Design, Innovation und Fertigung an jedem beliebigen Ort mit dem Fuse 1 und Fusion 360
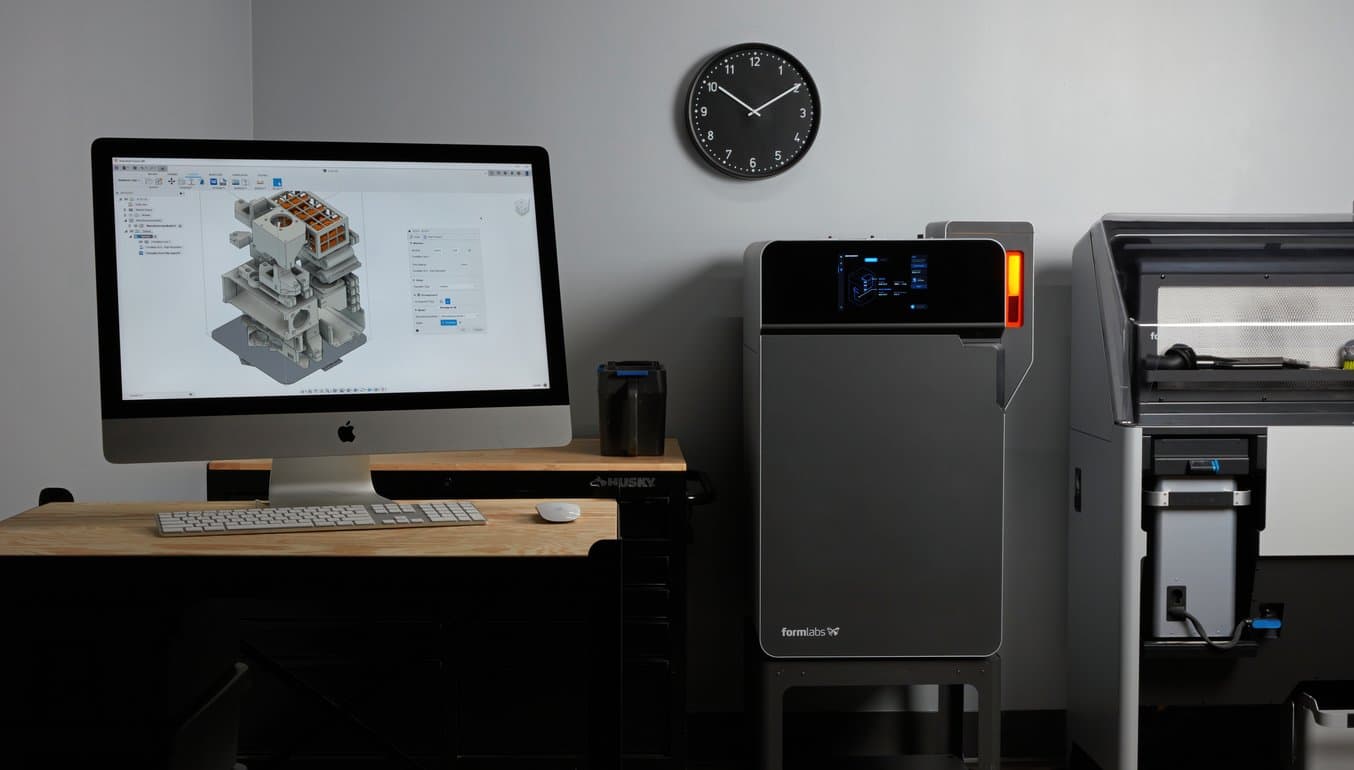
Der Formlabs Fuse 1 SLS-Drucker ist ab sofort noch enger mit den Tools für CAD-Design und 3D-Druck rund um Autodesk Fusion 360 integriert. Hierdurch wird die im Mai 2021 beschlossene Kooperation mit Autodesk dahingehend ausgeweitet, dass nun sämtliche Formlabs-Drucker innerhalb der Bibliothek von Fusion 360 verfügbar sind. So entsteht ein so umfassendes wie unkompliziertes Toolset, das Design, Innovation und Fertigung von Endverbrauchsteilen kompakt an einem Ort vereint.
Die Updates zur bestehenden Softwareintegration umfassen neue Features, durch die von der Designphase eines Produkts bis zu seiner Fertigung weniger Schritte vonnöten sind. So lässt sich über die grafische Benutzeroberfläche nun die Passung von Druckteilen in der Konstruktionskammer des Fuse 1 visualisieren und mit Kommentaren versehen, außerdem die Anordnung mehrerer Teile in kürzester Zeit automatisch optimieren. Individuell anpassbare Design-Dashboards sorgen dabei für weitreichende Reproduzierbarkeit sowie unkomplizierten Zugriff auf häufig benötigte Fertigungsabläufe. Dank der Möglichkeit zum direkten Export im FORM-Dateiformat aus Fusion 360 wird bei der Arbeit im Team zudem die Versionskontrolle erleichtert. Künftig wird dabei auch ein Direktexport nach PreForm möglich sein.
Formlabs ebenso wie Autodesk entwickeln ihre Tools stets mit der Hand am Puls der Anforderungen ihrer Nutzer-Community, zu denen insbesondere auch die Flexibilität gehört, Innovation an jedem beliebigen Standort umsetzen zu können. Genau dem trägt die Integration der funktionsstarken CAD-Plattform von Autodesk mit der professionellen SLS-Technologie von Formlabs in einem Verbund Rechnung, der von Designern und Ingenieuren bis hin zur Unternehmensführung alllen Beteiligten eine mühelos umsetzbare Methodik zur Fertigung an die Hand gibt. So auch die beiden Innovatoren, die wir im Folgenden vorstellen: Gestützt auf den Fuse 1 und Fusion 360 sind sie in der Lage, auf dem Weg zur Fertigung innovativer Lösungen für ihre Kunden nicht nur Kosten zu senken, sondern auch schneller im Sinne der Produktoptimierung zu iterieren.
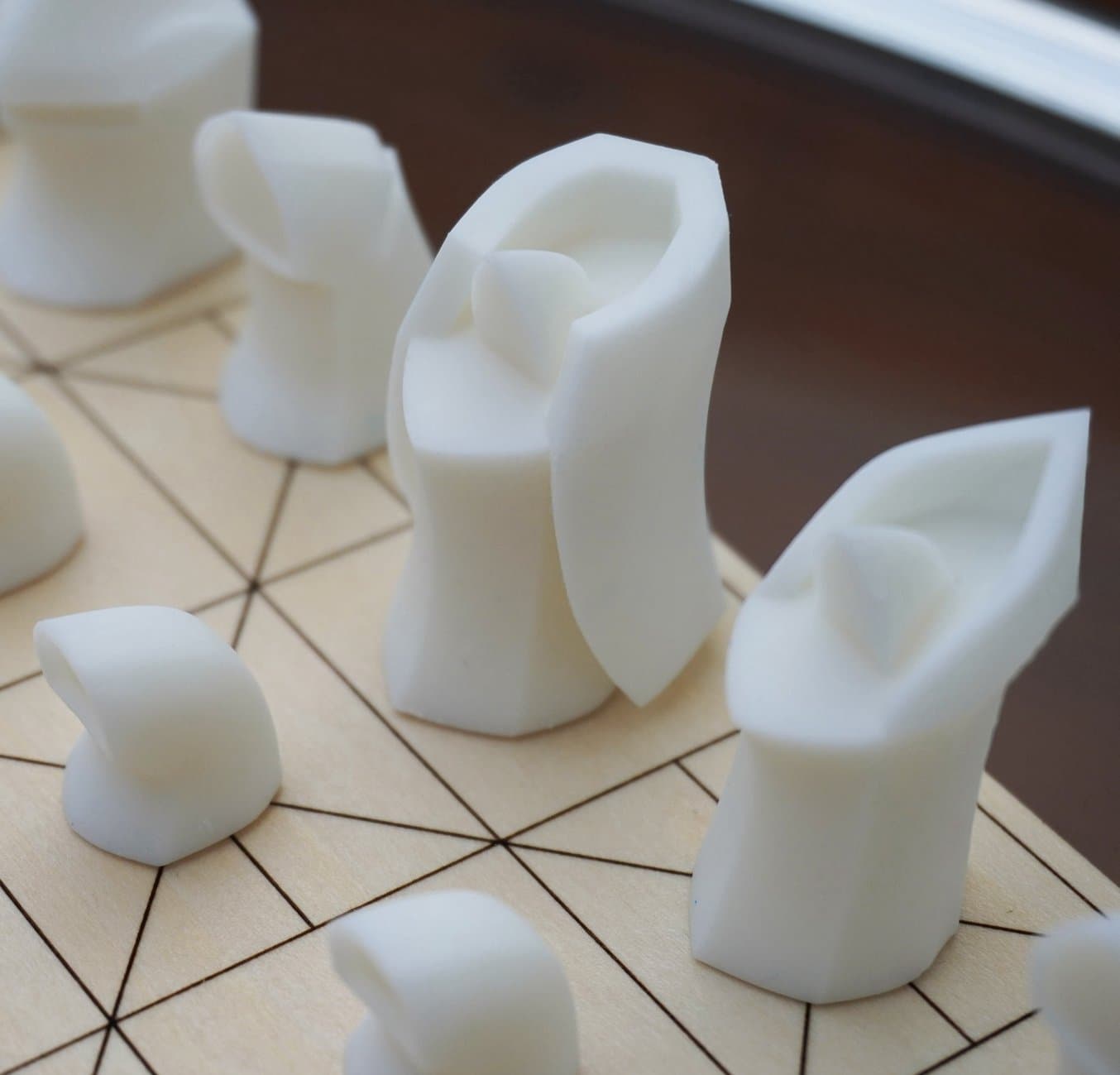
Integration von Formlabs und Fusion 360
Formlabs und Autodesk Fusion 360 arbeiten zusammen, um Ihren digitalen Arbeitsablauf zu optimieren ― mit einer neuen CAD-Software für 3D-Druck-Integration. Besuchen Sie unseren Integration Hub, um mehr über die neuesten SLA- und SLS-Funktionen von Fusion 360 zu erfahren, weitere Geschichten unserer Nutzer zu lesen und unseren Design-Leitfaden herunterzuladen. (Bild: Schachspiel von Will Qiu)
KUHMUTE: Mikromobilität besser gelöst
Als Peter Deppe und Scott Spitler KUHMUTE im Jahr 2018 ins Leben riefen, hatte die Popularität von E-Roller gerade ihre erste große Welle erfahren. Die Vorteile, die die Technologie als für alle einfach zugängliches Transportmittel bot, lagen für die beiden auf der Hand. Unzufrieden waren die Gründer aus Flint im US-Bundesstaat Michigan allerdings mit der mangelhaften Organisation rund um diese: Überall standen die E-Fahrzeuge in ihrer Heimatstadt im Weg herum, verursachten so etwa auch Probleme in puncto Sicherheit. Genau hier setzten die Gründer an, indem sie mit KUHMUTE eine universelle Ladestation entwickelten, die eine adäquat organisierte Infrastruktur für diverse E-Roller-Flotten zur Verfügung stellt. Und nicht nur das: Gestützt auf 3D-Drucktechnologie konnten sie die Ladestationen zudem so konstruieren, dass sie auch mit Rollstühlen, E-Bikes und Lieferrobotern kompatibel sind. Damit tragen sie auch Anwendern mit körperlichen Einschränkungen sowie unterschiedlichen Anforderungen an die Reisereichweite Rechnung.
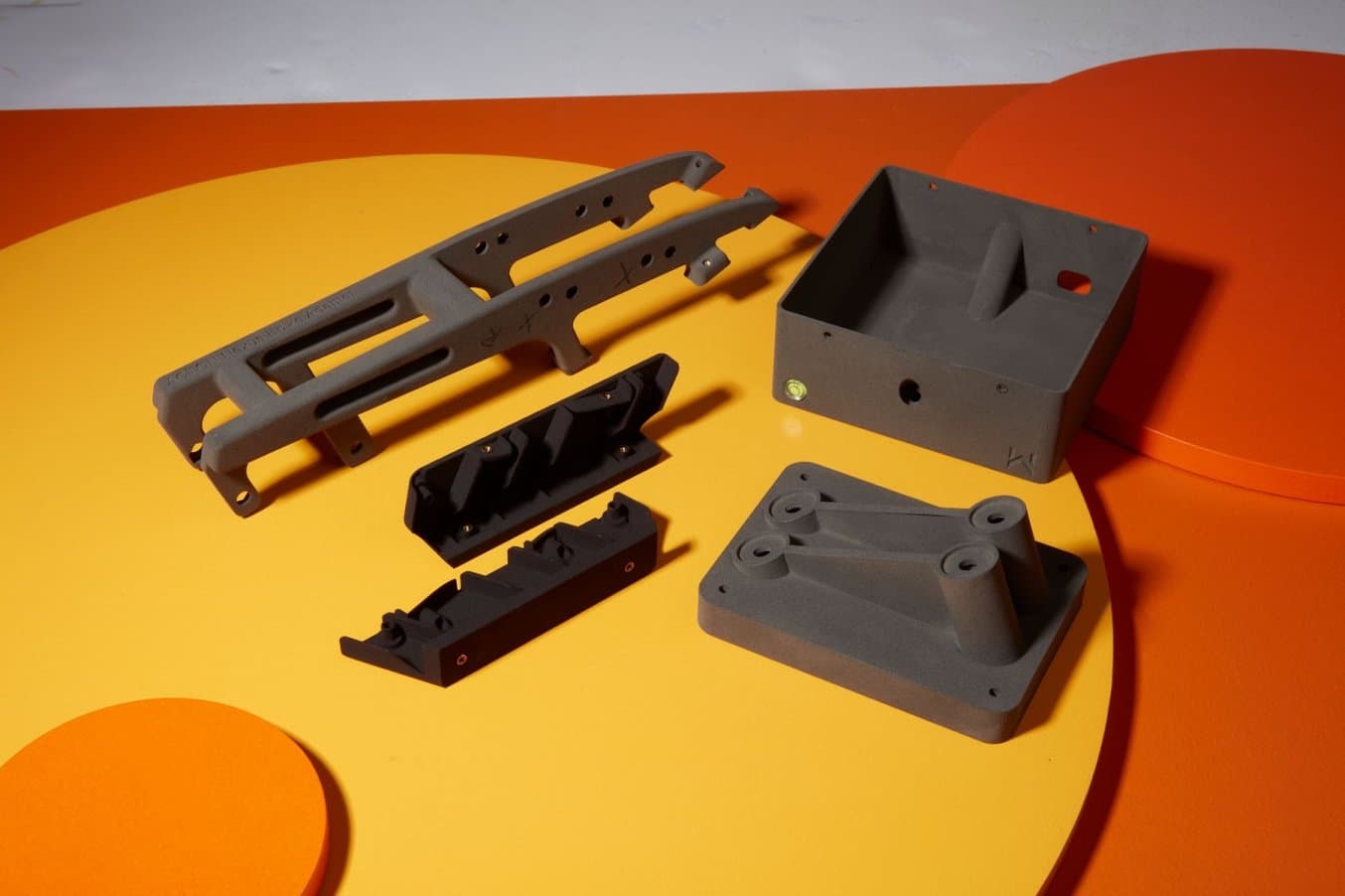
KHUMUTE setzt sowohl für den Druck von Prototypen als auch für die Serienfertigung auf SLS-Nylonteile aus dem Fuse 1.
Eine Vielzahl der Komponenten, die in der zur Endanwendung ausgelieferten Ladestation verwendet werden, werden aus SLS-Nylonpulver im Fuse 1 gedruckt. So etwa auch der Adapter, dank dem sich an allen Standorten mit KUHMUTE-Ladestation verschiedenste E-Fahrzeuge anschließen lassen.
Die ersten Schritte auf dem Weg zur Entwicklung der Technologie machte das Team in klassischer Start-up-Manier in der Wohnung eines Kollegen, bei dem sie mit einem 3D-Drucker im FDM- bzw. Schmelzschichtungsverfahren die ersten Teile fertigten. Die so entstandenen Prototypen der mechanischen Baugruppen machten jedoch schnell deutlich, dass es auf dem Weg zum Endprodukt mehr Präzision und Oberflächengüte brauchen würde. So kam das Team schließlich zum Form 3, der es direkt vom höchst intuitiven Bedienkonzept der 3D-Drucker und Software von Formlabs überzeugte. Dies gab im vergangenen Jahr dann den Anstoß für die Anschaffung eines Fuse 1, im Zuge derer man bereits kurze Zeit auch Teile für die Endanwendung aus SLS-Nylon druckte.
„3D-Drucker vermitteln uns unter anderem die Möglichkeit, die meisten Teile direkt bei uns im Betrieb zu fertigen. Neben der damit verbundenen Wettbewerbsvorteile bedeutet dies vor allem auch, dass wir Innovationen rund um unsere Vision von mehr Mobilitätsoptionen in städtischen Gebieten schneller umsetzen und vorantreiben können.“
Peter Deppe, Mitgründer und CEO von KUHMUTE
Die Vielfalt, die Formlabs dem Team in Sachen Materialauswahl bietet – dank seiner SLA- und SLS-Drucker kann es Teile aus Kunstharzen wie Clear Resin ebenso fertigen wie aus gesintertem Nylonpulver –, ist das eine. Das multifunktionale Toolset, das es mit Fusion 360 für das Design erhält, ist das andere. Sämtliche mit dem Design verbundenen Aspekte wickelt das Team mit Fusion 360 ab. Dazu gehören nicht nur Produktdesign und -visualisierung, sondern etwa auch Grafik-Renderings für die Website und Icon-Designs für die KUHMUTE-App. Hinzu kommt die enge Integration von Fusion 360 mit EAGLE. Damit kann das Team 3D-Modelle von Leiterplatinen in die CAD-Software importieren und so passende Designs für die Verkleidung ausgestalten.
Die KUHMUTE-Ladestationen für Mikromobilität werden bereits Ende dieses Jahres in diversen Städten der USA verfügbar sein. Wer dort also etwas Kleineres als ein E-Auto fährt, kann sich schon bald auf eine intelligentere Lösung zum Aufladen seines E-Fahrzeugs freuen.
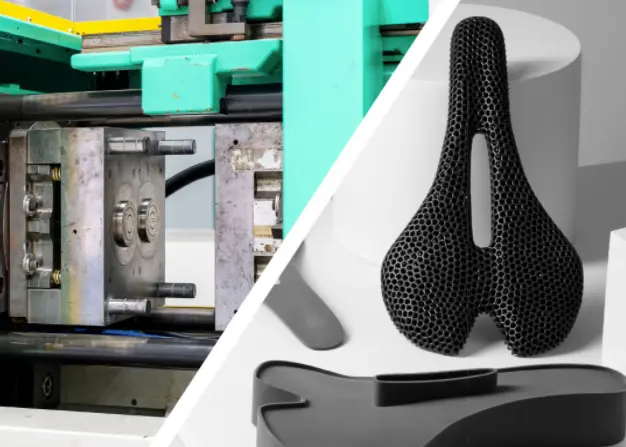
SLS-3D-Druck oder Spritzguss: Wann sollte man Spritzgussteile durch 3D-Druck ersetzen?
In diesem Whitepaper werden der Spritzguss und seine Vor- und Nachteile erörtert sowie der SLS-3D-Druck und die Anwendungen vorgestellt, bei denen er als ergänzende Technologie eingesetzt werden kann.
Partial Hand Solutions: Prothesen in Maßanfertigung
Mit der Gründung von Partial Hands Solutions verschrieb sich Matt Mikosz ganz der Entwicklung fortschrittlicher prothetischer Technologien, die von Amputation Betroffenen das Leben erleichtern sollen. Von Soldaten, die im aktiven Dienst Hände oder Finger verloren, bis hin zu Kindern, deren Gliedmaßen verschiedene Arten von Defekten aufweisen, hilft Mikosz Menschen aller Altersgruppen dabei, den Verlust oder das Fehlen von Körperteilen durch funktionelle Lösungen besser zu bewältigen. Prothesen dieser Art müssen für jeden Patienten maßgefertigt werden und zudem widerstandsfähig gegenüber hohen Belastungen sein. Entsprechend groß ist also die Herausforderung, dies zu einem erschwinglichen Preis umzusetzen.
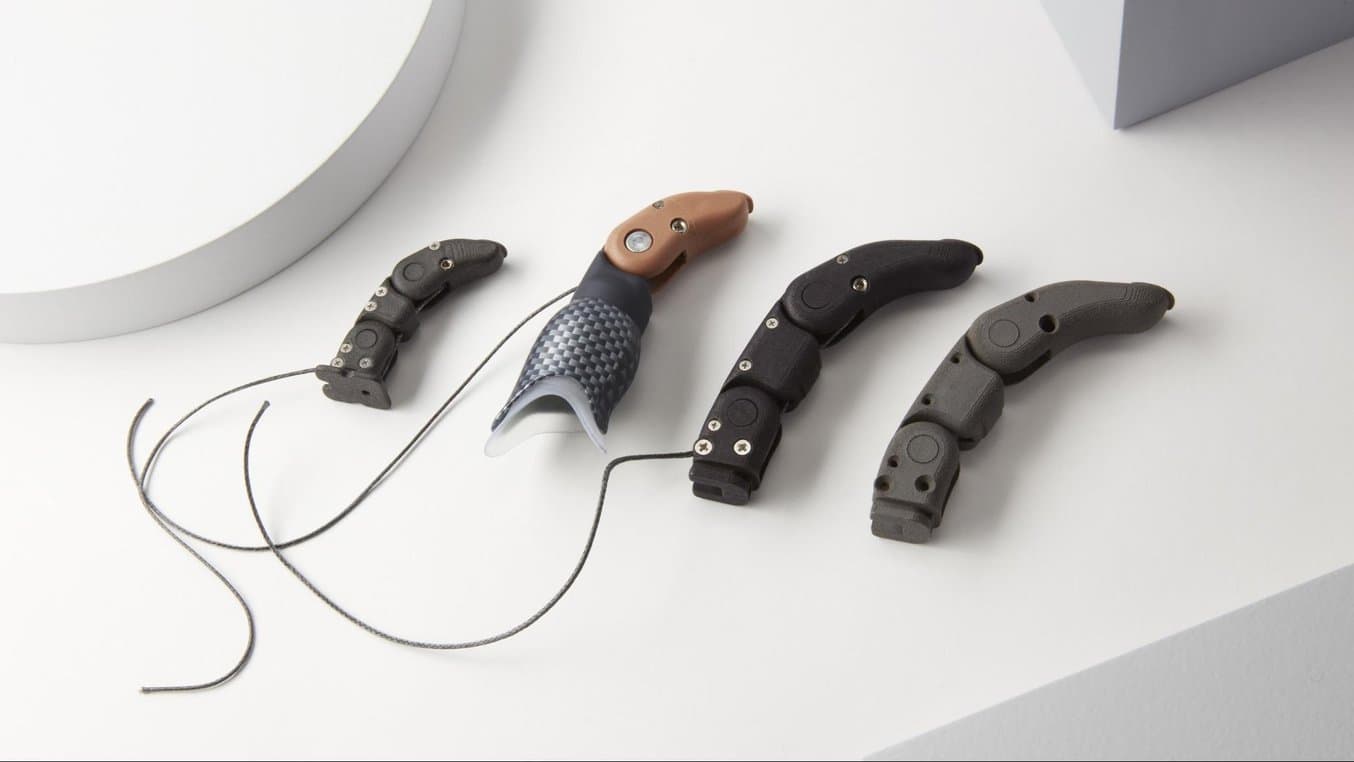
Die von Partial Hand Solutions entwickelten Fingerprothesen werden im Fuse 1 komplett mit Gelenkverbindung gedruckt.
In der Vergangenheit musste Mikosz eine Vielzahl von Teilen bei externen Dienstleistern in Auftrag geben, die diese via Spritzguss oder Zerspanung fertigten. Bis die fertigen Teile eintrafen, waren jedoch nicht selten Wartezeiten von bis zu zwei Wochen einzuplanen. Entsprechend gering war also der Spielraum zur Korrektur von Fehlern, zudem blieb insgesamt nur wenig Zeit, allgemeine Lösungen spezifisch auf einzelne Patienten zuzuschneiden. Mit dem Fuse 1 gedruckte Teile aus SLS-Nylonpulver waren dagegen buchstäblich über Nacht fertiggestellt. So konnte Mikosz binnen kürzester Zeit mehr Design-Iterationen realisieren und im Ergebnis auch deutlich präzisere Maßanfertigungen schneller an seine Patienten ausliefern.
„Für meinen Betrieb war 3D-Drucktechnologie geradezu ein Quantensprung. Als ich vor 14 Jahren anfing, musste ich Prototypen noch von externen Dienstleistern fertigen lassen – bei erheblichen Kosten, versteht sich. Große Experimente mit abweichenden Designs waren da kaum möglich, denn dies hätte mehr Prototypen und somit weiter in die Höhe schnellende Kosten bedeutet. Mit Fusion 360 und dem Fuse 1 ist der Kostenpunkt pro Prototyp dagegen um ein Vielfaches niedriger. Ich kann also stets so viele davon entwickeln wie nötig.“
Matthew Mikosz, Gründer von Partial Hand Solutions
Die Designs der Prothesen von Mikosz entstehen in Fusion 360. Für die Maßanfertigungen steht er im engen Austausch mit den Ärzten seiner Patienten, die er dank der integrierten Tools zur Remote-Zusammenarbeit von Fusion 360 direkt in den Entwicklungsprozess der Prothesen einbeziehen kann. Ist ein Design abgeschlossen, lädt er es einfach als STL- oder FORM-Datei zur Übergabe an den Fuse 1 herunter. Die so gedruckte Prothese ist dann auslieferungsfertig für den Patienten. Zuvor kann er dem fertigen Design jedoch noch einen individuellen Schliff verleihen. Hierzu hat er in seinem Labor die nötige Ausstattung zur Politur und Lackierung sowie zum Überzug von Mustern via Wassertransferdruck. Das sorgt für eine ansprechende Optik der 3D-Druckteile und damit einmal mehr für genau das, was Mikosz erreichen will: seinen Patienten zu mehr Mobilität und einer besseren Lebensqualität verhelfen.
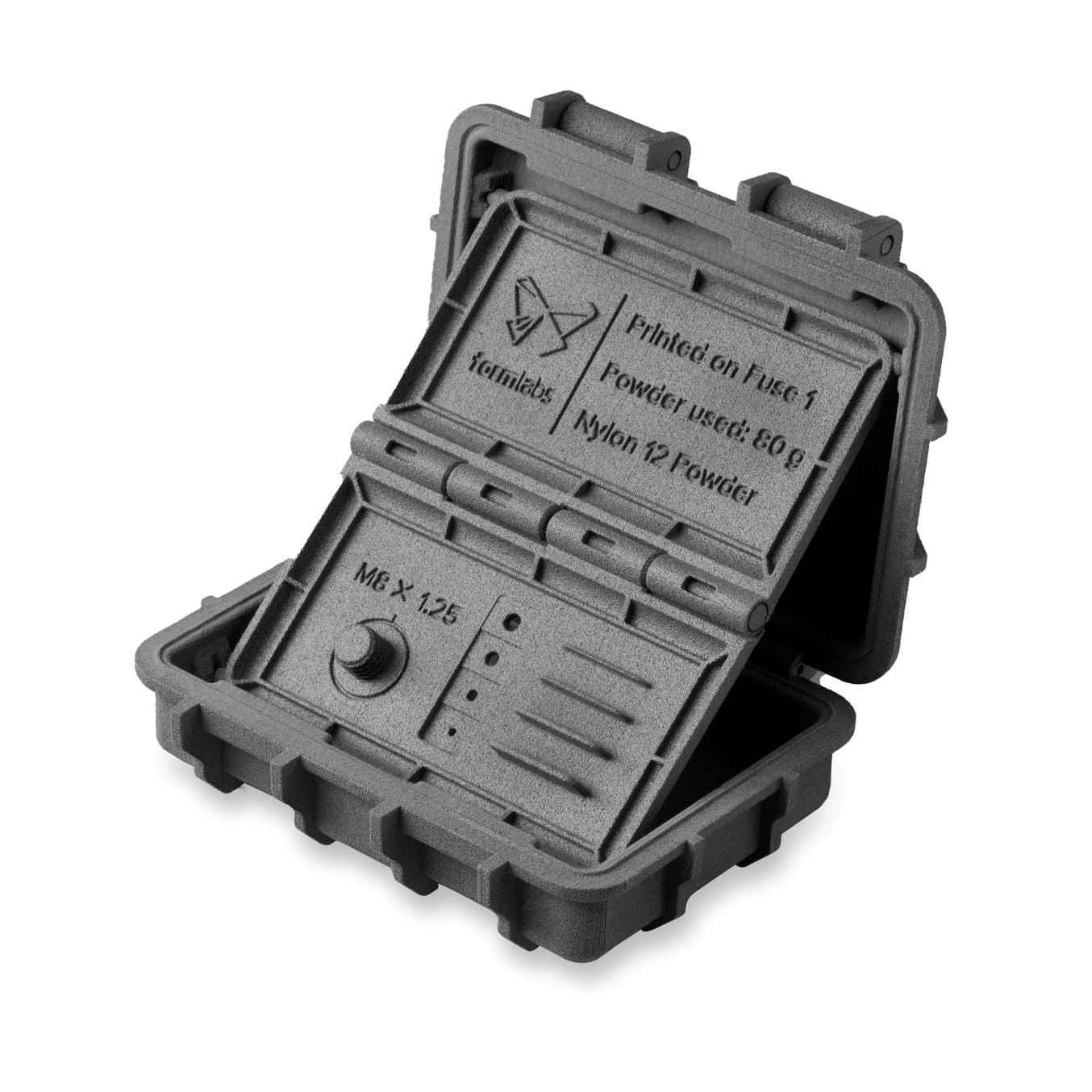
Kostenlosen Probedruck anfordern
Sie möchten die Festigkeit, Beständigkeit und Oberflächengüte von 3D-Druckteilen aus dem Fuse 1 aus erster Hand erleben? Dann fordern Sie direkt einen kostenlosen Probedruck aus Nylon 11 Powder oder Nylon 12 Powder bei uns an.