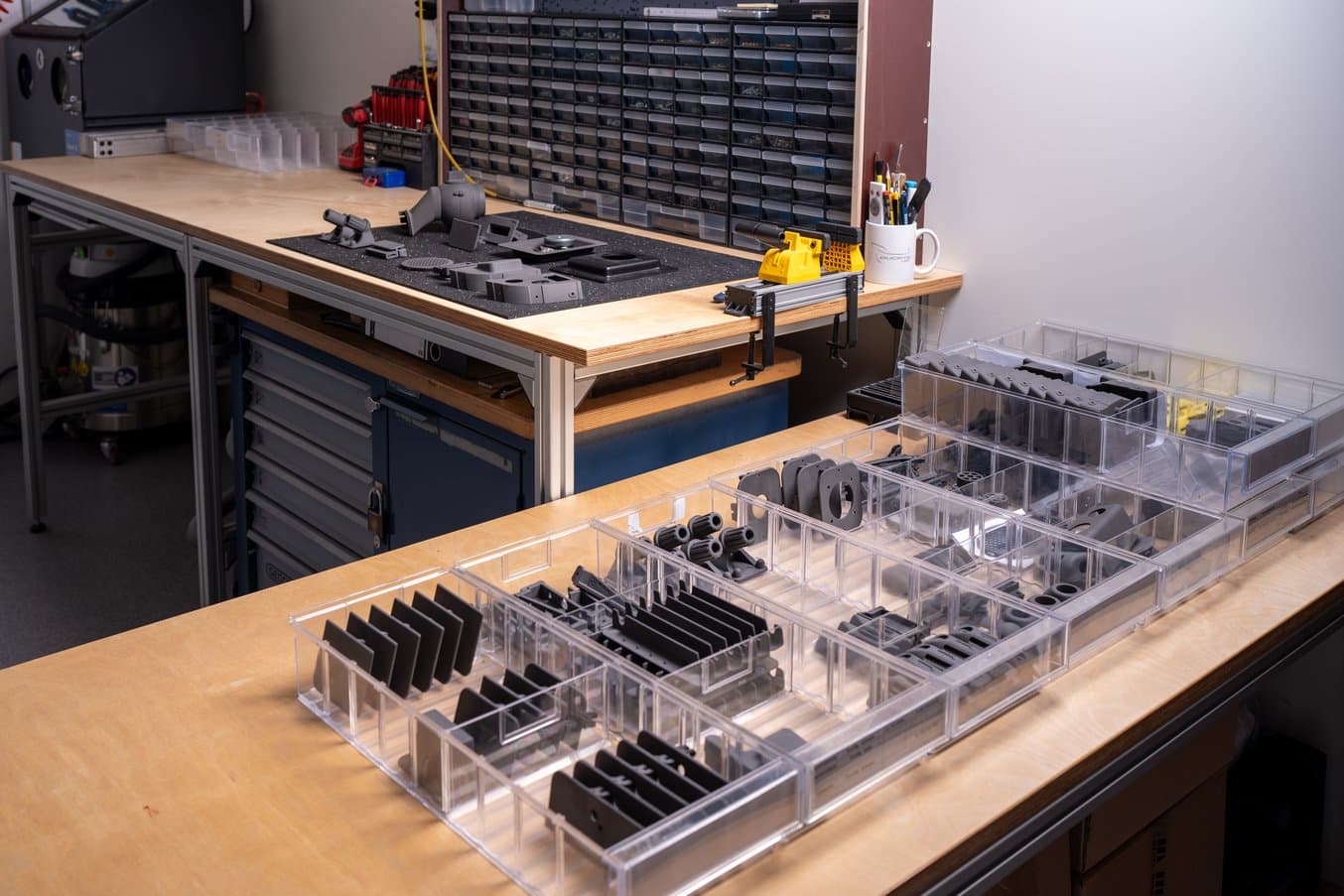
MOSOLF’s team uses SLS 3D printing to produce dozens of custom designs, from the smallest covers and enclosures to large, multi-piece assemblies and dashboard components.
“Requirements vary from state to state, from police station to police station. It's simply easier to make this possible with 3D printing. You can redesign quickly from vehicle to vehicle. If the vehicle is the same, then the contour remains the same, but the systems that are subsequently installed in the vehicle are very different,” said Morariu.
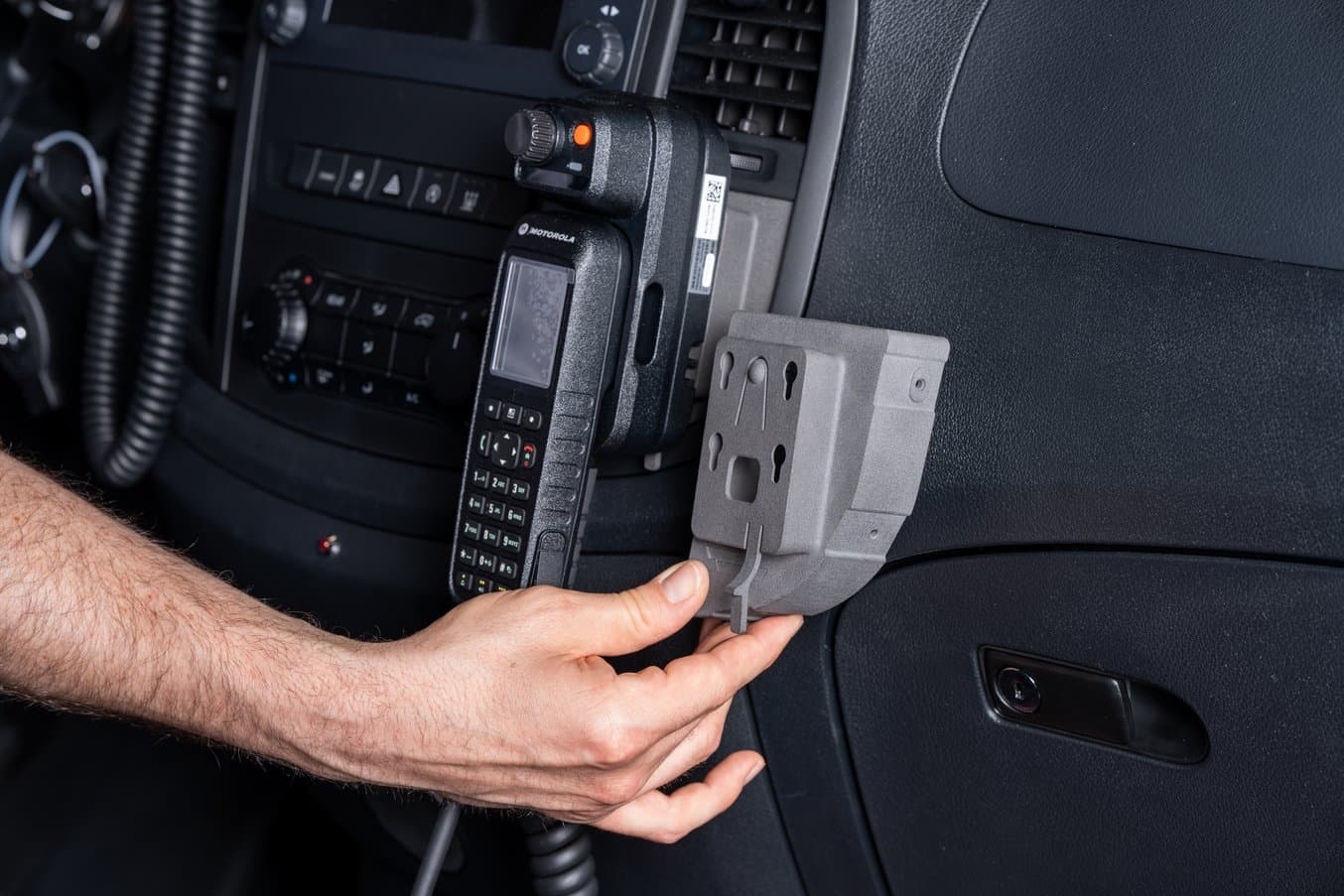
The radio mount is a great example of customization. The attachment to the console is the same for each Mercedes van, but the overall assembly can be easily modified with different mounts for radios of various manufacturers.
This ease of adaptation makes both prototyping and production substantially faster, especially as both prototypes and end-use parts can be produced on the same device.
“For me as a designer, there is nothing better than having an idea in your head today, drawing it, and then holding it in your hands and looking at it the next day,” said Morariu.
“The biggest impact of 3D printing on in-house production is that we have become significantly faster in many areas. With the traditional processes, we have delivery times of four to six weeks, especially if the parts need to be coated. With 3D printing, we can procure parts virtually overnight. If we didn't have access to 3D printing, our work processes would probably be much longer and more complicated because we would probably have to manufacture and adapt each part several times.”
Carsten Busam, Head of Project Planning, MOSOLF Special Vehicles GmbH
SLS 3D Printing | Sheet Metal Forming | Thermoforming | Injection Molding | |
---|---|---|---|---|
Time From Design to Prototype to Series Part | 1-2 weeks | 6-8 weeks | 6-8 weeks | 6-8 weeks |
Lead Time for End Use Parts | 1-2 days | 6-8 weeks | 6-8 weeks | 6-8 weeks |
Other Factors | No tooling required Easy customization Design freedom Superior aesthetics | Requires tooling Limited design freedom Harder to customize Worse aesthetics | Requires tooling Limited design freedom Harder to customize | Requires expensive tooling No customization options Less design freedom |
“Vehicles these days are becoming more beautiful, with more fluid interiors. Storage spaces are becoming more and more dynamic and complicated. 3D printing is very important for the design and ergonomics of the vehicle as you can't always achieve that with other technologies, such as thermoforming or sheet metal forming. The connection to the vehicle itself with these complicated shapes can also be best solved with 3D printing. With 3D printing, I can design more freely, I can fully develop my creativity in design and form.”
Tiberiu Morariu, Prototyping, Design, and Technical Conception, MOSOLF Special Vehicles GmbH
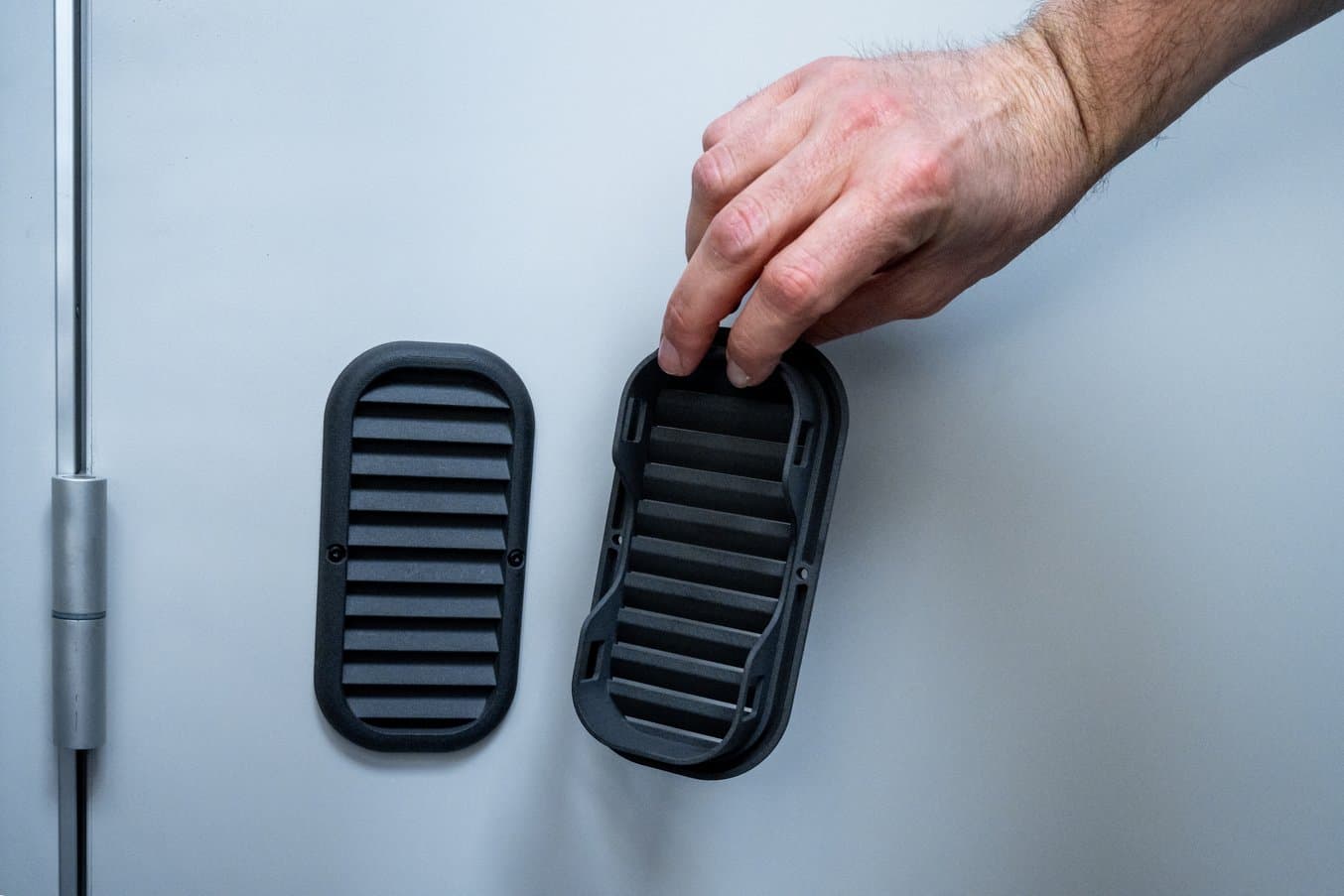
This air vent is a one-way valve that separates the black from the white compartment in a special vehicle for arson investigation. It’s an assembly with a relatively complex design consisting of three components that are screwed together. The team initially tried to produce it with FDM 3D printing, but ran into challenges due to the circular shape and thin walls, and moved to SLS 3D printing as it offers more design freedom.
One of the key benefits of SLS 3D printing is that engineers are familiar with the mechanical properties of the available materials, like nylon, which is commonly used in the automotive industry for producing both interior and exterior parts. MOSOLF’s team has a good understanding of how an SLS 3D printed nylon part will perform, so they can design with functionality in mind and even replace some original metal parts.
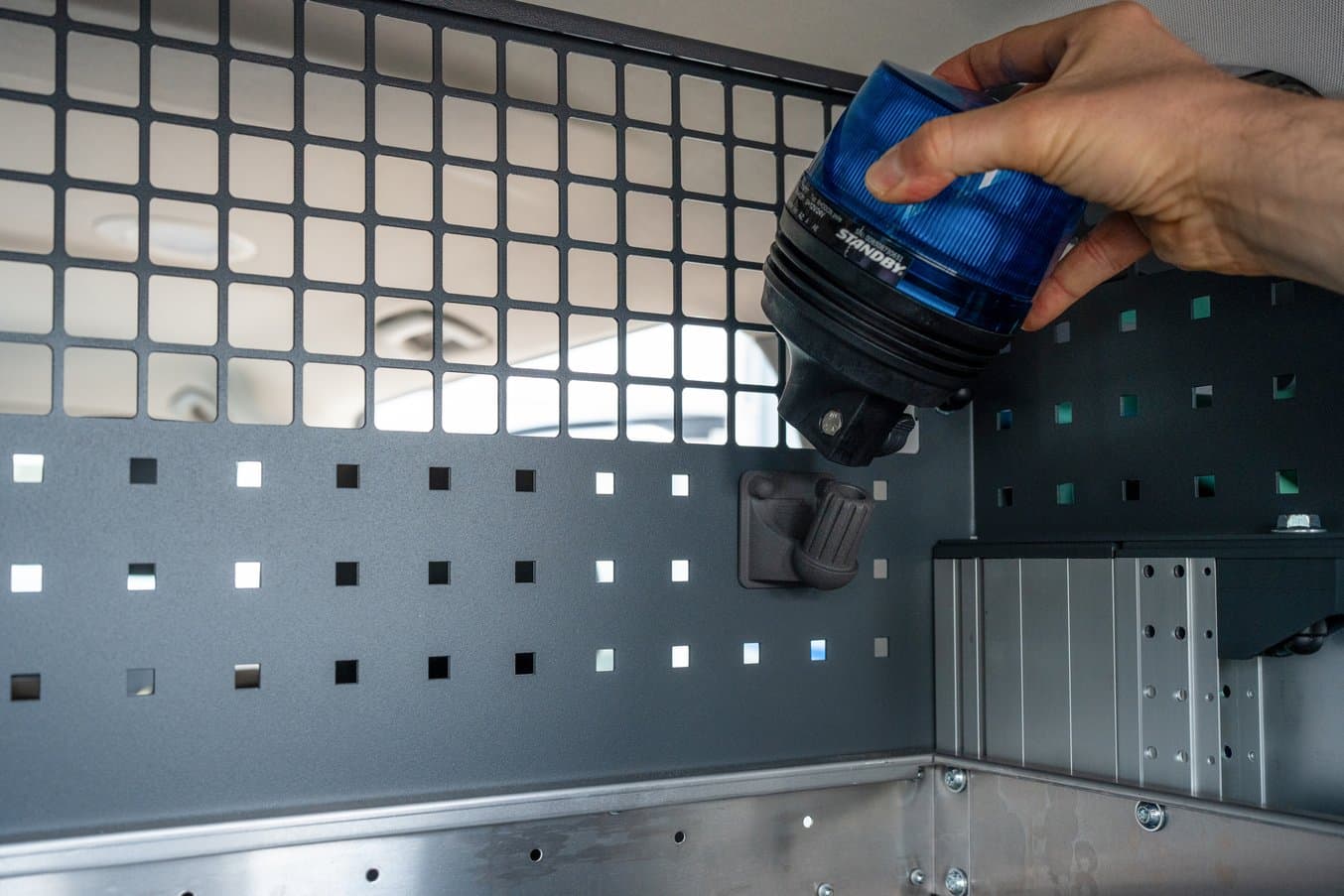
Clip-on mount in the cargo hold for a removable emergency light.
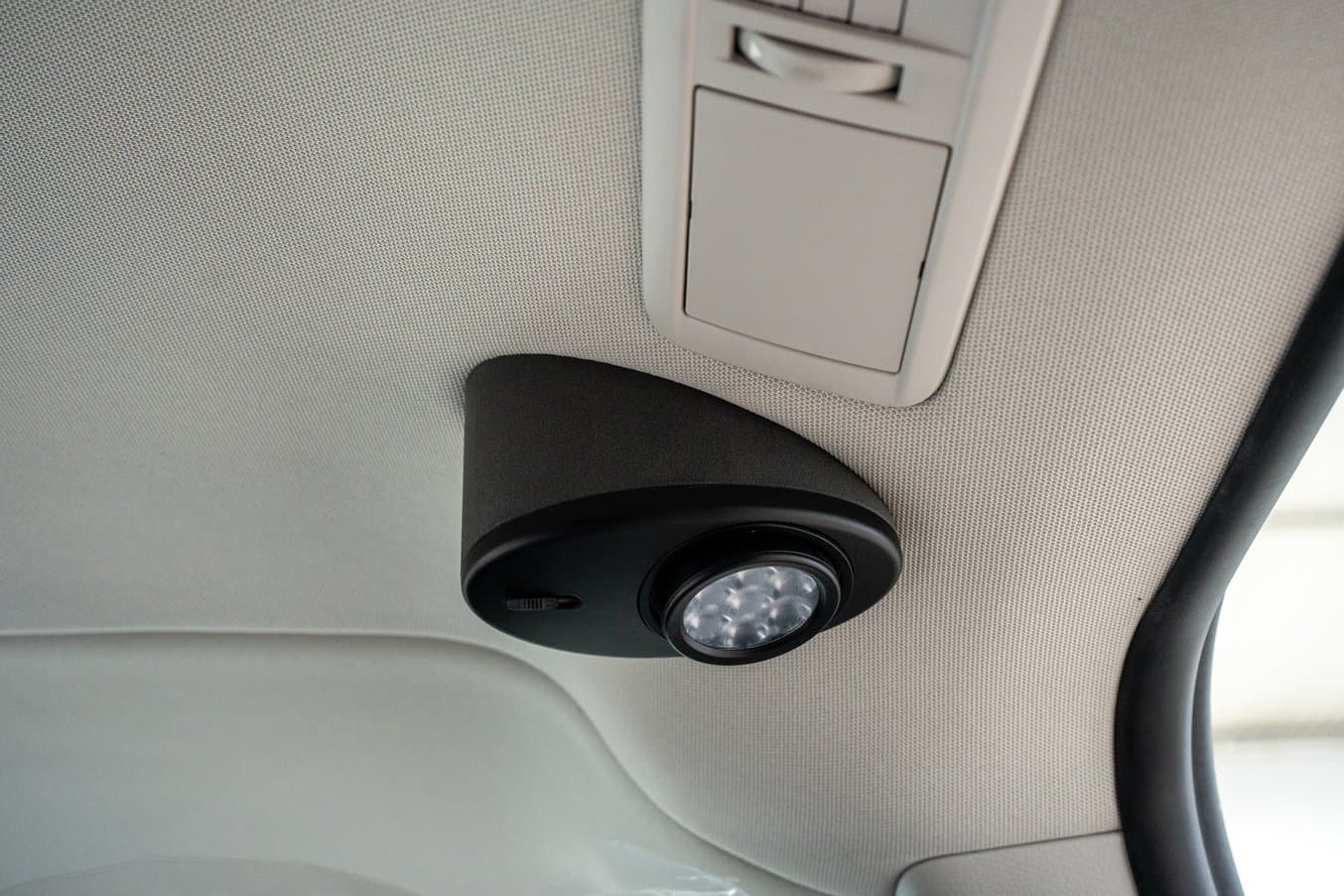
Housing and mount for a ceiling light.
“With the Fuse Ecosystem, you naturally have the perfect material. It is ready for use. It's been around for a very, very long time. It’s been thoroughly tested,” said Duda.
Besides durability, one of the most important criteria for automotive applications is heat resistance. With FDM materials, PLA is out of the question as its heat deflection temperature (HDT) is only around 50 ºC at 0.45 MPa. ABS has an HDT of 90 ºC at 0.45 MPa, which is better, but still on or below the limit for many applications. With an HDT of 171 °C at 0.45 MPa, Formlabs Nylon 12 Powder offers substantially higher heat resistance, which means that there’s no risk that functional parts like a radio holder will fail when the car heats up in the parking lot during the summer.
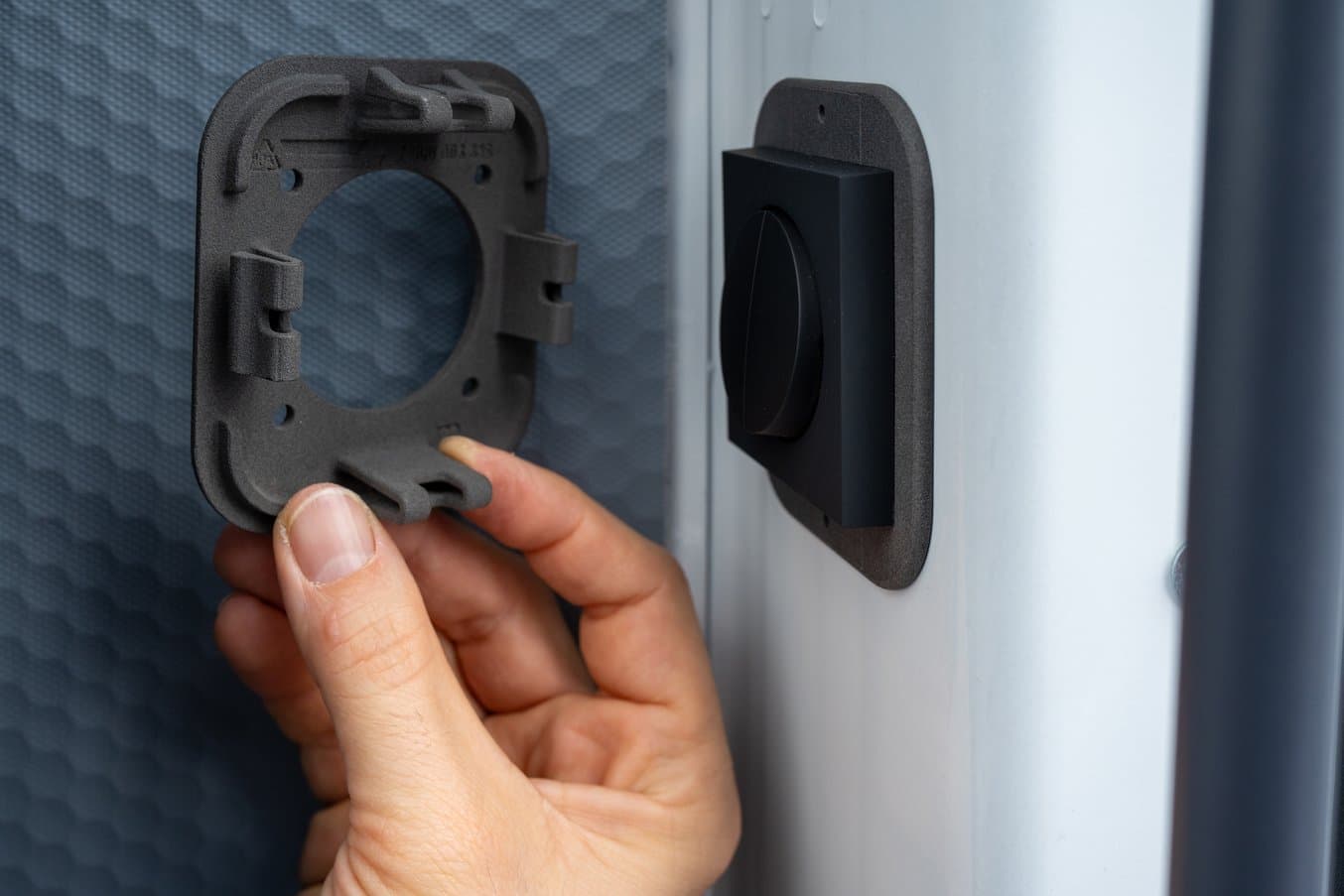
Electric socket housing.
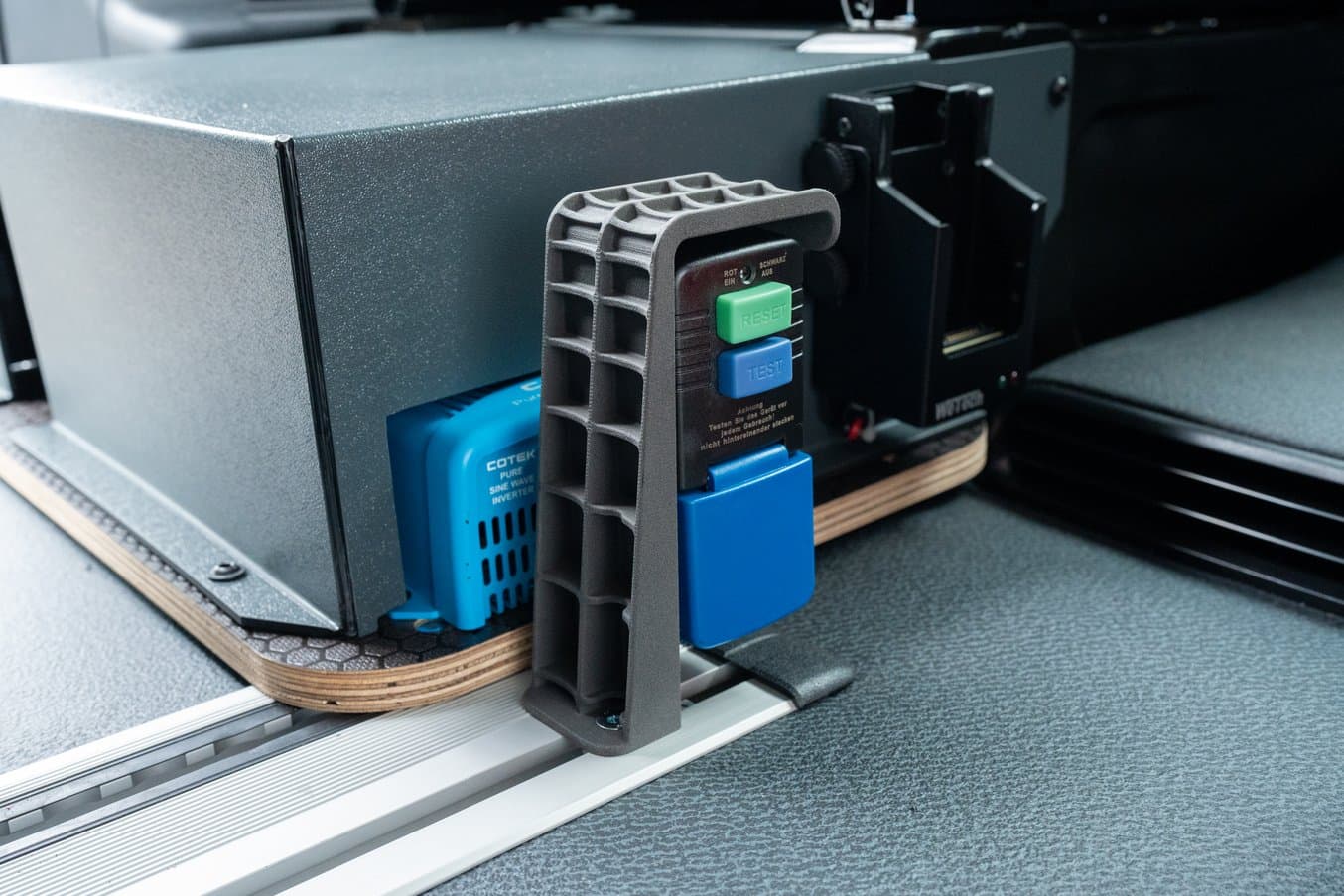
Protective cover to avoid accidental damage while moving within the vehicle.
In some instances, certain vehicles are leased to police or emergency forces and then sold to civilians or other branches of the state after their usage period. To allow for this, MOSOLF’s team has to retrofit these vehicles without damaging or permanently altering anything, so they can be more easily restored to their original state at the end of their service life. Additive manufacturing also makes this easier — instead of permanently modifying existing components, the team swaps them out with 3D printed parts that can be exchanged later.
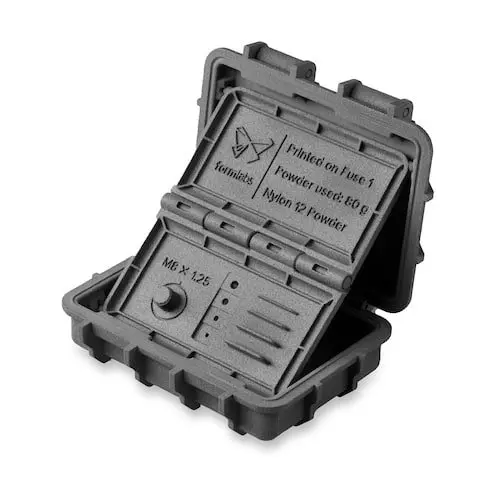
Request a Free SLS Sample Part
See and feel Formlabs quality firsthand. We’ll ship a free SLS sample part printed on the Fuse 1+ 30W to your office.
Police Vehicles of the Future Will Feature Even More 3D Printing
Building on their success with SLS 3D printing, MOSOLF’s and 3D-WERK’s teams are now evaluating how other materials and additional printers could be leveraged to replace an even wider variety of parts in special vehicles.
“It still happens to me now, after so many years of working in the additive field, that I stand in amazement in front of products that we have designed ourselves, that we have printed ourselves, with all the functionalities and possibilities that 3D printing offers,” said Michael Ringwald, Managing Director at MOSOLF.