Mit 3D-gedruckten Formen schafft Kastalon neue Produktkategorien für Polyurethan
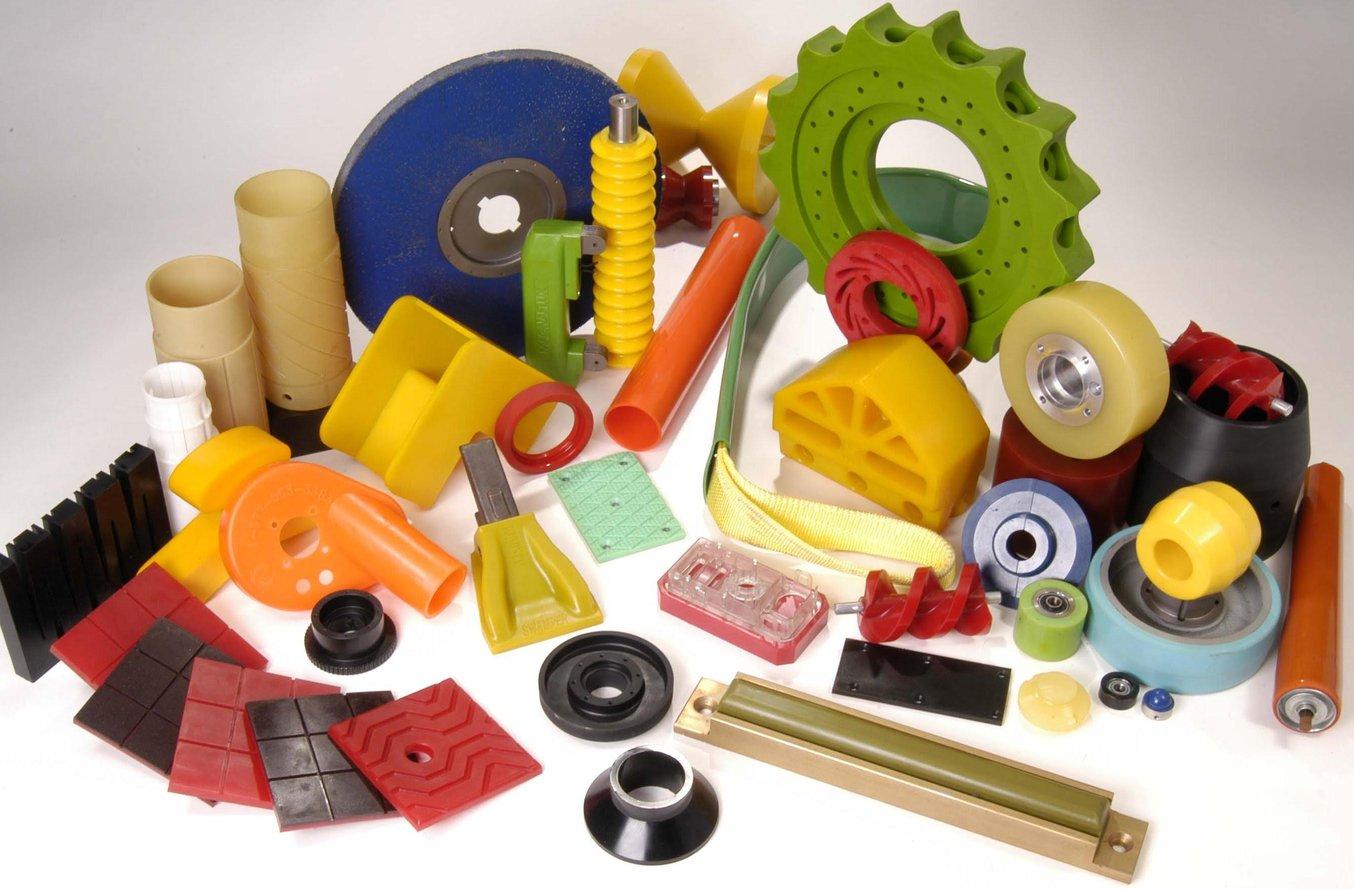
Sie sind von zentraler Bedeutung, aber dennoch oft übersehen: Förderrollen für Fertigungsstraßen, Bremsbeläge für Achterbahnen oder auch Unterlegkeile, die Kampfjets auf einer Stelle fixieren. Bauteile aus Polyurethan sind für den Betrieb eines Gesamtsystems häufig essenziell, obwohl es vielleicht nicht das erste Material ist, das uns beim Blick auf ein Produkt ins Auge fällt. Damit sie als Teil einer komplexeren Baugruppe reibungslos funktionieren, müssen Polyurethanteile mit Hinblick auf optimale Materialnutzung, enge Toleranzen und anhaltende Belastung oder Verformung konzipiert werden.
Der Polyurethan-Hersteller Kastalon mit Sitz in Illinois wendet seit Jahrzehnten Problemlösungstechniken an, um Tausende von individuellen Polyurethanteilen zu produzieren, die diesen vielfältigen Anforderungen gerecht werden. Produktingenieur Brian Baer hat uns erläutert, wie der Form 3L, ein großformatiger Stereolithografie-3D-Drucker (SLA), dem Unternehmen neue Möglichkeiten für die Herstellung von Produktionswerkzeug und Fertigungshilfsmitteln sowie bei der Produktforschung und -entwicklung eröffnet hat.
„Die Möglichkeit, mittels 3D-Druck komplett neue Formen fertigen zu können, stellt bei kleinen Änderungen und Anpassungen einen Riesenvorteil dar. Für uns ist es außerdem eine große Leistung, dass wir die Toleranz von +/- 0,005 Zoll einhalten können. Wir haben Dinge verwirklicht, die vorher nicht möglich waren, und das Produktionsvolumen wächst stetig an.“
Brian Baer, Ingenieur
Kastalon vereint 3D-Druck mit konventioneller Zerspanung
Kastalon entwirft und fertigt Hunderte von individuellen Formen für die Produktion von Teilen aus Polyurethan in Stückzahlen im sechsstelligen Bereich. Wenn Kunden Teile für die Endverwendung anforderten, beurteilte das Team von Kastalon das Modell bisher nach der Umsetzbarkeit des Formenbaus und stellte dann eine Form aus gefrästem Aluminium oder Stahl her.
In der Vergangenheit haben die Kosten und die Komplexität des Zerspanungsprozesses Kastalon – wie viele andere Kunststoffhersteller – manchmal dazu gezwungen, Aufträge abzulehnen, deren Formenbau zu kompliziert war oder die sich für Kleinserien und Prototypenfertigung nicht rentierten. Bei Formen mit zu vielen ineinandergreifenden Merkmalen, kleinen Kanälen oder Stiften waren der Vorgang des Designs, Fräsens und manchmal der kompletten Überarbeitung häufig zu ineffizient. Dennoch war es schmerzlich, Aufträge ablehnen zu müssen. Da Baer im Laufe seiner Ausbildung mit verschiedenen 3D-Drucktechnologien gearbeitet hatte, begann er nach alternativen Lösungen für den Formenbau zu forschen.
Jahre zuvor hatte ein früherer Vorstoß in die Welt des 3D-Drucks bei einem Teil des Teams schlechte Erinnerungen hinterlassen – deshalb suchte Baer bei seiner Recherche gezielt nach bestimmten Kriterien. Das Team benötigte ein Gerät, das Toleranzen von +/- 0,005 Zoll einhält, mit Materialien, die Gusstemperaturen von 80 bis 150 °C widerstehen, und zwar in einem bezahlbaren System.
„Erst als ich Formlabs gefunden hatte und die große Bandbreite an Materialien sah, die hohen Temperaturen standhalten und bestimmte Eigenschaften bieten, war mir klar, dass dieser Drucker tatsächlich für [unsere] Zwecke eingesetzt werden kann.“
Brian Baer, Ingenieur
Ende des Jahres 2022 kam der Form 3L im Betrieb von Kastalon an, doch bis alle Mitarbeitenden an Bord waren, bedurfte es einiger Tests. Einige Teammitglieder waren den Materialien und den erreichbaren Toleranzen gegenüber zunächst skeptisch, bis Baer ein paar Probeteile druckte. „Ich druckte ein Teil für unsere Werkstatt und sie prüften die Oberflächenrauheit Ra. Der Werkstattleiter war sehr beeindruckt, dass sie den Werten entsprach, die ich ihm gegeben hatte, und wie glatt das Teil tatsächlich war“, so Baer.
Inzwischen ist genau dieser Werkstattleiter der Erste, wenn es darum geht, Ersatzteile über 3D-Druck statt über Zerspanung herstellen zu lassen, wie Baer berichtet. „Er ist einer der Ersten, die 3D-Druck vorschlagen, wenn er sich für einen Auftrag anbietet. Die Werkstatt wird von größeren Projekten überschwemmt. Wenn es also etwas Kleines gibt, das sich auch drucken lässt, möchte er, dass wir das übernehmen und ihm mehr Bandbreite verleihen“, erzählt Baer.
Ein neues Kapitel für Design, Test und Betrieb
Der 3D-Druck eröffnet neue Möglichkeiten für das Formen von Polyurethanteilen. Das Entwicklerteam von Kastalon kann neue Designmerkmale und Geometrien ausprobieren, die mit Metallformen nicht umsetzbar sind, oder kleine Designänderungen durchführen, ohne dass dadurch eine zerspante Form obsolet wird. Das Team kann neue Designs mit Bestimmtheit realisieren, da es in der Lage ist, ausgiebig zu testen und zu iterieren, ohne befürchten zu müssen, dass die vielen kleinen Änderungen die Metallwerkstatt überfordern.
Form für Endabzieherklammer: Dank 3D-Druck umsetzbar
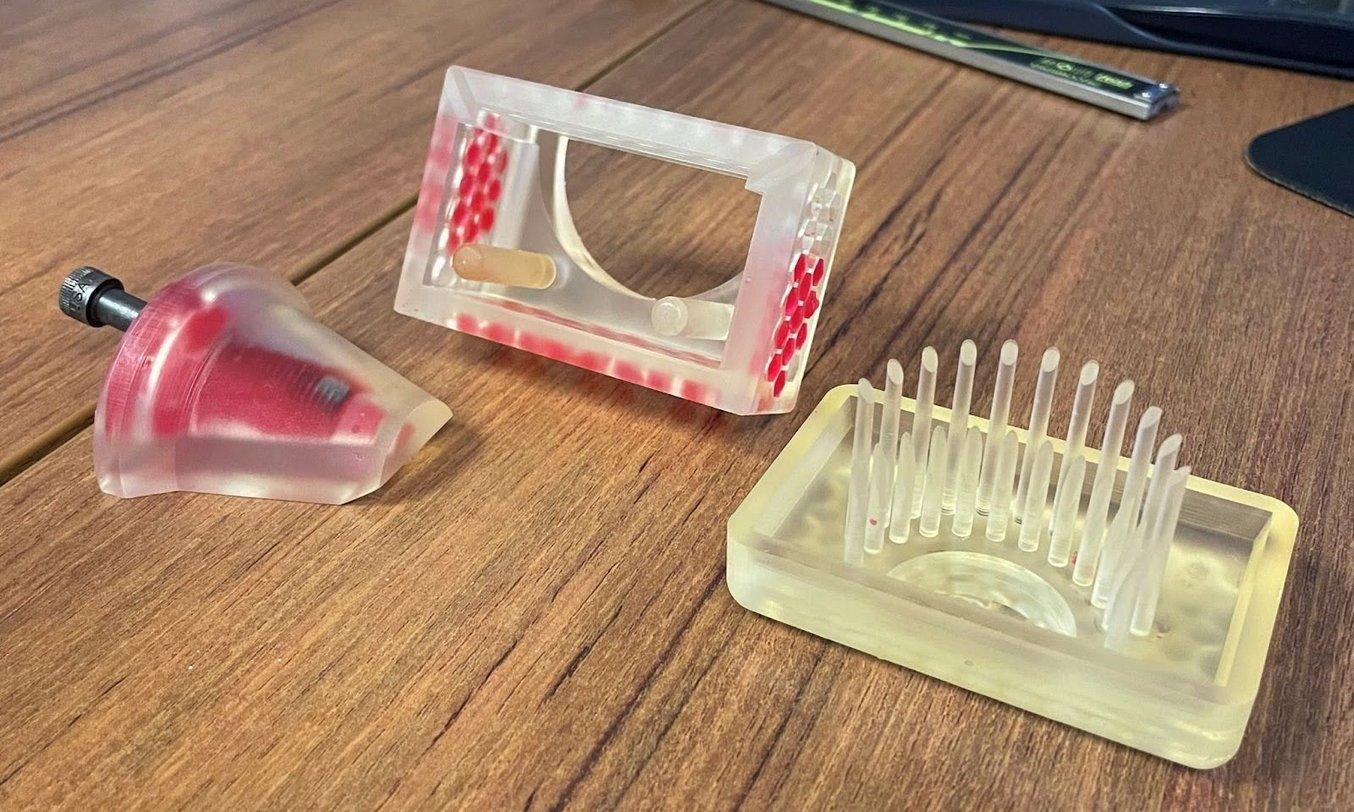
Kastalon musste einem Kunden eine Absage erteilen, der ein Teil mit 24 Sacklöchern mit Versatz von der Oberfläche anforderte – denn das Fräsen einer Gussform hierfür wäre schlicht zu schwierig gewesen.
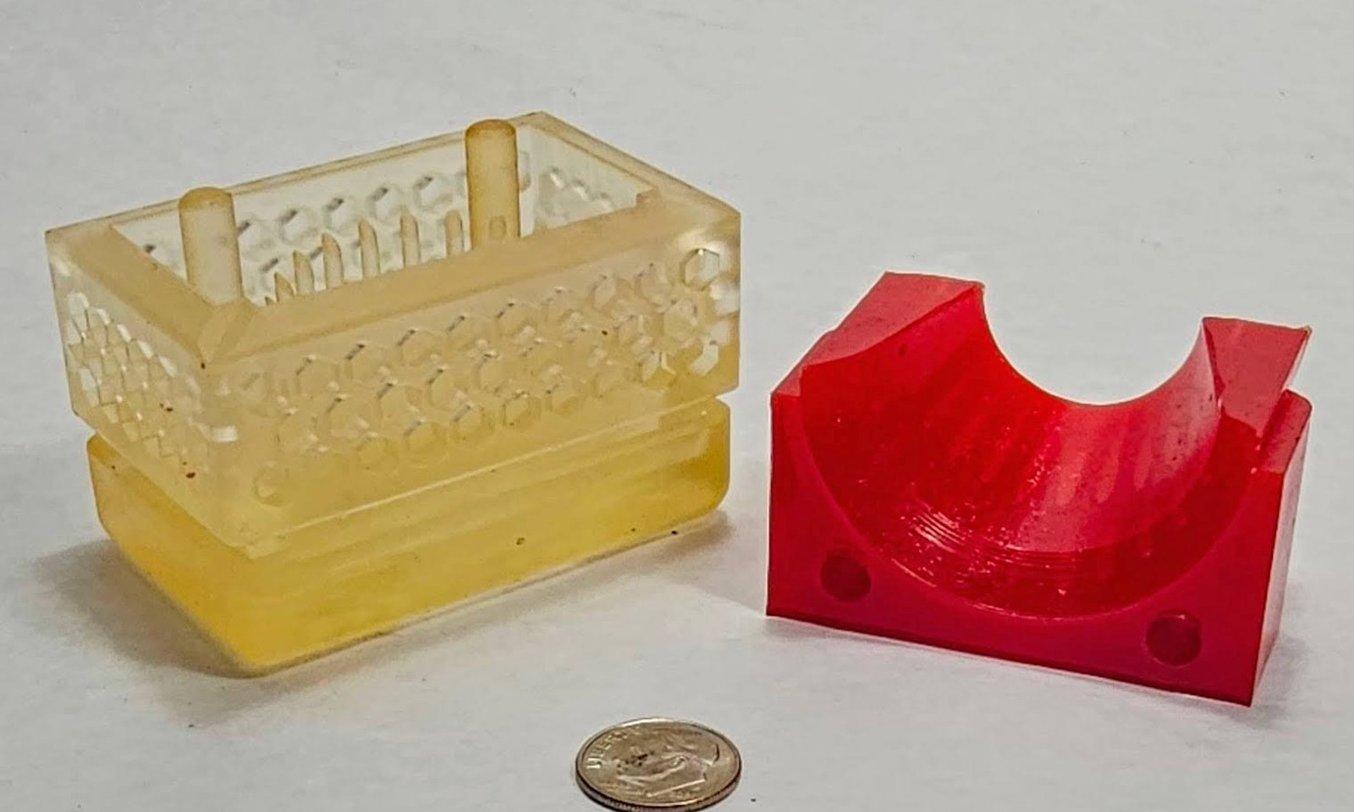
Mit dem Form 3L und High Temp Resin war Baer in der Lage, das endgültige Polyurethanteil (rechts) durch Guss in einer 3D-gedruckten Form in unter einem Tag zu fertigen.
Vor dem Erhalt seines Form 3L musste das Team von Kastalon einem Kunden mitteilen, dass es den Auftrag einer Endabziehklammer nicht umsetzen kann. Mit ausgiebigen Tests und Neuversuchen wäre es vielleicht möglich gewesen, allerdings reichen die 24 Stifte im Bauteil nicht komplett durch das Teil hindurch und weisen einen Abstand von nur 0,03125 Zoll auf.
Aufgrund dieser Abstände und der Tatsache, dass es sich um Sacklöcher handelt, die mit Versatz unter der Teiloberfläche enden, ließe sich dieses Teil mittels Zerspanungsverfahren nur extrem schwer und mit filigranen, langen Schneidwerkzeugen herstellen. Eine Alternative wäre, die Stifte einzeln zu produzieren und sie dann so zu befestigen, dass sie in der richtigen Ausrichtung positioniert sind. Da jeder Stift jedoch nur einen Durchmesser von 0,104 Zoll hat, wäre das keine leichte Aufgabe.
Nachdem es die verschiedenen möglichen Zerspanungsprozesse beurteilt hatte, musste das Team sich für die Ablehnung des Auftrags entscheiden. „Wir haben lange diskutiert, ob es möglich wäre, und es war eine schwere Entscheidung, dem Kunden eine Absage zu erteilen“, erinnert sich Baer.
Nur wenige Wochen später traf der Form 3L im Werk ein, und innerhalb eines halben Tages entwarf und druckte Baer die benötigte Form, womit er den geschäftlichen Nutzen des 3D-Drucks derart komplexer Geometrien demonstrieren konnte. Die Materialkosten lagen bei knapp über 30 $ und für das Design benötigte Baer etwa zwei Stunden. „Alle gewannen sofort einen riesigen Respekt vor 3D-Druck. Es öffnete vielen der Angestellten im Werk die Augen. Sie erkannten: Wir können jetzt mehr Aufträge annehmen, weil wir derartige Dinge nun realisieren können“, so Baer.
Quetschschutz-Räder
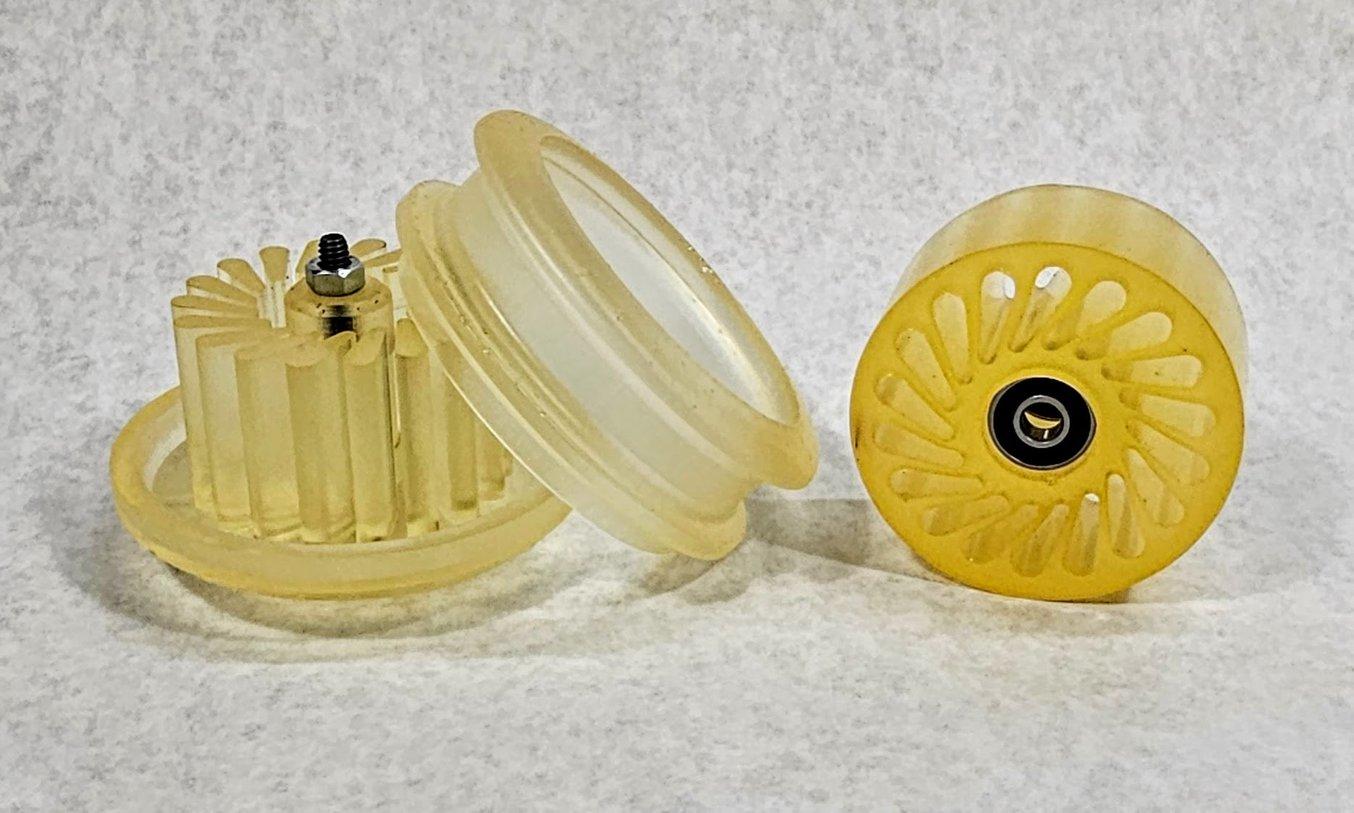
Diese Formen (links, oben und unten) und fertigen Räder (rechts) sind so konzipiert, dass sie sich bei Überbelastung gleichmäßig verformen. Durch die tropfenförmigen Öffnungen wird das Gewicht gleichmäßig verteilt, damit das Rad das Produkt nicht zerdrückt.
Der Form 3L glänzt in Fällen, wo sich Formen aufgrund filigraner Details schwer zerspanen lassen. Diese kleinen Quetschschutz-Räder, die dazu dienen, verformbare Produkte (beispielsweise Kartonverpackungen) auf Fördersystemen festzuhalten, werden anstelle von Federkonstruktionen verwendet. Statt dass eine Feder Druck auf den Karton ausübt, wird das Rad selbst gleichmäßig verformt, um den Karton sanft festzuhalten.
Allerdings weisen die Gussformen für die Räder einen äußerst kleinen Abstand zwischen den „Finnen“ auf, mit denen die tropfenförmigen Öffnungen in den Rädern geformt werden. Das macht die Herstellung der Form zu einer fast unmöglichen Herausforderung.
Die Räder haben eine Breite von 2 Zoll und zwischen den Finnen eine Wandstärke von 0,125 Zoll. Baer erklärt: „Zwei Zoll tiefe Löcher mit 0,125 Zoll Abstand mögen zwar möglich sein, aber man zieht den Zorn vieler Metallwerkstätten auf sich, wenn man ihnen so ein Design zuschickt.“
Zusätzlich zur Schwierigkeit des Zerspanungsvorgangs würde eine mehrteilige Aluminiumform auch den Montageprozess komplizierter machen. Es muss ein Kompromiss geschlossen werden: Entweder wird die Form einschließlich Finnen in einem Stück gefräst (wie in der obenstehenden Abbildung), was die Abstände für Zerspanungsmechaniker extrem schwer umsetzbar macht, oder es werden alle Finnen einzeln gefertigt und montiert, was mehr Aufwand für die Einrichtung und mehr Montage kleiner Teile bedeuten würde und damit zusätzliche Arbeit und Frustration verursacht.
Der 3D-Druck war hier die offensichtliche Lösung, und Baer konnte in Solidworks mit Leichtigkeit eine zweiteilige Form mit einem herausnehmbaren Lager entwerfen, die anschließend aus High Temp Resin und Rigid 10K Resin auf dem Form 3L gedruckt wurde. Mit der Form aus Rigid 10K Resin goss das Team 25 Räder für den Kunden, zu einem Bruchteil der Kosten eines zerspanten Formwerkzeugs. „Wir haben solche kleinen Räder in vielen Variationen und verschiedenen Stilen gefertigt, was vor dem Form 3L nicht möglich war, da es für uns nicht kosteneffizient war,“ so Baer.
Zerspanung | 3D-Druck | |
---|---|---|
Anzahl der Bauteile | 21 | 3 |
Designdauer | 7 Stunden | 3 Stunden |
Einrichtungsdauer | 5 Stunden | - |
Fertigungsdauer | 35 Stunden | 12 Stunden |
Gesamtzeit | 47 Stunden | 15 Stunden |
Interne Tests von Modellen für großformatige Federungen
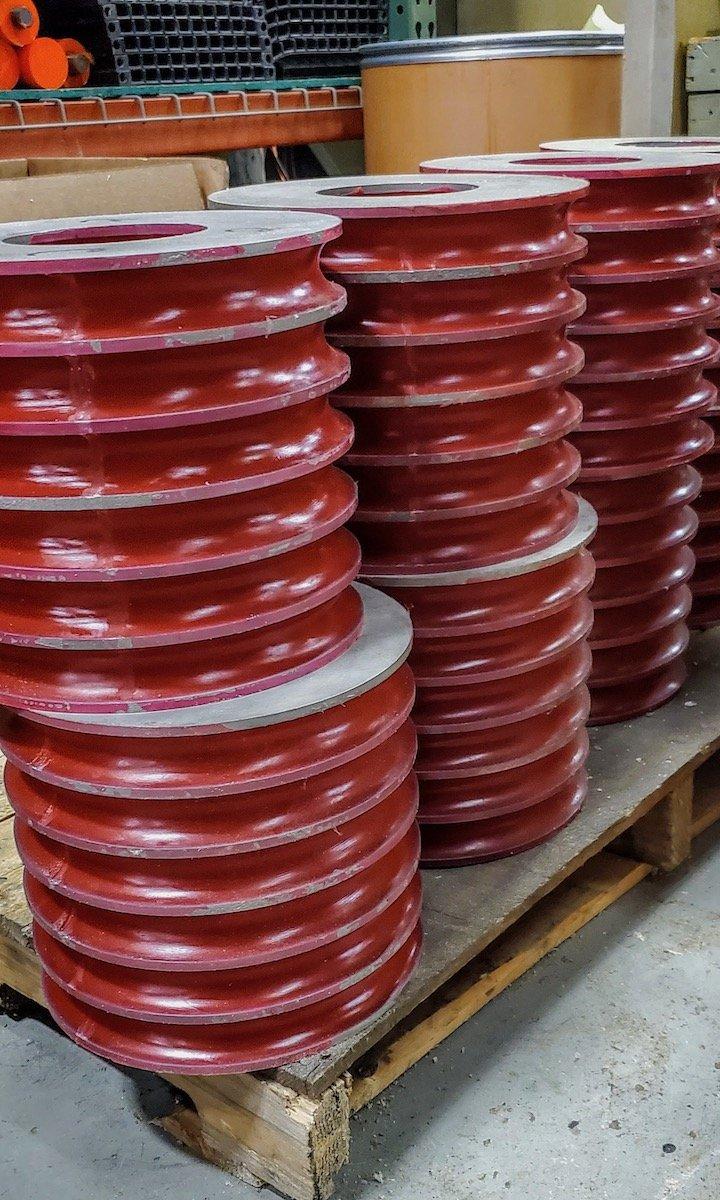
Polyurethanteile wie diese roten Federn werden üblicherweise durch Guss in großen Aluminiumformen produziert.
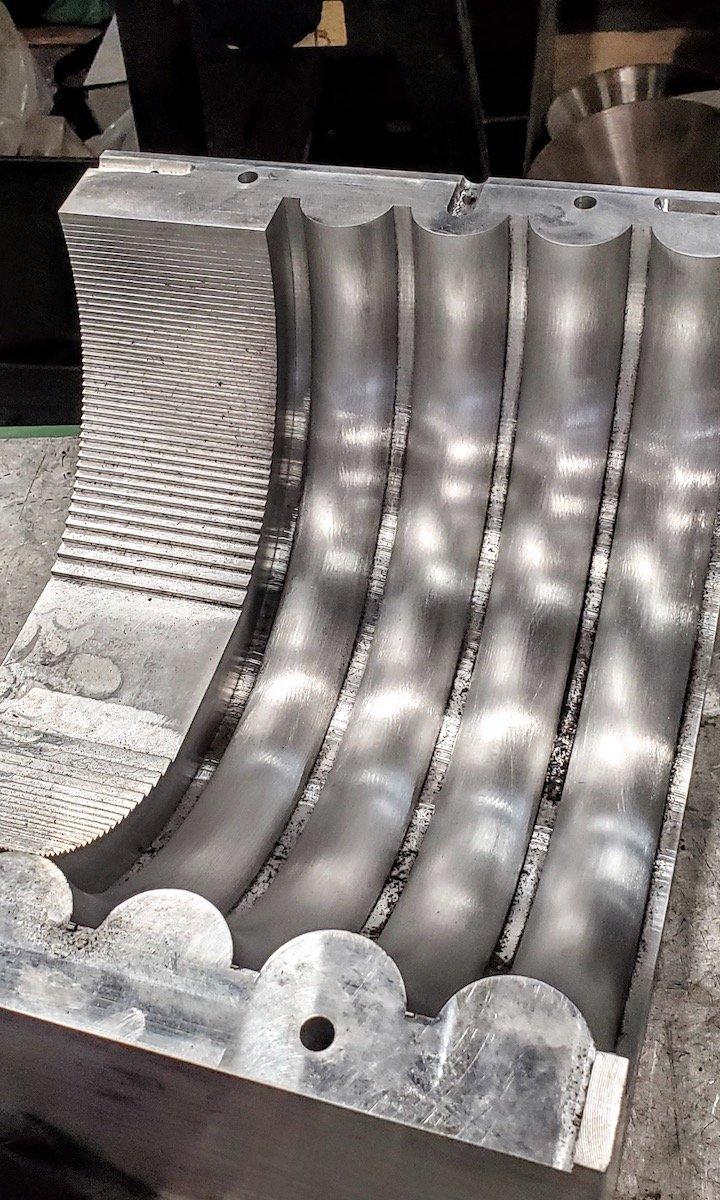
Solche Gussformen aus Aluminium, oder in einigen Fällen aus Stahl, kosten bei spanender Bearbeitung viel Zeit und Geld.
Das Baseball-Stadion Houston Astros ist für den Fall ungünstigen Wetters mit einer herausfahrbaren Kuppel ausgestattet. Mit von Kastalon hergestellten Federn wird diese straff und funktionsfähig gehalten, selbst bei Hurricane-Windstärken.
Vor der Fertigung von Gussformen wie denen für diese Federung im Stadion-Maßstab führt das Team von Kastalon an verkleinerten Modellen umfassende Tests von Design und Material durch. Indem das Design leicht variiert und die Veränderung der Federrate bei verschiedenen Geometrien und verschiedenen Polyurethan-Formulierungen überprüft werden, stellt das Team sicher, dass das Endprodukt für langanhaltende Phasen intensiver Belastung optimiert ist.
Trotz der Veränderung des Maßstabs waren Aluminiumformen aber dennoch kostspielig – besonders, wenn sie nur für die anfänglichen Testphasen gebraucht wurden. Der Form 3L erlaubt es dem Team nun, zu weitaus niedrigeren Kosten zahllose verschiedene Federdesigns zu testen, die zudem nicht die Kapazitäten der Werkstatt blockieren.
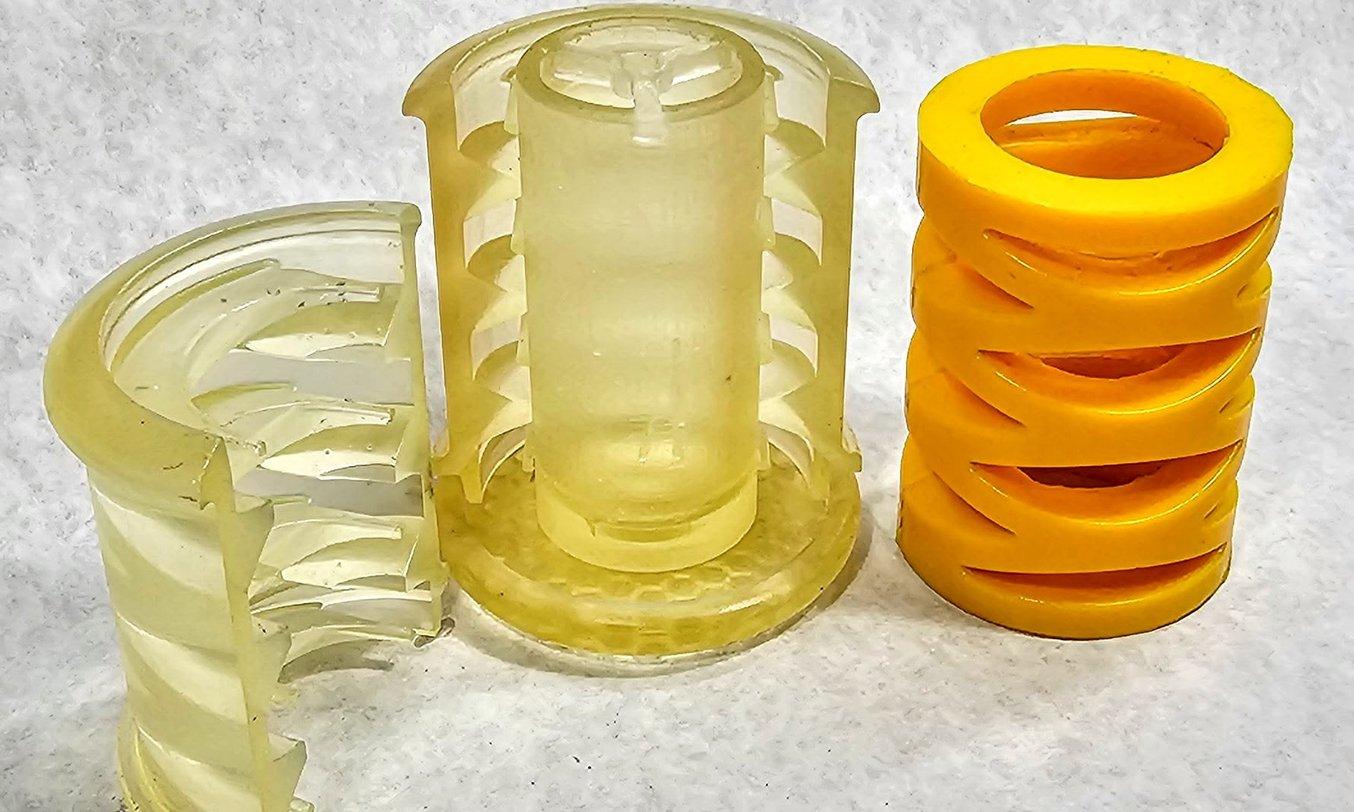
Diese Formen (High Temp Resin, links) und die Federn aus gegossenem Polyurethan (orange, rechts) sind Prototypen, deren Geometrie gestapelte Tellerfedern nachbildet.
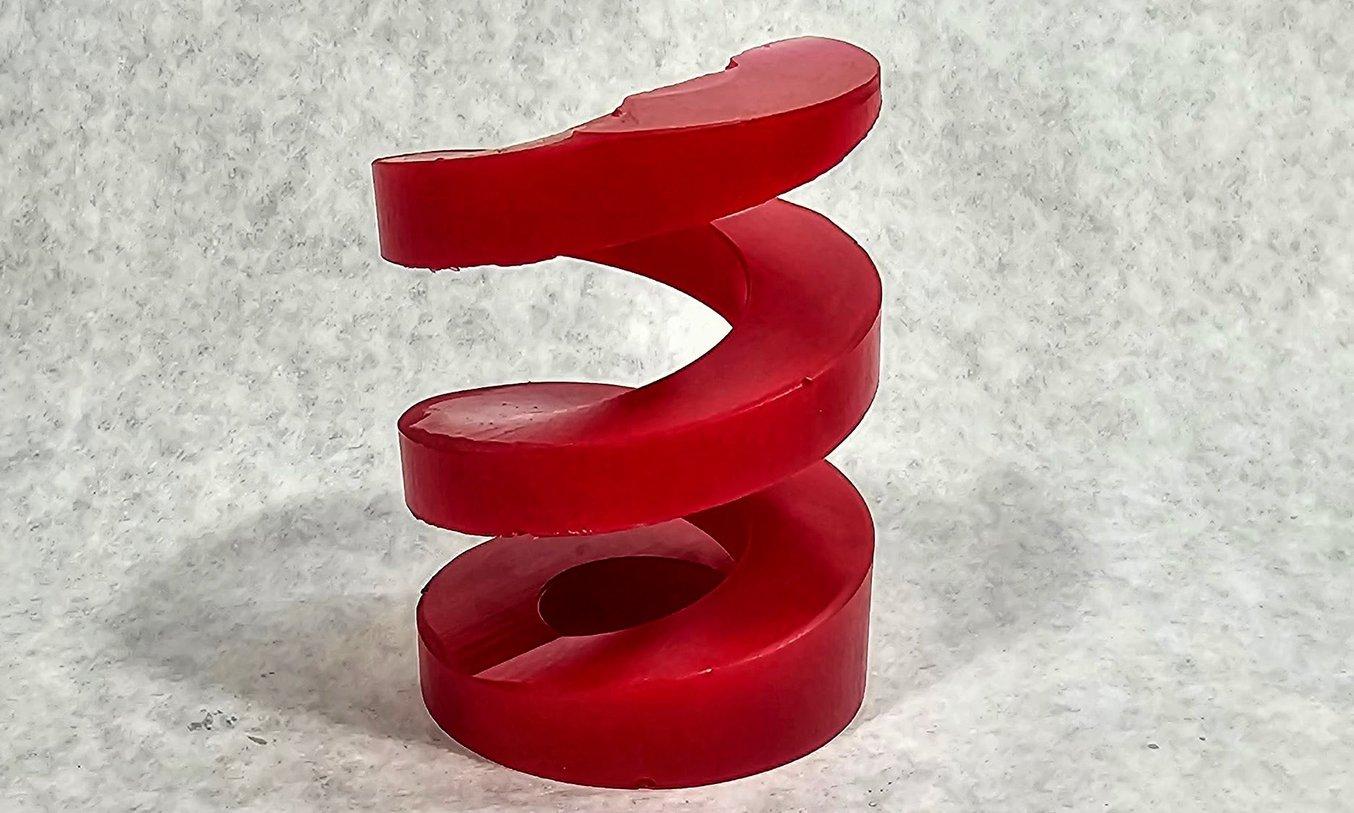
Der 3D-Druck macht es Baer und seinem Team möglich, mit neuen Geometrien und Designs zu experimentieren, ohne für die Metallwerkstatt mehr Arbeit zu generieren.
„Wir können jetzt eine Menge ausgefallener Formen und Geometrien drucken und testen, die vorher für Tests oder Forschung und Entwicklung allein unvorstellbar viel Geld gekostet hätten“, berichtet Baer. Neue, komplizierte Geometrien testen zu können, ohne hohe Zusatzkosten für das Zerspanen von Material und den Arbeitsaufwand zu verursachen, ermöglicht es Kastalon nicht nur, mehr Aufträge anzunehmen, sondern auch bessere Teile für seine bestehenden Kunden zu produzieren.
Gussform für Walzen: Zerspanung von weichem Polyurethan umgehen
Bei beschichteten Walzen oder Hülsen für Walzen beinhaltete der konventionelle Arbeitsprozess den Guss von Polyurethanmaterial in zylindrischer Form, wobei der Außenfläche in einem zusätzlichen Zerspanungsschritt die gewünschte Größe und Oberflächenflächenbeschaffenheit verliehen wurde. Der zusätzliche Arbeitsschritt des Fräsens von Rillen kann je nach Anwendung der Walze in einer Vielzahl von Stilen und Größen erfolgen. In diesem konkreten Fall stellte sich das Fräsen horizontaler Rillen in das weiche Polyurethan als eine mühsame Aufgabe heraus. Bei großen Bestellungen konnte dieser manuelle und arbeitsintensive Zerspanungsschritt den Profit des Auftrags schmälern und Stunden der Arbeitszeit in der Metallwerkstatt beanspruchen. „Das Zerspanen von weichem Polyurethan ist eine unsaubere Aufgabe, liefert nicht immer gute Ergebnisse und erzielt auch beim Schneiden nicht immer ein gutes Finish“, erklärt Baer.
Die Rillen direkt einzufräsen hätte pro Walze etwa drei Stunden gedauert. Die Herstellung einer Metall-Gussform durch Zerspanung war jedoch zu teuer und riskant, besonders, da vorher nie eine Form mit dieser Geometrie erstellt worden war und nicht klar war, ob der Vorgang funktionieren würde. Um eine Metallform herzustellen, hätte das Team ein Drahtwerkzeug oder eine Fräse mit einem Teilkopf benötigt – teure Ausrüstung, die stark auf bestimmte Geometrien und Anwendungen spezialisiert ist.
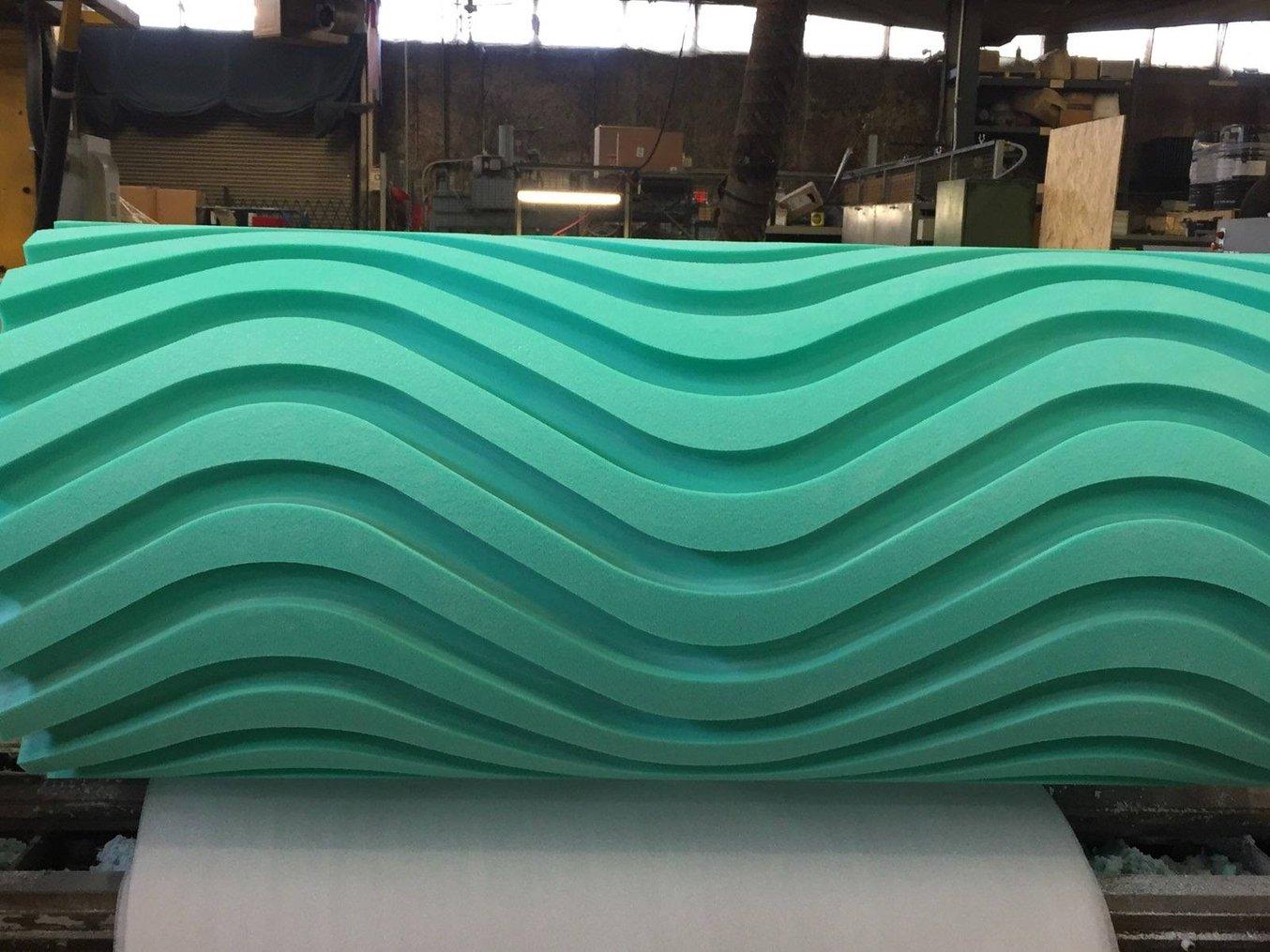
Die Zerpanung von weichem Polyurethan kann unsauber und zeitaufwendig sein, besonders bei großen Teilen wie dieser Walze, die als Zylinder gegossen und dann zerspant wird, um die endgültige Form zu erhalten.
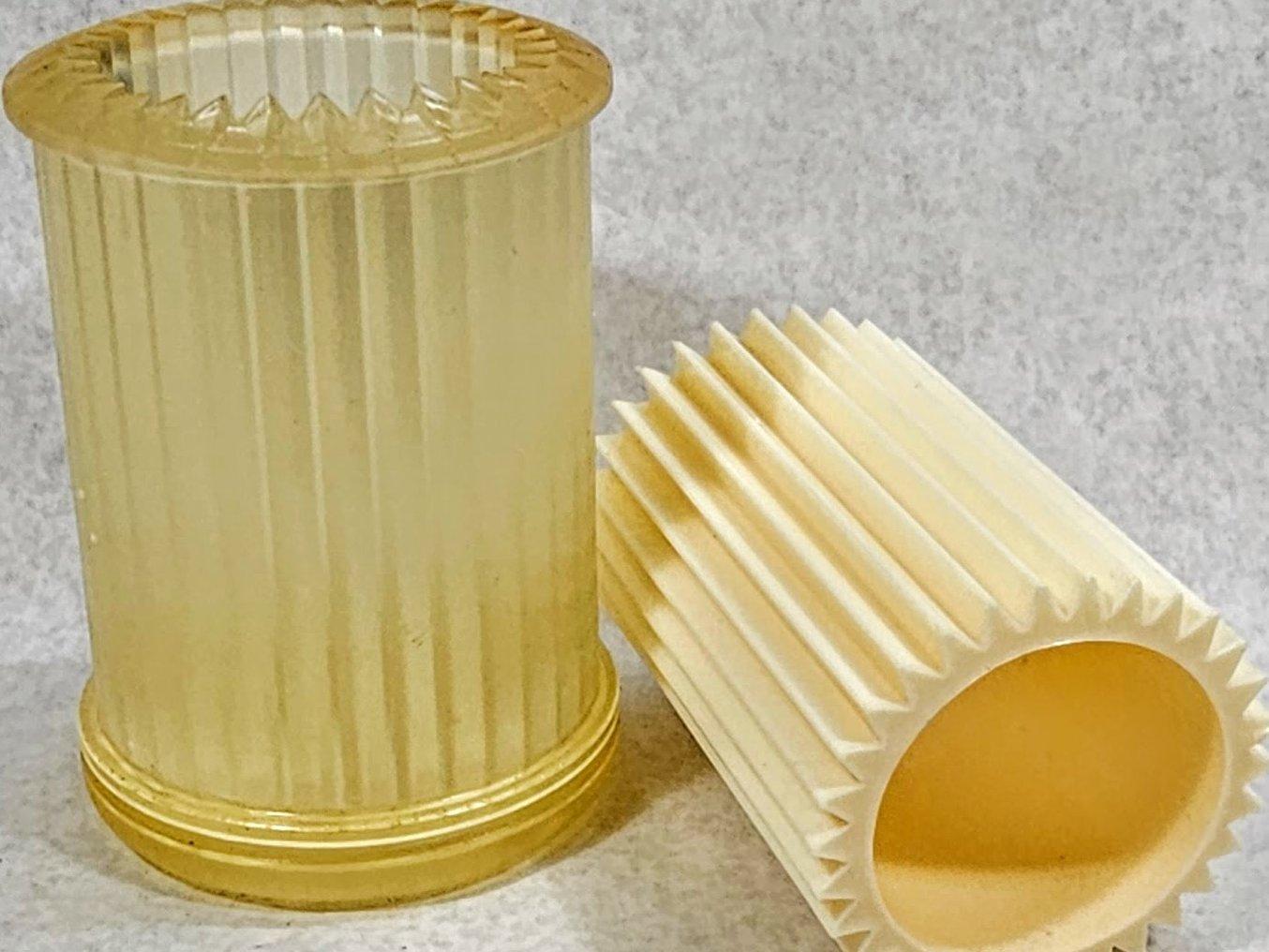
Sind die Werkstücke klein, kann das Fräsen von kleinen Rillen nahezu unmöglich sein. Baer erstellt vorgerillte Formen mit 3D-Druck, sodass direkt beim Guss ein fertiges Teil erstellt wird, das keine weiteren Zerspanungsarbeiten benötigt.
Baer erkannte die Sachlage und nahm es in die Hand, etwas Neues auszuprobieren. Er entwarf und druckte eine Form, mit der das Polyurethan direkt in die geforderte gerillte Geometrie gegossen werden konnte. Der direkte Druck der Form auf dem Form 3L aus High Temp Resin oder Rigid 10K Resin lieferte eine kosteneffiziente Lösung, mit der Stunden der manuellen Arbeit eingespart wurden.
Bei der Wahl eines Materials berücksichtigt Baer Auflösung, Schichthöhe, Kosten pro Liter, Festigkeit und Farbe/Transparenz. Davon ausgehend fällt seine Wahl meistens auf High Temp Resin oder Rigid 10K Resin. Für Prototypen, Einzelstücke oder sehr kleine Stückzahlen kommt High Temp Resin zum Einsatz, aufgrund seines geringeren Preises und der Transparenz – denn bei Prototypen ist es hilfreich, auch das Innere sehen zu können, um über Designänderungen zu entscheiden. Doch für Teile, die in größeren Mengen gegossenen werden sollen, stützt sich das Team auf die überlegenen mechanischen Eigenschaften von Rigid 10K Resin. „In letzter Zeit haben wir mehr Rigid 10K Resin verwendet, hauptsächlich weil es dem Entformungsprozess besser standhält.“
Zerspanung | 3D-gedruckte Form | |
---|---|---|
Teile pro Jahr | 40 | 40 |
Formeinrichtung | 1 Stunde | 1 Stunde |
Manuelle Arbeit nach dem Guss pro Teil | 3 Stunden | 0 Stunden |
Gesamtzeit | 160 Stunden | 40 Stunden |
Gesteigerte Kapazität und verbesserte Produkte
In weniger als einem Jahr hat der Form 3L den Entscheidungsprozess bei Kastalon völlig neugestaltet. Da das Ingenieurteam sich nicht mehr an die Einschränkungen konventioneller Zerspanung halten muss, kann es Aufträge annehmen, an die es sich zuvor nicht herangewagt hätte, und hat Prozesse optimiert, die bisher Tausenderbeträge für Arbeitszeit und Material verschlangen.
„Unser Durchsatz hat sich erhöht. Wir haben eine Menge Selbstvertrauen gewonnen, und die Aufträge für den Form 3L häufen sich stetig an. Wir können neue Dinge ausprobieren und dem Vertriebsteam dabei helfen, die Wünsche der Kunden zu erfüllen, auch wenn es zunächst nur ein oder zwei Dinge sind – einfach um zu zeigen, dass es möglich ist.“
Brian Baer, Ingenieur
Die Zerspanungsmechaniker von Kastalon haben sich durch ihre Präzision, Konsistenz und hervorragende Leistung einen Ruf erarbeitet. Das Repertoire durch 3D-gedruckte Formen zu erweitern war zunächst ein umstrittener Schritt, doch die Ergebnisse sprechen für sich. Nachdem die mechanischen Eigenschaften, Toleranzen und die geometrische Freiheit, die sich mit Stereolithografie erreichen lassen, einmal demonstriert waren, begann selbst der Werkstattleiter mit dem 3D-Druck von Teilen.
Um mehr über Rapid Tooling zu erfahren, besuchen Sie unsere Website rund um diese Anwendung. Um den Form 3L kennenzulernen, besuchen Sie unsere Produkt-Website.