Der Weg zum 3D-gedruckten Auto: Fünf Arten des 3D-Drucks revolutionieren die Automobilindustrie
Zwar werden Sie in absehbarer Zukunft noch kein 3D-gedrucktes Auto beim Autohändler erwerben können, doch der 3D-Druck ist schon seit vielen Jahren ein wesentlicher Bestandteil des Entwicklungsprozesses von Automobilen. Jedoch kommt der 3D-Druck in letzter Zeit verstärkt in der Fertigung zur Anwendung.
Der 3D-Druck bietet einen enormen Mehrwert für Lieferketten und stellt ein breites Spektrum von Produktionsanwendungen zur Verfügung. Die Technologie lässt sich immer leichter einsetzen und wird immer erschwinglicher, sodass Unternehmen additive Fertigungsverfahren betriebsintern zur Unterstützung von Fabrikabläufen anwenden können. Neue, widerstandsfähige Materialien erschließen Möglichkeiten für die Produktion hochpräziser, funktionaler 3D-Drucke, die als Ersatz für fertige Teile dienen können, leicht kundenspezifisch anzupassen sind sowie eine hohe Leistung bieten. Doch das ist nur der Anfang.
Im Folgenden erfahren Sie, auf fünf wesentliche Weisen, wie der 3D-Druck Innovationen in der gesamten Automobilindustrie vorantreibt, vom Design bis zur Fertigung und darüber hinaus.
1. Neugestaltung des Prototypenentwicklungsprozesses
Seit jeher ist die Prototypenentwicklung der häufigste Anwendungsfall für den 3D-Druck in der Automobilindustrie. Da Prototypen dank des 3D-Drucks deutlich schneller gefertigt werden können, wird Rapid Prototyping fast schon synonym mit 3D-Druck verwendet. Diese Technologie hat den Produktentwicklungsprozess revolutioniert.
Mittels 3D-Druck können Automobildesigner schnell einen Prototyp eines physischen Teils oder einer Baugruppe herstellen, vom einfachen Innenelement über ein Armaturenbrett bis hin zum maßstabgetreuen Modell eines ganzen Autos. Rapid Prototyping befähigt Unternehmen, Ideen in tragfähige Konzeptnachweise zu verwandeln. Diese Konzepte können dann zu Prototypen mit hoher Originaltreue weiterentwickelt werden und Produkte durch eine Reihe von der Validierungsphasen führen, die in der Serienproduktion enden. In der Automobilindustrie ist diese rasche Validierung absolut unerlässlich. „Wenn eine Automobilfertigunglinie auch nur eine Stunde lang still steht, entstehen beträchtliche Kosten“, so Andrew Edman, Leiter der Branchen Produktdesign, Maschinenbau und Fertigung bei Formlabs.
Mit dem betriebsinternen Stereolithografie (SLA) 3D-Druck können Designer und Ingenieure bei Ringbrothers ohne Einschränkungen, effektiv und kostengünstig Iterationen durchführen.
Früher war die Prototypenentwicklung zeitaufwendig und daher potenziell kostenintensiv, wenn ein Produkt mehrere Iterationen durchlief. Mittels 3D-Druck können höchst realitätsnahe und repräsentative Prototypen innerhalb eines Tages und zu deutlich geringeren Kosten erstellt werden. Desktop 3D-Drucker erlauben es Maschinenbau- und Designteams, die Technologie betriebsintern einzubringen. So werden mehr Iterationszyklen durchlaufen und die Distanz zwischen Konzept und Endprodukt verkürzt, was wiederum die gesamten Produktentwicklungsabläufe stärkt.
2. Herstellung maßgefertigter, komplexer und hochleistungsfähiger Teile
Der 3D-Druck eignet sich hervorragend für die Herstellung von Sonderanfertigungen zu deutlich reduzierten Kosten. Damit stehen Herstellern umfangreiche neue Möglichkeiten zur Verfügung, um neuartige Teile zu produzieren und ihr Produktangebot auszuweiten.
Kleineren Unternehmen, bei denen die Individualisierung im Zentrum der Markenidentität steht – wie die bei der Autowerkstatt Ringbrothers – hat der 3D-Druck neue Möglichkeiten eröffnet, hochwertigere und kreativere Arbeit zu leisten, und wichtigen Spielraum geliefert, um mit Sonderdesigns zu experimentieren und sie zu perfektionieren; ganz ohne die Sorgen, die potenziell teure und zeitintensive Fertigungsprozesse bei der Individualisierung mit sich bringen.
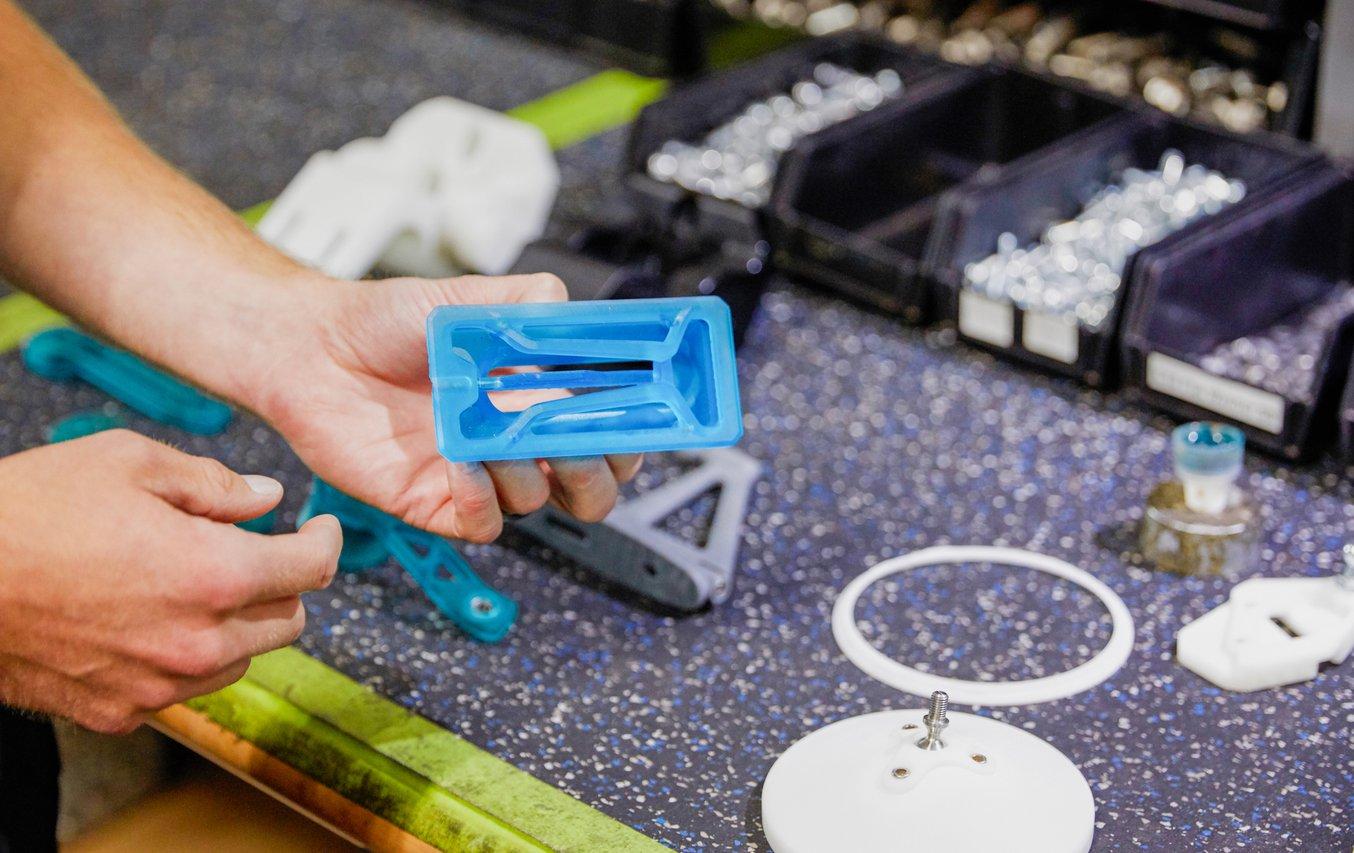
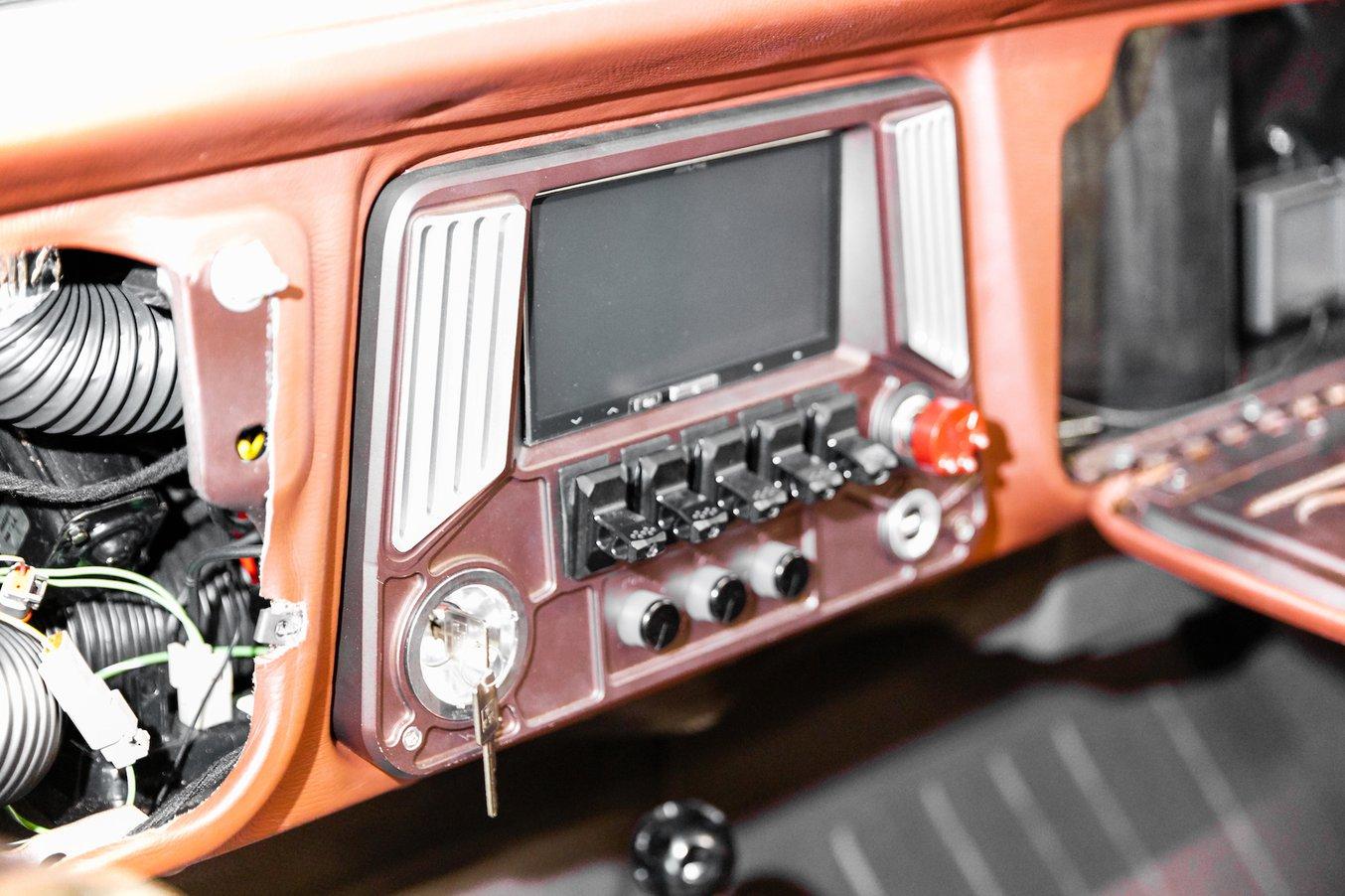
Ringbrothers stellt individuelle Endverbraucherteile wie diese Lüftungsöffnung mittels 3D-Druck her.
Größere Unternehmen kombinieren 3D-Drucktechnologie zudem mit herkömmlichen Fertigungsmethoden. Volkswagen hat seinen kultigen 1962er Bulli neu aufgelegt und seinen Benzinmotor durch einen Elektromotor mit 120 PS und einem Drehmoment von 234 Nm ersetzt. Das Konzept des „Typ 20“ kann zudem mit verschiedenen Verbesserungen aufwarten, die dem 3D-Druck zu verdanken sind, einschließlich generativ entworfener Aluminiumgussräder. Selbst die Radkappen wurden in 3D gedruckt: Sie sehen aus wie gestanzter Stahl, wurden aber auf einem Formlabs SLA 3D-Drucker hergestellt und anschließend galvanisiert, um Optik und Haptik von Metallteilen anzunehmen.
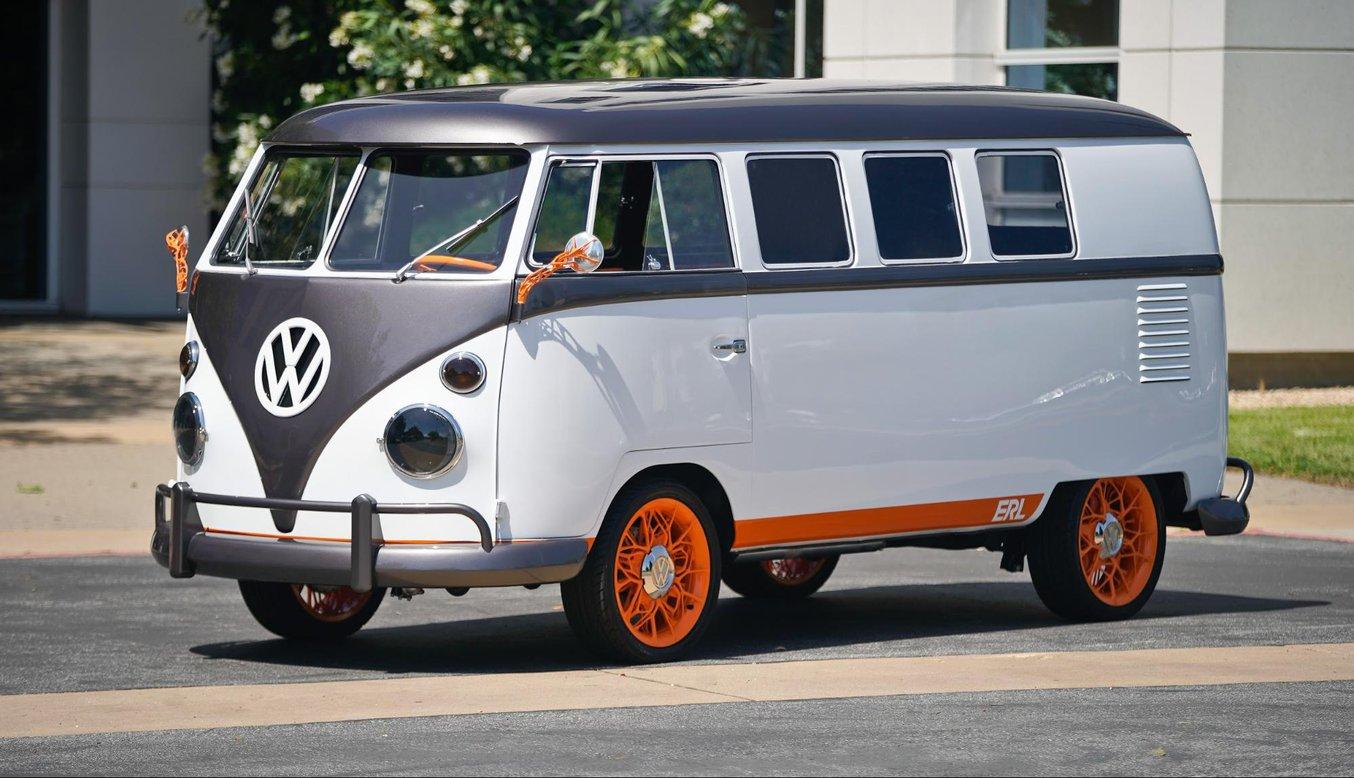
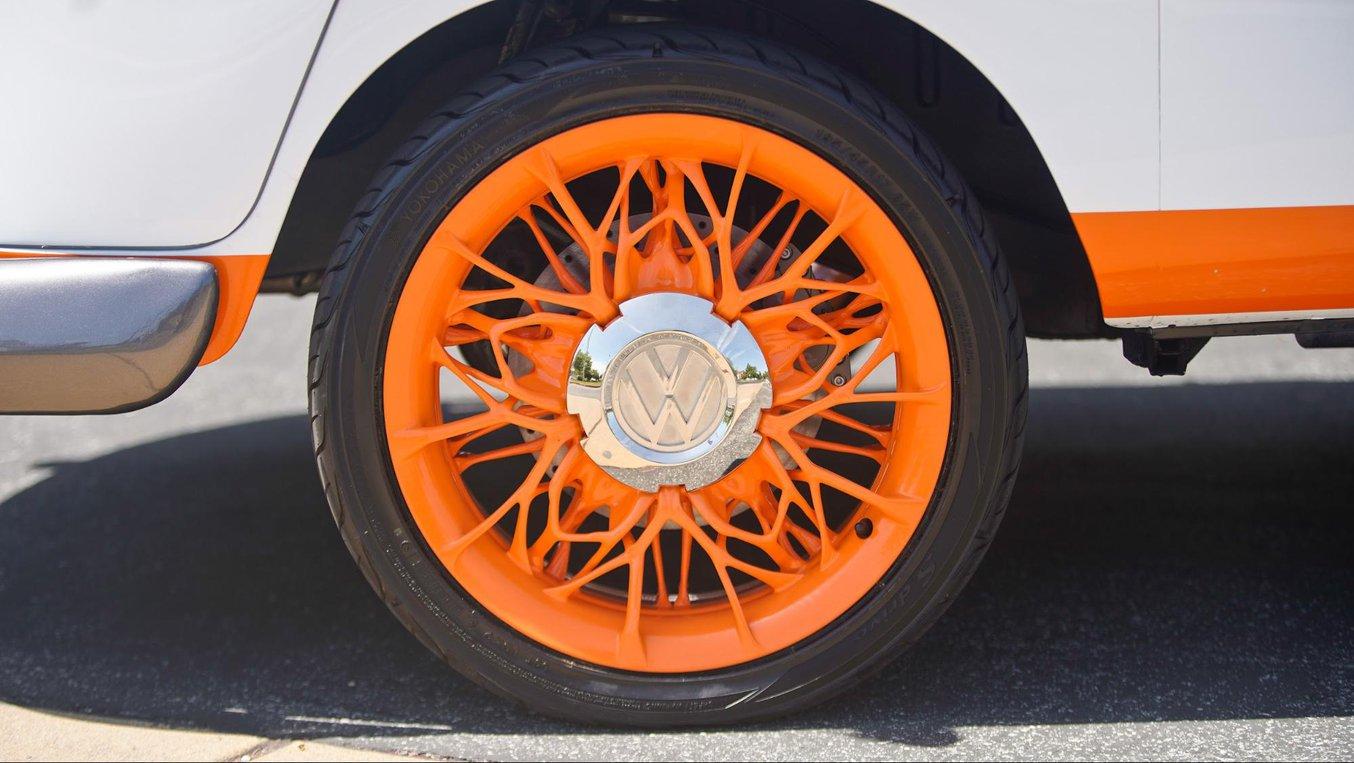
Die Radkappen des neuen Bulli wurden auf einem Formlabs SLA 3D-Drucker gedruckt und dann galvanisiert und poliert, um das Aussehen von verchromtem Stahl zu erzielen. (Bilder: VW)
Der Bentley Speed 6 ist ein weiteres Beispiel. Der Luxusautohersteller verwendete fortgeschrittene Metall-3D-Drucktechnologie, um detailliertere, filigranere Teile zu erstellen (Kühlergrill, seitliche Lüftungsöffnungen, Türgriffe und Auspuffanlagen), als dies mit seinen derzeitigen Produktionsmodellen möglich wäre.
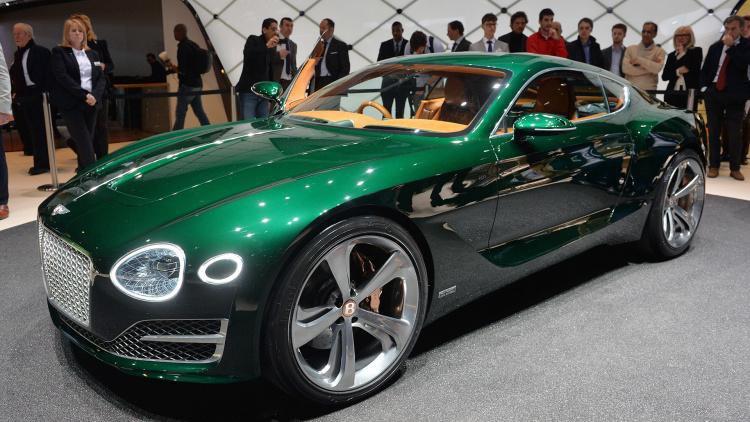
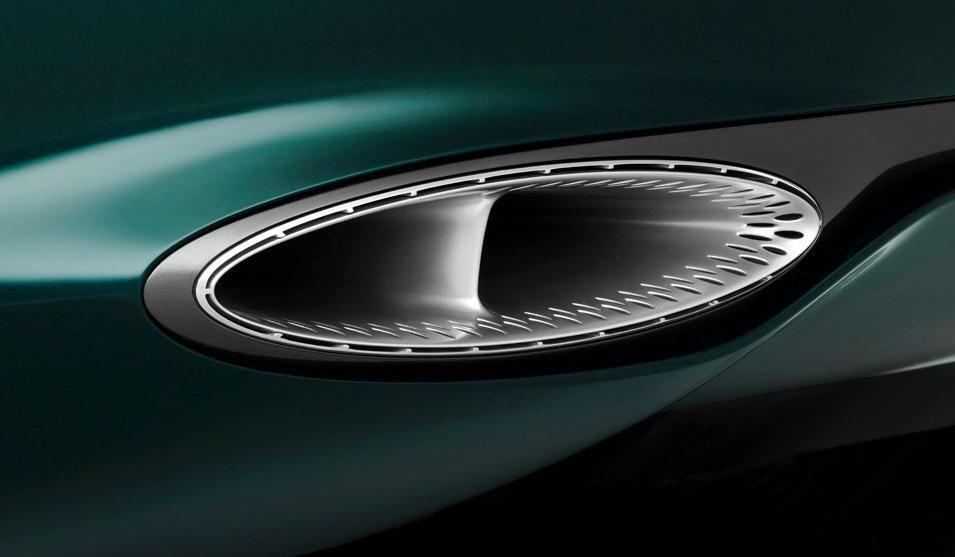
Bentley nutzte Metall-3D-Drucktechnologie, um filigrane Teile mit mikroskaliger Präzision zu erstellen. (Quelle: Bentley)
Doch die Anwendungen des 3D-Drucks beschränken sich nicht auf Klassiker und Konzept- oder Ausstellungsmodelle. Dank der Anpassungssoftware von Twikit bietet der britische Automobilhersteller MINI seinen Kunden die serielle Individualisierung seiner Autos mittels 3D-Druck, die damit die volle Kontrolle über das Design haben. Kunden können Innen- und Außenelemente ihres Fahrzeugs mit verschiedenen Schriftarten, Mustern und Bildern individuell anpassen und ihr Design mithilfe von 3D-Visualisierungen prüfen. Entscheidend für die Marktfähigkeit eines solchen Projekts sind die mittels 3D-Druck erzielten Kosteneinsparungen, die eine derartige Individualisierung für die Öffentlichkeit erschwinglich gemacht haben.
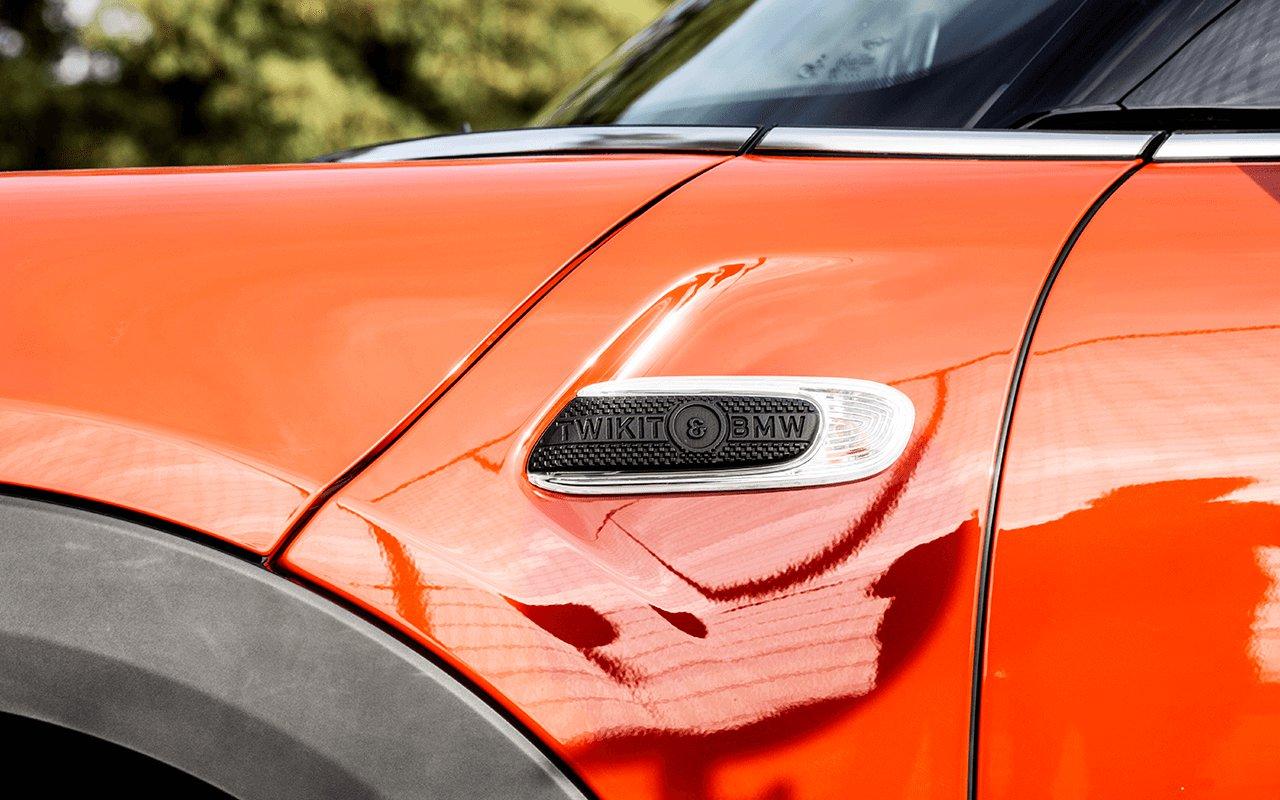
Dank der Zusammenarbeit von MINI mit Twikit erhalten Kunden die volle Kontrolle über das Design und können Innen- und Außenkomponenten ihres Fahrzeugs individuell anpassen. (Quelle: Twikit)
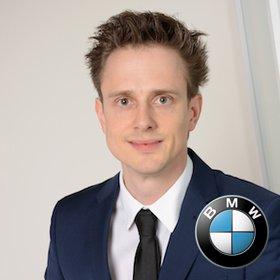
3D-Druck in der Produktion bei BMW
Sehen Sie, wie Christian Gröschel, Projektleiter von BMW, beschreibt, wie das Unternehmen ein Programm für additive Fertigung entwickelt und umsetzt.
Video ansehenDer 3D-Druck hat auch die Gestaltung von Teilen ermöglicht, die mit anderen Mitteln nicht produziert werden konnten. Der 8-Kolben-Monoblock-Bremssattel von Bugatti ist ein besonders prominentes Beispiel hierfür. Dank der exzellenten Materialeigenschaften verwendet Bugatti für bestimmte Komponenten Titan, doch die Bearbeitung mit herkömmlichen Methoden ist kostenaufwendig und kompliziert. Mithilfe des 3D-Drucks konnte Bugatti den Bremssattel nicht nur in ausreichender Stückzahl herstellen, sondern auch das Leistungspotenzial des Materials noch weiter steigern: Das Unternehmen verringerte das Gewicht der Komponente massiv und machte sie gleichzeitig erheblich steifer und fester als die herkömmliche Produktionsalternative (Aluminium).
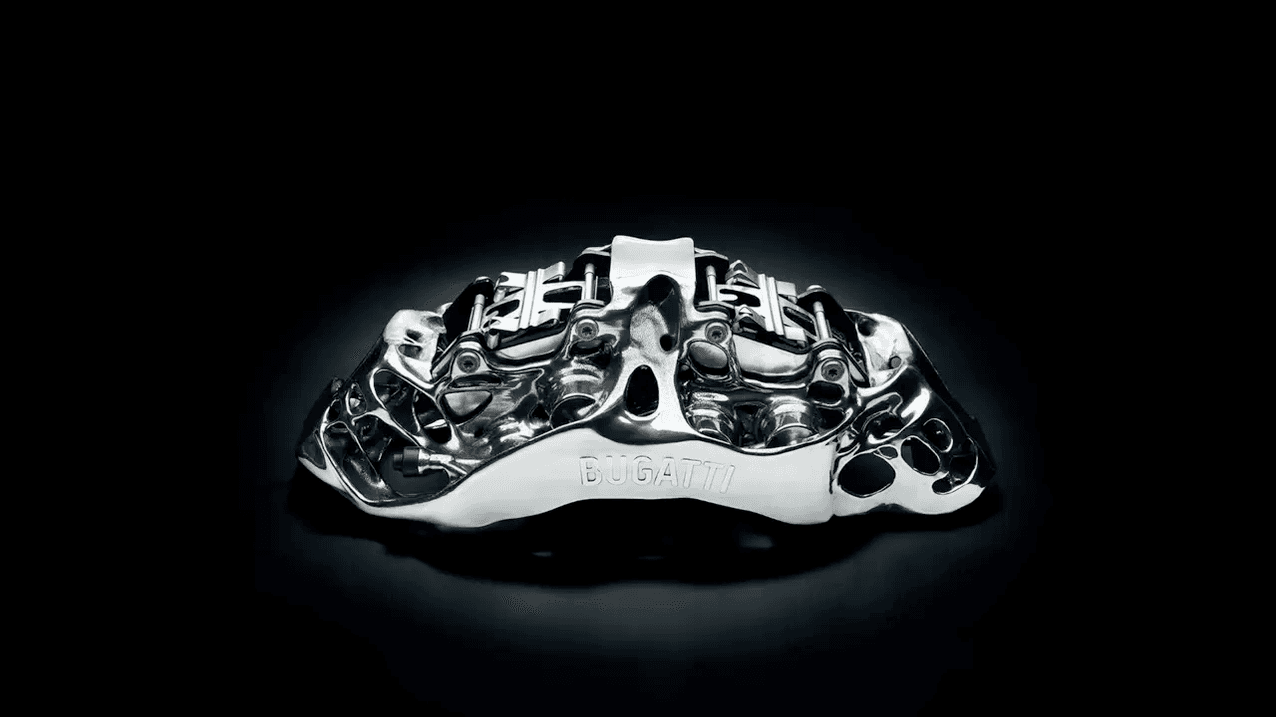
Der 8-Kolben-Monoblock-Bremssattel von Bugatti ist die größte mittels 3D-Druck hergestellte funktionale Titankomponente der Welt. (Quelle: Bugatti)
3. Herstellung von Werkzeugausstattung und Fertigungsmitteln
Ingenieure verwenden Fertigungsmittel, um Fertigungs- und Montageprozesse einfacher und zuverlässiger zu gestalten, Zyklen zu verkürzen und die Arbeitssicherheit zu verbessern. Automobilwerke und Zulieferer verwenden Tausende individuell entworfene (Halte-)Vorrichtungen, die jeweils speziell für den Endverbrauch zugeschnitten und hochgradig optimiert sind. Das Ergebnis ist eine starke Zunahme von individuellen Werkzeugen, die den Fertigungsprozess erheblich kostenintensiver und komplexer machen.
Die Auslagerung der Produktion dieser Sonderteile an Zerspanungsdienstleister, die Teile aus massiven Kunststoff- oder Metallblöcken fräsen, kann die Produktion um Wochen verzögern. Gleichzeitig erschweren derart lange Durchlaufzeiten die Anpassung an Veränderungen im Werk.
Die additive Fertigung kann die Durchlaufzeit auf wenige Stunden verkürzen und gleichzeitig die Kosten im Vergleich zur Auslagerung von Teilen an einen externen Dienstleister erheblich reduzieren. Da Komplexität nun keine zusätzlichen Kosten verursacht, können die Teile zudem besser für den Endverbrauch optimiert werden. Neue, widerstandsfähige 3D-Druckmaterialien erlauben es Herstellern außerdem in vielen Fällen, Metallkomponenten durch 3D-gedruckte Kunststoffteile zu ersetzen oder vor der endgültigen Entscheidung Werkzeugprototypen herzustellen und zu testen.
Damit wird die Herstellung von Fertigungsmitteln mithilfe des 3D-Drucks zu einem der größten Anwendungsgebiete der Technologie.
Pankl Racing Systems verwendet 3D-gedruckte Haltevorrichtungen, um Teile auf dem Förderband zu befestigen, während sie eine Reihe von Bearbeitungsvorgängen durchlaufen.
Das Unternehmen verwendet beispielsweise eine aus mehreren Formlabs SLA 3D-Druckern bestehende 3D-Druckstation, um ihre wichtigsten Produktionswerkzeuge herzustellen. Bei der Fertigung von Getriebebaugruppen erfordert jedes Teil, das das Unternehmen herstellt, eine Reihe von individuellen (Halte-)Vorrichtungen und anderen Werkzeugen, die speziell für das entsprechende Teil entworfen werden, während sie von Drehautomaten in mehreren Stufen spanend bearbeitet werden. Mithilfe des 3D-Drucks konnten die Ingenieure von Pankl die Durchlaufzeit von Haltevorrichtungen um 90 Prozent – von zwei bis drei Wochen auf weniger als einen Tag – reduzieren. Die Kosteneinsparungen lagen zwischen 80 und 90 Prozent; absolut gesehen 150 000 USD.
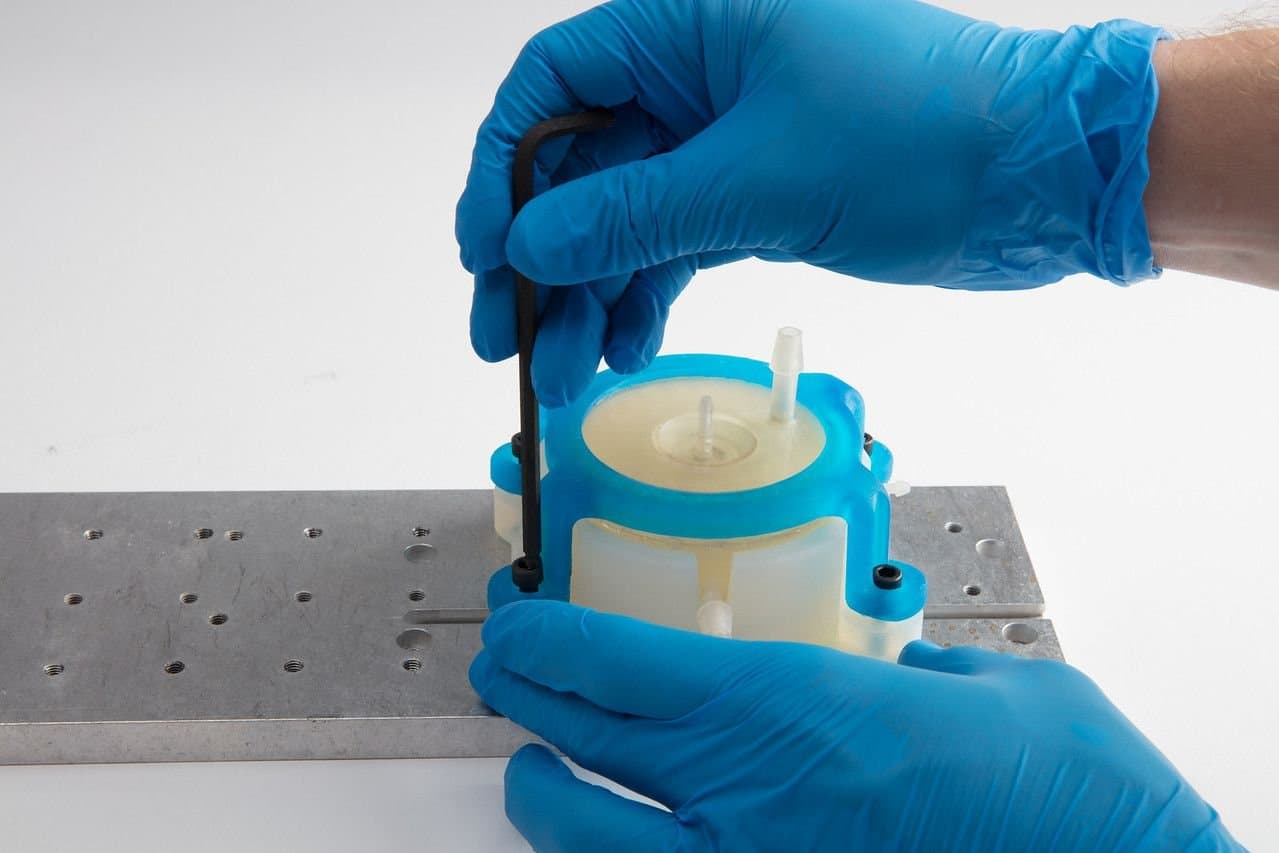
Konstruktion von Vorrichtungen mit 3D-Druck
Laden Sie unser Whitepaper herunter, um zu erfahren, wie Sie mit 3D-gedruckten (Halte-)Vorrichtungen Kosten senken, die Entwicklungszeit verkürzen und optimierte Produktionsabläufe schaffen.
Whitepaper herunterladen4. Die Lösung für das Ersatzteilproblem
Ersatzteile sind seit jeher ein großes Problem für die Automobilindustrie. Die Nachfrage ist von Natur aus sporadisch und unvorhersehbar, sodass sich die Herstellung von Ersatzteilen unter Umständen finanziell nicht rechtfertigen lässt. Doch ohne frei verfügbare Ersatzteile sinkt der langfristige Wert von Produkten und Reparaturen gestalten sich schwierig. Die präventive Herstellung von Ersatzteilen erfordert einen hohen Lageraufwand.
Der 3D-Druck verfügt über einzigartige Eigenschaften, dank derer er einen maßgeblichen Beitrag zur Lösung des Ersatzteilproblems der Automobilindustrie leisten kann. „Ich denke, einer der wichtigsten Faktoren [um das Ersatzteilproblem mittels 3D-Druck zu lösen] ist, Materialien zur Verfügung zu haben, die eine vergleichbare Leistung und Kosteneffizienz aufweisen wie herkömmliche Materialien. Wir kommen diesem Ziel immer näher“, so Edman. „Die Frage ist nicht in erster Linie: ‚Übernimmt der 3D-Druck die Produktion von Ersatzteilen?‘, sondern ‚Wann?‘“
Mit dem Einsatz von CAD können Entwürfe für alle Teile als Digitalkopie aufbewahrt werden, was die Bestandsführung überflüssig macht. Mit der Verbreitung von Benchtop-3D-Druckern können Ersatzteile auf Kundenanfrage im Geschäft produziert werden. Die Zugänglichkeit der Technologie wird Lieferanten ermutigen, neue Räumlichkeiten zu erschließen, um eine einfache Versorgung mit 3D-Druckersatzteilen zu ermöglichen.
Selbst Teile, von denen kein Bestand mehr verfügbar ist, können potenziell auf Wunsch auf Basis von digitalen Scans vorhandener Teile durch Reverse Engineering nachgebaut werden. Älteren Designs könnte so wieder neues Leben eingehaucht werden. „Es sind Oldtimer im Umlauf, die 50 Jahre oder noch älter sind. Eines Tages sind wir vielleicht in der Lage, diese mithilfe des 3D-Drucks auf eine automatisierte Weise zu unterstützen“, so Edman.
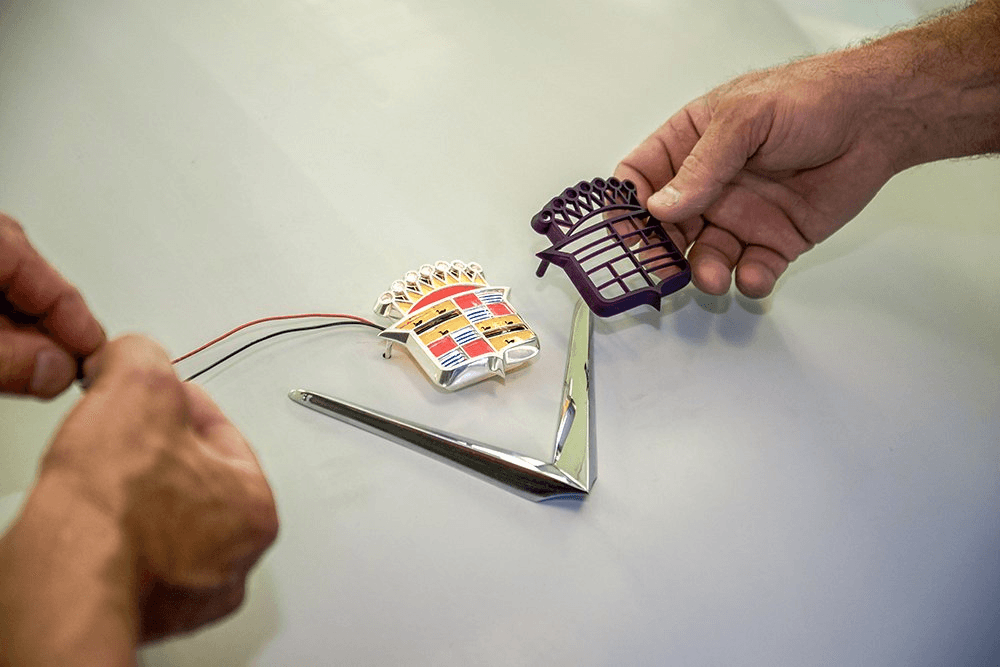
Ringbrother hat ein Cadillac-Emblem für ein maßgefertigtes Oldtimer-Fahrzeug reproduziert, indem das Unternehmen die Form in 3D druckte und dann in Metall goss.
5. Leichtere Fertigung von Standardteilen
Mit sinkenden Hardware- und Materialkosten wird der 3D-Druck immer erschwinglicher, sodass wir einen fortschreitenden Übergang zur Herstellung regulärer Automobilteile erleben werden.
3D-Drucker können auch bei der Fertigung von Standardteilen die Effizienz steigern. Dazu berichtet Edman: „Wo 3D-Drucktechniken rascher an Beliebtheit gewinnen, besteht die Möglichkeiten mithilfe der additiver Fertigungsmethoden Komponenten zu kombinieren. Sie könnten beispielsweise eine Baugruppe aus sechs oder sieben Teilen zu einem einzigen Druckteil zusammenfassen. Sie sparen Montagezeit- und kosten, selbst wenn die Einzelteile möglicherweise teurer sind.“ Durch die Zusammenstellung von Teilen können 3D-Druckmethoden zudem zur Gewichtsreduzierung und Verbesserung der Kraftstoffeffizienz beitragen.
Die Vielfalt an Materialien, die beim 3D-Druck zur Verfügung stehen, entspricht immer mehr den mechanischen Anforderungen verschiedener Fahrzeugkomponenten. Additive Methoden nähern sich in puncto Kosten rapide traditionellen Methoden (wie Formen oder Druckguss). Damit wird es von einem Produktivitäts- und finanziellen Standpunkt aus gesehen immer sinnvoller, den 3D-Druck auch für die Fertigung von Standardteilen zum Einsatz zu bringen.
+1. 3D-gedruckte Autos
Während die Markterschließung von vollständig 3D-gedruckten Autos noch einige Zeit entfernt ist, gibt es bereits einige spannende, richtungsweisende Projekte in der Industrie:
Der Light Cocoon von EDAG: Dieses Konzept des unabhängigen Automobilentwicklers EDAG verfügt über eine 3D-gedruckte, von der Natur inspirierten tragenden Struktur, die dem Gezweige von Bäumen nachempfunden ist. Obwohl das Tragwerk weniger Material verbraucht als ein herkömmliches Fahrgestell, werden alle Anforderungen an statisch relevante Bauteile erfüllt. Um das Fahrgestell gegenüber Witterungseinflüssen widerstandsfähig zu machen, ist das Tragwerk mit einem Stoff überzogen.
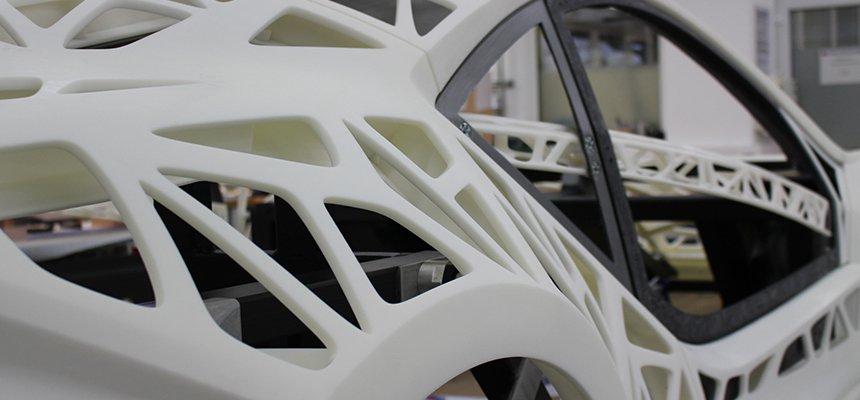
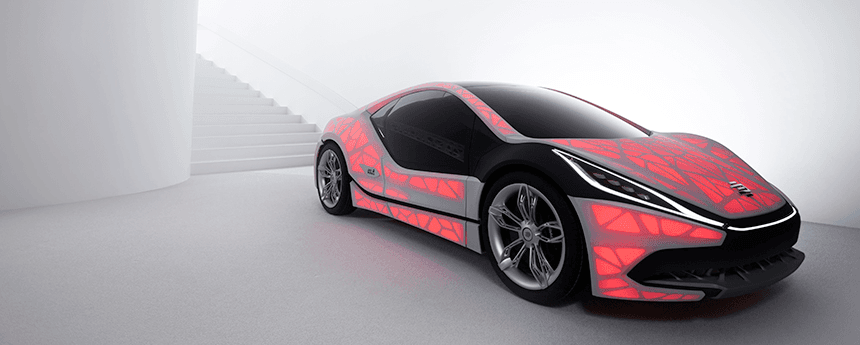
Neben seiner Witterungsbeständigkeit bietet die Verkleidung des Light Cocoon von EDAG absolute Design- und Individualisierungsfreiheit. (Quelle: EDAG)
The Blade: Das „erste 3D-gedruckte Superauto der Welt“ wird aus – für Superauto-Standards – kostengünstigen Materialien wie Kohlenstoffaserrohren und Aluminiumstäben hergestellt, die mit generativ entworfenen 3D-Druckmetallteilen kombiniert werden, um ein geringes Gewicht und eine hohe Leistung zu gewährleisten.
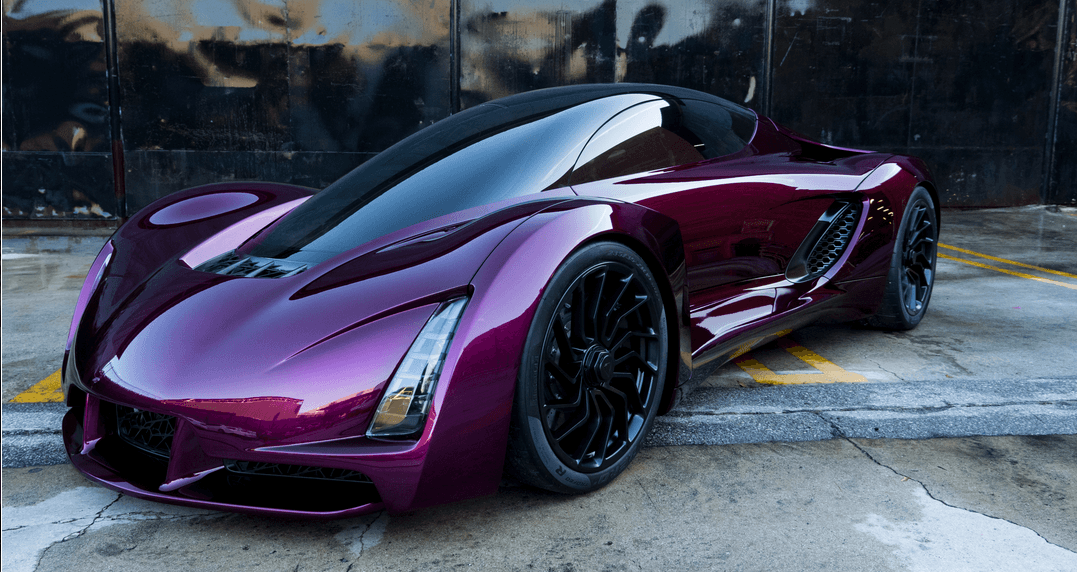
The Blade ist das „erste 3D-gedruckte Superauto der Welt“. (Quelle: Divergent3D)
Strati: Das erste Elektroauto der Welt, bei dessen Herstellungsprozess Local Motors massiv den 3D-Druck einsetzte. Das Auto besteht aus 50 Einzelteilen; deutlich weniger als die rund 30 000 Teile, aus denen sich ein herkömmliches Fahrzeug zusammensetzt. Sein Fahrgestell und die meisten tragenden Elemente wurden in weniger als 24 Stunden in 3D gedruckt – ein Wert, den das Unternehmen auf unter zehn Stunden senken will.
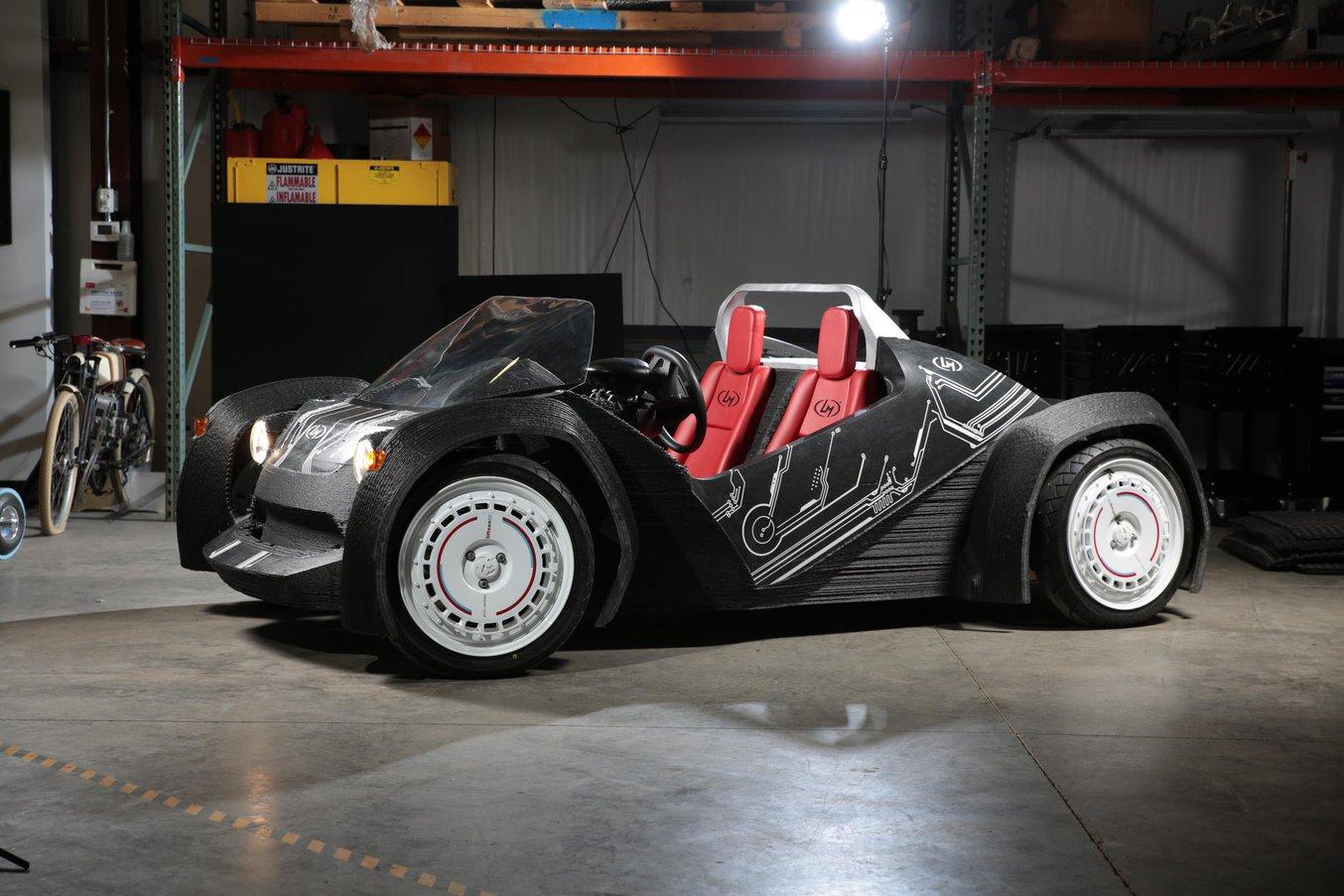
Strati besteht aus 50 Einzelteilen und wurde in weniger als 24 Stunden in 3D gedruckt.
LSEV: Das LSEV, von dem italienischen Unternehmen XEV entwickelt, könnte das erste „massentaugliche” 3D-gedruckte Elektroauto sein, das im weiteren Verlauf dieses Jahres auf den Markt kommen soll. Abgesehen vom Fahrgestell, den Sitzen und der Windschutzscheibe sind alle anderen sichtbaren Teile des LSEV ebenfalls in 3D gedruckt. Durch den umfassenden Einsatz des 3D-Drucks ist es dem Unternehmen gelungen, die Anzahl der Komponenten von 2000 auf nur 57 reduzieren, was zu einer Leichtbauweise mit einem Gewicht von nur 450 Kilogramm führte.
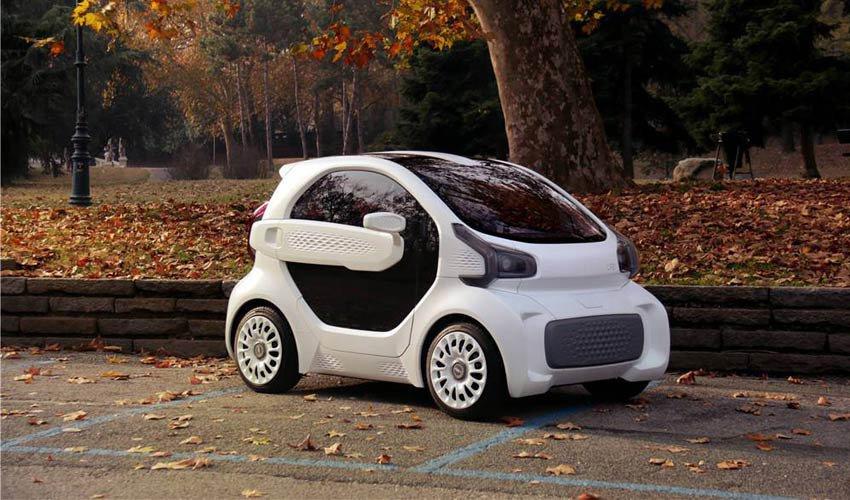
Das LSEV ist das erste „massentaugliche” 3D-gedruckte Elektroauto. Es soll im weiteren Verlauf des Jahres auf den Markt kommen.
Obwohl sich diese und viele andere Projekte, bei denen Autos mittels 3D-Druck hergestellt werden sollen, noch in der Konzeptphase befinden, ist nicht zu leugnen, dass der 3D-Druck verschiedene Bereiche der Automobilindustrie im Sturm erobert. In manchen Fällen überschreitet die 3D-Drucktechnologie Grenzen und hilft, völlig neue Möglichkeiten in Design und Herstellung zu erschließen. In anderen Fällen senkt die Technologie Produktionskosten und spart Zeit.
Mit dem wachsenden Verständnis für den Wert des 3D-Drucks in der Industrie und der zunehmenden Vielseitigkeit der Technologie und der verfügbaren Materialien wird dieser Trend weiter an Dynamik gewinnen.
Weitere Informationen zu Anwendungen für den 3D-Druck in der Fertigung